文 摘 综述了金属材料损伤分析中常用的五类物理冶金分析技术:组织结构分析技术;物理性能分析技术;化学成分分析技术;残余应力分析技术及原位分析技术。基于各类分析技术在金属材料损伤分析中的应用展开了详细讨论,并详细对比分析了各类分析技术在损伤分析应用中的优势和局限性,同时针对损伤分析过程中各类分析技术的选择和使用提出了基本的思路。
关键词 物理冶金,材料损伤,微观组织,原位分析,残余应力
0 引言
在金属材料的损伤分析中,分析人员最广泛采用的分析技术即为物理冶金分析技术,该类分析技术可直接有效地给出材料的损伤行为、材料的组织结构特征参量和材料的工艺过程之间的紧密的关联性,同时,可用于对损伤机理进行解释,并对损伤的预防提供支撑[1-3]。通过合理选取不同的物理冶金分析技术手段,损伤分析人员可得到材料中不同组成相的晶体结构、形貌(尺寸、形状和空间分布等)以及成分信息,还可得到材料的物理性能以及应力状态等[4-7]。本文将损伤分析中常用的物理冶金分析技术分为五大类进行了综述,包括组织结构分析技术、物理性能分析技术、化学成分分析技术、残余应力分析技术以及原位分析技术。
1 组织结构分析技术
金属材料的损伤、断裂和失效的特征和模式与它的组织结构密不可分,金属在不同载荷作用下,当沿它的特定原子面的原子结合被破坏时,不同的损伤、断裂或失效就会发生,见图1。通常情况下,金属中的组织结构缺陷或不连续性在此过程中起着关键作用,这些缺陷通常被分为点缺陷、线缺陷、面缺陷和体缺陷。图2给出了金属晶体中常见的组织结构缺陷,如原子固溶(置换型和间隙型)、空位、孔洞(点缺陷)以及位错(线缺陷)等[图2(a)];另外,由于绝大多数工程金属材料由多个晶粒或多种物相组成,晶界、相界面或孪晶界等组织结构的不连续性(面缺陷)会不可避免地存在于材料中[图2(b)][8-9],因此它所具有的这种多晶体(多相)属性在此过程中所起的作用是不容忽视的,例如,在载荷作用下,会导致位错沿特定滑移面运动,并在金属材料中的晶界或相界处发生塞积,导致裂纹形核和扩展,如图3所示[8]。
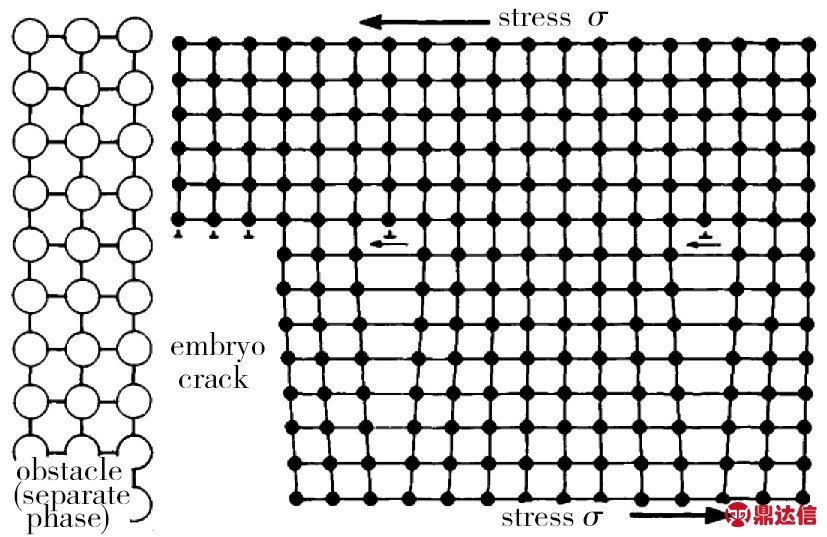
图1 载荷作用下的金属材料沿特定晶体学面开裂
Fig.1 Cracking along specific crystallographic plane in metallic materials subjected to load
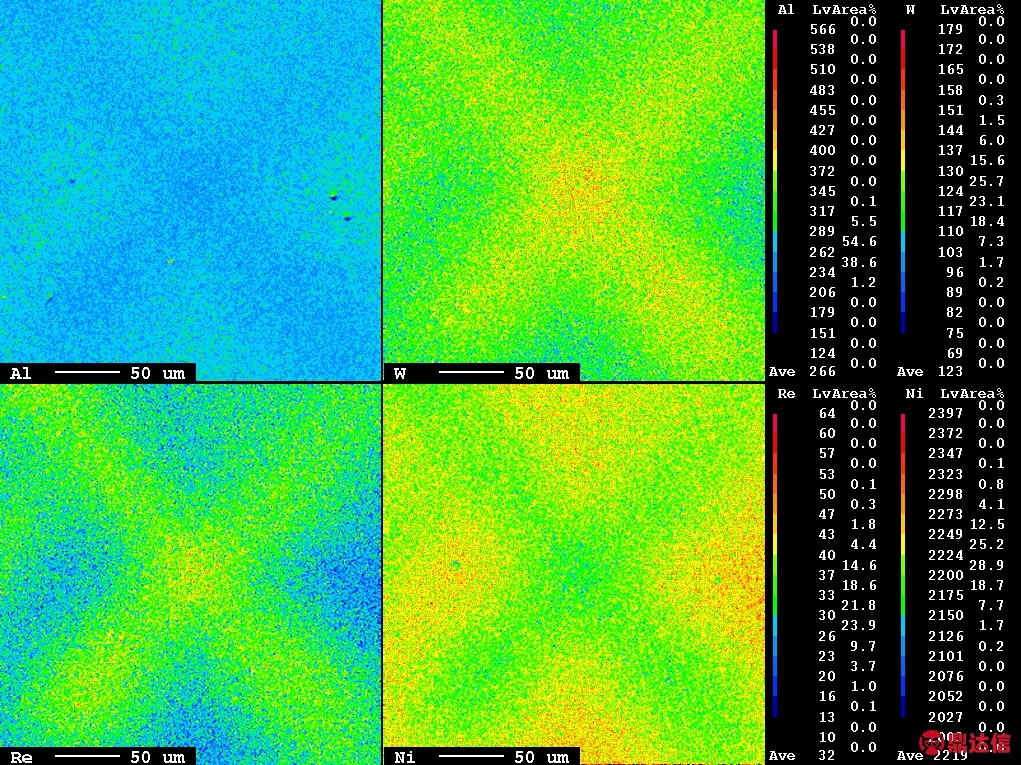
图2 金属材料中常见的组织结构缺陷
Fig.2 Microstructural defects in metallic materials
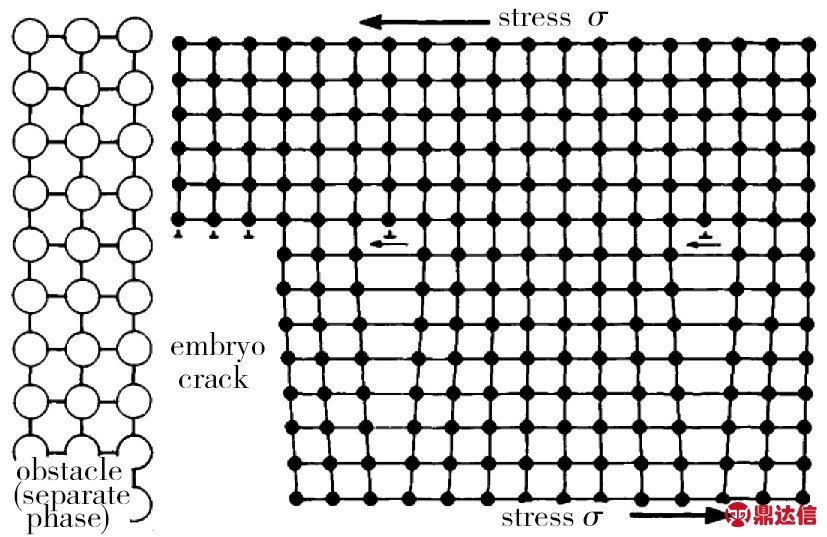
图3 载荷作用下发生位错运动,遇到障碍(第二相)时在相界处出现位错塞积,导致裂纹萌生
Fig.3 Dislocation motion under loadings leading to pile-up at phase boundaries and crack initiation
由此可见,只有对金属材料的组织结构特征进行深入分析,才能对材料的损伤过程有深层次的透彻的理解,进而才可全面掌握材料及构件的断裂和失效过程。这里将按照微观结构分析和组织形貌分析展开论述。
对于金属材料损伤过程的分析而言,常用的微观结构分析技术主要有透射电子显微术(TEM)、扫描隧道显微术(STM)和扫描透射电子显微术(STEM)等,这些技术手段已被广泛应用于金属材料在不同载荷条件下损伤过程的机理分析,如对损伤过程的结构特征和演变规律的分析等[10-17]。图4给出了一种镍基单晶高温合金在1 100 ℃、137 MPa下,经历了122 h 蠕变断裂后,在断口附近切取制备试样后的TEM 分析结果,图4(a)为TEM 明场像,观察方向为[001]方向,可以看出,在蠕变断裂过程中,位错在γ/γ'界面处塞积形成了明显的位错网,同时,通过高分辨TEM 图像分析γ/γ'界面结构特征[图4(b)],分析得出蠕变过程中位错网络与两种相的共格关系和晶格应变的协同作用特征[16]。利用STEM 分析手段可进行类似的损伤特征的分析[14-15],如图5所示,一种含Ru 镍基单晶高温合金在1 150 ℃、100 MPa 条件下,分别在蠕变第二阶段的前期[图5(a)]和后期[图5(b)]的STEM 图像,从图可见,在蠕变第二阶段的前期,大量的位错网络在γ/γ'界面处的基体γ 内沉积,而在γ'相内未发现位错;但是,在蠕变第二阶段的后期,有一些位错线出现在γ'相内,如图5(b)中箭头所示,作者由此认为,此时位错切入γ'相为主要的蠕变模式[15]。
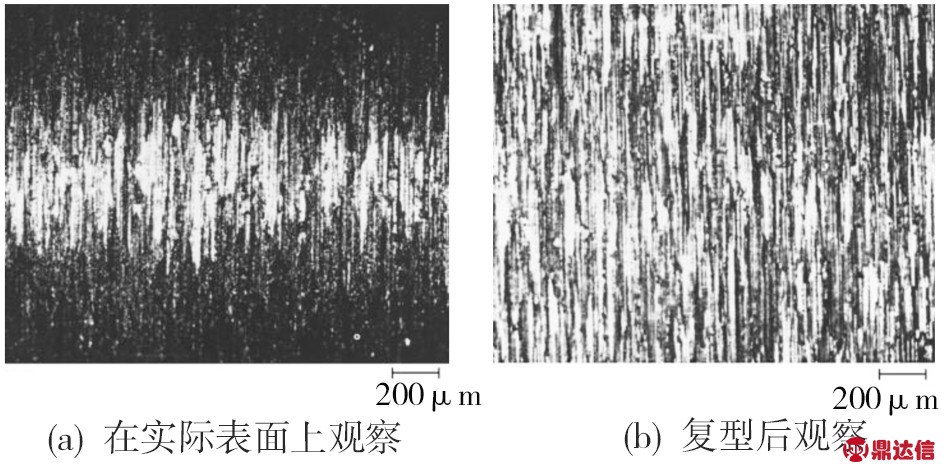
图4 一种镍基单晶高温合金在1 100 ℃/122 h蠕变断裂过程中,在γ/γ'界面处产生的位错网络
Fig.4 Dislocation network formed at the γ/γ'interface during creep of a nickel-based superalloy at 1 100 ℃for 122 h
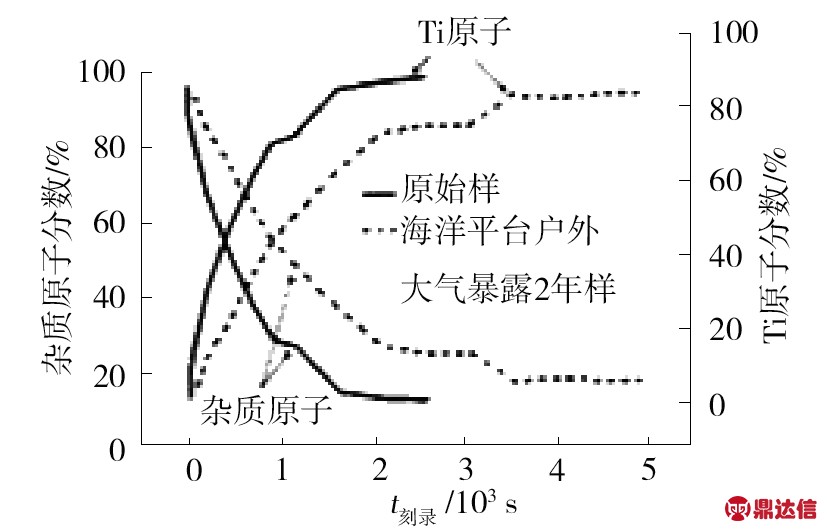
图5 一种含Ru镍基单晶高温合金在1 150 ℃、100 MPa条件下蠕变第二阶段的前期和后期的位错组态
Fig.5 Dislocation structure in the early phase and final phase of the second stage during creeping in a Ru-containing nickelbased superalloy at 1 150 ℃under 100 MPa
另外,在金属材料的损伤分析过程中,有时还需要利用其他结构分析技术来获取物相的晶体结构信息、晶粒取向和材料织构等方面的信息,来辅助分析和判断损伤的特征和机理,这时,一般采用的技术包括X射线衍射技术(XRD)和电子背散射技术(EBSD)等[11,18-20]。一种商业纯钛经如图6(a)所示的单向拉伸试验后,在10%的塑性应变时,试样表面产生大量垂直于拉伸应力方向的裂纹[图6(b)],经过EBSD进行晶粒取向分析后,作者将裂纹产生的位置(晶间或晶内)与晶粒取向和晶界角度关联了起来,从晶界结构的角度揭示了该类金属材料的损伤机理[21]。
如前所述,虽然目前比较常用的微观结构分析技术可以揭示金属材料损伤过程中的深层次的结构信息,更利于我们对材料的损伤特征和机理获得更多的理解,另外,随着相关技术的发展日益成熟,越来越多的相关设备和技术人员可供材料损伤分析人员使用。但是,此类分析需要分析人员具备很高的金属物理学和晶体学等方面的技术水平,这在一定程度上限制了相关技术手段的使用;相关分析样品的制备比较复杂,而且在样品制备过程中比较容易带来人为的假象,因此需要对样品的制备过程需严格控制,对于某些特殊的金属材料如金属基复合材料,往往需要使用聚焦离子束(FIB)等比较昂贵的手段制备试样;最后,由于所需的分析试样较小,一般为直径3 mm 的薄片甚至更小,这种情况下,所取试样对于所研究材料的代表性需要谨慎考虑。
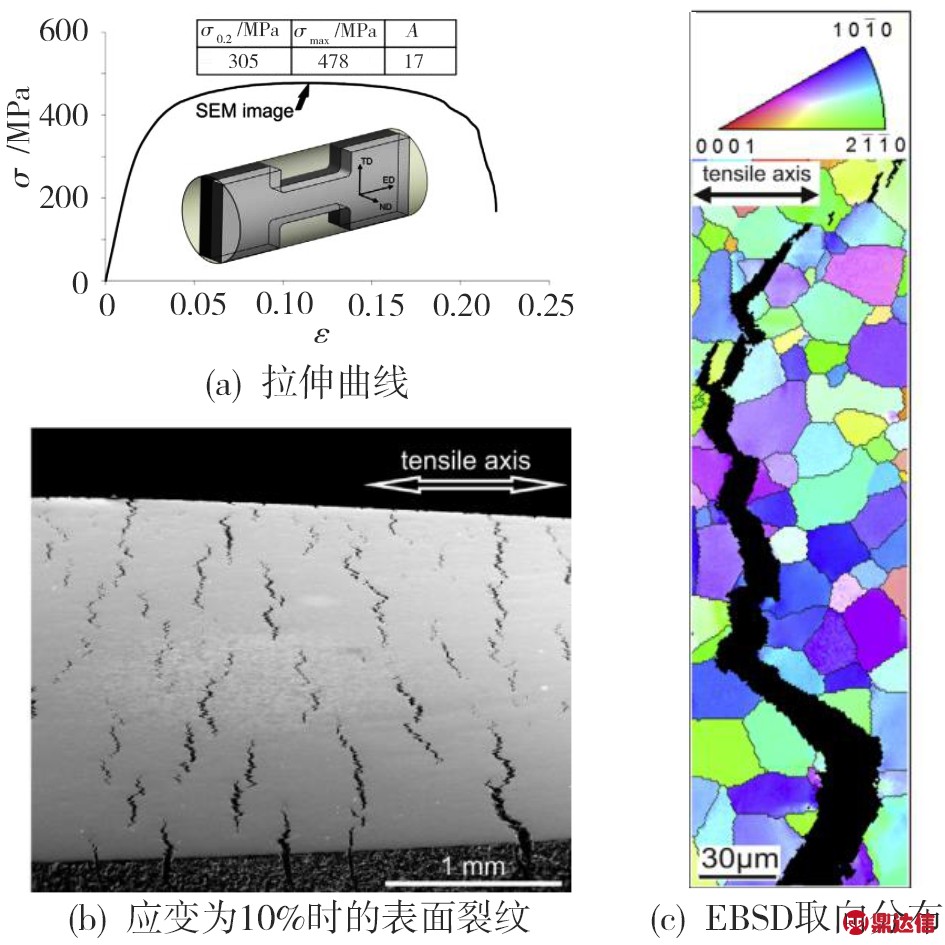
图6 一种商业纯钛单向拉伸损伤裂纹
Fig.6 Cracking in a commercially pure titanium under monotonic tension
与微观结构分析相比,组织形貌分析在工程应用方面显得更为直接和重要。根据分析的总体目的、要求和分析过程不同阶段的特点,可采用的分析技术手段的范围非常广泛,作者将根据自己的知识能力和工作经验,结合不同技术手段在金属材料损伤分析过程中的作用,讨论常用分析技术的特点和能力。
首先,现场金相技术经常用于对大构件的金相形貌进行现场分析,这种情况下,由于构件过大或者由于服役的要求,不能进行破坏后的实验室金相分析,所以,这类分析技术有时被称为无损金相技术或者原位金相技术。现场金相技术涉及多方面的工作,包括构件表面磨抛、金相腐蚀、观察和金相复型等,应根据分析的目的和要求做适当的取舍,其中,对需分析的区域进行复型后,需要在利用其他实验室分析技术对复型膜进行观察分析。需要的装置一般包括便携式磨抛工具、金相腐蚀工具、便携式金相显微镜和金相复型工具。该技术的优点在于它可以现场监测构件在整个服役期间的微观组织变化和损伤过程,同时,无论是针对平面还是曲面,精确合理的复型可以保证后续很高分辨率的微观组织分析;不足之处包括,该分析技术仅限于对表面特征的分析而无法获得内部的信息,复型技术仅能显示形貌信息而无法提供成分信息。作为损伤失效分析的一个重要技术手段,该技术已在全球范围内获得了广泛应用[1,22-25],有的国家已经发布了相关的检测标准供检测和分析技术人员参考和使用,如美国的ASTM E 1351(Standard Practice for Production and evaluation of Field metallographic Replicas)和德国的DIN 54-150(Nondestructive Testing Impression Methods for Surface Examination)。图7和图8给出了两个典型的现场金相分析技术的应用实例[22],一种在高温下使用的蒸汽钢管在使用一段时间后,发现在晶界处出现了蠕变空洞(图7),在利用现场金相技术及早检查发现这种损伤后,可以预防灾难性的失效破坏。在图8中,对一个轧辊的磨损表面进行分析,相比在实际表面上观察[图8(a)],通过表面复型技术显示出来的表面磨损痕迹更清晰[图8(b)]。
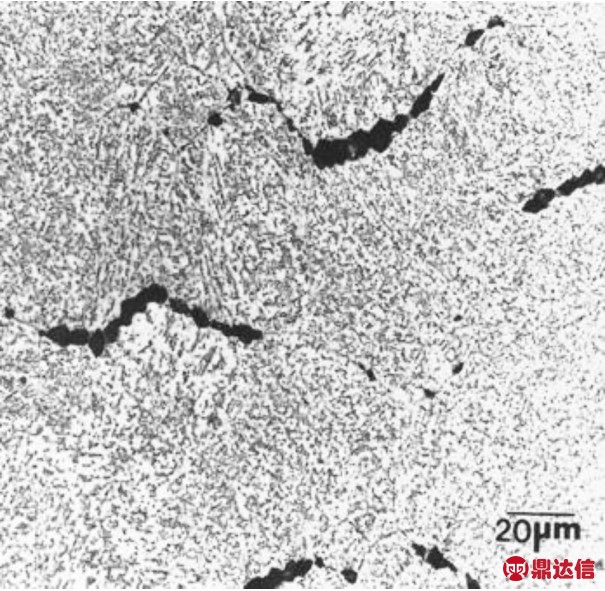
图7 蒸汽管线钢服役一段时间后出现晶界蠕变空洞
Fig.7 Creep voids at the grain boundaries in a steam pipe after service
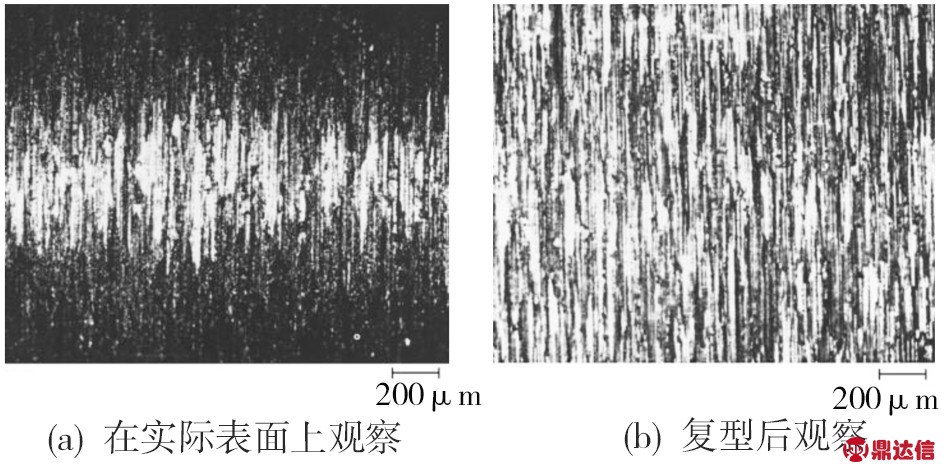
图8 某轧辊的表面磨损痕迹
Fig.8 Abrasion traces on the surface of a rolling rod
其次,光学金相技术(OM)在损伤分析是最有效的技术手段之一。首先,宏观照相术通常用来在1~50倍下,记录原始断口的信息,往往通过相机照相或者体式显微镜来实现,需要注意的是,在对断口进行下一步分析之前,应该记录尽可能全面的宏观特征信息,以备后续的综合分析。另外,光学金相分析技术是损伤失效分析中最常用的一种实验观测技术,目前已经发展得非常成熟,有各种各样配置的光学显微镜模式可供分析技术人员选择,包括明场模式、暗场模式、偏振光模式以及和其他样品制备技术结合起来,比如,与前面所述的复型技术或试样表面形膜/染色技术(即所谓的彩色金相技术)相结合进行组织分析。它能提供有关金属材料的基体组织、晶粒度、第二相等参数的定性或定量的观测结果,也能提供关于各种材料缺陷的信息。图9给出了经蠕变实验后的Ti-6Al-4V 合金的偏振光金相组织[22],该金相试样表面进行了染色处理,图中清晰地显示出了晶界处的蠕变裂纹。虽然光学金相分析技术在损伤失效相关的组织分析中占有重要地位,是一种普遍采用、不可缺少的实验观测方法,但它也存在一些局限性。这些局限性,主要同金相显微镜的景深小、分辨率不太高等特点有关,有时需要借助电子显微分析技术进行进一步判断。此外,光学显微镜不能用于断口观察,因此在损伤分析中,应该尽可能地把光学金相分析技术同其他实验观测技术结合起来,使各种实验方法相辅相成、扬长避短。
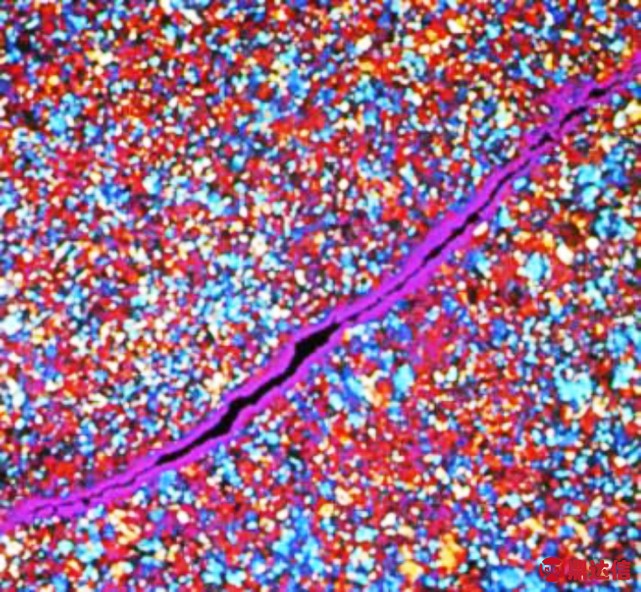
图9 Ti-6Al-4V合金经蠕变试验后的晶间裂纹
Fig.9 Grain boundary crack in a Ti-6Al-4V alloy after creep test
电子显微技术也被广泛应用于材料损伤和失效分析的表面形貌分析中,最常用的包括扫描电子显微术(SEM)和透射电子显微术(TEM)。在扫描电子显微术出现以前,TEM 就已经被应用于断口表面的分析,这方面需要与断口的表面复型相结合,复型膜会由断口表面的不同特征带来厚度的变化,当TEM的电子束穿透复型膜时,会因复型膜厚度的差异显示不同的衬度,从而对应显示出断口表面的不同特征。图10是用TEM 观察一种马氏体时效钢断口的复型膜的结果,图中可观察到明显的晶界析出物的形貌特征。然而,由于利用TEM 进行断口形貌分析时,需要进行断口复型,给分析工作带来了诸多不便,相比之下,扫描电镜的试样制备简单,有的试样可以不经制作直接放入电镜内观察。因而,更接近物质的自然状态,并能迅速地得到结果。而且,随着SEM 分辨率水平的不断提高,SEM 逐渐成为应用最广泛的断裂损伤分析手段,而TEM 只在要求极高分辨率时(优于1 nm)才使用,如在进行极细的疲劳条带分析时。图11为一种镍基沉淀硬化合金沿晶断裂后的断口形貌,图中对SEM形貌像与OM形貌像进行了对比。与光学金相技术相比,电子显微分析技术景深大,放大倍数范围宽,对粗糙的表面,例如凹凸不平的金属断口显示得很清楚,立体感很强[26]。另外,电子显微镜可以和能量/波长色散谱仪(EDS/WDS)等联用,进行化学成分分析,使得这种分析手段更加强大。
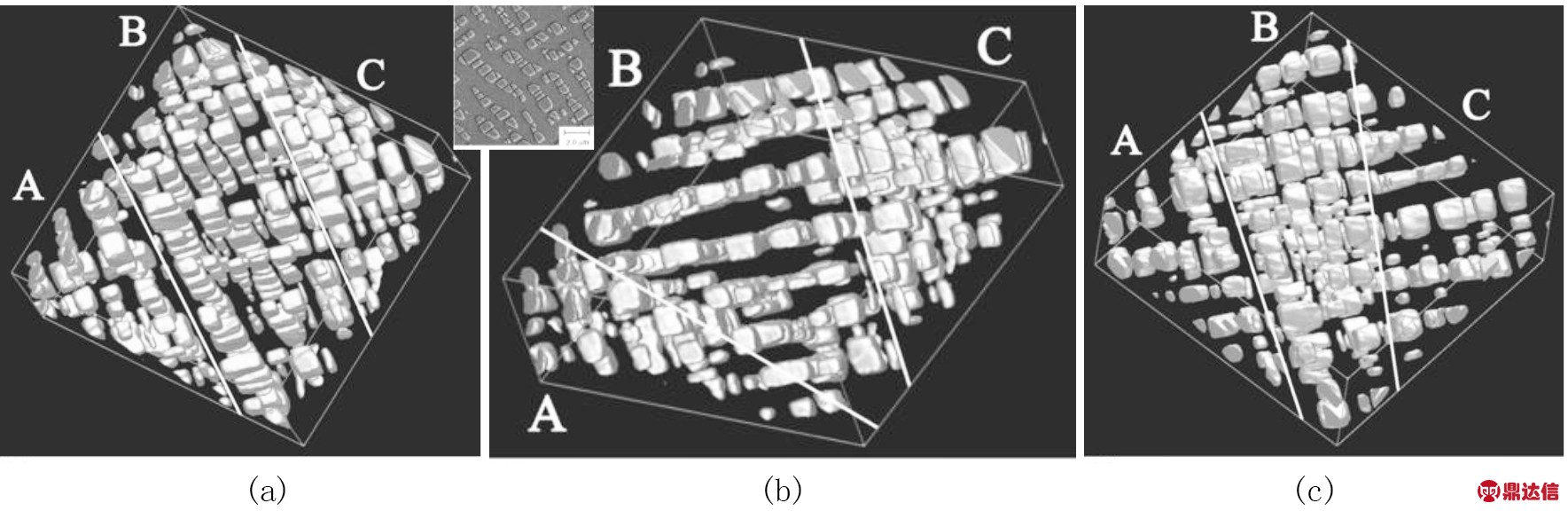
图10 TEM观察一种马氏体时效钢断口形貌
Fig.10 Fracture morphology of a martensite aged steel observed by TEM
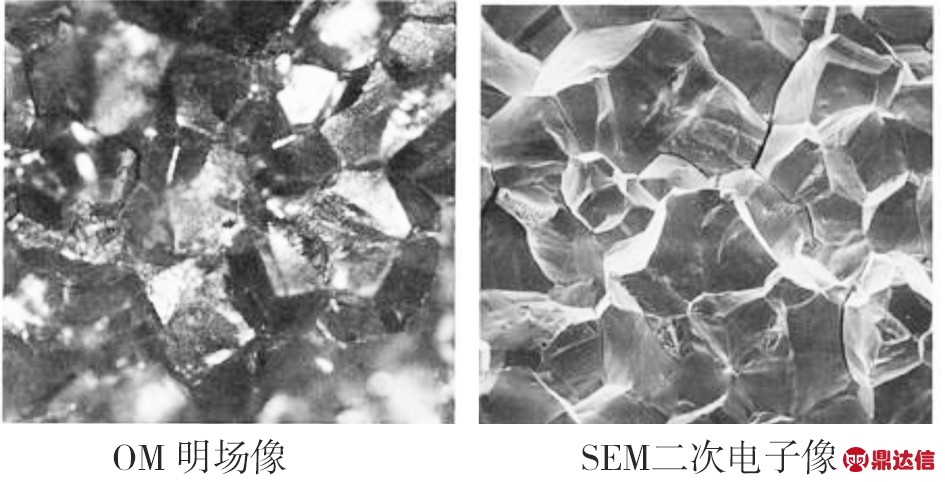
图11 一种镍基沉淀硬化合金的沿晶断裂特征
Fig.11 Intergranular fracture of a nickel-based precipitate hardening alloy
定量分析技术用于对组织形貌参量的定量描述,被广泛应用于材料质量控制、性能评价和服役评估,就材料损伤而言,常用的分析技术包括定量金相技术(定量显微分析术)和断口定量分析技术。
(1)利用定量金相技术可获得晶粒、空洞、析出相等的尺寸、含量及数量,以及材料的梯度结构的厚度或深度,如脱碳层、渗层、热处理硬化层、表面污染层和涂层等,基于如前所述的对材料微观组织形貌的分析,针对需要分析的组织形貌参量进行定量分析,这方面,为了保证分析结果的可靠性,大量的分析方法已被标准化,比如,ASTM E112、ASTM E 930和GB/T 6394 等规定了金属晶粒尺寸的测量方法,ISO 4967 和GB/T 10561 规定了钢中非金属夹杂物含量的测定方法,SAE AMS 4928 规定了钛合金表面污染层厚度的测量方法,另外,随着计算机水平的不断提高,图像分析方法也已经被广泛应用于微观组织形貌的定量分析,这种方法利用不同的算法和图像软件处理方法,对所需分析的微观组织形貌特征突出显示出来,从而对其进行定量分析,如ASTM E 1245 和ASTM E 1122 等规定了利用图像分析技术进行金属中夹杂物和第二相含量的测定方法,ASTM E 1382 规定了金属平均晶粒度的图像分析测定方法。这里仅列举了一小部分的标准测量方法,分析人员应根据具体分析的思路和要求,检索和利用相关的标准方法进行相应的分析和测量,图12和图13分别给出了钛合金表面α层和晶粒度分析的例子。
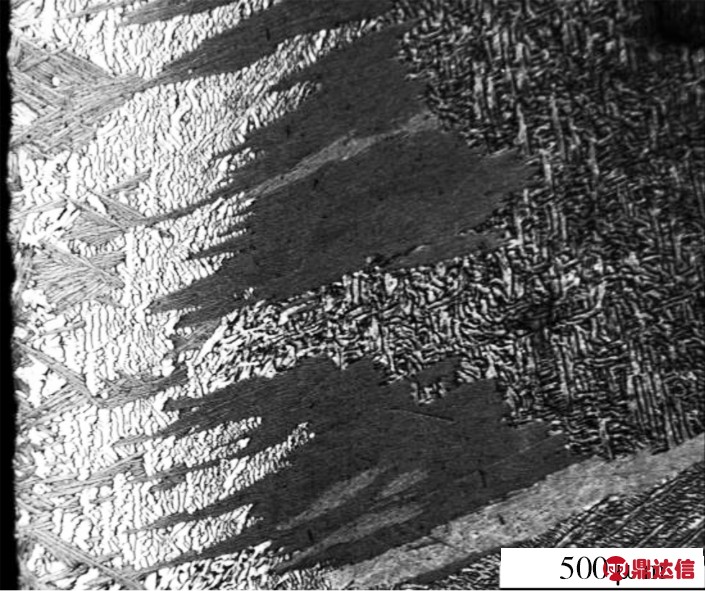
图12 钛合金表面富氧α层
Fig.12 The α case at the surface of a titanium alloy
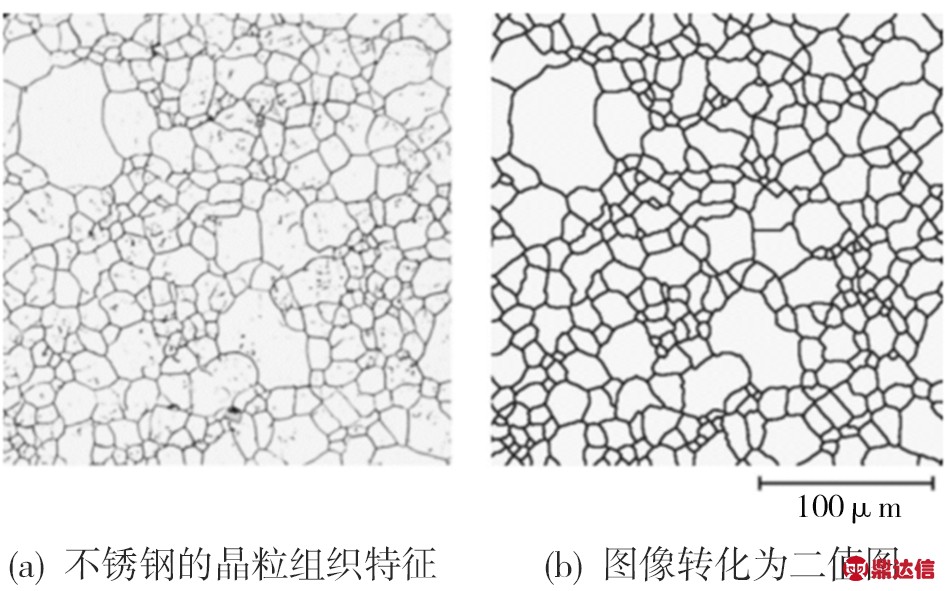
图13 一种奥氏体不锈钢的晶粒组织特征,经图像分析方法处理后(二值化),图像转化为二值图,突出显示晶界特征[22]
Fig.13 Grain structure of a austenite stainless steel(left),processed using image analysis method to obtain a binary image(right),are clearly revealed grain boundaries
(2)断口定量分析技术用于定量表述断口表面的特征信息,如面积、长度、尺寸、间距、取向和位置及其分布特征等,如疲劳条带间距、韧窝面积和体积等。定量分析一般基于断口表面的投影图像(如SEM图像等)、体式学方法和轮廓法。
最后,三维表征技术在很多情况下也被金属材料损伤分析人员所采用,该技术用于显示材料内部的三维组织特征,如形状、分布及各种特征的相互关联性等,如相组成、晶体(晶粒)取向、化学成分以及裂纹分布等,可以给出大量二维平面成像方法无法显示的特征,为材料损伤和失效分析带来更全面真实的信息。常用的手段包括:
(1)逐层切片方法,通过机械抛光或聚焦离子束(FIB),逐层去除材料并对应逐层成像显示所分析的特征(利用OM 或SEM 等),然后将所有成像切片重构,形成三维图像,显示所分析对象的三维特征,这种方法会对分析样品造成损伤[27-29],图14(a)~(c)为一种镍基高温合金中γ'析出相的三维重构图像,从不同视角显示了γ'析出相的分布、形貌和方向特征,其中,基体设置为透明,析出相为金属色,图像显示出了大量的二维图像不能显示的材料内部的固有特征(图14中的嵌入图片);
(2)X射线断层成像法,利用X射线穿透样品,逐层扫描成像后,重构形成三维图像,显示分析对象的特征,对分析样品不会造成损伤,特别适用于材料损伤过程的分析,如图15,利用同步辐射X 射线断层成像技术,分析了一种SiC 纤维增强钛基复合材料经受不同阶段的疲劳加载(FS1-FS7)后的裂纹扩展特征,其中的突出显示为裂纹,材料被透明化,小洞为裂纹绕过纤维扩展的区域[30]。
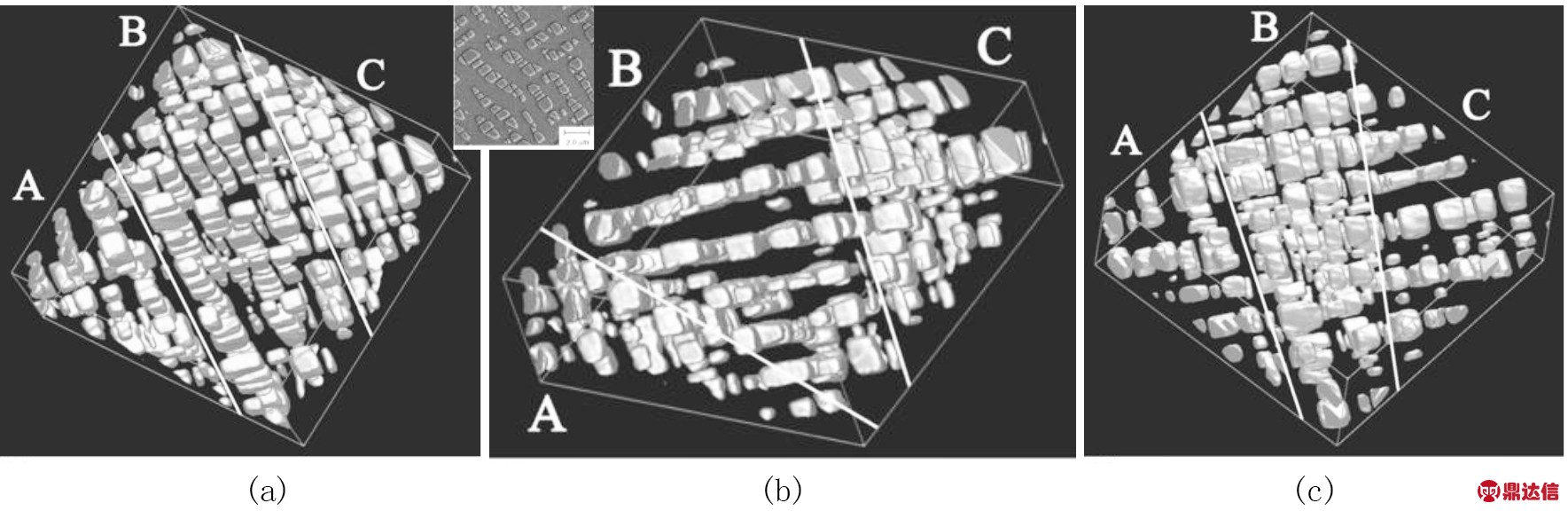
图14 一种镍基高温合金中γ'析出相的三维重构特征
Fig.14 Reconstructed 3D morphology of the γ'precipitates in a nickel-based superalloy
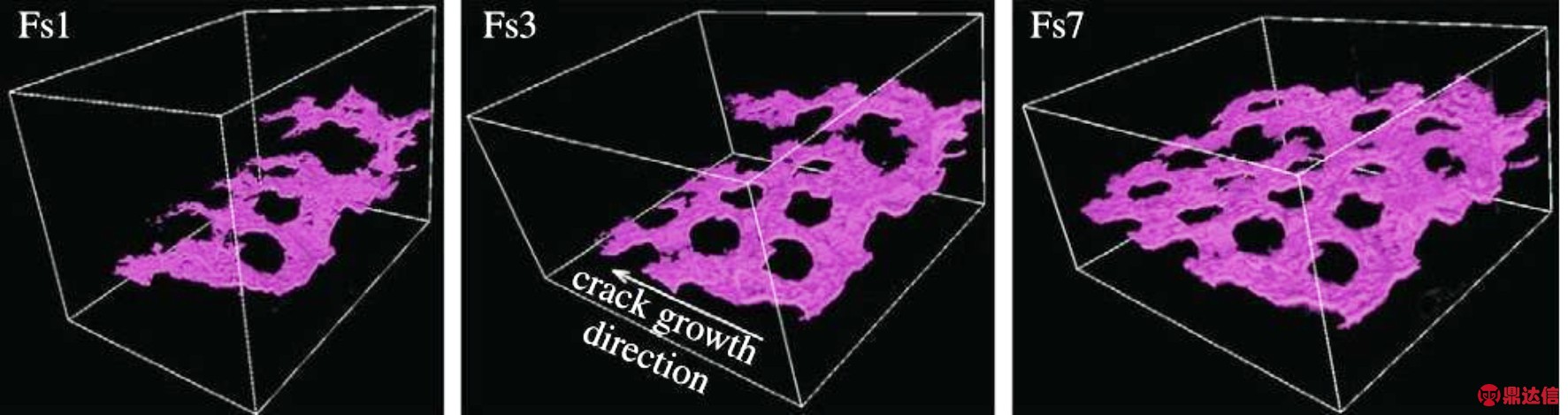
图15 一种SiC纤维增强钛基复合材料在不同疲劳加载阶段(FS1-FS7)的裂纹扩展特征
Fig.15 Growth of a crack in a SiC fiber reinforced titanium matrix composite under progressive cyclic loadings(FS1-FS7)
2 物理性能分析技术
金属材料在制造和服役过程中,不同的外界能量必然会施加于它,这些能量会来自于外力场、电磁辐射或高能粒子等,材料与之交互作用并产生不同的响应特征,这些响应特征称之为材料的物理性能,它们是进行材料损伤分析的必要基础,因此,选用适用的分析技术手段对其进行分析在很多情况下显得尤为重要[31]。
2.1 密度分析
金属材料的密度取决于原子的质量、尺寸及其排列方式,当金属被合金化后,由于元素的固溶和第二相的析出等,其密度会发生不同程度的变化,一般采用浸入法和X 射线法进行分析,浸入法是通过测量金属材料的质量和其体积而得到其密度的方法,而X 射线法通过测量材料的晶格参数,结合晶格类型,计算出单胞的体积和单位体积内晶胞的个数,并结合原子质量计算出单位体积内晶胞的总质量,从而得出材料的密度。材料密度是工程设计选材时必须考虑的因素之一,如图16为一种“材料性能图表”[9],用于工程设计选材时的参考之用。
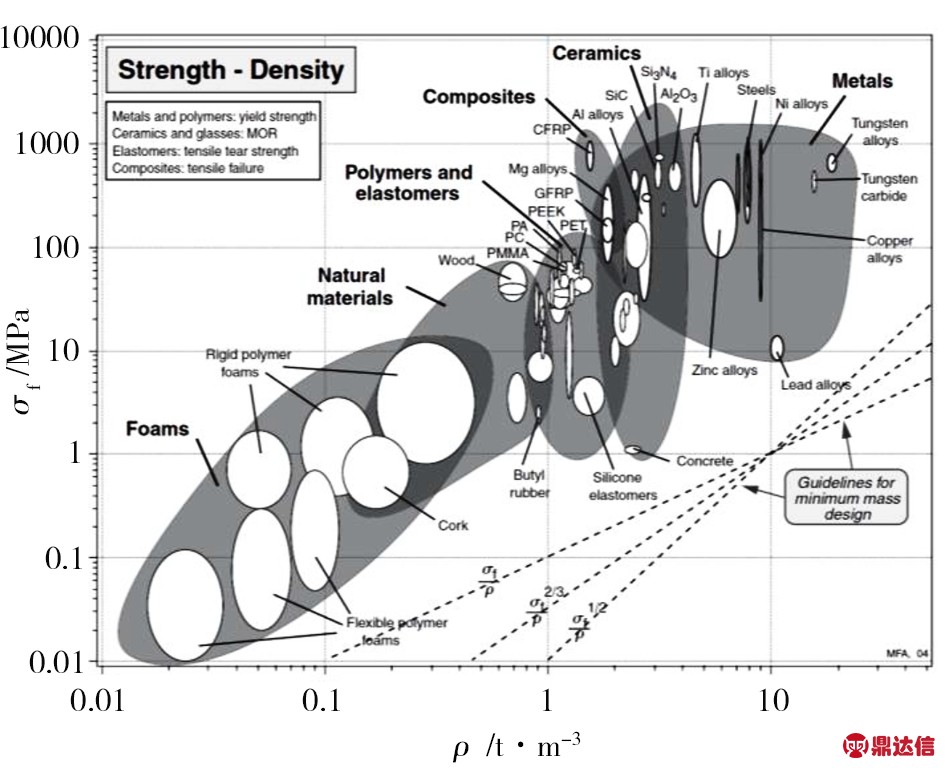
图16 材料设计强度与其密度的关系图
Fig.16 Relationship between the nominal strength and density of materials
2.2 热性能分析
通常是指对热膨胀性能(热膨胀系数、热导率等)进行分析,该系数与构件尺寸稳定性及不同构件之间的尺寸匹配性相关,在材料或构件的设计、生产制造和服役过程中,必须充分考虑其带来的影响。均可以利用专用仪器进行分析和测量。
2.3 扩散过程分析
扩散过程分析是理解金属材料在高温下的行为特征的必要条件,特别在材料制备、热处理、表面改性、氧化和蠕变过程中[32]。均匀金属材料的自扩散过程中,其扩散过程可采用放射性示踪法进行分析,对于异质材料,一般可采用化学分析方法,在金属材料中不同组成物质(组成相)的界面处元素的分布特征进行分析,结合菲克定律,可得出不同扩散过程的扩散系数[33-34]。图17为一种SiC 纤维增强的钛基复合材料中带碳涂层的SiC/基体界面的元素扩散特征。
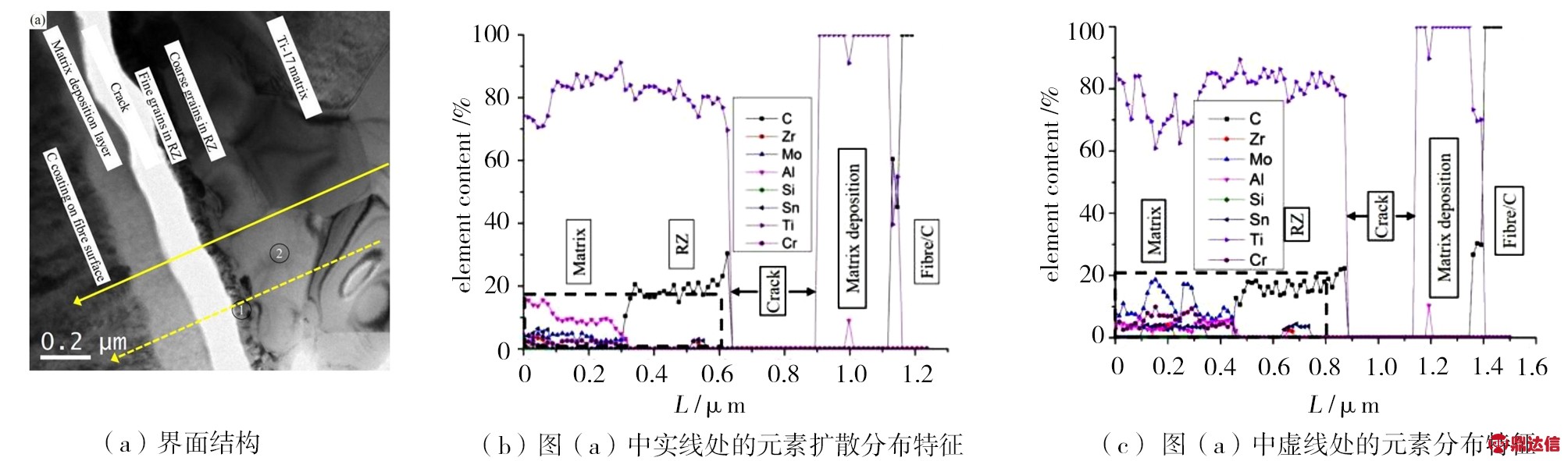
图17 一种SiC纤维增强钛基复合材料中带碳涂层的SiC/基体界面处的元素扩散特征
Fig17 Atom diffusion at the SiC/matrix interface in a carbon coated SiC fiber reinforced titanium matrix composite
2.4 相转变温度分析
一般包括对金属材料液相线温度(熔点)、固相线温度(初熔点)以及各种组成相的形成(析出/回溶)温度的分析。基本的分析方法包括差热分析(DTA)和差示扫描量热法(DSC),都是通过测量材料在加热或冷却过程中能量变化与温度的关系曲线图,在材料内部发生相转变时出现剧烈的能量变化(放热或吸热)而形成能量变化峰值,该峰值的位置即为相转变温度见图18。
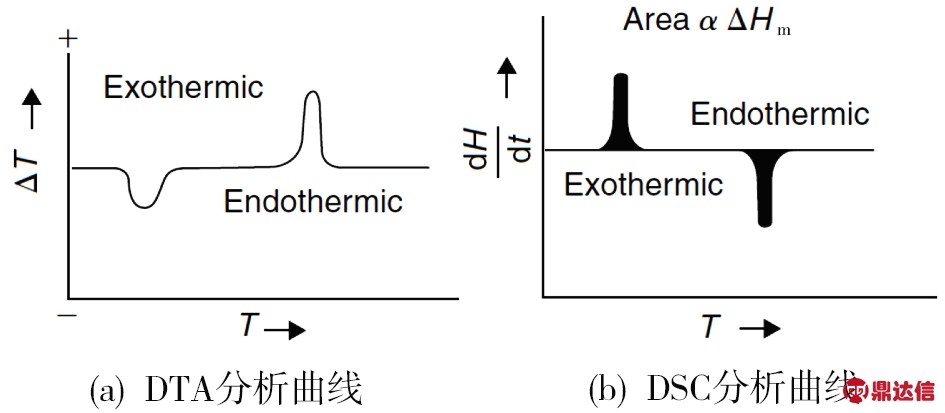
图18 差热分析(DTA)和差示扫描量热法(DSC)分析示意图
Fig.18 Schematic explanation of DTA curve and DSC curve
但是,这些方法受对能量变化探测灵敏度的限制,只有当能量变化足够大时,在曲线图上才会表现出明显的能量变化峰,因此,有时候并不能准确捕捉到相转变温度,尤其对某些含量较低的析出相,往往会埋没在曲线中。
为弥补这方面不足,可以采用等温相变淬火金相法,准确测量各类相转变温度,即使是含量非常低的析出相也可被识别出来,这种方法通过将材料在保护气氛中、恒定同温度下保温足够长的时间后淬火,磨制金相样品后观察和识别其金相组织,根据组织变化,可准确锁定某种相刚开始出现时的温度作为该相的转变温度[35-36],但与前面所述的两种方法相比,这种方法需要大量的等温淬火实验和金相试样制备与分析,比较耗时耗力。如图19所示,一种镍基高温合金的相转变温度的分析,利用等温相变淬火金相法获得的不同等温温度时的金相组织,可准确得出各种组成相的转变温度[36]。应用这类分析技术,可将金属材料或构件在高温服役时发生的相转变特征和实际服役温度关联起来,为材料或构件的超温损伤或失效的分析、评判和预防提供可靠的依据。
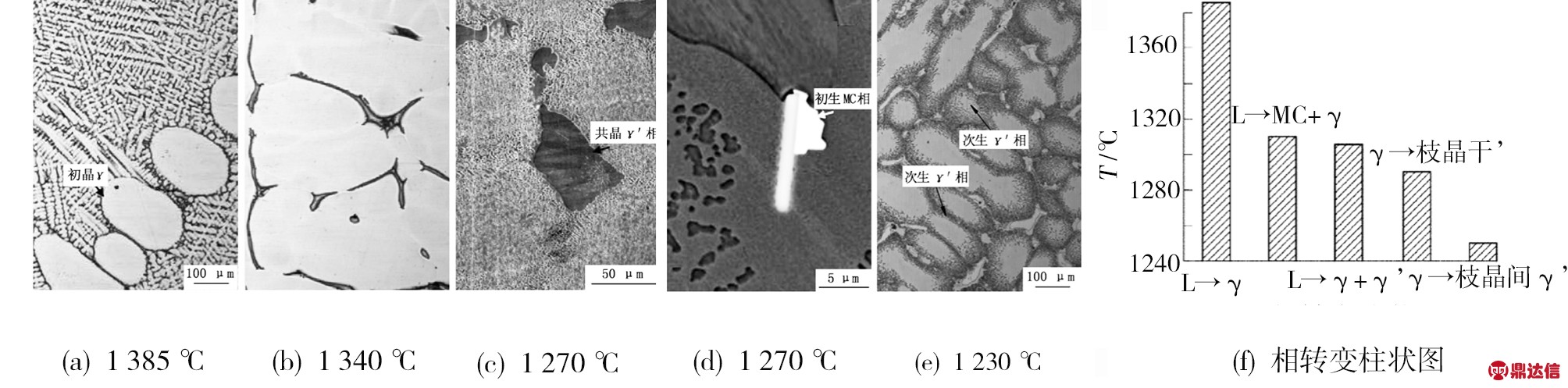
图19 一种镍基高温合金不同温度等温相变后的金相组织和相转变温度柱状图
Fig.19 metallographic morphology of a nickel based superalloy isothermally solidified at various temperatures(a-e),and a summary of phase transformation temperatures(bottom right)
3 化学成分分析技术
在材料的损伤分析中,常常需要对材料成分、外来物(如溅射附着物)、表面沉积物、腐蚀产物及氧化物等进行定性或定量分析,以便为最终的失效分析结论提供依据。金属材料的化学成分分析技术包括常规分析技术、表面及微区分析技术[7,37]。
3.1 常规化学分析技术
化学分析技术方法主要用于分析失效零件名义或宏观区域的材料成分,其主要方法有:
(1)湿法化学分析可准确分析含量较大的金属、阴离子的有无及其浓度;
(2)半定量发射光谱和原子吸收光谱用于分析合金成分;
(3)燃烧法用于测定金属中的碳、硫、氢、氮、氧的含量;
(4)点滴法可简单地定性分析金属中的合金元素、沉淀物、腐蚀产物、土壤等;
(5)各类光谱仪或X 射线谱仪,如红外、紫外光谱仪、光发射谱仪、原子吸收谱仪和分子荧光谱仪等,用于分析不同种类、不同含量元素的化学成分,可根据分析对象的具体特点和分析要求,选择合适的分析手段。
3.2 表面或微区化学分析技术
在失效分析中,相对于名义或宏观区域的成分分析而言,失效零件的材料表面/界面成分、状态及失效源区的微区成分和状态分析更为重要,尤其是对表面损伤或者由于诸如夹杂、成分偏析等造成的失效。目前主要的分析仪器有电子探针显微分析仪(EPMA)、X 射线能谱仪(EDS)、X 射线波谱仪(WDS)、俄歇电子谱仪(AES)、电子能量损失谱仪(EELS)、X 射线光电子谱仪(XPS)、场离子显微镜
俄歇电子谱仪,也称之为扫描俄歇显微分析仪 (FIM)、原子探针显微分析仪(AP)、低能离子散射谱仪(LEISS)以及二次离子质谱仪(SIMS)等。其中,配备X射线能谱仪、X射线波谱仪或电子能量损失谱仪(EELS)等,须配备在电子探针、扫描电镜或透射电镜上,以满足微区元素成分、状态分析的需要,下面就最常用的分析技术进行讨论,其他技术在必要时可参考相关文献(如文献[1,9,38-39]等)。
电子探针显微分析仪:它靠光学成像进行定位,广泛应用于平坦表面微区1 μm 区域的成分定性或定量分析。利用电子探针可给出所分析元素的线分布、面分布和定点区域的元素含量,元素分析的检出限可低至0.1%(w)左右。电子探针对表面无损伤作用,但缺点是对所分析的表面平整度有一定要求,无法分析粗糙的断面。常配备X 射线波谱仪(WDS)和X 射线能谱仪(EDS)进行元素分析,首先,X 射线波谱仪:X 射线的波长决定于被激发物质的原子序数,该仪器是利用探测X 射线的特征波长来进行的成分分析。波长色谱仪可分析到铍。一般来说,波谱仪的元素特征波长分辨率较高,这是它的突出优点。但是为了达到谱仪的精确聚焦,要求样品上X 射线的发射源(分析点)的几何位置严格的处于聚焦圆上;同时波谱仪难以在低速流和低激发强度的情况下使用,这是波谱仪的两个缺陷。其次,X 射线能谱仪:X射线能谱仪的最大优点是不损伤表面以及可同时适用于粗糙的断口表面和磨片表面的元素分析,因而是目前失效分析中最常用的微区成分分析仪器。X 射线能谱仪是测量特征X 射线能量来确定样品中元素的方法。这两种谱仪也可配置在扫描电镜或透射电镜上,将微观组织结构分析与化学元素分析有效集成起来。图20给出了采用电子探针WDS对一种铸造高温合金中元素偏析的微区成分面分布分析,可以直观地看到,W、Re 等重元素倾向于分布于枝晶干上,而Al和Ni更多地分布于枝晶间。(SAM),可分析2~3 nm以内厚度的极薄表层上除氢、氦以外的所有元素,比如在进行表面氧化等表面现象分析时可发挥重要的作用。俄歇电子谱仪分析的直径大于100 nm。可进行表面薄膜、涂层或污染分析、深度方向成分分布、断裂晶界或其他界面上的元素成分分析(如钢的回火脆性现象的分析)等,图21(a)为一种530 ℃回火空冷后的热作模具钢U 型缺口冲击后的断裂特征,断裂以沿晶脆性断裂为主,沿晶断裂晶界处的俄歇电子能谱分析结果见图21(b),发现沿晶界存在明显的杂质P元素的偏聚[该材料中的P 元素含量为0.031%(w)],说明该沿晶脆性断裂与晶界P元素的偏聚直接相关[40]。
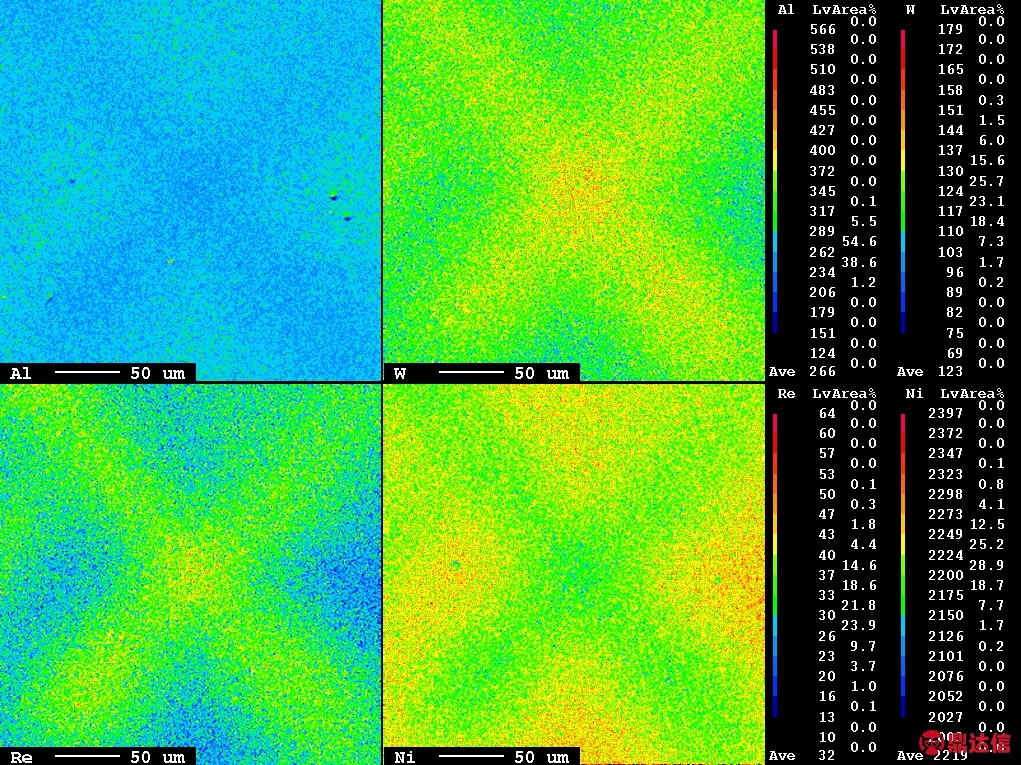
图20 利用EPMA/WDS对一种铸造镍基高温合金中元素分布进行分析的面分布图
Fig.20 Element mapping of a cast nickel-based superalloy using EPMA/WDS
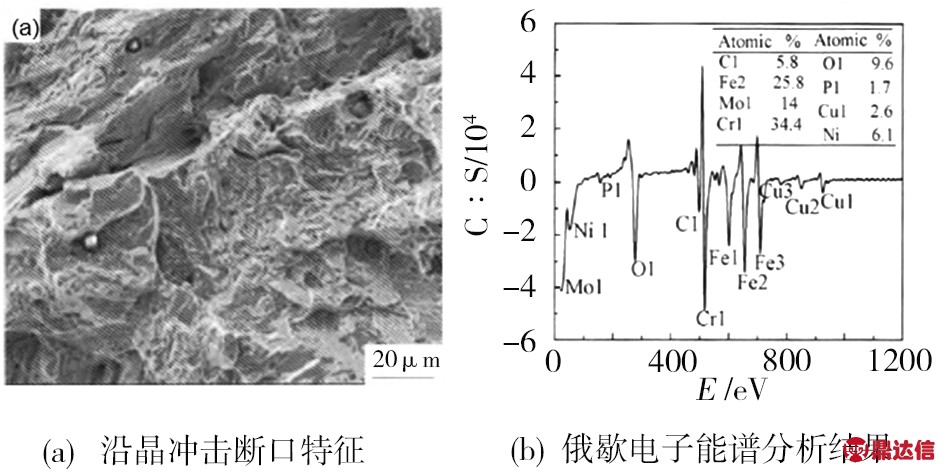
图21 一种热作模具钢的脆性沿晶冲击断口特征及沿晶断裂晶面处的俄歇电子能谱分析结果
Fig.21 Intergranular fracture morphology of a brittle hot work die steel under impact and measurements at the intergranular surface using AES
X 射线光电子谱仪(XPS):可进行除氢以外的表面元素分析、化学状态分析以及表层元素的深度分布特征的分析;不足之处在于较其他表面分析技术的数据采集时间长,一般情况下,定性分析需要5~10 min时间,定量分析根据须采集的信息需要1到好几个小时之久;另外,其平面分辨率和定量分析的准确度都不高。对一种TA15 钛合金进行了海洋平台户外大气暴露实验,并进行了断裂韧度的对比分析,发现大气暴露后的材料的断裂韧度较原始材料大幅度下降,材料的脆性断裂特征明显加剧,经X 射线光电子谱仪刻蚀分析表明,大气暴露试样表面的杂质原子氧含量较原始试样明显富集并向试样内部扩散(图22),引起了一种近表面效应,导致材料表面变脆,断裂韧度下降[41]。图23为一个利用X 射线光电子谱仪进行表面元素化学存在状态分析的例子,一种偏共晶Ni-Pb合金与钢珠进行磨损实验,磨损后利用X 射线光电子谱仪对Ni-Pb 合金表面进行元素状态分析,见图23(a)和(b),从Ni 和Pb 的结合能可以推断出,磨损表面[图23(c)]的Ni 和Pb 分别以Ni2O3和PbO 的形式存在,表明合金在接触压力和表面高温的共同作用下发生表面氧化形成了氧化膜,对摩擦过程具有润滑作用,改善了接触磨损抗力[42]。
二次离子质谱仪:可进行包括H 元素在内的所有元素的分析,表面成分分析的深度分辨率可达5~10 nm;可进行微量元素含量分析,分析范围为几个10-9到几个10-6;可进行元素沿深度方向或空间分布的特征的分析。但是,其分析过程是破坏性的,而且,其定性或定量分析结果会因元素或材料的不同而波动较大,分析的质量严格依赖于仪器设计的水平和分析操作的参数,分析时间一般在一到数小时范围内。一种不锈钢经不同能量激光表面处理后的表面H 元素的含量沿深度方向的分布特征见图24,其中,采用 133Cs +主离子束提高了对H 元素的二次离子的探测灵敏度[39]。
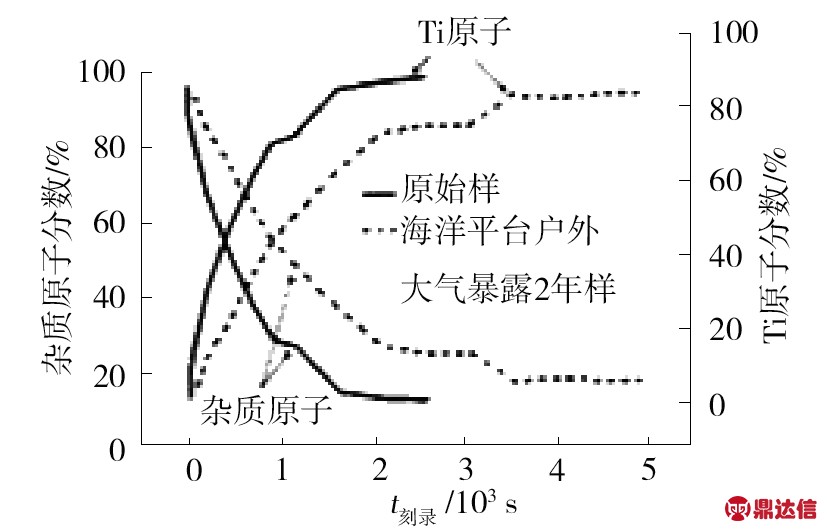
图22 一种TA15钛合金进行了海洋平台户外大气暴露实验后,X射线光电子能谱仪刻蚀检测结果(蚀刻速度3~5 nm/min)
Fig.22 Etching measurements using XPS on a TA15 alloy exposed to oceanic atmosphere with an etching rate of 3 to 5 nm/min
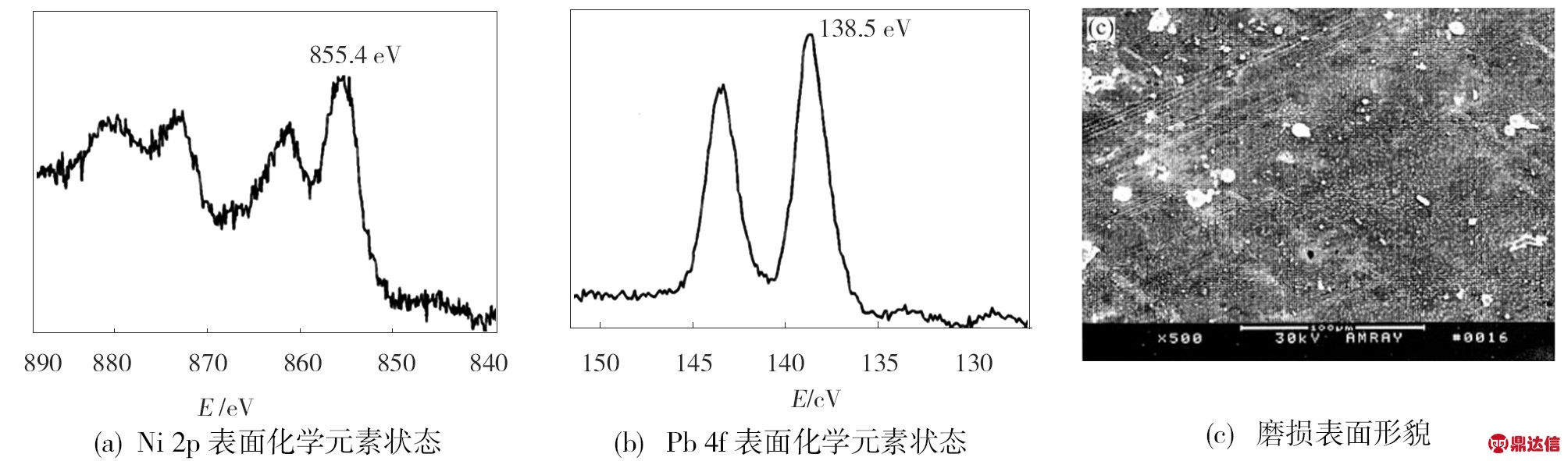
图23 一种Ni-Pb偏共晶合金与钢珠磨损后的表面化学元素(XPS)和形貌分析
Fig.23 Chemical element analysis using XPS and morphology by SEM for an off-eutectic Ni-Pb alloy worn by steel balls,during which
the contact force was 20 N and the sliding rate was 0.04 m/s
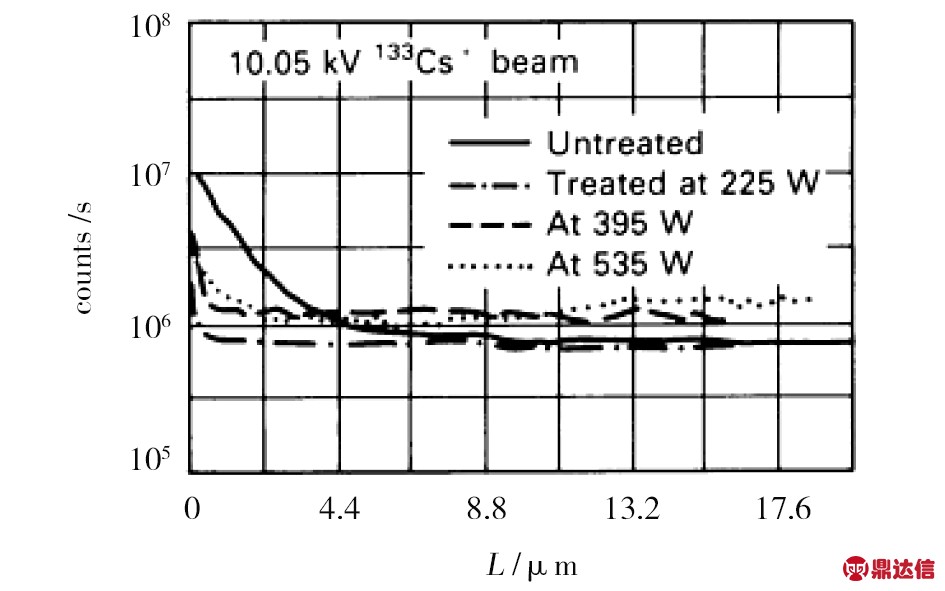
图24 二次离子质谱仪分析一种不锈钢经激光表面处理后的表面H元素沿深度方向的分布特征
Fig.24 Distribution of atom H along depth of a stainless steel after laser surface treatment measured using SIMS
4 残余应力分析技术
残余应力是固体内部自身存在的一类自平衡应力,它一般来源于材料或构件的制备过程、连接工艺、组装过程、热处理/表面处理或服役过程,会直接影响疲劳抗力和应力腐蚀抗力,也经常会在机械加工或热处理过程中引起扭曲,因此,如果未对其进行有效的分析和控制,在构件的加工、制备、热处理和服役过程中,会引起构件的意外失效;另一方面,在对残余应力准确认知的前提下,可以在构件中有意引入残余应力,从而延长构件的服役寿命。因此,对残余应力进行分析是材料损伤和构件失效分析中须考虑的[43-47]。
有很多分析技术可用于残余应力状态的表征,一般而言,分为两类分析技术。第一类是基于应力释放测量内部残余应力的技术,很明显,该类技术是有损的技术,须对材料或构件进行破坏,常用的最具代表性的是轮廓法和钻孔法,其中,轮廓法是利用线切割方法(EDM)剖切待测样件将残余应力释放出来,通过剖切面的平整度变化解析出该处的残余应力场和应力水平,其优点是测量装置简单,可得到剖切面法向的残余应力场,最重要的是,可以通过一次切割,得到二维应力面分布图,值得注意的是,在样品切割时要保证样件不发生移动,如图25所示,一种12.5 mm 厚的铁素体钢板的纵向焊接残余应力的分布特征[48]。钻孔法用于测量近表面的残余应力,在待测区域连接引申计并钻小孔,开孔后导致孔附近的应力释放,被释放的应变量可用引申计记录下来,从而解析出此处的原始的平面残余应力状态,ASTM E837 标准方法规定了该项技术的使用过程,该方法简单、操作成本低、对样品造成的损伤很小,不足之处主要有,打孔时孔壁会发生塑性变形,造成测量结果的偏离;只能得到近表面的残余应力(深度接近于孔径),通常为1 mm 左右;只能进行逐点测量,进行多点测量时,各点(孔)不能离得太近,间隔通常为5 mm。
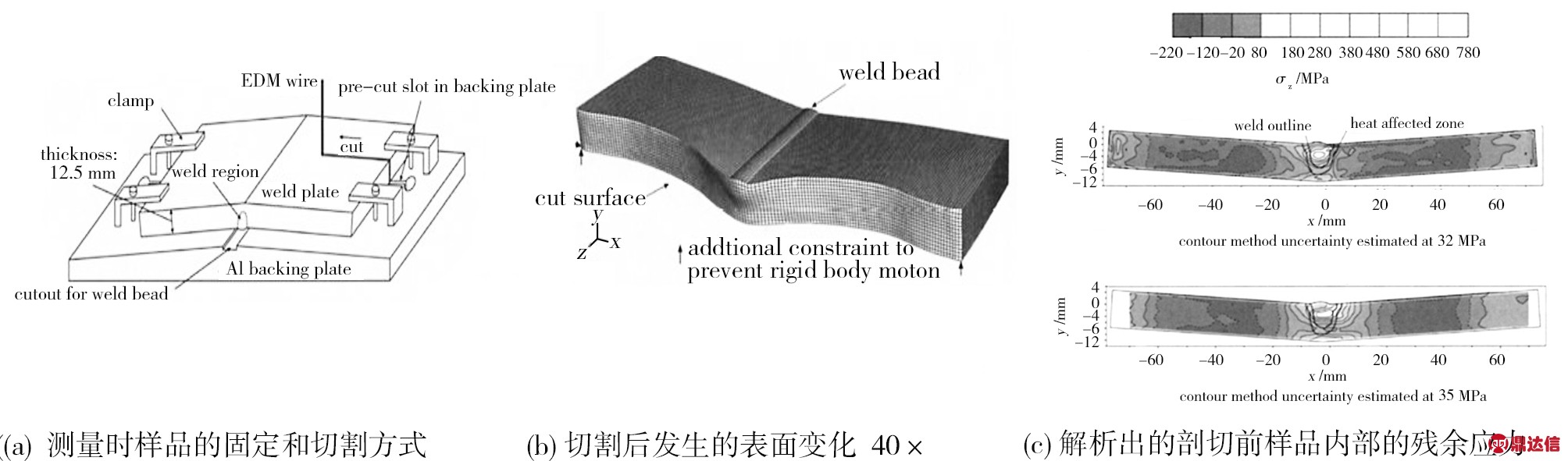
图25 轮廓法测量一种12.5 mm厚铁素体钢板的纵向焊接残余应力
Fig.25 Longitudinal residual stress in a 12.5 mm thick ferrite steel plate weld measured by contour method
第二类残余应力分析技术为衍射技术,属于无损分析技术,通常包括常规X 射线衍射技术(实验室级)、高能同步辐射X 射线衍射技术和中子衍射技术[44,48-49]。
常规X 射线衍射技术使用sin2ψ 方法进行残余应力测量,由于X 射线在样品中的穿透能力很弱,通常为20~30 μm,因此该方法假设待测表面法向的残余应力为0,可进行无标样的表面残余应力和应力场的测量,结合剥层技术,可进行近表面的残余应力分析,而且可利用便携式衍射仪进行现场的残余应力测量,但该技术对样品的表面状态非常敏感,相关的技术标准可参考ASTM E1426、ASTM E915 和HB 20116等。图26中,可看到一种TC4合金经快速切削后表面的β 晶粒变形特征[图26(a)],晶粒沿着切削方向被拉拽扭曲,厚度为几个微米;利用X 射线衍射法对不同切削速度引入的表面残余应力状态进行了分析,结果见图26(b),发现低切削速度会引入压应力,而当不断提高切削速度时,残余应力会逐渐变为拉应力[50]。同步辐射X 射线衍射技术和中子衍射技术均通过对比测量样品的晶面间距和无应力参考样品的晶面间距,得出样品内部的残余应变值和残余应力状态,须在专门的大科学分析装置上进行分析。同步辐射X 射线衍射技术可进行二维应力场分布的快速测量,分辨率优于1 mm,但由于其使用较低的衍射角,一般适用于薄板类样品的测量,另外三轴应力的测量也比较困难,图27中,对一个12 mm 厚的疲劳裂纹Al-Li 合金试样施加拉伸载荷,获得6.6 MPa·m1/2的名义应力强度的条件下[见图27(a)中的白色嵌入图片,图中的标记为测量位置,裂纹尖端位于零位置],利用同步辐射X 射线衍射技术分析裂纹尖端处沿裂纹张开方向的弹性应变/应力场[49];相比之下,中子衍射技术可进行三维应力场的测量,探测深度可达数厘米至数十厘米,检测方法已有相关的技术标准供参考和使用(如ISO/TS 21432和GB/T 26140),但测量成本非常昂贵,检测装置也不易获取。
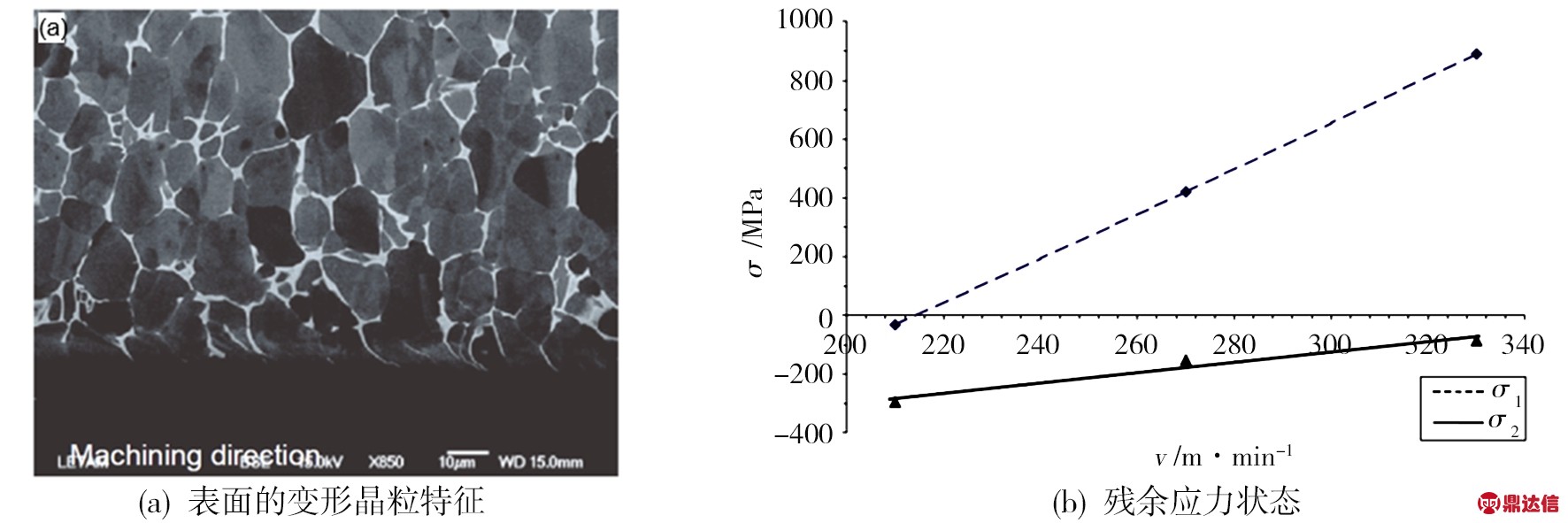
图26 一种TC4合金经快速切削后表面的变形晶粒特征和常规X射线衍射技术测得的残余应力状态
Fig.26 Deformed grain morphology of a TC4 alloy and the residual stress state measured by conventional X ray diffraction
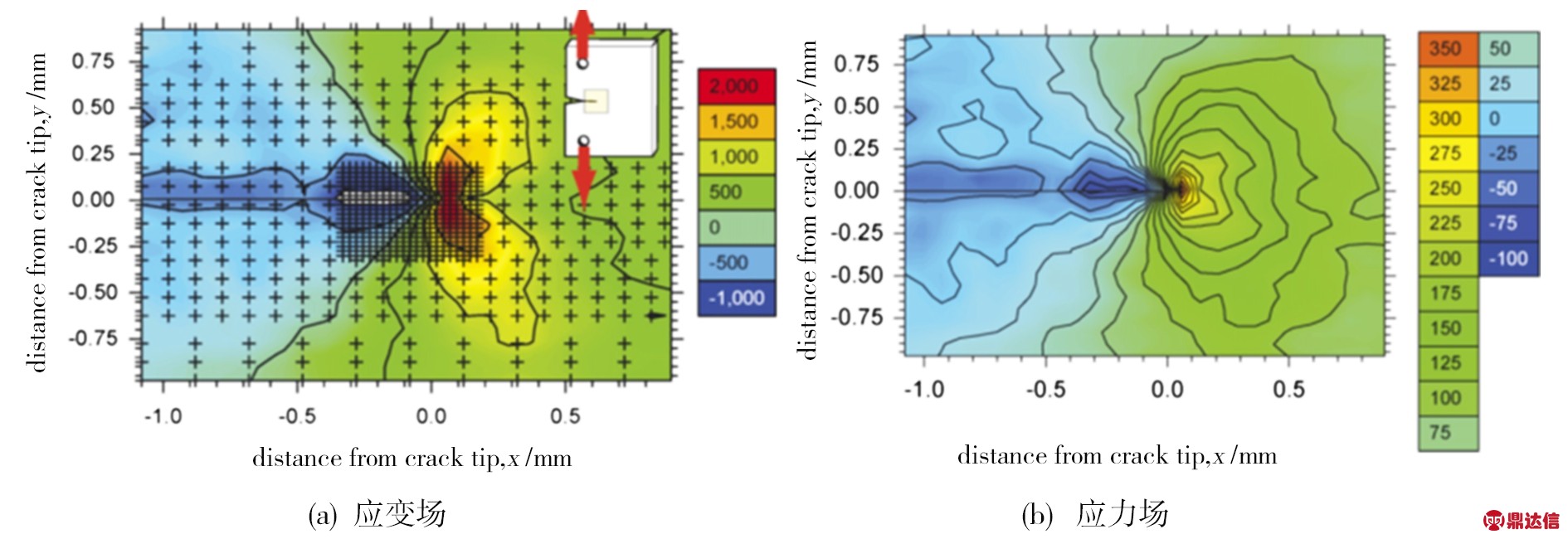
图27 利用同步辐射X射线衍射技术分析裂纹尖端处沿裂纹张开方向的弹性应变场和应力场
Fig.27 Elastic strain and stress along crack opening direction at crack tip measured using synchrotron X ray diffraction
5 原位分析技术
原位分析技术是指分析对象在被施以合适的外部载荷或环境条件(如温度和气氛等)下,对其损伤过程进行实时测量、监测和分析的一项技术,一般是在前面所提及的分析装置上,设计和集成适当的加载或环境发生装置后,设计合适的实验方案后对材料的损伤过程进行实时原位的观测和分析,因此,本质上讲,原位分析技术所采用的基本分析测量技术和手段即是前面所讨论的内容所覆盖的,但是所不同的是,可利用这些技术手段对材料的损伤全过程进行动态实时检测和分析,得到在非原位条件下进行的损伤、断裂和失效分析所无法获取的重要信息,因此,将其单独提出来进行讨论,主要讨论三种常用的原位损伤分析技术。
首先,基于扫描电子显微镜的原位分析技术,通常可在扫描电镜设备上配备不同的载荷台(如拉伸、疲劳等),分析材料的机械损伤过程;或者,可配备高温/低温台,分析材料的高温/低温损伤/相变特征等,分析过程中可结合扫描电镜的附属设备如能谱仪和EBSD 等的分析,针对各类损伤过程获取更多相关的信息[11,18,51-52]。例如,在配备有原位拉伸载荷台的扫描电子显微镜中,对一种定向凝固Ni3Al 基高温合金进行了动态拉伸过程的原位观测,如图28所示[52]。
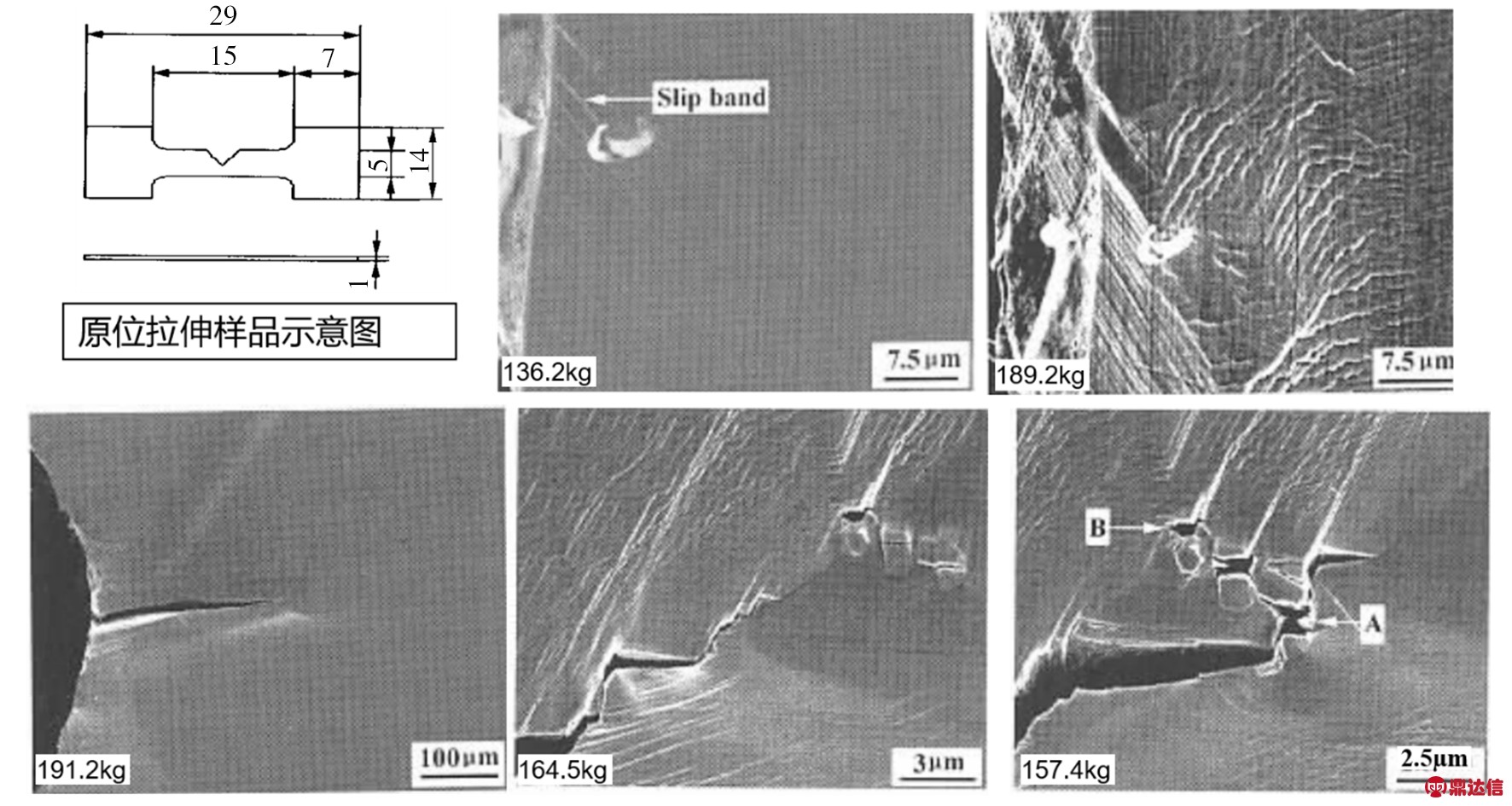
图28 针对一种定向凝固Ni3Al基高温合金,进行基于扫描电子显微镜的原位拉伸损伤过程观察
Fig.28 In situ observation of the tensile damage in a directionally solidified Ni3Al superalloy using SEM-based technique
所使用的样品的几何尺寸见图28中左上角图,为了便于观察,在试样中部切出一个V 型缺口;其它图像是在原位拉伸过程中,在不同的原位载荷条件下的扫面电子显微镜观察的显微组织特征。可以看出,拉伸初期,在缺口处出现了滑移带(1 362 N时)并逐渐出现交叉滑移(1 892 N 时),1 912 N 时出现裂纹,其后应力迅速松弛,裂纹向前扩展,裂纹周围出现多条互相交织的滑移带并出现碳化物颗粒开裂和碳化物/基体界面开裂(1 645 N 时),随后裂纹穿过开裂的碳化物颗粒(A处)继续向前扩展,而并未沿碳化物/基体界面的微裂纹向前扩展(1 574 N时)。
其次,基于X 射线衍射/断层成像的原位分析技术,在X射线衍射/成像设备上配备不同的载荷台(如拉伸、压缩或疲劳等),分析材料的机械损伤过程;或者,可配备高温/低温台,分析材料的高温/低温损伤/相变特征等,以及相关的应力应变分布和演化特征,并有效利用其三维表征功能,获取更加全面的信息[53-56]。例如,在基于同步辐射X射线装置的高温疲劳原位加载台上,对一种铸造Al 合金进行250 ℃条件下的疲劳损伤机理分析,其疲劳最大载荷为屈服应力的1.4 倍,应力比为0.1,见图29,所给出的三维形貌显示了原始合金的组织形貌(左图)和20次疲劳周次时的组织形貌(右图),细小黄色粒子为合金中的二次相粒子,紫色、绿色和橙色区域为原始合金中的铸造缺陷,水平箭头所指为起源于橙色空洞的裂纹,垂直箭头所指为二次相附近的小裂纹,分析得出了合金中的二次相粒子、铸造缺陷以及小裂纹的萌生特征[56]。
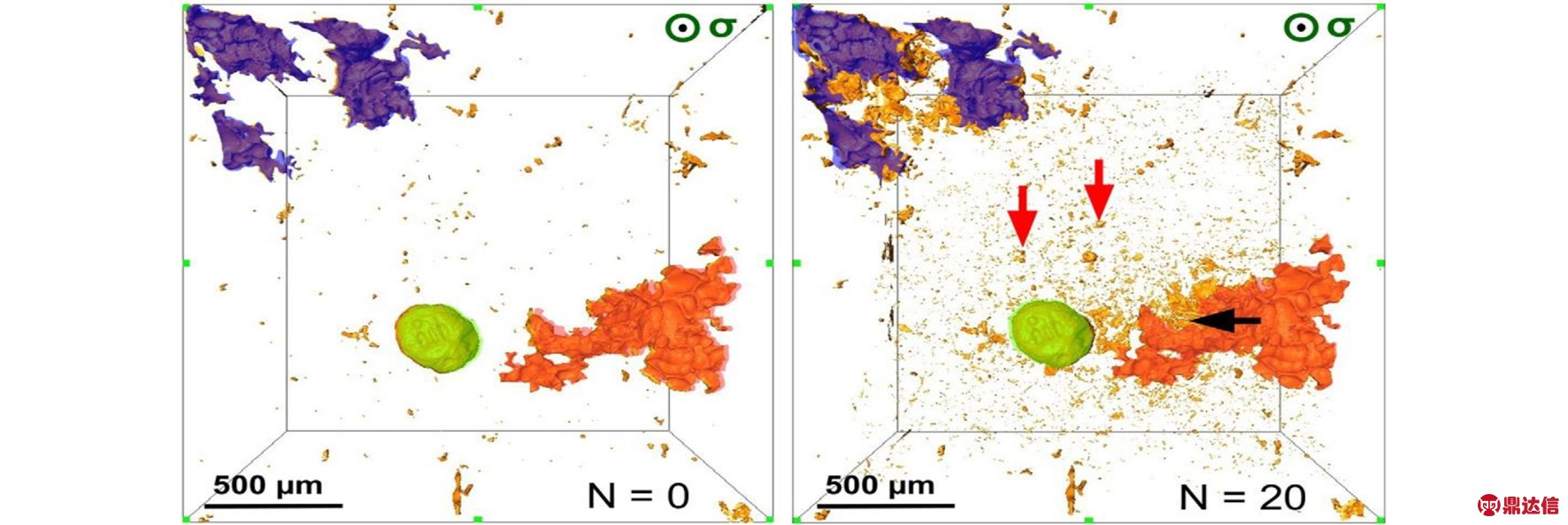
图29 基于同步辐射X射线技术对一种铸造铝合金进行高温(250 ℃)原位疲劳损伤机理研究的三维形貌分析
Fig.29 An in situ observation of the damage in a cast aluminum alloy using a synchrotron X ray diffraction-based technique at the temperature of 250 ℃
最后,数字图像关联分析技术(DIC),该技术可基于普通照相技术、光学金相技术、扫描电子显微分析技术或透射电子显微分析技术获得的图像,参照在载荷作用下材料固有的或人工引入的表面特征的变化,利用专业软件进行图像数字化和关联计算后,可进行从纳米尺度到宏观尺度的位移测量和应变特征分析,是进行损伤行为研究的强有力手段[57-62]。如图30所示,针对一种不锈钢,基于数字相机图像[图30(a)]中奥氏体基体上拉长的铁素体相,分析了样品在疲劳载荷作用下的表面位移和应变场面分布图[图30(b 和(c)],图中的亮点对应疲劳微裂纹,裂纹宽度为1 μm 左右,有效显示了加载过程中的位移场特征、应变场分布和裂纹扩展特征[2]。
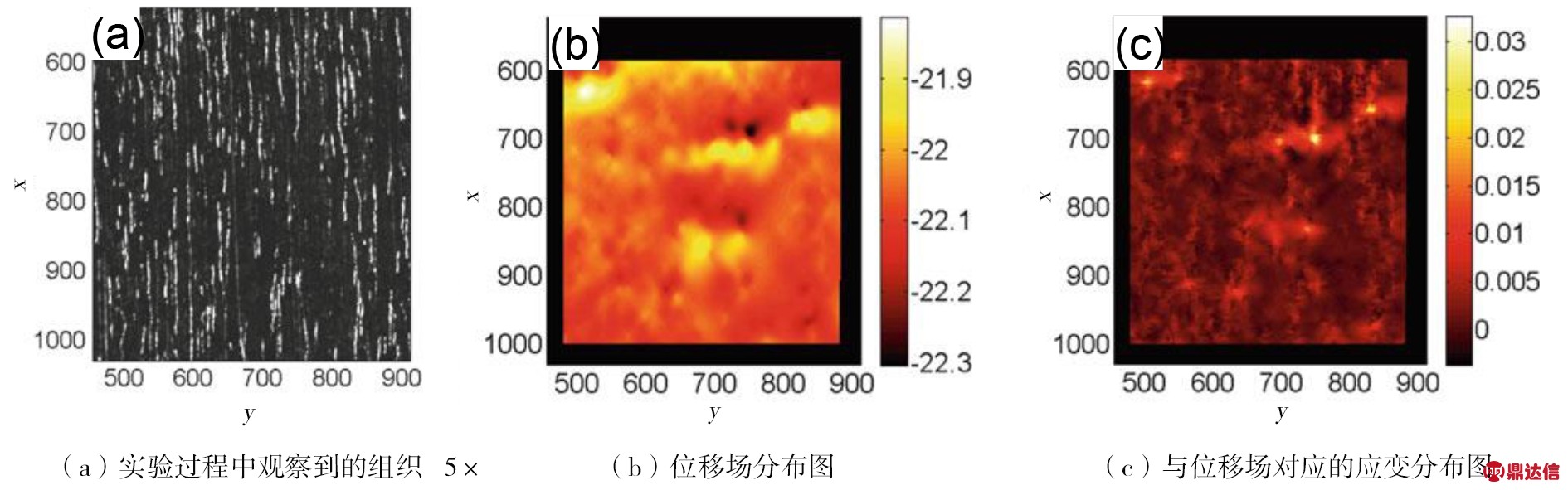
图30 利用DIC技术原位分析一种不锈钢在疲劳载荷作用下的应变场
Fig.30 An in situ measurement of the strain field of a stainless steel under fatigue loadings using DIC method
6 结语
综述了金属材料损伤分析中常用的物理冶金分析技术,不同的技术各有其特点和不足,能够给分析人员提供不同种类和不同层面的信息,在分析工作中起到不同的作用和解释不同方面的问题,因此,在实际的分析工作中,应根据分析的具体要求、技术手段的实用性和可用性以及分析人员的合理综合判断,有针对性地选取实用的分析技术,并将它们有效地结合起来,筛选合适的分析技术手段和装备,为分析工作获取有价值的综合信息。
随着物理冶金分析相关的硬件水平和技术水平的不断提高,无论在组织结构分析方面、残余应力分析方面,还是在化学成分分析方面,其分析技术的分辨能力(包括空间分辨率、探测极限等)都在显著提升,但同时也对分析过程提出了更加苛刻的要求,在这种背景下,如何将这些分析技术有效应用于金属材料的损伤分析中,并建立成熟稳定的分析技术,从而准确表征和探究其损伤行为特征和损伤机理等,是目前重要的研究方向之一;另外,在原位分析方面,近些年快速探测技术和原位环境的构建技术正在不断进步,如何应用这些技术,对材料在不同使用或服役的模拟环境下的损伤过程进行更加实时精准的原位监测,从而更加真实地反映材料的实际损伤行为特征,也正发展成为一个重要的研究领域;最后,如何将各类分析技术有机结合起来,并互为补充,针对金属材料的损伤行为,从原子尺度到宏观尺度,实现多时空条件下的跨尺度研究,也是目前的研究焦点之一。