摘 要:为解决满足高强度与轻量化要求的复杂框架类设备支架仿真模型不够精确的难题,通过在有限元分析设计的基础上,利用静力加载试验方法找出结构强度的薄弱环节,再建立结构力学模型进行失效机理分析,提出改进方案. 静力试验结果表明:新的设备支架未发生明显塑性变形,局部设计改进有效,满足了航空极限过载要求;仿真、试验与理论模型相结合的设计方法可实现以较少材料增量的方式提高产品强度,为框架类支架设计改进提供有效的方案.
关键词:机载;设备支架;强度;轻量化;静力试验
在飞机机舱中加改装任务系统,可将设备通过专用支架固定于载机平台上. 该类设备支架通常由航空铝型材组合装配而成,装配时将型材螺母块预先埋入型材槽中,通过型材连接件相互连接固定,型材螺母块通过螺钉将型材连接件与型材可靠连接,具有质量轻、成本低、维护性好等特点[1].
在适航标准中规定,机载设备的极限过载承受能力由重力加速度的相应倍数进行定义,分别为飞机航行方向的前向9.0 g、向下4.5 g、向上2.0 g、侧向1.5 g(其中g为重力加速度,下同)[2]. 机载设备支架可采用有限元仿真方式进行静载与模态分析,从理论上为设备机柜的优化设计提供思路,保证产品结构可靠性[3]. 然而,对于由型材组成的框架类结构,零件与螺接数量较多,准确的有限元模型较难建立且计算量大,仿真模型相对理想,无法充分验证产品结构强度并找到薄弱环节. 在工程实践中,对于复杂的结构问题,常采用理论计算与试验验证相结合的方式,进行结构改进,从而兼顾了仿真分析方法的高效性与试验验证的可靠性[4-5].
因此,本文针对一种机载设备支架的航空力学适应能力,期望在经过仿真分析获得的轻量化结构基础上,通过静力加载试验与力学模型分析相结合的方法,发现结构薄弱环节,进行失效模式分析,探讨失效机理,从而获得支架结构改进思路与方法.
1 有限元分析设计
根据产品功能需求,建立了设备支架的原始三维模型,再根据极限过载要求,对框架结构进行多次迭代分析,去除冗余零件,改善应力集中,保证结构强度,从而获得相对最优的主体结构. 框架整体高度为1 290 mm,长度为460 mm,宽度为331 mm.
以最大极限载荷为例,前向9.0 g过载的分析结果如图1和图2所示,最大位移量为1.38 mm,发生在框架顶板位置;最大应力为255.64 MPa,出现在底板连接件螺钉孔处,底板材料为2A12,屈服强度为280 MPa,最大应力小于屈服强度. 因此,经轻量化改进后,支架结构强度仍可满足极限过载要求.
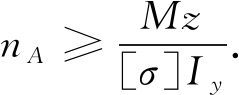
图1 前向9.0g变形云图
Fig.1 Displacement nephogram under 9.0g load along forward direction
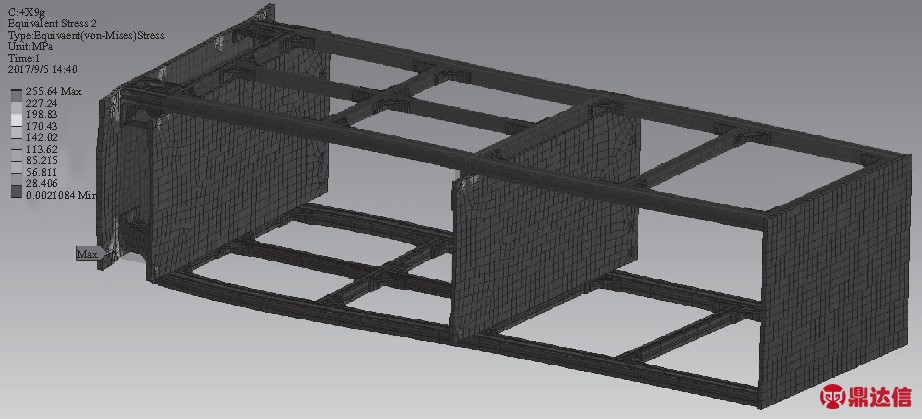
图2 前向9.0g应力云图
Fig.2 Stress nephogram under 9.0g load along forward direction
2 试验分析
2.1 试验方法
以前向9.0 g极限过载承受能力为例,采用静力加载方式对经过仿真分析的设备支架进行试验考核[6],加载点分别位于设备1、设备2和支架质心位置,最大载荷值分别为各设备自重的9倍重力加速度,即Fi=9mig,其中mi(i=1,2,3)分别为设备1、设备2和支架的质量;在设备支架顶部与中部位置各安装有两个位移计,用于监测加载过程中设备支架变形位移量;加载过程采用三级加载方式[7],逐级加载到9倍重力加速度对应载荷,保持载荷3 s后卸载,如表 1所示.
表1 x方向加载表
Tab.1 x-direction static test locations and loads

2.2 试验结果
当外部载荷加载到2级时,在支架支脚处发生失效,导致载荷加载失败,失效现象如下:
① 水平型材槽与内部的螺母块均出现塑性变形,螺母块脱出型材槽,如图3(a)所示;
② 竖直型材与连接件发生滑移,但型材与连接件未发生可见塑性变形,如图3(b)所示.
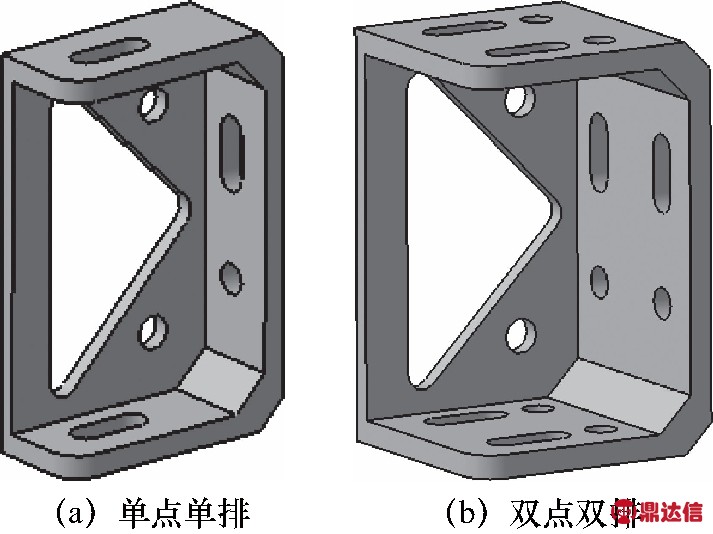
图3 失效位置
Fig.3 The failure location
初步分析可知,随着外载荷增加,失效位置应力增大,超过材料屈服强度,螺母块与水平型材发生塑性变形,型材槽口变大,螺母块脱出;同时,竖直型材与水平型材之间为固定连接关系,当水平型材发生塑性变形后,仅靠竖直型材与连接件间的摩擦力不足以提供竖直方向(z向)的约束力,从而发生滑移现象.
3 结构力学分析
3.1 研究对象
根据失效现象,可选取设备支架、螺母块和型材槽为主要研究对象,建立力学模型,进行整体与局部力学分析,从而获得失效部分的应力情况.
设备支架简化后的结构形式与坐标系如图4所示. 支架底部与机载平台固定连接,在xz平面和yz平面方向中心对称,设备1和设备2固定于支架内部,上下布置. 其中,设备1质量为53 kg,设备2质量为53 kg,支架质量为24 kg. 通过静力加载试验模拟飞机前向(+x向)极限载荷过载工况,在设备1、设备2和支架质心处施加集中载荷Fi=9mig. 铝型材规格为通用2040型材,装配时预先将螺母块埋入型材槽孔内,通过螺栓预紧力,将型材与连接件固定连接.
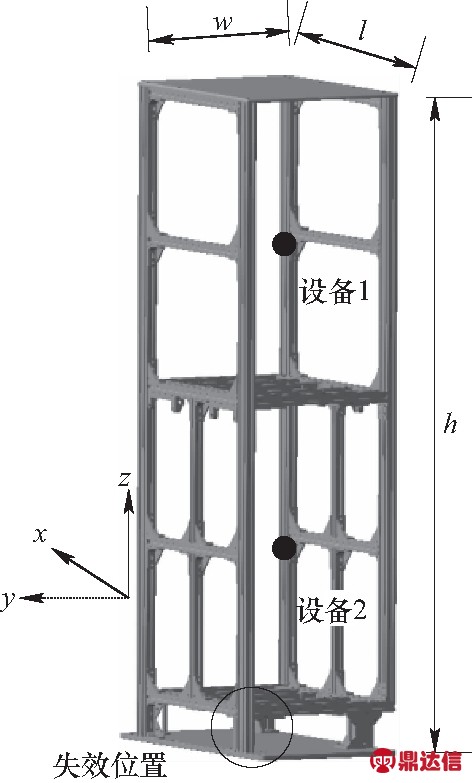
图4 设备支架简图与坐标系
Fig.4 Equipment framework sketch and coordinate system
3.2 力学模型
3.2.1 支架整体分析
支架与设备受到自身重力与外部9.0g静力载荷作用,将失效处简化为固定端,支架结构近似简化为悬臂梁力学模型,如图5所示. 将失效处的水平型材与连接件间等效为固定约束(点A),竖直型材与连接件间等效为滑块约束(点B). 设备1质量m1=53 kg,质心位置为点C,支架质量m3=24 kg,质心位置为点D,设备2质量m2=53 kg,质心位置为点E,对各质心位置进行空间投影,则F1,F2,F3分别为静力加载在设备1、设备2及支架的质心位置处的载荷;G1,G2,G3分别为设备1、设备2及支架自身重力;l1,l2,l3分别为质心位置距点A处的垂直投影距离;lA为点A处作用点距点O处的水平投影距离.
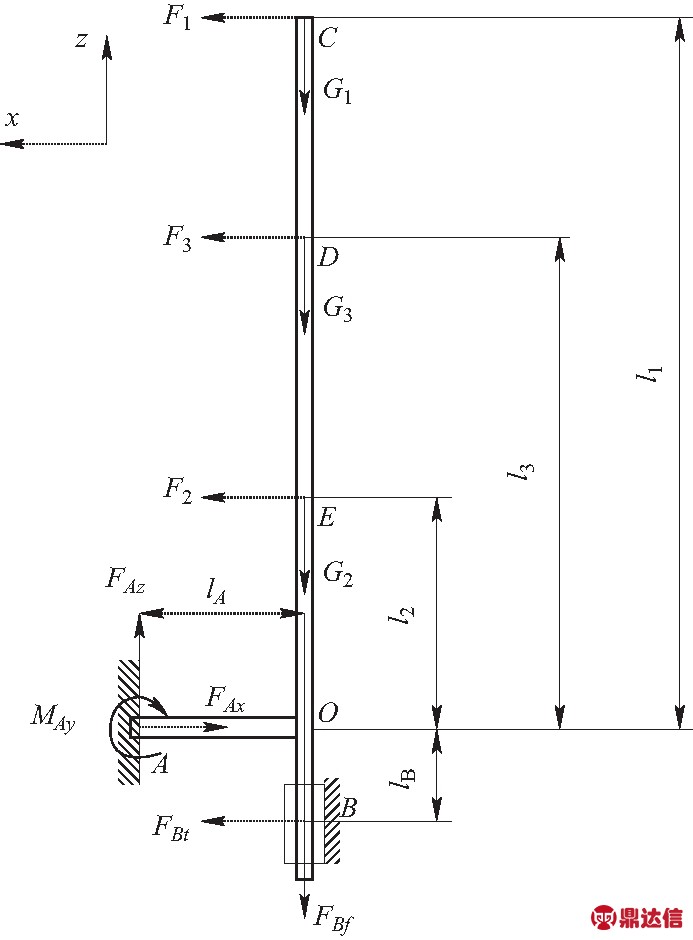
图5 支架受力分析简图
Fig.5 Equipment framework mechanical diagram
3.2.2 挠性变形分析
由上图可知,该结构为简单超静定梁形式,可采用叠加法建立变形协调方程为
ωO=(ωO)Fn+(ωO)Gn+(ωO)FB,
(1)
式中:ωO为点O处的挠度;(ωO)Fn为外载作用下O处的挠度,为重力作用下O处的挠度,
为点B处作用力作用下点O处的挠度,
为外载载荷;Gn为设备及支架自身重力;FBf为点B处型材与连接件间摩擦力;FBt为点B处型材与连接件间拉力;E为铝型材弹性模量;I为铝型材截面惯性矩.
由式(1)得
ωO=(ωO)Fn+(ωO)Gn+(ωO)FB=

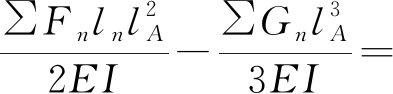
1.8×10-7,mm.
因此,当点A处假设为固支端时,铝型材的挠性变形量<1.8×10-7 mm,表明水平型材自身形变极小,竖直型材滑移失效不是由于水平型材挠性变形引起. 且相对于螺母块,水平型材可等效为刚性体.
3.2.3 点A处受力分析
根据图5受力分析简图,对点A处建立平面力系方程如下:
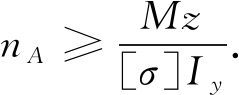
(2)
式中:MAy为点A处弯矩;FAz为点A处螺母块支撑力;k为摩擦面数量;nB为点B处连接点个数;F′为单个螺栓的预紧力;ln为外载荷作用点距点O处的垂直投影距离.
由式(2)易知,FAz>0,引起螺母块失效的有害力为弯矩MAy,为纯弯曲力学模型,则
3)
式中:FBf与螺栓预紧力F′相关,螺母块连接螺栓为是M5,材料为不锈钢,截面约为AS=14.18 mm2,屈服强度σS=480 MPa,摩擦面数量为2,摩擦因数取0.35,可得F′=(0.5~0.6)σSAS≈4 000 N. 当失效状态时,点B处连接螺栓个数nB=4,FBf=nBkF′f=11 200 N,对式(3)求解,可得
MAy=1 552 N·m.
3.3 强度校核
型材材料为6063-T5铝合金,屈服强度127 MPa,弹性模量68.6 GPa,螺母块材料为碳钢,屈服强度为235 MPa,弹性模量为200 MPa. . 螺母块螺纹孔截面惯性矩Iy=3.907 mm4,距形心最大距离z1=1.9 mm.
对螺母块分析校核,在静力加载过程中,水平型材槽内螺母块主要受螺栓拉力FT,型材槽对其支撑力FN,以及弯矩M,如图6所示,由于螺纹孔yz中轴面处截面尺寸最小,应力最大,对形心主轴的弯曲应力为
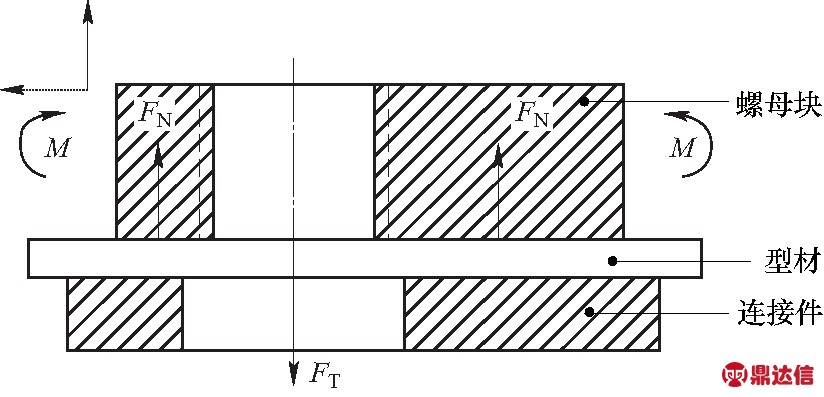
图6 螺母块受力分析图
Fig.6 Nut block stress diagram
(4)
式中:M为螺母块所受弯矩;z为截面距形心主轴最大距离;Iy为螺纹孔截面的惯性矩;nA为螺母块数量,即水平型材中连接点个数.
当连接点个数nA=1时,由式(4)可得截面处的最大弯曲拉应力为754.7 MPa,大于螺母块材料的屈服强度420 MPa. 因此,螺母块螺纹孔yz截面的最大拉应力超过材料抗拉强度,强度不足,从而发生塑性弯曲变形失效.
对型材槽分析可知,随着静载增大,螺母块弯曲变形不断发展,型材右侧开始与连接件分离,螺母块与水平型材接触面积减小,接触面法向局部应力急剧增大,超过了铝型材屈服强度,型材槽发生塑性变形,从而螺母块脱出.
4 改进与试验验证
4.1 连接件改进
由式(4)可知,螺母块所受最大拉应力与截面参数和连接点个数有关,连接点个数增加平均拉应力减小. 同时,由式(1)可知,增加连接点个数,螺母块所受弯矩MAy减小. 由于螺母块选用的为标准件,更改其尺寸或材料代价较高,而改变连接点个数,仅需更改连接件结构,即可有效降低平均应力,提高失效位置的连接强度.
根据民航飞机适航标准中极限过载设计要求[2],取安全系数为1.5,由σmax≤[σ]=420 MPa/1.5=280 MPa,可得
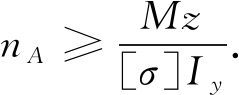
(5)
连接件与水平型材连接点个数nA≥2.7,可取nA=4. 因此,对连接件进行结构改进,由单点单排结构(图7(a))改为双点双排结构(图7(b)),连接件与水平型材连接点个数增加为4个,与竖直型材连接点个数增加为6个(含原有侧边2个).
此时,nA=4,nB=6,带入式(2)和式(4)计算得MAy=1532 N·m,则

因此,改进后的新型连接件与水平型材的连接数增加为4个,平均应力满足许用应力,理论上可满足强度要求.
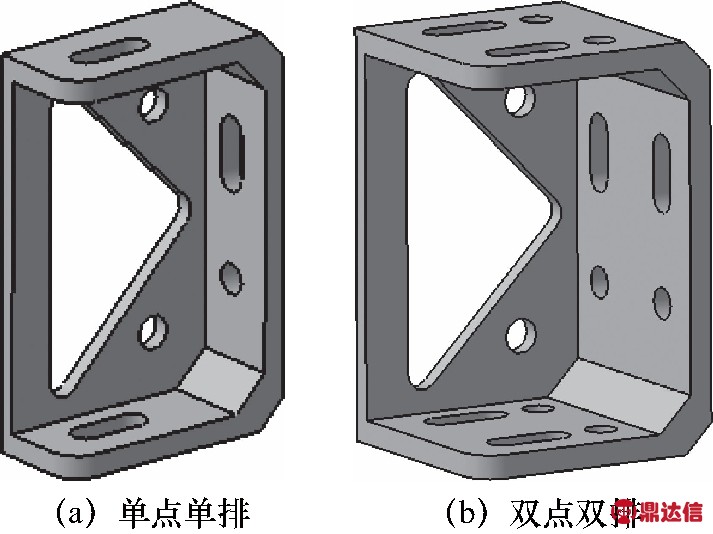
图7 新型连接件
Fig.7 New union piece
4.2 试验验证
对于改进后的设备支架重新进行静力加载试验,试验条件同2.1节,试验前后记录4个位移计的数值,绘制过程曲线如图8所示. 分析曲线可知,分级加载阶段,从0级加载到3级过程中,对曲线进行线性拟合,4个位移监测点的拟合系数均大于0.99,曲线线性度均较好,表明加载过程中设备支架主要发生弹性变形,未产生明显塑性破坏. 卸载极限载荷后4个位移监测点的位移基本回0,回0后的位移值均要小于0.85 mm,表明支架在加载过程中后未发生可见明显变形,内部结构件之间也未发生滑移. 因此,采用新型连接件后,设备支架可以满足前向9.0 g静力过载条件要求.
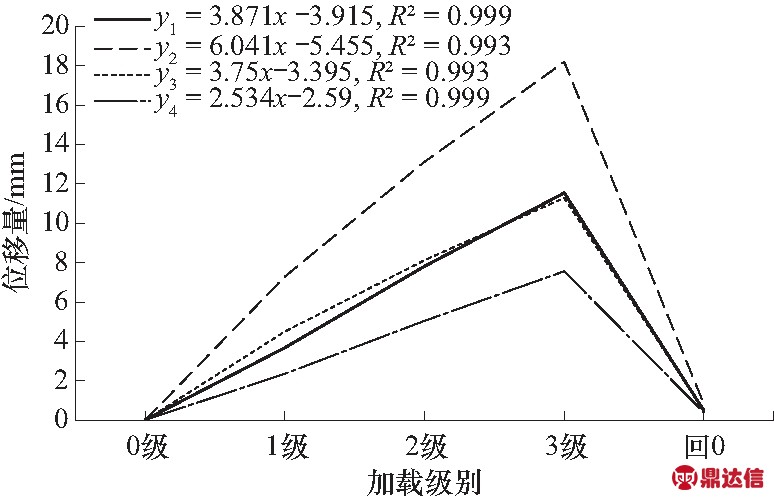
图8 x方向位移测量值
Fig.8 x-direction displacement curve
5 结 论
设备支架在静力加载过程中失效的主要原因为型材连接点数量不足,导致螺母块局部弯曲拉应力超过材料抗拉强度,发生塑性变形,从而引起支脚连接处结构破坏,载荷加载失败. 由于仿真分析模型在前期设计中进行了简化,相对较为理想,未能发现局部强度的不足. 建立的悬臂梁力学模型,获得了支架静力加载下的失效模式,可以为设备支架在机载条件下的受力特征分析以及相关结构设计提供参考依据. 框架类产品在有限元仿真分析的基础上进行试验分析,仅针对结构薄弱环节开展研究,以最少材料增量方式进行强度改进,保证了产品的轻量化与高强度要求.