作为节能减排的重要措施之一,汽车轻量化已成为必然趋势,其中铝合金在汽车轻量化中的应用逐渐推广[1-2]。在汽车用铝型材的挤压生产中,型材表面常常出现起鼓等缺陷,使型材呈凸形弯曲,挤压厂只能通过反复修模和试模来解决问题。随着挤压技术以及计算机软件和硬件条件的快速发展,基于有限元的数值模拟技术也日渐成熟,通过数值模拟,可以准确得到金属材料在挤压过程中的温度、流速以及应力应变情况,进而有针对性地对分流模具中分流桥、分流孔、焊合室、工作带、减震角等模具结构进行优化,来解决挤压生产过程中产品的缺陷问题[3-7]。陈浩[8]研究了多级焊合室对复杂空心型材挤压过程的影响以及分流孔的数量和布局对挤压过程的影响;王岩[9]针对“鱼”形空心型材的宽展挤压模具设计,分析了多级宽展和宽展角度对金属流速、温度、模具受力和焊合力等的影响;陈新欢[10]利用HyperXtrude有限元模拟软件,分析了铝型材多孔模具不同焊合室结构对型材流速、温度及焊合质量的影响。
对于行政事业单位来说,强化会计内部控制意识主要是为了发挥会计作用,保证行政事业单位可以依照当前的经济形势采取相应的经济管理措施,促进单位经济资源的高效利用。上级单位应加强行对行政事业单位领导的内部控制培训工作,将会计内部控制效果与考核相挂钩,从而树立单位领导层的内部控制理念,重视会计内部控制工作,积极主动去深入研究会计内部控制工作及办法。基层财务管理人员也应积极提高自身的责任意识和会计内部控制意识,多层次多方面提高自身业务管理水平,从而强化会计内部控制工作在实际执行过程中的水平,促进行政事业单位会计内部控制工作有效性提升。
本文作者结合公司实际挤压生产情况,利用Click2Extrude数值模拟分析软件模拟挤压过程,从焊合室中金属再分配的角度来分析型材起鼓缺陷的产生原因,并通过试模验证,有效解决了起鼓所带来的尺寸不合格问题。
1 3D模型建立
1.1 型材截面
本研究对象为某企业实际生产的汽车用6063铝合金型材,型材截面尺寸如图1。型材的最大壁厚2.02 mm,最小壁厚1.01 mm,截面积为871.21 mm2,周长740.45 mm。由于在实际挤压生产过程中,A区域位移方向为Y轴正方向,B区域位移方向为Y轴负方向,A区域向上凸,B区域向下凹,导致型材整体呈凸形,型材表面产生起鼓缺陷。
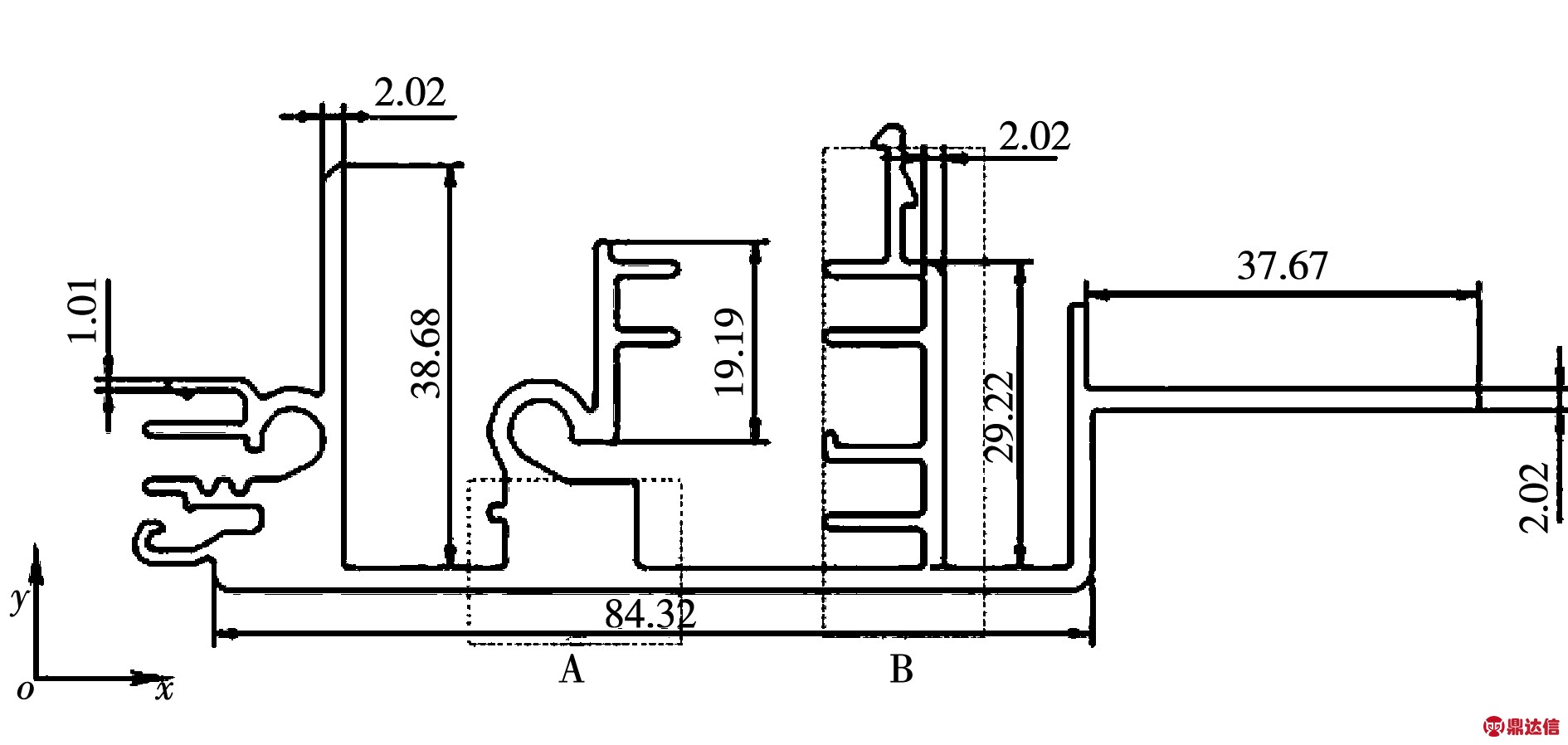
图1 型材截面
Fig.1 Profile section
1.2 模型的建立
根据图2所示的工作带尺寸,运用SolidWorks软件建立挤压模具的3D模型,如图3所示。上模尺寸为φ268 mm×65 mm,下模尺寸为φ268 mm×95 mm,挤压比为35.9。3D模型建立后,导入Click2Extrude中。设定挤压出料方向为Z轴正方向,A区域向内凹的方向为Y轴正方向。坯料直径178 mm,长度585 mm,铸锭材料为6063铝合金,模具材料为H13钢。设定铸锭加热温度480 ℃,模具加热温度450 ℃,挤压筒温度430 ℃,挤压速度为2 mm/s。
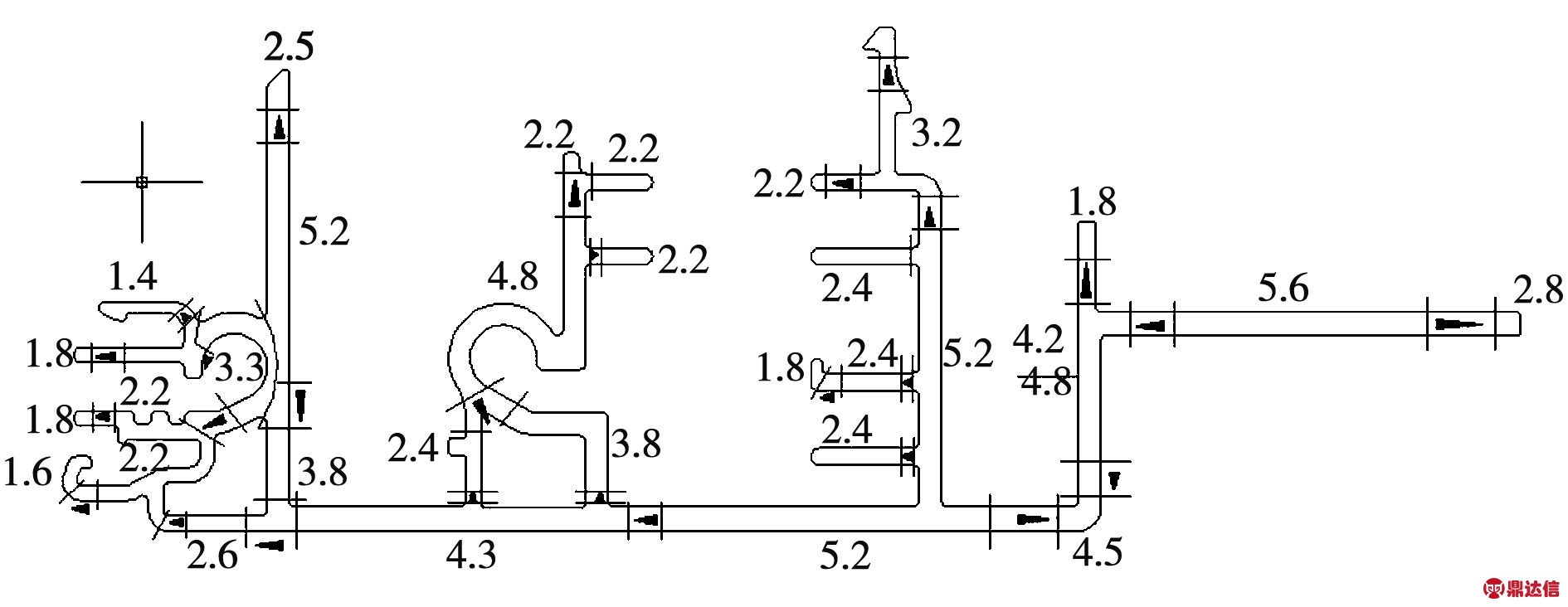
图2 工作带尺寸
Fig.2 Size of die band
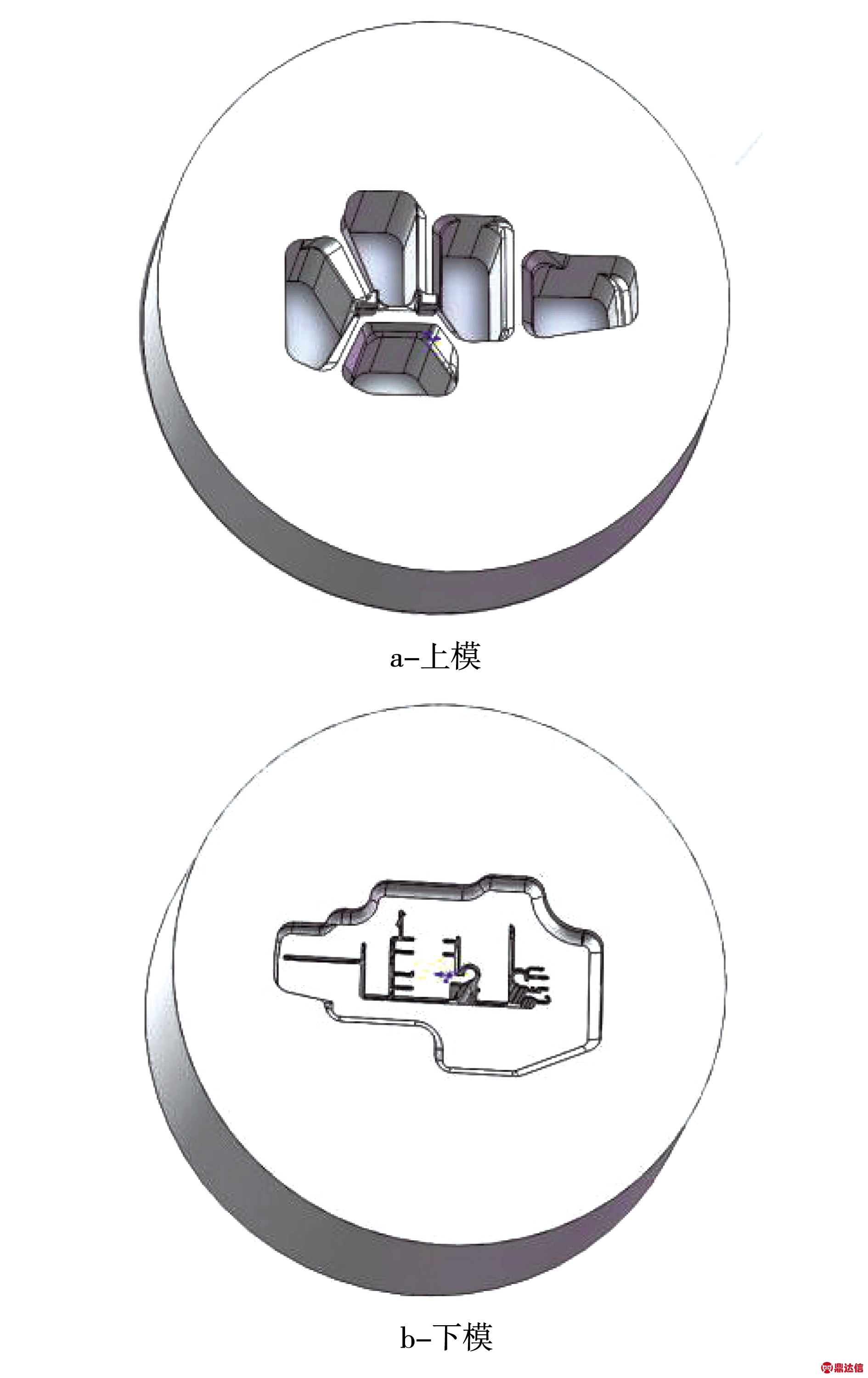
图3 模具3D模型
Fig.3 3D model of dies
2 模拟结果及验证
2.1 数值模拟结果分析
图4为型材在Y方向上的流速图、位移图。由图4可知,A区域的型材流速为3.92 mm/s,沿Y轴正方向;B区域的型材流速为1.93 mm/s,沿Y轴负方向,A、B区域流速差值为5.85 mm/s。A区域型材向Y轴正方向偏移,最大位移为0.233 mm,B区域型材向Y轴负方向偏移,最大位移量为0.11 mm,A、B区域的位移差为6.08mm。由于A、B区域的流速存在一定差值,导致其产生位移偏差,进而导致A区域向Y轴正方向凹陷,B区域向Y轴负方向凸起,最终引起型材表面起鼓缺陷。
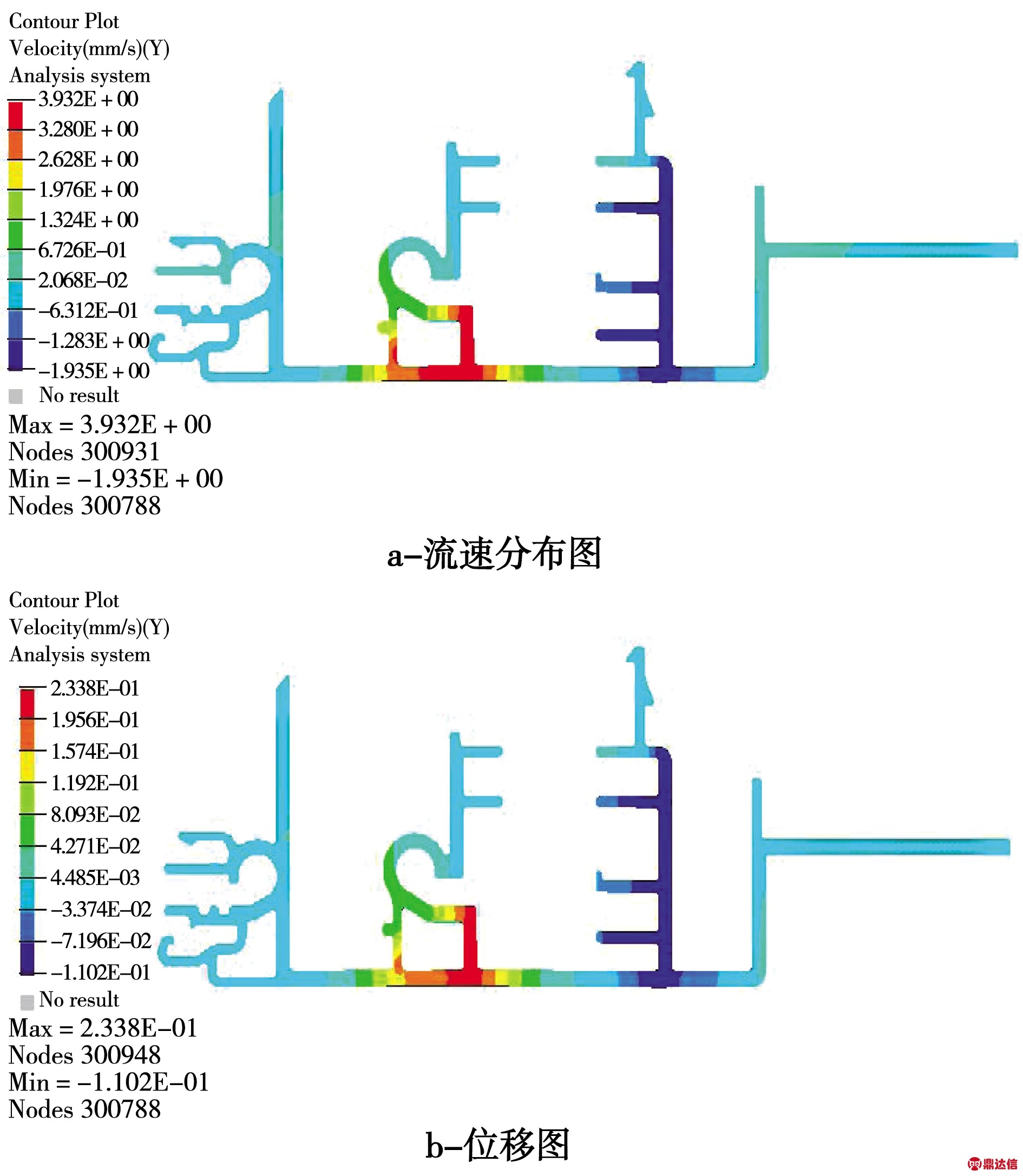
图4 Y方向上型材流速分布图和位移图
Fig.4 Velocity distribution and displacement diagram of profile in the Y direction
图5为分流孔、型材位置分布图。图6为模具各分流孔的流速分布图。
2.2.15 制剂长期稳定性试验 取铝箔包衣样品与薄膜包衣样品各200瓶,置于(20±2)℃、相对温度(40±5)%条件下,分别于放置第 0、3、6、9、12个月时取样,按“2.2.4”项下方法制备供试品溶液,再按“2.2.1”项下色谱条件进样测定,记录峰面积并以内标法计算样品含量,结果见表4。
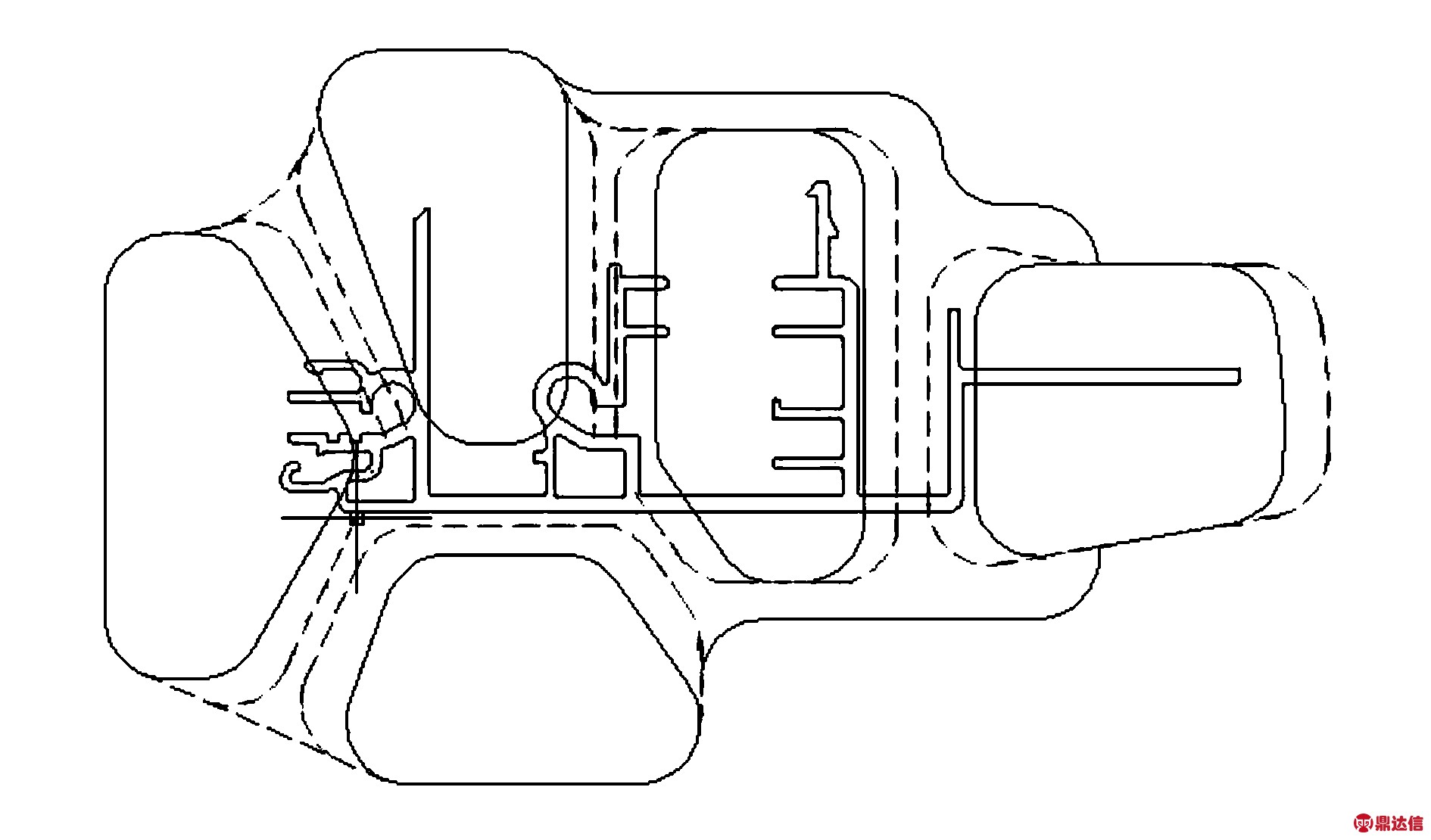
图5 分流孔、型材位置布置图
Fig.5 Arrangement diagram of portholes and profile position
分析图5、图6可知,1号分流孔的流速最快,然后依次为2号分流孔的、4号分流孔的和3号分流孔的。金属的流速由模具中心位置向周边位置是逐渐降低的,B区域型材在1号孔内,且B区域型材沿中心位置到周边都有覆盖,受到1号分流孔的影响,中心位置金属流速快,周边位置金属流速慢,金属流速慢的区域受到金属流速快的区域的拉应力。由于金属流动遵从最小阻力原则,所以B区域金属向Y轴负方向流动。A区域处于分流桥位置,由1、2、3号分流孔供料,且更为靠近2、3号分流孔。同时A区域处于模芯位置,金属通过上、下模共同作用后流出模孔。由于模芯的存在,金属在焊合室内的流动受到一定阻碍,所以A区域位置产生向上偏移,最终产生型材“起鼓”缺陷问题。
随着磨料质量百分浓度的增加,射流中的磨粒增多,使得对工件碰撞剪切的次数增多,从而增加了去除速率。但当磨料质量百分浓度太大时,射流中磨粒间的彼此碰撞几率增大,减小了与线材表面的碰撞几率,使得线材去除效率下降。此外,磨料质量百分浓度过大,进入沙管中的磨粒太多且进入的不均匀,使得磨粒不能及时随着高压水流射出,造成沙管堵塞,磨料随射流喷射的不均匀,使得对线材表面的去除效率下降,去除效果不稳定。因此,磨料质量百分浓度一般取60%为最佳。
人们的职业性质与之必须承受的社会责任是相应的。在国内,注册会计师必须站在独立的立场对公司的财务现状实施审查及审计工作,在这当中务必要保持公正、客观的审计态度,为企业财务的相关人员提供依据。注册会计师的相关原则有:履行相关责任以及恪守合理、客观、独立的原则,必须要始终保持的职业严谨态度,对于职业行为规范严格遵守,践行个人的职业责任等。为了可以规范注册会计师的相关行为,保障其工作的质量的有效性,提升注册会计师在群众中的良好形象,必须注重对国内注册会计师职业道德的培养。
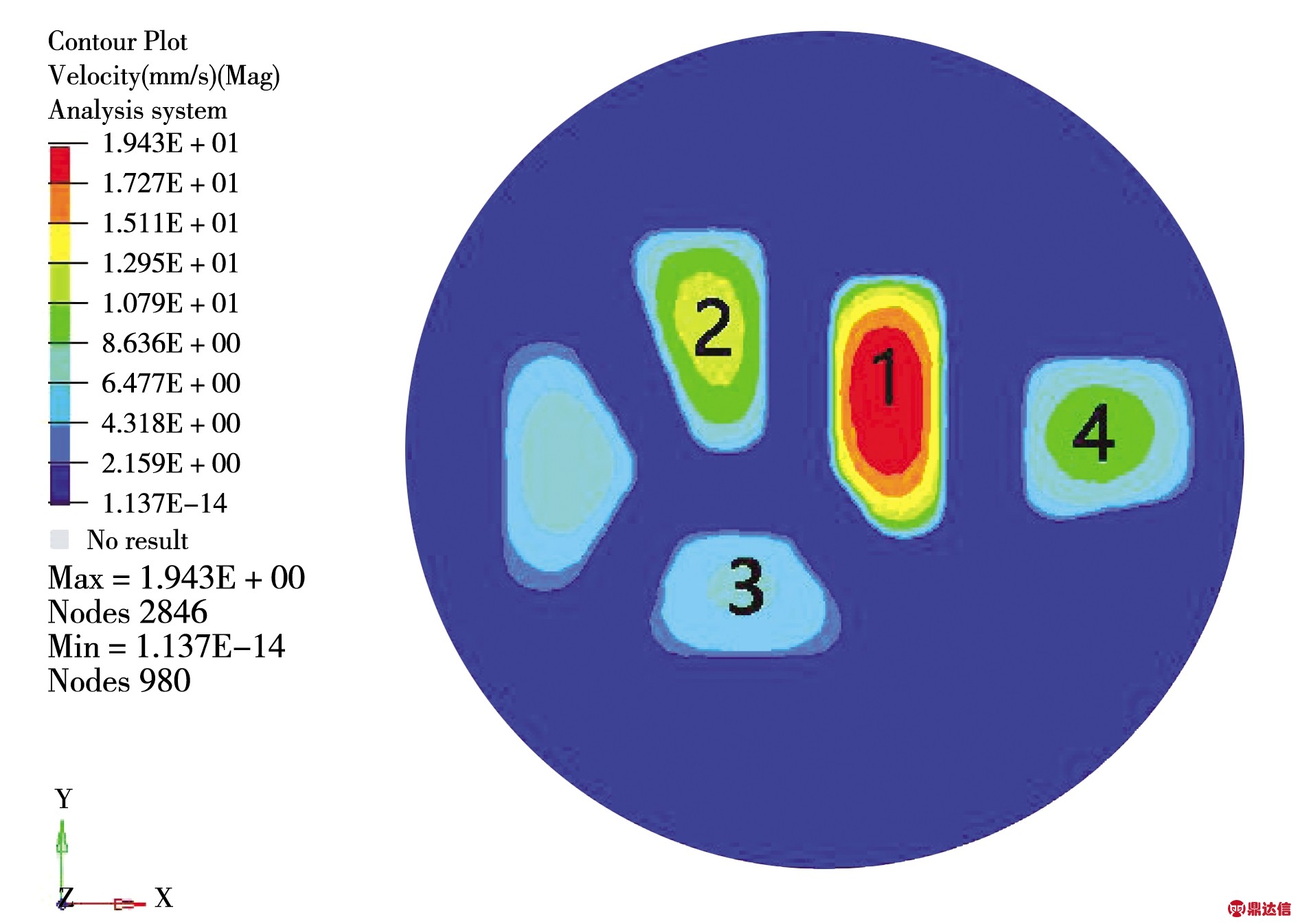
图6 分流孔流速分布
Fig.6 Velocity distribution of portholes
2.2 模具结构优化
根据数值模拟结果,可以初步判定为金属流量分配不均匀导致的金属流速不均匀,进而产生起鼓缺陷。金属经过分流孔分流后,在焊合室内重新焊合,同时,金属流量会重新分配。当焊合室高度不足时,金属没有足够的时间以及空间在焊合室内进行重新分配,直接通过焊合室,经工作带成型挤出。这种情况下,单个分流孔对金属的流速具有较大影响,分流孔中的金属流速不均匀直接导致型材出口处的金属流速不均匀,最终导致产品缺陷。所以通过增加焊合室高度给予金属足够的再分配空间,降低单个分流孔对金属流速的影响。为此,对上模进行沉桥处理,沉桥深度5 mm,焊合室高度则由10 mm变为15 mm。
图7为经过沉桥优化后的型材流速分布图和型材位移图。由图7可知,A区域的平均位移约为0.108 mm,沿Y轴正方向偏移,B区域的平均位移约为0.045 mm,沿Y轴负方向偏移,两者偏移量差值0.153 mm。A区域的平均流速为2.26 mm/s,方向沿Y轴正方向,B区域的平均流速为0.923 mm/s,方向沿Y轴负方向,两者流速差为3.19 mm/s。相比于优化前,A、B两个区域之间的位移偏差大大减小,剩余偏差量可通过拉伸矫直进行矫正。
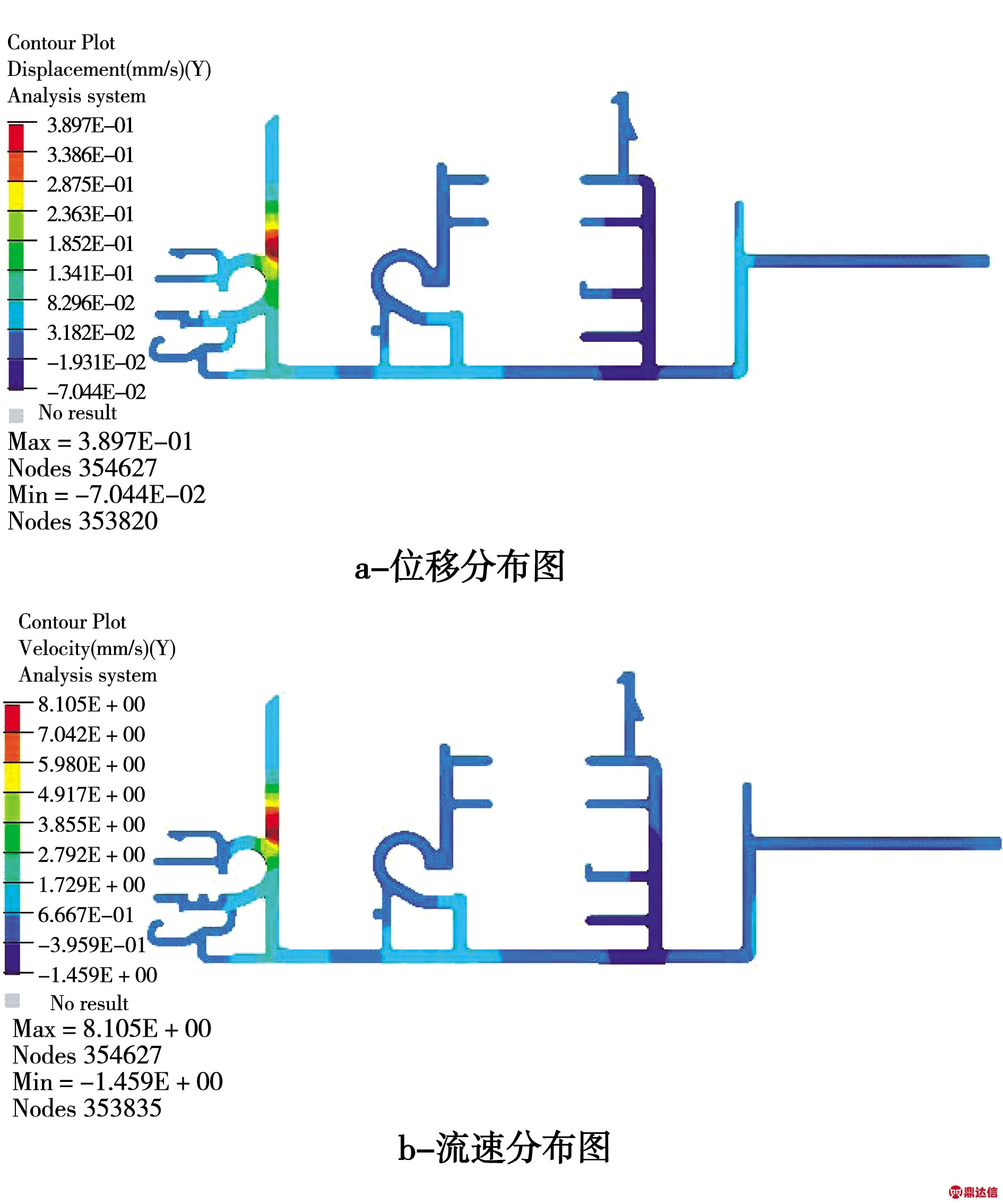
图7 优化后型材位移分布图和流速分布图
Fig.7 Optimized velocity distribution and displacement diagram
2.3 试模
通过对分流桥进行沉桥处理,增加焊合室高度等模具结构优化,在不改变其他挤压工艺参数的前提下,上机试模,挤压出的型材头如图8所示,型材通过拉伸、矫直处理,各部位尺寸在允许的公差范围内,无起鼓现象,满足客户要求。
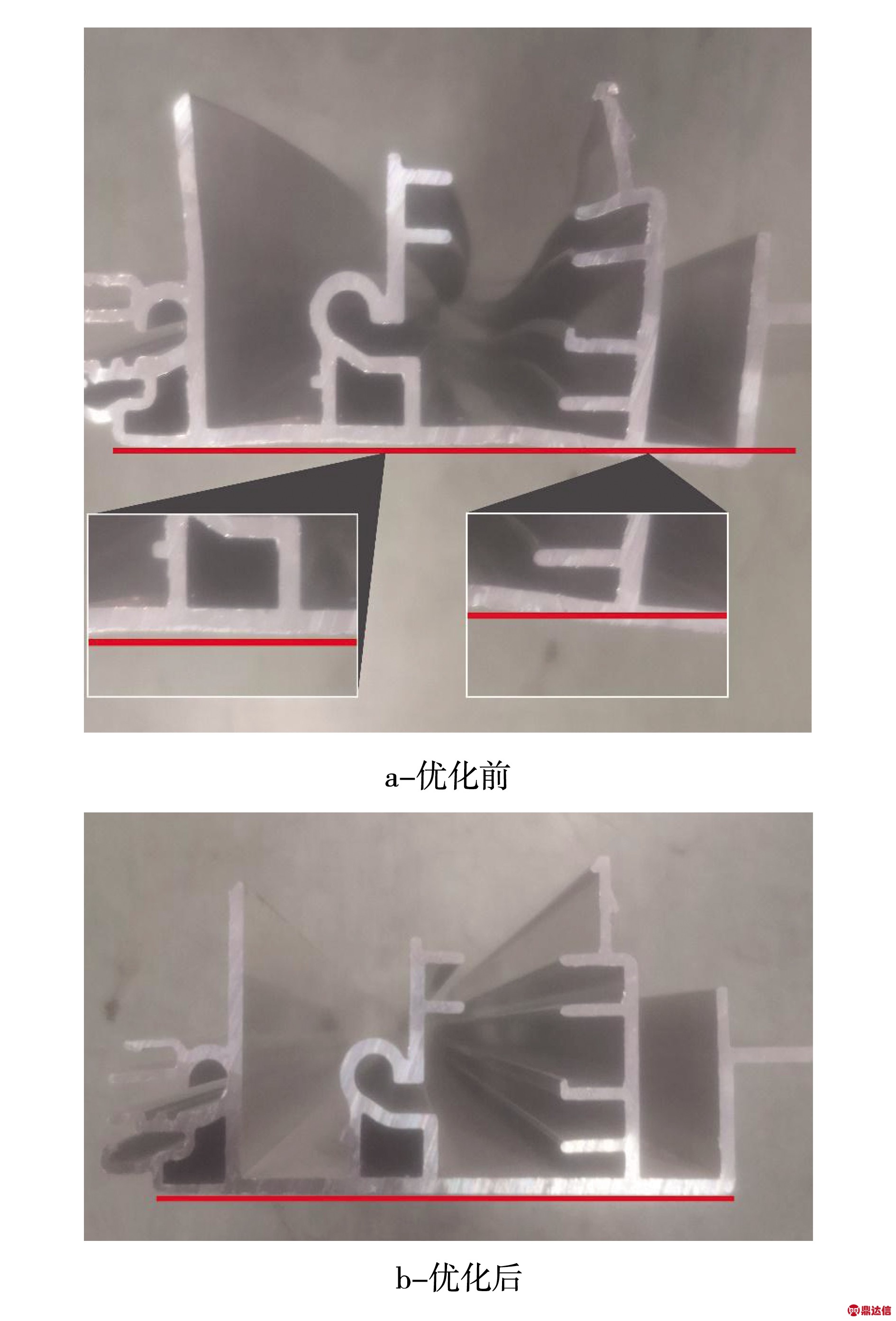
图8 模具优化前后的挤压型材
Fig.8 Profiles before and after optimization
3 结 论
1)数值模拟结果表明,该汽车用铝型材起鼓的表面尺寸缺陷是金属流量分配不均匀导致区域间流速差异而引起的。
2)通过对分流桥沉桥处理,并增加焊合室高度,使得金属流量在焊合室中的再分配更加均匀,型材的出口流速也更均匀,起鼓现象消失,挤压出尺寸合格的型材。