摘 要:由于现有印制电路板采用飞针或针床的接触式短路检测方法,存在着IC接触点小和检测区域受限两个主要弊端。本文开发出以电磁感测的非接触式印制电路板短路检测系统,该非接触式检测系统利用虚拟仪器LabVIEW将硬件和软件互相整合,将待测印制电路板某区域加上一定电压的正弦波信号,然后利用电磁感应探头测量印制电路板的电磁场密度分布情况,从而获取电路短路或开路的位置。该电路板短路检测系统通过实验证明,能够较准确发现电路板短路导线的位置,为印制电路板短路检测提供了新的方法。
关键词:LabVIEW; 印制电路板; 非接触式; 短路; 电磁感应
0 引 言
印刷电路板制作过程中,常见有因制作工艺问题而造成某两条不应该连接在一起的两导线短路,从而造成电子产品工作不正常甚至电源烧毁。一般业界常见的方式是采用飞针测试或针床测试等探针进行接触式测量[1],查找短路故障点。然而现今的集成电路(IC)的体积越来越小,印刷电路板上其引脚越来越细,引脚间距越来越小,已接近探针的极限,同时检测空间也受限于机械手臂的工作范围。
本文提出一种电磁感测的非接触的方式进行印刷电路板走线短路检测的方法,该方法是通过检测印刷电路板电路的短路与开路时电流产生电磁场的变化数据实现的,能够解决元件引脚体积和间距的限制,同时解决工作区域范围受限的问题,从而突破探针接触式检测的局限。
1 电路板检测系统整体设计方案
本设计采用NI公司整合式硬件,通过虚拟仪器LabVIEW将各个功能模块整合在一起,达到预期设计的目的。系统主要由人机操作界面模块、数据采集模块、四轴马达控制模块和感测器模块4个功能模块构成[2],如图1所示。
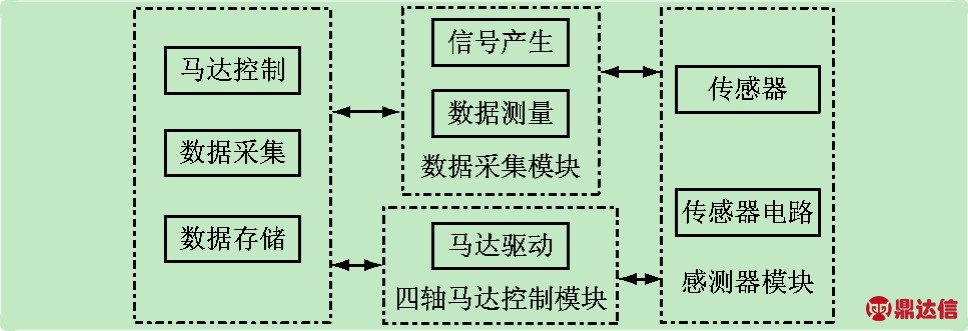
图1 电路板检测系统功能模块
1.1 人机操作界面模块设计
人机操作界面的前面板如图2所示,主要完成马达控制、数据采集和数据存储[3]。
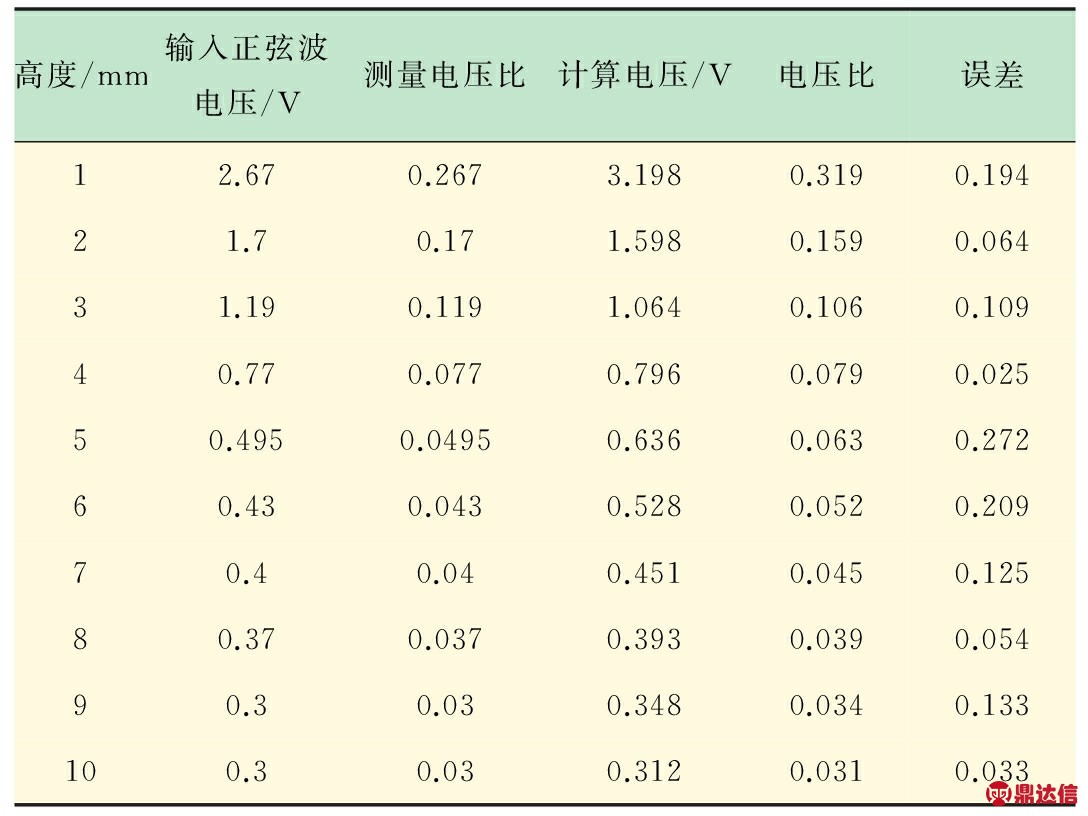
图2 人机操作界面
1.1.1 马达控制
电磁感应探头对电路板的扫描位置控制,由4组步进马达控制X方向、Y方向、Z方向与旋转角度,以实现使用者对电路板不同测量点的移动与测量。利用LabVIEW图形化[4]设计将图片、控制物件与显示物件整合在一起,让使用者可以更容易地了解操作方式,如图3所示,操作者可以直接修改所要达到的位置坐标。系统的X、Y、Z行程分别为200 mm×200 mm×50 mm,再加入了1个可以空中旋转马达,可以使感测器测量不同方向的导线。本设计使用PCI-7354做为马达控制卡与接线盒,并将其整合至系统内。
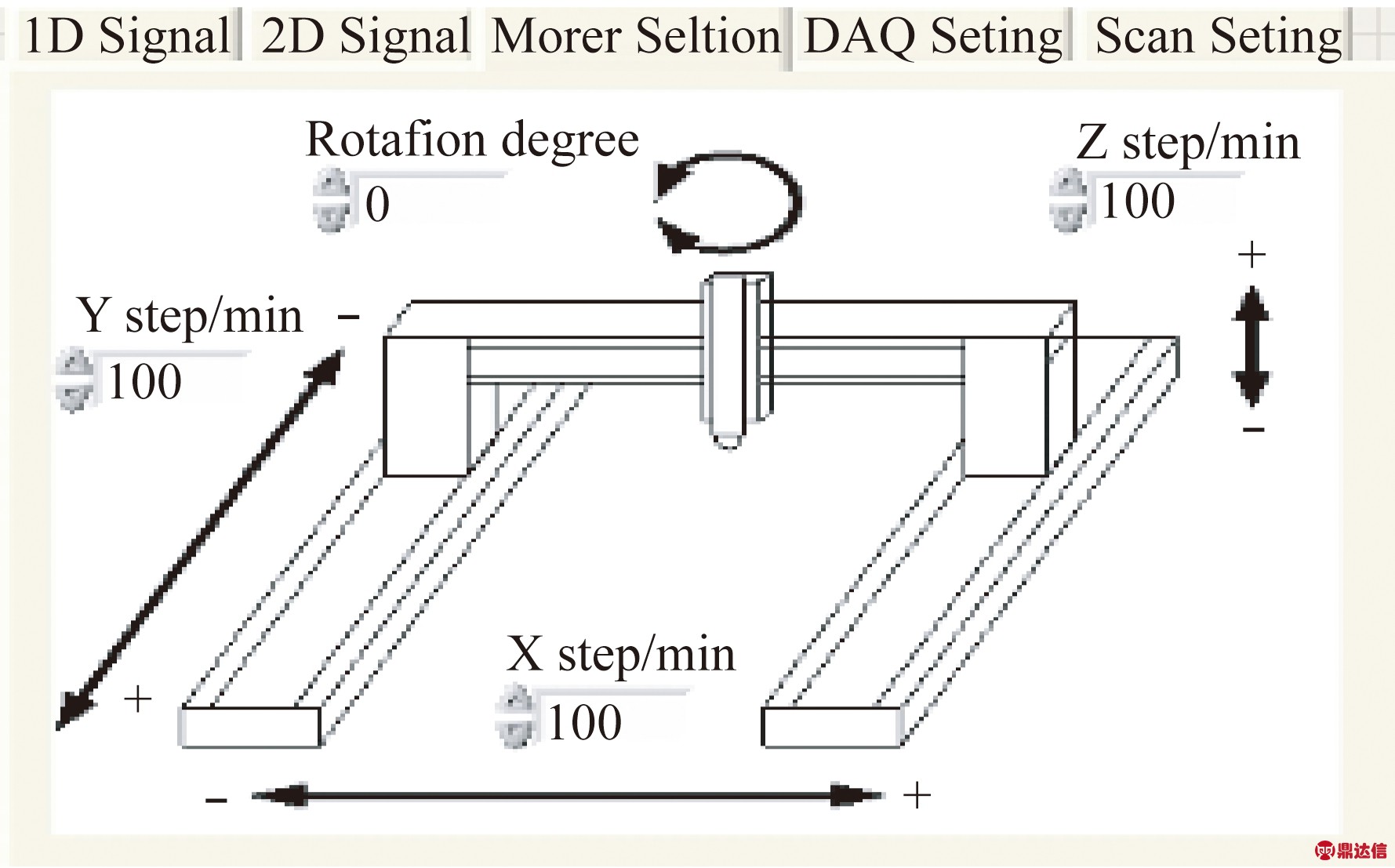
图3 马达控制界面
1.1.2 信号产生、采集和存储
非接触式电路板短路检测系统需要提供一个正弦波信号源,输入至待测印制电路板,再透过感测器量测感应的电磁信号。正弦波信号源参数设定可以由使用者自行调整频率与振幅,同时使用者根据选择感测器类型,让系统自行计算并输出合适的频率与振幅。
本文使用NI自行定义的TDMS(Technical DataManagement Streaming)的储存格式[5],因其具有使用者能够自行定义信号的属性及加快存取速度的优点。TDMS可以与最常用的Excel与Matlab互通,具有很好的扩展性。
1.2 数据采集模块设计
使用NI DAQ X系列的多功能信号采集器[6],提供一个稳定的正弦波信号源,并流经电路板导线系统后通过感测器再将产生的电磁场信号读取回系统,然后通过LabVIEW软件分析处理。并采用NI USB-6356做为信号产生与收集电路。
2 非接触式短路检测原理与物理模型
2.1 电磁信号端物理模型
本文提出的测量方法基本原理是电磁感应,由法拉第定律设计物理模型,图4为电流与其产生磁场的关系,图5为感应探头测量磁场的示意图,印制电路板导线短路的情况下,电流在流过的短路部分的长度范围内产生电场E或磁场B。磁场的强度与短路导线的长度和位置有关,并可由毕欧沙瓦定律(Biot-Savart Law)描述[7]:
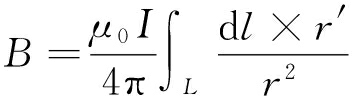
(1)
其中:L是导线长度的总和;dl是电流的向量;μ0是磁性常数;r是dl与电场计算的距离;r′为r单位矩阵向量。式(1)中表示出电流I与磁场B或电场E成正比,与距离r成反比,其电磁感应如图4、6所示。
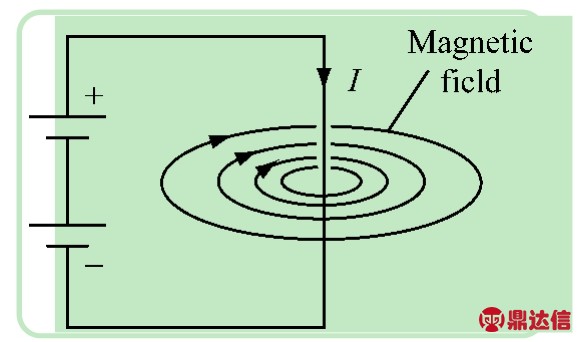
图4 电流与产生磁场的关系
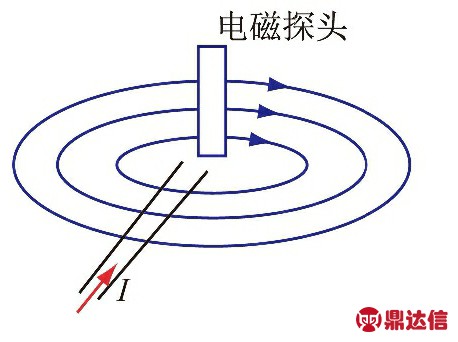
图5 感应探头与磁场的关系
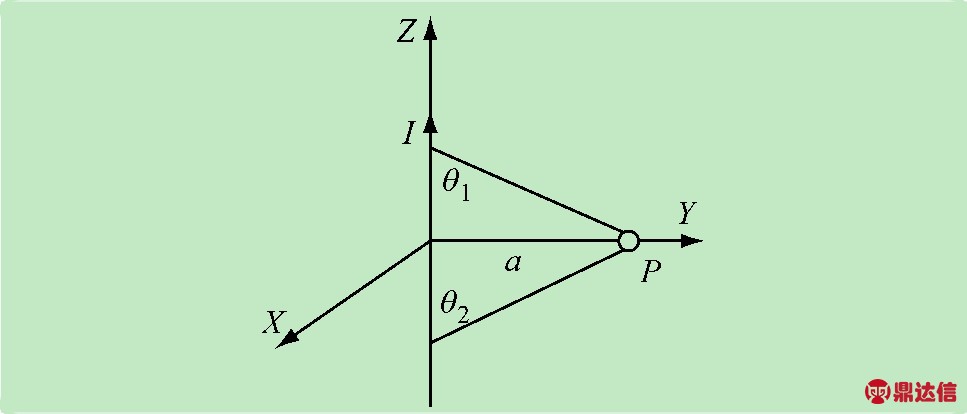
图6 磁场总量示意图
电流流经的路径会产生电场,其总磁通量可以分割成几部分的叠加,得到的总磁通量密度[8]:
B=∫dB
(2)
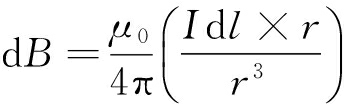
(3)
磁场总量的示意图如图6所示,有限线段电流I流过区域所产生在P点的磁场,其总量为不同角度θ与距离a的总合量[9],可推导整理成:

(4)
2.2 测量感应端的物理模型
非接触式测量重要的元件为电感,电感线圈可以感应到磁场能量并产生相对应的电压或电流,此信号作为后续系统测量与分析使用。磁场与电流的关系,可由毕欧沙瓦定律推导出。最后,推导出输入与输出的关系式为:
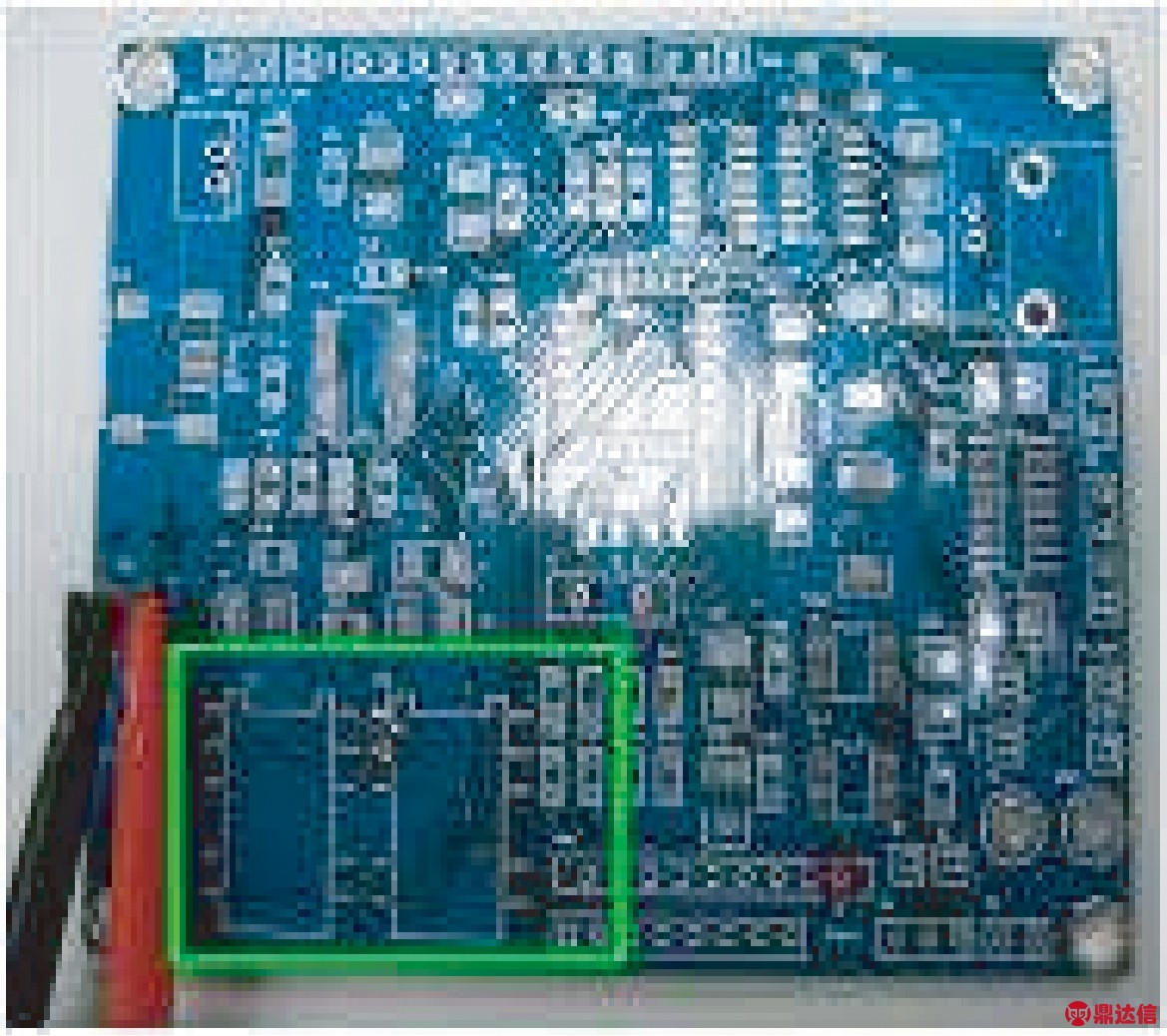
(5)
3 软件设计
系统软体设计采用Hierarchy[12]架构,使用LabVIEW内部子函数VI与自行设计的子VI,架构出测量系统软件程式设计如图7所示,程式架构主要由有限状态机[13]构成,并将主要的控制修改参数,用事件触发的方式来设计。

图7 软件设计图
4 实验测试
(1) 首先测试电磁感应探头是否可以感应电路板线路电流所产生的磁场。利用正弦波信号发生器产生一电流输入至电路板某一回路,并使用电磁感应探头接近此电流回路进行测试[14],测试结果如图8所示,在图8(a)无电流回路的情况下,示波器并无感应到任何信号,在图8(b)产生一电流回路,此时示波器上可看到正弦波信号由电磁感应探头捕获,此实验简单验证电磁感应探头对电磁感应的可行性。
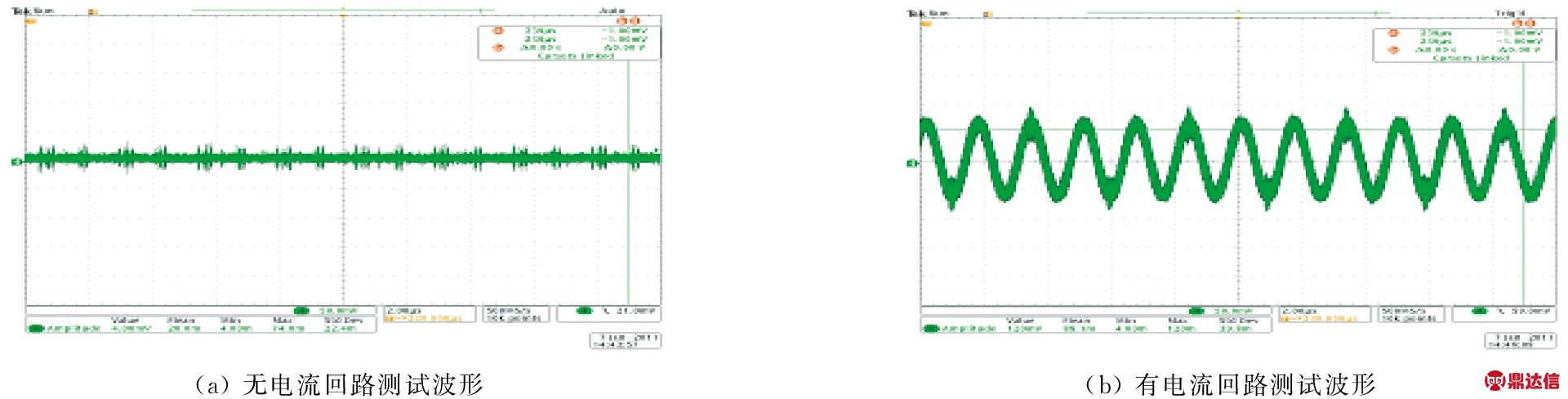
图8 回路测试波形
(2) 测试推导的物理模型是否与实际测量相近。相关参数L=100 μH,N=70,r=2.9 mm,α=00,输入电压1~10 V,测试数据如表1所示。
由表1可知,电磁感应探头量取电压值与其输入比值平均为0.156,若将参数代入推导的公式中,并求出计算的比值为0.127,两个数据的误差量为18%。
若改变测量时电磁感应探头与电路板之间的高度,并比较测量与计算的数值差异。其测试结果见表2。其测试的结果同上一个实验,其量测值与计算值皆有约12%左右的误差,不过对实验已经够用了。
(3) 电路板短路故障测量。将电路板大小约为100 mm×150 mm固定在XYZ平台上,预设电路短路如图9所框的区域,实验中电磁感应探头距离电路板高度为固定5 mm,通过DAQ系统来实现电磁感应功能。图9为设置短路故障的待测电路板,图10为电磁感应探头测量后的磁场强度分布图。由测试结果的电磁感应的强度分布可以发现,在电路板左下部短路区域部分呈现较强的电磁反应,其他部份相对比较低的强度反应,此现象正好符合图9左下框的短路区。
表1 测试数据
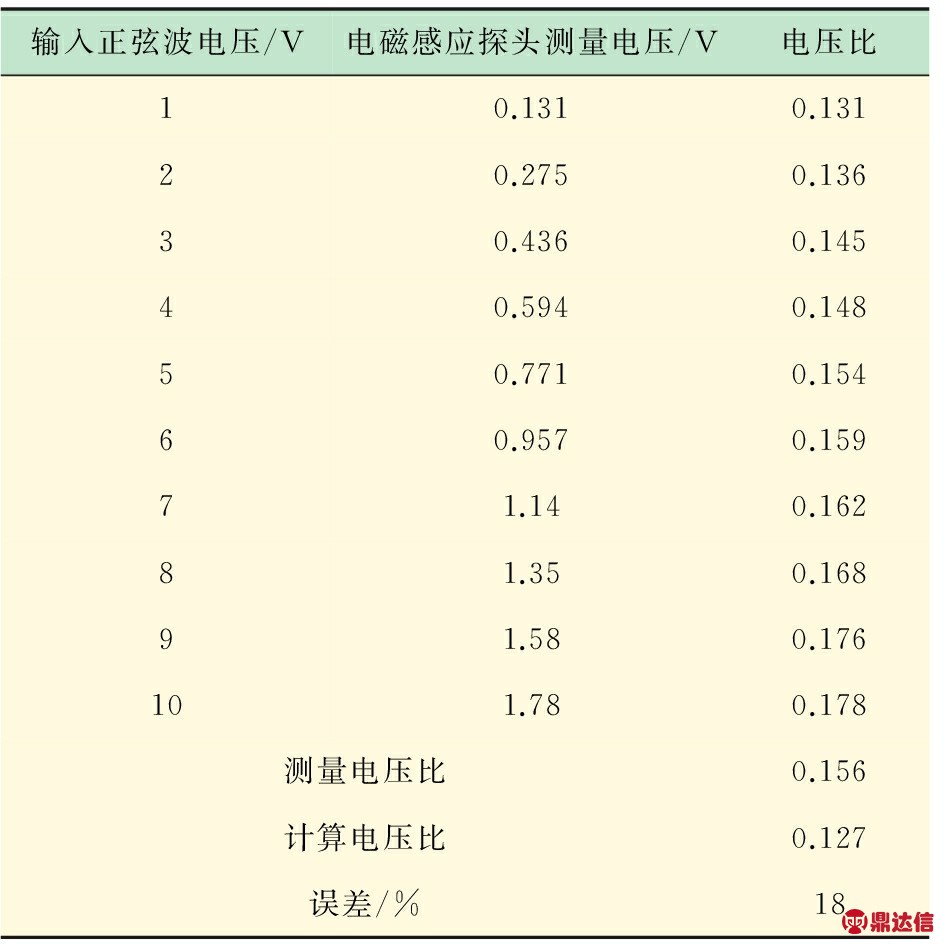
表2 改变测量高度的测试数据
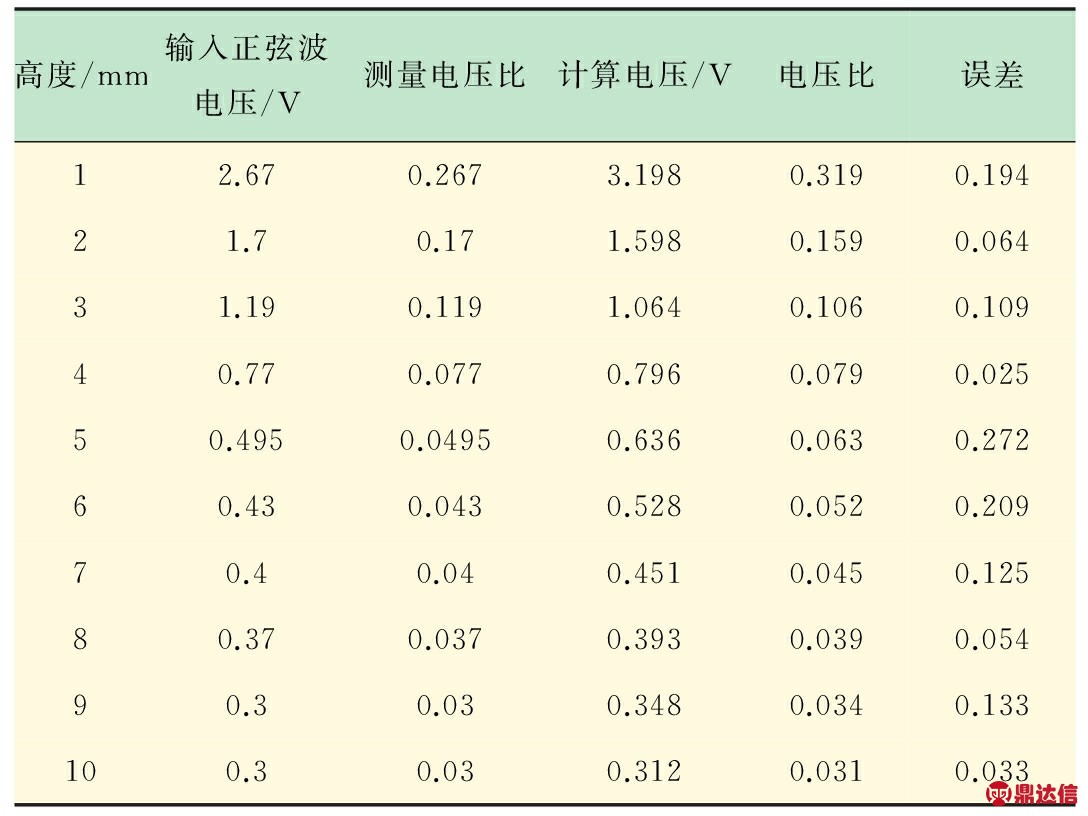
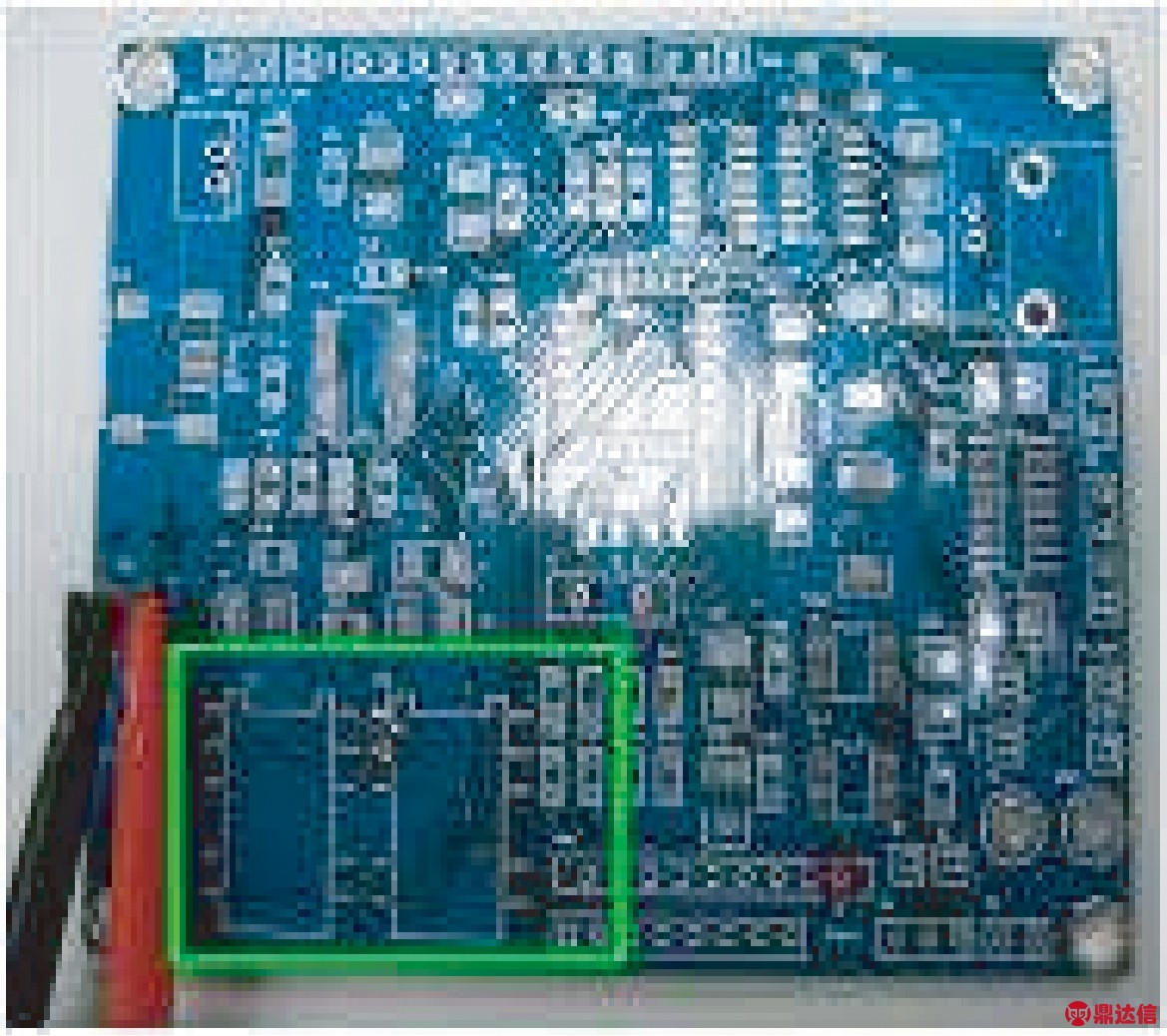
图9 预设短路的待测电路板
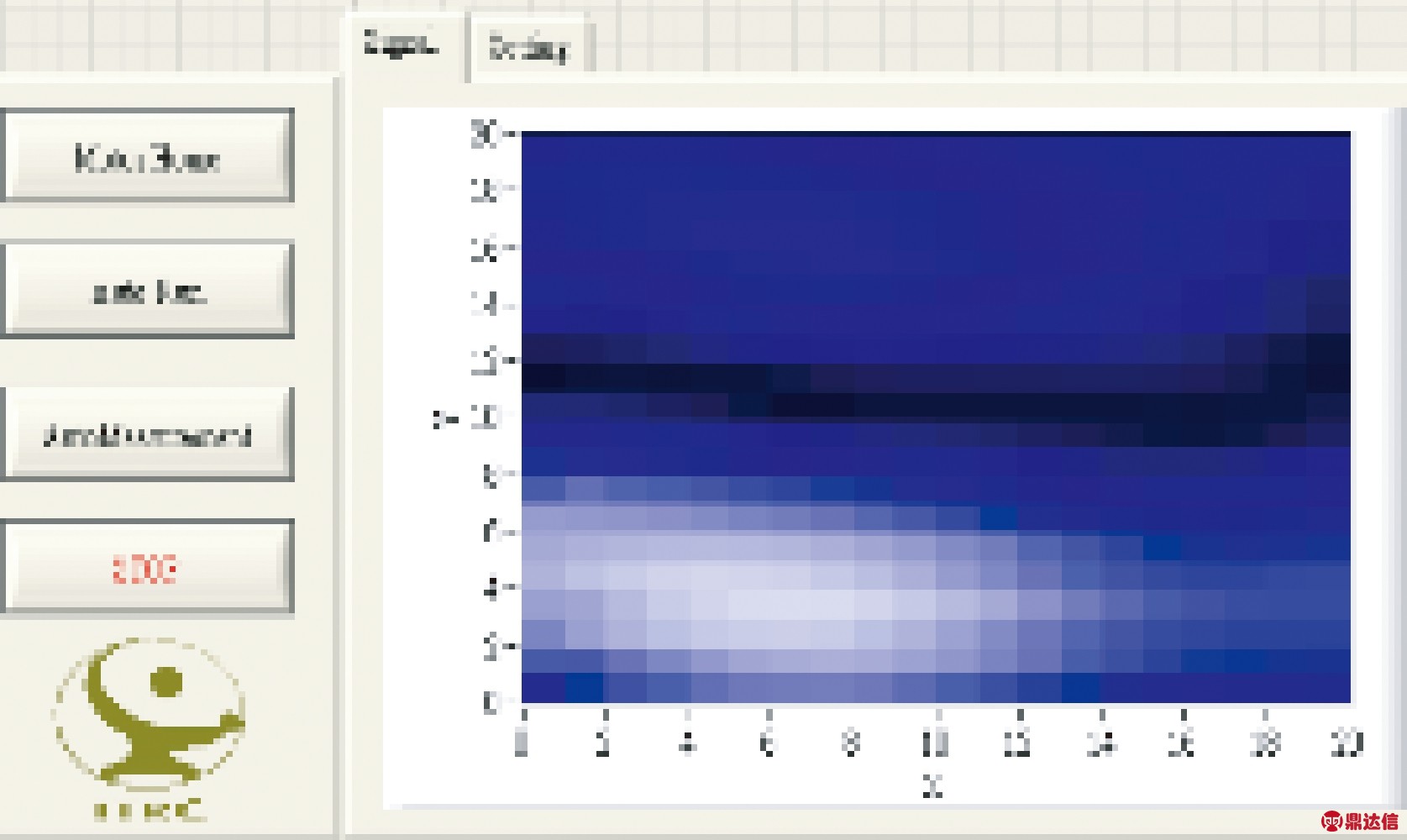
图10 磁场强度分布图
5 结 语
本设计针对印制电路板的短路检测方面,存在的接触点小和检测区域受限两项主要问题,提出了一套通过电磁感测方式,检测出电路板导线的短路与开路情况的解决方案。除了非接触测量引脚克服元件脚位限制之外,同时电磁探头设计成便携式,可解决工作区域范围受限的问题。本设计充分发挥了LabVIEW软件与硬件快速整合与验证的特色,为印制电路板的短路检测提供了另一个途径。