摘 要: 以某高性能普通三元件向心涡轮液力变矩器为参考样机,确定循环圆有效直径为425 mm,采用相似设计法得到同性能液力变矩器,并将其作为基准型,通过合理分割基准型泵轮叶片得到双泵轮液力变矩器的循环圆和叶片.设计了滑差离合器结构,给出了滑差离合器及摩擦片的主要技术参数.运用计算流体动力学(CFD)方法对所设计的双泵轮液力变矩器进行数值模拟,分别获得双泵轮状态、单泵轮状态及滑差状态3种状态下的能容特性和原始特性.通过对比分析可知,所设计的双泵轮液力变矩器能够通过滑差控制实现能容的连续可控性,可应用于装载机发动机与变矩器的变能容匹配.
关键词: 双泵轮液力变矩器;滑差控制;性能预测;滑差离合器;变能容
目前,对于装有液力传动系统的工程机械而言,发动机与液力变矩器之间的合理匹配及如何有效利用发动机功率等问题仍亟待解决[1].传统的匹配方式往往不能满足如装载机等工程车辆对于复杂作业工况的需求,其根本原因主要在于发动机与变矩器特性相对固定,两者匹配后的共同工作特性无法随作业工况动态变化.如何实现发动机与变矩器之间的动态匹配,提高发动机功率利用率,近年来受到越来越广泛的关注[2-3].实现发动机变功率和液力变矩器能容可变是解决这一问题的两种有效途径.基于滑差控制的双泵轮液力变矩器能够实现能容的连续可变,因此对其研究具有重要的理论价值和工程实际意义.
国外对于双泵轮液力变矩器的研究较早,美国的卡特匹勒公司便成功将其应用于装载机上,如CAT988B、992B及992C等.但当时主要用于解决轮胎打滑的问题,并未对其变能容特性进行深入研究[4-5].国内最早对双泵轮液力变矩器的研究始于20世纪80年代,由长沙矿山研究院、北京工业学院和沈阳矿山机器厂共同研制了国内第一台SBYB-465K型双泵轮液力变矩器,魏宸官[6]对其特性进行了深入研究.但上述所研究的双泵轮液力变矩器只能实现能容变化的两条曲线(单泵轮状态和双泵轮状态),能容曲线不是连续可变的.文中设计了能容连续可变的双泵轮液力变矩器,进行了计算流体力学(CFD)计算,对其性能进行了预测分析,为双泵轮液力变矩器的结构优化设计提供了重要的参考依据.
1 循环圆和叶片设计
相似设计法是现代液力变矩器设计的有效方法之一,其以现有高性能液力变矩器为参考样机,根据相似原理,设计出与参考样机保有同性能的新液力变矩器[7- 8].文中以某高性能三元件向心涡轮液力变矩器为参考样机,选择循环圆有效直径,采用相似设计法获取高性能液力变矩器作为基准型,对获得的基准型液力变矩器泵轮进行合理分割,得到带有主泵轮和辅助泵轮的四元件双泵轮液力变矩器.
以某发动机与参考变矩器样机进行功率匹配,选取发动机在高效工况点处的最大转矩为Temax=TB=1 266 N·m.图1为参考样机原始特性,可知高效工况点(i*=0.732)对应的泵轮转矩系数 =2.97×10-6.图中,
为泵轮转矩系数,i为转速比,ip1、ip2为与工作效率η=0.75对应的转速比,K为变矩比.经计算得到基准型液力变矩器有效直径为429 mm,为保证其形成系列化选取有效直径为425 mm.
再根据相似设计原理,以参考样机为设计模型,设计基准型液力变矩器循环圆和叶片,如图2所示.

图1 参考样机的原始特性
Fig.1 Original characteristics of reference prototype
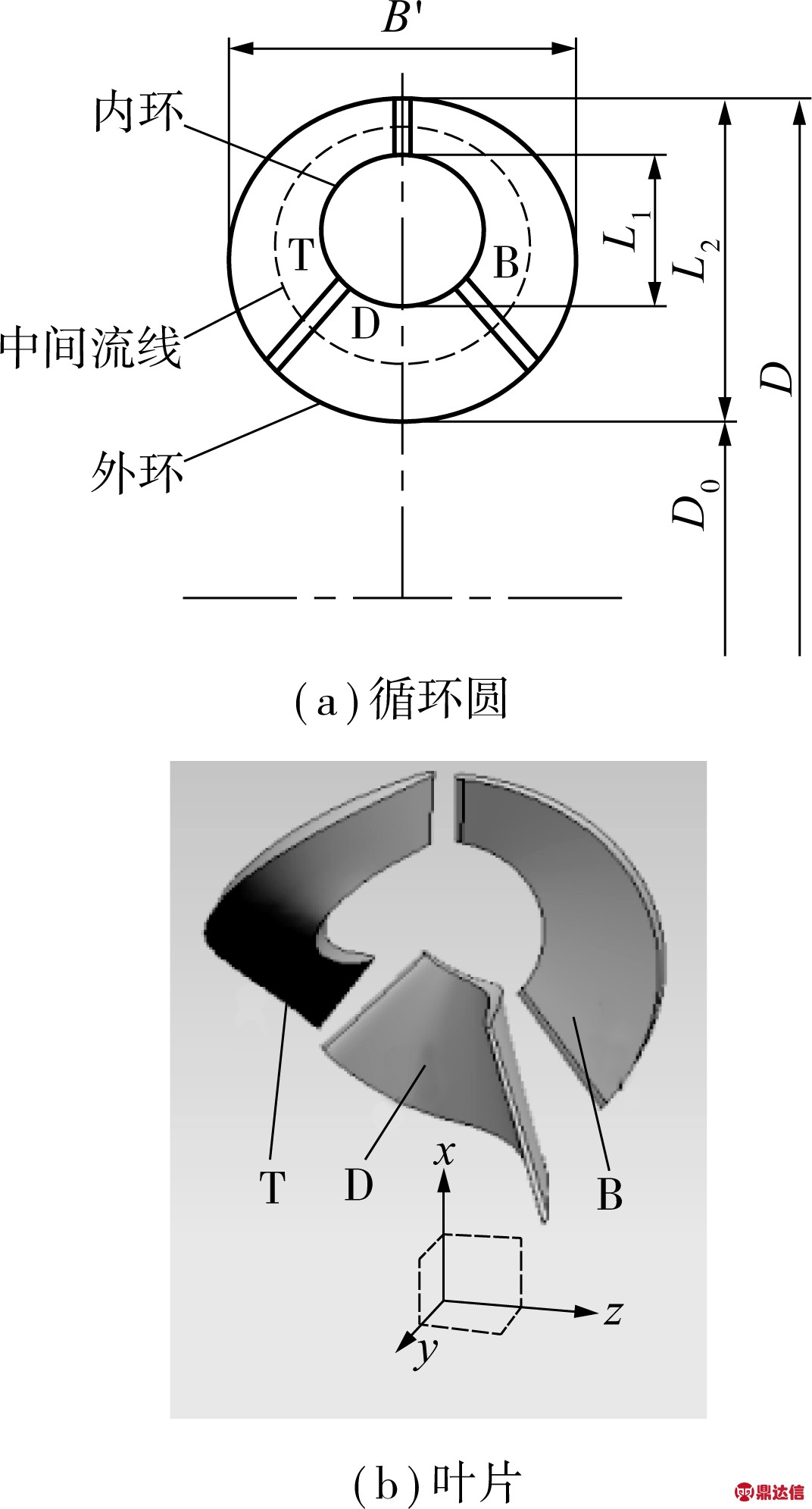
图2 基准型液力变矩器循环圆和叶片
Fig.2 Cycle round and blade of the standard torque converter
B—泵轮;T—涡轮;D—导轮
图2中,B′为循环圆的轴向宽度,D0为循环圆内径,D为有效直径,L1为循环圆内环的径向长度,L2为循环圆外环的径向长度.保证基准型液力变矩器涡轮和导轮不变,对其泵轮进行分割,分割位置根据双泵轮液力变矩器在滑差离合器完全分离时与发动机的匹配性能来确定[9].利用CFD技术经大量计算,文中最终以分割参数θ=60°处作为分割位置,得到双泵轮液力变矩器循环圆和叶片,如图3所示.根据工程设计经验,主泵轮B1与辅助泵轮B2之间的间隙选为3 mm.
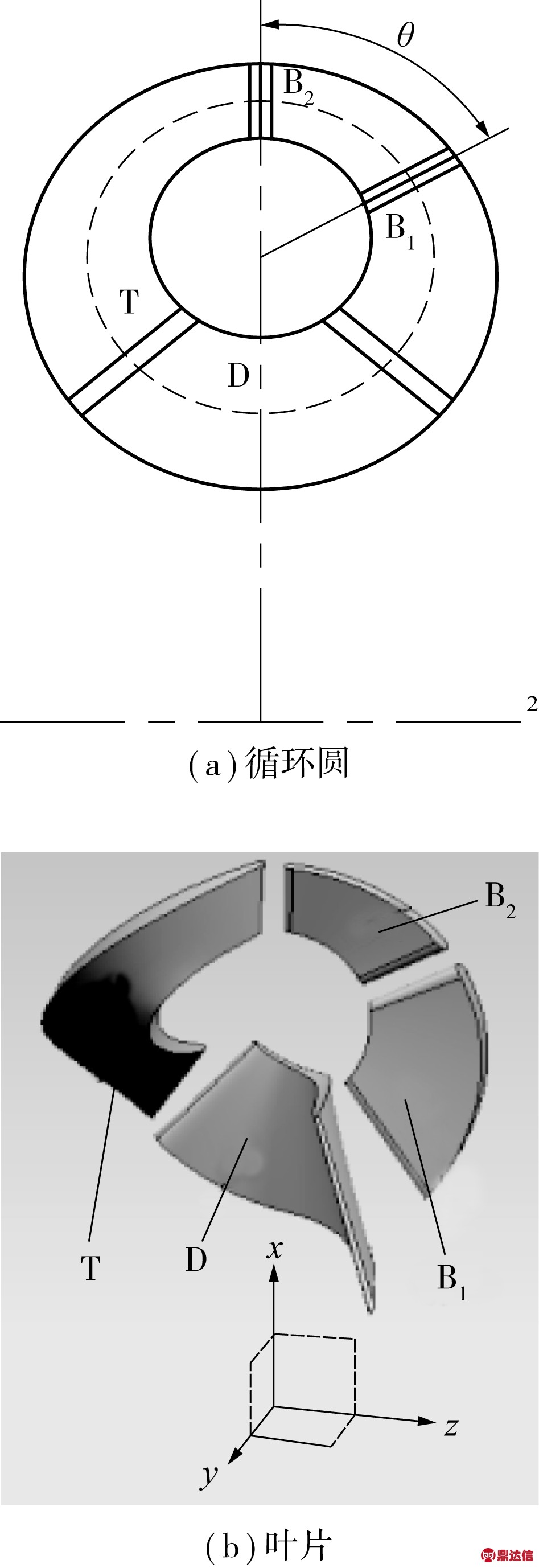
图3 双泵轮液力变矩器循环圆和叶片
Fig.3 Cycle round and blades of the double-impeller torque converter
2 滑差离合器结构设计
图4为双泵轮液力变矩器结构简图,其中L表示滑差离合器,I表示输入轴,O表示轴出轴.图5为根据简图设计的双泵轮液力变矩器总体结构.由图可知,主泵轮B1与辅助泵轮B2主要靠滑差离合器进行接合,滑差离合器结构设计的好坏直接影响双泵轮液力变矩器的性能[10].如图6所示,滑差离合器主要由主动摩擦片、从动摩擦片和油缸组成.主油路向油缸工作腔供油与变矩器侧腔形成压差推动活塞运动,主、从动摩擦片间的油膜厚度发生改变,通过液体的粘性传递摩擦片间的转矩,进而改变滑差离合器的滑摩状态.
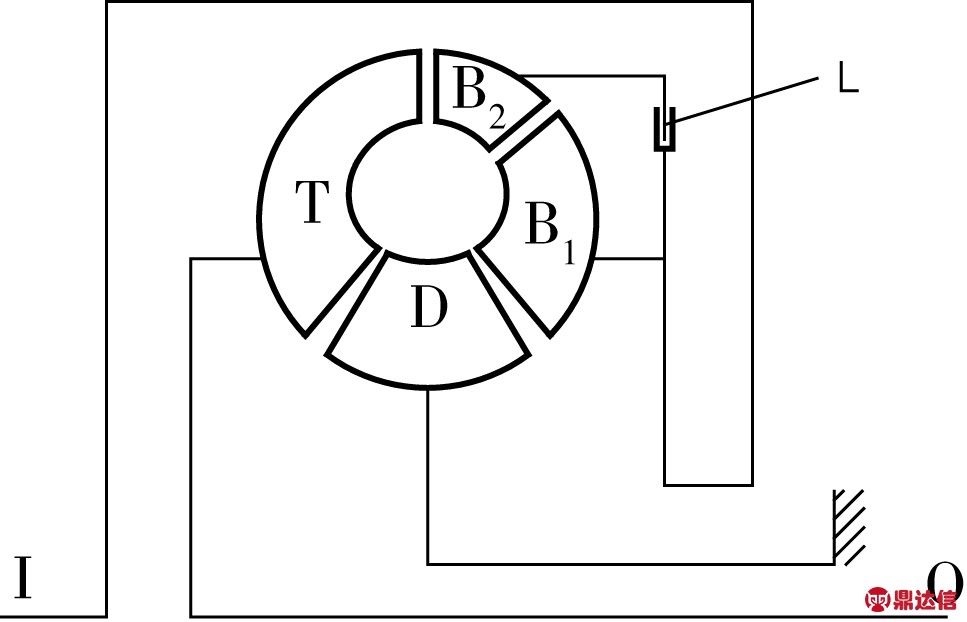
图4 双泵轮液力变矩器结构简图
Fig.4 Structure diagram of double-impeller torque converter
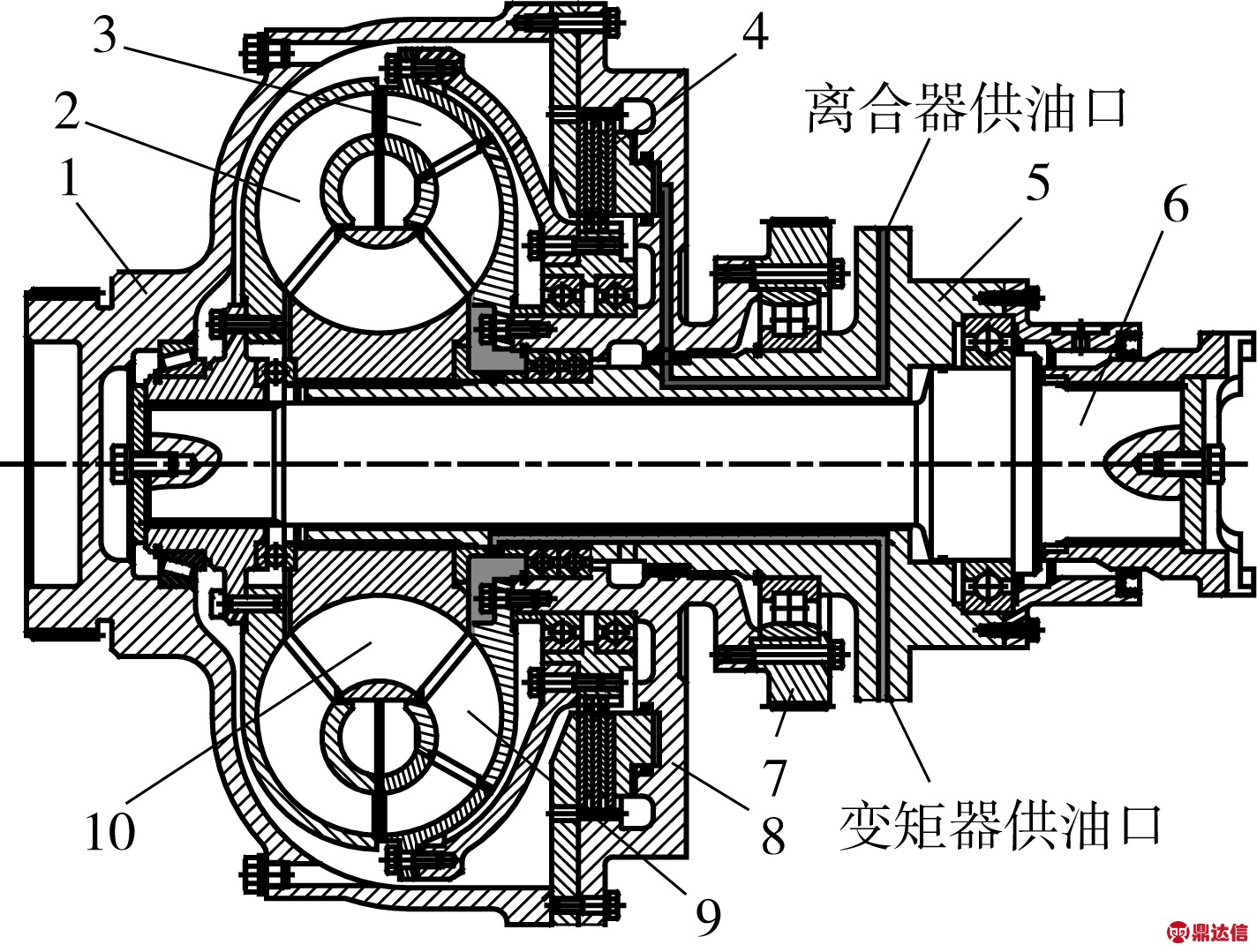
图5 双泵轮液力变矩器总体结构
Fig.5 General structure of double-impeller torque converter
1—罩轮(输入);2—涡轮T;3—辅助泵轮B2;4—滑差离合器;
5—导轮座;6—涡轮轴(输出);7—油泵驱动主齿轮;8—离合
器壳体;9—主泵轮B1;10—导轮D

图6 滑差离合器及摩擦片间的油膜示意图
Fig.6 Schematic diagram of oil film between slip clutch and friction plate
1—从动摩擦片;2—通孔;3—挡板;4—离合器壳体;5—花键I;
6—主动摩擦片;7—密封圈I;8—活塞;9—密封圈II;10—花键II;
11—滑差离合器供油通道
如图7所示,R1为摩擦片有效接触内半径,R2为摩擦片有效接触外半径,h1为主动摩擦片厚度,h2为从动摩擦片厚度,Δδ为油槽深度,θ1为油槽中心角,θ2为扇形单元中心角,ω1为主动摩擦片转速,ω2为从动摩擦片转速.与早期SBYB_465K结构相比,文中所设计的从动摩擦片为多片式结构,大大增强了滑差离合器传递转矩的能力,同时主摩擦片带有径向油槽,对偶的从动摩擦片为光片结构.

图7 主动摩擦片和从动摩擦片结构示意图
Fig.7 Schematic Diagram of active friction plates and driver friction plates
3 双泵轮液力变矩器性能预测
为了更好地表述双泵轮液力变矩器的工作状态,现对双泵轮液力变矩器工况进行如下定义:当滑差离合器工作腔压力高于某一值使离合器完全结合,主、辅泵轮同速旋转共同传递功率,称此工况为双泵轮工作状态,简称双泵轮状态;当滑差离合器工作腔压力低于某一值使离合器完全分离,仅主泵轮传递功率,辅助泵轮空转时,称此工况为单泵轮工作状态,简称单泵轮状态;调节工作腔控制压力处于某一范围内使离合器部分结合,此时主、从动摩擦片间存在滑差,主、辅泵轮以不同速度旋转传递较低的功率,称此工况为双泵轮液力变矩器滑差工作状态,简称滑差状态.由此可知,双泵轮液力变矩器特性由转速比和离合器滑差率共同决定.
双泵轮液力变矩器转速比和离合器滑差率的计算公式为:
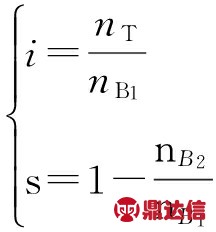
(1)
式中,s为离合器滑差率,nB1为主泵轮转速,nB2为辅助泵轮转速,nT为涡轮转速.
CFD数值模拟计算方法的日益成熟,增强了人们对三维流体运动进一步的认知.经大量实践证明,采用CFD方法对向心涡轮液力变矩器进行数值模拟,能够准确地预测变矩器的性能[11].该方法不仅大大缩短了设计周期,同时节约了设计成本,提高了生产效率,目前已被广泛应用于现代液力变矩器的设计中[12-17].如图8所示,文中同样采用CFD方法对3种不同工作状态下的双泵轮液力变矩器进行数值模拟计算,分别得到3种状态下各叶轮的转矩,进而求得各状态下变矩器的原始特性.
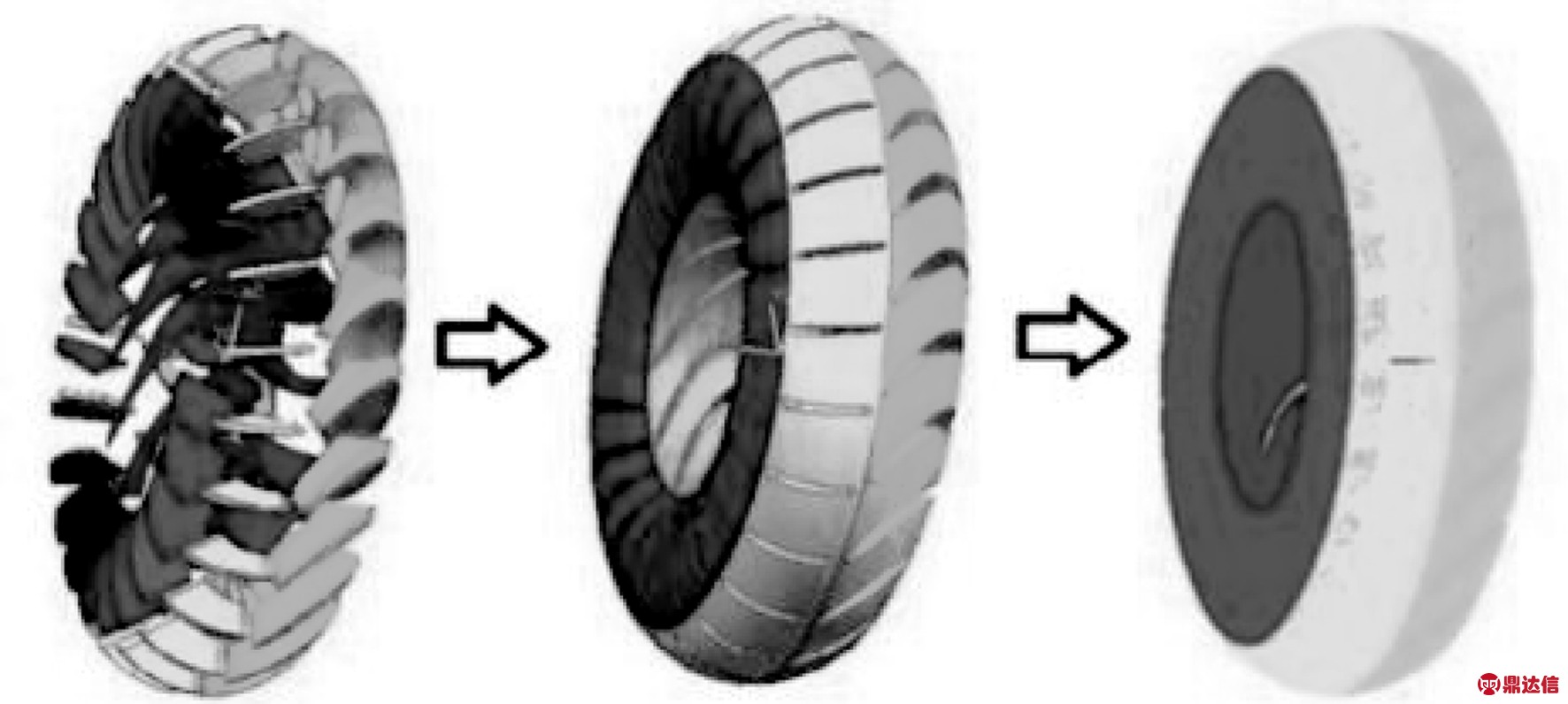
图8 双泵轮液力变矩器CFD数值模拟
Fig.8 CFD numerical simulation of double-impeller torque converter
3.1 双泵轮状态特性分析
双泵轮状态下滑差离合器完全结合,离合器滑差率s=0,主、辅泵轮同速旋转,经计算得到各叶轮转矩T随转速比的变化进行3阶拟合后的曲线,如图9所示.由图可知,涡轮转矩TT和导轮转矩TD随着转速比的变化与普通三元件向心涡轮液力变矩器的变化规律相同,主泵轮转矩TB1随转速比的升高先增大后减小,辅助泵轮转矩TB2随转速比的升高而减小.由图9可以计算得到双泵轮状态下的原始特性,与基准型原始特性进行对比,如图10所示.通过对比分析可知,双泵轮状态下变矩器传动效率和变矩比有所下降,泵轮转矩系数(能容)在低速比时升高而高速比时略有降低.
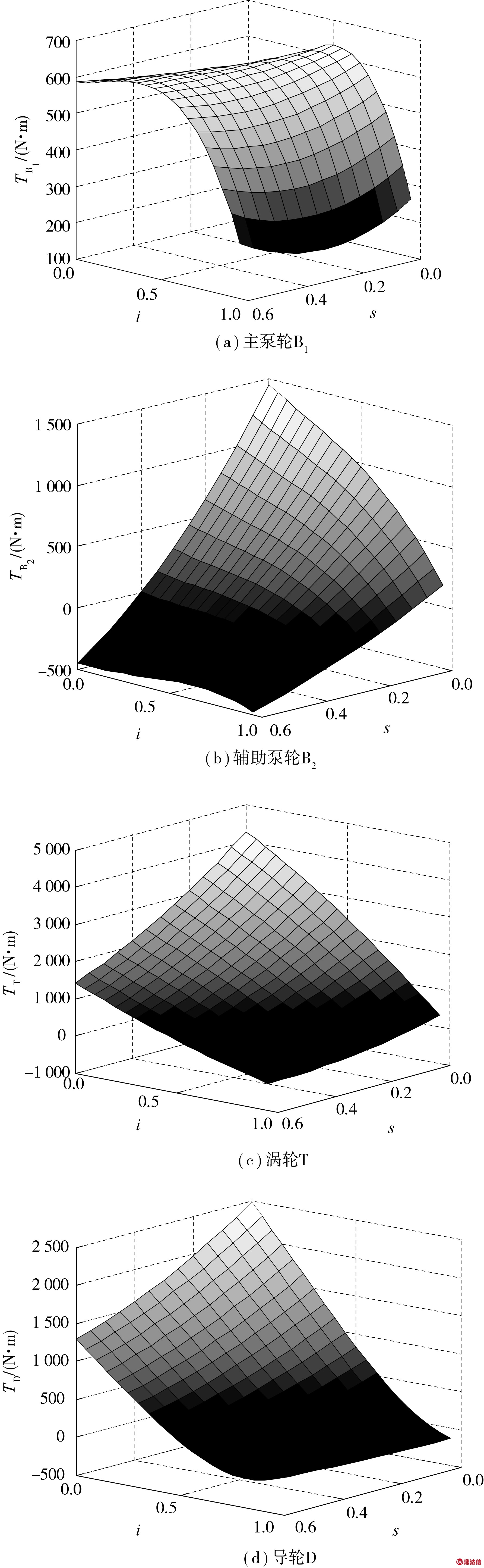
图9 双泵轮状态时各叶轮转矩与转速比的关系
Fig.9 Relationship between impellers torque and speed ratio in two working impellers state
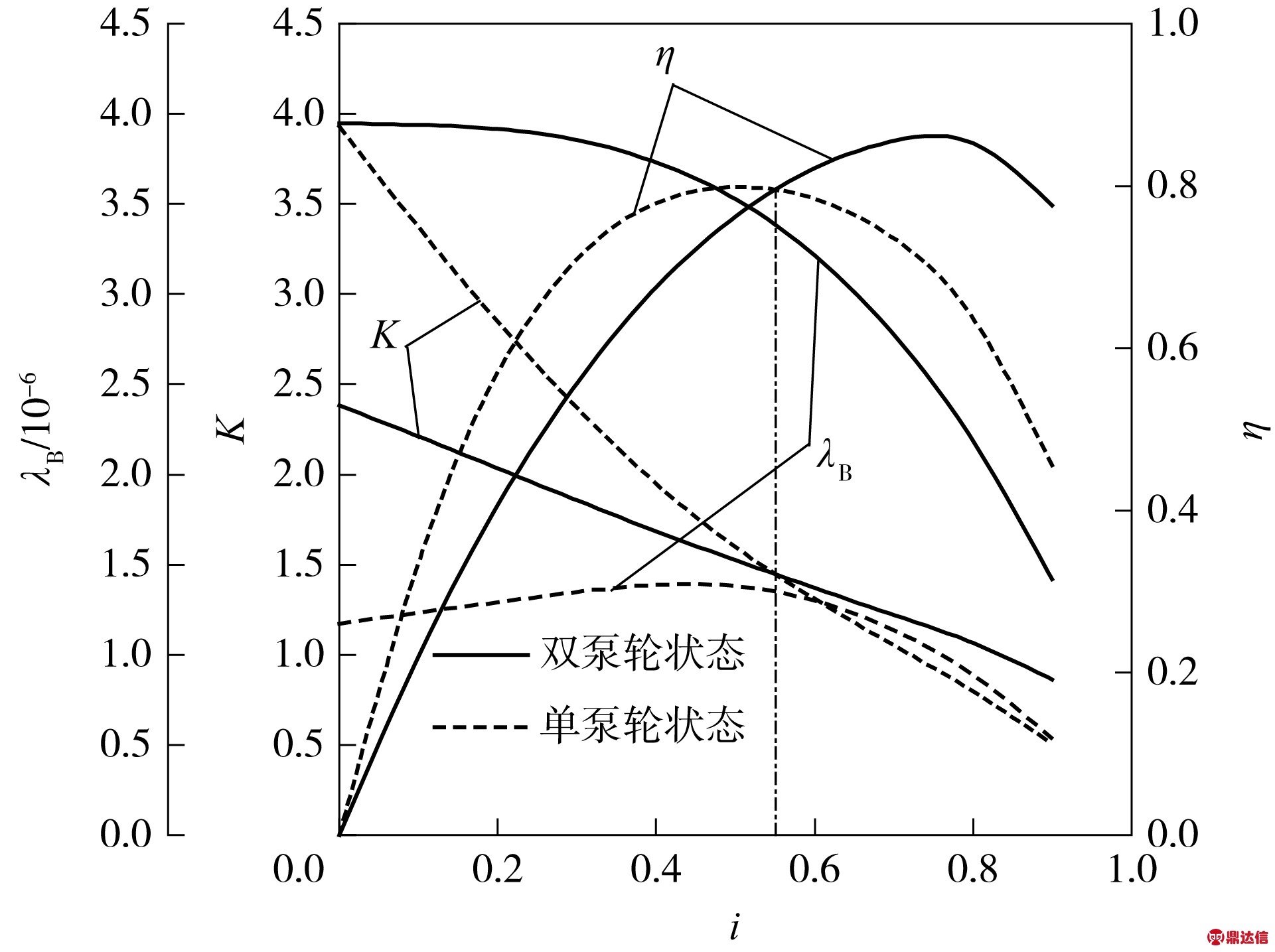
图10 双泵轮状态与基准型的原始特性对比
Fig.10 Comparison of original characteristics between double-impeller and standard torque converter
3.2 单泵轮状态特性分析
单泵轮状态时滑差离合器分离,辅助泵轮空转,仅有主泵轮单独传递转矩.当进行数值模拟计算时,由于辅助泵轮置于壳体内部,其转速无法获知,因此如何求得辅助泵轮空转转速往往成为首要解决的难题.对单泵轮状态下辅助泵轮进行受力分析可以发现,在忽略机械摩擦、液体粘性力等因素的前提下,其空转时辅助泵轮转矩为零,若通过多次CFD计算找到辅助泵轮转矩为零时的工况(s,i),即可解决这一问题.
图11为不同转速比下辅助泵轮转矩TB2随着离合器滑差率的变化曲线,通过直线TB2=0与各曲线的交点即可求得辅助泵轮转矩为零时的离合器滑差率si,根据式(1)得出辅助泵轮空转转速nB2,如图12所示,此时离合器滑差率称为空转离合器滑差率s′.

图11 辅助泵轮转矩与离合器滑差率的关系
Fig.11 Relationship between auxiliary impeller torque and clutch slip rate
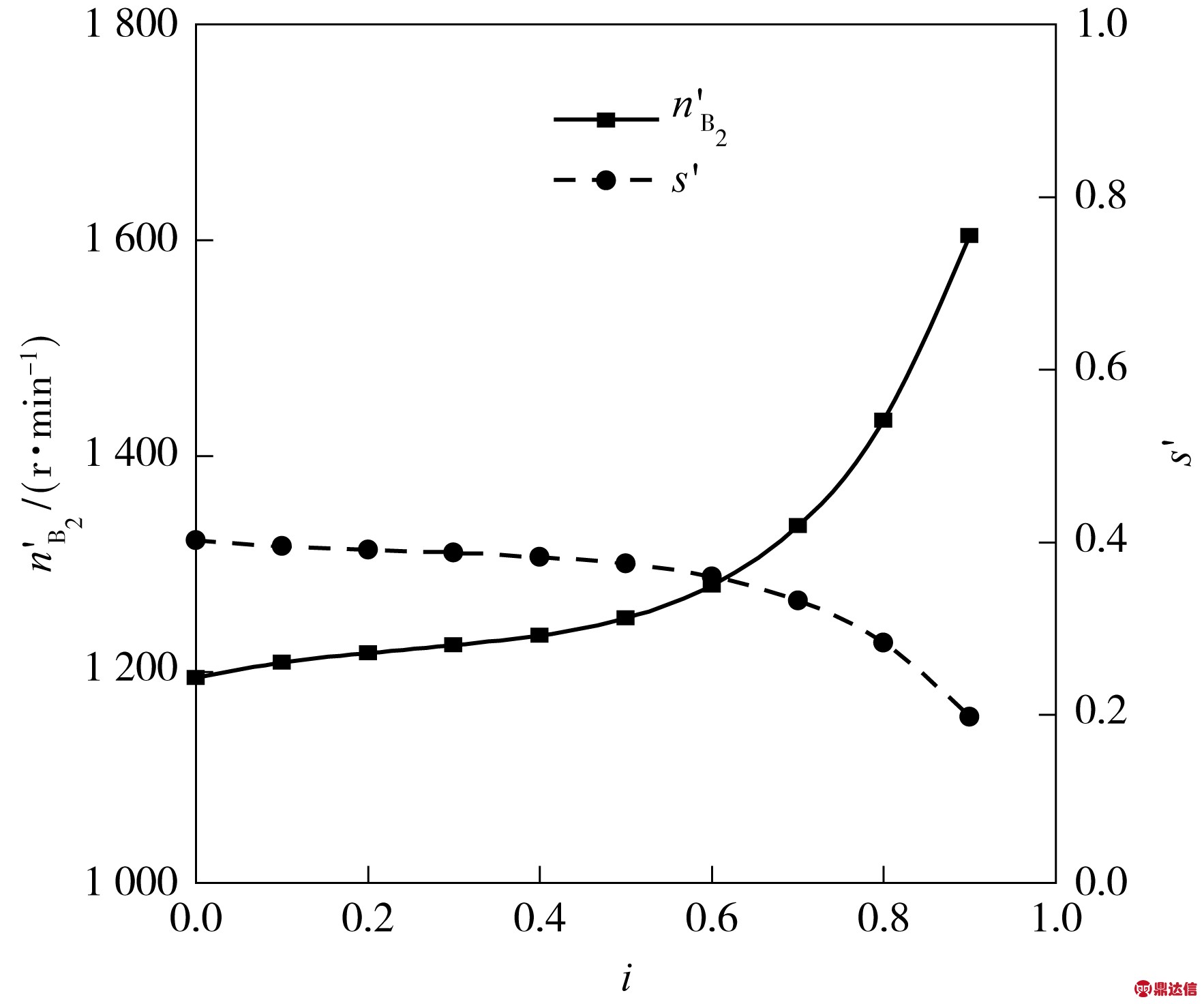
图12 辅助泵轮空转转速
Fig.12 Idle speed of auxiliary impeller
图13为单泵轮状态下各叶轮转矩随转速比变化进行3阶拟合后的曲线,可知涡轮转矩TT和导轮转矩TD随着转速比的变化同样与普通向心涡轮液力变矩器的变化规律相同.此时双泵轮液力变矩器辅助泵轮转矩为零,相当于由主泵轮、涡轮和导轮组成的三元件普通液力变矩器.将其原始特性与双泵轮状态下的原始特性进行对比分析,如图14所示.可以发现,单泵轮状态下变矩比在低转速比时逐渐增大,在高转速比时减小,泵轮转矩系数(能容)在整个转速比范围内减小.除此之外,与双泵轮状态下的特性相比,单泵轮状态下传动效率在低转速比下较高,而在高转速比下较低,两种状态下的泵轮转矩系数(能容)相差很大,能容调节范围较宽.

图13 单泵轮状态时各叶轮转矩与转速比的关系
Fig.13 Relationship between impellers torque and speed ratio in single working impeller state
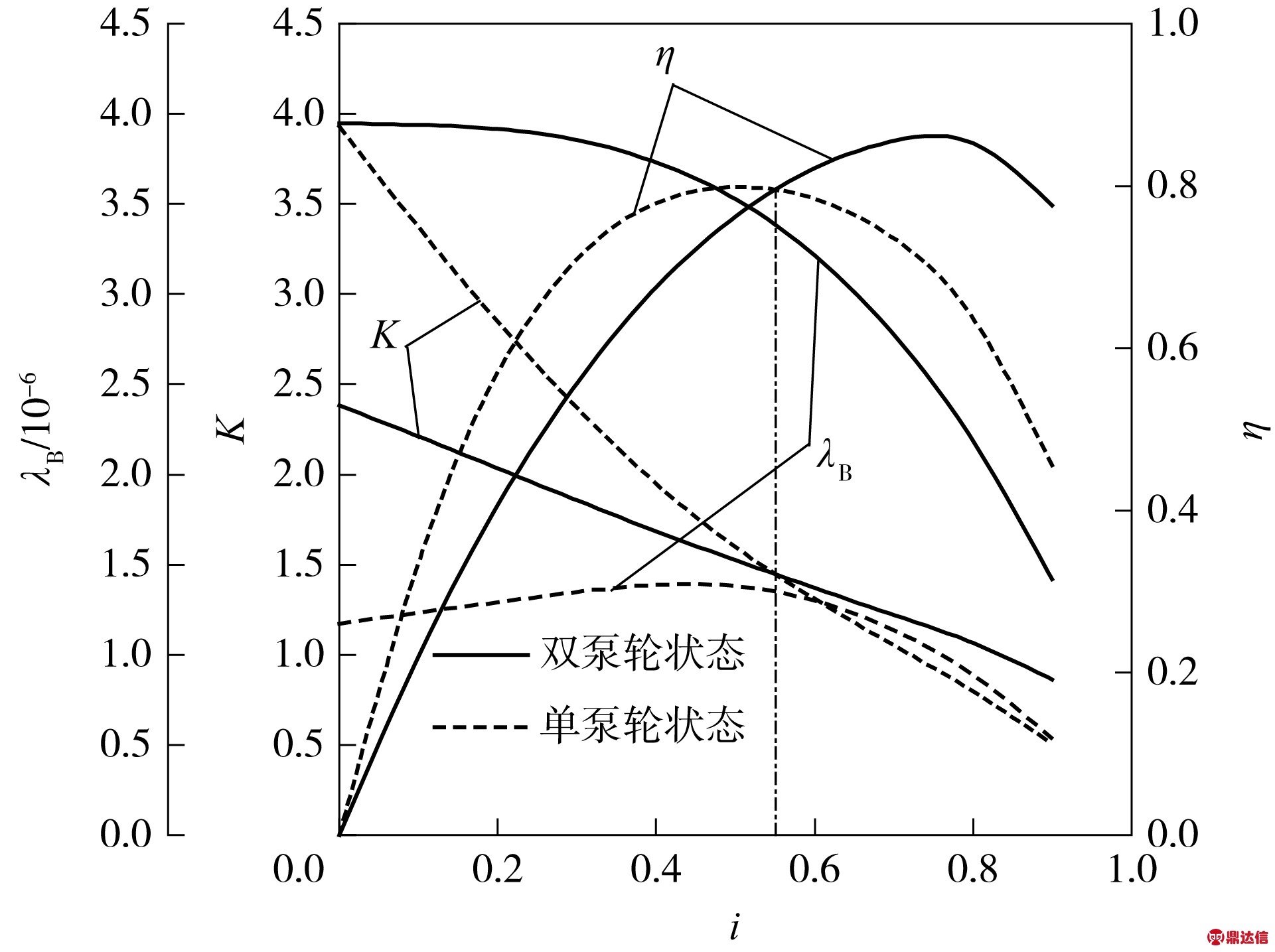
图14 单泵轮状态与双泵轮状态原始特性对比
Fig.14 Comparison of original characteristics between single working impeller state and two working impellers state
3.3 滑差状态特性分析
滑差状态是处于双泵轮状态和单泵轮状态之间的一种状态.此状态下滑差离合器部分接合,主、辅泵轮以不同转速旋转,通过主、从动摩擦片间液体的粘性传递动力.不同的离合器滑差率和转速比下变矩器的特性不同,图15为拟合出各叶轮转矩与转速比和离合器滑差率之间关系的三维曲面图.从图中可直观地看出,离合器滑差率一定时,涡轮转矩和导轮转矩随转速比的变化规律与普通向心涡轮液力变矩器的相同,主泵轮转矩随转速比的增加先增大后减小,辅助泵轮转矩随转速比的增加而减小;转速比一定时,涡轮转矩和导轮转矩随着离合器滑差率的增加而减小,主泵轮转矩随着离合器滑差率的增加变化不明显,辅助泵轮转矩随着离合器滑差率的增加而减小.根据得到的转矩特性可求得双泵轮滑差特性下的原始特性,如图16所示.
分别将离合器滑差率s=0,0.1,0.2,0.3的平面与图16所示的曲面求交线,可得到图17所示不同离合器滑差率下的双泵轮液力变矩器的原始特性.由图可知,随着离合器滑差率增大,低转速比时变矩比和效率升高而在高转速比时降低,整个转速比范围内泵轮转矩系数一直在降低.通过滑差特性分析可知,双泵轮状态即为滑差状态在离合器滑差率 s=0时的特例.通过图15可以发现,随着离合器滑差率的增加,辅助泵轮转矩值减小并出现负值现象,但在牵引工况下变矩器不会发生这种现象,而当离合器滑差率增加到临界空转离合器滑差率时,则辅助泵轮进入空转状态不再传递功率,此时为单泵轮状态.可见,滑差状态为双泵轮状态与单泵轮状态之间的某种状态.
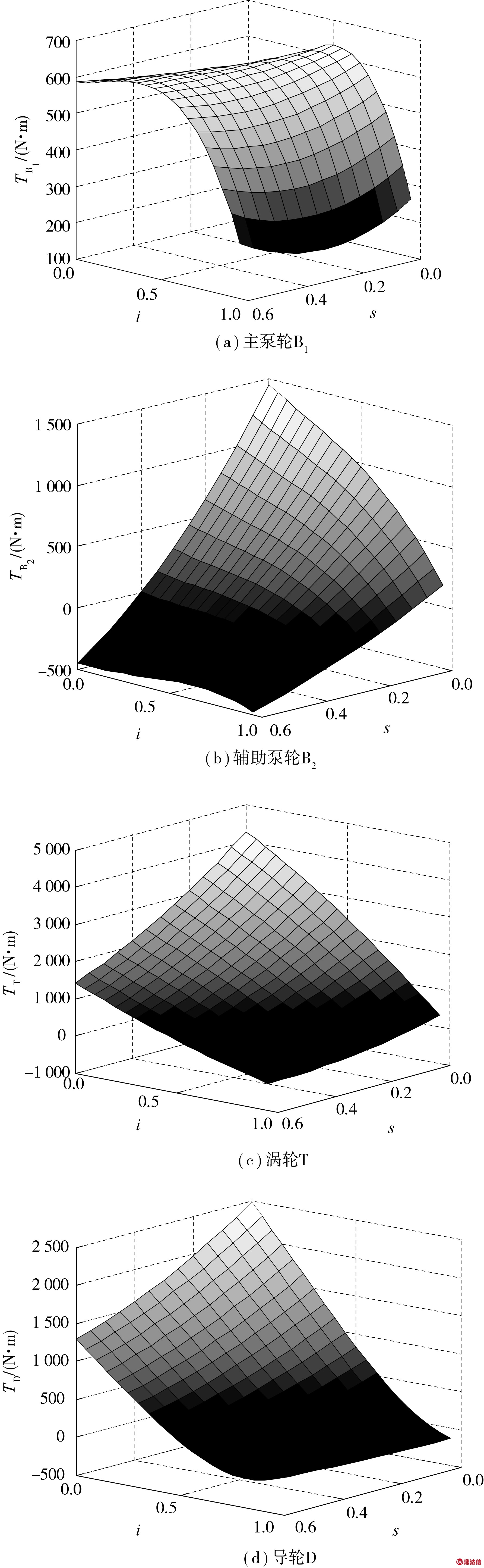
图15 叶轮转矩曲面拟合
Fig.15 Curved surface fitting of impeller torque

图16 双泵轮液力变矩器原始特性
Fig.16 Original characteristics of double-impeller torque converter
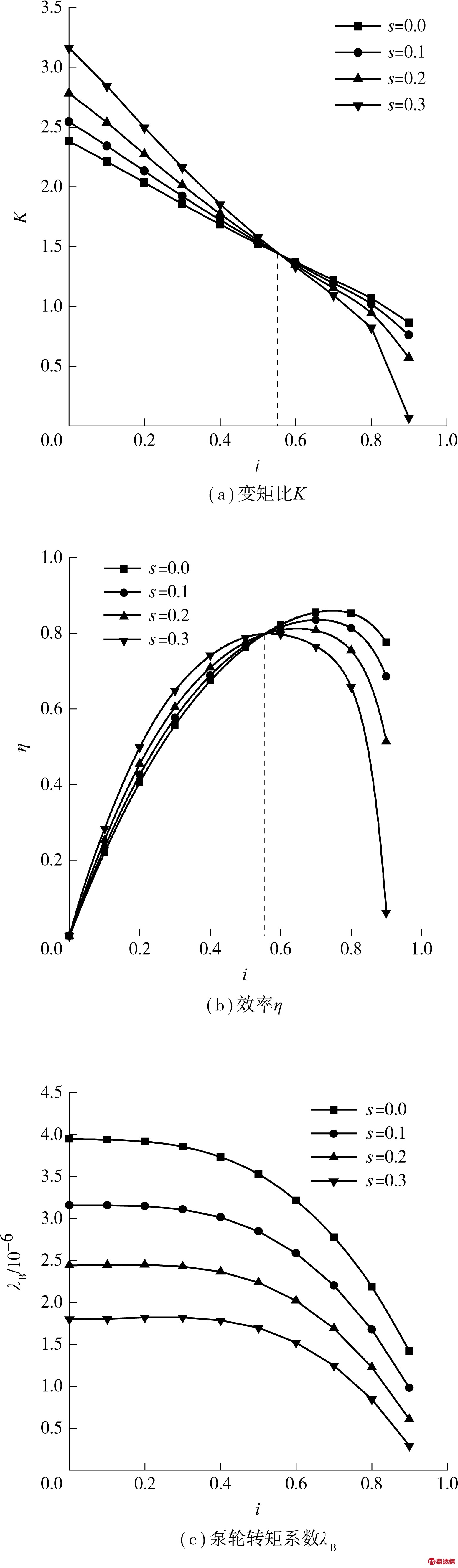
图17 不同离合器滑差率下双泵轮液力变矩器的原始特性
Fig.17 Original characteristics of double-impeller torque converter at different clutch slip rates
分析双泵轮变矩器各状态原始特性可知,泵轮转矩系数(能容)随着离合器滑差率和转速比的改变而变化,故通过滑差控制可实现对双泵轮液力变矩器能容的连续可控性.
4 结论
文中以现有高性能三元件向心涡轮液力变矩器为参考样机,采用相似设计法设计循环圆有效直径为425 mm的液力变矩器作为基准型,对基准型泵轮进行合理分割得到双泵轮液力变矩器循环圆和叶片.设计了多片湿式滑差离合器结构,给出滑差离合器和所设计摩擦片的主要技术参数.运用CFD技术方法分别对双泵轮状态、单泵轮状态和滑差状态下的双泵轮液力变矩器进行数值模拟计算,分别得到双泵轮状态、单泵轮状态和滑差状态下各叶轮转矩特性和原始特性.通过分析所设计的双泵轮液力变矩器在三种不同状态下的性能,可以发现,双泵轮液力变矩器的能容特性随着离合器滑差率和转速比的变化而变化,通过滑差控制能够实现对双泵轮液力变矩器能容的连续可控性,可应用于装载机发动机与变矩器的变能容匹配.