摘 要:为满足非道路柴油机国三排放要求,给S1100柴油机设计了一种净化消声器,在消声器排气进口和催化剂载体入口截面之间设置气流穿孔隔板以改善催化剂载体内部流场均匀性。用模拟计算的方法对穿孔隔板的参数和位置尺寸进行优化,使催化剂载体内部流场均匀分布,以提高排气污染物的催化转化效率,同时增长净化消声器的使用寿命。对设计的净化消声器与原消声器进行柴油机性能对比试验,结果表明:使用所设计净化消声器的柴油机,CO、HC、PM比排放分别为0.38、0.35、0.41 g/(kW·h),相比于使用原机消声器,分别降低了87.1%、67.0%、26.8%,而噪声略低于原机。由此可知,S1100柴油机能满足国三排放标准和噪声标准要求。
关键词:柴油机 单缸 净化消声器 设计 排放 催化剂
引言
我国单缸柴油机生产量和使用量大,年产量约占世界年产量的90%以上[1]。近年来,环境污染问题日渐突出,内燃机节能减排的要求不断提高。我国颁布非道路柴油机国三排放标准已有三年,单缸柴油机行业做了大量工作,在有效使用寿命内完全达到排放标准要求是一个难题,仅依靠传统的机内净化难以满足国三排放标准以及以后更趋严格的排放法规;内燃机的噪声也是重要的污染源,国家标准中强调了噪声污染的控制[2]。在减少排放和降低噪声方面,单缸柴油机受到各种结构因素的影响,将消声与催化结合于一体的措施是目前单缸柴油机技术升级较为有效的方案之一。
关于一体式净化消声器,国内外内燃机相关学者已经做了大量的研究。第一次进行催化消声一体尝试的是Ted等人[3],采用了V型床来设计气体流动较好的催化转化消声器,但效果并不理想;Charlcs H.B.[4]发明了一种直流净化消声器,消声作用明显降低;Kenneth[5]发明了一种结构较为复杂的消声器,该消声器入口采用扩张管,再接催化转化器,气体经过催化转化器后流经三段穿孔管,最后穿过出口。国内对净化消声器相关方面的研究比国外晚,刘文国[6]选取催化剂用量、催化剂的颗粒直径、开孔板的开孔率3个主要因素对轻型汽车尾气净化消声器进行了正交试验和分析;黄筱庆等[7]运用有限元法对装有催化剂载体的消声器进行声学性能和空气动力学性能的数值仿真计算和分析,分析不同结构参数对消声器性能的影响。以上研究多以模拟计算为主,且对小型柴油机的研究极少。为满足日趋严格的国家标准,本文以S1100柴油机为样机设计了一种净化消声器。通过对消声器内部流场进行结构优化以及试验分析,优化柴油机的性能,使其符合非道路柴油机国三排放标准。
1 净化消声器结构设计
S1100柴油机的排量为0.942 L,依据排量确定氧化催化剂载体的尺寸大小,考虑单缸柴油机振动较大,采用金属载体,表1为载体的主要参数。
表1 金属蜂窝载体参数
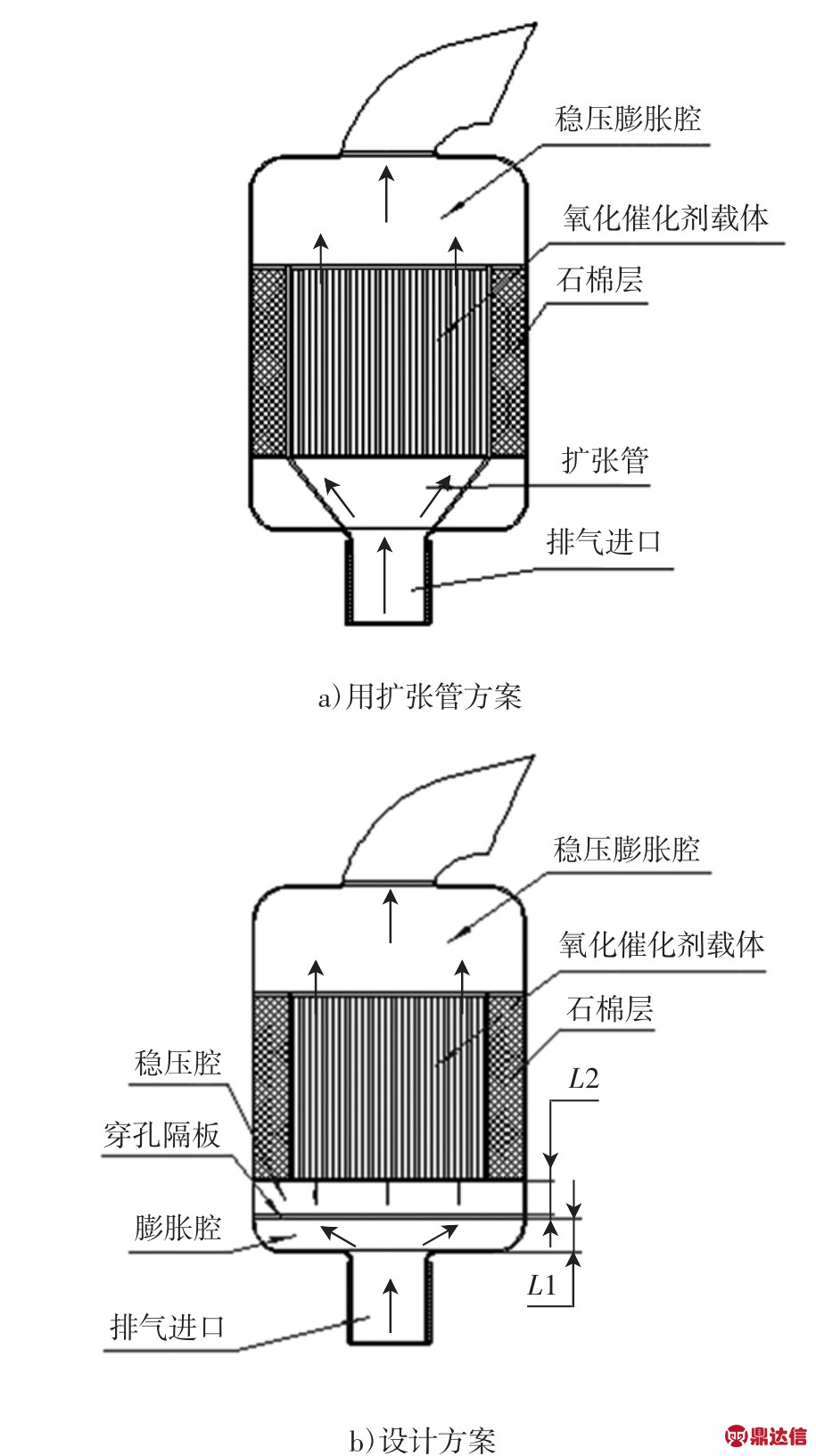
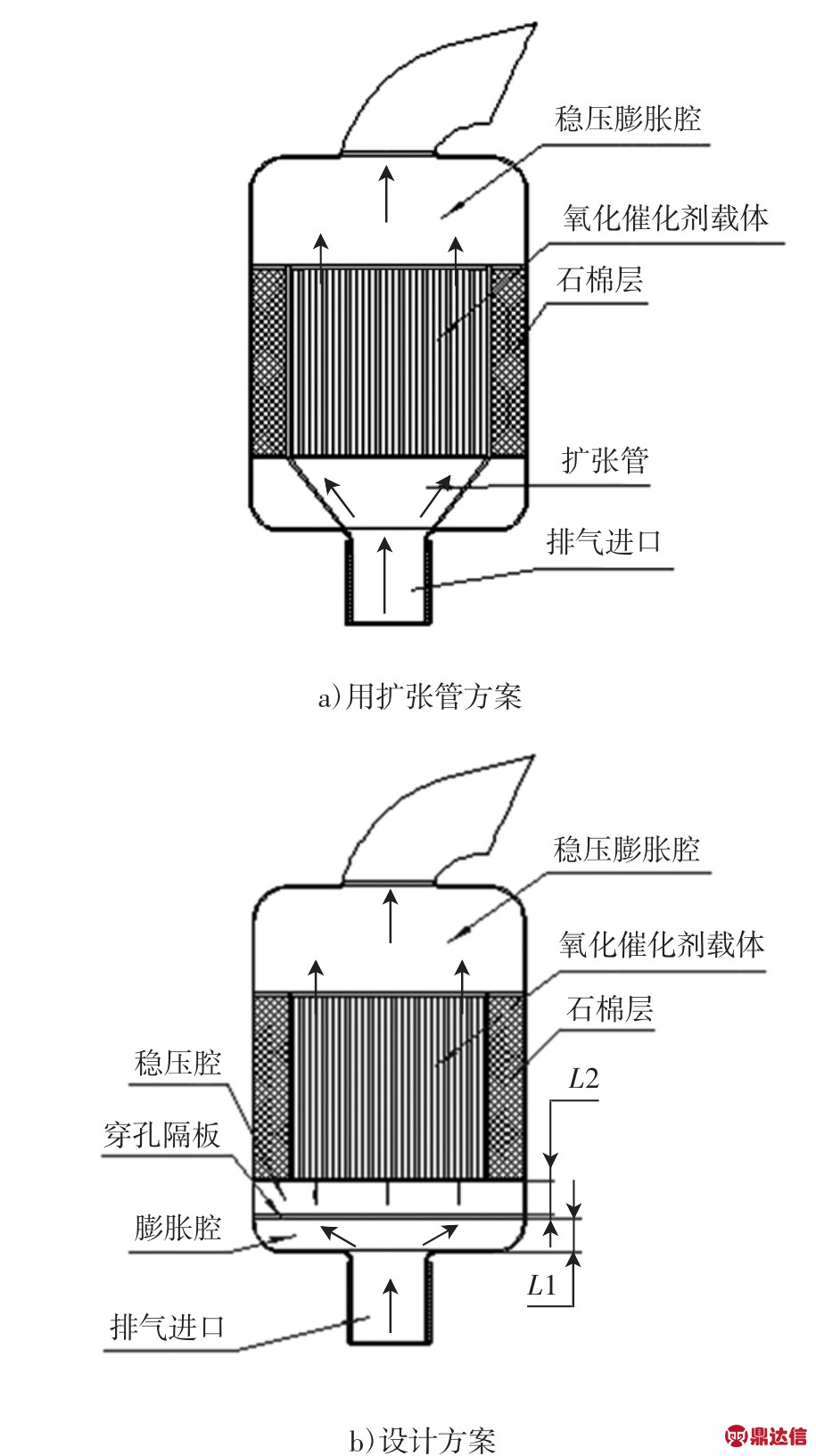
图1 净化消声器结构简图
净化消声器的尺寸保持与原柴油机用消声器相当,便于使用配套。图1是设计的2种净化消声器结构方案,图1a)为目前国内单缸柴油机用净化消声器结构简图(称为扩张管方案),由于单缸柴油机净化消声器结构空间有限,在壳体中装有氧化催化剂载体,采用扩张管结构对气流起导流和消声作用[8],氧化催化剂载体上分布有许多均匀小孔,对废气流有一定消声作用。前期试验结果显示,由于单缸柴油机消声器受结构尺寸限制,扩张管气流轴向长度小,难以达到气流较为均匀的目的,实际气流在扩张管的作用下从消声器进气口流到催化剂载体时,气流大多会从载体中心部分通过流出,周边气流速度很低,使载体内流场不均匀,催化剂的利用效率大大降低,因此需对净化消声器结构进行优化设计,通过结构设计来提高气流均匀性,从而提高氧化催化剂的转化效率,达到排气净化和消声的目的。
图1b)是为S1100柴油机设计的净化消声器结构简图,净化消声器包括圆柱形外壳体,外壳体上下两端分别为出气口和进气口,外壳体内部中间位置为氧化催化剂载体,氧化催化剂载体两端分别由2块定位板定位,在氧化催化剂载体与净化消声器壳体之间填充石棉保温材料,保证柴油机在中小负荷工作时载体内能有足够高的温度,使催化剂起作用。2块定位板分别与外壳体底端、顶端之间形成进气室和出气室,为使进气气流均匀,在进气室内加装穿孔隔板,穿孔隔板将进气室分成2个腔体,与进气口相联的称膨胀腔,穿孔隔板与催化剂载体入口底面构成稳压腔。穿孔隔板上有按一定规律分布的孔,对气流起整流作用,孔的分布对气流均匀有较大影响。膨胀腔和稳压腔的大小对气流均匀也有一定影响。穿孔隔板位置由图1b)中L1(气流穿孔隔板到下壳体底端端面的距离)和L2(气流穿孔隔板到氧化催化剂载体下端面的距离)的大小决定,在保证气流能均匀流入催化剂载体的前提下,应尽可能减小L1和L2,腔体大小对消声效果也有影响。对穿孔隔板上孔的分布、L1和L2的大小进行优化设计,用净化消声器的实际结构进行模拟仿真,找出最佳设计方案。
2 净化消声器的模拟仿真结果及分析
金属蜂窝载体内部可近似看作由许多相同的长而细的密集管道组成,由于管道的直径远小于氧化催化剂载体的直径,可将金属蜂窝载体作为一种多孔介质处理,用当量连续法对氧化催化剂载体进行模拟[9]。
由于载体管道尺寸细小,可认为载体内的气流为定常不可压层流,公式(1)、(2)为简化后的载体内气流的动量方程,由于金属载体内的多孔介质有很大的阻力,因此不考虑动量方程的对流项和扩散项。

式中:p 为压力,Pa;xi为压力在 x 方向上分量,Pa;vi为速度在x方向上分量,m/s;vd为沿催化剂载体轴线方向的载体入口处排气流的气流速度,m/s;Ki为渗透率,与轴向速度大小成正比;αi、βi为经验常数。在载体内,气流只沿轴向运动,因此轴向的α、β按照Hagen-Poiseuille公式确定,沿径向和周向取无穷大,即认为径向和周向的气流阻力很大,在这2个方向上没有流动[10-11]。
2.1 初始条件和边界条件
根据流体力学理论,净化消声器内部气体流动可看作三维可压缩粘性流动,使用Fluent软件,对净化消声器的实际结构进行模拟分析,通过模拟结果选择最佳方案。
利用连续方程、能量方程、动量守恒方程和热力学状态方程耦合标准k-ε湍流模型,建立净化消声器内气体流动的数学模型[12]。计算区域的边界包括进出口边界和固体壁面边界2种:
1)进出口边界。采用速度进口(49.7 m/s,依据发动机标定工况排气流量计算而得)、压力出口(标准大气压)边界条件以及温度和湍流参数。
2)固体壁面边界。固体壁面的温度采用绝热边界条件,固体壁面的速度采用无滑移边界条件[12],边界层速度采用湍流面律条件[13]。
2.2 净化消声器优化方案及模拟仿真结果分析
考虑到生产工艺要求,气流穿孔隔板的穿孔直径定为6 mm,对气流穿孔隔板的穿孔分布、L1、L2等参数设计了多种方案,分别研究结构参数对载体内气流均匀性影响。
2.2.1 穿孔隔板上穿孔分布的模拟结果分析
为减小进气穿孔隔板对排气的阻力,将气流穿孔隔板上穿孔的总面积设计为进气口截面积的1.5倍以上。穿孔分布于以穿孔隔板中心为圆心的同心圆环上,由于气流从消声器进气口流入,净化消声器中心位置流速过高,因此进气穿孔隔板中心的穿孔分布密度较周围区域小,同心圆环的直径大小可用来确定穿孔密度。
图2为设计的多种方案中2种较为典型的穿孔隔板穿孔方案图,方案1、2中6个同心圆的圆环半径都为 12、22、30、38、46、54 mm,不同的是方案 1 穿孔隔板的中心无气流穿孔,第1个同心圆环上的气流穿孔数较少;净化消声器内部气体流动模拟结果如图3所示,它给出了与图2设计的方案相对应的速度云图。
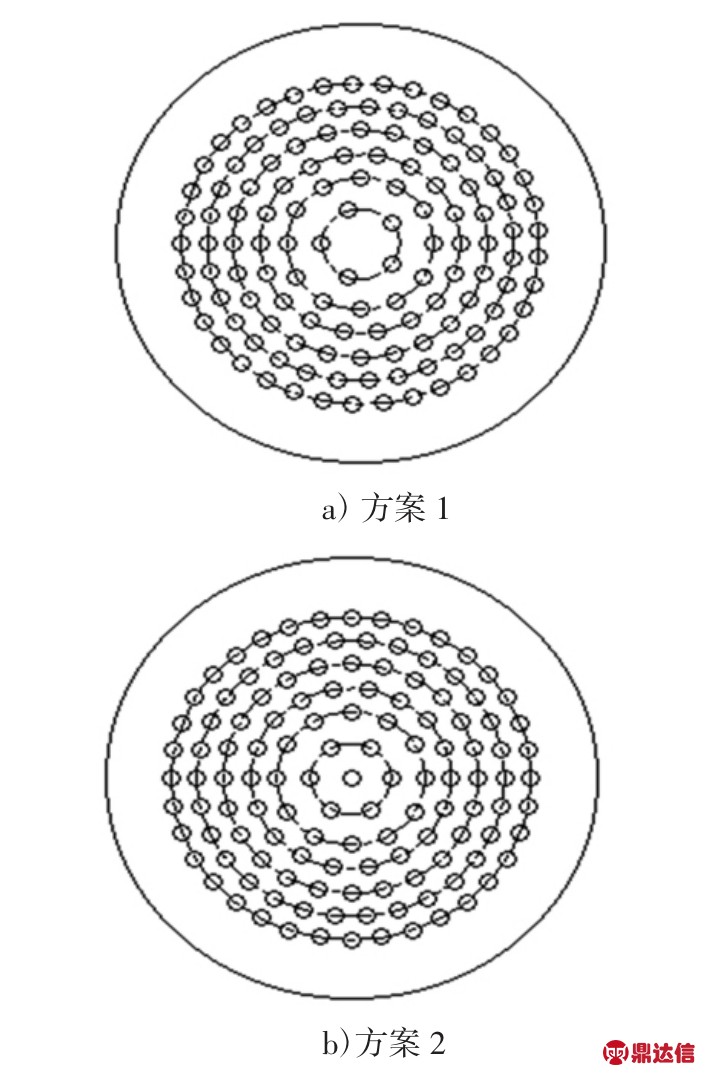
图2 不同穿孔隔板的穿孔分布方案图
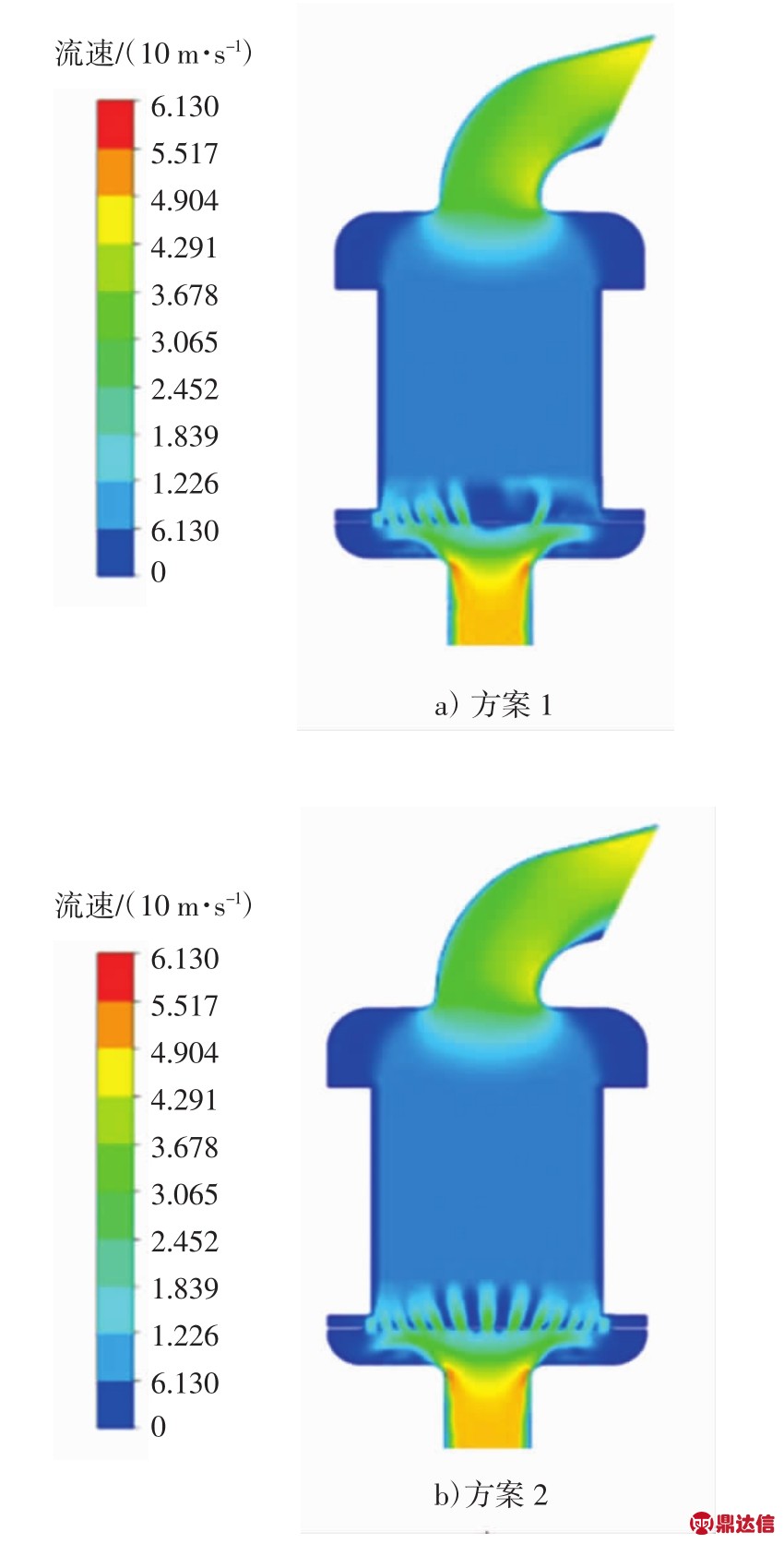
图3 气流穿孔隔板不同穿孔分布的计算速度云图
从图3可以看出,通过气流穿孔隔板进入氧化催化剂载体内的气流都比较均匀,方案1穿孔隔板中心的穿孔分布较为稀疏,在气流通过穿孔隔板时盲区比较大;方案2的气流盲区比方案1小得多,气流盲区较大会使气流通过穿孔隔板后均匀性较差,故选用方案2的穿孔布置方案作为进一步研究的基础。方案2中,每个同心圆环上穿孔的个数按圆心位置由内而外以6的倍数成倍增加。
2.2.2 气流穿孔隔板到下壳体底端端面的距离L1对气流均匀性影响
在选用穿孔隔板方案2为前提下,L1选用8~22 mm多种方案,分析气流穿孔隔板位置对气流均匀性的影响,图4是L1分别为8 mm、18 mm时净化消声器内部气流流场模拟的速度云图。通过图4左边的速度等值线分析速度云图可知,L1=8 mm时,周围区域流速较中间区域低;L1=18 mm时,中间区域与周围区域颜色相差不多,所以流速相近,气流比较均匀。结合仿真结果,考虑到安装空间的局限性,确定气流穿孔隔板到下壳体底端端面的距离L1=18mm为最佳方案。
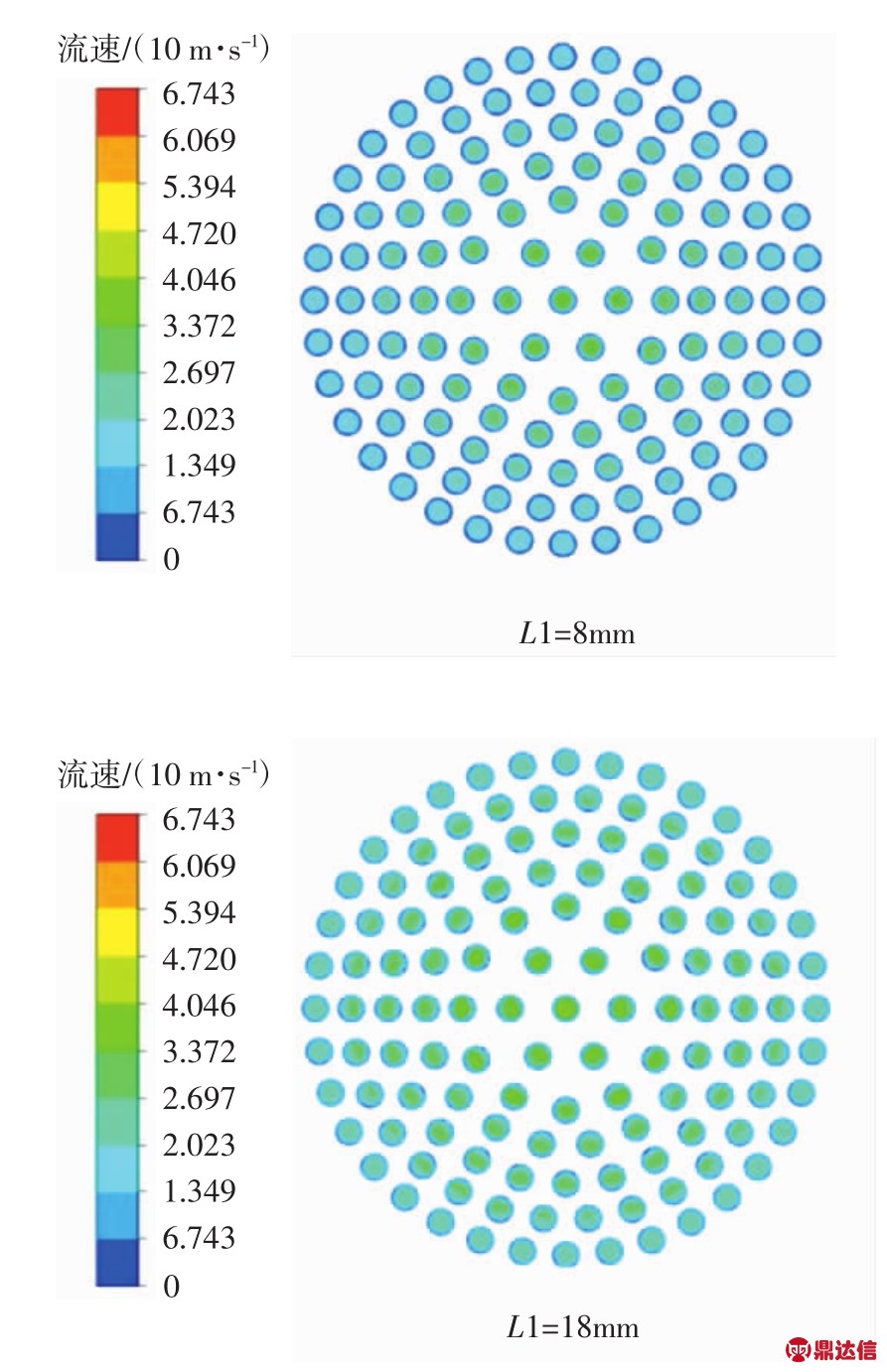
图4 L1尺寸不同时穿孔隔板处速度云图
2.2.3 气流穿孔隔板到氧化催化剂载体下端面的距离L2对气流均匀性影响
在选用L1=18 mm的前提下,L2选用12~28 mm多种方案,分析气流穿孔隔板位置对气流均匀性的影响,图5是L2分别为15 mm、25 mm时氧化催化剂载体入口处速度云图。根据图5左侧速度等值线分析可知,L2=15 mm时,氧化催化剂载体距离穿孔隔板较近,由L2=15 mm的速度云图可以看出,中间区域亮度较为明显,氧化催化剂载体入口处中心区域位置流速较高,周围区域流速较低;L2=25 mm时,氧化催化剂载体入口处与穿孔隔板距离最大,由L2=25 mm的速度云图可看出,周围区域流速与中间区域流速相近,气流基本均匀。由于气流进入氧化催化剂载体入口处时均匀性最为重要,因此在消声器空间允许的情况下优先考虑L2对气流均匀性的影响,由此可确定L2=25 mm为最佳方案。
2.3 优化后的净化消声器的最终结构设计
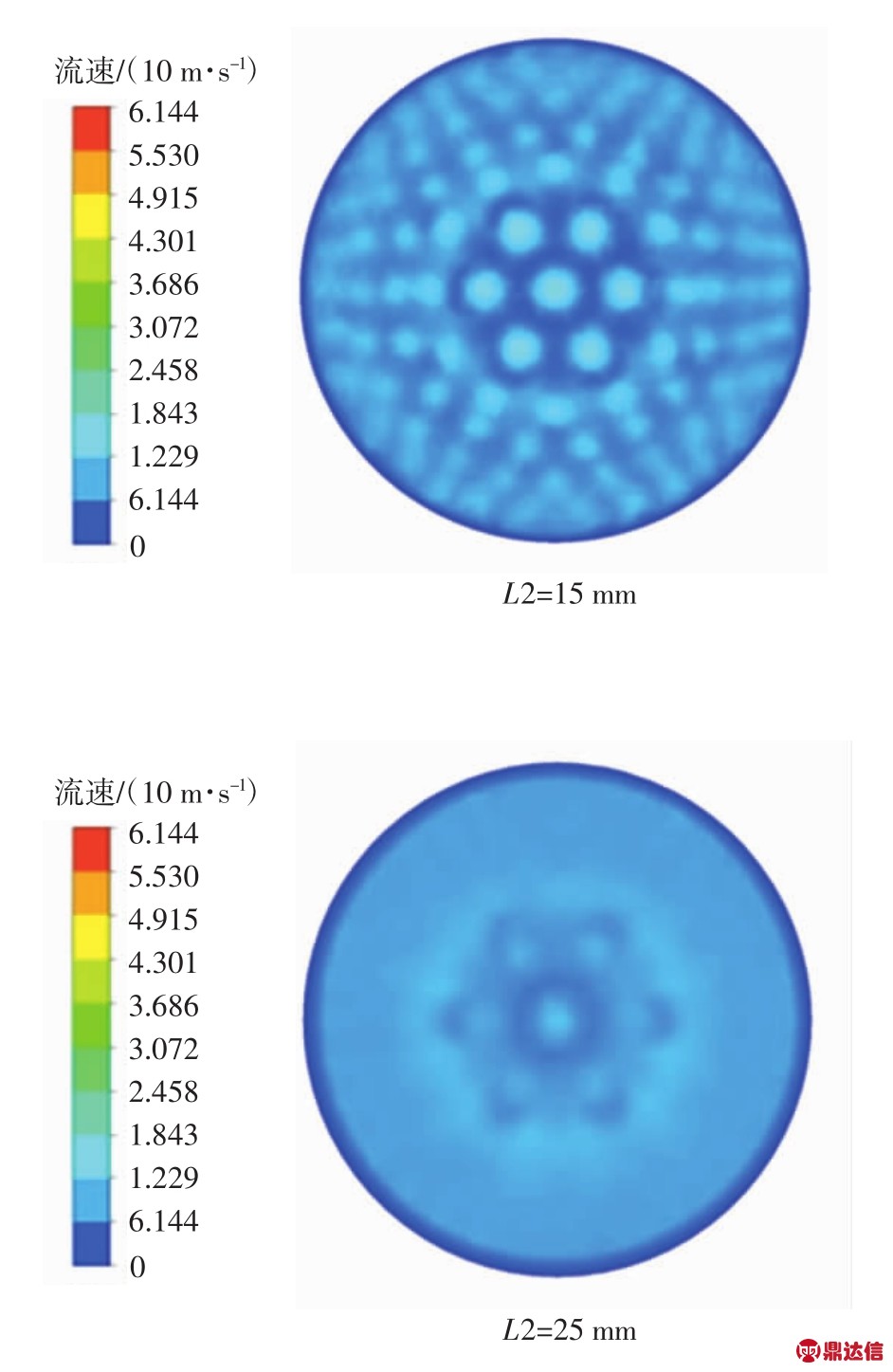
图5 L2尺寸不同时催化剂载体入口处速度云
由以上分析结果可知,穿孔隔板上穿孔分布采用方案2,L1=18 mm、L2=25 mm是优化设计后的结构。考虑到消声器的消声效果,在出气室中加装出气穿孔隔板,出气穿孔隔板上端设穿孔出气管,形成2腔的消声单元,进一步提高了净化消声器的消声性能,图6为最终设计确定的净化消声器结构简图。
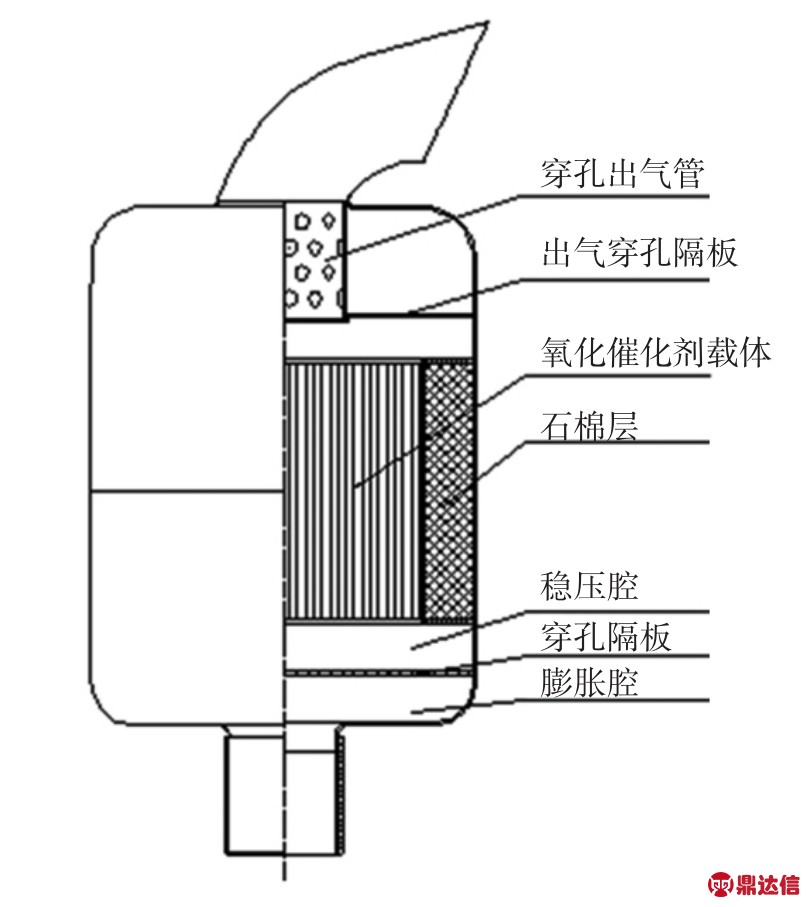
图6 净化消声器的最终结构简图
3 使用净化消声器的柴油机试验和数据分析
在S1100单缸柴油机上分别安装原机消声器与设计优化后的净化消声器,将2种消声器进行排放对比试验,试验按GB/T8190.4的8工况C1排放测试循环进行,柴油机的标定功率为11kW(2200r/min),排放结果见表2。表2中,原机试验结果是对换气、喷油和燃烧进行了优化,对活塞环、呼吸器等影响机油消耗的结构进行了改进的优化结果。
表2 S1100柴油机的排放测试结果g(/kW·h)
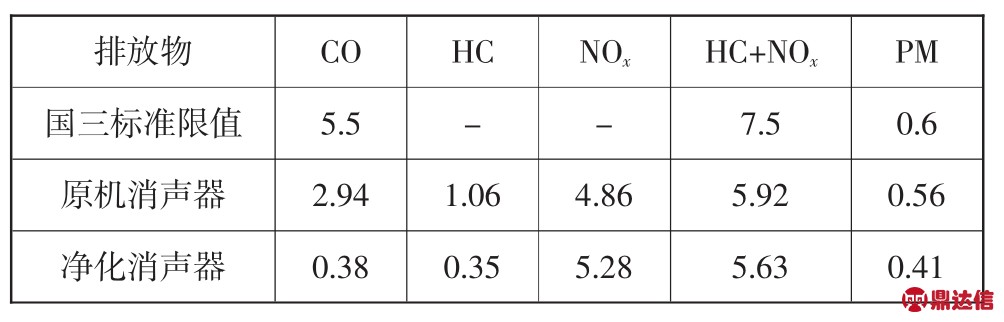
从表2可知,安装原机消声器,CO、HC、PM分别为2.94、1.06、0.56 g/(kW·h);安装优化后的净化消声器,CO、HC、PM分别为0.38、0.35、0.41 g/(kW·h),相比于原机,分别降低87.1%、67.0%、26.8%。使用优化设计后的净化消声器,柴油机的CO、HC、PM排放均远低于使用原消声器,特别是柴油机颗粒排放值与标准限值相比有一定的差值,按标准规定,S1100柴油机在3000h有效寿命期内需满足标准限值要求,因此使用优化消声器的柴油机在使用期内有较大的排放劣化余量。此外,由于排气气流均匀流过催化剂载体,提高了催化剂载体的使用寿命,因此柴油机排放能满足国三排放标准要求。与使用原机消声器相比,柴油机整机噪声实测结果略低,属同一个噪声水平,能满足噪声标准的限值要求。
4 结论
1)单缸柴油机用净化消声器由于受结构尺寸限制,在消声器排气进口采用气流穿孔隔板的结构,能改善气流在催化剂载体的流动均匀性。通过穿孔隔板穿孔分布和穿孔隔板位置参数的优化设计,S1100柴油机净化消声器能满足柴油机排放和噪声标准要求。
2)对S1100柴油机使用净化消声器与原机消声器进行对比试验,结果表明,使用净化消声器后,整机的 CO、HC、HC+NOx、PM 排放分别为 0.38、0.35、5.63、0.49 g/(kW·h),与使用原机消声器相比,分别降低了87.1%、67.0%、4.8%、26.8%,而噪声略低于原机,能满足国三排放标准和噪声标准要求。