摘要:对液压电机叶片泵内部的激振源和振动传递路径进行分析,通过对其结构进行适当假设和等效,建立液压电机叶片泵的虚拟样机模型,采用有限元法对液压电机叶片泵进行模态分析,获得其固有频率及对应振型.结果表明:动压支撑结构使得液压电机叶片泵的固有频率得到一定提高,有利于液压电机叶片泵的减振降噪;电机转子是产生振动的主要部件,低阶模态下电机转子与叶片泵可能存在共振现象.仿真结果为液压电机叶片泵的结构设计与减振降噪提供理论参考.
关键词:液压电机叶片泵;模态分析;减振降噪;有限元
液压电机泵是将电动机和液压泵直接集成为一体的新型液压动力单元,具有结构紧凑、噪声低、效率高、无外泄漏等优点,液压电机泵具有重要的研究价值和广阔的应用前景.
工程实际中,几乎所有设备都以各自特有的形态处在振动环境中,这不仅有碍产品功能的发挥,而且还会损害操作者的身心健康,污染环境.为使产品能够安全可靠地工作,必须保证结构系统具有良好的动态特性,以满足机械结构静、动态特性与低振动、低噪声的要求[1-2].本文通过对液压电机叶片泵进行有限元建模和模态分析,求得其固有频率与对应的振型图,从而研究液压电机叶片泵的振动特性,可为液压电机叶片泵减振降噪、改善其性能以及其运行的稳定性提供理论依据.
1 液压电机叶片泵的振动机理分析
1.1 激振源
电机泵的主要激振源可分为电磁振动、机械振动和流体振动,电磁振动是由于电机气隙中磁通相互作用,产生随时间和空间变化的径向力波,这种力波在气隙中是旋转的或是振动的,当电磁力波的频率与电机定子的固有频率相同或者接近时,就会引起共振;机械振动包括电机转子的旋转偏心与不平衡产生的振动、叶片的振动以及轴承的振动;流体振动主要是叶片泵中的油液通过配流盘接触高压腔时倒灌流量引起的压力冲击.其中主要激振源的激振频率见表1.
表1 主要激振源的激振频率
Tab.1 The exciting frequency of vibration source
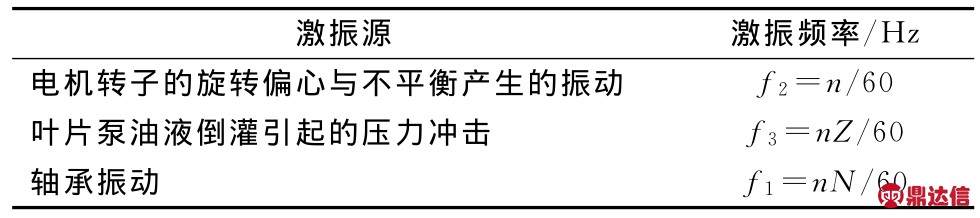
注:n为转速,Z为叶片泵的叶片数,N为轴承的滚子数.
1.2 振动传递路径
由图1所示的液压电机叶片泵内部结构图[3-5]分析可得出其振动的主要传递路径:
1)电机转子的旋转偏心与不平衡激发的振动,传递至主轴两端的轴承,左端的轴承将振动传递至前端盖、机座,而滑动轴承Ⅰ与滑动轴承Ⅱ分别将振动传递至泵芯座、出油口压盖,最终传递至后端盖、机座.
2)叶片的离心力和底部压力使叶片顶部在叶片泵泵芯定子的工作过渡曲线连接点上产生冲击引起的振动,依次传递至泵芯定子、泵芯座、后端盖,最终传递至机座.
3)配流盘处流量脉动、压力冲击等激发振动,传递至配流盘紧靠的出油口压盖和泵芯座.
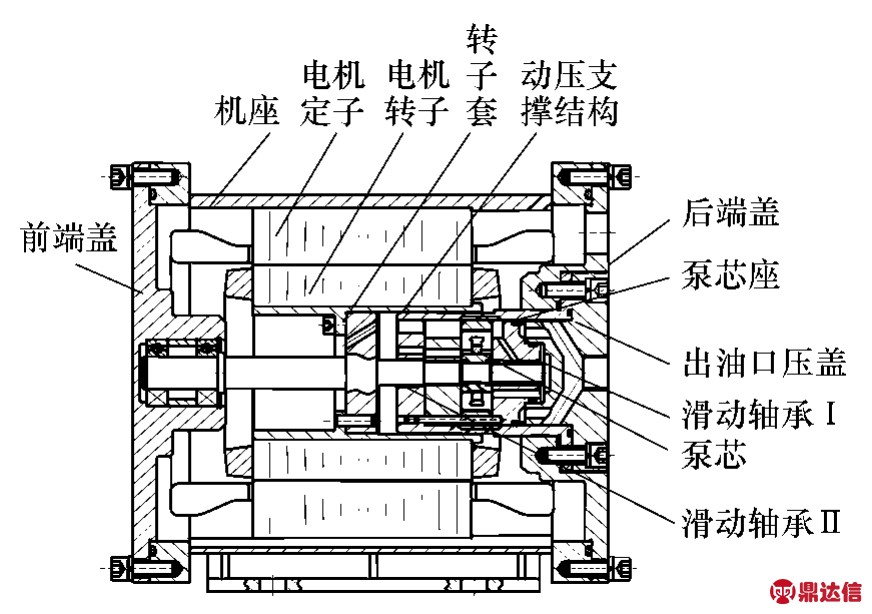
图1 液压电机叶片泵内部结构
Fig.1 Internal structure of electric motor-vane pump
2 液压电机叶片泵模型的建立
2.1 几何模型及材料属性参数设置
由于电机泵的结构零件较多,为了方便网格划分,缩短计算时间,因此在对整体振动特性影响不大的前提下,有必要对模型进行简化.具体简化操作如下:
1)忽略对整体振动特性影响较小的机座、前后端盖、泵芯座和出油口压盖上的小孔、倒角及电机转子的键槽等;
2)忽略对动态特性影响较小但占内存较大的机座、前后端盖与泵芯座之间的螺纹特征.
绕组对电机模态频率的影响一直是电机模态分析中的难点,主要原因是:
1)绕组端部形状复杂,建模难度大;
2)绕组的弹性模量等力学参数受槽满率和浸漆工艺影响较大,模态仿真参数难以确定.
本文在建立绕组模型时,做如下简化:
1)将绕组端部形状等效为与实际绕组体积相同的中空圆环体;
2)绕组密度按估算绕组中铜线、绝缘材料和气隙所占比例等效[6].
通过对电机泵进行以上假设和等效,由机座、电机定子、定子绕组、电机转子、端盖、叶片泵泵芯等主要零件组成的电机泵模型可以模拟电机泵的振动模态特性,电机泵的有限元模态分析三维模型如图2所示,表2为电机泵模型的材料属性.

图2 三维模型
Fig.2 Three-dimensional model
表2 模型的材料属性
Tab.2 Properties of materials of model
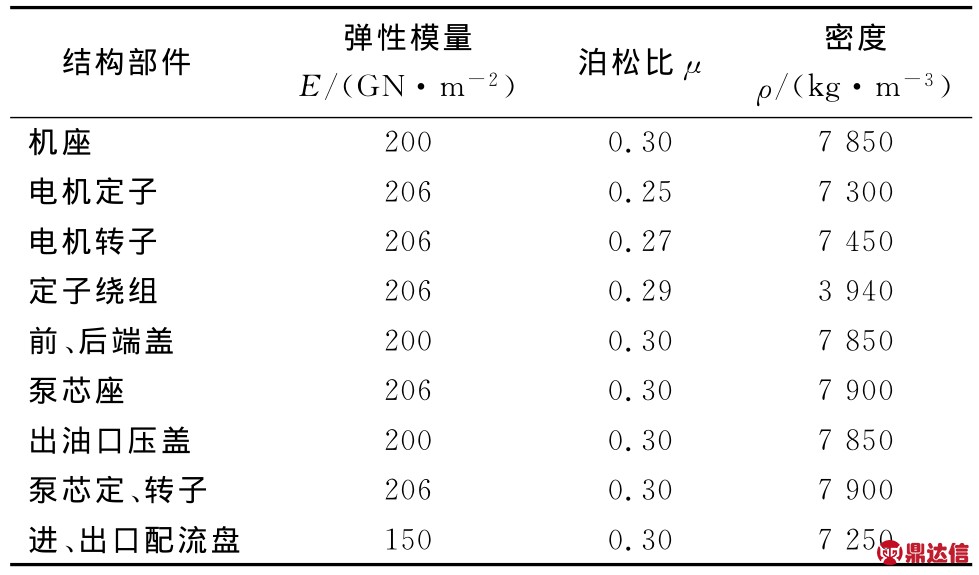
2.2 网格划分
由于电机泵的模型结构比较复杂,为达到提高网格质量并减少网格数量的目的,对导入到ANSYS Workbench[7]中的模型各组成部分分别进行网格划分,并对动压支撑处进行网格细化,这样可以加快运算速度并且对运算精度也影响不大.图3所示为电机泵振动模态有限元仿真模型网格划分图,其中有限元模型节点总数为3 612 604,单元总数为2 445 572.

图3 有限元模型及网格划分
Fig.3 Finite element model and mesh division
2.3 边界条件与约束
根据电机泵实际工作时的安装情况,设定以下边界条件:
1)根据地脚螺栓与地面固定的实际情况,按固定约束形式模拟这种螺栓联接,约束机座底部上4个螺栓安装孔上所有节点的自由度;
2)根据各主要结构之间螺栓固定的实际情况,按等效替换原理,以固定约束形式模拟电机泵主要结构之间的螺栓联接;
3)对电机泵内部的动压支撑结构设置滑动接触.
3 液压电机叶片泵的模态分析
利用ANSYS Workbench有限元仿真系统,对电机泵的有限元模型进行振动模态仿真,选择Block-Lanczos法进行求解,可获得其现有结构与边界条件下的固有频率和振型图.
图4为无动压支撑与有动压支撑的电机泵的前10阶固有模态频率对比图.
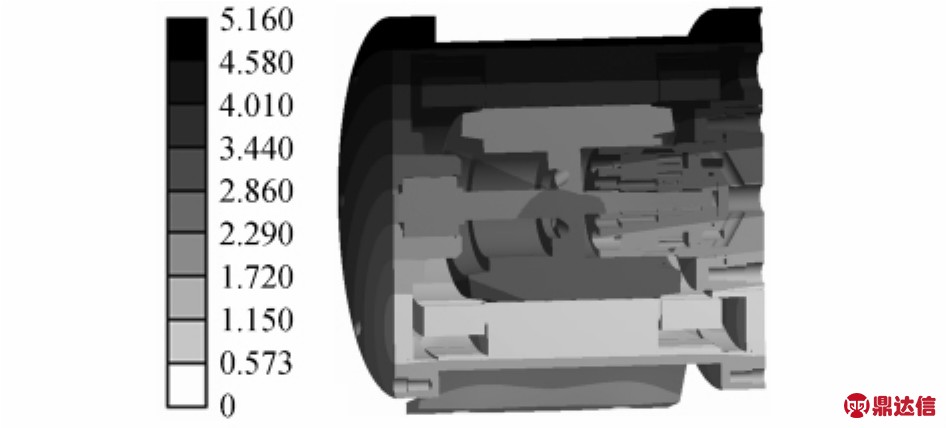
图4 模态频率对比
Fig.4 Modal frequency contrast
由图4可知,无动压支撑的电机泵的前3阶模态频率分别为62.411、140.13、156.78Hz,而有动压支撑结构的电机泵的前3阶模态频率分别为65.19、142.44、158.75Hz,后者的前3阶模态频率相比前者均有一定的提高,而第4阶至第10阶模态频率后者比前者在整体上有较大的提高,其作用使电机泵的结构刚度得到了加强,动变形降低,有利于降低电机泵的振动噪声.电机泵的一阶固有模态频率为65.19Hz,对应的临界转速为3 911.4r/min.
3.1 电机泵的模态分析
由于电机泵的前三阶固有振动模态对其运行工况具有重要的影响,现取前3阶模态振型图进行分析.图5~7分别为前3阶固有振动模态对应的振型图.
图5所示为一阶固有模态振型图,其固有模态频率为65.19Hz,振动主要发生在电机转子上,而其形式以电机转子轴线为中心,以两端轴承为支撑,电机转子偏离轴线旋转振动,电机转子铁芯外部整体振动位移最大为8.580mm,电机转子铁芯内部振动位移较小为4.770mm;一阶固有振动模态对电机泵的运行状况有重要的影响,由图5可知,当电机泵运行中的激励足够大时,能够引发一阶固有振动,严重时使电机转子铁芯与电机定子铁芯产生碰磨.
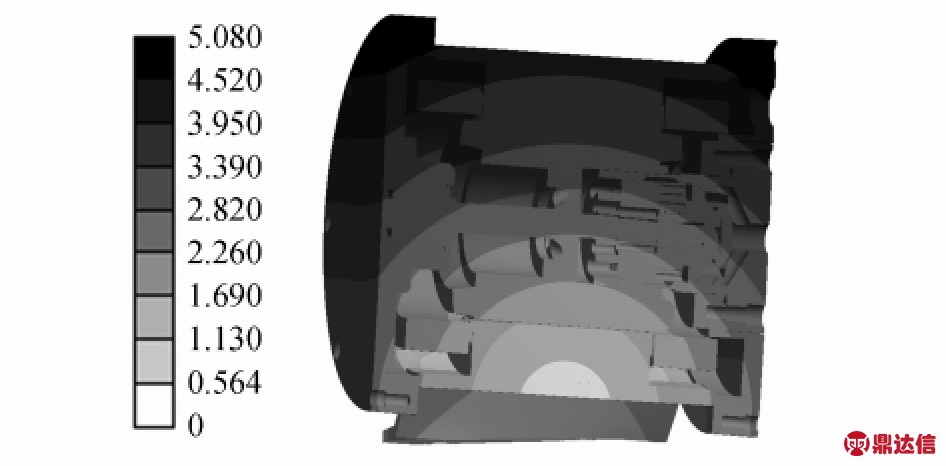
图5 一阶模态振型图(mm)
Fig.5 First-order vibration mode(mm)
图6为二阶固有模态振型图,固有模态频率为142.44Hz,主要振型为电机泵绕机座底部为固定约束的前后摆动,机座与电机定子的底部振动位移最小为零,电机泵总体振动位移自下而上逐渐变大,最大振动位移出现在机座、前后端盖的顶部,其值为5.160mm.电机转子的振型为绕电机泵中部为对称面的前后摆动,电机转子铁芯的左下端振动位移最大;二阶固有振动在电机叶片泵运行中对电机转子铁芯的端部产生重要影响,使得端部的磁场间隙变得不稳定,与电机定子铁芯的端部产生摩擦,可引起电机转子与电机定子的共振.
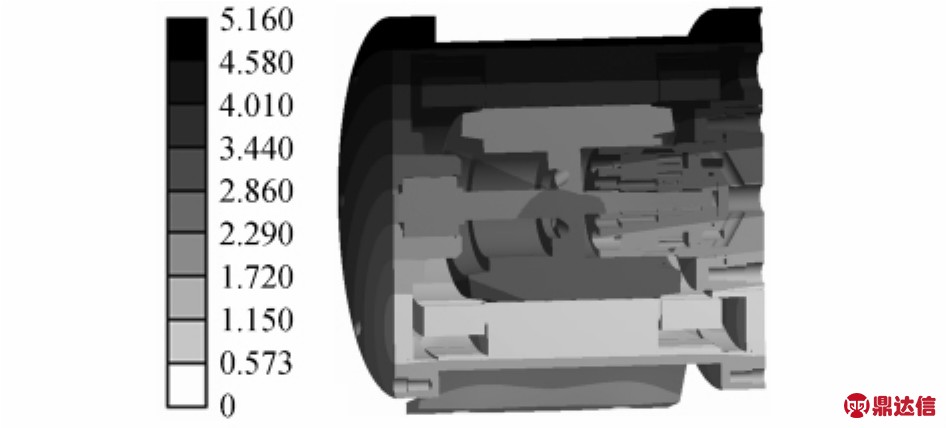
图6 二阶模态振型图(mm)
Fig.6 Second-order vibration mode(mm)
图7为三阶固有模态振型图,固有模态频率为158.72Hz,主要振型为电机泵绕机座底部为固定约束的左右弯曲摆动,机座底部的振动位移最小为零,电机泵总体振动位移自下而上逐渐变大,最大振动位移出现在电机泵两端的顶部,其值为5.080 mm.电机转子的振型为绕机座底部的左右弯曲摆动,电机转子铁芯的顶部振动位移最大,三阶固有振动对电机泵的影响与二阶固有振动的影响相似.
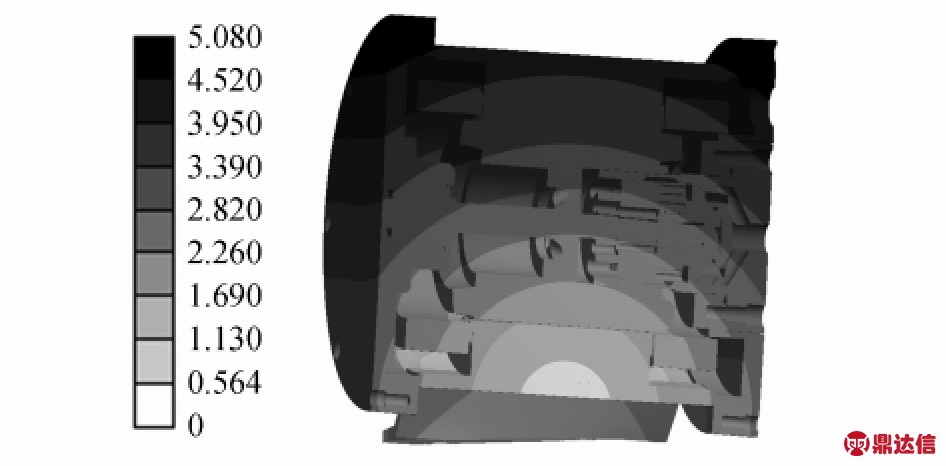
图7 三阶模态振型图(mm)
Fig.7 Third-order vibration mode(mm)
3.2 主要零件的模态分析
叶片泵机械噪声的频率可用下式给出[8]:

式中:k 为谐波次数,k=1,2,…;Z 为叶片数,Z=10;n为泵的旋转速度,n=600~1 800r/min.
叶片泵机械噪声谐波次数为2或4,谐波次数为2、4时叶片泵机械噪声的频率分别为

图8为电机转子、泵芯座和出油口压盖按实际约束边界条件得出的固有模态频率.
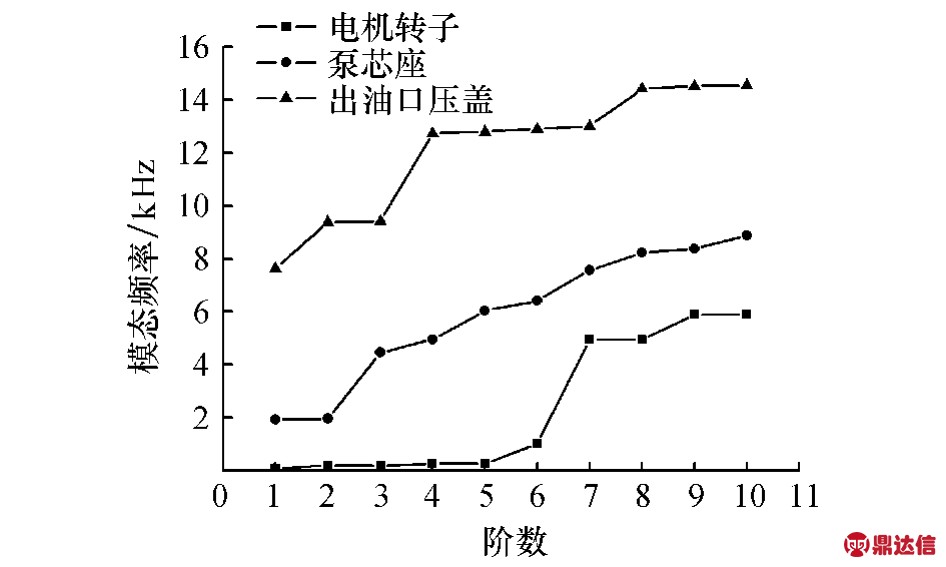
图8 主要零件模态频率
Fig.8 Modal frequency of main parts
由图8可知,电机转子的第4阶至第6阶的固有模态频率在叶片泵机械噪声频率范围内,电机转子与叶片泵可能存在共振现象.而泵芯座和出油口压盖的固有模态频率已远远超出了叶片泵机械噪声频率范围,所以这两者与叶片泵之间不存在共振现象.
4 结论
1)动压支撑结构使得液压电机叶片泵的固有频率有一定的提高,结构刚度得到了加强,动变形降低,有利于降低液压电机叶片泵的振动噪声.
2)电机转子是产生振动的主要部件,而电机转子的最大振动位移出现在其铁芯的端部、顶部,使电机泵铁芯端部、顶部的磁场间隙变得不稳定,严重时会引起电机转子铁芯与电机定子铁芯产生碰磨,影响电机泵运行的平稳性,增加其刚度可减小其振动位移,提高电机泵运行的平稳性.
3)在低阶模态下电机转子与叶片泵可能存在共振现象,而泵芯座、出油口压盖与叶片泵及电机转子不存在共振现象.