摘 要:为了研究离合器液压分离轴承缸体结构对密封圈压入力的影响,建立了液压分离轴承有限元模型,对液压分离轴承密封圈压入过程进行了分析,得到了密封圈压入力随位移变化的关系曲线,并与相关试验结果进行对比分析,验证了有限元模型的正确性。利用建立的模型,分析了轴承缸体结构参数以及与密封圈摩擦因数对压入力的影响。结果表明,在刚被压入时,密封圈受到的压入力波动较大,随后逐渐减小并趋于稳定。降低摩擦因数,增大缸体的内径和降低缸体外径可以有效地降低密封圈受到的压入力。该建模方法和结论对液压分离轴承的设计和结构优化具有一定的指导意义。
关键词:液压分离轴承;密封圈;压入力;有限元分析
离合器作为汽车传动系统的关键零部件,其操作系统的性能会直接影响驾驶人的主观感受。调查显示,在城市中,公交车驾驶人每天要踩800~1 000次离合器踏板;在相对拥堵的路段,小轿车每行驶100 km,离合器的分离次数就高达600次左右[1]。如果离合器操纵性能较差,在如此频繁操纵条件下,容易导致驾驶人疲劳驾驶,从而降低汽车的驾驶舒适性。此外,相关数据表明,在汽车维修公司中,离合器的维修率往往排在所有配件中的前三名,离合器分离不良、打滑和踏板沉重等故障,是造成离合器故障的主要原因[2-4]。除了离合器自身可靠性之外,离合器分离轴承性能也是影响离合器故障率的一个重要因素。分离轴承作为离合器操纵系统的重要零部件,其自身性能将直接影响到整个离合器踏板机构的操作舒适性,因此,对离合器分离轴承性能的进行深入研究是十分必要的。
目前,汽车离合器操纵机构所用的分离轴承主要分为机械式和液压式等2类[5-6]。其中,液压分离轴承具有摩擦阻力小、接合柔和和效率高等优点。近年来,由于材料性能的提高,制造工艺和设计方法的逐步完善,液压分离轴承的制造已日趋成熟;因此,液压分离轴承在各种类型的乘用车、商用车上被广泛采用[7]。从国内外研究现状来看,对于离合器分离轴承,大多数研究人员主要把它与离合器操纵系统整体配套进行相关研究[8-10],而单独对离合器分离轴承的相关研究文献较少,即使是研究离合器分离轴承,也只是研究拨叉式分离轴承[11],而单独对液压分离轴承的研究几乎没有。
为了研究离合器液压分离轴承缸体结构对密封圈压入力的影响,本文建立了液压分离轴承有限元模型,对液压分离轴承密封圈的压入过程进行了分析。计算得到了密封圈所受压入力随位移变化的关系曲线,并通过与相关试验结果进行对比分析,验证了有限元模型的正确性。利用建立的模型,分析了轴承缸体结构参数以及与密封圈摩擦因数对压入力的影响。本文的建模方法和结论对液压分离轴承的设计和结构优化具有一定的指导意义。
1 有限元建模与分析
1.1 有限元模型的建立
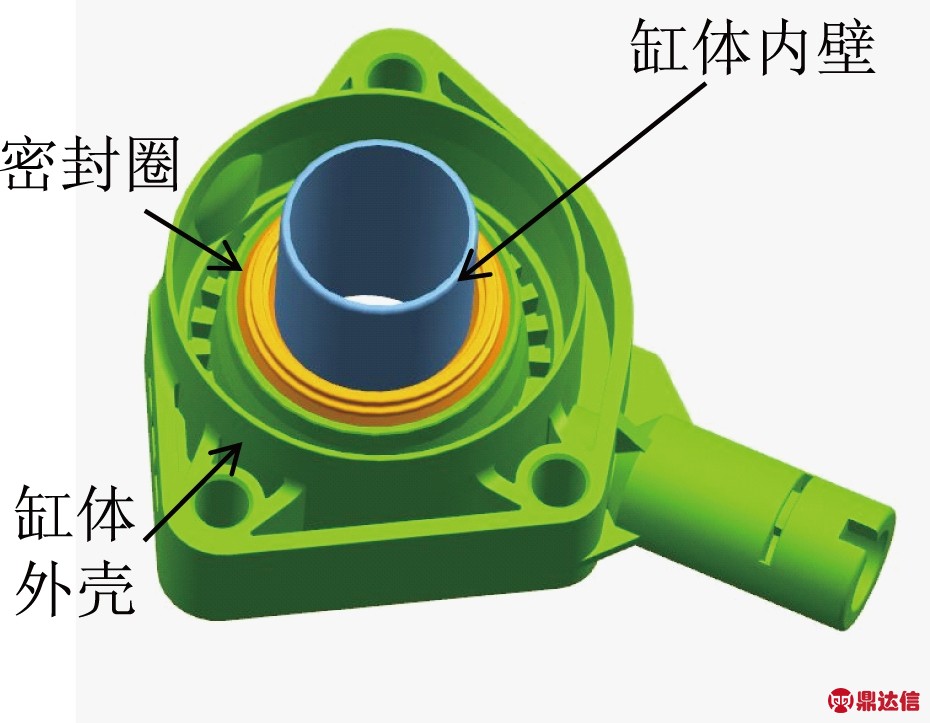
图1 液压分离轴承三维模型
由于本文主要研究分离轴承缸体结构对密封圈压入力的影响,在建模过程中,仅将液压分离轴承的缸体及密封圈部分做研究对象,其三维模型如图1所示。
提取缸体外壳和缸体内壁与密封圈接触的表面以及密封圈上表面,得到简化后的缸体模型,并保留完整的密封圈模型。为了给压盖一个位移载荷,将密封圈压入缸体中去,更好地模拟实际情况,在原始数模的基础上,增加了压盖部分,压盖的下表面外形与密封圈的上表面是吻合的,得到的有限元模型如图2所示。根据本文的研究内容,需要对密封圈压入过程进行动态模拟。将缸体固定,并在压盖轴向上施加一个25 mm的位移,压入密封圈。
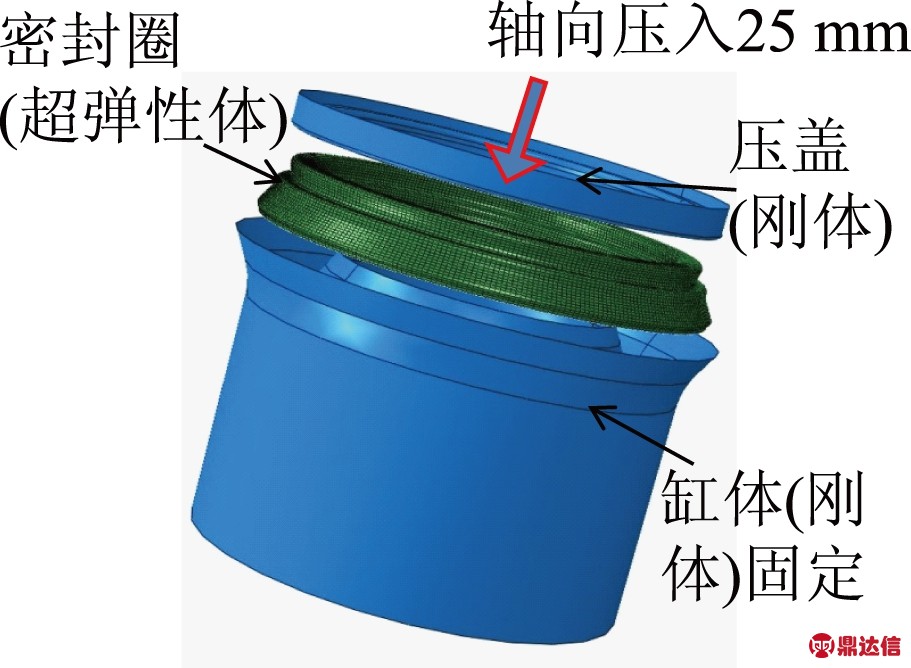
图2 液压分离轴承CAE模型
在CAE计算时,考虑到密封圈为橡胶材料,是整个模型中唯一的变形体,故将密封圈设置为超弹性体,压盖和缸体设置为离散刚体,不赋予材料属性。橡胶为非线性超弹性材料,可采用近似不可压缩弹性材料的Mooney-Rivlin模型作为橡胶的本构模型[12-13]。Mooney-Rivlin模型能够较好地模拟橡胶材料的力学行为,其应变能密度函数模型如下:
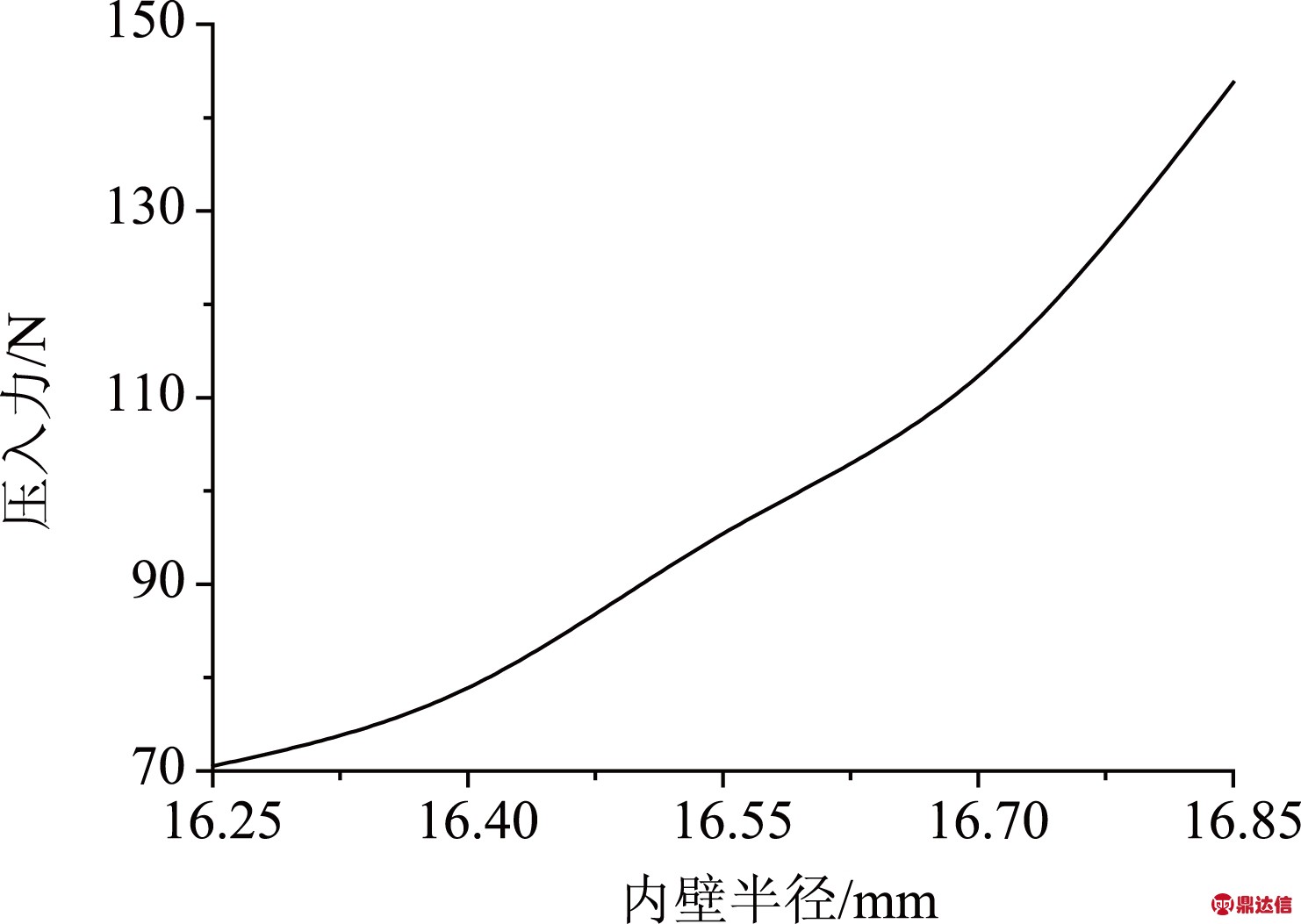
(1)
I1 = λ1 2 + λ2 2 + λ3 2
(2)
I2 = λ1 2λ2 2 + λ2 2λ3 2 + λ1 2λ3 2
(3)
式中,W为应变能密度;Cij为Rivlin系数;I1、I2分别为第1和第2 Green应变不变量;λ1、λ2和λ3为主伸长比。
本文采用典型的二项参数Mooney-Rivlin模型,则式1可变换为:

(4)
式中,C10和C01是材料的应变能偏量部分有关的2个材料常数,取C10=0.801 6,C01=0.126 9。
1.2 模型求解结果
利用上述建立的有限元模型对密封圈压入过程进行计算求解,结果如图3和图4所示。
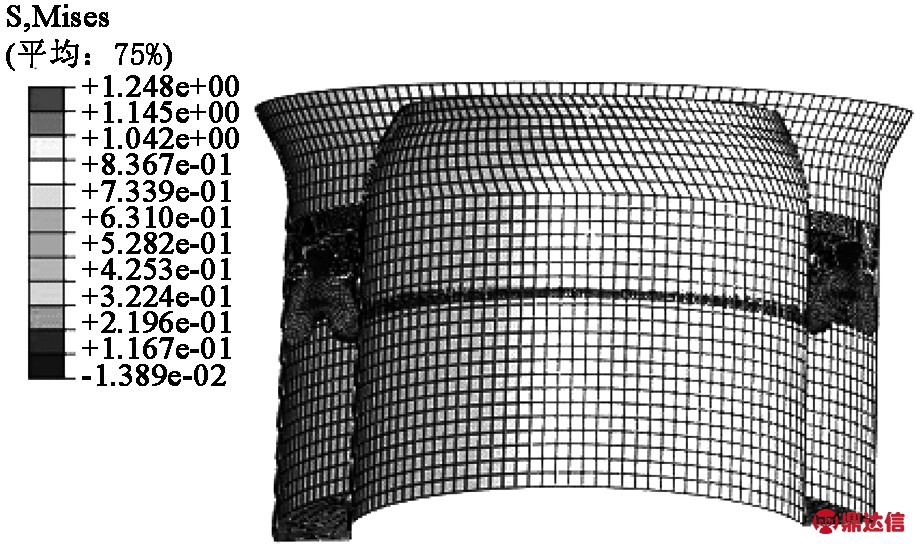
图3 密封圈压入中结果云图
图4 密封圈在摩擦因数为0.4时的压入力随位移变化曲线
从图4可以看出,在密封圈刚被压入的过程中,压入力波动非常大,随着位移的变化,在压入超过10 mm之后,压入力逐渐下降并趋于一个稳定值。这是因为在初始压入时,由于缸体存在倒角的缘故,此时压盖所受的支反力不仅是密封圈所受的摩擦力,还有缸体对密封圈轴向的压力。在完全压入缸体中后,压盖所受的支反力仅等于密封圈所受动摩擦力,理论上来说,此时密封圈所受摩擦力应为一个恒定的数值,但由于有限元软件计算本身的误差,计算结果会在一定数值左右波动。故取10 mm后的较平线段计算其平均值,作为密封圈受到的压入力。
2 试验验证
2.1 试验原理及过程
检测压入过程中密封圈所受的压入力,可以作为液压分离轴承开发阶段判断产品性能的重要依据。本试验采用液压分离轴承专用力值检测仪(见图5),配合特定的工装(见图6)进行测试。试验具体过程如下:1)将密封圈装入工装中的轴承凹槽,并把轴承组件压入工装中的缸体底部;2)将测试工装挂到测力仪挂钩上,摇动仪器手柄将工装放入底座夹具上,插入卡板使其固定;3)缓慢摇动手柄,使测力仪挂钩向上移动,直至拉动轴承组件与缸体分开。移动过程中测力仪会自动记录检测中的均值。为保证试验结果的准确性,重复上述步骤,进行3组试验,并记录试验结果。
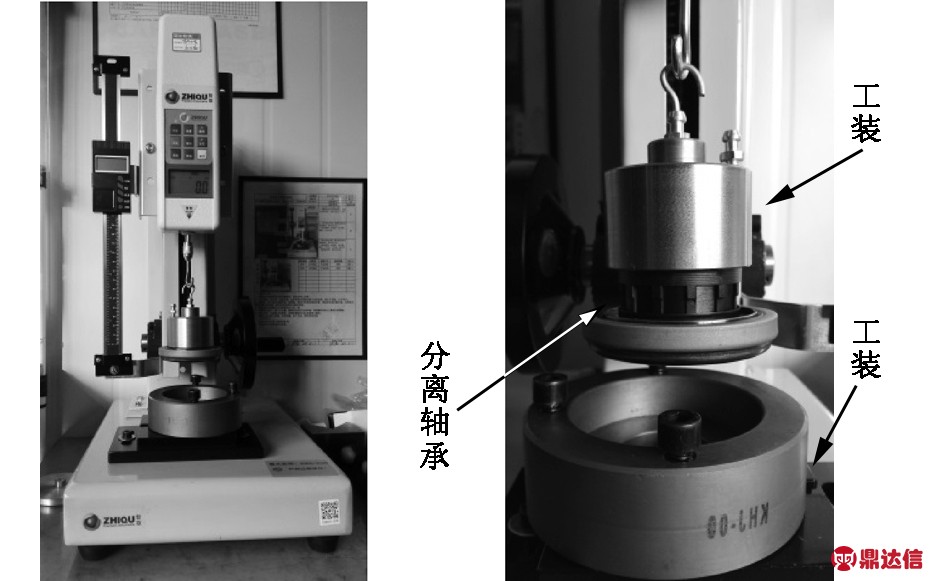
图5 力值检测仪图6 液压分离轴承专用工装
2.2 试验结果与仿真结果分析
将试验结果与CAE计算结果进行对比分析,结果见表1。从表1可以看出,3次测试结果差异较小,试验的一致性较好,橡胶密封圈在压入过程中受到的压入力约为75 N。而CAE计算出的结果为71.5 N,计算结果与试验结果误差约为5%,验证了所建模型的正确性。
表1 密封圈压入力试验结果与仿真结果对比
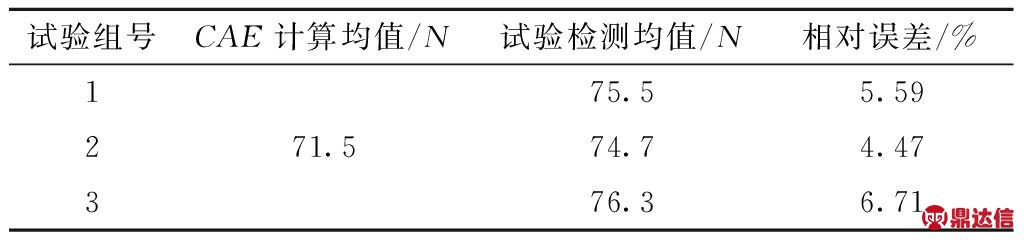
3 缸体结构对密封圈压入力影响研究
液压分离轴承是离合器操纵系统的重要组成部件,它将工作缸、拨叉及分离轴承合成一体,使得整体结构更加紧凑,离合器踏板力更加柔和。密封圈作为液压分离轴承的关键零部件,检测压入过程中其所受的压入力,可以作为液压分离轴承开发阶段判断产品性能的重要依据。而密封圈所受压入力与众多因素有关,如密封圈和缸体的材料、缸体内壁的表面粗糙度、缸体结构尺寸以及密封圈结构尺寸等。相对于其他因素的影响,缸体结构尺寸比较好调整;因此,本文将重点研究缸体结构对密封圈压入力的影响。
缸体与密封圈接触面之间的摩擦因数是液压分离轴承重要的性能参数,直接决定了密封圈压入过程中所受的压入力。摩擦因数主要与缸体和密封圈材料、缸体内壁表面粗糙度有关,实际中摩擦因数的获取由原材料供应商提供。利用建立的模型,计算不同摩擦因数对密封圈压入过程中压入力的影响情况,计算结果如图7所示。
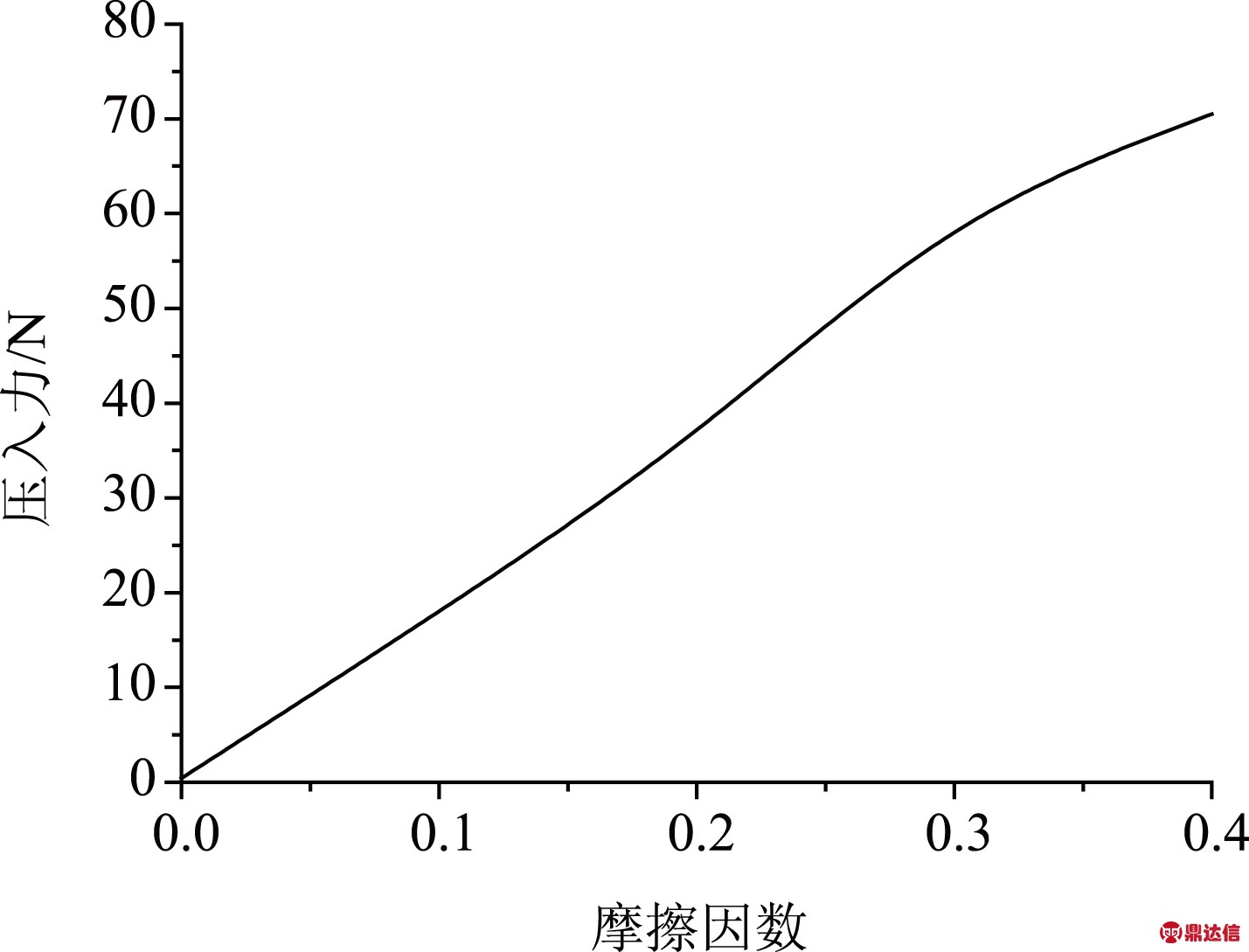
图7 摩擦因数对密封圈压入力的影响
从图7可以看出,随着摩擦因数的增大,密封圈所受压入力近似线性增大,表明在密封圈被压入之后,其受到的压入力主要是由于缸体与密封圈之间的摩擦力导致的。
缸体结构尺寸作为缸体结构的另一重要方面,是影响液压分离轴承性能的重要因素。设计合理的缸体结构尺寸,可以有效地改善液压分离轴承的整体特性。本文根据液压分离轴承缸体的结构特点,主要从缸体内壁和缸体外壁等两方面分别来研究对密封圈压入力的影响情况。利用建立的模型分别进行计算,得到的结果如图8和图9所示。
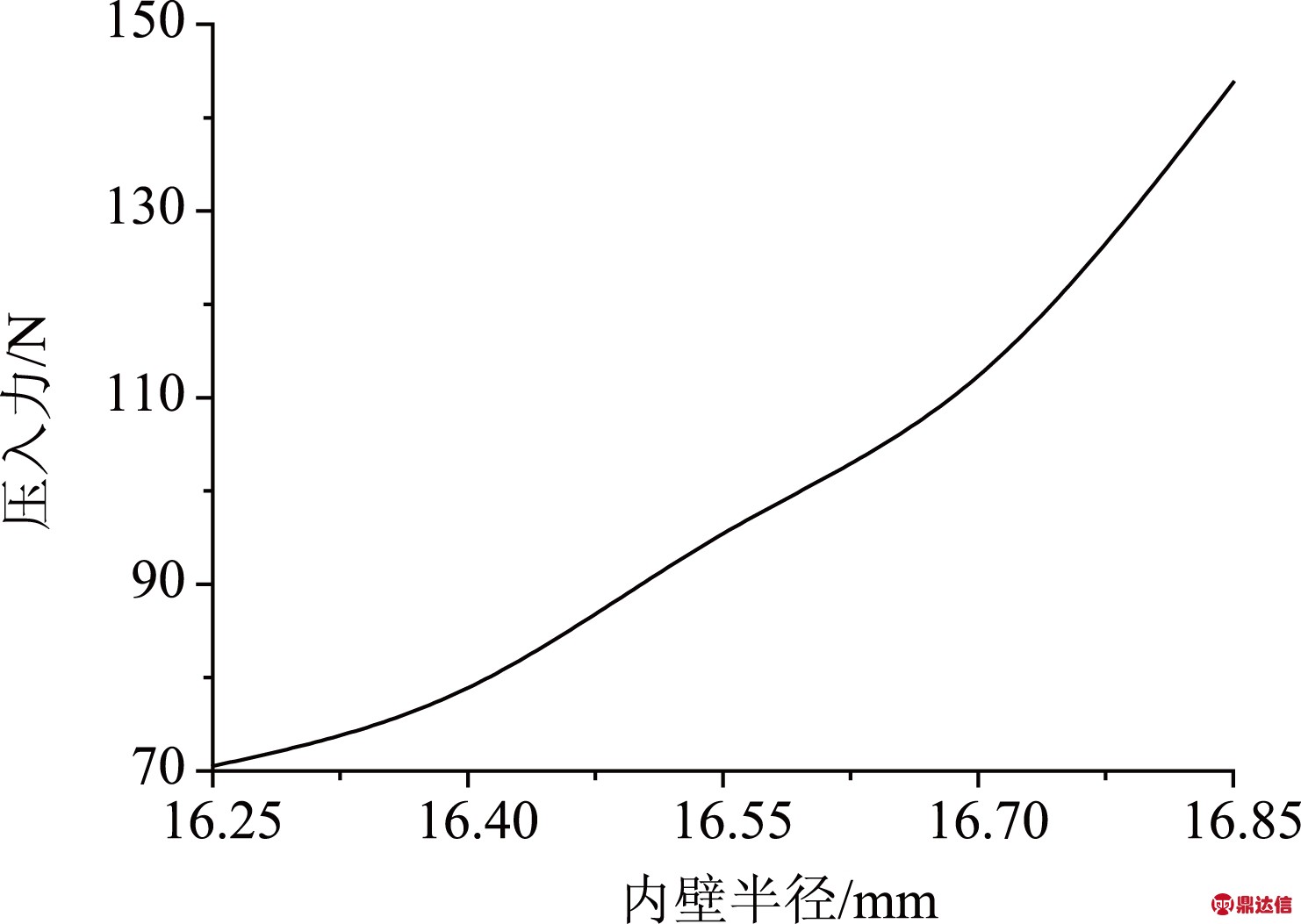
图8 缸体内壁半径对密封圈压入力的影响
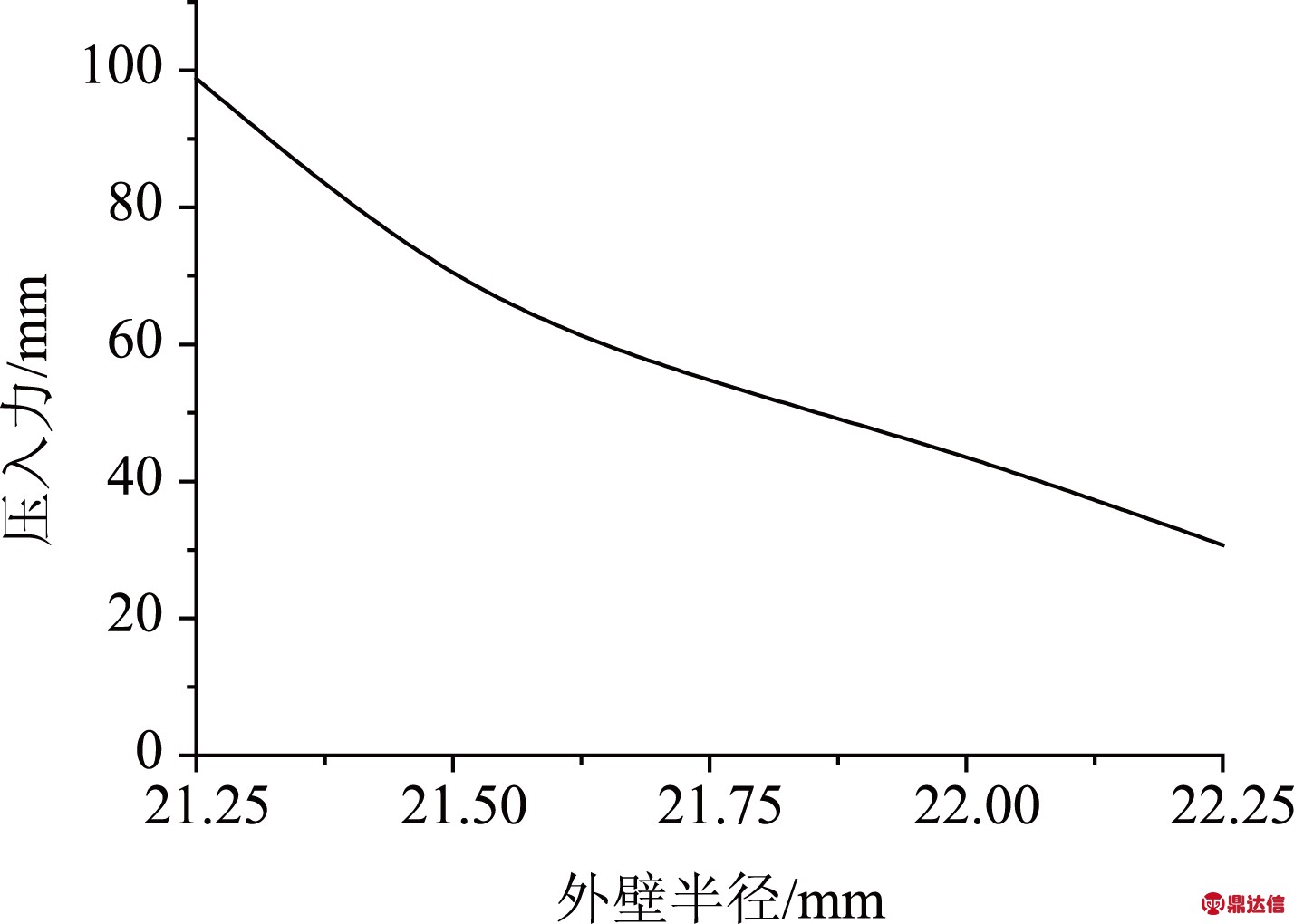
图9 缸体外壁半径对密封圈压入力的影响
从图8和图9可以看出,随着缸体内壁半径的逐渐增大,密封圈压入过程中所受压入力逐渐增大;同样随着缸体外壁半径的逐渐增大,密封圈压入过程中所受压入力逐渐减小。在分离轴承的设计过程中,可以通过调整缸体尺寸有效地改变密封圈所需的压入力。
4 结语
为了研究离合器液压分离轴承缸体结构对密封圈压入力的影响,建立了液压分离轴承有限元模型。对压入过程进行了分析,并进行了相关试验。利用建立的模型,分析了轴承缸体结构参数以及缸体与密封圈之间的摩擦因数对压入力的影响。由研究结果可以得出如下结论。
1)在密封圈刚被压入缸体时,由于其自身形变,产生的压入力波动较明显,随着压入位移的增大,形变区域稳定。当压入>10 mm之后,压入力逐渐下降,并趋于一个定值。
2)3次试验结果差异较小,试验一致性较好。利用有限元方法计算出来的结果与试验结果的误差仅约为5%,验证了所建模型的正确性。
3)随着摩擦因数的增大,密封圈所受压入力近似线性增大,表明在密封圈被压入之后,其受到的压入力主要由缸体与密封圈之间的摩擦力导致。增大缸体外径,减小缸体内径都可以有效地降低密封圈受到的压入力。