摘要: “叉指式微加速度计”的研制,需要使用高浓度硼扩散硅片,而硅片经过高浓度硼扩散后,硅片双面生长了一层硼硅玻璃,采用原有CMP工艺很难将其去除,不能在高浓度硼扩散层上制作更好的 “叉指式微加速度计”结构。针对上述问题,在CMP研磨抛光工艺中,通过改进双面粘片工艺,选择合适的研磨料和抛光料以及研磨盘和抛光盘,系统地考察了压力、转速、抛光垫、浆料、温度等因素对硅晶圆平坦化速率的影响,优化研磨抛光工艺流程及工艺参数,获得表面无划道、无麻坑、无桔皮的高浓度硼扩散硅片,表面粗糙度20A,达到 “叉指式微加速度计”工艺用片指标。
关键词:单晶硅;化学机械抛光;平坦化;抛光液
1 前言
随着半导体工业的飞速发展,集成电路 (IC)的设计线宽进一步的缩小,硅片作为IC芯片的基础材料,其表面粗糙度和表面平整度成为影响集成电路刻蚀线宽的重要因素之一。化学机械抛光 (Chemical Mechanical Polishing),简称CMP,是目前能提供超大规模集成电路 (VLSI)制造过程中全面平面化的超精密技术。用这种方法可以真正使整个硅晶片表面平坦化,而且具有加工方法简单、 加工成本低等优点 [1-2]。
2 CMP平坦化原理研究
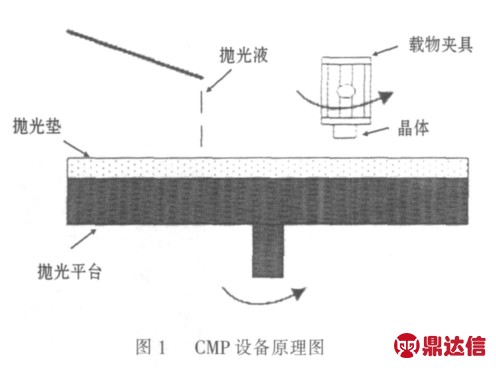
硅片CMP机台整个系统由一个旋转的硅片夹持器、承载抛光垫的工作台和抛光液输送装置三大部分组成。如图1所示。化学机械抛光时,旋转的工件以一定的压力压在旋转的抛光垫上,而由亚微米或纳米粒子和化学溶液组成的抛光液在工件与抛光垫之间流动,并产生化学反应,工件表面生成的化学反应物由磨粒的机械作用去除,即在化学成膜和机械去膜的交替过程中实现表面的 平 坦 化 [3]。
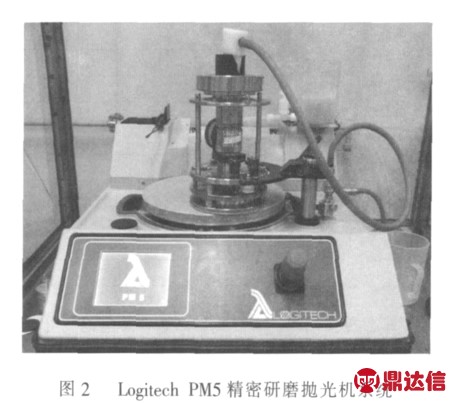
抛光液在抛光垫的传输和旋转离心力的作用下,均匀分布其上,在硅片和抛光垫之间形成一层液体薄膜,液体中的化学成分与硅片产生化学反应,将不溶物质转化为易溶物质,然后通过磨粒的微机械摩擦将这些化学反应物从硅片表面平坦化,溶入流动的液体中带走,即在化学成膜和机械去膜的交替过程中实现超精密表面加工,从而达到平坦化的目的 [4]。设备图如图2所示。
在这一过程中,吸附在抛光盘上的化学抛光液不断地对晶体抛光面产生侵蚀作用,生成胶状膜层。而该膜层又经机械磨削作用被不断割除从而暴露出新的表面,这种周而复始的对晶体表面不断的化学侵蚀和机械割除构成了化学机械平坦化的基本过程,这一过程看起来似乎非常简单,但由于被平坦化的对象不同,对影响其平坦化的参数就会有不同选择。当机械磨削和化学侵蚀同时作用于晶体表面时存在有如下关系 [5]:

其中:Vτ为侵蚀的切向速度;V p为机械抛光的法向速度;V n为化学侵蚀的法向速度;Vτ有效为有效切向的一级近似。
很显然要想获得理想化的加工表面,应使Vτ有效=0,即V p=V N,也就是说要使机械磨削作用与化学腐蚀作用保持相对的平衡。
3 高浓度硼扩散片CMP实验
实验用的硼扩散片直径100mm,厚约0.6mm,抛光机是英国Logitech PM5精密研磨抛光机系统,所有实验均在室温下完成,抛光机的抛光盘由电机驱动匀速旋转。每次只改变一种因素,其它参数不变,分别对压力、转速、抛光垫、浆料、温度等工艺参数的影响进行实验研究,对原有工艺进行技术改进,并提出相应解决方案。
4 技术改进及解决措施
4.1 贴片工艺改进
该设备使用时,先将产品贴在标准玻璃基片上,通过气压将玻璃基片吸附在磨头表面,才能进行加工。贴片要求平整,不允许翘曲和不平,其精度直接影响加工产品的质量。原贴片使用电炉作为热源进行加热,由于电炉升温过快,温度不可调整,不能精确控制贴片温度,容易造成玻璃基片碎裂,粘结剂熔化不均匀,造成贴片不平整。针对这种情况,现采用热板作为热源进行加热,热板升温均匀,可以精确控制温度,经过实验,摸索出贴片最佳温度(165℃~180℃),片内精度达到3μm以内,保证了贴片的平整度。
4.2 浆料配比浓度和浆料改进
在浓度从20%增加到30%时,平坦化速率达到最大值,继续增加浓度,抛光能力反而下降,说明此时一方面氧化物薄层的生成速度赶不上而破坏了化学——机械作用的平衡,化学作用和机械作用不再匹配,抛光粉粒子将直接作用到工件的表面上,形成划痕刻伤,所得到的表面也不光滑。另一方面抛光粉浓度增加,颗粒间碰撞次数也增加,颗粒之间出现团聚的趋势也增大,浆料稳定性下降,因此对抛光浆料来说,抛光粉的浓度保持在一个合适的条件下,才能发挥最大的效应,既保持了高平坦化速率,又不损伤表面。实验结果见表1,实验表明浆料的浓度在30%左右较为合适。
表1 浆料浓度、浆料改进前后对比表
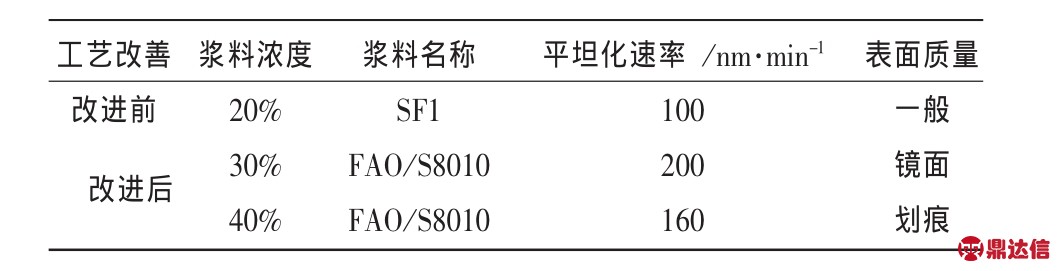
4.3 浆料流量控制改进
在CMP加工过程中发现,由于浆料流量过大,不能控制,大量浆料未经使用就直接被磨盘离心力甩出,浆料不能及时覆盖在晶片表面参与反应,造成晶片表面出现麻点。拆卸分析了浆料桶供料原理,并设计加工出4种规格的截流堵头,将截流堵头安装在浆料桶进料口的孔内,通过减少进料口容积,达到对流量的控制。改进后,浆料可以均匀覆盖在晶片表面,使之充分参与反应,表面状况非常好。一桶浆料使用时间由改进前的25分钟提高到60分钟左右,节约了时间,同时降低了成本。
4.4 抛光垫改进
抛光垫粘附在磨盘的下表面,它是在CMP中决定平坦化能力的一个重要部件。原有抛光垫在抛光一些晶片之后,抛光垫表面会变得平坦和光滑,达到一种称为光滑表面的状态,这种光滑表面的抛光垫不能保持抛光磨料,因此会显著降低平坦化速率,出现平坦化速率低,抛光表面质量不好问题。经过多次摸索、实验,改用聚胺酯抛光垫进行抛光,聚胺脂有像海绵一样的机械特性和多孔吸水特性,抛光垫中的小孔能帮助传输磨料、提高抛光均匀性和平坦化速率,从而可以获得较好的表面质量。抛光垫改进前后对比见表2。
表2 抛光垫改进前后对比表
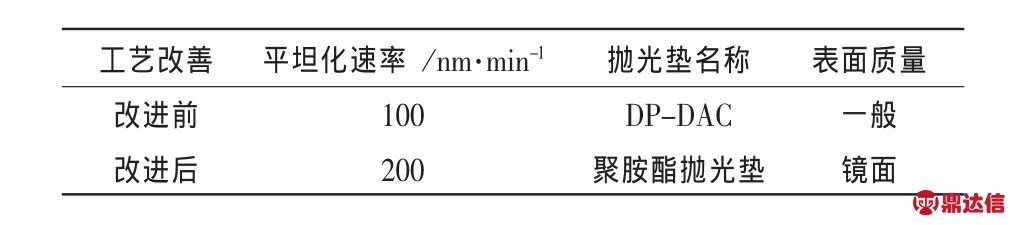
4.5 磨盘压力
硅晶片CMP平坦化速率与抛光压力之间的关系曲线如图3所示。从图中的数据可分析出,当抛光压力为零时,液流层较厚,CMP机械作用较弱,化学作用较强,平坦化速率较低;随着压力增加,抛光液在抛光片和抛光布之间起到了良好的润滑作用,既能有效地与硅表面反应,又能及时地将反应物从抛光片表面脱离,达到较高的平坦化速率。随着磨盘压力的增大,单晶硅晶圆的平坦化速率也随之增大,缩短了抛光时间,增加了产能,但使用过高的压力会导致不均匀的平坦化速率。根据实验情况,压力控制在10Pa为佳。
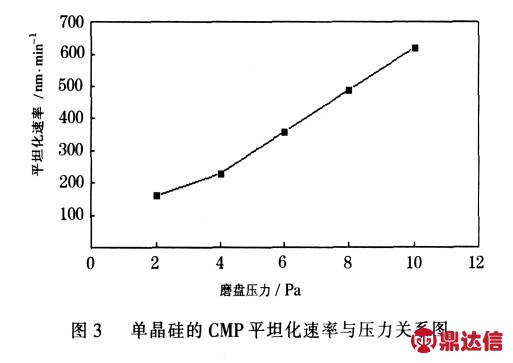
4.6 温度
CMP在加工过程中无论是酸性液体还是碱性液体,在对去除材料的化学反应中都是放热的反应,造成温度的上升,同时在加工过程中,由于抛光头的压力作用,以及抛光头及抛光盘的旋转具有做功的情况,所以有能量的释放,造成温度的上升,由于温度的上升,使化学反应速度急剧增加,这样使机械作用和化学作用不能达到合理的平衡点,造成不均匀的平坦化。对温度进行控制,从而对化学反应速度实现控制是必要的方法 [6],才能满足高浓度硼扩散硅片平坦化要求,得到完美表面。经过大量CMP实验,最终确定温度在25℃~30℃。
4.7 PH 值
实验结果表明,当pH=7时,抛光效率较低;当pH=9时,抛光效率显著升高。这是因为在碱性抛光液的化学作用下,硅晶圆表面将更容易形成一层软化层,继而在抛光垫的机械作用下更容易被去除。故当pH<9时,制约抛光效率的主要环节是化学作用;而当pH>9时,化学作用已经达到饱和,制约抛光效率的主要环节则是机械作用。经实验测定当pH=10.5时抛光效果最好。
5 结论
(1)摸索出了一套较好的CMP工艺技术路径。这条技术路径涵盖了微小颗粒的匹配、磨料的处理、不同抛光剂的优选、抛光盘的合理应用、温度、抛光压力、抛光盘转速的控制等工艺参数。
(2)获得表面无划道、无麻坑、无桔皮的高浓度硼扩散硅片,全局平面度1μm,表面粗糙度20,达到 “叉指式微加速度计”工艺用片指标。