摘 要:针对渐进成形中的破裂缺陷,将Oyane准则引入数值模拟中,有效预测了渐进成形中金属板料的成形极限.首先,针对DC56D+Z钢板,基于获取的Oyane准则材料参数,通过试验与数值模拟确定了破裂积分值I=4为破裂的临界条件.然后,基于响应面法建立了工艺参数与I积分值之间的非线性模型,且通过方差分析验证了该模型的有效性.研究得出:该数值模型可以有效预测最大破裂积分I值,I值随着成形角α、层间距Δz和工具头直径d的增大而增大,3个工艺参数的影响作用逐渐减弱,且α&Δz、α&d两种组合的交互作用影响较大.
关键词:渐进成形;Oyane准则;破裂预测;工艺参数;数学模型
渐进成形技术(incremental sheet forming,ISF)是一种针对金属板料的先进快速柔性成形技术[1-2].在无需专用模具的条件下,通过控制工具头的加工轨迹对板料进行逐层加工得到变形量大、形状复杂的产品.在小批量生产、产品定制、缩短研发周期和生产成本等方面具有优越性[3-4].目前,渐进成形技术在交通运输、医疗、航空航天等领域得到广泛应用[5-7].
现状干支渠均为土渠,边坡冲刷,底部淤积,输水能力不足。西片区南侧尚有3万多亩 (1 hm2=15亩,下同)耕地,通过引蛇家坝干渠水进行灌溉,需对区域内灌溉水系进行规划整治,以满足近期灌溉要求。
近年来,渐进成形的板材破裂及预测一直是研究的重点和难点.Hirt等[8]提出成形后板厚t与初始厚度 t0符合正弦定律 t=t0sin(90°-θ).Hussain 等[9]建立了渐进成形过程的经验成形极限图(FLD),并证明了当层间距和工具头直径在一定范围内时,所建FLD图的有效性.Huang等[10]设定最大厚度减薄率,通过板料减薄率的大小来判断断裂的发生.上述预测方法通常对加载路径有特殊要求,或不能有效地预测塑性较低金属的破裂情况.基于韧性破裂准则不依赖外界加载条件的特点及其在传统板材成形工艺的成功应用,有学者将此方法引入到板材渐进成形工艺中.李磊等[11]运用Oyane破裂准则证明渐进成形的成形极限远高于传统板材成形工艺.Malhotra等[12]运用Xue[13]提出的断裂准则取得了较以往模型更准确的成形力和破裂预测结果.目前关于破裂准则的研究不够深入,且不能对实际渐进成形加工起显著的指导作用.因此,找到适合预测渐进成形破裂情况的破裂准则,变得尤其重要.本文应用Oyane韧性破裂准则对渐进成形的成形极限进行了预测,并结合试验和有限元分析,确认了临界破裂积分值.基于响应面法建立了工艺参数与破裂积分的数值模型,探讨工艺参数及其交互作用对韧性破裂的影响规律.
1 韧性破裂准则的应用
1.1 Oyane准则
本文所使用的Oyane准则[14]为:
在谐振式光学陀螺信号检测系统中FPGA芯片40 MHz的系统采样率决定了系统中锁相放大器的采样率也为40 MHz。为了匹配时钟并保证较高的检测精度,数字低通滤波器的采样率也要求在40 MHz。对于信号检测系统而言,低通滤波器的截止频率以及阶数的可调节性可满足不同信噪比信号的检测,具有通用价值。

式中为破裂发生处的等效应变;σm为静水应力;
为等效应力
为等效应变;C、C1为材料常数.
墙体形式:墙面材质整改后只有面砖、外墙防水涂料两种;墙面色彩只有白色一种;围墙总高2.15m,墙体高1.8m;
为了后续应用的便捷,将Oyane准则变形为:

式中:I为积分值,当I大于一定临界值时,材料发生破裂.
品牌管理组织在图书馆并非是一个非常重要的组织,而品牌管理负责人也并不具备很大的权利,所以,管理层决策支持机制、相关人力资源的保障机制、图书馆各部门协调保障机制等一系列制度的预先确定是品牌管理组织得以正常运作的制度保障。
1.2 材料属性
试验采用尺寸为160 mm×140 mm×0.8 mm的DC56D+Z钢板为研究对象,其力学性能参数如表1所示.材料常数C和C1是Oyane准则应用的基础.本研究中,结合单向拉伸和平面应变拉伸得出C=-0.174,C1=-1.117 5.
表1 DC56D+Z钢板性能参数
Tab.1 Performance parameters of DC56D+Z steel plate

?
1.3 FEM模型
基于ABAQUS软件,建立的渐进成形CAE模型如图1所示,包括工具头、板料、支撑和上下压边圈五部分.模型采用S4R壳单元,板料与工具头的摩擦系数为0.05,板料与其余部件摩擦系数为0.25,上下压边力差值为2 000 N,刀具轨迹为UG处理好的相应数据(成形角 α、工具头直径 d、层间距 Δz).工具头网格大小为板料网格大小的1/4.Oyane准则通过VUMAT子程序实现.
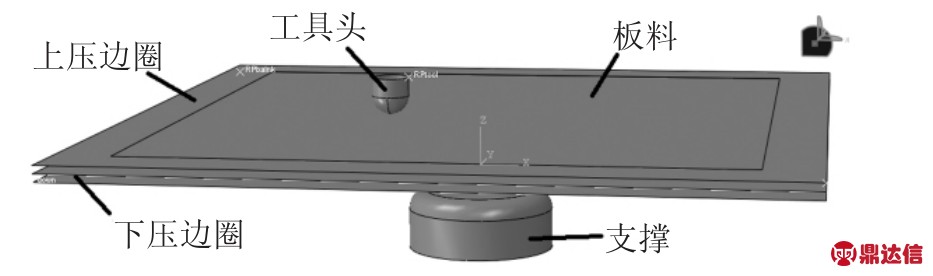
图1 板材数控渐进成形CAE模型
Fig.1 NC incremental sheet metal forming CAE model
2 Oyane模型对渐进成形的破裂预测
2.1 试验参数
采用重庆大学三轴数控渐进成形机NH3532分别加工成形角(α)为 75°、80°、85°、90°的四种去顶圆锥件,目标制件尺寸如图2所示.试验加工参数为:层间距Δz=0.5 mm,工具头直径d=8 mm,加工速度V=2 000 mm/s.此外,以相同的参数在ABAQUS软件上进行有限元模拟.
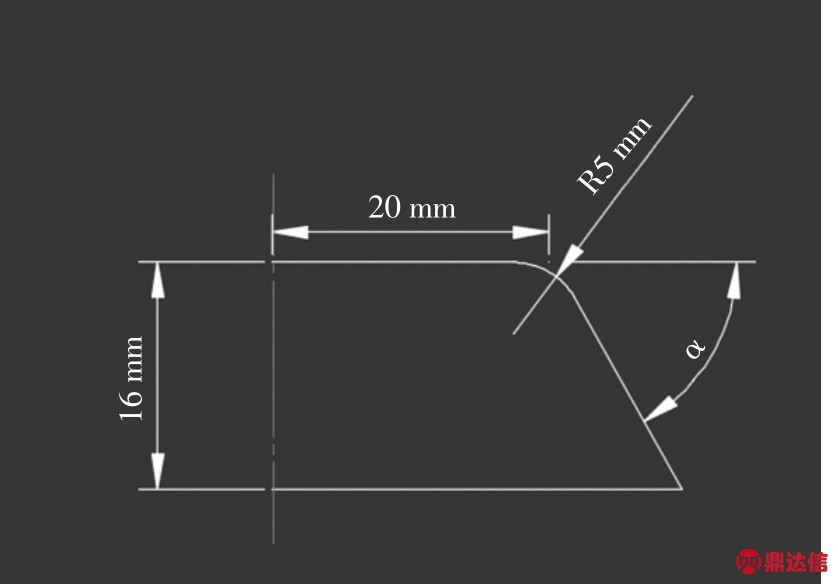
图2 目标制件尺寸
Fig.2 Size of target parts
2.2 预测结果与讨论
如图3所示,只有当成形角为75°时,制件才能成功加工,而成形角为 80°、85°、90°的制件均出现破裂现象.由此说明,这种加工条件下的目标制件的极限成形角为75°~80°间的某个角度.分析三组破裂制件的壁厚发现,三组试样从顶圆到侧壁厚度逐渐降低,当成形深度达到一定值时试样发生破裂,且三组试验的破裂均发生在制件侧壁.成形角α为75°、80°、85°、90°时的最大成形深度分别为:16 mm、8 mm、7.5 mm、6 mm.随着成形角的增大,最大成形深度逐渐降低.
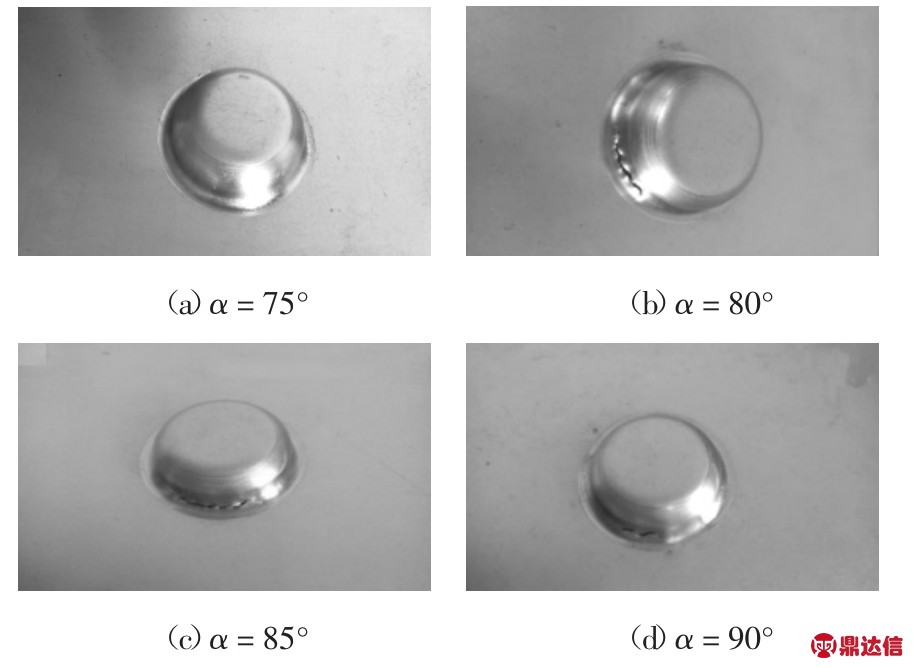
图3 渐进成形加工所得制件
Fig.3 Workpiece made by incremental forming
有限元模拟结果如图4所示,只有当成形角为75°时,才能完整模拟得到加工高度为16 mm的制件.整个加工过程中破裂积分I值从顶圆到侧壁底部呈现先增大后减小的趋势,这与渐进成形制件的板料厚度减薄率的变化情况一致[15],最大破裂积分值(I=3.45)出现在板料侧壁中下部位.当成形角为80°、85°、90°时,破裂积分 I最大值分别为 4.047、4.261、4.400,且其破裂时加工高度分别为8.230 0 mm、7.480 2 mm、5.937 0 mm,与试验结果吻合.破裂的三组最大积分I值均为略高于4的某值,然而,试验所测值为平均值,模拟测定为单元瞬时值,实际临界破裂积分值会比模拟测得的略小.因此,临界破裂积分值I=4可作为预测渐进成形过程中板材破裂是否发生的判据.
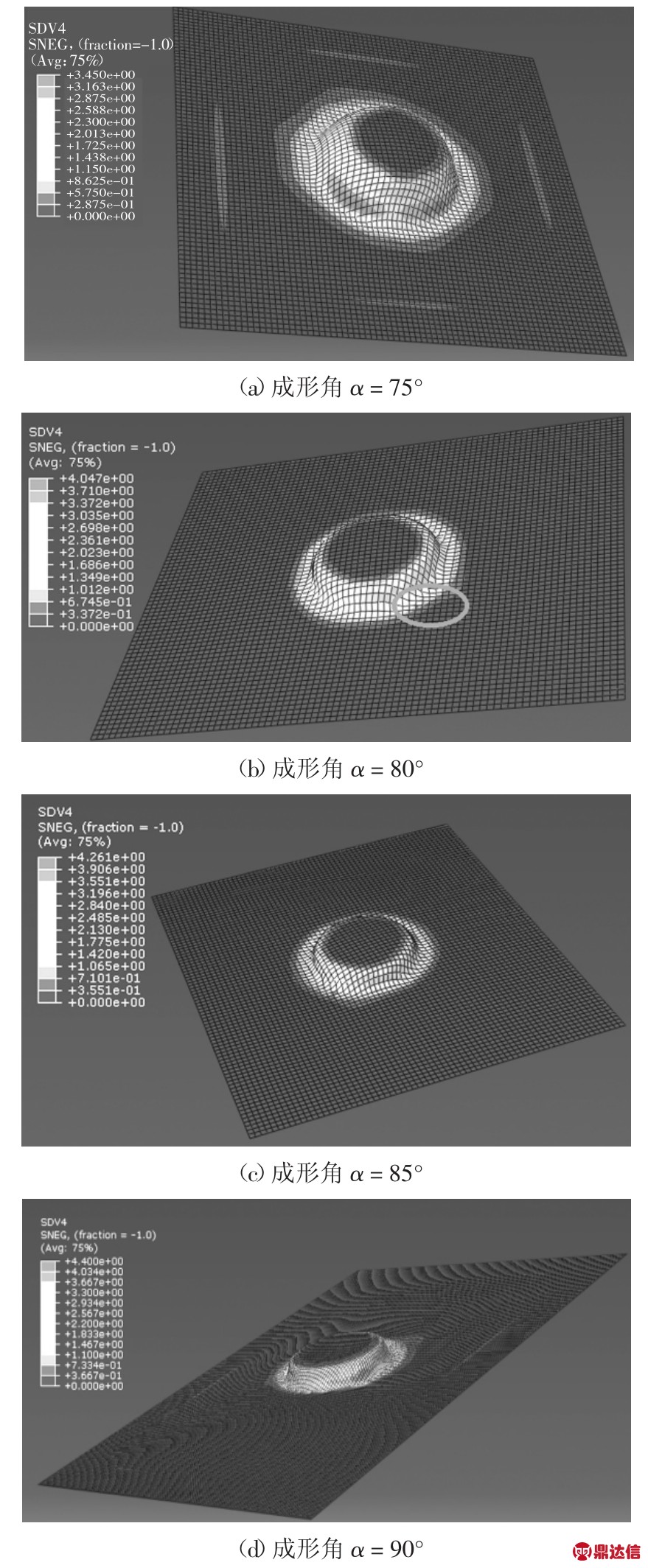
图4 不同成形角的有限元分析结果
Fig.4 Finite element analysis results of different forming angles
3 工艺参数对韧性破裂的影响
当I>4时,板材会发生破裂.为了避免板材发生破裂,探究工艺参数对破裂积分I值的影响规律意义重大.选用Design Expert软件中的Box-Behnken方法设计正交试验.为保证结果的有效性,将正交试验的中心点试验(α =40°,Δz=0.6 mm,d=10 mm)重复3次,共进行15组试验.因素水平如表2所示.
表2 因素水平
Tab.2 Factor levels
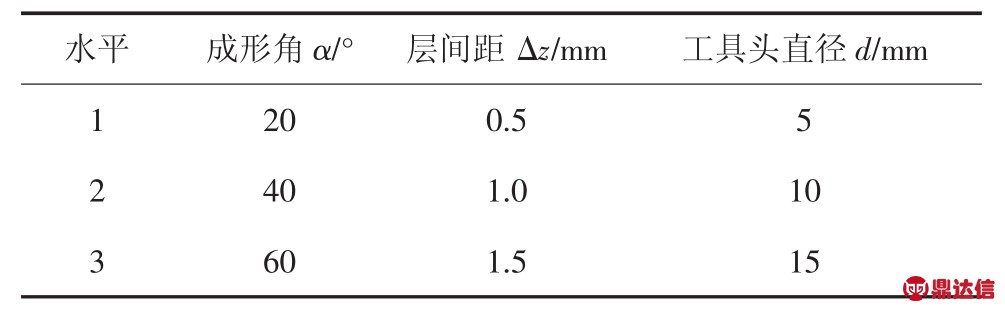
?
3.1 数值模型的建立
正交试验的数值模拟结果如表3所示,选用响应面模型中的二次模型[16]:
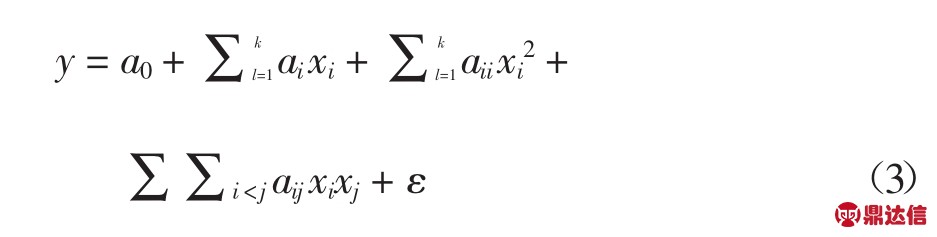
式中:y为响应拟合函数,即为最大破裂积分值I;k为变量组合数(k=15);a0,aii,aij为待定回归系数,个数为(k+1)(k+2)/2;ε 为随机误差;xi为相互独立的设计变量.
其实,类似问题完全可以通过坚持市场主导与政府引导相结合的新机制获得更好解决,例如《意见》中要求的健全区际利益补偿机制等等。应该看到,当下新出现的重大形势变迁是,中国依靠出口与投资双轮驱动的发展模式基本已经走到尽头,中国以及中国各地区下一步的发展,必须转向更为注重挖掘国内市场一体化带来的规模经济效应,因此,在这种倒逼形成的巨大压力下,我国区域协调发展机制破旧立新已迫在眉睫、势在必行。
为使港珠澳大桥桥墩警示标志能稳定工作,始终处于良好状态,并能在阴雨天气下连续工作20个日历天,需要对标志的供电系统进行精心的设计,包括灯器的选用,电池的选用、配置,太阳能板的选用、配置;输电电缆的选用等。
表3 正交试验安排及数值模拟结果
Tab.3 Arrangement of orthogonal test and results of numerical simulations
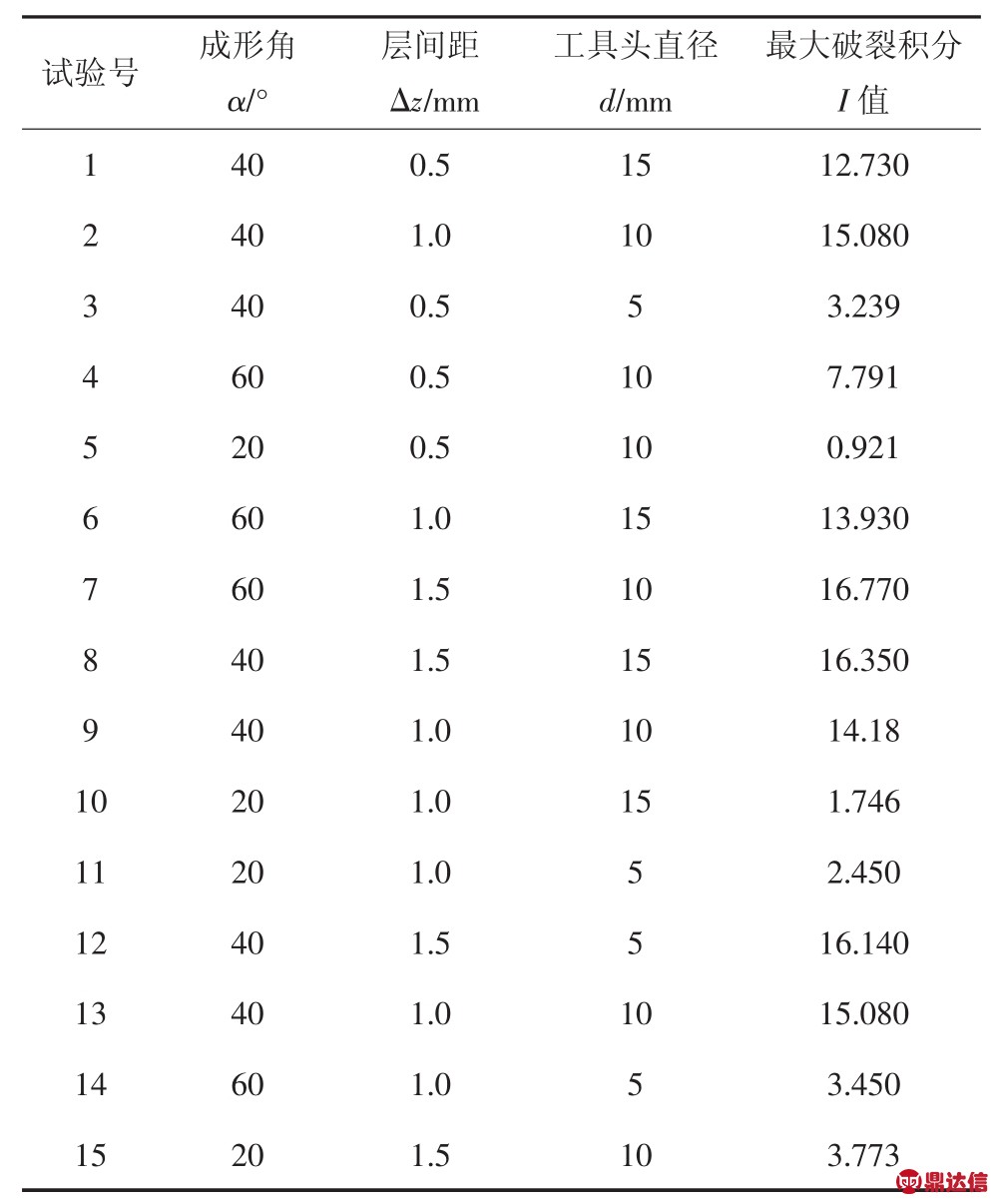
?
基于响应面法,得出最大破裂积分值I和设计的三种工艺参数的响应函数如下:
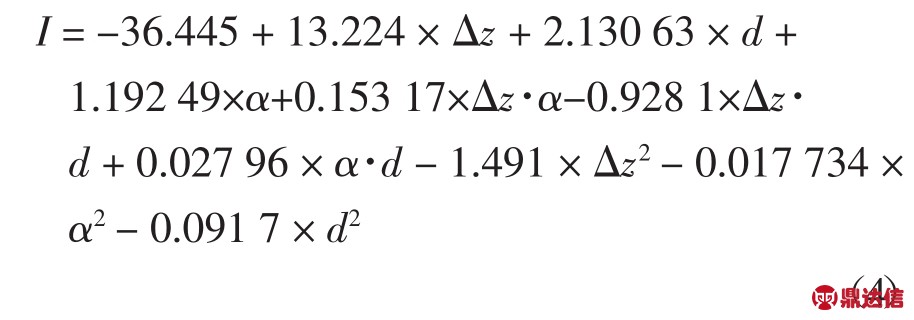
式中:Δz为层间距;α为成形角;d为工具头直径.
为了验证预测模型的有效性,进行方差分析.结果如表4所示:SS代表残差平方和;df为自由度;MS为均方差;F值代表了对应的可控因子对响应函数的影响的显著程度.p值=0.000 6<0.05,证明模型显著,且各参数对I值的影响的显著情况为:成形角>层间距>工具头直径.
表4 方差分析结果
Tab.4 Results of variance analysis
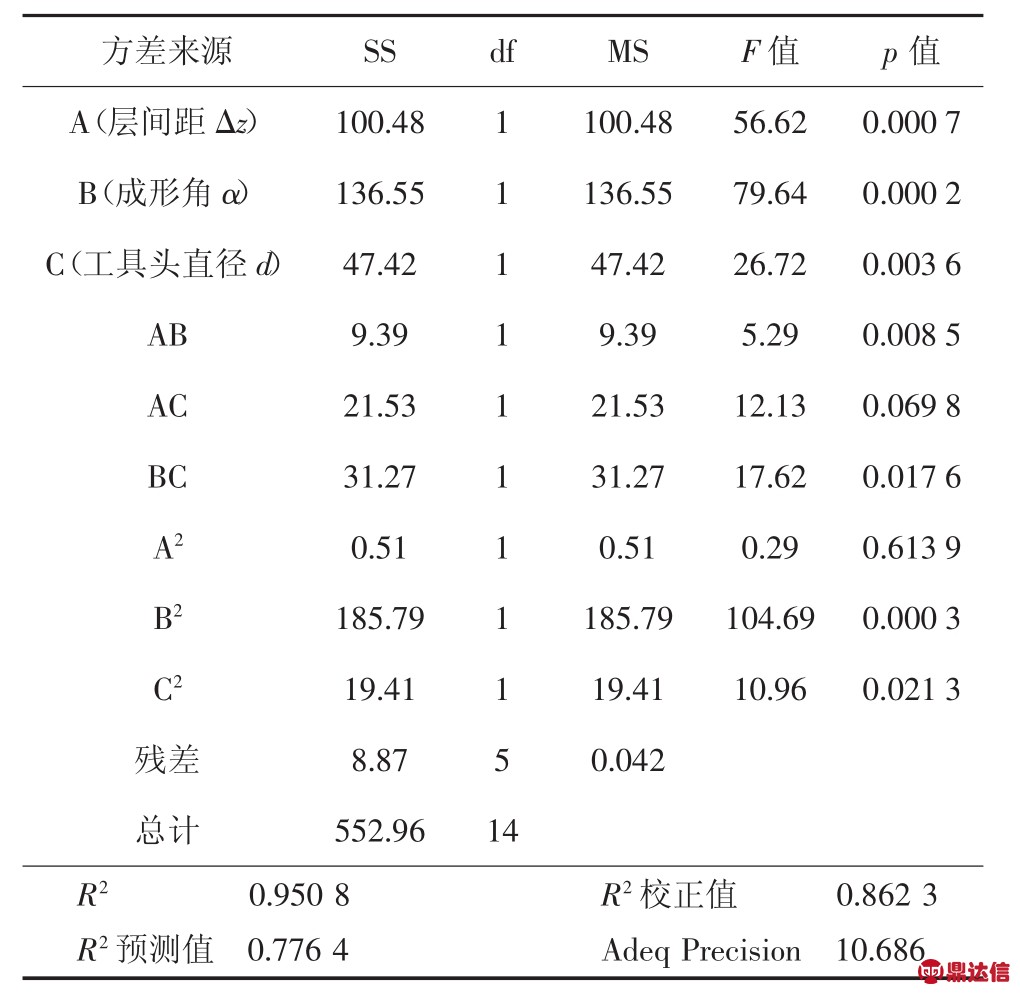
?
3.2 工艺参数的独立影响
图5所示为各工艺参数对最大破裂积分I值的影响情况.如图5(a)所示,随着工具头直径的增大,最大破裂积分I值增大.这种增大现象主要有两个原因:1)板料接触面积随工具头的增大而增大,进而使参与塑性变形的板料面积增大;2)最大破裂积分I值的增大与工具头加工过程中与板料摩擦产热有关.但整体的增大趋势较缓,表明工具头直径对最大破裂积分I值影响较小.如图5(b)所示,当成形角增大时,最大破裂积分值I显著增大,但增长趋势不呈线性,在成形角为40°~60°区间内增加趋势放缓.这与渐进成形过程遵循正弦定理一致,当成形角增大时,板料变形程度增加,最大破裂积分I值增大,当增加到某一临界值时,板料厚度急剧减薄直至出现破裂现象.如图5(c)所示,随着层间距的增加,最大破裂积分I值显著增大.引起这种变化的主要原因如下:随着层间距的增加,相同情况下板料成形所需的成形力更大,且两相邻加工层间重叠区域面积减小,板料流动能力减弱.成形角对最大破裂积分I值的影响最大,层间距次之,工具头直径最小.

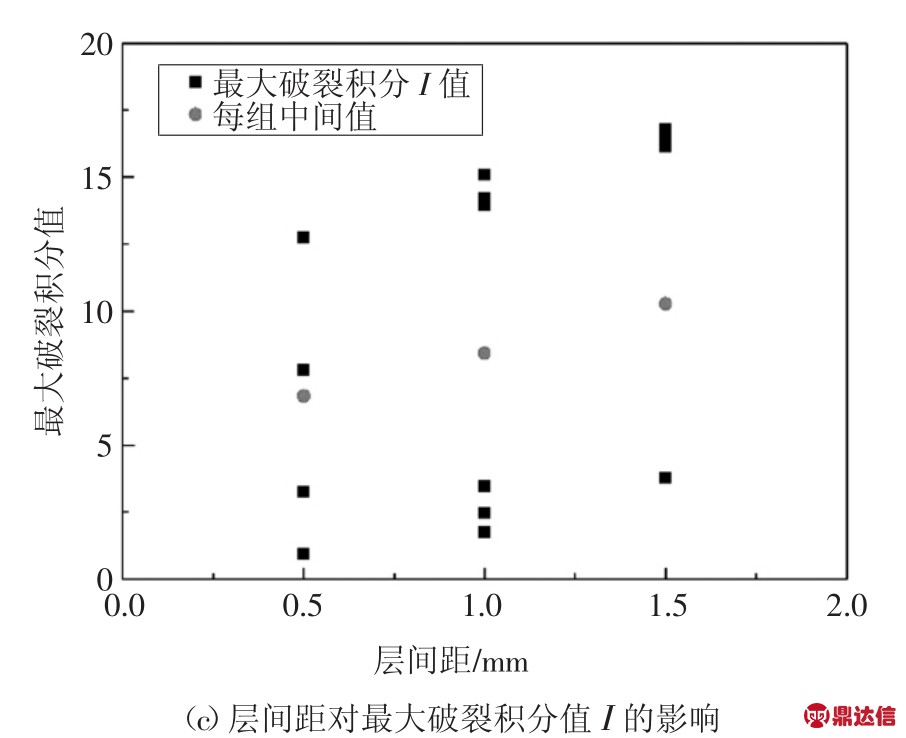
图5 工艺参数对破裂积分值I的独立影响
Fig.5 Effect of process parameters on the maximum value of I
3.3 工艺参数交互作用的影响
除了工艺参数对韧性破裂的独立影响,在实际加工过程中多种工艺参数的交互作用也起到一定影响,其对最大破裂积分I值的影响如图6所示.如图6(a)所示,当d=10 mm时,曲面图变化的坡度较大,则成形角对最大破裂积分I值影响较大,随着成形角的增大,最大破裂积分I值先增大后减小,在80°左右开始呈减小趋势.但实际加工成形中,成形角超过80°便难以单道次加工出制件.考虑实际情况后,最大破裂积分I值随成形角的增大而显著增大.等值线呈椭圆形,则层间距和成形角间的交互作用明显.
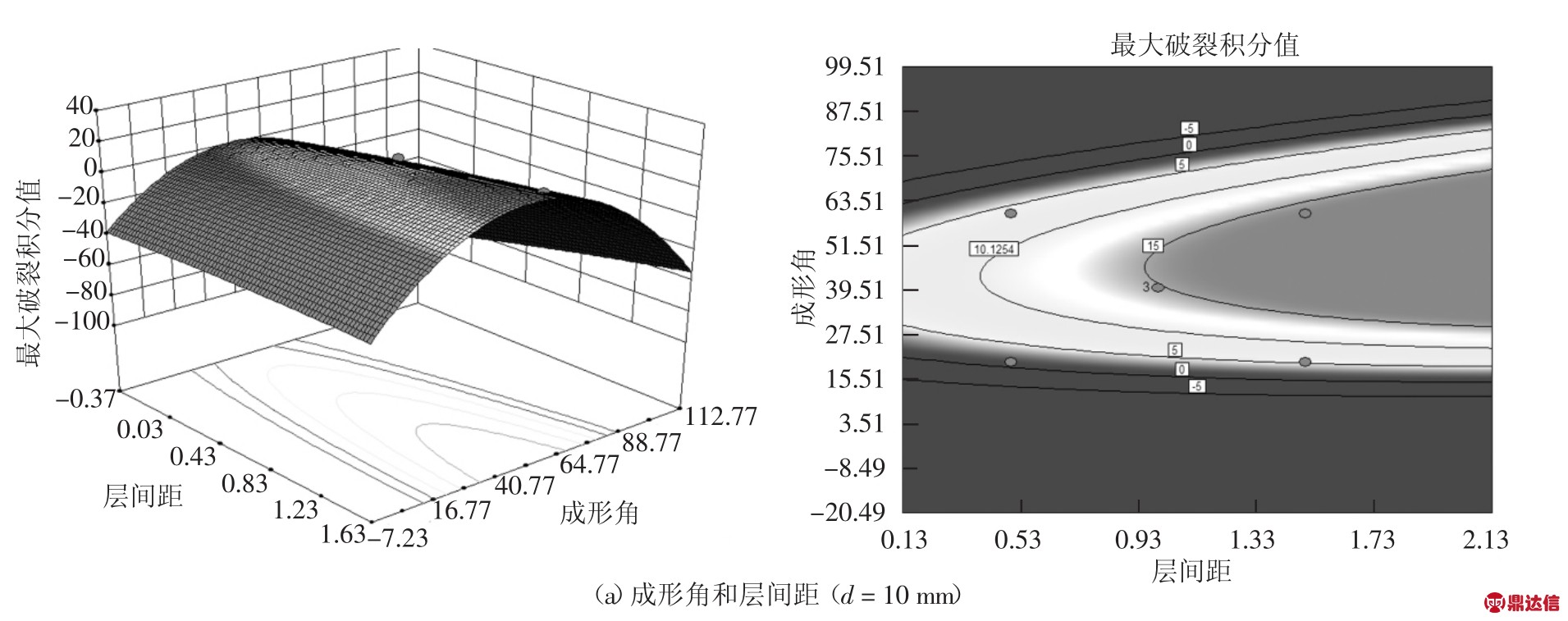
如图 6(b)所示,当 α=40°时,随着层间距的减小,最大破裂积分I值减小,且坡度较大,说明层间距对最大破裂积分I值的影响较大.随着工具头直径的增大,最大破裂积分I值增大,但相比层间距的变化坡度,曲面上升坡度较小,因此层间距对最大破裂积分I值的影响比工具头直径更小.等值线与椭圆形状相差较大,因此层间距和工具头直径间交互作用对最大破裂积分I值的影响较小.
如图6(c)所示,当d=1 mm时,随着成形角的增大,最大破裂积分I值增大,且曲面上升趋势明显,再次表明成形角变化对最大破裂积分I值影响波动较大.同理分析,工具头直径对最大破裂积分I值的影响小于成形角.等值线为椭圆且等值线间间隔很小,因此,成形角与工具头直径的交互作用对最大破裂积分I值的影响较大.
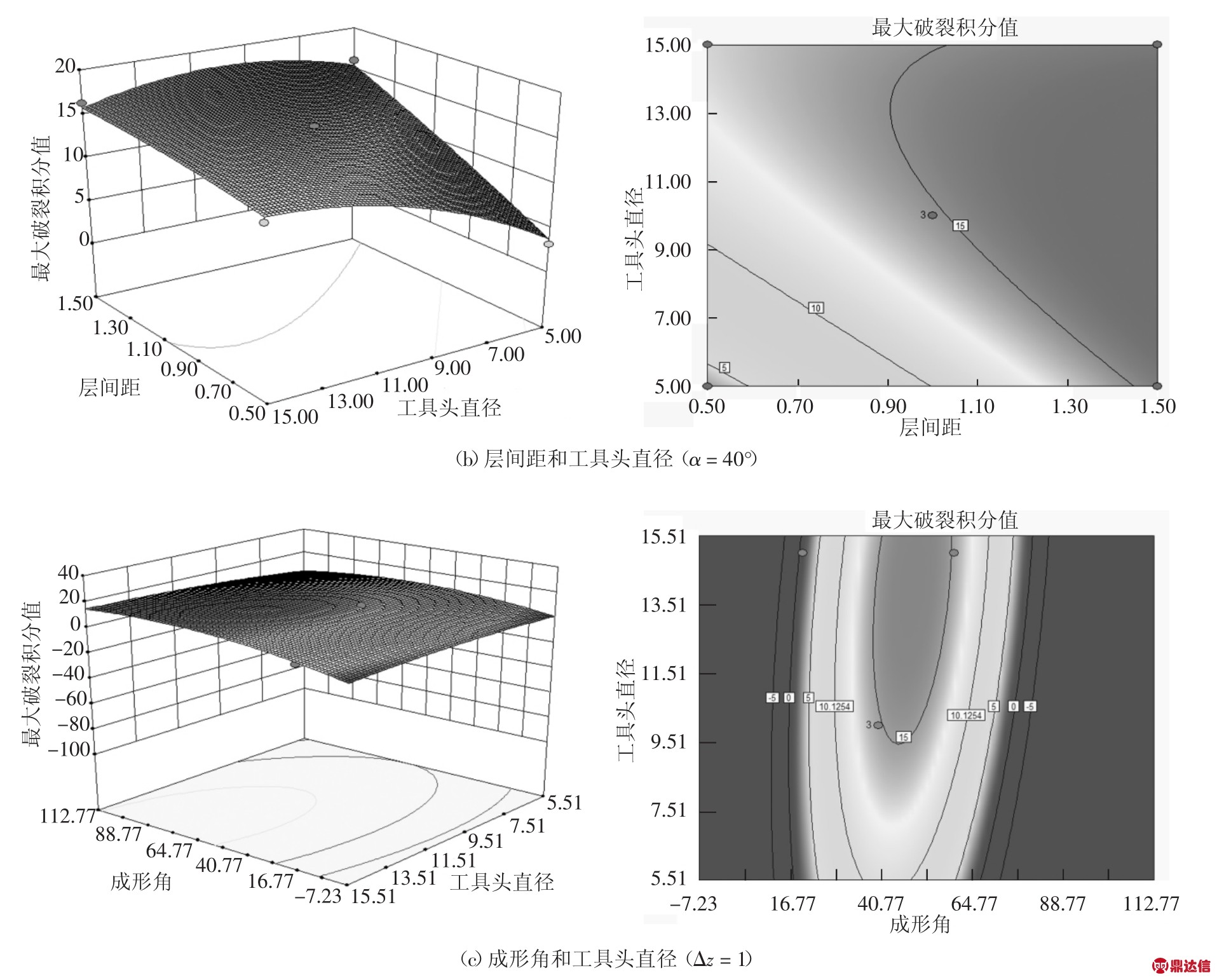
图6 各参数组合的交互作用对破裂积分值的影响
Fig.6 The interaction of parameter combinations on fracture integral value
4 结论
1)应用Oyane准则预测DC56D+Z钢板在渐进成形过程中的破裂情况,结合试验与有限元分析得出:破裂积分值I=4可作为渐进成形韧性破裂的临界值.
2)确定了预测最大破裂积分I值的数值模型,并结合方差分析验证了该模型预测的有效性.
长时间TH过量,就会损伤胰岛素功能,如果胰岛素分泌降解加快且分泌量减少后,孕妇的糖尿病以及相关并发症就会加重,同样,糖尿病也会导致孕妇出现甲状腺等疾病。相关学者研究指出,对糖尿病患者做好饮食控制,在血糖稳定后,患者甲亢危象以及并发症就会消除[7]。当孕妇甲状腺功能出现异常时,会导致其血脂指标紊乱,低密度脂蛋白胆固醇以及载脂蛋白、甘油三酯水平上升。
3)最大破裂积分I值随着成形角α、层间距Δz和工具头直径d的增大而增大,三个工艺参数的影响作用逐渐减弱,且α&Δz、α&d两种组合的交互作用影响较大.