摘 要:蒸汽发生器下封头组件与管板组件的最终环缝在局部焊后热处理过程中,为避免因支撑板变形而产生管子“DING”,对蒸汽发生器上部筒体检查孔与顶部支撑板的结构特点进行研究,设计辅助检测工装,制定了新型检测方案。通过对支撑板变形量的数据监测,拟合了变形量随温度变化的数据模型,为后续采取合适的工艺方案奠定了理论基础。
关键词:预防;DING;检测方案
0 引言
“DING”定义为按照西屋技术文件(APP-VL53-Z0-011)进行涡流检测,信号显示的管壁的永久变形[1-2]。在蒸汽发生器(SG)最终环缝的局部焊后热处理(PWHT)过程中,由于焊缝的加热,在热传导的作用下,管板会发生变形。同时在蒸汽发生器二次侧,外套筒、内套筒、锁定杆也会由于热传导、辐射和空气对流换热的作用下,受热产生变形。管板、外筒体、内套筒和锁定杆累积的变形会传递给管子支撑板(TSP),TSP变形超过一定角度时,管子和TSP三叶孔的间隙将闭合,当变形继续增加,TSP三叶孔的棱边将会接触U形管外壁,在接触点力的作用下,管子发生塑性变形后,产生凹坑。热处理结束,TSP恢复变形后,如果U形管接触位置的应力超过换热管的屈服强度,变形将不能恢复,如图1所示。这种不可逆的凹痕直接影响整个管系的安全性与寿命,对蒸发器的可靠性造成严重影响[3]。主设备制造商应通过顶部支撑板(即变形最大)的监测,找出热处理过程中变形量随温度变化的规律,采取合理的工艺路线、防止“DING”的产生。
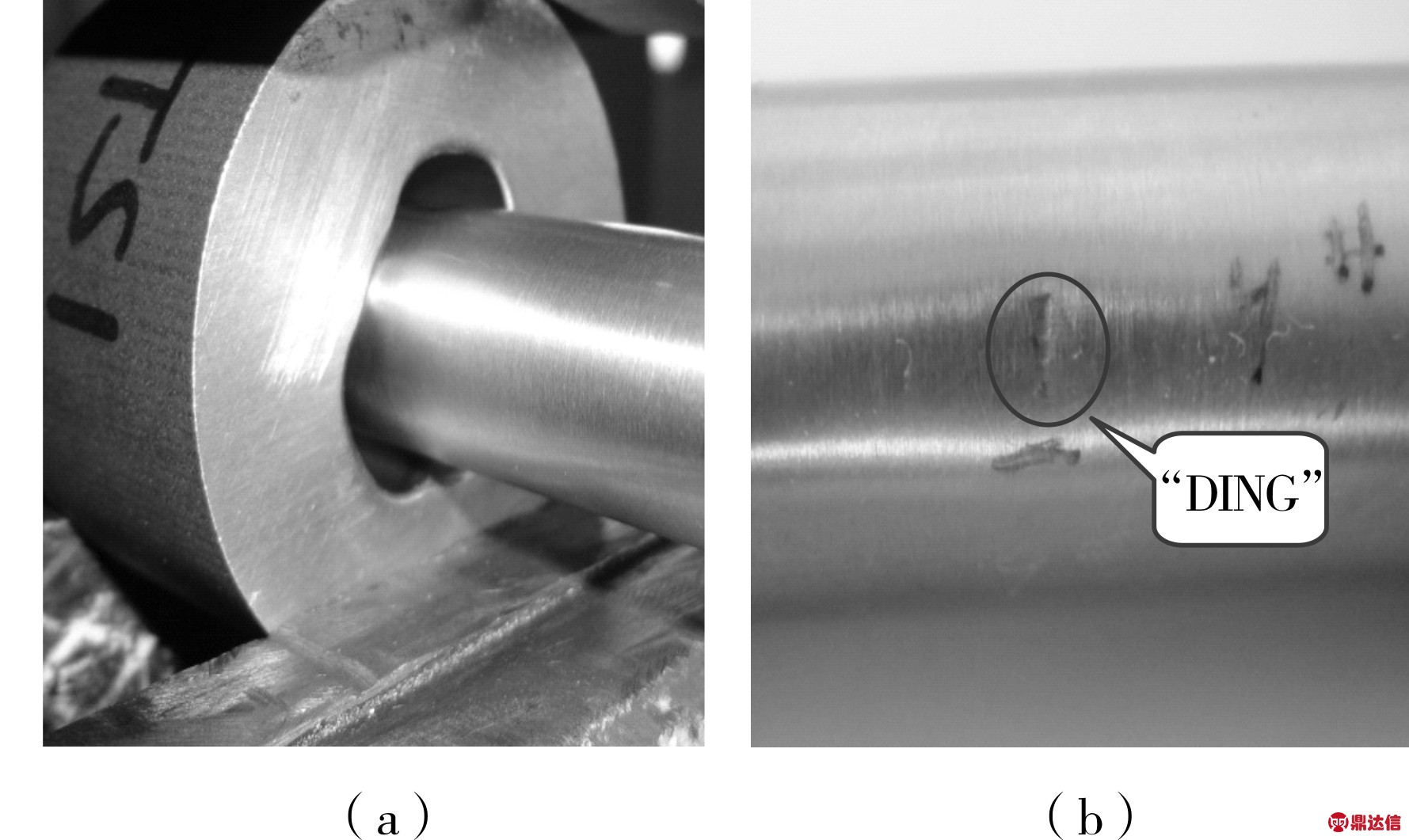
图1 “DING”的形成示意
1 测量方法
在整个局部热处理过程中,蒸发器水平放置并保证管廊轴线水平,对顶部支撑板的水平和垂直方位选4个点进行标识,通过上、下、左、右方位的变形监测来确定角位移变化。
1.1 检测工具
HCA28探头 2个,HCA500数据采集仪 2个,DAM200监测仪 1台,DGB-5B智能电感测微仪,6PG/A型电感式传感器(测头)[4]。
1.2 上、下方位的变形检测
(1)在支撑板的边缘与管廊轴线成90°,相隔180°的2处各放置2个高精度数字输出型单轴倾角传感器,2个作为主测量仪器,2个作为备件。
(2)根据传感器的结构特点,使用工装[5](见图2)与传感器的顶部触头旋合后,通过工装预留孔从锥体的大端送入,传感器通过磁铁紧密贴合于上部支撑板表面,测量开始前仪器清零。
(3)将HCA28探头、HCA500数据采集仪及DAM200检测仪通过连接装置进行连接。
(4)热处理过程中,每隔30 min记录一次HCA28探头所在部位支承板倾斜角度。
(5)热处理结束后,将采集的数据通过计算机导出,拟合出支撑板变形量随时间及温度变化的曲线。
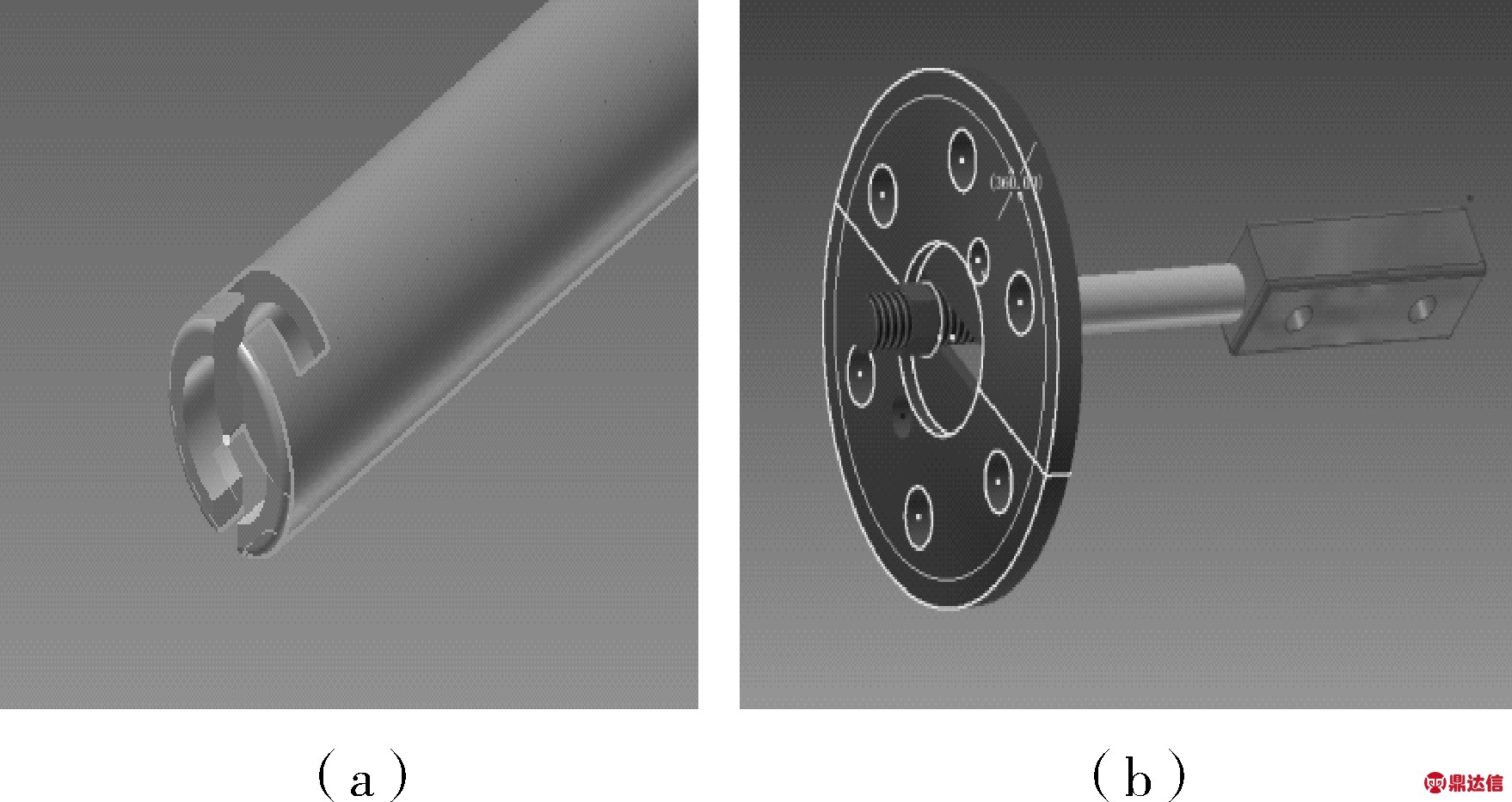
图2 传感器和测微仪辅助固定工装
1.3 左、右方位的变形检测
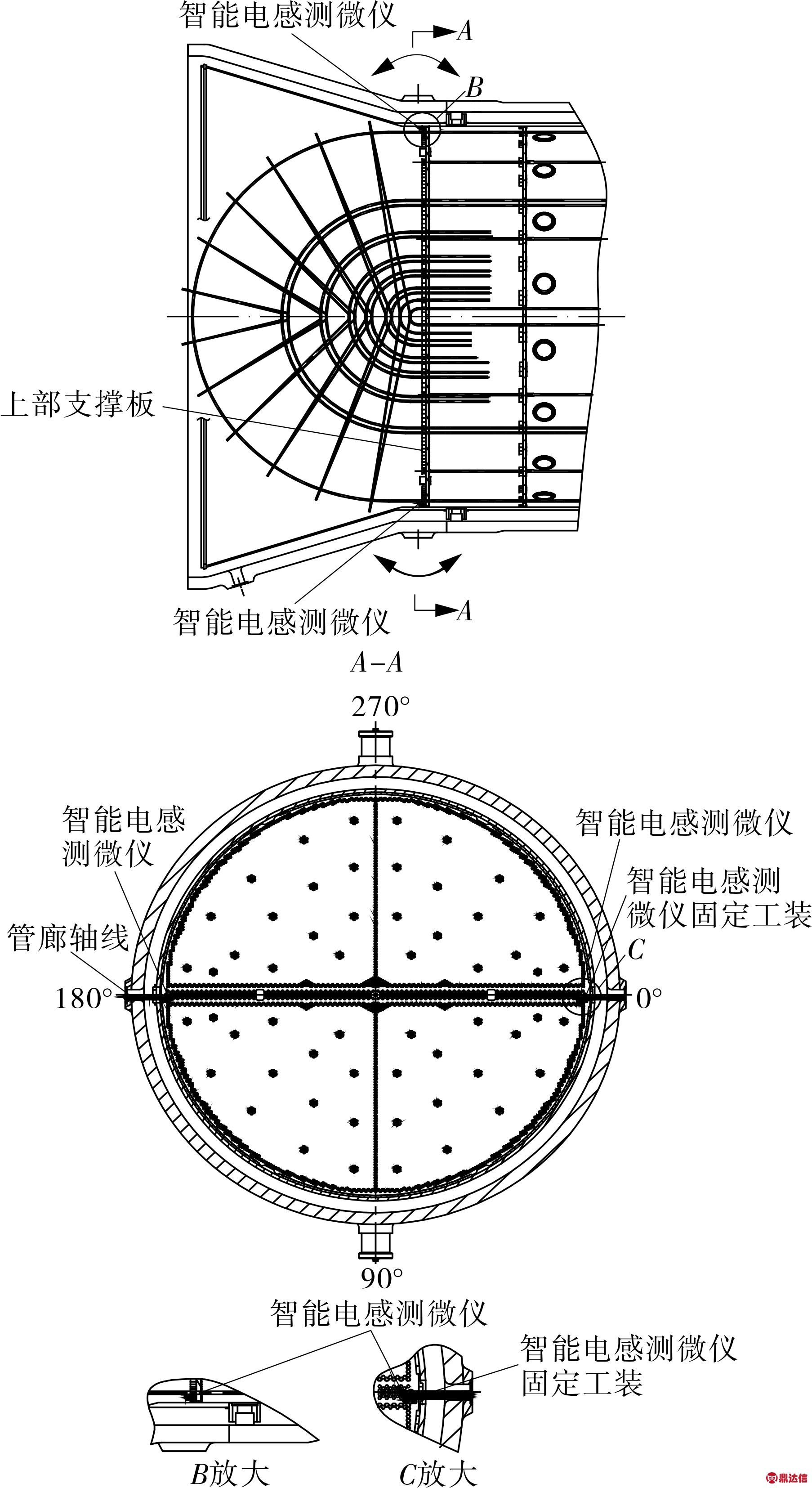
图3 测微仪固定位置示意
(1)通过支撑板管廊轴线0°和180°方向的2个手孔布置2台智能电感测微仪。
(2)在热处理过程中,电感测头需始终接触顶部支撑板的表面。使用智能电感测微仪固定工装,如图3所示,穿过上部支撑板的检查孔,沿管廊呈180°放置一组(2个)智能电感测微仪。
(3)开始测量前,必须记录每组测微仪的初始读数A1,A2。记录每组仪器的直线距离L(L≥100 mm),并每隔1 h记录每组仪器读数∣∣。原始角度β和角位移增量α的计算公式如下:
tanβ=(A2-A1)/L
(1)

(2)
2 测量原理
2.1 上、下方位的检测
局部热处理变形检测是通过对顶部支撑板4个方位的检测共同实现的,检测环境要求高温、高精度。由于支撑板安装在二次侧筒体内套筒内部,现场环境空间受限,因而对支撑板上、下方位变形监测选用了一套小体积、高精度远程控制倾角监测系统。该检测系统针对旋转轴与水平面非垂直以及检测空间狭小的情况,设计了一种小体积双轴倾角传感器(见图4)。来实现空间旋转角度的测量。该系统的测量探头采用高精度HCA28倾角传感器,HCA28探头将测量出的原始数据通过数据采集仪,经过运算处理后,将数据包最终传输给检测仪,实现了实时测量传感器输出相对于水平面的倾斜和俯仰角度。
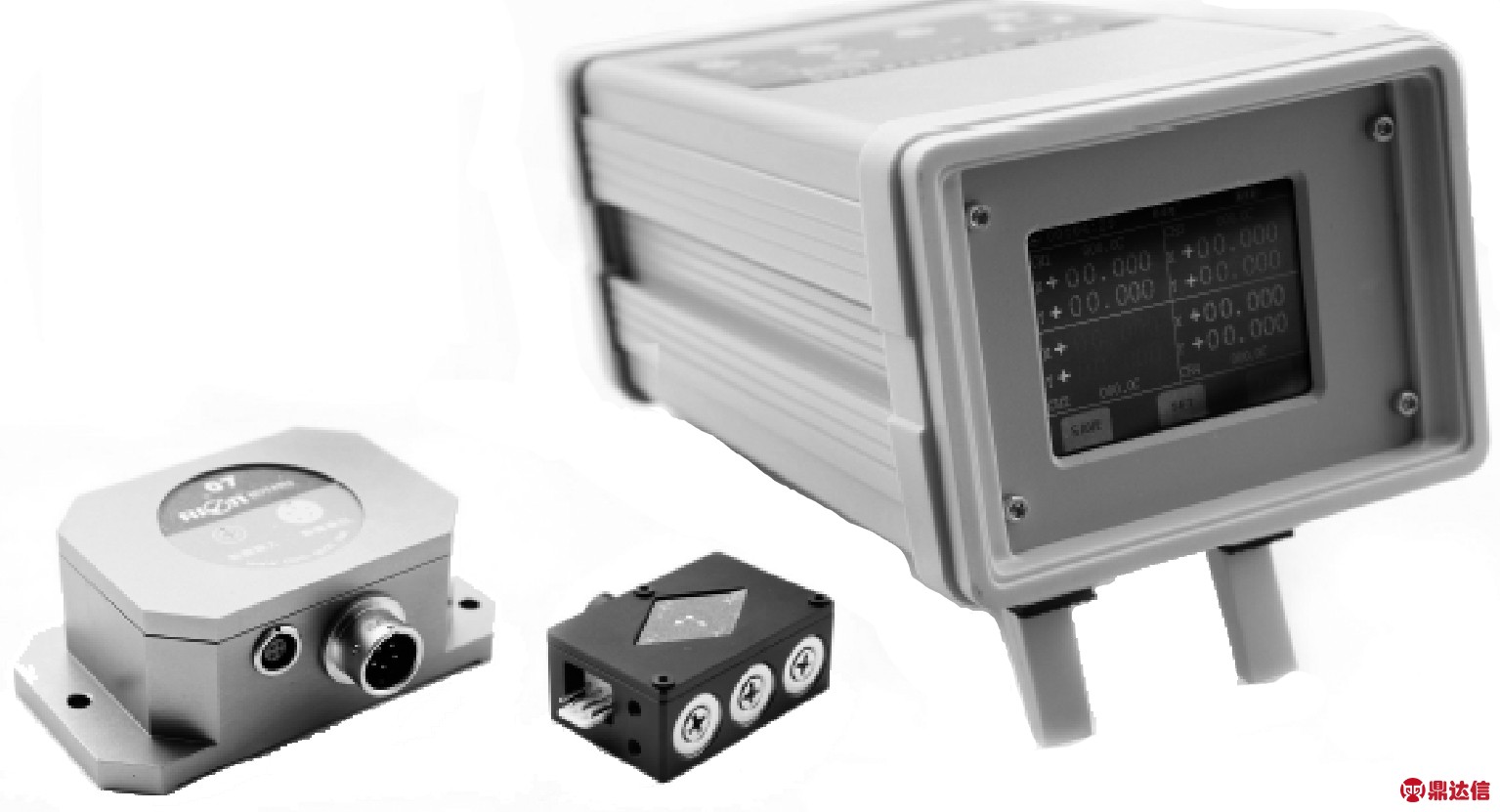
图4 高精度数字输出型单轴倾角传感器
测量探头最高工作温度为125 ℃,体积为45 mm×30 mm×18 mm,仪器的测量分辨率为0.001°角位移增量,量程为±5°,满足支撑板变形上、下检测的全部要求。
2.2 左、右方位的检测
双轴倾角传感器实现空间旋转角度的测量基于摆锤原理,所以支撑板左、右方位的变形监测选用DGB-5B智能电感测微仪与6PG/A型电感式传感器(测量头)组合的测量方法。智能电感测微仪是一种能够测量平面微小尺寸变化的精密测量仪器,由主体和测头两部分组成[6]。
由于管束组件已经安装完毕,同时顶部支撑板始终处于垂直安装状态,导致智能测微仪的电感测头在热处理的过程中无法接触到支撑板表面而且没有可以利用的测量支撑点,通过对顶部支撑板部位的实际测量发现上部筒体的检查孔与顶部支撑板存在一定的结构特点(见图5)。利用此结构特点研制了新型检测辅助工装,该检测工装利用检查孔作为固定点,通过双螺栓进行固定,并利用拉杆确保检测部位的可移动性;同时,智能测微仪上的电感测头也可以固定在如图2的检测卡头上,从而实现检测表面的接触。新型检测辅助工装不但解决了智能测微仪上电感测头在热处理过程中的接触问题;同时也给检测仪器提供了必要的测量支撑点。该仪器分辨度为0.001 mm,测量范围达±0.25 mm,每台仪器共计标配2个电感测头。
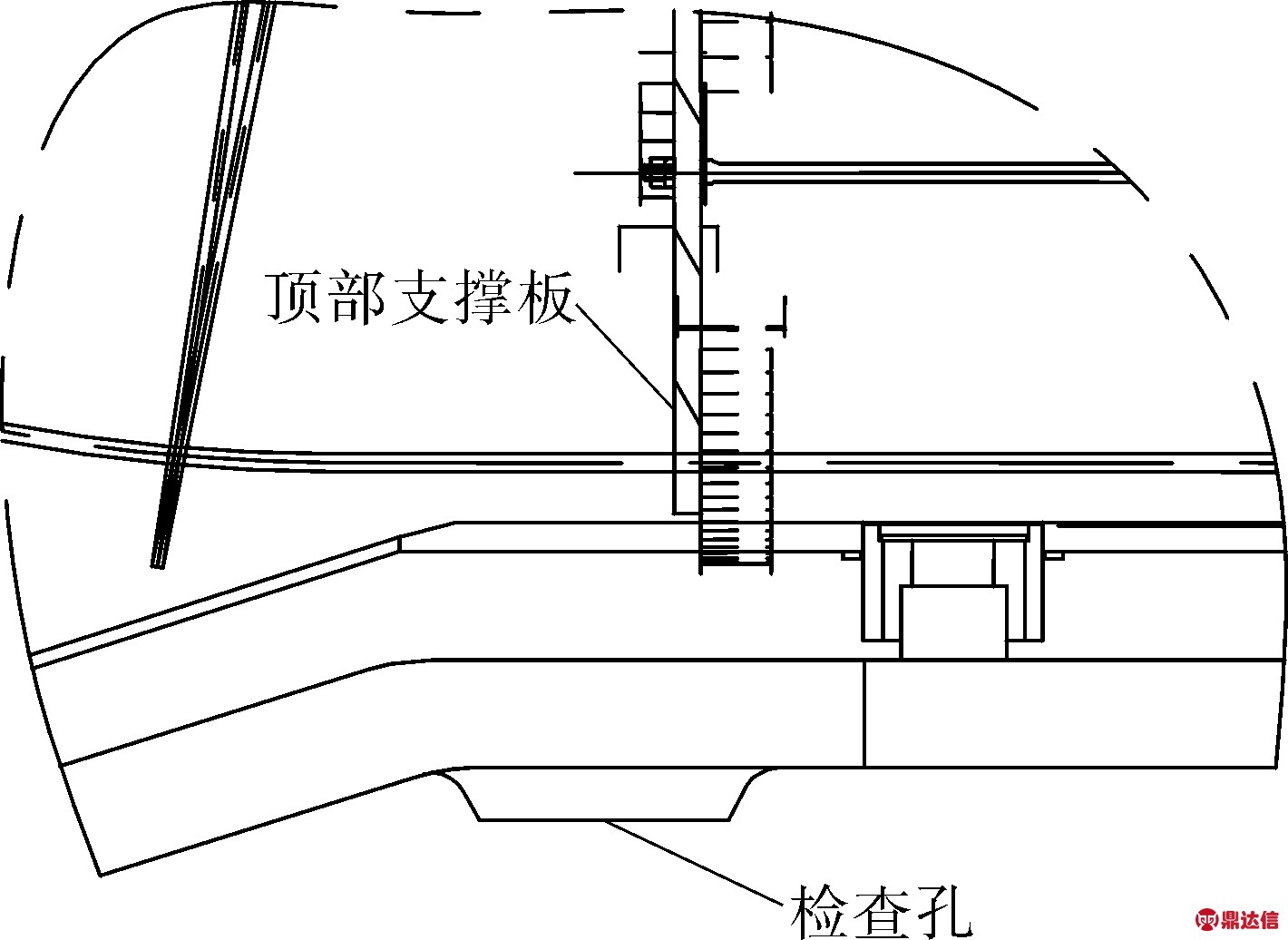
图5 顶部支撑板局部视图
3 二次侧支撑板变形的测量与模拟
3.1 支撑板变形测量数据采集
(1)热处理前,在SG二次侧套筒内将HCA28探头(CH1,CH4)放置于顶部支承板上部与下部位置;
(2)将HCA28探头、HCA500数据采集仪及DAM200监测仪通过连接装置进行连接;
(3)在热处理过程中,每隔30 min记录一次HCA28探头所在部位支承倾斜角度;
(4)热处理结束后,将采集的数据通过计算机导出,拟合出支承板变形量随时间及温度变化的曲线,见图6。
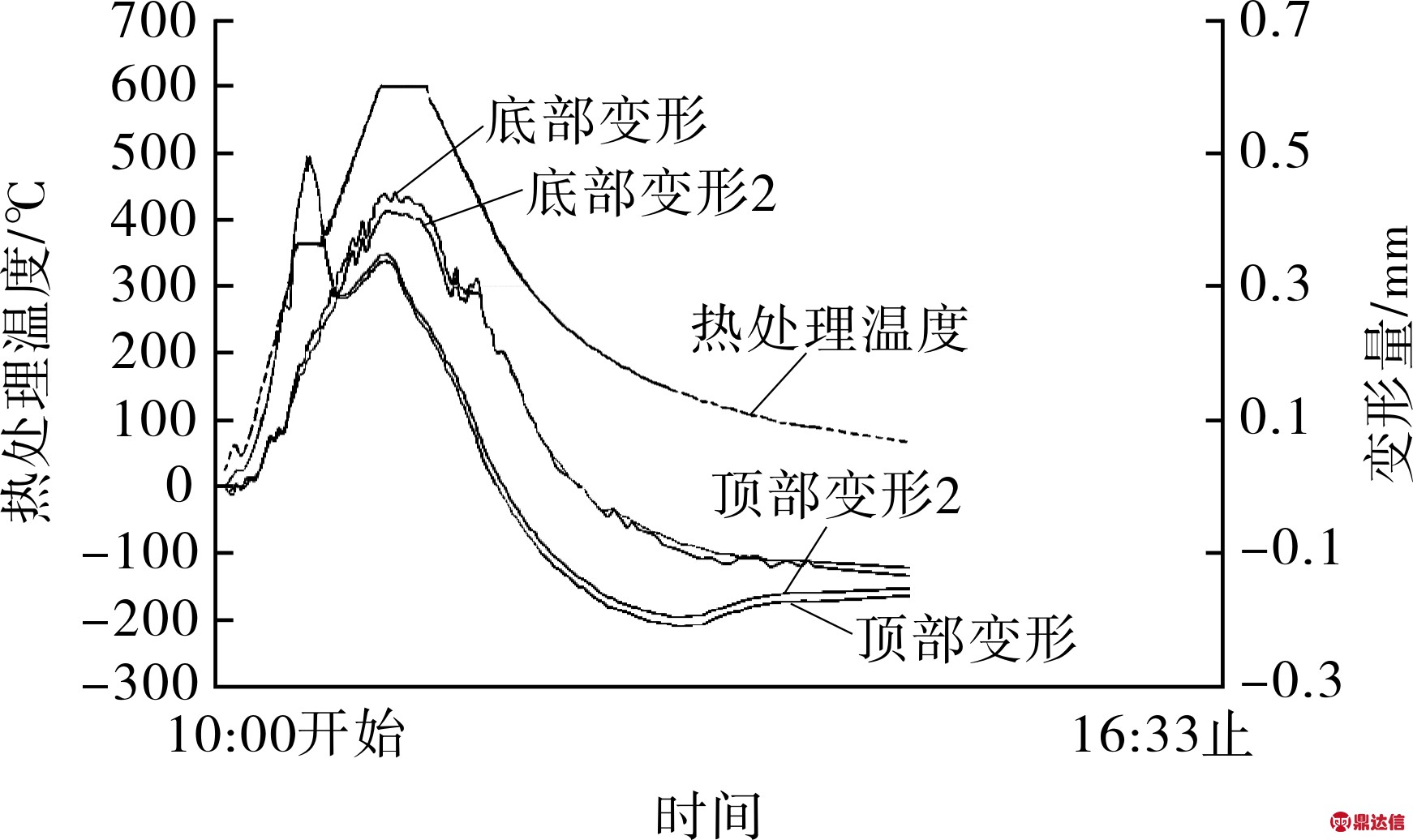
图6 变形量-温度-时间曲线
3.2 支撑板变形的限制条件
最终环缝在焊后热处理期间,如管板一次侧表面受热高于二次侧表面,管板会朝着一次侧表面方向产生变形。与下筒体及套筒相比,拉杆所受热输入量较小,因此膨胀量也较小。支撑板的变形是由拉杆将管子支撑板中心部位拉向管板造成的,当管子支承板边缘承受弯矩时引起边缘角位移。当支撑板相对偏转角超过1.5°将可能发生管子“DING”。在实际防“DING”操作中,支撑板的最大偏转角度按照1°进行控制,留有一定裕度,可有效保证热处理后不产生管子凹痕[7]。当拉杆在焊后热处理加热阶段受热,且在焊后热处理冷却阶段未能足够快的冷却,即产生支撑板向管板的相反方向弯曲。
从拟合的数据可以看出,距离管板最远的支撑板位置,支撑板顶部和底部的变形量随热处理温度的升高而增大,600 ℃时变形量达到最高,偏转角约0.5°。随着热处理温度的降低,变形量减小直至出现反变形,150 ℃左右反变形量达最大,随后变形慢慢恢复。顶部支撑板在热处理过程降温阶段出现反变形,说明拉杆的变形已经完全抵消了管板引起的变形,实际数据与理论分析吻合。通过该数据的反馈,可通过监测热电偶温度及支撑板倾角变化来调整焊后热处理方案。当要求补偿蒸汽发生器不同部件热膨胀量时,则引入空气流冷却二次侧内件。据变形规律,通过空气循环进行冷却或加热,控制二次侧内套筒、拉杆的温度和变形,使TSP的弯曲变形在可控范围内,防止了零部件热膨胀的不均匀产生“DING”[8]。
安装空气通风系统,为避免焊后热处理的热量传递到二次侧,安装风机A从蒸汽出口处向外抽风,同时安装另一风机B,从上部二次侧入口位置向外抽风,开放管板附近的4个手孔,向筒体内引入空气。在整个热处理过程中,风机A和B通过排出上筒体组件内的空气来减轻通过管束和其他内件的气流。热处理阶段使用风机具体使用的开启时段及开口位置的开闭将根据热电偶温度检测数据及支撑板倾角变化进行实际调整。当热处理达到空冷阶段后,停止操作。如果测得顶部支撑板转角超过1.5°,无论处于何种热处理阶段都要停止。在最终达到保温温度,风机流速或方向保持不变。可辅助ECT检测,ECT检查仅需检查顶部两块管子支撑板,基准ECT和确认ECT检查。
综上所述,对产品的质量控制应以提前预防及过程控制为主,在热处理过程中直接测量和控制“DING”的尺寸很不切实际,考虑到“DING”的产生主要与TSP与传热管间的相对变形有关,而监测TSP变形角度具有一定的可行性,因此设计了该试验,希望通过TSP变形角度的监测及时调整工艺方案,从而避免和减少传热管“DING”的产生,必要时配合涡流检测,“DING”预防工艺成功完成。
4 结语
通过对新检测技术和新检测工装的应用,对于支撑板变形监测获得了良好实践,从而给出了热处理过程中支撑板随温度变化而变形的规律,为后续蒸发器制造过程中管子“DING”的防治,提供理论参考。