摘要:本文用实例介绍了小孔节流闭式静压导轨修复方案、方法,并对静压导轨损坏原因、静压导轨附属件设计和静压导轨日常维护要点进行了探讨。
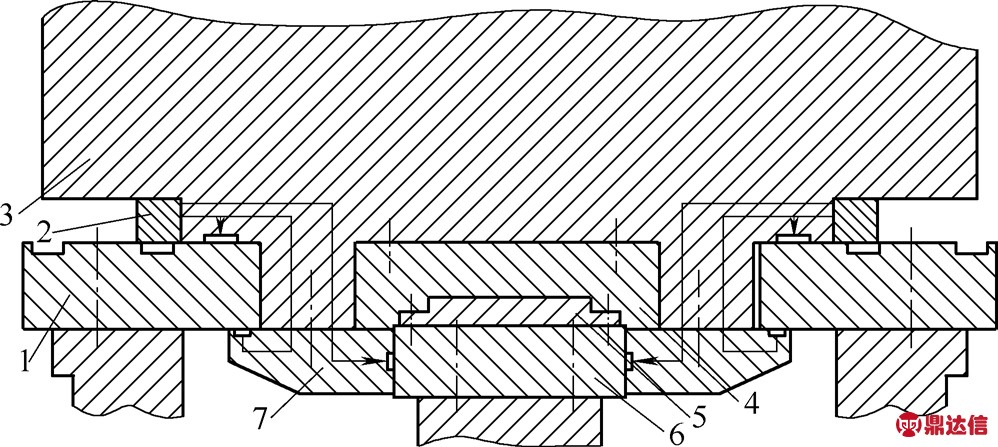
扫码了解更多
静压导轨技术在精密机床上应用十分广泛。由于静压导轨配套的辅助设计缺陷或日常维护不良,导致静压导轨损坏情况发生较频繁,本文通过以下案例,说明静压导轨损坏后修复方法、并对静压导轨辅助件设计及其日常维护给出设计建议。
1.问题分析
某公司凸轮轴生产线经过随动磨床加工后,全部凸轮表面存在整圈的轴向震纹。如图1所示,检测静压导轨上下浮起量(浮起量要求0.018mm~0.029mm)前后4个点:前端0.018mm、0.02mm,后端左右均为0.002mm;横向浮起量要求0.02mm塞尺不过,实测间隙0.08mm,拆卸导轨防护后,发现静压导轨支撑面前后端均出现不同程度的划伤。
由此可以判定:静压导轨各浮动面的磨损导致其各配合面间不能建立刚性的压力油膜抬升浮动面,加工过程中整个砂轮台处于前后不平衡状态,最终反馈到工件表面一周产生震纹。
如图2所示,该导轨的液压控制原理:液压系统通过定量泵和过滤系统给3节流孔组提供液压,通过件3和件7中的液压管路,把油压传递到件1的上下表面,充满静压腔并建立油膜,使砂轮台上下浮动;同时通过件7油路,液压传递到件6左右两侧静压腔,建立油膜,控制砂轮台的左右浮动。综上,该静压导轨为定压、闭式形式。
2.解决方案确定
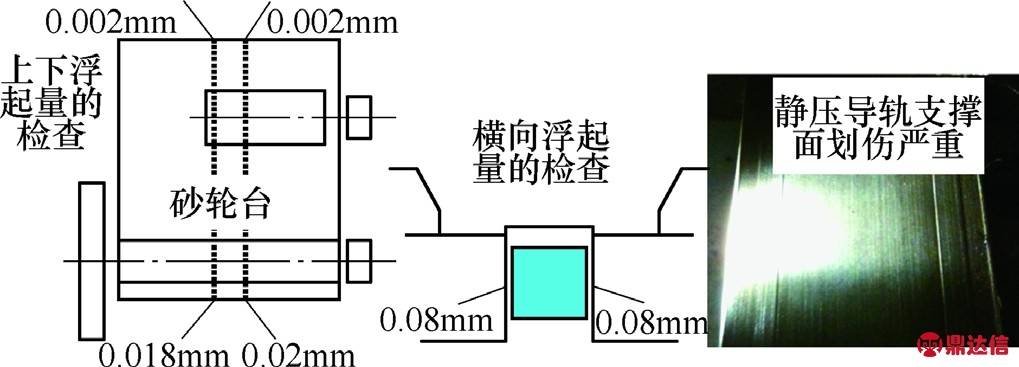
图1 静压导轨浮动量的检查
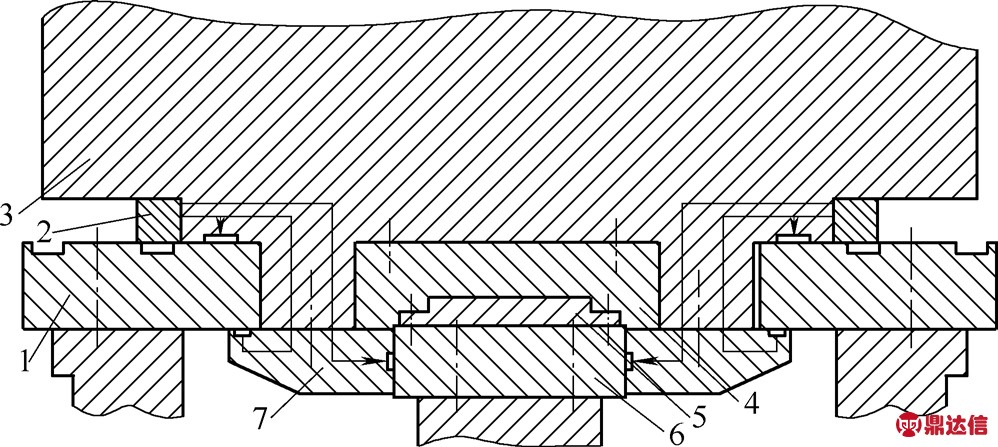
图2 静压导轨液压回路
1.静压导轨板 2.静压导轨节流孔组(φ0.4mm) 3.静压导轨静压腔体(砂轮台本体)4.直线电动机次级部分 5.直线电动机初级部分 6.静压导轨横向导轨 7.静压导轨压板
通过以上分析,以图2件6为基准,对该导轨进行修复,具体修复方案和过程如下(其他形式的静压导轨修复方法类似)。
从机床上移出砂轮台进给部分,拆卸直线电动机的次级部分,拆卸后利用绝缘材料覆盖直线电动机初级部分。由于直线电动机初级有强磁性,拆卸过程一定要遵循直线电动机拆卸方法和要求进行,具体如图3所示。
分解和修复方案的确定,如图4所示。
(1)测量导轨组件1、件3、件4和件7表面(图示中部分)硬度(一般为铸件本身硬度)。根据硬度的情况确认导轨表面是否做相关热处理。
(2)确定导轨拆卸顺序,由于横向基准重新找正较困难,件7不进行分解,在机床本体上进行研磨;左右件3从砂轮台上优先拆卸;件1和件4从砂轮台中整体吊装(不分解)。
(3)吊装分离导轨。预吊装件4(砂轮本体),拆卸左右件3固定螺栓,分别抽出左右件3,整体吊出件4(砂轮本体)。
(4)测量各面磨损情况,确定各导轨间尺寸。如图4所示,详细测量并记录件4表面1,件3表面1、表面2,件1表面1、表面2,件7表面1、表面2的全段磨损量和导轨尺寸,进行下一步修复量的制定。
(5)静压导轨装配关系封闭环的确定。D-C=0.036~0.058mm(D为件4与件1装配后尺寸,C为件3的厚度),B-A=0.02~0.03mm(B为左右件1装配到件4后的尺寸,A为件7的宽度),两侧间隙一致。
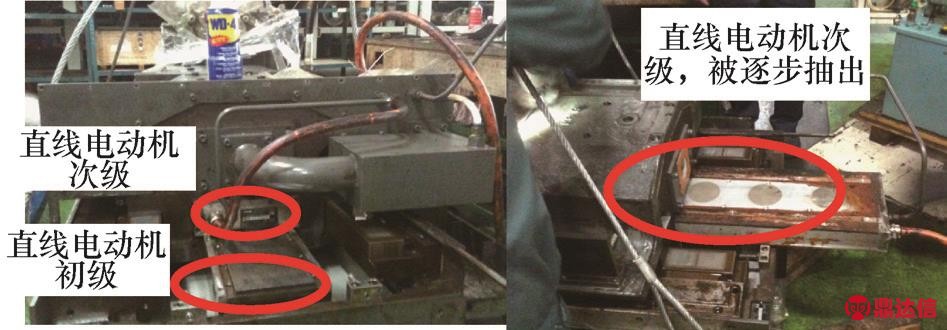
图3 直线电动机的拆卸
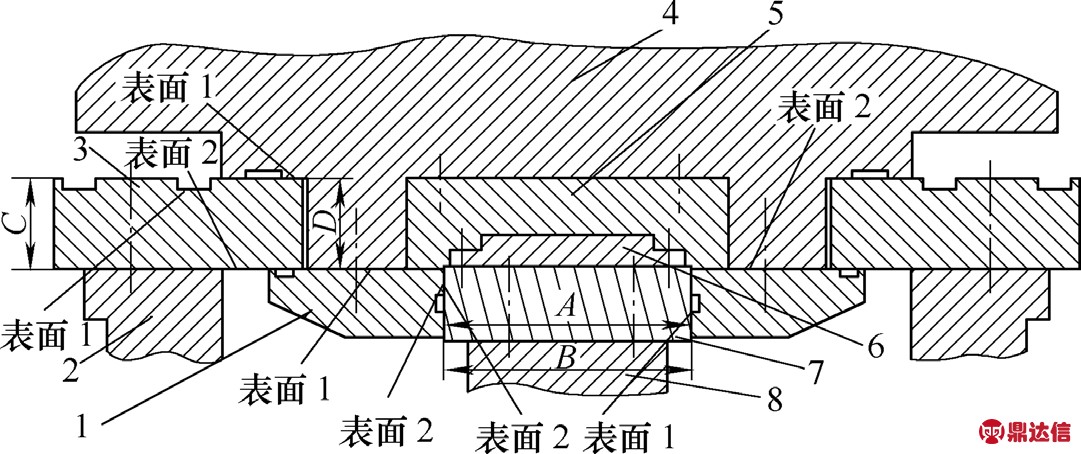
图 4
1.静压导轨压板 2、8.机床本体 3.静压导轨板 4.静压导轨静压腔体(砂轮台本体)5.直线电动机次级部分 6.直线电动机初级部分 7.静压导轨横向导轨
(6)静压导轨各导轨表面的磨削加工(利用与导轨要求精度相匹配的导轨磨床加工)。①图4中左右件3同时在导轨磨床上磨削,要求如图5所示,单面固定找正后,磨削磨损面,见光后,翻面,找正,磨削另外一面,直至见光。记录磨削后的尺寸C(见图4),并测量磨削后导轨的平行度、直线度和平面度,加工到要求。②吊装砂轮台(图4中件4和件1所在部分),如图6所示,通过件4表面1和件1上底平面找正砂轮台本体,装夹,磨削左右件1表面2,每个面磨削见光即可,记录磨削后的尺寸B(见图4),并测量两边的平行度,单边的直线度和平面度,加工到要求。③从砂轮台(图4中件4)处拆卸件1(左右两处),以件1表面2为基准,两件导轨同时找正夹紧,修磨件1表面1,修磨后测量表面1直线度、平面度,直至达到图样要求,具体如图7所示。④以图4中件4表面1左右两个面为基准找正砂轮座,夹紧,磨削表面2(左右两边达到相同尺寸,同时磨削),直至两表面同时见光,利用高度千分尺测量尺寸D(见图4),通过同时修磨件4表面2,达到D-C=0.05mm的尺寸。测量各面间的平行度,各面直线度、平面度加工到图样要求,具体如图8所示。
(7)各导轨面的配研和装配。导轨磨削后,为保证静压腔与导轨面间具有良好的密封性,需要确认和拖研各个导轨配合面间的接触面积。
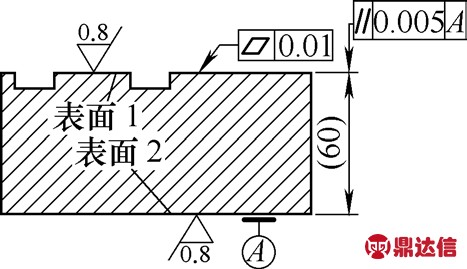
图5 静压导轨板修复
研磨图4中件7两端表面、件4表面2(左右两处)与件3表面1(左右两处)、件1表面2与件7表面1之间的贴合面积。
把床身(砂轮台横向托板)放置在工作台(镗床等工作台面)上,找正,如图9所示,固定,然后清洗床身处导轨安装面,制作铸铁研板,涂研磨颗粒,保证研磨后件7表面1、表面2直线度、平面度在0.01mm之内。
在机床本体上安装件3(左右两处),在件4上只安装一侧的件1,件3表面和件7侧面涂铅粉,手动来回拖动件4进行研磨,确定各面的接触面积,如果不到90%,需要钳工手动研磨。对静压导轨板上滑台高点涂细颗粒磨料,进行研磨,然后涂铅粉进行贴合面积的确认,反复拆卸导轨板,直至合研接触精度研点数20点/25mm×25mm,具体如图10所示。
按照同样的方式对其他导轨面进行合研,直到接触精度研点数20点/25mm×25mm。
砂轮架导轨副的组装。砂轮架滑台上的件经过上述修理后,再次进行清洗。直线电动机永磁体表面、初级线圈表面用丙酮清洗。用煤油清理节流孔油路分配板管路,并用气体检查节流孔的通畅。
安装图4中件4和件1,参考图1、图4调整到如下要求:D-C=0.036~0.058mm(D为件4与件1装配后尺寸,C为件3的厚度),B-A=0.02~0.03mm(B为左右件1装配到件4后的尺寸,A为件7的宽度)。
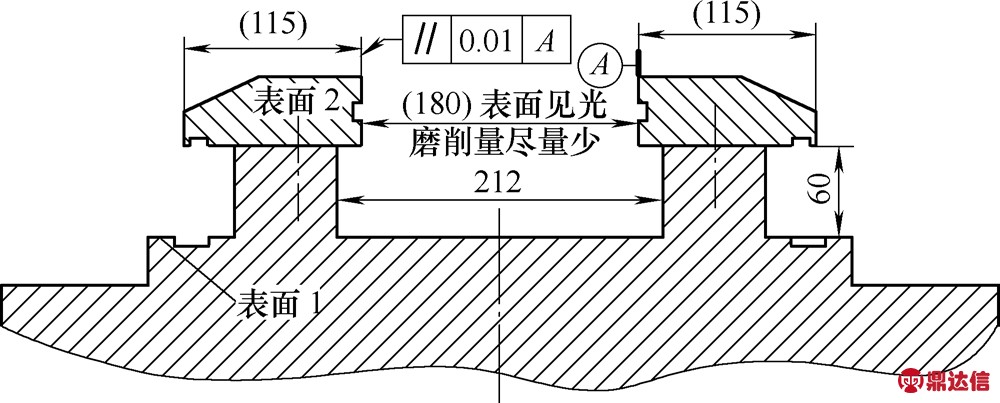
图6 静压导轨压板表面2修复
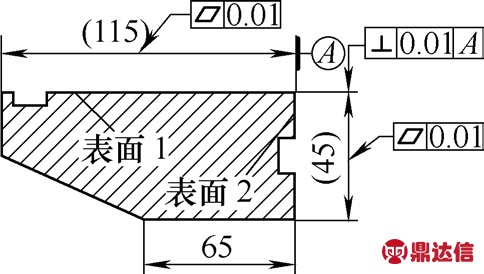
图7 静压导轨压板表面1修复
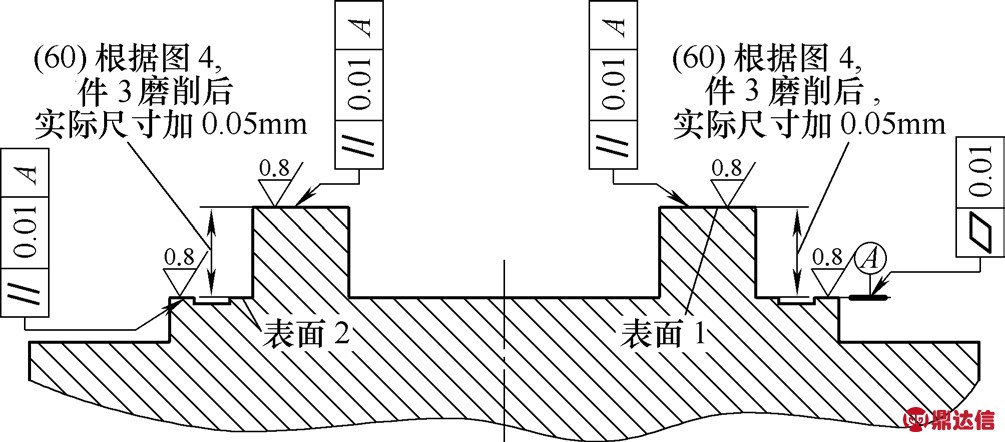
图8 静压导轨腔体(砂轮本体)修复
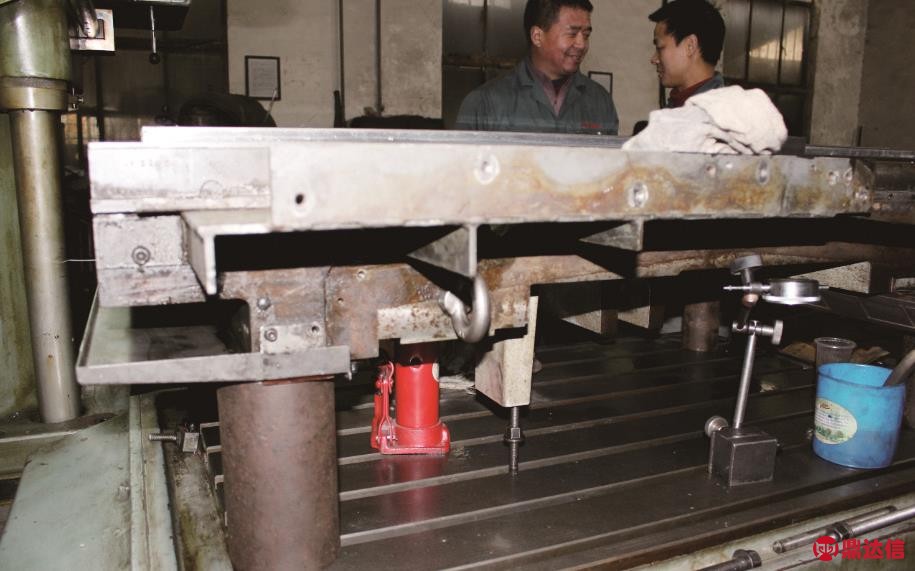
图9 砂轮台床身(横向移动滑台)固定和拖研
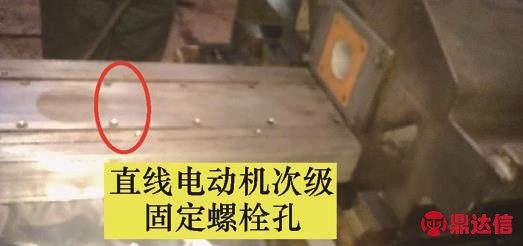
图10 导轨合研接触面积验证
由于横向导轨副间隙小,不易安装,参考图11所示制作四件安装导向块,导向块分别安装在压板(导轨3)端面的工艺孔上,进行安装调整。安装后,用塞尺测量各个导轨副间间隙是否符合要求。
直线电动机安装、试机。装配直线电动机初级线圈时,要严格按照与拆卸相反的顺序逐步的进行装配,次级固定螺钉的拧紧顺序及转矩也要严格按照要求进行(由于次级线圈为铝制品,安装螺栓顺序和方法需提前确认),如图12所示。
安装其他液压管路,通油后观察回油是否正常,手推砂轮架滑台感觉滑台的摩擦阻力是否均匀,并测量浮动量。
3.原因总结
静压导轨价值高,损坏后修复时间长、技术要求高,势必会对企业生产和维修成本带来极大影响。从静压导轨原理分析,静压导轨并非损耗件,不会出现上述损坏。出现上述故障,主要原因是导轨本体及其附属设备设计不成熟或维护使用部门使用维护不当导致,根据作者对静压导轨类设备多年维护经验,对引起静压导轨损坏的原因进行以下总结。
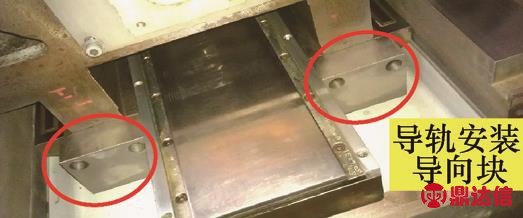
图11 横向导轨副的安装
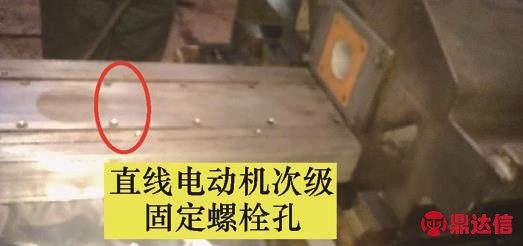
图12 直线电动机次级线圈的安装
(1)使用的油品牌号不符合要求。静压导轨加入了不正确的油品牌号或长时间使用变质油品,导致油品黏度系数降低,静压油膜建立不起来,浮动量小,容易使导轨间产生接触,产生磨损。
(2)静压导轨供油系统过滤系统失灵,大量颗粒堵塞静压导轨的节流孔,导致个别腔体的油量不足,建立不起压力和间隙,导轨部分处于滑动摩擦状态,长时间导致导轨的磨损。
(3)静压导轨防护设计不良或老化,导致磨削颗粒或污泥进入静压导轨间隙中,从而研磨导轨,导致静压导轨的磨损。
(4)切削液的侵入,切削液作为加工中刀具/工件润滑和冷却的重要介质,切削液流路在机床内堵塞或者导轨防护失灵情况下,切削液会进入导轨副的油路系统,随着切削液进入的还有大量磨削/加工颗粒,会导致静压油变质(黏度减小,浮动量不足)、侵入的颗粒在导轨副间作用,损坏导轨副。
4.提出建议
因此在静压导轨附属系统设计和维护提出以下建议。
(1)在设计静压导轨防护时,考虑可动部分防护间密封方式的加入和选择;机床内切削液回流通道/槽的水势和水压设计,以及防磨屑堆积。
(2)静压导轨液压系统过滤系统的设计,在泵的吸入口设置通油能力大(泵流量2倍以上)初级滤芯,泵出油口至导轨节流阀间设置单级或双级过滤器,要求过滤精度小于等于静压导轨的浮动量间隙。回油管路一般设置油水分离装置,且回油进入油箱口处放置强磁铁,用于吸附油中磁性金属颗粒。
(3)增加合理的机床切削液防止飞溅装置和切削液回流通道顺畅性设计。在工件主轴旋转或工件旋转作用下,切削液会以一定压力飞溅到导轨防护上,进而进入防护内,需要在设计时增加切削液防飞溅装置。
(4)需要定期对静压导轨液压系统进行维护。定期更换各级过滤滤芯;定期检测液压站油温和压力情况;定期更换液压油和清理油箱等工作。
(5)静压导轨各节流孔(见图2中件2)的定期疏通和相关密封的定期更换。
(6)及时清理机床内各切削液回流通道,特别是磨床,回流通道堵塞会导致切削液短时间大量积聚机床内部,从而漫过防护进入静压导轨区域,对此需要充分了解该机床对切削液防护结构,制定详细的清理维护计划。
(7)静压导轨各防护的定期更换,及时更换变形和受切削液侵蚀的防护,有利于防止切削颗粒的进入。