摘要:在正常生产槽上采用直接加阻流块稳定液体流速的方法降低电耗,在技术条件基本不变化的情况下直接降低电压100mV,对电流效率没有影响,吨铝可降低能耗200kWh~300kWh。
关键词:阻流块;电解槽;电压;节电
当前国内电解铝生产企业面对生存的压力,纷纷采用新工艺、新技术来降低生产成本。在结构变化上归纳起来分为两大方面:一是采用异型阳极,二是采用异型阴极。其目的是通过改变槽内型结构来稳定液体流速,降低极距的方式减少热收入,从而达到降低能耗的目的。我厂目前运行的电解槽都是刚刚投产的在产槽,如果采用新型槽结构达到降耗的目标的话一次性投入太大。在产槽上直接添加阻流块的原理与新型结构电解槽相同,在正常生产过程中直接添加阻流块就能实现节能降耗的目的。从2010年9月份与沈阳铝镁设计研究院有限公司合作,在4台200kA槽上放块实验,经过6个月的运行时间,电压由4.05V降到3.95V,最低电压到3.90V,槽况平稳、电流效率基本没有损失,吨铝可降低能耗200kWh~300kWh。
1 槽控机控制系统优化
为了适应电解槽铝液流态化技术要求,需要对电解槽槽控机控制系统进行优化升级,更新样板槽的相关软、硬件,进行现场培训及相关调整、安装。针对放块电解槽技术特点现场培训与调整的主要内容,为优化氧化铝浓度控制;确定电解槽出铝与换极过程中的技术条件调整;优化热平衡控制;优化应用电解槽监督管理系统。
2 槽外部保温
由于电解槽需要长期在低电压条件下运行,为维持电解槽正常生产时的热平衡,需要对电解槽进行外保温维护。
为了避免电解槽出现过热现象,实现其平稳地降电压,保温分为两个阶段进行。第一阶段为4.0V以上;第二阶段为4.0V以下。
保温的部位主要为电解槽大面、小面和底部。其中电解槽大面分为斜侧板、炭块区域和熔体区域,小面自下而上分为第一、二、三层。
3 阻流块的安放
3.1 SY200电解槽首批放块技术应用技术条件
为了顺利开展铝电解槽铝液流态化节能技术推广,需选择符合要求的电解槽进行第一批阻流块放块示范。为确保推广工作的顺利进行,第一批进行的SY200电解槽要求如下:槽龄不超过1200天;炉底基本平整,无明显沉淀,采用两水平测量阳极下软性沉淀量不大于2cm;炉底压降不大于350mV;电解槽槽况稳定,最近一个月内未曾发生过大的波动;电解槽铝液铁含量不大于0.15%、硅含量均不大于0.6%;电解槽铝液水平不低于系列平均值,不大于系列平均值2cm;电解槽电解质水平在过去的一个月平均值不低于系列平均值,不大于21cm;电解槽最近一个月的平均噪声不大于40mV;电解槽最近一个月平均温度稳定,标准偏差不大于10℃,平均温度不低于系列平均温度;电解槽过热度为5℃~15℃;电解槽阴极小软带无明显偏流,阴极钢棒温度无异常;电解槽最近一个月分子比稳定,标准偏差不大于0.12;电解槽电解质中的MgF2,LiF,KF,CaF2成分稳定,无明显波动,且与系列电解槽平均值基本相同。
3.2 阻流块在槽内摆放位置图
每台电解槽内放入阻流块26组,组合形式见图1,在槽内摆放位置见图2。
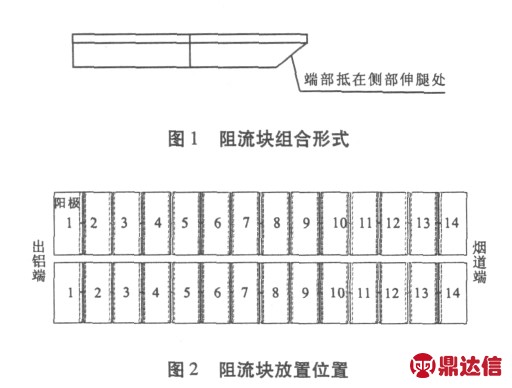
3.3 阻流块的预热
为了防止阻流块放入电解槽后遇到高温电解质和铝液,温度骤升发生裂纹或断裂,首先要对阻流块进行预热,使其温度达到200℃左右。
3.4 阻流块的吊放
预热后的阻流块放入电解槽中,因此吊放阻流块的吊具也是必须的。每台槽需要配套对应吊装用铝杆26套,预热后的阻流块放入吊具中,利用天车吊放入电解槽中。利用换极时间逐渐安放的方式,放块时间需要15天的时间。
4 试验槽的工艺技术条件控制
4.1 设定电压以及平均电压控制
阻流块试验槽的设定电压在阻流块放置的过程中会有所提高,这是因为考虑到放置阻流块过程中对电解槽的影响,例如槽内铝的流动性、氧化铝的溶解度等,在放置完之后会抬高设定电压15mV~20mV来稳定槽况。待槽况平稳之后,开始组织降电压,降电压的幅度可以从曲线图上看出。最终试验槽的设定电压降到了3.90V保持在3.95V设定电压见图3、平均电压见图4)达到了预期的目标。
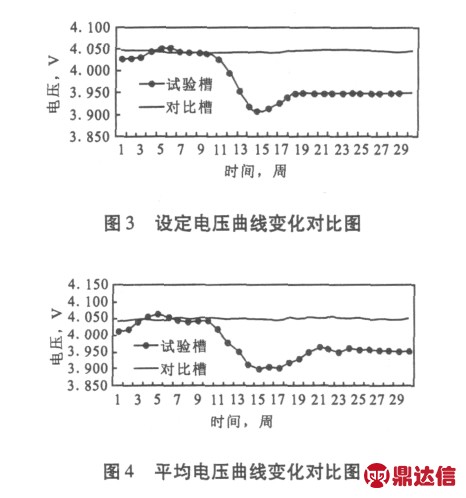
4.2 电解槽温度控制
在放置阻流块的过程中,电解槽的温度开始会比对比槽的高,这是由于放置阻流块对电解槽是一种外界干扰,同时它会造成氧化铝的溶解速度减慢,所以在前期会通过提高电压以及分子比的方式来稳定槽况,这也就造成了电解槽温度的上升。在后续的实验过程中,电压逐步降低,试验槽保持偏高的分子比,电解槽温度趋于正常(图5电解质温度变化曲线对比图)。
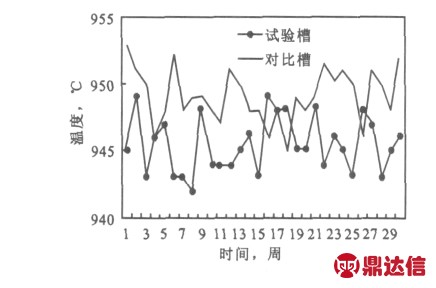
图5 电解质温度变化曲线对比图
4.3 铝水平控制
铝水平控制方面,在降电压的过程中,出铝量有所加大,以防止过热度和电解槽温度出现异常,影响到氧化铝的溶解性,在电压降到目标值之后,保持一定的铝水平来达到新的能量平衡。
4.4 分子比控制
试验槽的分子比整体相对于对比槽有所提高,以保证氧化铝正常的溶解性。
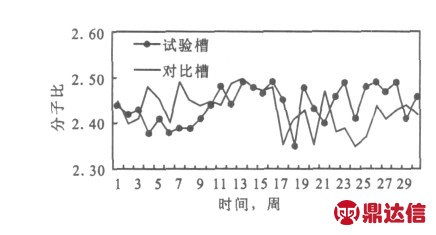
图6 分子比变化曲线对比图
4.5 氧化铝浓度控制
通过采用新的槽控技术解决了加阻流块后氧化铝浓度偏高的问题,保证了项目的平稳运行。氧化铝浓度控制变化曲线对比如图7。
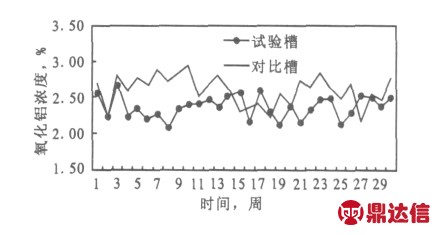
图7 氧化铝浓度变化曲线对比图
4.6 炉底压降
试验槽的炉底压降呈现逐步上升的趋势,一方面是由于放置阻流块之后,降低了槽内铝的流动性从而降低了电解质的流动性,导致了氧化铝的溶解速度降低;另一方面是由于后续的降电压造成的。炉底压降的有效控制一直是困扰阻流块试验的一个难点和重点。
表1 炉底压降变化表单位:mV
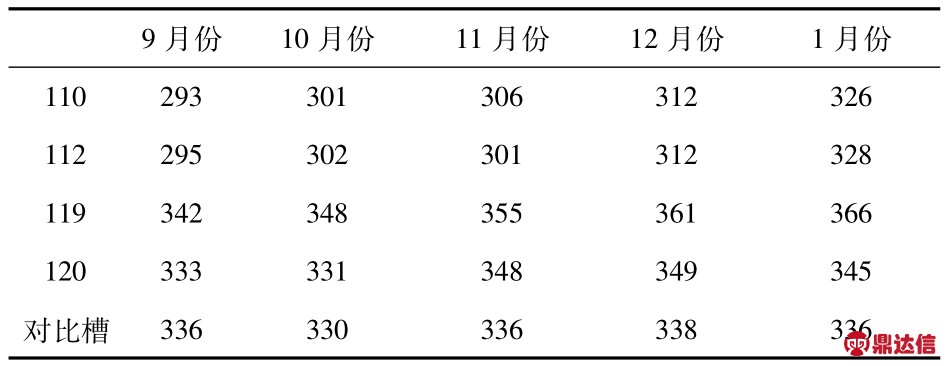
4.7 与兄弟单位生产技术指标的对比
与国内铝厂采用阻流块技术的生产指标对比,可以看出各厂由于电解质成分存在弱小的差距以外,其它各项技术指标相似。通过了解,采用阻流块技术的电解槽能耗降低效果明显。与兄弟单位技术指标对比情况见表2。
表2 生产技术指标对比表

5 结语
(1)添加阻流块的试验槽与对比槽相比,电流效率基本上没有大的差距,但阻流块的平均电压降低0.09V,最终试验槽吨铝电耗降低200kWh~300kWh,效果比较明显。
(2)本次使用的阻流块质量稳定,没有出现阻流块熔化的现象,电解质成分稳定。
(3)在实验过程中,炉底压降的控制还是一个难点,炉底沉淀较多,而且由于阻流块降低了铝液的流动性,同时在炉底形成一定范围的死角,造成炉底沉淀难化,如果炉底温度把握不好,最终有可能造成结壳,从而影响炉膛控制。
(4)在电压3.90V运行情况下,电流效率降低1%且槽况稳定性差、炉底压降持续升高,不利于长期的稳定生产。
(5)从目前添加阻流块槽实验效果以及其他厂家的效果来看,应用阻流块技术的电解槽设定电压维持在3.95V,电解槽可以长期稳定运行,太低会造成后续槽况稳定性变差。
(6)放置阻流块槽在实验进行的6个月的时间内,试验效果比较明显,达到了降低电耗的目标。
(7)对放置阻流块的电解槽在技术条件上还需要继续摸索,争取取得更好的效果。