摘 要:针对舰船因排气管或其附件设置不合理所造成的危害,对舰船排气管设计计算进行二次开发程序设计,以90 000 t半潜船排气系统为例进行验证。结果表明,该程序的应用可提高设计效率,优化排气管的布置及其附件的设置,保证排气管安全可靠。
关键词:AutoCAD;二次开发;排气管;设计
舰船排气管的设计在舰船轮机设计中只占据极小的一部分,然而,由于舰船排气管设计缺陷所造成的后果却不容小觑。例如,某船由于排气管绝缘材料及厚度的选择不合理,造成机舱内排气管外包镀锌铁皮夏季温度超过60℃,船员根本无法在附近进行日常的巡查维护,最后只能通过给排气管加装一层护栏将就一下;再如,某船排气管由于支架设置不合理,增压器出口后的一段水平管段在试航时由于振动过大造成排气管破裂,试航回来之后重新设置支架并增加弹性支承才得以解决;又如,某船由于排气管支架设置不合理,造成烟囱内的一段垂直管段上的几个弹性支承受力不均,其中两个弹性支承根部焊接处断裂。此外,排气管波纹管裂纹、排气管背压过高也都曾有过记录[1]。因此,合理的排气管设计应引起设计人员足够的重视[2- 3]。
1 排气管设计的内容
1.1 排气管的布置及原理设计
舰船排气管的布置主要包括排气管在机舱(舱室)及烟囱内的走向、膨胀节的设置、固定支承及弹性支承的设置、防雨罩的型式、排气管附件(消音器、火星熄灭器、SCR等)的布置等[4];舰船排气管的原理设计主要是管材选型、放泄管的设置及水封型式等。排气管的布置及原理设计可以分两份图纸体现,也可以合并在一份图纸中。
1.2 背压计算
舰船排气管的背压计算主要有以下方法[5]。
1)查表法。
查制造厂提供的图表,查得直管段压降和管路附件的当量长度,计算总压降。
2)管段计算法。
管段计算法就是逐一计算每一管段的压降后叠加求和得总压降。
(1)按《船舶设计实用手册》提供的公式计算。
对于直管段摩擦阻力P1,有

(1)
式中:λ为直管段摩擦阻力系数,按可压缩流体的特性进行计算;di为管段内径,mm;l为管段长度,mm;V为烟气流速,m/s;ρ为烟气密度,kg/m3。
对于管路附件的局部阻力P2,有
P2=0.5·ζ·V2·ρ
(2)
式中:ζ为局部阻力系数。
(2)按《MAN guide》中提供的公式计算。
(3)当量计算法。将管路中的弯头、三通等附件转换为当量直管段长度,然后计算总压降。
1.3 膨胀量计算
直管段的膨胀需要进行计算进行人工补偿[7]。其计算方法主要有:
1)查表法。按照GB/T 12522- 2009提供的图表查出每米排气管的热膨胀量。
2)计算法。
(1)按照GB/T 12522- 2009提供的计算公式计算。
(2)按《船舶设计实用手册》提供的简易公式估算,每米排气管温度每升高100 ℃约伸长1.2 mm。
(3)按《船舶设计实用手册》提供的公式计算。
1.4 膨胀应力计算
σ=E·α·δΔt[8- 9]
(3)
式中:σ为管段受热时所产生的应力;E为材料的弹性模量;α为线膨胀系数。
1.5 绝缘厚度计算
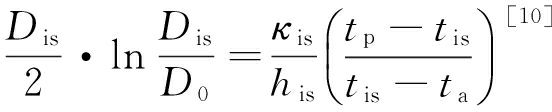
(4)
式中:κis为隔热材料的导热系数;his为隔热材料的换热系数,包括辐射换热系数和对流换热系数;tp为管内介质温度;tis为隔热层外镀锌钢板表面温度;ta为环境温度。
1.6 尾管长度计算
消音器排气口尾管长度可按CB*3338—88提供的公式计算。
2 程序设计
尽管舰船排气管的设计在舰船轮机设计中只占据极小的一部分,但它的计算却涉及到流体力学、材料力学、传热学、材料学以及声学等多方面的内容[11- 15]。由于计算量较大,设计人员在设计过程中也仅仅是以计算背压和校核膨胀量为主,必要的时候进行一下绝缘厚度的校核,膨胀应力一般交由弹性支承厂商进行校核,消音器尾管长度只有在对环境噪音非常苛刻的时候才会校核。
目前国内的相关设计基本上都是在AutoCAD的环境下进行的,一般的设计单位也都拥有计算排气管背压的Excel模板,但这些对合理的排气管设计来说都有所欠缺,而且效率不高、可视化也不强[16]。
2.1 编程工具选择
目前的AutoCAD二次开发的工具有VisuaILISP、VBA、ObjectARX以及.NET API等[17]。.NET API在AutoCAD 2006开始推出,功能强大而学习要求低。因此,就以.NET API作为本次二次开发的编程工具。
2.2 数据处理
2.2.1 通用参数
通用参数是排气管计算的基本参数,如:烟气参数(温度、密度、动力粘滞系数等,如表1所示)、绝缘材料参数(导热系数、工作温度等)、MAN guide中推荐的管件阻力系数(角度、半径直径比、阻力系数等)、《船舶设计实用手册》中推荐的管件阻力系数(角度、半径直径比、光滑管、粗糙管、阻力系数等)、机舱流动风速、管路粗糙度,等。这些参数在相关的计算中都有可能用到,因此,将这些参数以表的形式都保存到数据库中,程序随用随取。数据库采用Microsoft Access数据库。
表1 烟气参数表(部分)
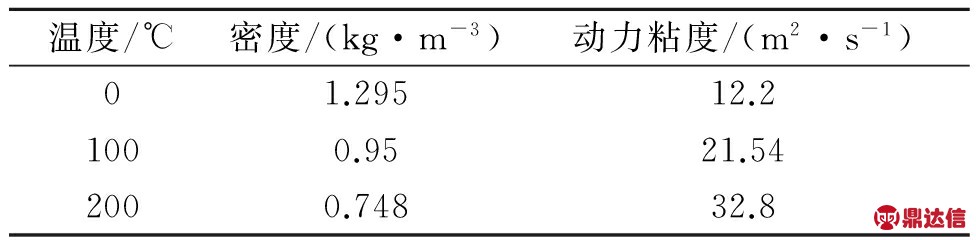
2.2.2 排气管参数
排气管参数是指当前项目排气管相关的一些参数,包括排气管外径、壁厚、绝缘材料类型、绝缘材料厚度、当前管段类型(直管段、弯管、废气锅炉、消音器、SCR等),等,这些参数随项目而变。因此,利用AutoCAD图元的XData属性将这些参数附着在指定的图元上,程序执行时可随时读取所需的参数[18]。
2.3 前期准备
新建一个AutoCAD图形文件,根据排气管布置图按各管段的相对位置在三维环境中绘出各排气管的走向图,并在每根排气管的起点绘出代表排气管横截面的圆。代表不同排气管的图元可以放置在不同的图层中,也可放在同一图层中。放在同一图层中时,要对各个排气管进行编组(AutoCAD命令“GROUP”或“G”)。图层名称或编组名称应与图1中的归属定义一致。
为了绘图的方便,一般采用把代表不同排气管的图元绘制在不同的图层中的方法。
2.4 程序功能
2.4.1 定义输入参数
定义输入参数就是将当前排气管的基本参数,如废气参数、绝缘材料参数、柴油机参数、排气管壁厚(程序直接读取排气管外径参数)等,见图1,“附着”后,定义的输入参数都保存在当前图形中。
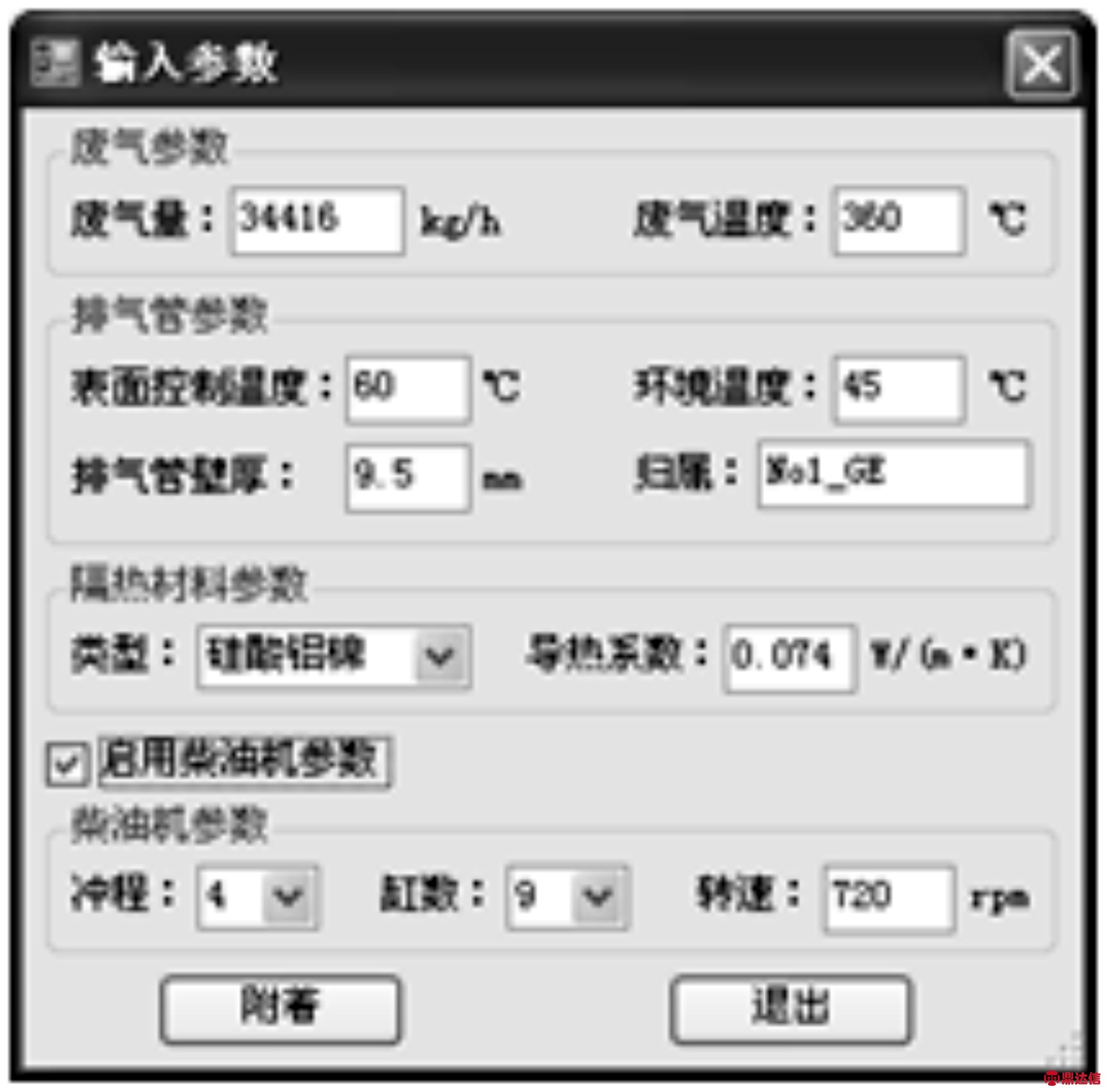
图1 输入参数界面
2.4.2 查看输入参数
执行查看输入参数功能可以直接命令程序读取先前附着的输入参数。
2.4.3 初始化
初始化功能先自动进行管段编号,然后根据输入参数预定义各管段。初始化会提示用户是按图层进行初始化还是按编组进行初始化。
2.4.4 定义/查看管段信息
初始化完成后即可进行管段定义,见图2。其中的类型包括了实际排气管附件,如,“PIPE”、“ELBOW”、“BOILER”、“SILENCER”、“BELLOW”、“REDUCER”、“DAMPER”、“SCR”等等,其中的直管段(“PIPE”)和弯头(“ELBOW”)已经由程序在初始化时自动定义。可以直接查看以决定是否修改。
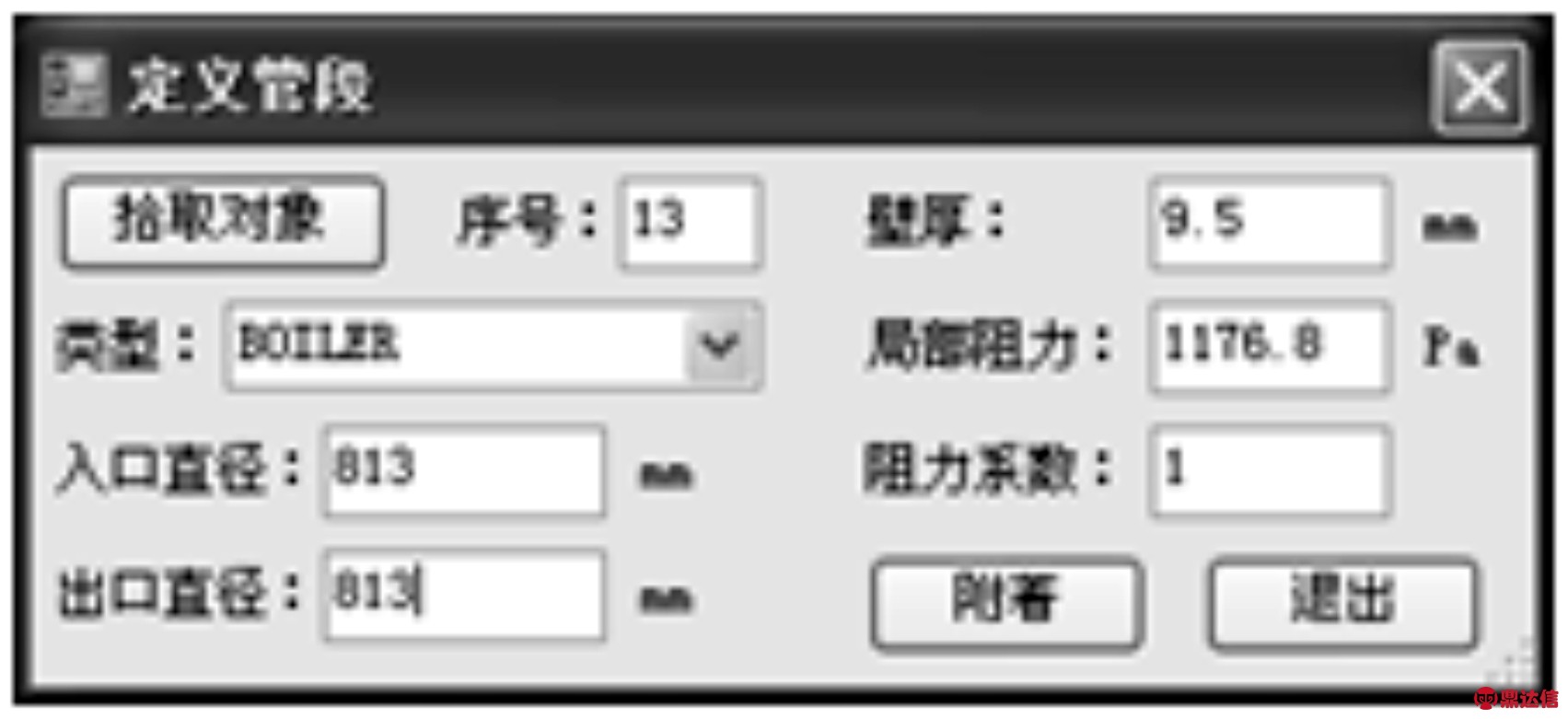
图2 定义管段
2.4.5 计算背压/生成背压计算报告
所有管段信息定义完成后,可以令程序进行背压计算。程序采用的计算方法是《船舶设计实用手册》中的流体力学的公式进行计算,计算完成后可以直接生成背压计算报告。
2.4.6 校核隔热层厚度
程序可根据输入参数先计算出辐射换热系数和对流换热系数,然后根据隔热材料的换热系数计算出保证表面控制温度下的一个5进位隔热材料的最小厚度。
2.4.7 定义/查看支承信息
如果需要校核排气管的支承设置是否合理,可以在程序中进行支承位置、支承类型及支承能力等参数的定义,同样也可进行信息查看。
2.4.8 校核支承
支承定义完成后即可对支承的受力进行校核,由于直管段可通过膨胀节进行人工补偿,其受力仅考虑管段重力,此处不予考虑振动时的冲击力和船舶摇晃时的横向力,弯头处采用自然补偿,其附近的支承还承受热应力,是校核的重点[19]。
2.4.9 校核膨胀节
支承定义完成后同时也可进行膨胀节的校核,主要是校核膨胀节的位移是否能满足附近直管段的膨胀量。
2.4.10 校核防雨高度
对于隔热材料未包覆到烟囱顶板的排气管,防雨罩的高度不会造成什么影响,因高度不足而进入的雨水会被高温蒸发。但对于隔热材料未包覆到烟囱顶板的排气管,尽管因高度不足而进入的雨水也会被高温蒸发,但蒸发的雨水会进入隔热材料,造成这一区域隔热材料的失效。
在校核防雨罩高度之前,先要利用程序定义烟囱顶板位置及防雨罩的安装位置,然后就可以获得这一段管段的膨胀量,只要防雨罩的防雨高度大于该膨胀量加上一定的余量即可。
2.4.11 计算尾管长度
程序根据图1提供的柴油机参数,可以很顺利地获得消音器后的排气管艉管长度。该功能对非柴油机排气管不起作用。
3 计算示例
以90 000 t半潜船的排气系统为例,其排气管布置图见图3(为简要说明,只取其左舷的3台主发电机和1台辅助发电机),相应的排气管走向图见图4。
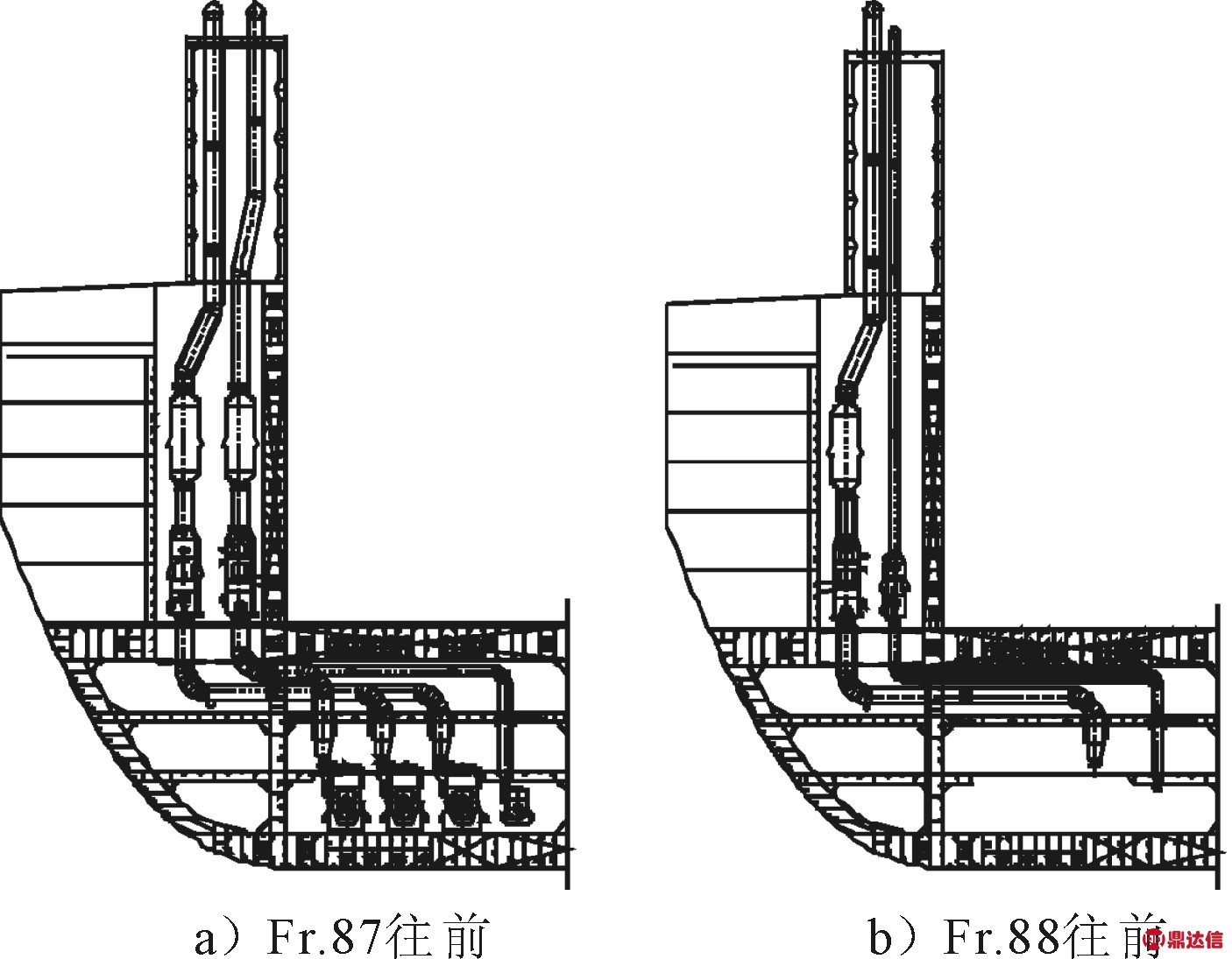
图3 原船排气管布置
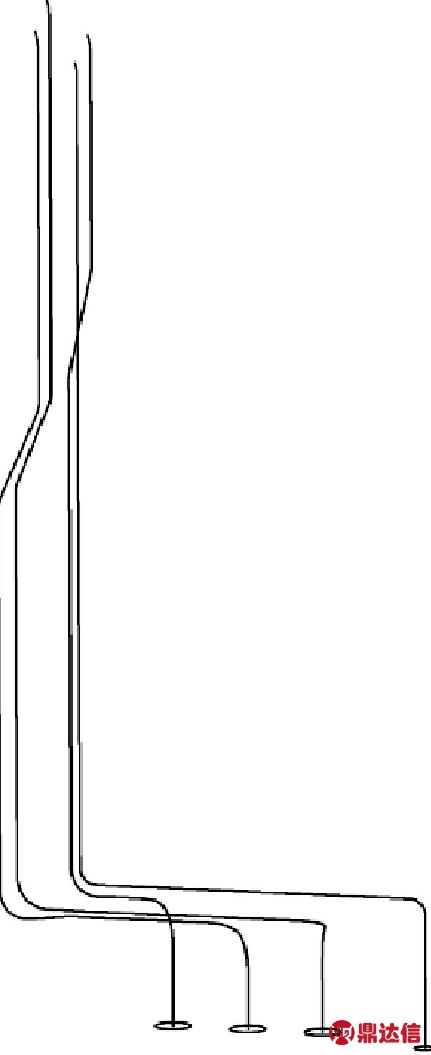
图4 排气管走向
3.1 背压计算
1号主发电机(图3中左边第1台)排气管的背压计算报告部分内容如下:
序号 管段类型 管段阻力 阻力系数
…… …… …… ……
8 BELLOW 331.8 0.150
…… …… …… ……
10 PIPE 27.8 0.020
…… …… …… ……
17 SILENSER 784.5 1.000
…… …… …… ……
23 ELBOW 331.8 0.065
…… …… …… ……
总阻力:2 986.2 Pa
最大允许背压为4 000 Pa(柴油机制造商提供),计算结果满足要求。
3.2 隔热层厚度计算
程序计算的推荐隔热层厚度为70 mm,实船包覆的隔热层厚度采用推荐厚度。
4 与其他软件的交互
对于可以使用AutoCAD图元的三维设计软件(如SB3DS等),设计人员可以直接调入已有的排气管走向直接进行排气管三维设计。同样,从这类可导出AutoCAD图元的三维设计软件中导出排气管走向,也可加以利用,经过定义后完成上述计算。
5 结论
程序的开发给设计人员带来了极大的便利,提高了设计效率,同时,排气管及其附件的布置也更合理,从设计上保证了排气管背压计算更准确,优化了膨胀节、支承、消音器等的设置。
当然,要保证排气管在实际运行中的良好状态,施工工艺、材料质量、废气源状态等各方面因素也都不可忽略。