摘要:以J公司多晶硅电池片生产线为原型,以Flexsim仿真软件和Pro/E建模软件为基本工具,对多晶硅电池片生产线中的设备和电池片进行建模和仿真分析。将该仿真系统应用于实际教学中,结果表明,该系统对教学具有一定的辅助作用,可以实现设备性能、电池片变化分析,还可以在Flexsim平台上进行系统优化。
关键词:太阳能;电池片;多晶硅;流水生产线;Flexsim
在太阳能电池片生产企业中,企业的核心生产流程主要包括9个工序,即初级筛选-清洗制绒-扩散-去PSG-PECVD-丝网印刷-烧结-激光刻蚀-分选测试[1],任何一个工序出错都会造成不必要的浪费。因此,如何合理地安排各个工序中生产设备的加工任务,使得各工序的加工任务量适中,并且尽量减少制品积压,是太阳能电池片生产企业亟待解决的问题。生产线仿真是以计算机支持的仿真技术为前提,对生产线的各个元素和生产过程建模。在虚拟的环境中反映出生产制造全过程,从而更有效地组织生产计划使企业获得更大利润。Flexsim是美国Flexsim Software Production公司出品的一款商业化离散系统仿真软件,采用面向对象技术,并具有三维显示功能,建模快捷简单,仿真分析能力强大。因此,提出使用Flexsim仿真软件和Pro/E建模软件,对J公司生产现场的太阳能电池片生产流水线进行仿真,建立多晶硅电池片生产仿真系统,以便提高6S管理水平。
1 多晶硅电池片生产仿真系统
1.1 模型的建立
依据J公司多晶硅电池片生产线上各个环节的仪器和功能,利用Pro/E建立仪器模型,针对电池片经过不同工艺后的变化进行外观仿真。将建立好的模型图保存为后缀名为wrl格式,通过Deep Exploration模型转换大师软件将其转换成3ds格式 (3ds格式容量最小且可以成功导入Flexsim软件中)。
1.1.1 初级筛选
图1为初级筛选的设备及硅片模型。
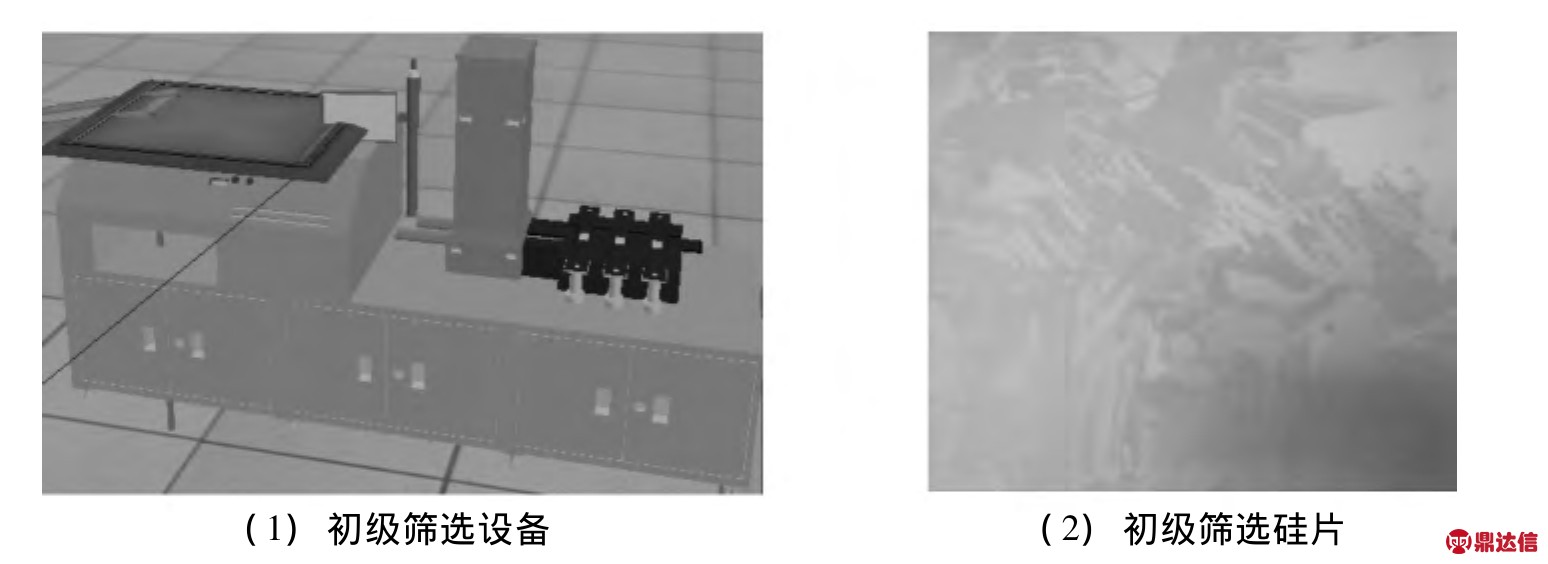
图1 初级筛选设备及硅片模型图
电池片生产中常常因为外购硅片的质量问题造成生产中不必要的耗材浪费,因此本工艺通过红外线照相机检验硅片的表面平整度、是否有微裂纹、表面油污等,然后根据检验结果进行分类。出现破片、裂纹、缺角、缺口、崩边、翘曲等问题的硅片将送回硅片厂进行重新加工,出现轻微线痕、脏污、性能不良等问题的硅片将进行反面二次筛选。图1(1)是设备模型,将不同硅片测试分类后流入图中的储物盒。图1(2)是初级筛选后的外观合格硅片,如该硅片的少子寿命、体电阻数值在允许范围内,则该硅片将从末端的储物盒继续流向下一生产环节。本仿真系统还设计了多片不合格的硅片模型进行筛选,用不同深浅的黑点和不同粗细的横线表示油污、线痕和裂纹。
1.1.2 清洗制绒
图2(1)是制绒设备模型图,图2(2)为制绒硅片模型图。
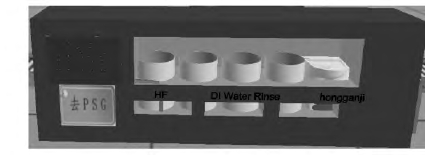
图2 制绒设备及硅片模型图
利用酸溶液对多晶硅不同晶体取向上具有不同腐蚀速率的腐蚀特性,在硅片表面形成起伏不平的绒面,增加太阳光在电池片表面的吸收次数以提高吸收率,这种绒面变化是微米级别的。为了表现绒面的细微变化,制绒硅片模型中用虚线斜框表示绒面。而实际生产中仅仅使用酸溶液是不够的,还需要去离子水漂洗电池片,需要KOH将多孔硅面上的小孔腐蚀,使其成为较平滑的凹面、需要HF和HCl的混合液去除其余金属杂质[2]。
1.1.3 扩散
图3(1)为扩散炉模型图,图3(2)是扩散后的硅片侧面指示图。
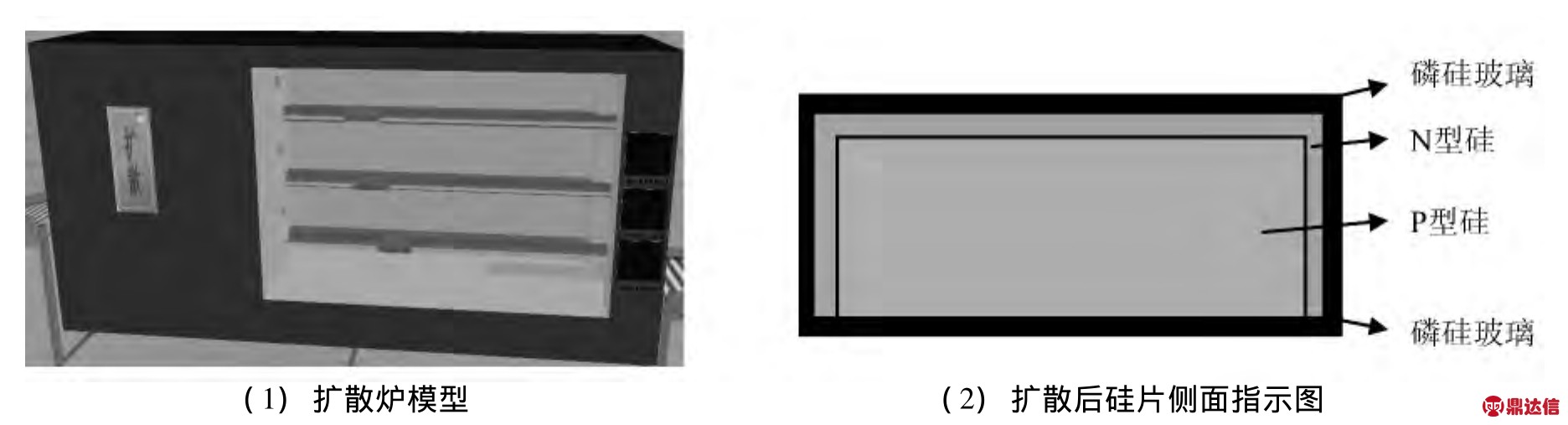
图3 扩散硅片及设备模型图
硅片是P型晶体硅,置入扩散炉里的石英管中,利用三氯氧磷液态源扩散法在硅片上扩散磷离子,使其形成PN结。它是电池片发电的重点部分。扩散前的硅片是P型硅,扩散后在硅片表面形成N型硅,还产生成一层含有磷元素的SiO2,称之为磷硅玻璃 (PSG)。磷硅玻璃和电池片侧面的N型硅均需在后面的工艺中去除。
1.1.4 去PSG(磷硅玻璃)
图4为去PSG模型图。
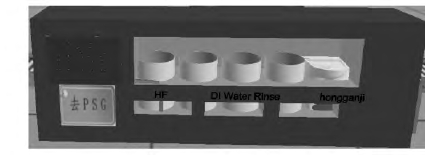
图4 去PSG模型
扩散时产生的磷硅玻璃会阻止光吸收,同时又是绝缘的。工艺上采用HF酸腐蚀,也需要其他溶液的辅助。此环节也是需要多个容器,除了HF酸,还需要去离子水对电池片进行漂洗。扩散和去PSG时硅片的变化属于微观变化,该环节流通的电池片依然采用制绒硅片模型,只是在仿真系统的设备模型边上放置图3(2)。
1.1.5 PECVD(等离子增强化学气相沉积)
图5(1)为PECVD后硅片,图5(2)为管式PECVD设备模型。
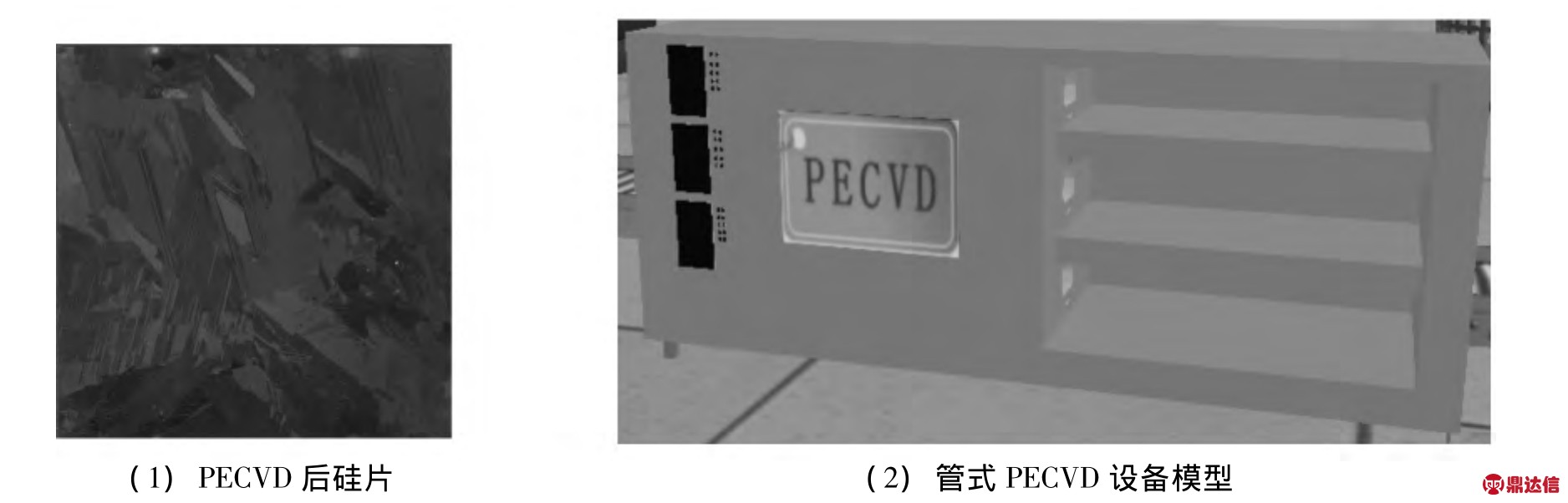
图5 P ECVD硅片及设备模型图
光在硅表面的反射损失率高达35%左右。为减少硅表面对光的反射,采用PECVD方法,在硅片上沉积出深蓝色的氮化硅减反射薄膜,如图5(1)所示。利用薄膜干涉原理[3],可以使光的反射大大减少,电池的输出电流就有很大增加,效率得到相应提高。
1.1.6 丝网印刷
图6为丝网印刷设备及电池片模型图,其中图6(2)为印刷背面电极 (银铝浆),图6(3)印刷背面电场 (铝浆),图6(4)为印刷正面电极 (银浆)。
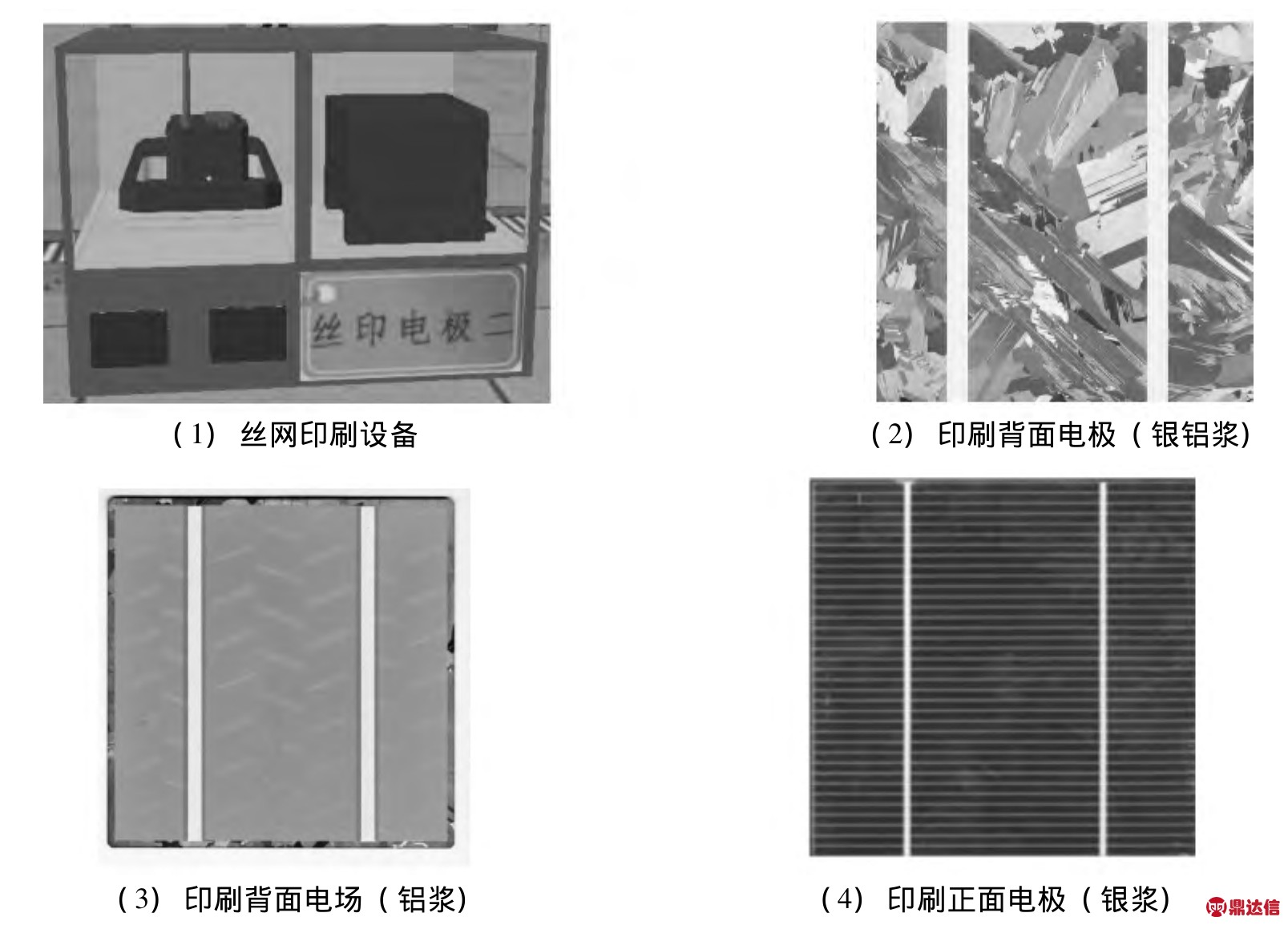
图6 丝网印刷设备及电池片模型图
采用图6(1)所示设备,利用刮刀、钢网把浆料印刷在电池片的正负电极,将电池片产生的电流导出,该环节分背面电极、背电场和正面电极3个步骤,三者不同的是浆料的成分和钢网的尺寸,3个步骤生产后的电池片模型分别用图6(2)、(3)和 (4)表示,涂上的浆料分别是银铝浆、铝浆和银浆。电池片尺寸和电极尺寸严格按照156电池片要求。
1.1.7 烧结
图7是烧结设备的模型。
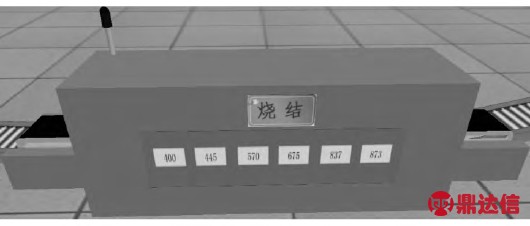
图7 烧结设备模型
经过丝网印刷后的电池片不能直接使用,需经烧结炉快速烧结,将有机树脂粘合剂燃烧掉,剩下几乎纯粹的、由于玻璃质作用而密合在电池片上的银电极,使浆料和硅片形成良好的欧姆接触。模型中显示了炉内不同位置的温度。
1.1.8 激光刻蚀
图8是激光刻蚀的设备模型。
激光刻蚀设备最重要的组成就是中间部分的激光器,采用波长为355 nm的脉冲紫外激光作为激光光源。扩散工艺中电池片的正面和侧面都成为N型半导体,造成上下短路,几乎没有输出电压。利用高能量聚焦激光束沿着烧结后电池片正面近侧端周边照射一圈,使被照区域熔化、气化,在电池片正面近侧端周边刻蚀出一定深度的凹槽,从而实现将电池片上下电极分开。
1.1.9 分选测试
图9是分选测试模型。
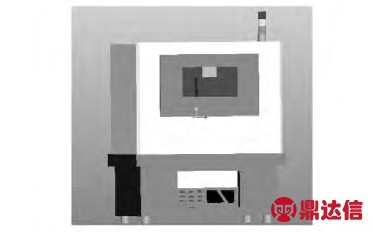
图8 激光刻蚀设备模型
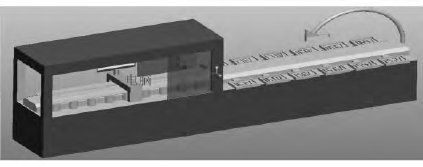
图9 分选测试模型
分选测试分为2步,先在暗箱里以氙灯作为照明光源模拟国际检测标准在暗室里检测电池片,获得电池片的开路电压、短路电流、最大功率点、转换效率、填充因子等相关参数,显示在电脑上,然后再根据电池的转换效率对电池片进行分类。模型中特别标明氙灯和效率分选盒。分选后的电池片还将经过人工外观检验后包装入库。
1.2 系统建立和仿真
以图1~9的模型为基础,在Flexsim导入相关设备和硅片的3ds模型,模型中各个实体所涉及的时间参数尽量依据实际生产监测数据进行设置。此外,为了让系统更接近实际生产线,搭建厂房布局,添置厂房内相关挂图、运输工具等。编译模型并运行此模型,用Flexsim自带的avi制作器记录一片硅片经过每个生产工艺到最终的电池片生产的整条3D动画流程。
2 仿真系统在教学中的应用
以J公司的多晶硅电池片生产线为原型,探究每个环节相关设备的特征和作用,应用Pro/E建模和Flexsim仿真软件完成了多晶硅电池片生产系统的仿真系统的建立和分析,并将该系统应用于实际教学中,应用效果显著。(1)通过仿真系统的介绍可以获知各个设备的重要组成部分及功能,加深对太阳能电池片生产过程的认识,更好的学习整套生产工艺。(2)从硅片到电池片的整个生产工艺就是为了提高电池片对太阳能的吸收率,降低其反射率,通过该系统,硅片在经过每个环节后的微观变化一目了然。进而引导学生采用其他生产工艺继续改进电池片的光电转换效率。(3)系统中各个实体所涉及的时间参数设置是以实际生产监测数据为基础,因此学生可以在Flexsim平台上得到系统参数如零件的通过时间、机器的利用率、生产率、等待零件数目等,进而提出提高生产线效率的优化方案,达到改进系统设计的目的。