【摘要】由于原塑件结构以及原模具结构设计上细小的、但却是致命的缺陷,导致投产后塑件的废品率居高不下,而且成型晶片插槽的弧形镶片,经常发生断裂损坏而不得不停产修理,使生产难以顺利进行。
关键词:晶片插座;注射模;改进
1 对塑件—晶片插座的分析
(1)晶片的尺寸精度:一种晶片,是只有名义尺寸而未标注尺寸公差的晶片。而另一种晶片则是标注了配合公差且有具体的配合精度要求的晶片。
(2)晶片插座由此也分为两种类型。一种是超声波切割机切割晶片过程中,用来插放切好但尚未研磨、抛光的圆形晶片的普通周转工具。另一种则是专门用来插放已经研磨、抛光好,经检测完全合格的圆形晶片的精密专用周转工具。这两种晶片插座,其形状、结构都一样,但是其尺寸精度和材料配方则大不相同。因此,插放粗加工晶片插座上的插槽尺寸按粗加工晶片尺寸,留有较大间隙,而插放精加工晶片插座的插槽尺寸,则有较为严格的尺寸精度要求。
(3)插放粗加工晶片插座的材料用普通的、廉价的聚丙烯(PP)即可,而插放精加工晶片插座的材料,则必须在聚丙烯中加入较大比例的耐油优质橡胶,使之具有优异的弹性和柔韧性,以确保精加工晶片插入时,不受损伤而且具有一定的包紧力和防止震动避免碎裂的功能。
改进前的塑件,如图1所示。
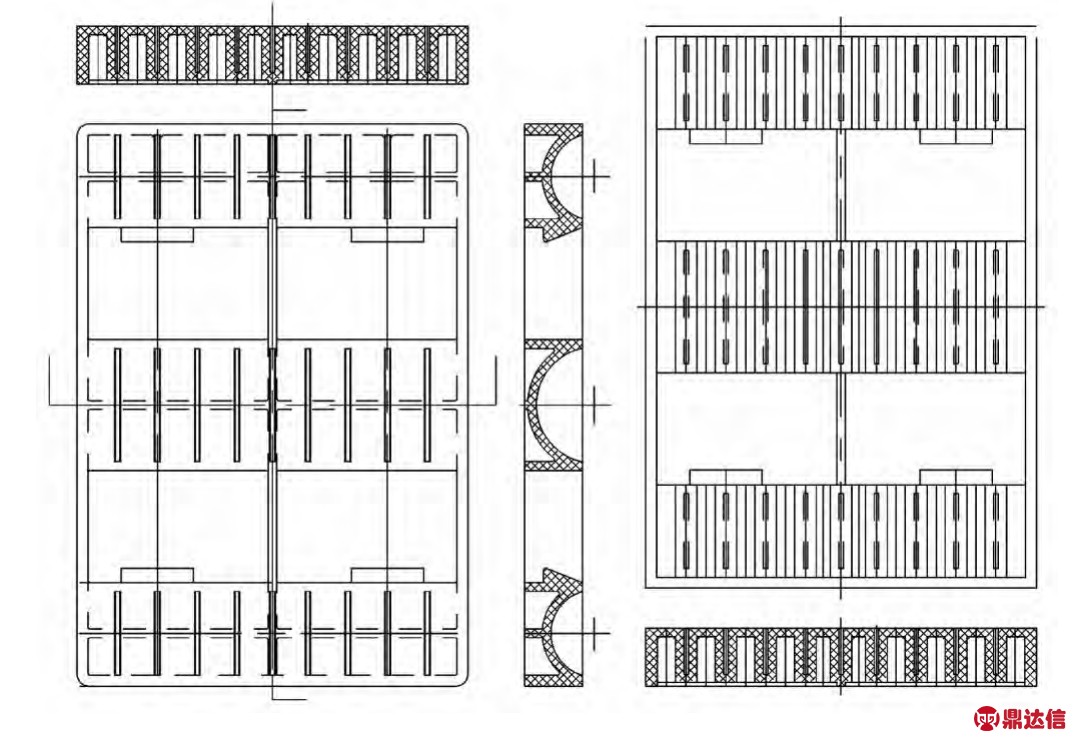
图1 改进前的塑件剖视图
存在的问题:
(1)塑件整体结构的工艺性太差。塑件的设计者对塑料模具以及塑料成型工艺似乎还比较陌生。
(2)晶片的插槽:设计成直上直下的结构,没有脱模斜度,脱模困难。上端入口处,既无倒角,也无圆角。切片工人反应,切好的晶片很难顺利插入,插片比切片累多了。
(3)由于插座整体结构设计不当,对插座在使用过程中的受力状况和可能产生的应力变形,未进行深入的分析和研究,所以,在使用过程中产生了较大变形。
(4)插座原设计,对晶片切片粗加工后以及研磨、抛光精加工后的巨大差异性,未进行深入细致的了解和分析,所以,只设计了一种插座。加之,为了降低插座的制造成本,选用廉价的聚乙烯成型,因此,其适应性很差,很不好用。改进前后晶片插槽断面对比如图2所示。
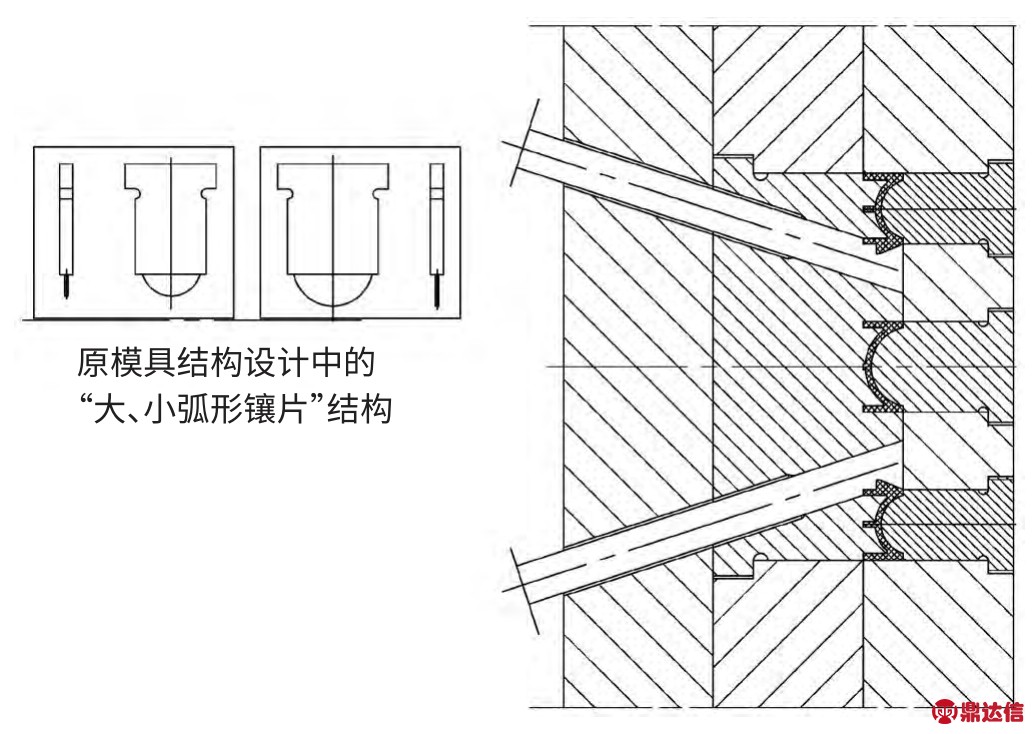
图2 晶片插槽断面放大
2 原模具结构的分析
原模具结构,如图3所示。
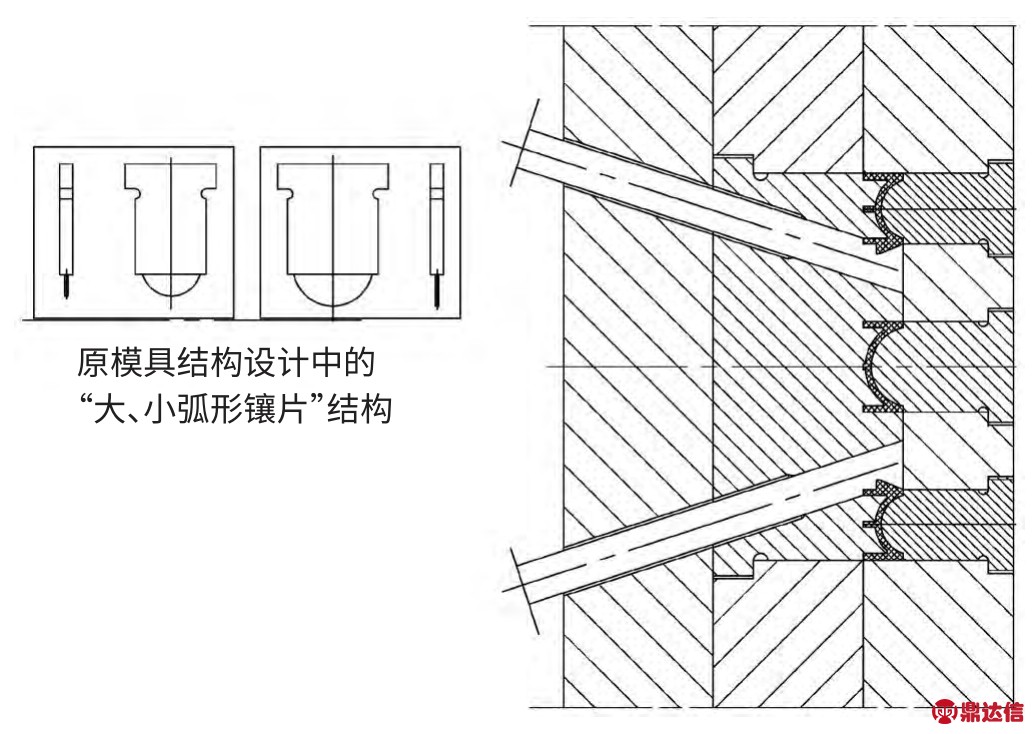
图3 原模具结构
存在的问题:
(1)由于原设计将塑件置于定模板中成型,塑件中的4个卡扣,不能直接脱模而只能采用斜推才能脱模,制造难度必然加大。
(2)由于原设计者未“吃透”塑件,因此,塑件原设计中存在的上述诸多问题,未能逐一有效解决,所以,一再出现因脱模困难以及塑件结构不合理而造成塑件严重变形,并多次发生弧形镶片断裂损坏停产修理以及废品率居高不下的局面,使生产不能顺利进行,生产任务难以完成。
3 改进后的塑件结构
改进后的塑件剖视图如图4所示。
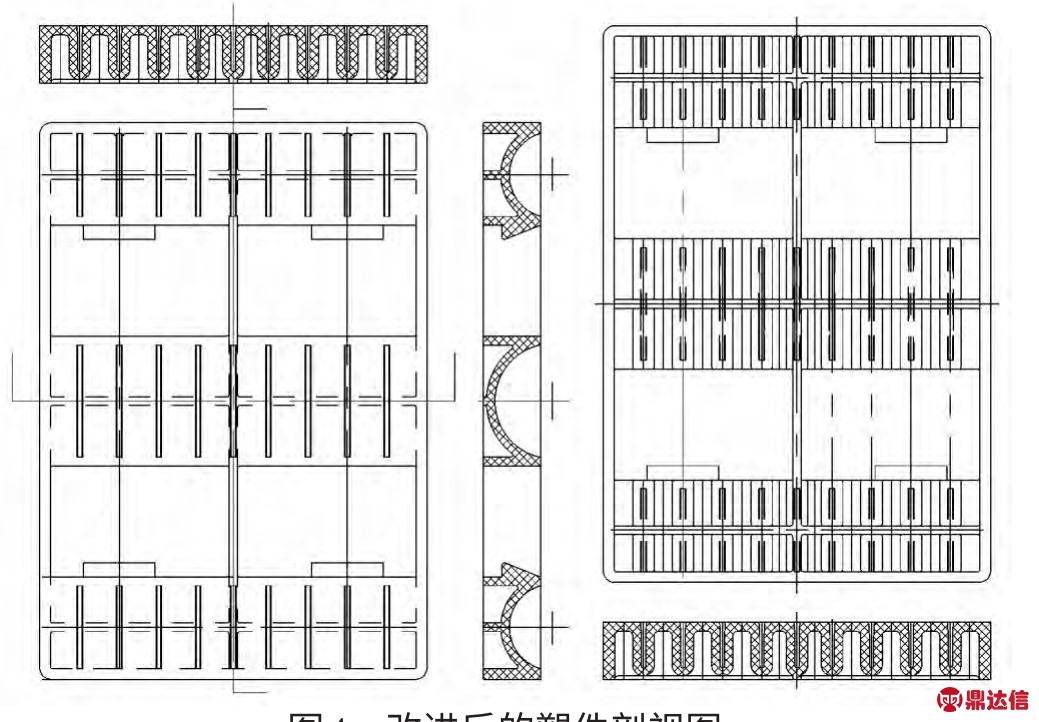
图4 改进后的塑件剖视图
通过与客户、与塑件设计者的反复沟通、解释,得到对方的理解和同意后,将模具作出以下改进:
(1)将塑件改为图4所示之结构:在三排弧形插槽的反面横向,分别添加了一条加强筋;在塑件纵向正中央也添加了一条加强筋,从而与四周的边框构成了犹如“丰”字形的围框结构,具有较好的结构强度,彻底解决了塑件的变形问题。
(2)将晶片插槽的断面结构尺寸改为图2 中所示的喇叭形、边口倒圆的合理结构。一是解决了晶片插入难的问题,使之易于插入,大大减轻了切片工人的劳动强度,切片工人大加赞赏;二是彻底解决了弧形镶片的断损问题,使生产能够顺利进行
(3)将粗加工后的晶片切片以及研磨、抛光精加工后的晶片,分别设计为两种相应的、精度不同的插座,而且采用不同的塑料成型:粗加工后的晶片切片插座用普通PP料成型即可,而研磨、抛光精加工后的晶片,则在PP 料中,添加了比例较大的耐油优质橡胶,大大提高了插座插孔的柔韧性和弹性。研磨、抛光后的晶片插入时方便,插入后牢固、可靠,试用后,效果极佳。
4 改进后的模具结构
改进后的模具结构如图5所示。
5 模具的主要零件
模具的主要零件如图6所示。
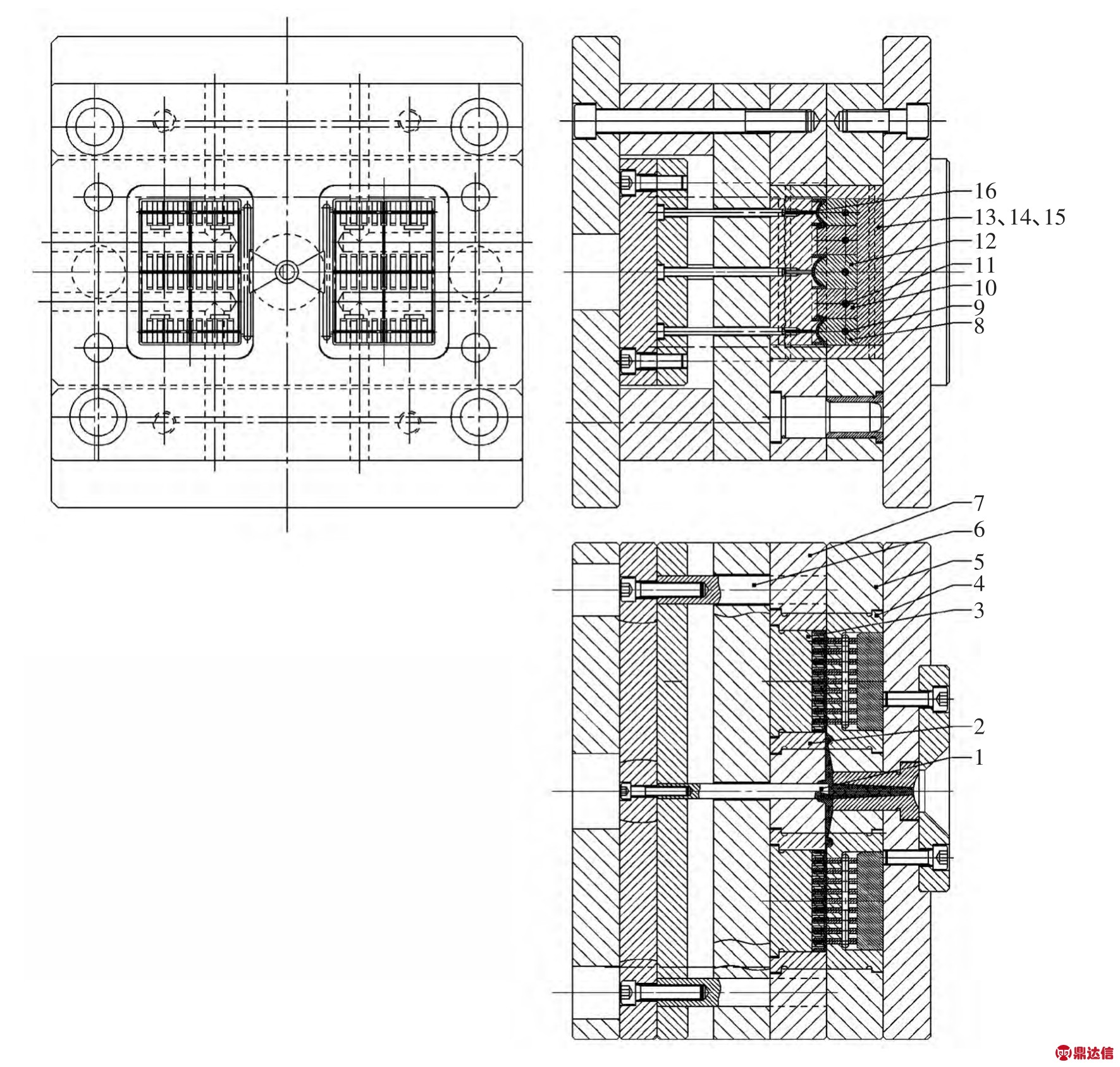
图5 改进后的模具结构
1.拉料杆 2.动模型腔镶套 3.动模型芯镶件 4.定模型芯镶套 5.定模板 6.复位杆 7.动模板 8.定模弧形小镶片 9.圆形镶片长固定销 10.矩形镶片 11.矩形镶片短固定固定销 10.矩形镶片 11.矩形镶片短固定销 12.定模弧形大镶片 13、14、15.(大、中、小)衬垫 16.推杆
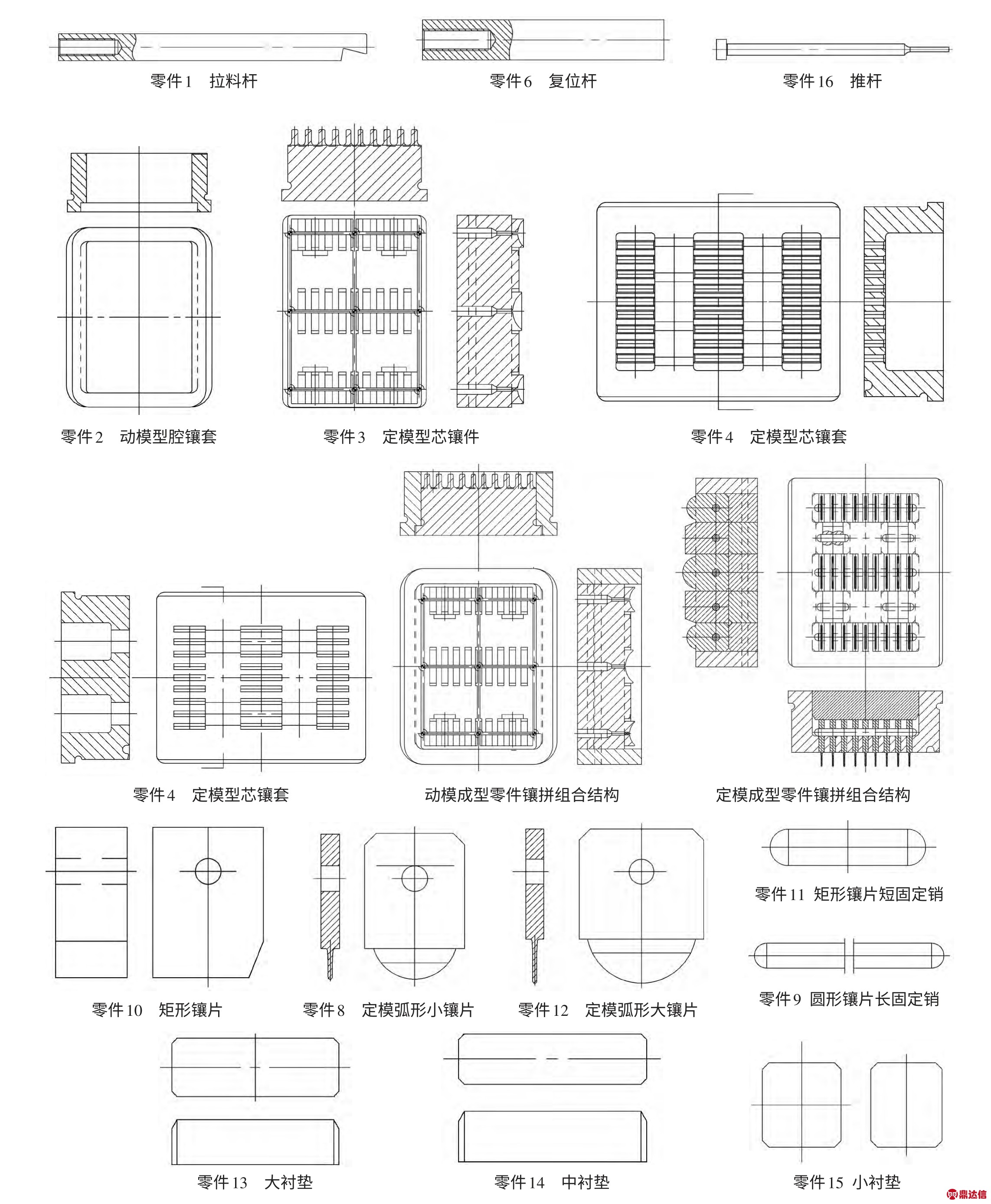
图6 模具主要零件
6 模具成型塑件过程各步骤的分解图
模具成型塑件过程各步骤的分解图如图7~图12所示。
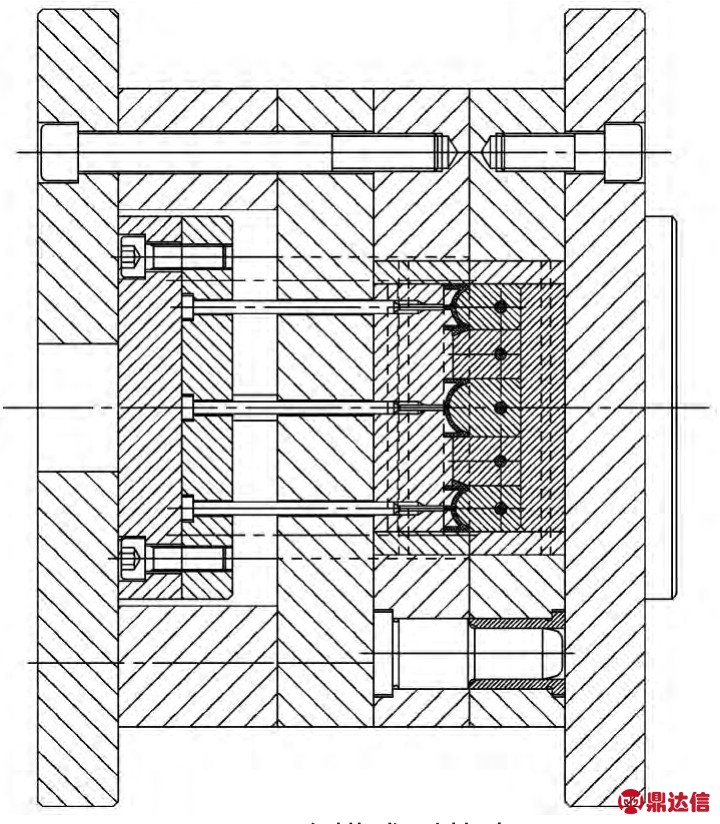
图7 合模成型状态
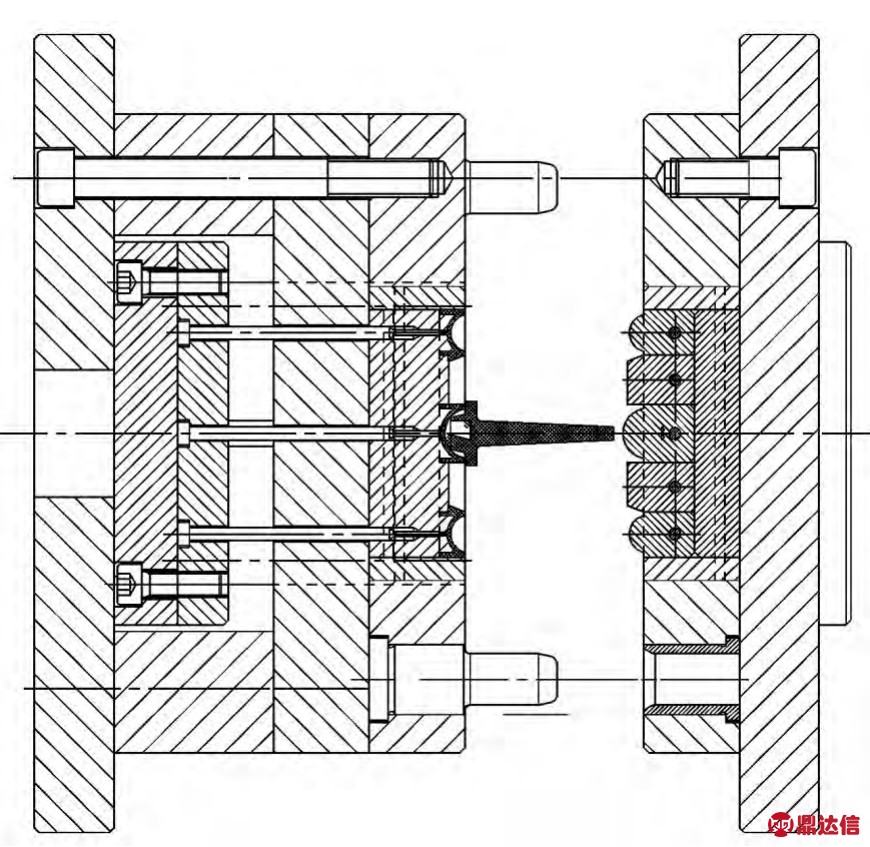
图8 开模状态
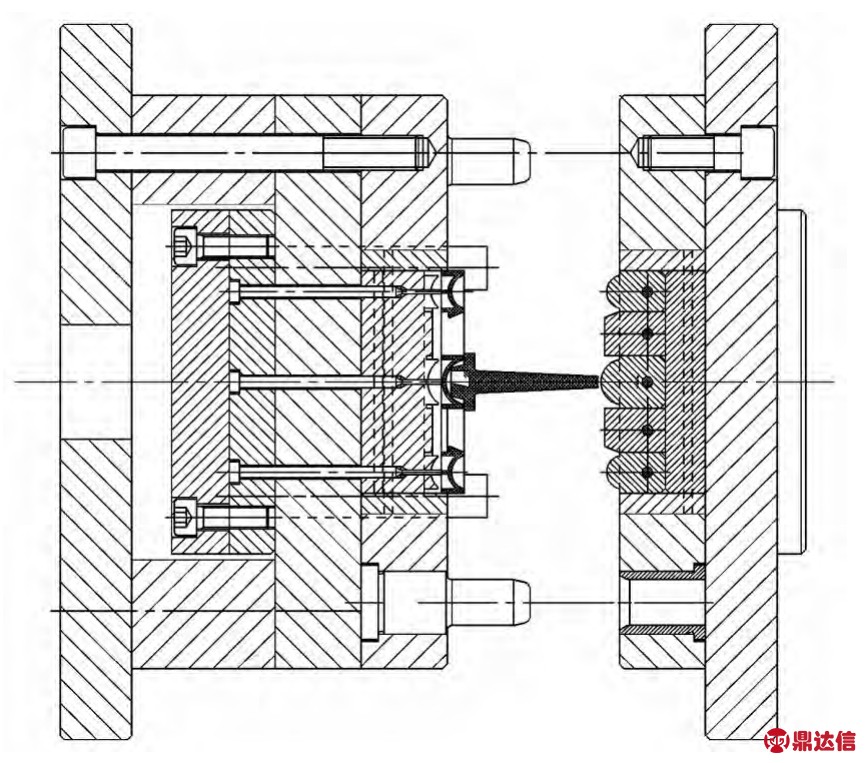
图9 推出塑件状态
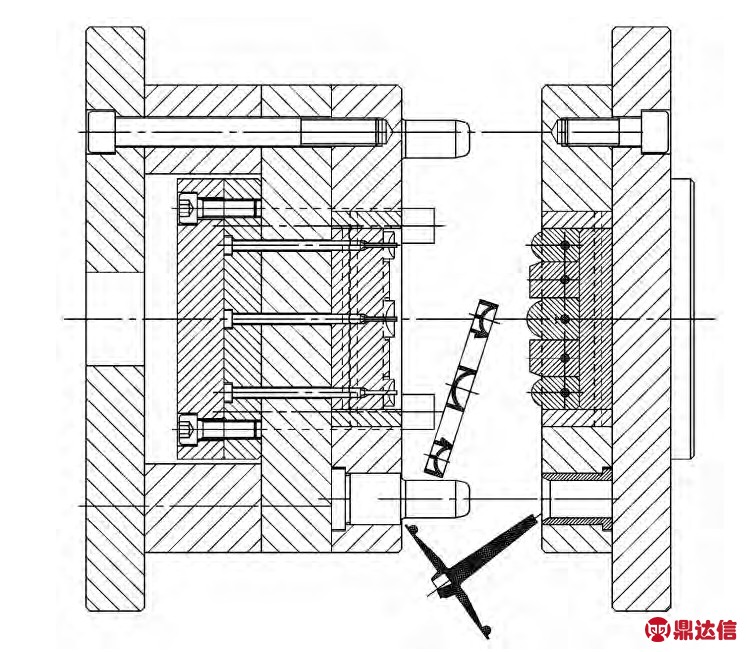
图10 塑件坠落状态
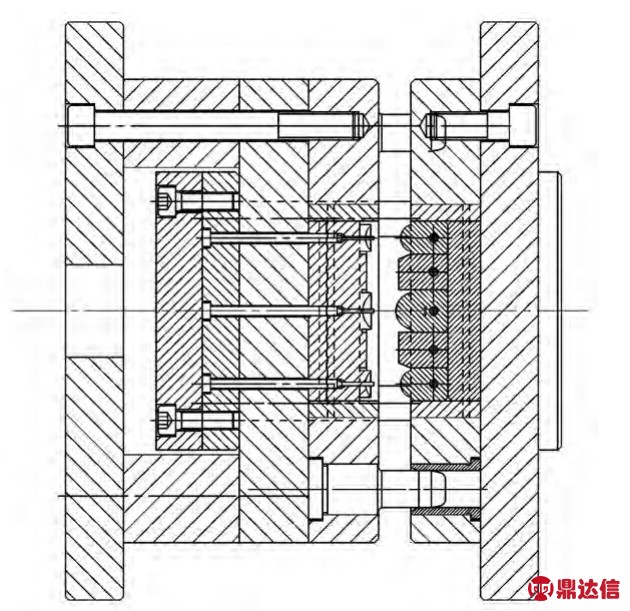
图11 复位初始状态
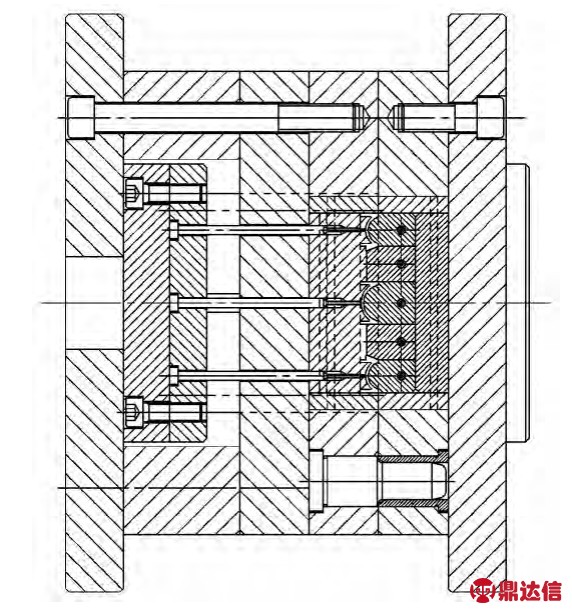
图12 完全复位状态
7 结束语
此模具经试模投产后,性能稳定,塑件质量良好,废品率从未超3‰,连续生产一年多,从未停过产,生产工人赞誉有加,受到客户好评。