摘 要:介绍了双作用式叶片泵的工作原理和总体结构,基于Unigraphics软件对这一叶片泵进行建模装配,进而对叶片泵定子进行加工编程。与此同时,基于ANSYS软件对叶片泵转轴进行静力学分析,得到转轴在特定工况条件下的位移云图与应力云图。
关键词:叶片泵 软件 分析
1 研究背景
叶片泵是在石油、轻工、船舶、航天等领域中广泛应用的旋转机械,是发动机润滑系统的重要部件。叶片泵从油底壳吸取液压油,向整台发动机各个摩擦部件持续提供压力润滑油。如果叶片泵的供油量不足,将会导致发动机缺乏足够的润滑压力,从而造成发动机严重磨损。
叶片泵在工作过程中,转轴起到至关重要的作用,转轴的结构强度直接影响叶片泵的工作性能。此外,叶片泵定子两端面和内型腔的粗糙度直接影响叶片泵的供油压力及工作环境的稳定性,定子的加工精度要求很高。笔者对叶片泵的转轴和定子进行分析研究。
2 叶片泵工作原理
双作用式叶片泵转子转一周,叶片在槽内往复运动两次,完成两次吸油和排油,其工作原理如图1所示。
双作用式叶片泵主剖视图如图2所示,由泵体、转子、叶片和配油盘等构成密闭空间。基于密闭空间大小的改变,转轴带动转子和叶片作逆时针旋转,同时叶片在槽内作往复运动。
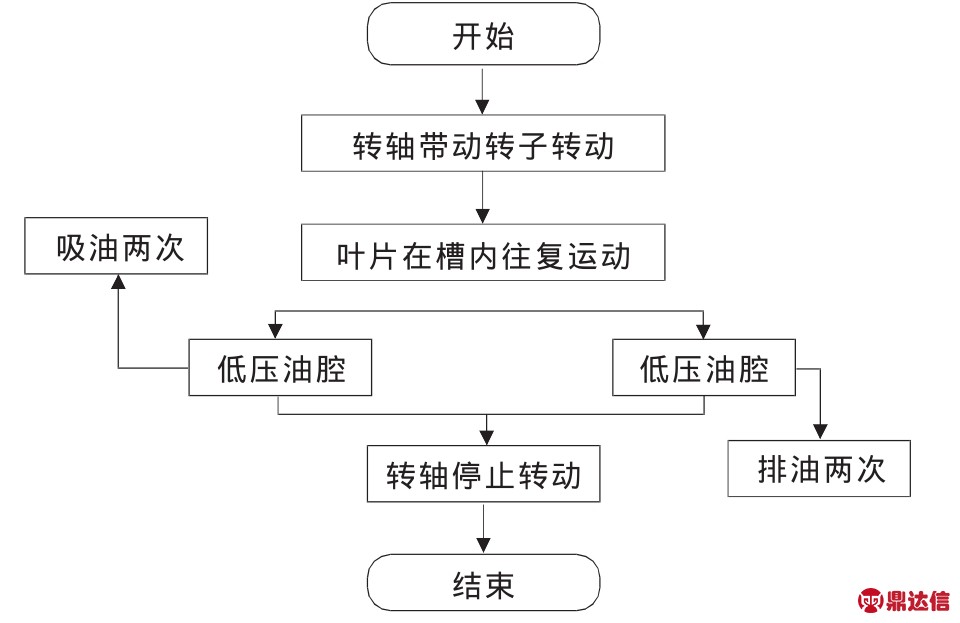
▲图1 双作用式叶片泵工作原理
当叶片由定子内表面小半径端移向大半径端时,叶片外移,密闭空间增大,形成局部真空,吸入油液。当叶片由定子内表面大半径端移向小半径端时,叶片被压入槽内,密闭空间减小,油液被压出。这样,转子转一周,叶片在槽内往复运动两次,完成两次吸油和排油,因此存在两个吸油区和两个排油区。
3 叶片泵总体结构
双作用式叶片泵共计21种零件,根据工作原理和各个零件之间的装配关系,绘制总体结构示意图,如图3所示。
4 建模装配
采用Unigraphics软件对双作用式叶片泵进行零件实体建模,并进行装配。
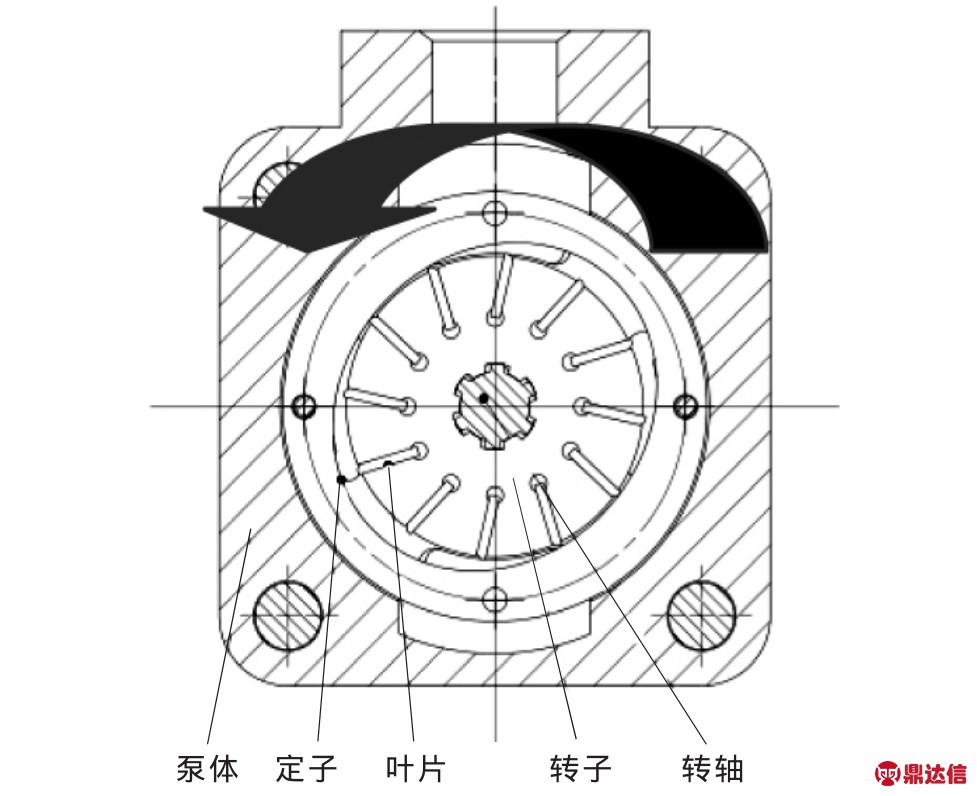
▲图2 双作用式叶片泵主剖视图
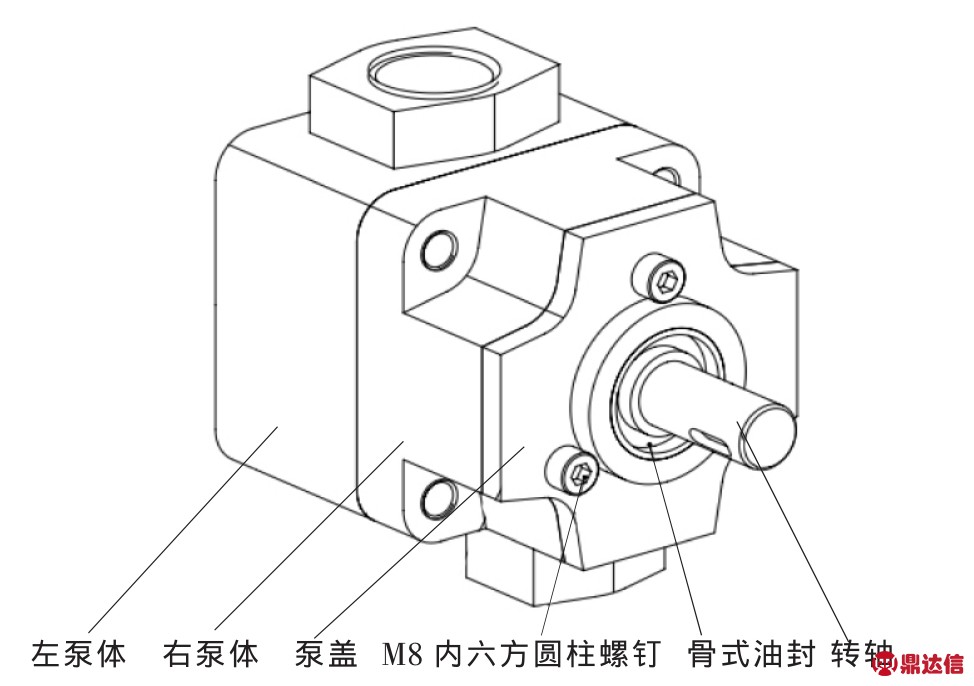
▲图3 双作用式叶片泵总体结构
为了得到叶片泵装配后在空间中的大体形貌,对其进行六视图投影,如图4所示。
在Unigraphics软件中将零件设置成不同颜色,以便于区分、识别和装配。
叶片泵爆炸图如图5所示,由图5可以清晰地看出叶片泵中21种零件及各种零件的数量,还可以看出叶片泵各个零件的大致安装顺序和安装位置。
5 定子加工编程
双作用式叶片泵的定子外立面为圆柱面,内表面为椭圆柱面,选用三坐标铣削加工方式进行加工。确定加工环境为mill_planar,设定安全抬刀距离为10 mm,如图6所示。
创建毛坯时,由于定子外立面为圆柱面,因此选用包容圆柱体得到最小毛坯形体,同时设置毛坯余量为2 mm,如图7所示。
加工定子时共设置四道工序,创建三把铣刀,直径分别为15 mm、10 mm、3 mm,如图8所示。
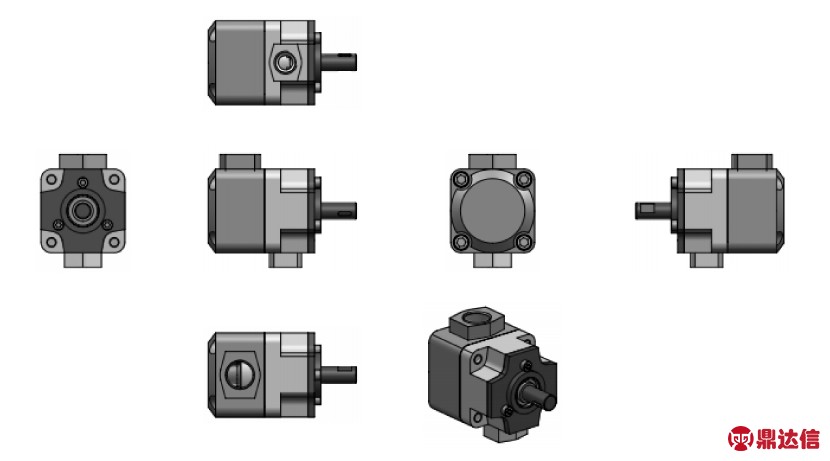
▲图4 双作用式叶片泵六视图投影
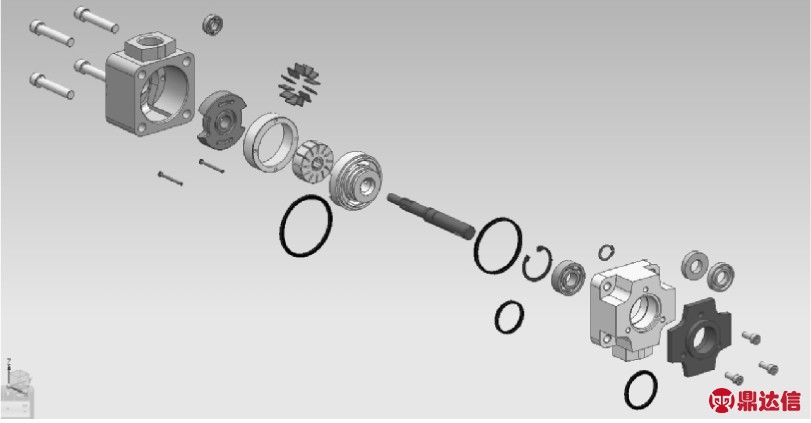
▲图5 双作用式叶片泵爆炸图
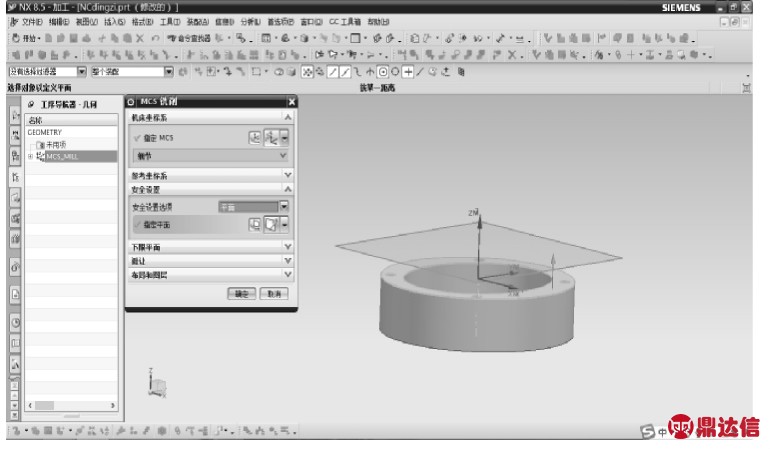
▲图6 设置加工环境与安全抬刀距离
φ15铣刀为粗铣刀具,刀具下圆角半径设置为2 mm,总长为75 mm,刀刃长度为50 mm。刀具夹持器在库中调取,选用06号。φ10铣刀为精铣刀具,刀具下圆角半径设置为0,总长为75 mm,刀刃长度为50 mm。刀具夹持器在库中调取,选用06号。φ3铣刀为铣削孔刀具,刀具下圆角半径设置为0,总长为75 mm,刀刃长度为50 mm。刀具夹持器在库中调取,选用06号。
创建四道工序,依次为粗铣定子轮廓、铣削孔、精铣平面、精铣侧壁。每道工序均设定部件边界、毛坯边界、检验边界,并指定底面、选择刀具,不同的工序设置有所不同。
粗铣的切削模式为跟随周边,每次切削深度最大为2 mm,最小为1 mm。精铣的切削模式为跟随轮廓,每次切削深度最大为1 mm,最小为0.5 mm。切削参数为层铣、深度优先和顺铣,其它参数基本为系统默认参数。
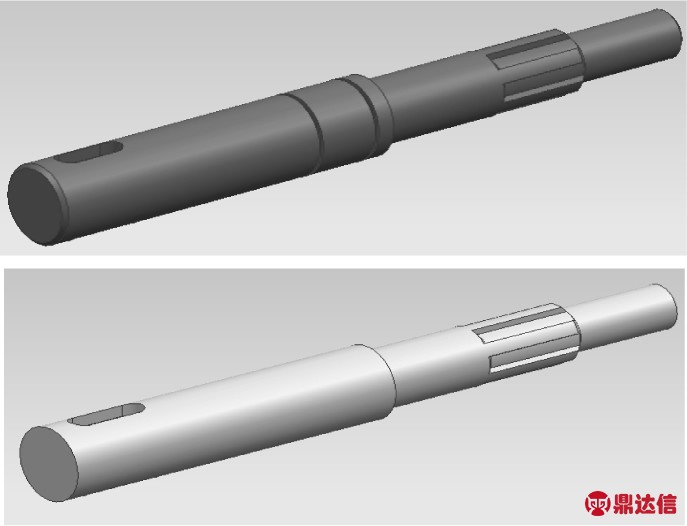
▲图7 创建毛坯
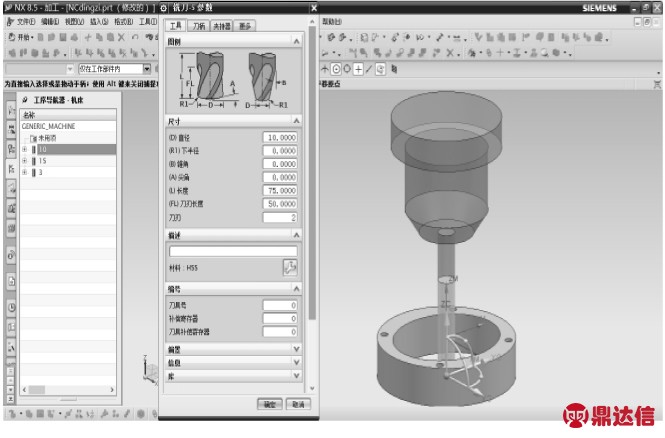
▲图8 创建刀具
通过设定每道工序,生成铣削加工时的刀具轨迹。由于每道工序设定的参数略有不同,因此刀具轨迹也不尽相同。四道工序的刀具轨迹如图9所示。
定子数控加工设定完成之后,通过后处理选定加工机床为三坐标数控铣床,设定文件名,然后可以导出数控加工代码文件。
以精铣平面为例,该道工序的数控加工代码如下:
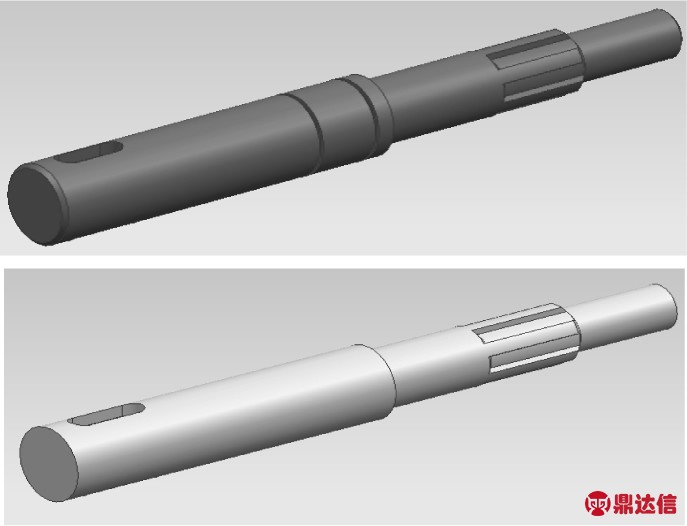
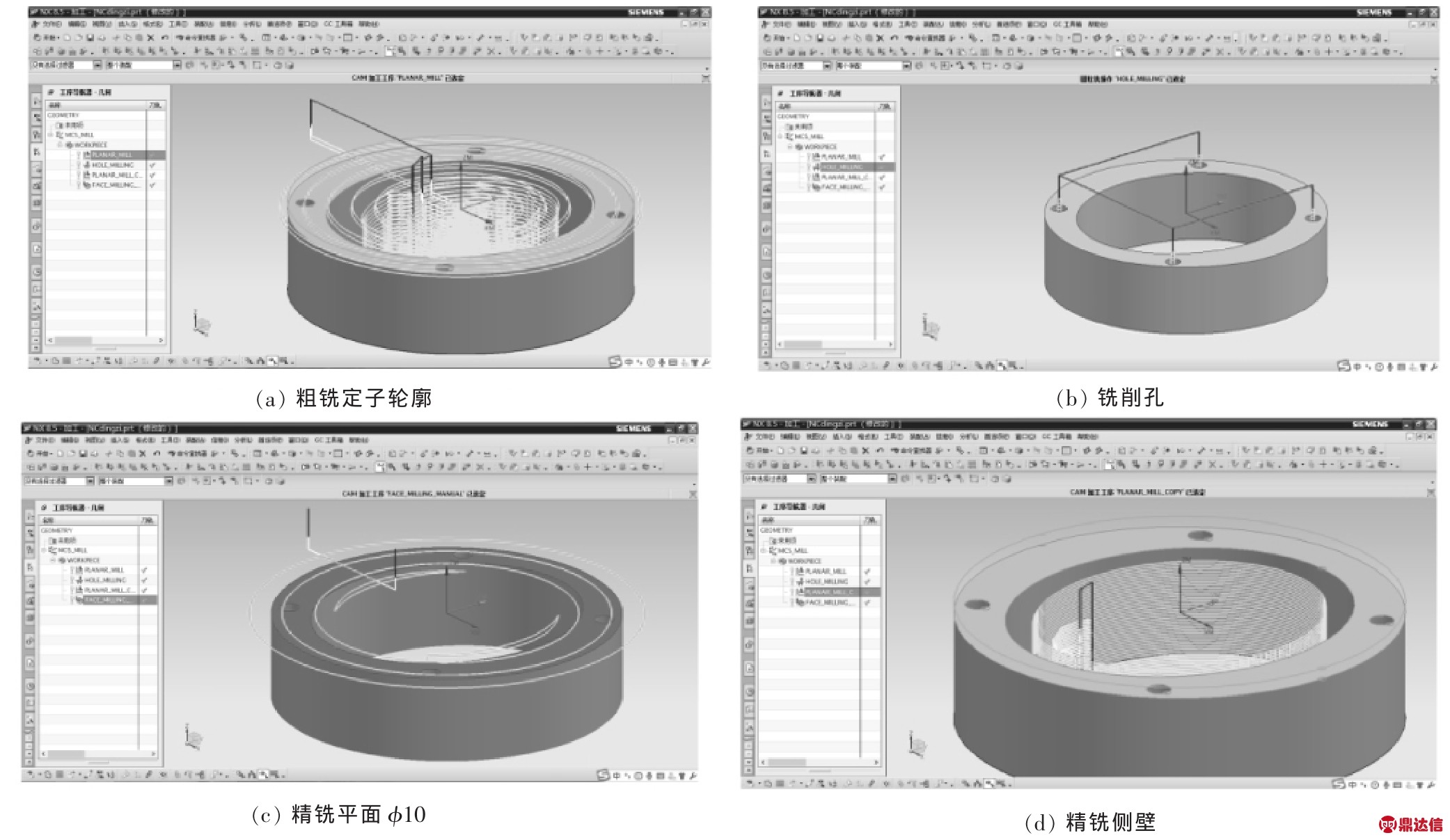
▲图9 各道工序刀具轨迹
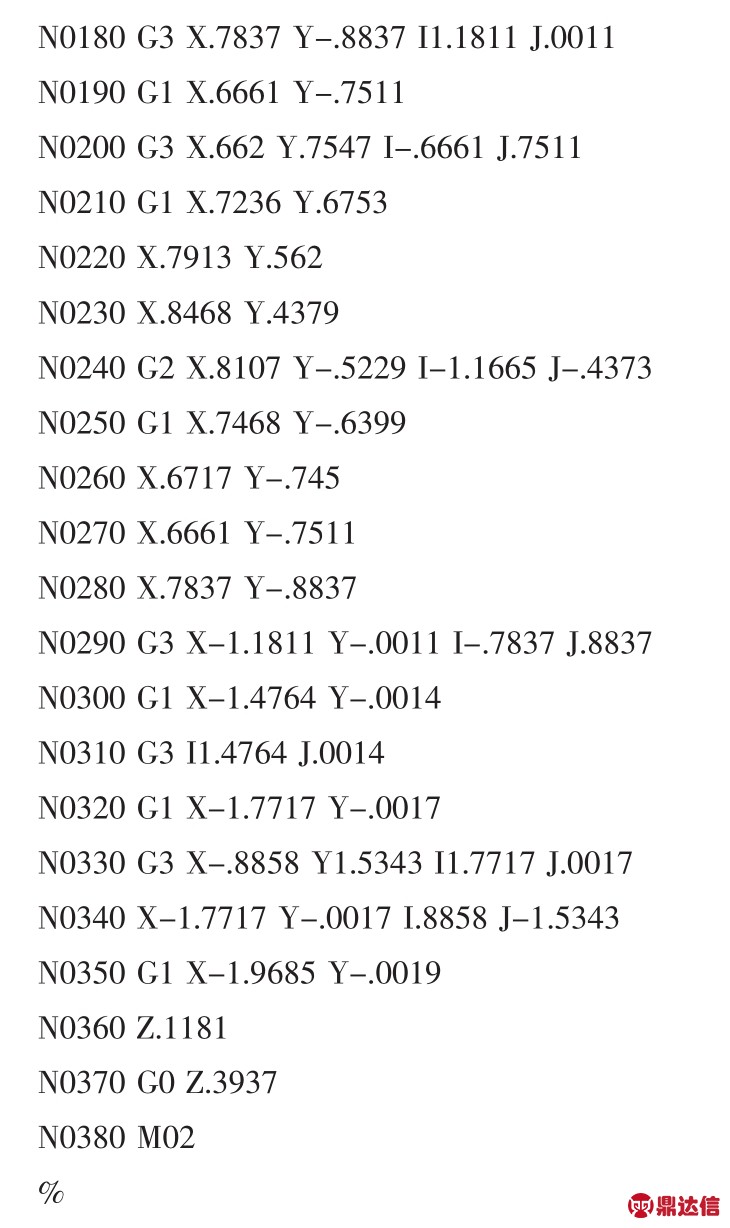
6 转轴静力学分析
由于转轴结构较为复杂,因此对其模型进行简化。将轴上两边倒角、两个轴用弹性挡圈的环形槽和小端加工时留下的顶针埋头孔全部去除,其简化模型如图10所示。
在Unigraphics软件中进行建模,导出时为.x_t格式文件,在ANSYS软件中可以直接打开。
在ANSYS软件中定义单元为Solid,类型选择Node187,节点为10。轴的材料为45号钢,弹性模量为200 GPa,泊松比为0.3。定义转轴材料属性如图11所示。
采用四面体自由计算对模型进行网格划分,网格疏密等级设置为3,选择全部,如图12所示。
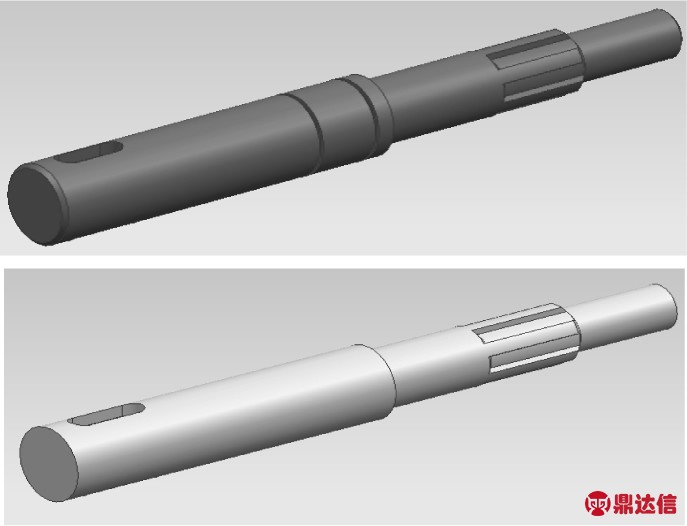
▲图10 转轴简化模型
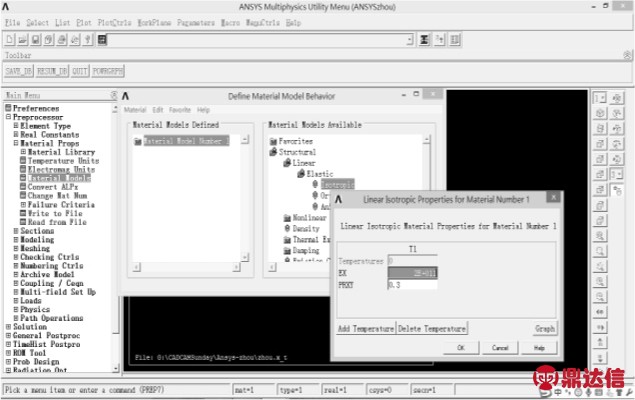
▲图11 定义转轴材料属性
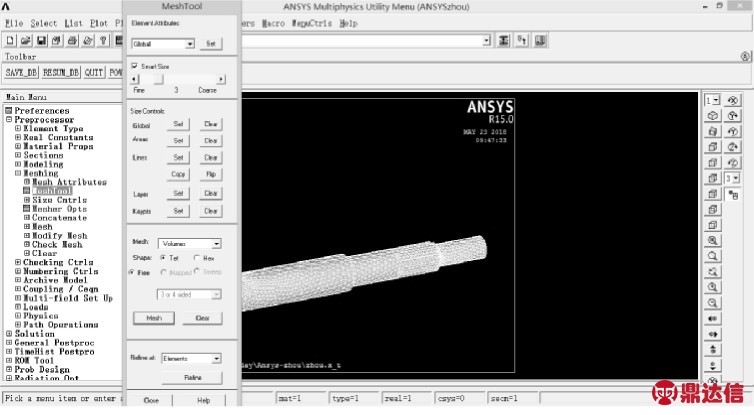
▲图12 转轴模型网格划分
根据转轴的真实工况条件,对转轴模型施加边界条件。在转轴的粗端面施加边界条件为完全约束,在转轴的细端面施加边界条件为固定Y方向运动,如图13所示。
此叶片泵的基本参数中,排量为25 mL/r,额定转速为960 r/min,压力为6.3 MPa,驱动功率P为3.3 kW。 转矩 T=9 550 P/n=9 550×3.3/960=32.828 N·m,根据T=FR,转轴粗端半径R1为10 mm,细端半径R2为6 mm,可得出在粗端和细端的力F的大小。
转轴粗端的键槽受力和转轴细端的花键受力简化为均布载荷q,已知键槽长度L1为20 mm,花键长度L2为25 mm,根据F=qL,可以求得键槽均布载荷为164 140 N/m,花键均布载荷为218 853 N/m。在键槽和花键处施加载荷,如图14所示。
所有约束添加完成之后,进行求解,得出在载荷作用下转轴会产生微小变形。转轴总位移云图如图15所示,总应力云图如图16所示。转轴最大位移出现在花键一端,其值为0.446 48×10-7m。转轴最大应力也出现在花键一端,其值为571 478 Pa。
7 结束语
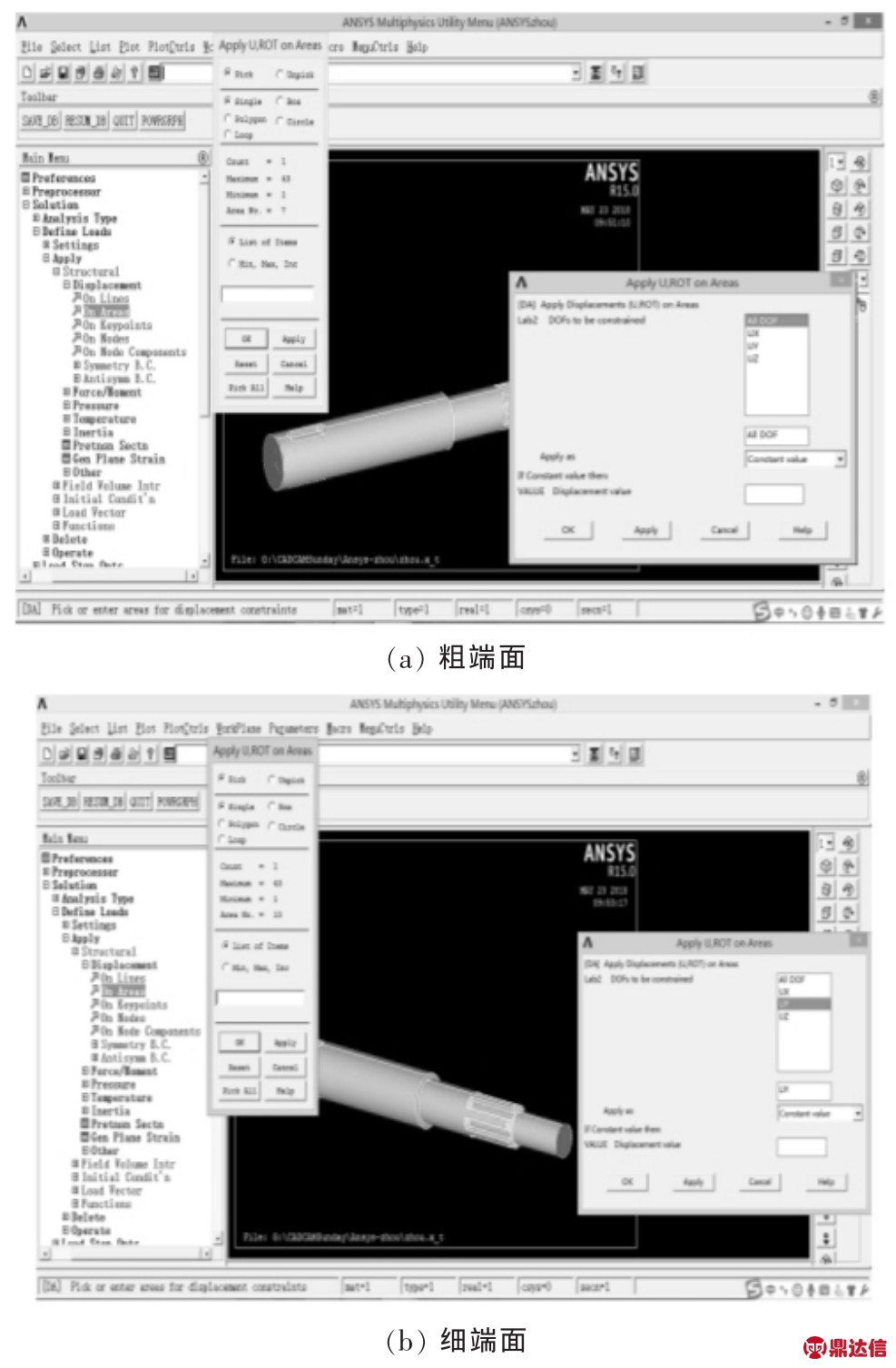
▲图13 转轴模型施加边界条件
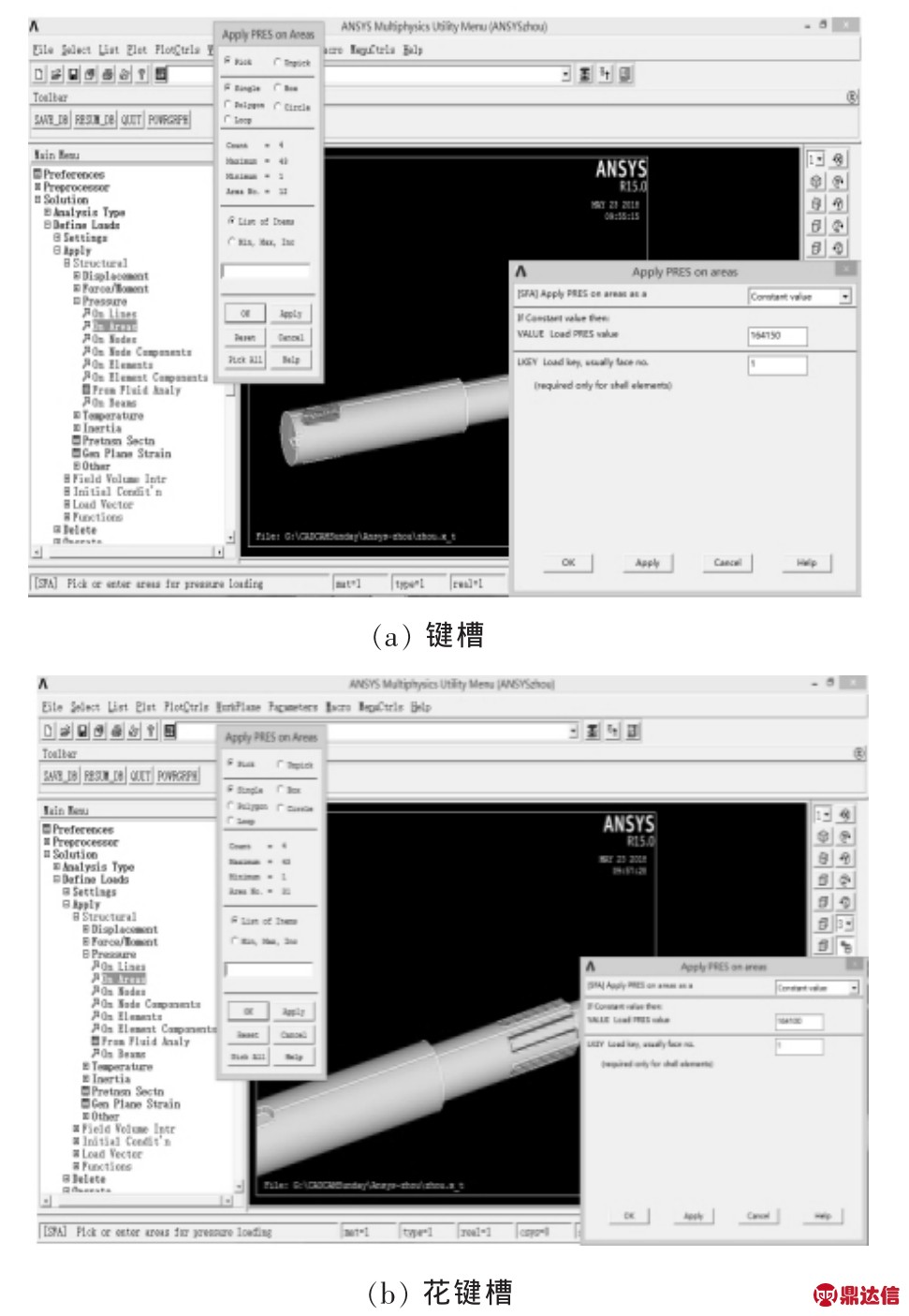
▲图14 转轴模型施加载荷
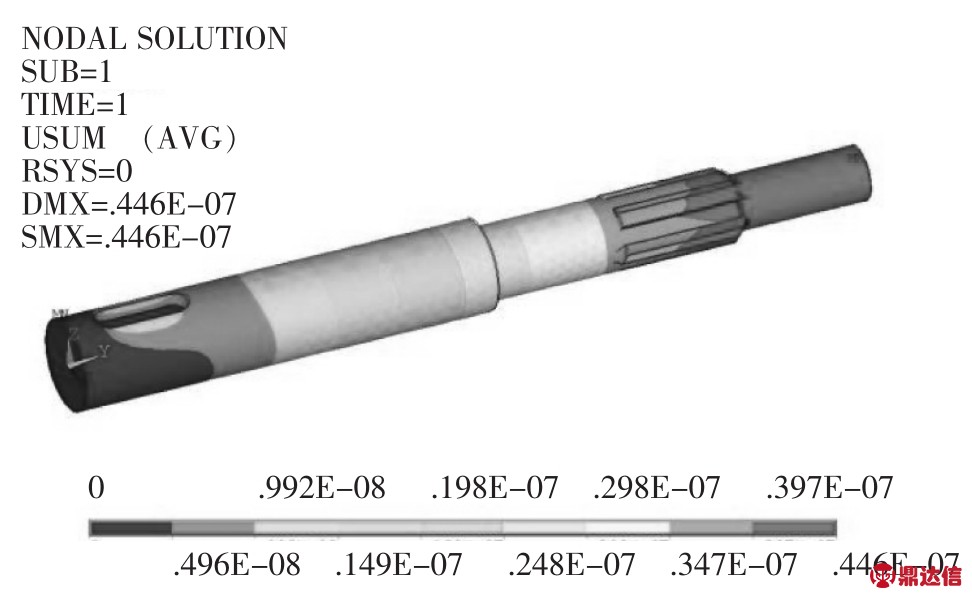
▲图15 转轴总位移云图
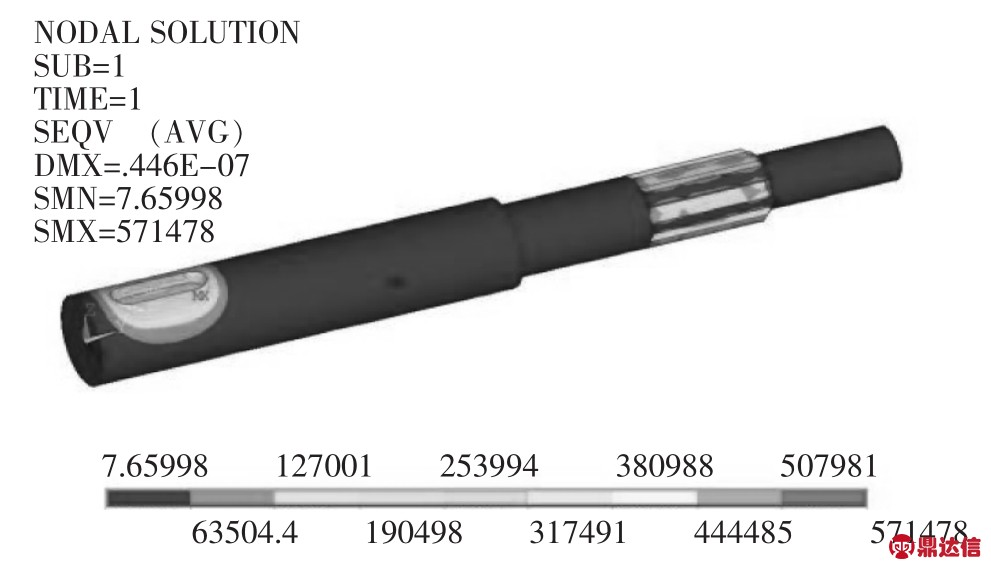
▲图16 转轴总应力云图
笔者对双作用式叶片泵的工作原理和工况条件进行分析,应用Unigraphics软件对其进行建模和仿真,并对定子进行数控加工编程,生成数控加工代码,可用于机械制造。
应用ANSYS软件对叶片泵转轴进行有限元分析,求得转轴在载荷作用下的总位移云图和总应力云图,可知在工作时转轴变形很小,但长期在循环转矩作用下危险截面处于花键部分,应对转轴花键部分采取措施,如在转轴外设置增强强度和抗振性能的装置,以避免转轴在花键处损坏而导致报废。