摘 要:基于UG NX对拆码垛机进行联合仿真,首先在MCD模块进行模型的相关定义,然后将模型通过OPC协议与PLC和触摸屏相连接,通过PLC和触摸屏来控制模型的运动。通过该模型,研究各个运动机构在PLC的控制下运动速度的减速、加速、运动轨迹和运行时间否满足要求。通过模型的仿真运行,可以确定设备各个机构的最佳运行速度和行程开关布置位置,减少了现场调试的工作量。
关键词:拆码垛机;机电联合仿真;运动学;MCD;UG NX
0 引言
随着德国政府提出《德国2020高技术战略》,工业4.0的概念已经深入人心。我国政府也提出:到2025年迈入制造强国行列。我国的工业制造加工业将迎来发展的快车道[1]。
随着加工制造设备更新换代的加速,现代机械、电气设计的时间也在不断的缩短,新的设计方法层出不穷。现有的常用设计方法通常为:将机械设备建立模型后对该模型进行有限元仿真分析和运动学仿真分析,对电控程序在软件内运行调试,最终待机械设备和电气设备安装完成后进行联合调试,以确保该设备符合设计要求。这种设计方法虽然在设计阶段有部分机械和电气调试仿真,但机械仿真和电控程序仿真始终是互相独立、不相关的。
西门子公司的UG NX软件集成的机电概念设计(MCD)模块具有将机械运动仿真和PLC控制程序进行集成仿真的功能。该功能可以在虚拟环境中对所设计的产品进行快速评估,增强机械、电子和自动化设计师的协作,而且通过虚拟样机的调试减少了制造样机的时间和成本[2]。
本次研究的码垛机主要用于物流箱的拆垛和码垛功能,在设计过程中建立基于UG NX的虚拟样机,并运用MCD模块对其进行虚拟仿真分析,以得到相关运动数据。
1 码垛机简介
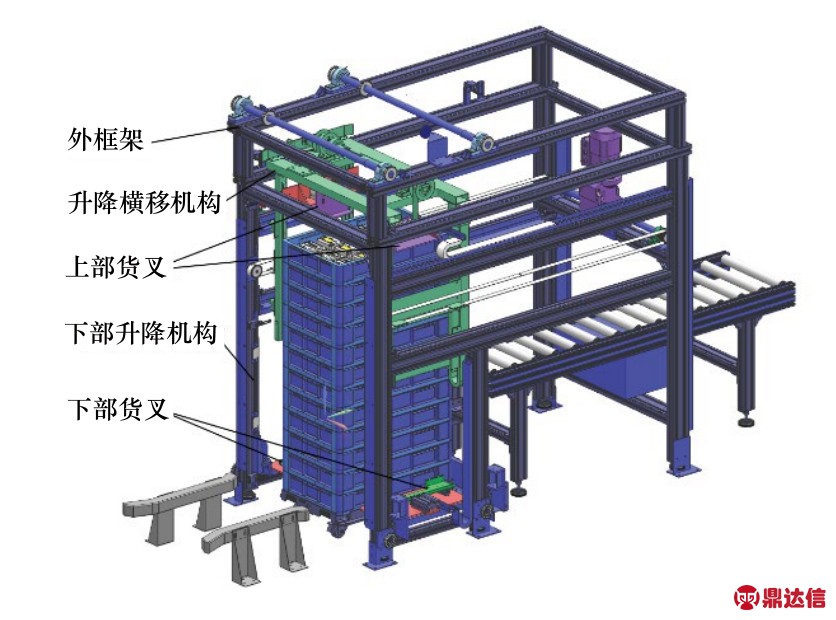
图1 码垛机示意图
本次所研究的拆码垛机是针对电表存储单元电表周转箱,主要功能:入库时进行拆垛功能,出库时进行码垛功能。
总体方案和工作原理。
拆垛:
1)首先人工推运由12个周转箱组成的箱垛到预定位置(图1中垛体所处位置);
2)箱垛到位后下部货叉在水平方向伸出,使货叉叉头伸入底部周转箱中部卡槽内;
3)货叉伸出到位后,下部货叉向上提升50mm;
4)与3)同时橫移货架后退到箱垛取放货位置;
5)与4)同时橫移货架货叉运行至顶部周转箱取货位置;
6)4)、5)到位后橫移货叉伸出使货叉叉头伸入顶部周转箱边部两卡槽内;
7)橫移货叉伸出到位后,该货叉提升并带动周转箱提升20mm,使该周转箱与其他周转箱分离;
8)然后橫移货架携带周转箱向前移动(向辊道方向);
9)橫移货架到达辊道取放货位置后,橫移货叉带动该周转箱下降,直至将周转箱放在辊道上,随后货架货叉分开;
10)之后橫移货架后退移动到箱垛取放货位置。辊道转动输送辊道上箱体离开。
程序重复5)~10)步骤直至12箱体运送完毕完成拆垛过程。
2 MCD模块简介
MCD可为产品设计的全新方法提供支持。功能分解作为机械、电气以及自动化学科之间的通用语言,通过这种设计手段,在产品设计的早期概念设计阶段,可以协调各个学科进行协同设计,并行运行。
1)机械工程师可以根据模型的外形尺寸和运动规律创建机械模型。
2)电气工程师可以根据仿真来确定光电传感器或驱动器的参数。
3)自动化编程人员可以设计机械的基本逻辑行为,首先设计基于时间的行为,然后定义基于事件的控制[3]。
MCD可对一系列行为进行仿真,包括验证机械概念所需的一切,涉及运动学、动力学、碰撞、驱动器弹簧、凸轮、物料流等方面。
3 虚拟样机的联合仿真
3.1 仿真设置
首先将模型导入至机电概念设计模块MCD的基本运行流程如图2所示。
1)对设备升降、抓取、气缸、箱子等需要运动的部件,定义其刚体的属性;定义完成后软件会自动赋予部件质量属性。同时对于箱子设置对象源和对象收集器,对象源表示箱子可源源不断的从这里生成;对象收集器则是收集这些箱子的。
2)定义碰撞体:对于有接触和力的传递部件,需要在其刚体属性的基础上对其进行碰撞体定义。抓取手一次要抓取一个箱子,从位置1移动到位置2;则需要对抓取手与箱子有力的传递位置定义碰撞体;或者对整个抓取手和整个箱子全部定义位碰撞体。
3)运动副的定义:对各种运动需要定义其运动副才能运转,UG NX提供了多种运动副可以使用,用法与运动学仿真一致,也可以通过运动学仿真定义后再导入到机电概念设计内使用。对堆垛机定义升降、横移、抓取等运动。如图3、图4所示。
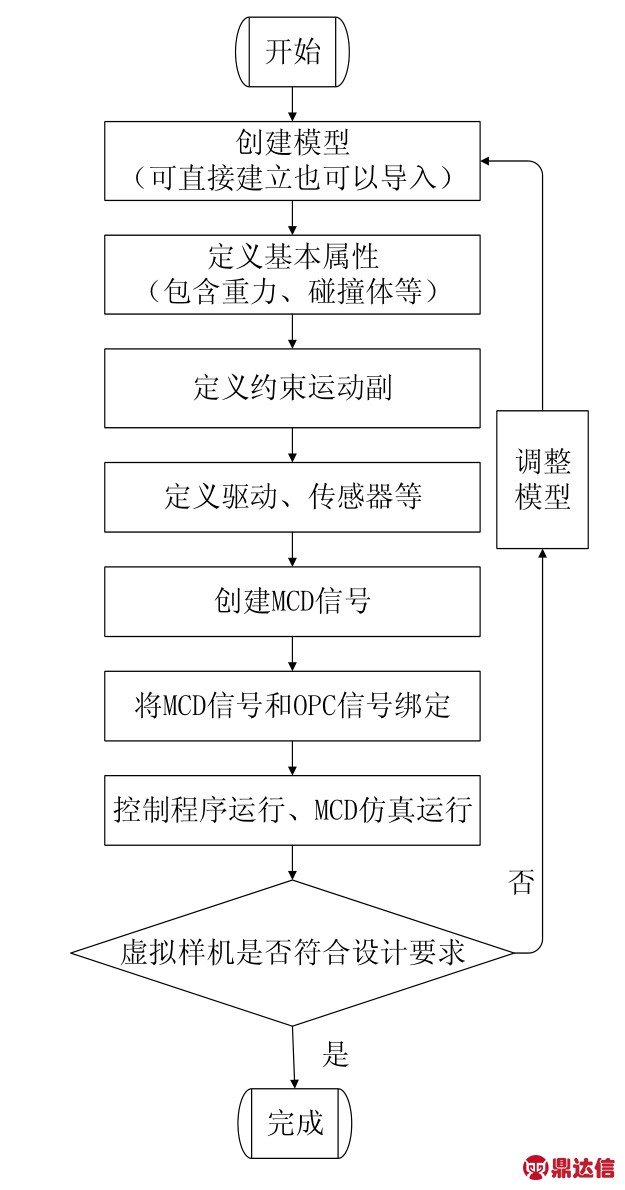
图2 MCD仿真流程图
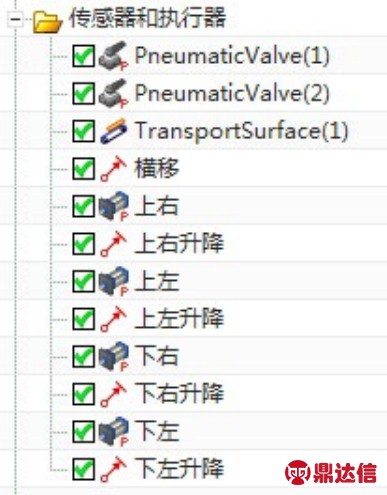
图3 定义运动副
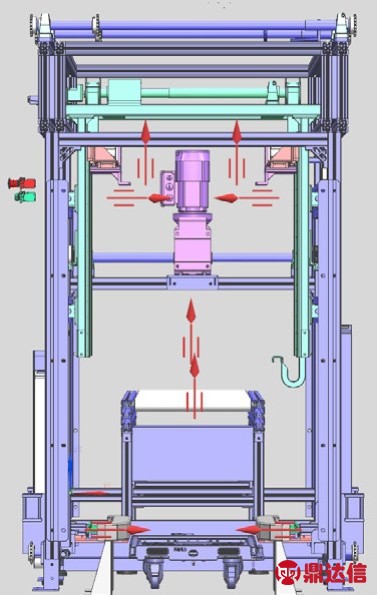
图4 运动方向示意图
4)添加传感器:UG提供多种传感器设置,有位置传感器、碰撞传感器等。当所定义的运动达到设计条件时,相关的传感器就会触发,得到信号。整个设备需要添加位置传感器、检测传感器、碰撞传感器等多种检测信号;这些信号可以通过OPC协议将信号反馈给PLC。

图5 定义的传感器和执行器
5)对升降和横移的运动副添加运动控制:相关运动副预先添加初始速度、位移量、力和扭矩的参数;对液压缸和气压缸也有相应的驱动方式可以添加,而液压缸和气压缸的运动要通过液压阀和气动阀来控制。
6)托辊的面定义位传输面:对这个面可以赋予一个运动速度,然后整个托辊的上表面即可按照这个速度稳定的运行。
7)信号:MCD可以创建多种信号,这种信号以不同的数据类型和符号名存储在符号表内。这些信号源于之前所创建的传感器、速度控制量、位置控制等。这些信号可以通过OPC与外部控制器进行的信号映射关联。
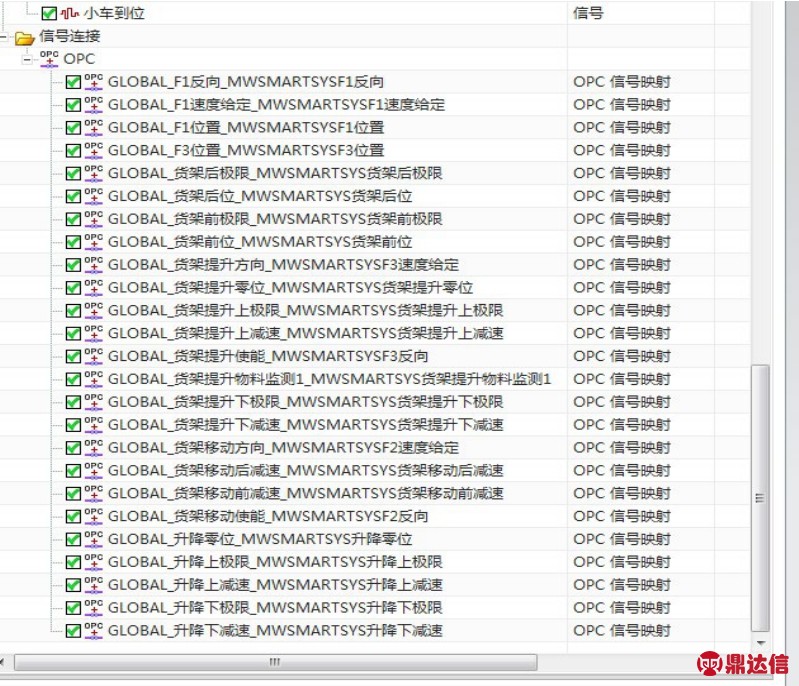
图6 OPC信号匹配图
8)当所有的信号都建立以后,与外部PLC程序进行连接,同时运行PLC程序和MCD程序进行仿真[2]。这时候操作外部触摸屏对设备进行运行控制,以查看设备在PLC控制程序下的运动是否符合设计要求。
3.2 MCD与运动学仿真结果对比
针对研究RigidBody(7)即上部货叉进行研究,主要研究货叉在横移过程中速度与位置的关系,从而得出整体升降横移机构的横向、纵向运动规律[4]。
如图7所示:横向移动零位与目标位相距950mm,距离零位和目标位相差100mm时触碰减速开关,横移速度开始减速;超过零位和目标位100mm时极限开关触发,横移急停。
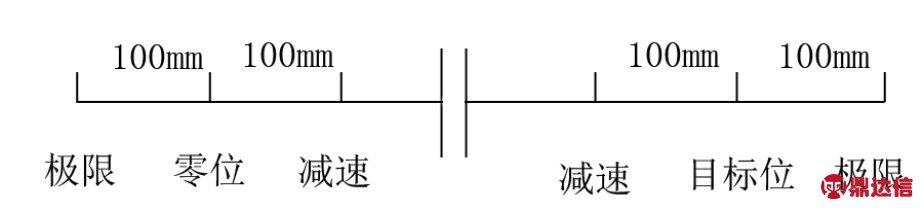
图7 横移位置示意图
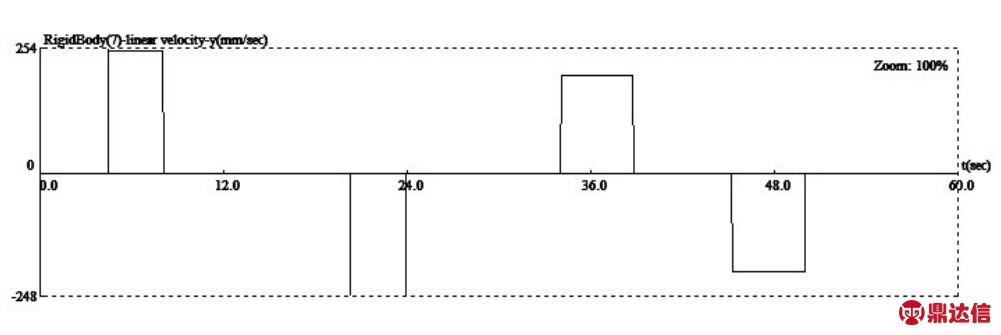
图8 运动学仿真横移速度图
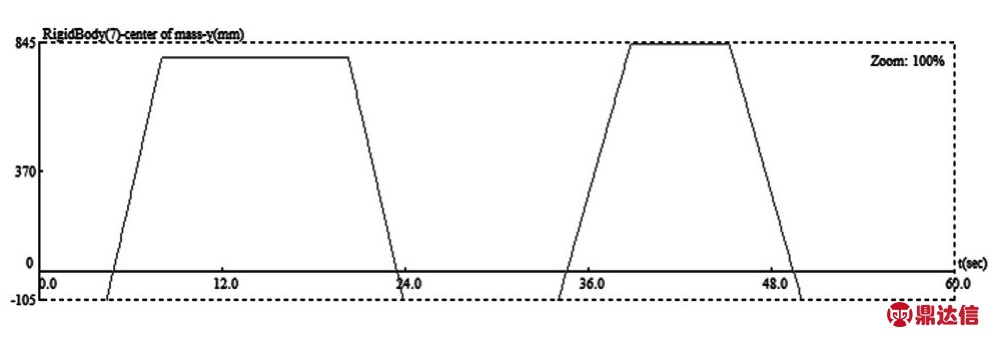
图9 运动学仿真横移位置图
图8所示为模型进行运动学仿真时所得到的结果,图9为运行学仿真时横移速度与时间的关系。根据图8可以看到,当横移开始运行时速度由0突然变位设定速度;当横移停止时速度也由运行时直接下降为0。从而导致图9的结果,也就是设备横移的位置与时间是线性相关的,是一个非常理想的运行状态[5]。
而根据实际经验,电机的转速不可能由0突然增加为额定转速,中间有一个缓慢加速的过程。而用运动学仿真分析很难分析到电机转速的加速和减速,也就很难分析到由于这个过程所导致的后果。致使仿真结果不能够准确反映现实情况。
图10和图11为利用MCD进行仿真后得到的结果。图10是仿真时速度与时间的关系,从图中可以明显的看到速度由0增加到设计速度的加速过程;在设备以设计速度横移一段时间后触碰减速开关后减速的过程;减速到寻位速度后开始缓慢横向移动,直至运行到目标位后停止。同样当反向运动开始后横移的速度也有加速、减速、寻位等过程。这就使得横移位置与时间的关系如图11所示较为真实可靠,而不是一个线性的关系。
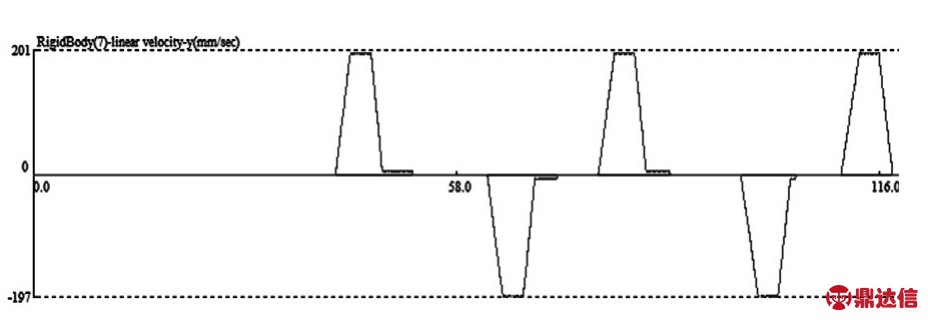
图10 MCD仿真横移速度图

图11 MCD仿真横移位置图
综上所述可以得到结论:MCD机电概念设计仿真研究速度、位置与时间的关系所得的结果较运动学仿真更为真实、可靠。
3.3 MCD研究堆垛机升降横移速度与位置关系
运用MCD进行仿真时得到的仿真结果不只可以输出图,也可以输出每次运行后得到的数据,数据可以导出到外部表格文件内。所以在实际仿真运行时需要调用数据,以确定确切的数据。
图12和图13为升降横移机构的升降速度和升降位置与时间的关系。由图可以看到对于不同高度的箱子升降机构的运行速度是不同的,以适应不同的高度。根据升降机构位置高度数据与实际箱子的高度数据相对比,可以得到设计数据与实际运行数据略有偏差,但是偏差范围在容错范围内,所以升降运动满足设计需要。
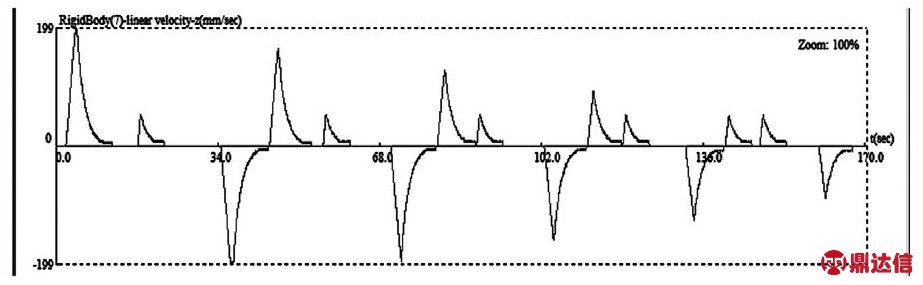
图12 升降横移机构升降速度
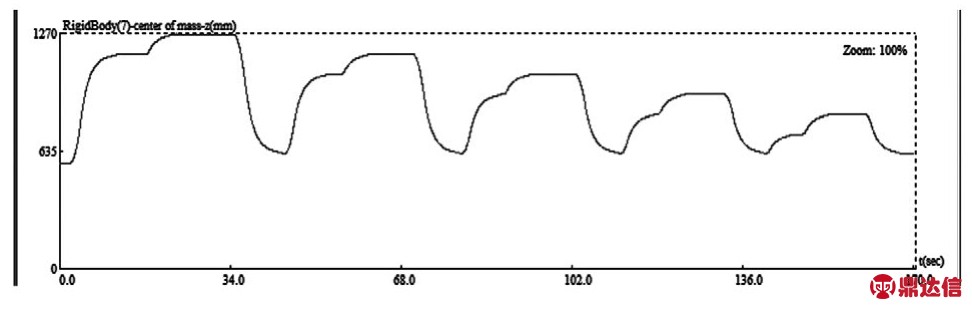
图13 升降横移机构升降位置
升降横移机构横向移动时其位置也有一定偏差,这个偏差与横移的质量、质心、速度、减速开关位置等有关。设定预定正向位置为845,负向预定位置为105。
横移速度初始设置为260mm/s,运行后数据如下图所示正向偏差达到34mm,负向偏差达到15mm。偏差略有些大,为了减小偏差,降低横向移动的运行速度;由260mm/s降低为200mm/s。
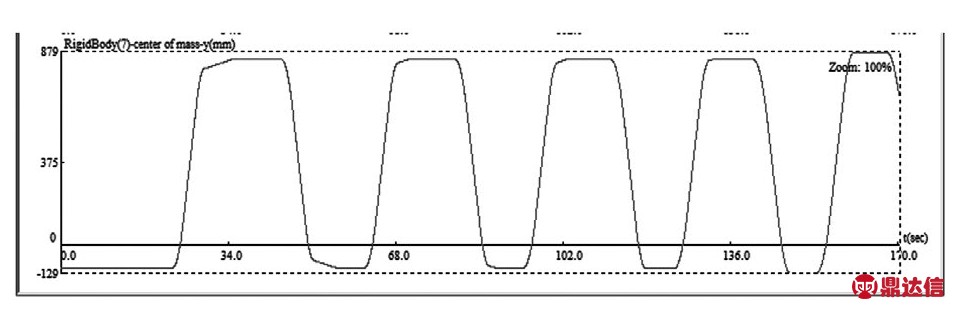
图14 升降横移机构横向移动位置图
当速度为200mm/s时,运行后数据如图11所示正向偏差达到4mm,负向偏差达到7mm,满足容错空间。
4 结论
1)通过本文研究可得:MCD机电概念设计仿真在研究速度、位置与时间的关系时的结果较纯运动学仿真更为真实、可靠。
2)拆码垛机横向移动的速度应该设定为200mm/s较为合适。