纯电动汽车是汽车行业未来的发展趋势,其NVH性能备受广大消费者的重视和关注[1]。电动汽车相比传统汽油车在电机及传动系统的振动噪声方面存在较大差别[2-3],由于没有发动机噪声的掩盖效应,电辅助系统噪声更为突显,真空泵[4]等电器件工作时的振动噪声在电动汽车静置时非常明显,影响驾乘舒适度,因此研究电动汽车真空泵对车内噪声的影响机制[5],降低制动真空泵工作时产生的振动噪声问题尤为重要。
本文针对某电动汽车在踩踏制动踏板时真空泵工作振动引起车内噪声大的问题,分析真空泵工作原理及其振动噪声特性,膜片式真空泵因其结构特点和工作机理,具有工作振动大、辐射噪声小的特性,根据传递路径原理通过理论分析和试验分析,找出真空泵所致车内噪声主要是通过安装支架传递的结构噪声,针对原隔振垫方案隔振性能不足的问题,对隔振系统进行相关参数的优化分析,最后提出隔振垫优化方案,通过试验对比验证该优化方案具有良好的改善效果。
假设有一个数据集D={(xi,yi|i=1,2,…,N)},其中xi∈Rn,yi∈Rm分别作为特征向量和样本标签。含有M个隐层节点的单隐层神经网络的输出可表示为:
(2)由(1)知,y=f(x)的图象与y轴交点的纵坐标为2,且各部分所在直线斜率的最大值为3,故当且仅当a≥3且b≥2时,f(x)≤ax+b在[0,+∞)成立,因此a+b的最小值为5。
1 真空泵的NVH特性及问题分析
1.1 真空泵的NVH性能特点
当前纯电动汽车的真空泵主流应用类型是叶片式电动真空泵和膜片式电动真空泵,两类真空泵形式和结构存在一定差异,NVH性能各有优劣。叶片式真空泵由于自身结构原因,工作时石墨叶片与金属腔体摩擦、撞击,产生较大的工作噪声,根据工程实测经验,在自由声场的测试环境中,其近场(5 cm)噪声达80 dB(A);膜片式真空泵因其双膜片水平放置,工作时推杆在腔体内做往复循环运动,工作过程振动较大[6],所产生噪声较大,根据工程实测经验,其近场噪声在70 dB(A)水平;
近日,科技部公布了2013年重点新产品计划立项情况,甘肃大禹节水集团股份有限公司申报的“马铃薯专用地膜起垄浅埋滴灌灌水器”项目得到立项支持。
1.2 真空泵对车内噪声影响分析
某电动汽车采用膜片式真空泵,踩制动踏板致使真空泵运转时,主观评价车内真空泵工作噪声较大。针对上述问题,通过LMS测试设备采集车辆静置状态下真空泵本体振动、真空泵辐射噪声、主要传递路径振动(测点布置在一级隔振和二级隔振支架上)、车内噪声。采用LMS Test.Lab 软件分析其试验数据,分析结果如表1所示:车内主驾驶员右耳噪声声压级为46.8 dB(A)、真空泵近场(5 cm)噪声声压级为65.6 dB(A)及真空泵本体振动加速度为15.6 m/s2。通过频谱分析可知,车内真空泵噪声主要贡献频率是51.4 Hz,来源于真空泵的振动基频激励。
表1 原状态真空泵振动加速度、近场噪声及车内噪声声压级
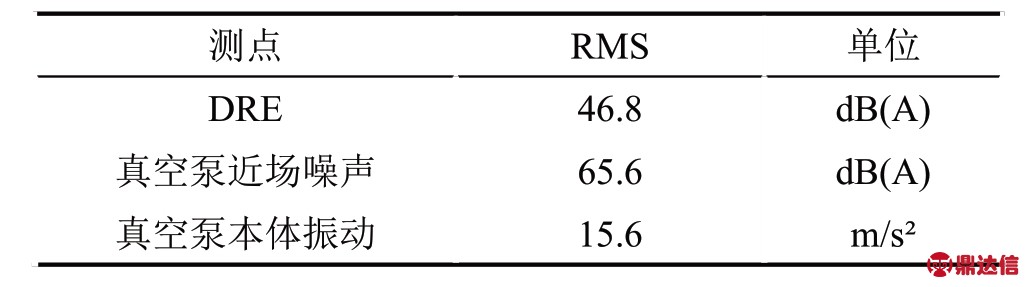
测点RMS单位DRE 46.8 dB(A)真空泵近场噪声65.6 dB(A)真空泵本体振动15.6 m/s²
通过分析该试验车真空泵安装位置、真空泵工作激励特性及传递路径,得出如图1所示真空泵振动噪声传递路径分析原理图。
根据“激励源-传递路径-接受者”分析模型,真空泵工作时,主要结构噪声主要由真空泵通过隔振橡胶垫传递到真空泵支架,再次经过隔振垫后传递到副车架,之后由前舱纵梁向车身传递,从车身辐射至驾驶员耳旁,部分结构噪声通过真空管路、真空罐、真空助力器传递;空气噪声由整车声学包和车身密封控制,不易被驾驶员感知到[7-8]。
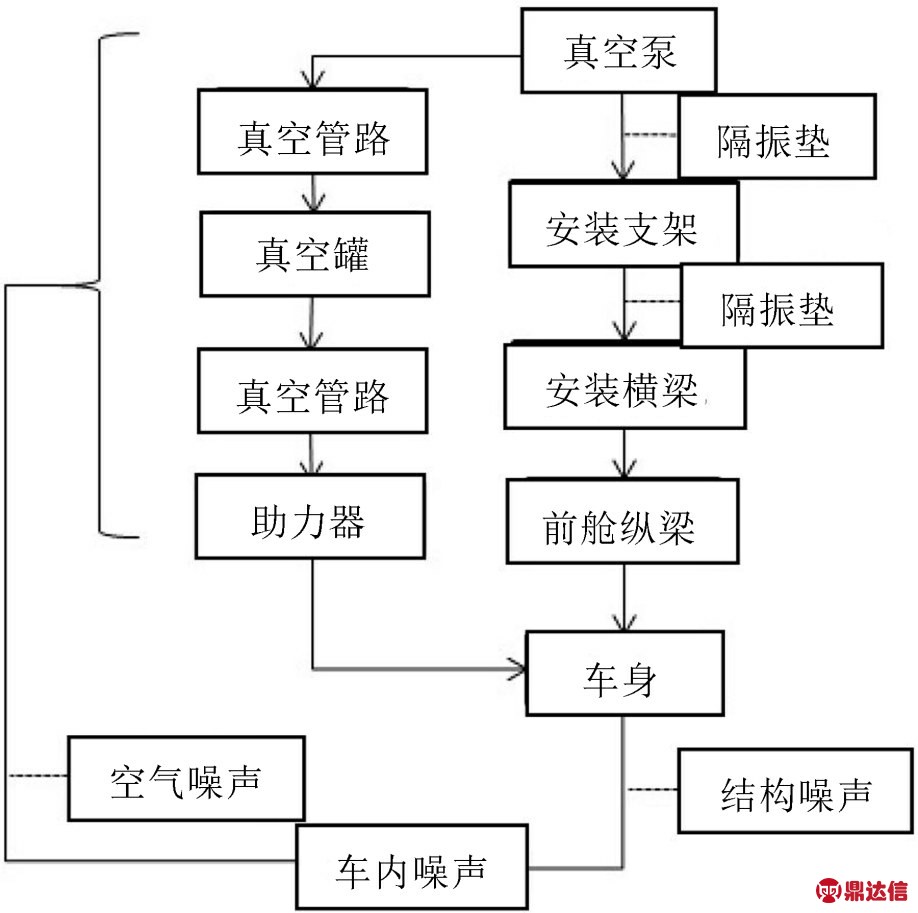
图1 真空泵振动噪声传递路径分析原理图
为了确认真空泵的主要贡献路径,在真空泵安装位置断开悬空,切断真空泵支架路径的结构噪声传递,保持真空泵管路正常连接不变,且在基本不改变真空泵所处位置的前提下,踩制动踏板运行真空泵,测得车内主驾驶员右耳噪声声压级是36.6 dB(A),较原状态车内噪声降低10 dB(A),由此可见,真空泵支架传递结构噪声是该真空泵车内噪声主要贡献路径,符合膜片式真空泵振动大、辐射噪声小的特点。
2 真空泵结构噪声传递路径优化分析
对于真空泵等电器激励件,常规使用的隔振垫是如图2(a)和图2(b)所示工字型隔振垫,该隔振垫通过螺栓和内圈刚套实现激励源与安装点之间的固定及隔振,该类型的隔振垫主要通过外圆周面的中间凹槽卡住激励源侧,依靠单侧橡胶进行隔振。该隔振垫方案便于隔振垫安装,但隔振垫物理空间利用率较低。
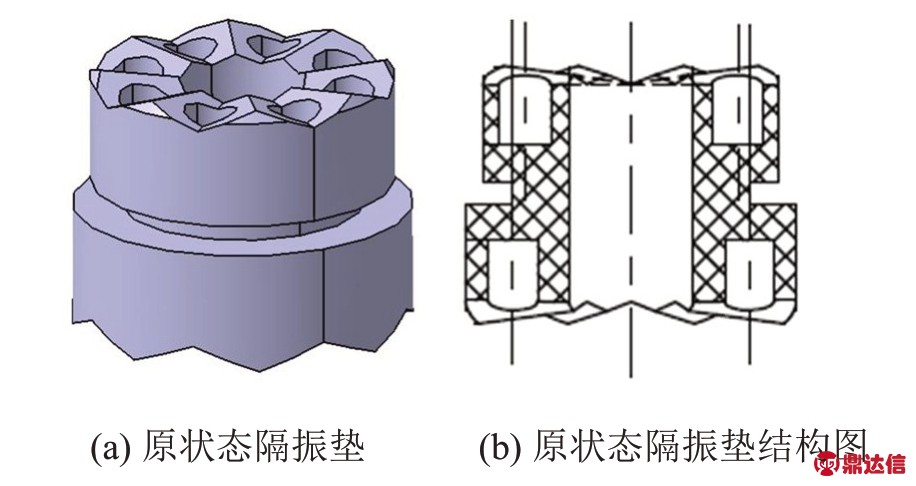
图2 隔振垫
真空泵原状态下采用该工字型隔振垫方案实现双层隔振,根据第二级隔振试验测试结果(如图3和表2所示)可知:振动主要考察0~200 Hz范围内RMS值隔振率为8.1 dB,真空泵的主激励频率51.5 Hz 处的隔振率为8.3 dB,该隔振垫方案的隔振率较低,导致真空泵结构噪声传入车内。为了降低车内真空泵噪声,需要提高传递路径的隔振率,更大程度地衰减真空泵的激励传递。隔振效果取决于隔振系统的刚度,而影响隔振系统刚度主要因素是弹性原件的刚度,即需降低隔振垫的刚度。圆柱形橡胶垫刚度经验公式为[9]
表2 原状态隔振垫隔振率试验结果/dB
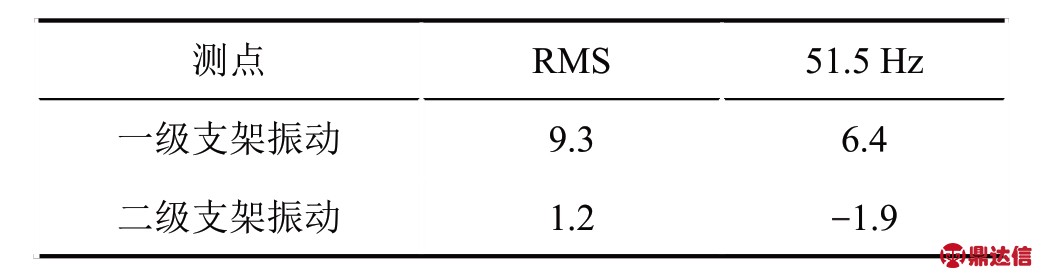
测点RMS 51.5 Hz一级支架振动9.3 6.4二级支架振动1.2-1.9
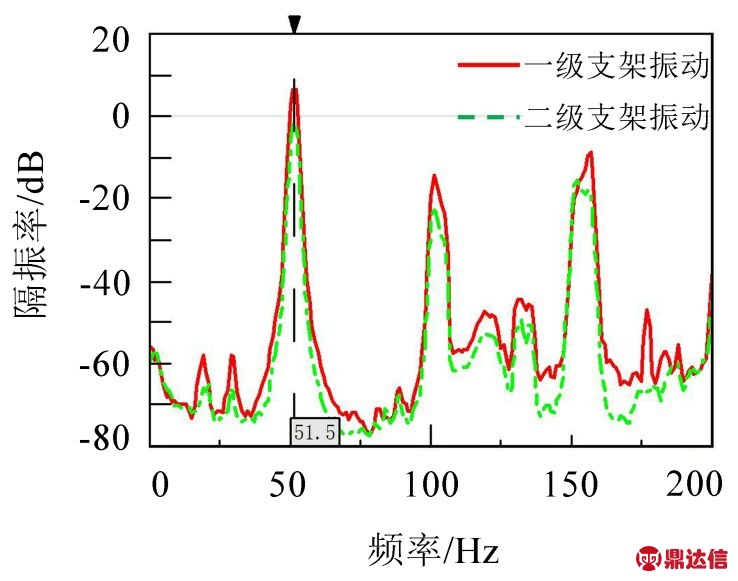
图3 原状态隔振垫隔振率试验结果

式中:K是橡胶隔振垫刚度,m是形状差数,E是弹性模量,A和H分别代表胶块的面积和厚度。
可见,可以通过降低弹性模量或者加厚隔振垫厚度降低隔振垫的刚度。影响弹性模量数值的主要因素是胶块的硬度和胶块压缩量,通过降低胶块硬度可以更有效降低其弹性模量。
该隔振垫样件硬度是邵氏40度,由于需要兼顾隔振垫的疲劳耐久等其他性能,进一步降低隔振垫硬度的空间较小,可采用增加隔振垫厚度的方案。
针对上述分析结论,将该结构隔振垫加厚8 mm(如图4所示)后,实施同样工况测试。
由如图5和表3中测试结果分析可知,工字型隔振垫加厚8 mm 后,车内噪声有所改善,驾驶员右耳总声压级由46.8 dB(A)下降至44.9 dB(A),降低约2 dB(A),真空泵激励峰值所对应的噪声峰值由44.0 dB(A)下降至33.3 dB(A),降低10.7 dB(A),总体改善较小。
城头,活着的人每走一步,不是碰着死人的脸,就是踩到死人的腿,有时要费很大劲,才能把脚从死人堆里拔出来,脚是拔出来了,血水却直往下淌。
主观评价车内真空泵噪声有所降低,但依然不一种隔振性能更优的隔振垫方案。可接受,需要进一步提升隔振性能,减小结构噪声向车内的传递。而原状态隔振垫在降低硬度和增加厚度方面的措施对隔振性能提升有限,由此,需要找出一种隔振性能更优的隔振垫方案。
我国《宪法》第39条规定:中华人民共和国公民的住宅不受侵犯。禁止非法搜查或者非法侵入公民的住宅。在这一宪法条文中,住宅不受侵犯权的内涵主要集中于两点:(1)住宅不受侵犯中的“侵犯”如何界定?(2)非法搜查和非法侵入中哪些行为可以被认定为是非法?明确了这两点之后住宅不受侵犯权的涵义也就清晰可见了。
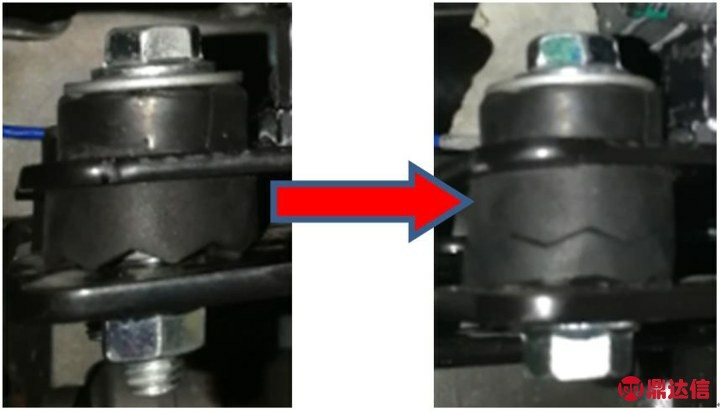
图4 原状态隔振垫加厚示意图
表3 原状态隔振垫加厚前后车内噪声对比/dB(A)
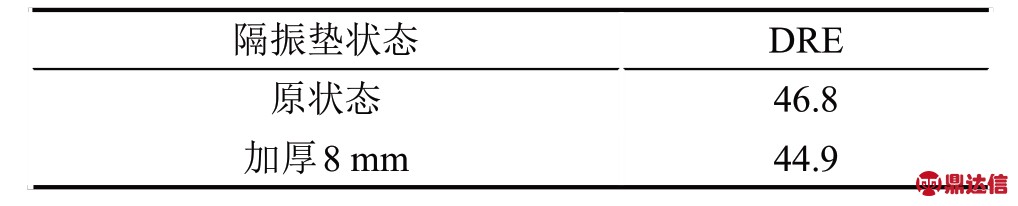
隔振垫状态DRE原状态46.8加厚8 mm 44.9
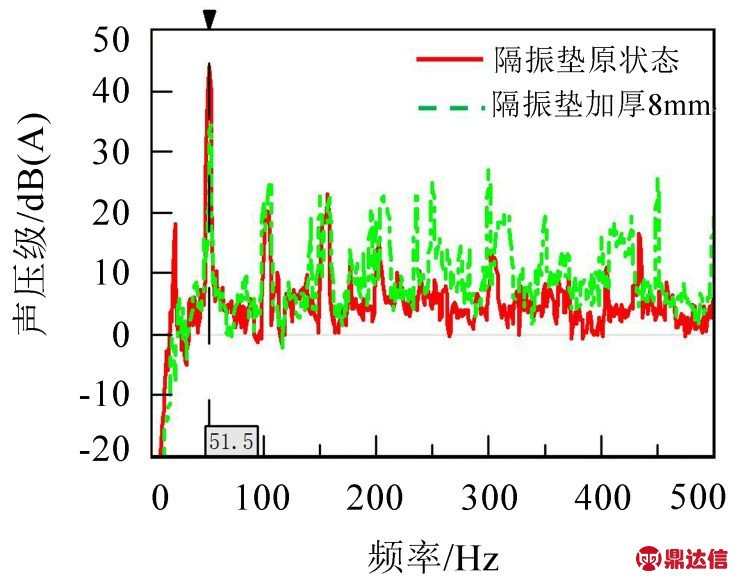
图5 隔振垫加厚前后车内噪声试验对比
3 改进方案分析与试验验证
悬置所具有的良好隔振性能跟悬置特定的结构有关,见图6。悬置通过铁芯与激励源电驱系统连接,外铁圈通过悬置支架与副车架连接,中间起隔振隔声作用的橡胶块处于无限制的自由振动状态,如悬置受外力作用,橡胶与外铁圈内壁压死,隔振性能会急剧下降。如同安装状态下的工字型隔振垫上表面受螺栓法兰面或刚套限制压紧(见图4),将削弱该类型隔振垫的隔振性能。
受上述原理启发,提出以下无贯通螺栓孔隔振垫的优化方案,如图7(a)和图7(b)所示,主要亮点是将隔振硫化橡胶安装在螺栓所在的铁圆面之间,上下螺栓分别连接激励源和被动侧安装位置,中间的橡胶块类似悬置橡胶,处于无限制的自由振动状态,能充分发挥其隔振性能。
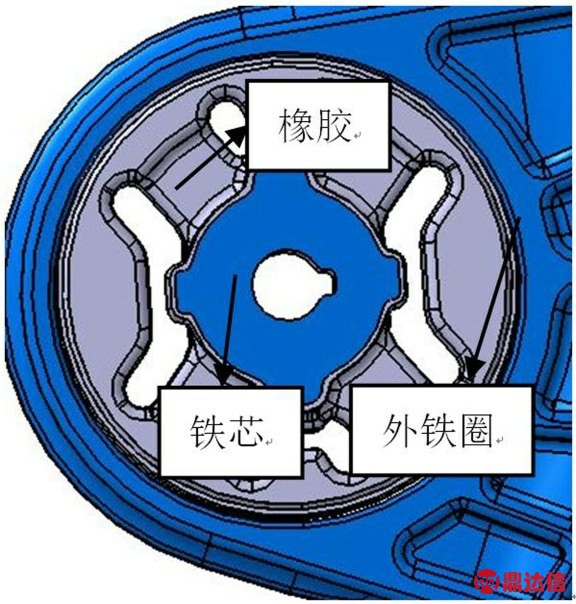
图6 悬置结构示意图
某橡胶悬置动刚度曲线如图8所示,橡胶隔振元件在200 Hz以内的动刚度基本稳定,而250 Hz以后开始出现高频硬化现象,动刚度大幅度提升。膜片式真空泵主要振动能量分布在前200 Hz,优化方案中的无贯通螺栓孔隔振垫属性类似橡胶悬置,在中低频段具有良好的隔振性能,能有效地隔离膜片式真空泵的主要振动激励能量,解决真空泵结构噪声传递问题。
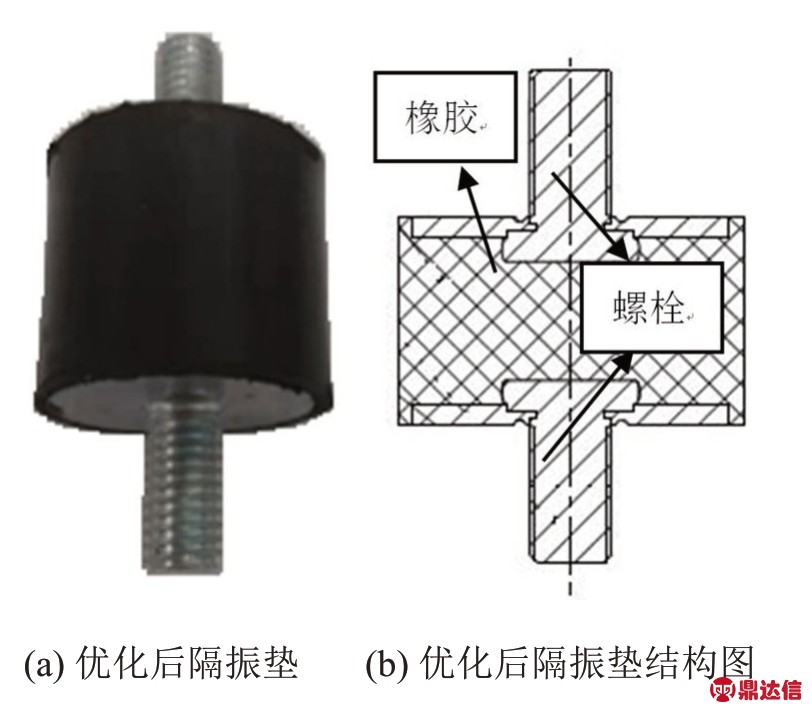
图7 隔振垫
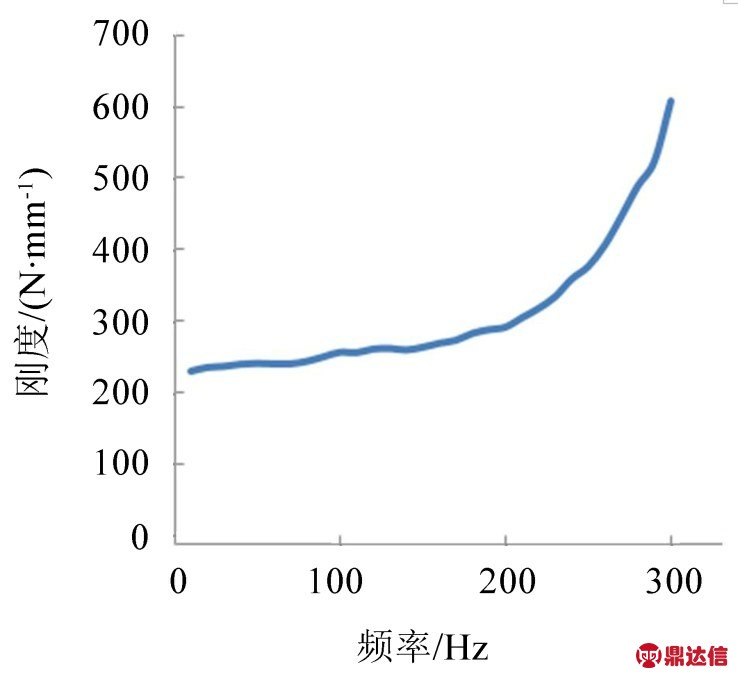
图8 橡胶悬置各频率段刚度曲线图
将真空泵隔振垫更换成优化方案中的无贯通螺栓孔隔振垫,依然采用双层隔振,根据第二级隔振试验结果(如图9和表4所示)可知:在主要考察范围0至200 Hz 内RMS值隔振率为13.9 dB,真空泵的主激励频率51.5 Hz 处的隔振率为14.9 dB,隔振率较原方案提升70%以上,改善效果显著。
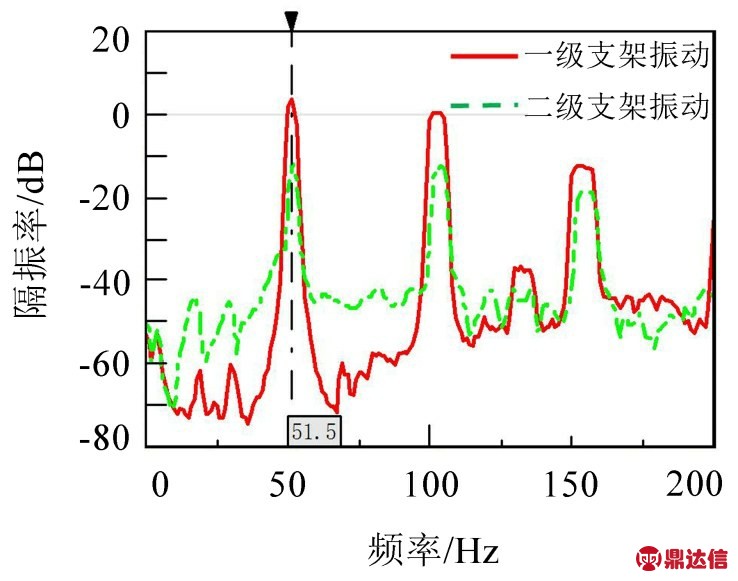
图9 采用优化方案后隔振垫隔振率试验结果
表4 优化后隔振垫的隔振率测试结果/dB
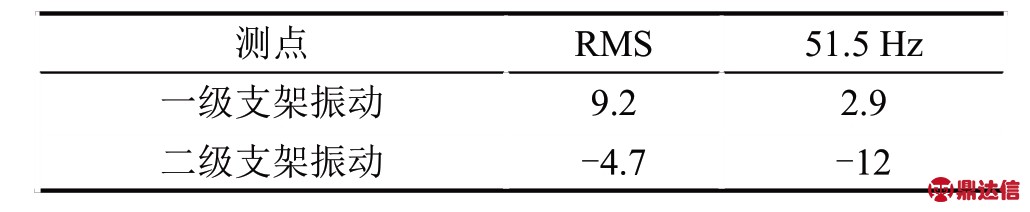
测点RMS51.5 Hz一级支架振动9.22.9二级支架振动-4.7-12
对比隔振垫优化前后的真空泵车内噪声试验结果,如图10和表5所示。驾驶员右耳总声压级由46.8 dB(A)下降至37.6 dB(A),改善9.2 dB(A),真空泵激励峰值所对应的噪声峰值由44.0 dB(A)下降至28.1 dB(A),改善15.9 dB(A)。车内噪声问题改善明显,主观评价车内只听到轻微的真空泵噪声,完全可接受,有效解决了车内真空泵噪声大的问题。
应以控制径流系数为重点,强化地表径流控制和人为生产建设活动土石方综合利用;强化雨水控制和集蓄利用,提高雨洪利用程度;适当拓展河道空间,建设滨河(湖)绿带;强化城区河湖水质改善;加强小流域内排洪水系的连通与疏浚,降低城市防洪压力。
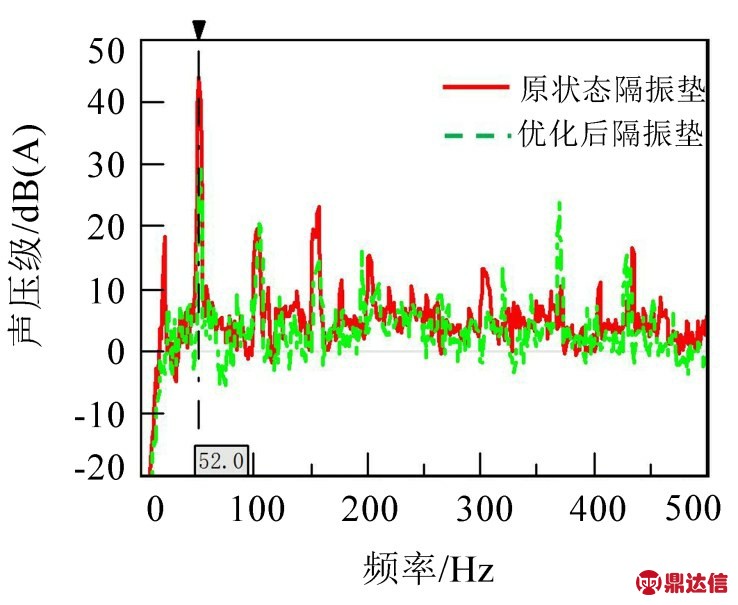
图10 隔振垫优化前后车内真空泵噪声测试结果对比
表5 优化隔振垫前后车内噪声对比结果/dB(A)
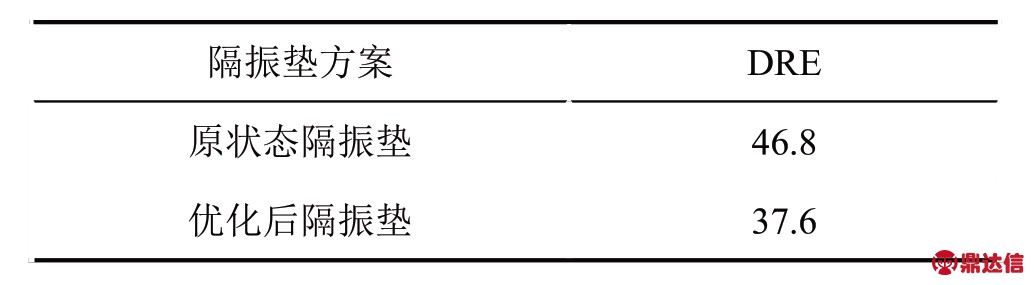
隔振垫方案DRE原状态隔振垫46.8优化后隔振垫37.6
由此可见,无贯通螺栓孔隔振垫方案相比原方案隔离结构噪声具有明显效果,其与双层隔振措施相配合,可成为解决结构噪声问题的优秀方案。
4 结语
膜片式真空泵噪声传递以结构声为主,提升隔振垫的隔振率是解决结构声传递问题的最有效措施。分析橡胶隔振垫材料属性可知,降低橡胶隔振垫硬度和增加厚度可提升其隔振率,但是改善有限。从具有良好隔振性能的悬置结构原理出发,提出无贯通螺栓孔隔振垫结构方案,使隔振性能大幅度提升,有效解决车内真空泵噪声大的问题,表明该隔振垫方案对结构噪声问题具有显著的改善效果。本文的工作内容和成果对其他车型及相似的结构噪声传递问题的解决具有较好的指导意义。