摘 要:文章分析锂离子电池轧制过程中影响极片压实密度均匀性的因素,对极片轧制设备影响电池极片横向厚度不均匀性和纵向不均匀性的具体因素进行重点研究。通过对轧辊进行受力分析,得出横向厚度均匀性与轧辊挠度变形的关系;通过仿真分析了辊径、轧制力以及极片宽度等因素对轧辊变形的影响;通过试验探究了轧制力、极片宽度对极片厚度一致性的影响规律。研究结果表明,轧制力、极片宽度对轧制后的极片厚度一致性有非常重要的影响。
关键词:轧辊变形;电池极片;厚度一致性;轧制力
动力型锂离子电池需成组后才能作为动力源,而电池成组后,单体电池间性能的不一致成为电池组使用性能差、循环寿命短及安全性低等问题的主要原因,电池不一致性问题成为制约我国动力电池发展的关键。评价电池极片一致性的性能指标主要为极片厚度的均匀性。极片厚度的均匀性又可分为横向厚度均匀性和纵向厚度均匀性,2种厚度均匀性较差的原因存在差别。产生极片横向厚度差的主要原因为轧辊弯曲变形、机座变形、主要受力件的弹性变形等;极片纵向厚度差将会是周期性存在,其主要原因为轧辊、轴承、轴承座等的加工精度以及安装精度误差[1-5]。
极片的横向厚度差主要由轧辊的挠度变形引起,因而分析轧辊的变形是分析极片一致性影响因素的关键[6]。轧辊辊身的变形与其自身的结构和所受的力有关,因此,研究轧辊的辊径、轧制力的大小以及极片的宽度等因素对辊身的变形非常必要。
1 轧辊刚度变形计算
轧辊可理解为阶梯轴,截面变化明显,计算其变形比较复杂,本文利用多个参考系梁的挠度和转角的合成关系,分析轧辊在受力状态下的变形情况,然后再采用数值模拟的方法,建立参数模型对轧制过程中承受轧制力的轧辊进行静态模拟仿真,得到不同工况下轧辊的变形分布,这样既可较真实地反映轧辊受力情况,又可方便地得到不同条件下轧辊的轧制规律。
轧辊受力模型如图1所示。图1中,取3个截面,即截面1、截面2、截面3,其对应长度分别为L1、L2、L3,各段的抗弯刚度分别为EI1、EI2、EI3,支座A的反力为RA和截面B的剪力为QB。
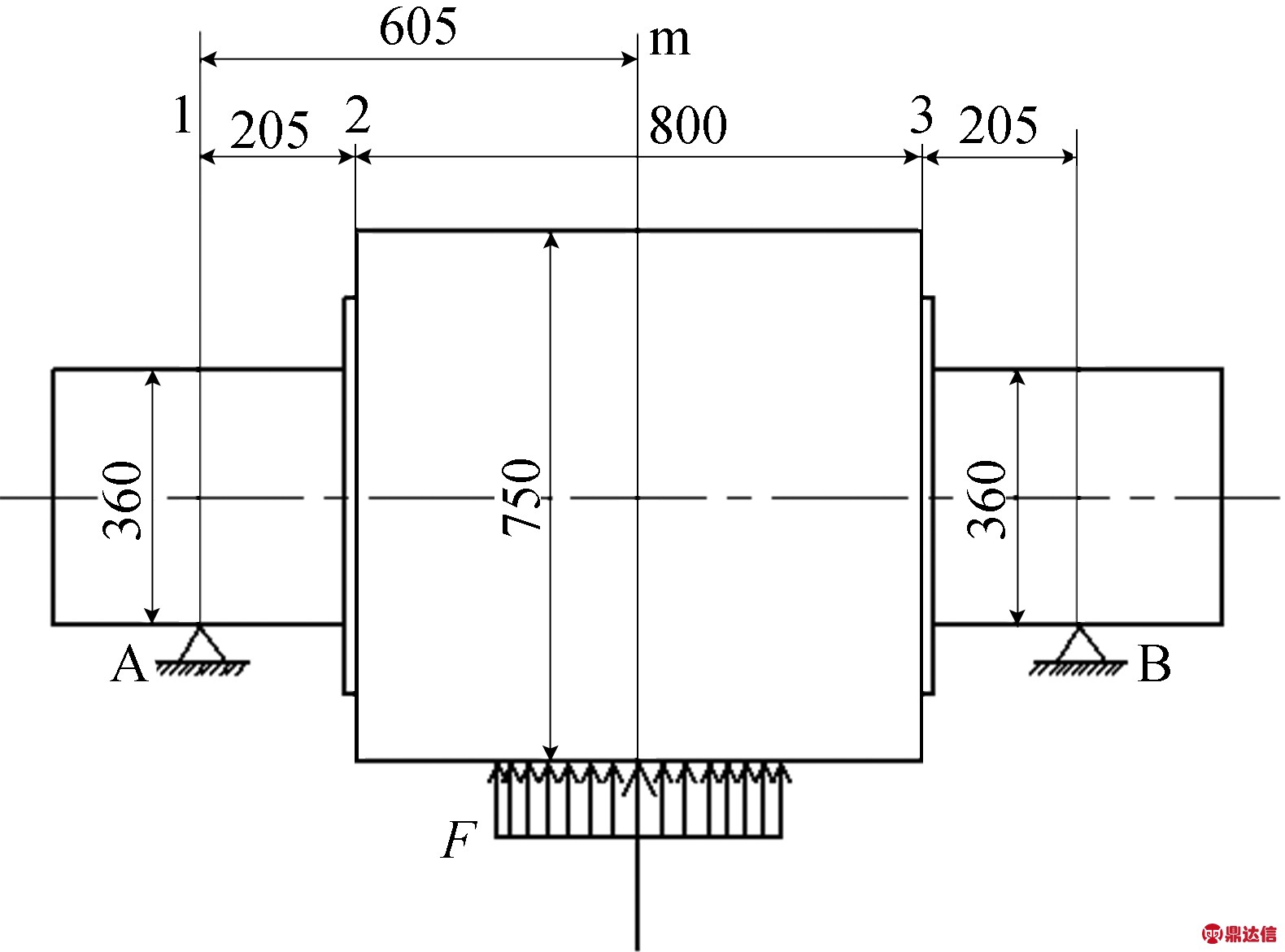
图1 轧辊受力模型
计算由QB、F所引起截面B相对于梁截面1固连的动系1的相对挠度计算公式如下:
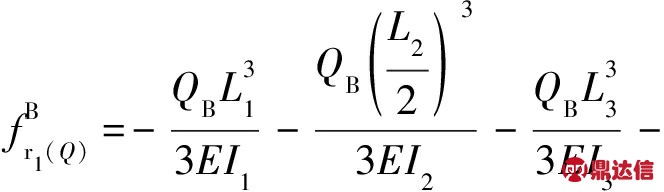
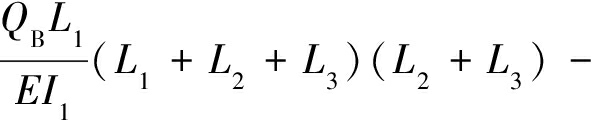
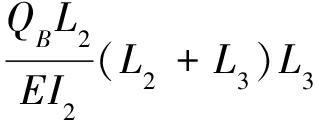
(1)
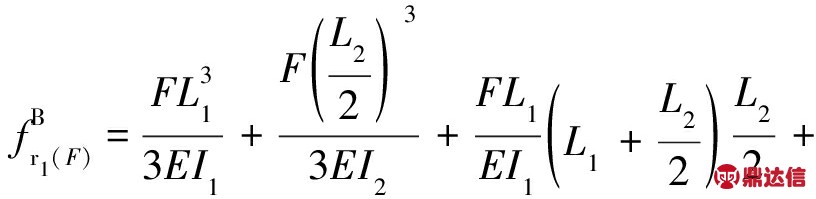
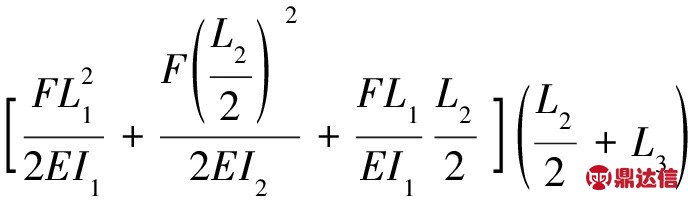
(2)
因此,截面B相对于动系1总的相对挠度为:
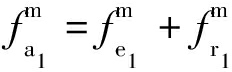
截面B在支座B处,因此其绝对挠度=0。若以支座B为静参考系,则截面B的绝对挠度
等于动系1对截面的牵连挠度
和截面B相对于动系1的相对挠度
之和,即
而牵连挠度
=θA(L1+L2+L3),则可求得转角θA。取截面m,即轧辊最大变形处,求出截面m上的剪力Qm和弯矩Mm,再计算截面m相对于梁截面1固连的动系1的相对挠度
公式为:
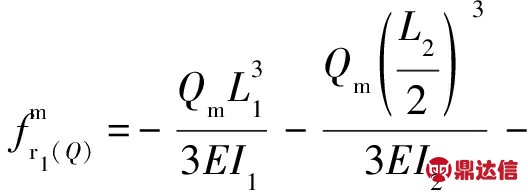
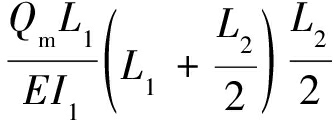
(3)
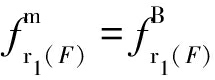
(4)
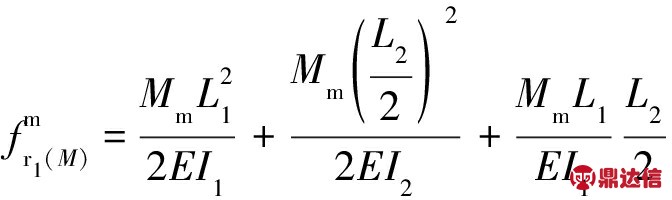
(5)
则有:

(6)
而动系1对截面m的牵连挠度为:
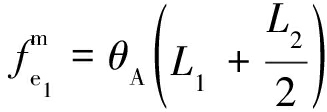
(7)
则截面m的变形量为:
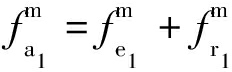
(8)
取轧制力为最大时,即轧制力为2 000 kN,将数据代入(1)~(8)式,可得轧辊轧制区最大变形量约为57.264 μm。
2 建立轧辊有限元模型
在ANSYS Workbench中建立轧辊的实体模型,实际工作过程中是2个辊对极片进行轧制,为了简化模型,在受力分析时只对其中1个辊进行分析。对实体模型进行简化处理,去除尺寸较小的圆孔、凹槽、圆角等细小结构,以便于网格划分和节省求解时间。
对轧辊的材料属性进行设置,弹性模量设为236 GPa,泊松比为0.3,密度为7 810 kg/m3,强度极限为620 MPa。
2.1 划分轧辊有限元网格
采用网格划分工具mesh对轧辊进行网格划分,设定网格尺寸为15 mm,以辊径800 mm的轧辊为例,模型划分完成后其节点数为966 631,单元数为275 381。
2.2 确定轧辊边界条件
有限元模型的边界条件主要指施加在模型上的约束和载荷,确定模型的约束边界是有限元分析的基础[7]。本文对轧辊进行不同工况下的静态仿真分析,在轧辊轴承部分进行圆柱约束(cylindrical support),将轴向(axial)、切线方向(tangential)及径向(radial)设定为固定(fixed),用压力(pressure)代替极片反作用在轧辊上的轧制力,并垂直于辊面均匀施加在轧辊与极片接触区域的辊身表面上。分析时施加具体的约束条件和载荷。
3 极片一致性能的主要影响因素
3.1 轧制力对极片一致性能的影响
以辊径为800 mm的轧辊作为分析对象,该
轧辊模型的主要参数见表1所列。
通过改变轧制力大小,得到轧辊变形的规律。设定6种轧制力(F)的工况,分别为:工况1(F=500 kN)、工况2(F=1 000 kN)、工况3(F=1 500 kN)、工况4(F=2 000 kN)、工况5(F=2 500 kN)、工况6(F=3 000 kN)。得到的轧辊变形云图如图2所示。
表1 轧辊模型主要参数
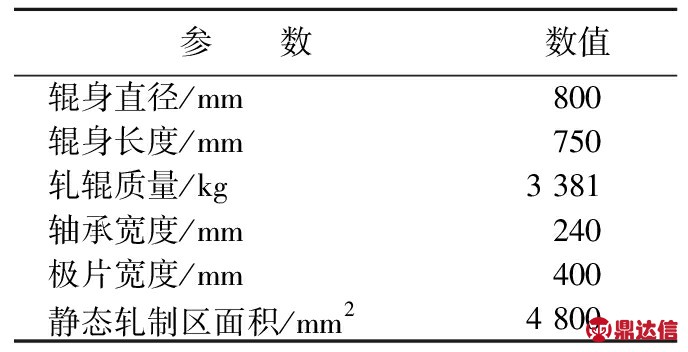
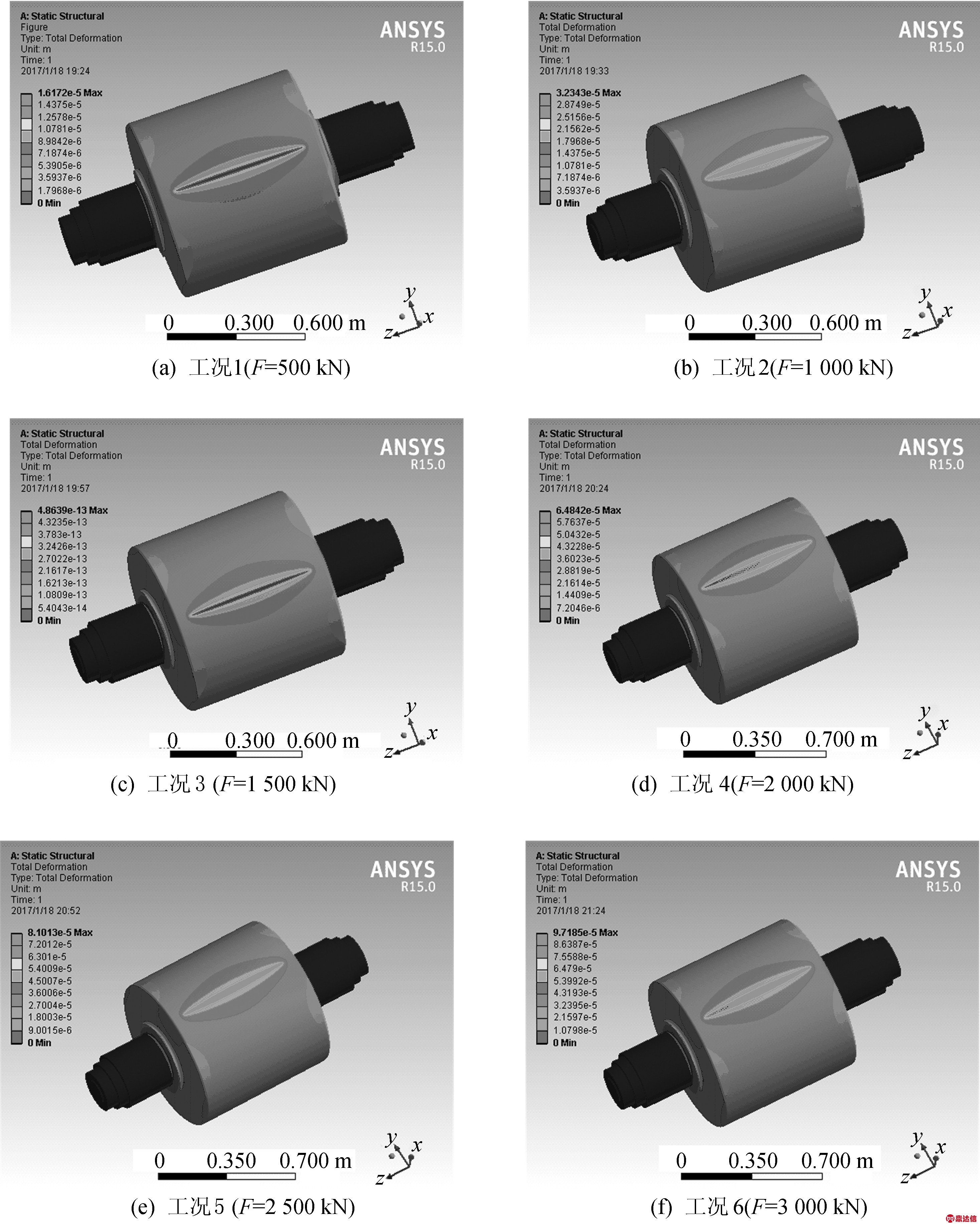
图2 6种轧制力工况下的轧辊变形云图
极片边缘应力集中,导致其变形比极片中部变形大很多,在实际生产时会将极片2个边缘一定宽度范围的厚度误差忽略不计。6种工况下的轧辊最大变形和极片截面厚度差值,见表2所列。表2中,F为轧制力,N为辊身最大变形,T为极片截面厚度差。
表2 6种轧制力工况下辊身最大变形和极片截面厚度差

在6种工况下,取辊身变形区沿轴线方向的若干点,两端的点取向内移3 mm取得,作出6种工况下辊身总变形曲线,如图3所示。
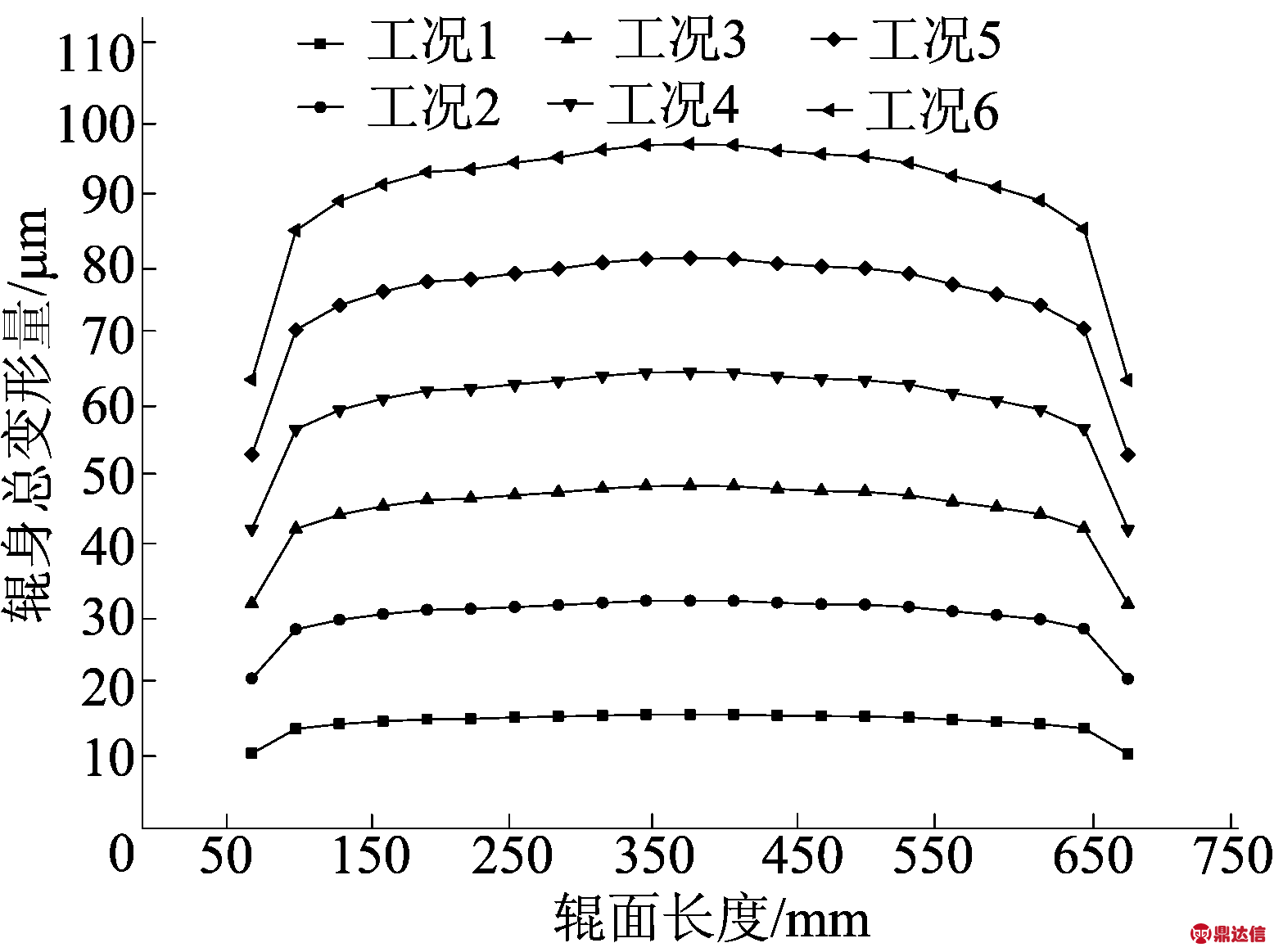
图3 6种轧制力工况下轧辊辊身总变形曲线
从表2、图3可以看出,在相同辊身直径和极片宽度条件下,轧辊辊身的总变形随着轧制力的增大而增大,工况6时轧辊总变形为97.185 μm,比工况1时的轧辊总变形(16.172 μm)增大了81.013 μm;轧制区域辊身总变形量的差值也增大,工况6时轧制区域辊身总变形量的最大差值为33.503 μm,工况1时轧制区域辊身总变形量的最大差值为5.591 μm,由于轧辊两端轴颈承受轧制力增大,引起轧辊挠度变形增大,最终导致极片截面厚度差也随之增大。
3.2 极片宽度对极片一致性能的影响
极片宽度是根据电池设计尺寸与生产工艺要求而确定的,一般常用的分条之前的极片宽度在200~700 mm之间。为了更加明显地显示极片接触区域的变形,采用单因素法,即保持轧辊施加轧制力2 000 kN不变,只改变极片宽度(L),分为工况1(L=200 mm)、工况2(L=300 mm)、工况3(L=400 mm)、工况4(L=500 mm)、工况5(L=600 mm)、工况6(L=700 mm)。6种工况下静态轧制区面积见表3所列。表3中,L为极片宽度;S为静态轧制面积。
极片宽度不同在进行网格划分时需要的印记大小也会相应改变,采用六面体网格划分方法,网格大小为15 mm,得到网格均匀的模型,对模型进行圆柱约束并施加载荷,分析得到轧辊的变形情况,如图4所示。
表3 6种极片宽度工况下轧辊静态轧制区面积

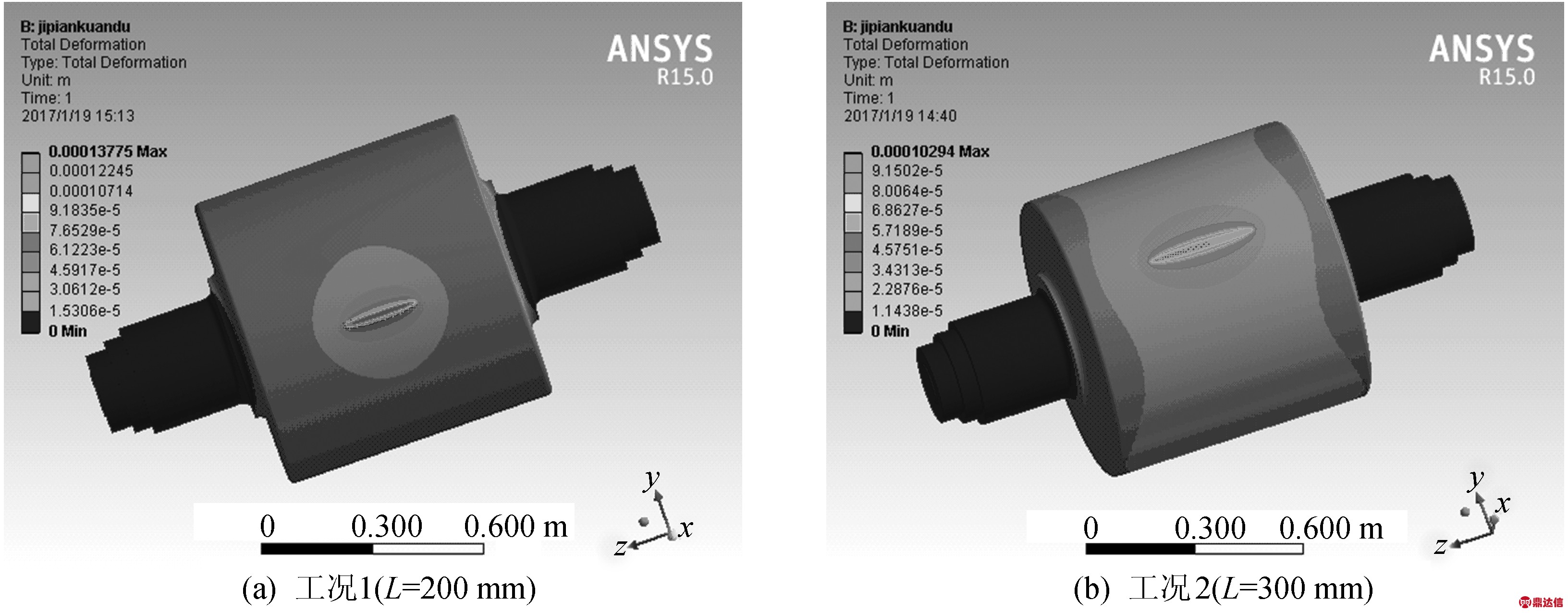
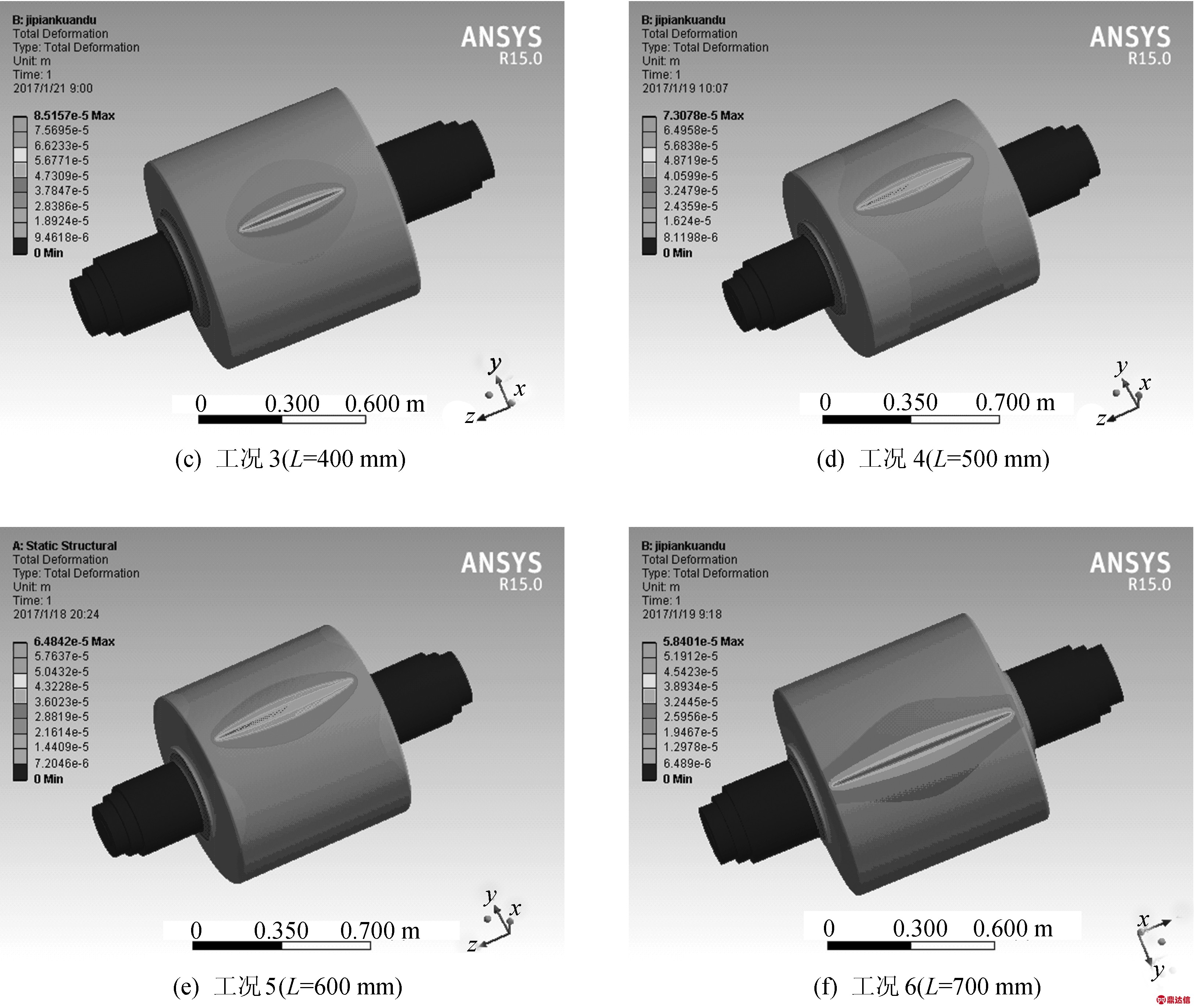
图4 6种极片宽度工况下的轧辊变形云图
6种工况下的辊身最大变形值和辊身总变形量最大差值见表4所列。
表4中,L为极片宽度;N为辊身最大变形;H为辊身总变形量最大差值。
表4 6种极片宽度工况下的N、H

在6种工况下,取辊身变形区沿轴线方向的若干点,作出6种工况下的辊身总变形曲线,如图5所示。
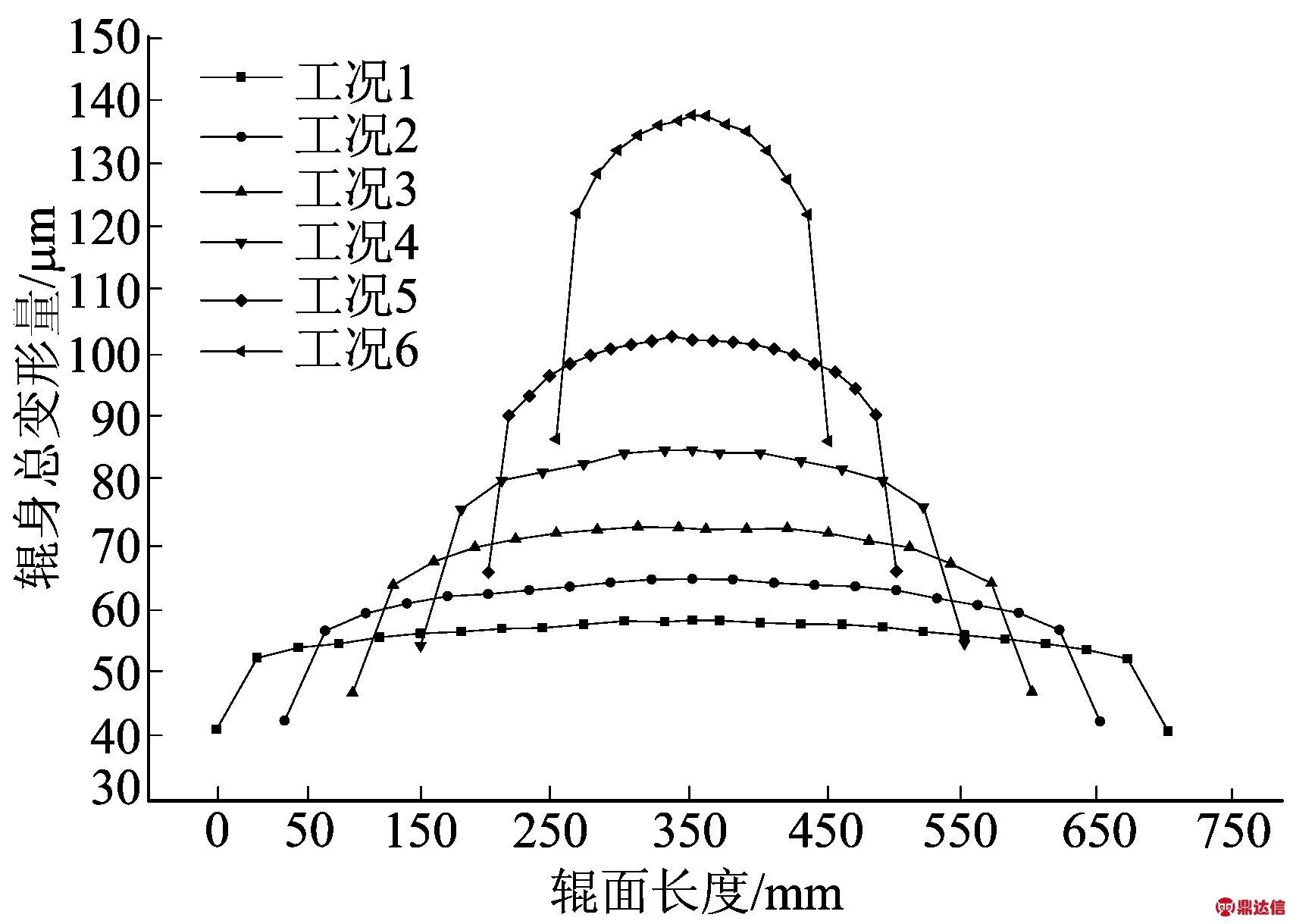
图5 6种极片宽度工况下轧辊辊身总变形曲线
从表4、图5可以看出,在极片宽度不同的情况下,轧辊的辊身总变形差别比较大,工况1(L=200 mm)时,辊身最大总变形为137.75 μm,工况6(L=700 mm)时,辊身最大总变形为58.401 μm,辊身最大总变形减小了79.349 μm。
轧制区域轧辊的辊身总变形量最大差值由工况1的51.301 μm,减小到17.479 μm,减小了33.531 μm,因此,在轧制力相同的情况下,辊身最大变形随着静态轧制面积(即辊身和极片接触部分)的增大而减小。由此可以发现,工况1相比于工况6的静态轧制面积减小4.0×103 mm2,即极片与轧辊之间的接触面积减小4.0×103 mm2,在相同轧制力的情况下,工况1中的轧辊受力集中程度要大于工况6,当增大极片宽度即增大静态轧制面积时,轧辊受力集中程度在逐渐减小,因此辊身总变形也在逐渐减小。
3.3 轧辊辊径对极片一致性能的影响
轧辊的辊径是一个重要参数,由于辊径与轧辊的变形直接相关,辊径对电池极片厚度的影响较大[8-9]。
设定轧制力为2 000 kN、极片宽度500 mm不变,采用目前常用的轧机辊径φ500 mm、φ600 mm、φ750 mm、φ800 mm等,设定4种轧辊尺寸,即工况1(φ500 mm×550 mm)、工况2(φ600 mm×600 mm)、工况3(φ750 mm×800 mm)、工况4(φ800 mm×800 mm)。4种工况下静态轧制区面积见表5所列。表5中,S为静态轧制区面积。
表5 4种轧辊尺寸工况下轧辊静态轧制区面积

其他参数设定同上,应用相同的网格生成方法得到4种工况的网格划分情况:工况1,节点148 892,单元44 902;工况2,节点227 424,单元67 926;工况3,节点442 070,单元130 044;工况4,节点479 300,单元138 738。对4种工况下的轧辊作仿真分析得到轧辊总变形云图,如图6所示。
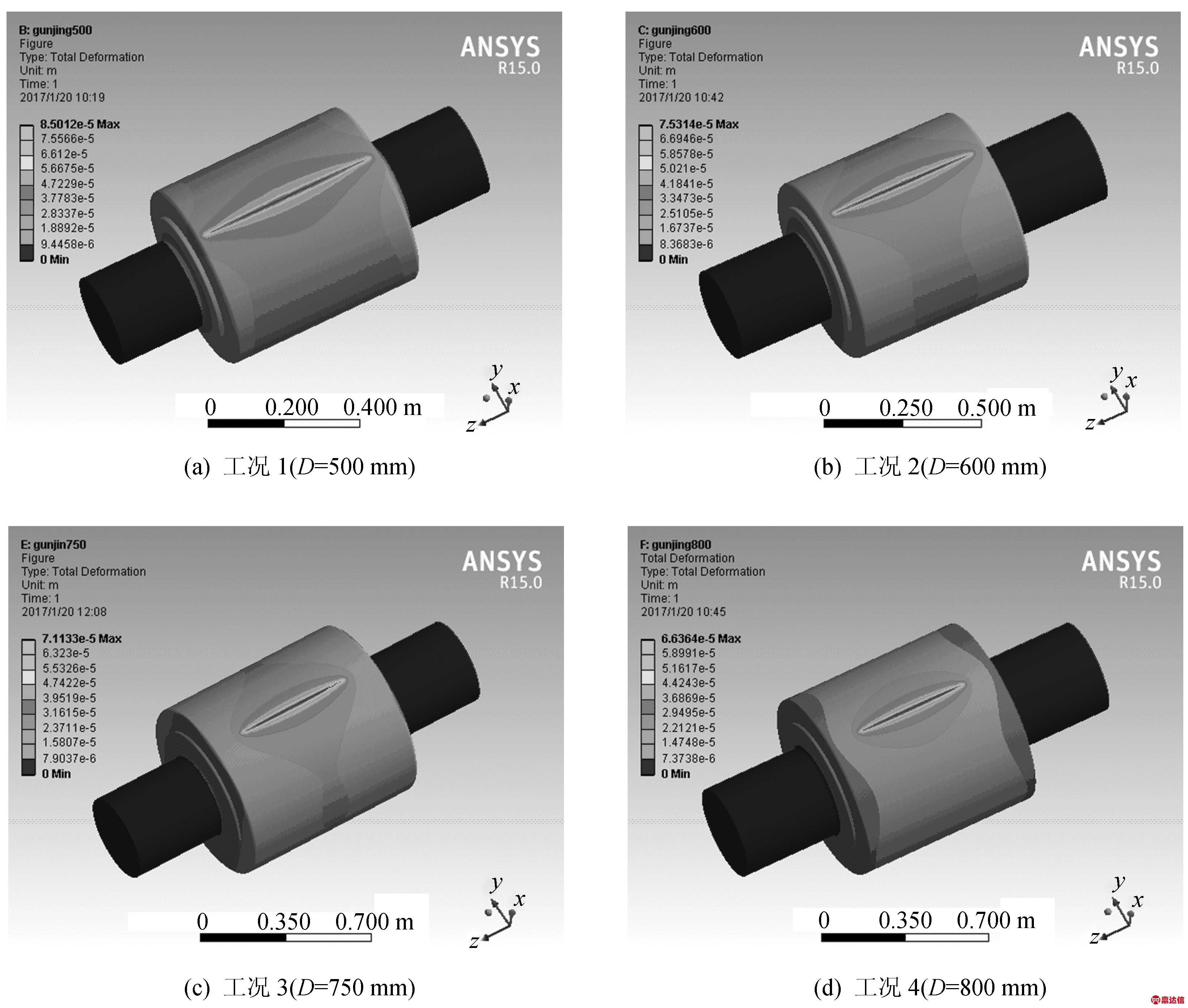
图6 4种轧辊尺寸工况下轧辊总变形云图
4种工况下的辊身最大变形和辊身总变形量最大差值见表6所列。表6中,D为辊径;N为辊身最大变形;H为辊身总变形量最大差值。
在4种工况下,取辊身变形区沿轴线方向的若干点,作出4种工况下的辊身总变形曲线,如图7所示。
从表6、图7可以看出,工况2(D=600 mm)时辊身的总变形比工况1(D=500 mm)时的辊身变形小,工况4(D=800 mm)时的辊身总变形比工况3(D=750 mm)时总变形小。
表6 4种轧辊尺寸工况下的N、H
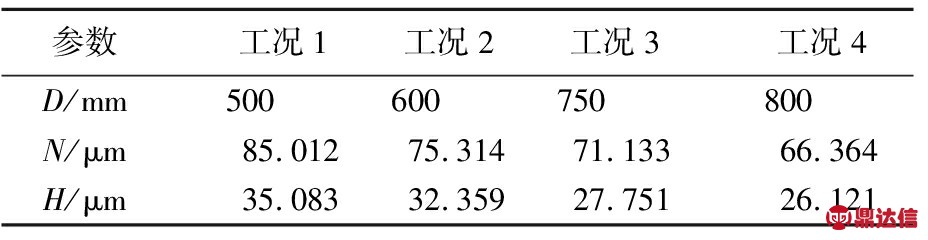
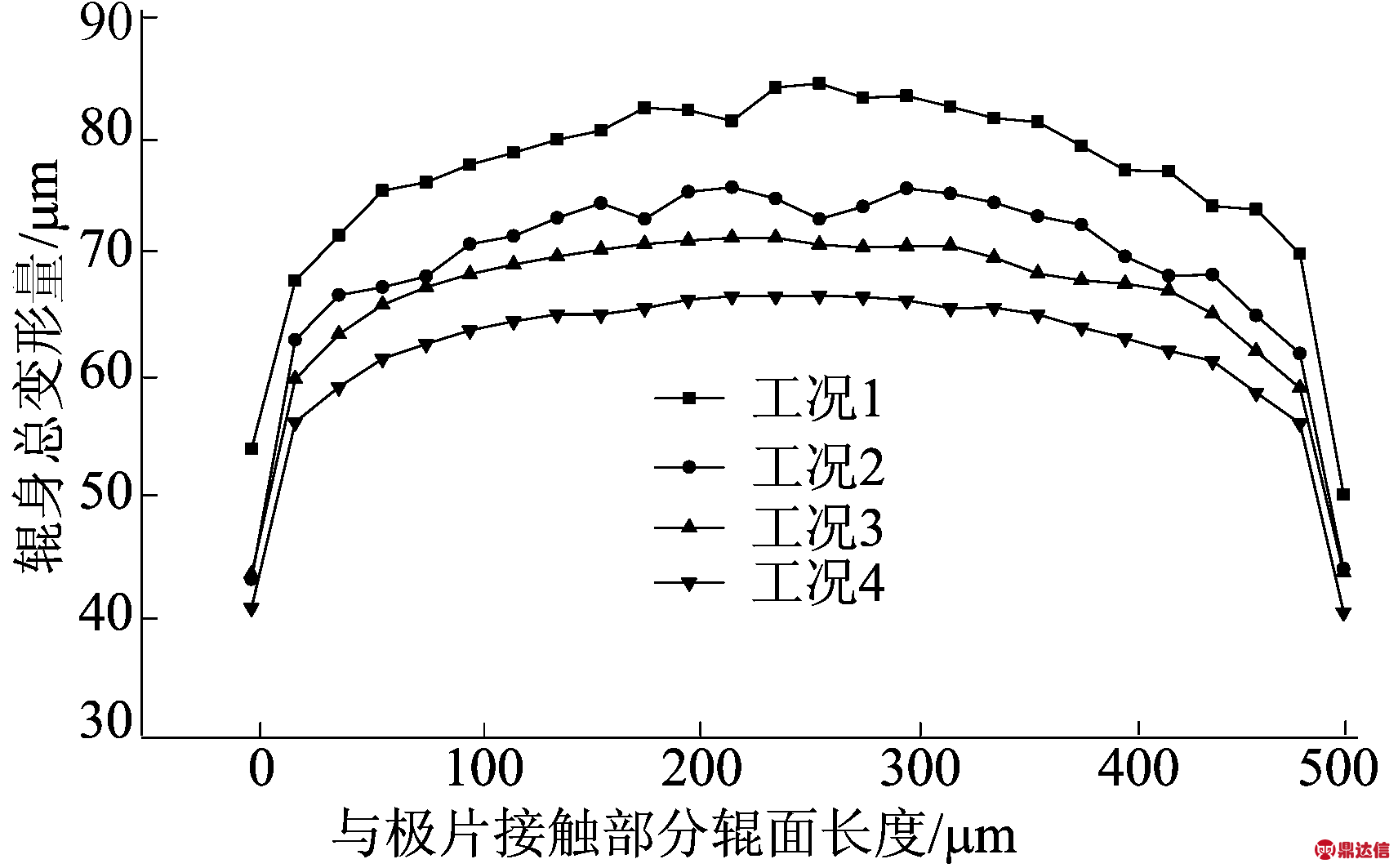
图7 4种轧辊尺寸工况下辊身总变形曲线
由3.2节分析可知,极片的宽度对轧辊的变形影响较大。在分析辊径变化时,轧辊辊身宽度也在相应变化,辊径为750 mm时的辊身宽度为800 mm,辊径为600 mm时的辊身宽度为600 mm,正是由于辊身宽度的差距使得工况2的辊身变形与工况3的辊身变形相近,工况2的辊身最大变形要比工况1的辊身最大变形小9.698 μm,工况4的辊身最大变形要比工况3的辊身最大变形值小4.769 μm。在没有极片宽度的影响下,辊径的变化对辊身的变形影响将更大,比较工况4和工况3轧制区域辊身总变形最大差值的影响,可以看出,工况4的厚度差为26.121 μm,工况3的厚度差为27.251 μm,且从图7可以看出,工况4时在辊身中部的变形曲线最为平缓,表示辊身变形均匀性最好,极片的厚度均匀性也将提高。
辊身的直径和宽度比是衡量辊径变形的重要指标,下面比较直径和宽度比值相等的2种工况,即工况2(D=600 mm)和工况4(D=800 mm),工况2的最大变形为75.314 μm,工况4的最大变形为66.364 μm,最大变形减小了8.95 μm;工况2时轧制区域辊身总变形最大差值为32.359 μm,工况4时的轧制区域辊身总变形最大差值为26.121 μm,减小了6.238 μm。由以上分析可以看出,辊身的变形直接影响极片截面厚度的均匀性,因此辊径的变化对电池的一致性存在较大的影响。
4 试验数据分析
在某极片轧制设备公司的协助下,使用公司产品型号为XJSR80×75-C的电池极片轧制设备进行试验,试验所用的极片涂布材料为磷酸铁锂,极片的涂布厚度为0.180 mm,分析轧制力时用的极片宽度为600 mm,分析极片宽度时,由于没有合适尺寸的极片产品,不同宽度的极片是通过裁剪得到的。测量工具为数显千分尺。
(1) 改变液压系统的作用力,在保证其他参数不变的情况下,实现轧制力的变化。分为6种工况:工况1(F=500 kN)、工况2(1 000 kN)、工况3(F=1 500 kN)、工况4(F=2 000 kN)、工况5(F=2 500 kN)、工况6(F=3 000 kN)。采用恒压力轧制。
采集20个极片横向等间隔的采样点,得到极片的厚度曲线,如图8所示。
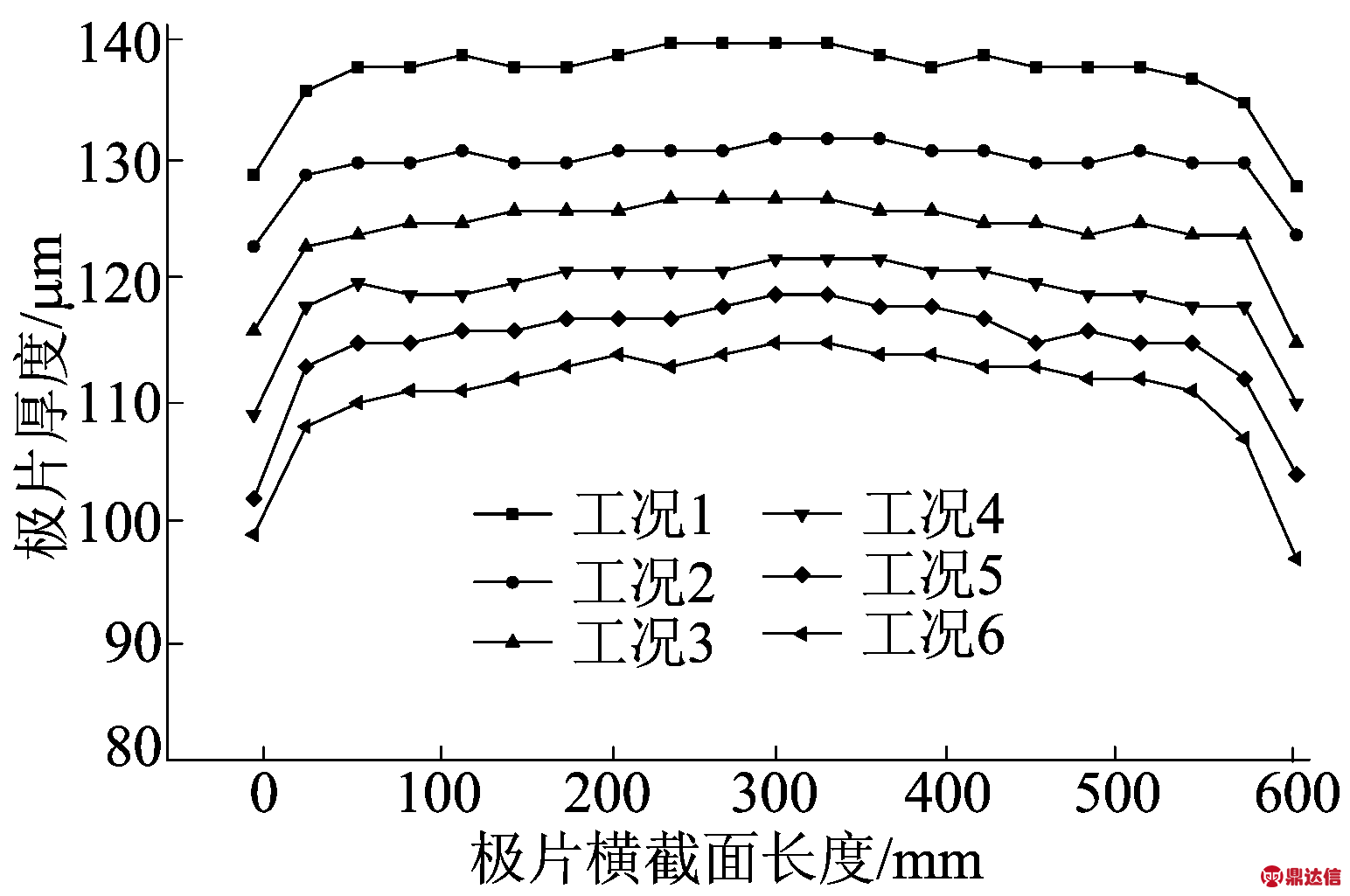
图8 6种轧制力工况下极片厚度变化曲线
比较图3和图8,极片在轧制力变化的情况下,极片变形基本与轧辊的变形相符。从图8可以看出,工况1时极片的厚度曲线比较平缓,极片的厚度差为12 μm;工况4时极片的厚度曲线有些波动,但是波动程度并不大,极片的厚度差为13 μm,厚度差变大;工况6时,从极片厚度曲线的形状能明显看出中间厚两边薄的现象,厚度差也达到了18 μm。轧制力的变化引起轧辊变形以及极片的厚度差变化,不同的电极材料需要的压实密度不同,因此在满足压实密度的要求下,选取相对小的轧制力能有效减小极片的不一致性。综合以上分析可以得出,轧制力对极片的厚度均匀性影响较大。
(2) 改变极片宽度,分析极片宽度变化对极片一致性影响。将轧制力设定为2 000 kN,将极片宽度的试验工况定为6种:工况1(L=200 mm)、工况2(L=300 mm)、工况3(L=400 mm)、工况4(L=500 mm)、工况5(L=600 mm)、工况6(L=700 mm)。得到的极片厚度曲线如图9所示。
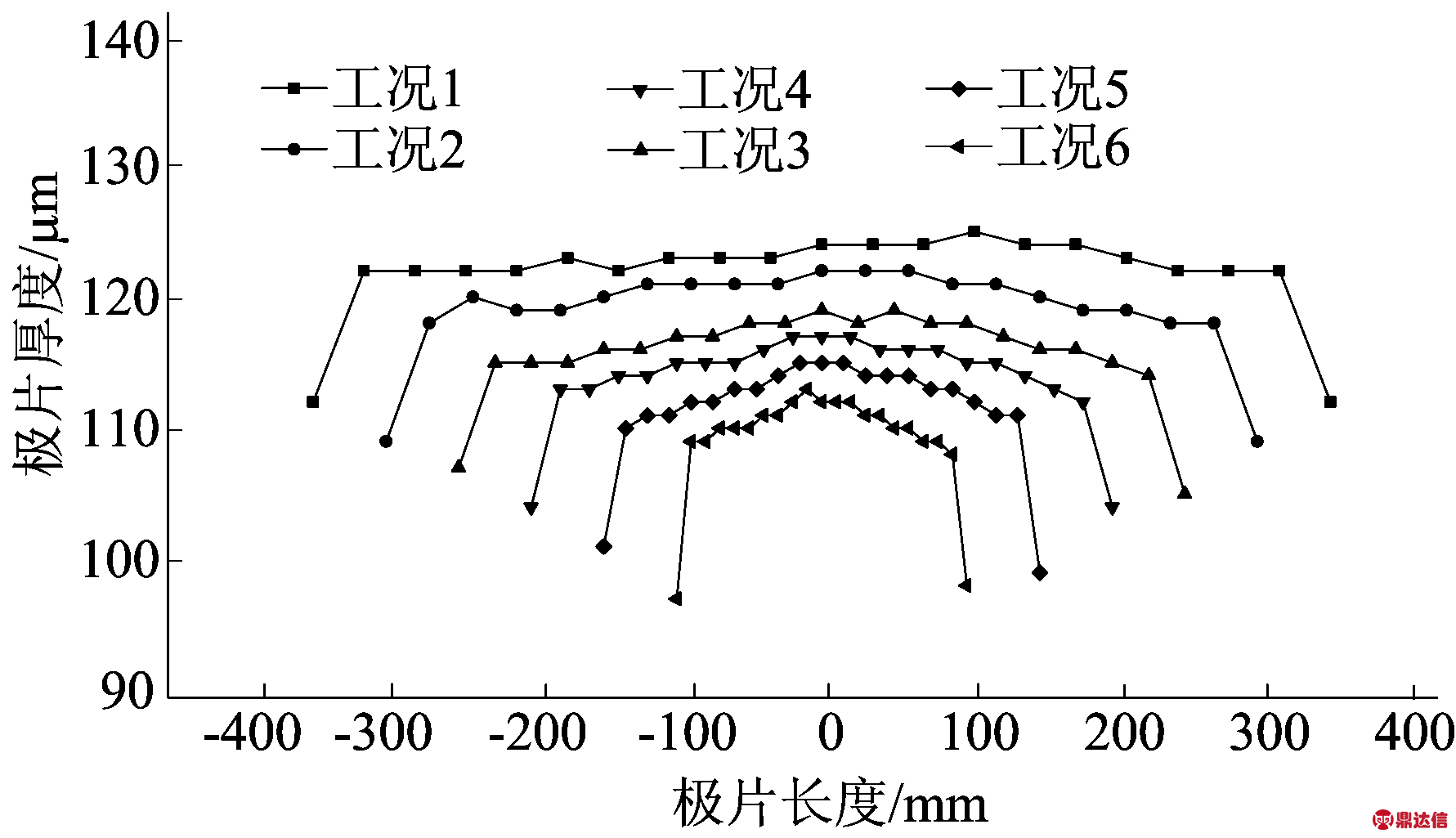
图9 6种极片宽度工况下极片厚度变化曲线
比较图5和图9可见,极片宽度的改变会引起轧辊的变形变化,作用到极片上的影响结果为极片厚度的变化。在一定轧制力作用下,工况6时极片的厚度曲线比较平直,波动比较小,极片的最大厚度差为11 μm;工况1时极片的厚度曲线出现波动较大的现象,极片的最大厚度差为16 μm,增大了36%,极片的厚度差随着极片的宽度减小而变大。由以上分析可以得出,极片的宽度是影响极片厚度一致性的一个非常重要的影响因素。
5 结 论
本文研究了极片轧辊对电池极片一致性能的影响,分析了极片的纵向不均匀性的影响因素。对极片的横向厚度不均匀性的原因进行仿真分析,发现轧制力、极片宽度以及轧辊的辊径都会对轧辊的挠度变形产生影响,分析了影响极片一致性的原因。仿真分析结果表明,轧制力变大,轧辊本身的变形也在逐渐增大,由于轧辊两端轴颈承受轧制力,引起轧辊挠度变形增大,最终导致极片截面厚度差也随之增大;当增大极片宽度即增大静态轧制面积时,轧辊受力集中程度在逐渐减小,因此辊身总变形也在逐渐减小;辊径变大,辊身的变形将变小,极片厚度均匀性变好。采用某公司XJSR80×75-C的电池极片轧制设备进行现场试验,对极片横向等间隔进行采样,试验结果表明轧制力、极片宽度对轧制后的极片厚度一致性有非常重要的影响。