摘 要:通过化学气相沉积法,在PCB微钻上沉积超硬SHD涂层,采用扫描电子显微镜,拉曼光谱仪对涂层微观形貌与成分进行了分析,并进行了φ0.3 mm与φ3.4 mm的超硬SHD涂层微钻与未涂层微钻的对比加工测试。结果表明,加工TU-872SLK高速高频板时,超硬SHD涂层钻头使用寿命是未涂层钻头的40倍以上。
关键词:超硬SHD涂层;高速高频板;微钻;孔粗;使用寿命
0 前言
印制电路板(PCB)是纤维增强并含有铜箔、树脂的层状复合材料,在加工PCB的过程中,硬质合金微型钻头的磨损较为严重[1]。为提高板材的耐热性、导热性、机械性能或尺寸稳定性[2],添加陶瓷填料,或使用难加工树脂的高速高频板,对微钻的耐磨性提出了更高要求。
钻削这类板材,不仅微钻使用寿命降低,对孔位精度、孔粗、钉头、披锋等特性或缺陷的控制也更为困难。
针对以上问题,深圳市金洲精工科技股份有限公司根据PCB微钻的工作特点,研发出超硬SHD涂层工艺,大幅提高了微钻加工高速高频板材的寿命,并显著改善了小孔孔位精度,大孔的孔粗、披锋和钉头。
以下使用φ0.3 mm和φ3.4 mm的超硬SHD涂层微钻,分别与未涂层微钻进行对比加工测试,分析了钻孔后钻头的磨损情况,以及小孔孔位精度,大孔孔壁粗糙度,孔口披锋和孔壁钉头的变化。
1 实验方法
1.1 实验材料
实验钻孔测试用PCB微钻由深圳市金洲精工科技股份有限公司生产,全长38.1 mm,柄径d=3.175mm,钻径φ=0.3 mm,3.4 mm。
1.2 涂层样品制作
涂层沉积设备为改进的适用于生产超硬SHD涂层微钻的CVD(化学气相沉积)设备,制作流程如图1。
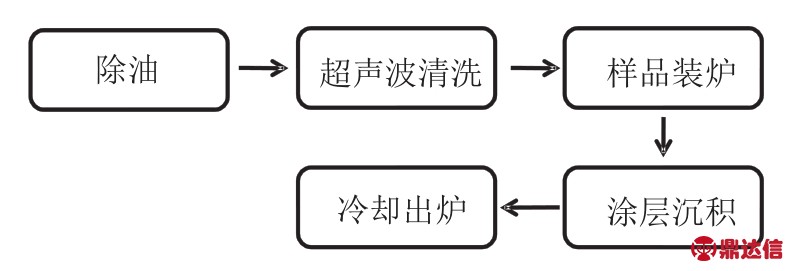
图1 超硬SHD涂层微钻制作流程
1.3 涂层样品分析测试方法
实验采用日本电子JSM-6701F场发射扫描电子显微镜分析涂层截面形貌;采用TAKAYA STMTXU CCD显微镜观察钻头磨损情况;采用LEICA DM2500M金相显微镜观察孔粗,钉头和披锋;采用英国Renishaw公司的Invia拉曼光谱仪分析涂层相组成。
采用HITACHI NDR-1V212E型钻机进行钻孔加工,测试微钻为深圳市金洲精工科技股份有限公司生产的超硬SHD涂层微钻,与对应规格型号的未涂层微钻,测试参数如表1所示。
2 涂层性能分析
2.1 拉曼光谱分析
图2是超硬SHD涂层的拉曼光谱图。由图可见,涂层在1 333.22 cm-1处有一个特征峰,这是金刚石相的特征峰,并且峰型尖锐,说明金刚石晶粒晶型完整,结晶度高。在1 553.99 cm-1附近有一个弱峰,这是非金刚石碳的拉曼峰[3]。
对比金刚石特征峰和非金刚石特征峰的强度和尖锐度,表明涂层中金刚石相含量很高,而石墨及其他非晶碳等杂质含量很少。杂质含量越少,涂层硬度和耐磨性越好。
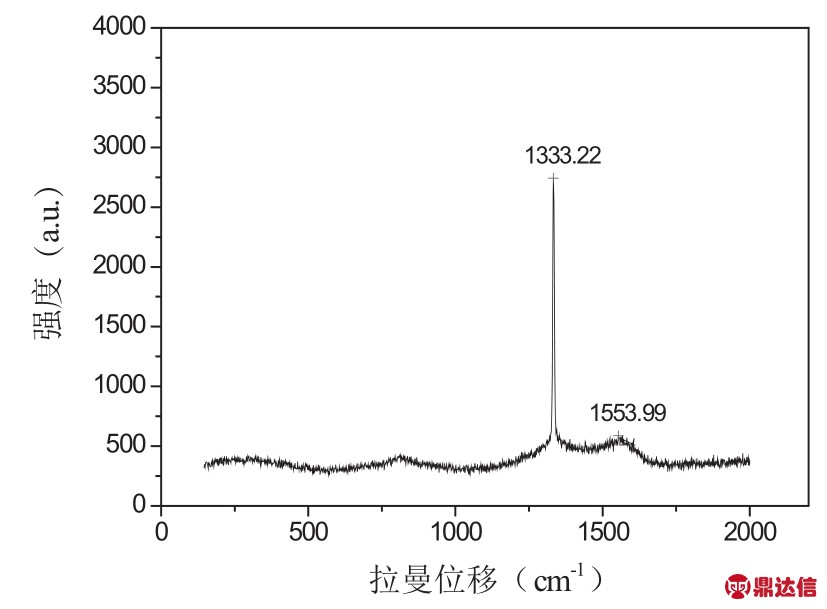
图2 超硬SHD涂层拉曼光谱图
2.2 涂层截面形貌
图3是涂层截面微观形貌。由图可见,涂层晶粒细小,为纳米涂层;涂层组织致密,无微裂纹、孔洞、夹杂等缺陷;涂层与硬质合金基材间无明显的分界面,涂层和基体之间具有良好的结合力。
与市面上常见的微米涂层相比,纳米涂层表面更为光滑,摩擦系数小,可有效提升钻孔时的排屑流畅度,降低积屑瘤产生几率,提升微钻使用寿命,并改善加工孔的孔粗,塞孔,钻污等问题。
3 超硬SHD涂层在高速高频板上的加工性能
表1 钻孔测试实验条件

3.1 磨损性能
图4为使用φ0.3 mm未涂层微钻与超硬SHD涂层微钻钻孔的后刀面磨损照片。未涂层微钻加工500孔后,后刀面磨损严重;而超硬SHD涂层微钻加工20 000孔后,后刀面磨损轻微,未见涂层崩缺或脱落。
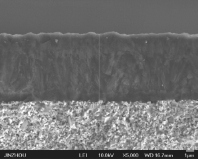
图3 超硬SHD涂层截面SEM形貌
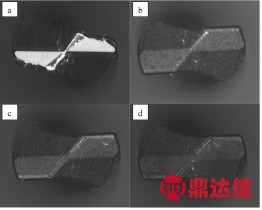
图4 φ0.3 mm微钻磨损图
(a)未涂层微钻500孔;(b)涂层微钻500孔;(c)涂层微钻10 000孔;(d)涂层微钻20 000孔
图5为φ3.4 mm未涂层微钻加工250孔,与φ3.4 mm涂层微钻加工250孔,10 000孔与20 000孔的后刀面磨损照片。由图可见,未涂层微钻加工250孔后,切削刃已显著磨损;而超硬SHD涂层微钻,在加工250孔后,后刀面几乎无磨损,未见涂层崩缺或脱落的现象,加工至20 000孔,涂层磨损也很轻微。
通过上述结果可知,超硬SHD涂层钻头用于高速高频板,无论加工小直径通孔,还是大直径的定位孔,安装孔等,使用寿命均为未涂层钻头的40倍以上。这与超硬SHD涂层接近天然金刚石,高达(80~100)GPa的硬度,很低的摩擦系数和极高的热导率[约20 W/(cm·K-1)]有关[3]。极高的硬度保证了超硬SHD涂层的耐磨性,低的摩擦系数和高的热导率,则起到帮助散热,促进排尘的作用。
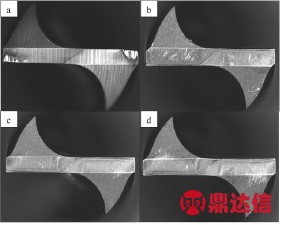
图5 φ3.4mm微钻磨损图
(a)未涂层微钻250孔;(b)涂层微钻250孔;(c)涂层微钻10 000孔;(d)涂层微钻20 000孔
3.3 孔位精度
图6是φ0.3 mm未涂层钻头与超硬SHD涂层钻头加工TU-872SLK高速高频板材的孔位精度箭靶图。由图可见,500孔时,涂层钻头的孔位精度显著优于未涂层钻头。测试10 000孔后,涂层钻头孔位精度依然较未涂层钻头500孔高。
孔位精度差异原因在于超硬SHD涂层的高耐磨性。涂覆超硬SHD涂层,大幅缓解了钻头因切削刃磨损导致的受力不均,同心度下降,造成斜孔的现象,也使钻尖横刃磨损速率大幅降低,提高了下钻时的定位精度。
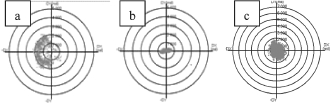
图6 加工TU-872SLK板孔位精度
(a)未涂层500孔,Cpk=1.236;(b)涂层500孔,Cpk=4.389;(c)涂层10 000孔,Cpk=2.215
3.4 孔壁粗糙度
表2是φ3.4 mm超硬SHD涂层与未涂层钻头加工TU-872SLK板的孔粗。加工此类较难钻削的高速高频板时,相较小直径微钻,钻大孔时更易出现孔粗超差的问题,导致NPTH孔内残铜等缺陷。如图所示,未涂层钻头加工150孔时,孔粗即达65.6 μm;超硬SHD涂层钻头加工至20 000孔,孔粗仅19.3 μm。
超硬SHD涂层钻头切削刃,刃背和刃带受高硬度涂层保护,不易磨损或崩缺,是孔粗显著优于未涂层钻头的原因。
3.5 孔口披锋
表3是φ3.4 mm超硬SHD涂层与未涂层钻头加工TU-872SLK板的孔口披锋。如图所示,未涂层钻头加工250孔时,孔口披锋即达12.6 μm;超硬SHD涂层钻头随着加工孔数的上升,孔口披锋从250孔的4.8 μm,降低至10 000孔的3.2 μm,又上升至20 000孔的5.3 μm,改善效果显著。
3.6 孔壁钉头
表4是φ3.4 mm超硬SHD涂层与未涂层钻头加工TU-872SLK板的孔壁钉头。如图所示,未涂层钻头加工250孔时,厚18 μm铜层钉头达2.0,厚35 μm铜层钉头达1.6;超硬SHD涂层钻头加工250孔,10 000孔,20 000孔时,钉头均小于或等于1.5。
4 结论
表2 超硬SHD涂层微钻加工TU-872SLK板孔壁质量
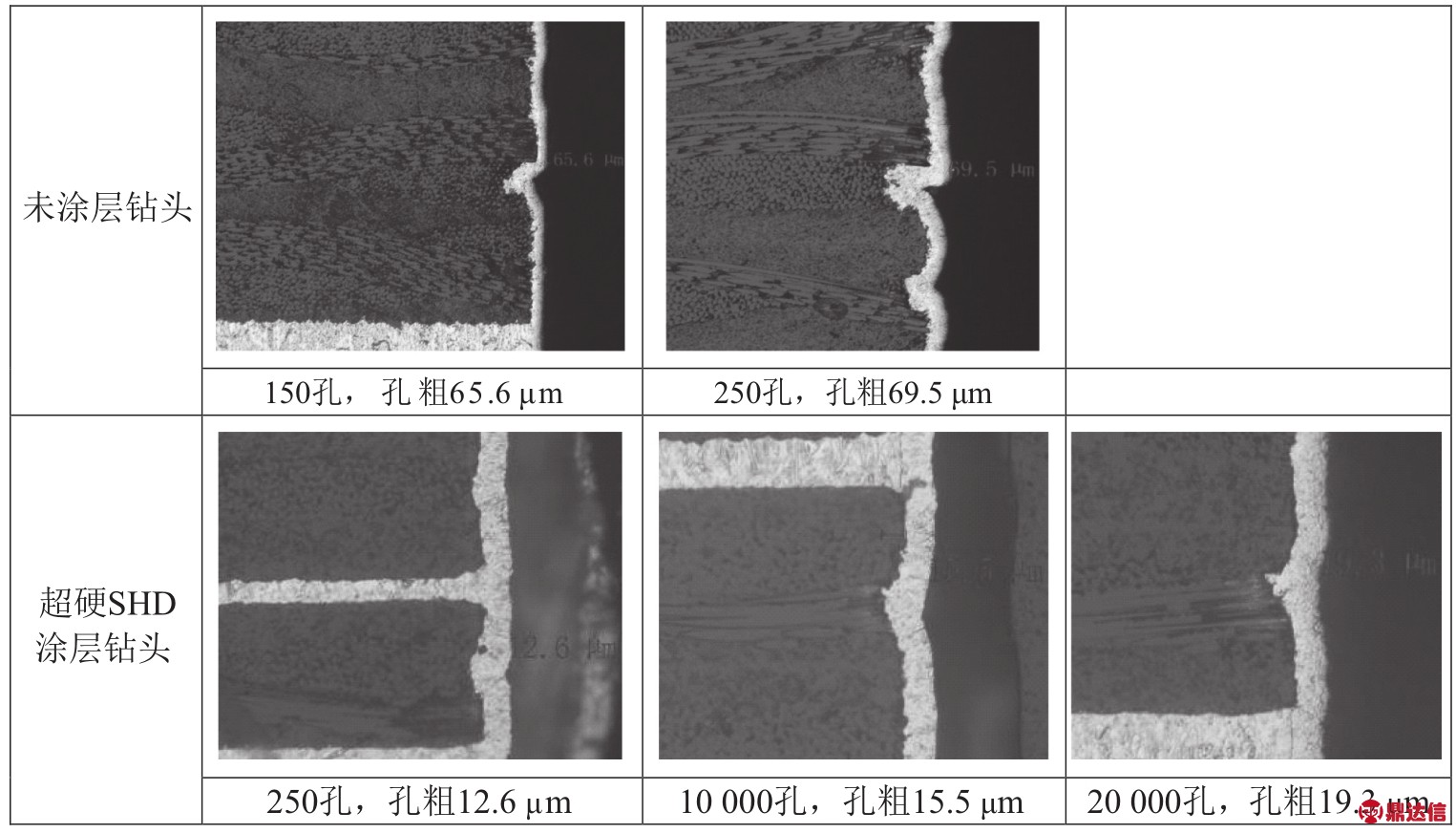
表3 超硬SHD涂层微钻加工TU-872SLK板孔口披锋

在PCB钻头上,采用CVD法沉积了纳米超硬SHD涂层,涂层金刚石相纯度高,晶粒细小,组织致密。
使用φ0.3 mm及φ3.4 mm超硬SHD涂层PCB钻头加工高速高频板,耐磨性均远高于对应规格的未涂层钻头,其中φ0.3 mm超硬SHD涂层钻头寿命是未涂层钻头的40倍以上,φ3.4 mm超硬SHD涂层钻头寿命是未涂层钻头的80倍以上。
使用超硬SHD涂层钻头,小孔孔位精度,大孔的孔口披锋,孔壁钉头和孔粗也得到很大程度改善。大孔孔粗由未涂层钻头250孔69.5 μm降至涂层钻头的20 000孔19.3 μm。