摘 要:蒸汽发生器支撑板加工质量直接影响后续穿管、焊管及胀管可实施性及难易程度,是蒸汽发生器制造中的关键环节。根据实际制造过程中汇总的经验及相关问题,对CPR1000蒸汽发生器中支撑板钻孔、拉孔及倒角流程进行了阐述,为以后支撑板的制造提供参考。
关键词:蒸汽发生器;支撑板;钻孔;拉孔;倒角
0 引言
蒸汽发生器是将核岛及常规岛分隔的压力边界,其中一回路中放射性冷却剂经进口接管进入水室封头并流入传热管内,管子外围与二回路给水接触通过热交换进行热量传递,同时管子-管板结构有效阻隔了一回路放射性冷却剂进入二回路中[1-3]。
CPR1000蒸汽发生器传热管束采用U型管形式,弯曲部分装有防震条,直管段部分间隔放置支撑板用以固定管束,支撑板上开有四叶梅花孔,这种孔型减少了管子外围与支撑板的接触面积,能使之获得更大流量,而且大大减少了腐蚀物及化学物质的沉积,改善了该区域的腐蚀状况[4-6],但较圆形管孔加工困难,且清理难度较大。
1 支撑板规格参数
CPR1000蒸汽发生器支撑板厚度薄,孔系数量多,加工后精度及平面度要求高(见表1、图1),对机床精度、工艺系统稳定性、刀具性能、加工工装防变形能力要求严格,制造难度系数大、控制水平要求极高[7]。
表1 蒸发器支撑板规格

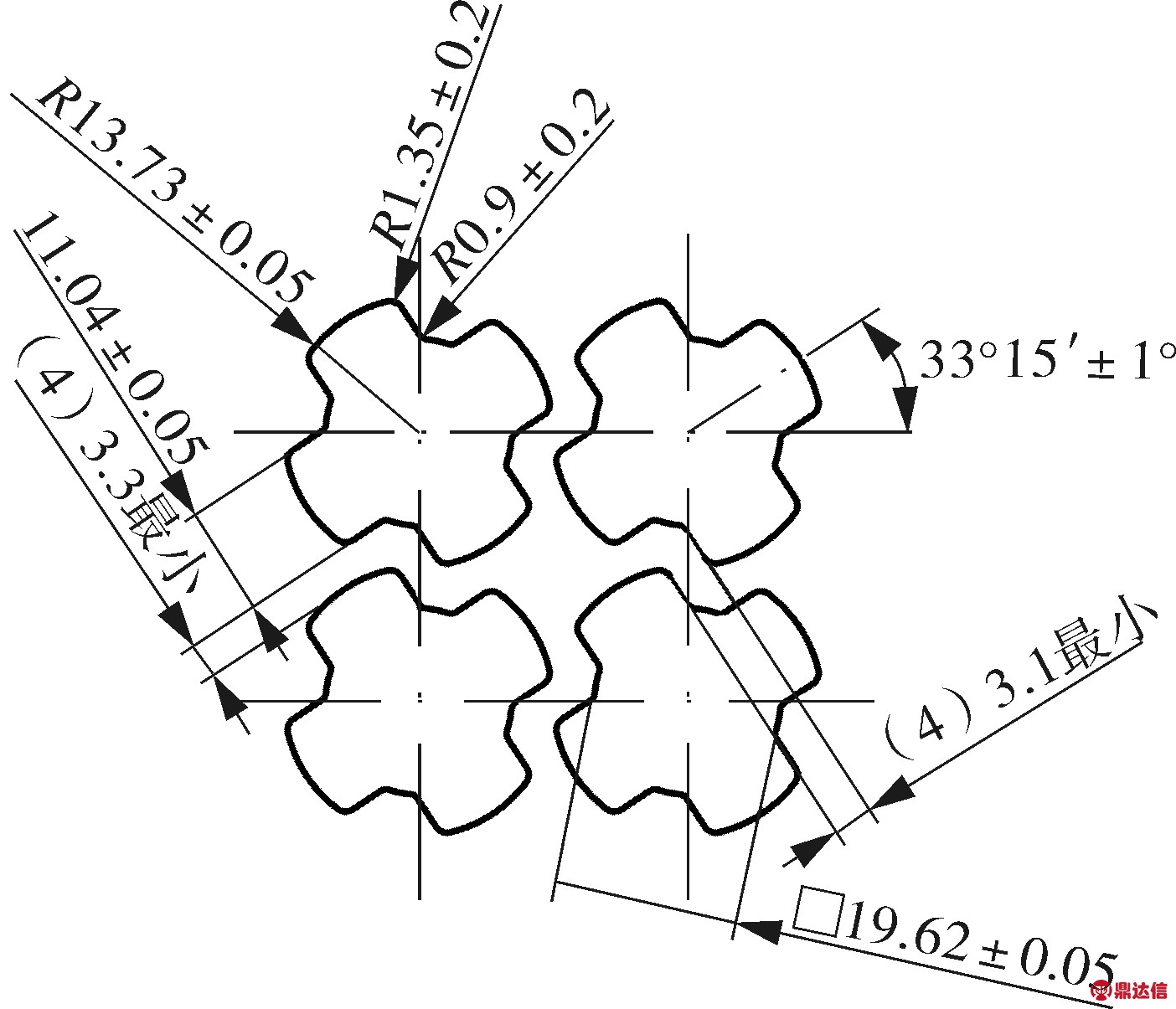
图1 梅花孔尺寸要求
2 支撑板加工
支撑板来料后进行超声波复探,合格后检查记录自由状态平面度,借助胎具进行钻孔,钻孔完毕后再次进行自由状态平面度检查,经清理打磨及自然时效后,在专用机床进行梅花拉孔,清理打磨后进行倒圆角、抛光工序,铣外圆及键槽符合图纸要求,然后进行最终检查,全部合格后清洗包装放入专用存放架内。
2.1 支撑板钻孔前准备
采用龙门式六轴立式数控钻床进行支撑板钻孔加工,最大加工工件直径达φ6000 mm,最大钻孔深度达300 mm,钻孔精度达IT9级,粗糙度达Ra3.2,位置度偏差±0.10 mm,钻削刀具采用U钻。加工时六轴同时进行,为保证同一行不同轴所钻孔的位置度要求,加工前首先进行机床Y向直线度检查。
工字型平尺平行于机床Y向放置于工作台中间,且工作面处于竖直面(见图2)。首先3#主轴百分表表头接触平尺工作面两端进行找正,注意全行程为4975 mm,然后各轴分别在全行程范围内测量(见图3)。
由于支撑板厚度小,在钻孔时受力易变形,难以保证钻孔后的平面度要求,因此设计了专用胎具用于实现找正、装夹固定及防变形需求。胎具由底平板、支撑垫墩、螺纹垫墩及周边顶紧器组成,4个周边顶紧器用于找正及防松,支撑垫墩和螺纹垫墩上面铣平共面,靠把装在螺纹垫墩内的螺钉及周圈均布的压板将支撑板预紧固定。把合原则:周边压板把合时首先把合高点处螺栓,其余按对称点成对把合;螺纹垫墩内的螺栓待支撑板钻通一个孔后立即把合该孔(见图4),待所有螺栓把合后,松开压板及顶具按从中心到周边的顺序对所有把合螺栓进行相应的最高预紧力把紧。
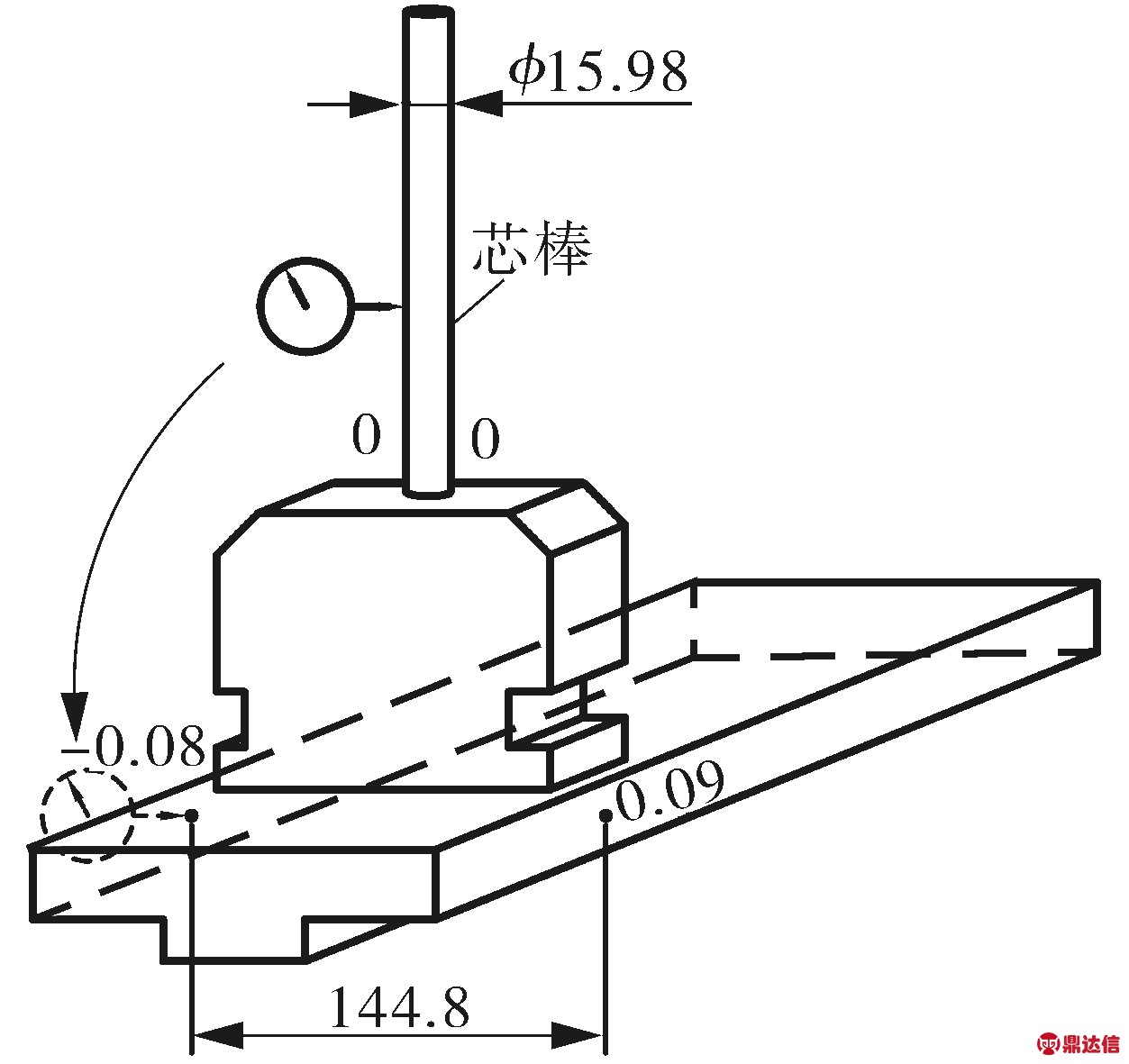
图2 Y向直线度测量示意
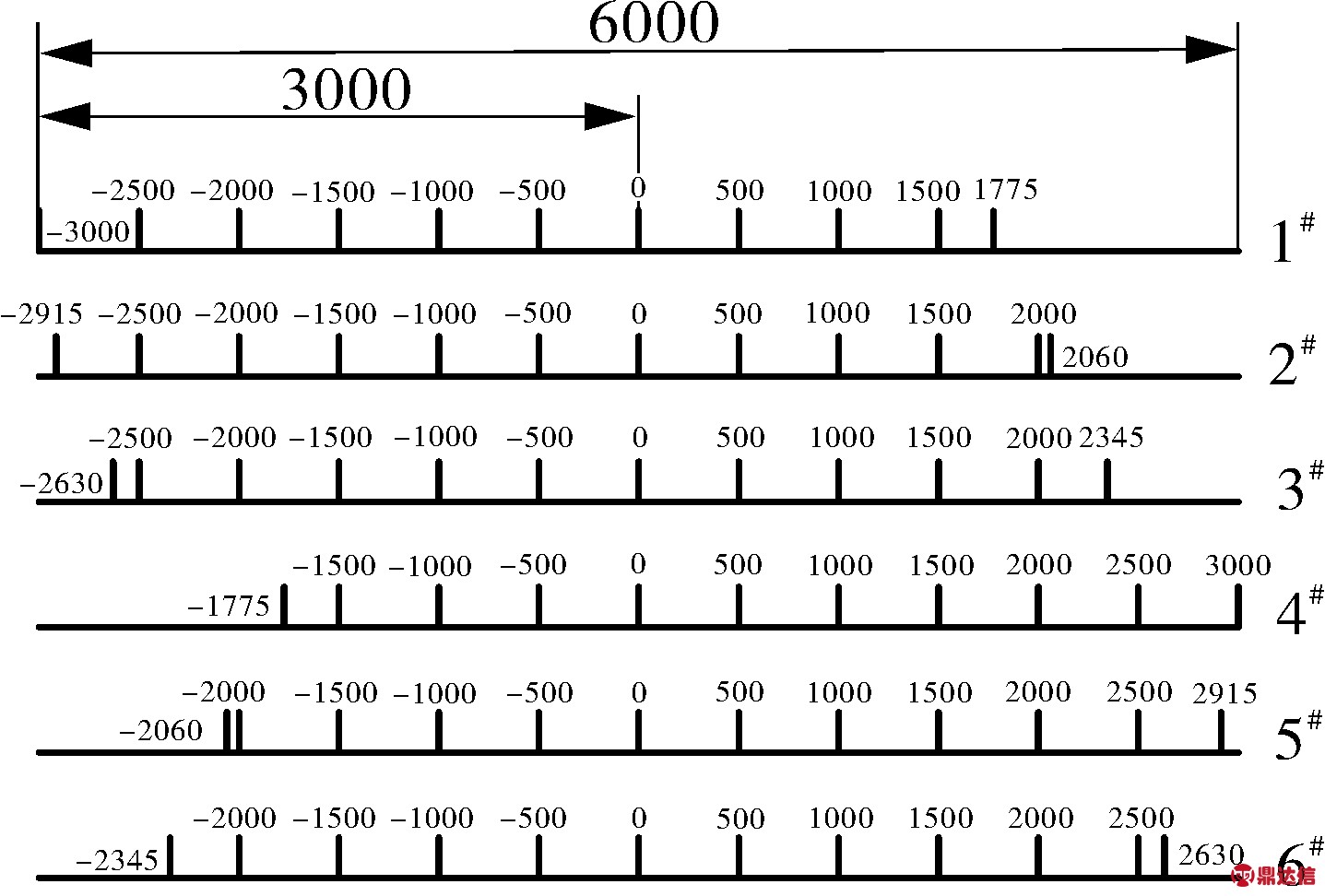
图3 各轴测量点位
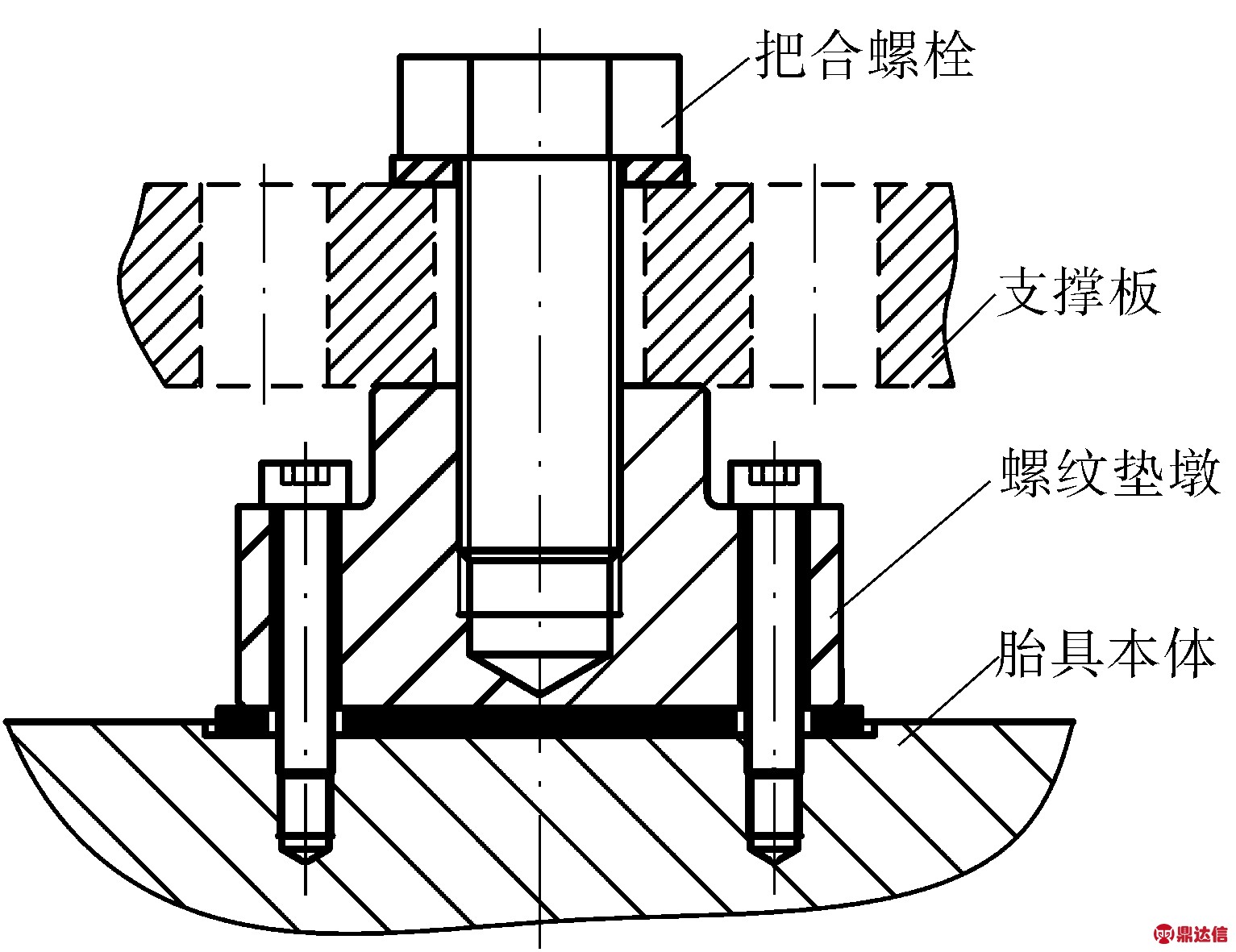
图4 支撑板与胎具把装图
2.2 钻孔流程
装夹把紧后,检查并记录支撑板夹紧后的平面度,正式钻孔流程如下:
(1)在试验件上钻一列孔,检测并记录其X、Y两向偏差及孔径,确定轴间距满足加工要求;
(2)精镗基准孔,进行切削参数试验,调整切削参数,直至钻孔精度和切削满足要求,经过试验后推荐参数n=3300 r/min,f=135 mm/min;
(3)在支撑板上钻首行孔,检查记录首尾孔X、Y两向偏差;
(4)执行专用钻孔程序,每班次加工前要重新校对工件零点,检查记录首行孔X、Y两向偏差、每100次循环更换刀片并抽检孔径孔桥及粗糙度;
(5)扩钻把合孔,用寻边器按照把合各孔周围X、Y向4个相邻孔定心,记录各孔4个相邻孔直径,保证孔位置合格;
(6)通止棒、孔距检测仪检测所有孔径及孔桥,目视检查粗糙度;
(7)机床打表检测所有列首尾孔X、Y两向偏差;
(8)检查记录自由状态平面度。
2.3 钻孔过程控制
(1)专用胎具按规程规定的预紧力矩把合压紧支撑板;
(2)钻孔程序首次使用前,所有孔用专用打点器进行打点试验,所有孔位合格后方可在支撑板上进行钻孔;
(3)钻孔中按班次轮流、对称进行90°侧和270°侧区域的钻孔,保证工件残余应力均匀释放,以避免工件已钻孔区域变形造成孔径和位置度超差。
(4)加工支撑板的周边刀片使用寿命不超过100个孔/钻孔循环,中心刀片不超过200个孔/钻孔循环。
2.4 支撑板梅花拉孔
拉孔采用行星滚柱丝杠立式内孔拉床,拉刀通过拉刀提升装置及拉头完成拉削加工(见图5)。拉削最大加工范围φ4800 mm,加工最大工件厚度40 mm,该拉床的夹持装置对拉削变形能起到很好的控制作用。
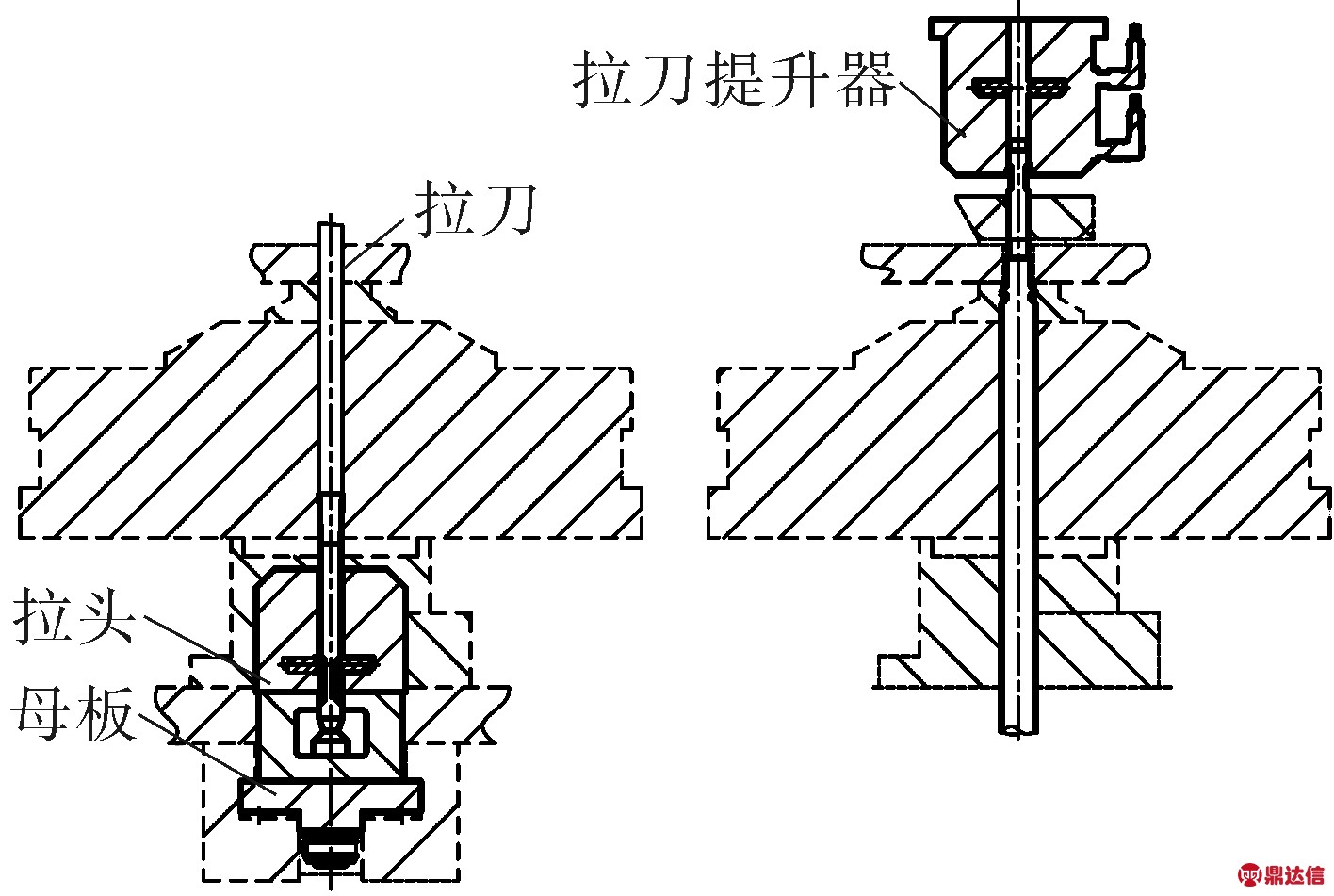
图5 拉刀拉下-提升安装示意
加工产品前,对机床进行精度检测时发现拉头孔中心连线与Y轴平行度超差为0.5 mm,而工艺要求机床精度为0.1 mm,属于严重超差。因拉头结构由6个单独的集成块组成,各拉头没有调整结构,仅靠本体的定位孔一次性定位,从设计原理上来讲,不需要重新调整,因此从本体定位孔的制造精度来排查精度影响因素。
使用高精度立式加工中心检测拉床拉头,检测所有拉头包括备件的倾斜及偏心情况。
检测拉头倾斜操作步骤:
(1)母板按端面找正(见图6),平面度0.02 mm以内,Z向旋转0 mm;
(2)将拉头下端φ30 mm定位销装入母板上与之配合的定位孔,拧紧底部螺栓,保证装配牢靠;
(3)复检母板各项找正精度;
(4)将机床厂商提供的芯棒装入拉头定位孔,用百分表检测芯棒垂直度偏差,上端清零,拉至母板宽度方向两端面位置,记录百分表读数,其中检测芯棒有效长度250 mm。
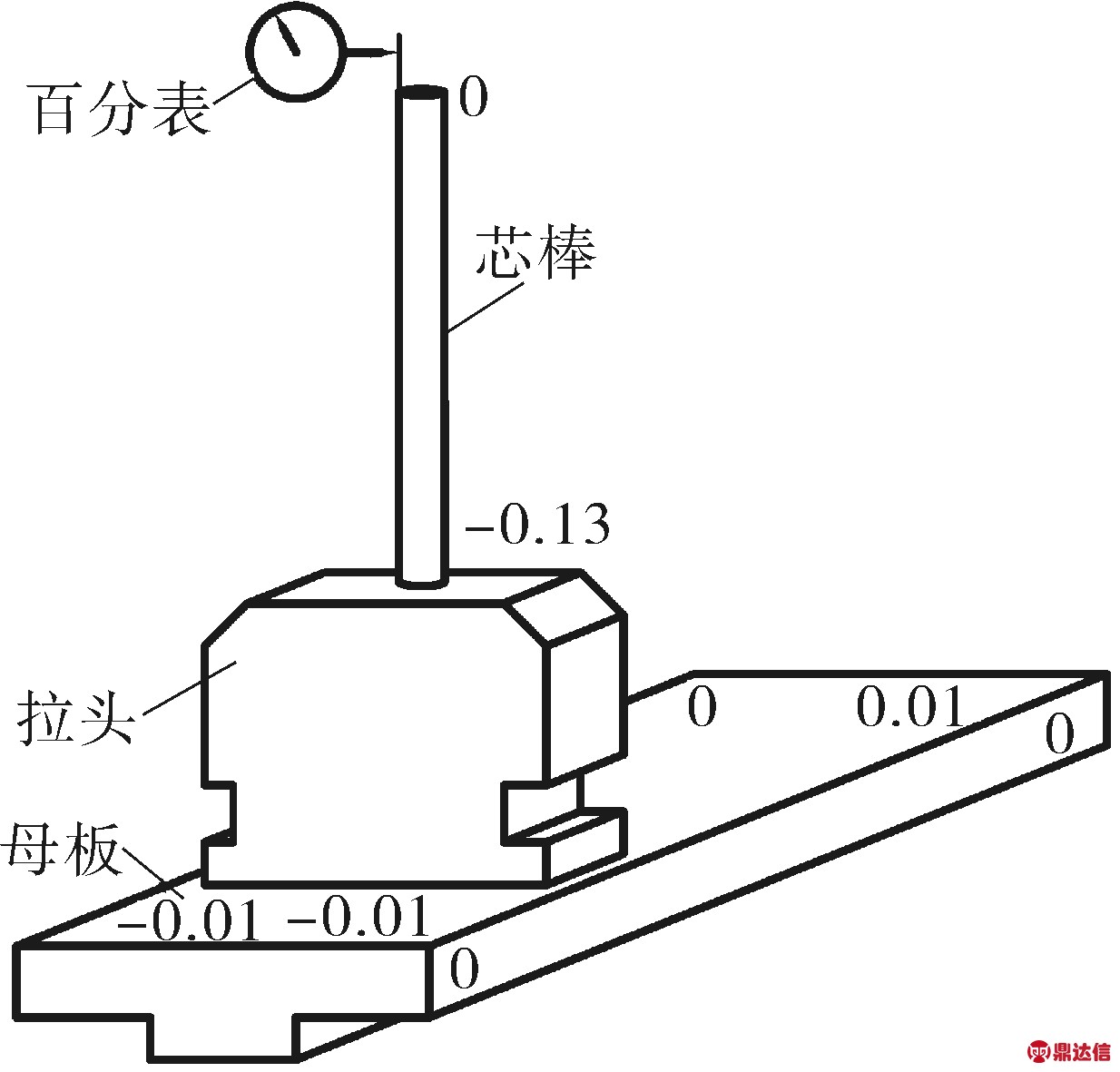
图6 拉头倾斜检测
接上步检查进行拉头偏心检测,例如其中一个拉头的数据:测量出芯棒直径(φ15.98 mm)及母板宽度实际尺寸(144.8 mm),用百分表分别在芯棒两侧压表清零,向母板两侧移动相同距离(64.41 mm),表显分别为-0.08 mm和+0.09 mm,得出拉头定位孔中心偏心0.085 mm(如图7所示)。
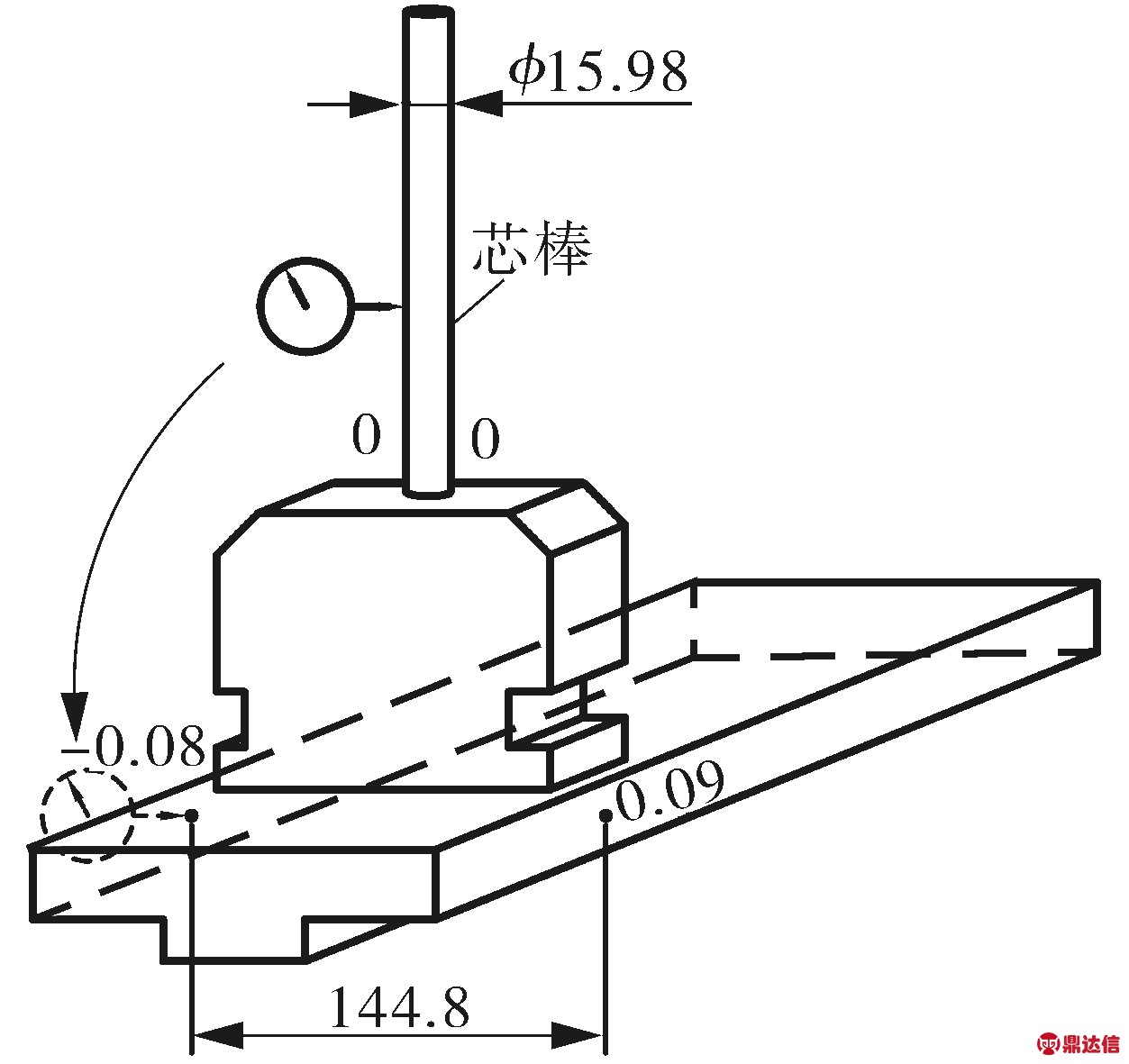
图7 拉头偏心检测
按上述方法对18个拉头偏心情况进行测量与记录,挑选出制造误差最小的6个最优品进行组合,组合后的6个拉头倾斜和偏心误差0.1 mm以内,满足设备精度要求。在实际生产中,要求每班次拉表检查拉头孔中心连线与Y轴平行度,超差则停机汇报。
为了保证拉刀重磨后所拉梅花孔的光洁度及各项尺寸要求,规定新拉刀最大重磨次数为10次,每次重磨后寿命为1100~1500孔,重磨后必须进行拉削试验。
2.5 倒角及抛光
在龙门立式抛光机床上进行支撑板倒角及抛光加工,支撑板依靠定位销、基准销及顶具在机床上找正装夹,倒圆角前需用钩型深度卡尺测量并记录支撑板厚度。
加工前,用与蒸发器支撑板同规格的试验件进行倒圆角试验,以选择合适的毛刷完成支撑板去毛刺、倒角。Y轴(滑台水平移动方向)行进速度900 mm/min,X轴(龙门纵向移动方向)行进速度75 mm/min,毛刷轴自转转速2000 r/min,公转转速低档。去毛刺刷Z向(刷头垂直方向)补偿:Z=0.02 mm/2 min,倒角刷Z向补偿:Z=0.1 mm/15 min。
(1)使用工具:机床自带毛刷(8支)+改进前国产毛刷(4支),毛刷竖直状态旋转。使用机床自带毛刷累计打磨时间110 h(达到去除飞边毛刺、棱角倒钝效果);改进前国产毛刷累计打磨时间20 h,支承板中心部位孔端圆角达R0.8(如表2所示)。
表2 打磨时间及圆角尺寸(1)
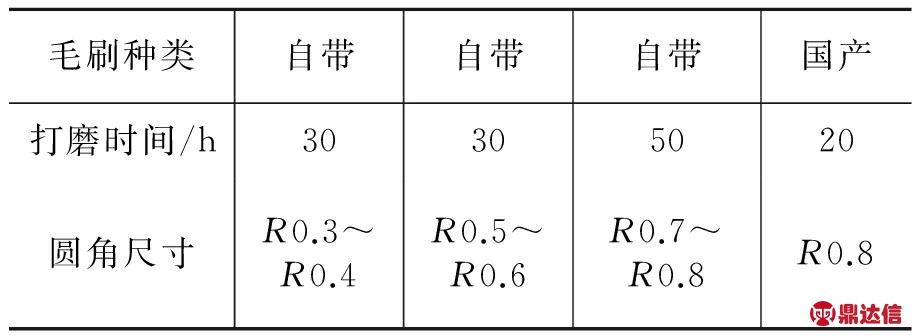
(2)使用工具:国产钢丝刷(4支,刷丝直径φ0.3 mm)+改进后国产磨料刷(4支,刷丝直径φ1.85 mm),毛刷竖直状态旋转。使用钢丝刷累计打磨时间20 h;使用磨料刷累计打磨时间31 h,支承板中心部位孔端圆角达R0.8(见表3)。
表3 打磨时间及圆角尺寸(2)
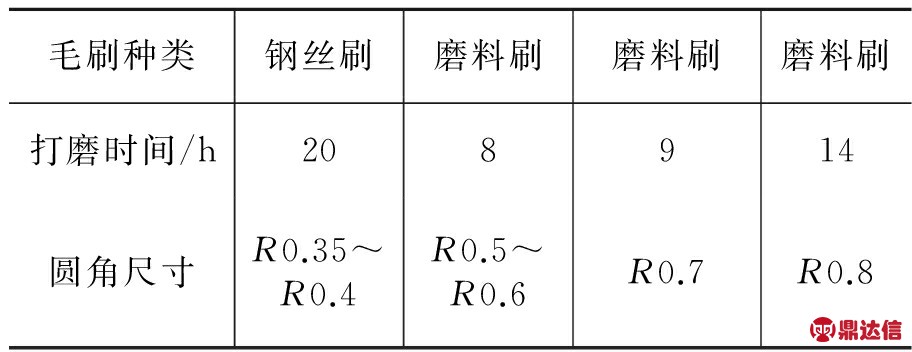
(3)使用工具:钢丝刷(刷丝直径φ0.3 mm)+细磨料刷(刷丝直径φ1.65 mm)+粗磨料刷(刷丝直径φ1.85 mm),毛刷由竖直状态旋转变为倾斜状态,使毛刷端面与支承板端面成固定夹角。使用钢丝刷打磨时间共计7 h(达到去除飞边毛刺、棱角倒钝效果);更换细磨料刷(刷丝直径φ1.65 mm),细磨料刷打磨时间共计30 h,支承板中心部位孔端圆角达R0.6~R0.7;更换粗磨料刷(刷丝直径φ1.85 mm),粗磨料刷打磨时间共计14 h,支承板中心部位孔端圆角达R0.8(如表4所示)。
表4 打磨时间及圆角尺寸(3)
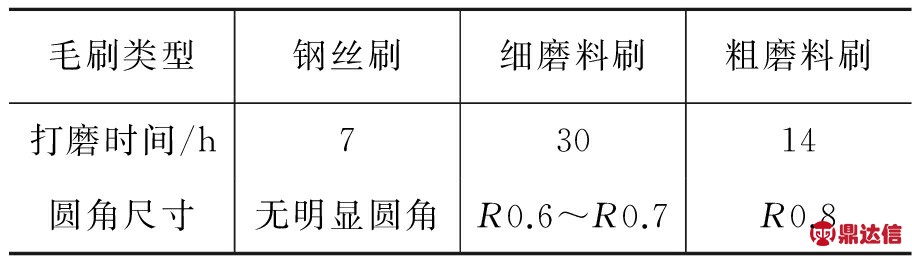
(4)磨料丝粒度改进,由原来46目改进为36目,发现磨料丝回弹性能及打磨加工效率提高。
(5)钢丝刷(刷丝直径φ0.5 mm,减小了钢丝密度,以增加钢丝刚性和回弹性能),磨料刷直径φ1.85 mm,粒度36目。钢丝刷打磨8 h,磨料刷打磨40 h。
根据试验结果,选用直径φ0.5 mm的不锈钢钢丝刷和直径φ1.85 mm,粒度36目的磨料刷进行打磨。支撑板一次侧、二次侧打磨后,需分别用钩型深度卡尺测量并记录支撑板厚度。中间过程中应注意观察,防止局部打磨过重,使得区域厚度减薄。由于钢丝刷的作用仅起到倒钝作用,用过一遍之后,刷丝端部即被磨圆,再用时很难起到倒钝作用,规定钢丝刷的使用寿命不超过1块支承板,以此提高钢丝刷的打磨效率。对一块支撑板倒圆角时,共计消耗4组磨料刷。使用内孔抛光刷对所有内孔进行抛光操作以达到图纸粗糙度要求,使用寿命约为2块支撑板,使用时应及时更换。
3 结语
通过总结支撑板制造过程中遇到的问题,不断地完善及改进支撑板的各加工工步,结合专用工辅具进行辅助制造,保证了支撑板钻孔、梅花拉孔及倒角抛光的制造精度,并大大地提高了生产效率。