摘 要:针对目前烟草物流中心采用的人工分拣包装效率低下的问题,项目研发团队研发了一套具有良好适应性、安全高效全自动异型烟码垛及包装流水线。采用了伺服控制技术、PLC控制技术、图像识别技术、机器人技术以及人机交互技术等多项先进技术实现了全自动异型烟码垛及包装流水线系统的功能并详细论述了系统的特点、原理、控制过程及关键技术。通过现场的安装调试,全自动异型烟码垛及包装流水线运行性能良好,完成了对异形烟全自动码垛及包装流水线的要求。
关键词:码垛包装机;可编程控制器;伺服技术;机器人技术;图像识别
1 引言
长期以来,我国烟草配送中心由于异型烟的尺寸各异,难以和标准烟一样实现自动化分拣、包装,而人工的包装方式效率低下、劳动强度大且出错率高、人工成本高,远远不能满足当今烟草分拣包装的需求。在配送中心,商品必须先按客户的订单从配送中心进行人工分拣,挑选订单的不同品牌的条烟是配送中心中所有作业最费力的,其劳动量占配送中心的60%。现在,许多国内配送中心采用电子标签和RF手持终端进行订单内产品的分拣。
在国外,烟草配送中心已经采用同一条流水线采用多台码垛机对不同品牌的条烟在同一垛位进行码垛并包装,包装的香烟品牌种类多,使用的巷道少。国外学者已经解决采用多台工业机器人进行协同工作,并且采用状态归并和变迁简化等方法提高机器人分拣及包装的效率,缩减劳动规模并能自动优化订单结构。使总包装的差错率减少60%以上。相比与国内较为先进。为了改变这一现状,各科研院所都在致力于开发一种安全和高效的包装系统。针对这一问题,某公司研发了一套异型烟智能包装线,采用了机器人技术、图像识别技术、基于互联网的集散控制技术等多项先进的自动化技术,实现了异型烟的智能识别、自动码垛及包装,工业机器人采用优化的码垛算法实现可以根据码垛要求来实现抓取不同数量的异型烟,并进行堆码[1-5]。详细论述了全自动异型烟包装码垛系统的控制设计。
2 系统组成及工作原理
2.1 机械组成及原理
根据订单结构,经过异型烟摄像识别无误后,将主分拣线出来的异型烟经摆臂皮带机分成上下两层,各个订单进入各个工位的机器人自动码垛(根据订单结构,大订单以包为单位进入各自码垛机器人),机器人码完一垛烟后,经皮带机自动向前移动一个工位,让机器人继续下一垛烟的码垛,经送烟机构往横移机构里送烟;最后横移机构自动将垛烟移至裹膜机入口,推烟机构将其送入裹膜机自动裹膜热收缩;裹膜机包装好的烟包有序出来后进行影像复核并自动贴标。异型烟全自动码垛及包装线机械结构,如图1所示。
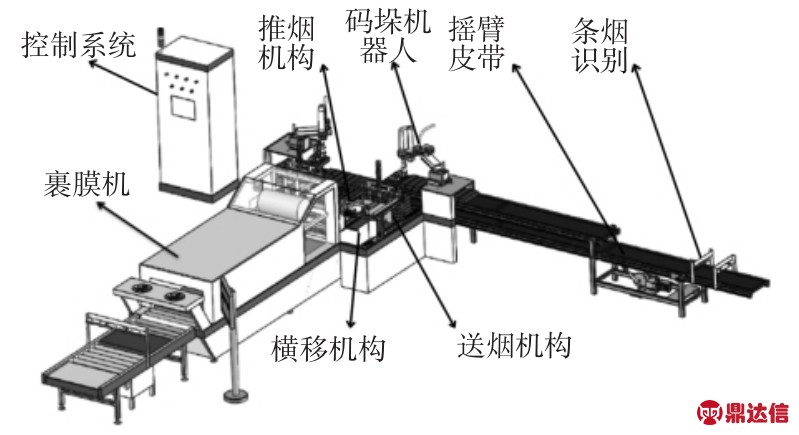
图1 异型烟全自动码垛及包装线机械结构
Fig.1 Shaped Cigarettes Automatic Palletizing and Packaging Line Mechanical Structure
2.2 控制系统的组成
整个异型烟智能化包装线成套设备控制系统由4个控制单元组成,分别为分拣控制单元、码垛控制单元、输送检测控制单元、包装控制单元。每个单元都由相应的控制核心及其辅助元器件各自组合成小的控制单元,详细论述了包装控制单元的控制设计。包装控制单元电气控制系统框图,如图2所示。系统由控制模块、操作模块、检测模块、执行模块组成,其中控制模块的控制核心主要是PLC,操作模块主要是人机交互页面,检测模块主要是光电开关,激光测距开关等。执行模块主要是交流接触器、电磁阀、电机等。其工作过程为:客户提交订单,由工控机分析出适合码垛形状的新订单,新订单按照当时的工况判断哪一层的码垛机器手来进行堆码,并进行包装。所走路线是经过条码识别系统单元,摇臂皮带单元,到达码垛工作单元。堆垛完毕后经送烟机构和推烟机构的有效配合进入裹膜单元进行裹膜。

图2 电气系统框图
Fig.2 Electrical System Block Diagram
3 系统设计及主要技术确定
3.1 硬件设计
要求设备高速连续运转20小时以上,否则将会影响异型烟包装的全部过程,造成巨大的损失。由于PLC具有控制精度高、操作方便、可控性好,并且适应工业现场的高温、冲击、震荡等恶劣环境,所以PLC来控制异型烟包装的整个过程。选用的德国西门子公司的317型PLC,CPU具有大容量程序存储器,可用于要求很高的应用和多任务自动化系统,在具有集中式和分布式I/O的生产线上作为集中式控制器使用,对二进制和浮点数运算具有较高的处理能力,用于大量的I/O扩展,在PROFIBUS上实现等时同步模式。由上位计算机构成的异型烟码垛及包装线的硬件连接图,如图3所示。
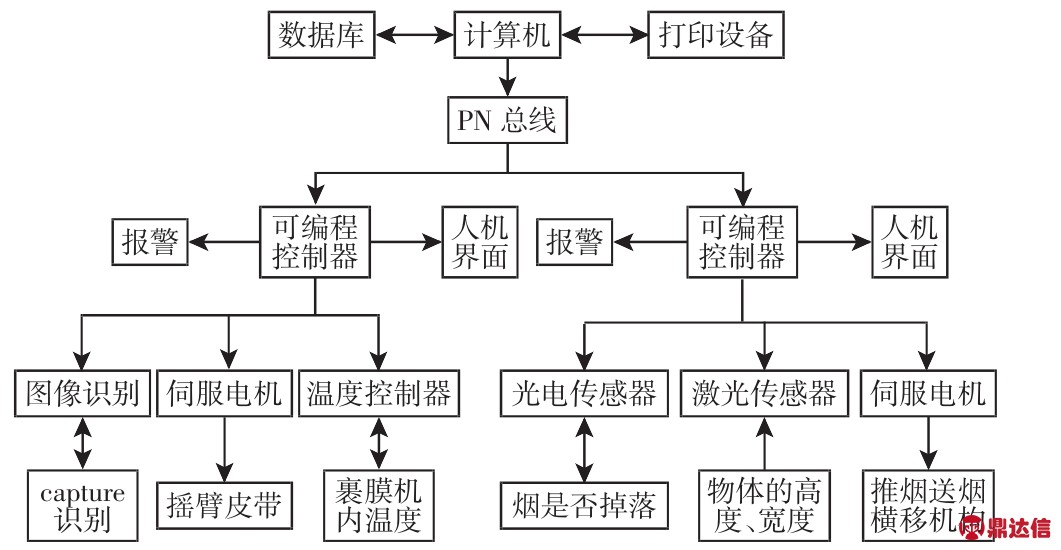
图3 硬件连接图
Fig.3 Hardware Connection Diagram
在PLC控制系统中,主要有96个输入点,64个输出点。考虑到尽量品种单一化,采用的模块尽量一致,主要包括:西门子品牌CPU314c—2PN(6ES7 314-6EH04-0AB0)数目:2 个;西门子公司输入模块 32-SM321(6ES7321-1BL00-0AA0),数目 3 个;西门子公司输出模块32--SM322(6ES7 322-1BL00-0AA0),数目2个。
3.2 软件设计
系统主要包括码垛机器人堆码设计和分层设计。考虑到码垛及包装线的执行元件和状态检测元件数量较多,故不能采用那种梯形图的设计方法,而采用单元化的状态流程图设计法来设计软件,如图4所示。其主要构想主要是把复杂的系统,划分为若干个简单系统,然后逐个进行逻辑设计,接着对简单系统进行一个系统性的综合[3]。
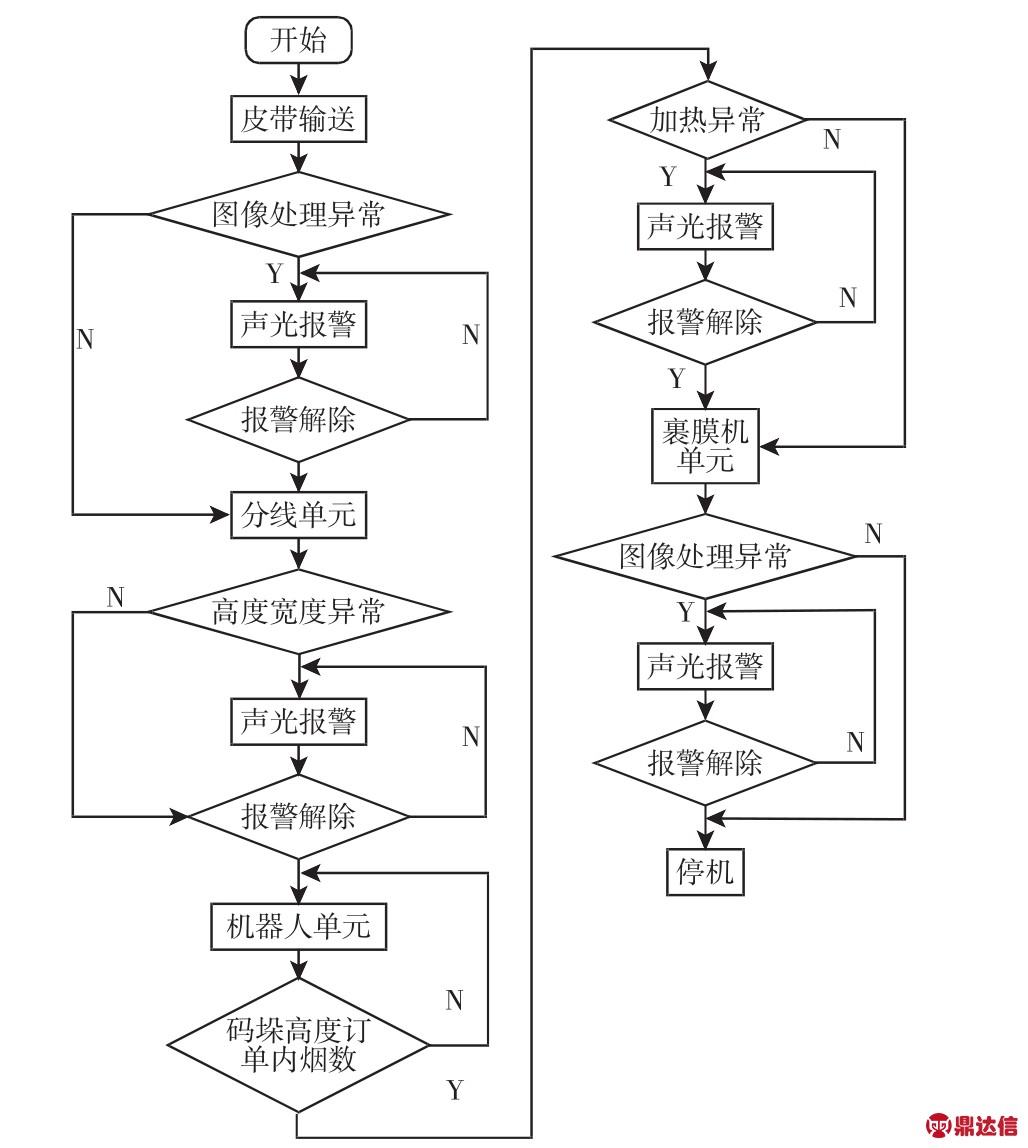
图4 单元化状态流程图
Fig.4 Unit Status Flow Chart
3.3 关键技术
在这个系统中主要环节主要包括分层环节、码垛算法、自适应模糊调整环节,保护环节,人机交互环节。(1)分层环节:在下落机下面是有一条主传送带,要在分层机构进行分流。主传送带往摇臂皮带方向运动,当主传送带异步电动机处的检测开关检测到信号时,就表明主传送带上的异型烟要进入分离区,此时异步电动机带动摇臂皮带进行上下层分离[2,4]。分层基本原则:在传送带存储区内的异型烟数量没有超过设定的最大值的情况下,优先给下层皮带,然后再传输到上层皮带,直到所有的订单处理完毕。(2)码垛核心算法:与标准烟相比,异形烟的长宽、高度尺寸大小不一,而且还要适合机器人把异型烟摆放最佳额的码垛形状,故要先把客户提交的订单重新组合,采用排序算法先按照高度进行升序排列,然后根据异型烟的宽度进行分类,宽度按照降序排列,目的是为了让同种品牌的条烟排在一起。
为了使码垛机器人码垛位置有一定的先后性,故把异型烟摆放平台进行分层,如图5所示。假设平台总宽度为W,然后将平台从正中间平分成两份,左边为码垛位置1和2,右边为码垛位置3和4。码垛方式是从中间往两边进行堆码,位置控制顺序如下:
放一条的情况:2--->1--->3--->4
放两条的情况:12--->23--->34
放三条的情况:123
放四条的情况:1234
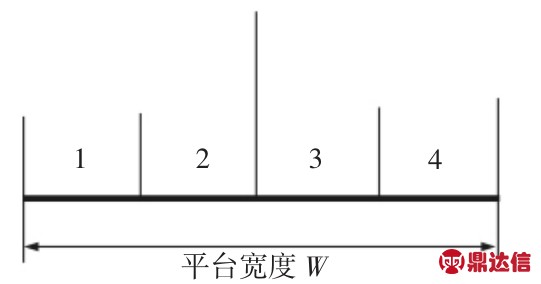
图5 码垛平台宽度
Fig.5 Palletizing Platform Width
工业机器人在进行堆码工作时建立如下数学模型:
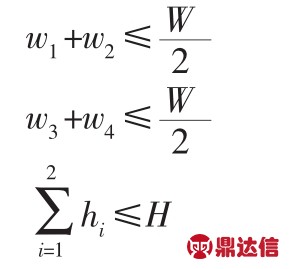
式中:w1、w2、w3、w4—传送带上异型烟的单条宽度;hi—传送带上的单条异型烟高度;H—同一垛位异型烟总高度。
为了提高码垛机器人的工作效率,采用码垛算法进行码[6-8]。码垛机器人进行异型烟抓取是优先考虑四条烟的情况,然后考虑三条烟的情况,再其次考虑两条烟的情况,最后考虑一条烟的情况。通过激光测距传感器获取高度数据,以防超过高度的设定极限值,皮带上的高度差不能超过设定极限值,皮带上的第一条和第二条宽度之和、第三条和第四条宽度之和不能超过平台宽度的一半,根据抓取异型烟数目条件建立的数学模型如下:
(1)当抓取四条烟的情况时:

(2)当抓取三条烟的情况时:

(3)当抓取两条烟的情况时:

测量装置测量靠近传送带端头四条烟相对于传送带表面的高度和四条烟的烟宽,数据如表1所示。单位mm:
表1 产品约束参数
Tab.1 Product Constraint Parameters

通过上表数据得出满足机器人抓取四条烟的情况。
例如:顾客提交了一个订单,有三种品牌的八条烟,五条A品牌的烟,两条B品牌的烟,一条C品牌的烟。进行订单重组后后订单为AAAAABBC,根据码垛条件,机械手第一次码垛的时候优先抓取四条A品牌的烟,分别放在码垛平台上第一层的1、2、3、4位置,第二次码垛的时候抓取一条A品牌的烟放在码垛平台上第二层的2位置,第三次码垛的时候抓取两条B品牌的烟放在码垛平台上第二层的3、4位置。第四次码垛的时候抓取1条C品牌的烟放在码垛平台上第二层的1位置。
(3)模糊控制算法:由于码垛机器人启动时会产生较大的初始偏差和位置变化率,此时控制器会产生一种较大的力矩输出,为了避免这样的情况,故可以通过调节误差及误差变化率来控制,此算法使机器人系统响应速度快。模糊算法主要有两个输入e和ec,三个输出△Kp、△Ki和△Kd。五个参数的论域,将他们模糊化为 7 个等级,如{NB,NM,NS,ZO,PS,PM,PB},分别表示负大,负中,负小,零,正小,正中,正大。模糊控制规则,如图6所示。
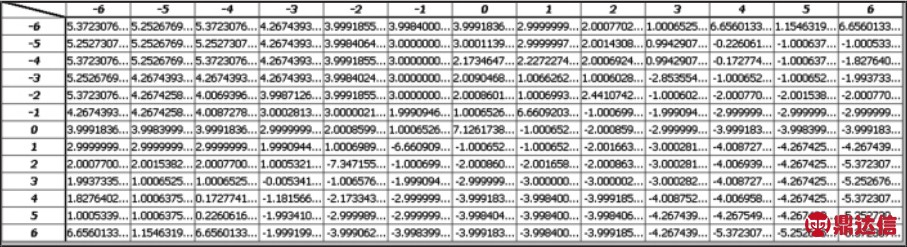
图6 模糊控制规则图
Fig6 Fuzzy Control Rule Diagrm
通过MATLAB进行仿真试验,使输入信号为正选信号,幅值是6,得到关节跟踪曲线,如图7所示。
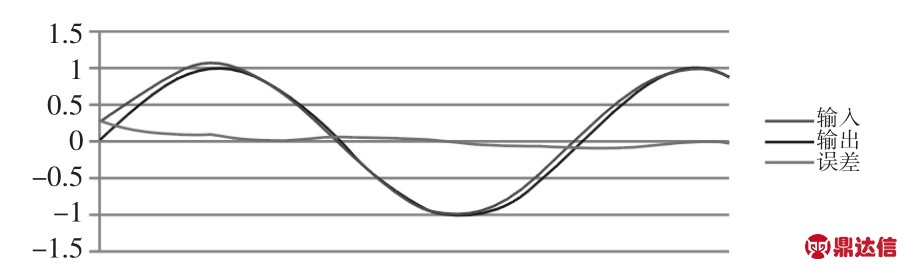
图7 关节跟踪曲线
Fig.7 Joint Tracking Curve
通过上图可以看出,误差逐渐减少并控制在一定的范围之内,证明此算法适合此系统。
(4)保护环节:为了保障整个码垛包装系统的运行的可靠性,除了选用一些优质的元件以外,还采取了需要有效的安全措施。例如,码垛机器人为了防止执行机构伤人,设置了光电开关和接近开关,其信号是输入PLC中,PLC根据数据来判断是否要紧急停车。
(5)人机交互环节:PLC在系统中主要是完成信号实时采集、脉冲量累计、预警报信号检测与报警输出等,并与现场中的传感器连接。由上位机进行复杂计算、保存历史数据,同时采用数据库作为系统的实时和历史数据库。下位机采用梯形图编制程序,主要是实现数据采集、脉冲计数转换、报警逻辑判断、通信格式的转换。数据通讯机制是采用计算机的串行通信来实现的,通过计算机与PLC网络之间的连接来实现对码垛包装系统的实时控制,采用RS-485通讯方式,好处可以减少数据在介质传输中受到外界环境的干扰。计算机可以随时在线接收现场的相关信息,计算机也可以实时的发送控制指令,使整个系统处于安全、高效的状态,已达到管理的目的。计算机控制系统的硬件系统组成包括完成数据检测和数据采集的装置,数据采集装置是用来接受温度和电流等信号的,然后把接收到的信号转变成计算机控制系统可以识别的信号;完成计算机输入信号和输出信号转换的PLC模板,PLC模板连接计算机和外部环境设备,可以与控制系统进行数据交流;完成数据加工处理的中央处理机,中央处理机可以对录入的数据信息进行计算,计算出系统工作的参数,之后把参数等数据输出给其他设备;显示器和键盘鼠标等专用的控制设备,它们是用户和计算机进行交流的工具,可以帮助系统在线检测,对参数实现在线修改。
4 应用效果
通过现场的试验,模拟不同类型的客户提交不同的产品订单,每个订单含有不同品牌的产品,得到的部分试验数据,如表2所示。
表2 试验数据
Tab.2 Test Data
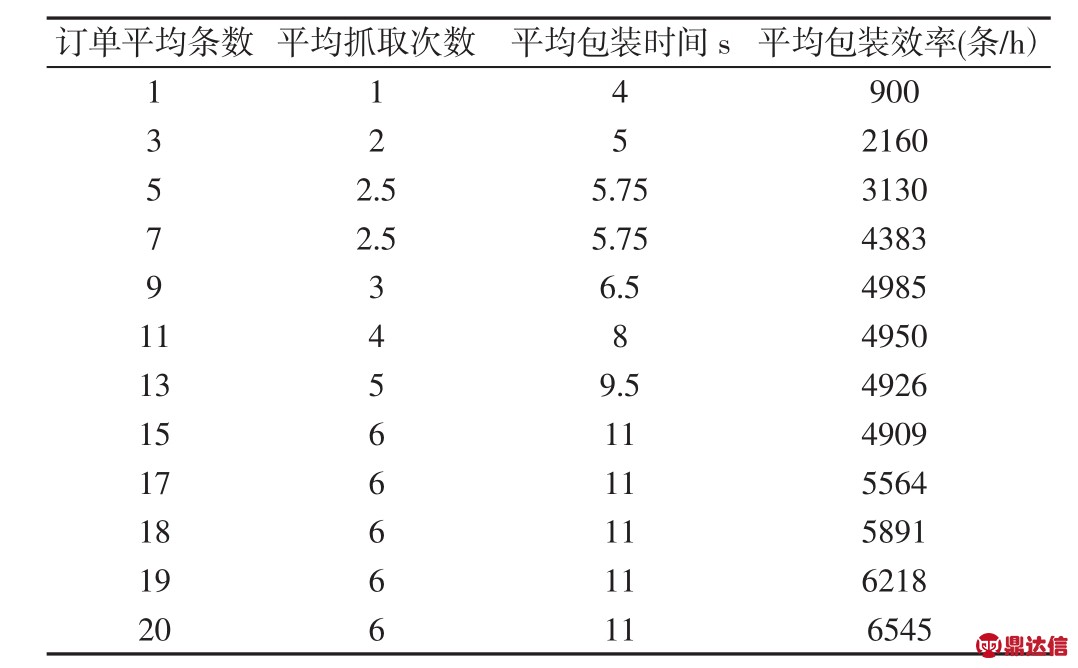
采用优化的码垛算法,可以实现按照指定的条件进行不同数量的抓取,并能够堆码出平稳的跺型。机械手码垛每次抓取1~4条,每次动作时间1.5s;移垛时间2s,包装效率高、垛形好,满足卷烟包装及配送要求。现场采集获取的数据,如图8所示。
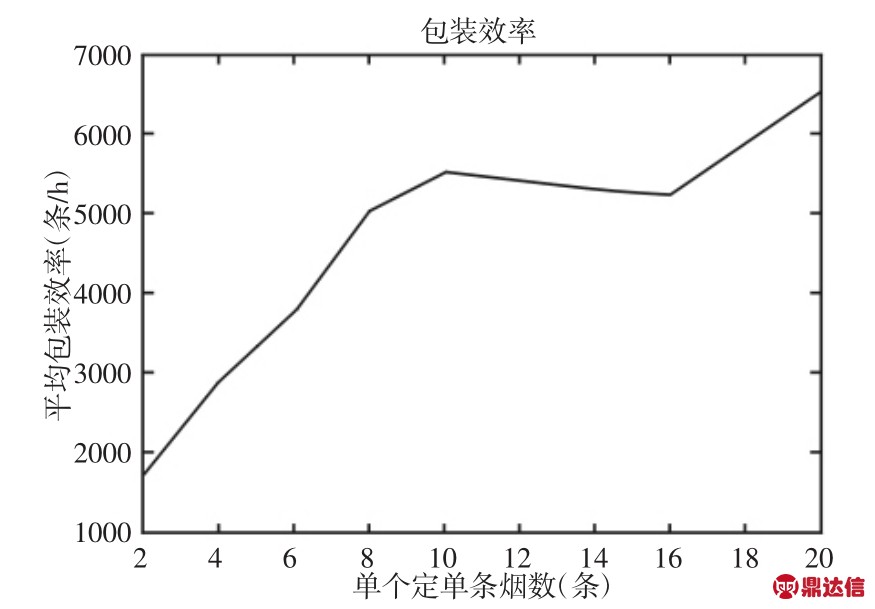
图8 打包效率
Fig.8 Package to Complete the Efficiency
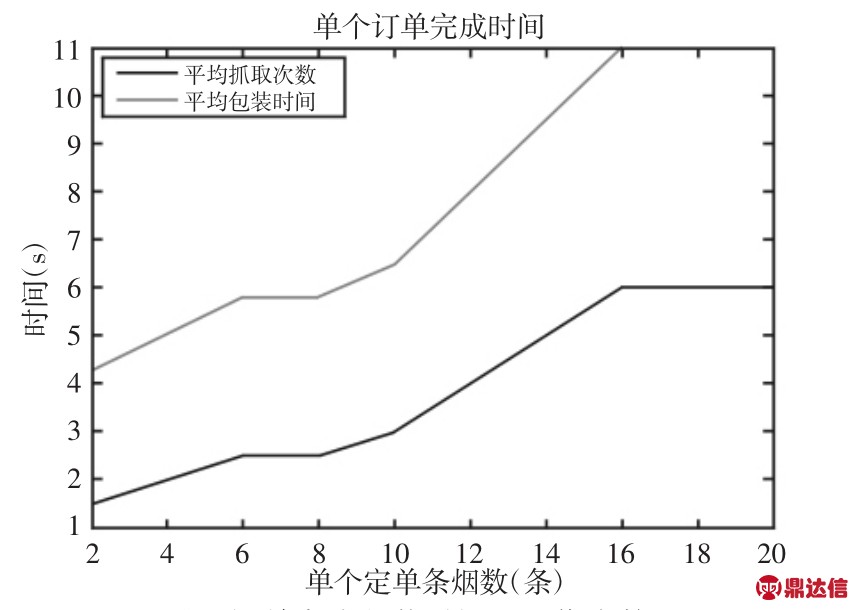
图9 订单完成包装时间及工作次数
Fig.9 Order to Complete the Packaging Time and the Number of Work
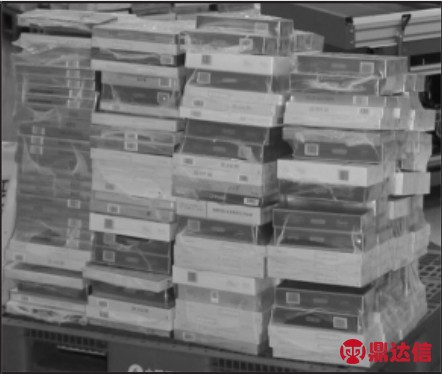
图10 码垛包装效果
Fig.10 Palletizing Packaging Effec
5 总结
全自动码垛及包装系统系统采用了机器人技术、图像识别技术、基于互联网的集散控制技术等多项先进的自动化技术,实现了异型烟的智能识别、码垛和包装,平均包装效率为6545条/h,居行业领先地位。项目成果已经在温州及德阳烟草物流中心成功应用,设备采用模块化设计,易于操作、维护,性能可靠,对提高卷烟配送物流的全局智能化具有重要意义。