摘 要:利用夹杂物示踪、系统取样、扫描电镜及能谱分析研究了轴承钢GCr15中D类和DS类夹杂物来源和夹杂物形成的演变规律,分析了夹杂物的成分、形貌、平均粒径大小和夹杂物数量的变化,为优化生产工艺,冶炼高质量轴承钢提供必要的理论依据。
关键词:轴承钢;夹杂物;来源
轴承钢的工作条件极为复杂,承受着各种高的交变应力,如拉力、压力、剪力和摩擦力等,为保证其较长的使用寿命,钢中的氧化物夹杂、硫化物夹杂、点状夹杂、碳化物(如碳化物液析、条状碳化物、带状碳化物及网状碳化物等)[1-4]的不均匀性都有严格要求。
轴承钢中D类DS类夹杂物是不变形夹杂物,对轴承钢的疲劳寿命极为有害,在实际生产中应采取手段控制该类夹杂物的产生。目前某特钢采用转炉—LF—VD—软吹—CC流程生产轴承钢,但是存在D类DS类夹杂物超标的现象,为此对其轴承钢GCr15的生产采用夹杂物示踪和系统取样等技术来探索轴承钢中D类DS类大颗粒夹杂物来源和夹杂物形成的演变规律,为冶炼高质量轴承钢生产提供必要的理论支持。
1 试验方案
钢中非金属夹杂物的来源非常复杂,为了确定夹杂物来源采用示踪剂进行追踪。在钢包渣、中间包覆盖剂、中间包打结料中分别加入碳酸钡、氧化镧、氧化铈等示踪元素进行夹杂物来源分析[5]。
为全面了解整个生产过程中各工序钢水洁净度的变化,进行了现场生产试验,在LF—VD—CCM—成品过程中取3炉分别取提桶样,将提桶样加工成气体棒、钢屑、和金相样,并取一定渣样。气体棒加工规格为Φ5×25 mm;未氧化的钢屑取样20 g分别为CCM1、CCM2、CCM3;金相样由自动磨样机制样;炉渣样分别为VD1-1、VD3-1、LF3-1,以用于全面分析夹杂物来源。试样选取具体工序位置如表1所示。
为进一步检验钢中夹杂物的种类、形貌和大小分布情况,本研究制备电镜样,采用SEM进行观察,并结合能谱分析,观测方法为在电镜放大300~400倍的视野下,按照从左到右逐行进行观测,看到有比较明显的夹杂物之后再进行放大倍数观测,每一个金相试样观测找出20~30个夹杂物,通过能谱分析出夹杂物的成分、大小、形貌;利用扫描电镜Feature功能,选取100个视场,在放大1 000倍的情况下扫描观测夹杂物特征,分析了夹杂物的平均粒径大小变化和夹杂物数量的变化。
表1 系统取样方案

2 试验结果和分析
2.1 冶炼过程夹杂物行为的分析
2.1.1 LF喂铝前
LF喂Al线前的典型夹杂物的典型形貌和成分见表2。
表2 LF喂Al线前的典型夹杂物的典型形貌和成分
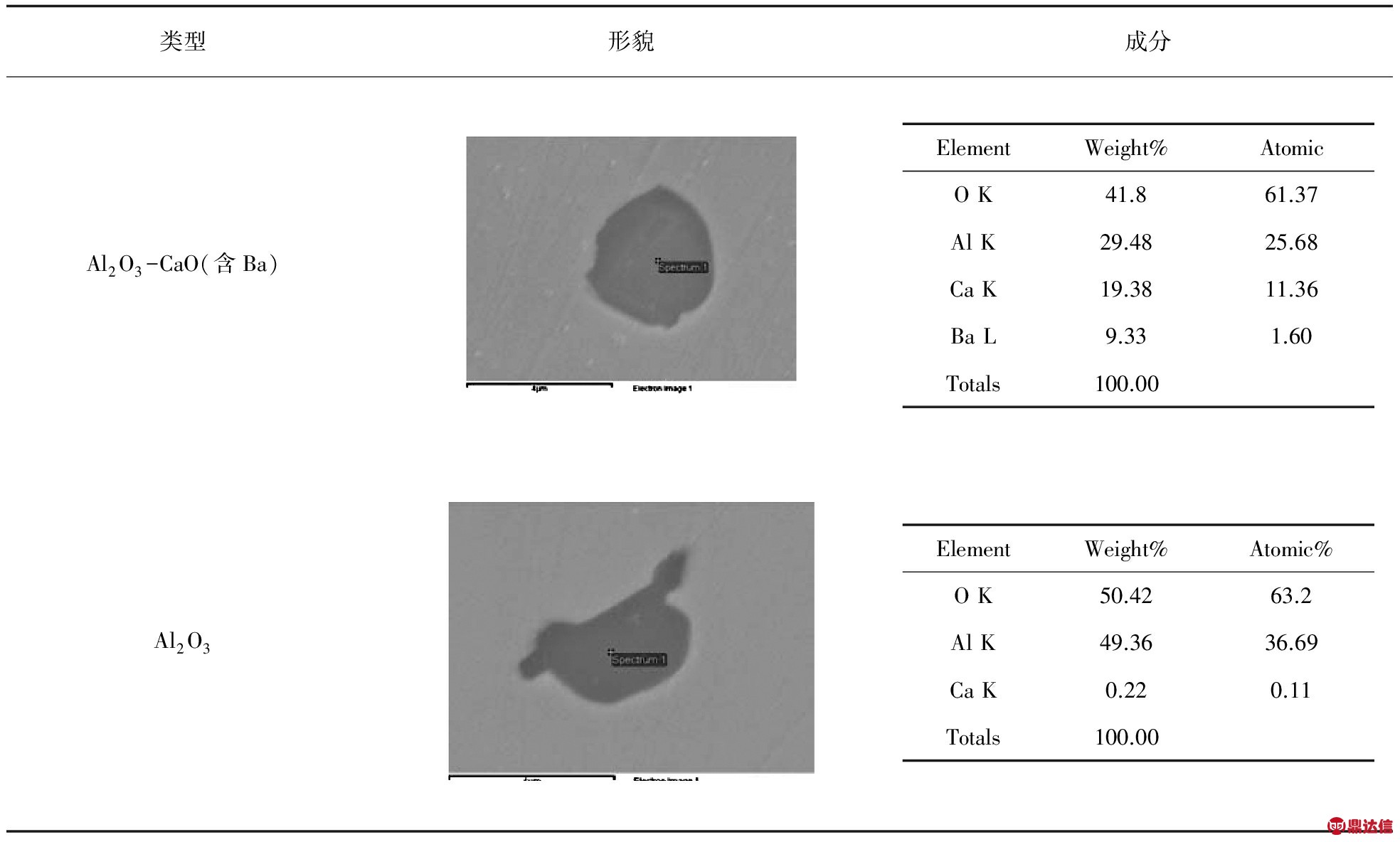
可以看出在LF喂线前主要是Al2O3夹杂,不含有Mg元素;在此夹杂物中含有Ba元素的夹杂物是Al2O3-CaO夹杂,说明该夹杂可能来自于钢包渣,在转炉出钢之后加入一批石灰,石灰没有来得及熔化就进入夹杂物了,造成该成分中含有一定量的CaO。
2.1.2 LF喂铝后
LF喂铝后的夹杂物典型形貌、成分见表3所示。
LF喂Al线后主要夹杂物是MgO-Al2O3,以及少量的MgO-Al2O3-CaO,MgO-Al2O3基本不含有Ba,说明其主要是内生夹杂物,而MgO-Al2O3-CaO有的含有Ba元素其可能来源于钢包渣中;另外相对比于喂铝之前,在喂铝之后出现了Mg元素,有可能是渣中的MgO或者是钢包中耐材镁碳砖中的Mg被还原出来,从而造成钢中Mg含量上升。
2.1.3 LF精炼结束
LF精炼结束时的夹杂物典型形貌、成分见表4所示。
表3 LF喂铝后的夹杂物典型形貌、成分
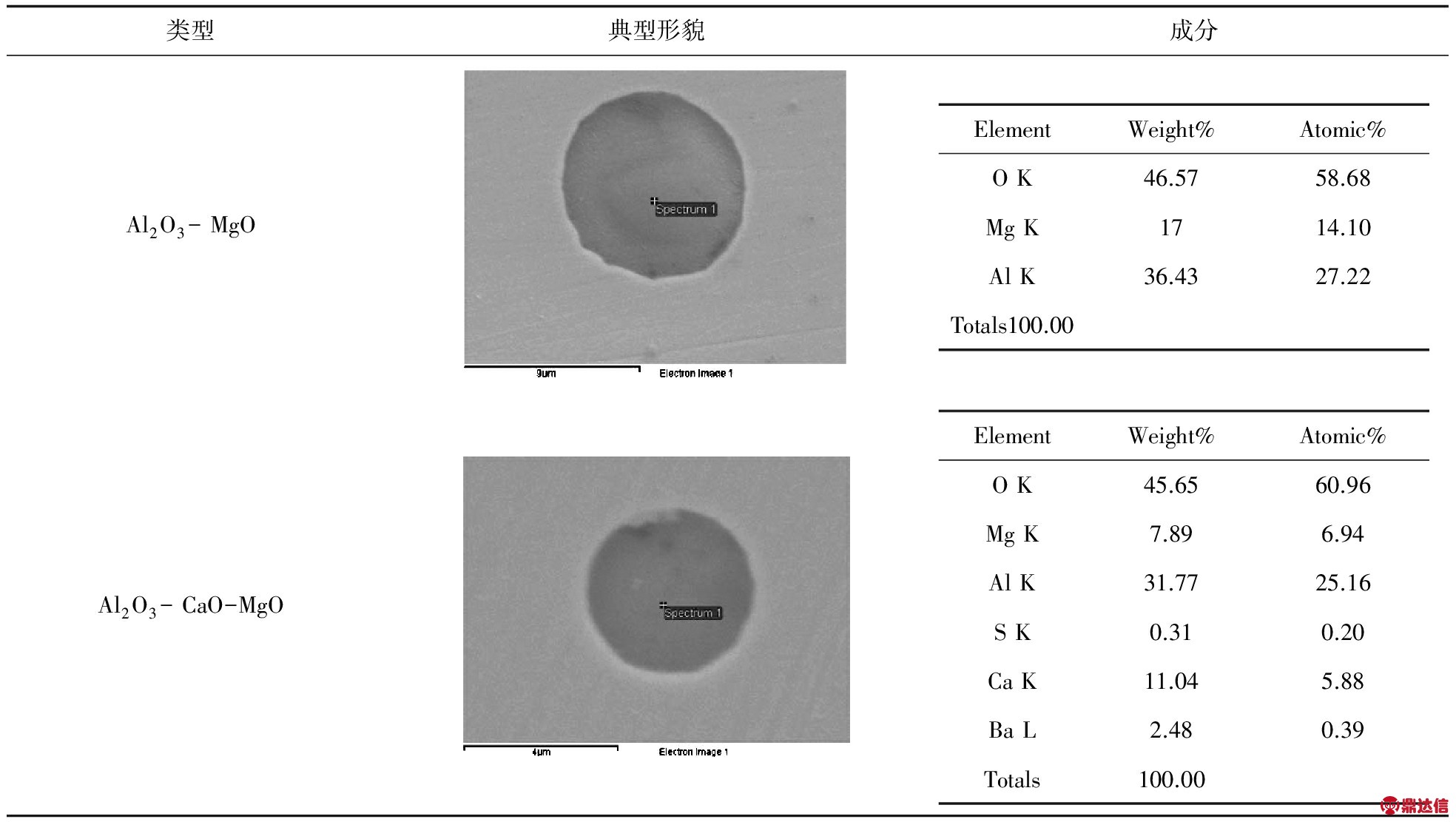
表4 LF精炼结束时的夹杂物典型形貌、成分
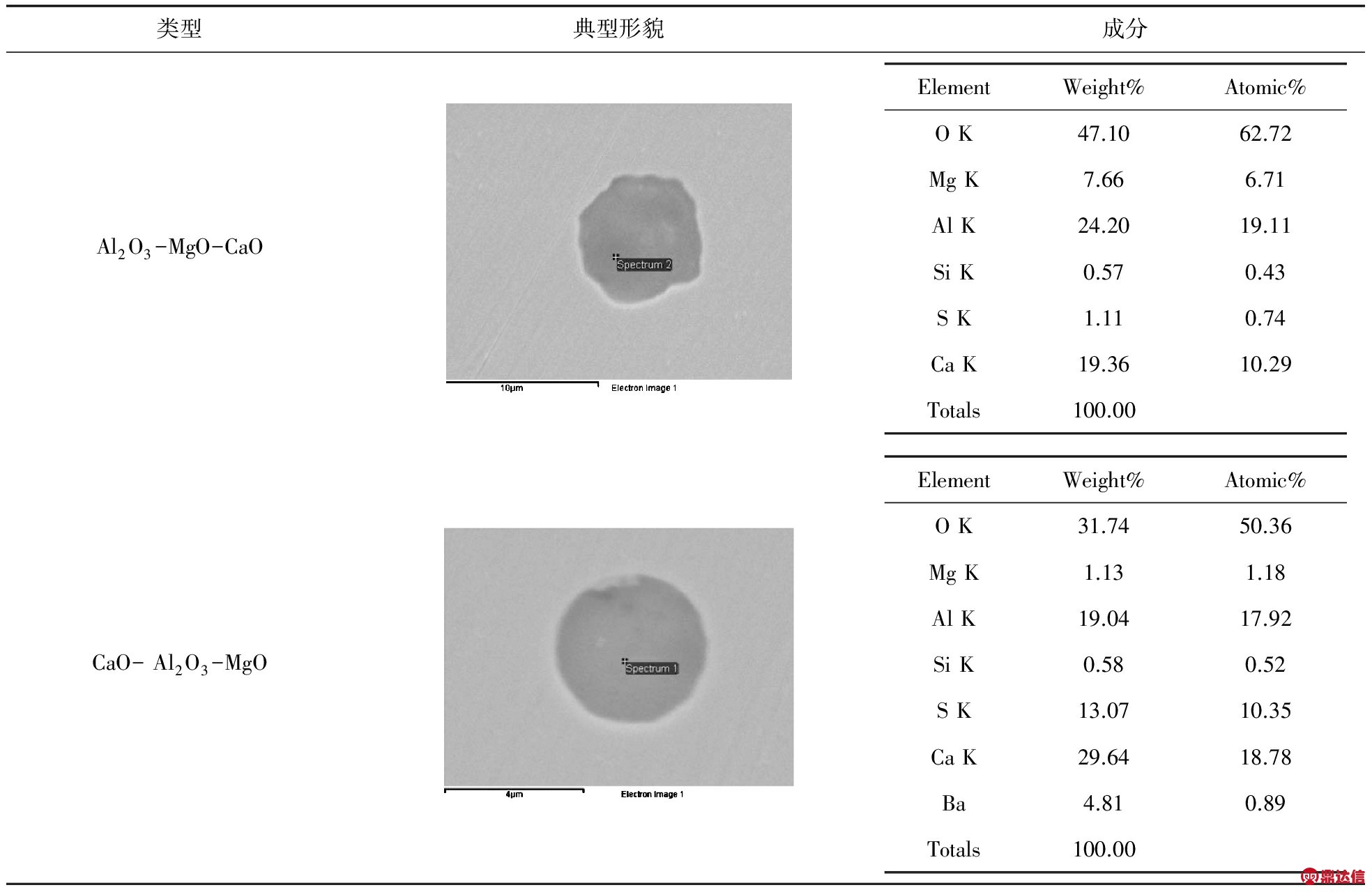
可以看出LF结束后夹杂物中主要以Al2O3-CaO-MgO夹杂物为主,说明随着LF精炼的进一步进行,由于钢水中残余的Ca、Mg的元素的存在,以及电极的还原、钢包耐材的影响,造成夹杂物成分逐渐发生变化,而向复合夹杂物转变。
2.1.4 VD破空、VD软吹12分钟、VD出站和连铸中间包
VD破空、VD软吹12分钟、VD出站、连铸中间包时的夹杂物典型形貌、成分见表5所示。
表5 VD破空、软吹12分钟、出站和连铸中间包时的夹杂物典型形貌、成分
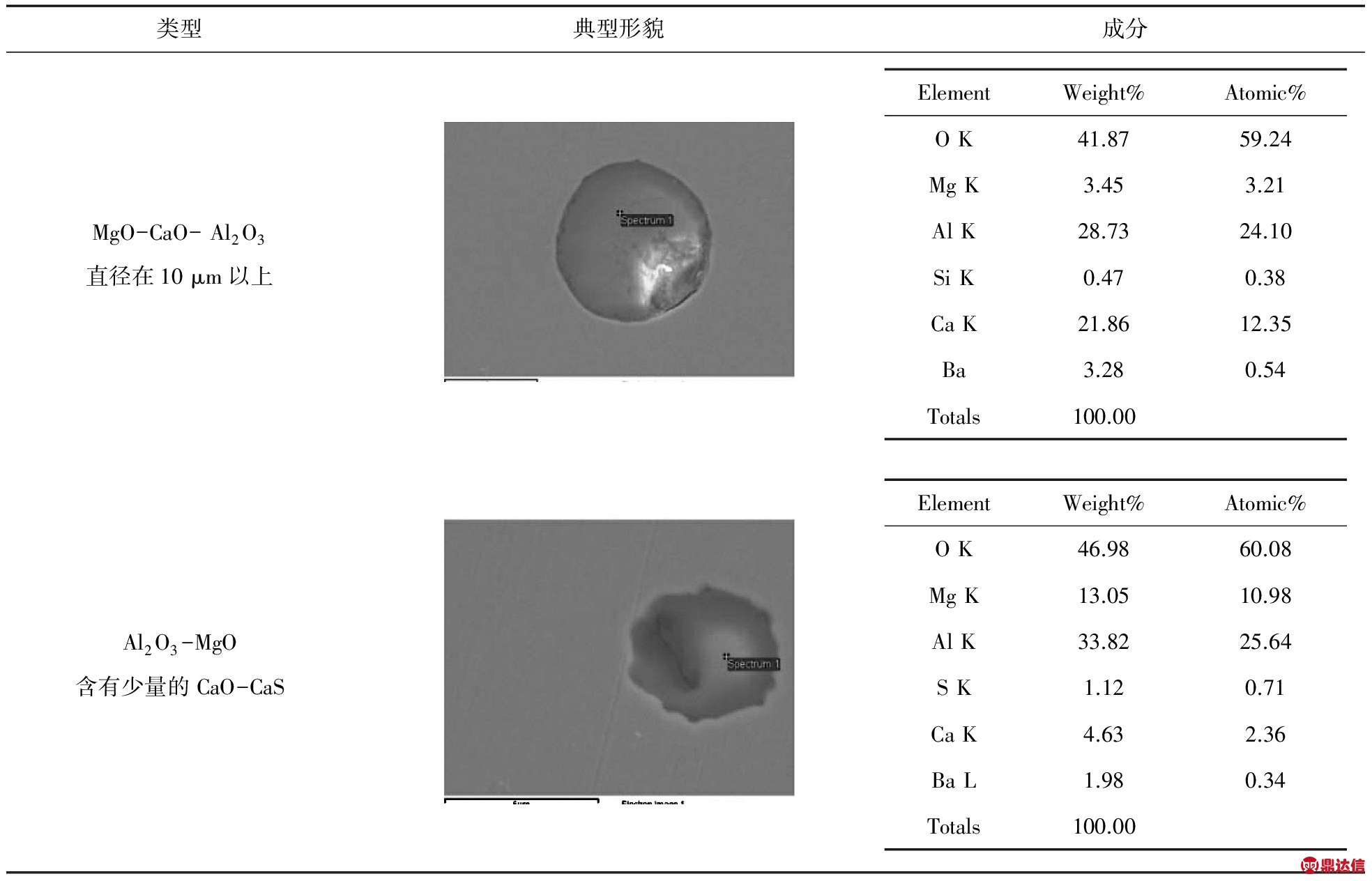
VD上台夹杂物类型是MgO-CaO- Al2O3为主,有的伴生一些硫化物等夹杂,夹杂物基本上为球形夹杂物。 Al2O3含量在80% 左右,MgO质量分数和CaO质量分数在有一定的波动。
2.1.5 棒材
棒材中的夹杂物典型形貌、成分见表6所示。
表6 棒材中的夹杂物典型形貌、成分
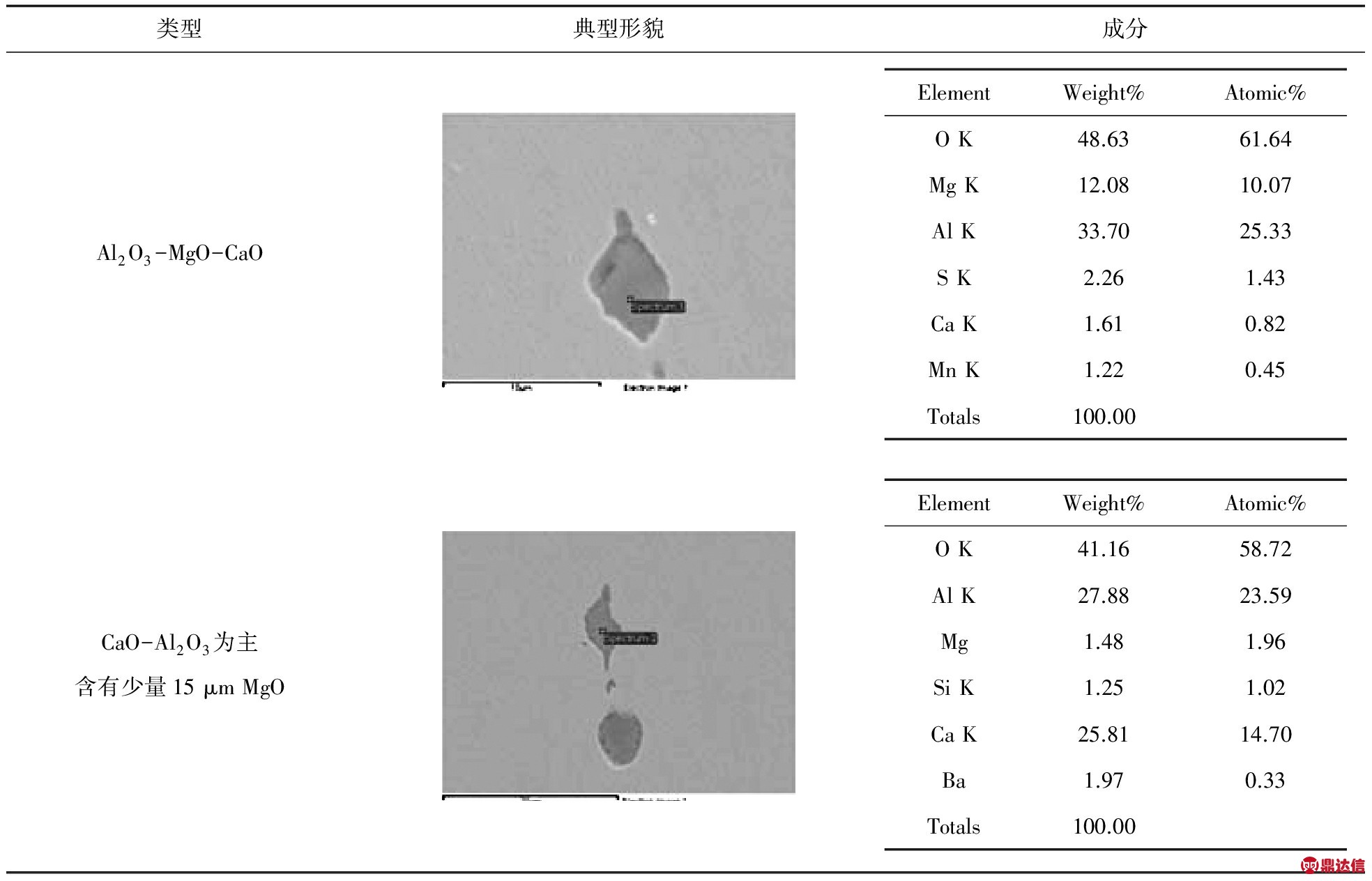
棒材中夹杂物主要类型为MgO- Al2O3,部分夹杂物含有少量的CaO,夹杂物类型为椭球形夹杂,Al2O3质量分数在70%~90%之间,MgO质量分数10%~30%附近波动,CaO质量分数在0~10%之间。在此夹杂物中CaO质量分数很低的。
2.2 各工序夹杂物演变规律分析
分析了各个工序的平均值之后,做出整个工序的含量变化,在一个三元相图中进行观察,夹杂物演变规律如图1所示:
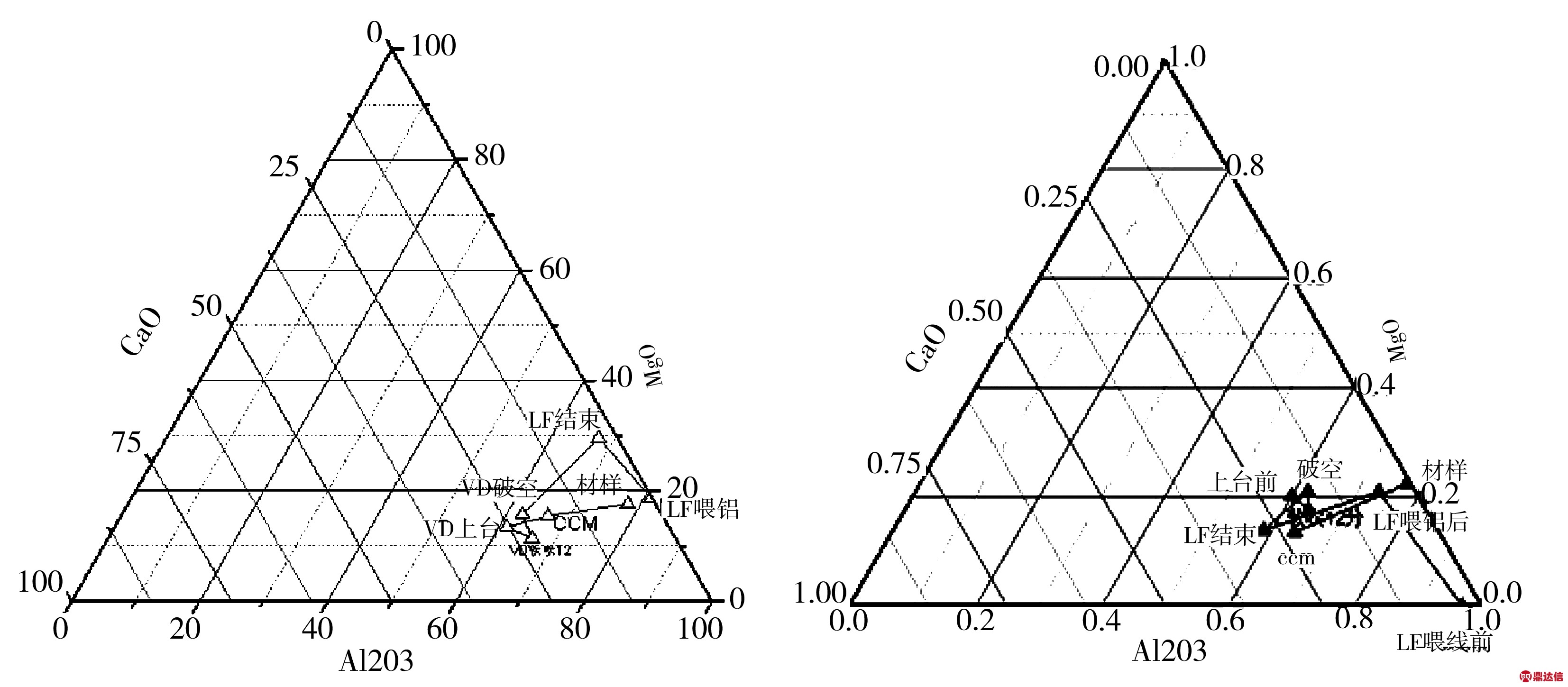
图1 夹杂物成分演变三元相图
从图1可以看出从,从氩站到材上整个工艺过程中夹杂物中的Al2O3质量分数先降低后逐渐上升;MgO质量分数在整个冶炼过程中基本保持稳定,大约在10%~20% 之间,而CaO的质量分数随着精炼时间的变化逐渐增加,在VD后基本保持稳定。但是在材上由于Al2O3的质量分数增加,CaO的质量分数出现较大的波动,这可能是随着温度的降低,Al和夹杂物中的CaO的再平衡反应造成的。
随着LF精炼的进行,纯Al2O3逐渐变为Al2O3-MgO-CaO的复合夹杂,而对于内生夹杂物的去除,由于Al2O3和钢水的不浸润的特征,其去除速度是最快的,为此在冶炼过程中应利用这个特征做到夹杂物的早去除和快去除,以降低大颗粒夹杂的数量,提高钢质水平。为此应做到早成白渣和保证渣的碱度和CaO/Al2O3的比值1.6-1.8。
2.3 各工序工序夹杂物平均粒径以及数量分布的变化分析
各工序夹杂物平均粒径、数量、大于13 μm的数量如图2所示。
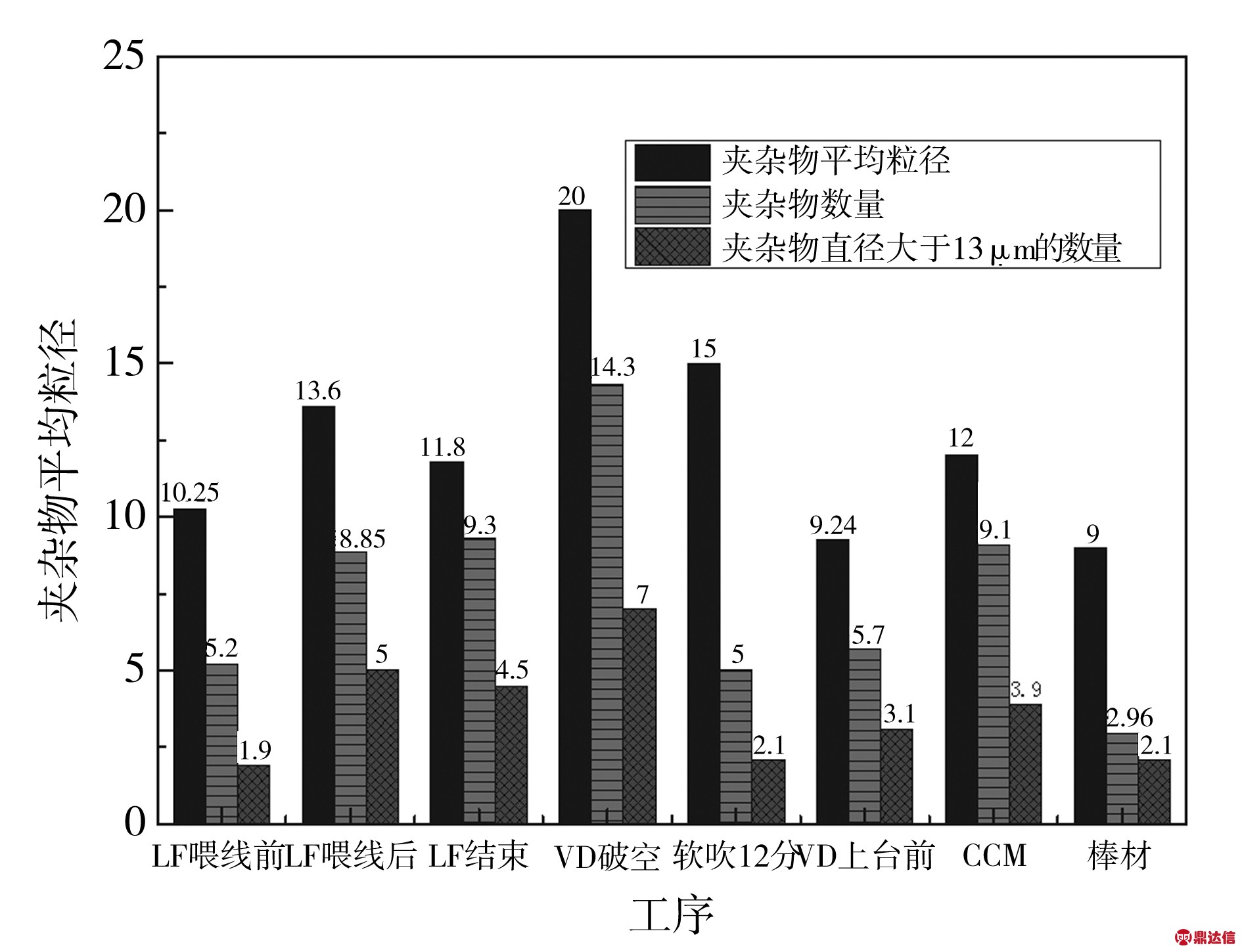
图2 各工序夹杂物平均粒径、数量、大于13 μm的数量
从图中可以发现,LF处理前夹杂物数量较多且粒径较大,LF处理后夹杂物数量明显减少且粒径变小。由此可见,LF炉外精炼对改变夹杂物的数量和大小是至关重要的;在VD破空后,钢水中的夹杂物数量和粒径均出现了上升,说明由于真空的大气量搅拌,在去除气体的同时,造成了钢水的污染,同时结合Als的大幅度降低,Al的二次氧化也造成夹杂物含量的上升,为此在VD精炼过程中应采取一定的措施(比如:在真空度较低下,开始搅拌;搅拌适当控制底吹气量等)减少VD中钢水的污染,同时强化软吹效果;对比大于13 μm夹杂物数量都是在VD破空后和连铸中包达到最大值,到了材样后降到最低值,第二炉比第一炉的材样中夹杂物数量低,并且两炉中夹杂物数量变化规律也基本上接近。
2.4 各工序含示踪元素的大型夹杂物分析
为了确定铸坯中显微夹杂物的来源,对LF-VD-CCM-材样各工序中含有示踪元素的夹杂物个数进行了统计,统计结果如图3所示。
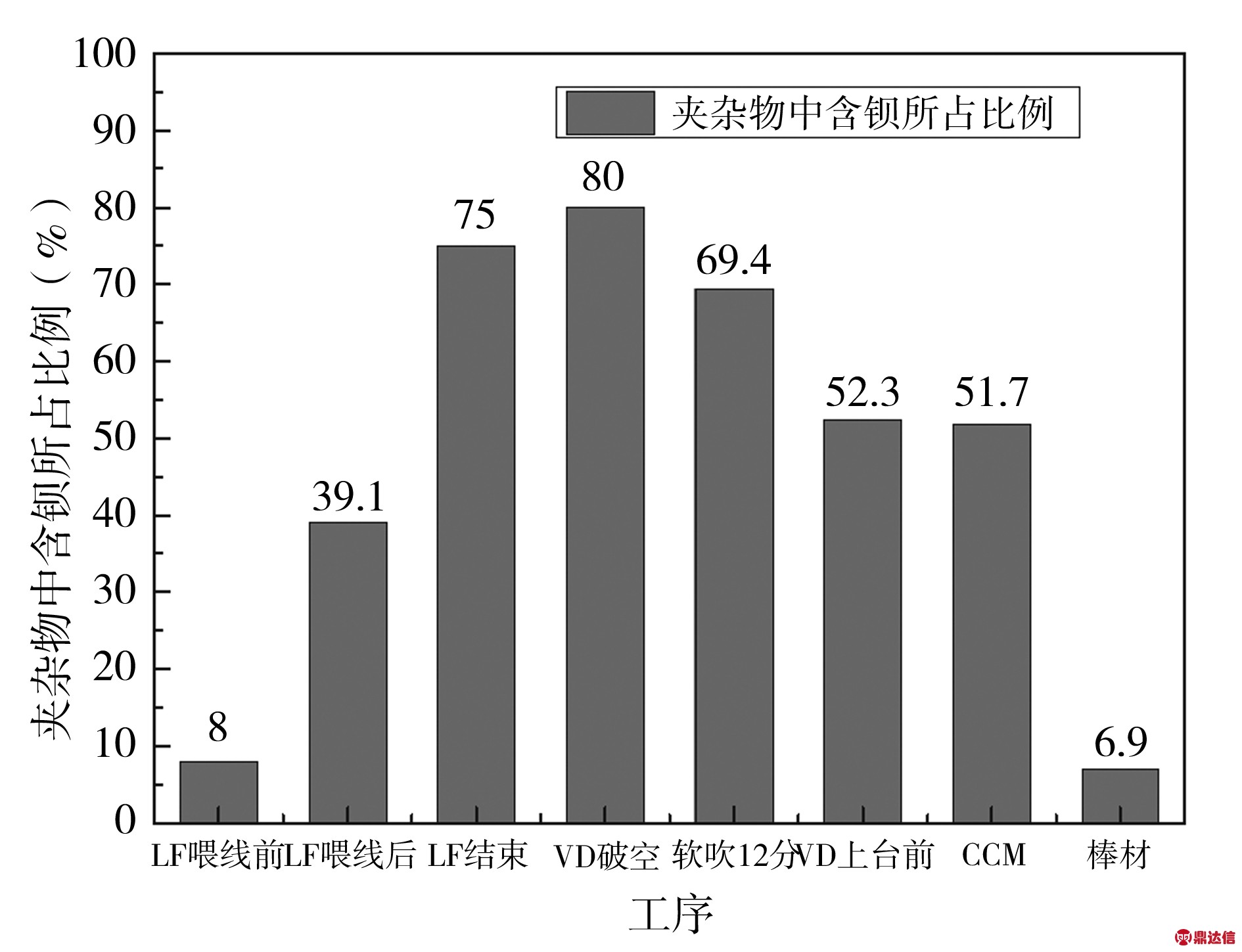
图3 夹杂物中含钡所占比例
从图中可以看出,冶炼过程夹杂物中没有检测到含示踪元素La和Sr,大颗粒夹杂物主要不是来源于中间耐材和中包渣,同时没有发现K、Na等保护渣成分,说明冶炼过程中基本没发生大颗粒的保护渣卷入的现象。
在LF喂铝之后就检测Ba元素,说明在LF喂铝阶段钢包渣就已经进入到夹杂物中;并且从LF喂铝之后夹杂物中含Ba比例逐渐升高的,到VD破空之后含钡比例最高值达到80%,之后夹杂物中含钡比例逐渐下降。说明钢包渣的卷入是大颗粒夹杂物的一个重要来源,为此一方面改变钢包渣的粘度,使卷入的钢包渣尽可能以大的液滴存在,这样在后期软吹过程中有利于夹杂物的上浮,同时应强化软吹,保证足够的软吹时间,同时控制软吹的气量,以减少钢包渣的卷入,生成新的大颗粒夹杂物。
3 结论
(1)从LF喂铝之后到最终材样Al2O3质量分
数先降低后逐渐上升,材样的Al2O3质量分数与LF喂铝之后的含量差异不大;MgO质量分数变化不大,LF结束之后含量达到最大值30%,材样MgO质量分数与LF喂铝之后差异不大,几乎持平;在LF喂铝之后夹杂物中不含有CaO,到LF结束之后出现了CaO,之后CaO质量分数是逐渐上升的,到材样中CaO质量分数又降低了大约为4%左右。
(2)对于内生夹杂物的去除,利用Al2O3和钢水的不浸润的特征,要早去除和快去除,以降低大颗粒夹杂的数量,提高钢质水平。为此应做到早成白渣,保证渣的碱度和CaO/Al2O3的比值在1.6-1.8。
(3)VD破空后,钢水中的夹杂物数量和粒径均出现了上升,为此在VD精炼过程中应采取一定的措施(如:在真空度较低下,开始搅拌;搅拌适当控制底吹气量等)减少VD中钢水的污染,同时强化软吹效果。
(4)夹杂物中没有检测到含示踪元素La和Sr,大颗粒夹杂物主要不是来源于中间耐材和中包渣,同时没有发现K、Na等保护渣成分,说明冶炼过程中基本没发生大颗粒的保护渣卷入的现象。在LF喂铝之后就检测Ba元素,说明在LF喂铝阶段钢包渣就已经进入到夹杂物中;并且从LF喂铝之后夹杂物中含Ba比例逐渐升高的,之后夹杂物中含钡比例逐渐下降。说明钢包渣的卷入是大颗粒夹杂物的一个重要来源。