摘 要:将硝酸镍溶液与氧化石墨烯溶胶混合后冷冻干燥,然后通过真空热还原得到负载过渡金属催化剂的石墨烯粉末。以天然气为碳源,在1 000 ℃下采用化学气相沉积工艺,在石墨烯表面和边缘生长碳纳米管,碳纳米管将孤立的石墨烯片层结构有效地联接起来,组成空间互联网络结构,从而构建了电子、热能和载荷有效传输的通道。
关键词:石墨烯; 碳纳米管; 化学气相沉积
1 Introduction
Graphene, one atomic layer thickness (0.335 nm), is a kind of novel two-dimensional atomic crystal with sp2 hybridized carbon atoms arranged in honeycomb lattice like the single atomic layer of graphite. Graphene is the ideal two-dimensional nanomaterial at present, and is the basic unit to build zero-dimensional fullerenes, one-dimensional carbon nanotubes (CNTs) and three-dimensional graphite materials[1-3]. The connection between the carbon atoms in graphene is very flexible, and hence, when there is external mechanical force, the atomic plane is bended but carbon atoms do not have to rearrange to accommodate external force. This stable structure gives rise to the excellent flexibility of graphene[4]. The electron of graphene can travel in the orbit without being scattered off course by lattice imperfections and foreign atoms. The velocity of electron reaches 1/300 of the light speed, which is 100 times faster than that of the silicon chips in the computer. Therefore, graphene when made as tiny transistors, can significantly increase the CPU speed of a computer, and when made as cable, can greatly improve its conductivity and strength compared with the traditional copper and aluminum. Because the thermal conduction mechanism of graphite material is based on electrons, graphene also has a high thermal conductivity up to 5 300 W·m-1 ·K-1, which is three times as much as that of diamond and graphite, and 25 times as much as that of traditional silver, copper and aluminum[5]. Therefore, it also has an attractive prospect in the application as a high thermal conducting material. Graphene has the highest strength, even harder than diamonds, and 100 times higher than the strength of the best steel in the world[6]. Graphite is rich in the resources on the earth, meanwhile graphene has the highest strength, the best electrical and thermal conductivity, so it enjoys fascinating development prospects in the future. Currently, there are many methods for the preparation of graphene. The oxidation-reduction method, in which graphite is oxidized to graphite oxide[7-11] that is dispersed in liquid phase for further processing, is easy to operate and control and suitable for mass production. So it is the main preparation method for graphene. But the disadvantage of this method is that the crystal size of graphene is small and the excellent properties of graphene can not be retained. A number of previous works have reported chemical vapor deposition (CVD) growth of CNTs on graphene. A 3D pillared vertically-aligned CNT (VACNT)-graphene architecture with a controllable nanotube length was demonstrated, which has a high specific capacitance and remarkable rate capability [12]. Microsupercapacitors based on 3D graphene/CNT carpets were fabricated in-situ on nickel electrodes[13]. A method to bond graphene and single-walled CNTs seamlessly during the growth stage was disclosed[14]. The metal-graphene-CNT structure was used to directly fabricate field-emitter devices and double-layer capacitors[15]. A simple and scalable method to fabricate 3D few-layer graphene-multi-walled CNT hybrids on metal foam foils (nickel foam) via a one-step ambient pressure CVD was described[16]. 3D graphene-CNT hybrids were synthesized by a two-step CVD method, which can be used as novel 3D electrochemical electrodes for sensing applications[17]. A hybrid system with VACNTs grown on reduced graphene films was reported[18]. In this paper, we investigated the reduction methods of graphene oxide to graphene and the effect of concentration of catalyst on the growth of nanotubes on the surface and edge of graphene lamellae structure. The CNTs overcomes the defect on the small size of graphene, then the isolated graphene lamellae structure can be connected together effectively to form a spatial network structure by the CNTs, seting up the effective transmission channel for electrons, thermal energy and load.
2 Experimental
The graphene oxide was synthesized according to the modified Hummers method [7]. A mixture of a transition metal salt solution and the graphene oxide solution was frozen at 80 ℃, then dried in a vacuum freeze-drying machine (Beijing Bo N2000 company). The apparatus for CVD experiment was an electrical furnace equipped with a horizontal quartz tube 50 mm in diameter, 1 000 mm in length, and 150 mm long in reaction zone in the middle shown in Fig.1. The dried powder was uniformly dispersed at the the bottom of a quartz boat that was put into the reaction zone the CVD furnace, heated up to 300 ℃ within 2 h under vacuum, and kept the vacuum condition at this temperature for 1 h. The vacuum valve was closed, and the high purity argon was filled slowly. The furnace was heated up to 1 000 ℃ within 4 h under the protection of the high purity argon. Then methane was introduced into the furnace as the carbon source and the CVD reaction took place for 30 min. The flow rate of methane was controlled at about 10 cm3/min, and argon 60 cm3/min. Finally, the methane and power were turned off to let the furnace cool down to room temperature under the protection of argon. The samples were analyzed by a TESCAN MAIA3 LMH 6700F scanning electron microscope (SEM). The powder samples were compressed into pellets by an infrared tablet compression machine with thicknesses of around several hundred micrometres and bulk densities of around 1.0 g·cm-3. The electrical conductivity was measured by a standard four-probe resistivity measurement system with an SZ85 digital multimeter (Suzhou Telecommunication Factory, China). In order to eliminate contact resistance, and each sample pellet was cut into rectangular shape and measured three times to obtain an average value.
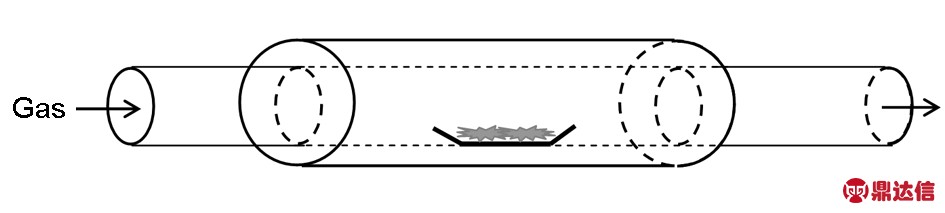
Fig. 1 Schematic diagram of the horizontal CVD furnace.
3 Results and discussion
3.1 Effect of high temperature treatment on morphology of graphene oxide
The graphene oxide, which is prepared by the improved Hummers method, has a very large surface area. There are a large number of adsorbed water molecules on its surface since the graphene oxide powder is prepared by vacuum freezing drying method. Also the graphene oxide powder contains hydroxyl, carboxyl, carbonyl groups and other rich oxygen-containing functional groups. Graphene synthesized by reducing the graphene oxide with hydrazine hydrate and vacuum freezing drying method, still adsorbs a large amount of water molecules on its surface and contains a small amount of oxygen-containing functional groups. The graphene oxide has large pores due to the rich hydroxyl, carboxyl and carbonyl functional groups on its surface and large water adsorption, which is reflected as in Fig.2a. Fig.2b is the SEM image of the graphene oxide sample heated to 1 000 ℃ within 5 h under the protection of argon, which shows that the pore size is reduced significantly. This could be ascribed to the fact that removal of the oxygen-containing functional groups of the graphene oxide at high temperature eliminates the polar interaction among layers of graphene oxide, giving rise to collapse of large pores.
Fig.3a is the morphology of the graphene obtained by hydrazine reduction. As shown in Fig.3a, pore size of graphene is still very large as the result of large water adsorption and a small amount of oxygen-containing functional groups. Fig.3b is the SEM image of the reduced graphene heated to 1 000 ℃ within 5 h under the protection of argon. It can be seen from the Fig.3b that the pore size of the graphene is reduced by the high temperature treatment that removes the oxygen-containing functional groups[19-21]. The reason for the reduction of pore size is similar to heat-treated graphene oxide.
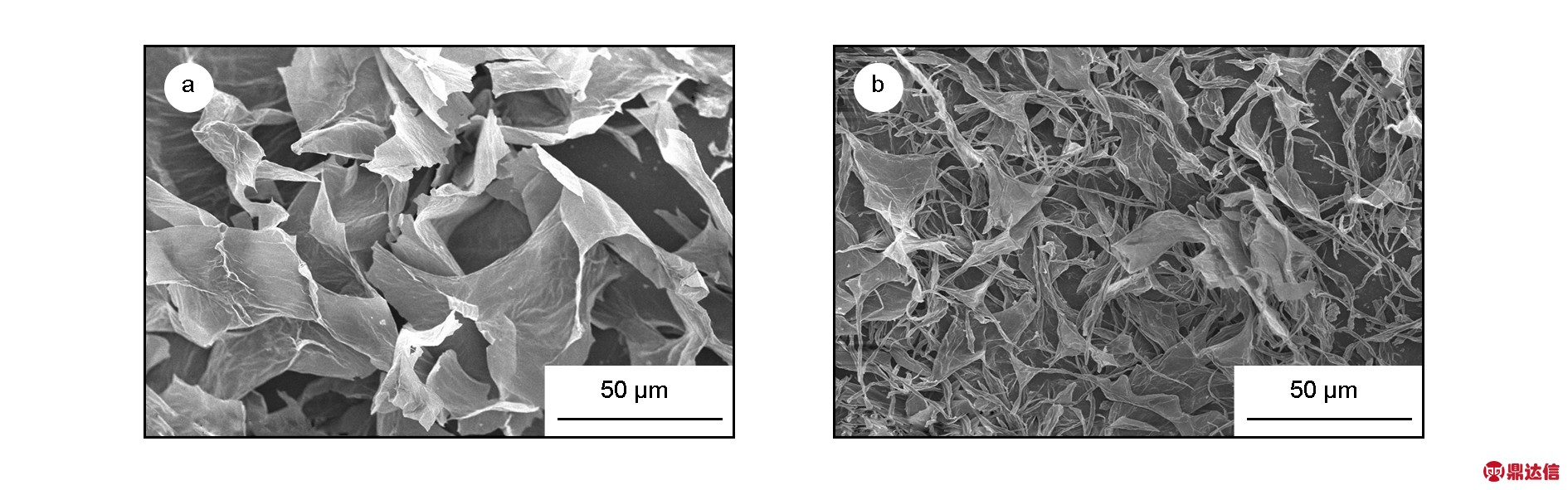
Fig. 2 SEM morphologies of (a) graphene oxide and (b) the sample after high temperature treatment.
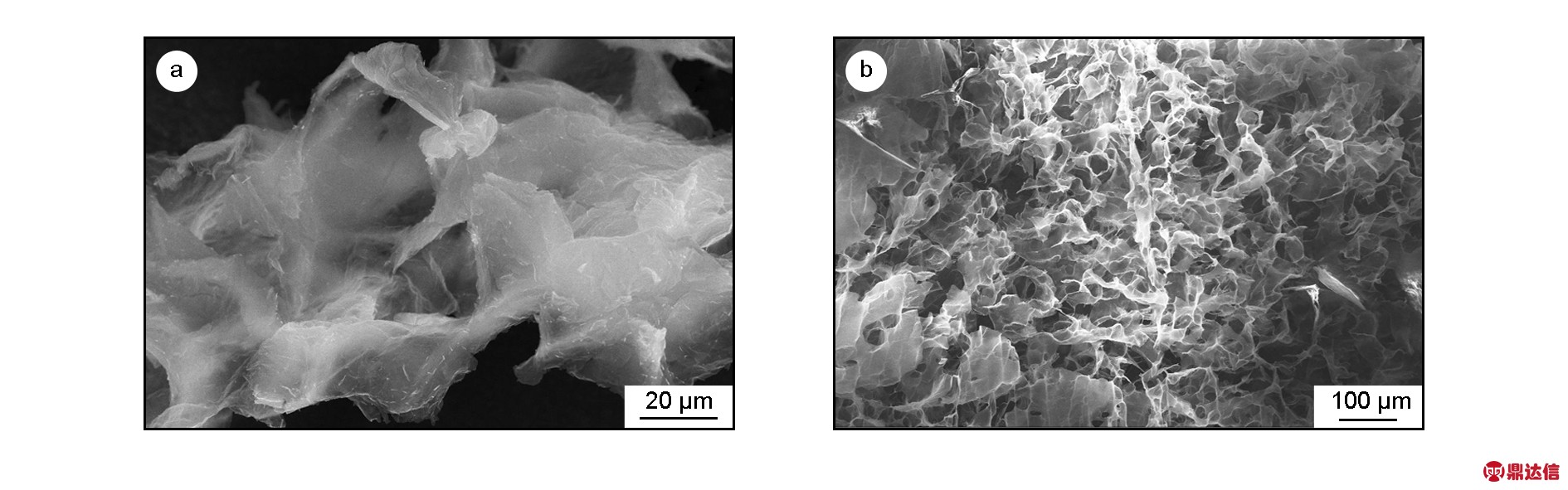
Fig. 3 SEM morphologies of (a) the hydrazine-reduced graphene and (b) the sample after high temperature treatment.
based on the analysis above, we changed the original experimental conditions. The as-prepared graphene oxide powder was uniformly dispersed at the bottom of the quartz boat and put into the horizontal CVD furnace as shown in Fig.1. The furnace was slowly heated up to 300 ℃ within 3 h under vacuum, and continued to vacuum at this temperature for 1 h, then the vacuum valve was closed and the power was turned off to let the furnace cool down to room temperature. A small amount of thermally-reduced sample was removed for detection, and the remaining sample still was put again into the horizontal CVD furnace and heated to 1 000 ℃ within 4 h under the protection of high purity argon. Methane was introduced into the furnace as the carbon source and the CVD reaction took place for 30 min. Fig.4 is the SEM image of the thermally-reduced sample. As shown in Fig.4, the thermally-reduced sample has a large pore size and thin pore wall. Water molecules and oxygen-containing functional groups of the graphene oxide are gradually removed, and finely reduced graphene is obtained due to the slowing heating up and vacuum condition.
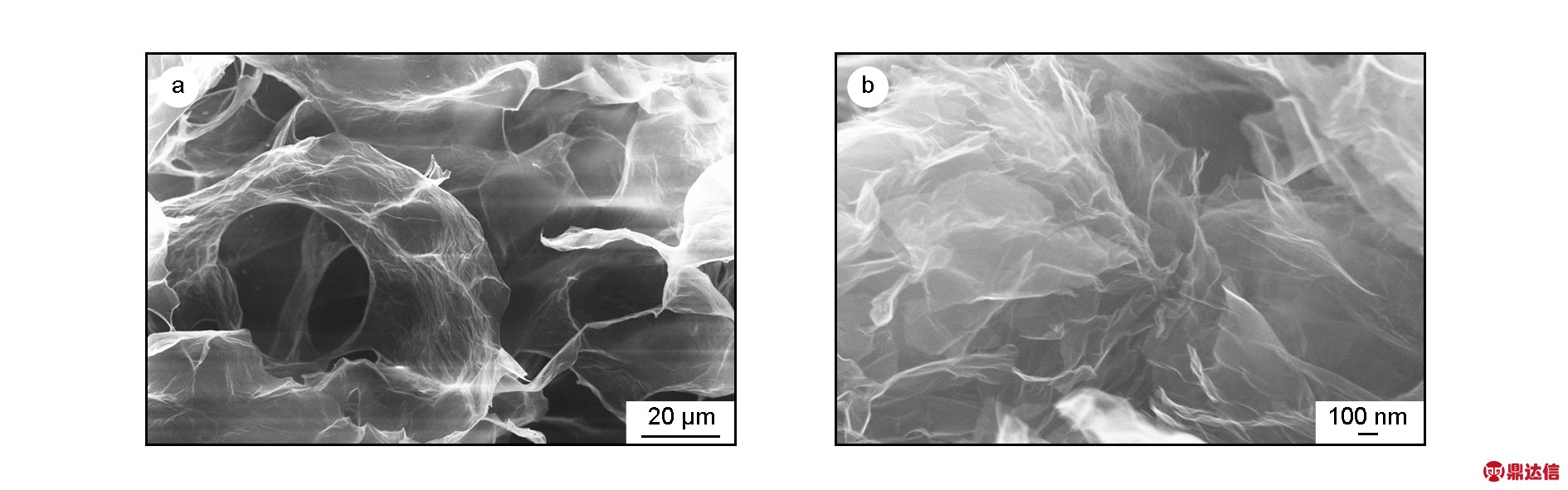
Fig. 4 SEM morphologies of (a) the thermally-reduced graphene and (b) the the sample after high temperature treatment.
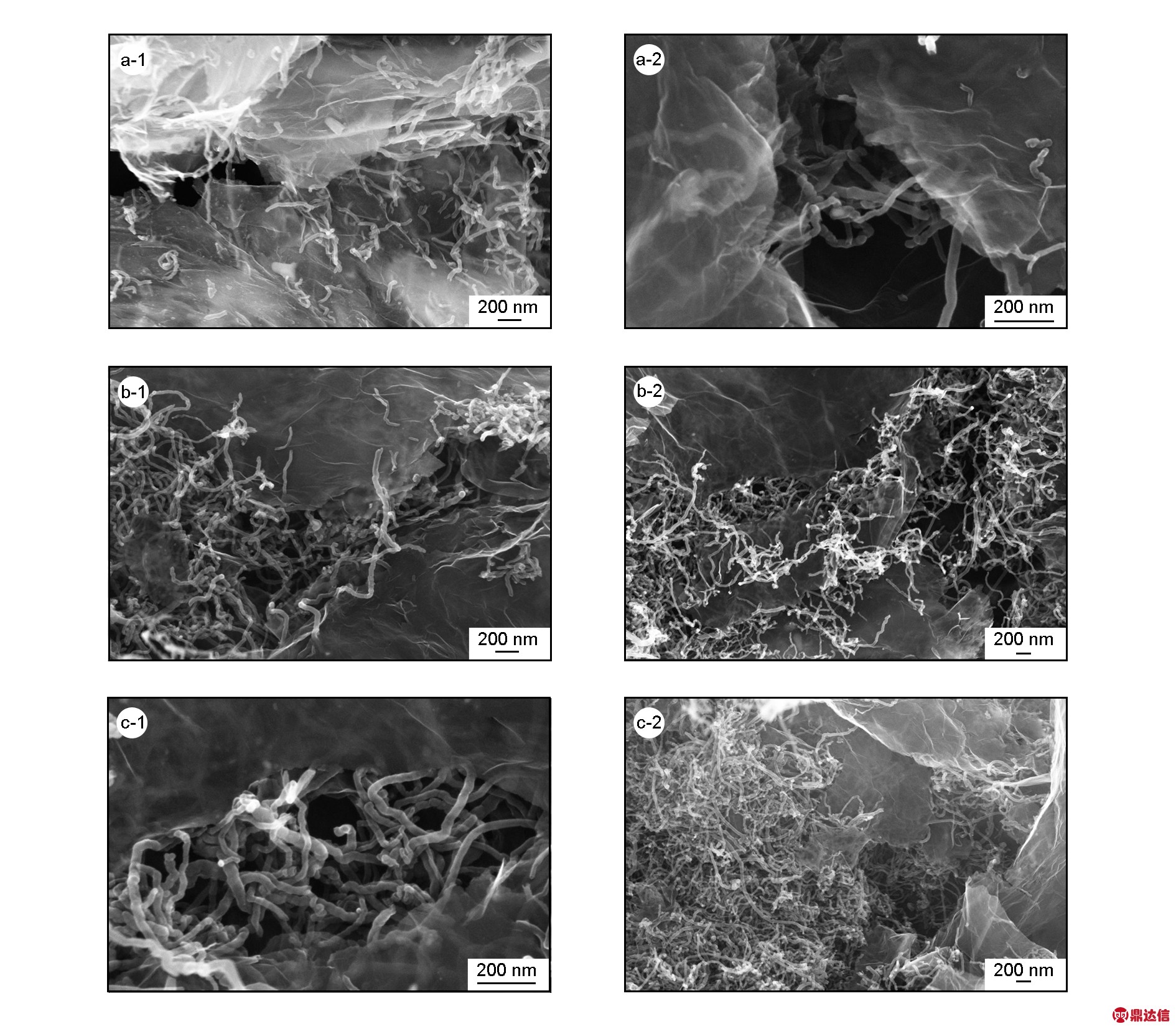
Fig. 5 SEM images of CNTs grown on graphene.Graphene oxide immersed in (a) 0.005 mol/L of [Ni2+]; (b) 0.01 mol/L of [Ni2+] and (c) 0.02 mol/L of [Ni2+].
3.2 Effect of catalyst concentration on CNT growth
It is widely believed that carbon atom clusters formed by adsorption and decomposition of hydrocarbon compounds on the catalyst surface play critical roles in the growth mechanism of CNTs, and the carbon atom clusters diffuse through metal particle phase to the other side of catalyst surface, which deposit on this side, forming CNTs. Therefore, the particle size and particle concentration of the catalysts are the main factors that play important roles in CNT growth. The edge and surface of graphene are the active adsorption sites CNT and the specific surface area of graphene is up to 2 630 m2/g theoretically. Nickel nitrate solution was first mixed with graphene oxide that contains rich oxygen-containing functional groups, most of the Ni element were adsorbed on the edge of the graphene oxide other than the surface of the graphene, so we can see from Fig.5 that most of the CNTs grew on the edge of the graphene. Fig.5a, b, c are the SEM morphologies of samples after CNT growth by CVD with the Ni(NO3)2 concentrations of 0.005, 0.01 and 0.02 mol/L, respectively. As revealed in Fig.5, the CNT density on the surface and edge of graphene increases with the Ni(NO3)2 concentration. When the concentration of Ni(NO3)2 in the solution is small as shown in Fig.5a, the concentration of Ni particle loaded on graphene is low, so the CNTs grew sparsely. While the concentration of Ni(NO3)2 in the solution is high as shown in Fig.5c, the density of CNTs grown on graphene is increased significantly.
3.3 Effect of CNTs grown on graphene on the electrical conductivity
Table 1 lists the electrical conductivity of the graphene after the vacuum thermal reduction and the graphene with CNTs grown on its surface and edge. From the experimental results, it is found that the conductivity of the graphene increases after CNTs growing on its surface, which is ascribe to the fact that CNTs connect the isolated graphene lamellae effectively to form a spatial network structure that acts as electron transmission channels. We can also see from Fig.5, the SEM image of the samples, the CNTs grown on the edge or the surface of graphene effectively connect the isolated lamellae graphene together. The experimental data in Table 1 also shows that the conductivity increases with the Ni(NO3)2 concentration. And the reason is that the higher is the concentration of Ni(NO3)2 in solution, the larger the density of CNTs on graphene, and the better the connection of the lamellae structure of the graphene by CNTs, the higher is the conductivity.
Table 1 Electrical conductivity of the samples.

4 Conclusions
Using methane as the carbon source, CNTs were grown on the surface and edge of the graphene by CVD at 1 000 ℃. The isolated graphene lamellae can be connected effectively by CNTs to form a spatial network structure CNTs that provides the effective electron transmission channels.
[1] Matthew J A, Vincent C T, Richard B K. Honeycomb carbon: A review of graphene[J]. Chemical Reviews, 2010, 110(1): 132-145.