摘 要:通过分析摆动导杆式抽油机在一个工作周期内导轨的受力情况,求得导轨某一时刻受到的最大应力。利用ANSYS Workbench对导轨进行静强度分析,以确保所选型的导轨在抽油机的工作过程中,不会发生过大弯曲变形而失效。
关键词:摆动导杆式抽油机;导轨;强度分析;ANSYS Workbench
0 引 言
目前我国油田的地面采油设备主要采用游梁式抽油机,由于其具有结构简单、使用可靠、操作维护方便,以及在恶劣的自然环境中能够长期可靠安全运行等特点,使其在油田开采过程中得到了较为广泛的应用。但由于该抽油机载荷不均匀系数CLF偏大,使得曲柄轴上的净转矩峰值过大,波动过大,同时能耗也随之变大[1]。
因此,开发一种节能型抽油机就显得十分重要。摆动导杆式抽油机就是一种节能型抽油机,它是利用摆动导杆机构替换常规型抽油机的四连杆机构而生成的一种节能型抽油机[2]。由于摆动导杆机构比四连杆机构有更大的极位夹角,更能符合油井抽汲过程中慢提快放的特点,所以更加节能。导轨是摆动导杆式抽油机重要的组成部分,对导轨强度的校核就显得十分重要。
导轨属于细长杆件,工程中对某些受弯杆件除强度要求外,往往还有刚度要求,即要求它变形不能过大。若构件的变形超过允许值,即使仍然是弹性的,也看作已经失效[3]。所以有必要对导轨的刚度进行计算并校核,检验其是否满足工作要求。
1 摆动导杆式抽油机总体结构与导轨选型
图1是摆动导杆式抽油机总体结构示意图。从图中可以看出,摆动导杆式抽油机比常规式抽油机多增加一个后支架,将电动机和减速器整体放在前支架上,而将导轨的支点后移放在后支架上,曲柄、滚轮和导轨都为双侧结构布置,这样可以均匀传递动力。驴头通过前横梁与导轨相连,这样导轨就可以传递动力给驴头,使驴头上下摆动。平衡重放在曲柄相反的一侧,以平衡驴头悬点载荷的转矩。滚轮作为连接曲柄与导轨的构件 ,在抽油机的运行过程中起到十分重要的作用。滚轮不仅传递曲柄的转矩,而且在导轨上进行滚动。图2所示为滚轮和导轨接触简图,从图中可以看出,滚轮和导轨属于线接触,导轨的截面宽度就是二者的接触线长度。
导轨采用标准的钢轨,不仅选型方便,而且还能大大降低抽油机的制造成本。钢轨采用43 kg/m,轨高为134 mm,底宽为114 mm,头宽为70 mm,腰厚为14.5 mm,理论质量为44.653 kg/m,图2为钢轨的几何参数。导轨的两端采用垫块用螺栓螺母连接而成;垫块一方面控制上下导轨的间距,另一方面可以将导轨和横梁连接在一起。图3是导轨与垫块连接示意图。
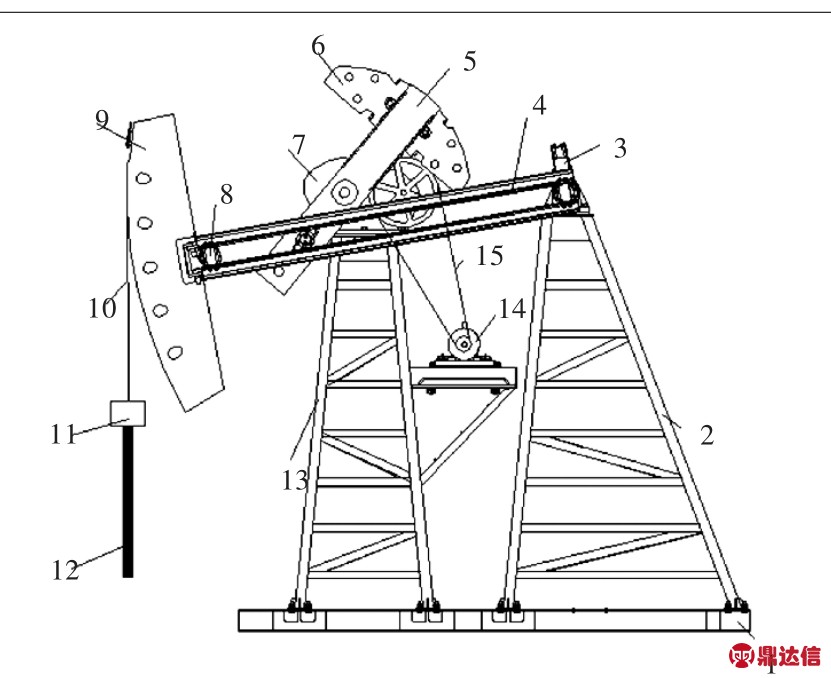
图1 摆动导杆式抽油机总体结构示意图
1.底座 2.后支架 3.后横梁 4.摆动导杆 5.曲柄 6.曲柄平衡重 7.减速器 8.前横梁 9.驴头 10.钢绳11.绳杆连接器 12.抽油杆 13.前支架 14.电动机15.带传动
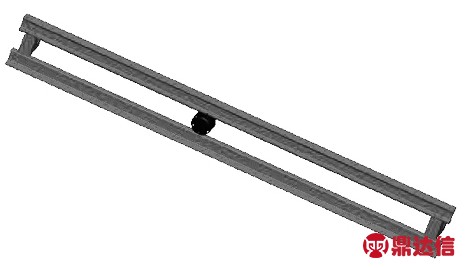
图2 滚轮和导轨接触示意图
2 导轨的受力分析摆动导杆式抽油
机在一个循环周期内,滚轮与导轨之间属于线接触。滚轮接触应力的计算是一个弹性力学的问题。对于线接触,弹性力学给出的接触应力计算公式为
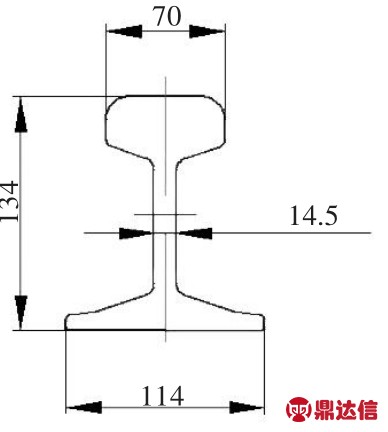
图3 钢轨几何参数
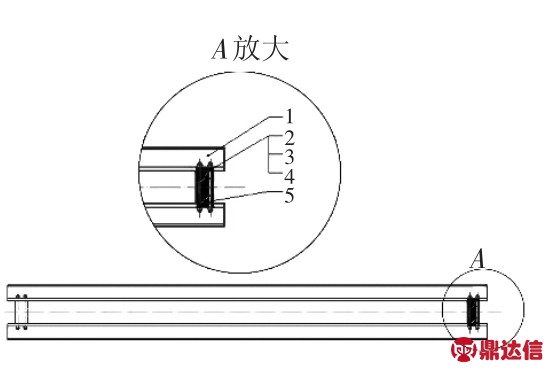
图4 导轨与垫块连接示意图
1.滑轨 2.螺栓 3.垫圈 4.螺母 5.垫块
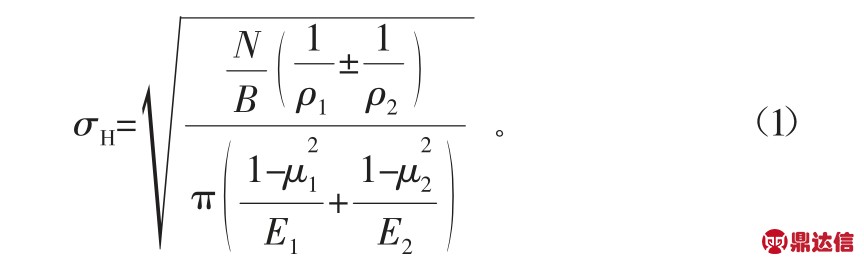
式中:N为作用于接触面上的总压力,即电动机输出轴的切向力;B为初始接触线长度;ρ1、ρ2为零件1和零件2初始接触线处的曲率半径,通常,令称为综合曲率,而
称为综合曲率半径,其中正号用于外接触,负号用于内接触;μ1、μ2为零件1和零件2材料的泊松比;E1、E2为零件1和零件2材料的弹性模量。
由以上分析可知,在摆动导杆式抽油机的一个循环周期内,可以利用MATLAB软件绘制出滚轮在一个周期内所受的应力,如图5所示。
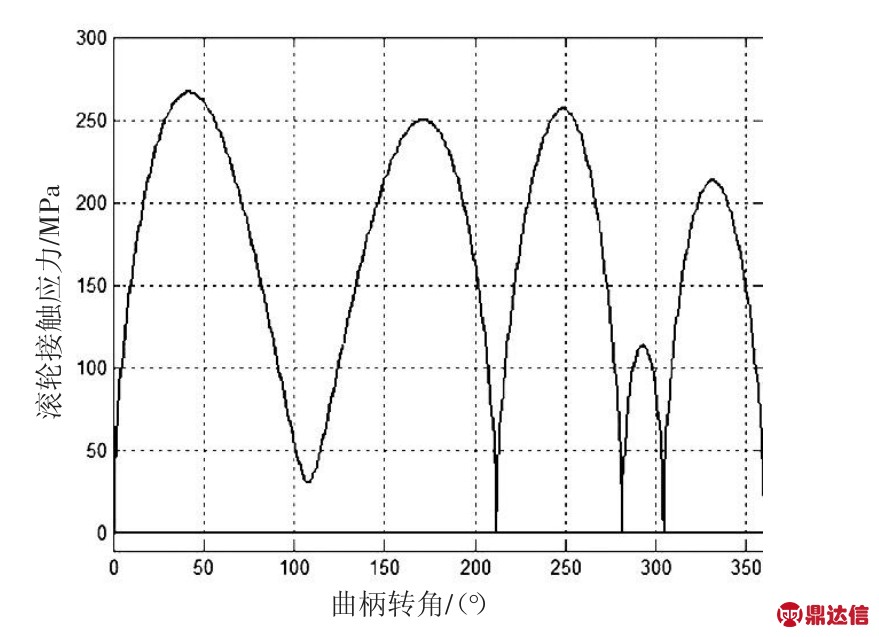
图5 滚轮与导轨接触应力图
由图5可以看出,曲柄转角为40°时,滚轮接触应力达到了最大值,最大值为266.848 MPa。滚轮此时所受的接触力为9437.325 N。
2.1 导轨的受力分析
图6为经过简化处理过导轨的受力分析图,在摆动导杆式抽油机的运行过程中,导轨的一端和驴头相连,即导轨的一端承受悬点载荷,另一端固定在支架的轴承座上,滚轮在导轨上滑动。根据材料力学可知,导轨在弯曲变形时,一端可以设定受活动铰链所约束,另一端受固定铰链所约束,导轨两端之间受到随位置变化的力的作用。
2.2 导轨的弯曲计算
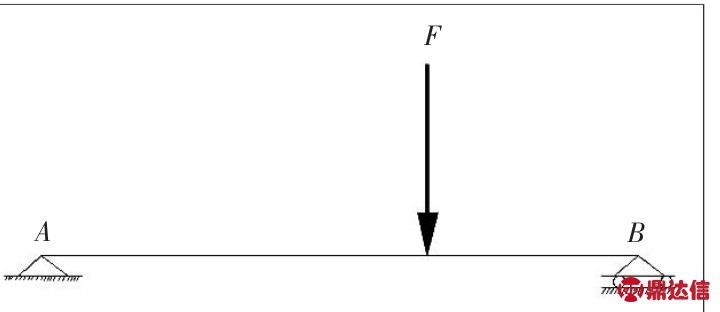
图6 导轨受力图
导轨受弯曲变形,应用材料力学的知识,采用叠加法求弯曲变形,导轨的挠曲线方程为:
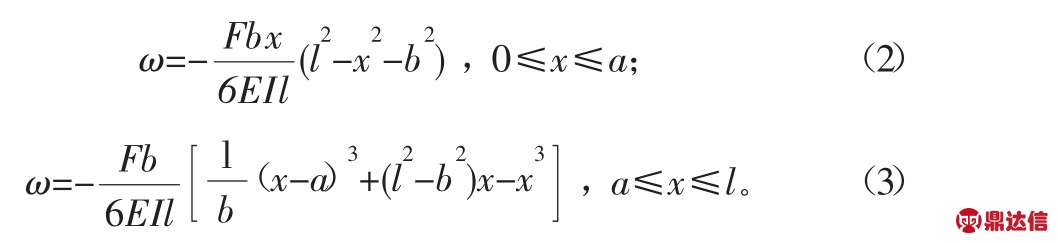
导轨的端截面转角为:
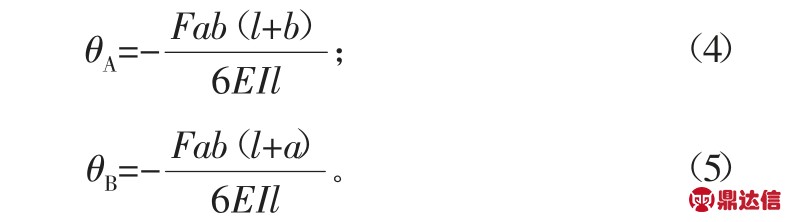
导轨的最大挠度为:
设a>b,在
在x=l/2处
式中:ω为受弯杆件的挠度;F为杆件受的接触力;θ为杆件的截面转角;I为杆件的极惯性矩;E为杆件的弹性模量;l为杆件的长度;a为受力点与端点A的距离;b为受力点与端点B的距离。
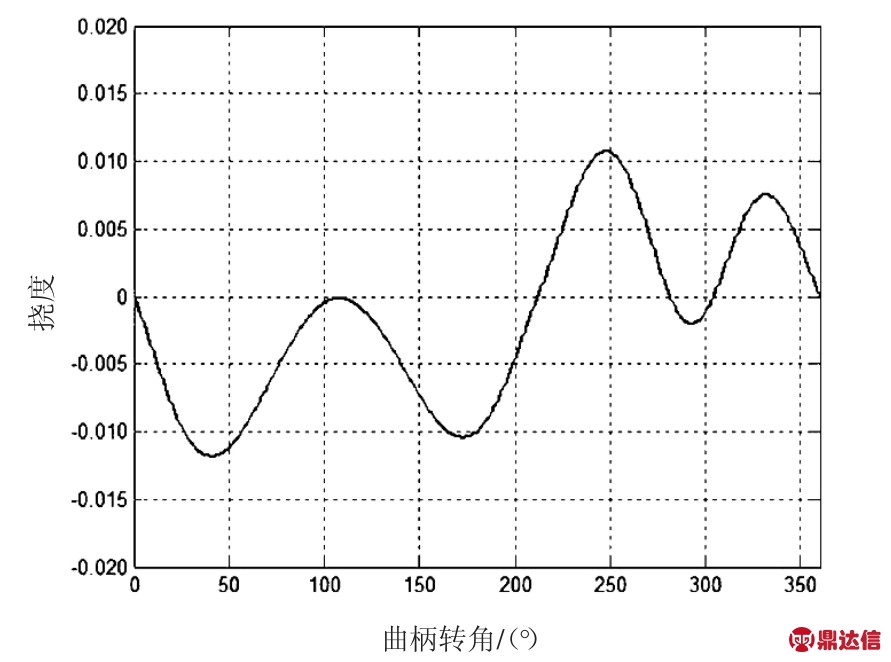
图7 导轨挠度曲线图
由以上分析可知,并利用MATLAB软件可以绘制出摆动导杆式抽油机一个工作循环过程中,导轨的挠度曲线图。
从图7可以看出,导轨的最大正挠度为0.011,最大负挠度为0.012。即导轨在最大负挠度时,变形是最大的。此时导轨受到滚轮的正压力为9437.325 N。此时悬点载荷为37.107 kN。导轨的固定端距正压力施加位置的距离为2.588 m。
3 导轨有限元分析
3.1 建立分析模型
在ANSYS Workbench软件中,建立导轨模型,导轨模型可以简化为简支梁受载问题,钢轨两个铰链点之间的长度为3683 mm。
3.2 材料属性
导轨的材料选择结构钢,结构钢的物理属性如下:弹性模量为200 GPa,密度为7850 kg/m3,泊松比为0.3,抗拉压强度为250 MPa[4]。
3.3 网格的划分
根据软件设置,网格单元大小设置为10 mm,相关度设置为100%,采用四面体网格划分,划分结果共有739个节点,369个单元。结果如图8所示。
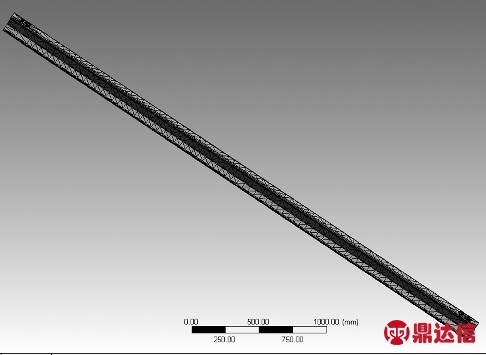
图8 导轨网格划分图
3.4 施加约束和载荷
在摆动导杆式抽油机一个工作循环周期内,当导轨在最大负挠度时,距离导轨简支约束2.588 m 处,导轨受到9437.325 N的正向压力。导轨的一端采用简支约束,另一端采用铰链约束[5]。
3.5 求解结果
导轨采用梁单元进行分析,经过以上分析可以得到导轨的变形云图、最大弯曲应力、梁单元的剪力和弯矩。
从图10~图12分析可知,导轨的最大变形为2.447 9 mm,导轨的最大弯曲应力为29.987 MPa,导轨的总弯矩为7.261 5×106 N·mm,最大剪力为6631.5 N。可以看出,最大弯曲应力远远小于结构钢的抗拉压强度,符合强度理论。
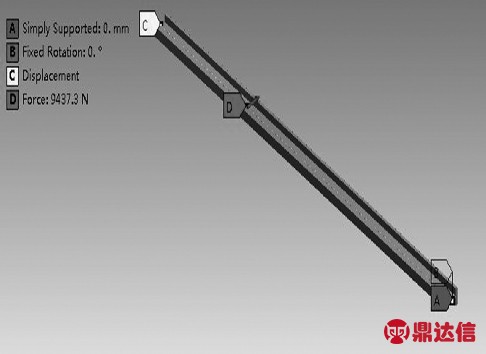
图9 导轨约束与载荷图
4 结 语
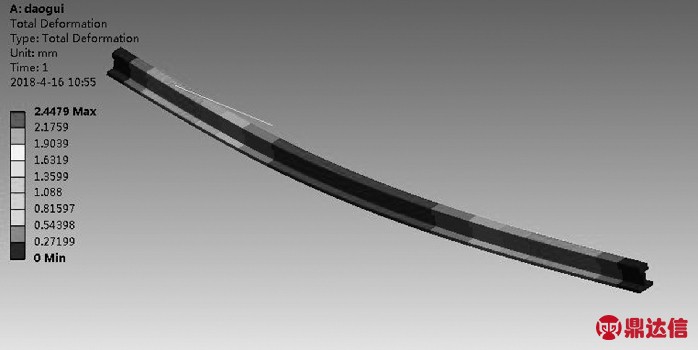
图10 导轨应变云图
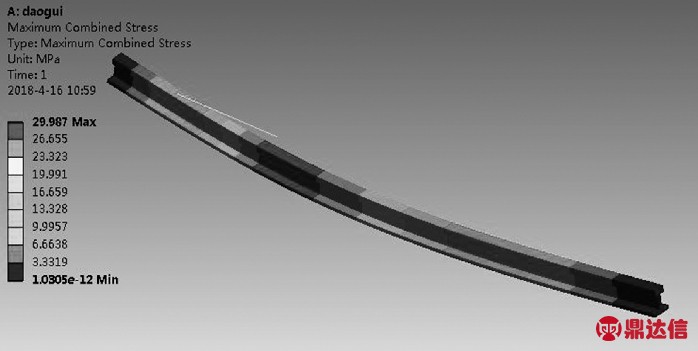
图11 导轨弯曲应力图
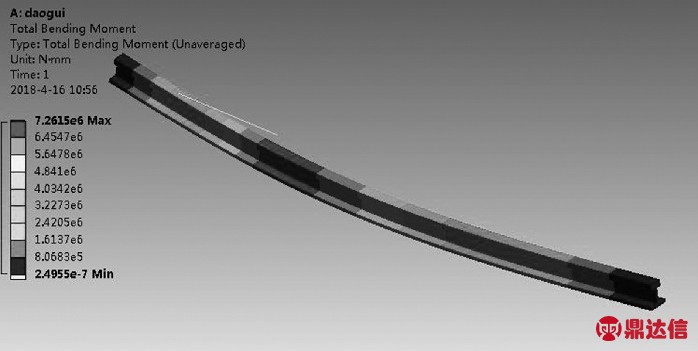
图12 梁单元弯矩图
本文通过分析常规抽油机存在的高能耗问题,提出一种节能型抽油机。导轨是摆动导杆式节能型抽油机的重要组成部件,对导轨的强度分析就显得十分重要。通过对导轨在抽油机的一个循环周期内受力情况的分析,得出导轨的最大受力位置。利用ANSYS Workbench静力分析模块对导轨进行分析,得到其应力、应变云图。通过结果分析,可知所选型的导轨符合抽油机的工况要求,不会发生过大变形而失效。