摘 要:设计一种新型液压促动器,采用直驱式容积控制技术与单出杆对称液压缸相结合,具有控制灵活、出力大、无溢流节流损失、发热量低、效率高、正反向运动特性相同等优点。对系统中各元件进行深入剖析,建立系统非线性模型,进行AMESim/Simulink联合仿真,并与传统的线性传递函数模型仿真结果进行对比分析,探究系统死区非线性的成因,同时搭建实验平台进行研究,验证了仿真结果的正确性。
关键词:DDVC;单出杆对称液压缸;液压促动器;电液伺服系统;FAST工程
引言
应用于FAST工程(500 m口径球面射电望远镜)的液压促动器是一种接收控制信息并对受控对象进行控制作用的装置,主要由液压执行机构和控制机构组成[1-2]。现有的液压促动器采用直接驱动式容积控制技术(Direct Drive Volume Control,DDVC)控制单出杆非对称液压缸,具有控制灵活、出力大、无溢流节流损失、发热量低、效率高等优点[3]。为进一步提高液压促动器集成度及系统性能,本研究提出了一种新型液压促动器,将直驱式控制技术与单出杆对称液压缸相结合,在具有直驱式液压系统优点的同时,还具有正反向运动特性相同等优点。
1 电液伺服系统设计
1.1 液压原理
图1为直驱式单出杆对称液压缸电液伺服系统原理图,该系统为液压位置伺服控制系统。以交流永磁同步电机为动力源,驱动可双向旋转的定量泵,通过功能定制的集成阀组,最终驱动单出杆对称液压缸[4-6]。
1.2 单出杆对称液压缸
单出杆对称液压缸两腔作用面积相等, 同时内置磁致伸缩位移传感器,其结构如图2所示,在活塞杆内径处加装一细长套筒,套筒末端安装定位磁块,位移传感器测杆固定于缸底。p3口内部为空腔,在p3处加装微型消音器,目的是在执行器运动时降低空气流动产生的音噪,同时阻挡空气中的脏物对油缸的污染。
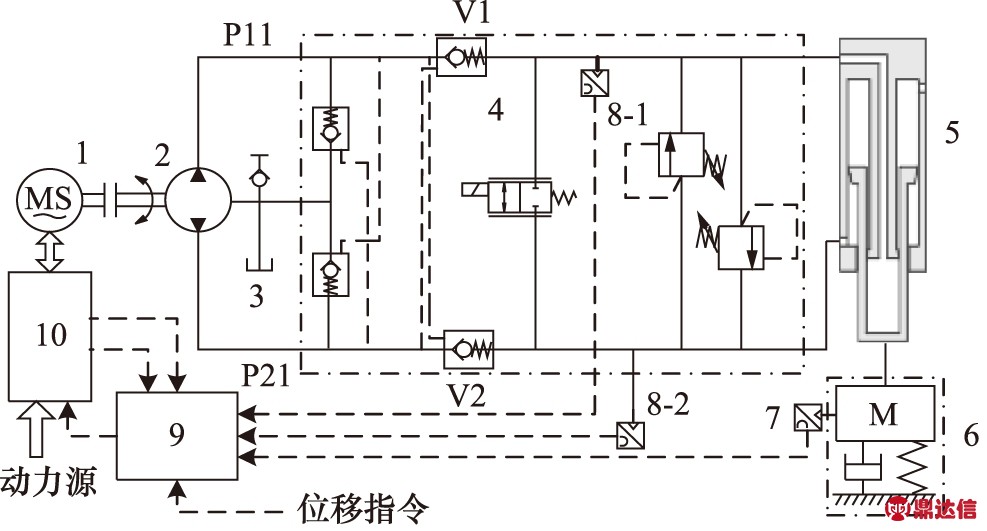
1.伺服电机 2.双旋向泵 3.密闭油箱 4.集成阀块 5.单出杆对称液压缸 6.等效负载 7.位移传感器 8.压力传感器 9.可编程控制器 10.交流伺服驱动器
图1 直驱式单出杆对称液压促动器系统原理图
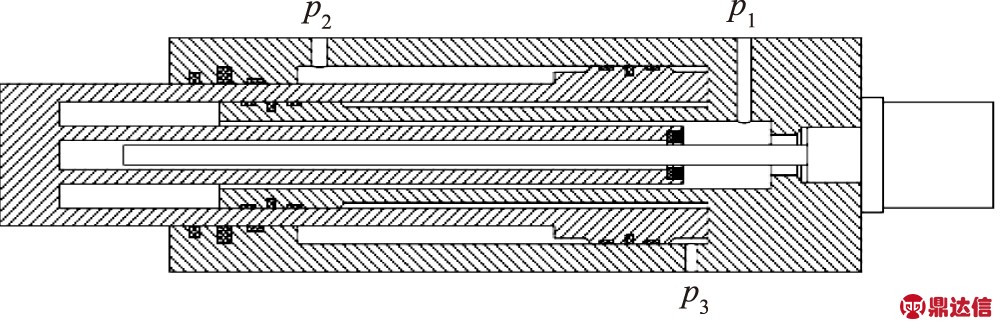
图2 单出杆对称液压缸内部结构示意图
1.3 密闭增压油箱
油箱采用全封闭式设计,内置弹簧和活塞,油箱内充入油液后,油液推动活塞,活塞压缩弹簧,通过弹簧的反弹力实现油箱的增压。活塞有机械限位,可防止油箱压力过高损坏齿轮泵外泄油口密封件。油箱内部结构如图3所示。由于油箱增压由弹簧实现,所以无论执行器如何放置,在弹簧的作用下都能保证油箱向闭式回路中正常补油。
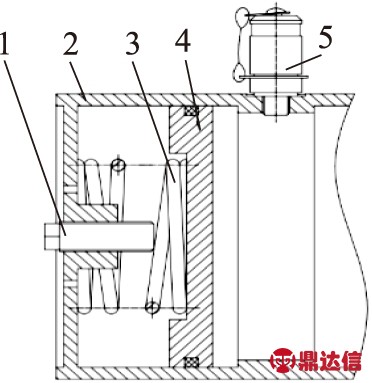
1.限位螺钉 2.油箱 3.增压弹簧 4.增压活塞 5.测压排气阀
图3 密闭增压油箱内部结构示意图
1.4 集成化总体结构
液压动力单元(包括交流伺服电机、集成阀组、液压泵、密闭增压油箱)一体化设计,其中液压泵内置于密闭油箱, 经由壳体和外泄口的油液直接回到油箱。伺服电机与液压泵固定在集成阀块的两侧,通过阀块中心通孔处的联轴器传递扭矩。此外,集成阀块直接固定在液压缸缸底上,油路均布置在液压缸壳体内部,实现了无管化设计。其整体结构如图4所示。
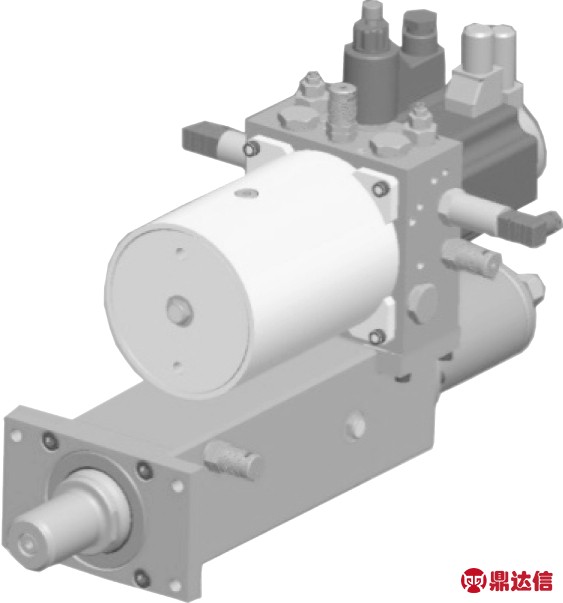
图4 整体结构图
2 AMESim/Simulink直驱式电液执行器控制系统联合仿真
以往采用典型泵控缸动力机构线性传递函数模型对于直驱式系统的计算和仿真,虽然简洁高效,但大都忽略了系统的死区非线性作用。本研究在AMESim/Simulink环境下搭建包含电机泵环节、补油环节、执行液压缸非线性摩擦等因素的系统复合模型,以更全面地模拟系统工作特性,重点是模拟液压促动器的死区非线性。
2.1 永磁同步电机传递函数模型
永磁同步电机的电压方程、转矩方程和运动方程如下:
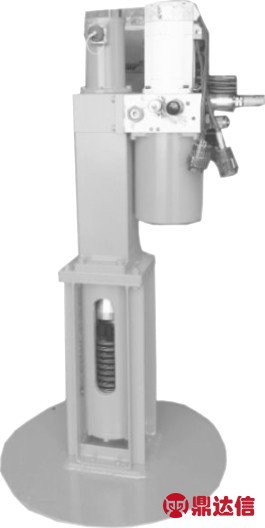
(1)
式中, Uq—— q轴电压,V
R —— 电机阻抗,Ω
儿童对成人图画书讲读有更倾向于心理和情感层面的期待和诉求。在图画书阅读中,儿童需要和成人一起经历阅读过程、唤起体验、增进趣味,享受亲密的情感氛围及沟通交流的愉悦,分享彼此的发现和体会,共同探索共同发现,这些都构成和加深了儿童阅读图画书的快乐体验。图画书讲读这一方面的目的和价值需要我们加以重视,不仅是在家庭开展的幼儿亲子阅读中,而且在学龄儿童的教室里,呼应儿童阅读心理、满足儿童的情感需求,也应确定为教师为学生讲读儿童图画书的出发点和重要目标。
KE —— 电机反电动势常数,V·(rad/s)-1
ωm —— 转子转速,rad/s
J —— 转子等效转动惯量,kg·m2
B —— 转子转矩黏滞系数,N·m·(rad/s)-1
iq —— q轴电流,A
ψf —— 永磁体磁链,Wb
Kt —— 转矩常数,N·m/A
Tm —— 转矩,N·m
TL —— 负载转矩,N·m
将式(1)进行拉氏变换,并将逆变器、控制器延迟简化为两个一阶延迟环节[7],时间常数为Ti和Tc。电机转速环和电流环控制器均采用PI控制器。各环节传递函数如式(2)所示:
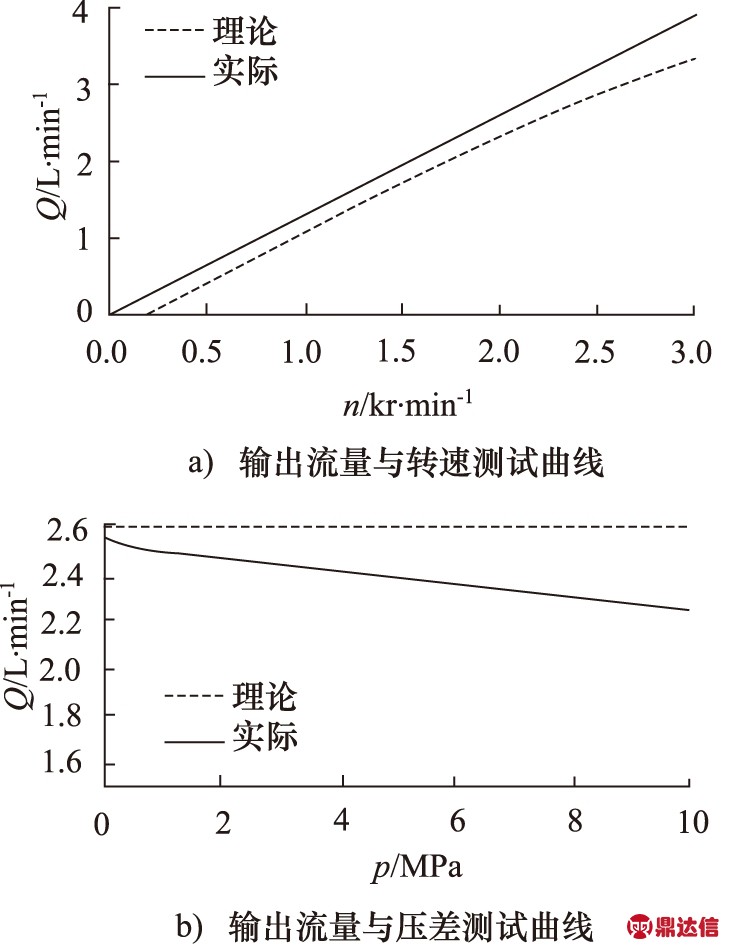
(2)
式中, GASR(s) —— 转速环PI控制器传递函数
GACR(s) —— 电流环PI控制器传递函数
Gic(s) —— 逆变器和数字控制器等效传递函数
GPMSM_C(s) —— PMSM电气部分传递函数
GPMSM_M(s) —— PMSM机械部分传递函数
εωm —— 角速度偏差
ksp —— 速度PI控制器比例参数
ksi —— 速度PI控制器积分参数
εiq —— 电流偏差
kcp —— 电流PI控制器比例参数
kci —— 电流PI控制器积分参数
2.2 泵控缸动力机构AMESim模型
为全面真实的反应系统在运行过程中的状态变化,建立了带外泄口的容积泵子模型和液控单向阀HCD子模型,使其仿真结果与样本参考特性曲线一致。
容积泵子模型如图5所示,在容积式泵理论模型基础上增加了外泄油口。
如图6所示为容积泵AMESim模型输出流量与电机转速、泵进出油口压差关系的测试曲线,测试结果与样本参考特性曲线基本一致。
如图7所示为容积泵AMESim模型输出扭矩与电机转速、泵进出油口压差的关系测试曲线,测试结果与样本参考特性曲线基本一致。
按照液控单向阀的内部结构,将阀分为壳体、液控活塞和球阀阀芯三部分,搭建出与之等价的HCD模型如图8所示。

图5 容积泵AMESim模型
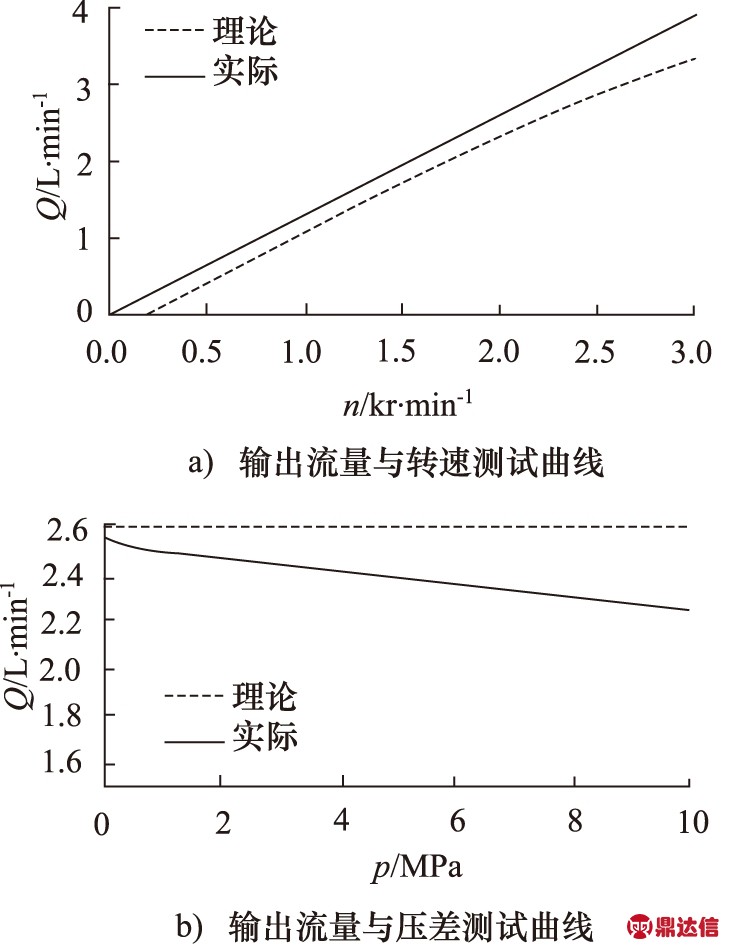
图6 泵输出流量测试曲线
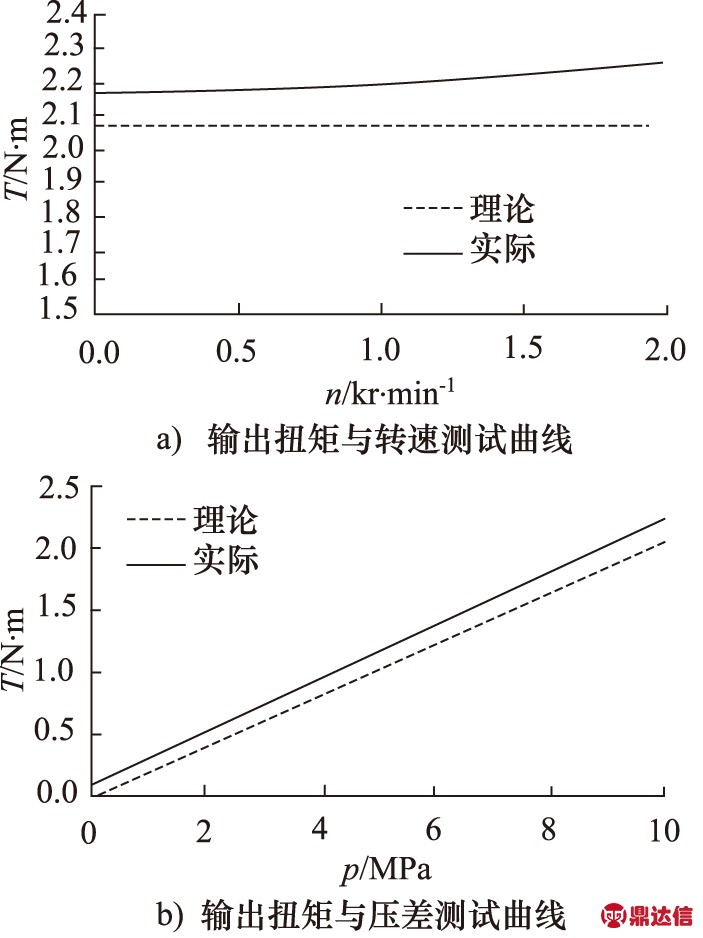
图7 泵输出扭矩测试曲线
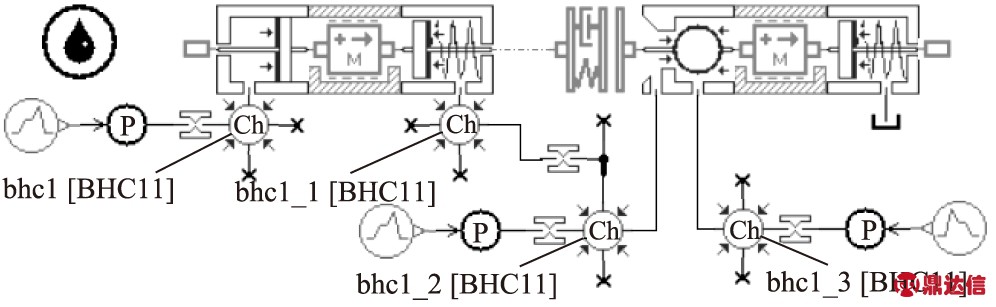
图8 液控单向阀AMESim HCD模型
经仿真测试,得到液控单向阀正向开启和液控开启时的压差-流量特性曲线,如图9所示,测试结果与样本参考特性曲线基本一致。
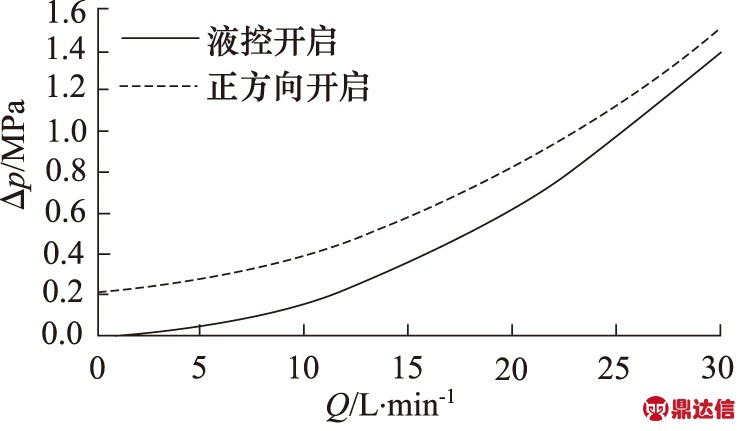
图9 液控单向阀稳态压差-流量特性测试曲线
子模型测试准确后,建立了泵控缸动力机构AMESim总模型[8],如图10所示。
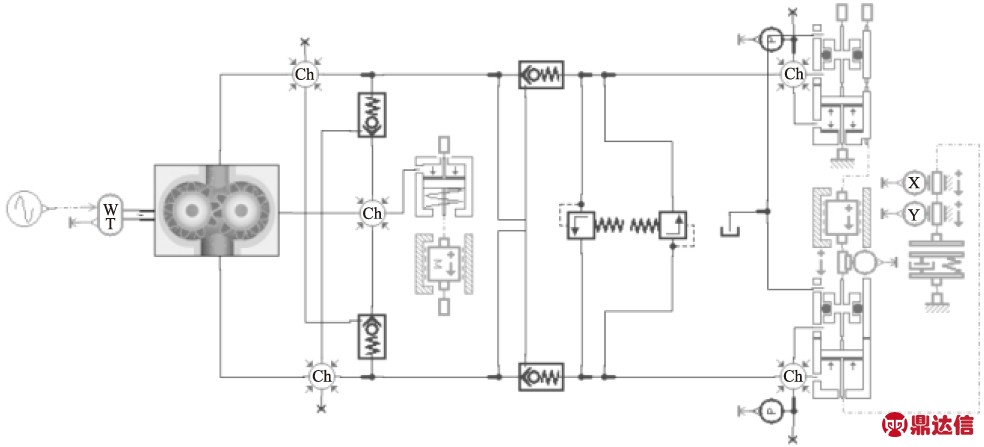
图10 泵控缸AMESim总模型
给定幅值为3000 r/min,频率为1 Hz的电机转速正弦信号,得到泵控缸位移响应和速度响应曲线分别如图11和图12所示。相比于传统的泵控缸线性传递函数模型,可以看到泵控缸AMESim模型位置响应略微有些滞后,总体而言执行器速度与电机转速满足线性关系。但在正反方向运动切换时,存在明显的死区非线性。
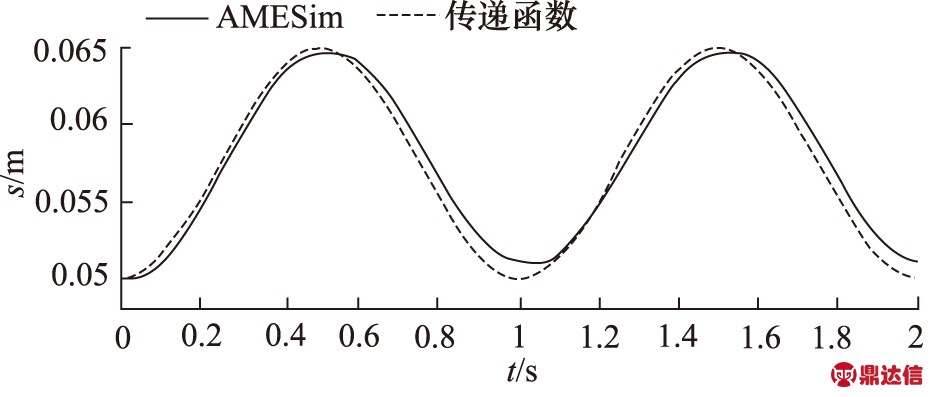
图11 泵控缸位置响应曲线
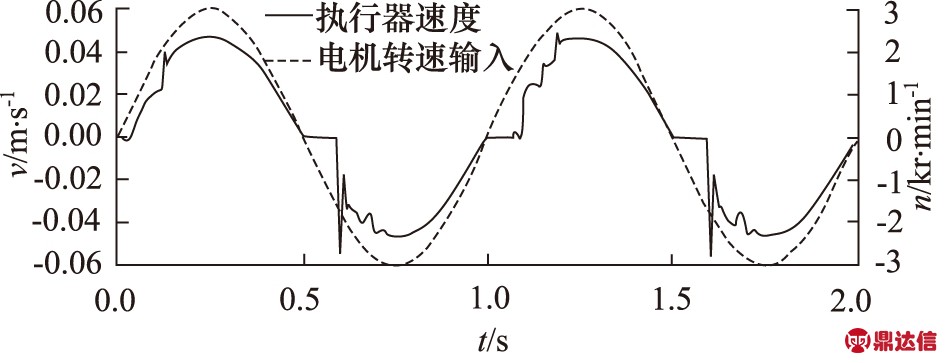
图12 泵控缸速度响应曲线
这种死区非线性作用不仅是由于泵低速供油不足,而是泵低速特性、补油环节吸排阀切换作用、双向液压锁切换作用以及管路动态特性等共同作用的结果。图13为泵吸排油口的压力响应曲线,在电机换向之后,泵吸油口压力迅速降低,但此时补油环节尚未起作用,泵吸空是导致执行器产生死区非线性的一个原因。短暂的延迟后,补油环节起到作用,使吸油口压力恢复正常,执行器正常工作。这同时表明了增压密闭油箱无动力补油是有效的。
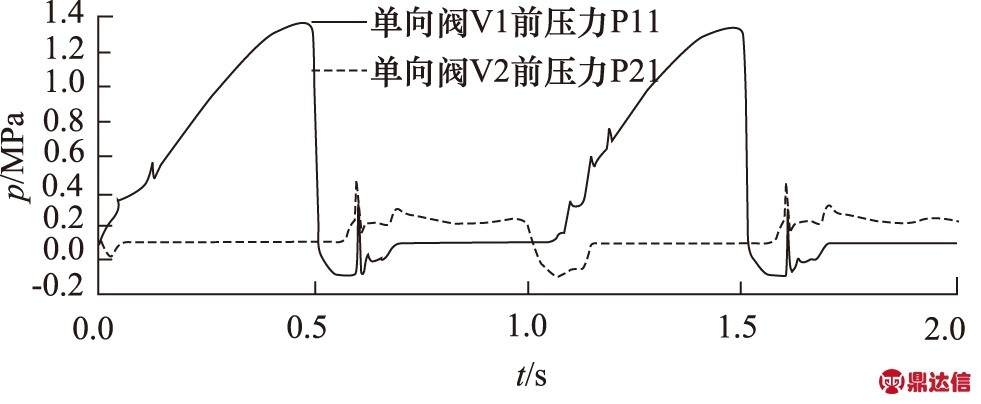
图13 泵吸排油口压力响应曲线
2.3 AMESim/Simulink联合仿真
将泵控缸AMESim模型封装成S函数,与永磁同步电机传递函数模型组成系统复合模型,采用经典PID控制器在Simulink中进行仿真分析(见图14)。同时与传统的泵控缸线性传递函数模型进行对比分析。仿真结果与实验结果如图15、图16所示。
3 实验研究
为了验证联合仿真模型的合理性,搭建了系统实验硬件平台,包括样机主体结构、加载弹簧支座、电气驱动、测量系统以及DSP集成开发电路。软件方面,在CCS集成开发环境下编写DSP实时控制程序,在上位PC机LabVIEW中编制采集和控制程序,然后通过以太网通讯实现上下位机的互联。如图17所示为实验系统组成结构图。
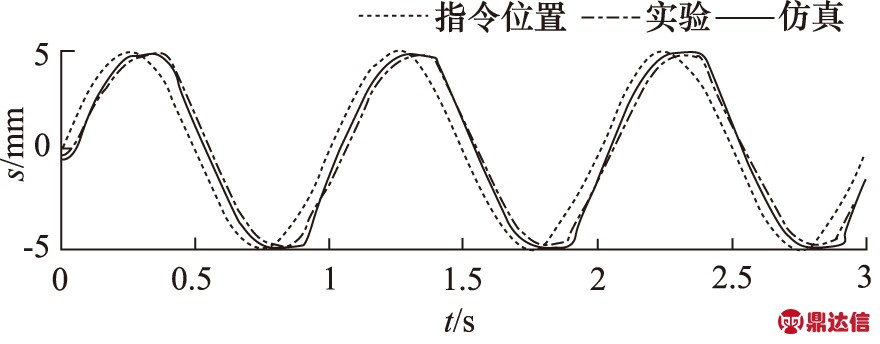
图15 位置跟踪实验和仿真对比
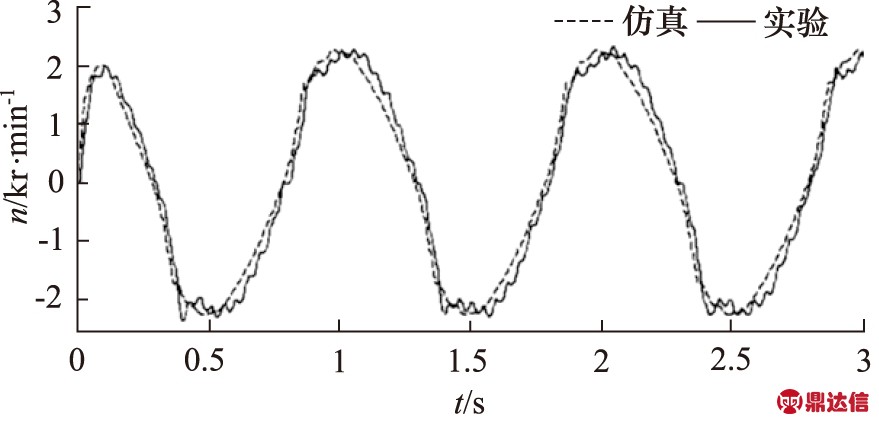
图16 电机转速实验和仿真对比
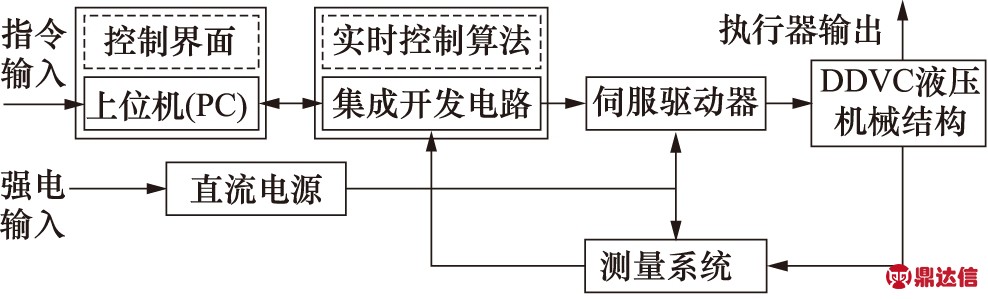
图17 实验系统组成结构图
如图18所示为系统实验样机实物图。单出杆对称液压缸:缸径70 mm、活塞杆外径56 mm、活塞杆内径42 mm、行程100 mm、额定压力10 MPa;电机功率750 W;泵排量1.3 mL/r;采用碟形弹簧模拟弹性负载,碟形弹簧组弹性刚度260 N/mm、最大负载力13 kN、最大压缩行程54 mm。
按照仿真实验中的控制器参数进行配置,进行正弦位置跟踪实验,并与仿真结果对比,如图15所示。可以看出,实测的位置跟踪曲线与仿真曲线在执行器换向时皆产生死区非线性,并且两者拟合度较高。
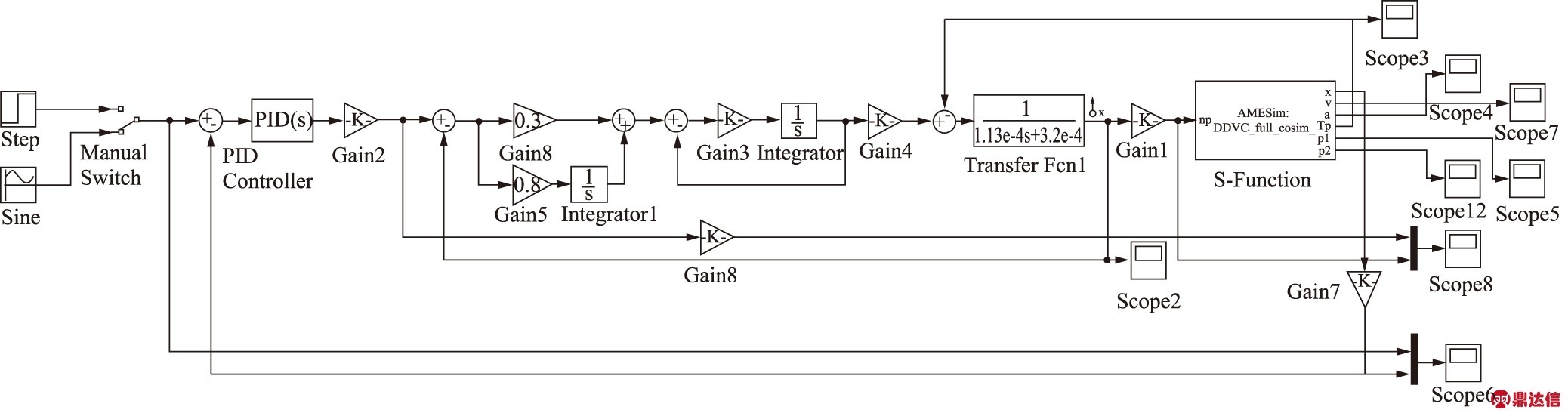
图14 AMESim/Simulink联合仿真模型
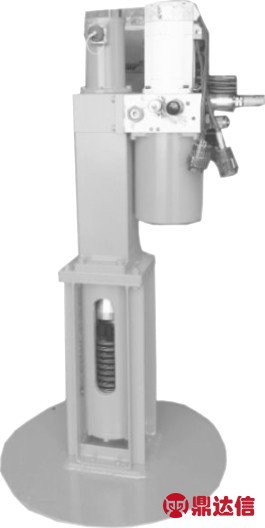
图18 系统实验样机
伺服电机转速仿真和实验对比曲线如图16所示,可以看出实测的伺服电机转速与仿真曲线拟合度也很高。通过图15和图16的对照关系,电机换向后,迅速反向加速以补偿执行器死区非线性产生的位置跟踪偏差,从而验证了系统AMESim模型中对于形成系统死区非线性仿真的正确性。
同时,分别在执行器处于空载和加载(2.6 kN和7.8 kN)时,进行正弦位置跟踪实验,以观察外负载力对死区非线性的影响,实验结果如图19所示。可以看出,空载时,死区非线性较小,引入外负载力后,死区非线性加剧,同时,随着外负载的继续增加,死区非线性保持在一定范围、变化不大。
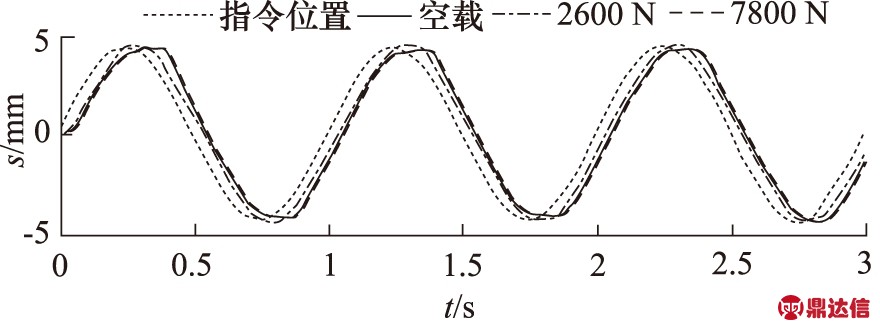
图19 变负载正弦位置跟踪实验
4 结论
(1) 新型直驱式单出杆对称液压促动器具有控制灵活性、出力大、无溢流节流损失、发热量低、效率高、正反向运动特性相同等优点,适合应用于FAST等场合;
(2) 通过系统非线性AMESim/Simulink联合仿真模型的仿真分析,并与传统线性传递函数模型比较,发现系统存在明显的死区非线性,产生的原因为在电机换向后,泵吸油口压力迅速降低,但此时补油环节尚未起作用,泵吸空导致死区;
(3) 通过实验对仿真模型进行验证,实验结果与仿真结果拟合程度较高,验证了系统联合仿真模型的准确性。建立了从结构设计,到软件平台仿真,最后到实际测试直驱式系统模型的对应关系,为后续直驱式产品的设计研发提供了重要参考。