摘要:安全阀作为承压系统主要的安全附件对保证化学与能源工业装置的安全运行起着举足轻重的作用。近年来,随着承压系统工作压力与温度环境等日益严苛,对安全阀性能也提出了更加精准与严苛的要求。为了探索先进安全阀的设计、制造与运维技术,本文概述了安全阀的研究现状和取得的重要技术进展,包括安全阀动作和排量性能的精准设计、安全阀密封设计、安全阀抗震设计、安全阀可靠性的精准设计、热态试验验证及安全阀本身的结构完整性保障和健康监测等,在此基础上,指出了今后亟待解决的若干科学技术问题,包括极端工况(高温、高压、地震、火灾等)流体流场下安全阀瞬态响应的计算模拟技术、极端工况下安全阀全性能试验装置和试验方法、精确测量安全阀流量系数的多尺度方法、智能安全阀技术、极端工况安全阀结构完整性评价技术。
关键词:安全阀;设计;试验;抗震;可靠性;结构完整性
安全阀是承压设备和管路上作为超压保护的安全附件,是承压系统中最后也是最关键的一道被动的安全措施。安全阀不需要借助外力,只需要在介质作用下就能够实现开启,不受其他外部动力、信号影响。当介质压力超过规定设置后,安全阀会自动开启,通过排放系统介质保证系统压力不超过设定数值。当系统压力降低至一定范围后安全阀重新闭合,减小介质进一步排放造成的损失。在历史上,人类开始通过加热产生蒸汽,便有了安全利用蒸汽的问题。二千多年前中国人使用带铰链外盖的大锅,可以较安全地产生蒸汽,据考证,这是最早的安全阀雏形。真正有工业意义的第一个安全阀或应归功于法国人Denis Papin在1681年发明的蒸汽压安全泄放装置,它保证了蒸汽压蒸煮器的安全使用[1]。一百年后安全泄放装置被瓦特等应用于蒸汽机的安全保障,大大推动了工业革命的进程。随着工业化规模的不断扩大,安全阀已广泛应用于国民经济各个领域中,能够防止锅炉、压力容器或压力管道等承压装置和设备因超压发生破坏,保障了设备的正常运行和人员安全,同时也保障了工业文明的实现[2-3]。
大量事故经验表明,安全阀本身的失效也会造成灾难性的后果。很多安全阀除具有安全阀防护功能外,其本身的可靠性在系统中具有至关重要的作用。如1988年7月的帕尔珀·阿尔法石油钻塔事故中因为一个失效的安全阀,导致液态天然气泄漏,泄漏导致的大火将300个工作平台烧毁,167人遇难。又如,压水堆核电系统中普遍使用的稳压器安全阀是核电站一回路中最重要的阀门,是保证反应堆冷却剂系统及其相连管道和设备安全的关键设备。如果稳压器安全阀无法正常开启将可能导致一回路压力边界破损,而其动作后无法回座更可能造成熔堆事故。
人类进入21世纪以后,能源短缺、环境恶化问题日益严峻。为了提高化工与能源过程的效率,装置的工作条件与规模均向更加极端化的方向发展,生产过程大型化、服役环境严苛化以及高参数运行、高能量储备的趋势使得事故更具有灾难性、中断性以及社会性[4]。这对安全阀的大型化、泄放能力、长期可靠性也提出了更加严苛的要求,同时,在计算科学、信息科学、材料科学、制造科学、测量科学等学科快速进步的今天,也为构建更加精准的安全阀技术体系提供了可能。当前,严苛条件下承压系统安全阀技术面临的主要挑战涉及安全阀动作和排量性能的精准设计和热态试验验证、安全阀密封设计及加工、安全阀抗震设计和试验验证、安全阀可靠性的精准设计、安全阀失效分析和健康监测等方面。本文在综述世界范围内安全阀技术研究现状的基础上,重点总结了高端安全阀精准设计、制造与运行维护亟待解决的若干科学技术问题。
1 安全阀的精准设计技术
1.1 安全阀动作和排量性能设计
20世纪中叶,苏联学者康德拉契娃对安全阀的设计、试验进行了系统研究,认为安全阀的开启动力学方程可表达为二阶线性微分方程(不可压缩流体)和三阶微分方程(可压缩流体)[5]。后Singh[6]采用二阶微分方程和可压缩流体一阶微分方程对弹簧式安全阀进行了研究。随着计算机技术的飞速发展,计算流体力学(CFD)被广泛应用于安全阀设计计算领域,该方法将安全阀内部流场和动作特性的研究引向深入。初期的研究主要采用流场稳态模拟方法,主要包括背压对流动特性之间的影响[7]、压力波导致的安全阀颤振[8]、可压缩与不可压缩流体模型对模拟结果的影响[9]等。研究的重点在于安全阀两相流泄放过程的模拟和计算。Darby[10]提出了一种适用于安全阀的简单有效的两相泄放系数。Leung[11]把两相可压缩流动的排量系数进一步关联为不可压缩流动的液体排量系数。Boccardi等[12]将安全阀的两相流难点归纳为:热力学不平衡造成压降与相变之间的关系难以确定,由此导致的延迟蒸发未在两相流研究中予以考虑。
流场的稳态模拟方法虽然简单,但无法描述安全阀从开启到回座的动作特性。瞬态模拟方法虽然复杂、计算量大,但可以准确捕捉安全阀的动作特性和内部流场的特征变化,瞬态模拟目前成为安全阀CFD研究的焦点。Ortega等[13]使用二维动态模型,对安全阀排放过程进行了瞬态模拟,通过计算获得了开启高度与排量随时间变化的动态曲线。但是模型过于简单,且未进行试验验证。Song等[14-17]运用动网格技术对安全阀从开启到回座的整个过程进行数值求解计算,研究了压力、马赫数随时间变化的分布趋势,并着重对开启和回座位移、速度、加速惯性力变化进行了分析,但其模拟结果缺乏实验验证。华东理工大学研究团队采用了网格预变形、动网格、流域分块、外接虚拟大容器等模拟技术,并利用二阶微分方程对阀瓣的动态特性进行了编译,精确地计算了阀瓣的运动状态,如图1所示。同时,该团队采用响应面法对上调节圈、下调节圈、调节套和调节螺钉等4个调节机构对主蒸汽安全阀启闭压差的调节规律进行了研究,模拟结果得到相关试验验证[18-19]。技术进步推动了高端安全阀技术的产业化实现,研制并成功供应巴基斯坦C3/C4项目的主蒸汽安全阀和辅助系统安全阀,巴基斯坦K2/K3项目的主蒸汽安全阀、NSSS和BN1等辅助安全阀。
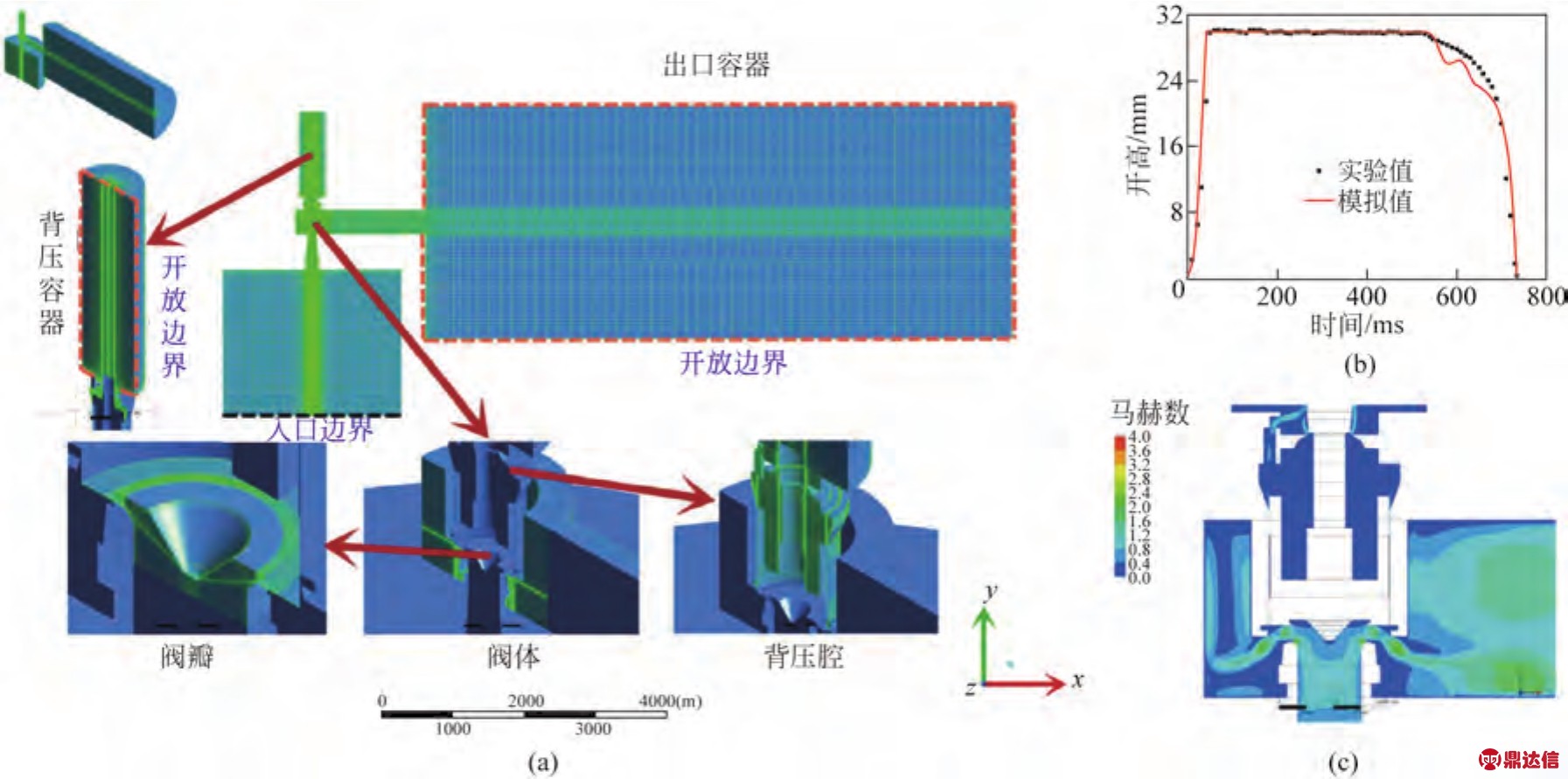
图1 基于动网格技术安全阀动态模拟[18]
虽然安全阀动作和排量模拟技术以及在得到了巨大的发展,相关方法的实用性也得到了广大使用单位的认可。但仍存在如下的一些问题:整定压力无法准确模拟,即应用动网格技术安全阀整定压力仍需人为设定;现有计算技术只能够模拟阀瓣沿垂直方向的运动,排放过程中阀瓣及阀瓣座的晃动问题无法通过计算直接获取;无法准确模拟阀瓣导向结构之间的摩擦作用;缺少对先导式安全阀动作行为的研究;临界和超临界蒸汽安全阀内部流场和安全阀的动作、排量特性研究仍处于空白。
1.2 安全阀密封性能设计
为保证高温高压安全阀的密封性能,此类安全阀主要采用金属密封结构。目前金属密封设计主要通过查阅相关手册[20]确定密封结构参数,但手册数据多来自经验,并不适合高温高压极端工况下金属结构密封的精确设计。金属密封的研究主要包括微尺度接触以及微通道中的泄漏。针对微尺度接触,通过模型计算法[21-24]以及有限元计算方法[25-28],已经能够获得不同接触应力情况下所对应的接触面积以及接触面积中平均高度等参数。基于接触过程中获得的密封面平均间隙,结合狭缝泄漏立方定律就能够对密封面中的泄漏进行估算[29-31]。Liao等[32-33]将接触面简化为螺旋形通道与径向通道的组合,使用立方定律对密封面中的泄漏进行了估算。Anwar等[34]使用有限元方法研究安全阀在接触过程中宏观变形对密封的影响,但对接触过程中的粗糙度均进行了较大程度的简化,与实际金属面存在一定的偏差,同时未对微尺度流通通道中可能出现的介质壁面滑移现象进行考虑。
为了讨论介质在密封界面微通道中的流动情况,特别是具有粗糙壁面的微通道中介质的流动,借助介观模拟方法Lattice Boltzmann Method(LBM),Cao等[35-37]采用规则结构代替粗糙面,对突起结构对流场特别是壁面速度的影响进行了研究 。 Kleinstreuer[38]、 Bahrami[39]、 Xiong[40]、 Cao[41]等采用分子动力学方法研究了随机生成的无规则粗糙面对微通道中介质流动的影响。研究中考虑了微流道中粗糙面以及流体壁面滑移的影响,但受限于计算数量,分子动力学方法只能够对有限长度通道中的介质流动进行模拟,无法模拟计算宏观长度微流道中的泄漏量。
此外,安全阀因为其特殊结构,密封比压的确定与密封中径的选取直接相关。通常情况下认为密封中径为密封面内径与外径的平均,但实际情况可能与此存在较大的误差。Gorash等[42]通过有限元模拟讨论了安全阀多次动作后密封面中径的变化以及该变化对整定的影响。
目前,对于安全阀密封的精确计算和设计仍然主要依靠经验,许多问题亟待解决,如:金属密封面微尺度变形中,密封面凸起采用宏观力学本构产生的误差;宏观长度下考虑实际粗糙面结构的微通道泄漏量的计算;不同密封宽度、密封比压下接触面变形及泄漏的定量计算等。
关于安全阀密封面的加工,Ai等[43]采用有限元模拟和中子衍射残余应力测量相结合的方法,研究了安全阀阀座密封面在堆焊、热处理、车削以及阀瓣冲击下的残余应力的演化过程,如图2所示,提出采用多次冲击降低堆焊密封面残余应力的方法[44]。密封面的研磨对安全阀密封性能的保障至关重要。安全阀密封研磨手段主要包括手工研磨和机械研磨。其中,手工研磨精度高,但工作强度大、研磨效率较低。随着研磨装备的发展,安全阀密封结构的全自动机械研磨技术也得到了快速的发展。机械研磨装置具有较高的研磨及精度,相关产品在安全阀生产单位也得到广泛的应用。朱海清等[45-47]通过实验及理论研究,对机械研磨过程中研磨路径、研磨颗粒大小、研磨转速等具体研磨工艺进行了大量研究,也得出了许多有益的结论。但对于很多密封结构,因为受到结构的限制无法使用机械研磨,例如高长径比的小口径阀座,因重心太高研磨面受力不均匀、容易出现倾倒而无法使用机械研磨。同时,生产实际经验显示手工研磨的最终效果一般优于机械研磨。所以,通过对手工研磨工艺的剖解、分析,通过人工智能技术模拟人手动作以实现安全阀密封面高精度自动研磨是未来发展的方向。
1.3 安全阀抗震设计
对于应用于可能出现振动的系统中的安全阀,通常会对安全阀的抗震能力进行要求。对于安全阀的抗震分析方法主要包括静力法、反应谱法和动力分析法。静力法将振动载荷折算为固定载荷后对安全阀进行应力计算、校核。该方法应用的前提条件是结构的一阶固有频率比工况振动频率高很多,且工况振动不会造成结构大尺度变形。相对静力法,反应谱方法将结构在振动工况中的动力学特性与振动特性之间进行之间关联,能够更加准确地反映结构的自振周期、振型等特性。但在实际操作过程中通常将振动作用力进行静力化处理,属于准动力理论。动力分析法主要为时程分析,对振动、频谱和持时等参数进行数值化处理后,采用直接积分法计算得出结构在整个振动时域中的振动状态全过程。目前基于实际使用工况,安全阀的抗震分析主要是采用静力法。刘龙等[48]计算了核电弹簧式安全阀的固有频率并采用静力法对安全阀在地震载荷的结构完整性进行了评定。肖琼等[49]采用静力法对核电阀门进行了抗震进行分析并修改了阀门设计。
目前国内外对安全阀地震载荷下的抗震分析主要针对地震期间或者地震后下模态分析及结构优化,计算安全阀在各种复杂这下的应力和变形(包含地震载荷),缺乏地震载荷下安全阀动作性能的研究,而安全阀在地震工况下的动作性能对于确保核电站的抗震性能是至关重要的。针对此问题,Lv等[50]建立了安全阀双向流固耦合动态模拟方法,准确设置了流固耦合交界面和固体间交界面,同时对流体流场区域和固体结构区域进行计算。加入了横波和纵波作为地震载荷,初步探索了安全阀在地震波条件下的动作性能,如图3所示。同时搭建了地震载荷下安全阀动作性能的试验装置,试验和模拟相结合优化了安全阀的抗震性能。
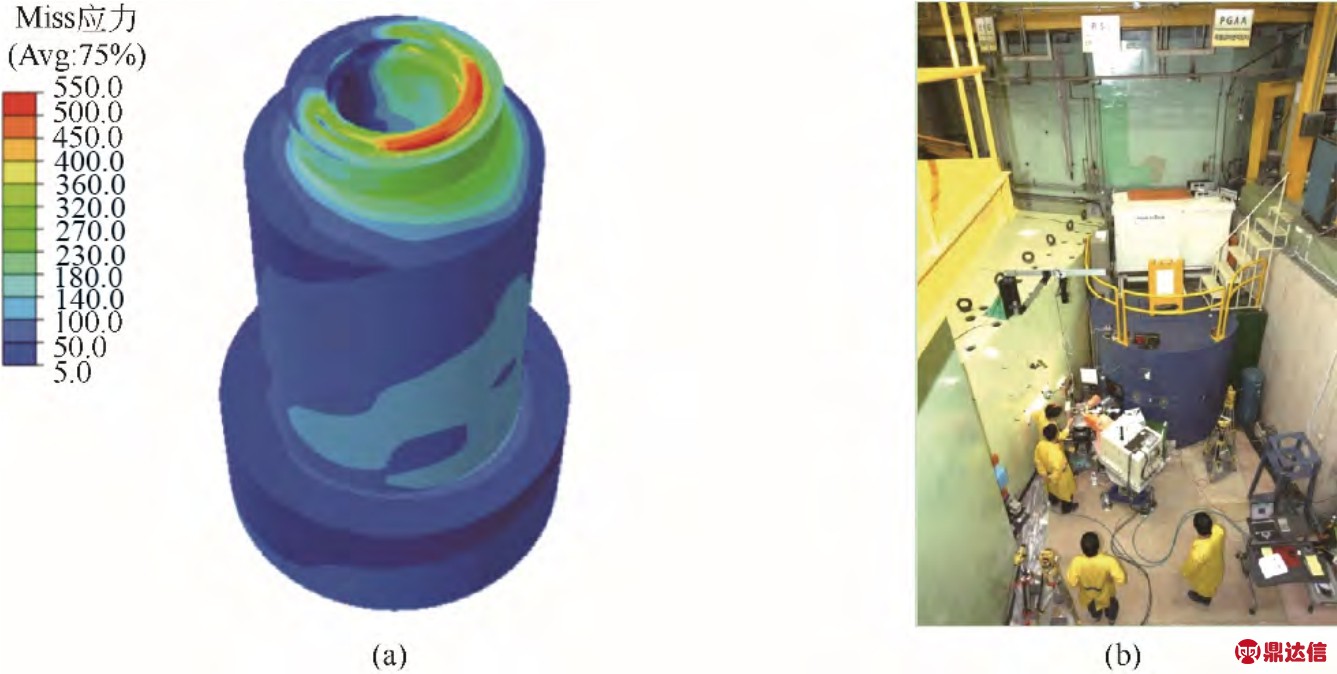
图2 50次阀瓣冲击后的安全阀阀座Mises残余应力场分布中子衍射残余应力测量装置[43]
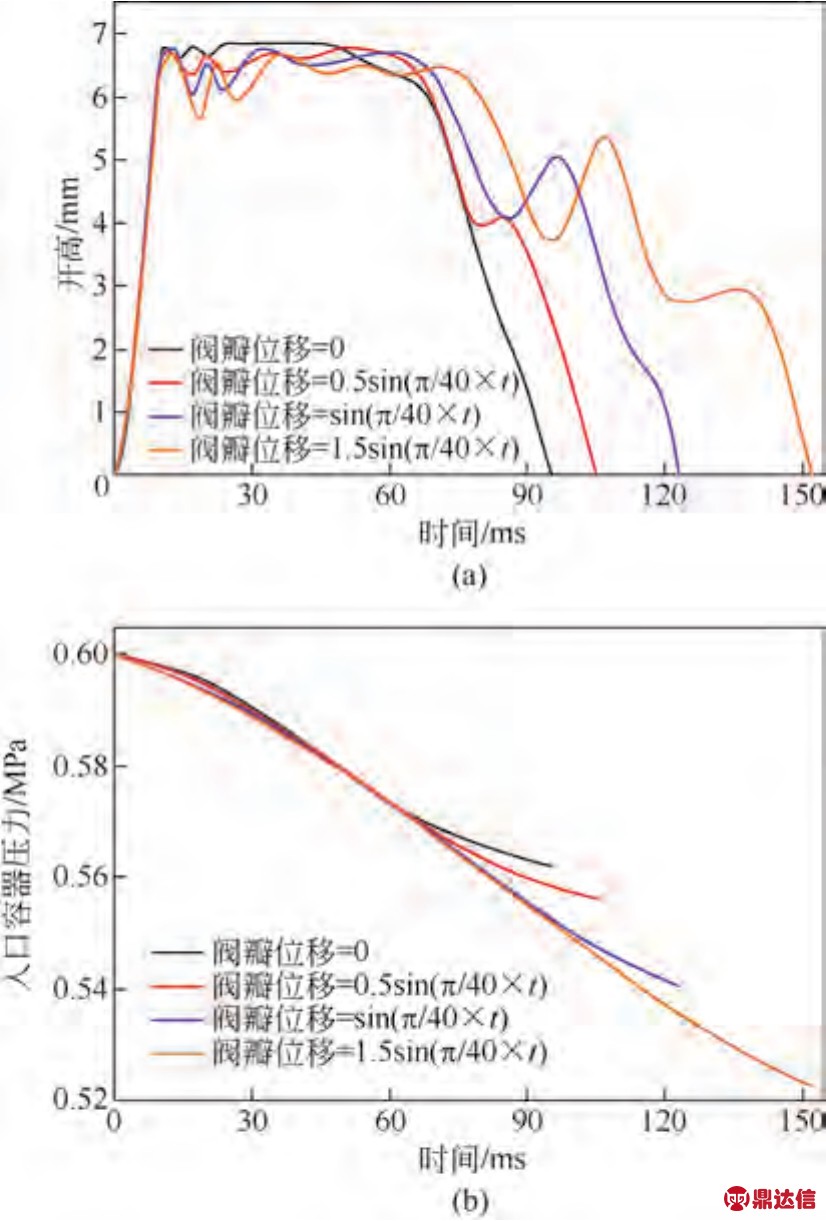
图3 不同振幅竖直正弦波地震载荷下开高及阀前压力容器内压力随时间的变化曲线[50]
目前,地震载荷下的安全阀动作性能的研究刚起步,尚有许多难题亟待解决:目前基于流固耦合的安全阀的动态特性模拟对结构进行了大量的简化,这些简化的合理性有待论证;安全阀地震载荷下的动作性能的试验装置是采用的压缩空气为介质,如何将压缩空气的结果推演至蒸汽介质阀门的性能需要研究。
1.4 安全阀可靠性设计
现今的抗疲劳设计方法主要包括名义应力法、局部应力应变法和损伤容限法,前两种方法已经在安全阀的设计中得到了应用,但将损伤容限方法应用于阀门结构完整性分析中的报道尚较少。除了将安全阀的疲劳寿命作为其结构完整性参数外,安全阀的开启和回座失效概率作为衡量安全阀可靠性的重要指标,其有效的计算方法一直是国内外学者的研究热点。Bukowski等[51-52]对世界知名安全阀制造商提供的安全阀使用数据进行分析,安全阀在五年之内超压不启跳的失效率处于10-8~10-7次/年之间。Sheesley等[53-54]将量子响应分析法(quantal response analysis,QRA)引入到安全阀失效概率中,并提出失效函数的两种确定方法。但量子计算法对数据的要求较高,拟合方程与数据区间之间必须满足一定的分布规律,否则无法获得有效的拟合函数。Goble等[55]使用统计特征分析法(statistical signature analysis,SSA),对安全阀失效概率进行了统计,但因为常规安全阀校验数据中只对安全阀校验时间和最终校验结果进行记录,所以使用该方法获得的失效概率无法与除使用年限外的其他参数进行。同时需要指出,现有的研究中缺乏对安全阀实际使用环境、介质工况、阀门类型等因素对安全阀可靠性影响的研究。近年来,为提高安全阀的可靠性,从源头上降低安全阀的失效率,虽然安全阀可靠性研究取得了一些成果,但仍存在如下的不足:安全阀开启和回座失效概率的研究尚缺乏,尤其缺乏弹簧刚度分布、导向套和阀瓣座的摩擦力分布等关键数据;缺少长时运行安全阀各个部件材料损伤数据。
2 安全阀热态性能试验技术
造成我国安全阀技术水平相对落后的关键问题之一是安全阀热态试验技术的落后。安全阀是“小阀门、大台架”。安全阀热态试验台架包含锅炉、容器、控制阀和控制系统,造价近亿元,试验技术远比安全阀本身复杂得多。目前,安全阀热态试验主要是依照美国标准ASME PTC 25,该标准规定了对试验过程和测试精度的要求,但如何实现试验过程则是一大挑战。安全阀热态试验装置最早出现在美国。目前美国Tyco公司分别在Stafford、Wrentham等地建有热态试验试验台架。建于Wrentham的试验台架始建于1949年,后来逐步完善,试验介质为饱和蒸汽,设计压力10.3MPa。建于Stafford的试验台架,试验介质为饱和蒸汽,最大试验压力10.2MPa。以上试验台架在进行大口径、大排量安全阀热态试验时存在安全阀频跳问题。即安全阀在一次测试过程中会出现多次的开启与回座,试验过程对安全阀的密封面将造成显著的损伤。另一方面,安全阀设计和制造工艺不合理也会造成安全阀的频跳。而由于试验装置和方法的缺陷所带来的安全阀测试中的频跳将会掩盖产品本身的问题,这将在安全阀的实际使用中埋下重大安全隐患。
目前国内已有若干具有安全阀型式试验资质和能力的机构,但均没有以蒸汽为介质的热态试验系统。国内共有4套热态安全阀试验台架建,都采用实验台架整体升压直至安全阀起跳,进而测量安全阀力学性能的方法,安全阀业内称之为“自由膨胀法”。“自由膨胀法”不符合ASME PTC 25标准的要求,存在如下的缺点:自由膨胀无法满足高参数、大排量安全阀试验过程中稳定排放的要求;采用自由膨胀法,造成整定压力和排放压力测量值相同,造成安全阀测量的额定开高偏低。针对这一问题,华东理工大学研究组建成国内外参数最高的安全阀高温高压热态试验装置[56-57],如图4所示,准确控制蒸汽流动和蒸汽品质,实现了阀门动作和排量性能的精准试验,通过变形监测保障了试验装置的安全[58],该安全阀热态试验装置为三门、海阳核电主蒸汽安全阀,CAP1400主蒸汽安全阀,巴基斯坦C3C4和K2K3主蒸汽安全阀、C3C4稳压器安全阀等众多核电高压蒸汽安全阀进行了试验测试。
此外,对于高温安全阀,特别是蒸汽安全阀在全阀等比例缩小进行排量系数的测量,但由于安全阀结构复杂,如何等比例缩小又不失去物理本质相似,没有确定的方法,根据九阀法测试出的排量系数的误差也无法确定。以上问题仍是目前高温高压安全阀行业的难题,影响了安全阀的性能和承压系统的安全。
3 在役安全阀结构完整性保障
对安全阀进行定期检测与安全评定是保障生产试验过程中如果使用常温空气进行整定试验,还需要使用相应的修正系数对整定压力进行修正。世界主要安全阀生产厂家均对本公司所生产的安全阀给出了具体的温度修正系数。虽然对此整定压力的偏差在行业内被广泛承认,但是对其原因却无解释,理论上的突破仍然十分必要。华东理工大学研究组[59]采用经典密度泛函理论模拟了安全阀密封面内的楔形狭缝内空气和蒸汽吸附作用力,发现正是由于在楔形狭缝中的空气和蒸汽吸附力差异造成了整定压力的偏差(图5)。
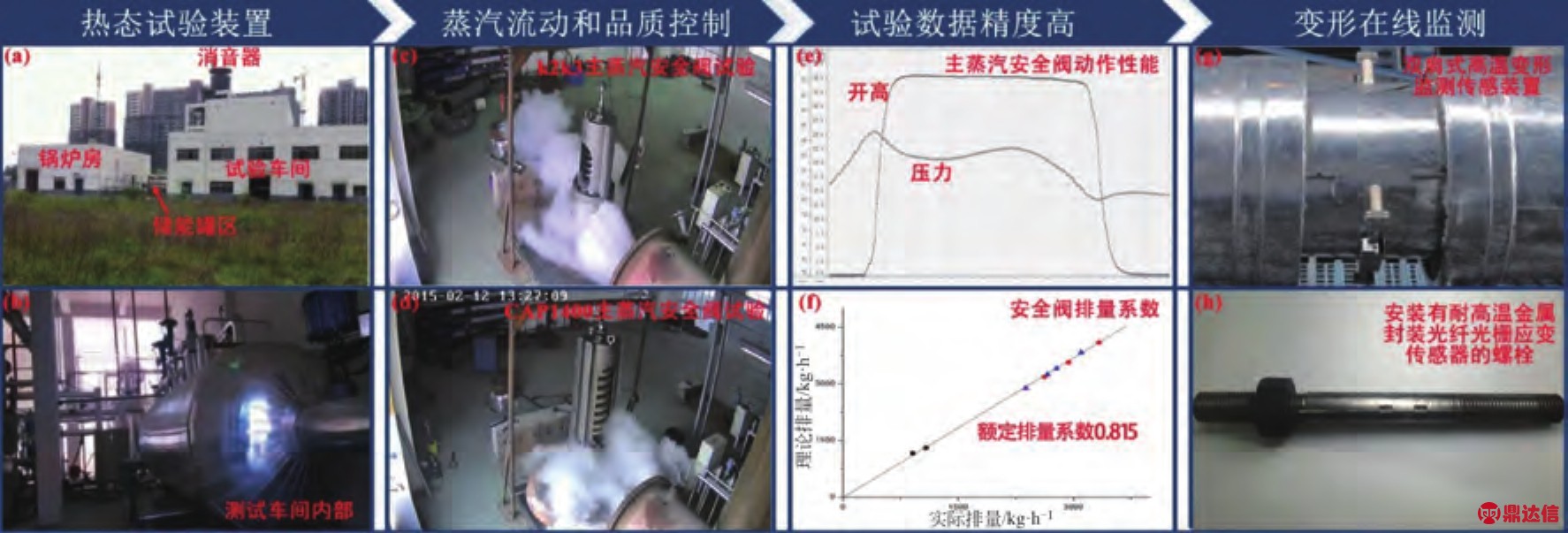
图4 安全阀高温高压热态试验技术
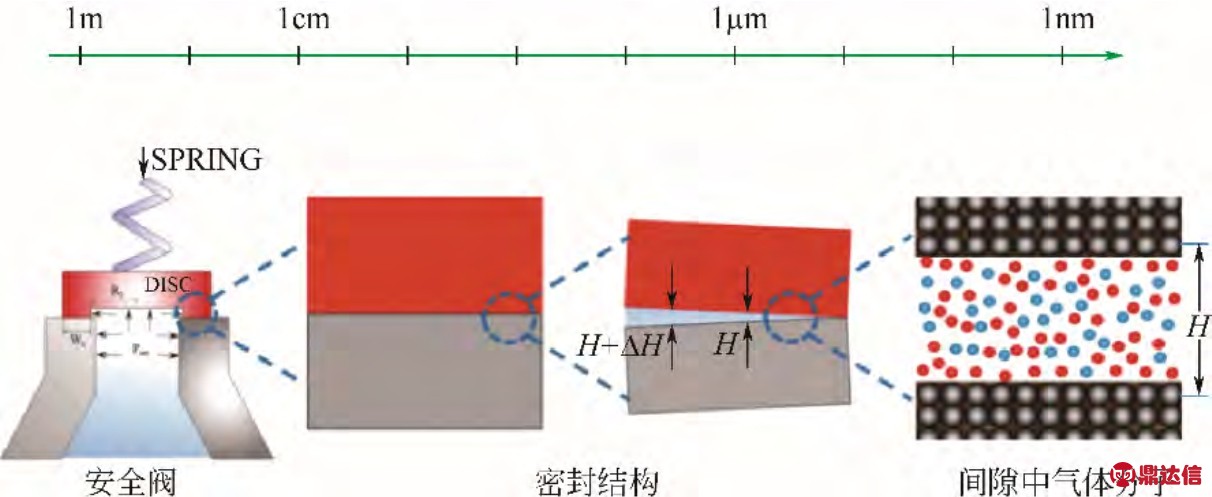
图5 基于经典密度泛函理论的安全阀密封面楔形狭缝吸附力模型[60]
但是,目前国内外的安全阀热态试验装置仍然无法满足超临界以及超超临界火电高温高压安全阀的试验参数。另外,对于大口径高温高压蒸汽安全阀的排量试验行业内多采用九阀法,即将大口径安安全的重要措施,但对于部分安全阀因工况特殊不具备定期校验的条件,采用何种方法完成对安全阀延期使用风险的评估,一直是国内安全阀校验研究的热点问题。针对高温阀门与管线的失效,在大量前期研究工作的基础上[60-61],我国已制订了行业标准《含缺陷高温压力管道和阀门安全评定方法》[62],该标准同样适用于高温高压安全阀承压边界的安全评定。近年来基于风险检验的方法也被引入到安全阀延期校验的研究中[64]。基于风险的检验是一种综合考虑安全阀失效概率与经济风险的评估方法。该方法在分析系统可能存在风险的基础上对事故所产生的后果进行综合评定,通过风险排序确定系统薄弱环节。同构分析最终达到确保系统本质安全和减少运行费用的目的,实现检修策略的优化管理。金承尧等[64]通过对弹簧的失效、安全阀的操作条件、履历和管理水平等4种可能导致安全阀失效因素的失效概率进行分析,结合安全阀失效后可能对人员、设备和环境等可能产生的危害进行综合模糊评价。通过失效概率与失效后果等级,对安全阀的风险等级进行表征并给出了安全阀的检维修策略。Chen等[65]对安全阀的主要特征参数进行误差分析后选出了主要失效因素,将安全阀本身的故障视为失效发生的条件性因素,结合失效危害等级最终确定安全阀的校验周期。金大仁等[66]通过失效模式、影响及危害性分析(failure modes effects and criticality analysis,FMECA)方法对安全阀进行分析,给出安全阀的多种失效模式与危害,并重点分析安全阀寿命与弹簧之间的关系。李智斌[67]使用模拟数学分析的方法对具有相同风险优先数的部件的重要度进行排序计算,引入专家打分机制并通过反模糊化的处理,对具有相同风险优先数的故障模式之间的相对危害度大小进行比较,从而确定其风险优先数等级。然而该部分工作并未进一步对安全阀进行失效模式、影响及诊断分析。
智能安全阀技术是今后的重要发展方向,特别是结构健康监测技术在不同领域的成功尝试值得借鉴。在设计制造阶段不能确保安全阀服役可靠性的情况下,如何采用在线健康监测技术对阀门的早期失效进行防控是一个非常值得关注的课题。于新海等[68]发明了一种蒸汽安全阀的在线泄漏检测装置,通过在安全阀密封面处安装发出固定超声频率特征的发声装置,可望实现安全阀介质泄漏的在线检测,避免了射流噪声和环境噪声对检测结果的扰动。
虽然已有学者用不同的风险评估方法对阀门进行失效评估,并由此给出了维修检测周期,但是仍然存在以下问题:虽然考虑到了安全阀的失效原因与部件之间的联系,但失效的物理机制与动力学规律、失效概率的精确分析、苛刻环境下适用的传感器以及如何对不同安全阀个体实现精准维修,仍是亟待解决的问题。
4 结语
近年来安全阀技术取得了显著的进步,集中体现在安全阀的精准设计(流场模拟、动态特性研究、金属密封面密封性能的计算、安全阀的抗震分析、安全阀可靠性设计)、高温高压热态试验以及结构完整性的保障等。但随着安全阀应用的工况越来越严苛,对安全阀的性能提出了新的和更高的要求。本文认为未来应重点在以下方面开展研究工作,以满足化工与能源工业承压系统长周期安全稳定运行的要求。
(1)精确描述安全阀从开启到回座全过程、阀瓣两自由度运动、适用于临界和超临界流体流场的瞬态模拟技术;
(2)超临界和超超临界蒸汽安全阀全性能试验的试验装置和试验方法;
(3)基于九阀法的精确测量安全阀流量系数的等比缩小方法及其误差计算方法;
(4)金属密封面泄漏量的精确计算方法;
(5)通过人工智能技术模拟人手动作以实现安全阀密封面高精度自动研磨;
(6)地震工况下安全阀的动作特性模拟和试验验证技术;
(7)基于大数据的安全阀开启和回座失效概率的计算技术;
(8)智能安全阀技术,包括极端环境传感器、在线健康监测及智能调控技术;
(9)极端工况(高温、高压、地震、火灾等)安全阀结构完整性评价技术。