摘要:全自动硅片下料机在生产过程中,容易受到刻蚀工艺机台碎片的影响,出现堵片、流片等问题,从而降低良品率。通过分析工艺机台产生的几种碎片形态,提出了加装碎片检测装置和改造下料机翻转结构的解决方案;该方案能及时检测碎片,并通过优化后的结构处理碎片,提高了设备的稳定性。
关键词:全自动硅片下料机;碎片分析与处理;结构优化
随着光伏行业的快速发展,竞争日趋激烈,降本增效已经成为所有光伏企业必须面对的问题。目前,降低碎片率,减少返工片,提高良品率是降本增效最行之有效的方法。全自动硅片下料机是太阳能电池片刻蚀工序的重要设备之一[1]。多晶硅片由于其本身的物理特性,在经过制绒、清洗、扩散、刻蚀等工序的自动化设备后,不可避免地会产生隐裂片。这些隐裂片在通过刻蚀工艺机台进入下料翻转机构时容易变成碎片,若不及时处理,在传输过程中会造成堵片和流片,影响生产效率,还会导致更多的返工片和不良片的产生。本文分析了全自动硅片下料机正常生产过程中产生碎片的主要原因,并提出了相应的设计方案以及优化解决方法。
1 下料机结构及碎片原因分析
全自动硅片下料机主要是由碎片检测装置、翻转组件、纵向传输段、横向传输段、缓存组件、装片组件、自动换篮组件等组成[2-3]。其结构示意图如图1所示,其中下料翻转组件的主要作用是将硅片翻转180°,避免硅片刻蚀面接触皮带产生脏污和印迹,提高硅片的转换效率。
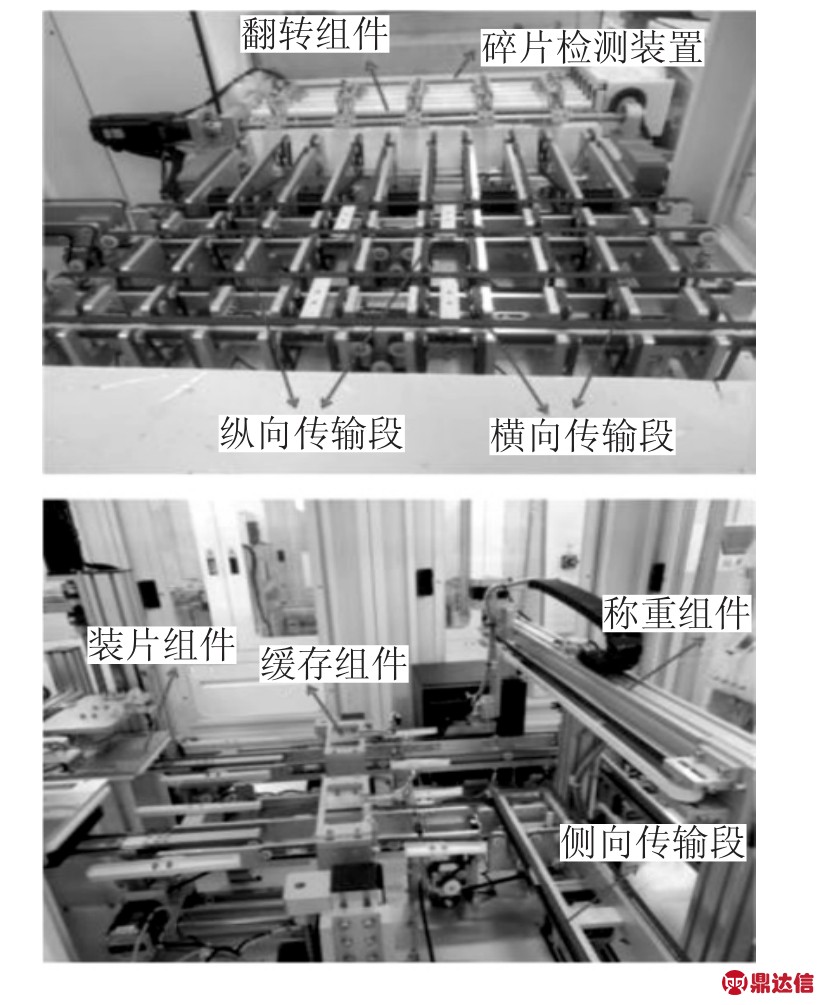
图1 全自动硅片下料机的结构示意图
太阳能电池片在经过多道工序后,会产生部分缺角片。在全自动硅片上料机入口处,操作人员若未及时发现碎片、缺角片将随刻蚀工艺机台直接流入下料机,图2(a)所示是在全自动下料机入口处发现的缺角片。这类缺角片在进入装片组件和缓存组件时,容易堵片,造成二次碎片。
隐裂片在经过中间工艺机台的滚轮时,可能会变为碎片,这部分碎片在传输过程中会粘连在一起,如图2(b)所示。这部分碎片也会引起下料传输段的堵片,另外由于传输皮带上残留液体的存在,还会对后续接触皮带的硅片造成大批量的污染,所以提前对带液片进行检测,让工作人员及时处理,会避免很多损失。
由于受刻蚀槽内的滚轮水平等因素影响,槽体内有时会发生大量堵片,如图2(c)所示。这种情况如不及时处理会造成大量硅片报废,造成重大损失,这就需要下料机有一定的报警功能。如果上料机投料一段时间后,下料机传感器没有感应到硅片,则需提醒操作人员留意刻蚀槽内是否堵片。
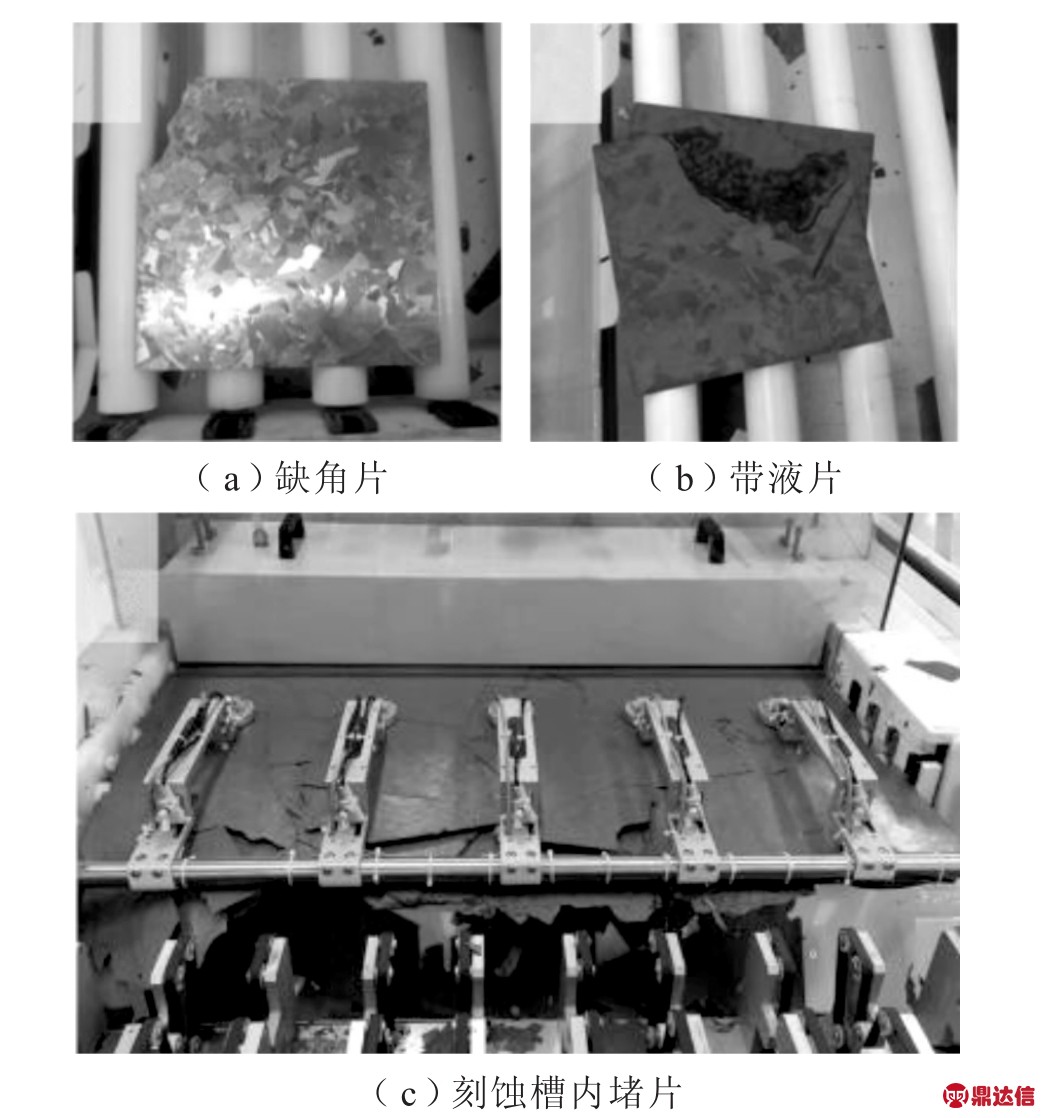
图2 常见的工艺机台碎片形式
除了上述几种常见的工艺机台碎片形式,下料翻转吸盘在取片过程中,受吸盘高度和气压的影响,也会产生碎片。这部分碎片也需要进行相应的处理,以减少堵片的风险。
2 碎片的优化处理
2.1 碎片预处理
针对上述几种常见的刻蚀槽碎片,在刻蚀槽滚轮速度一定的情况,通过比较两个传感器感应的时间来判断硅片是否为碎片。在不显著增加成本的情况下,在设备前预装10个传感器,每道配置2个传感器,每个传感器需安装在硅片的边缘,如图3所示。
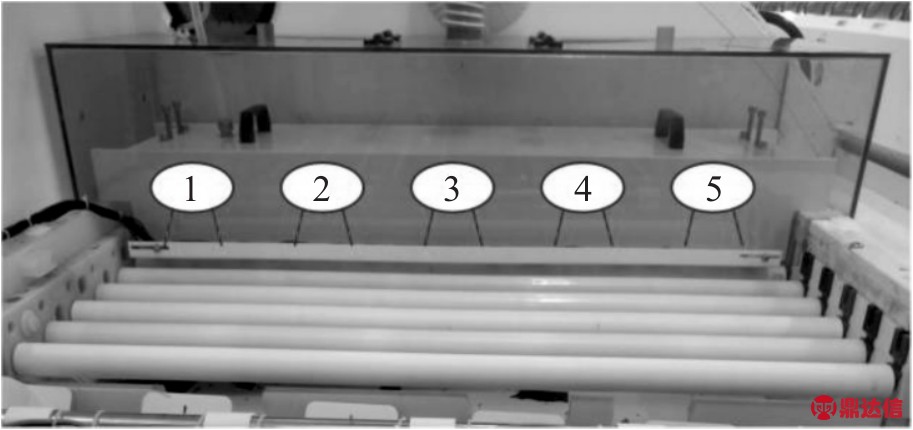
图3 传感器安装位置
碎片检测主要有两种方法,一种是与正常片通过传感器的时间比较,主要针对大部分缺角片,另一种是同道两个传感器相互比较,主要针对纵向半张硅片的情况。
参数设置界面如图4所示,速度检碎设定值是基于正常片通过传感器的时间来设定。速度检碎的检测精度受扫描周期和滚轮速度的影响,本文所论述的PLC扫描周期在5 ms左右,若滚轮速度保持在2.5 m/min,检碎误差在±2 mm。现场可根据实际运行情况,适当的放大实际检测值与设定值之间的差值。界面中会显示硅片通过左右两侧相应传感器的时间,方便操作人员根据硅片的片源大小更改参数。另外,针对纵向半张的硅片,程序中设置差值检碎设定值。若其中一个传感器感应到硅片,在设定值范围内,另一个传感器还未检测到硅片,则该张硅片设定为碎片。
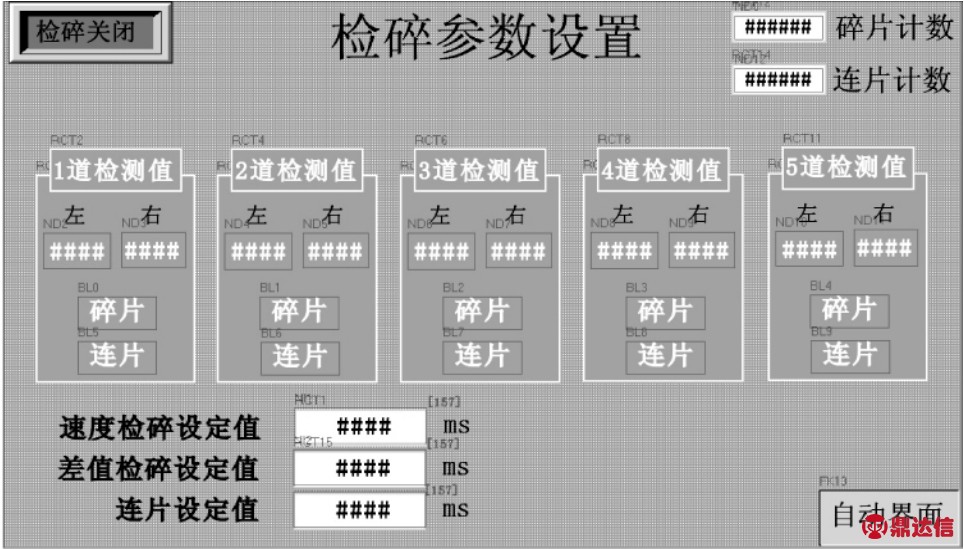
图4 触摸屏检碎参数设置
当使用上述两种方法检测出碎片时,该道吸盘不打开,碎片不会翻转到纵向传输段,而是随滚轮运动自行滑落到收料盒,这样不会对传输段造成影响。
针对上节提到的刻蚀槽堵片情况,参数设置界面增加连片设定值功能,当硅片通过传感器的时间大于设定值,则该硅片为带液片或刻蚀槽产生大量碎片,翻转机构会自动转向放片位,使得硅片掉落到收片盒,并报警提示相关生产人员,解决刻蚀主机台连片问题。另外,本方案还统计碎片数和连片数,设备人员查看相关数据,可以及时发现主机台异常。
2.2 翻转机构优化设计
由于收料盒内硅片摩擦因素的影响,加上刻蚀槽传动速度较慢,经常会出现碎片不能顺利滑落的现象。此外,翻转机构回位时可能会碰到正在倾斜滑落的硅片,容易产生更多碎片,堵塞刻蚀槽出口。针对这些情况,对吸盘连接件进行改造。改造后的设计可避免吸盘连接件接触运动中的硅片,能够在不影响正常生产的情况下让硅片自然滑落,也不会造成二次碎片。
图5所示为改造前及改造后的翻转机构,改造前无收料盒,遇到碎片时会将翻转结构抬升,让硅片全部滑到前置收料盒。这种结构会造成大量返工片,并且每次出现带液片都需要擦拭皮带,严重耽误产能。改造后的设备则完全解决了上述问题。
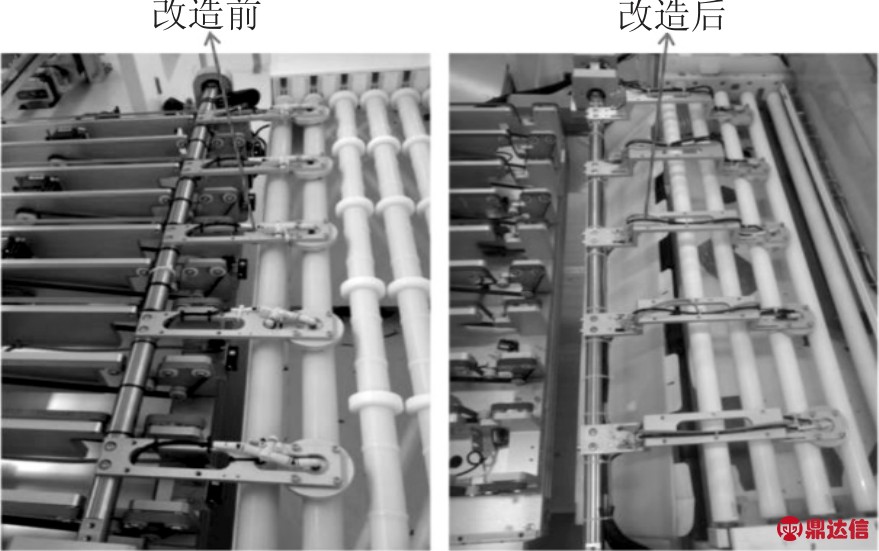
图5 翻转机构改造前后对比图
2.3 传输段优化设计
图6所示为吸盘到达放片位时的状态。若碎片发生在翻转过程中,吸盘到达放片位时,吸盘两端的传感器没有感应到硅片,则判定为碎片,该道纵向传输皮带的速度立即转为快速,将硅片送到前置收料盒,不让碎片进入横向传输段,避免在进入缓存组件前造成堵片。
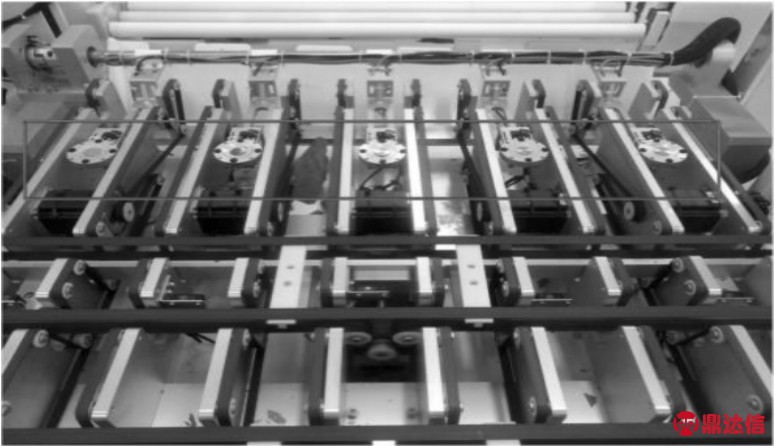
图6 纵向传输段优化
3 优化效果
下料翻转机经过优化设计后,碎片通过翻转机构的状态如图7所示。图中吸盘翻转到取片位时,连接件不会碰到运动中的硅片,而掉落中的碎片也不会影响吸盘吸取下一排的硅片。此外收料盒的角度也可以调节,保证硅片能够顺利掉落。
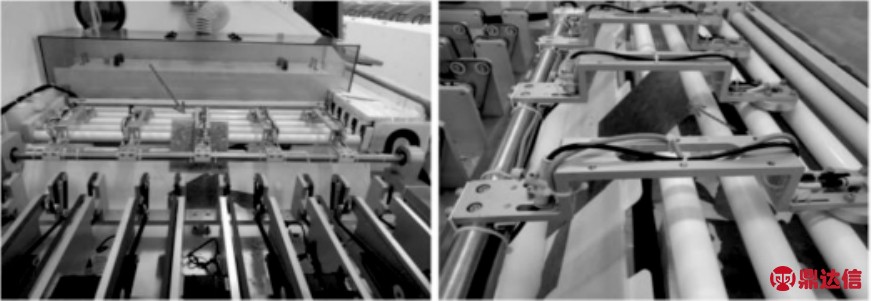
图7 改造后碎片滑落过程
4 结论
通过对全自动刻蚀下料机在生产过程中产生碎片的问题进行分析研究,提出了加装碎片检测装置和改造下料机翻转结构的解决方案。加装碎片检测装置,不仅能够有效地检测碎片,防止碎片进入纵向传输段,对槽内连片和大范围堵片也能起到很好的预警作用。而且改造后的下料翻转结构不会碰到正在掉落的碎片,也不会产生二次碎片,提高了全自动刻蚀下料机的稳定性和可靠性。优化后的下料机装片效率可以达到5000片/h,碎片率控制在0.03%左右,达到了厂家的技术要求,有望在一些老旧机台的改造中得到推广。