铝型材具有良好的加工性、耐蚀性和耐磨性,在建筑行业得到广泛应用。 通过表面处理可以提高建筑铝型材表面硬度、耐蚀性能和耐磨性能等,表面处理技术已成为扩大铝型材应用范围的关键[1-3]。 建筑铝型材阳极氧化传统工艺中,槽液温度必须控制在20±2 ℃,超过该温度,氧化膜会被破坏起粉,导致铝合金型材报废。 铝合金阳极氧化是一个发热过程,如果不采取降温措施,产生的热量会导致氧化槽液温度很快上升,因此,为了使槽液温度控制在20±2 ℃,传统工艺必须开启冷冻机使冷却系统水温保持在5~10 ℃,能耗较大。
十九大报告明确了习近平新时代中国特色社会主义思想,并把其写进了党章。习近平党的纪律建设思想作为习近平新时代中国特色社会主义思想的重要组成部分,对于我们坚持以习近平新时代中国特色社会主义思想为引领,进一步认识十八大以来党的纪律建设理论创新成果,并以全新宽广的视野探索新时代加强党的纪律建设的战略举措具有根本性、长远性的理论指导作用。
建筑铝型材宽温阳极氧化工艺中,槽液温度上限可以提高到35 ℃左右,因此可以大大节省冷却系统能耗,该节能工艺的研究及应用已成为目前研究热点之一,然而目前建筑铝型材行业通过改变阳极氧化工艺参数提高阳极氧化工艺温度上限的报道较少[4-5]。 本文选取6063-T5 建筑铝合金型材为研究对象,在传统硫酸阳极氧化工艺基础上加入添加剂GYK-1,研究添加剂GYK-1 含量对阳极氧化工艺温度上限、阳极氧化电压及成膜速度的影响,试图探索出一种能适应工业生产的建筑铝型材宽温快速阳极氧化节能工艺,为铝型材厂提供一种节能途径。
1 实验材料及方法
1.1 实验材料
实验试片为常用的6063-T5 建筑铝合金型材阳极氧化前坯料。
1.2 工艺流程
阳极氧化工艺采用建筑铝合金型材阳极氧化常用工艺,流程如下:脱脂→水洗→碱蚀→水洗→水洗→出光→水洗→阳极氧化→水洗→水洗→电解着色→水洗→水洗→封孔→水洗→水洗→风干。
具体工艺参数如下:
1) 脱脂。 在质量浓度150 g/L 的H2SO4 溶液中常温处理3~5 min。
2) 碱蚀。 碱蚀溶液为45 g/L 的NaOH+20 mL/L的碱蚀添加剂GYE-2。 碱蚀处理温度40 ~60 ℃,时间5~8 min。
3) 出光。 在质量浓度100 g/L 的HNO3 溶液中常温处理1~2 min。
4) 阳极氧化。 溶液为180 g/L 的H2SO4+20 g/L的Al3++GYK-1(根据实验要求调整)。 电流密度150 A/m2,氧化时间20 min,阴极材料为锯齿状纯铝板,温度根据实验要求调整。
5) 电解着色。 着色溶液为10 g/L 的SnSO4+20 g/L 的H2SO4+20 g/L 的电解着色添加剂GYZ-2。 常温,交流电压18 V,着色时间3 min。
6) 封孔。 常温封孔剂GYS-3 用量5 g/L,pH=6.0~6.5,常温,时间12 min。
习近平总书记在党的十九大报告中指出:“坚持富国和强军相统一,强化统一领导、顶层设计、改革创新和重大项目落实,深化国防科技工业改革,形成军民融合深度发展格局,构建一体化的国家战略体系和能力。”这是以习近平同志为核心的党中央着眼新时代坚持和发展中国特色社会主义,着眼国家发展和安全全局作出的重大战略部署。
1.3 阳极氧化温度控制
根据实验要求的氧化槽液温度,通过阳极氧化槽底部的不锈钢管分别通入冰水、自来水或热水调节槽液温度。 氧化过程中通压缩空气搅拌。
1.4 实验过程判定标准以及适宜工艺参数的确定
所有试片在经阳极氧化、电解着色、封孔、风干后,观察膜层是否起粉(或者氧化膜还没有起粉,但已经变得不透明或灰色时也判断为起粉),并与未添加GYK-1 的基准试片比较着色效果、外观质量,最终优化出GYK-1 用量、允许温度上限、氧化时间范围等适宜工艺参数。
1.5 氧化膜膜厚测定
采用QuaNix 4500 涡流测厚仪测定氧化膜厚度。
2 实验结果与讨论
2.1 GYK-1 用量对阳极氧化温度上限的影响
阳极氧化宽温添加剂GYK-1 主要由有机和无机两大组分复配而成,其中有机组分主要是络合剂、表面活性剂,无机组分主要是导电盐等,三者构成比例约为2 ∶1 ∶1。 GYK-1 可在氧化膜表面形成吸附层,具有隔离溶液的效果,减缓硫酸对氧化膜的溶解,使氧化膜成长速度提高。 GYK-1 的络合作用使溶液中的Al3+形成络合物,当氧化膜表面H+浓度较高时,能离解出Al3+,提高膜表层溶液的Al3+浓度,抑制氧化膜的溶解速度,提高氧化膜被硫酸溶解破坏(起粉)的温度上限,即提高阳极氧化工艺温度上限。
固定H2SO4 浓度180 g/L、Al3+浓度20 g/L、氧化时间20 min、电流密度150 A/m2,GYK-1 用量对阳极氧化温度上限的影响见图1。
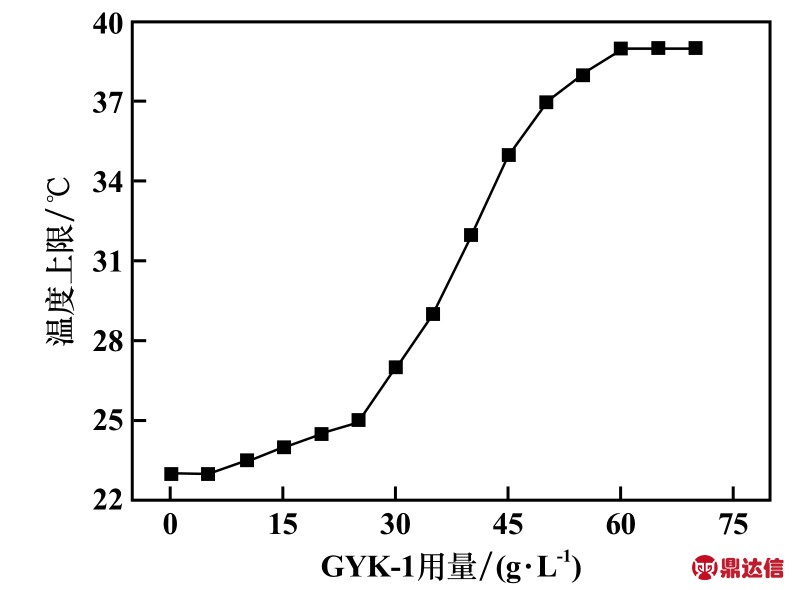
图1 GYK-1 用量对阳极氧化温度上限的影响
由图1 可知,当溶液中不含GYK-1 时,阳极氧化允许温度上限为23 ℃。 随着GYK-1 用量增加,首先温度上限提高较慢;当GYK-1 用量达到25 g/L 后,温度上限提高较快;当GYK-1 用量达到50 g/L 时,温度上限提高到37 ℃;再继续增大GYK-1 用量,温度上限变化不大。 综合考虑,GYK-1 适宜用量为50 g/L。
2.2 GYK-1 用量对阳极氧化电压的影响
相同条件下,GYK-1 用量对阳极氧化电压的影响见图2。
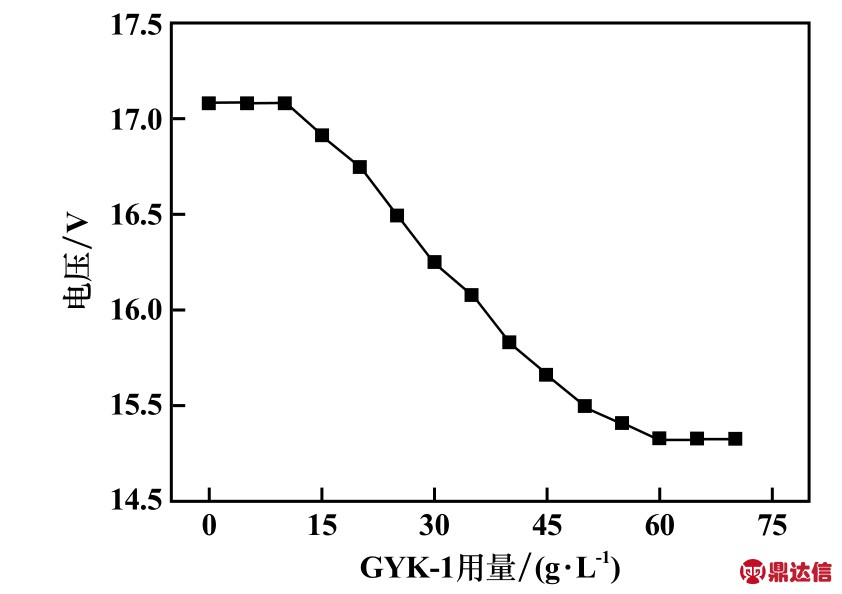
图2 GYK-1 用量对阳极氧化电压的影响
由图2 可知,随着GYK-1 用量增加,阳极氧化电压逐渐降低,即电耗减少。 GYK-1 用量较低时,电压下降较慢;当GYK-1 用量超过10 g/L 后,电压下降较快;当GYK-1 用量达到60 g/L 时,电压降至14.9 V;再继续增加添加剂,电压变化不大。
于是保安离他而去,花匠离他而去,厨子和女佣离他而去。他们在这里工作太久却没有得到什么,他们的离去太过正常。或许他们至死都不知道他们一直在为玩偶服务——他们是卑贱的奴仆,玩偶是高贵的主人,这实在充满讽刺;或许某一天,当他们突然在自己的脚跟或者脚趾间发现几道淡紫色的伤疤,当他们突然在某一个隐蔽的地方发现属于自己的保修卡、信誉卡、使用说明……当那一天真的来临,迎接他们的,首先是恐惧,然后是哀伤。
2.3 GYK-1 用量对阳极氧化成膜速度的影响
相同条件下,GYK-1 用量对阳极氧化成膜速度的影响见图3。
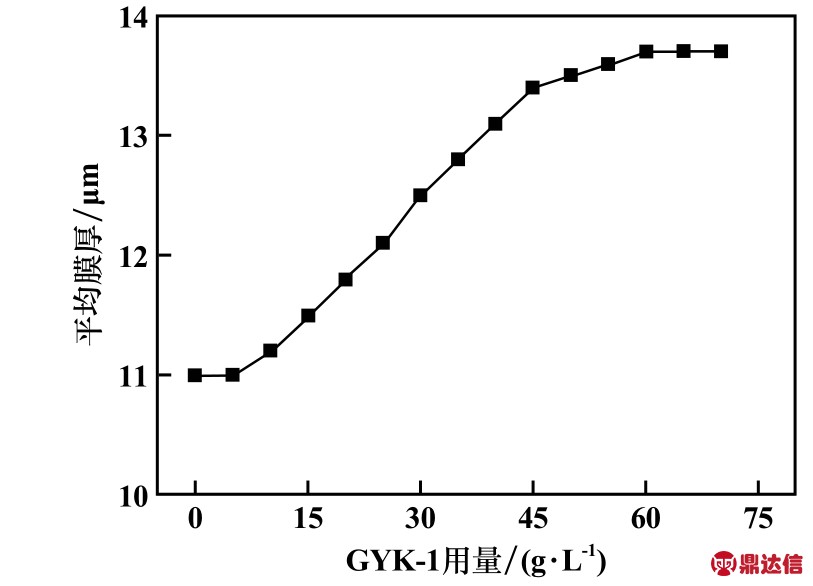
图3 GYK-1 用量对阳极氧化成膜速度的影响
从图3 可以看出,随着GYK-1 用量增加,平均膜厚逐渐增加。 因GYK-1 中的表面活性剂在铝合金阳极氧化过程中吸附在阳极表面,形成了一层薄薄的吸附膜,随着添加剂浓度增加,表面活性剂在氧化膜表面的吸附愈来愈多,甚至覆盖在整个阳极表面上,从而阻碍了电解液对阳极表面氧化膜的溶解,提高了氧化膜的成膜速度。 但表面活性剂在氧化膜表面的吸附增加到一定程度后,并不能无限制阻碍电解液对阳极表面氧化膜的溶解,当GYK-1 用量增加到50 g/L 时,平均膜厚13.5 μm,比不加GYK-1 时的膜厚增加约20%;之后再继续增加添加剂,平均膜厚增加不明显。 因此,GYK-1 用量取50 g/L。
Priamus系统技术公司把注意力集中在模腔内的传感器上,该公司德国部负责人Erwin Konig认为注塑工艺是一个非常复杂的制造过程,需要不断调节,所有的调节都会对注塑部件的质量产生或多或少的影响。此外该工艺过程还会受到多变的外部影响,这些外部变化对部件质量有决定性的影响。
1.1 研究对象 纳入 2018年1月至 6月在海军军医大学(第二军医大学)长海医院心血管内科行冠状动脉造影检查的老年患者 345例。纳入标准:住院患者,年龄≥60 岁,性别不限,接受冠状动脉造影术检查;排除标准:1 个月内曾服用肾毒性药物,碘过敏,肾动脉狭窄,休克,急性肾功能衰竭,血液透析,恶性肿瘤,配合度差,冠状动脉造影证实为扩张性心肌病、肥厚性心肌病等疾病,以及临床资料不全的患者。本研究已通过海军军医大学(第二军医大学)长海医院医学伦理委员会审批。
实验发现,氧化膜平均膜厚达到10 μm 所需的阳极氧化时间可缩短20%(16 min),在降低能耗的同时,提高了生产效率。
频综产生射频激励信号,其频率在时间上按三角波规律变化。激励信号经发射机放大后,通过发射天线转换成电磁波信号向外发射。电磁波信号遇到目标后,一部分能量被反射回接收天线,接收天线将回波信号转换为射频信号(RF),经低噪放放大后送入接收机。由于回波信号具有一定时间延迟,回波信号延迟后与本振信号就存在一定的频差,频差关系如图2所示[6]。
2.4 Al3+浓度对氧化温度上限的影响
在建筑铝型材阳极氧化工艺中,Al3+浓度对氧化温度上限的影响十分明显。 一方面,阳极氧化溶液中若没有Al3+,难以获得正常的膜层厚度,膜层的耐蚀性和耐磨性也差。 另一方面,由于硫酸对氧化铝的溶解作用,Al3+在阳极氧化溶液中不断积累。 过多的Al3+使氧化槽液导电性能下降,引起电压升高,电能消耗增大,同时氧化膜透明度下降,出现条纹、斑痕等不均匀现象,甚至可能出现膜层烧伤和封闭后变黑等现象。
随着计算机快速发展和零部件加工精度需求的提升,插补技术在数控机床加工过程中不可或缺,其中,三次B样条插补技术由于能够较为精确地表征自由曲线曲面的形状,在实际加工过程中得到了广泛的应用。三次B样条插补技术控制顶点的方式为反算法,即通过构造的轮廓曲线达到精确控制模型每个数据点的目的,并且可还原曲线的原有形状,同时在数据点间进行插值,计算容易且曲线光滑。为提高生产效率,在加工过程中采用连续B样条插补的方式,不仅可以多点加工一次完成,还能减少运行过程中电机的起停频率。
固定H2SO4 浓度180 g/L、GYK-1 用量50 g/L、氧化时间20 min、电流密度150 A/m2,Al3+浓度对阳极氧化温度上限的影响见图4。
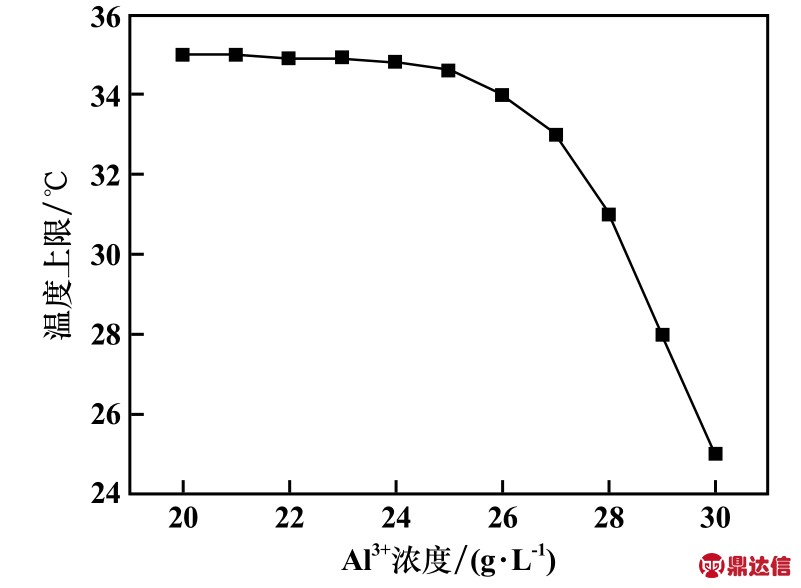
图4 Al3+浓度对阳极氧化温度上限的影响
建筑铝型材传统阳极氧化工艺中一般控制Al3+浓度15~20 g/L。 由图4 可知,随着Al3+浓度增加,氧化温度上限首先缓慢下降;当Al3+浓度达到25 g/L 后,氧化温度上限下降较快。 为避免频繁更换氧化槽液,控制经济成本,建议Al3+浓度控制在20~25 g/L。
①根据室内试验和现场模拟试验结果,采用8 cm或10 cm作为砂浆过渡层施工厚度都能够达到很好的黏结、缓冲和防渗作用,且力学性能和适应变形能力差别不大,考虑到经济因素,选择8 cm作为推荐施工厚度。
2.5 优化工艺参数
综合以上实验数据,优化出建筑铝型材宽温阳极氧化适宜工艺条件为:H2SO4 浓度160 ~180 g/L,Al3+浓度20~25 g/L,GYK-1 用量50 g/L,温度35±2 ℃,电流密度150 A/m2,氧化时间16 min。
3 生产应用
实验室中阳极氧化可以采取恒电流控制,精准地将氧化电流密度控制在150 A/m2,但在绝大多数生产厂家,现场操作人员不可能精确计算每一挂氧化料面积,实际都是采取恒压控制,因此使得实际生产中电流密度基本上在120~180 A/m2 范围内变化。
(2)强化培训,提高船员准入标准:船员管理处要从源头抓起,加强船员的培训和考核力度,提高广大船员的安全意识和实际操作技能;
在实验室优化出的节能工艺基础上,充分考虑生产实际中电流密度变化大、铝型材形状和结构复杂等各种因素,需适当降低阳极氧化温度上限、增加氧化时间和电压。
本研究优化出的节能工艺在山东某铝型材厂实施工业应用,每吨铝材的GYK-1 消耗量为5.0 kg。 阳极氧化具体工艺参数为:H2SO4 浓度160~180 g/L,GYK-1用量50 g/L,Al3+浓度20 ~25 g/L,温度30 ~33 ℃,电压15 V,时间17 min。 按此工艺生产,对该厂产品抽检,按GB/T 5237.2—2008[6]中AA10(16 h)标准规定进行CASS 实验,测试阳极氧化膜耐蚀性,检测结果均为9~10 级,均为合格;按标准规定进行落砂实验,测试阳极氧化膜耐磨性,检验均为合格。
宽温阳极氧化工艺温度上限为33 ℃,一般控制在30~33 ℃,只要冷却系统的冷却水温度保持在18~25 ℃就可以实现槽液温度控制。 当地气温在18 ℃以下时,不需要开启冷冻机,通过冷却塔就可以使冷却水池温度保持在18~25 ℃(只有当冷却水温度超过25 ℃时才开启冷冻机),因此可以大大节省冷冻系统能耗。
该厂氧化生产线全年节省电耗3 264 512 度,按相关资料数据(每消耗1 000 度的电能,就相当于排放了0.785 吨二氧化碳)计算,采用宽温阳极氧化节能工艺后,该厂每年可减排二氧化碳2 562 吨左右,节能减排效果明显。
该厂一条年产10 000 t 铝型材的阳极氧化生产线使用以上节能工艺,一年节省费用(节省的电费扣除化学药品配槽及消耗费用)约90.7 万元((626-547)×12 752-100 000 =907 408),具有良好的经济效益。 使用该工艺前后能耗及综合成本对比见表1。
表1 山东某铝型材厂使用该工艺前后能耗及综合成本对比

时间 年产量/t用电量/(kW·h)吨电耗/(kWh·t-1)节省电量/(kWh·t-1)GYK-1 配槽/万元GYK-1 消耗/(元·t-1)综合成本/(元·t-1)年节省成本/万元使用前 10 536 8 249 688 783 0 0 0 626 0使用后 12 752 6 720 304 527 256 10 125 547 90.7
4 结 论
1) 优化实验得到适宜建筑铝型材宽温快速阳极氧化节能工艺条件为:H2SO4 浓度180 g/L,GYK-1 用量50 g/L, Al3+浓度20~25 g/L,温度30~33 ℃,氧化电压15 V,氧化时间17 min。
2) 采用以上节能工艺条件进行建筑铝型材宽温阳极氧化,氧化槽工艺温度上限由22 ℃提高到33 ℃,大大降低了冷冻系统能耗;氧化槽电压降低10%、阳极氧化时间节省20%,进一步降低了阳极氧化能耗,提高了生产效率;同时,氧化膜耐蚀性、耐磨性均能达到相应国家标准。
3) 该节能工艺是一种可行的建筑铝型材宽温快速阳极氧化节能工艺,其应用具有良好的经济效益和社会效益。