0 引言
薄壁球壳件特别是轻材料结构件,因其结构相对复杂、相对刚度较低和壁厚较小等特点,加工中需要使用特殊的工装进行装夹固定。而在实际加工中,不同的装夹方式甚至装夹过程会使薄壁球壳在加工前已经产生不同程度的变形,并影响装夹约束状态和加工模态。由此,薄壁球壳在机床上的装夹状态及其产生的整体或局部变形会影响工件的加工精度,也造成了不同程度的加工误差[1-3],从而影响炸药武器在聚心爆轰作用下的等压变形精度,并进一步影响炸药爆轰性能。
近年来,随着互联网的普及以及创新创业活动的广泛开展,以新产业、新业态、新商业模式为代表的“三新”经济蓬勃发展。要使“三新”经济保持长久的活力,仅依靠产业、业态、模式的创新是远远不够的,在充分发挥经验优势的同时,要谨防落入“路径依赖”的陷阱。应该充分认识到技术进步是推动“三新”经济发展最核心的要素。要做大规模,需要更多技术创新和成果转化来实现。对于企业来说,要加强研发投入,将科技成果与制造业、服务业、农业等更多的领域结合起来,实现科技进步对全产业链的正向溢出,通过创新驱动来扩大自身发展空间。
组成滑体的物质成份为强风化泥灰岩中的软弱夹层,结构松散,透水性强,抗剪强度低,易于雨水入渗,降低软弱夹层抗剪强度,下伏中风化泥灰岩透水性差,位于土岩界面上的强风化泥灰岩易软化变形,形成贯通性滑带,引发整体滑坡蠕动。
关于薄壁球壳等弱刚性零部件加工装夹的相关研究已有较多,各自针对的问题也不尽相同。其中,王运巧等[4]和刘胤等[5]以减小装夹过程的弹性变形为目标,基于商业虚拟软件开展了弱刚性结构件铣削加工的装夹物理模型研究。李双跃等[6]以及Menassa等[7]和Kashyap等[8]利用有限元虚拟建模技术实现了加工件装夹优化并选择最佳定位支撑位置,从而减小了装夹变形。张磊等[9]和Kaya[10]通过不同方法研究不同装夹方式和装夹布局,明确了装夹力以及装夹位置对复杂薄壁件的影响。虽然现阶段的研究成果较多,但针对薄壁半球壳的车削加工装夹研究较少,并多以传统机械夹紧力作为研究点。
当前基于机械装夹的薄壁件加工变形主要从材料、工艺和夹具等角度进行控制或优化,且研究对象多为薄壁平面件。对于薄壁球壳,由于其传统机械卡盘式夹具造成的宏观变形较大,在某些特殊生产过程中一般采用真空吸盘式工装对球壳类零部件进行装夹。真空吸盘式工装又分为弧面、锥面以及平面3种形式,在车削过程中弧面及平面贴合吸具的设计与加工成本太高,表面质量要求也较高,不适用批量式生产。
因此,有必要基于现行锥面吸具,针对薄壁球壳在车削加工中的夹紧力、装夹位置以及装夹变形等进行研究,结合材料力学与有限元仿真技术,给出锥面吸具的优化设计方法并进行效果对比。
1 薄壁球壳真空吸附力学状态
1.1 球壳受力分析
根据理论力学和材料力学分析,薄壁半球壳经过与真空锥面吸具贴合(即由球壳外表面和吸具的内锥面实现接触)会出现整体和局部形变。加工前,薄壁球壳与真空锥面吸具之间的吸附装夹示意图如图1所示。
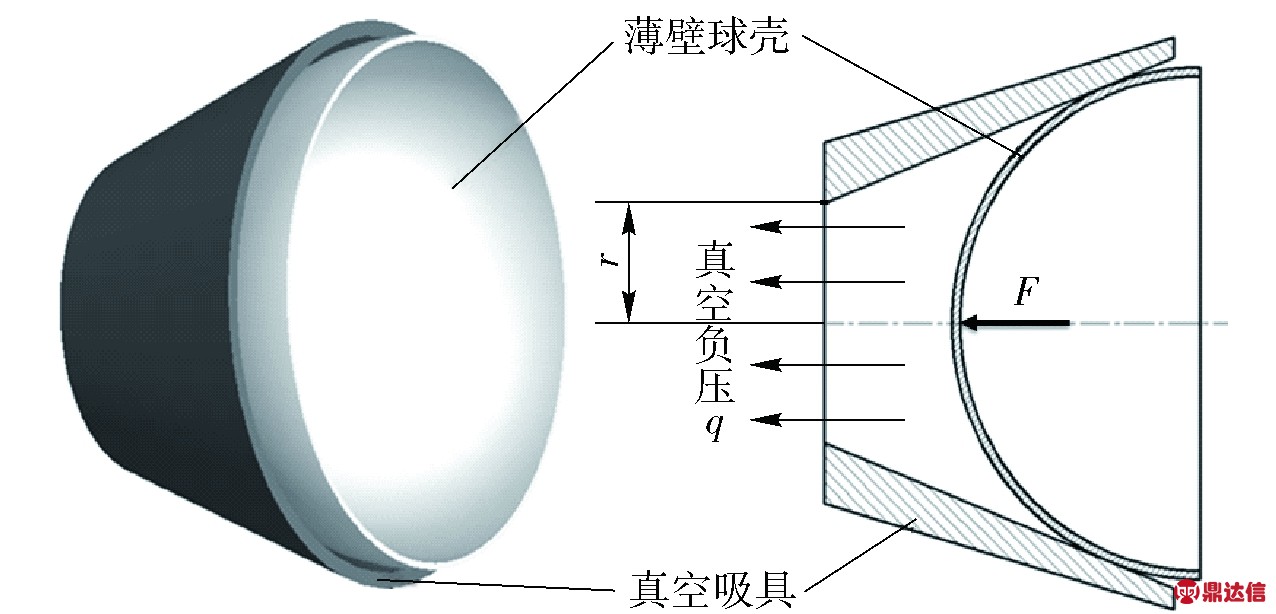
图1 真空吸附装夹示意图
Fig.1 Clamping state during vacuum suction
图1中,q为真空负压,即吸附状态时的真空内外压强差。由图1可知,薄壁球壳与真空吸具装夹后,吸具内锥面与球壳外弧面形成圆周线接触,开启真空负压q后实现吸附装夹。由于吸具锥面对球壳形成了线支承并产生支承力,同时球壳内表面受到空气均布压强,产生等效作用力F,从而使球壳产生装夹变形。在考虑对称的情况下,球壳受力状态如图2所示。
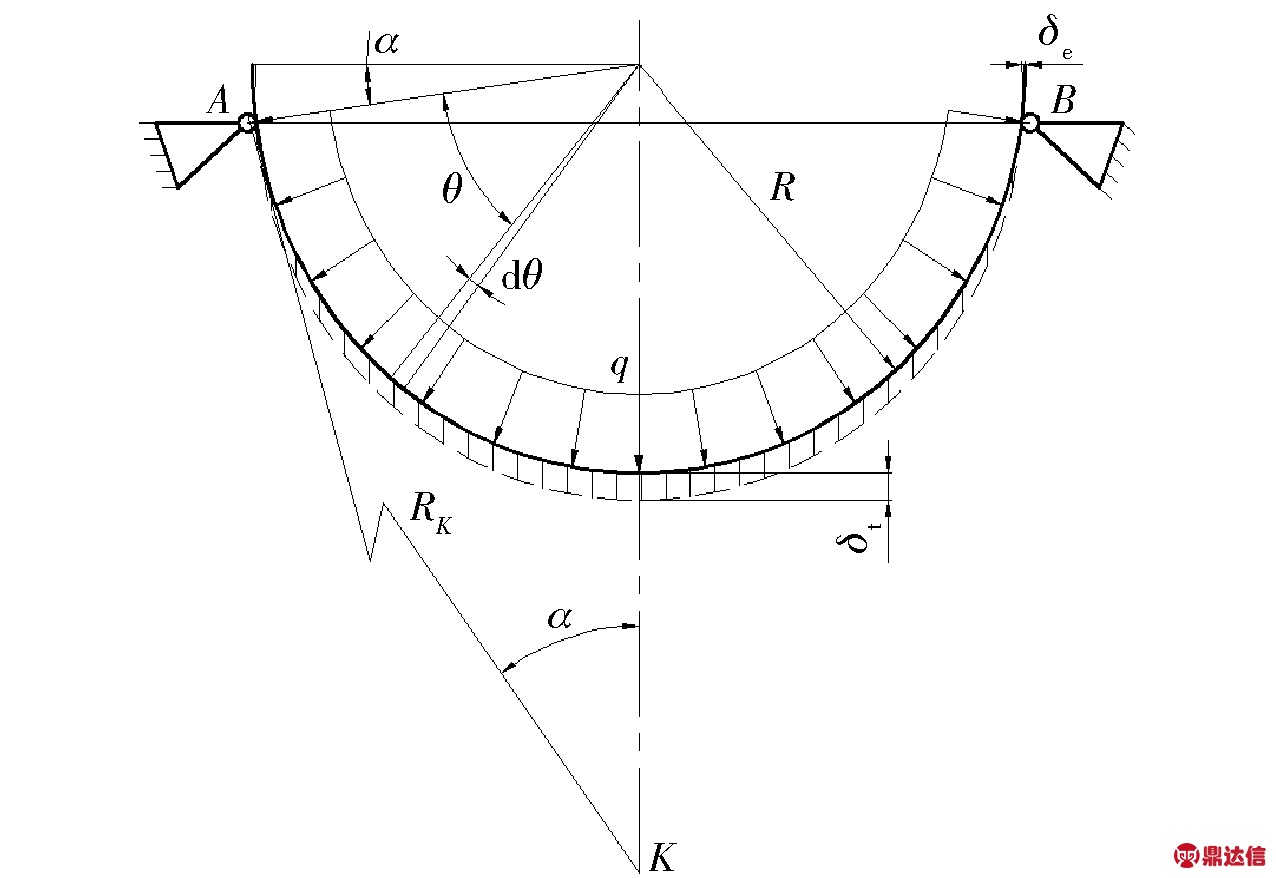
图2 球壳应变及其应力分布状态
Fig.2 Strain and stress distribution states of spherical shell
图2中:α为吸具锥面角度与端面到支承点- 圆心连线之间的角度相等;R为球壳表面半径;θ为支承点- 圆心连线与计算点- 圆心连线之间的夹角;dθ为该微元段对应的弧度;δe为球壳端面变形量;δt为球壳顶部径向变形量;RK为锥面吸具的锥心位置距支撑点的距离,K为吸具锥面的虚拟锥心;A、B为任意截面处球壳的支撑点。
(2)完善标准法律。推动沿江各省制定和执行严于国家标准的地方水污染物排放标准,重点行业执行水污染物特别排放限值。加强洞庭湖等湖泊水环境质量评价标准研究,根据客观实际,制定更加科学的评价标准,尤其是总磷的评价标准。国家层面制定《长江保护法》,加速《渔业法》修订,启动《畜禽规模养殖污染防治条例》修订,制定《洞庭湖生态经济区环境保护条例》《洞庭湖生态环境补偿办法》等并推进地方立法。
可将正圆弧形薄壁球壳件等效为薄壁缓倾斜球壳壳体[11]。根据材料力学中的薄壁壳体计算与理论[12],球壳微元段径向受力状态关系为
dp=qRdθsin (α+θ)2πRcos(α+θ).
(1)
由(1)式可得出,球壳整体径向压力为
).
(2)
在空气压强作用并忽略球壳产生吸附滑移的情况下,球壳底部产生的径向挠度为装夹后的最大静态变形位置,其变形量计算的一般形式为
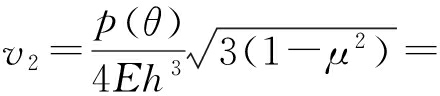
,
(3)
式中:E、h、μ分别为球壳材料的弹性模量、球壳壳体厚度、泊松比。
1.2 真空吸附力学模型
1.1节明确了薄壁球壳加工前的装夹静态力学状态,而在实际装夹过程中,还需要进一步考虑真空吸附和加工过程的可靠性与变形控制。
1)在吸具与工件形成的密封容积内,通过真空源抽出一定量的气体、产生真空负压q,进而吸具产生的等效吸附力[13]为
,
(4)
式中:k为真空有效吸附力系数,一般取值为0.9;C为换算系数,各参数单位为MPa、mm2、N时,取值为1;N为吸附时的安全系数,水平装夹时N≥4,垂直装夹时N≥8;S=nπr2k′为吸具的有效吸附作用面积,其中n为吸盘数量,r为吸具有效吸附半径,即吸具的最小真空管径,如图1所示,k′为吸取力方向的投影面积系数,根据图2所示几何关系,其值通过(5)式确定:
,
(5)
吸具有效吸附半径r=25 mm,为恒定值。
根据(5)式,在薄壁球壳采用水平装夹进行车削时,所需的真空吸附力为
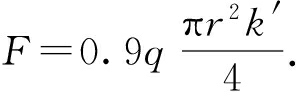
(6)
根据(6)式,可得出在球壳重力和吸具结构确定的情况下,真空负压的设定范围为
同样的,法律角度的思考亦就权力的内容与限度展开,对概括财产代理人进行规范,某个主体授予他权力自由管理后者的财产。保罗的三个法言与莫德斯丁的一个法言使我们得以了解《学说汇纂》中的整体情况。
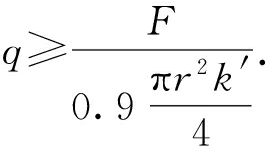
(7)
由(7)式即可得出真空负压q的范围。在初设真空负压q时,F可等效为球壳重力G.
综上所述,在宫颈癌早期筛查中实施护理干预及健康知识宣教能够有效改善患者焦虑、抑郁状态,增强其疾病健康知识掌握和运用能力,具有极高的临床应用价值。
2)在进行车削时,为保证球壳能被吸紧, 在车削加工中不会转动滑移,必须使由球壳所受到的吸附力产生的与真空吸具之间的摩擦力Ff大于安全系数Q与切削力Ft的乘积,而摩擦力的大小与工件接触支承力Fn有直接关系,球壳所获得的支承力越大,则摩擦力越大。因此,球壳的切削力Ft与摩擦力Ff之间的关系为
IMF:拉美地区需巩固长期增长势头。5月11日,国际货币基金组织(IMF)在《西半球区域经济展望》报告中指出,拉丁美洲和加勒比地区经济增速从2017年的1.3%提高到2018年的2%,2019年经济增速预计可达2.8%。其中,巴西和阿根廷等国经济复苏、大宗商品价格走高等因素将拉动南美地区经济增长,墨西哥及中美地区在短期内将受益于美国经济的强劲发展。
Ff=ηFn≥QFt,
(8)
式中:η为铝合金与钢之间的摩擦系数,取值0.6;Fn为球壳总支承力,等效于工件接触支承力;Q为安全系数,取值为2.
根据图2和(2)式可得出,总支承力Fn与真空度之间的关系为
Fnsin α=p(θ).
(9)
已知6061铝的车削力大小为
华为称,关于具体指控内容还非常少,华为并不知晓孟晚舟有任何不当行为。相信加拿大和美国的法律体系最终会给出公正的结论。华为还称,遵守业务所在国的所有适用法律法规,包括联合国、美国和欧盟适用的出口管制和制裁法律法规。
,
(10)
式中:ap为切削深度;f为进给量;v为切削速度。
将(2)式与(8)式、(9)式、(10)式联立,可得出真空负压q的预设下限值为
.
(11)
3)吸具内的真空负压q应在真空发生器最大真空负压的一定范围内选择,以提高真空吸着的能力,又不致使吸附的响应时间过长。而根据球壳加工过程中真空吸附系统的操作规程,真空负压应在真空发生器最大真空负压值的63%~95%范围内选择,即
Pinheiro和Faustino讨论了红细胞与具有不同反离子(Li+, Na+, K+, Lys+和Tris+)的Nα,Nε-二辛基赖氨酸盐之间的相互作用[136]。表面活性剂与红细胞膜之间的相互作用随浓度不同呈截然相反的双向模式:在低浓度区防止低渗溶血,而在高浓度区则引起溶血。
q∈(0.63qmax,0.95qmax).
(12)
真空吸具在设计之初通常采用工件装夹后的夹紧误差,即装夹变形量来表征或评价吸具的设计参数[14]。因此,由(11)式、(12)式、(7)式与(3)式联立,并受到顶部变形量限值δl的控制,即可得出球壳真空吸附装夹变形的数学优化模型:
,
s.t.
(13)
根据(13)式,吸具设计过程中的装夹变形优化变量为锥面角度α,考虑加工稳定性的优化变量为真空负压q.
通过(3)式、(6)式以及(9)式便可以表征薄壁球壳采用真空吸附装夹的力学状态,而(13)式则可作为优化真空锥面吸具及设定真空负压的基础理论与计算方法。
2 有限元仿真
根据薄壁球壳与真空吸具的装配关系,本文采用有限元软件ABAQUS来建立球壳真空吸附装夹的仿真模型。薄壁球壳材料为6061铝合金,其弹性模量及泊松比分别为E1=72 GPA和μ1=0.33;球壳尺寸为外径R=60 mm, 厚度h=1 mm,球壳质量G=1.71 N.
真空吸具材料为45号钢,其弹性模量及泊松比分别为E2=210 GPA和μ2=0.3. 表面经过硬化处理,不考虑其锥面受力变形,可将其简化为刚体。
以支撑接触位置为界,整体有限元仿真模型在真空负压作用下受力矢量q的状态如图3所示。
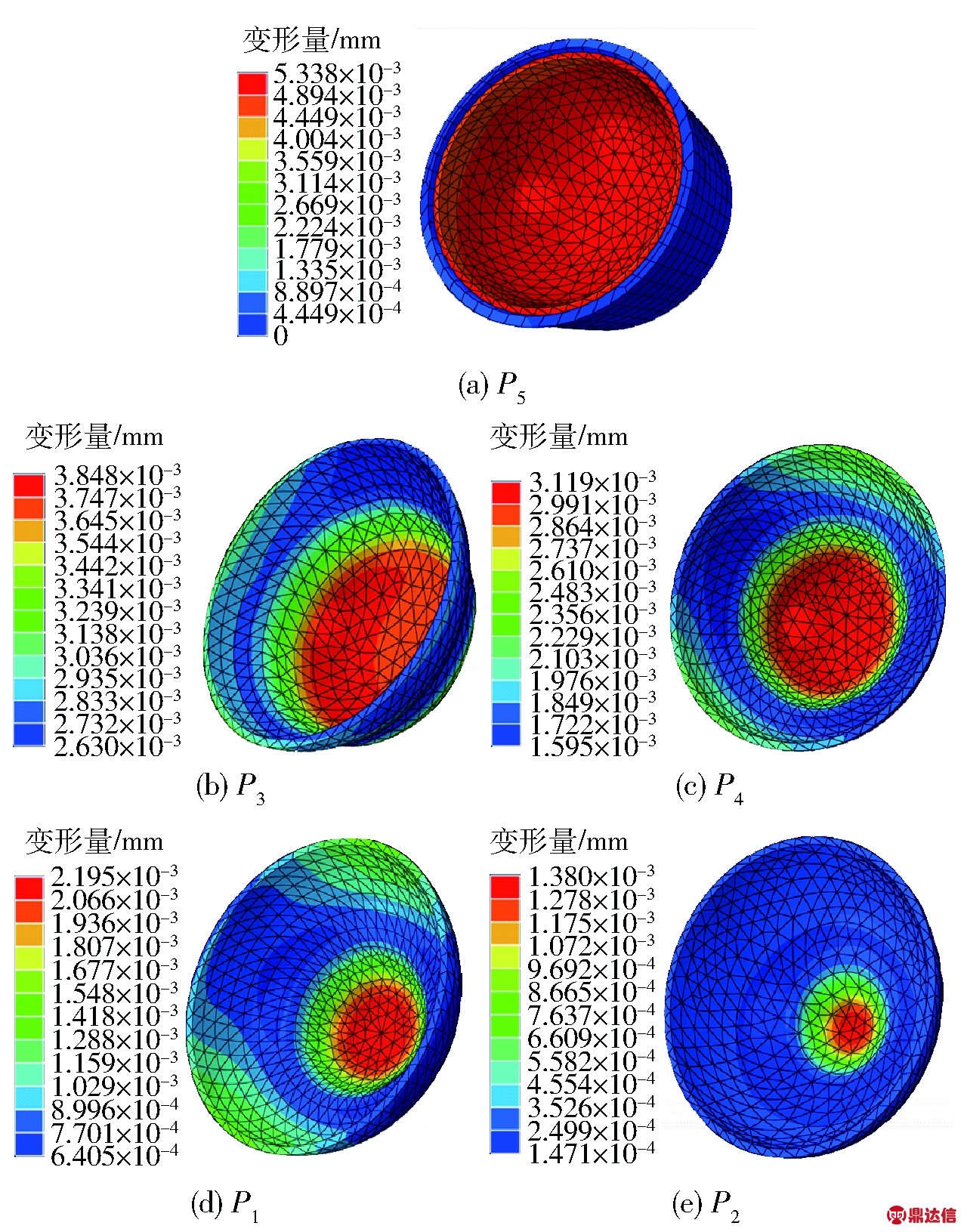
图3 装夹吸附受力状态的有限元模型
Fig.3 Finite element model of suction
图3中,球壳与真空吸具分别采用C3D10(六面体)以及C3D8R(四面体)的三维应力实体单元。
由于注水系统首先要满足注水井压力需求,因此选取干线末端井和破裂压力较高的典型井计算相邻注水站是否能够满足注水压力需求。
2.1 仿真状态分析
在装夹过程中,由于装夹布局参数的不同,薄壁件的装夹变形程度也不同,装夹布局参数引起的工件装夹变形规律能够通过有限元方法获得[15]。
1.2 二级胸痛中心 相关研究发现[14],二级胸痛中心管理模式对此类患者的救治有很大帮助作用,比如可显著降低胸痛确诊用时,缩短住院天数,患者的治疗成本也明显降低。这种模式还需要通过院前传输心电图与周边县医院关联,而为患者及时接受PCI提供支持;同时和上级胸痛中心沟通而接受指导,在无法有效处理情况下,还可以将患者直接转入上级医院,或者调派医生来处理相关难度较大的技术问题。这种管理模式对抢救STEMI患者的效果很明显,患者的再灌注治疗时间明显减少,且死亡率、患者预后等指标都有一定改善,在经济落后地区具有较高的应用推广价值[14]。
现将球壳的真空吸附接触位置以球壳弧面坐标表示,如图4所示。
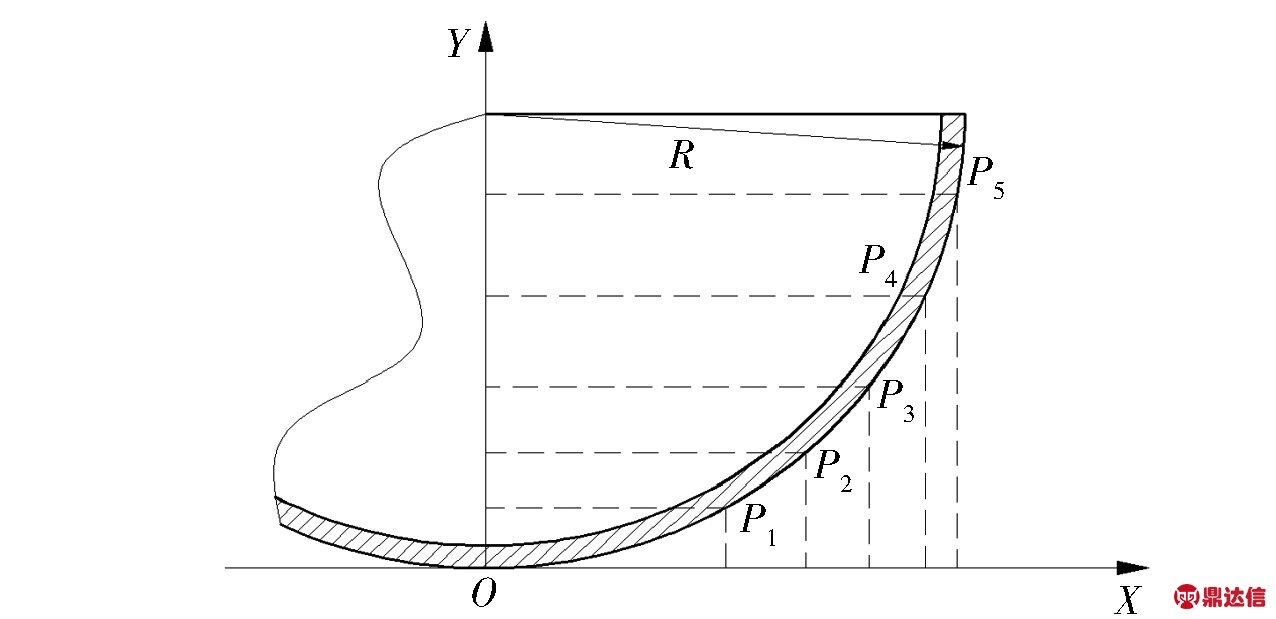
图4 球壳吸附的不同接触位置
Fig.4 Contact positions of suction
根据吸附状态下接触的位置不同,吸具的锥面角度也存在差异,各位置坐标状态如表1所示。
概念模型是指以文字表述来抽象概括出事物本质特征的模型,在生物教材中主要以概念图、示意图的形式来呈现。学生的认知是一个从混沌到清晰,从无序到有序的螺旋上升过程。凌乱、繁杂的知识无法有效纳入知识结构、形成整体的认知。只有结构化的知识才有助于学生记忆、理解和迁移。而概念模型是对事物的抽象提炼,能让知识有序编码,以系统化和结构化的形式与学生原有的认知结构对接、整合,从而极大地提高学习效率。因此,概念模型是学生学习重要概念的工具。帮助学生构建概念模型是解决认知无序性的关键。在教学实践中,教师充分利用教材蕴含的丰富素材,发挥概念模型的作用,可有效提高学生的认知能力。
表1 吸附接触位置的坐标数据
Tab.1 Coordinate data of every point in contact positions
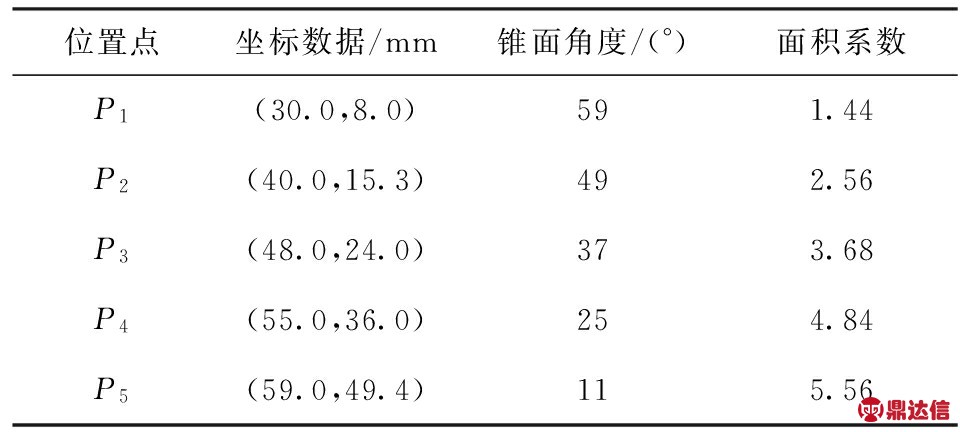
位置点坐标数据/mm锥面角度/(°)面积系数P1(30.0,8.0)591.44P2(40.0,15.3)492.56P3(48.0,24.0)373.68P4(55.0,36.0)254.84P5(59.0,49.4)115.56
根据表1所示吸具的锥面角度,分别针对球壳建立吸具的仿真模型。已知现阶段在球壳加工过程中设定的真空负压q=0.001 MPa. 5个不同吸附接触位置的仿真变形效果如图5所示。
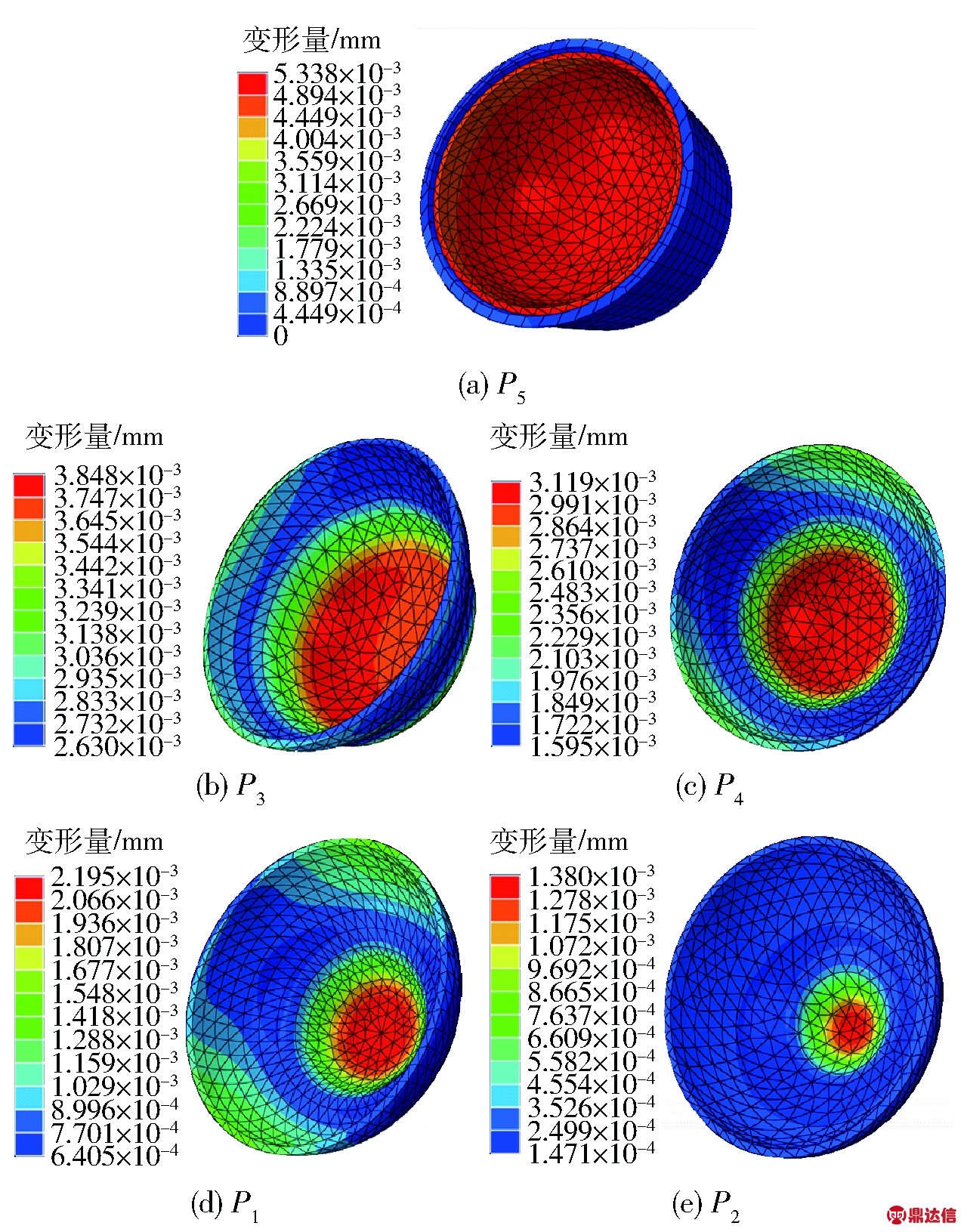
图5 不同接触状态下底部变形量
Fig.5 Deformation of shell in different contact states during suction
将球壳尺寸、材料数据以及真空负压代入(3)式中,可得出在相同真空负压下,吸具锥面角度与球壳装夹变形量之间的关系,如图6所示。
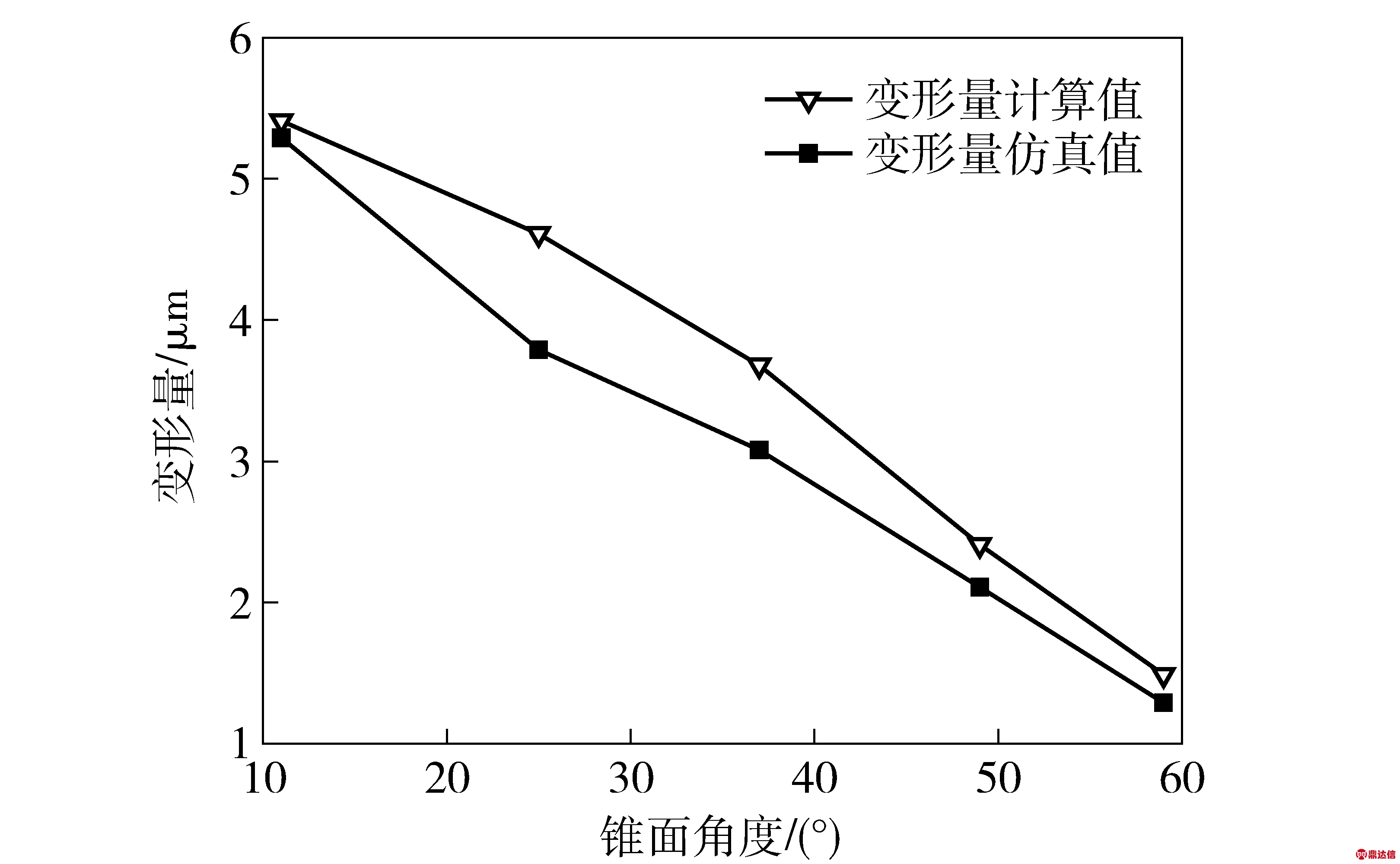
图6 仿真后的变形趋势
Fig.6 Deformation trend after simulation
由图6可知,装夹变形程度与吸具锥面角度之间呈反比,即吸具锥面角度越大,球壳变形量越小。
2.2 真空负压分析
图6中的变化趋势是在真空负压保持一致的情况下得出的。因此,根据(5)式,当吸附同一球壳时,根据吸附位置的不同,稳定吸附时所需的真空负压也存在差异。可以预知的是,锥面吸具角度越大,将球壳装夹固定在吸具上所需的真空负压最小值就越大,造成的球壳变形也就越大,从而对吸具系统提出了更高的要求。
根据(7)式理论模型、球壳状态数据以及相同仿真路径,可以得出在球壳不同吸附接触位置进行装夹时所需的最小真空负压,如图7所示。
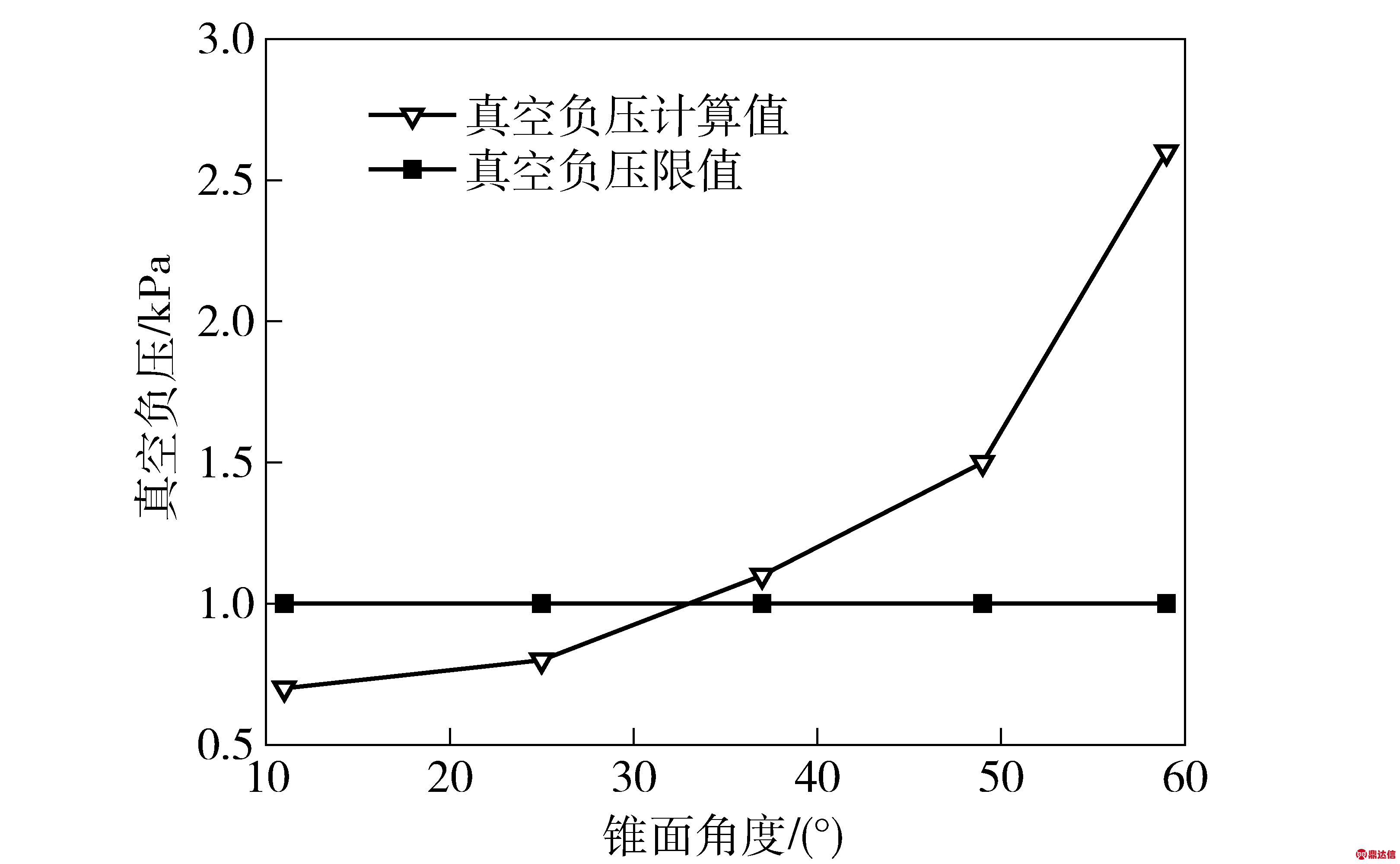
图7 所需真空负压变化趋势图
Fig.7 Changing curves of different vacuum negative pressures
由图7可知,锥面角度越大,所需最小吸附真空负压越小。当锥面角度α>37°时,所需最小真空负压已经明显大于当前真空负压限值(0.001 MPa),在该真空负压作用下的球壳在P1点处的变形量如图8所示。
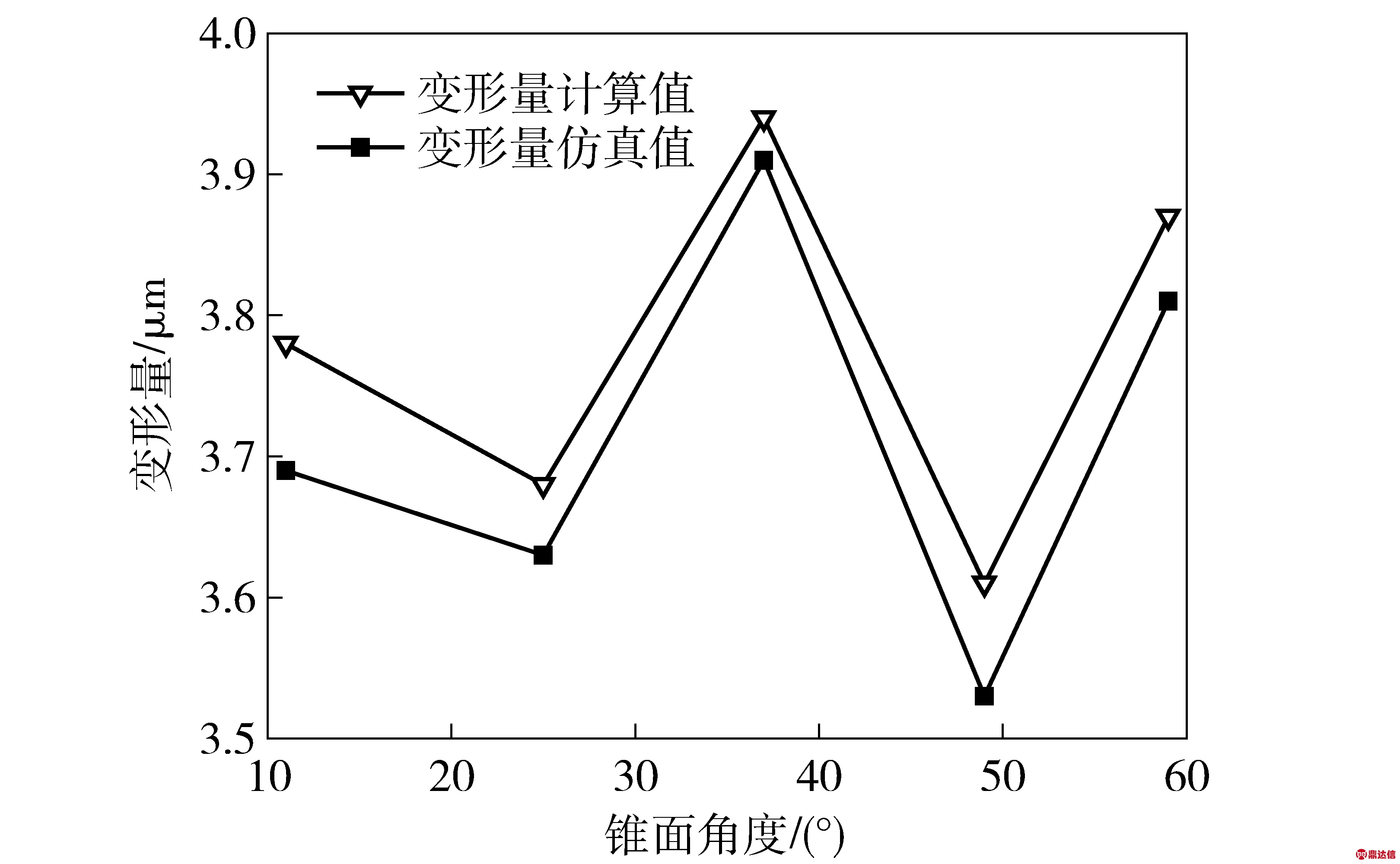
图8 所需最小真空负压状态下的球壳变形趋势
Fig.8 Deformation trend of spherical shell under minimum vacuum negative pressure
结合图6并由图8可知,在设计真空吸具所需的最小真空负压作用下,当锥面角度α>37°时,相对于图6,对应球壳的装夹变形量增大了。
对于恶性嗜铬细胞瘤及其转移瘤无法实施手术者,可实施联合化疗,半数以上的患者可部分或完全缓解达两年左右。
3 优化分析与设计
根据前文分析,球壳变形及其幅度大小与真空吸具的锥面角度α以及真空负压q有关。因此,根据(13)式可以对真空吸具进行优化设计。
优化前,需要明确设计输入条件如下:
1)待加工的薄壁球壳尺寸状态;
2)车削加工相关参数;
3)现有真空负压可用范围。
已知球壳材料为6061铝合金,球壳外径R=60 mm,厚度h=1 mm;铝合金与钢之间的摩擦系数η=0.6. 切削参数为:切削深度ap=0.3 mm;进给量f=0.1 min/r;切削速度v=100 m/min;真空吸附口半径r=25 mm;真空负压最大值qmax=0.001 0 MPa.
加工前,根据加工技术要求,球壳在真空吸附状态下产生的装夹变形量需控制在δl≤3 μm,则(13)式所建立的数学优化模型变形为
,
s.t.
(14)
由(14)式得出的吸具锥面角度优化选择范围为
α∈(17.4°,29.6°).
(15)
将所属各参变量代入(14)式中,得出球壳真空吸附装夹的真空负压与锥面角度的优化结果为
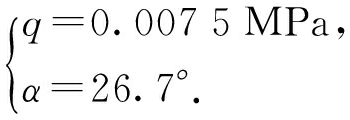
(16)
根据上述优化结果,得出的吸附变形理论计算值为δt=2.31 μm,符合吸附装夹的变形控制要求。仿真结果和吸具样件(α=26.5°)如图9所示。
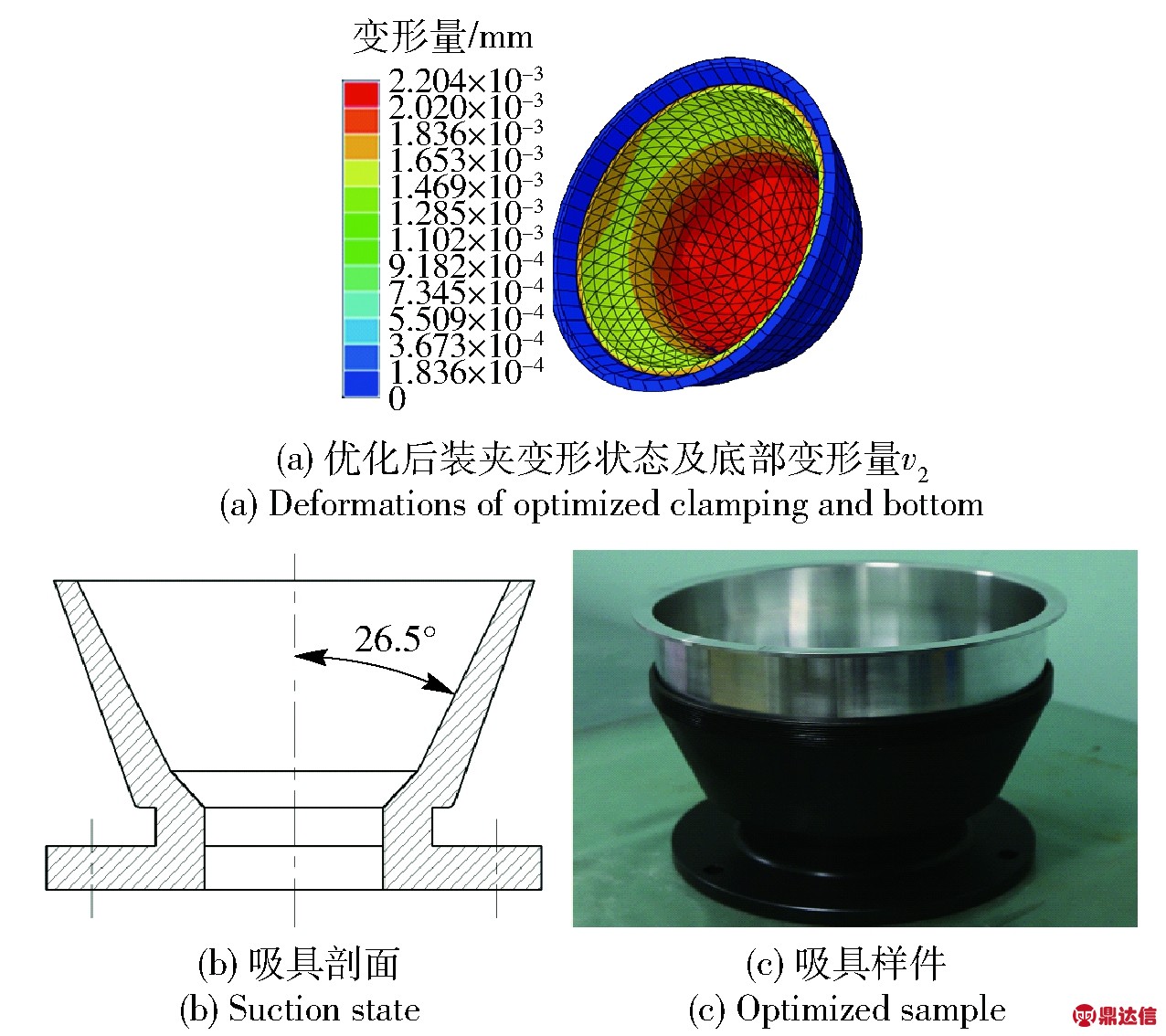
图9 优化结果及吸具样件
Fig.9 Optimized results and suction instrument prototype
图9的仿真数据显示,吸附变形的仿真值为2.17 μm,吸附后所产生的装夹变形量减小了。
采用瑞典Serein公司产croma564改进型三坐标测量仪进行测量,其标准系统测量分辨率为0.05~0.07 μm,测量精度为0.5 μm. 此外,设计一个适用于工装与真空吸附系统的小型大理石平台,中间开孔以方便测量时的真空管路连接,先采用0.003 MPa进行球壳的初始固定,然后在精度为0.1 μm的端面激光位移传感器测量下进行装夹与端面对中,使其端面跳动控制在0.5 μm以下。
虚拟仿真实验教学是现代实验教学方式之一,其借助多媒体和信息技术虚拟出仿真的实验环境,能起到弥补教学资源不足、丰富教学内容的作用。作为一种辅助教学手段,虚拟仿真教学对丰富学生药剂学知识体系、突破实体实验限制、提高实验安全性、降低实验成本、提升学生的实验技能起到重要作用。将虚拟仿真实验教学作为教学平台,正确认识其教学特点,把常规实验和虚拟实验教学有机结合,合理设计,科学论证,积累更多的经验,对高校应用虚拟仿真教学和培养药剂学应用型人才有着重要意义。
采用同平面垂直对称4点法,分别对经过优化后吸具样件和原36°锥面吸具装夹后的球壳内表面进行检测。分别在P1~P5所处的平面内(如图10中P1所处的同平面垂直4点P11~P14)检测,并与装夹前的球壳对应位置进行数据对比,采用测量点的内深变化量作为标定,从而得出装夹变形量。
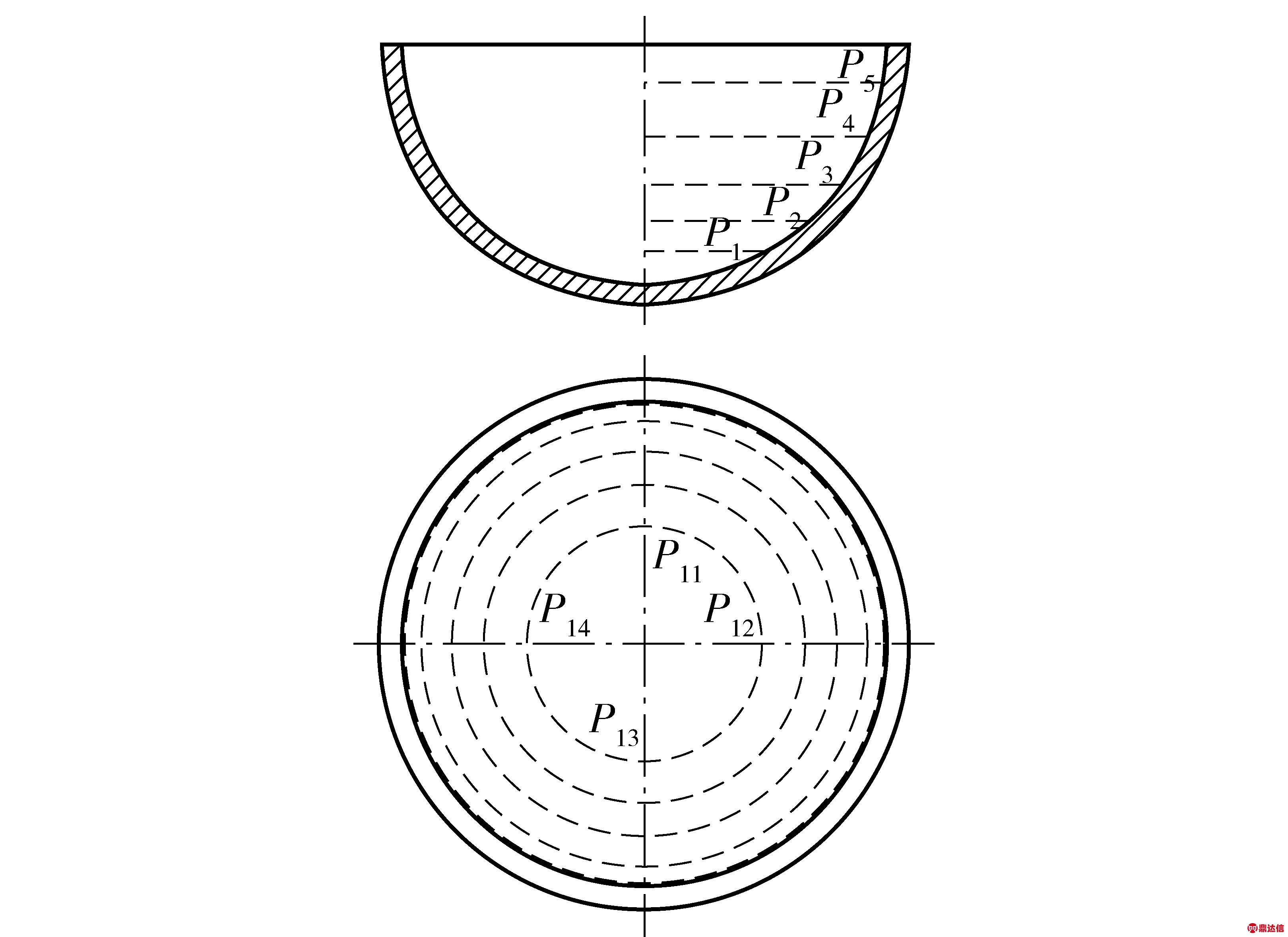
图10 三坐标测量球壳位置
Fig.10 Measuring position of sphere shell based on CMM
经过检测后,原36°锥面吸具在0.007 5 MPa真空负压作用下,对比装夹前后的球壳测量数据,得出球壳的装夹变形量如表2所示。
经过检测后,优化后的吸具样件在0.007 5 MPa真空负压作用下,对比装夹前后的球壳测量数据,得出球壳的装夹变形量如表3所示。
由表2与表3的实际测量数据对比分析可知,优化后的吸具样件在球壳装夹后,球壳的变形量为1.60~2.80 μm,较原36°吸具的变形量大幅减小,整体变形控制效果明显。其中,25°位置由于接近球壳与吸具的接触点,其变形量最小;11°位置受到球壳整体变形影响,其变形程度较球壳底部小;球壳底部由于相对远离吸附支撑点,其变形也最大。
表2 原36°锥面吸具装夹前后的变形量
Tab.2 Measured data of the shell at 36°based on CMM μm
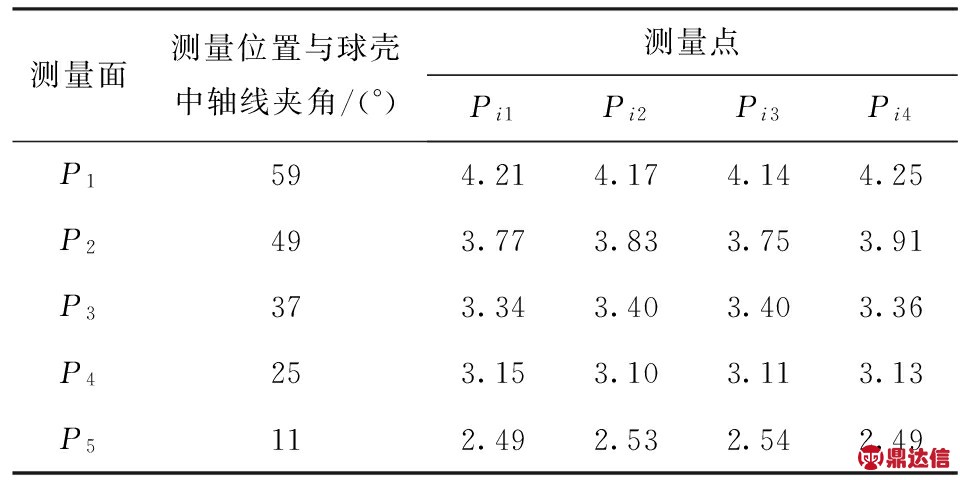
测量面测量位置与球壳中轴线夹角/(°)测量点Pi1Pi2Pi3Pi4P1594.214.174.144.25P2493.773.833.753.91P3373.343.403.403.36P4253.153.103.113.13P5112.492.532.542.49
表3 26.5°锥面吸具装夹前后的变形量
Tab.3 Measured deformation data of shell at 26.5° based on CMM μm

测量面测量位置与球壳中轴线夹角/(°)测量点Pi1Pi2Pi3Pi4P1592.742.672.722.68P2492.452.442.462.43P3372.032.012.042.02P4251.631.611.641.60P5111.931.961.911.95
综上所述,考虑到实际吸附装夹中存在一定的滑移以及测量误差,可以认为本文真空吸具的结构优化设计是合理有效的。
4 结论
通过理论分析和实例计算,得到如下结论:
1)吸具锥面角度与真空负压影响薄壁球壳真空吸附状态下的装夹变形。
2)基于该薄壁球壳真空吸附的力学状态等效数学模型及变形控制,可以较精确地得出吸具锥面角度的优化选择范围。
3)优化后的实例计算、仿真分析以及样件测量