摘 要:基于有限元分析软件LS-DYNA 对设计的一种薄壁、中空且带加强筋的铝合金保险杠横梁的摆锤和台车试验进行了有限元模拟;并进行相关试验,与钢制横梁的碰撞性能进行对比。结果表明:在20km·h-1低速碰撞条件下台车有限元模拟与实际试验结果吻合较好;铝合金横梁较原钢制横梁有更好的刚度和吸能性能;在相同的碰撞试验条件下,钢制横梁的吸能性有限,而铝合金横梁能够在较大的速度范围内保持较高的吸能性能。
关键词:铝合金;保险杠横梁;碰撞;吸能性能
0 引 言
降低油耗、减少排放、提高安全性能是当今全球汽车工业所必须面对的问题[1],汽车轻量化则是实现汽车节能减排的一个重要措施。据国际权威部门统计,汽车所用燃料的60%消耗于汽车自重,汽车质量每减轻10%就可以降低油耗6%~8%[2]。铝合金型材具有密度小、强度高、耐蚀性好等特点,在达到同样的力学性能指标下,可比钢减轻47%[3]故而,其可作为替代钢制保险杠的材料。通过优化合金成分,合理安排热处理工艺以及优化保险杠的结构,可提高铝合金保险杠的吸能性,在减轻车身质量的同时满足其安全性能的要求。
研究保险杠的耐撞性对提高汽车的碰撞安全性具有重要意义[4]。近年来,随着我国汽车安全强制性法规的逐步实施,对保险杠耐碰撞性能的要求也愈来愈高。从设计角度考虑,希望能在开发阶段即预知保险杠结构碰撞安全性能是否满足法规的要求,同时找出结构设计上的缺陷,提高保险杠的碰撞性能,从而降低试验和试制费用,提高产品的竞争能力,因而有限模拟仿真软件在保险杠设计过程中的应用也越来越广泛[5]。目前,国外在汽车碰撞计算机模拟方面的研究已具备了相当扎实的基础,而我国在此方面的研究尚处于起步阶段,碰撞试验研究和计算机模拟碰撞研究的基础都很薄弱[6-7],相关文献也不多。
为此,作者以显式动态有限元理论为基础,根据国内某车型原钢制保险杠横梁设计出中空、带有加强筋的铝合金保险杠横梁结构。运用LS-DYNA 软件进行了有限元仿真模拟分析及实际台车试验验证,对比分析了铝合金横梁和钢制横梁在碰撞过程中的吸能性能及变形行为,期望对汽车保险杠的设计优化提供了一定的参考。
1 保险杠横梁有限元模型的建立
根据某汽车公司提供的钢制保险杠横梁截面形状及尺寸,设计出一种薄壁、中空且带加强筋的6061铝合金保险杠横梁结构,其相比于原钢制保险杠横梁,减轻38%,横梁的3D 结构如图1所示。
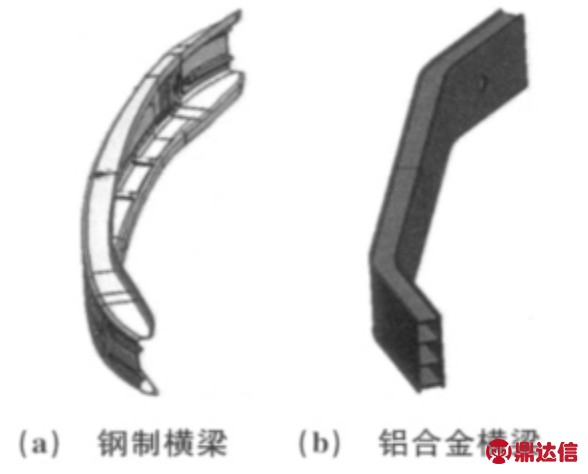
图1 不同材料保险杠横梁的3D模型
Fig.1 3Dmodels of bumper beams with different materials:(a)steel beam and(b)aluminum alloy beam
将保险杠横梁的3D 模型导入Hypermesh 有限元软件中进行网格划分,网格划分时应尽量使网格大小均匀,避免出现小单元、夹角单元和翘曲的壳;为了节省计算时间和保证精度,保险杠前碰撞横梁选取Belytschko-Tsay 单元类型,其有限元模型如图2所示。考虑应变速率对材料应力-应变曲线的影响,横梁选择24 号材料模型[8-10],其中钢材(DC04)及6061铝合金材料参数如表1所示。
2 摆锤冲击试验有限元模拟结果
摆锤冲击试验的目的是考察低速碰撞过程中整车所受的损伤,要求保险杠系统在冲击过程中无明显的塑性变形和表面损伤[11]。根据SAE 标准[12]中有关保险杠低速碰撞系统的相应规定和标准,建立保险杠横梁摆锤冲击有限元模型,进行低速摆锤冲击有限元仿真计算。其中摆锤质量为2 274kg,撞击中心离地面高445mm,摆锤冲击的速度为4km·h-1。
由图3可知,钢制保险杠横梁在x 方向上的变形集中在其中心部位,最大变形量节点的位移为5 2.61mm;铝合金横梁的变形则分布于其中心两侧,其最大变形量节点的位移为4.855 mm。由此可知,铝合金横梁较钢制横梁有更高的刚度,能够在轻微碰撞下为车辆提供更好的保护。
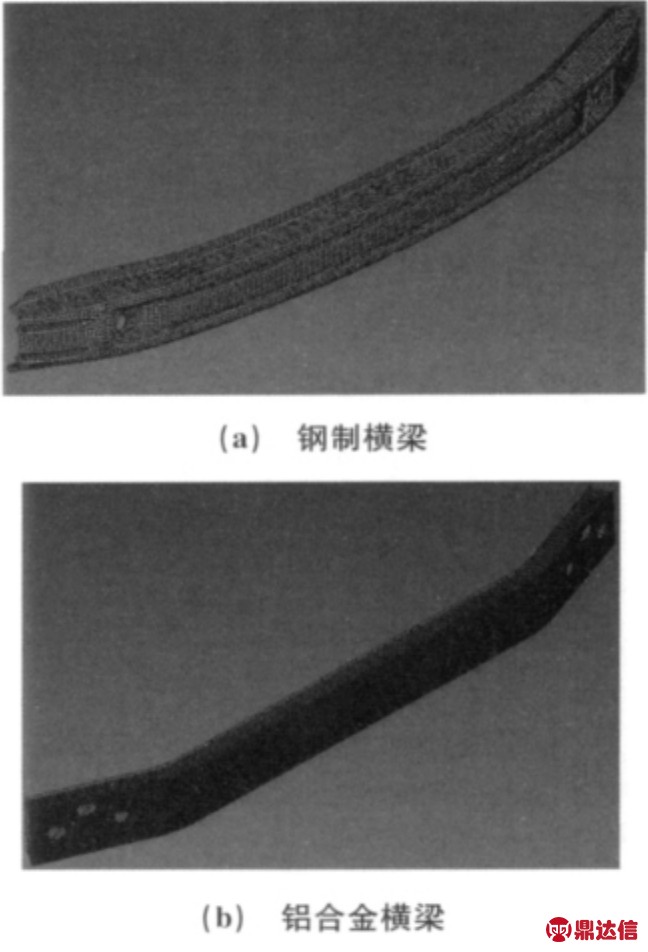
图2 不同材料保险杠横梁的有限元模型
Fig.2 Finite element models for bumper beams with different materials:(a)steel beam and(b)aluminum alloy beam
表1 DC04钢及6061铝合金的材料参数
Tab.1 Material parameters of DC04 steel and 6061aluminum alloy
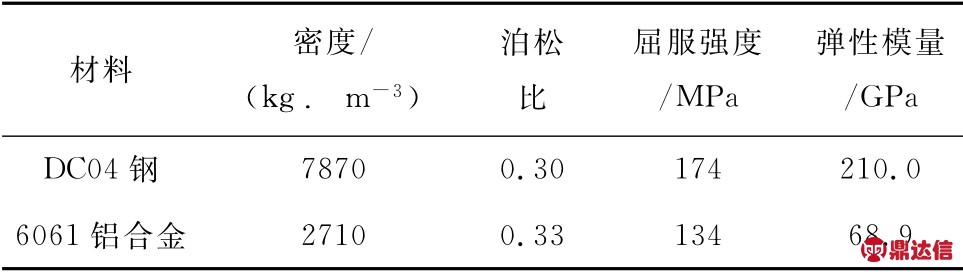
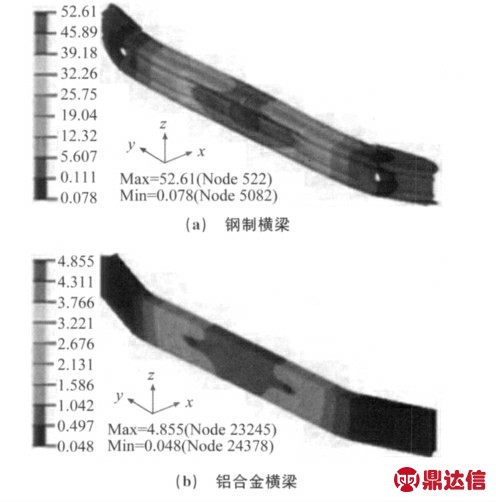
图3 不同材料保险杠横梁摆锤冲击试验变形云图
Fig.3 Deformation contours for bumper beams with different materials in pendulum impact test:(a)steel beam and(b)aluminum alloy beam
3 有限元模拟及试验结果
3.1 台车试验
通过装有保险杠的可移动台车替代实车进行碰撞试验来分析保险杠的安全性能[13]。将钢制保险杠和铝合金保险杠固定在台车前端组成台车碰撞试验装置,如图4所示。台车统一配重后总质量为1 180kg,并分别以20km·h-1和50km·h-1的速度撞向刚性壁障。
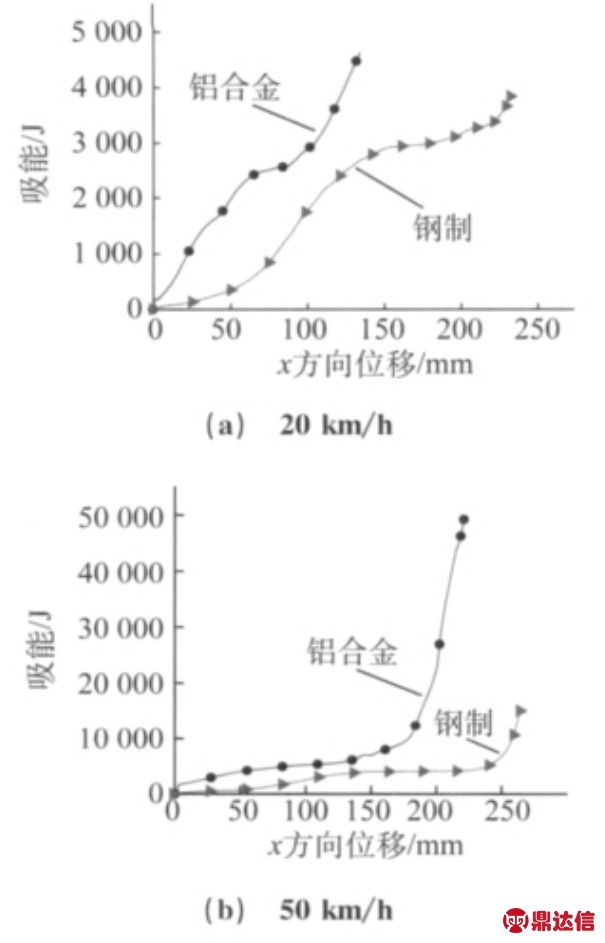
图4 台车碰撞试验装置
Fig.4 Equipment of platform crash test
3.2 低速碰撞的有限元模拟及试验结果
3.2.1 20km·h-1低速台车碰撞过程中保险杠横梁的变形
在碰撞过程中,钢制保险杠横梁由于是弧形过渡且刚度较低,横梁先被压平整后吸能盒开始变形吸能,碰撞完成后横梁趋于平整。铝合金保险杠横梁由于存在折角,其刚度相对于别的部位都要高,在整个碰撞过程中横梁及吸能盒的变形同时进行;当折角与刚性壁障接触后,横梁整体受到一个扭矩的作用,最终导致横梁中心向内凹陷。由图5 与图6对比可以看出,两种不同材料保险杠横梁的变形有限元仿真结果和实际试验结果吻合较好。
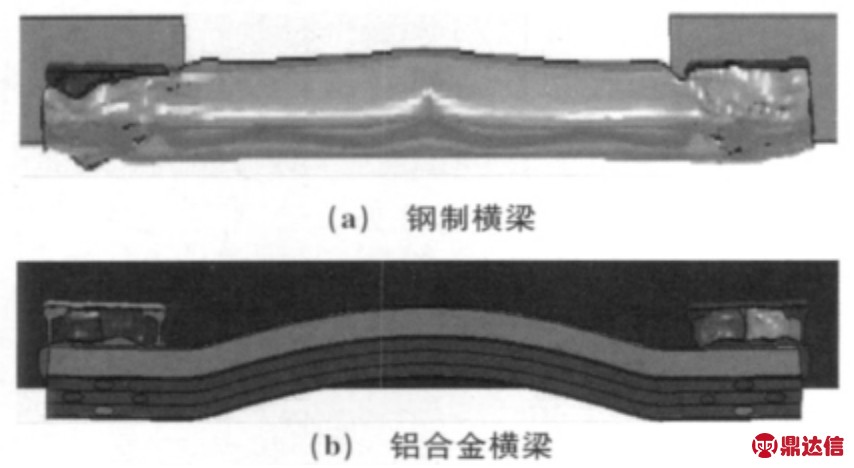
图5 不同材料保险杠横梁有限元模拟低速碰撞的变形结果
Fig.5 Deformation for finite element simulating the low rate crash of the bumper beams with different materials:(a)steel beam and(b)aluminum alloy beam
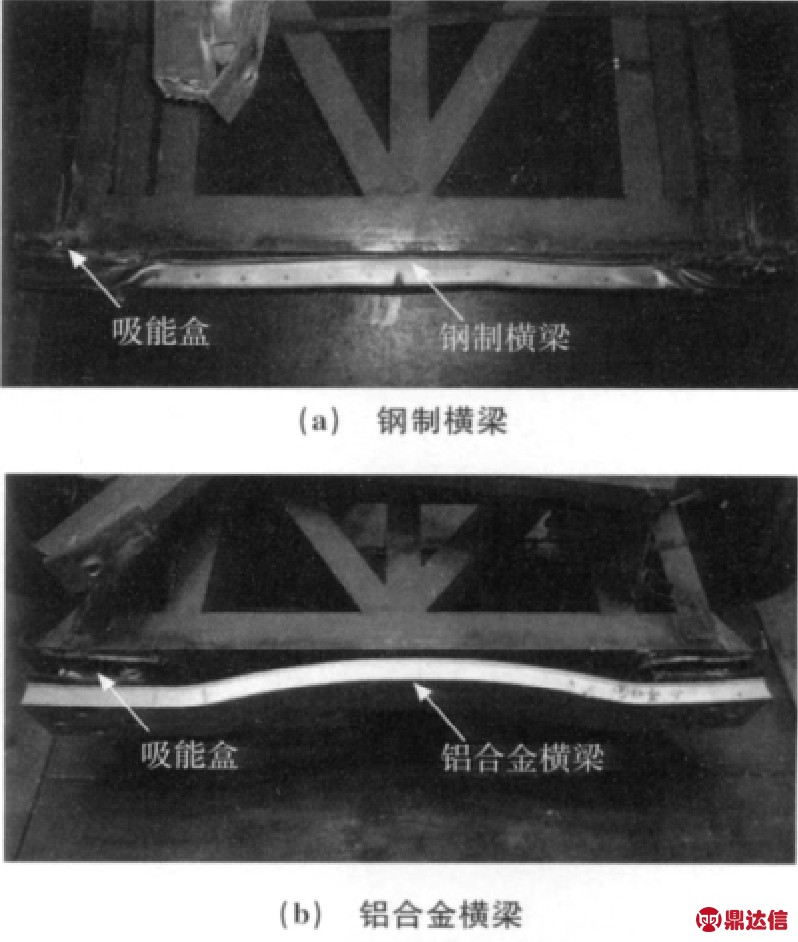
图6 不同材料保险杠横梁在低速碰撞试验过程中的变形结果
Fig.6 Deformation of the bumper beams with different materials during low rate crash tests:(a)steel beam and(b)aluminum alloy beam
3.2.2 20km·h-1低速台车碰撞的加速度曲线
图7中20km·h-1低速台车碰撞试验与模拟仿真的加速度时间-历程曲线吻合较好。由图7(a)可知,装有钢制横梁的台车在碰撞变形初期加速度上升较为平缓,平均加速度较低,承载能力较弱,于20ms左右达到第一峰值;在20~40 ms这段时间内,台车的加速度有波动但幅度不大;40ms时加速度急剧上升,吸能盒开始变形,直至60ms时吸能盒被完全压溃,保险杠总成失效,台车车身与刚性墙发生刚性碰撞,此时台车加速度达到最大峰值。
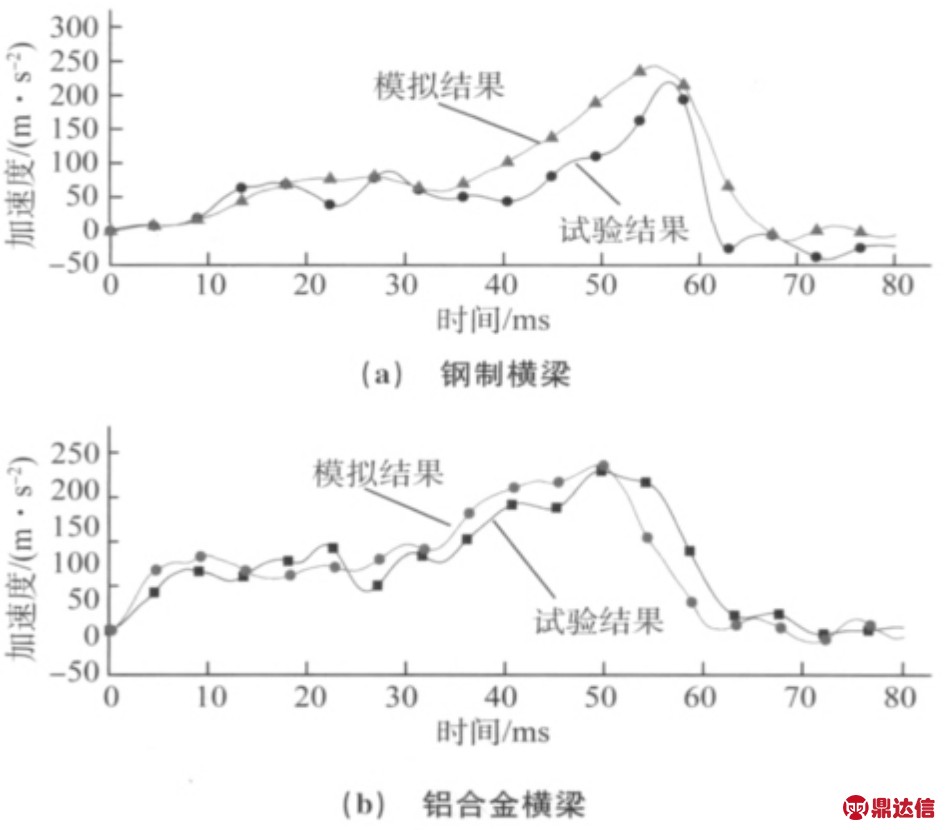
图7 不同材料保险杠横梁在20km·h-1碰撞时的加速度-时间曲线
Fig.7 Acceleration-time curves of the bumper beams with different material crashed at the rate of 20km·h-1:(a)steel beam and(b)aluminum alloy beam
由图7可知,低速台车碰撞过程中铝合金横梁的平均加速度与钢制横梁的相当,但铝合金横梁的加速度第一峰值及最大峰值的出现都提前。在10ms时加速度达到第一峰值并于30ms左右加速度继续上升,50 ms时加速度达到最大峰值。与钢制横梁相比,铝合金横梁的加速度曲线出现波峰的次数多,但铝合金横梁加速度曲线的最大峰值较钢制横梁的下降了41m·s-2,这对乘客的安全具有重大意义。由此可知,铝合金保险杠横梁的安全性能比钢制的更好。
3.2.3 20km·h-1低速台车保险杠横梁吸能性能的有限元模拟
由图8可知,在低速碰撞条件下,由于铝合金横梁具有更高的结构刚度,在相同变形量的条件下比钢制横梁能够吸收更多的能量,其整体吸能效果明显优于钢制横梁的。在碰撞过程中,当铝合金横梁变形量为136mm 时吸能盒被完全压溃,横梁吸能达到峰值4 704J;而钢制横梁在变形量为230mm时吸能盒充分变形,横梁的吸能峰值为3 830J。对比试验数据可知,铝合金保险杠横梁吸能量较钢制保险杠模梁提高了22.82%,这从另一方面也证明铝合金横梁的安全性能要优于钢制横梁的。
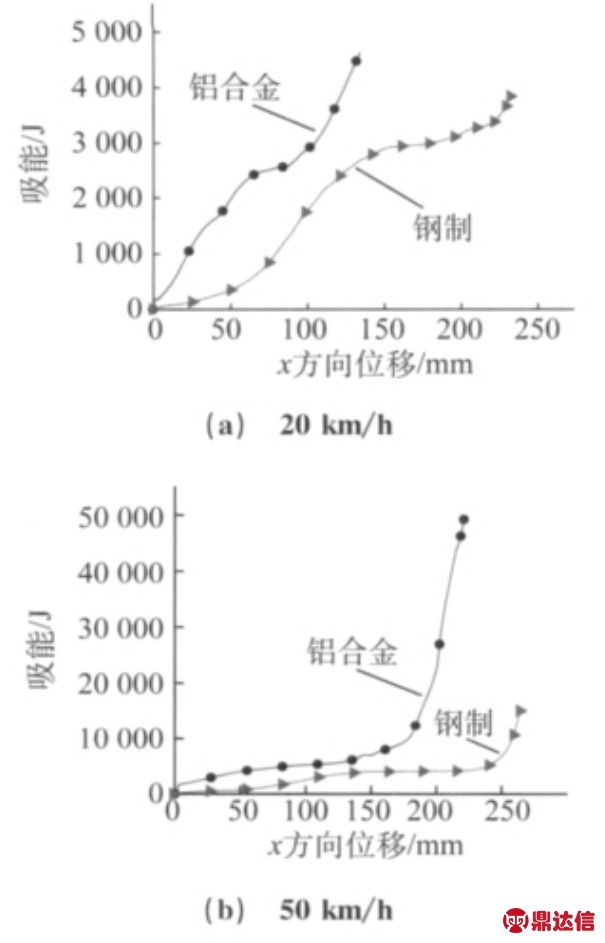
图8 有限元模拟不同保险杠横梁碰撞的吸能曲线
Fig.8 The energy absorbing curves for finite element simulating the crash of the bumper beams with different materials
3.3 50km·h-1高速台车碰撞保险杠横梁吸能性能的有限元模拟
对比图8可知,钢制保险杠横梁在高速碰撞条件下吸能值较低速碰撞时增加了2.95 倍(达到15 167J),而铝合金保险杠横梁的吸能值提高了9.45倍(49 151J)。由此可知,相对于铝合金横梁,钢制横梁的吸能性能存在一定的极限,在高速碰撞中不能吸收更多的能量,碰撞安全性较低;而铝合金横梁则能够在较大的速度范围内保持较好的吸能性能。
3.4 铝合金保险杠横梁的吸能机理
铝合金保险杠横梁由前端面、后端面、外侧和加强筋四个部件组成,如图9所示。
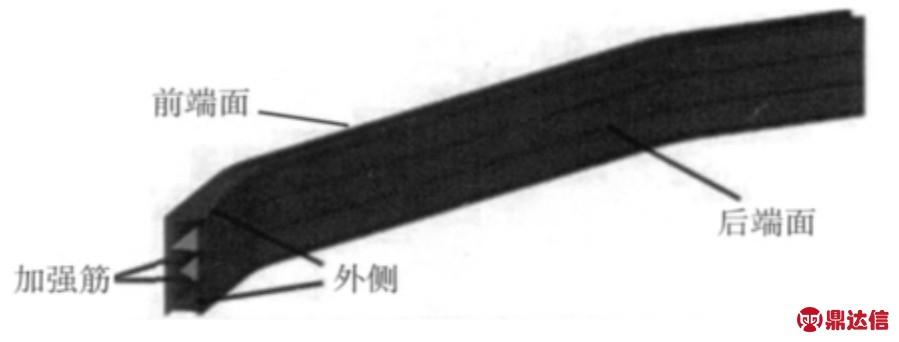
图9 铝合金横梁的结构示意
Fig.9 Sketch map of aluminum alloy bumper beam
在台车正面碰撞过程中,横梁通过各部件的弹塑性变形来吸收能量,其中两对加强筋的溃缩变形可以吸收很大部分的能量。图10中四条曲线分别代表铝合金保险杠横梁在50km·h-1高速碰撞有限元模拟过程中各部件的吸能指数。在碰撞过程中,当铝合金保险杠横梁与刚性墙开始接触时,横梁截面开始发生溃缩变形,加强筋和外侧结构在此过程中发生欧拉屈服,吸能指数迅速增加,超过其他两个部件约5.5倍;当加强筋屈服后则会出现折屈,吸能性能急剧下降,吸能指数趋于恒值[14]。由此可知:在碰撞过程中,中空且带有加强筋截面结构的铝合金横梁由于加强筋结构的影响,使截面吸能性能明显提高,而钢制横梁无类似的加强筋结构。
对比两种横梁的有限元模拟及试验结果表明:薄壁、中空且截面带有加强筋的铝合金前保险杠横梁具有质量轻,碰撞安全性好,成型工艺简单等优点,是替代传统钢制保险杠横梁的理想结构材料。
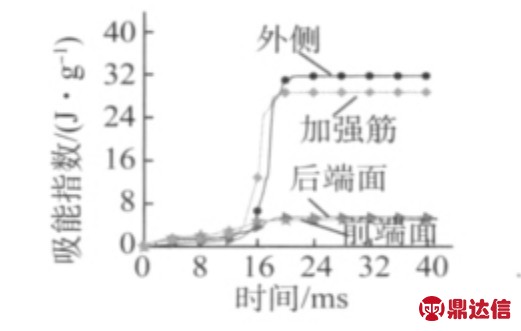
图10 铝合金横梁各部件在50km·h-1高速碰撞过程中的吸能曲线
Fig.10 Energy absorbing curves of each part of aluminum bumper beam in crash test at 50km·h-1
4 结 论
(1)薄壁、中空且带加强筋结构的铝合金横梁较钢制横梁质量减轻了38%,且具有更好的安全性能。
(2)在20km·h-1低速碰撞条件下,台车碰撞有限元模拟结果与实际碰撞结果吻合较好。
(3)铝合金保险杠横梁较钢制保险杠横梁有更好的刚度及吸能性能,在相同的变形条件下,前者能吸收更多的能量。
(4)在不同碰撞速度下,钢制横梁的吸能性有限,而铝合金横梁能够在较大的速度范围内保持较高的吸能性能。