摘要:普通的污水沉降罐收油工艺易导致罐上部浮油表面出现严重老化和结蜡,影响后续工艺设备的正常运行,无法实现有效收油。而且冬季温度低的时候容易形成硬油盖,无法收油。试验一种新型的利用沉降罐出口电动阀与液位计联锁控制,使沉降罐液位保持在收油与溢流之间的高度范围内的沉降罐自动收油工艺,实现连续自动收油并降低了传统收油工艺改造费用。并根据其试验情况进行跟踪分析,确定其实用性,并提出改进的建议。
关键词:沉降罐;自动收油;油盖;连锁控制;跨电场
1 现状
污水站沉降罐的收油情况是减轻过滤段处理负荷的关键,同时也是制约着油田采出水处理效果的一个重要因素,它的处理效果主要是受沉降罐的收油、排泥、加药等情况影响。第七采油厂目前虽然各站实施了连续收油工艺改造,但是由于沉降罐所采用的收油结构为固定式,需要在罐顶用调节堰控制液位达到收油槽高度时,才能收到污油,实际生产中无法实现有效收油,易导致罐上部浮油表面出现严重老化和结蜡,影响后端电脱水器正常运行。而且沉降罐内表层的污油会在冬季气温低的情况下形成油盖,使罐内污油老化进而形成硬油盖,使罐内的污油无法回收,油层厚度的不断增加,罐内污水的有效沉降空间不断减少,从而使污水的有效沉降时间缩短,对污水处理效果产生较大影响。
目前,油田沉降罐顶部污油的回收方法有沉降罐收油槽收油工艺、浮油收集器收油工艺和浮动连续收油工艺等(表1),传统的收油工艺均为间歇式运行,冬季罐内污油易老化进而形成硬油盖,影响处理水质。第七采油厂主要采用的是收油槽收油工艺。为了更好地解决收油槽收油工艺调节堰生锈,使用年限短,沉降罐浮油回收问题,开展自动收油工艺试验。
2 沉降罐自动收油工艺
2.1 试验区概况
葡二联1#污水处理站目前有500 m3污水沉降罐4座,包括:2座一次沉降罐φ7.6 m×13.4 m;2座二次沉降罐φ8 m×11.4 m,均采用调节堰控制液位(常规固定收油工艺)收油工艺,调节堰平均7—8年需维修更换,而且由于容器上部收油进入油系统后,受硫化物影响电脱水器频繁垮电场,影响油系统平稳运行,所以试验前没有实现有效收油。罐内污油高度超过0.7 m,导致出水含油量较高,站内出水平稳达标难度较大,试验前的收油工艺采用沉降罐收油槽收油工艺,流程见图1。有收油泵2台,型号为DY6-25×3、流量为6m3/h、扬程为75m,运一备一。
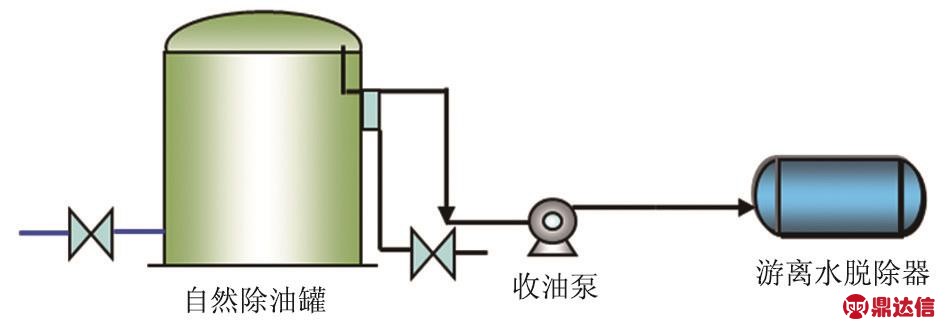
图1 试验前沉降罐收油槽收油工艺
2.2 自动收油工艺原理
自动收油工艺主要是利用PLC系统或二次仪表,对沉降罐内液位和界面进行测定,并与设定的值进行比较,根据差值通过PLC系统程序调节或二次表的报警动作对电动阀或变频器发出相应的指令,使其动作,从而使液位和界面稳定在一定范围内,自控原理见图2。
表1 不同收油工艺介绍及优缺点对比
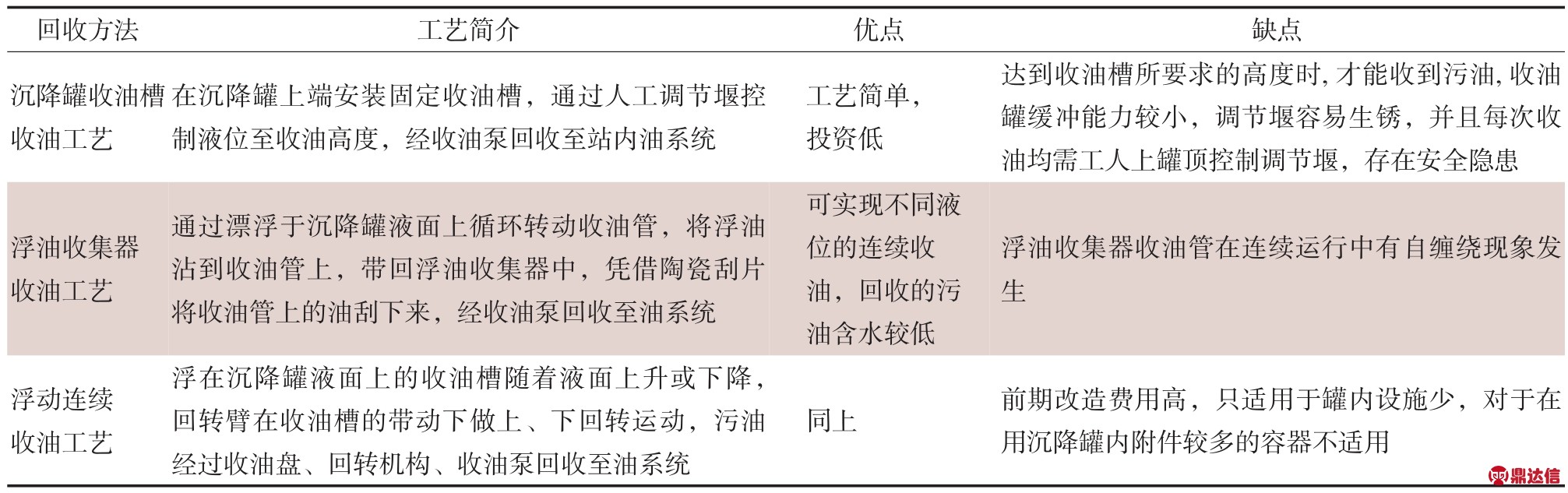
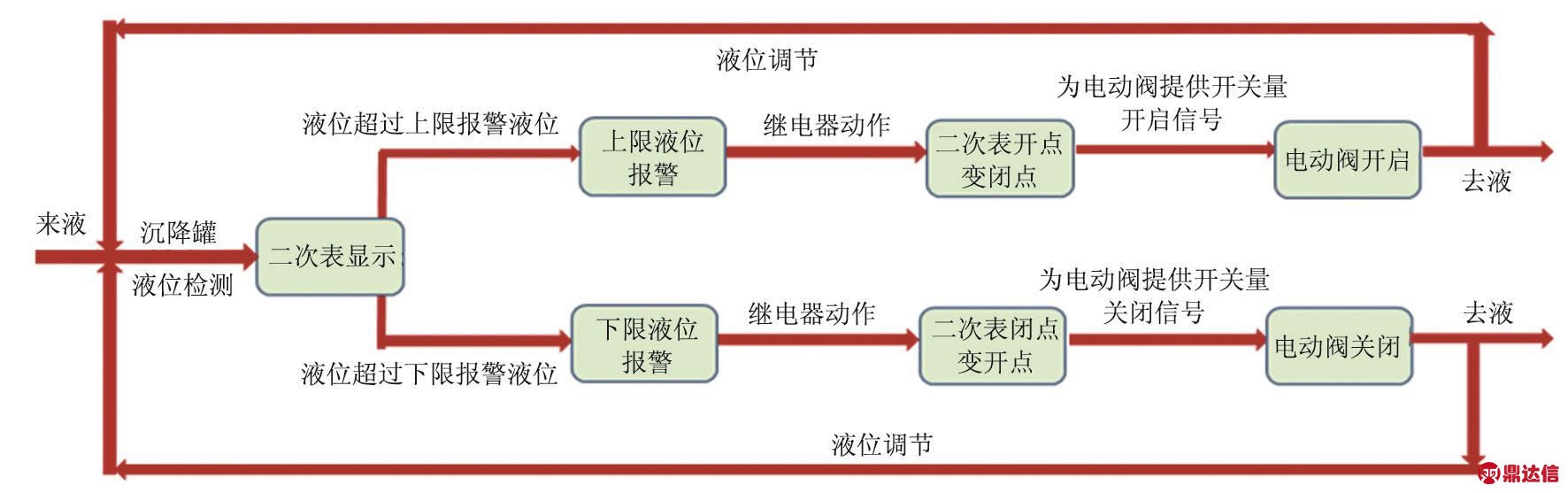
图2 液位自控原理
利用一次沉降罐已建的液位计,接入新建的仪表控制箱,用于罐内液位高度的测定,一次沉降罐的出水管安装电动阀1个,与罐液位高度进行联锁,根据设定液位值与罐内测定的液面高度进行对比,通过PID调节,控制沉降罐出口电动阀的动作,确保沉降罐内液位平稳控制在收油高度,保证收油时不至于收水过多[1-2]。
在一次沉降罐内加装液位界面传感器1套,用于罐内油水界面高度的测定,通过与一次沉降罐液位的对比,确定油层厚度,收油泵安装变频器1台,液位界面传感器二次显示后进入新建变频柜,与收油泵变频形成闭环控制。在PLC系统(或智能数字调节仪)设定油水界面的高度范围(界面传感器和液位计两者之间的差值就是油层厚度),并通过数字量输出点控制收油泵启、停,油水界面低于设定下限值时自动启动收油泵,油水界面高于设定上限值时关闭收油泵,这样油厚始终保持在PLC系统或二次调节仪表设定的较小的范围内[3-5],达到自动收油的目的,工艺流程见图3。
2.3 现场试验
现场工艺改造完成后,根据一次沉降罐的收油槽高度12.4 m,首次设定上、下限报警液位并试验运行(表2)。
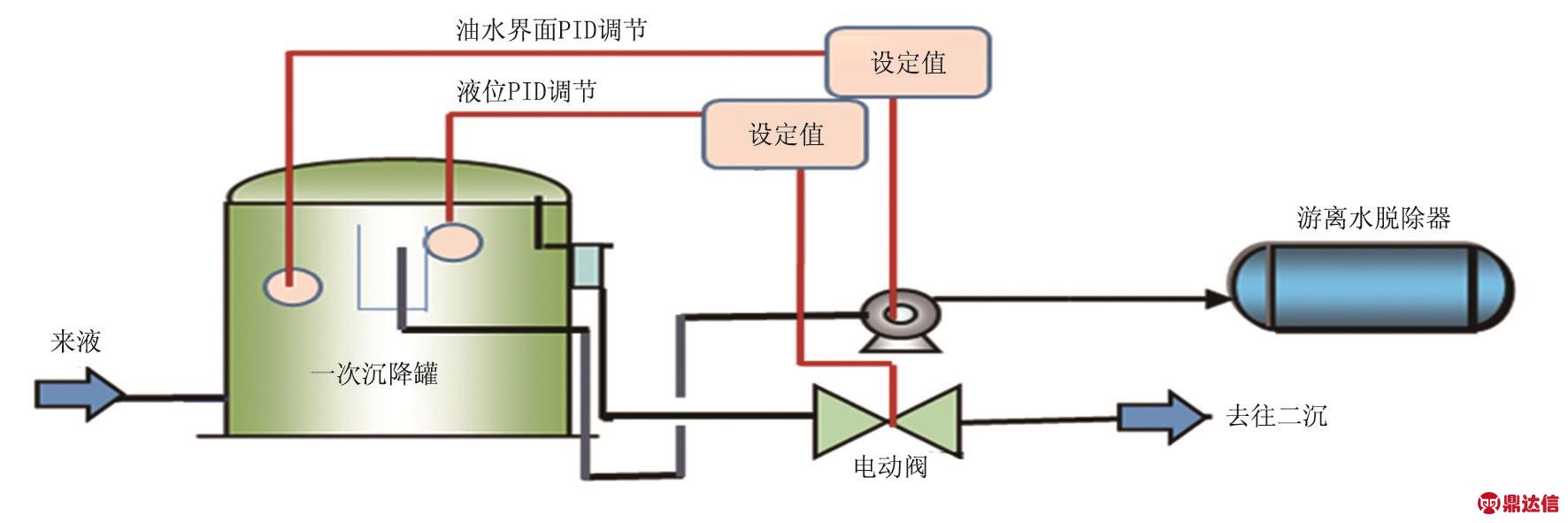
图3 自动收油试验工艺流程
首次运行时,沉降罐油厚数据经测为70.6 cm,收油泵工频运行,通过泵房看窗观察,发现收油泵看窗所收均为污油,收油泵运行8.25 h后,观察收油泵看窗所收污油颜色变淡,上罐顶检测罐顶油厚不到10 cm。通过持续观察、检测罐顶油厚,当液位显示为12.4 m时收油槽口未露出液面,经过多次调整、试验,最终确定二次仪表的高低液位报警值(表2)。
表2 二次仪表报警液位设定值 单位:m
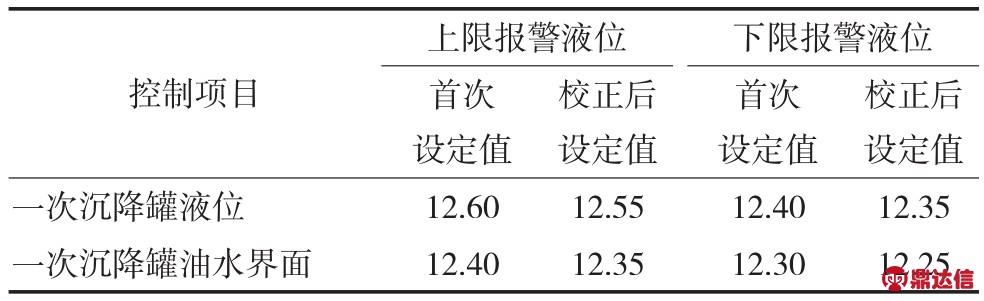
2.4 收油泵优化运行试验
为确保原油脱水系统平稳运行、水质有效提升,对收油泵运行周期及排量等参数进行了优化,摸索总结沉降罐自动收油工艺科学的运行管理方式。根据对沉降罐油层厚度的跟踪分析发现,沉降罐每天油厚增加5.42 cm(图4)。
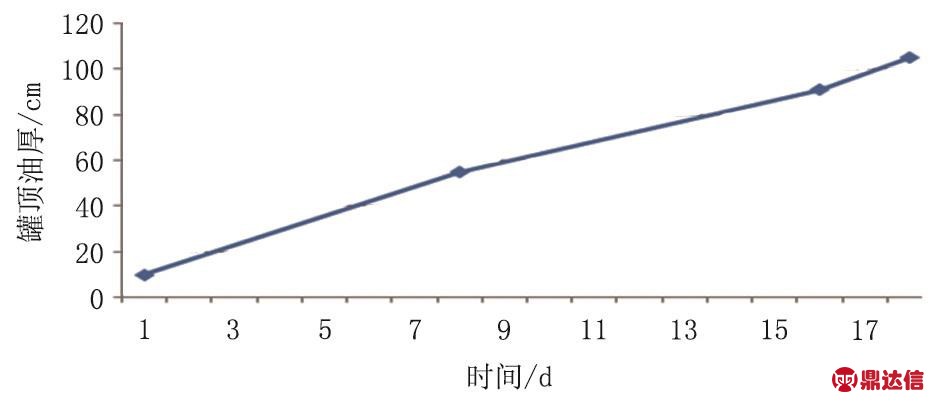
图4 沉降罐罐顶油厚随时间变化曲线
3 结论
1)常规收油槽收油工艺费用主要包括罐内清淤、调节堰成本及安装,费用为10.9万元,自动收油工艺主要包括变频器、一次表、二次仪表箱和电动阀等,费用为8.7万元,节省了2.2万元。
2)经过运行发现沉降罐自动收油工艺能实现罐顶污油的有效回收,有利于降低污水的含油量,同时自动收油工艺不需要工人上下罐人工操作,减少了工人的劳动强度,解决了调节堰容易生锈,使用年限短的问题。
3)采取沉降罐出口电动阀与液位计联锁控制,使沉降罐液位保持在收油与溢流之间的高度范围内的沉降罐自动收油工艺,可实现根据油层厚度自动启、停收油泵,达到自动收油的目的,改变了传统收油工艺依靠人工上罐顶操作调节堰、来液不稳定时液位和油水界面不易控制等问题,具有很好的推广前景。
4)沉降罐自动收油工艺依赖于一次仪表的测量准确度,静压式液位计较磁性浮子液位计测量稳定性更好,但是存在一定误差,为方便在沉降罐内安装油水界面仪,建议浮球式油水界面仪的高度宜在2.5 m以内。
5)建议结合沉降罐清淤、罐体维修改造,增设沉降罐出口电动调节阀及油水界面仪;结合节能改造,增设收油泵变频控制。
经过一年多的运行发现,根据来液含油量的不同,收油泵5天左右自动启泵一次,泵工频运行时间为2—3 h,污油厚度适中保持在0.3 m以下。取样检测对比收油前后污水水质,含油量由58 mg/L降低至44.6 mg/L;悬浮物由126 mg/L降低至42.7 mg/L。
为了进一步优化收油泵的运行,减少收油泵自动启动次数,开展按照沉降罐罐顶油层厚度不超过0.8 m运行试验,经过9—11月试验,收油泵15天左右自动启泵一次,泵工频运行时间为8 h,取样检测对比收油前后污水水质,含油量由92 mg/L降低至53.2 mg/L;悬浮物由54 mg/L降低至35.6 mg/L。