摘要:为解决某型航空发动机试车过程中W形金属密封环剥落失效问题,在完成断口分析的基础上,对W形金属密封环装配应力、工作应力进行分析。结果表明,初始装配时的压缩量偏大、工作环境压差较高是造成密封环剥落的主要原因。对W形密封环各参数的影响进行分析,提出合理控制初始装配压缩量范围、增加壁厚的改进措施。发动机长试验证了W形密封环改进措施的有效性。
关键词:航空发动机;W形金属密封环;失效分析;强度
W形金属密封环凭借其高压缩回弹率和自紧密封功能,在航空发动机、燃气轮机领域的应用越来越广泛,如CFM国际公司和GE公司最新打造的Leap发动机(配装国产C919飞机),在高、低压涡轮7个不同位置使用了不同形式的W形密封环结构。但由于制造工艺尚不完全成熟,国内W形金属密封环存在如整环平整度不好、焊接接头不可靠等问题,以往研制发动机用W形金属密封环多为进口件,国产化率低,国内相应的基础研究工作也开展较晚。目前国内对金属密封环的研究更多关注O形、C形和Ω形[1-4]等密封环,对W形密封环的研究相对较少,且主要集中在理论分析和试验器条件下的研究工作。刑敏杰[5]对W形金属密封环密封性能及泄漏进行了研究;龚雪婷等[6]对W形密封环的弹塑性接触进行了有限元分析;王晨希等[7]对W形密封环的压缩回弹性能和密封性能进行了分析;索双富等[8]对W形密封环轴向刚度影响因素进行了研究。上述研究都是基于理论分析,而对W形密封环在工程实际领域方面的应用研究及失效模式报道较少。本文作者通过对航空发动机实际试车过程中发生的一起W形密封环掉块故障的分析和改进设计,希望对W形密封环的工程应用起到一定的指导作用。
1 试验发动机密封环结构及材料
在航空发动机中应用的W形密封环实际上并不都是简单的“W”形,如文中试验的某型发动机W形密封环为非对称结构,装配于图1中A、B、C 3个零件间,被A、B 2个零件轴向压紧,与C零件在半径方向约有0.5 mm径向间隙,作用是将A零件前后腔隔开,维持前后腔压差,W形密封环的具体结构如图2所示,关键结构参数见表1。
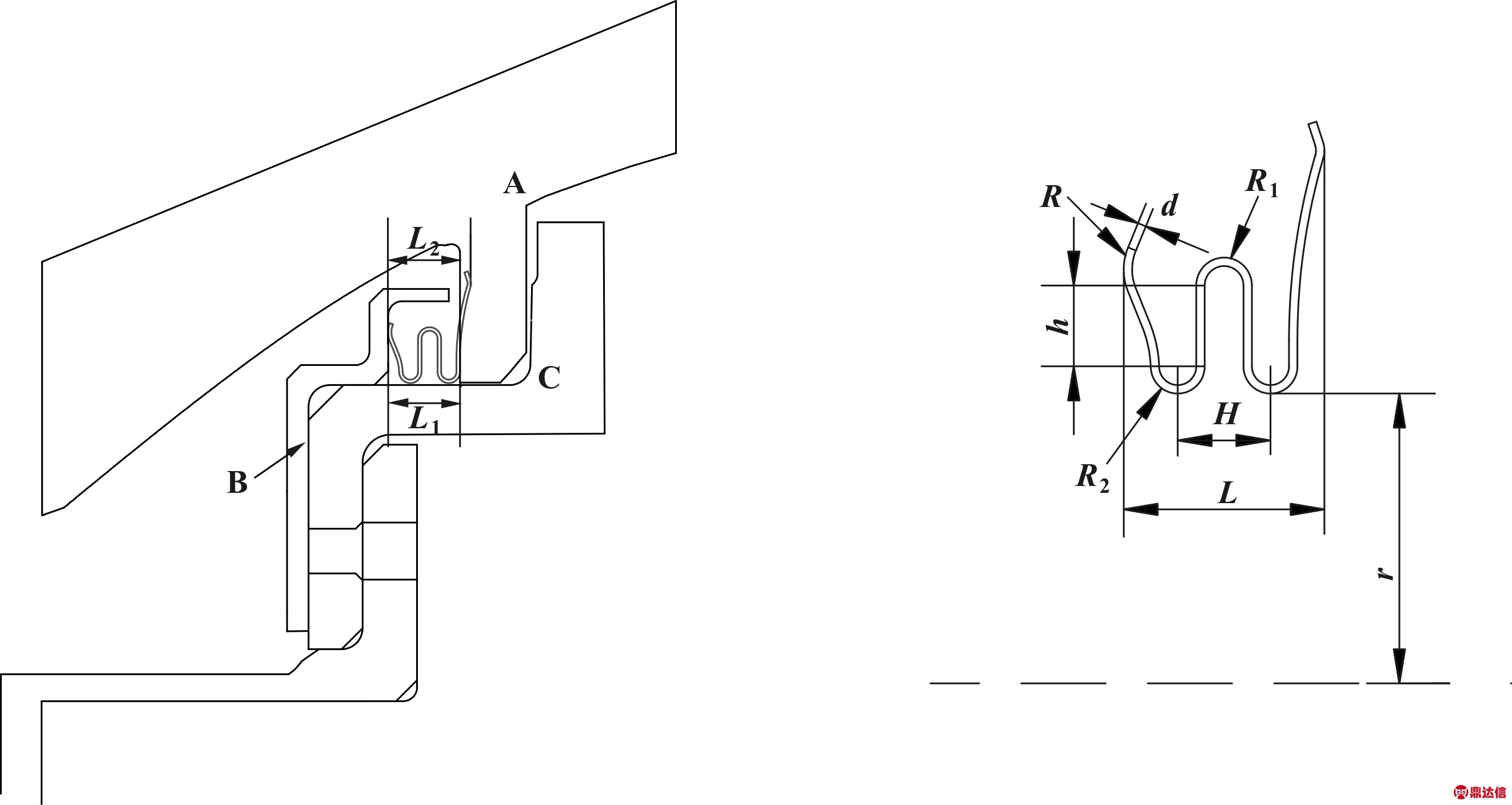
图1 W形密封环装配结构 图2 W形密封环结构形式
Fig 1 W-ring assemble structure Fig 2 Structure of W-ring
表1 W形密封环关键结构参数
Table 1 Key structure parameters of the W-ring mm

注:r为密封环内径;L为密封环宽度(自由状态);H为波谷宽度;h为波高;R为接触面曲率半径;R1为波峰半径;R2为波谷半径;d为壁厚。
试验的W形密封环采用镍基高温合金材料GH738,耐温能力可达815 ℃,在高温下强度仍然很高,抗腐蚀性能优良。其基本力学性能参数[9]见表2。
表2 GH738材料力学性能
Table 2 The mechanical property parameters of GH738
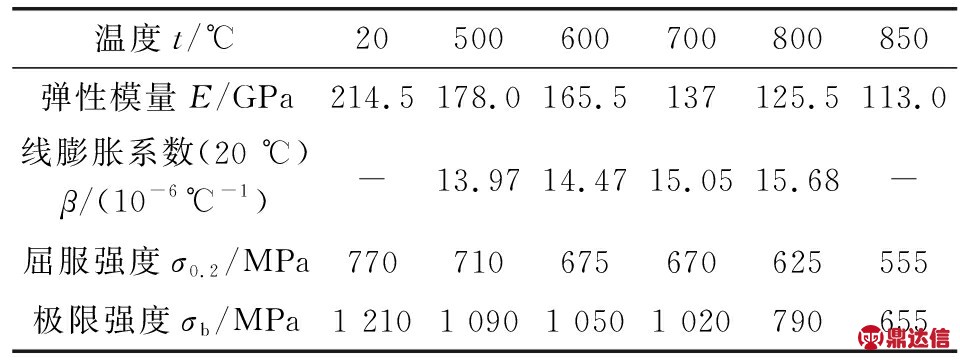
2 密封环故障现象及断口分析
该型发动机在经历短时试车后,频繁出现密封环局部掉块情况,带来发动机空气系统失衡问题,给发动机使用带来了安全隐患。失效的密封环典型形貌如图3所示。
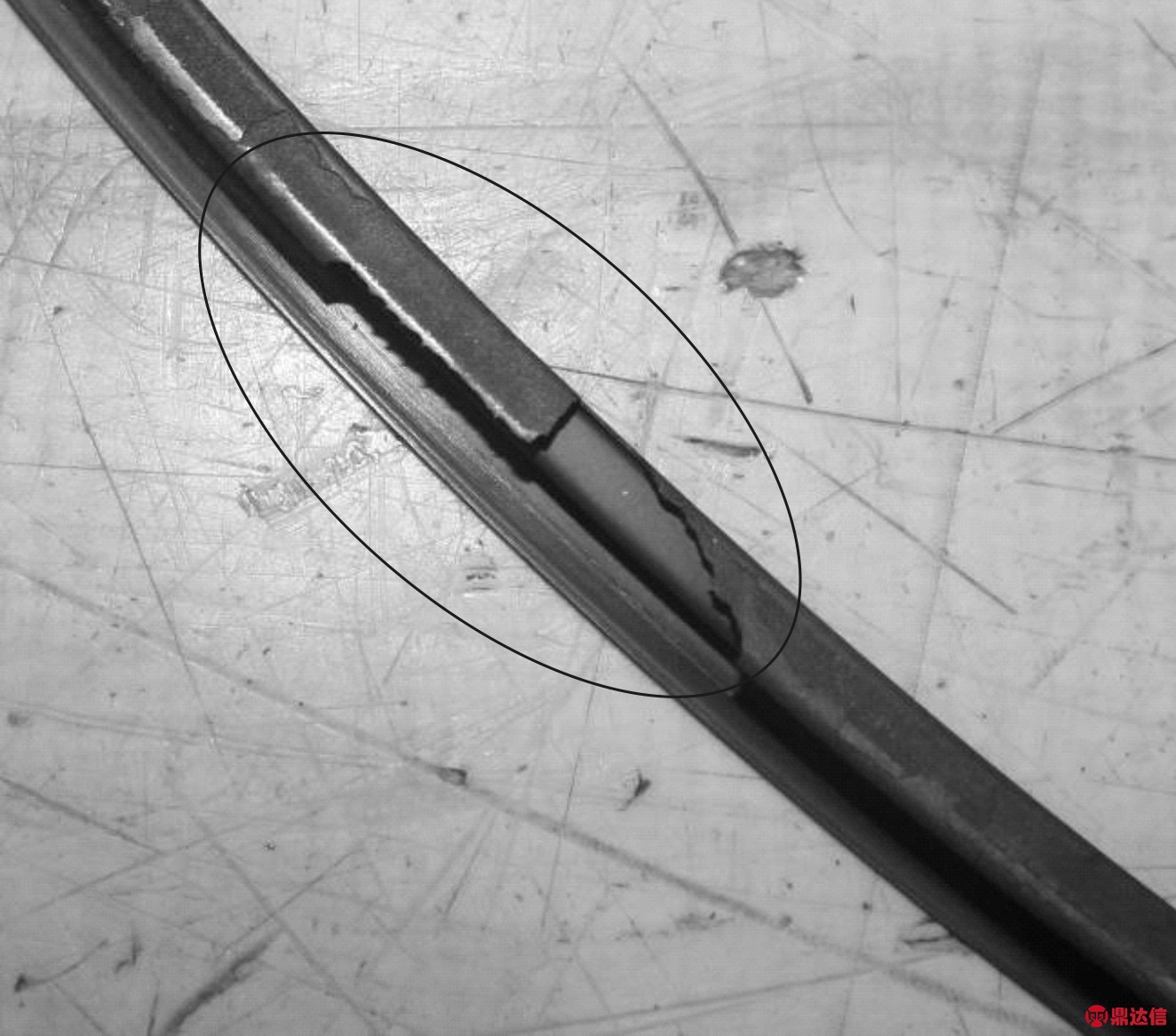
图3 W形密封环故障形貌
Fig 3 The photo of the failed W-ring
从W形密封环上掉块区域取样进行断口分析,宏观形貌如图4所示,断口较平缓,起伏不大,可见到较明显的疲劳弧线和放射棱线特征,表明断口性质为疲劳。根据疲劳弧线及放射棱线的方向判断,疲劳起始于W形密封环内表面(如图4中箭头所指)。
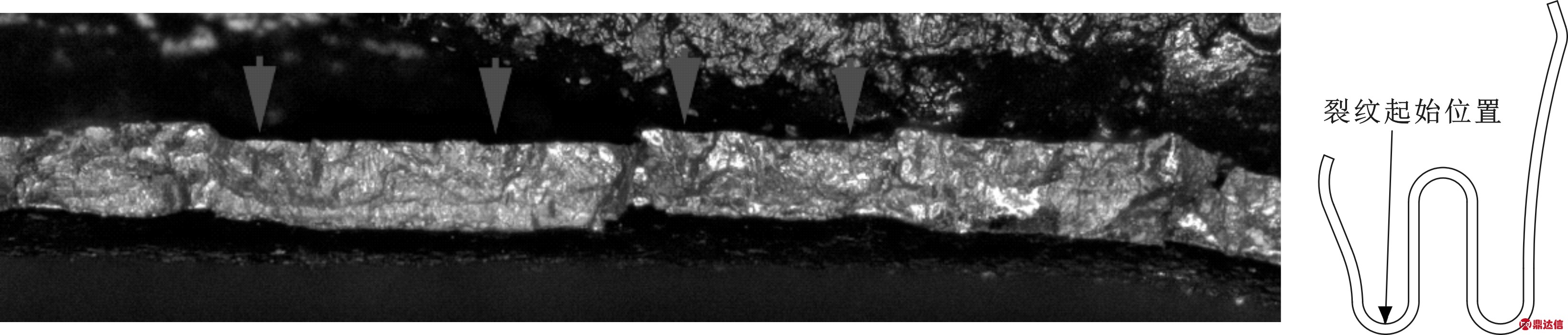
图4 W形密封环断口宏观形貌及对应位置
Fig 4 The morphology of the failed W-ring and fracture location
3 密封环受力分析
W形密封环的受力主要有2个方面,一是初始装配过程中受到的轴向挤压装配应力,二是工作工程中所受到的压力。
3.1 装配产生的应力分析
为了使得W形密封环在工作过程中保持密封效果,W形密封环要一直保持轴向受压缩状态,因此在初始装配时A、B零件对W形密封环产生初始轴向压缩,考虑零件尺寸加工公差后,轴向压缩量L=L2-L1=0.5~1.2 mm。
因W形密封环以及相邻结构都具有轴对称的特点,采用轴对称模型进行分析;因与W形密封环相邻结构的刚性要远大于W形密封环本身,可对相邻部件进行适当简化。装配前W形密封环为自由非压缩状态,仿真分析模型如图5所示。
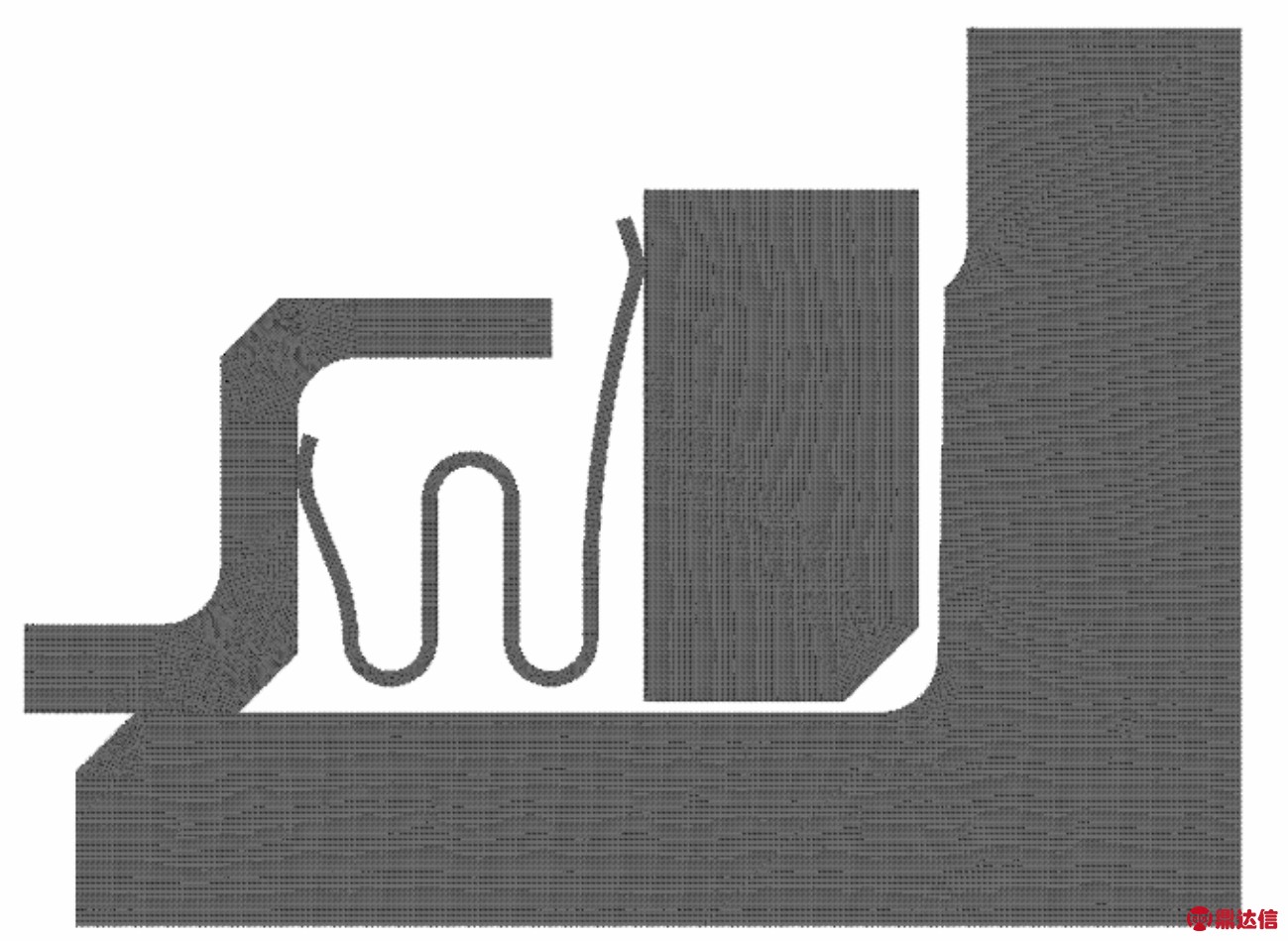
图5 W形密封环仿真分析模型
Fig 5 Finite element model of W-ring
装配过程在室温进行,从图6中可以看出,当初始装配压缩量较小时,只有点1、2发生接触,裂纹起始位置应力水平较低;继续增加压缩量时,因W形密封环不是左右对称结构,W形密封环出现“倾斜”的趋势;当压缩量增加达到0.72 mm后,出现第3个接触点,这时因W形密封环的接触边界条件发生突变,裂纹起始位置的应力增量变大;压缩量达到0.88 mm时W形密封环裂纹起始位置应力云图见图7。分析这一装配过程可知,初始装配时在裂纹起始位置会产生了一个压应力。初始装配压缩量不宜过大,否则会使应力超过材料的屈服强度;另外压缩量也不可以太小,否则密封环的变形不足以填满密封面的表面粗糙,在微观上形成微小的泄漏通道。
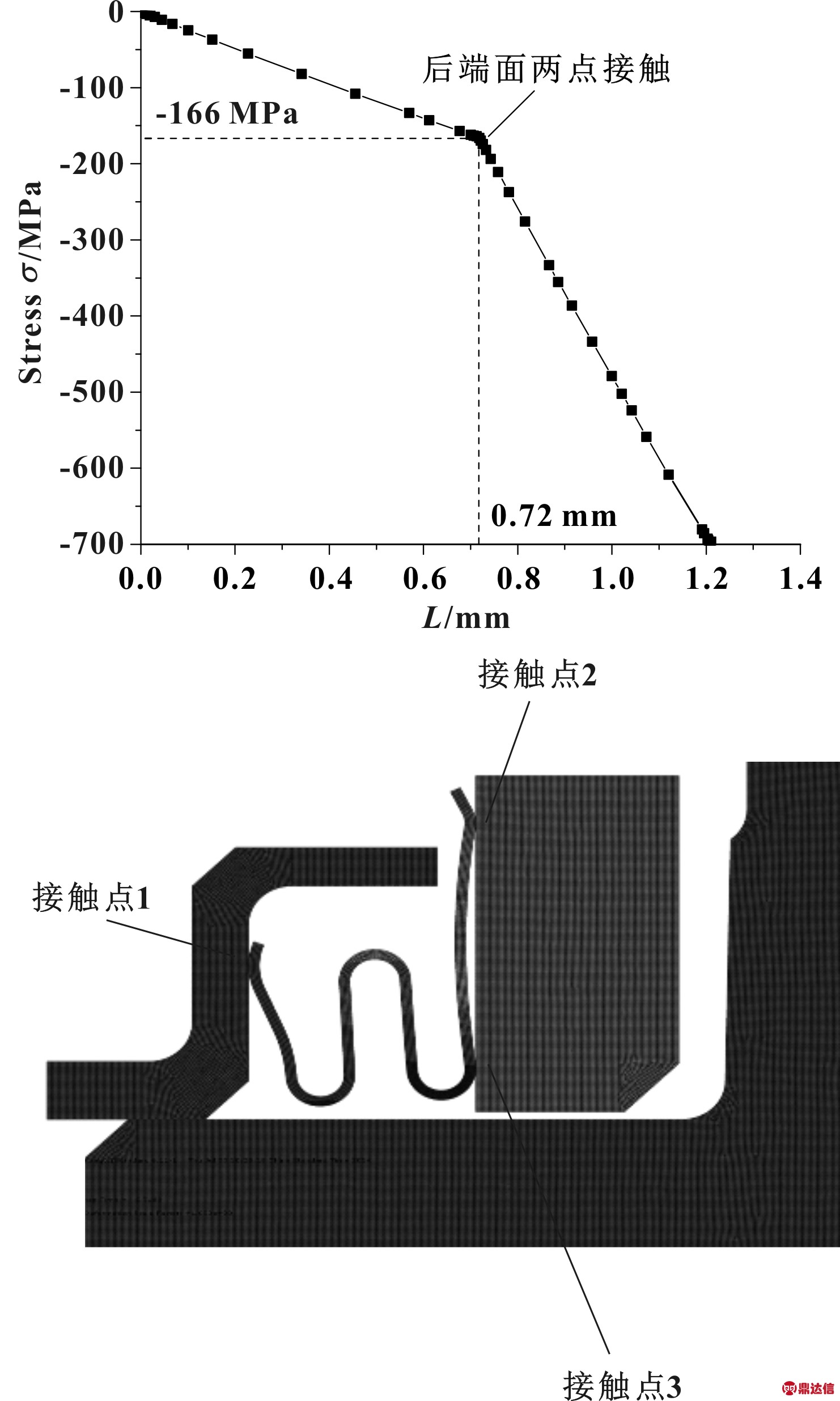
图6 轴向压缩量与裂纹起始位置应力的关系
Fig 6 Relationship between axial compression and stress of crack initiation
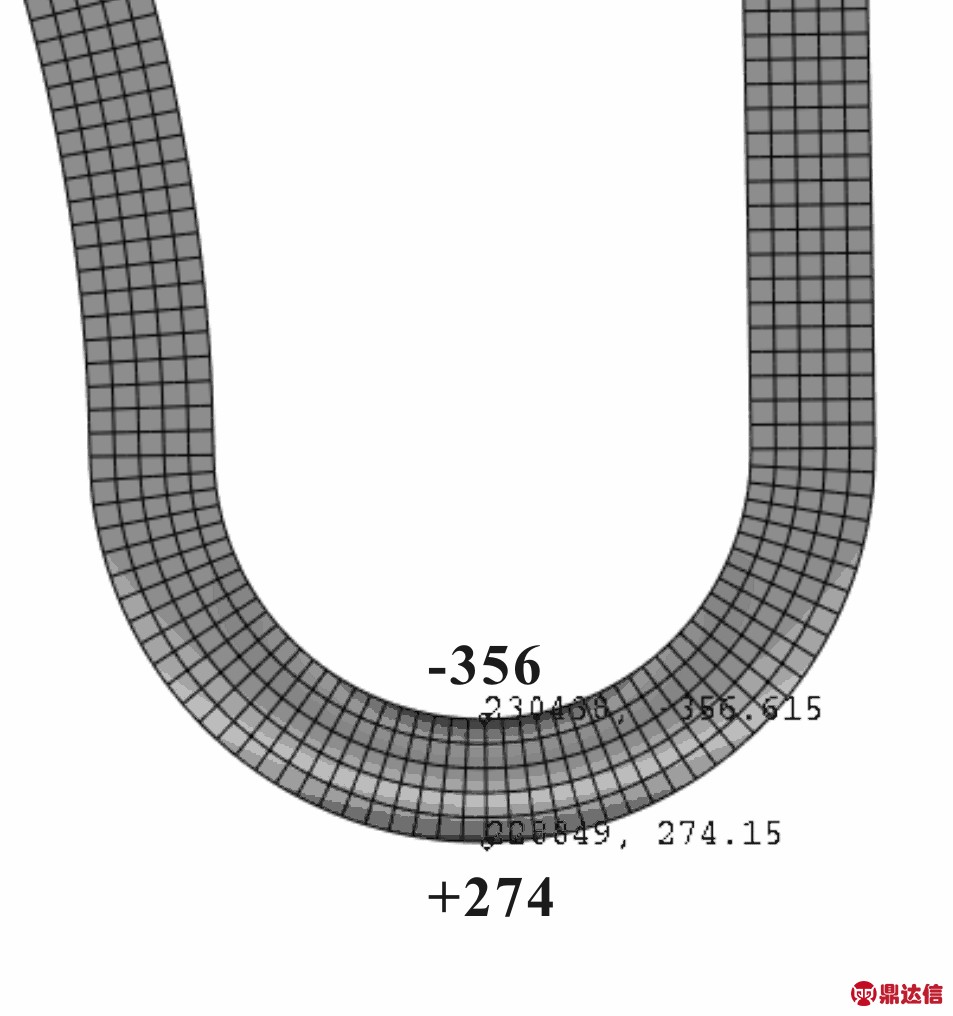
图7 W形密封环压缩量0.88 mm时裂纹起始位置的应力分布云图
Fig 7 Stress distribution of crack initiation of W-ring when the axial compression is 0.88 mm
3.2 压差产生的应力分析
W形密封环为金属薄壁结构,热传导性能优良,相邻结构的材料线膨胀系数与W形密封环基本一致,因此温差较小,不会产生大的热应力,高温700 ℃工作环境主要影响W形密封环材料力学性能。被W形密封环隔开的前后腔的压差,随着发动机状态的升高而逐渐变大。如图8所示,当压差达到0.7 MPa左右时,W环与C零件发生接触;压差继续增大时,裂纹起始位置应力增量会比未接触C零件时大,这一过程在裂纹起始位置的应力均为拉应力;当达到最大压差1.87 MPa时,因压差引起的裂纹起始位置应力水平已经达到774 MPa(见图9),超过了材料的屈服强度,局部进入塑性,不利于W密封环长期可靠工作,也不利于W形密封环的回弹能力。
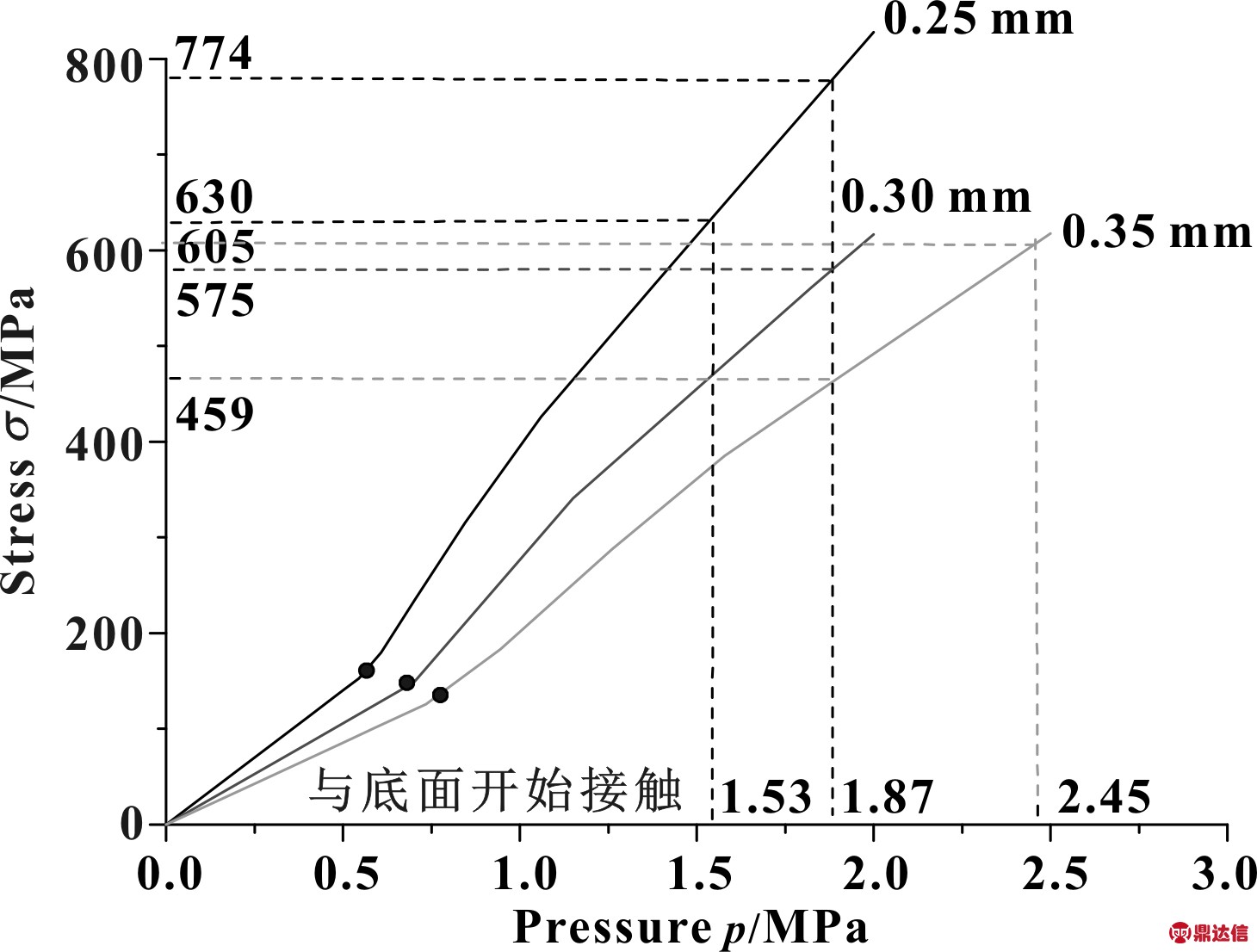
图8 不同W形密封环厚度条件下裂纹起始位置应力水平
Fig 8 Stress of crack initiation of W-ring with different wall thickness
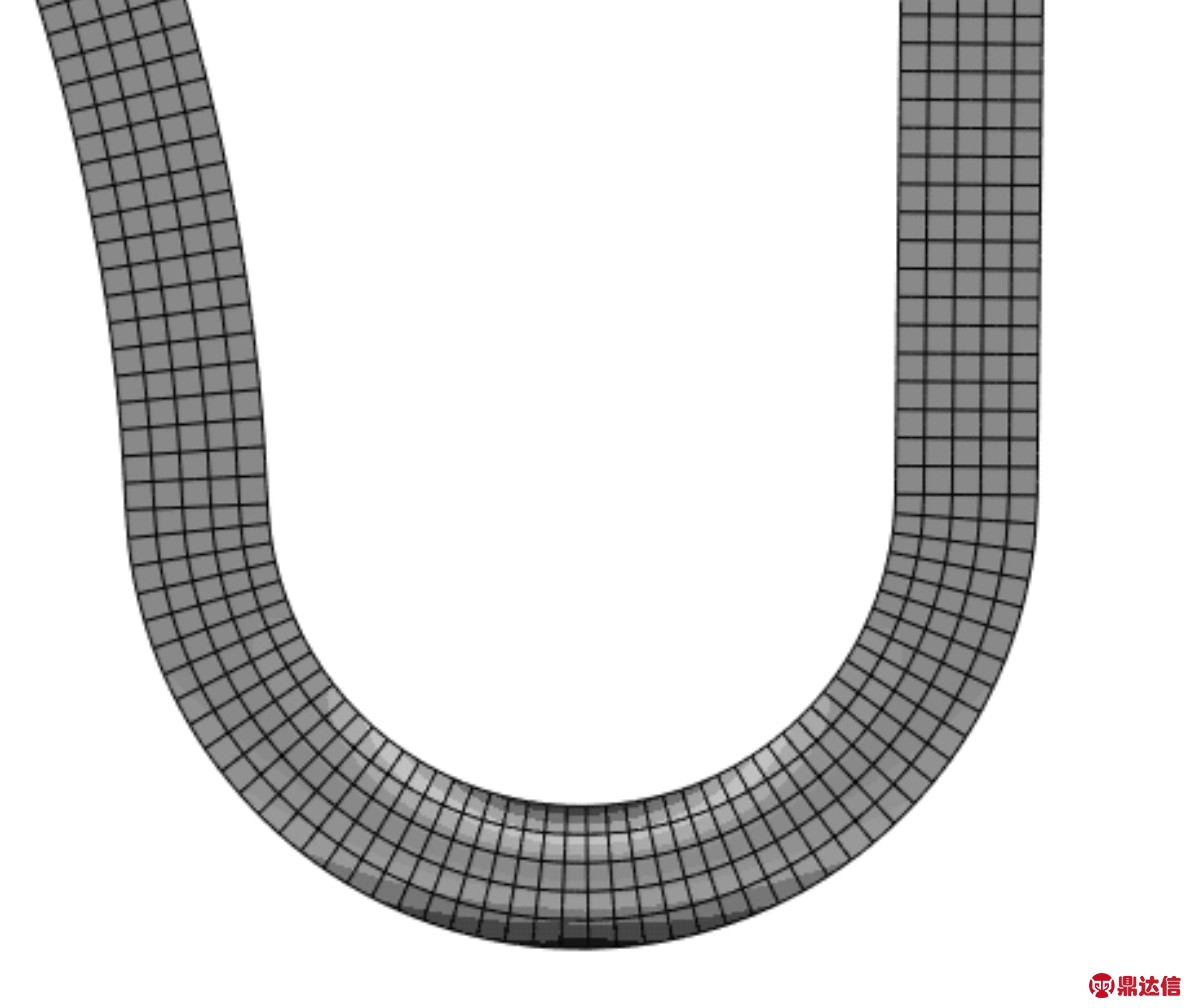
图9 W形密封环在1.87 MPa压差作用下裂纹起始位置应力分布云图
Fig 9 Stress distribution of crack initiation of W-ring when the working pressure is 1.87 MPa
4 改进措施
4.1 W形密封环关键结构参数分析
初始装配过程引起的压缩量会在裂纹起始位置产生压应力,工作过程中的压差会在裂纹起始位置产生拉应力,2种应力起到抵消作用。因此故障排除的重点是使这2种应力在合理范围内,一方面使峰、谷值应力的绝对值较小,使静强度满足要求;另一方面要保证峰谷值应力之差也较小,使疲劳寿命满足要求。
W形密封环的关键参数主要包括壁厚(d)、波高(h)、波峰半径(R1)、波谷半径(R2)、密封环内径(r)、密封环层数等,根据文献[8]中对关键参数论述,并结合此次故障特点,可以得出以下结论:
(1)增加壁厚(d)有利于提高W形密封环的耐压能力,但轴向刚度增加会使回弹能力变差,且会带来加工难度的增加;
(2)降低波高(h)有利于提高耐压能力,但回弹能力变差,且对回弹能力较为敏感;
(3)波峰半径(R1)、波谷半径(R2)对耐压能力影响不大,但受加工制造限制,两者取值一般基本相当;
(4)密封环内径(r)越大,耐压能力越弱,但其受相邻装配件半径限制,可调整范围很小;
(5)密封环层数越多,耐压能力越弱,但其改动会受到相邻装配件的轴向预留空间限制,且会带来结构稳定性问题和加工难度增加问题。
4.2 W形密封环壁厚改进措施分析
通过对这些关键参数分析,在不改动相邻零部件的条件下,选择适当增加W形密封环壁厚(d)的改进措施。为比较W形密封环壁厚的影响,选择了3种不同壁厚值,其应力变化规律如图8所示,强度储备如表3所示。从计算结果来看,将密封环壁厚改为0.3 mm即可满足强度设计要求。
表3 压差为1.87 MPa时不同壁厚W形密封环裂纹起始位置应力及强度储备
Table 3 Stress and safety reserve factor of W-ring with different wall thickness at working pressure of 1.87 MPa

4.3 初始装配压缩量改进措施分析
故障W形密封环的装配压缩量主要受相邻尺寸零件的实际公差影响,为兼顾W形密封环的装配应力和密封性要求,参考第前文装配应力计算结果,规定装配W形密封环前,对装配间隙L1、W形密封环轴向长度L2进行测量,必要时对相邻零件补加工,从而使初始装配压缩量控制在0.5~0.95 mm范围内,保证装配应力在合理范围内。
4.4 综合改进效果分析及验证
采取上述两项措施后的W形密封环计算结果见表4。原裂纹起始位置应力峰、谷值之差由774 MPa降低到575 MPa,降低约26%,经估算寿命可提高8倍;同时改进后的W形密封环应力都在弹性范围内,回弹能力强,也有利于提高密封性能。
表4 W形密封环改进前后疲劳循环峰谷值应力水平比较
Table 4 Comparison of stress of W-ring before and after improvement

改进后W形密封环随发动机整机完成初始飞行前规定的长试工作,性能良好,充分证明故障原因分析的正确性和改进措施有效性。
5 结论
分析得出W形密封环掉块的原因是,初始轴向压缩量偏大、工作中压差偏高造成裂纹起始位置应力较高,发动机状态不断变化产生交变载荷,最终导致疲劳裂纹产生。提出合理控制初始装配压缩量范围和增加壁厚的改进措施,使装配产生的压应力和压差产生的拉应力部分抵消,保证峰谷值应力之差较小,提高疲劳寿命。改进后的W形密封环通过了发动机长试验证,证明改进措施有效。