摘要:硅片分离过程中需顶针将其顶起直至脱离基座,方便机械手抓取硅片。顶针加工质量的优良对硅片分离过程影响很大。针对硅片顶针磨削成型问题,设计了一台三轴联动硅片顶针磨床。首先分析了硅片顶针加工技术要求,拟定了顶针加工工艺,设计了磨床机械结构本体;之后,规划了磨床磨削控制系统功能,并采用“PC+运动控制卡”的方式开发了相应的运动控制模块、参数设置模块、文件管理模块,视觉检测模块等;最后,通过实验验证了磨床设计的合理性和可靠性。
关键词:运动控制卡;工业CCD;磨削;展成法
0 引言
半导体硅片经一系列加工处理后输出反应室时需特殊的顶针将其顶起,使其与基座分离[1]。顶针传统的加工方式是依靠工人手动控制工作台进行磨削加工,生产效率低下,对工人技术依赖较高,无法实现可重复加工。
顶针加工最关键的是顶端的圆弧磨削,由于圆弧加工精度要求很高,传统的控制技术已经满足不了顶针磨削机床的需求,而计算机数控技术(CNC)的出现使得顶针磨削自动化变为可能[2]。目前,我国的硅片顶针磨床系统尚在研制阶段。近些年来,运动控制器因为其控制精度高、响应速度快、开放性好、体积小等优点,被机械自动化行业广泛应用[3-8]。本文针对顶针的加工,设计了一款专用磨床,其控制系统采用"PC+运动控制卡"的方式组成,实现对硅片顶针的自动化加工。
1 磨削工艺的确定
1.1 硅片顶针加工技术要求
顶针的加工非常精密,如图1所示,其前端为锥面,加工公差为±0.5°。最前端为一圆弧,加工公差为±5μm。
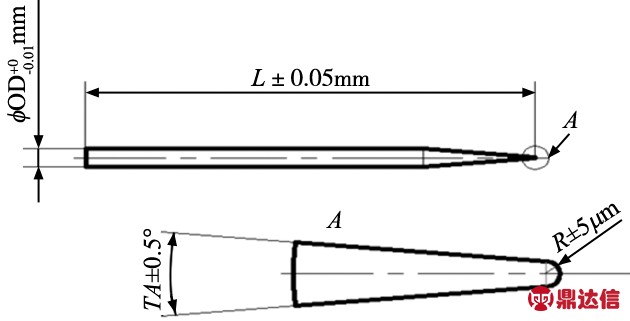
图1 硅片顶针工艺图
1.2 硅片顶针加工工艺分析
本文以某公司生产的锥度10°、顶端圆弧半径25μm的顶针为例对顶针磨削展开讨论。
1.2.1 锥度加工工艺
首先对顶针锥度进行加工。图2为加工锥度示意图,其过程是将棒料贴近砂轮,以待加工棒料与砂轮端面夹角为5°的位置为起始位置,进行X、Y轴进给即可完成锥度磨削加工。进给方式、进给顺序和进给量依次为y1,x,-x;y2,x,-x; ……yn ,x,-x。其中Y轴进给次数n与单次进给量yn,可由实验调试具体确定,通过实验调试,不断改变进给量或进给次数,找到磨削效果最好、磨削时间最短的最优进给方案,实现顶针锥度的加工。

图2 锥度磨削示意图
1.2.2 减小90°切削余量工艺
锥度加工后完毕,存在90°时切削余量过大进而圆弧加工过程中造成断针现象频发的问题。为避免此现象发生,需进行Y轴单轴进给以减小切削余量,如图3所示。
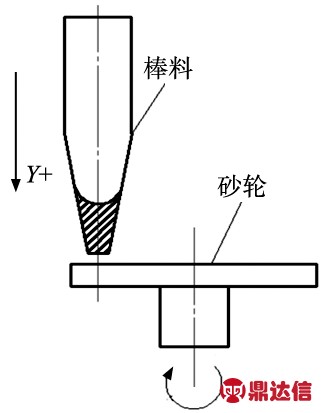
图3 减小90°切削余量加工示意图
1.2.3 展成法圆弧磨削工艺
顶针的圆弧磨削采用展成法[9-10],如图4所示。展成法圆弧磨削即顶针在夹具主轴带动下绕自身轴线转动,砂轮在电机带动下绕自身轴线转动。初始时棒料锥面与砂轮端面贴合,通过磨床三轴联动带动棒料转动实现圆弧加工。

图4 展成法圆弧加工
如图4b为转台中心和棒料间的位置关系,O为棒料待加工圆弧圆心,A为转台中心。展成法圆弧磨削成型实质上就是保持待加工圆弧圆心O不动,同时转台中心A围绕圆心O转动。设OA=l,∠AOB=α旋转角度为θ,初始时,使棒料锥面与砂轮端面贴合,棒料轴线与砂轮端面成5°。此时,记录A点坐标为(x1,y1,5°),设此时OA相对于X轴夹角为β,则β=α+5°。
设待加工圆弧圆心O点坐标为(x0,y0,r0),则:
(1)
图4a中加工完成时,转台旋转了θt=85°,取插补步长为t=0.1°,插补次数为:
n=θt/t
(2)
θ=β+it(i=0,1,2..n)
(3)
设旋转过程中任意时刻转台中心A点坐标为(x,y,r),则:
(4)
式中根据式(2)计算出计算出展成法中的圆弧上的一系列点,通过插补实现转盘中心A绕待加工圆弧圆心的转动,在此过程中,如图4a所示,棒料旋转过程中始终与砂轮端面相切于点D,通过砂轮的磨削不断去除多余材料最终成型为圆弧。
综上所述,顶针从棒料到成品的磨削工艺为:上料→锥度加工→减小90°切削余量→视觉识别待加工圆弧圆心→展成法圆弧磨削→视觉检测。
2 机械结构设计
本文设计的半导体硅片顶针磨床含有三个自由度,X、Y、R三轴联动实现展成法圆弧磨削,在此过程中,S轴通过同步带传动带动主轴旋转进而带动顶针棒料旋转;相机采用海康威视工业相机,分辨率2592×1944;镜头采用慕藤光MZ7.0XC变倍镜头,能在1.4X~9X之间自由变换,且不改变工作距离。半导体硅片顶针磨床如图5所示,该磨床各轴的重复定位精度参数如表1所示。
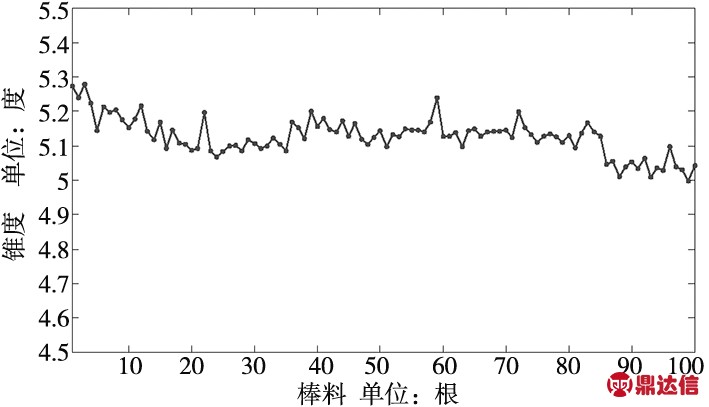
图5 顶针磨床设计图
表1 磨床各轴重复定位精度
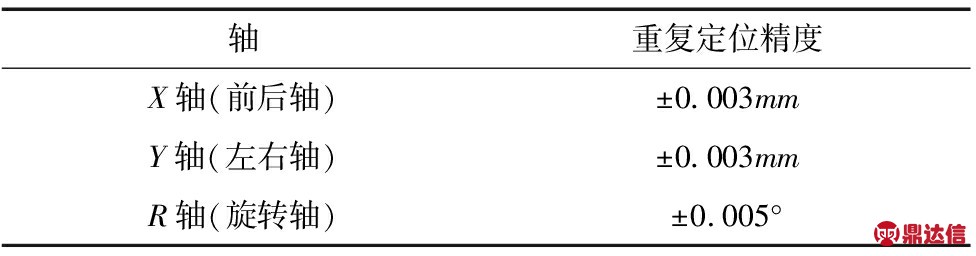
3 控制系统设计与样机的实验
3.1 控制系统组成
本文设计的磨床控制系统,采用“PC+运动控制卡”作为控制系统核心,外接端子板连接伺服驱动器实现对电机的控制图如图6所示。
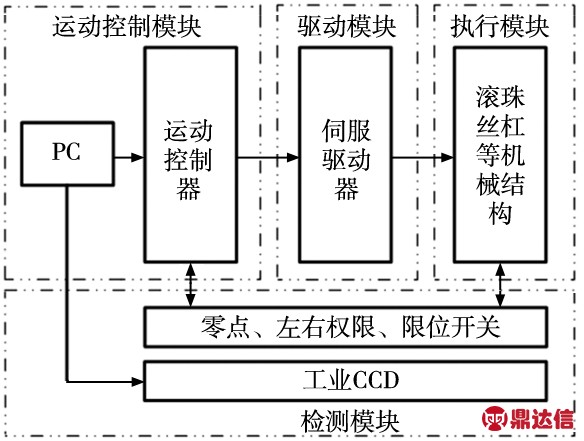
图6 控制系统设计简图
3.2 控制系统软件界面
系统人机交互界面如图7所示,是连接操作员与磨床控制系统的窗口,比较直观地展现了磨床的功能,方便操作人员查看运行状态、设定磨床参数、控制磨床运行。
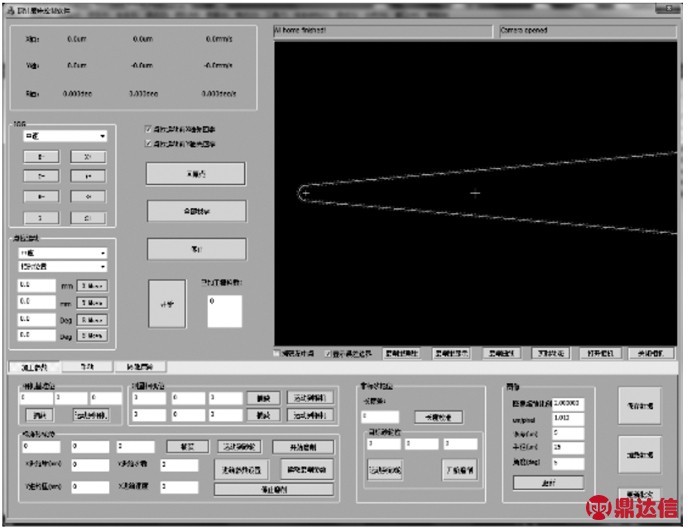
图7 人机交互界面
运动控制模块:磨床的运动控制模块通过调用固高运动控制器提供的动态链接库,实现对磨床各轴的控制
参数设置模块:与工件加工要求和控制相关的参数都可进行配置。可以配置的参数包括相机位置参数、砂轮位置参数、加工进给参数等。
视觉检测模块:识别不同棒料的长度差、识别待加工棒料圆弧圆心、测量磨削余量、检测加工结果。
文件管理模块:包含不同批次的加工参数,更换批次时直接配置相应批次的加工文件即可。
3.3 样机实验
3.3.1 误差补偿
展成法磨削圆弧实质上就是控制棒料绕待加工圆弧圆心转动。为验证实际加工路径与理论轨迹是否一致,进行如下操作:在进行圆弧磨削开始前,将工业CCD相机设在加工工位相近的位置,操作磨床使棒料左端面中心点与相机中心标定点重合,控制棒料围绕相机标定中心旋转,重点观察棒料左端面中心点和相机标定点是否有偏差。其中,图8是试验中棒料实际轨迹所在位置图,从图中可以看出棒料实际位置和理论轨迹偏差较大。因此,为了保证磨床的磨削精度,必须对此偏差进行修正。数据补偿的获得由如下方法进行。
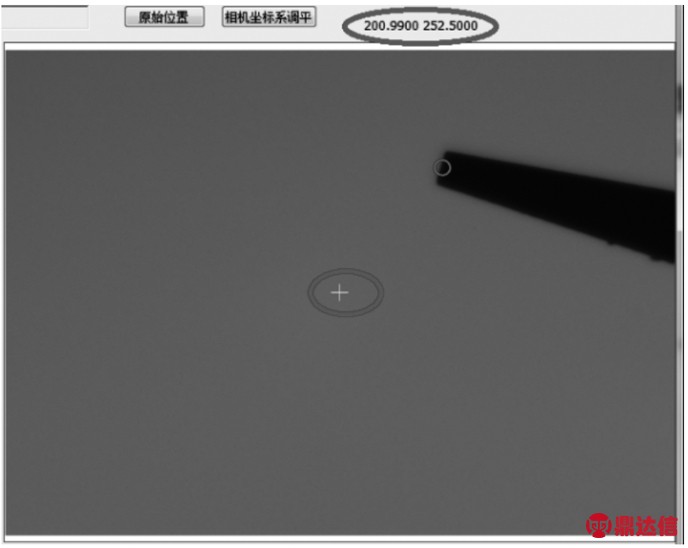
图8 偏离现象
绕相机标定点转动的过程中,将棒料左端面中心点与相机标定点相应角度对应的X轴、Y轴差值记录下来。将记录下来的数据按每0.1°一个数据进行样条插值并生成补偿文件。
加载生成的补偿文件并运行展成圆弧加工程序,棒料左中点与相机中心点基本重合。补偿后,X轴、Y轴偏差如图9所示,偏差均在±5μm内。

图9 补偿前后X轴、Y轴偏差对比图
3.3.2 锥度与圆弧的加工
运行锥度加工程序进行锥度加工,如图10所示为连续100根棒料进行锥度加工的结果,锥度均在5±0.5°范围内,符合锥度加工要求。
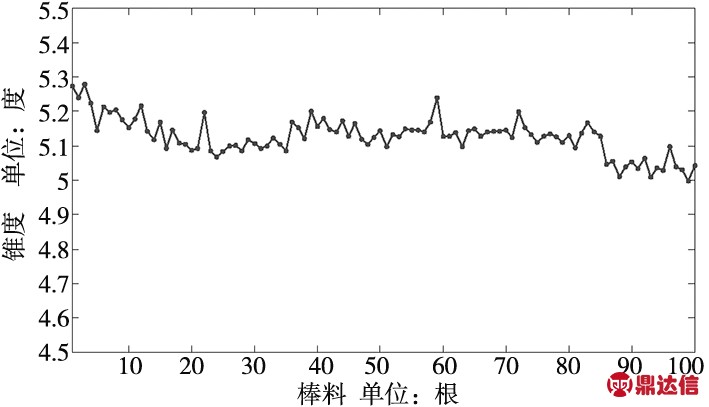
图10 锥度加工结果
加载补偿文件,进行圆弧加工。测量加工完毕的棒料(如图11所示),加工的锥度为4.898°、4.903°,取其平均值为4.9005°,在误差要求的5±0.5°范围内;圆弧左端点偏差为-2.10μm,在加工允许误差在±5μm范围内,符合加工要求。
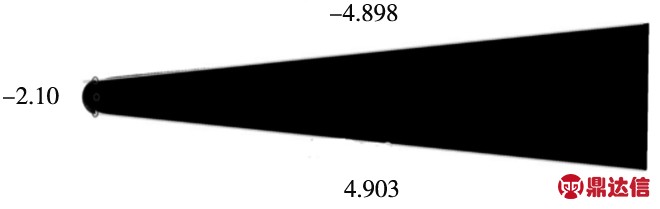
图11 顶针加工检测
4 结论
本半导体硅片顶针磨床采用“PC机+运动控制卡”搭建控制系统,配合视觉检测实现了顶针的锥度加工和圆弧加工:
(1)设计开发了半导体硅片顶针磨床,搭建了"PC+运动控制卡"的控制系统。
(2)实现了一次装夹中对顶针进行锥度、圆弧加工成型并在线检测加工结果。
(3)经实验验证,加工的顶针成品加工质量稳定,一致性好;每根棒料由装夹至加工检测完毕耗时90s,加工效率高。
综上,本文设计的硅片顶针磨床合理可靠,且具有很大的实用价值。