摘 要:磨削工艺直接影响着磨削后晶片的参数,在这些参数中,表面粗糙度是鉴别晶片几何参数好坏的重要指标之一。分析了磨削工艺中砂轮粒度、砂轮进给速度对表面粗糙度的影响。
关键词:晶圆减薄;磨削;表面粗糙度
集成电路(integrate circuit,IC)是电子信息产业的核心,是推动国民经济和社会信息化发展最主要的高新技术之一。IC的制造离不开高精度、高表面质量的硅片,全球90%以上的IC都要采用硅片。随着半导体晶圆直径的增大和芯片厚度的超薄化,对晶圆表面加工质量和加工效率提出了更高的要求,需要研究和开发更先进的硅片超精密加工技术与设备。而大直径(≥300mm)硅片的先进加工技术和设备的引进要受到发达国家限制。因此,我们必须依靠自己的力量研究具有自主知识产权的大直径硅片的超精密加工技术与设备。随着硅片尺寸的增大,对超薄晶圆面型精度的要求也不断提高。例如,JB-802型全自动晶圆减薄机采用2000#砂轮可以将φ200 mm晶圆磨削到70μm,表面粗糙度(Ra)小于0.02μm;BGP300全自动晶圆减薄抛光一体机可以将φ300 mm晶圆磨削抛光到50μm,表面粗糙度(Ra)小于0.005μm。晶片表面粗糙度(Ra)是晶圆减薄抛光机的一项重要指标,直接影响后续的各项封装工艺和芯片的最终质量。因此,通过不断完善磨削工艺参数,如砂轮粒度、主轴进给速度等,最终达到降低磨削后晶圆的表面粗糙度。如图1所示。
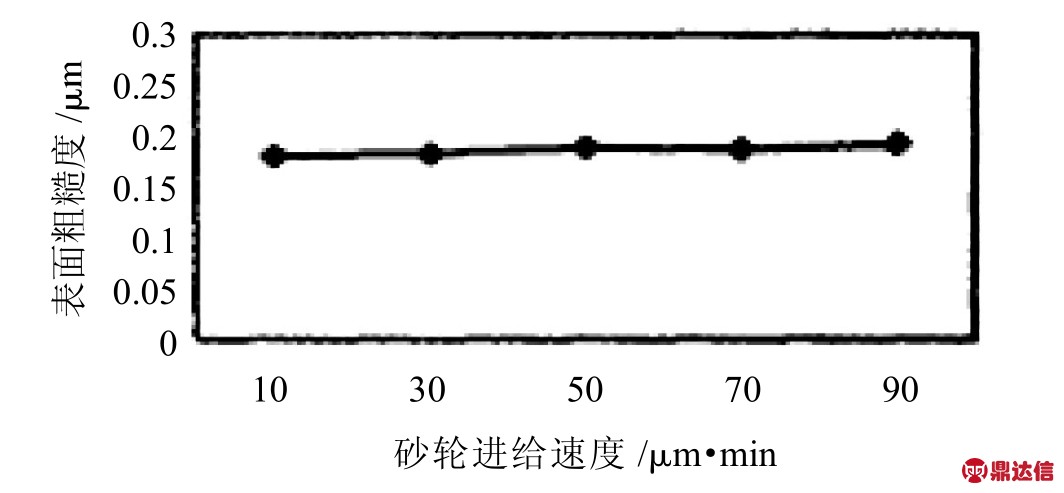
图1 超光滑晶圆示意图
1 硅片表面粗糙度的定义及评定参数
1.1 硅片表面粗糙度的定义
硅片表面粗糙度是指硅片表面具有的较小间距和微小峰谷不平度。它属于微观几何形状误差,表面粗糙度越小,则表面越光滑;反之,则表面越粗糙。
1.2 表面粗糙度的评定参数
粗糙度轮廓的算术平均偏差Ra在一个取样长度内纵坐标Z(x)值绝对值的算术平均值。其计算公式为:
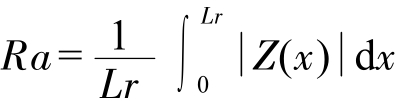
式中:Z(x)是取样长度内硅片基体表面结构的轮廓曲线函数。
其中取样长度Lr,用于判定被评定粗糙度轮廓不规则特性的X轴向上的长度。
2 晶圆减薄机工艺过程和原理
2.1 晶圆减薄机工艺过程
硅片背面磨削一般分为两步:粗磨和精磨。在粗磨阶段,采用粒度46#~500#的金刚石砂轮,轴向进给速度为100~500 mm/min,磨削深度较大,一般为0.5~1 mm。目的是迅速地去除硅片背面绝大部分的多余材料(加工余量的90%)。精磨时,加工余量几微米直至十几微米,采用粒度2000#~4000#的金刚石砂轮,轴向进给速度为0.5~10 mm/min。主要是消除粗磨时形成的损伤层,达到所要求的厚度,在精磨阶段,材料以延性域模式去除,硅片表面损伤明显减小。
2.2 晶圆减薄机磨削原理
当前主流晶圆减薄机的整体技术采用了In-feed磨削原理设计。为了实现晶圆的延性域磨削,提高减薄质量,通过减小砂轮,使设备的进给运动分辨率小于0.1μm,进给速度最小1μm/min。另外,为了提高减薄工艺的效率,进给系统在满足低速进给的前提下,要尽可能实现高速返回(见图2)。

图2 In-feed磨削原理示意图
3 实验研究
3.1 实验设计
准备9片φ200 mm(8英寸)晶片,进行减薄试验,记录减薄时的各项工艺参数及最终所磨削晶片的表面粗糙度值,对这些参数进行比较,最终得到砂轮粒度、砂轮进给速度和表面粗糙度之间的关系,方案设计见表1和表2,磨削实验用JB-802晶圆减薄机。
3.2 工艺操作步骤
针对方案一:取4片晶圆片,更换砂轮型号,依次为#325、#600、#2000和#3000,其它磨削参数不变。
表1 方案一:磨削主要技术参数
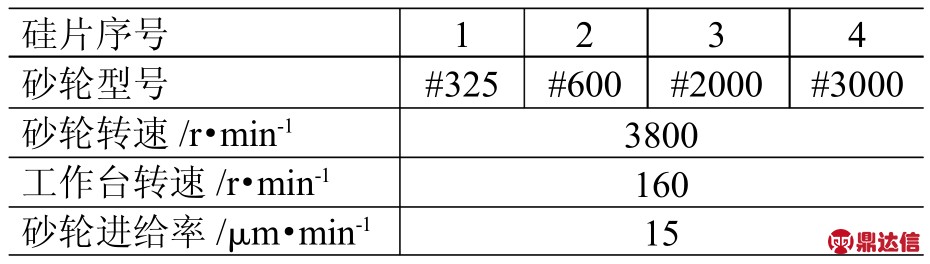
表2 方案二:磨削主要技术参数
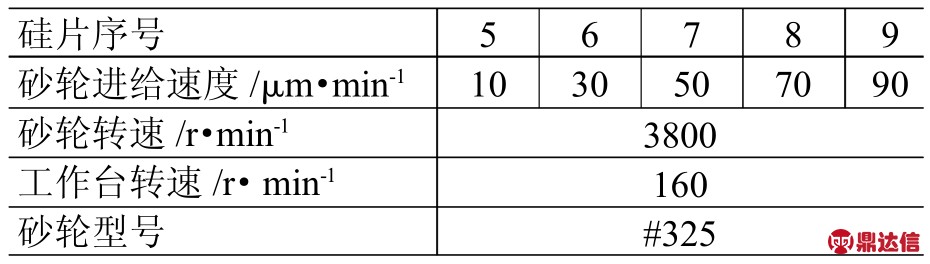
针对方案二:取5片晶圆片,设置砂轮进给速度,依次为10μm/min、30μm/min、50μm/min、70μm/min和90μm/min,其它磨削参数不变。
3.3 测量设备及方法
通过Xi-100轮廓仪,读取5个点晶圆片表面粗糙度数据,测量方法如图3所示。
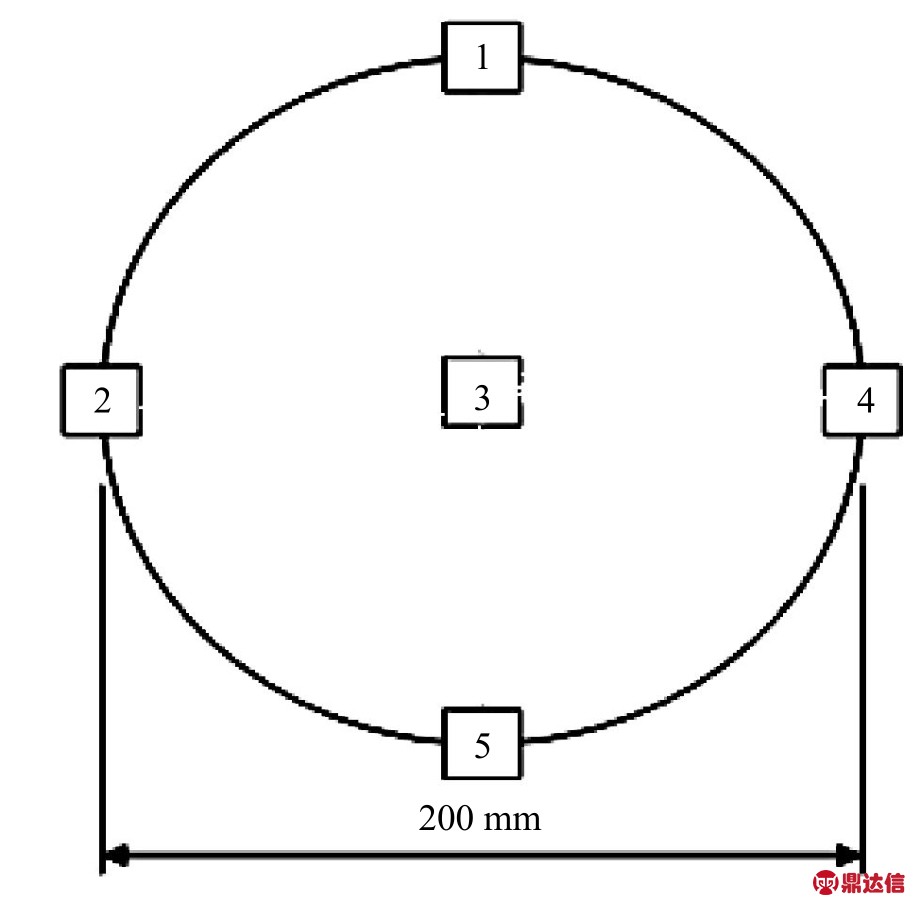
图3 晶圆表面粗糙度检测位置示意图
3.4 实验结果
通过Xi-100轮廓仪,读取5个点晶圆片表面粗糙度数据,选择5个点表面粗糙度最大值,数据如表3所示。砂轮粒度与表面粗糙度关系见图4所示,砂轮进给速度与表面粗糙度关系见图5所示。
我们取4号片,通过轮廓仪Xi-100系统测量,表面粗糙度Ra为4.141 nm,表面峰谷St为36.52 nm,见图6所示。
表3 晶圆片表面粗糙度值
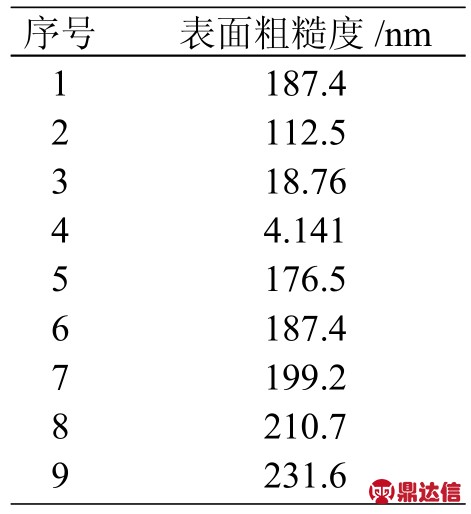
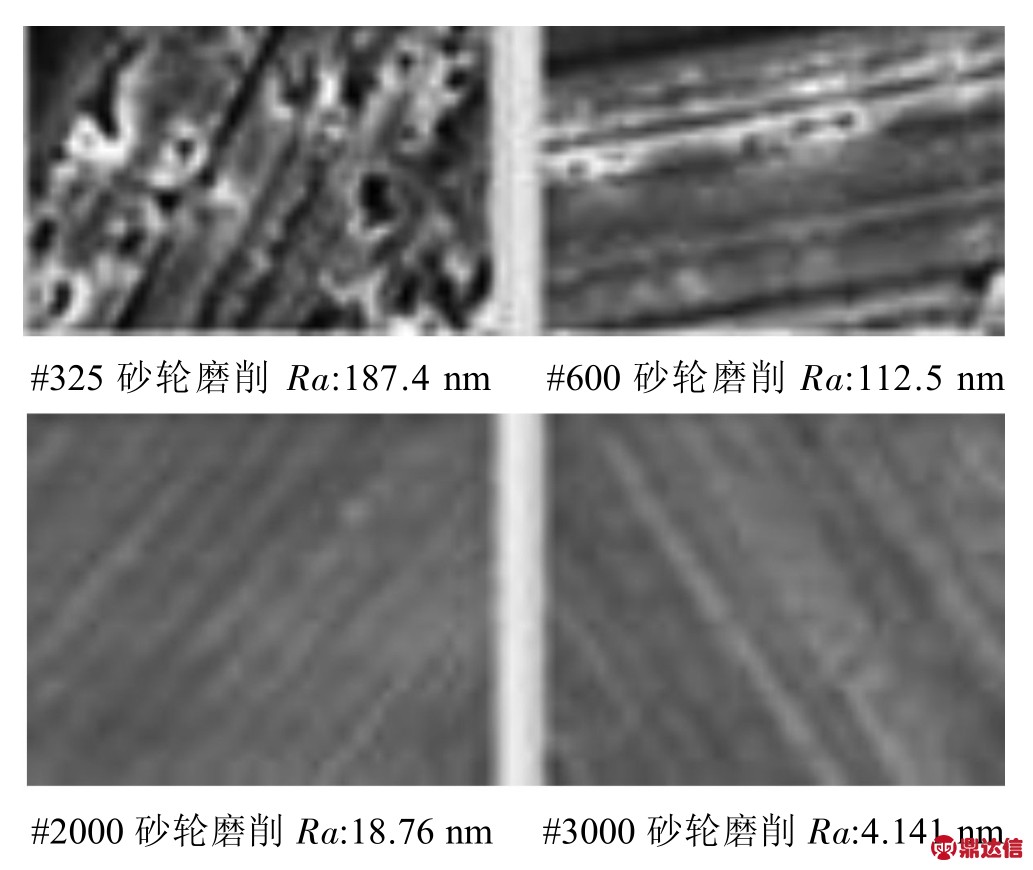
图4 砂轮粒度与表面粗糙度的关系
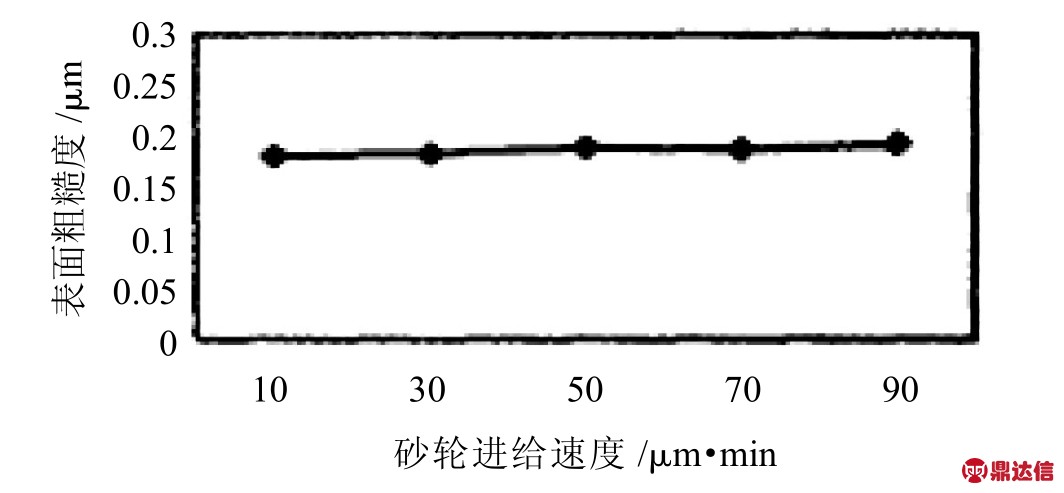
图5 砂轮进给速度与表面粗糙度的关系
3.5 结果分析
为了研究砂轮进给率、砂轮转速、工作台转速对硅片表面粗糙度的影响规律,分别对它们进行试验研究。
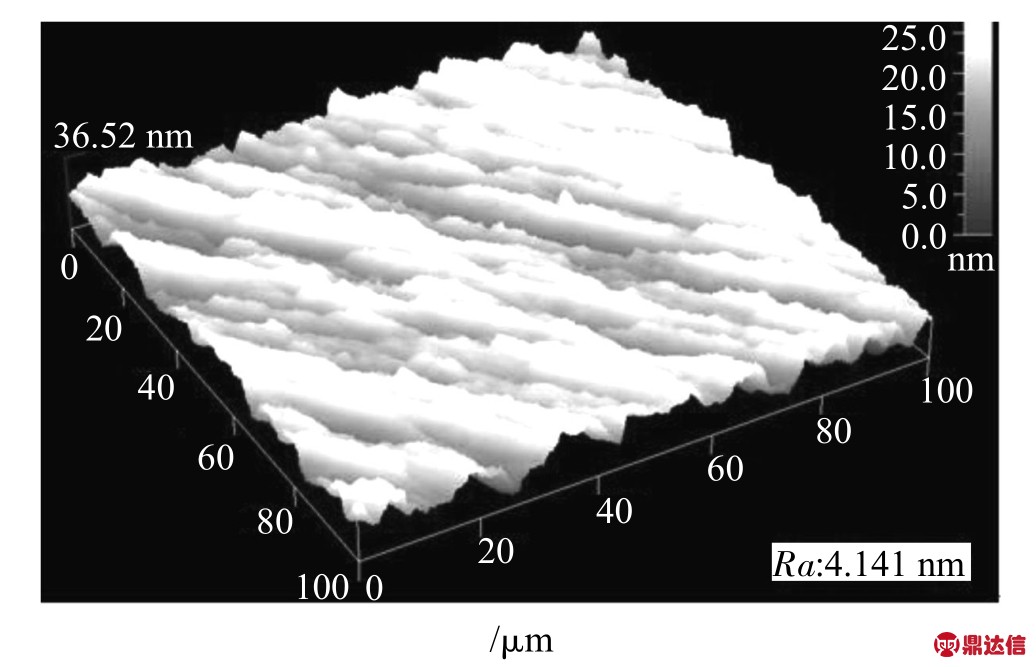
图6 晶圆表面轮廓图
通过实验得出如下结果:
(1)当其它磨削参数不变时,随着磨轮磨粒尺寸的减小,晶圆表面粗糙度减小,而且同一粒度砂轮磨削硅片的表面粗糙度常常在一个范围之内。因此,为了降低硅片的表面粗糙度,就要在一定范围内减小砂轮磨粒尺寸,不过这样会降低材料去除率,延长了加工时间,增加成本。
(2)当其它磨削参数不变时,硅片的表面粗糙度值随着砂轮进给率的增大而增大,且表面粗糙度值增大的很快。因为砂轮进给率增大而转速不变时,砂轮磨削深度增大,从而对硅片表面的切削力和挤压力也增大,单位时间内去除的材料增多,材料脆性断裂的趋势增大,损伤深度也增大。因此,为了降低硅片的表面粗糙度值,就要在一定范围减小砂轮进给率,不过这样会降低材料去除率,延长了加工时间,增加成本。
4 结论
综上所述,砂轮粒度、砂轮进给率对硅片表面粗糙度的影响巨大。因此,在晶圆磨削过程中,对砂轮粒度、砂轮进给率等工艺参数的合理设置,有助于降低晶圆的表面粗糙度值,从而提高磨削后晶圆的表面质量。