摘要:为了获得运动型排气噪声,本文研究了汽车排气系统消声器结构对运动声学品质的影响。通过改变消声器的内部结构,建立与之对应的GT-Power模型,利用一维流体动力学原理对排气系统的声学性能进行模拟和仿真,并运用声学测试平台测试节气门全开加速时的尾管噪声。验证了去除排气系统的中排消声器并在后排消声器内加入消声棉的结构,可明显提高噪声的运动性,另外,消音棉的利用可以有效降低高频噪声,消声器进气管处的穿孔结构可以有效消除中低频噪声。
关键词:汽车排气系统,GT-Power,消声器设计,排气噪声实验
1 引言
汽车排气系统的噪声是汽车噪声的重要组成部分,排气系统可以看成是由管道和声学元件组成的系统,这些元件使得一些频率的声波通过,同时也阻止了另一些频率的声波,从而达到消音效果[1]。在排气系统的设计中,声学性能的实现是其重要的设计目标之一。目前国内汽车排气系统还主要停留在降低噪声的阶段,但是如何让声音听起来舒服,满足特定客户群要求的研究还比较少。
汽车噪声主要分为豪华型噪声、力量型噪声和运动型噪声。豪华型噪声主要以低声压级、发火阶次及其谐阶次为主导,半阶次成分少,给人平稳的感受。力量型噪声主要以发火阶次贡献的噪声为主导,有一部分半阶成分,给人动力充足,响应迅速的感受,其噪声频率成分以100~500 Hz为主,其中在180~300 Hz之间的声音最强,发动机转速一般为2000~4500 rpm。运动型噪声是在力量型的基础上增加半阶次成分,提高半阶次能量占比,无主导阶次,发火阶次及其谐次成分量级差不多,没有占绝对分量的阶次,其声压级高,声音明亮、有赛车的声音,发动机转速一般在3000 rpm以上[2]。
本文以某车型的排气系统设计为例,利用一维流体分析软件GT-Power对其声学特征进行仿真分析,研究优化结构方案能否满足运动型噪声的要求。制作试验样件进行声学的测试,比较试验结果与仿真结果,验证运动型噪声的实现情况。
2 排气系统结构设计
某车型系统噪声为力量型噪声,所分析车型匹配的发动机为1.4 L、110 kW涡轮增压汽油发动机,该车型排气系统如图1所示。该系统采用两级消声器设计,后消声器采用迷管型,内部不安装消音棉,如图1(c)所示。
为了使该汽车噪声变为运动型噪声,对原有的设计进行了两种方案的改进设计。由于运动型噪声声压级高,声音明亮,故改进方案取消了中间消声器,如图2(a)所示。又由于运动车型在工作时,主要转速在3000 rpm以上,应当避免高频的噪声,给人低沉有力的感受,所以改进方案中的第一种方案在后级消声器中添加了消音棉,用以减低高频噪声[3],如图2(b)所示。改进的第二种方案在第一种方案的基础上在进气管上设计两排穿孔,并减小出气管穿孔的长度[4],如图2(c)所示,声波从进气口进入后一部分通过小孔进入消声器第一腔,由于声波通道截面积的变化,造成声抗的改变,从而增加消声器的传递损失。
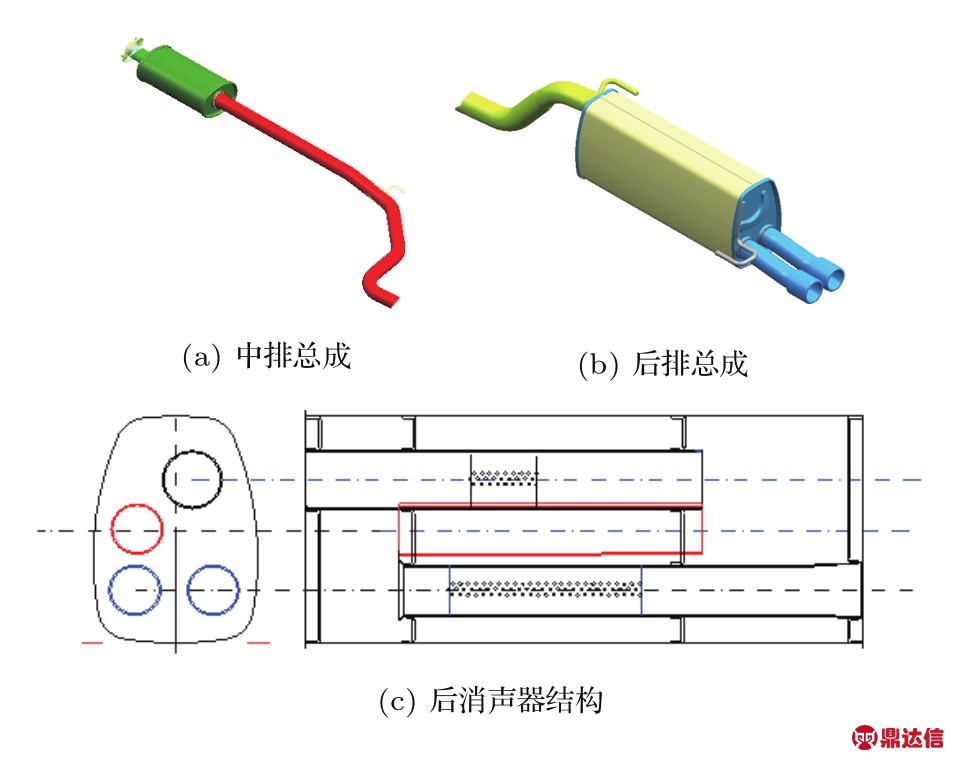
图1 原始双消声器设计方案图
Fig.1 Original double muffler layout
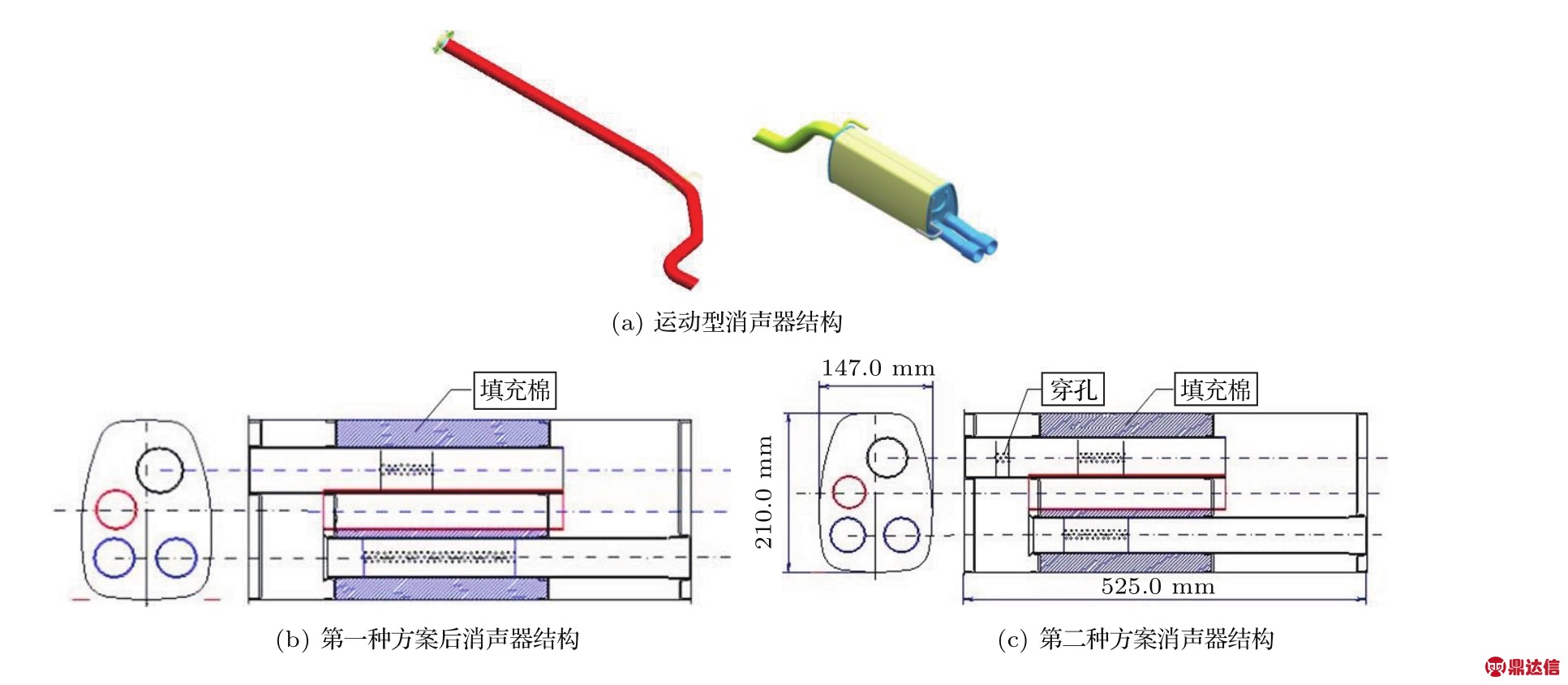
图2 运动型噪声设计方案图
Fig.2 Sportive noise muffler layout
3 一维流体模拟
运用GT-Power将结构设计转变成一维流体模型并计算以上三种不同结构下的尾管二阶、四阶、六阶噪声情况。二阶、四阶、六阶噪声指由发动机二阶、四阶、六阶振动引起的噪声。以发动机的转频为基频(即第一阶),其陪频为二阶;对于转速为n的4缸发动机,一阶频率为n/60 Hz,二阶频率为2n/60 Hz,四阶频率为4n/60 Hz,六阶频率为6n/60 Hz。计算结果如图3所示。
由图3(a)整体噪声可知,方案一和方案二取消了中间消声器后,在发动机低转速情况(1800 rpm~2500 rpm)下,噪音分贝值比原有设计方案有所下降,在2000 rpm时,噪声降低得最多,最大达到7 dB。随着发动机转速逐渐提高,当转速超过2700 rpm时,改进后的单消声器方案的分贝值要明显大于原来使用两个消声器的方案,在3500 rpm时方案一比原双消声器结构的分贝值提高了8 dB。
对比使用单消声器的方案一和方案二,方案二的整体噪声分贝值在较低转速阶段(1700 rpm~2500 rpm)时低于方案一,当转速超过3000 rpm时,分贝值要大于方案一,提升整车噪声的运动感,这也验证了消声器进气管处的穿孔结构可以用于低频的消音。
由图3(b)–图3(d)可以看出,在低转速时,三种方案的发动机二阶振动噪声、发动机四阶振动噪声基本相同,方案二的发动机六阶振动噪声要高于原始方案和方案一;高转速时,方案二的发动机二阶振动噪声要略低于原始方案和方案一,但是方案二的四阶和六阶噪声要明显高于原始方案和方案一。另外,改进结构后的方案二噪声的发火阶次及其谐次噪声分量级基本一致,不再是某个阶次噪声占主导地位,说明方案二的结构更加符合运动学噪声的要求。
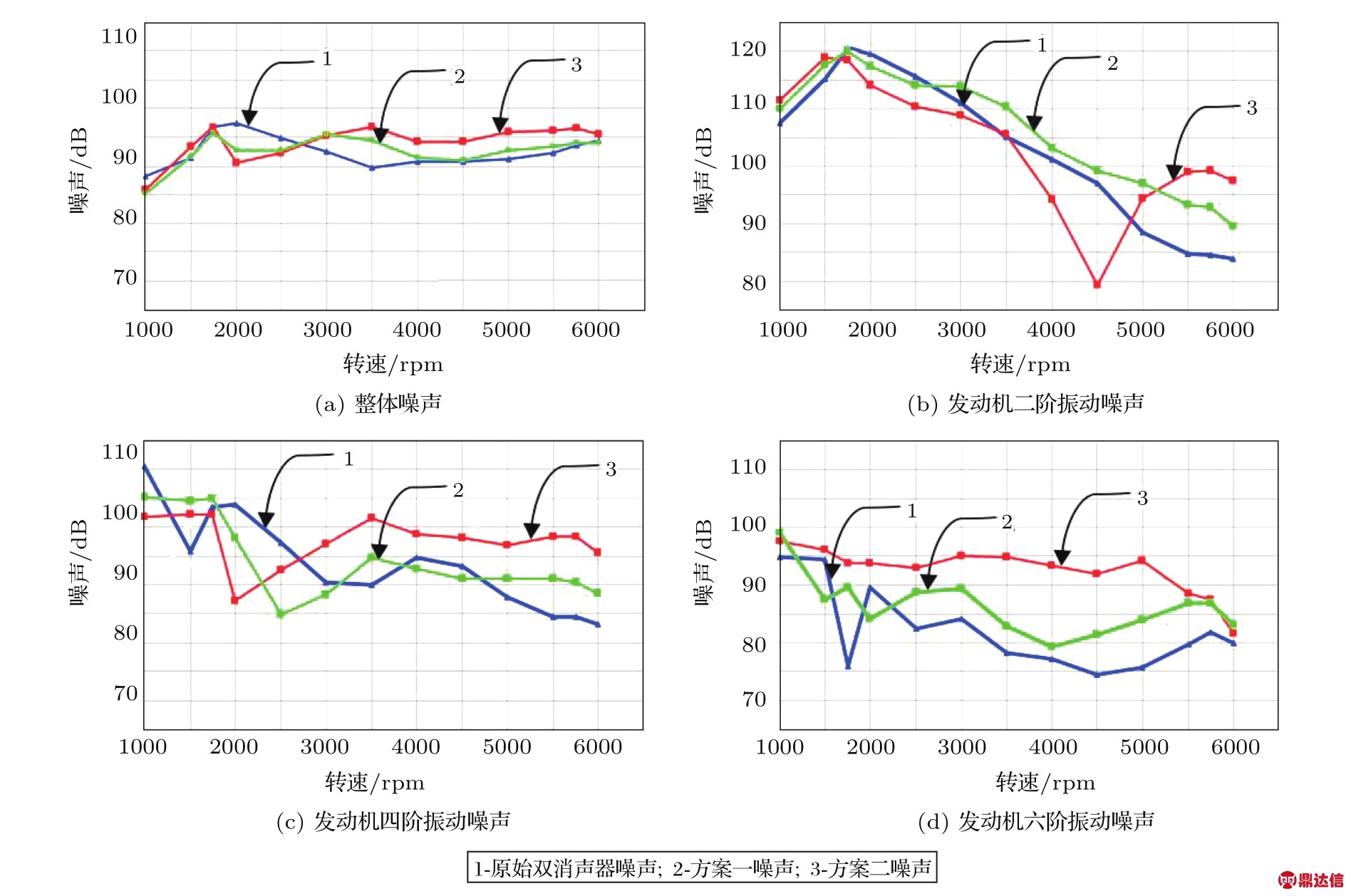
图3 GT-Power计算的尾管噪声
Fig.3 Tail pipe noise in GT-power simulation
4 尾管噪声试验
根据双消声器和单消声器设计方案进行实际测试。将实验车辆及测试设备置于半消声室中,在转毂试验台上对排气系统的尾管噪声和辐射噪声进行测定,实验时使监视器上的水温低于工作温度(<80°C)。将麦克风与尾管中心线呈45°倾斜放置,并距离500 mm,如图4所示。将变速器置于3档,汽车节气门全开,使发动机转速从最低稳定转速增加到6000 rpm,获取声音的实时测量值,如图4所示。
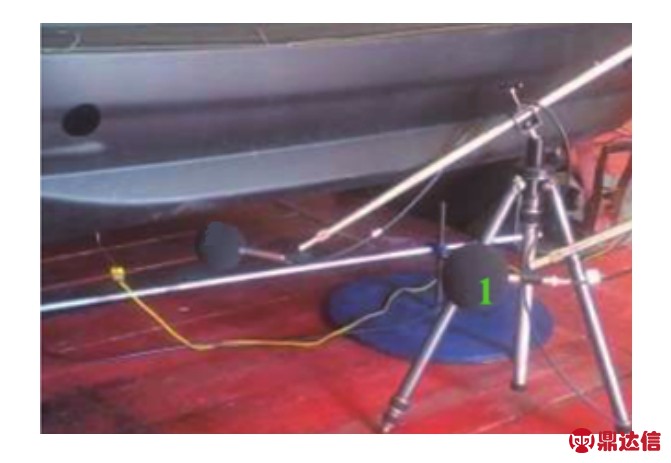
图4 尾管噪声试验
Fig.4 Test of tail pipe noise
输入所有关于测试车辆和排气管的噪声曲线,得到实测的汽车排气尾管噪声,检查测试数据的一致性,取3~5组测试数据的平均值作为测试结果。与GT-Power的模拟计算值作对比。采集到的整体噪声和发动机二阶、四阶、六阶振动尾管噪声如图5所示。
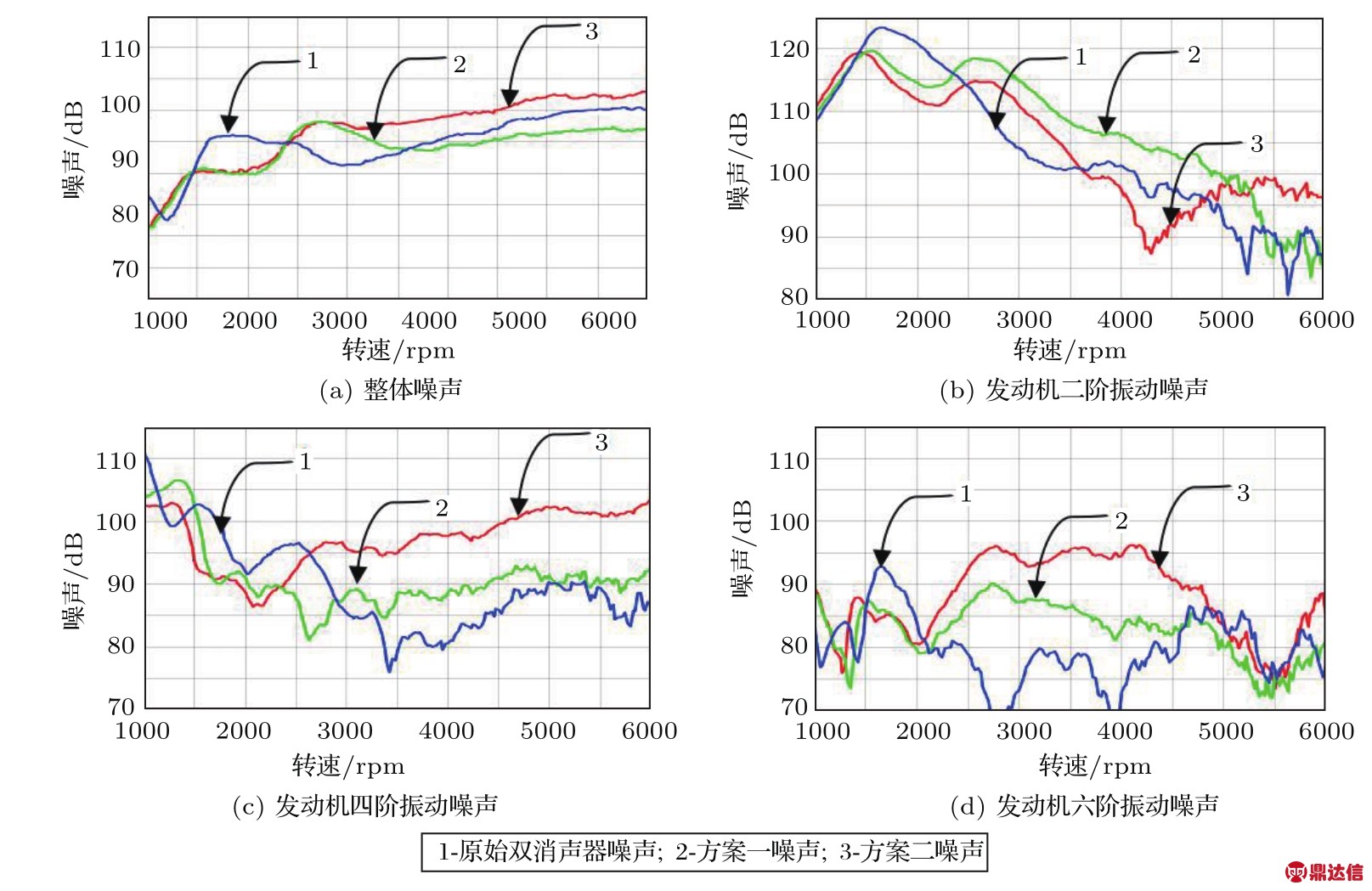
图5 尾管噪声节气门全开试验阶次图
Fig.5 The WOT acceleration order of tail pipe noise
从图5可以看出试验测量结果基本与GTPower分析结果基本一致,图5(a)可知,方案二在发动机转速为1000 rpm~1500 rpm时,整体噪声值线性上升至90 dB。发动机在1500 rpm~2000 rpm时,噪声值稳定,当发动机转速在2000 rpm~3000 rpm时,噪声迅速提高至98 dB,并在3500 rpm时降至93 dB,之后分贝值趋于平稳。通过图5(b)–图5(d)可知,对整体噪声,发动机转速在1000 rpm~1500 rpm时,二阶振动噪声贡献的最大,当转速超过2500 rpm时,各阶次噪声无主导阶次。实验结果也说明在改进消声器结构后,能够得到较良好的运动型噪声。
为了更直观的展现噪声的特性,将尾管噪声值利用Colormap图的形式表示,如图6所示。通过Colormap图将噪声、发动机转速、频率同时显示,可以清晰全面的反映当前的振动或噪声状态,进而进行优化设计或者是故障诊断[5]。在Colormap图中,x轴向变量为发动机转速、y轴向数值为FFT变换下的噪声频率。而在x-y区域内则对应噪声的大小数值,通过颜色的深浅来表示[6]。
从尾管噪声的Colormap图中可知,在采用双消声器结构的原始方案中,在发动机低转速区间,低频率的发火阶次噪声分贝占主要噪音,其余阶次噪声份量很少,运动型噪声效果差。在发动机转速约3500 rpm以上时,原始方案开始出现3000 Hz~10000 Hz范围的高频噪声,这些高频噪声容易造成发动机噪声品质变差,出现杂音。
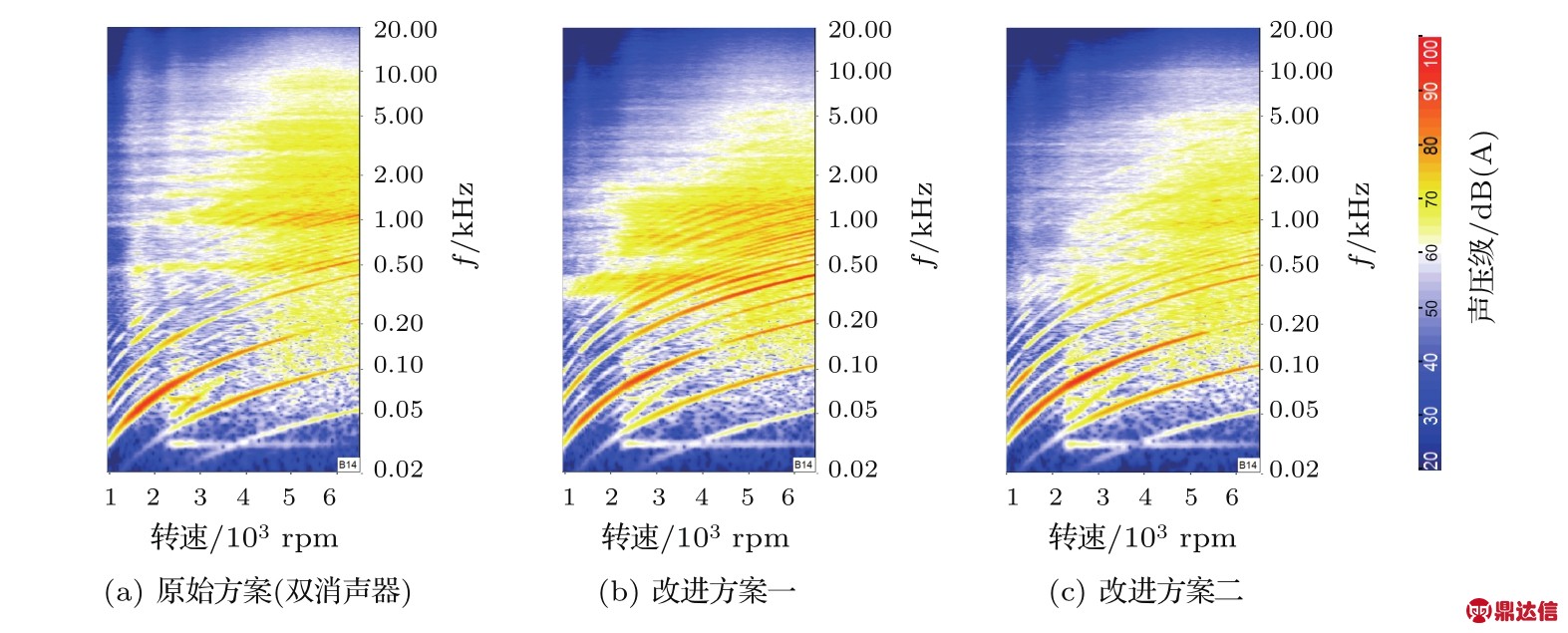
图6 尾管噪声节气门全开加速试验Colormap
Fig.6 The Colormap of WOT acceleration of tail pipe noise
采用单消声器的第一种方案时,除发火阶次外,其余谐次频率的分贝值也增高了,增加了半阶次的能量占比,声音的线性度也提高了,这种声音会更加动感清亮[7]。因为添加了消音棉,3000 Hz以上的高频噪声基本消除。但是在1000 rpm~2000 rpm转速范围内会有约400 Hz的噪声,在2000 rpm~4000 rpm转速范围内出现较多的500 Hz~1800 Hz的噪声,这使得该方案在低转速阶段的噪声品质变差。
第二种方案中加入进气管穿孔结构后,在整个转速范围内中高频杂音都基本被消除,同时各阶次噪声所占份量接近,运动型噪声性能良好。
5 结论
(1)通过GT-Power一维流体模型和实验分析可知,去除排气系统的中排消声器并在后排消声器内加入消声棉后,排气系统整体噪声在发动机低转速时变化不大,在发动机高转速时整体噪声有略微增大。
(2)将后排消声器改为进气管处穿孔结构的方案二相对另外两种方案,各阶次噪声对整体噪声的影响更加均衡,可明显提高噪声的运动性。
(3)Colormap图的分析研究表明,消音棉的利用可以有效降低高频噪声,进气管处的穿孔结构可以有效消除中低频噪声。
(4)通过试验测试验证了使用单个消声器的改进方案可以达到消音的要求。同时,提供了一种运动型噪声品质汽车消声器的设计思路。