摘 要:针对单缸柴油机排气消声器在中低频段消声效果不理想的问题,提出一种新的消声器结构优化方案。首先,利用Virtual.Lab和Fluent软件进行消声器声学优化以及流场优化。然后对两种消声器动力性能进行对比分析,并通过功率损失试验和插入损失试验对比分析优化前后的消声器。仿真结果表明,优化后的消声器在中低频段消声效果优于原消声器,且内部平均温度比原消声器有所降低。试验结果表明,在典型扭矩点和功率点噪声分别降低约4.0 dB和3.6 dB,均降低明显。优化后的消声器在不同转速工况下插入损失提升效果均十分显著,但功率损失率仍在允许范围内,这证明了新消声器结构的可行性。
关键词:声学;单缸柴油机;消声器;消声性能;结构优化
如今,我国对汽车噪声控制的要求越来越高,因此对于汽车厂家而言,降噪是一个急需解决的问题。在汽车的所有噪声中,汽车发动机的排气噪声是最主要噪声,通常情况下,该噪声可以超过整体发动机其他噪声10 dB~15 dB以上[1]。在柴油机工作过程中,主要的噪声来自于机械、空气动力以及燃烧,其中最突出的噪声来自于机械动力[2]。若要降低排气噪声,安装排气消声器是一种最简单有效的方法。为了尽可能消除排气噪声,必须设计出高性能的消声器[3]。
近年来,国内外研究人员经过不断探索,在消声器研究方面取得不少成果。Singh等[4]提出了一种混合合成流入边界条件,并应用于简单的膨胀消声器,分析其内部的流动声和声脉冲相互作用。Jena 等[5]通过数值模拟研究了用于测量无平均流量消声器的声传输损耗测量技术。Sakamoto等[6]以门缘厚部内的消声器为研究对象,通过对3种消声器的理论分析和实验,测定声音传输损失,来评价消声器的性能。Kumar等[7]利用CFD 对消声器出口的速度进行了分析,开发了优化模型对其进行了分析。
国内对消声器的研究也在不断进步,白云等[8]建立了简单扩张式抗性消声器模型,并对其结构和消声性能进行了模拟仿真分析。温逸云等[9]运用有限元法,通过对穿孔分布、插入长度、扩张腔直径、穿孔率等各项参数分析,研究这些因素给消声器性能带来的影响。彭菊生[10]建立了相关的理论模型,并借助于声学软件Sysnoise仿真分析某款汽车排气消声器在性能方面传递损失。翟华等[11]通过分析锻压装备中的大功率电机产生的噪声,提出了微穿孔板这一新型消声结构。杜华蓉等[12]针对某载货汽车发动机排气消声器在中、低频区域消声效果较差问题,提出了两种消声器结构优化方案。
1 原消声器主要性能研究
1.1 评价消声器性能的指标
消声器性能评价主要指标有两部分,其一是声学性能指标,其二是动力学性能指标。在声学性能这一评价指标中,主要包括插入损失和传递损失等,空气动力学指标主要包括压力损失和功率损失比等。
传递损失LTL指消声器进出口端声功率之差,其计算公式为

在式(1)中,消声器进口端声功率级用LW1 来示,出口端声功率级用LW2表示,其单位是dB;进口端声功率用W1表示,出口端声功率用W2表示,其单位是W。
传递损失所反映出的仅仅是消声器自身所具备的声学特征,这仅仅与其结构形式有着直接关系,并不受外界因素的影响。
LIL表示插入损失,就是在消声器安装前后,其出口位置声功率级或者是声压级出现的差值,以下是其表达式:

在式(2)中,消声器安装之前的某个测点位置声功率级用LWi来表示,安装之后的声功率级用LWt来表示,其单位是dB;安装前某个测点位置的声功率用Wi 来表示,安装之后的声功率用Wt 来表示,其单位是W。
测量插入损失有比较简单的方法,其对于测量环境也并无很高的要求,所以实现起来也更加容易,通过该测量结果,不仅可以将消声器自身所具备的消声性能反映出来,同时也可以将其和外部综合声学性能体现出来。
Δp代表压力损失,为当一定量的平稳气流在消声器内部时进口处和出口处的平均全压差[13]。因为本次研究的消声器两端有相同的横截面积,所以可将其气流静压差看做压力损失,其公式为
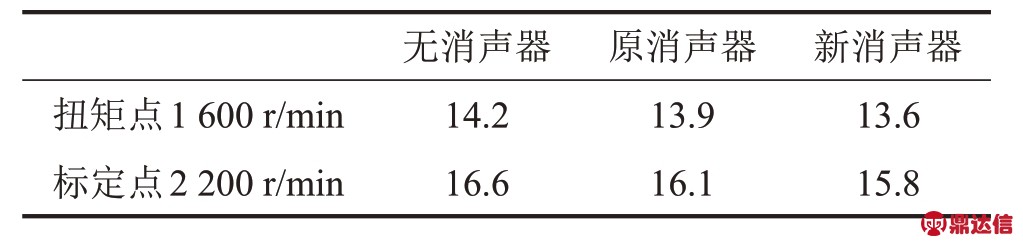
在式(3)中,截面直径用d 来表示,气流速度用ρ来表示,流速用ν 来表示,原来的压力用pν 来表示,管道长度用l来表示,摩擦阻力系数λ为0.024[3]。
通过式(3)可知:气流速度的平方和气流阻力损失之间有着正比关系,在气流速度加大过程中,阻力损失量也会增加。而随着压力损失的增加,消声器功率消耗也会增加,随之而来的就是排气温度以及排气背压的上升[14]。因此,出于对声学性能以及空气动力性能考虑,在消声器设计过程中,流速应该较低一些。
RN代表功率损失比,它指当发动机处在标定工况条件下时消声器安装之前和安装之后功率差值的百分比,即:
式中:Pe1与Pe2分别代表安装消声器前后发动机的功率,一般单位为kW。
功率损失比体现了阻力损失对发动机性能产生的影响。测量功率损失比时,应该尽量保证发动机状态和试验环境不发生变化,一般要控制RN ≤5 %。
通常情况下,插入损失与功率损失比通过试验测试分析得到,消声器的传递损失与压力损失利用软件仿真分析计算得到。
1.2 原消声器声学性能分析
本文针对一款在用消声器消声效果不好的问题开展研究。该消声器外部主要由进气管、排气管和壳体组成,内部由2块穿孔板将整个腔体分隔为3个腔室,如图1所示。其内部结构较为简单,可能是导致其消声效果不理想的主要原因,因此考虑通过改变其内部结构对原消声器进行优化。
测量该消声器实物的尺寸,在UG 中建立原消声器三维模型,并在Hypermesh 中对其进行网格划分,得到了相应的声学网格,然后借助于LMS virtual.Lab 软件分析声学性能,将空气按照流体材料进行定义,将单位声功率作为消声器入口位置的边界条件,将出口位置的属性定义为AML层,将分析频率控制在1 Hz 至5 000 Hz 之间,将步长设置为10 Hz。通过计算得出了消声器原来的传递损失[15],具体情况如图2所示。

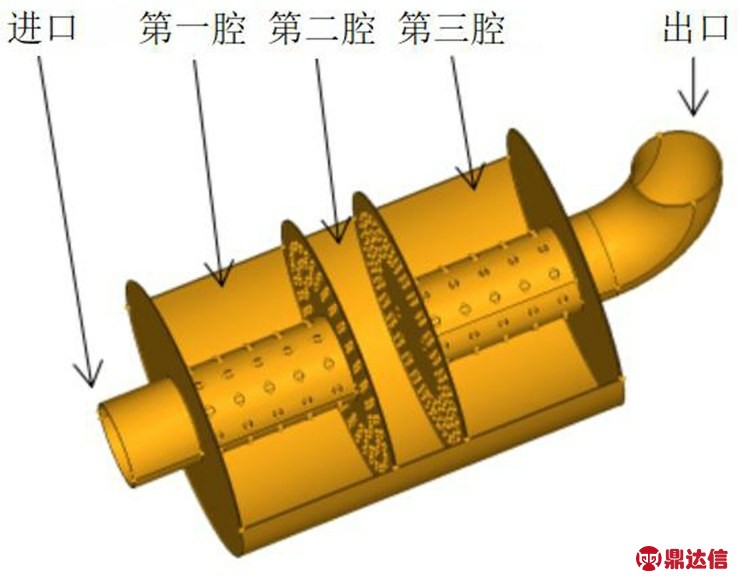
图1 原消声器模型
由图2可知,原消声器在低频段尤其是1 000 Hz以内的传递损失较低,确实存在低频区消声效果不理想的问题。消声器优化设计中常用的一种方法就是优化消声器的内部结构,在保证消声器高频区消声效果的同时,提高消声器在低频段的消声性能。另外,也要控制其功率损失不能过高。
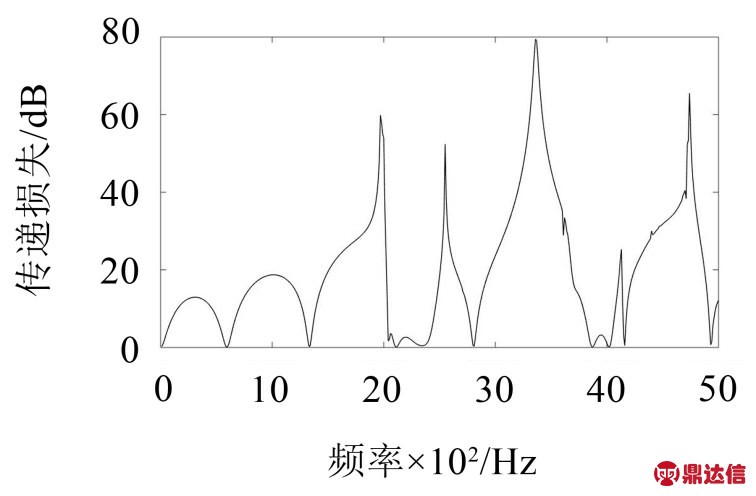
图2 原消声器的传递损失频谱
2 消声器结构优化
2.1 消声器结构优化方案
单级扩张式消声器是最简单的消声结构,它的传递损失为

在式(5)中,扩张比用m表示,m=R2/r12;扩张室的半径用R表示,扩张室的长度用L表示,入口管的半径用r1表示,波数用k表示,k=2π/λ,声波的频率将会对其起到决定性作用。
当kL是的奇数倍时,sin(kL)=1,消声量取最大值,即:

与最大消声量TLmax 相对应的频率称为峰值频率。扩张室长度和峰值频率分别为
当kL是π的整数倍时,sin(kL)=0,此时消声量TL=0。扩张室长度和峰值频率分别为由以上分析知:当扩张室长度是波长四分之一的奇数倍时,消声量取最大值;而当其是波长二分之一的整数倍时,消声量为0[3]。
当m 比较小时,消声量会非常小;随着m 增大,消声量会以和m值对数近似的量级有规律增大。随着扩张比增加,消声量也会增加。为实现低频消声量的增加,可通过提升扩张比的方式来实现。而很多在实际问题中,由于客观条件对其有限制作用,所以并不是越大的扩张比就越好。通常情况下,应该将扩张比控制在9<m<16 之间[16]。因为安装的空间有限,所以在对消声器进行优化之后,不应该改变其外形尺寸,扩张室的半径为R=80 mm,同时,由于消声器入口连接着发动机的排气管,所以应该保持其进口直径不变,r1 =25 mm,算得扩张比m=R2/r12 =10.24,符合要求。
长径比是消声器的长度与直径的比值。在不改变其长度的情况下,扩大消声器的长径比,就可以减小其扩张比,进而降低消声量。高频率消声器有着更差的效果,低频率的消声器效果会好些;反之
越小,低频消声效果差,但高频消声效果要好一些,因此长径比不宜过大也不宜过小。一般情况下,取L/D=1.5~8[17]。优化后消声器长度可适当增加,但由于安装空间的限制,不可增加过多,优化后消声器长L=370 mm,直径D=160 mm,长径比为2.312 5,达到要求。
消声器中的腔数也会影响到消声量,按照消声量所要达到的值,可以根据其腔数将其分成3大类。第一类消声量在10 dB(A)以上,此类消声器腔数通常为2个至3个;第二类消声量在15 dB(A)以上,此类消声器腔数通常为3个至4个;第三类消声量在20 dB(A)以上,此类消声器腔数通常为4个。出于实际消声量的考虑,最终决定采用4腔形式的消声器。
在消声器基本参数确定之后,就可以原来消声器进行优化处理,建立新消声器模型。图3为优化后的消声器。由于消声器安装空间的限制,消声器的总体外形尺寸保持不变。优化后的消声器与原消声器相比,总体尺寸没有太大变化,只在长度上将原第二腔拉长了10 mm,并用一块隔板将其分隔成两个腔室,成为了优化后消声器中的第二腔和第三腔,长度均为25 mm。另外两个腔,即第一腔与第四腔的长度与优化前的第一腔与第三腔长度一样,仍均为90 mm。
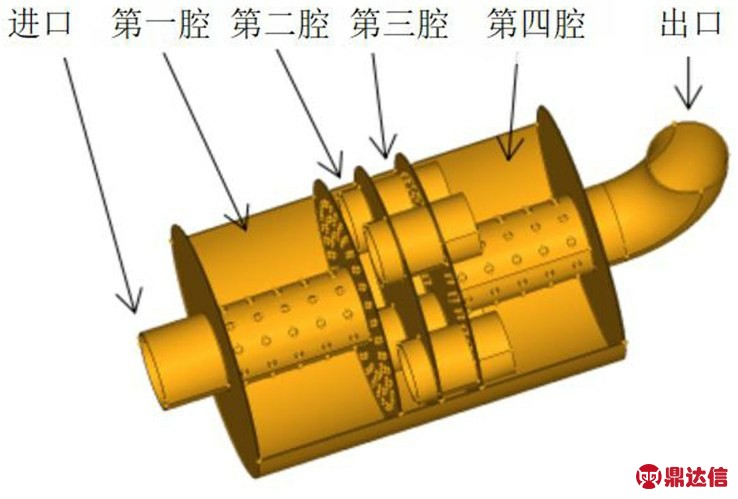
图3 优化后消声器模型
优化后的消声器进气管长131 mm,出气管长186 mm,进出口直径为50 mm,均与原消声器相同,且进出气管均为穿孔管,穿孔数为50,孔径均为5 mm。第一、二腔与第三、四腔之间均为穿孔板,穿孔的孔径同样均为5 mm,分别在距圆心45 mm、55 mm和65 mm处等间距分布,数量分别为24个、30个和36个。这些尺寸均与原消声器相同,并未改变。
为了保证消声器内部的流通性,优化后的消声器增加了4个均布的内插管,以连通第二腔与第四腔。出于加工难易程度的考量,内插管在通过穿孔板时,应尽可能不要干涉到已有的穿孔,同时也要保证一定的长径比和扩张比。因此在尺寸上,最终选择内插管的外径为40 mm,如图4所示。
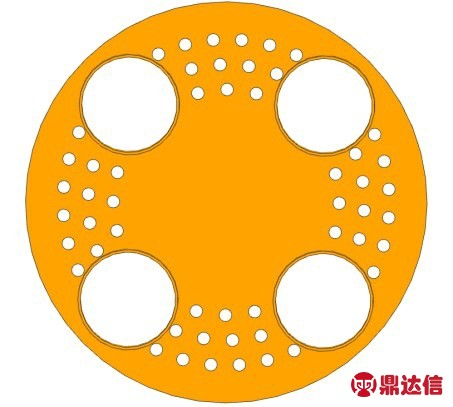
图4 内插管和穿孔板
文献[3]中,分别将进气管和排气管的长度设置为L/2 和L/4,并得到了较好的消声性能。本文尝试将这种方法应用在内插管上,即第二腔中的内插管长度为第二腔长度的1/2,也就是12.5 mm;第四腔中的内插管长度为第四腔长度的1/4,长度为22.5 mm。这样,加上第三腔的长度25 mm以及两块板的厚度1 mm,4个内插管的长度均为62 mm。
2.2 消声器流场分析
在对UG中建立好的消声器三维模型进行流体分析和声学分析之前,需要先进行网格划分,流体分析和声学分析采用同样的有限元模型。其中声学分析在LMS virtual.Lab中进行,此软件对声学网格长度单元的要求较为严格,声学网格单元应不大于最大波长的1/6,最大波长λ可以表示为

式(7)中:c为声速340 m/s,fmax为最大分析频率5 000 Hz。
声学网格则为

由于模型的尺寸总体较小,因此网格尺寸取为4 mm,以原消声器为例,在Hypermesh 中进行网格划分后的有限元模型如图5所示。
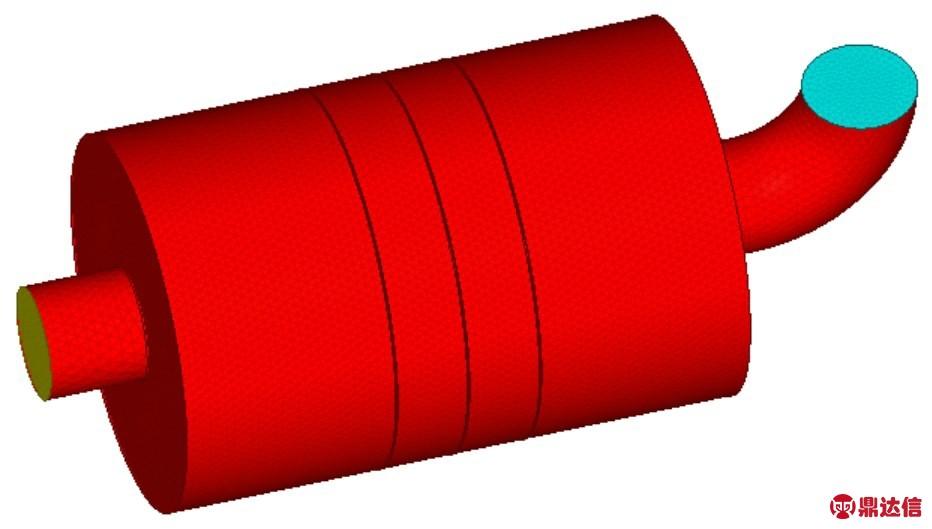
图5 原消声器网格划分
在Hypermesh中分别对优化前后的消声器进行网格划分,得到其流体网格,通过Fluent软件对消声器进行流场对比和分析[18]。首先将有限元模型导入Gambit 软件中,定义消声器的进出口边界以及壁面边界,将质量流量作为其进口位置的边界条件,设置进口质量流量为0.028 kg/s。进行台架试验得到消声器进口温度为575℃,因此将进口的温度设置为848 K,环境温度设置为300 K。将压力出口作为出口边界条件,和外界之间没有压力差。壁面材料是Q235,平均散热系数是11 333 W/(m2·K)。
压力场计算结果如图6所示。可知压力主要集中在进口管内,流体从进口管流入到腔体内以及从腔体内流出到出口管时,压力均有明显下降。原消声器内部的压力从第一腔到第三腔呈递减趋势,而因为有内插管的连通,新消声器第二、三、四3个腔室内的压力相差不大。
温度场计算结果如图7所示。可以看出:原消声器进口管内的温度最高,出口管内的温度最低,进口管内与第一腔内的温差很大;新消声器仍是进口管内温度最高,但最低温度出现在在第三腔,这主要是因为隔板的存在。
速度场及速度矢量的分布如图8所示。
可以看出:由于消声器壁面对高速气流的阻碍,进出口附近产生了涡流,这也是此处产生较大局部压力损失的原因。新消声器因为增加了隔板并有内插管连通,所以流体直接从第二腔室进入第四腔室,因此第三腔内流体的流速最低,这也解释了为什么第三腔内的温度最低[19]。
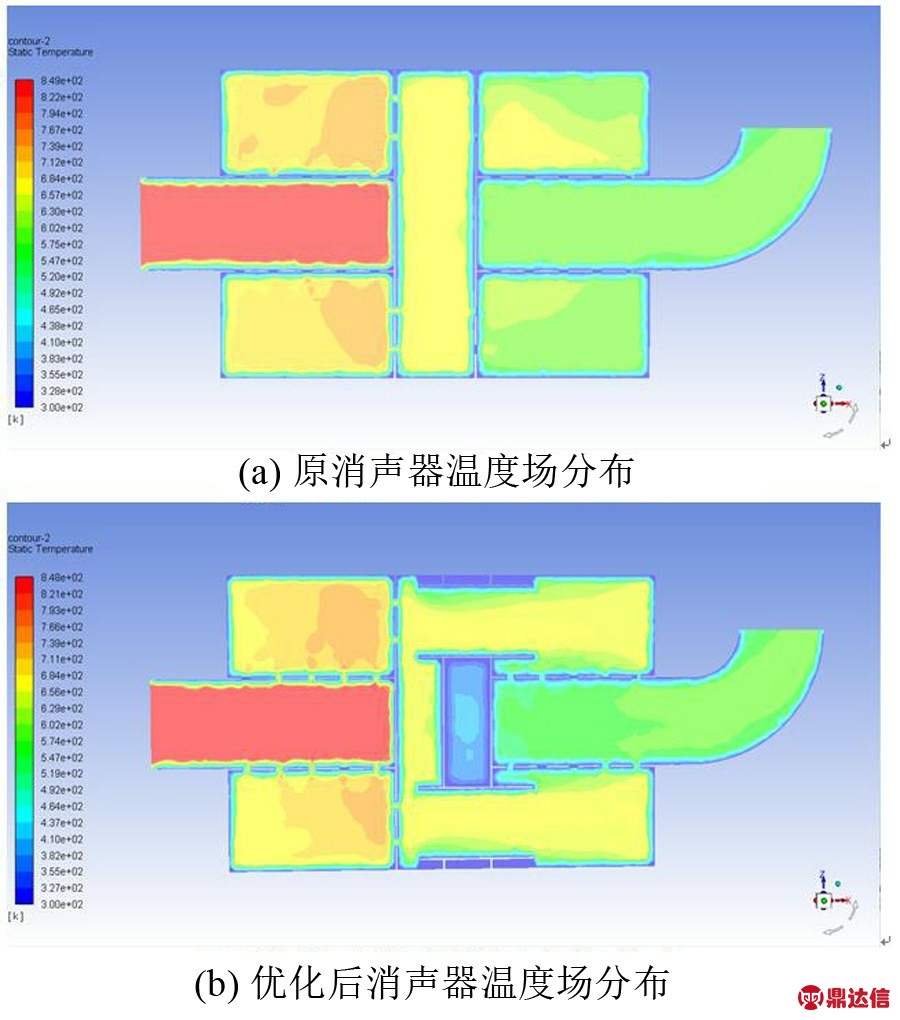
图6 压力场分布
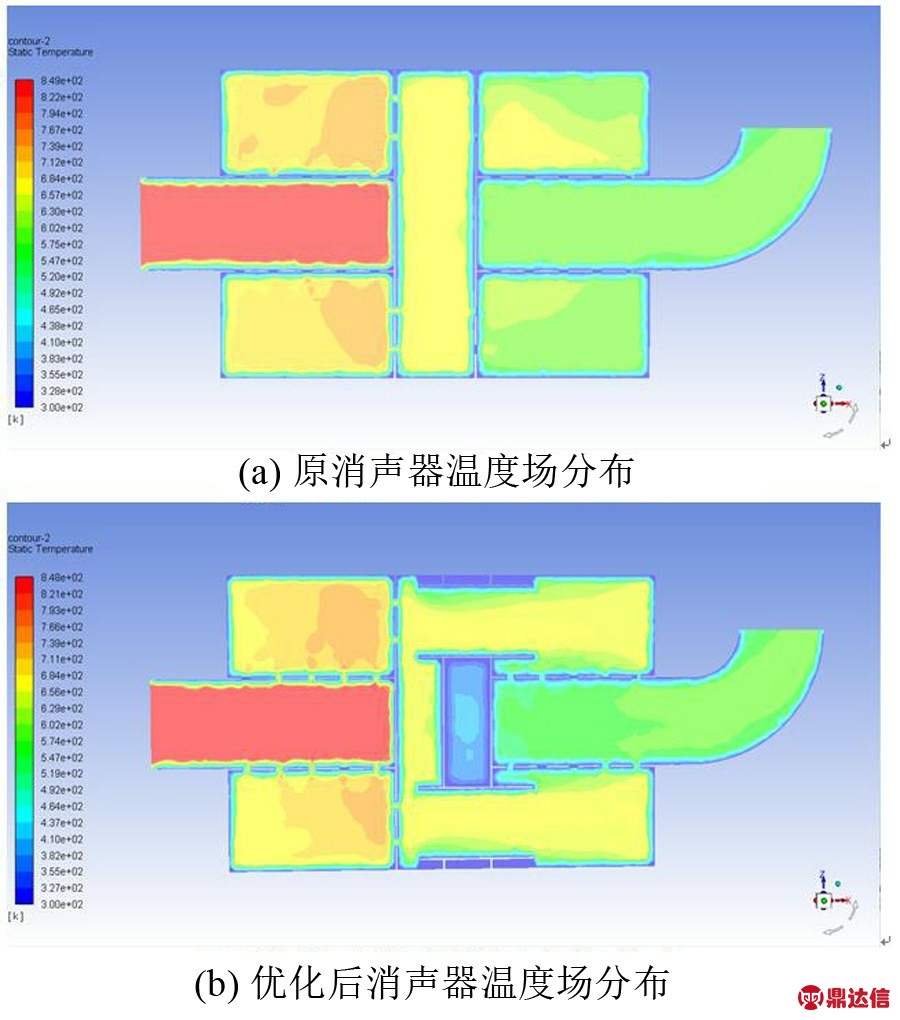
图7 温度场分布
排气消声器流体性能的计算结果如表1所示。原消声器压力损失为2 065.7 Pa,优化后消声器压力损失为1 815.2 Pa,优化后消声器压力损失比优化前低250.5 Pa,降低了12.12%;优化后消声器平均温度为433.6℃,比原消声器的438.9℃降低了5.3℃;优化前后消声器内流体的平均流速变化不大。
2.3 分析消声器所具备的声学性能
再一次利用LMS virtual.Lab 软件来对比和分析消声器在优化之前和优化之后的性能,然后将计算出的传递损失和消声器原来的传递损失进行对比,图9是其对比结果图。
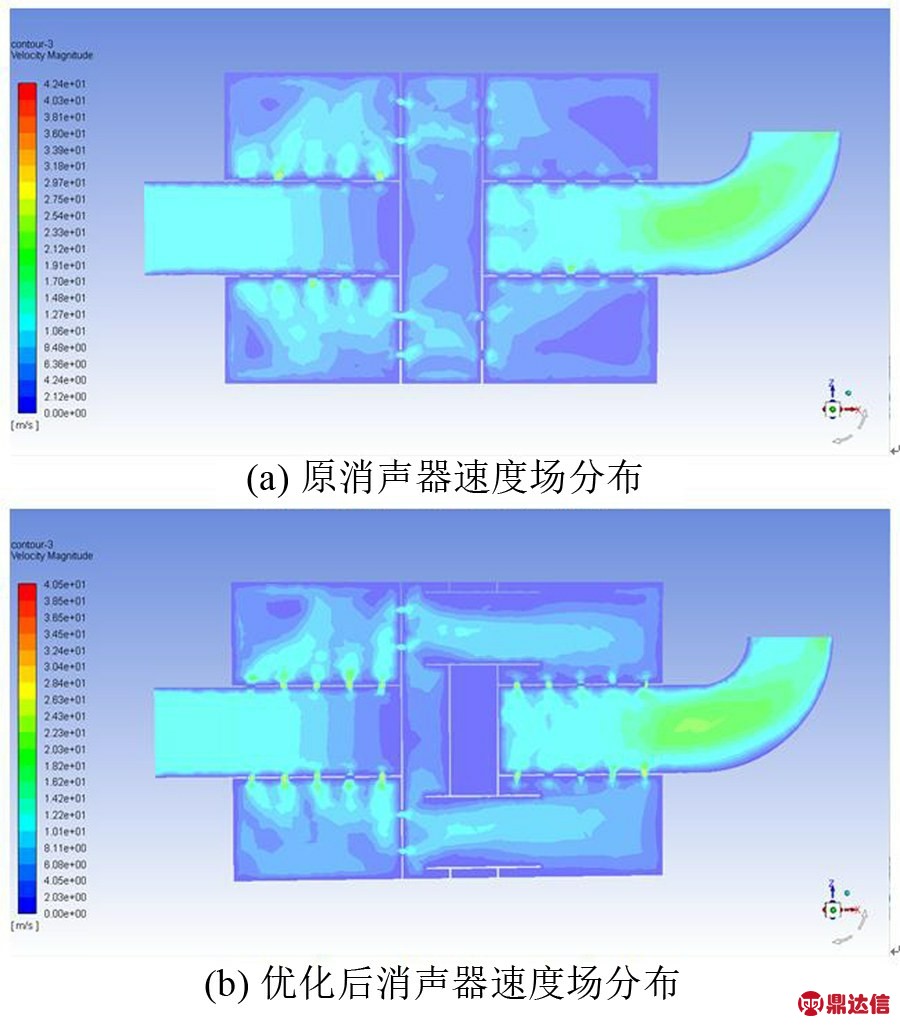
图8 速度场分布
表1 优化前后消声器流体性能对比
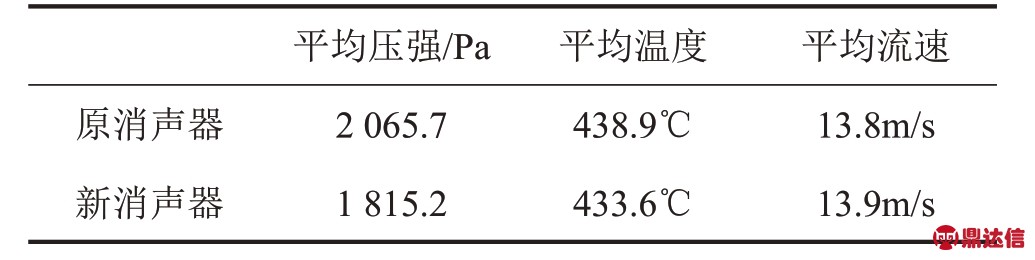
可以看出:在500 Hz~2 000 Hz范围内优化后消声器的传递损失大于原消声器,且其峰值将近66 dB;在3 000 Hz~5 000 Hz范围内也基本上大于原消声器,峰值高于89 dB。优化后消声器消声性能明显改善。
3 试验与验证
根据插入损失的定义,测定消声器插入损失时,在安装消声器前采用空管作实验,在给定测点上测出声压级,根据测点声压级求出声功率级,然后再在同等条件下测量安装消声器后同一测点处的声压级,同样再求出声功率级,由前后两次声功率级之差求出各频带的插入损失。在对消声器进行声学试验的过程中,可将试验设置在柴油机台架上,将LMS公司所生产的Test.Lab形式数据采集系统作为测试设备,将杭州爱华公司生产的AWA14423 声传感器作为声学传感器。
整个试验过程都应该按照JB/T 5081-2008《中小功率排气消声器》实施,测量噪声与背景噪声声压级之差应在10 dB以上,测点位置的风速最好不超过1 m/s。具体测点位置要求如图10所示。
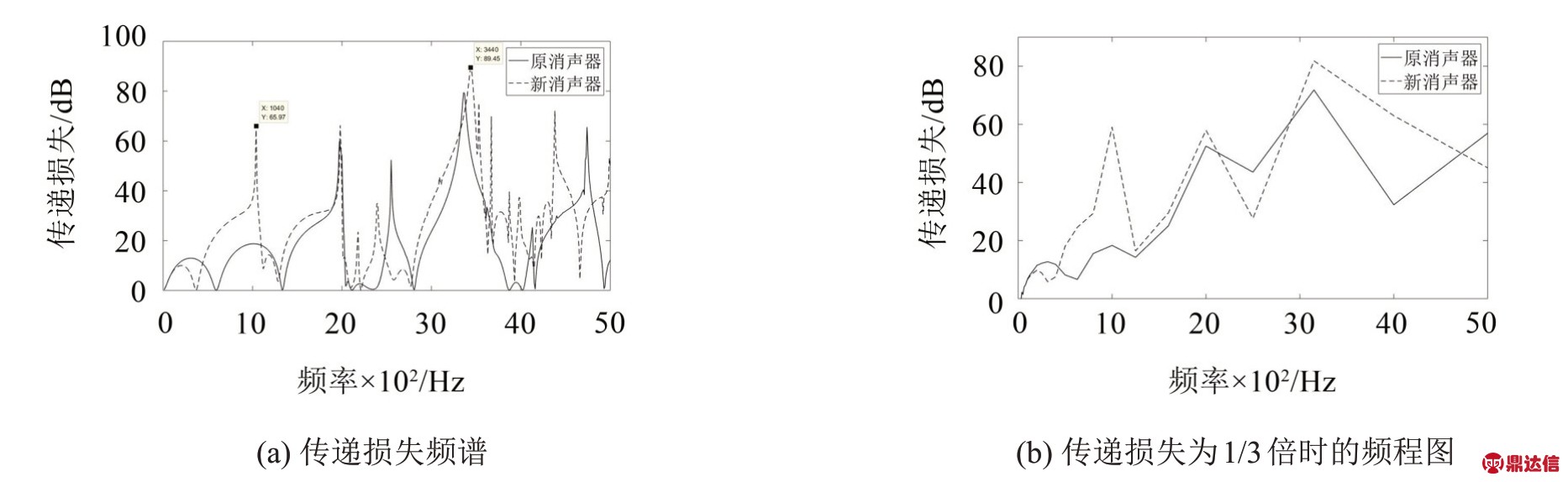
图9 消声器优化之前和优化之后传递损失对比

图10 排气消声器声学测试示意图
排气消声器声学测点布置如图11所示。在进行试验时,传声器与地面以及排气口之间的距离都是0.5 m,和排气孔气流轴向方向的角度是45°。具体的试验过程中环境噪声是68.05 dB(A),风速在1 m/s以下,和标准完全相符。
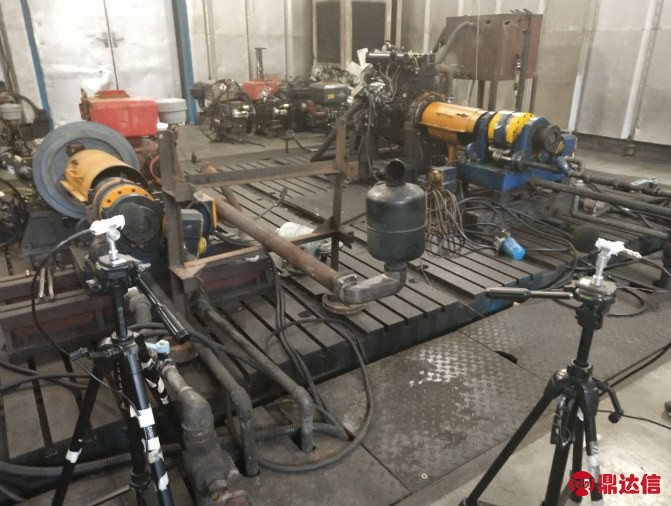
图11 排气消声器声学测点布置
试验在发动机空载怠速为800 r/min以及满载状态下进行,其中满载转速分别为1 600 r/min 和2 200 r/min。各消声器在测点位置声压级如表2所示。
对比安装前后以及优化前后消声器噪声可以发现,安装消声器后,排气噪声明显降低,尤其在1 600 r/min和2 200 r/min时,下降量分别达到19.39 dB(A)和18.41 dB(A)。优化后的消声器在原消声器基础之上在达到了更好的消声效果,在1 600 r/min时消声量达到了23.43 dB(A),比原消声器高出了4.04 dB(A);在2 200 r/min和怠速状态下也分别达到了22.03 dB(A)和2.85 dB(A),同样也比原消声器分别高出了3.62 dB(A)和1.7 dB(A)。
表2 优化前后消声器在测点位置的噪声/dB(A)
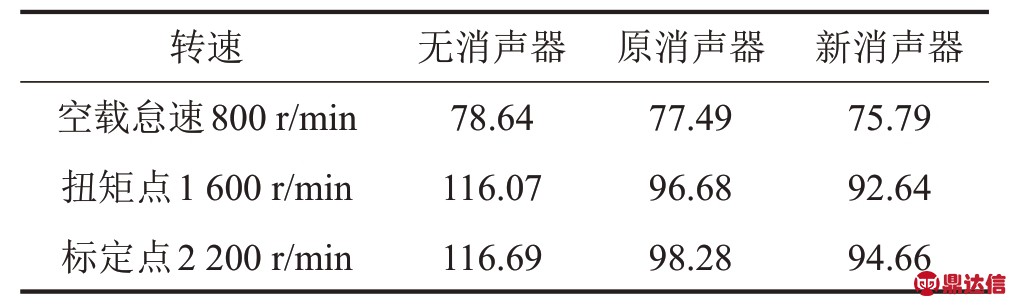
在未安装消声器、安装原消声器以及安装优化后的消声器时,柴油机的输出功率如表3所示,测试消声器性能指标的单缸柴油机,其额定转速为2 200 r/min,额定功率为16.6 kW。
表3 安装不同消声器后柴油机的输出功率/kW
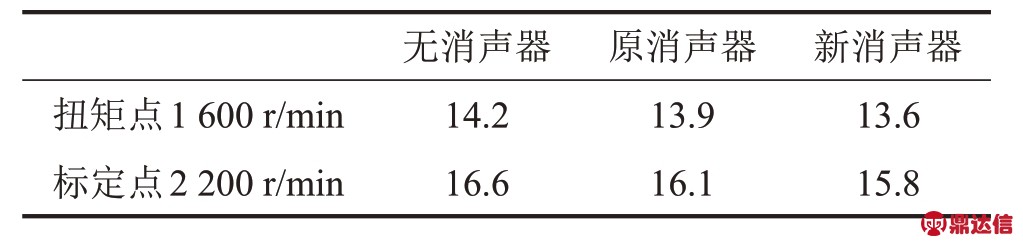
表4为《中华人民共和国汽车行业标准QC/T631-2009汽车排气消声器技术条件》中关于插入损失和功率损失比限制的规定,本文所研究的消声器适用于中型车,在功率点和扭矩点的消声量均达到了中型车要求的20 dB(A),满足要求。
根据式(4)计算优化前后消声器在扭矩点和标定点的功率损失,算得优化后消声器在扭矩点1 600 r/min处的功率损失为4.23%,比原消声器的2.11%高2.12%;优化后消声器在标定点2 200 r/min处的功率损失为4.82%,比原消声器的3.01%高1.81%。优化后消声器的功率损失在各转速工况下都比原消声器高,但都小于5%,满足要求。
表4 插入损失和功率损失比限值

由测量数据可得安装优化前后消声器时发动机频谱之间的对比结果,图12是其具体的对比情况。在测量过程中发现,主要的排气噪声能量都集中在了4 000 Hz 之内,所以本次研究中仅仅对这一范围内的排气噪声进行特性对比和分析。
根据对比分析可得,各消声器在各转速工况下在大部分频率段为均能有效降低排气噪声,尤其是低频噪声。优化后消声器在各频段频谱明显降低,降噪效果优于原消声器。
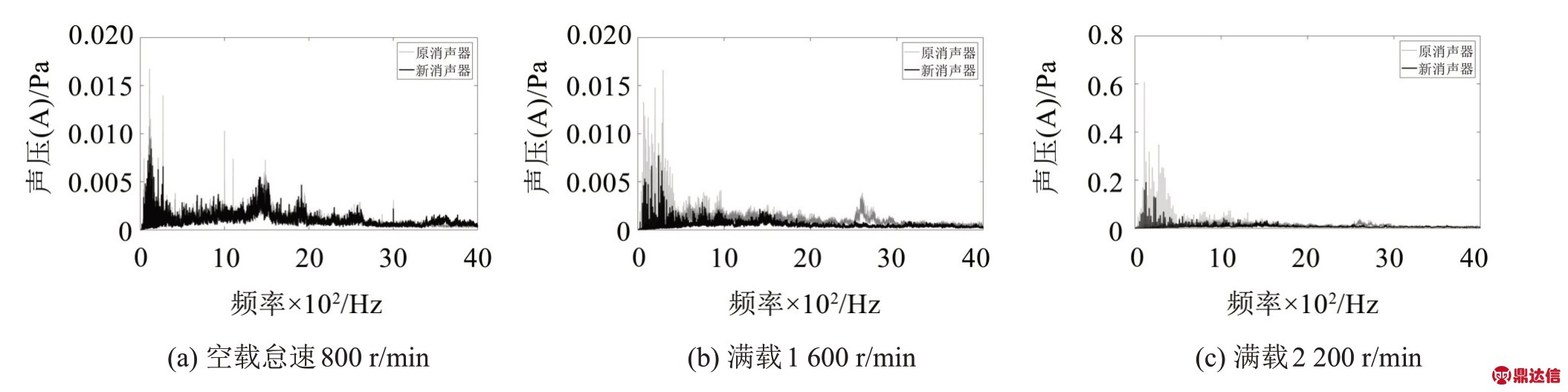
图12 发动机频谱对比
4 结语
(1)改变消声器结构及尺寸,用隔板增加消声器腔室的数目,并通过内插管确保其内部的连通性,可以有效降低排气噪声。
(2)优化后消声器的降噪能力在高频区和低频区均较优化前有所提高,其中,在3 500 Hz附近比优化前高出近10 dB(A);在1 000 Hz 附近比优化前高出47 dB(A)以上。优化后消声器在扭矩点(1 600 r/min)和功率点(2 200 r/min)的消声量分别比优化前提高了4.04 dB(A)和3.62 dB(A)。
(3) 优化后消声器的压力损失较优化前降低12.12%;其内部平均温度也比原消声器降低5.3°C。在扭矩点和功率点的功率损失比虽然较优化前有所增加,但都在柴油机功率损失比所要求的5%以内,说明消声器的优化方案有效。