摘 要:基于显式动力学有限元分析软件,以混合细胞自动机(HCA)作为优化计算模型,对铝合金前碰撞横梁的结构进行优化设计。针对拓扑优化结果,采用模拟退火法优化横梁壁厚尺寸,获得薄壁、中空且带有加强筋结构的铝合金前碰撞横梁设计方案。以 6061铝合金前碰撞横梁替代某车型原钢质横梁,通过台车碰撞进行仿真模拟与实验验证。结果表明:铝合金前碰撞横梁比原钢质前碰撞横梁质量减轻了25%,且具有较高的抗弯曲强度,低速碰撞下,铝合金前碰撞横梁较原钢质件系统吸能提高了45.6%。
关键词:铝合金;碰撞横梁;混合细胞自动机;吸能性能;拓扑优化
汽车保险杠一般由塑料保险杠壳体、碰撞横梁和左右两个碰撞盒以及其他部件组成。汽车碰撞横梁是汽车的安全防护装置之一,可在车辆碰撞中吸收缓和外界冲击力,以提高车身碰撞安全性能[1-2]。铝合金具有密度低、延展性好、易加工等特点[3],是汽车碰撞横梁的理想材料。通过优化前碰撞横梁的结构和合理采用热处理工艺,可在减轻质量的同时满足安全要求,提高铝合金前碰撞横梁的吸能性能[4]。目前,拓扑优化技术在工业设计领域得到广泛应用,但是,传统的拓扑优化方法在处理材料非线性、接触和高应变速率等非线性动力学问题时[5]存在诸多困难。而以混合细胞自动机作为优化计算模型,可对非线性动力学系统进行拓扑优化,在优化碰撞吸能部件的耐撞性方面具有极大的潜力,并具有较高的鲁棒性与普适性[6]。模拟退火法是一种启发式随机搜索过程,具有全局性、高效性等特点[7-8],结合拓扑优化结果,可用于汽车吸能部件的形状和尺寸优化[9],是解决工程优化问题的常用数值优化方法。
本文作者采用6061铝合金材料,结合拓扑优化与尺寸优化技术,设计新型铝合金前碰撞横梁,用于替代某车型原钢质横梁,在减轻质量的同时提高横梁的耐撞性,并通过台车碰撞进行仿真模拟与实验验证,研究铝合金前碰撞横梁与原钢质件吸能性能。
1 混合细胞自动机法
细胞自动机(CA)由 NEUMANN[10]于 20世纪 50年代提出,用来模拟生物系统的细胞间自组织现象。20世纪80年代WOLFRAM[11]利用细胞自动机法代替偏微分方程来描述复杂非线性系统。2004年,TOVAR[12]发展了混合细胞自动机法(HCA),该方法结合局部控制减少了计算中的数值不稳定性。混合细胞自动机法将设计空间离散成一个由规则单元组成的细胞自动机,每一个局部细胞自动机根据设计法则修改设计变量,通过局部控制将局部应变能密度(SED)转换成为目标函数,具有更快的收敛速度[13-14]。
与传统细胞自动机不同,混合细胞自动机采用局部控制法则,使局部临域内平均应变能Ui尽可能接近局部应变能目标 U*。局部优化问题的数学表达式如下:
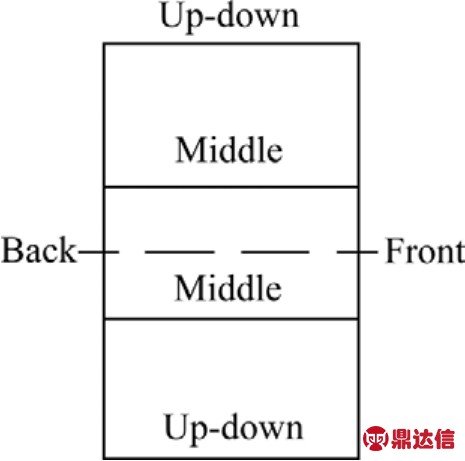
式中:ρi为相对密度,0≤ρi≤1。
在CA寻求最优解的过程中,局部控制能使全局系统获得稳定的局部最优解。局部控制可以用如下形式表述:

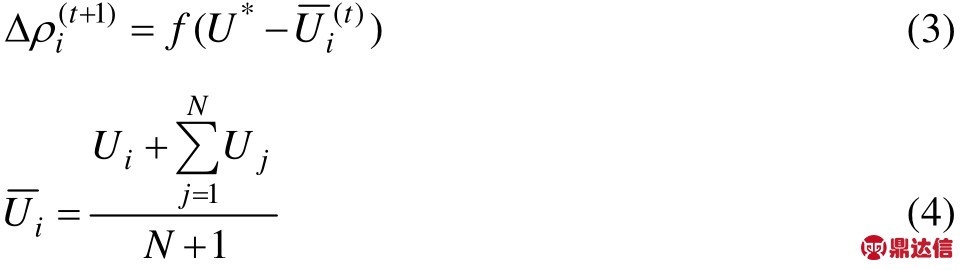
式中:t为时间步;i为局部细胞单元;j为临域细胞单元;N为临域细胞单元数量; Δ ρ i(t)为密度变化。局部控制常采用Two-position控制法则,该法则定义局部密度变化为 U i- U *的简单函数:
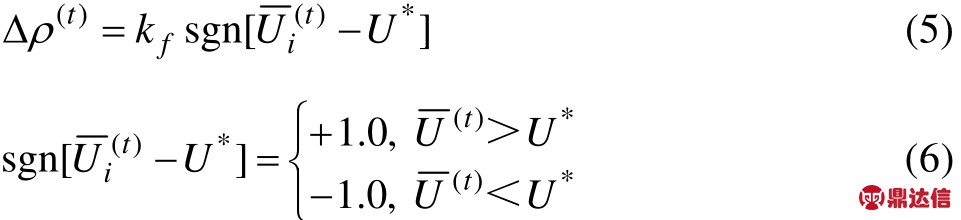
式中:kf是恒正常数[12-14],在本模拟中取kf = 0.1。
2 铝合金前碰撞横梁的优化设计
2.1 碰撞横梁拓扑优化
通过冲击力学性能试验,得到钢和铝合金的Johnson-Cook本构关系[15]。表1所列为前碰撞横梁材料的本构参数。采用Johnson-Cook本构模型能较好地描述金属材料的应变强化效应、应变速率效应和温度软化效应,特别适用于描述较高应变速率条件下材料的力学性能[16]。
表1 碰撞横梁材料Johnson-Cook模型的本构参数
Table1 Johnson-Cook material model constitutive parameters of bumper
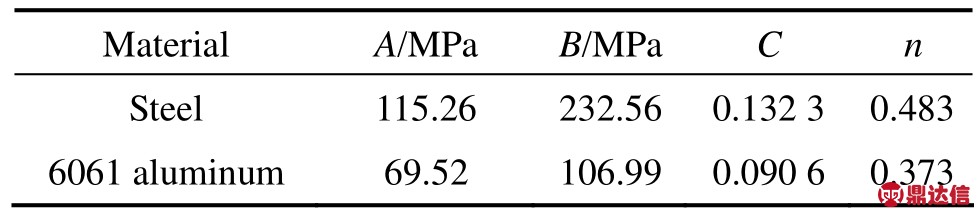
传统拓扑优化常采用变密度法求解,基于数学规划法的优化框架,能够解决大多数工程问题。传统拓扑优化算法多应用于准静态加载问题,以提高结构的刚度。但对于汽车前碰撞横梁在碰撞过程中的大变形、接触非线性、材料非线性等复杂问题,传统拓扑优化方法无法求解。因此,应采用混合细胞自动机作为优化计算模型,对原钢质前碰撞横梁的设计空间进行拓扑优化。
在低速碰撞条件下,铝合金前碰撞横梁主要通过弯曲变形与截面压溃两种变形方式吸收碰撞中的能量[1,17],如图1所示。图1中箭头方向为加载方向,虚线为变形前状态,实线为变形后状态。拓扑优化充分考虑这两种变形方式,可获得抗弯强度高、吸能性能优的碰撞横梁设计方案,其优化流程[14]如图2所示。
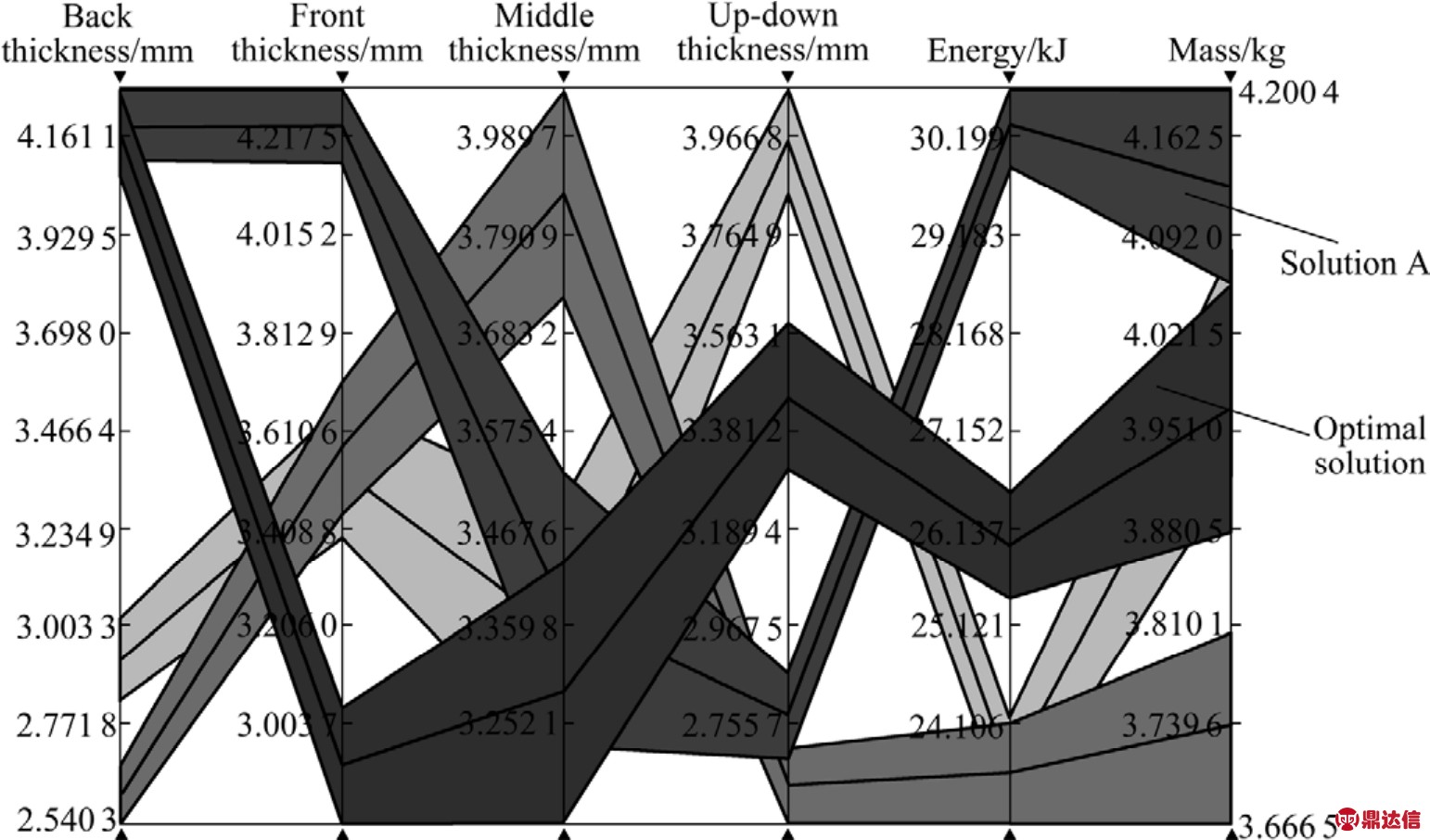
图1 汽车前碰撞横梁变形方式
Fig.1 Deformation modes of front bumper: (a) Bending;(b) Section deformation
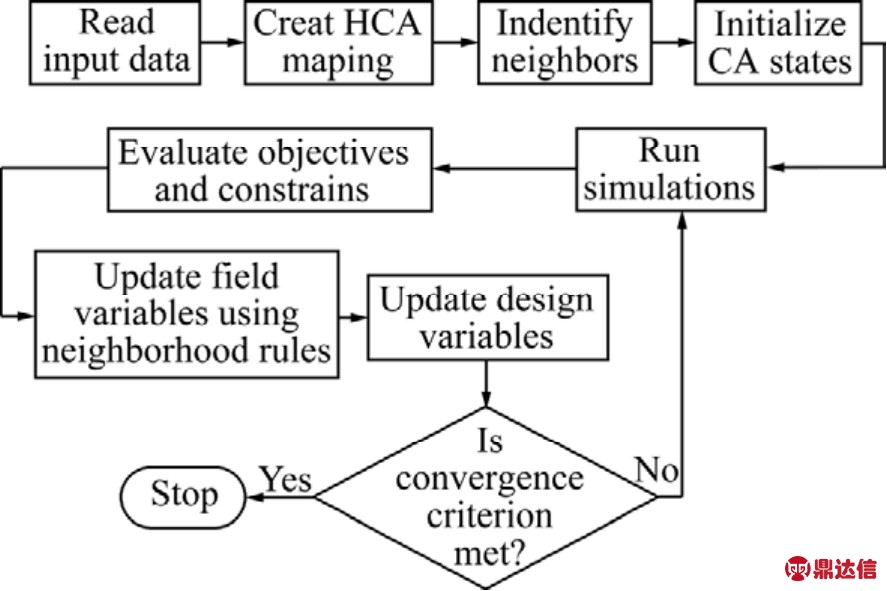
图2 混合细胞自动机拓扑优化流程[14]
Fig.2 Flow chart of topology optimization by hybrid cellular automata method[14]
2.1.1 横梁弯曲变形拓扑优化
根据铝合金前碰撞横梁弯曲变形对横梁结构进行优化。图3所示为铝合金前碰撞横梁拓扑优化模型示意图。由图3可知,深色区域为设计空间,浅色区域为碰撞盒,横梁与碰撞盒通过共节点的方式连接,碰撞盒完全约束平动及转动自由度。初始条件下,刚性墙(柱)分别以13.3 m/s的速度与横梁发生碰撞。因铝合金前碰撞横梁具有对称性,为提高计算效率仅建立1/2模型。使用混合细胞自动机法进行拓扑优化分析,同时考虑两种碰撞模型并加入挤压成型工艺约束,挤压方向沿横梁水平方向。
图4所示为铝合金前碰撞横梁拓扑优化结果。由图4可知,随着迭代次数的增加,铝合金前碰撞横梁截面中间深色部分的材料被不断删除,壁厚逐渐减薄,最终优化结果显示横梁截面呈封闭的矩形。在相同外力作用下,背部封闭式结构的变形量小于背部开口式结构的,在弯曲变形过程中能够产生更大的抗力[18],因此,背部封闭截面形状的铝合金碰撞横梁具有较高的抗弯曲强度,能够将碰撞过程中的作用力均匀地向两侧吸能结构传递,并通过自身变形吸收较多的能量。
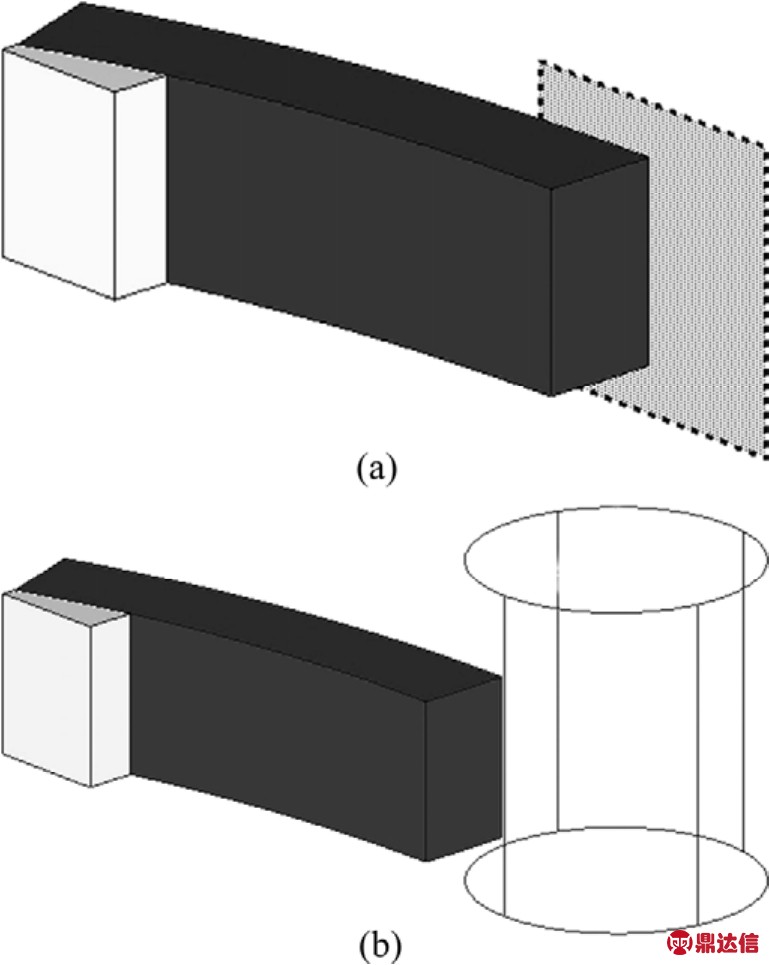
图3 铝合金前碰撞横梁拓扑优化模型示意图
Fig.3 Topology optimization models of aluminum bumper:(a) Rigid wall model; (b) Rigid pole model
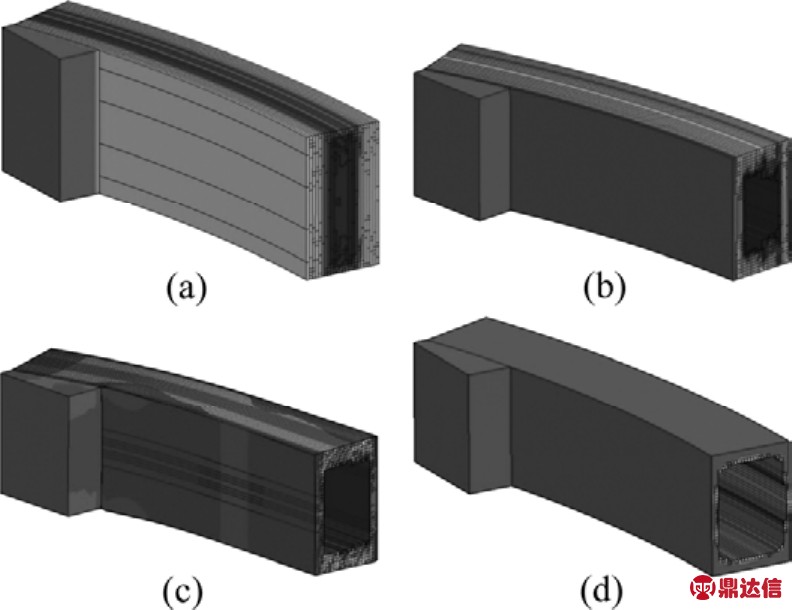
图4 不同迭代次数后混合细胞自动机拓扑优化铝合金横梁密度分布云图
Fig.4 Density distribution contours of aluminum bumper topology optimization by hybrid cellular automata method at different iterations: (a) Iteration 1; (b) Iteration 5; (c) Iteration 15; (d) Iteration 54
2.1.2 横梁截面压溃变形拓扑优化
根据铝合金前碰撞横梁弯曲变形后截面发生压溃变形的情况,对横梁截面加强筋的分布进行优化。矩形区域为设计空间,以表示碰撞横梁截面,左侧约束所有平动及转动自由度、模拟碰撞盒与横梁内侧的连接作用。刚性墙从右侧以13.3 m/s的速度与设计空间发生碰撞,如图5所示。
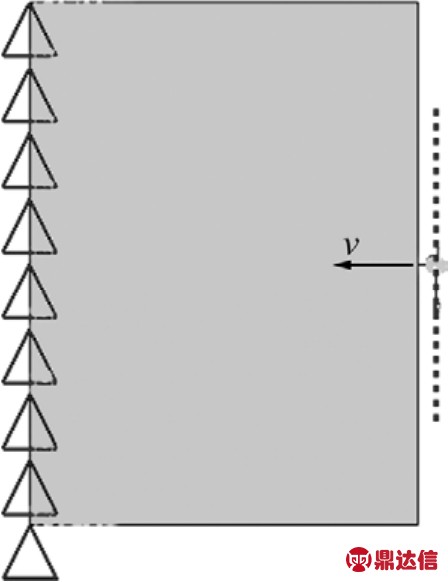
图5 铝合金前碰撞横梁截面加强筋拓扑优化模型示意图
Fig. 5 Schematic diagram of cross-section model of aluminum bumper topology optimization
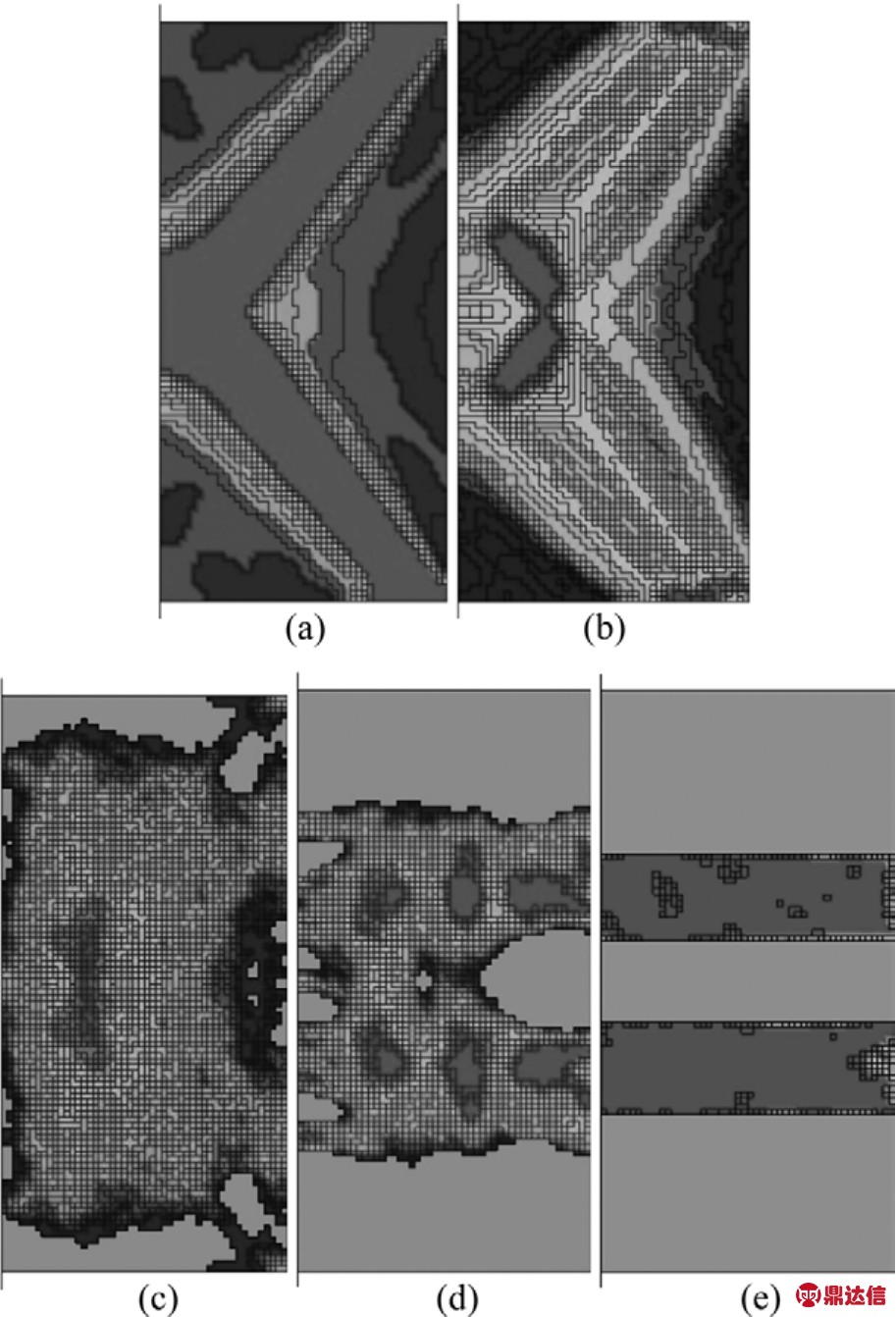
图6 混合细胞自动机拓扑优化横梁截面密度分布云图
Fig. 6 Density distribution contours of bumper cross-section topology optimization by hybrid cellular automata method:(a) Iteration 1; (b) Iteration 3; (c) Iteration 8; (d) Iteration 20;(e) Iteration 60
图6 所示为铝合金前碰撞横梁截面加强筋分布的拓扑优化结果。由图6可知,计算首先得到三角形结构的截面加强筋分布,但该结构仅适用于提高静刚度,结构失稳后变形抗力较小,吸能性能较差。随着迭代次数的增加,截面上、下两侧材料首先被删除,中部材料逐渐减少,最终优化结果为横梁截面两条加强筋沿受力方向呈水平分布。该截面结构的铝合金前碰撞横梁,相当于横梁内部加入了碰撞盒,加强筋失稳后继续折叠变形,可以吸收较多的能量。同时,横梁内部增加两条加强筋可显著增大抗弯曲强度,提高横梁在偏置碰撞、斜向碰撞或者柱撞时的耐撞性。
2.1.3 横梁截面拓扑优化结果
综合以上两个变形条件下的拓扑优化结果,背部封闭式结构在发生弯曲变形过程中能够产生更大的变形抗力,具有较高的结构强度,同时水平分布的加强筋结构能够在失稳后继续吸收能量,具有较优的吸能性能。设计铝合金前碰撞横梁截面形状,结构沿中心水平线呈对称分布,如图7所示。
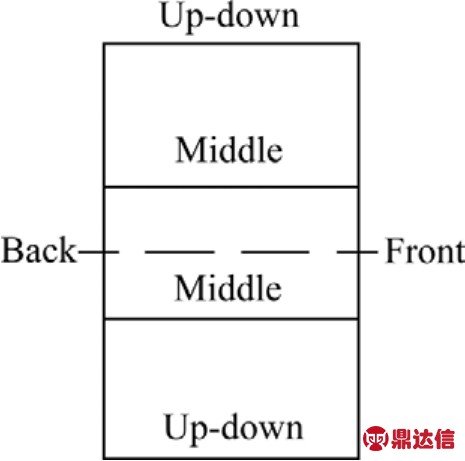
图7 铝合金前碰撞横梁拓扑优化截面形状示意图
Fig. 7 Schematic diagram of cross-section of aluminum bumper topology optimization
2.2 碰撞横梁尺寸优化
根据拓扑优化的结果,使用模拟退火算法优化铝合金前碰撞横梁截面尺寸。考虑横梁在冲击载荷作用下的吸能性能,建立有限元模型。将横梁两端与碰撞盒装配处节点耦合1 000 kg集中质量单元,并以13.3 km/h的速度撞向无限大刚性墙,使用LS-DYNA显式模块计算碰撞过程中横梁的吸能性能。铝合金前碰撞横梁有限元模型如图8所示。
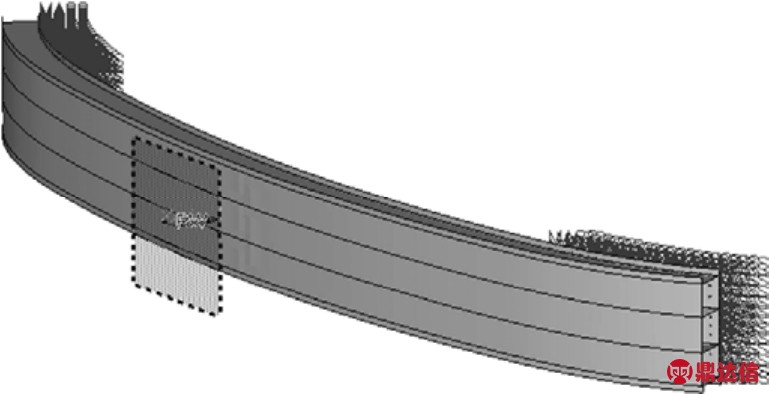
图8 铝合金前碰撞横梁有限元模型
Fig. 8 Finite element model of aluminum bumper
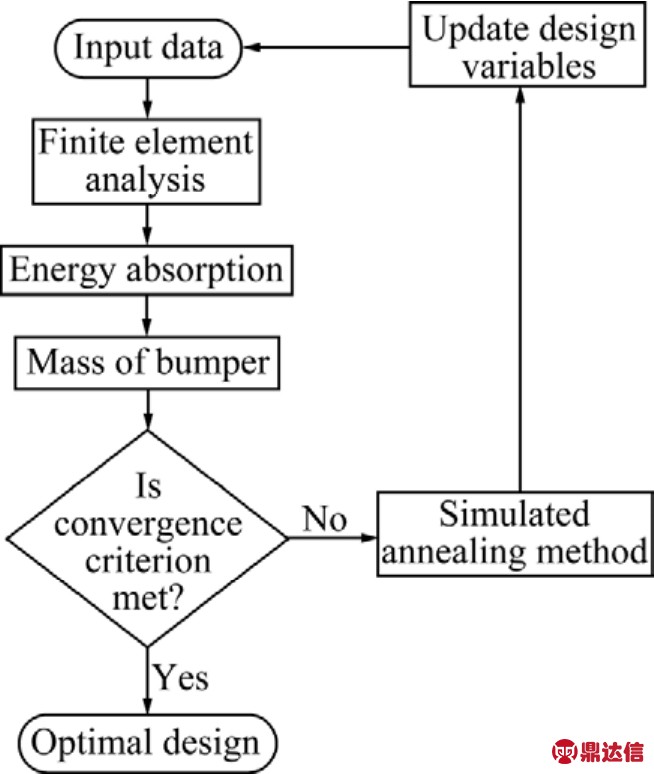
图9 铝合金前碰撞横梁优化流程
Fig. 9 Flow chart of optimization of aluminum bumper
图9 所示为铝合金前碰撞横梁优化流程图。由图9可知,壁厚作为输入变量,同时影响横梁的吸能性能与质量,通过采用模拟退火算法不断更新输入变量,最终满足收敛准则,获得铝合金前碰撞横梁最优设计方案。表2所列为优化系统设置参数。由表2可知,铝合金前碰撞横梁各部位初始壁厚均为3.0 mm,为满足横梁轻量化设计要求,约束横梁总质量小于4.0 kg,优化目标为横梁总吸能性能最优。最终优化结果同时考虑吸能性能与横梁质量对目标函数的影响,获得质量轻、吸能性能优的铝合金前碰撞横梁设计方案。
经过7 300次迭代,使用欧氏距离相似度准则,对优化数据进行分类处理,将相似数据组合到不同子集中,生成系统树图。使用4等级截断系统树图,绘制平行坐标图,如图10所示。由图10可知,左侧4条平行坐标轴分别对应设计变量Back、Front、Middle、Up-down,坐标轴 Energy为优化目标,坐标轴 Mass为系统约束。观察图10中4种设计方案可知,方案A的吸能性能最优,该方案中间两条加强筋(Middle)壁厚最大,能够大幅度提高横梁的吸能性能,但横梁总质量超过了系统约束(4.0 kg);深色加粗方案的吸能性能仅次于方案A的,且横梁总质量恰满足系统约束,因此,该结果为最优尺寸方案。观察该方案壁厚分布可知,最大壁厚为横梁的内、外两侧(Front & Back),而中间两条加强筋(Middle)的壁厚最小,该方案有利于提高碰撞盒与横梁内侧连接的稳定性,防止横梁在碰撞过程中脱落。
表2 模拟退火法优化条件参数
Table2 Optimization parameters of simulated annealing method
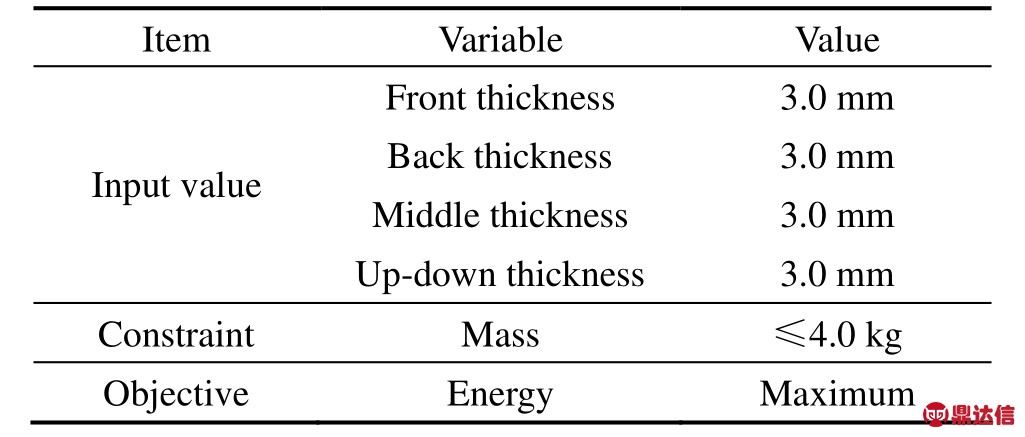
2.3 铝合金前碰撞横梁最终设计方案
综合考虑加工、装配等因素,结合尺寸优化结果合理调整壁厚,最终获得的铝合金前碰撞横梁截面尺寸如图 11所示。该设计方案充分利用铝合金成形性能优良的特点,可通过挤压工艺一次性加工出铝合金前碰撞横梁。
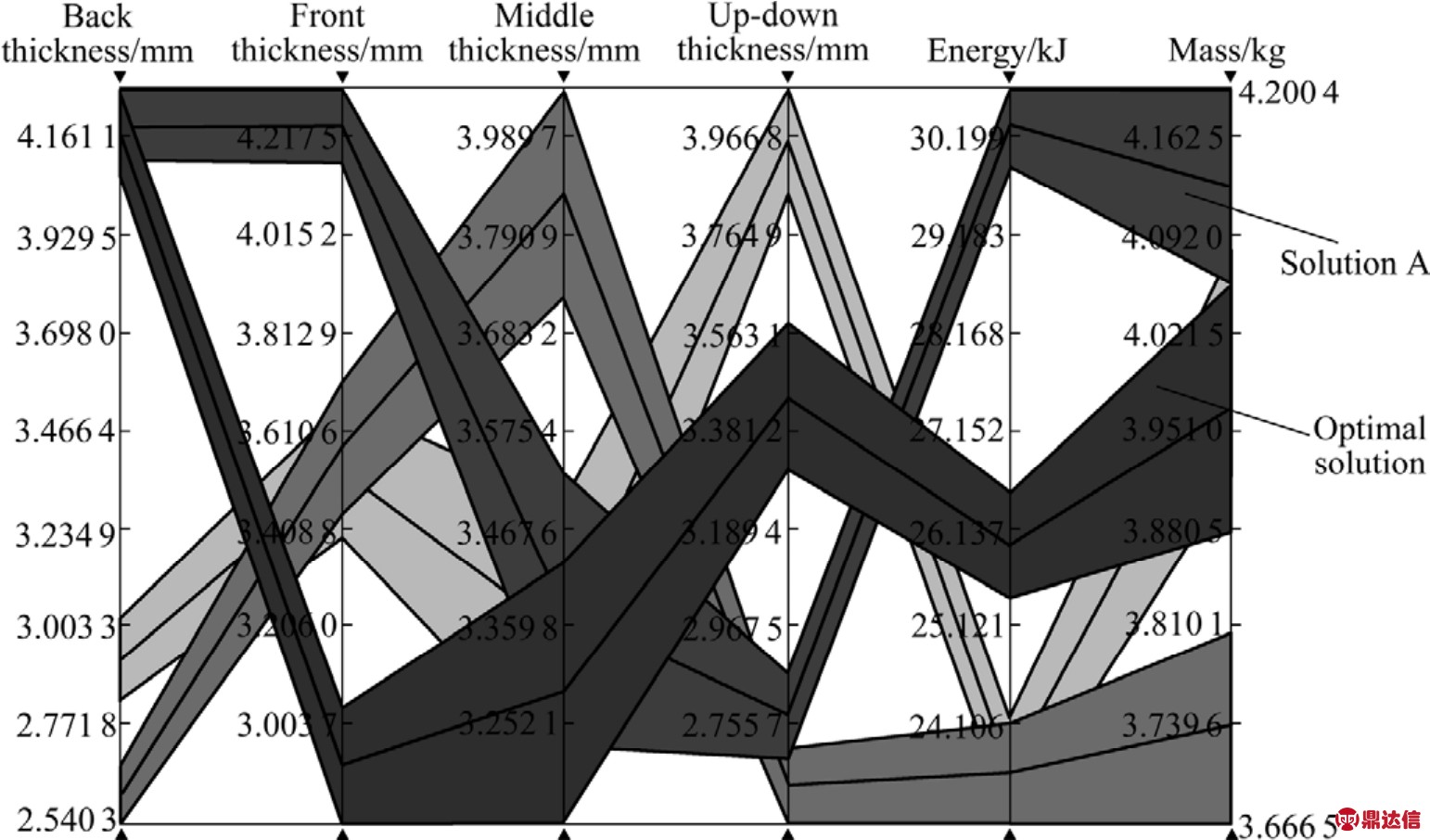
图10 模拟退火法优化结果平行坐标图
Fig. 10 Parallel coordinate plot of simulated annealing optimization results
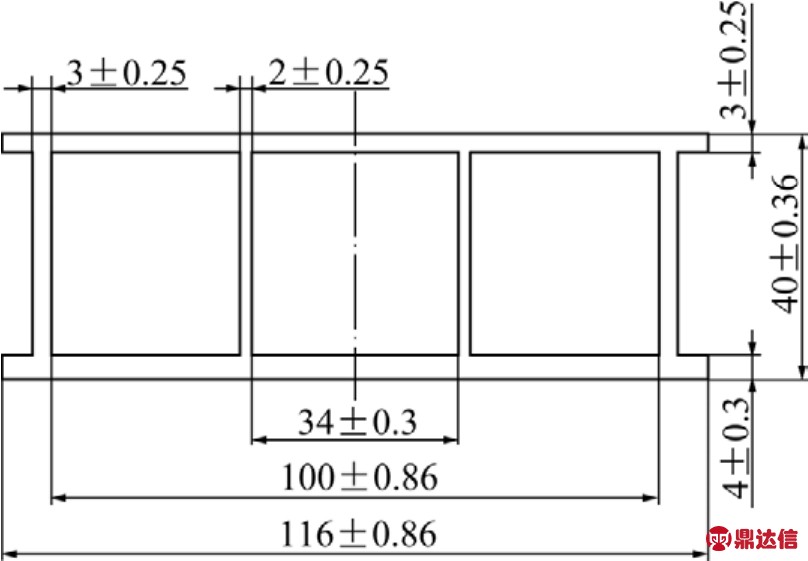
图11 铝合金前碰撞横梁型材截面尺寸
Fig. 11 Cross-section dimensions of aluminum bumper (mm)
根据某车型原钢质前碰撞横梁外形,设计出弧线形铝合金前碰撞横梁,如图12所示。铝合金前碰撞横梁的质量为3.71 kg,比原钢质横梁(4.95 kg)质量减轻了25%。
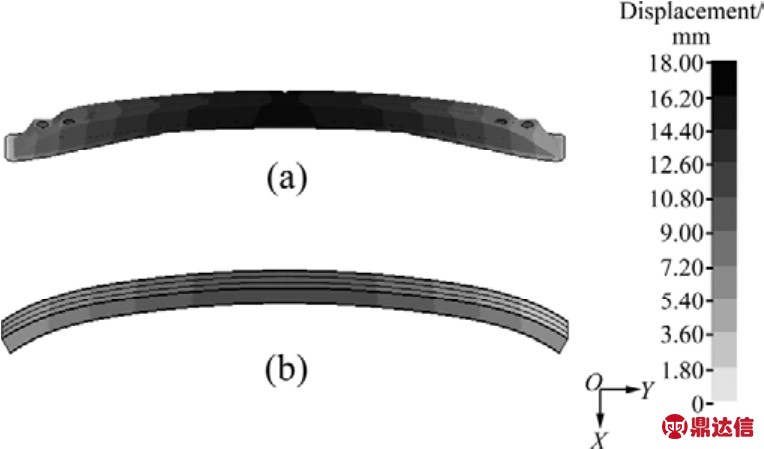
图12 汽车前碰撞横梁模型
Fig. 12 Models of automotive front bumper: (a) Steel bumper;(b) 6061 aluminum bumper
3 前碰撞横梁性能分析
3.1 横梁抗弯曲强度分析
在横梁中部沿X方向施加5.0 kN的作用力,两端约束除Y方向外所有平移自由度,并约束X和Y轴的转动自由度。使用LS-DYNA隐式求解模块计算,最终得到横梁X方向的位移云图,如图13所示。由图13可知,在5.0 kN的作用力下,钢质碰撞横梁X方向最大变形量约为18 mm;而铝合金碰撞横梁由于具有封闭式加强筋结构,其抗弯曲强度较高,在相同条件下,X方向的最大变形量仅为8.6 mm。
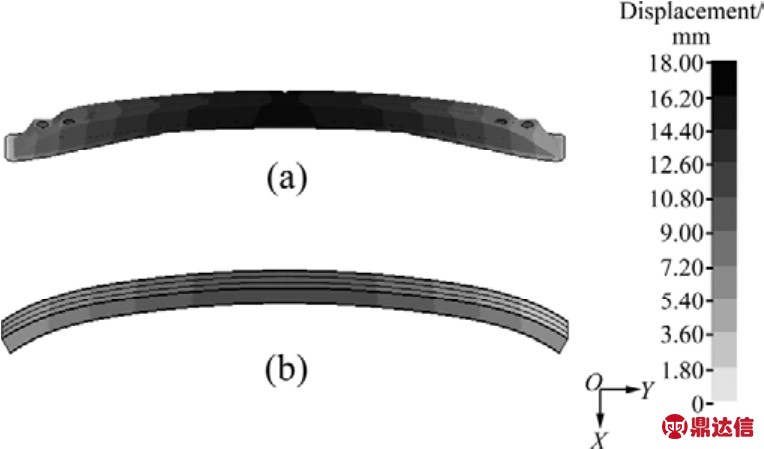
图13 汽车前碰撞横梁抗弯曲变形X方向位移云图
Fig. 13 X displacement contours along direction X of front bumper during static bending: (a) Steel bumper; (b) 6061 aluminum bumper
3.2 台车碰撞实验
为了进一步研究铝合金前碰撞横梁的碰撞吸能性能,钢质横梁采用点焊方式,铝合金横梁通过螺栓方式与原钢质碰撞盒总成连接,并固定在台车前端组成台车碰撞实验系统,台车统一配重1 180 kg,并以20 km/h的速度匀速撞向刚性壁障。在刚性壁障右方放置一台REDLAKE-LE高速摄像机,拍摄频率为1 000 f/s。台车左右B柱位置各安装两个量程均为±1 000 g的X向加速度传感器,采集碰撞过程中的加速度曲线。
图 14所示为高速摄像机拍摄的两种台车碰撞系统前碰撞横梁与刚性墙碰撞前的状态。
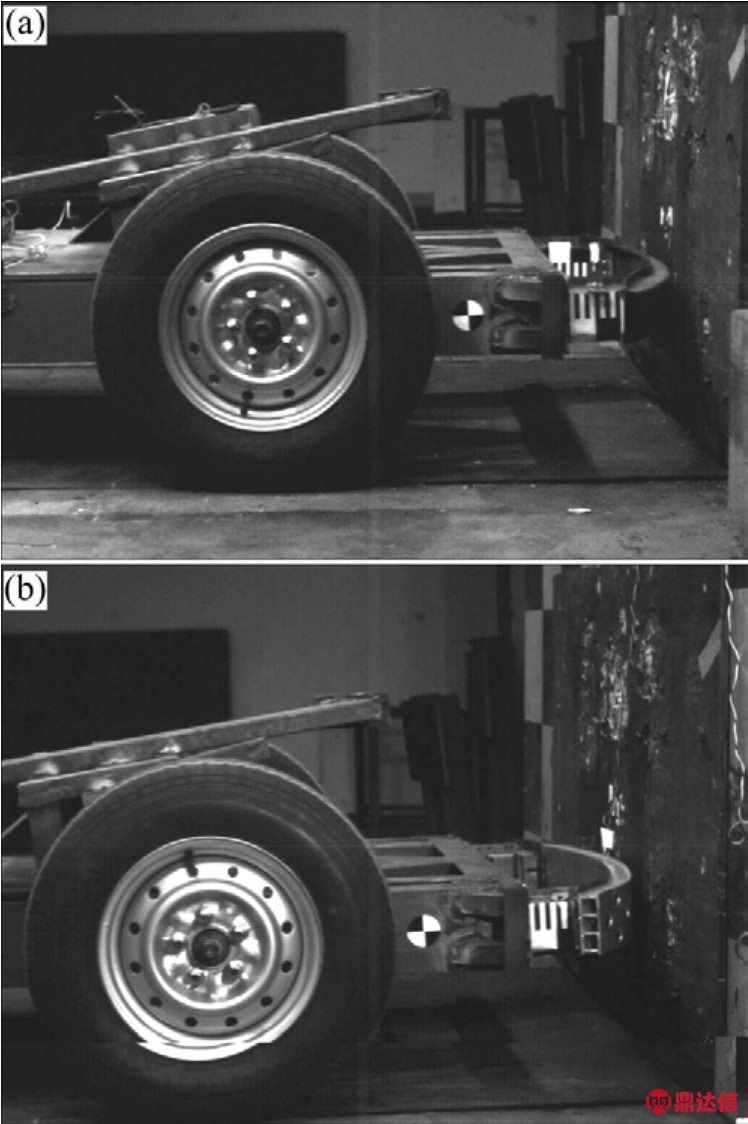
图14 20 km/h下台车碰撞实验
Fig. 14 Crash test at 20 km/h: (a) Steel bumper; (b) 6061 aluminum bumper
3.3 台车碰撞仿真
建立钢质碰撞横梁与铝合金碰撞横梁有限元模型,其材料模型采用Johnson-Cook本构方程,考察应变速率对材料力学性能的影响。通过计算机仿真研究前碰撞横梁在碰撞过程中的变形情况及吸能性能,为使仿真模型具有可对比性,台车统一配重1 180 kg,并以20 km/h的速度匀速撞向刚性壁障。图15所示为台车碰撞横梁变形实验与仿真结果对比。由图 15可知,在20 km/h低速碰撞条件下,前碰撞横梁弧形段压溃,碰撞盒充分变形,变形状态良好。对比实验与仿真结果,横梁及碰撞盒变形仿真结果与实验结果吻合较好。在低速碰撞条件下,钢质前碰撞横梁弧线段完全压溃,截面发生较大变形,而铝合金碰撞横梁截面未发生明显变形,说明铝合金横梁具有更高的结构强度。
图 16所示为实验与仿真台车加速度—时间历程曲线对比。由图16(a)可知,某车型钢质横梁碰撞前期平均加速度较小,台车于30 ms时加速度达到第一个峰值,40 ms时加速度继续上升,至60 ms前碰撞横梁完全压溃,台车车身与刚性墙发生刚性碰撞,台车加速度达到第二个峰值。由图16(b)铝合金前碰撞横梁与钢质横梁台车加速度—时间历程曲线对比可知,铝合金碰撞横梁台车的平均加速度与原钢质碰撞横梁的相近,但台车加速度第一个峰值提前出现,20 ms时台车加速度达到峰值,30 ms时加速度继续上升,至60 ms碰撞盒完全压溃,台车加速度达到第二个峰值,两次峰值间隔较钢质的横梁增大,其中,6061铝合金前碰撞横梁加速度最高峰值下降。两种台车系统加速度曲线峰值均低于300 m/s2,其均值不超过150 m/s2,其中,6061铝合金前碰撞横梁的加速度曲线变化平稳,加速度无明显峰值,能够对车内人员起到更好的保护作用。仿真结果与实验数据在加速度波形、峰值大小和时间历程上都基本一致,仿真模型与实验具有较高的近似程度,仿真精度较高。
3.4 前碰撞横梁吸能性能对比
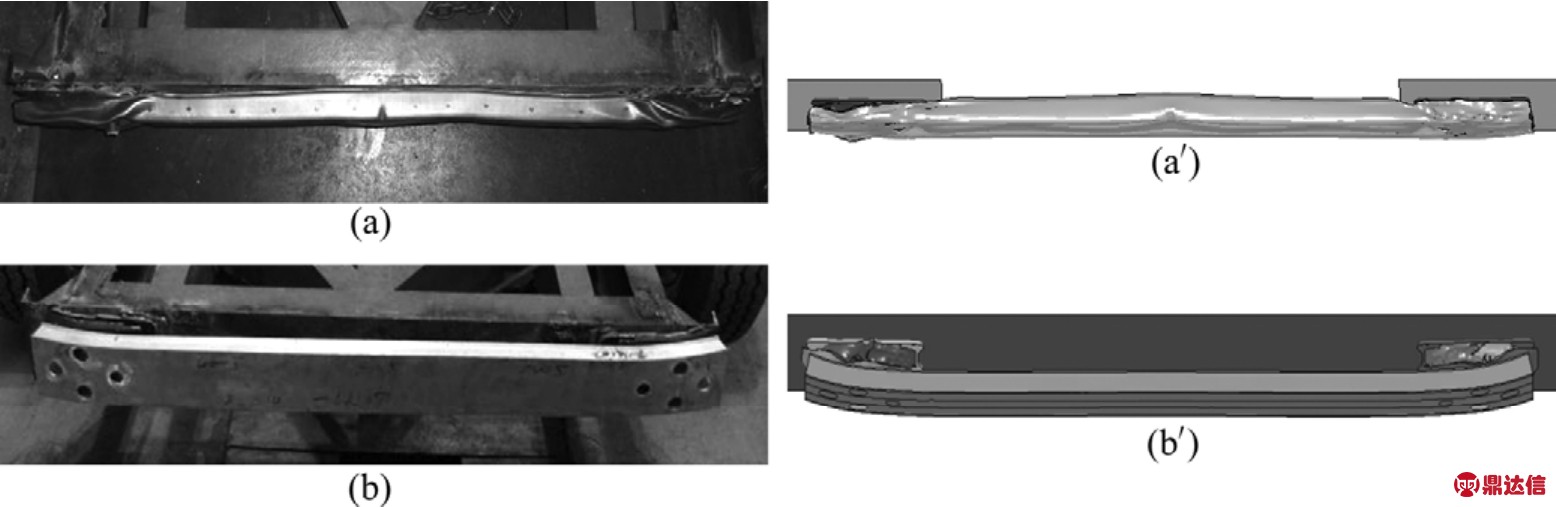
图15 20 km/h下台车碰撞横梁变形仿真与实验结果对比
Fig. 15 Comparison of simulated deformation ((a′), (b′)) with tested result ((a), (b)) of front bumper crash test at 20 km/h: (a), (a′)Steel bumper; (b), (b′) 6061 aluminum bumper
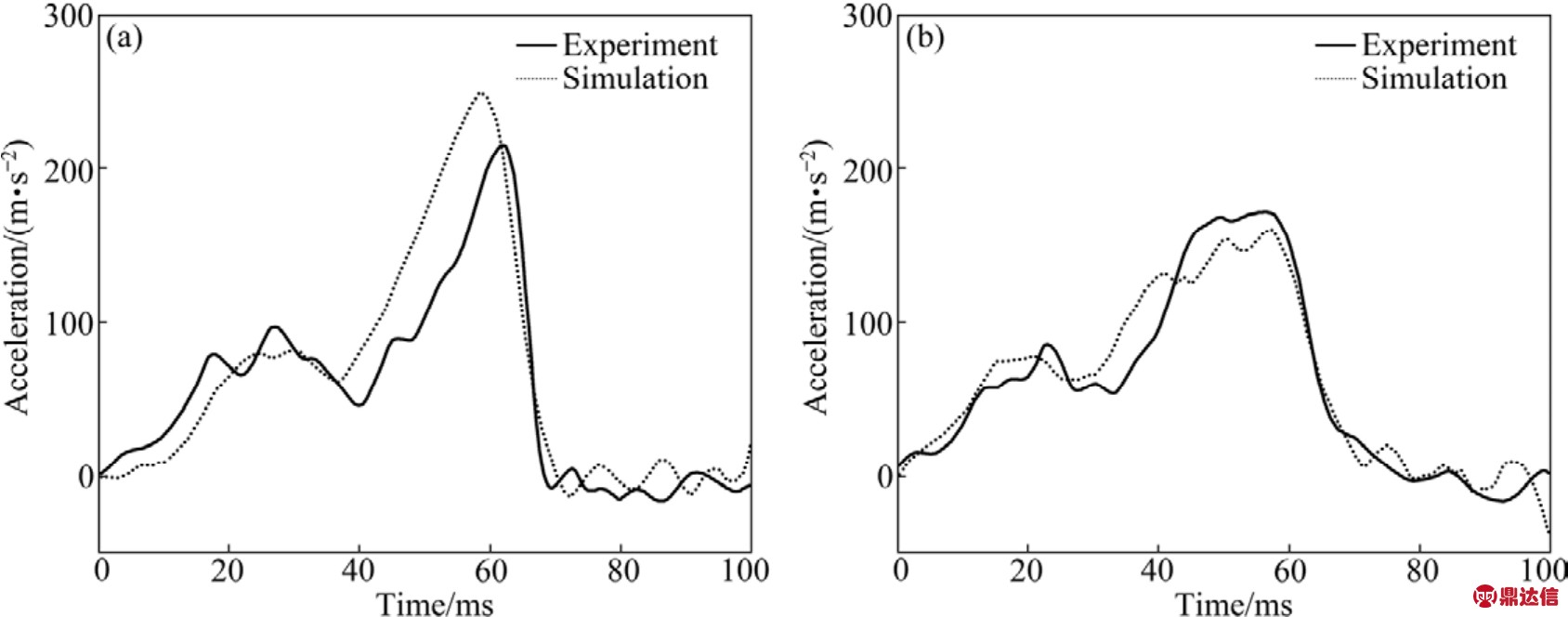
图16 前碰撞横梁加速度—时间历程曲线
Fig. 16 Acceleration vs time curves of front bumper: (a) Steel bumper; (b) 6061 aluminum bumper
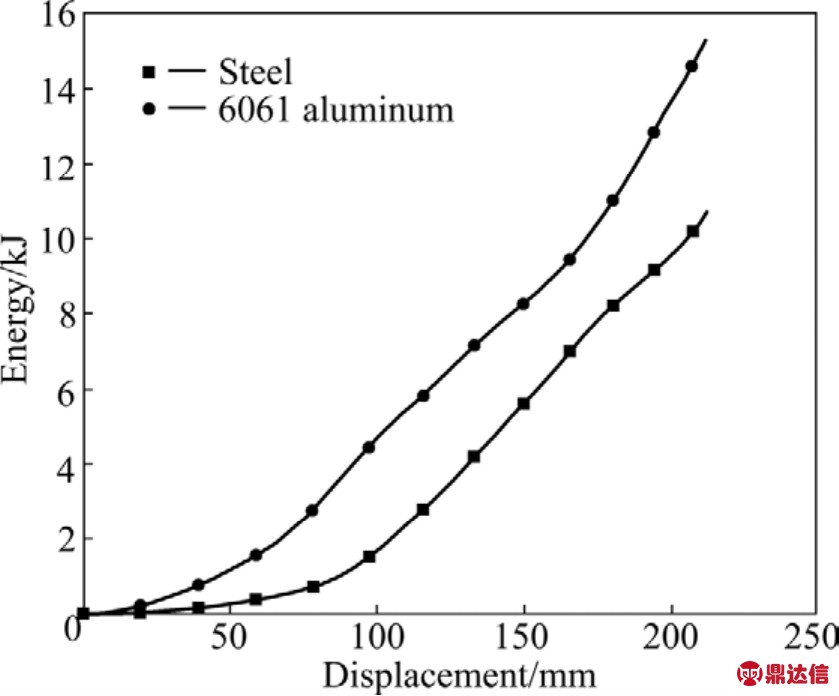
图17 前碰撞横梁20 km/h低速碰撞系统的总吸能曲线
Fig. 17 System energy absorption curves of front bumper in low speed crash test of 20 km/h
上述台车仿真模型中,两种台车系统碰撞盒均采用原钢质结构,仅碰撞横梁不同。对两种材质前碰撞横梁的台车系统进行20 km/h碰撞条件下吸能性能分析。图17所示为两种前碰撞横梁在20 km/h碰撞条件下系统吸能曲线。由图17可知,在低速碰撞条件下,由于铝合金碰撞横梁具有更高的抗弯强度,在相同的变形量下能够吸收更多的能量,其整体吸能效果明显优于原钢质件的。当变形量为210 mm时,碰撞盒充分变形,钢质前碰撞横梁系统吸能10 500 J,6061铝合金前碰撞横梁系统吸能15 283 J。6061铝合金前碰撞横梁较原钢质横梁系统的总吸能提高了45.6%。
对比两种材质前碰撞横梁吸能性能的结果表明:采用混合细胞自动机与模拟退火法优化可获得薄壁、中空且截面带有加强筋的铝合金前碰撞横梁,其质量轻、抗弯曲强度高,碰撞安全性好,且成型工艺简单。因此,6061铝合金前碰撞横梁相比钢质横梁具有更好的安全性能与轻量化效果,是替代传统钢质前碰撞横梁的理想结构。
4 结论
1) 采用混合细胞自动机拓扑优化可获得薄壁、中空且截面带有加强筋结构的铝合金前碰撞横梁设计方案。
2) 采用模拟退火算法可获得合理的铝合金前碰撞横梁壁厚分布,优化后的6061铝合金前碰撞横梁较原钢质横梁质量减轻了25%。
3) 在5.0 kN的作用力下,原钢质横梁沿X方向的最大变形量为18 mm,铝合金碰撞横梁的最大变形量为8.6 mm,其抗弯曲强度较高。
4) 碰撞仿真和实验结果表明,6061铝合金前碰撞横梁较原钢质横梁系统的总吸能提高了45.6%。