摘要:设计并制作了总厚度为0.85 mm的超薄平板热管,热管的毛细芯采用烧结多孔槽道结构,实现了槽道和多孔结构的结合,根据该结构制作了一个铝制模具。该热管设计结合了超薄化和易制作的特点,对热管性能测试搭建了实验平台,分析了加热功率、铜粉粒径、槽道数目对热管热性能的影响,热阻和最大传热能力用来表征热管的性能。结果表明在加热功率为14 W时,放置铜板和热管的加热铜块温度分别是102℃和66℃,热管有效降低了热源温度;当铜粉粒径较大时热管的热阻和传热极限也较大,粒径减少时出现相反现象。相比单槽道结构,双槽道结构出现了更低热阻,两者最小差异为21%。
关键词:超薄平板热管;烧结;多孔槽道结构;传热;铜粉粒径;热性能;实验验证
引 言
进入21世纪来,电子技术和信息产业快速发展,电子器件的微型化、集成化已经成为当今电子技术发展的趋势,电子芯片的高集成、高封装密度以及高工作频率使得芯片的温度快速升高。研究表明,电子元件的损坏率与工作温度呈正相关,当电子器件长时间处于高温工作状态,其可靠性会出现明显下降[1-3]。如何对电子设备进行高效散热是电子产业发展的一个瓶颈[4-5]。
热管作为一种高效的相变传热工具,由于其具有高导热性、优异的均温性能、运行可靠性等特点,被广泛应用在能源、航空、电子元件等领域的散热,是现阶段解决狭窄空间散热的一个理想方案[6]。在热管的发展上出现了各种不同形式的热管如平板热管、圆柱热管、脉动热管、环路热管等。受到尺寸的限制,电子器件中所应用的热管必须既轻薄又具有较好的热性能以及与电子设备易结合,这促使了超薄平板热管的发展,一般将厚度小于2 mm定义为超薄。
平板热管一般分为蒸发段、绝热段、冷凝段和毛细芯结构,在热管运行中,毛细芯起到了重大作用,常见的吸液芯有单一型和复合型,单一型包括沟槽式[7-8]、丝网式[9-10]、烧结式[11-13],复合型是单一型的组合,即沟槽-丝网、沟槽-铜粉等[14-17]。
在平板热管的制作中主要的成型工艺分为上下平板焊接和圆柱热管压扁,有许多学者对此进行了相关的研究。对于上下板焊接形式,Zhou等[18]提出了一种采用10层500目(0.028 mm)铜网作为毛细芯的热管,该毛细芯被切割成槽道结构用于气液分离,热管的厚度为1.2 mm,该热管在自然对流冷却情况下其传热极限为12 W。刘昌泉等[19]制作了厚度为1.3 mm的采用多尺度吸液芯的超薄平板热管,该吸液芯由多孔介质底层和多孔介质丝构成,并进行了化学改性处理,未经过化学处理和处理过的热管样品的最高功率分别是83.7 W和44.3 W。Lv等[10]使用经过亲水处理的铜网作为热管的毛细芯,其样品的厚度为0.95 mm,传热极限为20 W时的热阻是0.05℃·cm2·W-1。Lee等[20]制作了厚度为1 mm的平板热管,其管材为纯铜,在内部首先烧结了一层亲水处理的铜网,并在其上方放置了三层宽度为10 mm的粗铜网,其有效热导率超过1000 W·m-1·K-1,但是其传热极限极小。Yang等[21]在热管底部采用槽道作为液体通道,盖板采用针肋和针肋阵列形式作为气体通道,整体厚度1.525 mm,实验结果表明,针肋热管的热阻是固态硅的52%~60%,针肋阵列热管的热阻是17%~20%。Mizuta等[22]在盖板和底板采用突起结构来强化沸腾,中间采用四层多孔结构间隔的形式来组成气体和液体通道,整体厚度为2 mm,实验结果表明最大热通量超2 MW·m-2,最小热阻值为0.08 K·W-1。
对于压扁形热管也有较多的研究。Aoki等[23]采用压扁成形的方法研制出厚度为0.7 mm和1 mm的铜丝超薄热管,并对其性能进行了试验研究。Yang等[24]提出了一种采用低花费高性能的超亲水编制带毛细芯热管,该热管厚度仅为1 mm,毛细芯位于热管中间位置,两端是气体通道,实验结果表明该热管的传热极限能达到20 W。Li等[25]制造了三种不同复合毛细芯-单弓形铜粉沟槽吸液芯、双弓形铜粉沟槽吸液芯和丝网沟槽吸液芯,实验结果三种结构的热管其传热极限分别是12、13、14 W。Lee等[26]对压扁工艺成形的烧结吸液芯超薄热管制作方法进行了研究。Zhou等[27]使用泡沫铜和丝网组成复合毛细芯,采用压扁工艺制作了厚度为0.8 mm的热管,在最佳充液率的情况下,其蒸发热阻是0.29 K·W-1,其传热极限为5 W。为了进一步减少厚度,有研究者利用蚀刻技术进行微结构构造。Ding等[28]采用蚀刻技术在钛合金基板上加工出直径为5 μm,高度为50 μm,中心间距为10 μm的圆柱体阵列吸液芯结构,其成品厚度仅为0.6 mm,最大热导率为350 W·m-1·K-1。Lewis等[29]采用光刻技术在高分子聚合物薄膜表面加工出不同尺寸及间距的微型凸台,形成相互交错、相通的微槽道吸液芯结构,研制出厚度只有0.3 mm的可变形超薄热管(FTGP)传热极限为9.54 W时,超薄热管的热阻值最低为11.92℃·W-1,有效热导率为 541 W·m-1·K-1。Ivanova等[30]研制出一种用硅片代替金属外壳的超薄、超轻平板热管,采用蚀刻技术在厚度为0.5 mm的硅片表面加工出正六面体结构,通过实验研究发现,当冷凝段温度恒定在50℃时,超薄热管的极限传热可达70 W,热阻为0.9℃·W-1。Oshman等[31]制作了一种使用高分子聚合物作为管材,厚度为1.31 mm的柔性热管,在弯曲角为0°时,加热功率为15 W时得到了最小热阻1.2 K·W-1。
从上述文献可以看出,学者对超薄热管已经开始了研究,对于压扁形热管其应用由于压扁宽度受到了限制,微结构蚀刻技术存在制作成本高、工艺复杂耗时等问题,不适合批量生产。而焊接式平板热管可根据实际应用条件灵活设计和制作,但是其相对厚度较大,厚度小的结构仅适用于实验研究。基于上述,本文提出了一种采用焊接式制作工艺毛细芯采用烧结多孔槽道的超薄平板热管,通过设计的铝模具实现简单高速的铜粉填充,制作了厚度仅为0.85 mm的超薄平板热管,本研究详细介绍了制作过程,并对加热功率、铜粉粒径、槽道数目对热管的影响进行了研究。
1 热管的制作
图1是超薄平板热管的结构图,整个热管分为三个部分:盖板、底板和烧结铜粉毛细芯。热管的整体尺寸L×W×H=149 mm×20 mm×0.85 mm。热管外壁所用材质为C1100紫铜。图1中1为紫铜盖板,其厚度为0.15 mm,采用切割技术制作而成;2为紫铜底板,其中间部分为凹腔结构,底板采用的是化学蚀刻的方法,通过药剂控制腐蚀腔体的深度,其整体厚度为0.65 mm,其中腔体深度为0.55 mm;3为烧结槽道铜粉毛细芯;4是除气口,用来安装除气管以进行工质充填;5的作用是为了进行储液以及提供工质在横向的流动,提高热管烧干极限。该结构中槽道铜粉结构既作为液体回流通道也能作为热管的支撑结构,防止在制作的时候出现塌陷。另外,该结构的的蒸气通道和液体回流通道是独立的,能够实现气-液分离,降低气-液交界面的剪切力,减少流动阻力,提高热管的传热性能。
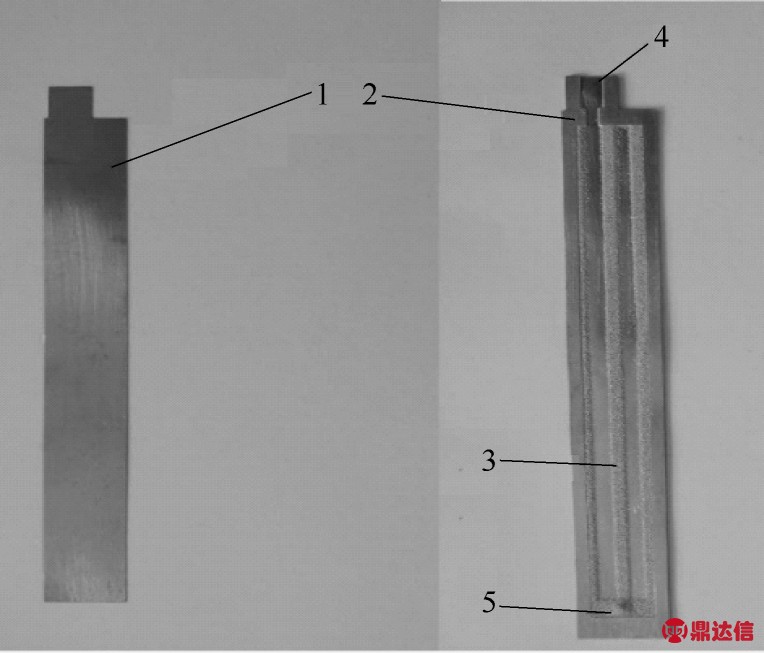
图1 平板热管结构
Fig.1 Flat heat pipe structure 1—top plate;2—bottom plate;3—sintered copper powder;4—extraction opening;5—sintered copper powder
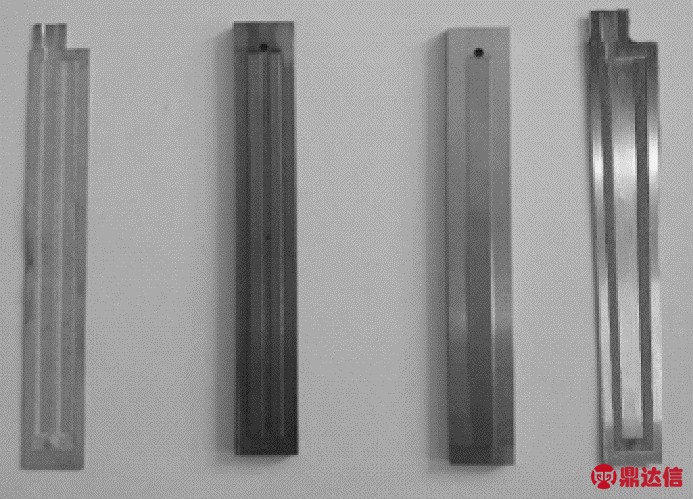
图2 模具和样品
Fig.2 Molds and samples
在本次实验中,超薄平板热管的具体制作流程如下。由于底板和盖板表面会存在油渍、切屑等杂质,且铜在空气中易被氧化,因此对底板和盖板要进行清洗,首先用抛光剂进行浸泡,浸泡时间铜板的表面情况而定,一般为5 min。随后对表面进行擦洗,擦洗之后的铜板连续过3次纯净水。将抛光之后的铜板放置到抗氧化剂溶液中进行处理,浸泡10 min,随后将铜板连续过3次纯净水,将两种试剂处理后的铜板放置到烤箱中烘干,烘干温度110℃,时间为5 min。接着使用填粉模具进行铜粉充填,该模具材料为铝,采用机械加工方式制作而成。图2为两种不同结构的模具以及底板在使用模具之后的实物图。本结构采用设计好的模具和填粉设备进行填粉,首先将图1的底板放置在填粉设备上。如图2所示,模具中间部分为突起结构,其厚度与底板腔体厚度相同,而且模具宽度与底板宽度一致。将模具与底板相对而扣,使突起部分位于底板凹腔位置,并通过调整模具与底板使之左右两端对齐,随后启动填粉设备,将底板和模具压紧,用气体将铜粉通过模具表面小孔打入底板,气体由高压氮气瓶提供,压力设置为0.3×106Pa。进入腔体的气体从底板和腔体的间隙中排出。根据多次的填粉结果和时间的关系,最后选择20 s作为充填时间。填充完毕后将模具取走,即可得到图2的样品。将填粉之后的底板进行高温烧结,烧结炉中有氮气和氢气作为保护气,烧结温度设置为900℃,烧结时间设置为4 h。接下来将底板涂抹一圈焊膏,将盖板放置在底板上并压紧,封装后的热管进行二次烧结,烧结温度设置为700℃,烧结总时间为4 h。焊接完成后待热管温度降低将紫铜除气管装入除气口,并且用高周波焊接机进行焊接。焊接之后的热管进行工质充填,由于热管厚度的问题,在填充上采用先抽真空再灌注技术,即负压充填,考虑到热管的厚度负压设定为10.6 Pa。充液时的环境温度为25℃,负压充填后,认为热管工质内部饱和压力与同等环境温度下的饱和压力相同,因此运行压力大概为3000 Pa,冲液完成以后,铜管会被自动夹扁。最后对热管进行尾端焊接,防止漏气。根据文献[25],本文热管充液率φ选择80%。
2 实验步骤
2.1 实验系统
图3是实验测试系统。由实验部分、加热部分、冷却部分、供电系统、数据记录部分以及绝热夹具组成。实验部分分为蒸发段、绝热段和冷凝段,其长度分别是Le=25 mm、La=55 mm、Lc=40 mm。加热部分使用铜块作为模拟热源,铜块表面打磨光滑以减少接触热阻。铜块中间插入一根电阻加热棒,使用交流电给其供电,加热功率最大为50 W。加热铜块放置到平板热管底部,其有效接触面积为25 mm×20 mm,为了减少接触热阻,在热管与铜块之间涂上一层很薄的高热导率导热膏(热导率为10 W·m-1·℃-1)。冷却部分使用水冷铜块,铜块中间为腔体,两端分别是进出水。冷却水由恒温水箱提供,在整个实验过程中冷却水流量恒定为1 L·min-1,水温恒定为30℃。为了保证热管和加热铜块、冷却铜块接触良好,使用夹具将其压紧并锁死,确保实验数据的准确性。另外为了减少热损失,夹具与铜块和热管之间均采用绝热材料包裹。
使用YOKOGAWA MV2000来监视和记录贴附在热管表面的热电偶的温度并传输到计算机,T型热电偶的记录精度是±0.2℃。图4是热电偶的位置分布,共使用5个热电偶贴附在热管的上表面,其中蒸发段2个(102、103),绝热段1个(104),冷凝段2个(105、106),用高温胶布将其固定并压紧确保其有效接触。另外还有1个热电偶(101)固定在加热铜块表面用来监控加热铜块温度。根据实际需求,当热源温度即101温度达到80℃或者温度出现突增后就停止实验,当温度在3 min之内波动小于0.5℃,认为热管达到了稳定状态,记录数据并处理。所有的热电偶在使用之前都进行了校准,保证实验数据的准确性。
2.2 数据处理和不确定性分析
热阻和热源温度以及最大传热能力一般被用来评估热管的性能,在本文中,热管的总热阻R为

式中,Q为加热功率,Te为蒸发段平均温度(102,103),Tc为冷凝段平均温度(105,106)。热管的最大传热能力应为出现烧干现象前的传热极限。从热阻图中可知,在热阻曲线发生陡增前,即热阻为最小值时,应为热管的传热极限。
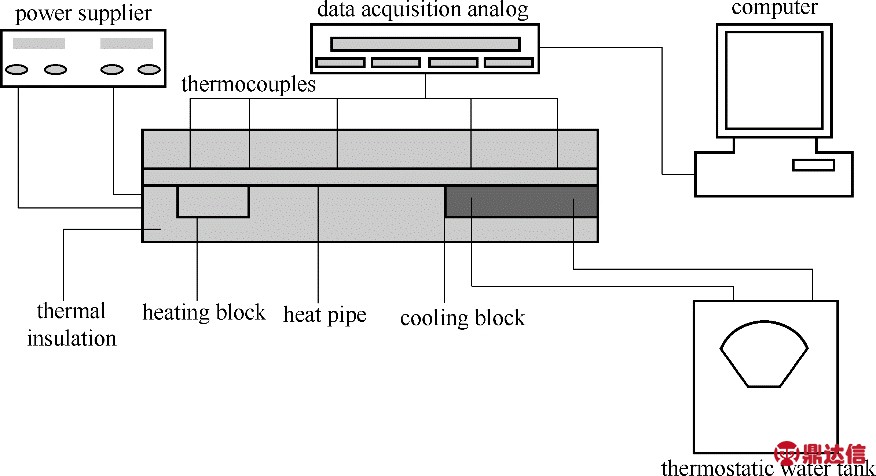
图3 实验装置原理图
Fig.3 Schematic of experimental testing system
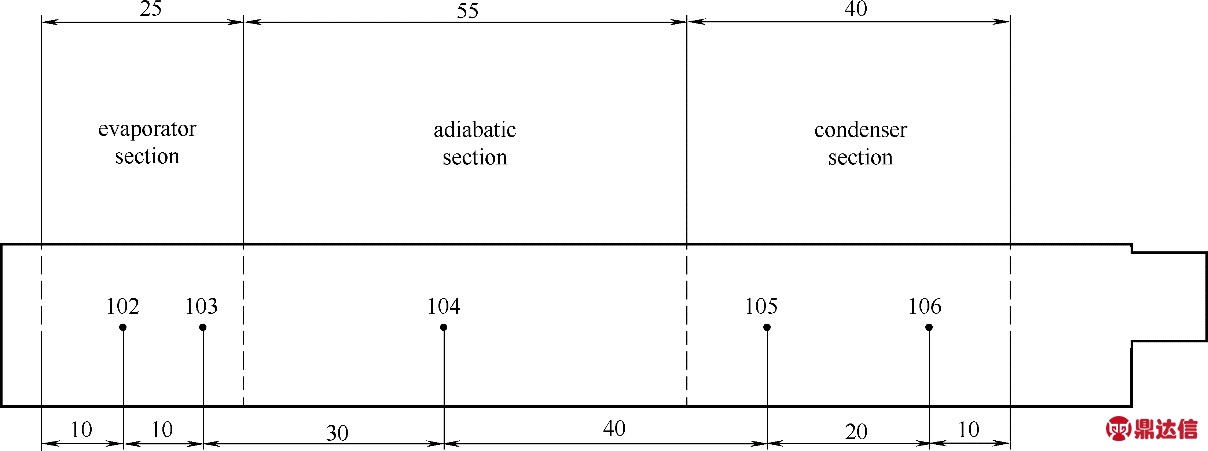
图4 热电偶分布
Fig.4 Distribution of thermocouples
对于实验中的传热系数误差分析,采用了Kline等[32]的不确定性分析方法,考虑到仪器误差,电箱提供的加热功率不确定度为1%;测量误差引起的不确定度为1.2%;热电偶测温误差引起的不确定度为0.74%。在这种情况下,热阻的不确定度为1.7%。另外为了减少实验误差,本实验数据取3次重复实验的平均值。
3 结果与讨论
3.1 平板热管与铜板对比
图5和图6是热管和铜板在不同加热功率下的温度分布,铜板在厚度与长宽尺寸上与热管一致。从图中可以清楚地看到在整个加热测试中,热管的温度都要低于铜板,两者的温差随着加热功率的增大也在进一步增加。在电子元件冷却中,电子设备本身的温度即本文中的加热铜块温度是衡量冷却性能的一个重要指标。对于热电偶101,放置热管和铜板在14 W时的最高温度分别是66℃和102℃,两者相差36℃,表明该超薄热管能有效降低热源的温度。另外在整个测试中铜板蒸发段与冷凝段的温差都比热管大很多,这个值随着加热功率的增加而增大。在加热功率为14 W时,热管蒸发段和冷凝段的温差为5.1℃,而铜板的温差为52.9℃,两者相差10倍。相比铜板,超薄平板热管表现出了极好的性能。
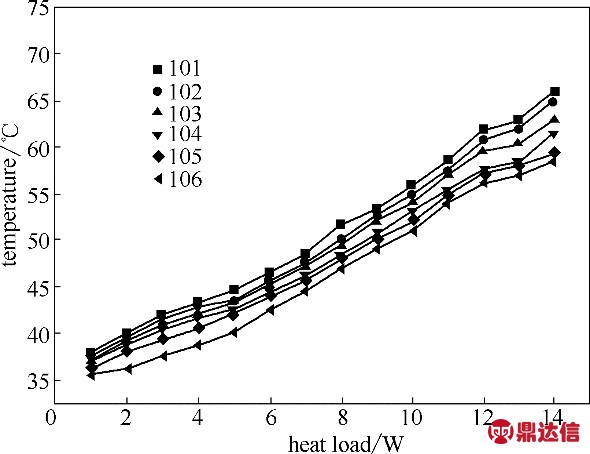
图5 热管在不同功率下的温度分布
Fig.5 Heat pipe temperature distributions under different heat load
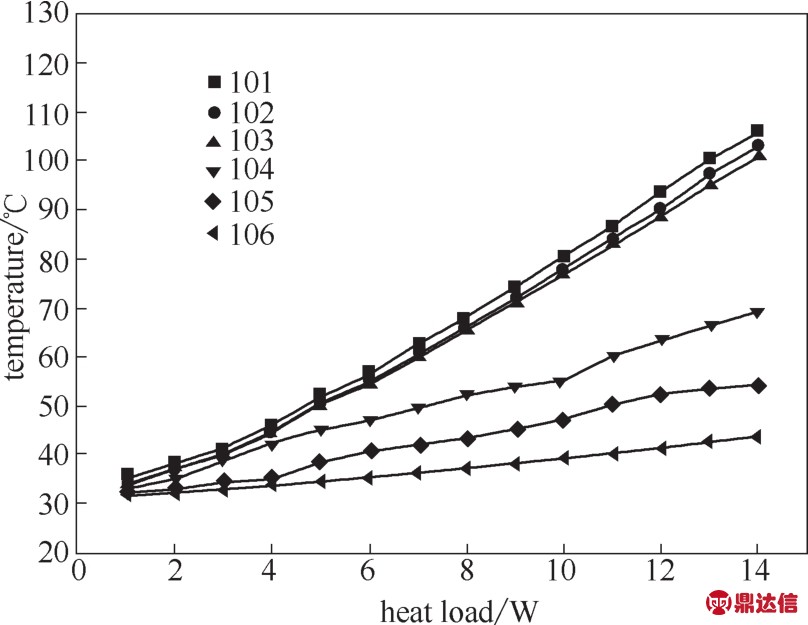
图6 铜板在不同功率下的温度分布
Fig.6 Copper plate temperature distributions under different heat load
图7为热管在加热功率从1 W变到14 W时的动态温度分布。从图中可以明显看出随着加热功率的增大,蒸发段的温度逐渐增大。当输入功率发生改变时,蒸发段的温度迅速发生变化然后在重新达到稳定状态,意味着本文热管的响应速度较快。主要原因是因为热管内部气液结构的分离减少了工质流动阻力。另外从图中可以看出蒸发段温度在加热功率为1 W时达到平衡所需时间较长,可能是热管初期工质蒸发过程不强烈,主要是铜板的导热,因此温度持续上升。随着热源温度的继续升高,热管开始进入启动状态,蒸发段的温度开始不再持续上升,最终蒸发段温度达到稳定状态,也意味着热管内部达到平衡状态。
图8是热管和铜板在不同加热功率下的热阻。热管在加热初期时其热阻较大,随着功率的增加,热阻开始出现下降,随着加热功率的继续增加热阻的下降幅度变小。相比热管,铜板的热阻随着加热功率的增加而增大。在加热功率为14 W时,热管和铜板的热阻分别是0.24℃·W-1和3.78℃·W-1。
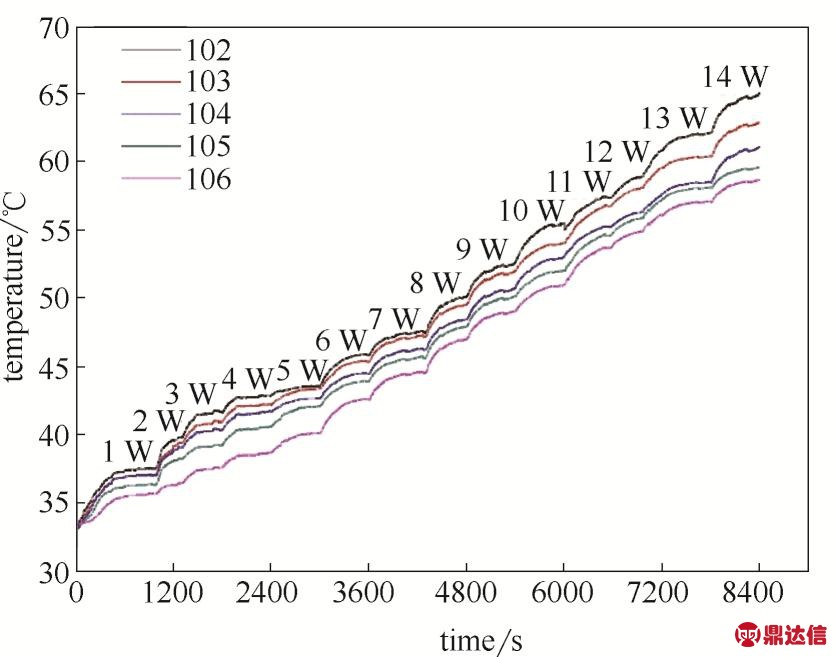
图7 热管加热功率从1 W至14 W时的动态温度特性
Fig.7 Dynamic temperature characteristics of heat pipe under incremental total heat inputs ranging from 1 W to 14 W
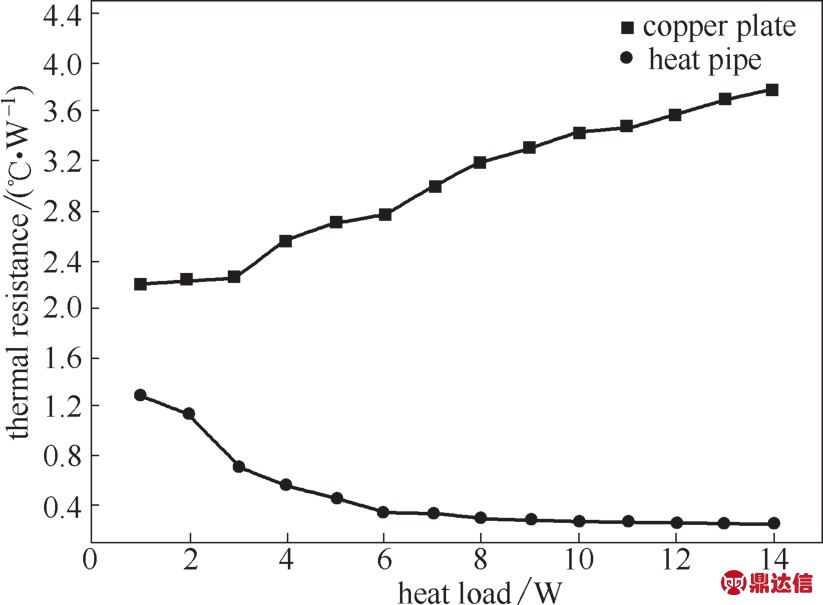
图8 热管和铜板在不同功率下的热阻
Fig.8 Thermal resistance of heap pipe and copper plate under different heat load
在相对较小的加热功率时,其蒸发过程不明显,蒸发段的液膜厚度较大,导致蒸发段部分的热阻较大。随着加的增热功率加,液膜厚度变薄,蒸发段和冷凝段之间的气-液界面的弯月面半径的差异增大,蒸汽速度会加快,加强了热管的传热性能,因此导致热阻会出现减少,当功率继续增大在毛细力不能平衡工质蒸发和冷凝回流时,会导致蒸发段液膜非常薄,进而发生烧干现象,导致整体热阻出现增加。
3.2 不同铜粉粒径的影响
对于烧结铜粉毛细芯,孔隙率会影响热管的性能。本文热管的铜粉采用三种不同粒径,其烧结后的孔隙率会有不同。孔隙率计算采用如下公式[33]
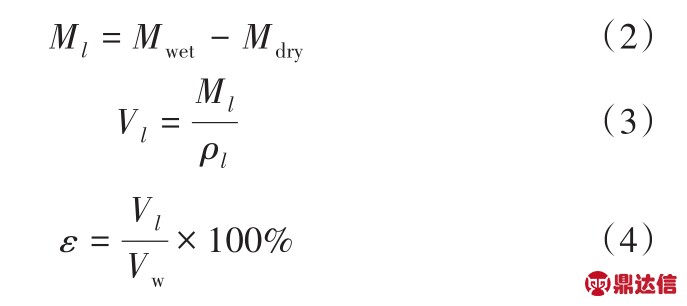
式中,Ml是工质质量,Mwet是被湿润的样品质量,Mdry是干燥样品质量,Vl是毛细芯吸收的水,ρl是水的密度,ε是孔隙率,Vw是烧结后的样品体积。
不同毛细芯的孔隙率ε如表1所示。
表1 毛细芯孔隙率
Table 1 Porosity of wick structure
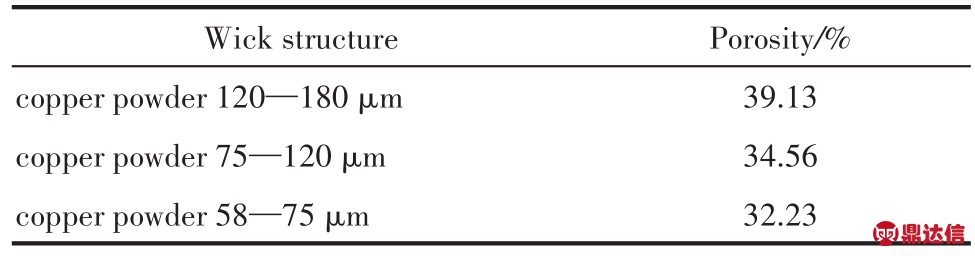
图9和图10是两种不同结构热管在不同粒径下的热阻与功率的关系。从图中可以看出无论是单槽道还是双槽道,铜粉粒径对热阻的影响都类似。在同一功率下随着铜粉粒径减小,热阻降低。还应该注意的是,随着铜粉粒径减小,Qmax降低。
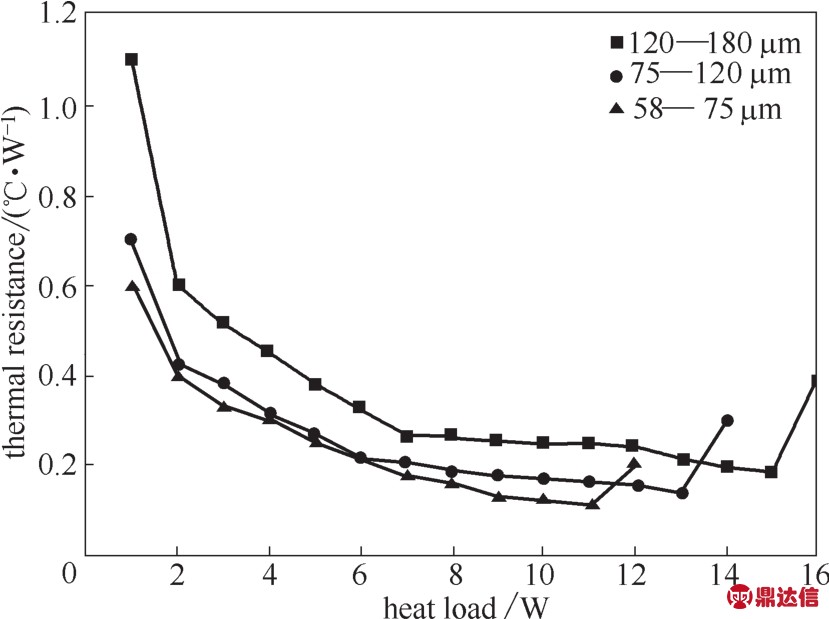
图9 铜粉粒径对性能的影响(双槽道)
Fig.9 Copper particle size effect on performance(double channel)
从图9可以看到当铜粉粒径为120~180 μm时,其最低热阻为0.18℃·W-1,相应的Qmax为15 W,当铜粉粒径为75~120 μm时,其最低热阻为0.13℃·W-1,此时Qmax为13 W,当铜粉粒径为58~75 μm时,最低热阻为0.11℃·W-1,其Qmax为11 W。从图10也可以得到类似的结论。原因如下:在烧结铜粉热管中,不仅需要毛细力来促进液体回流也需要足够的液体工质来满足散热需要,根据文献[34],孔隙率会影响毛细芯性能,在低孔隙率时毛细芯会有较大毛细力但是相对的其工质较少,在毛细芯毛细力较大时,液体工质回流会更快,使得热阻会较低,但是由于工质量少,使得热管容易出现烧干,降低了热管的传热极限。在表1中,铜粉粒径与孔隙率呈现正相关,小粒径其孔隙率也较小。另外在本文中,热管充液率是一样的,因此孔隙率的不同会导致充液量的差异,排除了相同充液量对实验的影响。综上,120~180 μm粒径的热管表现出更高的Qmax以及更大的热阻,而58~75 μm粒径的热管表现出较小的Qmax和热阻,而75~120 μm其Qmax和热阻均处于中间。
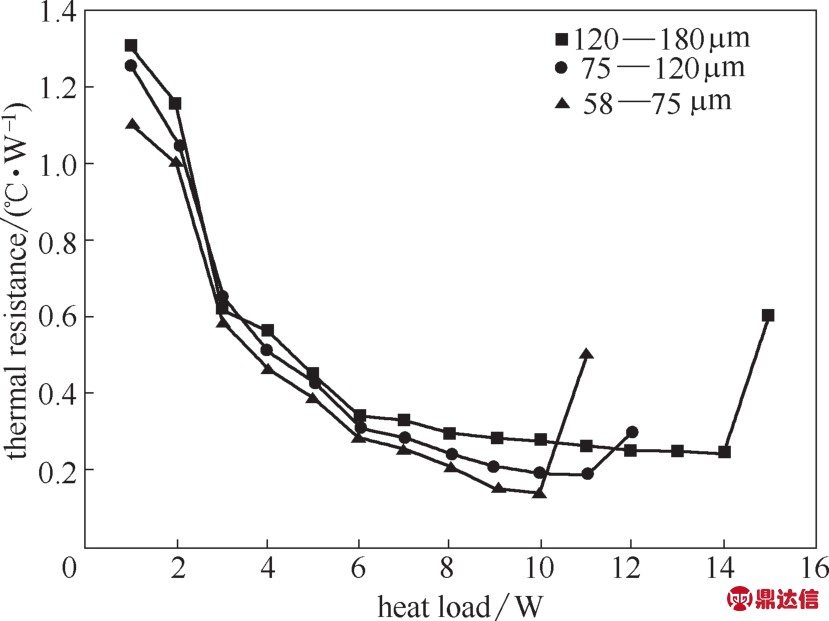
图10 铜粉粒径对性能的影响(单槽道)
Fig.10 Copper particle size effect on performance(single channel)
3.3 槽道数对热管性能的影响
为了研究不同烧结多孔槽道结构中槽道数对热管性能的影响,制作并测试了单槽道热管和双槽道热管。如图2所示,两种结构的区别在于槽道数目,两者的铜粉体积和腔体体积都是1∶1,在本文中,腔体的总宽度为14 mm,对于单槽道结构其槽道宽度是7 mm,两边的铜粉宽度分别是3.5 mm。对于双槽道结构其槽道宽度分别是3 mm和4 mm,由于热管充液口需要用填充模具封堵防止漏粉,因此在设计上采用不等距,铜粉的宽度分别是2 mm、3 mm和2 mm。
热管在不同槽道数的热阻如图11所示。在三种不同铜粉粒径的情况下,单槽道的热阻都比双通道要大,在粒径为120~180 μm时,两者的最低热阻分别 0.24℃·W-1和0.18℃·W-1,在粒径为75~120 μm时,两者的最低热阻分别是0.18℃·W-1和0.13℃·W-1,在粒径为58~75 μm时,两者的最低热阻分别是0.14℃·W-1和0.11℃·W-1。另外从图中可以看出,在低功率时两种结构的热阻差异较大,随着功率的增加,差异逐渐减少,在热管发生烧干前,三种粒径热阻的差异分别是25%、27%、21%。
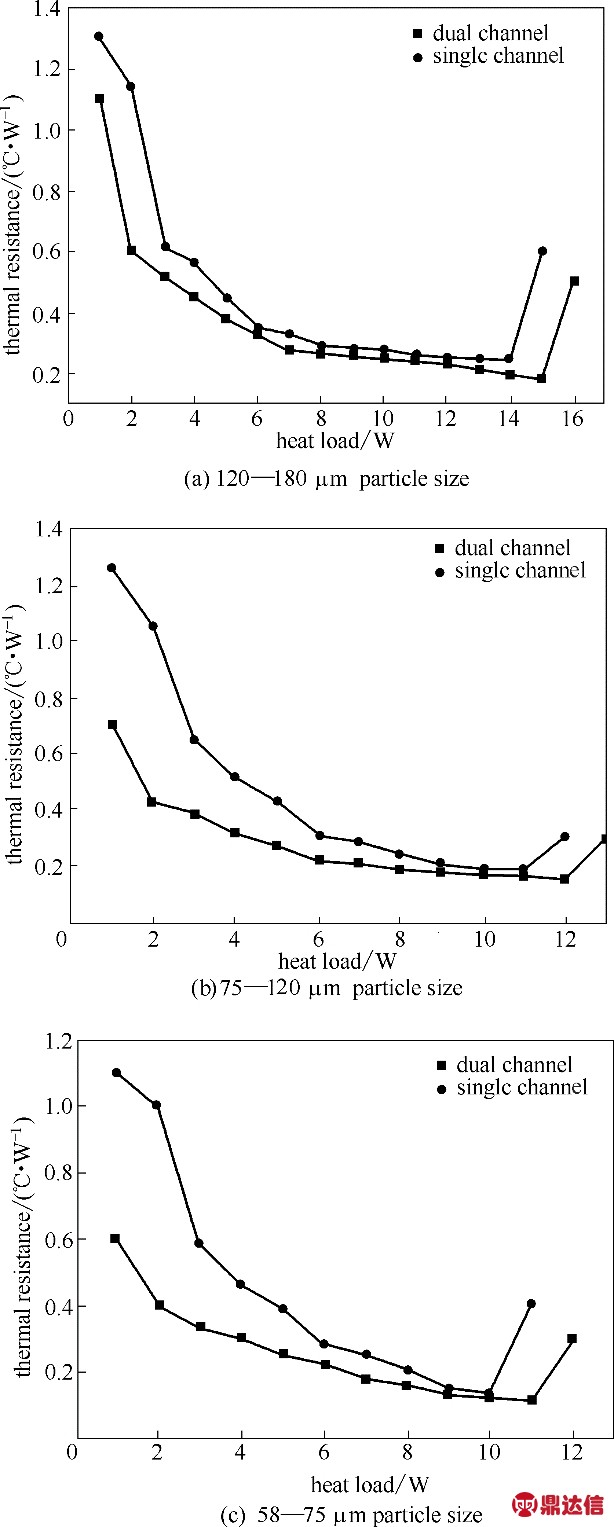
图11 槽道数对热阻的影响
Fig.11 Effect of number of channels on thermal resistance
图12是两种槽道结构的示意图,黄色部分为毛细芯,白色部分为气体通道,白色圆圈为液滴,红色线是工质流动方向。对比图12(a)、(b)可以看出,相比单槽道结构的毛细芯,双槽道结构的毛细芯间隔近。该热管的气体腔体没有烧结铜粉,采用的是纯铜底面,工质在径向回流能力相对较弱,当气态工质在冷凝段变为液滴时,单槽道结构在热管中心位置的液体相比双槽道结构难回到两端的毛细芯,而双槽道结构虽然也存在有一定间隔,但是其间隔相比单槽道结构小很多,槽道中间的液态工质回流到毛细芯更加简单,因此在三种粒径的情况下,双槽道结构的热阻都比单槽道要小。另外,从图11可以看到,在加热功率较小时,双槽道结构和单槽道结构的热阻差异大,随着加热功率的增大,两者差异逐渐减少。原因可能是:当加热功率较小时,由于蒸发过程不强烈,导致冷凝段的工质少,冷凝的工质假设为相同粒径的液滴,在双槽道结构中,液滴回到毛细芯的距离比单槽道要小,因此造成热阻较小。当功率加大之后,冷凝的液滴数量会增多,导致液滴容易形成连续,通过毛细芯的作用,处在中心位置的工质也容易被吸回到蒸发段,导致两种结构的差异减少。
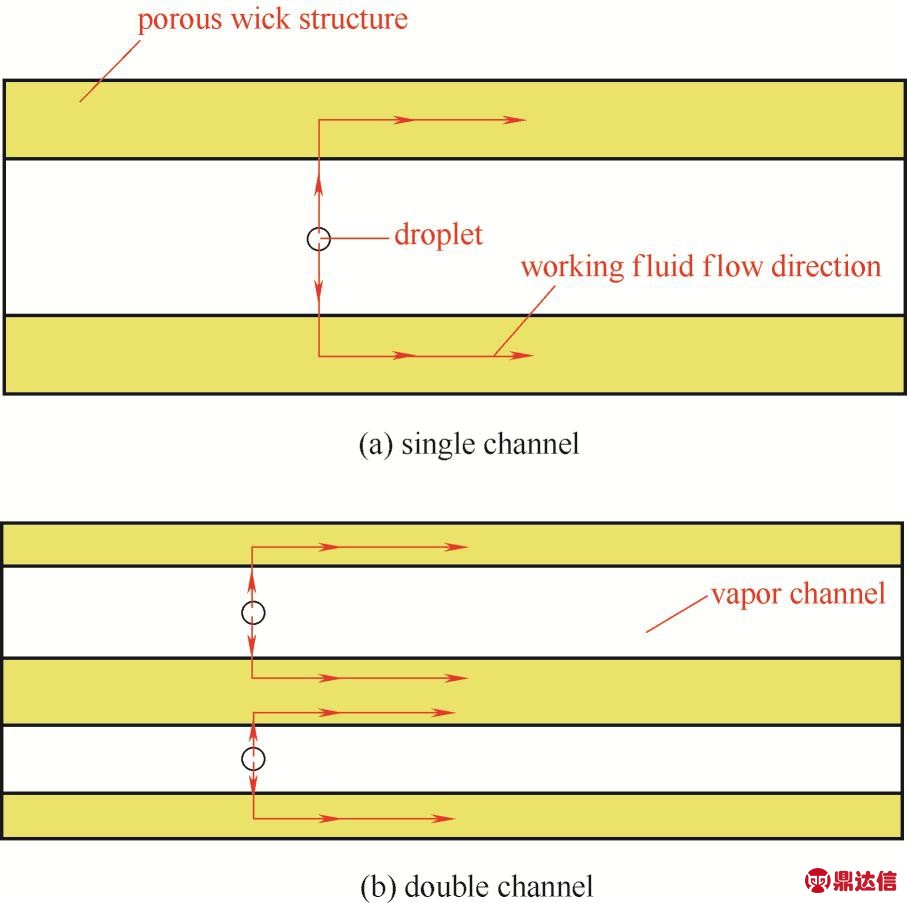
图12 两种槽道结构
Fig.12 Schematic diagram of two channel structures
4 结论
基于热管制作工艺问题,设计并制作了采用焊接工艺毛细芯为烧结多孔槽道结构的超薄平板热管,相比已有文献,该热管制造简单。研究了加热功率、铜粉粒径以及槽道数目对热管传热性能的影响,结论如下。
(1)本文的超薄平板热管厚度仅为0.85 mm,相比纯铜板,该平板热管能有效降低热源的温度,并且蒸发段和冷凝段的温差只有铜板的1/10。
(2)铜粉粒径对热管影响较大,不同铜粉粒径导致孔隙率的差异,进而影响热管的性能,在双槽道结构粒径为120~180 μm时,传热极限为15 W,热阻为0.18℃·W-1。粒径为58~75 μm时,传热极限为11 W,最低热阻为0.11℃·W-1。
(3)在所有加热功率条件下,单槽道热阻值比双槽道更高。在加热功率较小时两者热阻的差异较大,随着加热功率的增加,两者的差异逐渐减少。在三种不同粒径下,在热管出现烧干前,两者差异最小为21%。