摘要:针对高加速度高精度定位气浮平台对气浮导轨高刚度高承载能力的要求,采用二维线性插值和有限元法推导平面气浮空气轴承的静态性能公式,利用数学软件MATLAB编写有限元程序计算气浮导轨的静态性能并分析相关参数对静态性能的影响。有限元分析结果表明:当气浮平台中节流孔之间的排距与气浮面宽度的比值为一定值、气浮厚度为另一定值时,气浮平台的角刚度和承载能力得到较优值。研究结果为气浮导轨的静态性能优化提供了理论参考,为气浮平台的结构优化提供了方向。
关键词:气浮导轨;承载力;有限元编程
气浮导轨的承载能力和刚度是保证高加速度高精定位气浮平台性能的重要因素[1-3]。一般情况下,导轨气浮面积的增大和节流孔数量的增多虽然可以不同程度上提高导轨性能,但同时也造成了精加工气浮面积的增大,加工难度以及生产成本的提高,甚至增加气浮导轨被由外力作用、灰尘以及温度变化导致的变形卡死的危险。因此设计时,在满足结构性能的前提下,应尽量减小导轨的气浮面积和节流孔的数量。针对平台的整体结构特点,气浮导轨在承载着活动部件的自身重力的同时,还承载着由于直线电机驱动力未通过平台质心,在启/停的瞬间产生的冲击力以及该冲击力引发的作用于X轴和Y轴移动滑台的气浮导轨上的瞬时扭矩,因此导轨的静态性能必须进行准确计算。
通常采用有限元法来计算气浮导轨的性能,在编写有限元程序时,为便于分析各种参数(比如数量、间距、排距和气膜厚度)对导轨静态性能的影响,需要将平台的结构尺寸进行参数化处理,进而对导轨结构进行优化。
文中研究的是用于芯片制造设备的高加速度高精度定位气浮平台的气浮导轨设计,给出了气浮导轨的结构设计,并依据有限元分析方法,分析其结构的静态性能并对各结构参数(如间距、排距、数量和气膜厚度)进行优化。
1 气浮导轨
高加速度高精度定位气浮平台的结构如图1[4] 所示。气浮导轨由上导轨、下导轨以及供气系统3部分组成,其中上导轨上面开有节流孔,其承载原理如图2所示。当供气压力为P0时,气体经节流孔c后压力变为Pd,最终流至外边界,此时压力变为标准大气压力Pa。两导轨间存在气体压力分布,将上导轨上下表面气体压力差值进行积分得到导轨承载能力W。当节流孔直径取定值φD时,此时气膜h=(h1+h2)变大,导轨承载能力变小,导轨下沉,气膜h重新变小,恢复到稳定值。反之,当气膜h变小,导轨承载能力增大,导轨上浮,气膜h重新变大,恢复到稳定值。综上所述,当外载荷为一定值时,气浮导轨稳定在一定厚度的气膜上,保证导轨内外稳定。
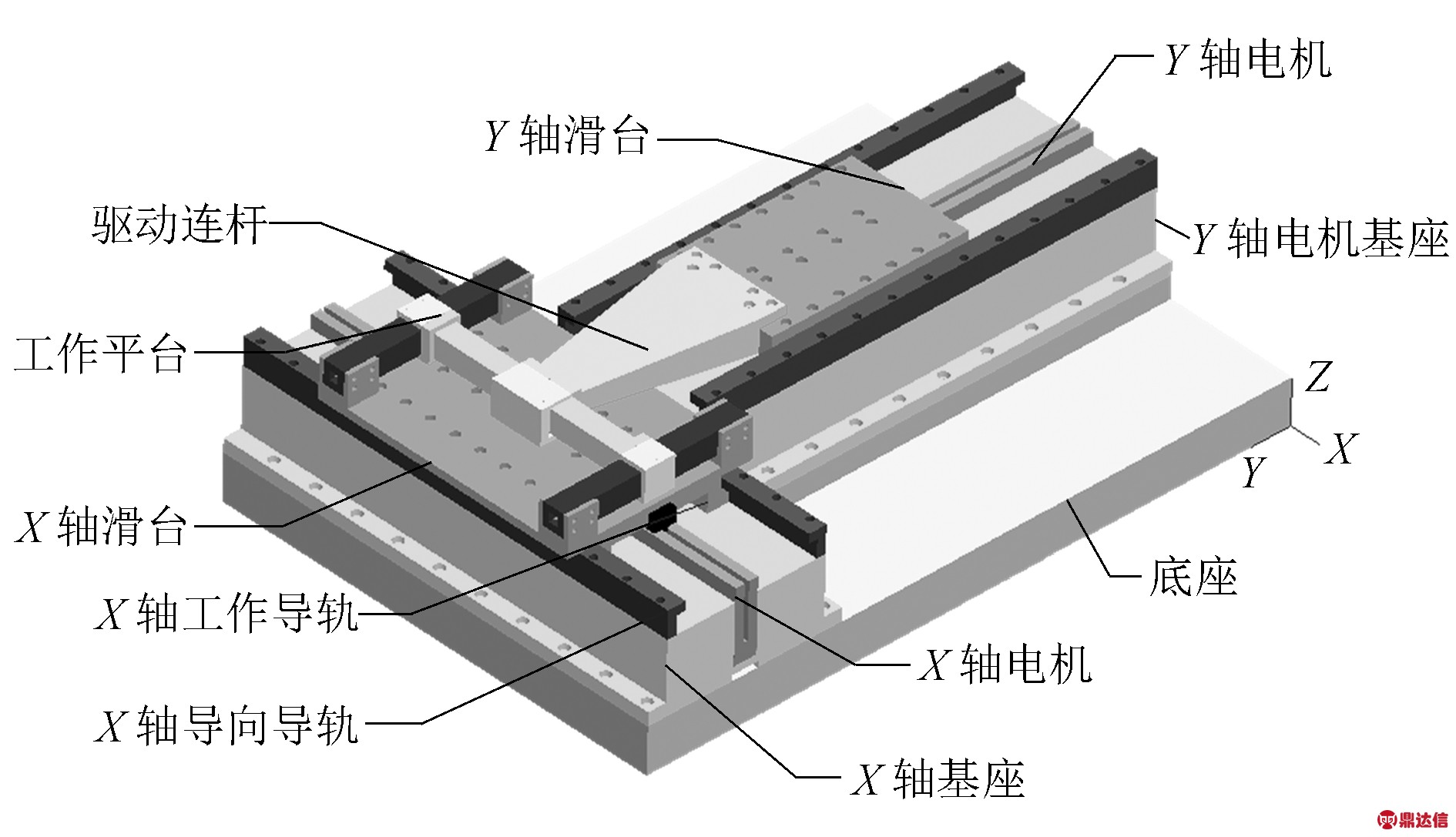
图1 高加速度高精度定位气浮平台结构示意图

图2 气浮导轨原理图
由于实际工况下气浮导轨需要较强的静态承载能力,因此文中选择小孔式节流导轨[5];同时考虑到气浮平台采用广义并行结构时导轨需要承受一定的扭矩,以及气浮平台加工的难易程度,文中选择闭式静压导轨结构。
2 气浮导轨设计
2.1 气体润滑的公式表示
气浮导轨中雷诺公式成立的相关假设如下:1) 间隙内的气体流体为牛顿等温流体,流态为层流,因而不予考虑能量方程问题;2) 流场为定常流场,因此各状态量对时间的微分项可以略去;3) 与黏性力相比,忽略流体惯性力及体积力的影响;4) 在假设1)的前提下,忽略高度方向的气体流速;5) 压力和黏度在膜厚度方向上无变化;6) 流体在固定界面无滑移,即贴于界面的气体流速与界面速度相同;7) 对于数量级,设长度以及宽度方向上为1,间隙高度方向上为10-4[6]。
通过运动方程、连续性方程、等温条件下的状态方程以及上述假设条件下的雷诺公式,得到可压缩性流体Reynolds方程:
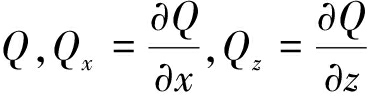
(1)
式中:h为流体膜厚度;μ为流体黏度;p为流体压力;V为运动表面y方向上的速度分量,表示的是气膜厚度的变化速度,。
2.2 气体分布有限元公式推导
图3所示为气浮导轨典型模型,其中B表示x向导轨的宽度,L表示z向导轨的长度,h为气膜厚度,B1为节流孔之间的排距,Orifice为节流孔[7-8]。
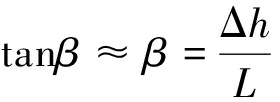
图3 气浮导轨模型
通过节流孔的气体流量公式:
mi=φ
(2)
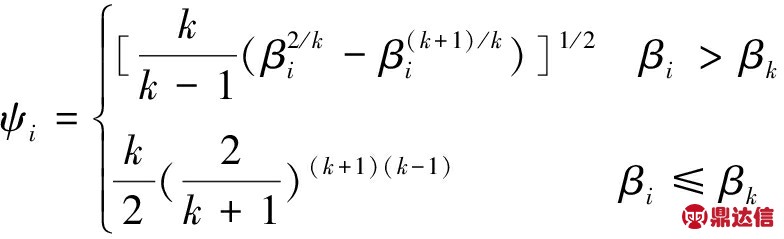
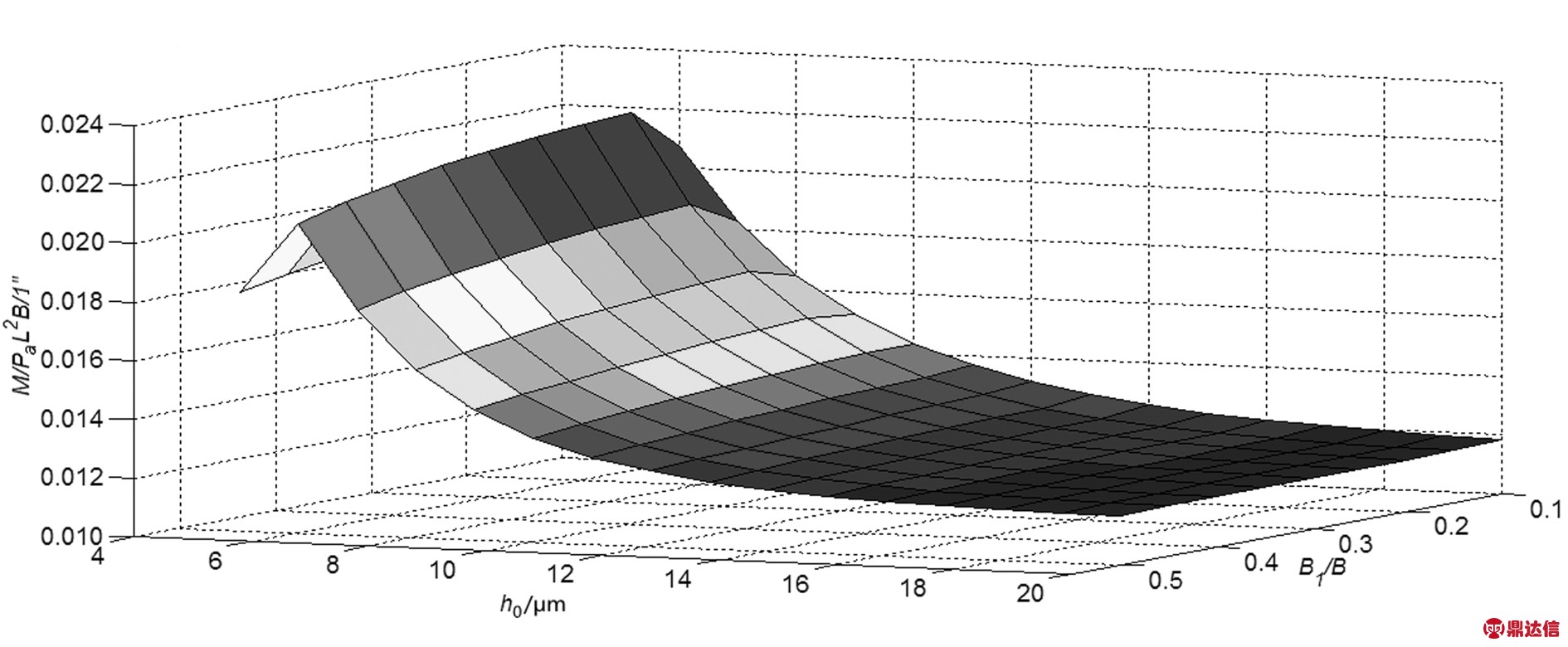
式中:mi为第i个节流孔的气体质量流量;ps为供气压力;ρa为标准大气压力下空气密度;,为节流压力比,其中pdi为节流孔后压力;k为气体比热比,空气的k=1.4;ψi为流量函数;φ为流量系数,本文φ=1;A为节流孔节流截面面积。
对式(1)进行公式变换可得:

(3)
将式(3)无量纲化:

(4)
式中,是p的无量纲值。
,为气膜厚度的无量纲值,其中Δh是h在z=0和z=h时的差值,Δh=0.3μm[4]。由于β很小,在计算中,
,所以
。在节流孔处δj=1,在非节流孔处δj=0。
引入新的变量,可压缩Reynolds方程可表示为
的偏微分方程:
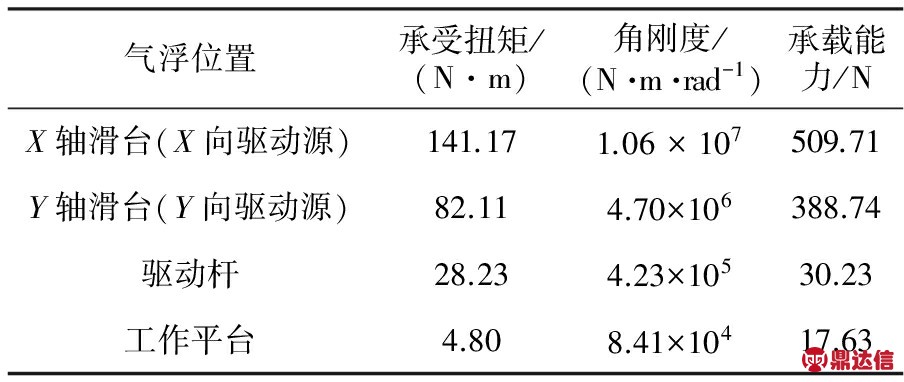
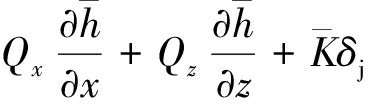
(5)
设*表示待求压力的初始值,求出关于x,z的函数
和
,其中
)表示待求压力分布的预置值;
取决于S2。
(6)
将式(6)代入式(5)得

(7)
式(7)在Ω域内|Γ,其变分形式可表示为

(8)
其中插值函数:
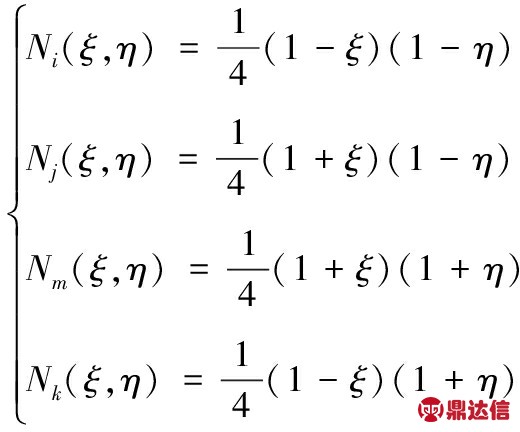
(9)
相应地,局部坐标系和整体坐标系下的导数转换可表达为
(10)
泛函J(Q)可以表达为对于各单元积分之和,即∬e{}dxdz,其中记号
表示对全部单元求和;或
Je,其中
代表典型单元e上的泛函。
(11)
Je适用于任何单元,为Qi,Qj,Qm,Qk的函数,由此得到的总体泛函Je,为各节点压力函数Q的二次多元函数。这样对于泛函J求取极值的问题就转化为求解多元函数的极值问题。

(12)
将式(12)简化为
K·Q=B
(13)
其中各参数:
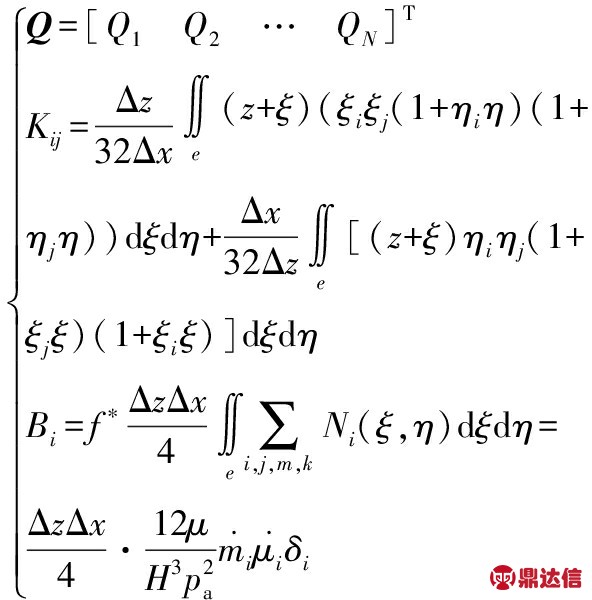
(14)
将边界节点上压力分布函数值代入式(13),得到K0个关于内部节点未知压力分布函数Qn(n=1~K0)的方程,按行重新编号得到新的线性代数方程组:
K·Qn=B n=1,2,…,K0
(15)
节点气压分布如图4所示。
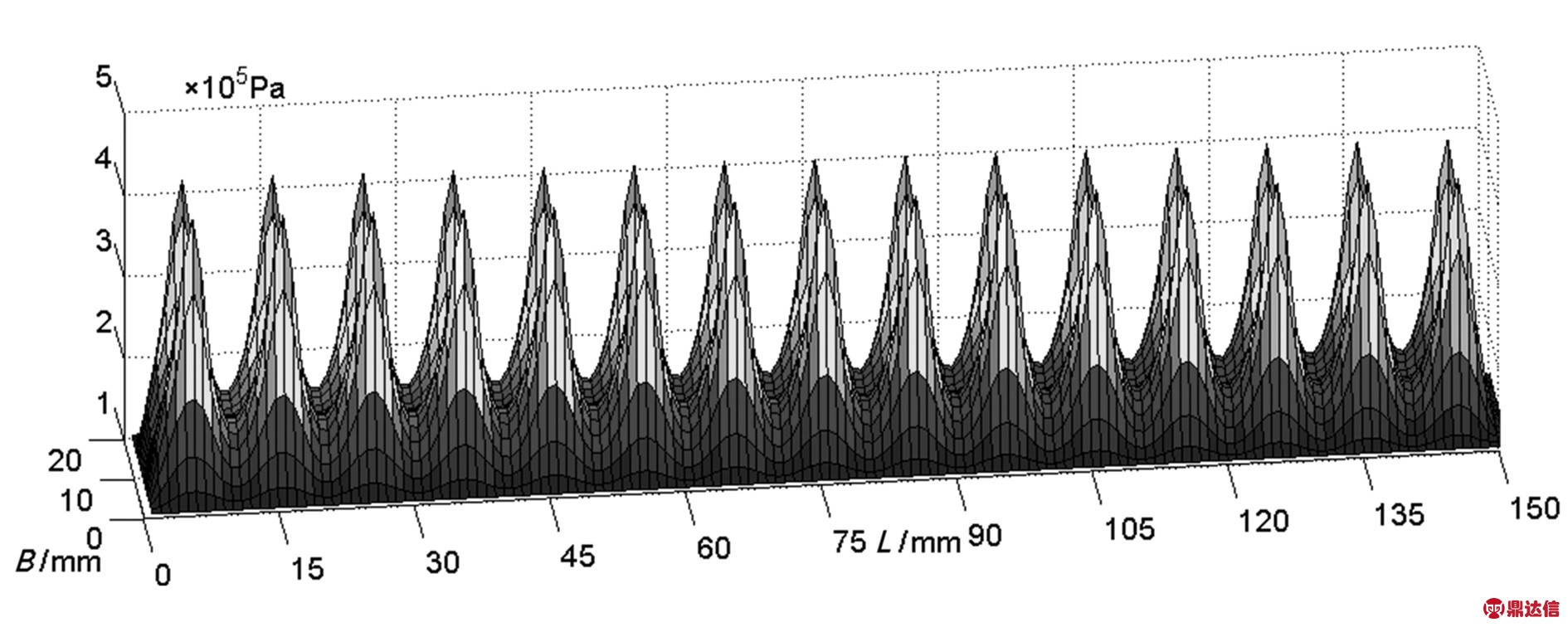
图4 节点的气压分布图
2.3 气浮导轨静态性能公式推导
每个单元的无量纲承载能力可以通过下式来计算:

(16)
单元的承载能力可表示为:
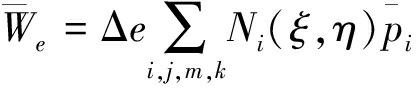
(17)
气浮导轨表面承受的扭矩可通过式(18)计算。
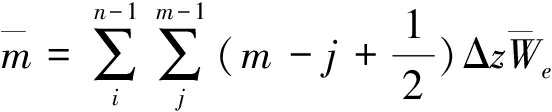
(18)
根据式(19)和图5计算气浮导轨表面合力。
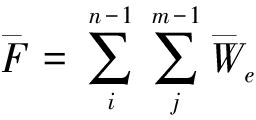
(19)
图中2;ε为导轨安装误差;F1,F2为气膜产生的气浮力;Δh=|h2-h1|;L为气浮导轨长度;F3与
是F2的等效力,产生扭矩;h1为气浮导轨上表面的平均气膜厚度;h2为气浮导轨下表面的平均气膜厚度。如果h1>h2,气浮导轨上下表面压力不同产生扭矩。
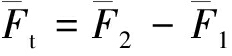
(20)
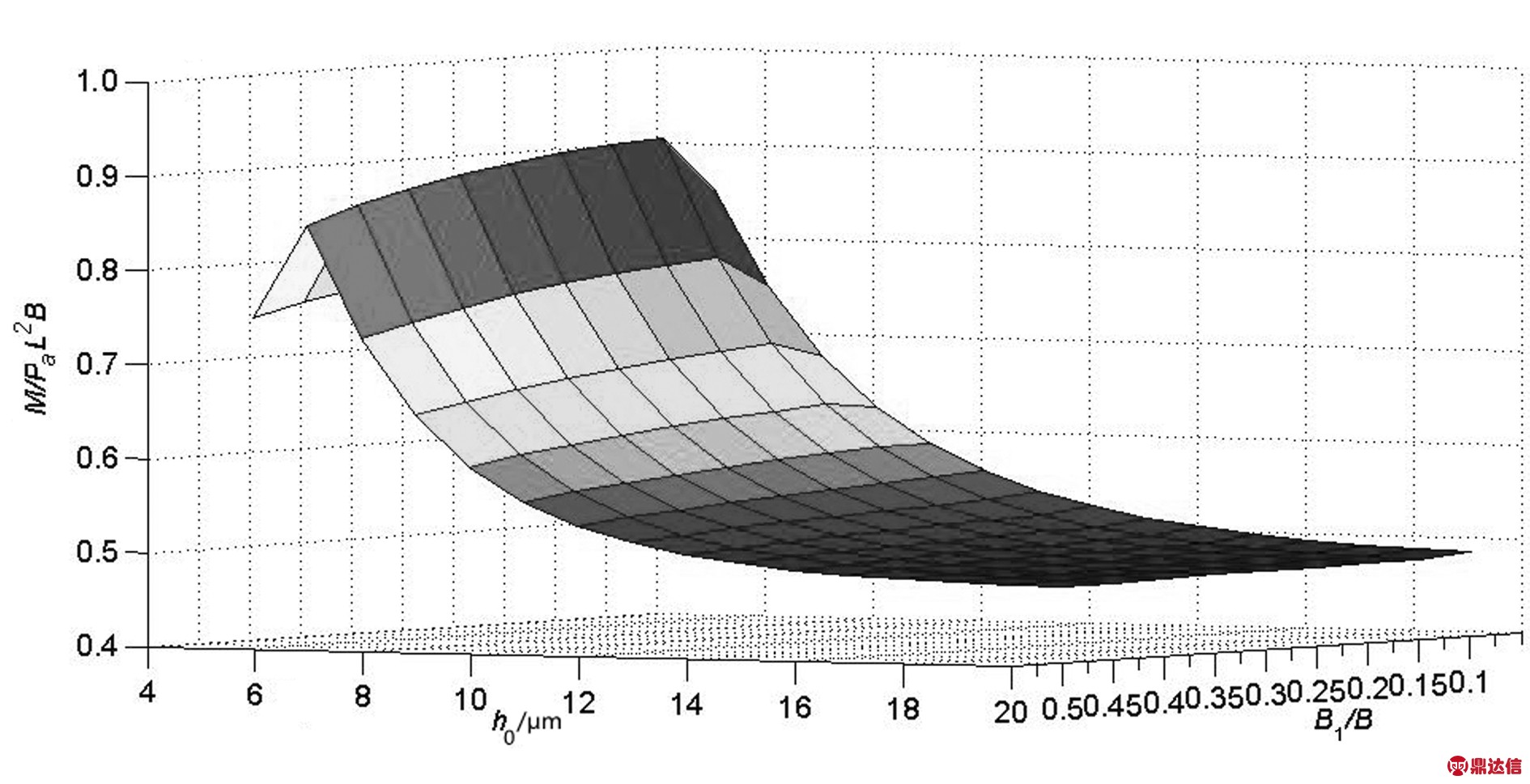
图5 受扭矩作用后导轨气浮面位移
导轨承载力:
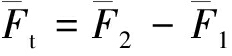
(21)
导轨角刚度:

(22)
3 气浮导轨有限元计算与优选
根据第2章所推导的公式,通过MATLAB编写程序,求取优化设计参数[9]。节流孔数量、节流孔排距、气膜厚度和节流孔直径等因素的选取会影响气浮导轨的性能。供气压力Ps设定为5×105Pa,节流孔直径设定为0.8mm[1] (根据文献中实验,节流孔的选取不宜过小),大气压力设定为1×105Pa,X方向和Y方向导轨长度分别设定为300mm和220mm(如图1所示)。对气浮导轨不同参数时的静态性能进行分析,其中节流孔排距B1和导轨所能承受的最大扭矩之间的关系如图6所示。从图7中可看出,当B1/ B≈0.15时,导轨承受角刚度最大。通过图6与图7可得,在气膜厚度h达到6μm时,气浮导轨能承受的扭矩最大,同时具有的角刚度最大。图中M为气浮导轨承受的总扭矩。
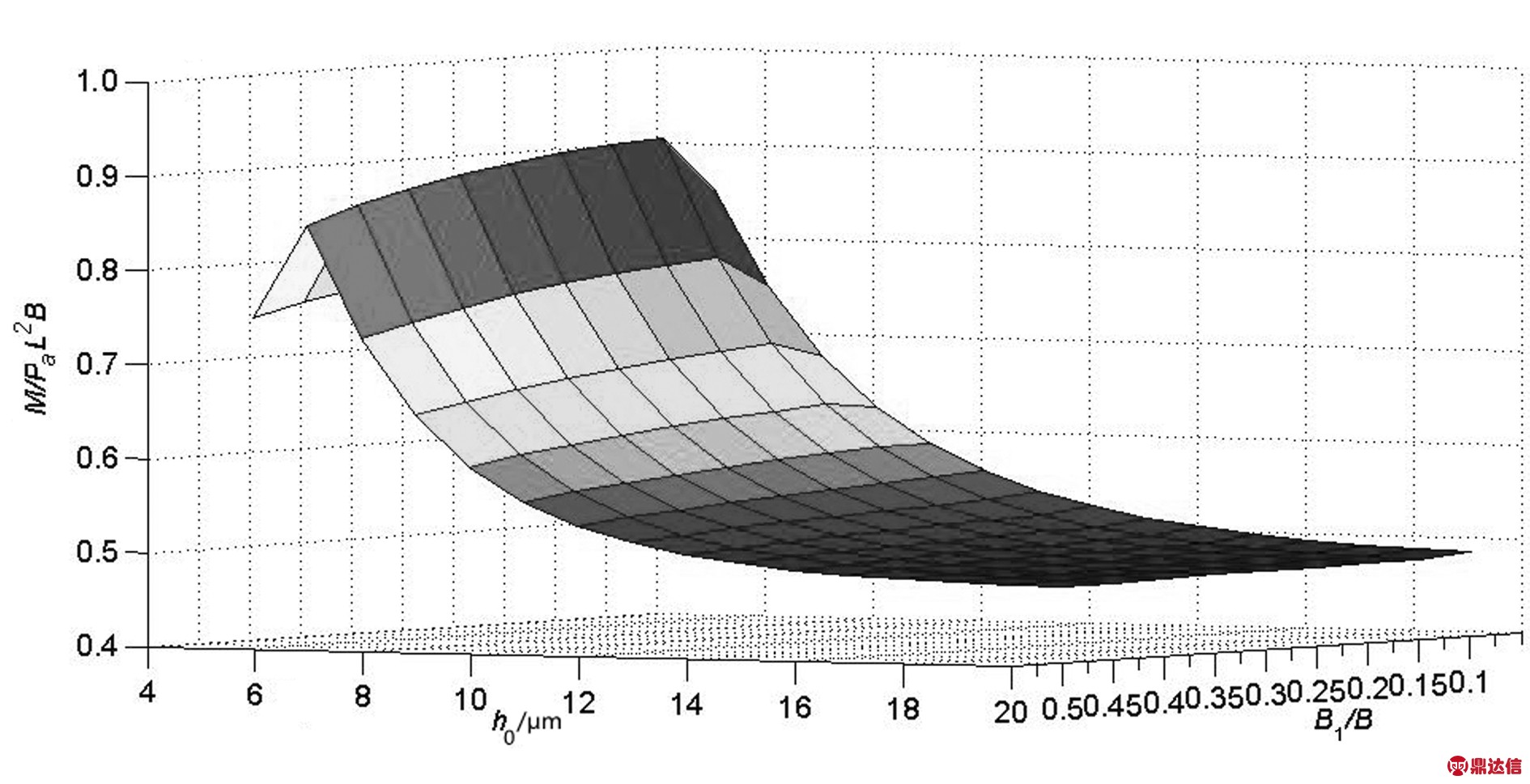
图6 节流孔排距与气浮导轨所承受扭矩的关系图
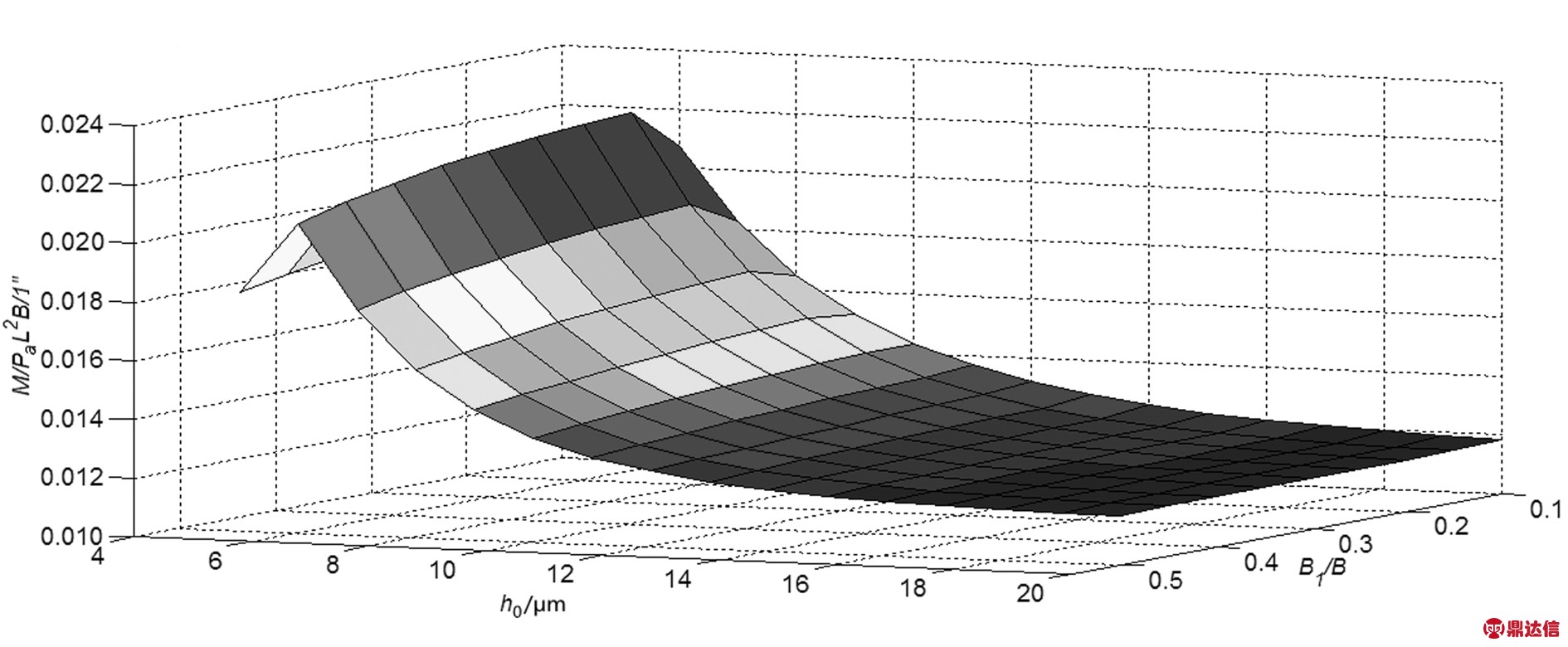
图7 节流孔排距与导轨角刚度的关系图
当B1/ B≈0.15时,角刚度与气膜厚度关系如图8所示,h0是气浮导轨下表面气膜厚度。由图可得以下结论:角刚度随着气膜厚度的增大而降低;气膜厚度h0与h1取6μm时,气浮导轨的角刚度达到最大。图8中M/PaL2B表示的是角刚度,代表在1″能承受的扭矩为M/PaL2B。
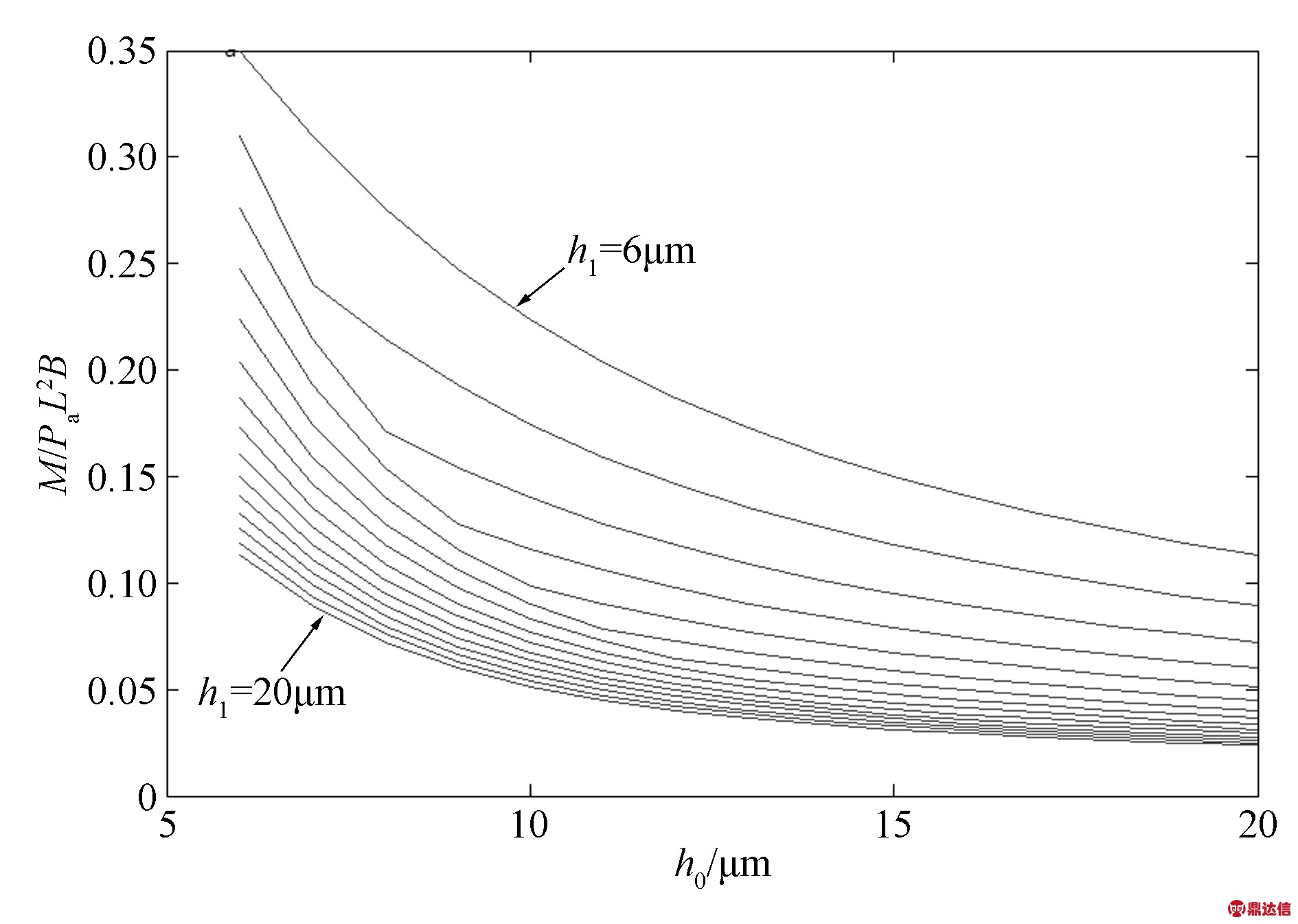
图8 当B1/ B≈0.15时,角刚度与气膜厚度关系
当B1/ B≈0.15时,承载能力与气膜厚度关系如图9所示。由图可得,当气膜厚度分别取h0=6μm和h1=20μm时,气浮导轨承载能力达到最大。考虑到气浮导轨承载面加工难度以及导轨承载能力,导轨上下气膜厚度和不大于20μm,单侧气膜厚度最大不超过14μm,因此在角刚度满足设计要求的前提下,选择气膜厚度为6μm。图中F/PaLB表示的是承载能力与大气压产生的力的比值。
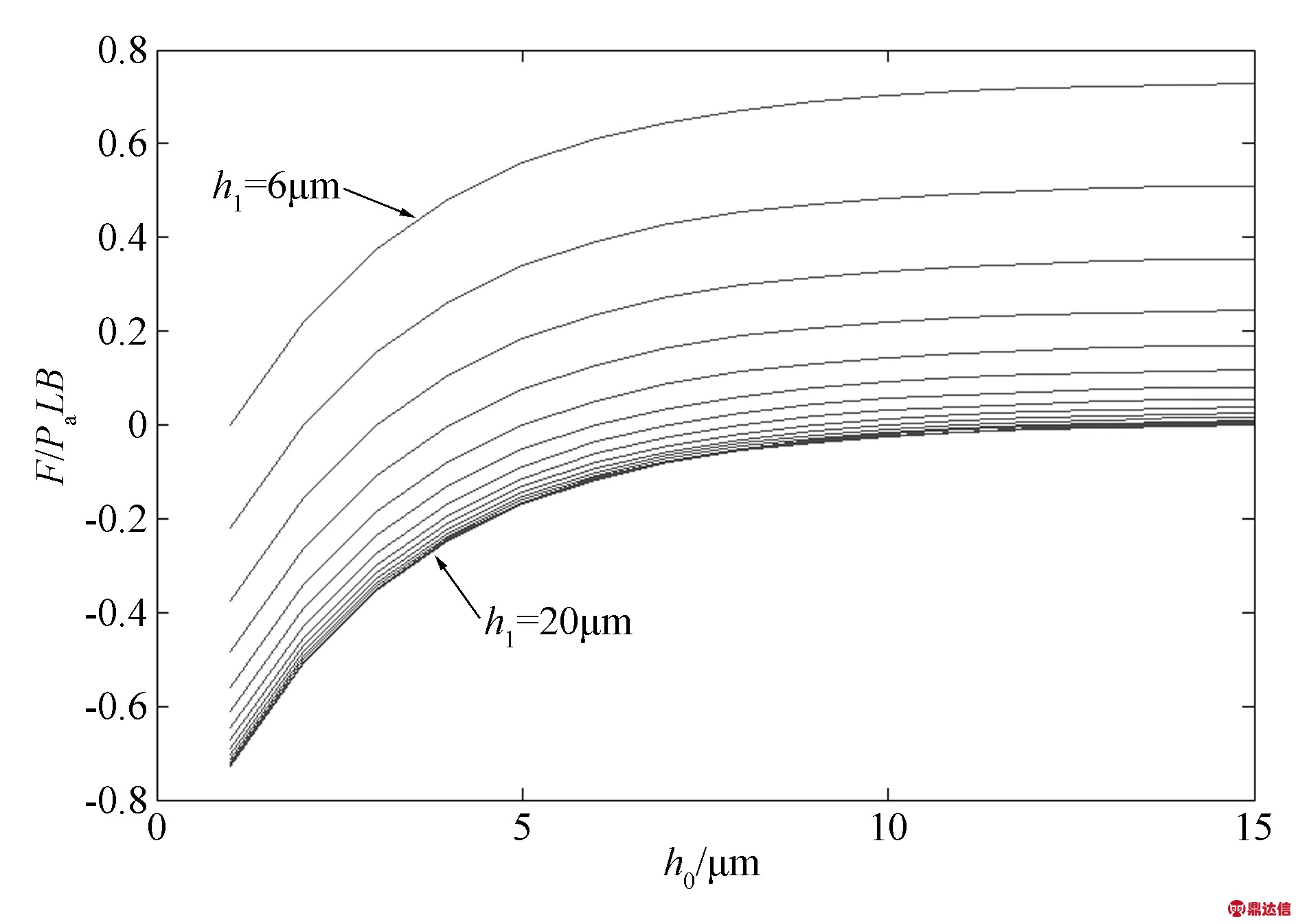
图9 当B1/ B≈0.15时,承载能力与气膜厚度关系
平台中各气浮导轨静态性能计算结果见表1。
表1 气浮平台内气浮导轨静态性能
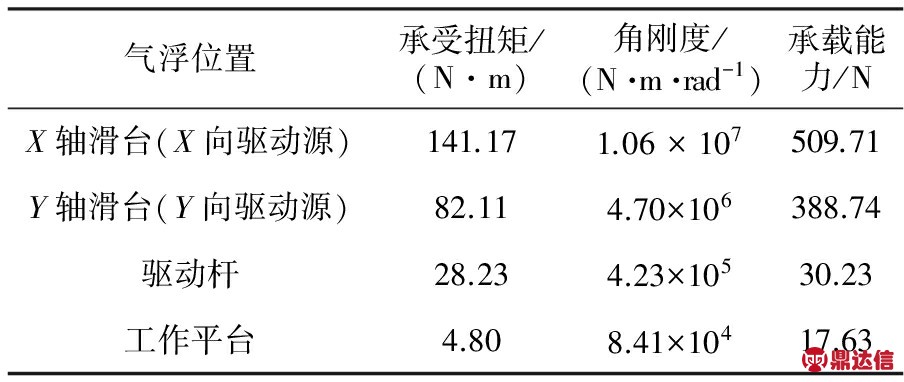
4 结束语
由于条件限制,文中所涉及的有限元分析缺少试验支撑,因而文章更倾向于理论方面的研究。气浮导轨在电子制造设备中普遍使用,其性能严重影响设备的加工精度与效率,因此对导轨的承载能力进行计算是必要且必须的。有限元分析为气浮导轨承载能力分析提供了新方法。本文分析的气浮导轨的结构相对简单,对气浮导轨设计具有一定的指导作用,但具有一定的局限性,后续工作需要提供试验支撑,同时针对更复杂的气浮导轨结构进行有限元研究。