摘 要:为解决数控渐进反向成形过程中板材与支撑之间形成密闭空腔,腔内空气不断被压缩而产生的对板材的反作用力影响板材件成形质量和成形精度问题,提出一种可由待成形板材件的CAD模型自动生成带有通气孔特征的支撑体三角网格模型的方法。给出了计算支撑体空腔体积与空腔内压强的算法、自动识别复杂板材件凹部数量与位置的算法,及其在合适的位置生成通气孔进而生成带有通气孔的支撑体三角网格模型的算法。应用实例表明,所提算法能够自动生成带有通气孔的支撑体。成形实验表明,板材件成形过程中密闭空间的形成会导致成形件鼓包变形甚至破裂,而带有通气孔的支撑体能够有效地解决上述问题。
关键词:板材成形;数控渐进成形;支撑体;密闭空间;通气孔
0 引言
金属板材数控渐进成形技术是一种新兴的柔性成形技术[1],该技术将快速原型技术中的分层制造思想与塑性成形技术有机结合在一起,将复杂的三维模型离散为二维等高线层,使挤压工具头沿着等高线层轨迹以包络模型轮廓的方式进行逐层逐点挤压,最终成形出具有一定空间几何形状的钣金件[2-3]。在当代个性化数字制造的社会环境下,数控渐进成形技术在多品种小批量钣金件的加工制造领域具有广阔的应用前景[4-6]。
数控渐进成形技术一个必不可少的环节,是对成形件的尺寸精度、表面质量具有较大影响的支撑制作[7],一般都将与被成形件相同形状的形体作为支撑[8],这种支撑可采用化学木材等材料用数控铣削的方法制作[9],也可采用纸叠层快速成形技术制作纸基支撑[10],亦可采用钢质结构作为支撑[11]。Franzen等[12]提出用与主工具头做同步运行的副工具头作为支撑的成形方法,Essa等[13]研究了这种支撑的有效性,认为这种支撑有助于抑制反弹变形;查光成等[14]根据渐进成形厚度减薄余弦定理,将加工件的表面离散为标准模板库(Standard Template Library, STL)模型,且STL模型各三角面片顶点坐标的x,y值保持不变,而z坐标值在z轴负向偏置一个原始板材厚度,在此基础上生成支撑体表面模型,使得挤压工具头与支撑之间保持合理的间隙。笔者前期研究提出由待成形板材件的CAD模型直接生成可自适应板材厚度变化并能保证挤压工具头与支撑之间的合理间隙的支撑CAD模型自动生成方法[7],研究了能够自动生成可根据加工要求自动调整大小的支撑STL模型生成算法[15]。然而,上述有关支撑研究均未考虑在支撑上设置通气孔,为此本文提出一种面向数控渐进反向成形的、带有通气孔的支撑体自动生成方法。
1 总体思路
在数控渐进成形中,为保证非轴对称钣金件和含有台阶等形状复杂钣金件的表面质量和成形精度,必须做出一套与待成形钣金件形状相同且相互匹配的支撑体,使其在成形过程中给钣金件提供反作用力,同时在一定程度上维持非加工区域的空间几何形状不变。在数控渐进反向成形过程中(如图1),板材与支撑之间形成密闭空间,当工具头持续向下进给运动时,密闭空间内部空气持续被压缩,压缩后的空气产生对板材的反作用力。这种反作用力,对于不断被拉伸变薄还有较强的反弹倾向的板材件来说,所产生的不良作用不容忽视,其会使板材件产生变形,从而影响钣金件的成形精度。鉴于此,本文提出在支撑底部设置通气孔,以消除由此类因内部气体压缩产生的反作用力影响板材件成形精度的问题。
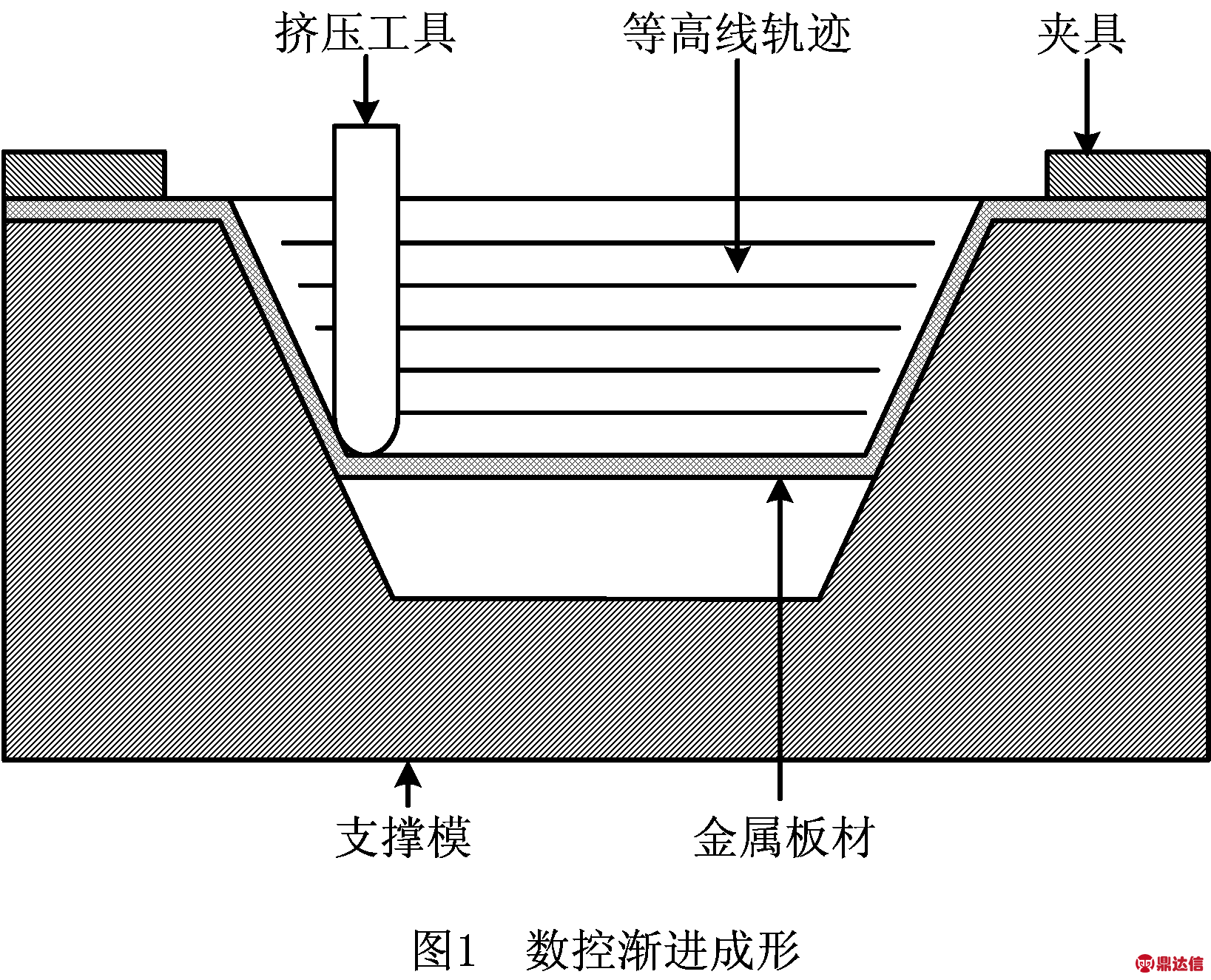
2 板料与支撑之间密闭容腔的体积与压强计算
根据Boyle’s law(玻义耳定律)在密闭容器中的定量气体,在恒温下,气体的压强和体积成反比,即P0×V0=P1×V1,其中:P0为恒温状态下的大气压强,V0为初始状态下的体积,P1为体积变化后的压强,V1为变化后的体积。
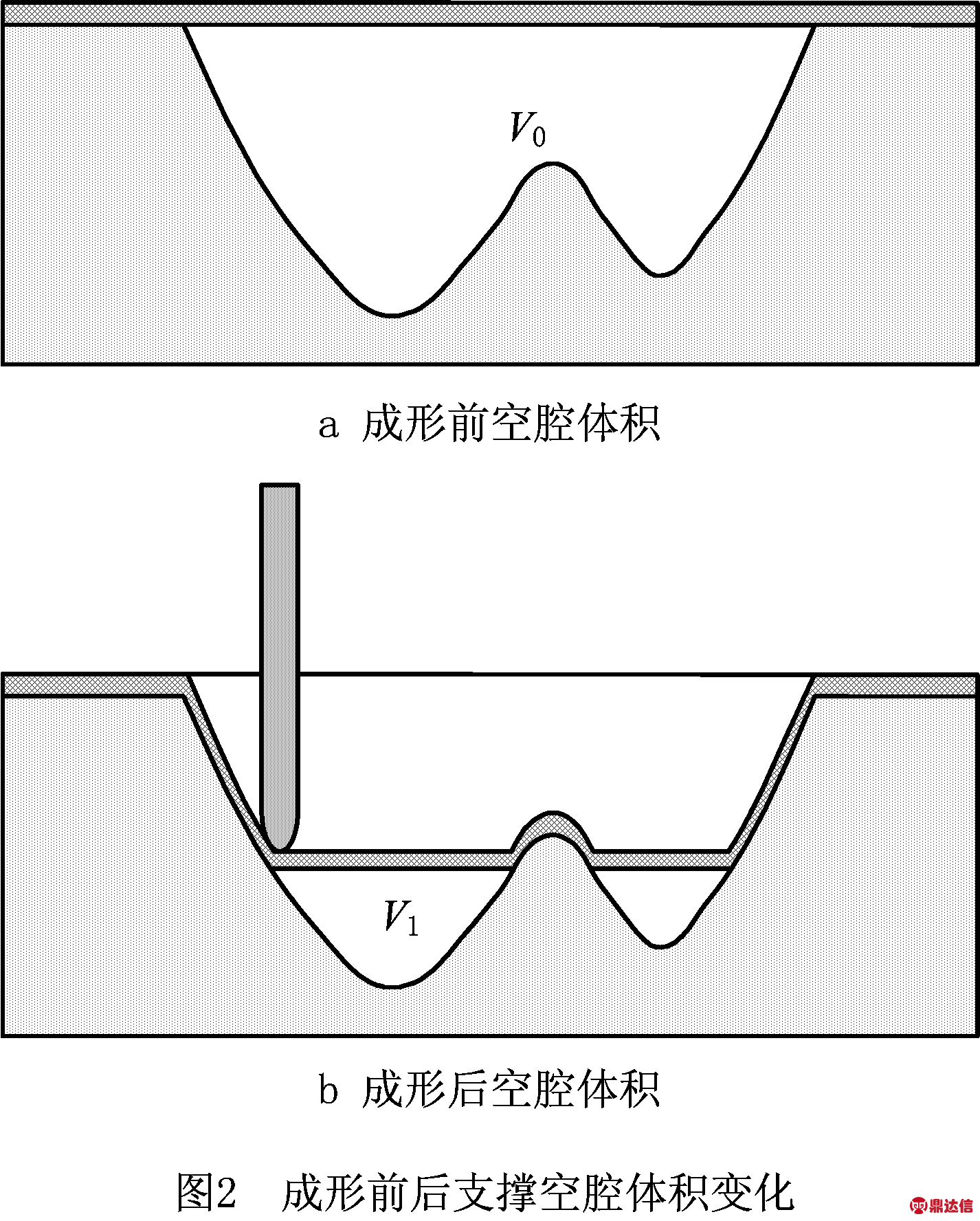
本文将待成形板材件视为盖,将支撑体视为底和壁,由待成形板材件和支撑体形成的空间视为容器,该空间在渐进成形过程中形成密闭容器(如图2),并将待成形板材件在成形前后所对应的支撑体凹部空腔内空气体积V0和V1作为可直接检测计算的自变量。由玻义耳定律计算公式可得渐进成形后钣金件成形区域与支撑体凹部间的空气压强为P1=P0×V0/V1。根据待成形板材的材料特性,以用户设定压强[P]为成形过程中板材不受影响的许用压强,可以判断出某一成形过程在满足成形精度的前提下是否能够顺利进行。
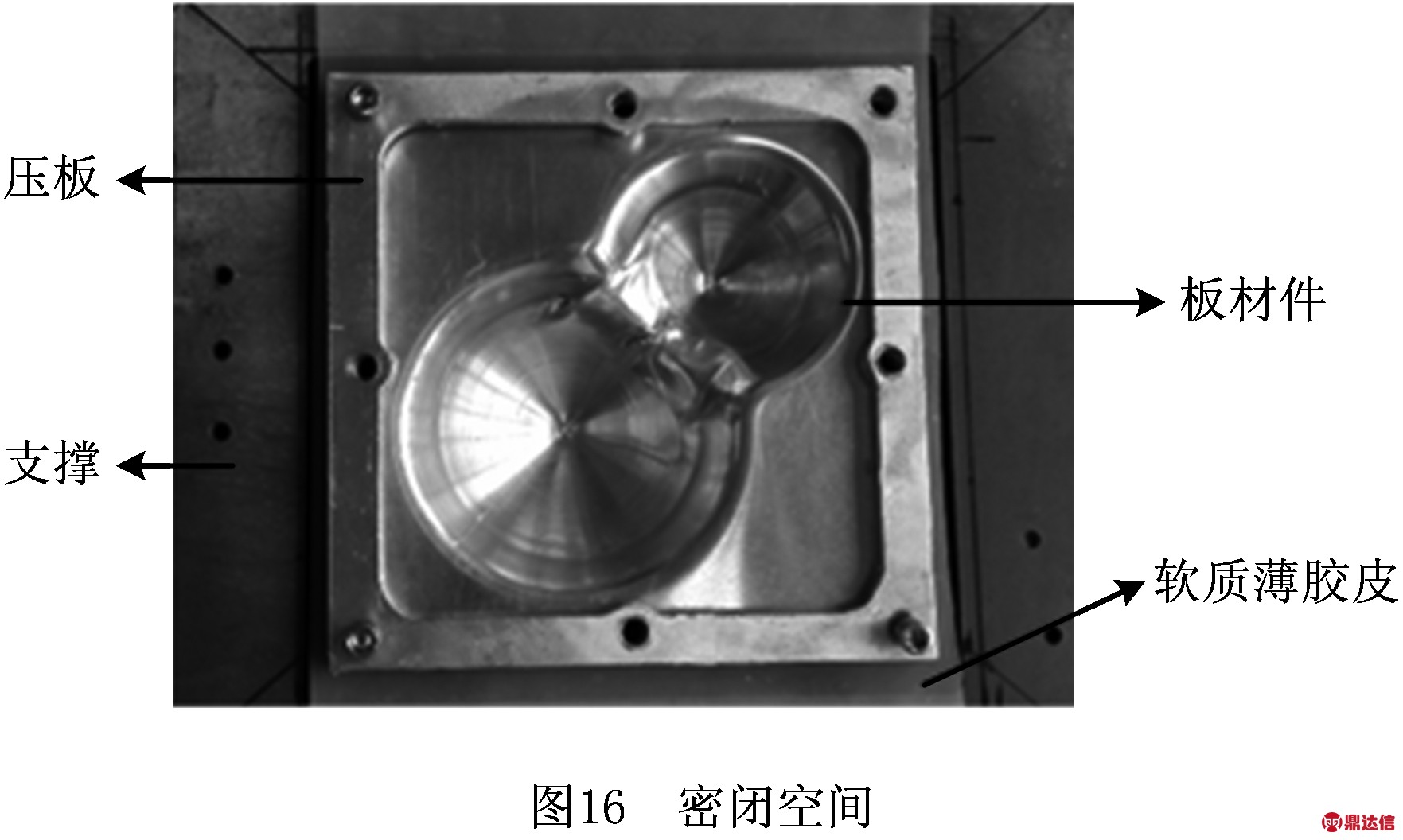
对于支撑体凹部空间内气体体积的计算,本文以微积分的方式将凹部空间分解为多个棱柱,再将所有棱柱体积累加得到凹部空间体积。棱柱微元以三角面片作为底面,但板材件STL模型中支撑凹部的三角面片可能会出现狭长尖锐和面片尺寸较大的情况,导致以该三角面片作为棱柱的底面求得的凹部空间体积误差较大,因此本文将支撑凹部空间的边界环内部支撑上平面区域进行三角网格细化后得到的三角面片作为棱柱微元的底面,具体细化方法采用郑淑贤[14]的三角网格划分方法(以下有关三角网格化问题都采用此法),细化结果如图3所示。以细化后△ABC的中心点O为原点,以模型所在笛卡尔直角坐标系Z轴负方向为射线方向做射线BO′,交支撑模型原凹部表面三角面片于点O′,以OO′为三棱柱的高,求得三棱柱微元的体积:
Vi=Si×hi;
(1)

(2)
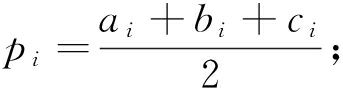
(3)
hi=OO′。
(4)
式中:三棱柱微元的体积为Vi,底面面积为Si△ABC;ai,bi,ci为三角形三边边长;pi为三角形半周长;hi为三棱柱的高。
在不考虑支撑以板材减薄率设计的情况下,钣金件成形后与支撑凹部间的空腔体积为理想状态下成形钣金件模型变形区体积与实际状态下钣金件模型变形区体积之差,其中理想状态下钣金件厚度为板材初始厚度,实际状态下钣金件厚度为板材按减薄率t=t0×sin θ减薄后的厚度,如图4所示。
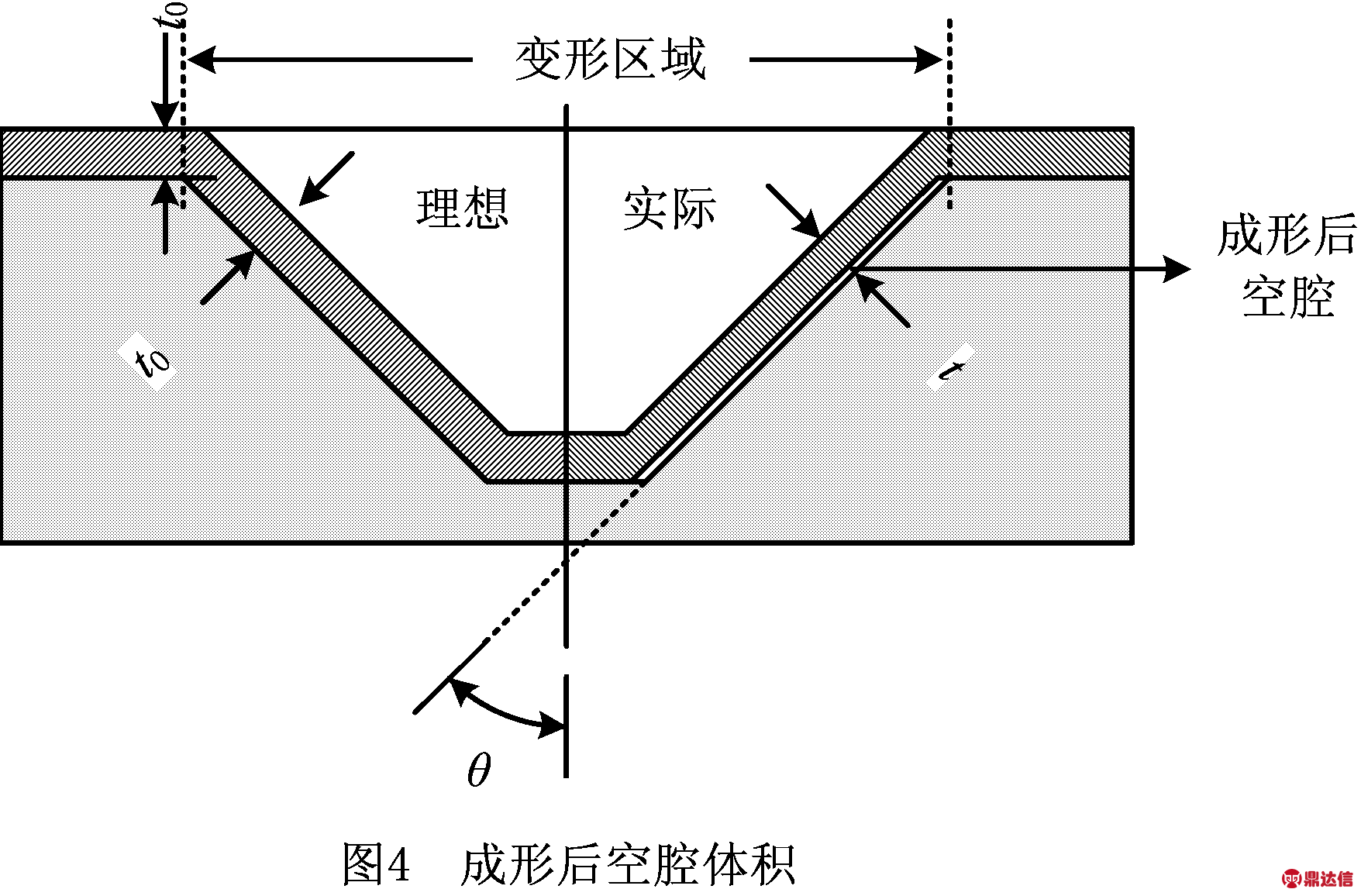
支撑凹部渐进成形前后空腔体积的计算流程如下:
(1)将凹部区域边界线段按顺序首尾相连得到封闭的平面区域多边形,称为线环。将线环投影到XOY平面上,得到XOY平面的封闭区域投影线环,并将其进行三角网格化,求出三角网格化后各三角面片的面积和各三角面片的中心O。
(2)将支撑凹部表面各三角面片向XOY平面上投影,即将支撑凹部表面三角面片各顶点Z值赋值为0,使之位于XOY平面,找到点O落在其内或其上的三角面片,并利用找到的投影三角面片所对应的原三角面片三顶点作平面方程。
(3)以各三角面片中心O为射线原点向Z轴负向作射线,交步骤(2)中所求平面方程对应的平面于点O′,并以所求得的三角面片面积和OO′距离(即三棱柱的高)求得三棱柱微元的体积,将所有三棱柱微元体积累加得出渐进成形前板材与支撑体所形成的空腔内部气体体积。
(4)以待成形钣金件模型外表面三角面片为三棱柱底面,以初始板材厚度为高求出理想状态下钣金件模型变形区域的体积。
(5)以三角网格细化后的支撑凹部区域三角面片为三棱柱底面,以初始板材厚度为高求出实际状态下钣金件模型变形区域的体积。
其中,将上表面矩形边点和下表面矩形边点以a→a′→b→b′→c→c′…的形式穿插存入同一个点链表,依次取相邻3个点构成一个三角面片。三角面片法向量的确定分为两类:①“上—下—上”类,即“P11-P12-P13”,如图7所示,此时三角面片法向量n=(i,j,k)用向量积求出,即n=P11P12×P11P13;②“下—上—下”类,即“P21-P22-P23”,此时三角面片法向量为n=P21P23×P21P22。
(7)用玻义耳定律公式P1=P0×V0/V1求出渐进成形后压缩气体的压强比值。
(8)将求得的压强与用户设定许用压强作比较,判断该压强是否会影响成形板材件的表面质量及成形精度。
②颈源性头痛常常不表现在它的病理改变部位,其疼痛的部位常常模糊不清,分布弥散。尽管患者疼痛部位多变,其实仍有规律可循。本人多年的临床实践中发现颈源性头痛查体压痛点符合“四部27点规律”,只要符合“两部2点或2点以上规律”的颈源性头痛诊断率极高,医生诊断时也容易掌握。其中,绝大部分颈源性头痛的患者枕部有压痛点[3]。
3 带有通气孔的支撑体模型生成算法
3.1 通气孔生成位置确定
(1)提取作为支撑凹部内表面的钣金件模型外表面。
(2)对外表面利用水平面进行等距分层切割,将切割每个三角面片得到的线段行去重处理,并利用线段首尾相连的特性将各个线段存入一个临时线链表m_LayerValleyTemp中。
(3)比较此排完序后的线链表m_LayerValleyTemp中线段个数与该层线链表m_LayerLineList[b-1]中所有线段的个数。如果两者相等,则说明该层中未出现第二个凹坑的情况,将m_LayerValleyTemp中的线段都存入m_LayerValley[b-1][0]中。如果两者不相等,则说明本层存在两个或两个以上凹坑,求出此线链表中所有线段端点线环的中点,判断该中点与上一层所有线环中点在XOY平面内的位置关系;如果中点距离小于设定距离半径r=5 mm,则将该线环中的所有线段存入对应凹坑线链表m_LayerValley[b-1][c](c为对应凹坑)中。因为等距分层切割的层间距较小(约为0.2 mm~0.5 mm),板材件模型变形区域变形上下具有较好的连续性,所以上下两层线环中点的距离非常小,而不同凹特征之间的横向距离远大于两层纵向距离(切层层间距),因此本研究将线环位置的判断距离设定为r=5 mm。在实际应用中,允许用户根据具体情况自行设定。
(4)继续判断m_LayerLineList[b-1]线链表中是否还有剩余线段。如果有剩余线段,则继续按上述方法取环,并判断其所对应的凹坑,将其存入对应的凹坑链表中。
(5)取出每个凹坑线环最后一个线段个数不为0的层线环,求线环中各线段端点xyz的平均值,即求得线环中间点,并将该中间点作为通气孔端面圆圆心的位置。
3.2 带有通气孔的支撑体生成
(1)以已求得的通气孔位置点为圆心做一个圆,即求得该圆的圆周点坐标,坐标值为x=r×cos(r_angle),y=r×sin(r_angle),r_angle等差递增,范围为0~2π。
(2)将圆周上的各点沿模型所在的笛卡尔直角坐标系Z轴正向在XOY平面内投影到模型外表面上,找到该点落在外表面上对应的三角面片,以三角面片做平面,求以该点以及(0,0,1)为方向向量的直线与平面的交点,得出一系列落在模型外表面上的点。
(3)将模型外表面上各三角面片的顶点与所做通气孔圆做比较,判断将三角面片顶点投影到XOY平面时,各顶点是否落在圆内,如果三角面片中有一个顶点落在圆内,则将该三角面片从模型外表面链表中删除。
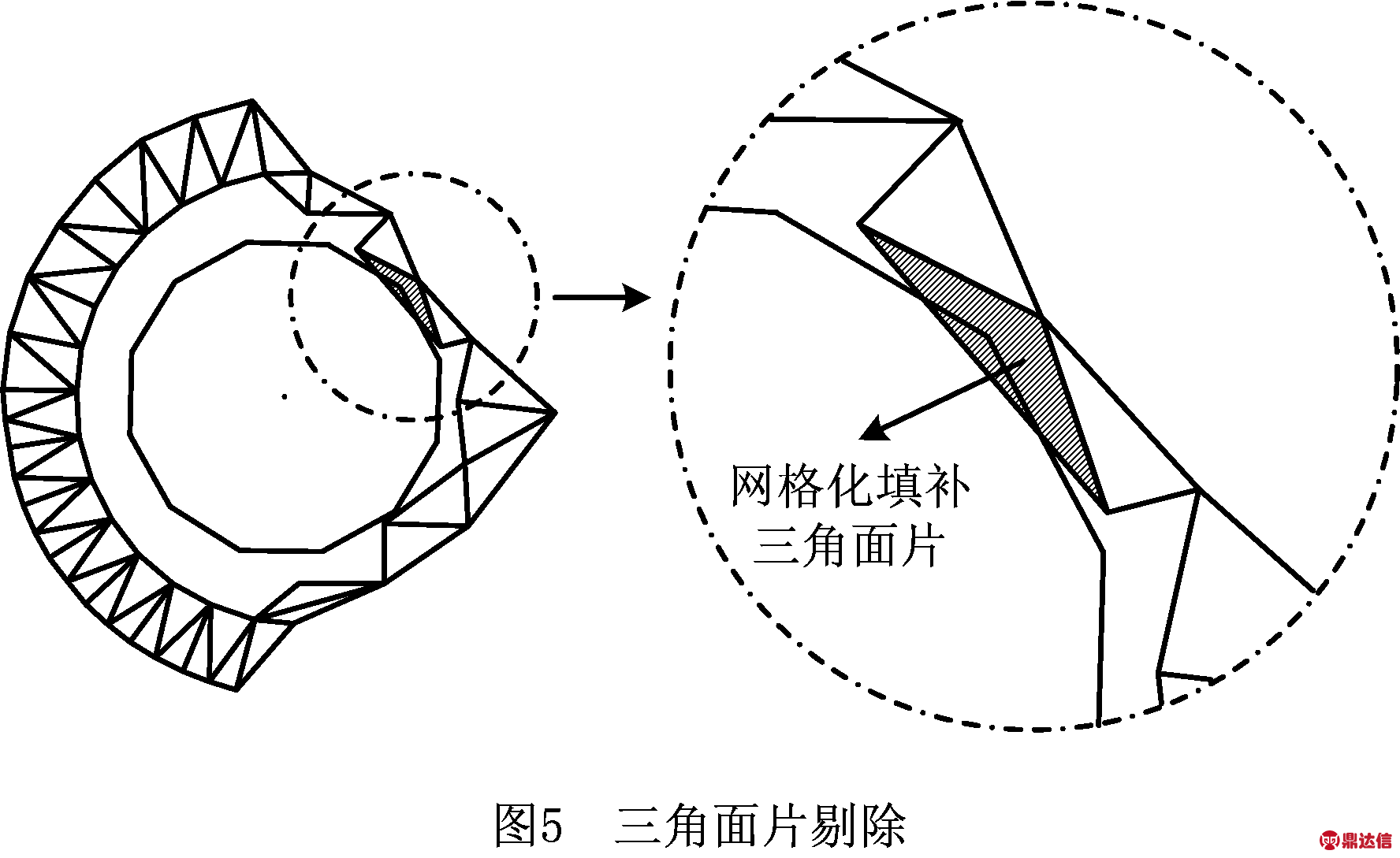
(6)以理想状态下待成形钣金件模型变形区体积与实际状态下钣金件模型变形区体积之差作为渐进成形后钣金件与支撑凹部空腔气体体积。
(4)删除所有通气孔位置三角面片后,产生一个具有不规则封闭孔洞的模型凹坑表面,提取其中单边环(即提取仅被一个三角面片共用的边),并根据首尾相连的特性将各边以顺时针方向排序。
(5)将通气孔位置单边环的点环(图6中的内点环)和构造通气孔圆点与支撑凹部表面交点环(图6中的外点环)合并为一个有序封闭的点环。合并后,为避免网格化时由于三角面片的缺失而产生缝隙,需在外点环中加入P1,在内点环中加入P3。因为点P1和点P4距离以及点P2和点P3的距离均为0,所以点P1和点P4以及点P2和点P3分别是同一点。在合并点环中,点的存储顺序为“P1-P2-以P2为起始的逆时针内点环-P3-P4-以P4为起始的顺时针外点环”。
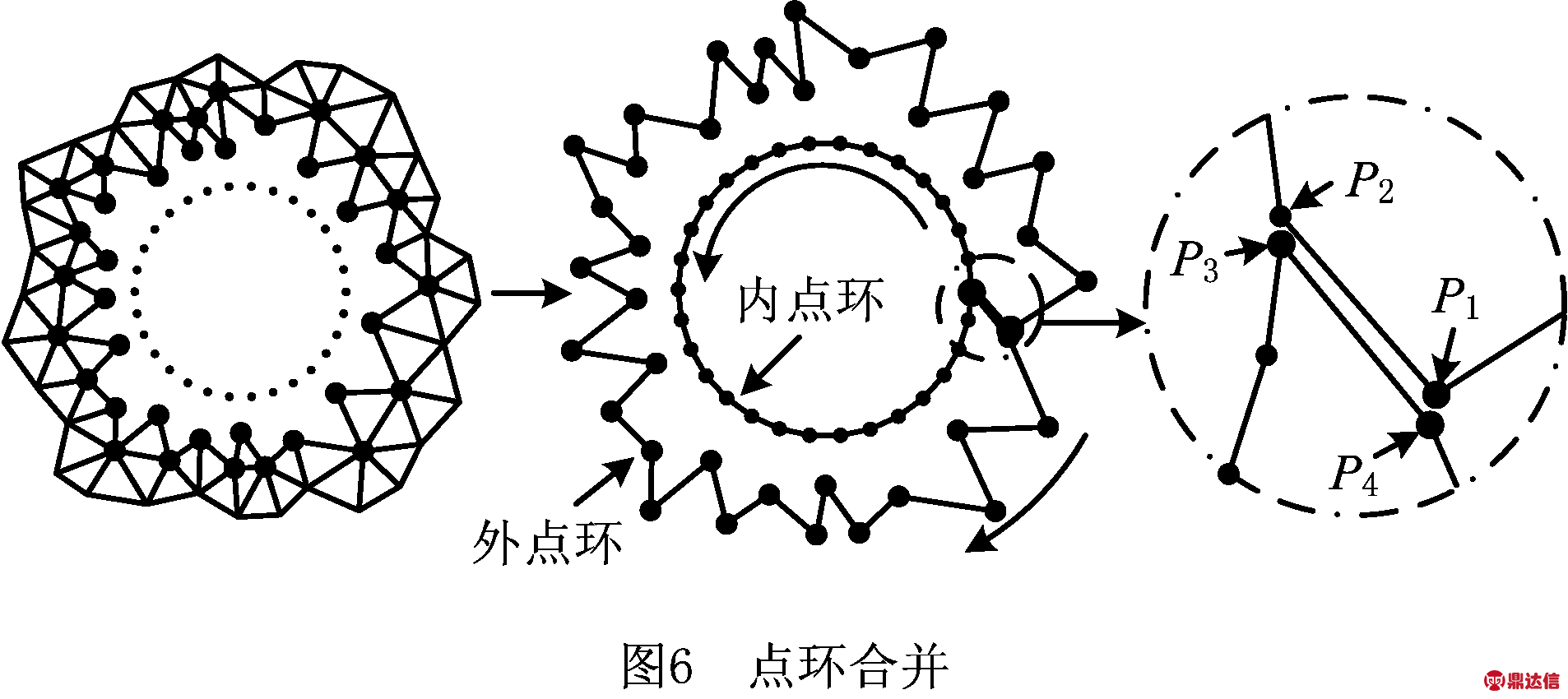
(6)对合并后的点环进行三角网格化,并以支撑缺口处的边环点为拟合对象,采用最小二乘法拟合到原支撑凹坑表面上。
(7)提取待成形板材件外表面并投影到XOY平面上形成投影线环,求出其最小包围矩形并按用户需求设定的距离将最小包围矩形向外偏置。
(8)以扩展后的矩形为基础,用上表面矩形边点和提取到的支撑凹部表面投影线环组成一个封闭点环,通过对其进行三角网格化构造支撑上平面。
(9)以扩展后的矩形为基础,将上表面矩形边点向下偏置生成下表面矩形边点,用上表面边点和下表面边点构造支撑实体的4个侧面。
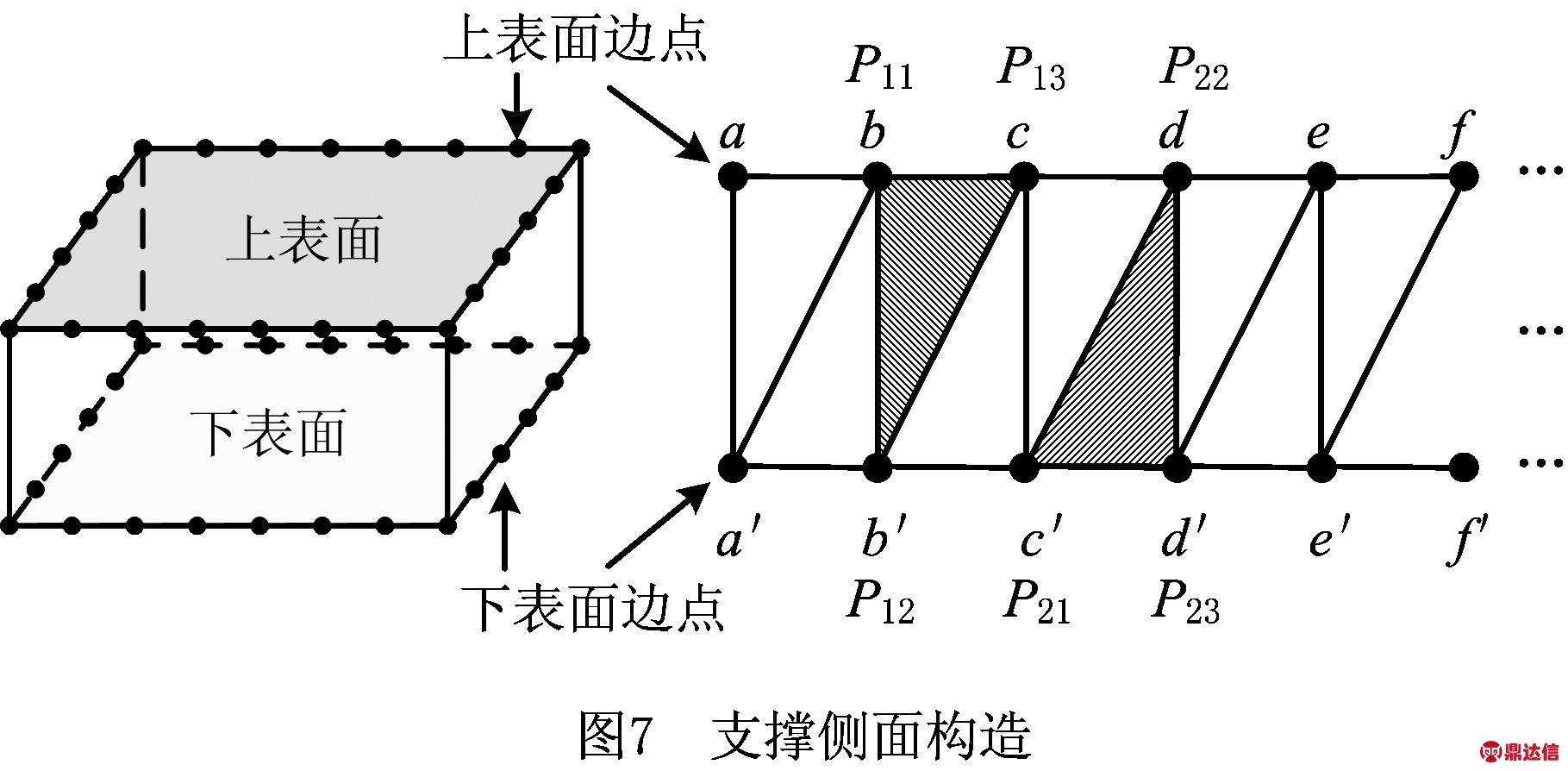
当剔除的三角面片范围较小时,对点环进行三角网格化时会出现新增的三角面片将封闭点环某一点包含在内的情况(如图5),为防止这种不合理的三角面片的产生,加大三角面片的剔除范围,即增大剔除所用圆半径。
(10)用下表面边点环经三角网格化得到支撑体下平面。
(11)以同样方式剔除所构造的支撑底面通气孔位置三角面片,并将合并后的点环进行三角网格化后填补因剔除三角面片而导致的不规则支撑底面。
(12)输出生成的带有通气孔的支撑体STL模型。
4 算法应用实例
本文在Windows 7环境下,利用VC++6.0,C++和OpenGL实现了上述算法的软件系统,并以如图8所示的多谷板材件STL模型为实验对象给出了算法应用实例。
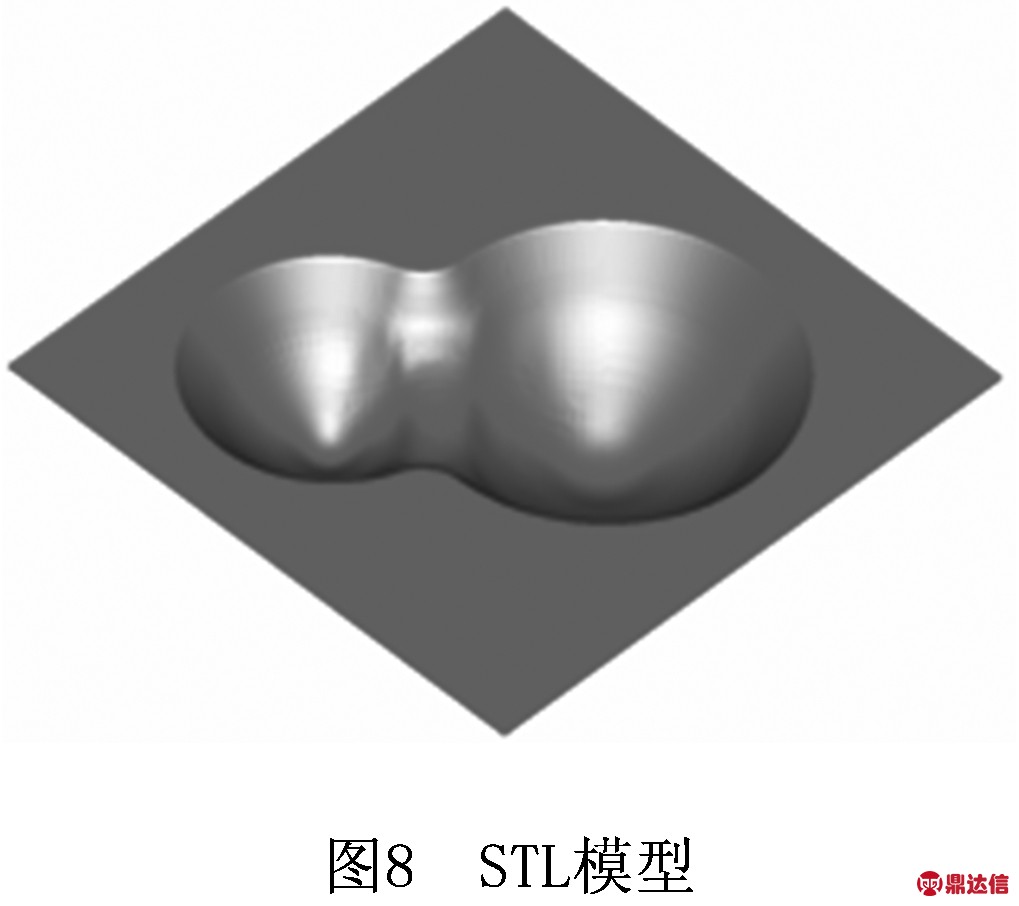
图9a~图9c分别为识别出的凹部、确定出的通气孔位置及将通气孔内三角面片剔除了的模型。
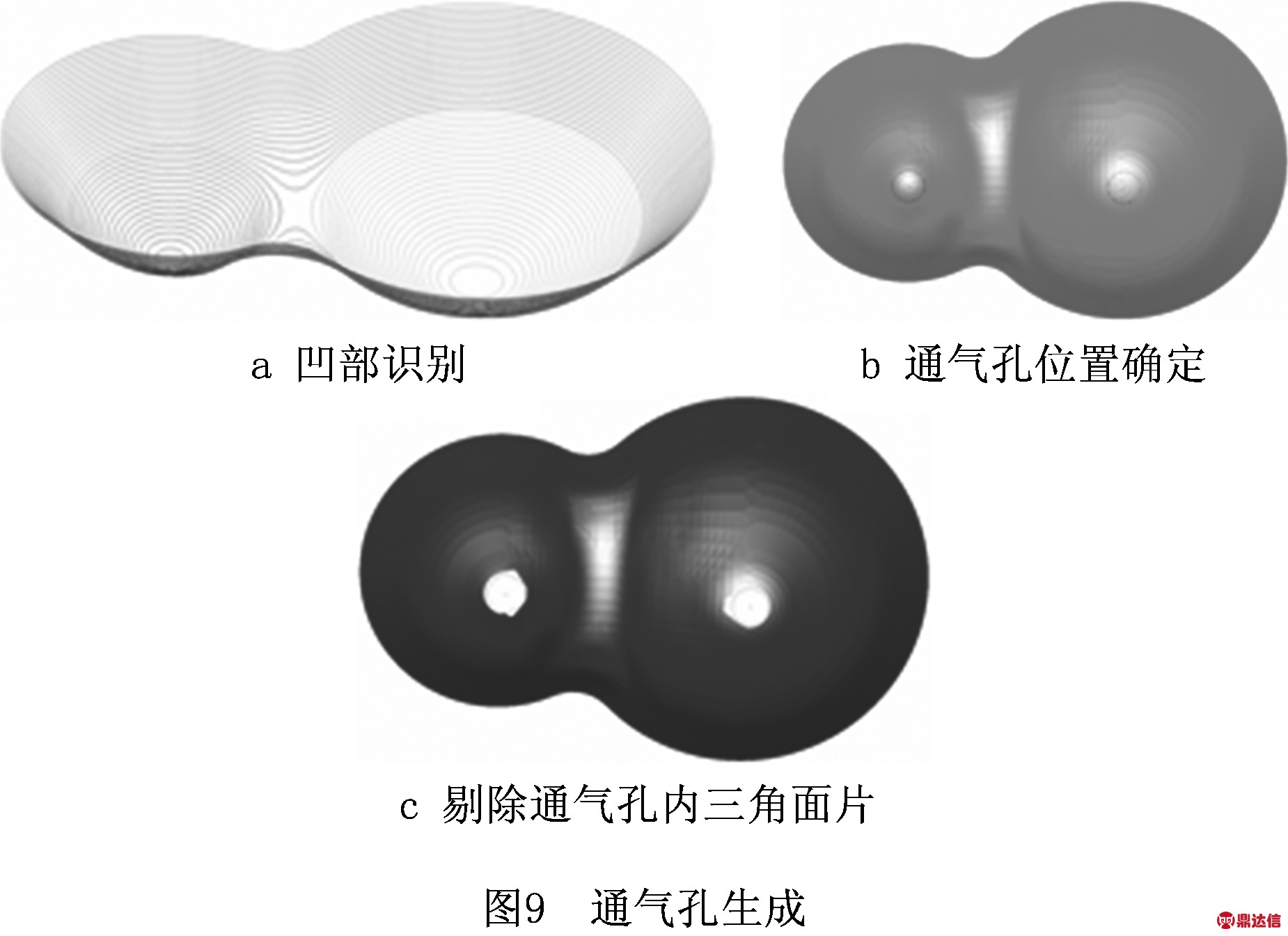
图10a所示为利用最小二乘法拟合并进行三角网格化的与通气孔边相连接的曲面,图10b所示为经三角网格化的通气孔内表面。图11a~图11c分别为生成的支撑上表面和通过把支撑向水平面投影构造的支撑侧面。图12所示为最终生成的支撑体的STL模型。
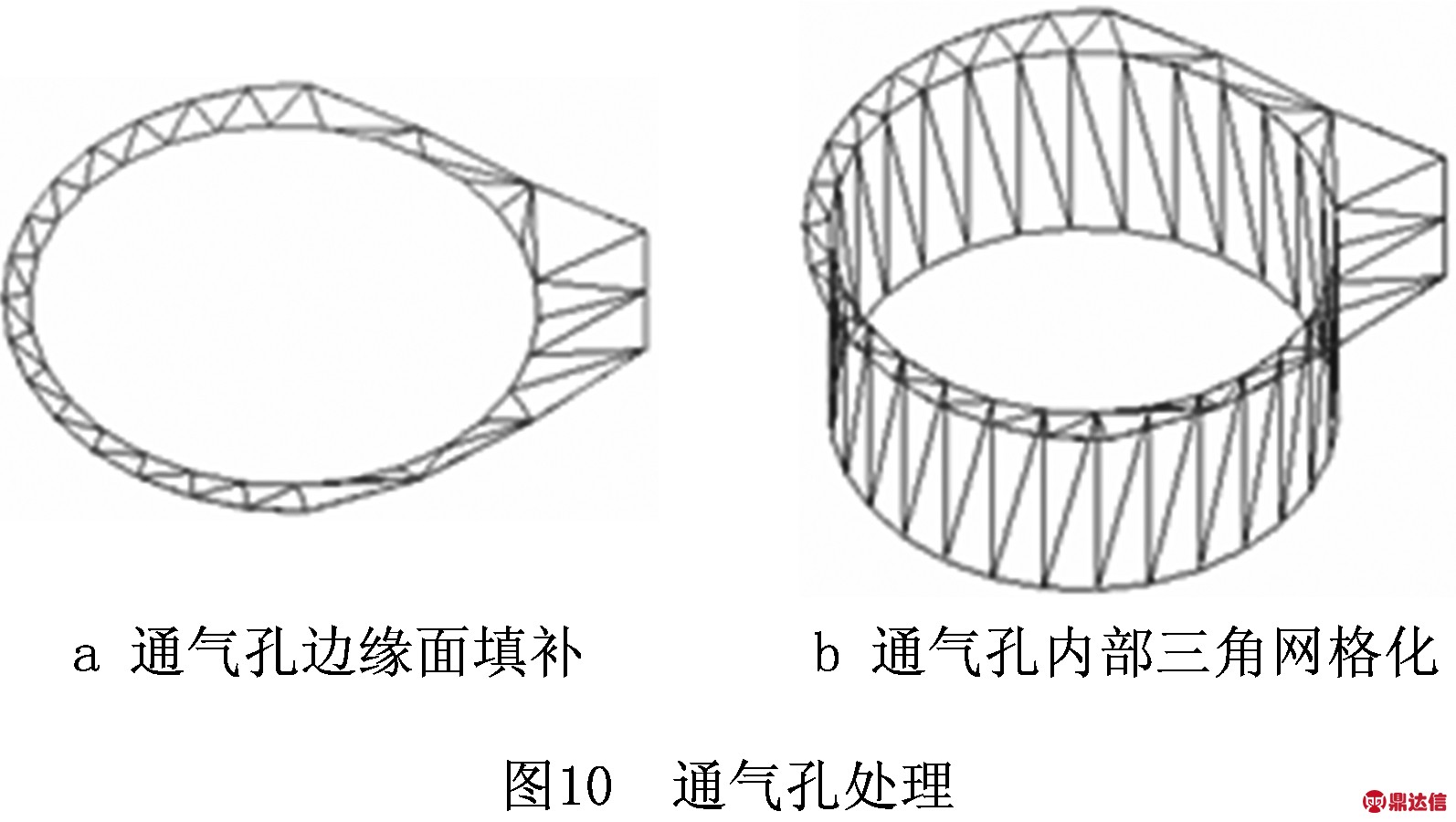
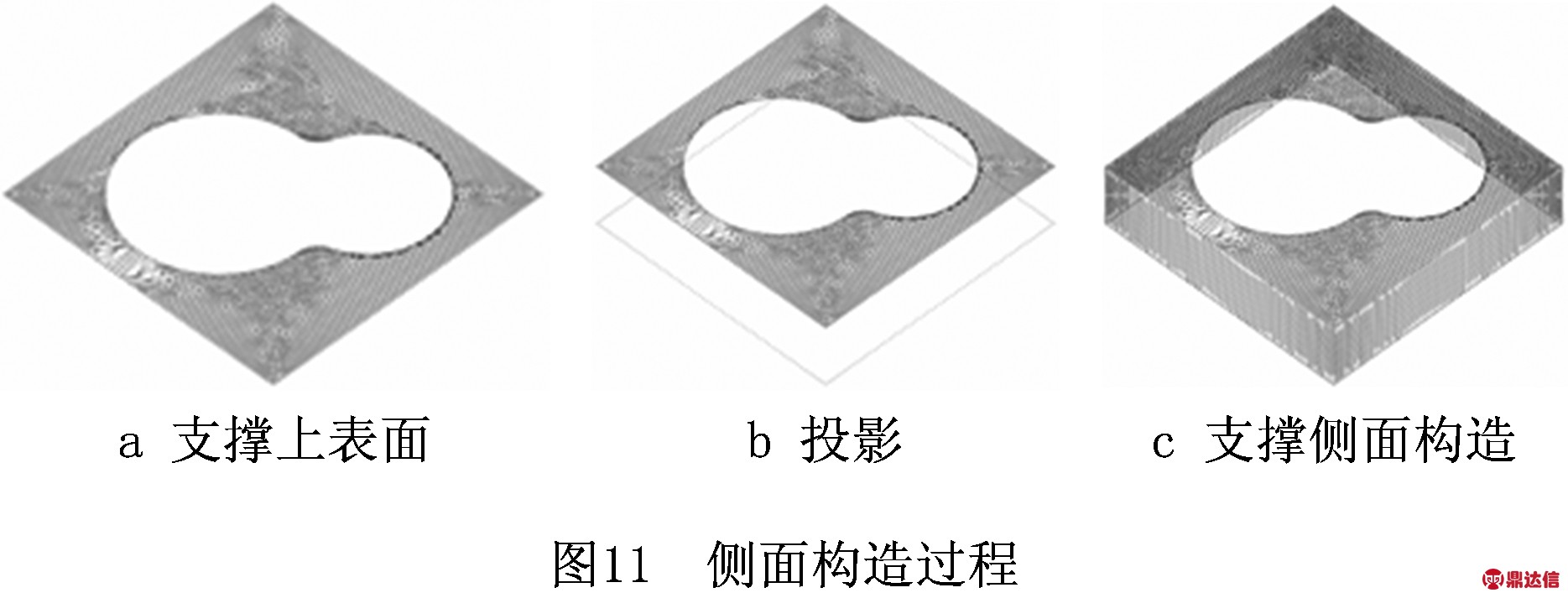
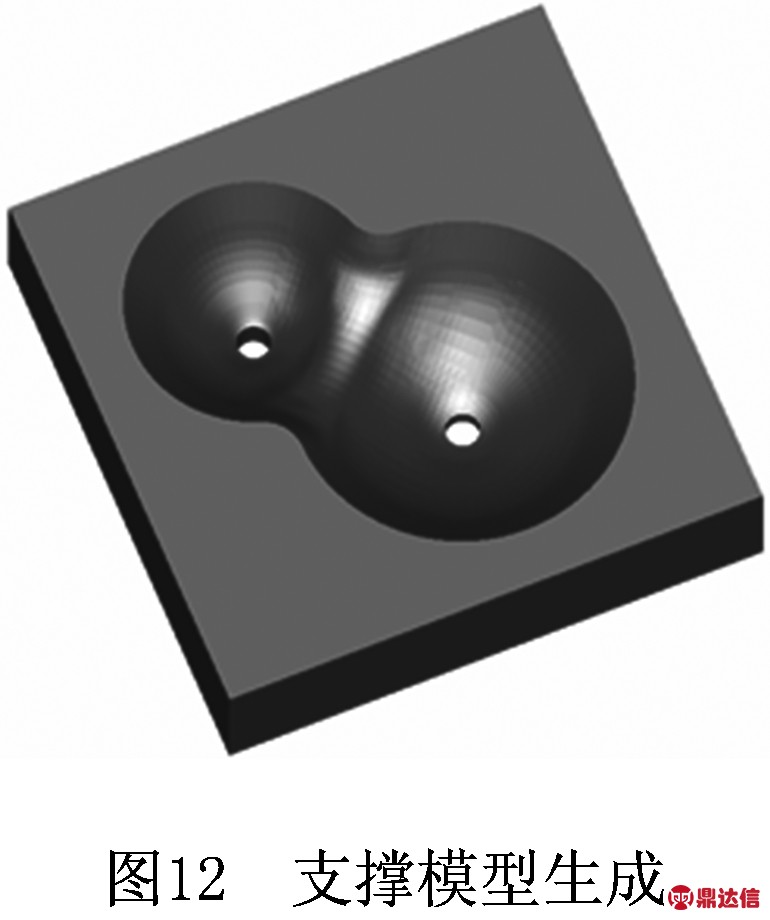
图13所示为将支撑凹部空间的边界环内部区域进行三角网格化并细化处理后得到的三角面片为三棱柱微元的底面;图14所示为数控渐进反向成形前后板材与支撑体空腔之间的气体体积计算结果。
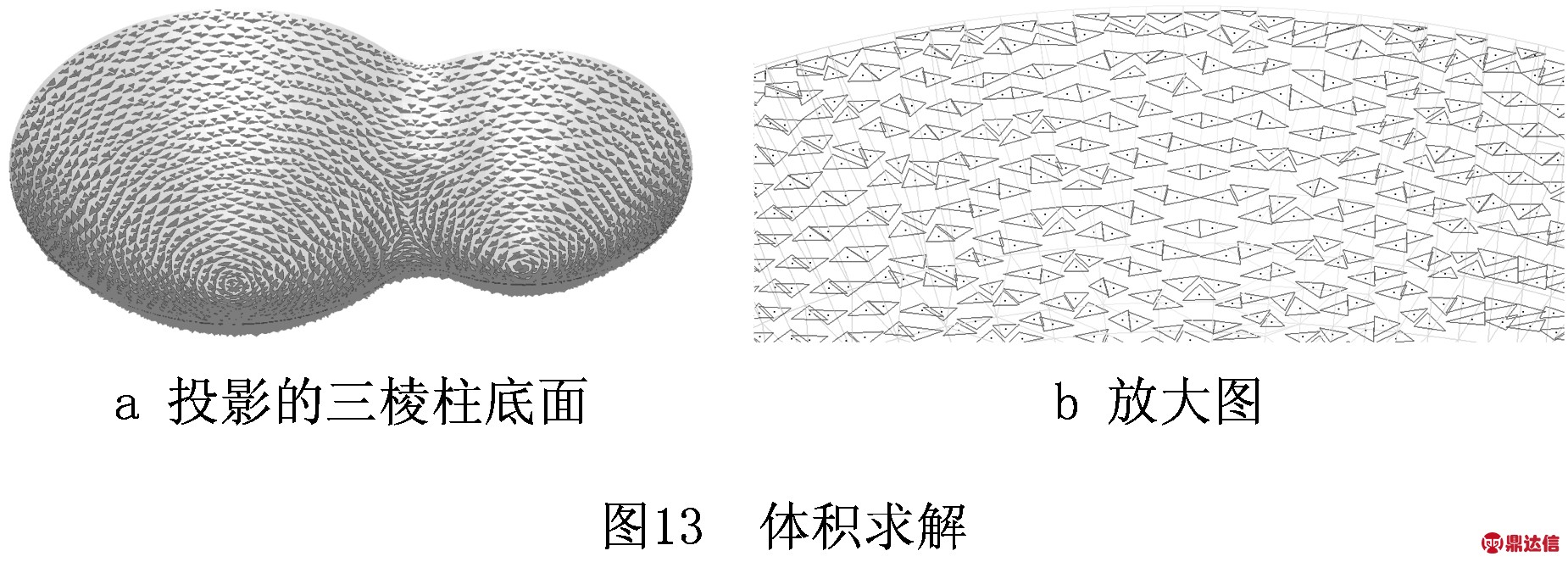
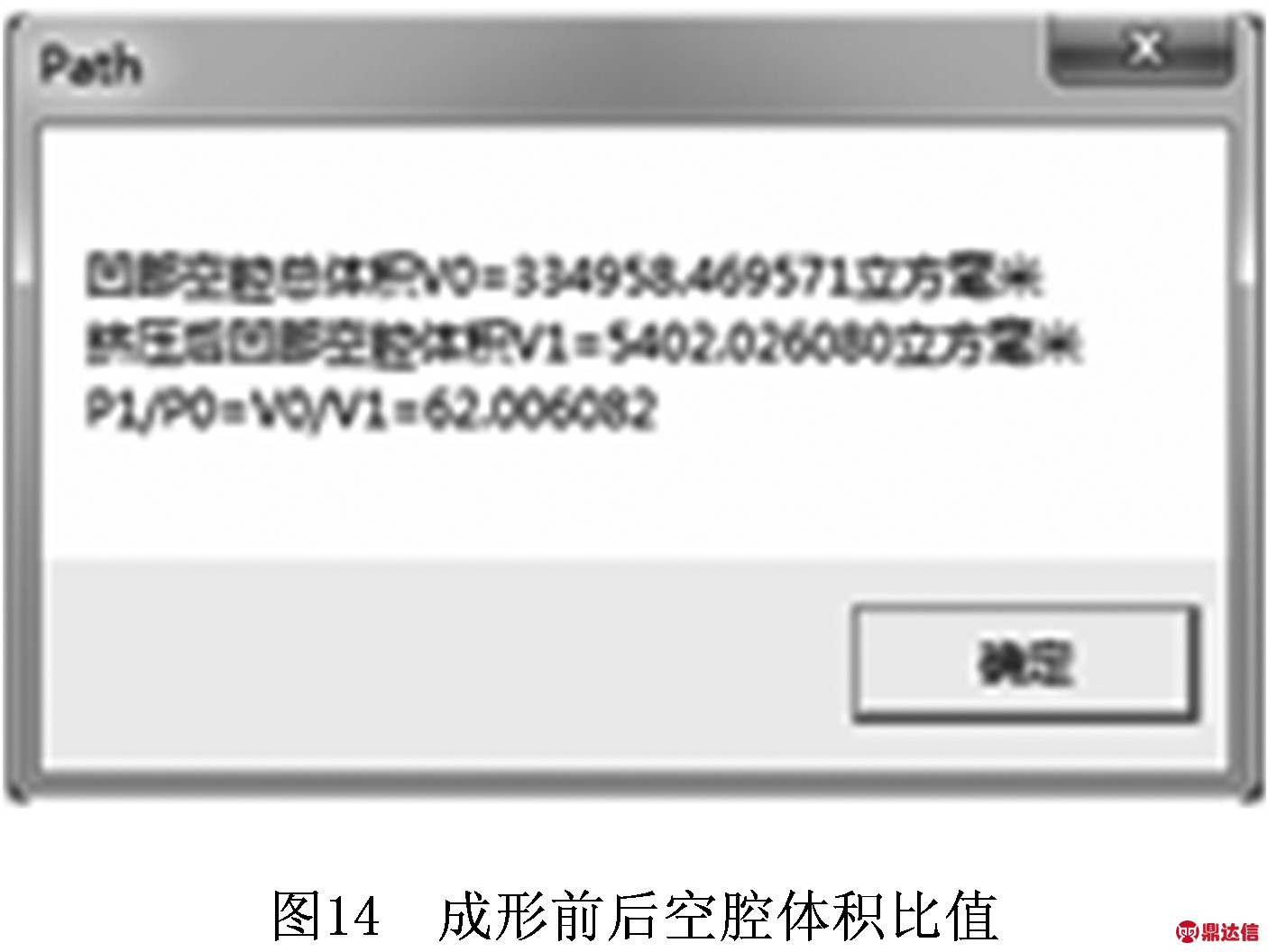
5 成形实验
为验证板材和支撑凹部形成的密闭空间在渐进过程中由于压强增大对板材件的成形质量是否产生不良影响,本文以算法实例中由板材件CAD模型自动生成的支撑体STL模型为实验对象,用MDX-540雕刻机加工出如图15所示的实验用支撑体,并进行了板材件的数控渐进成形对比实验。第一组实验为形成密闭空间环境下的板材渐进成形,第二组为支撑体带有通气孔的板材渐进成形。两组实验均采用厚度为0.88 mm的1 060铝板,以直径为10 mm的球形工具头按层间距0.2 mm进行渐进成形加工,进给量均为1 000 mm/min,润滑油为机油。
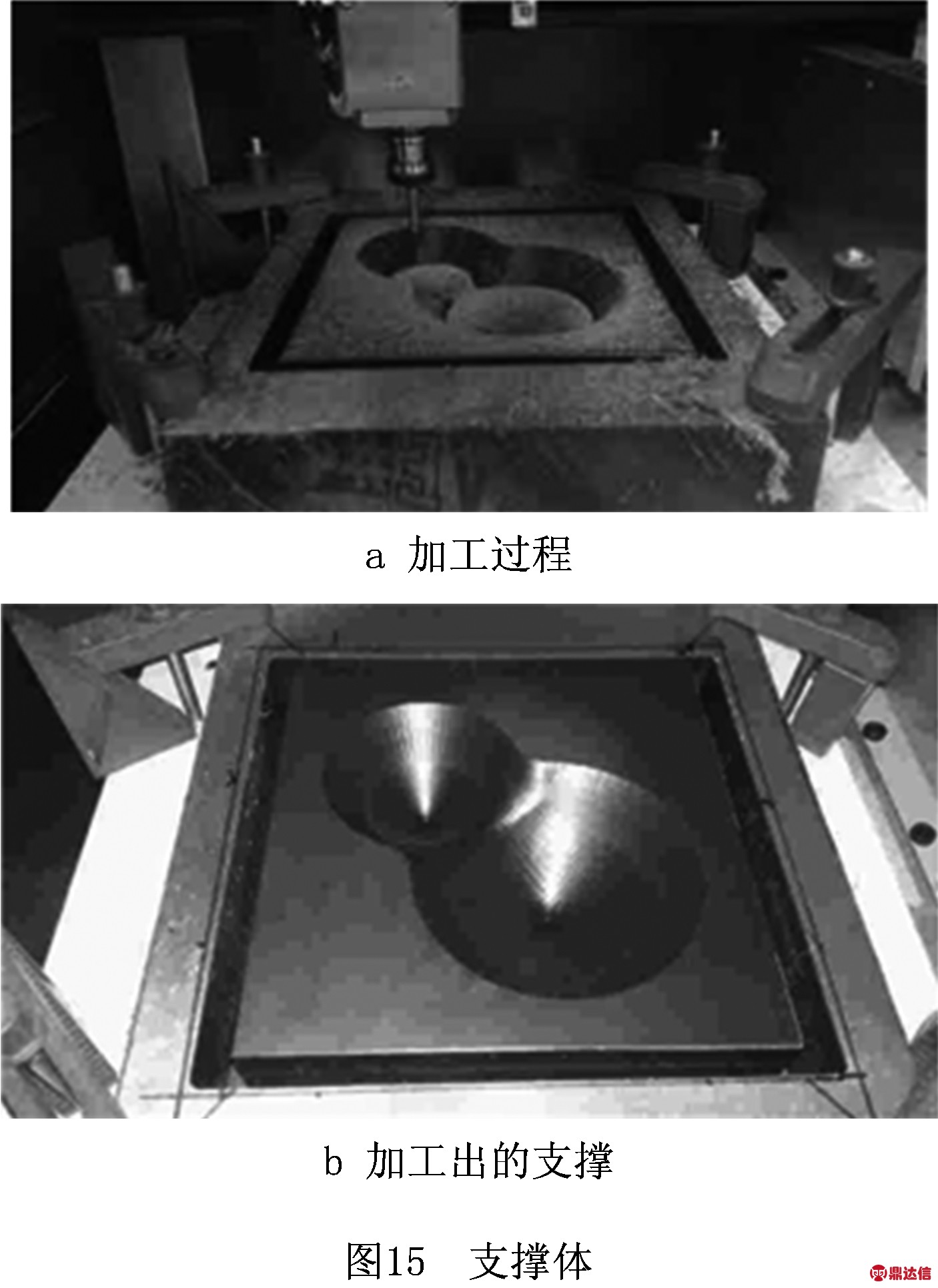
第一组实验中,为达到所需密闭空间的目的,采用如图16所示的在板材与支撑体间放置软质薄胶皮并使用压板压紧的方法。
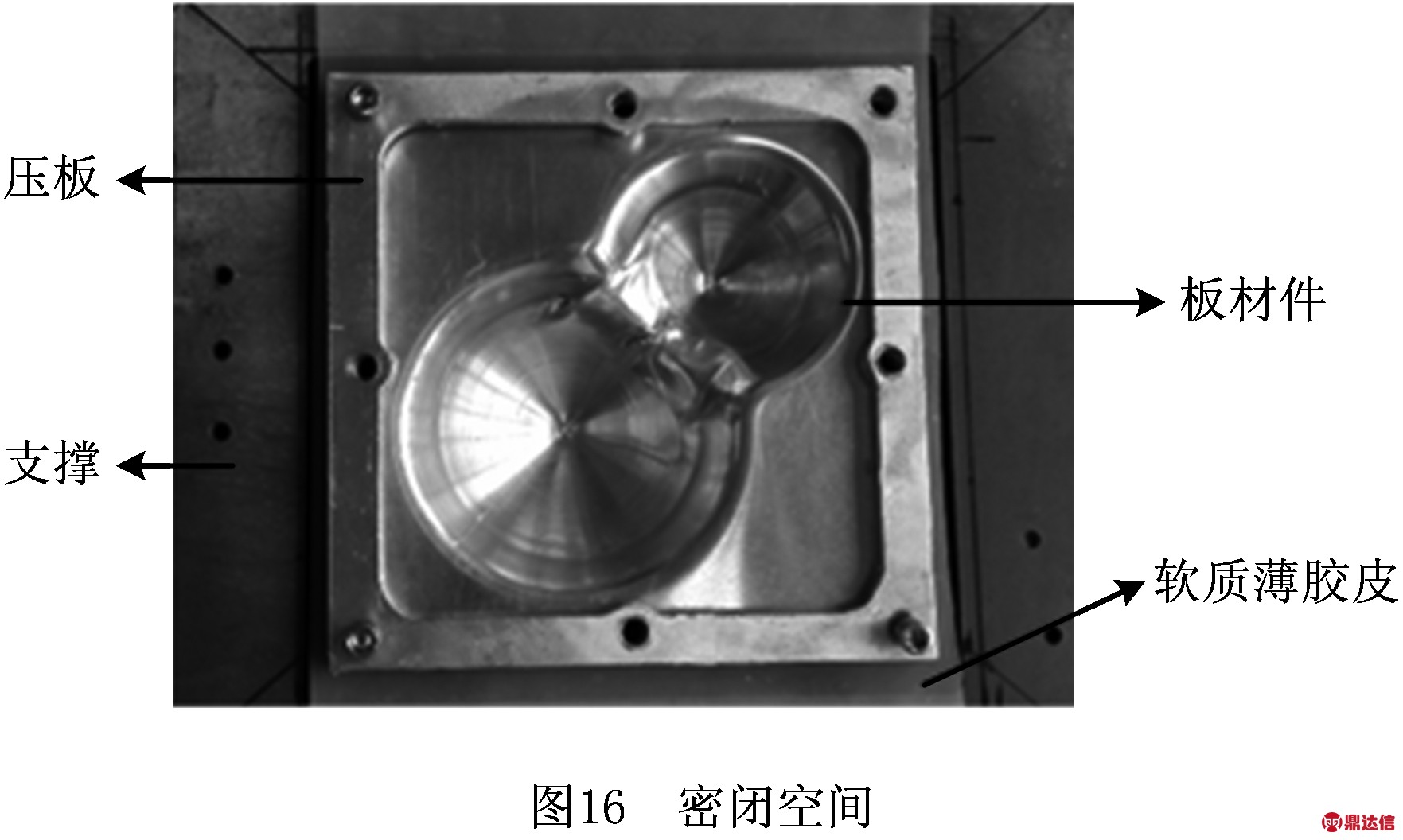
实验过程中,当挤压成形到板材件理论1/4深度时,板材上开始出现如图18a所示的鼓包现象,此时板材与支撑凹部形成的密闭空腔挤压前后体积之比约为V0/V1=1.905(如图17),即此时空腔内挤压前后压强之比为P0/P1=1.905,实验过程持续进行,板材件出现如图18b所示的破裂现象。
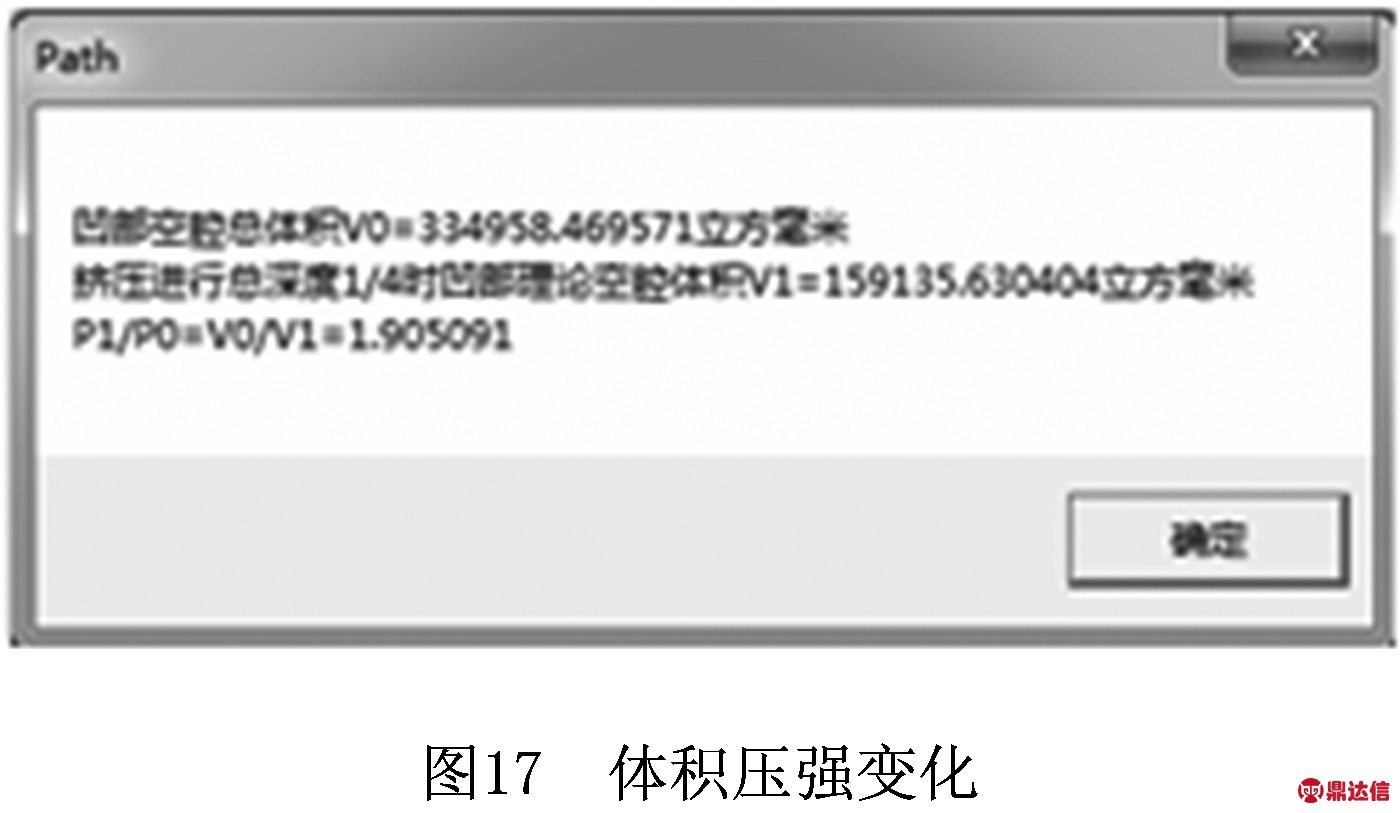
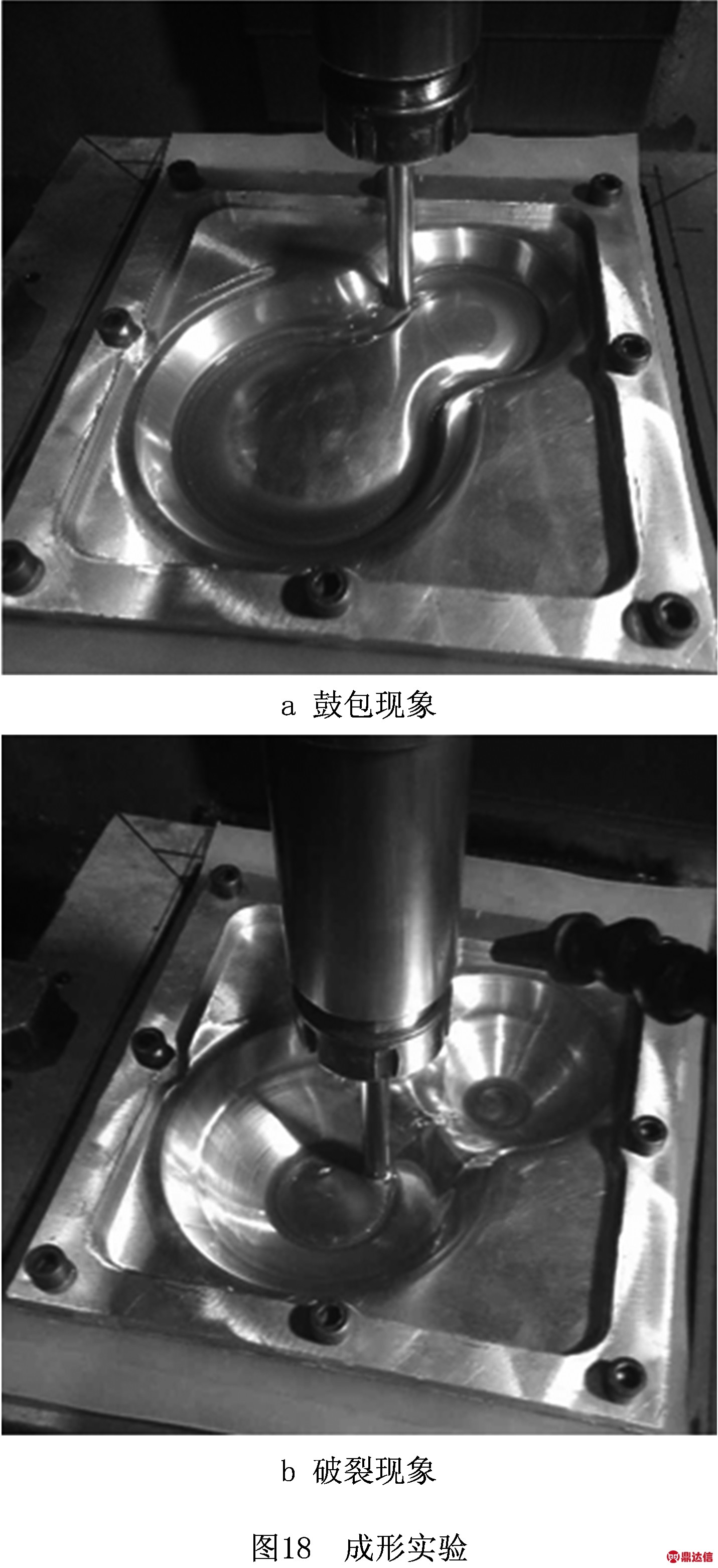
在板材件与支撑凹部形成密闭空间的情况下,板材件在成形区域存在明显鼓包和破裂的现象,除此之外,在板材件凹部边缘轮廓处也存在触感明显的凸起,同时在板材件凹部表面存在挤压工具头挤压过程中留下的明显的断断续续的痕迹,如图19所示,第一组成形实验板材件如图20所示。
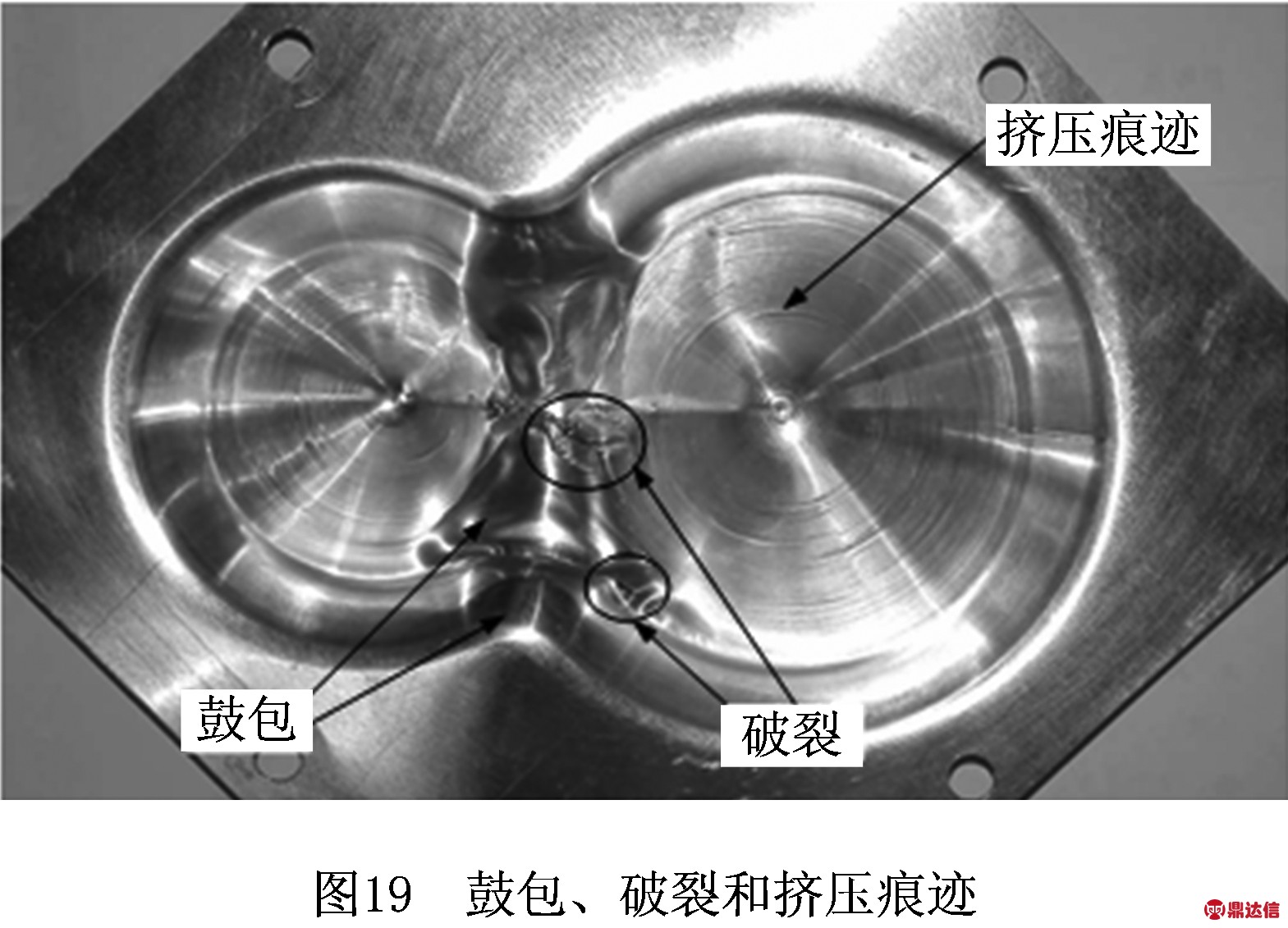
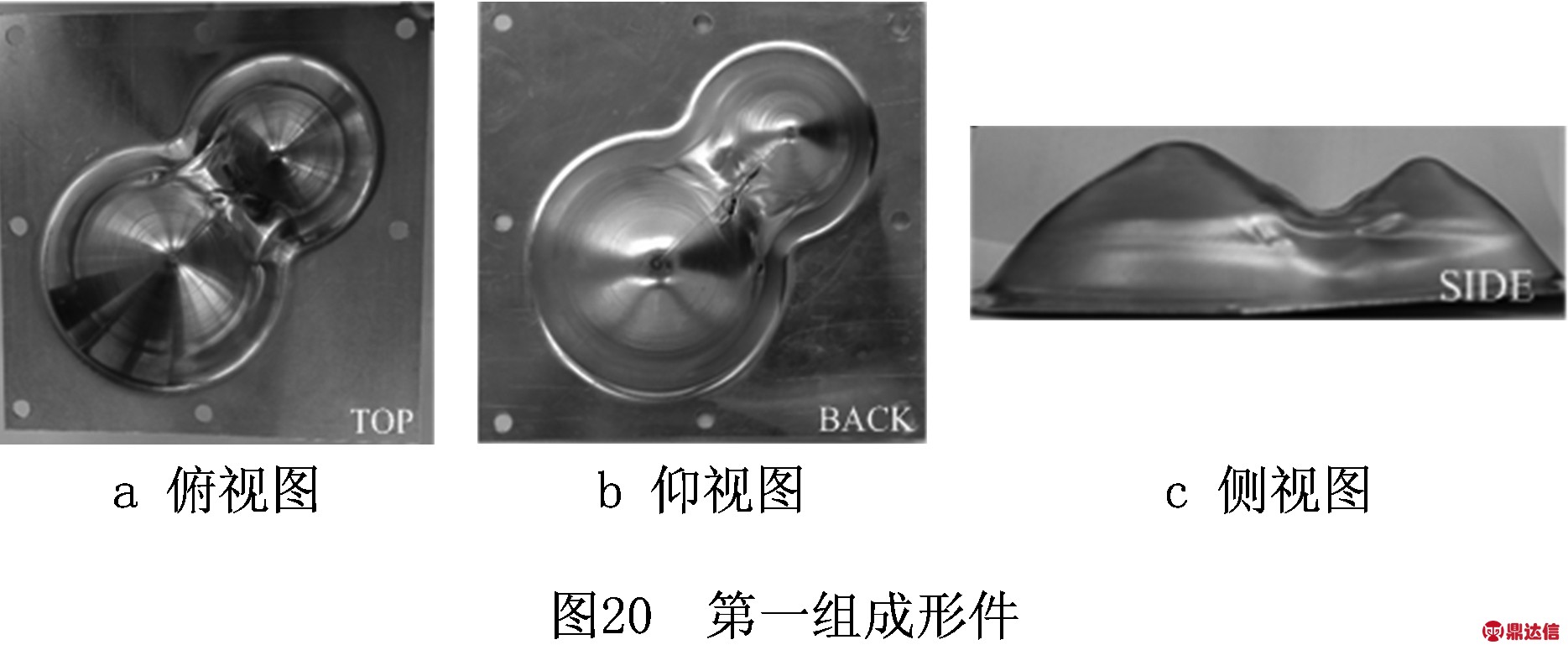
成形件在板材与支撑凹部空间形成密闭的情况下,出现了鼓包和破裂现象,鼓包发生在厚度相对较薄的区域且位于成形区域边缘部位。由于数控渐进成形为自上而下进行且成形区域所在空间体积自上向下减小,除板材件被挤压变形的区域外,板材鼓包现象一开始就在凹部边缘产生,并随着成形过程的进行逐渐增大,这与理论分析相吻合。同时,因板材件成形区域在成形过程中受内部压强增大的影响而产生鼓包变形,使工具头在板材件表面留下明显挤压痕迹。
在第一组实验的基础上,第二组实验在支撑各个凹部最低点(如图21)的位置加工出通气孔的条件下进行,实验过程如图22所示。
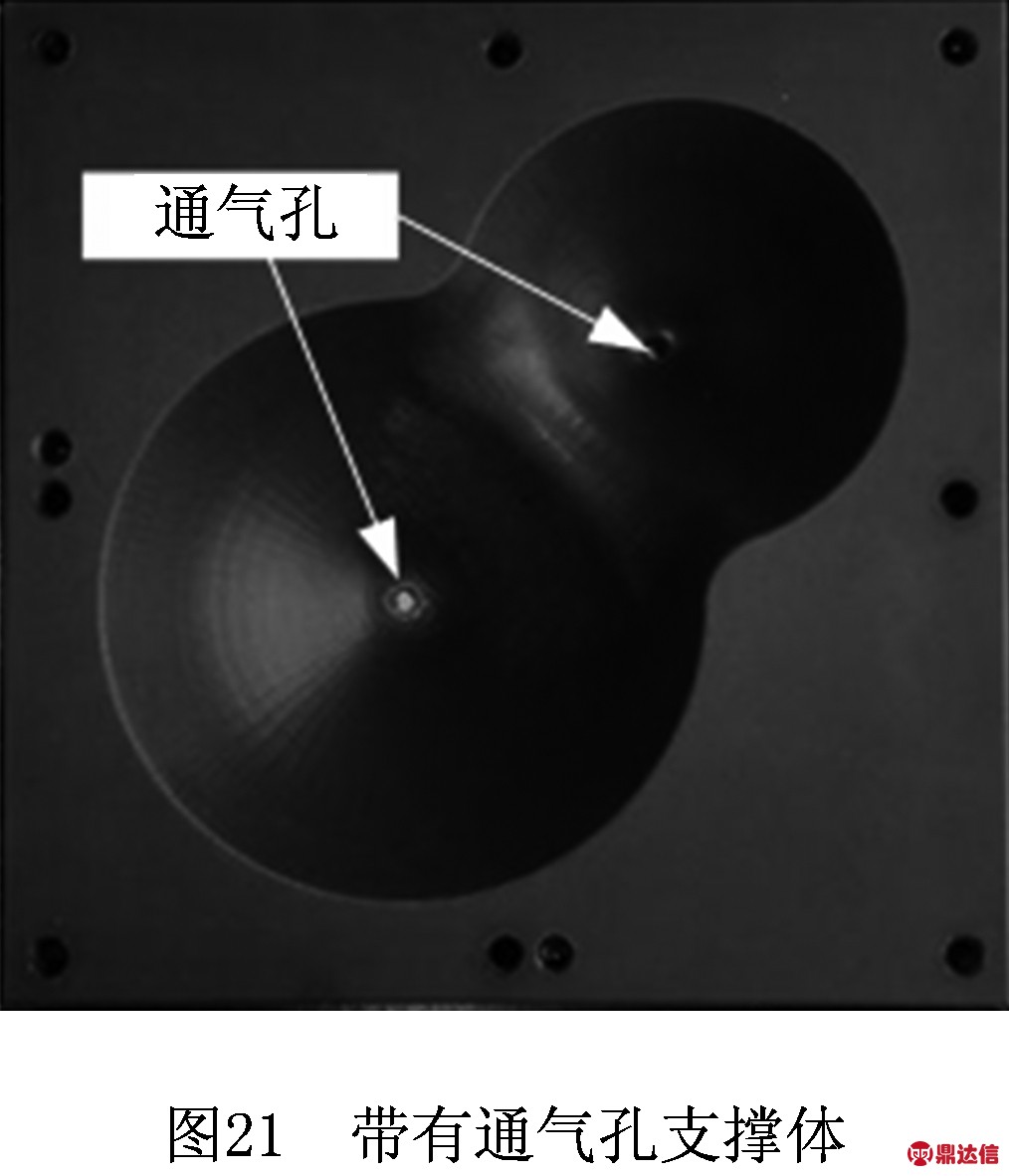
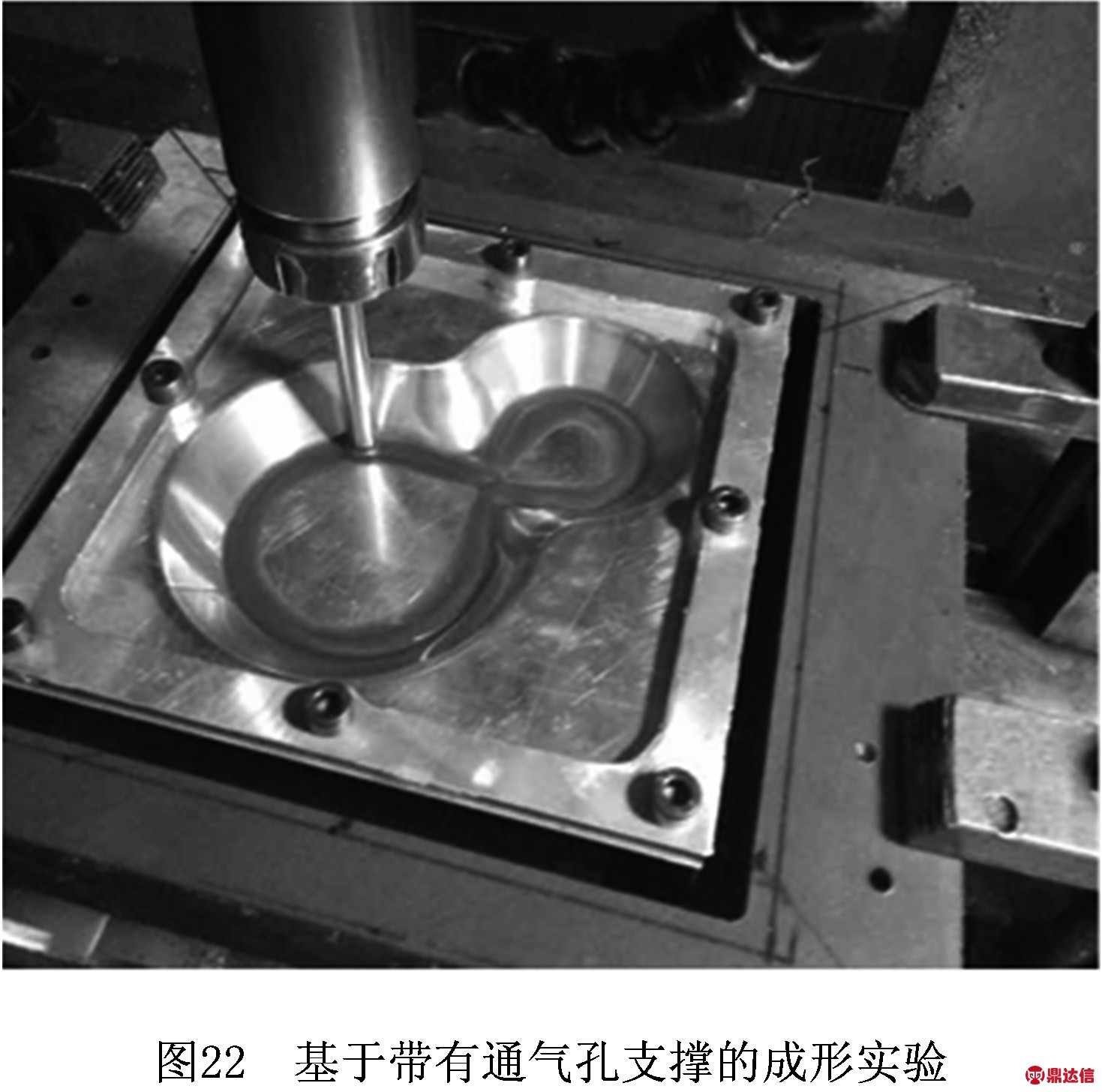
第二组成形实验板材件如图23所示,板材件与工具头接触的表面成形质量较好,未出现鼓包、破裂现象以及挤压痕迹。说明支撑上通气孔的存在,消除了凹部密闭空间的形成,对平衡板材件与支撑凹部空间内外的压强起到了一定的作用。
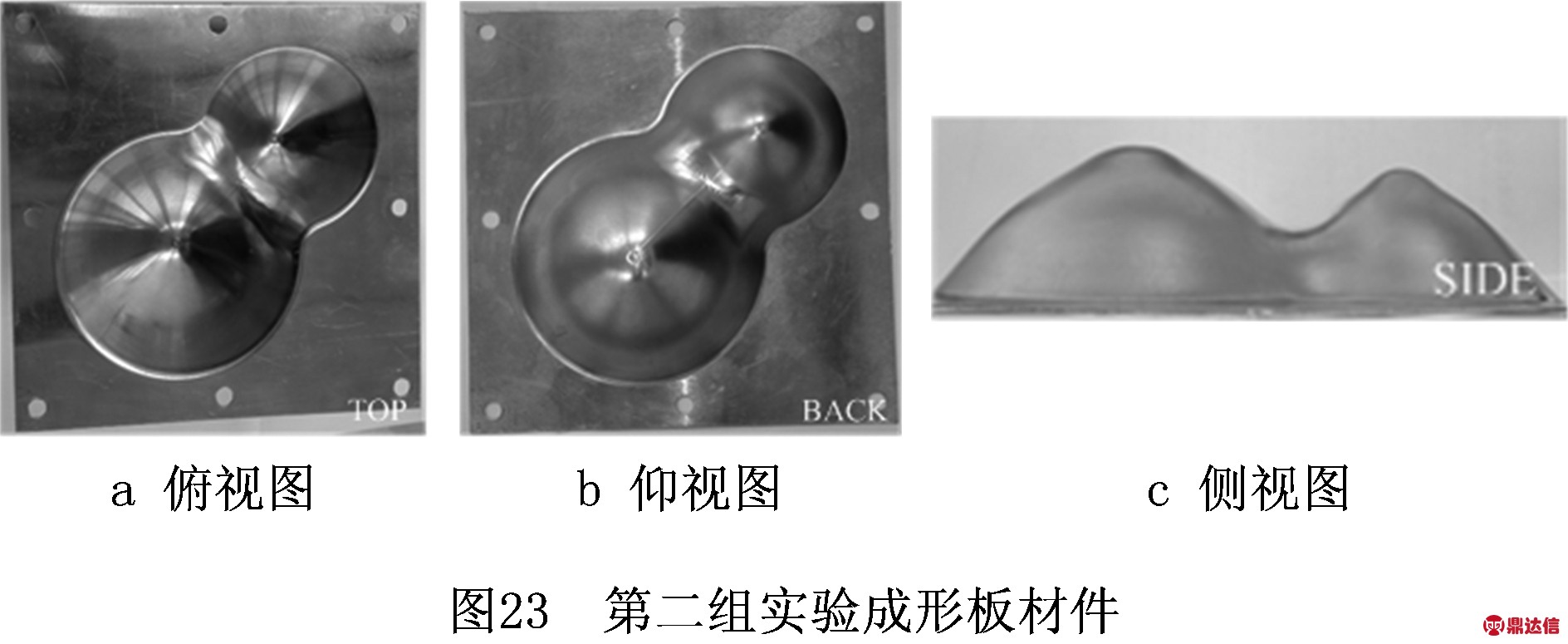
6 结束语
针对渐进成形中密闭空间形成及其应对策略的研究,可得出板材与支撑之间密闭空间的形成会导致待成形板材件产生鼓包、破裂以及表面划痕等问题,影响板材件的成形质量和成形精度。本文提出的算法能够从待成形板材件的CAD模型自动生成出带有通气孔的支撑体。这种带有通气孔的支撑体能够有效地解决由于板材与支撑之间形成密闭空间而引起压强增大,进而影响板材件的成形质量和成形精度的问题。
作为渐进成形支撑体方面的研究,本文研究为消除支撑体在渐进成形中存在的对板材件成形质量的隐患,间接提高板材成形精度提供了一个新的思路,在今后的研究中有必要将这种存在隐患的问题考虑在成形误差之内。