摘要:为预测重载越野车辆传动系统中密封系统的流固耦合特征,综合考虑密封环在微小约束空间内的受力状态以及密封间隙流场中的流动特点,建立了密封环双向流固耦合数值模型并提出了求解策略。采用多物理场代码耦合工具MpCCI联合FLUENT与Abaqus软件对旋转密封系统进行双向流固耦合数值计算,获得了旋转密封间隙流场中油液的流动状态。分析了密封环变形对密封系统泄漏量和密封环摩擦转矩的作用特征,通过双向流固耦合的动态模拟考察了传动系统工况对密封环性能的影响。利用车辆传动系统密封环综合性能试验台进行了密封性能的试验测试,对比发现计算值和试验值的变化规律具有一致性,验证了密封流固耦合数值模型及其计算结果的正确性。
关键词:传动系统;密封环;流固耦合;密封试验
0 引言
在车辆工程领域,涨圈型密封环(下文简称“密封环”)主要应用在车辆先进传动系统中,包括汽车自动变速器、双离合变速器、无级变速器等变速机构[1-3]。在重载越野车辆中,密封环主要布置在综合传动系统中。密封环作为传动系统的核心基础零件,为保证车辆传动系统正常运行发挥重要作用。
在微小约束空间内,密封环在力负荷作用下发生变形并且与轴槽侧面接触产生摩擦,由此会对密封间隙流场的流动状态产生影响,导致施加在密封环上的油液压力发生相应变化。可见,密封结构与密封流体之间存在显著的耦合特征[4-6]。如何考虑密封间隙流场流动状态与密封环力负荷、变形之间的耦合关联及其交叉影响特性,是密封流固耦合研究中需要考虑的关键问题。
流固耦合分析是揭示密封机理和研究密封性能的一种重要且可靠的手段,国内外学者通过理论分析[7-10]、仿真建模[11-14]和试验研究[15-16]的方式进行了相关研究。LIAO等[17]充分考虑了密封结构、密封间隙流体域以及它们之间的耦合关系,建立了核主泵用流体静压性机械密封流固耦合分析理论模型,对机械密封变形、间隙流场进行了分析,得到了密封泄漏随核主泵中压差的变化规律。孙丹等[18]提出了一种基于ALE(arbitrary Lagrange-Euler)流固耦合方式的刷式密封的求解模型,研究了压力和密封结构对密封接触变形和接触应力的影响。MIYAKE等[19]建立了密封流固耦合模型并进行试验,研究了密封间隙流动导致的轴系振动的问题。由国内外研究现状可知,对于密封流固耦合问题,研究方法较为多样,但对复合材料密封环的流固耦合研究较少。密封环的受力变形及其密封间隙流动对密封性能影响显著,如何快速有效地获取车辆传动系统密封环的耦合特征及其影响机制,是密封设计过程中需要解决的问题。
本文以重载越野车辆大功率传动系统的密封环为研究对象,结合密封系统结构特点和服役条件,提出采用多物理场代码耦合工具MpCCI联合FLUENT与Abaqus软件对密封系统进行双向流固耦合分析,考察油液压力、旋转轴转速、油液温度等条件对密封性能的影响。
1 流固耦合模型及其耦合方法
重载越野车辆传动系统中的密封环装配在旋转轴凹槽中,密封原理如图1所示。在油压p0作用下,密封环一侧端面AB与旋转轴凹槽一侧紧密贴合并相对转动,构成主要密封面。在油压和自身弹力作用下,密封环沿径向胀开,在密封面AD形成辅助密封面。密封环工作过程中在油压作用下发生变形,密封环变形会反作用于密封间隙内的油液,从而影响油液的流动。仅对密封内油液或密封系统的结构进行计算,显然与实际工况不符,会造成结果失真。密封结构场与密封间隙流场存在耦合,在计算中会形成相关数据的交换,数据交互的位置在密封环与密封间隙流场的重合面(DC面与CB面)上。
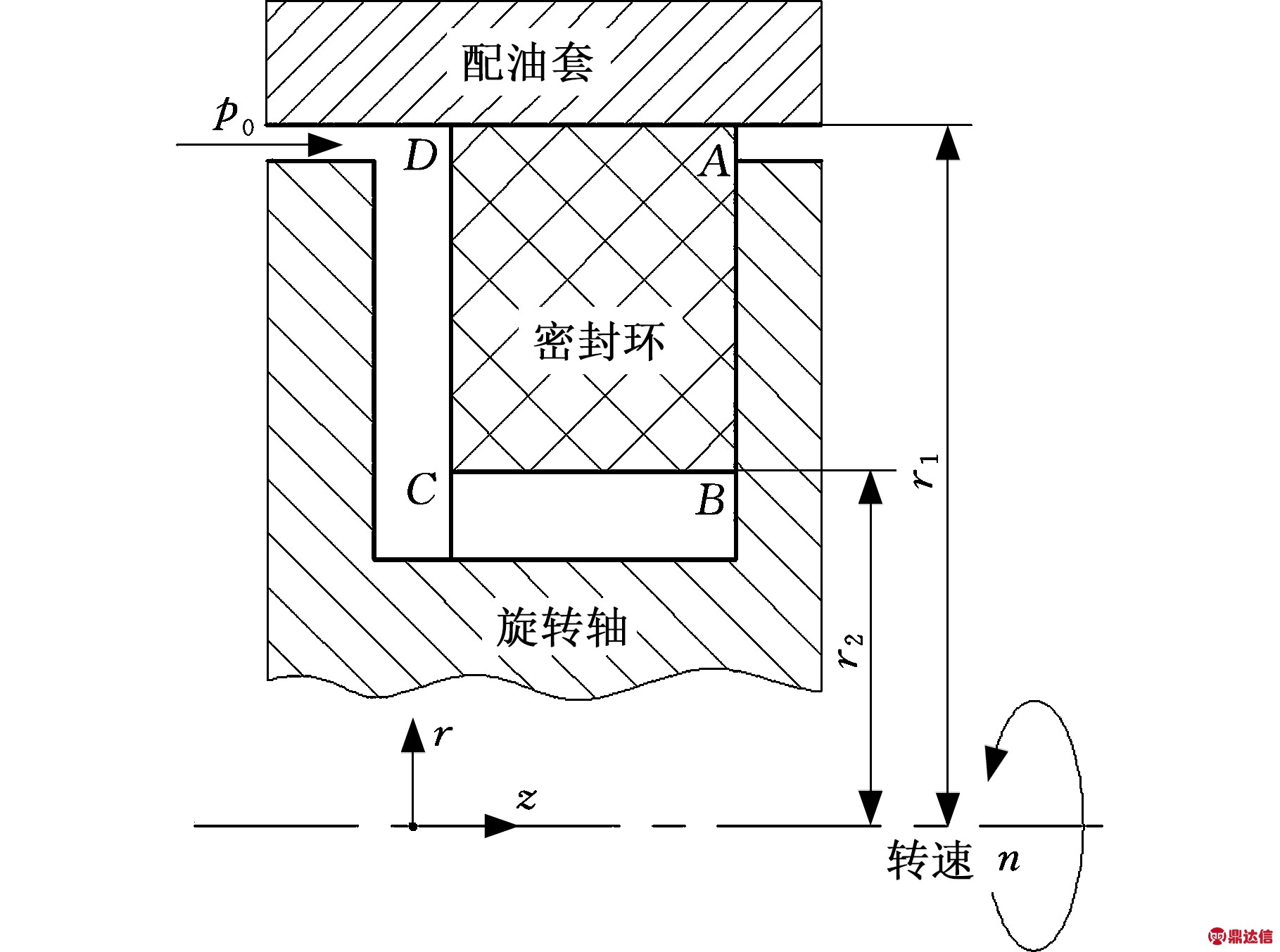
图1 密封原理图
Fig.1 Sealing schematic diagram
利用三维建模软件CATIA建立旋转密封间隙流场流体计算域的模型。在工作过程中,间隙流场中油液主要从密封环切口中泄漏,建立的密封流场计算域模型如图2所示,工作时密封环切口间隙为2 mm。为提高计算精度,对流体域模型进行六面体网格单元的划分,经过网格无关性验证,划分为六面体单元216 023个,单元节点268 564个。密封间隙流体域如图3所示,流体域与旋转轴圆周面重合的旋转壁面记为w1,与配油套内圆面重合的壁面记为w2,流体域与密封环重合的边界面即耦合面记为wcp,密封流场与结构场的数据交互就是通过耦合面上的数据交换来实现的。
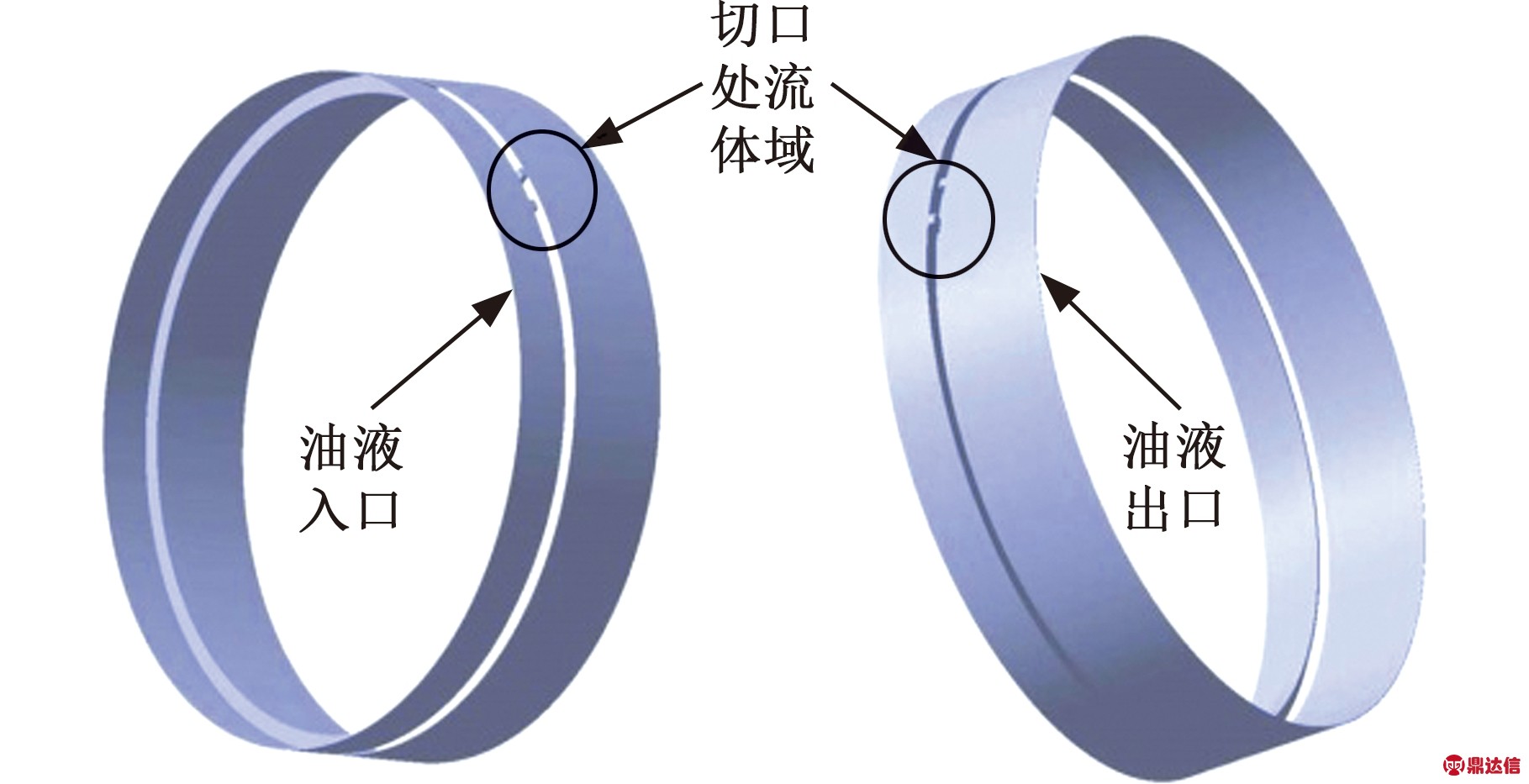
图2 密封间隙流场计算域模型
Fig.2 Calculation domain model of sealing gap flow field

图3 密封流体域网格边界
Fig.3 Sealing fluid domain boundary
将密封环和旋转轴的三维实体模型进行装配,为保证流固耦合计算数据的有效交互,需要维持密封系统结构场与流场的相对位置不变。对密封环和旋转轴的三维模型离散并进行网格单元的划分,其中密封环的部分网格如图4所示,密封环的单元数为58 579,节点数为69 842;旋转轴的单元数为9212,节点数为10 687。

图4 密封环离散单元
Fig.4 Discrete elements of sealing ring
在密封流固耦合交界面处,固体与流体的应力、位移相等[20],即在密封流固耦合面处应力和位移满足下述方程:
df=ds
τfnf=τsns
式中,d为位移;τ为应力;n为应力张量的法向量;下标f表示流体,下标s表示固体。
密封环在油压的作用下,与旋转轴凹槽侧面紧密贴合并相对转动,在密封面发生摩擦接触,对于此类型非线性接触仿真计算,选择能够高效求解包括接触在内的非线性问题的有限元软件Abaqus/Explicit作为密封结构计算的工具。在力负荷作用下密封环发生变形,会造成密封间隙流场的形状改变,进而影响通流性。但是在流场计算中,密封变形的位移等参数信息不易直接提取。因为计算过程中密封边界会瞬态变化,所以在流场计算中选择FLUENT软件来处理密封边界变动的问题。FLUENT的算法是基于完全非结构化网格的有限体积法,Abaqus的算法基于有限单元法,所以在流固耦合计算中无法实现数据的直接交互传递。
本文采用FLUENT+Abaqus+MpCCI进行密封环流固耦合计算。通过FLUENT对旋转密封间隙流场进行计算,得到密封流固耦合面的油液压力,通过多物理场耦合代码工具MpCCI实现压力数据的传递,Abaqus获得油液压力数据后,作为边界条件进行密封结构场的计算,得到力负荷作用下的密封变形,再次通过MpCCI将密封面变形数据传递给FLUENT,然后FLUENT根据密封面变形数据修正密封间隙流场的流体域。引入旋转雷诺数判断旋转密封间隙流体的流动状态,即Reθ=ωr2/ν。其中,ω为流体旋转速度,r为旋转半径,ν为油液的运动黏度。经过测算,所研究流体的旋转雷诺数都小于20 000,即临界旋转雷诺数[21],所以认为密封间隙流场内油液的流动为层流。设置残差值为1×10-5,以此进行循环,时间步长为1×10-4 s,时间步为30 000步,每个时间步的最大迭代次数为30,在计算过程中忽略密封环浮动的影响。图5所示为密封系统流固耦合计算过程。
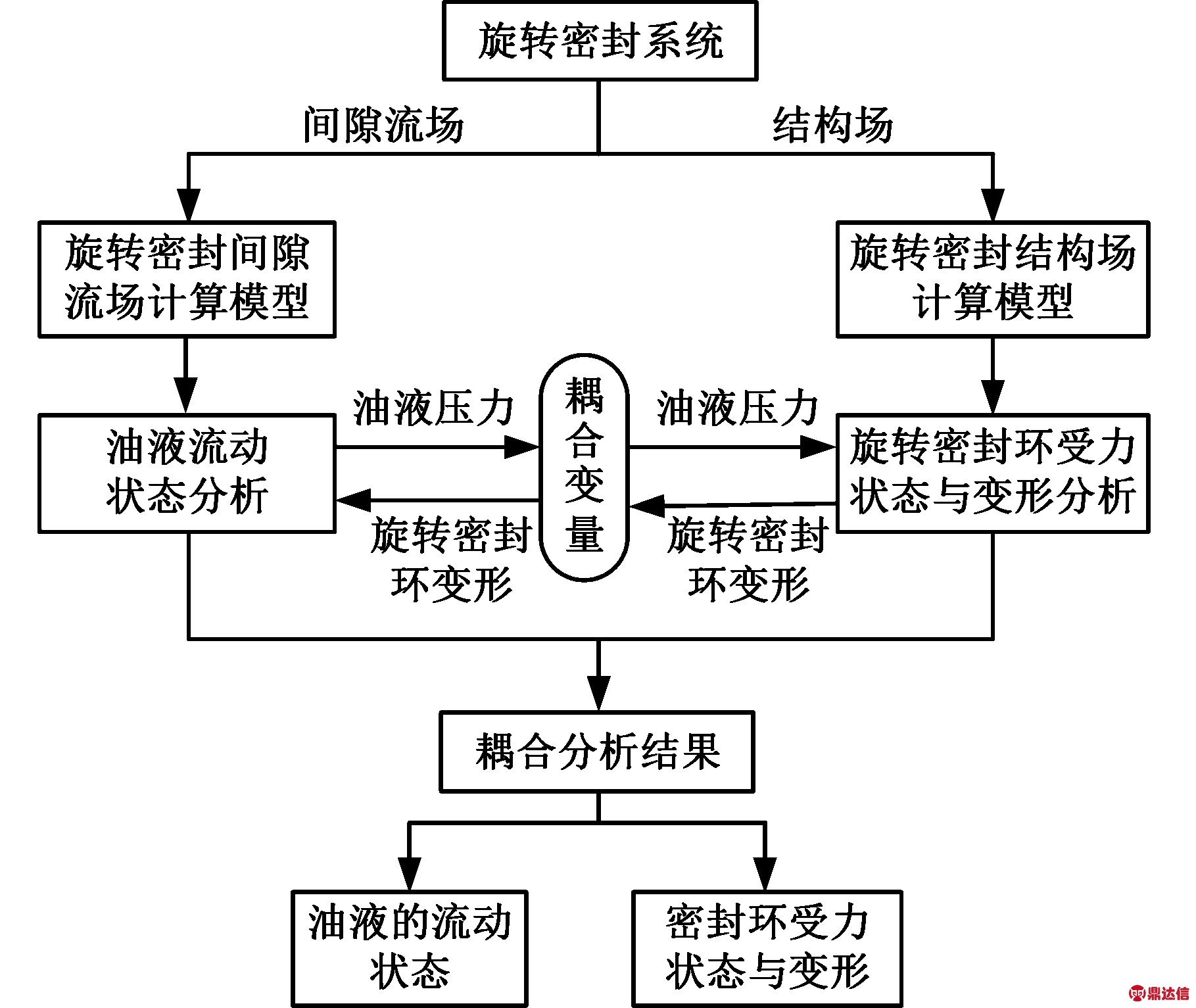
图5 密封流固耦合计算流程
Fig.5 Calculation process of sealing fluid-structure coupling
采用本文提出的方法对不同转速、压力和油温下的密封环主要性能参数进行计算,耦合计算收敛后,通过FLUENT后处理功能可以导出密封截面上的泄漏量等数据,在Abaqus后处理模块中选择接触工具,得到转矩等密封结构分析的相关结果。
2 结果与讨论
以外径125 mm密封环作为研究对象,密封环材料为PTFE(聚四氟乙烯)复合材料,旋转轴材料为38CrSi。入口边界条件为压力入口,进口压力1~3 MPa,旋转轴转速n为1000~6000 r/min。采用的润滑油为15W-40机油,40 ℃下的密度和黏度分别为844.5 kg/m3和103.6 mm2/s,100 ℃下的密度和黏度分别为814.5 kg/m3和15.65 mm2/s。耦合计算中,密封环和旋转轴结构与材料参数如表1所示,密封环由圣戈班公司加工。
表1 计算所用参数
Tab.1 Calculation parameters
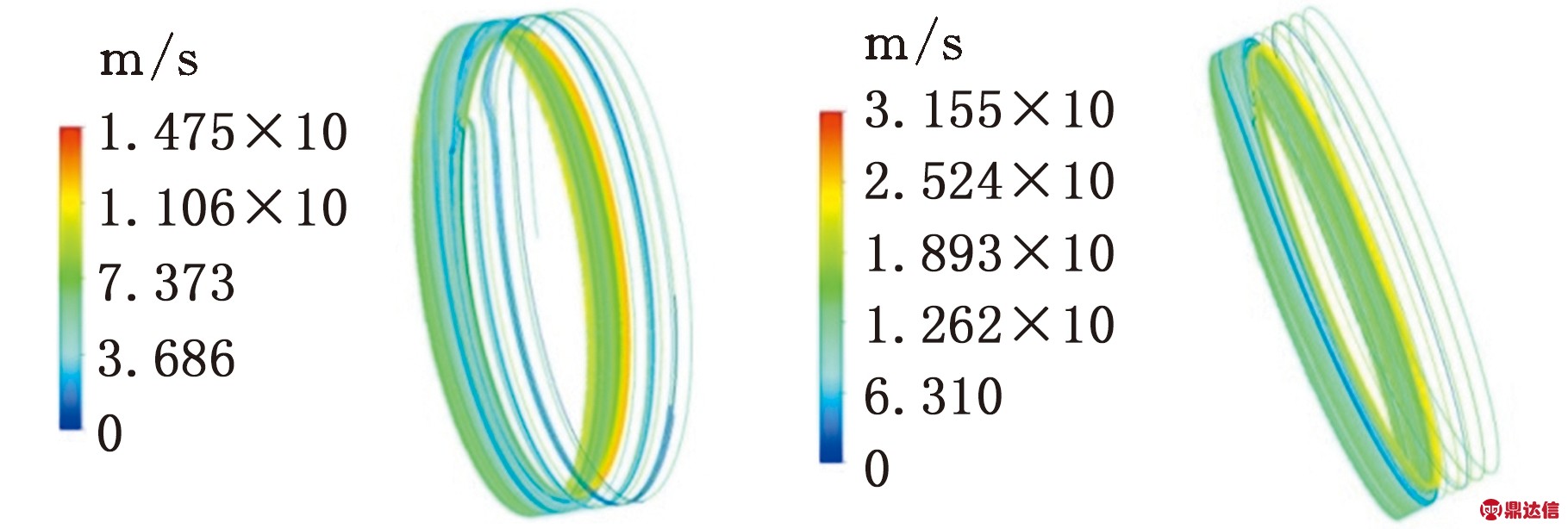
密封流固耦合计算中,参数传递发生在密封结构场和流场的耦合面上,随着计算过程多次往复交互传递,以便为下一个时间步密封流场和结构场的计算提供边界条件。采用瞬态计算,在计算过程中,首先通过FLUENT软件计算油压,将得到的压力作为边界条件通过MpCCI传递到Abaqus中进行结构体的计算。在后续仿真过程中,Abaqus将计算得到的位移传递给FLUENT进行网格更新。直到密封性能参数不随时间步变化或前后时间步长的密封参数值保持在预设的区间内,完成耦合计算过程。
由密封流固耦合计算得到不同工况下密封环的变形云图,见图6、图7。从图中可以看出,在不同的油液、转速和油温作用下,密封环的变形主要集中在与主密封面相对的端面(即DC面),由主密封面到非密封面变形逐渐增大。同时发现,密封环主密封面的外径变形较其他位置的变形大,这是因为配油套与旋转轴存在0.2 mm的缝隙,在缝隙位置密封环没有轴向约束,会在油压作用下存在较大的形变。对整个密封环来说,最大的变形区域在流固耦合面,随着压力和转速的提高,与压力p=1 MPa和转速n=1000 r/min工况相比,变形量增大近30%(图7),同等条件下,油温的影响不显著。尽管密封面的变形较小,但是密封间隙流场尺寸同样较小,所以密封面变形对间隙流场的流动特性会产生影响,有必要考虑密封流固耦合特性。
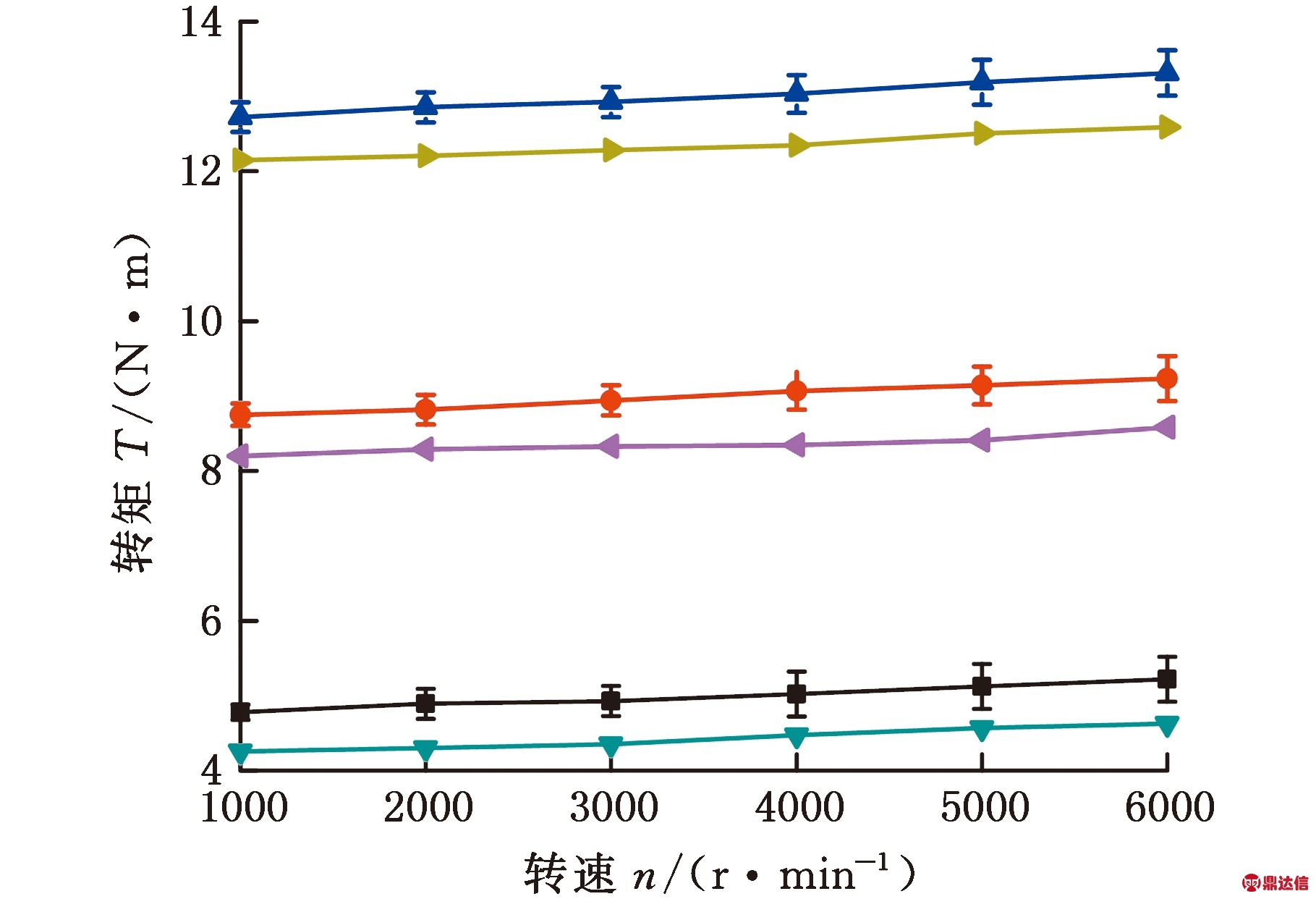
(a)40 ℃ (b)100 ℃
图6 密封环变形云图(p=1 MPa,n=1000 r/min)
Fig.6 Deformation cloud of sealing ring
(p=1 MPa,n=1000 r/min)
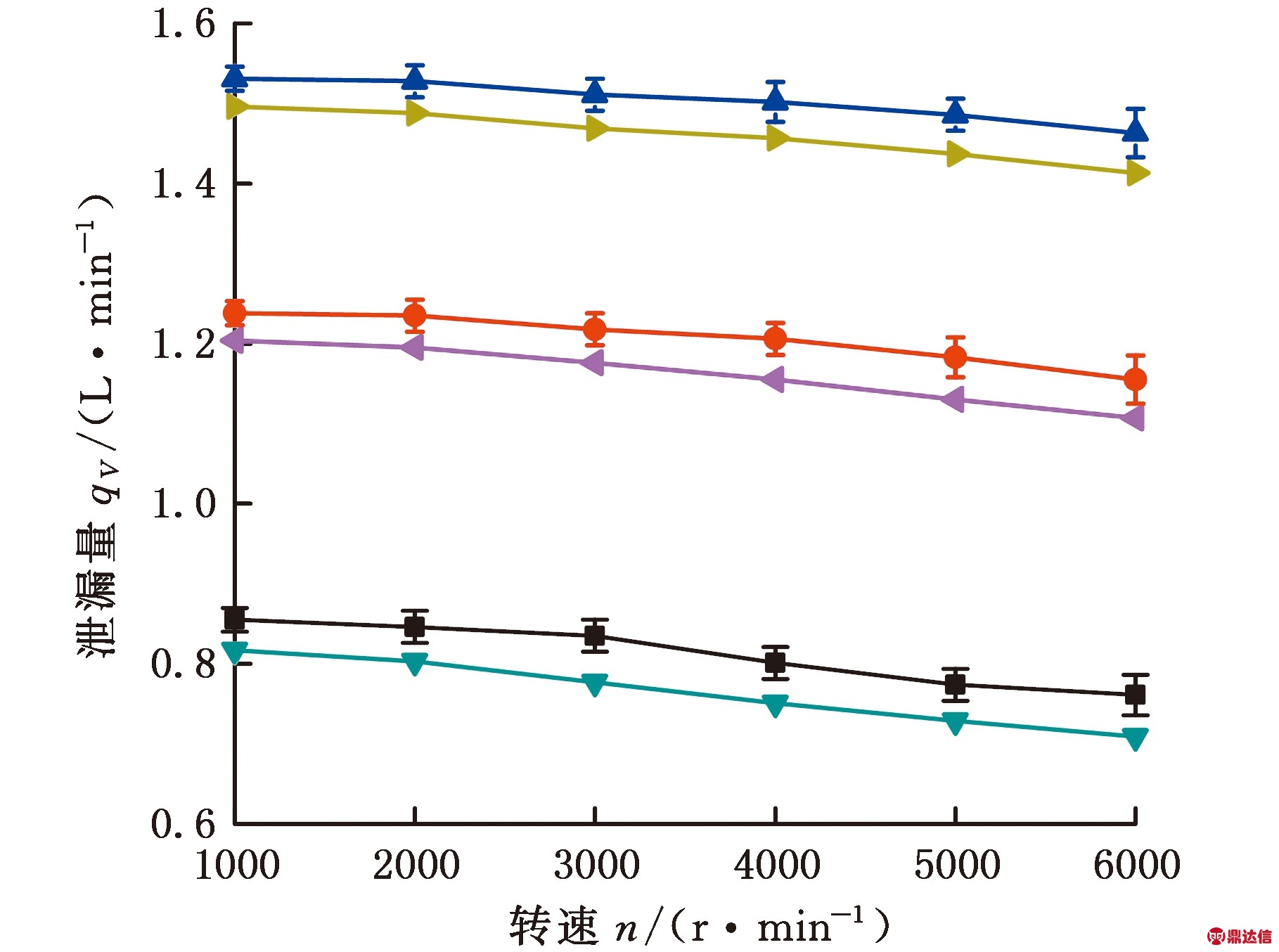
(a)40 ℃ (b)100 ℃
图7 密封环变形云图(p=3 MPa,n=4000 r/min)
Fig.7 Deformation cloud of sealing ring
(p=3 MPa,n=4000 r/min)
利用后处理软件CFD-Post对流固耦合计算后密封流场的结果进行处理,得到了不同压力和转速下的密封流场的流速流线图,见图8。由图8a和8b可知,在同样的转速下,随着压力的提高,密封间隙流场内油液有较为明显的轴向流动趋势,密封切口处流动效应增强,3 MPa时的泄漏量较1 MPa时增多。由图8c和图8d可知,旋转密封间隙流场内油液的流动明显随轴旋转,并且随着转速的增大,流场内的油液更加贴近旋转壁面(w1),转速由1000 r/min增至4000 r/min时,油液绕轴旋转现象愈加明显,由图可知,油液绕轴旋转现象的增强将导致油液沿轴向的流动困难,油液更多地集中在入口段,而较少从密封切口泄漏。
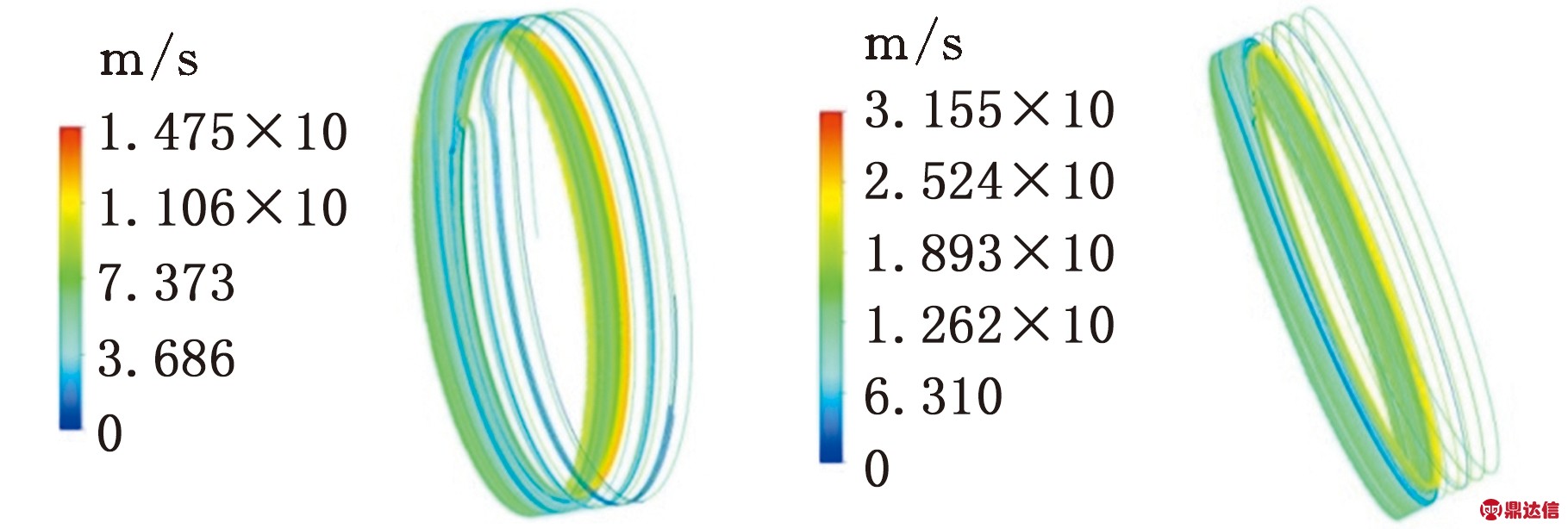
(a)p=1 MPa, (b)p=3 MPa,
n=2000 r/min n=2000 r/min
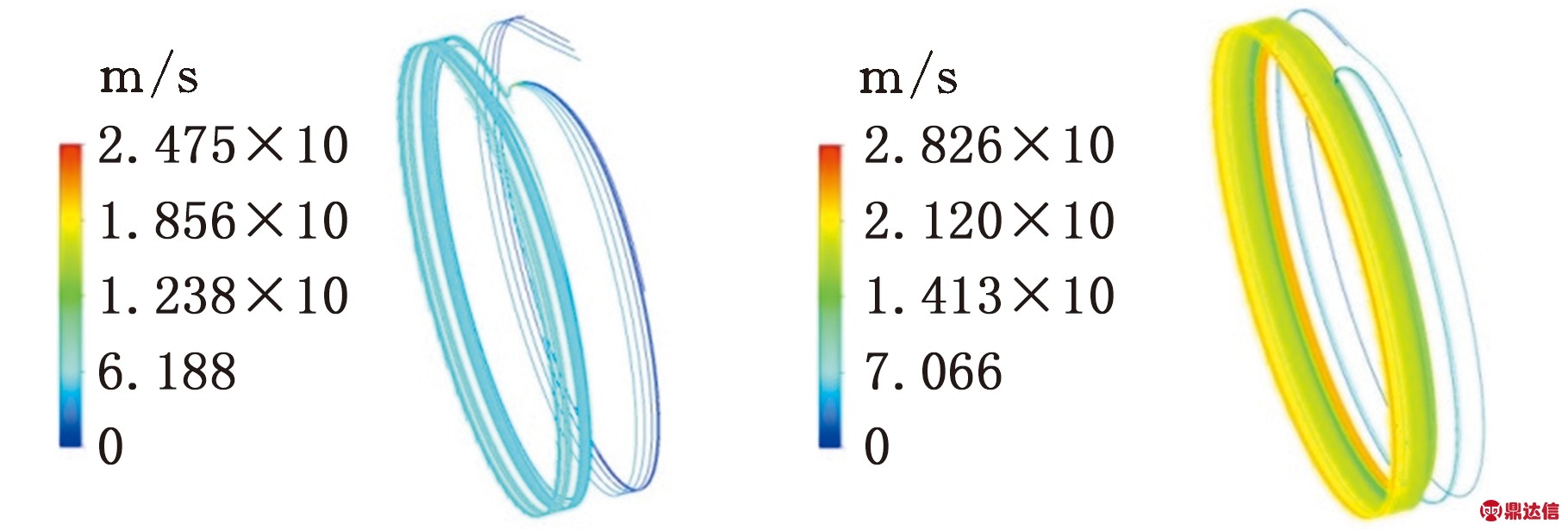
(c)n=1000 r/min, (d)n=4000 r/min,
p=2 MPa p=2 MPa
图8 密封流体流速流线图
Fig.8 Streamline diagram of sealing fluid velocity
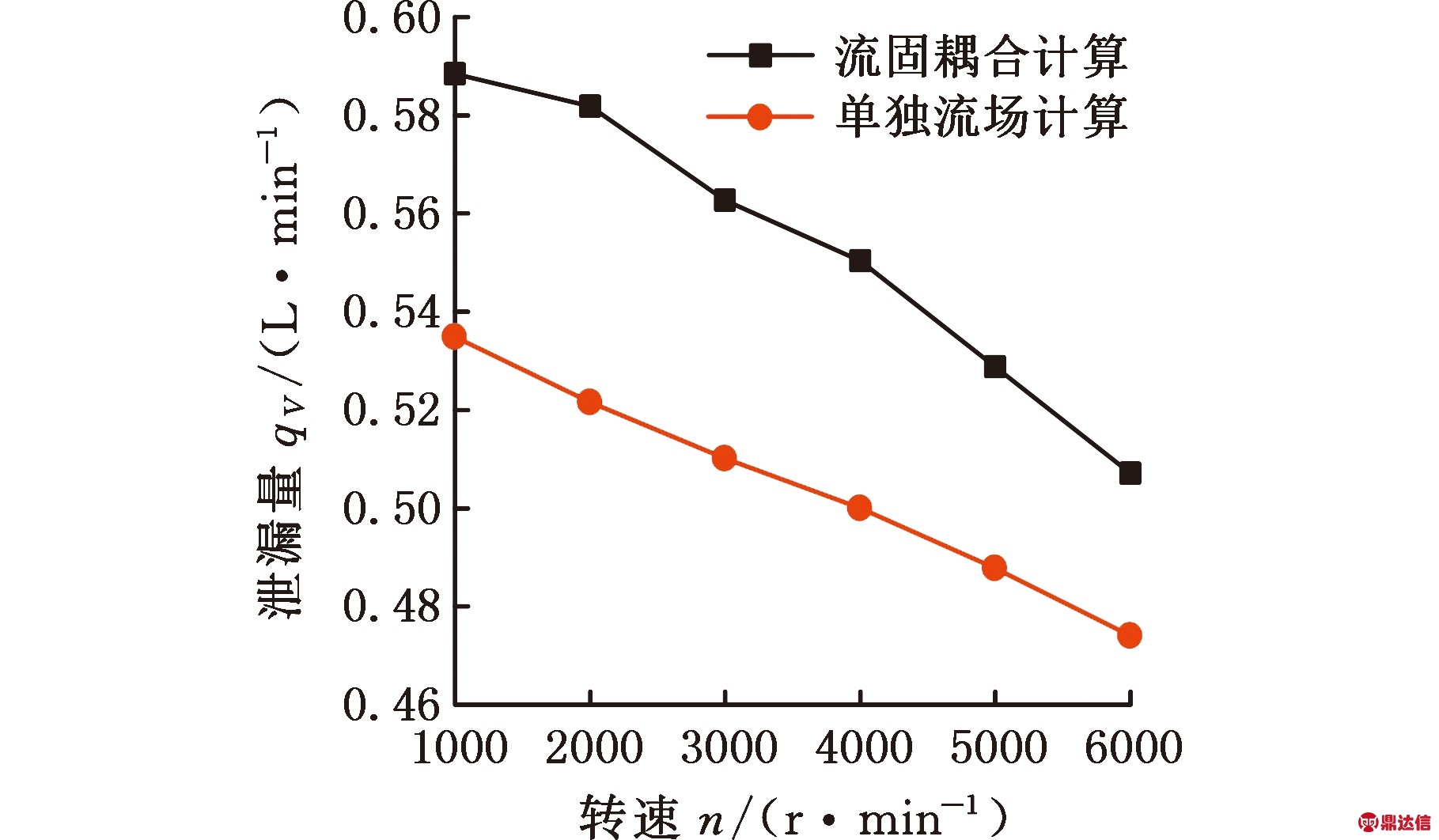
(a)40 ℃
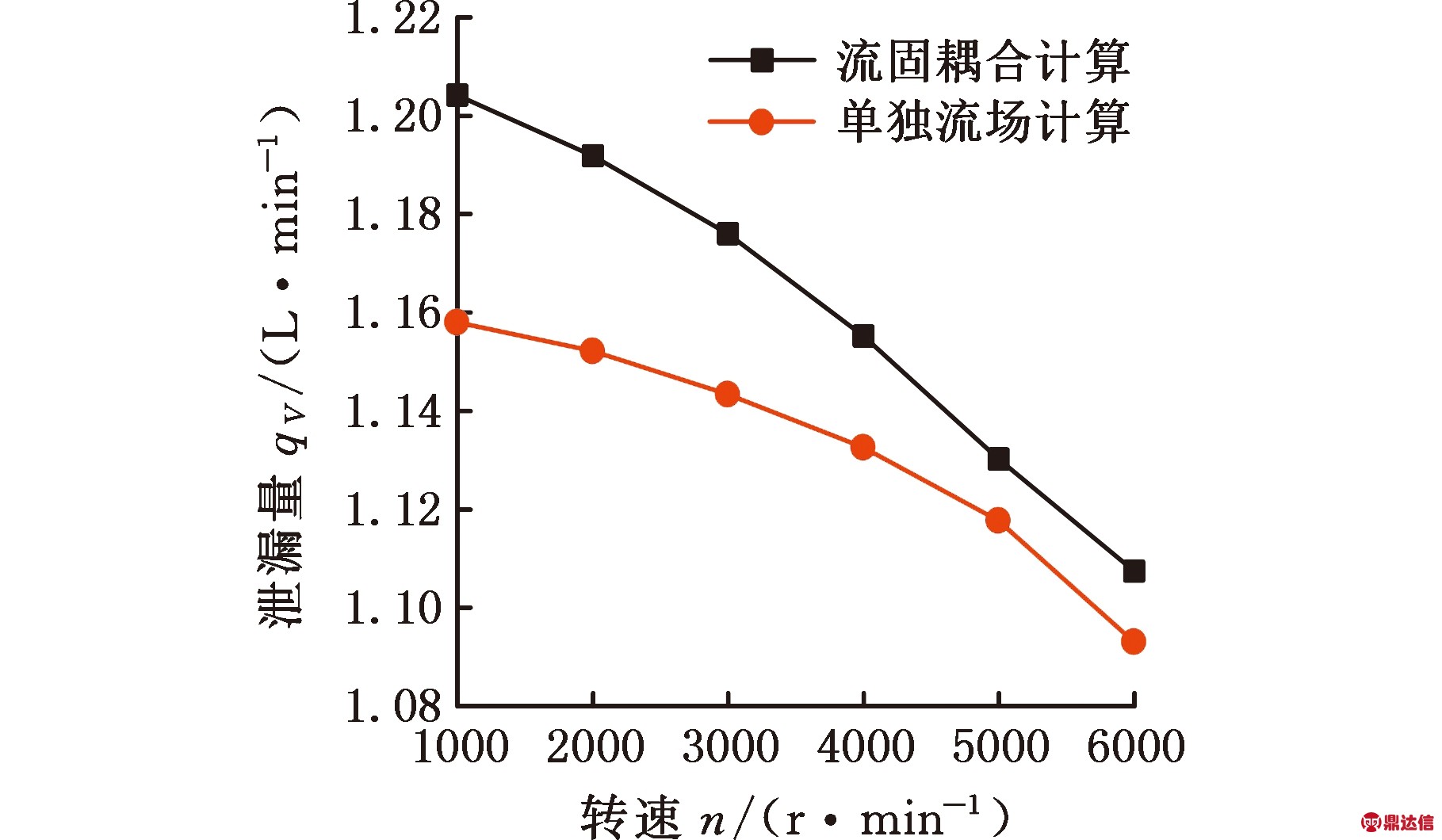
(b)100 ℃
图9 泄漏量随转速变化曲线图(p=2 MPa)
Fig.9 Leakage curves with speeds(p=2 MPa)
为进一步考察流固耦合计算对密封泄漏量的影响,观察流固耦合计算和未经流固耦合的流场计算(即单独流场计算)的结果,对比验证密封环变形后对密封间隙流场的影响。图9所示为入口油压为2 MPa时不同转速下的泄漏量,图10所示为旋转轴转速为3000 r/min时不同入口油压下的泄漏量。由图9可知,在相同的入口压力下,无论是流固耦合计算还是单独流场计算,泄漏量都随着转速的增大而减小。但是两种计算方法在不同的速度区间内的差值不同,在1000~3000 r/min范围内差异较大,在4000~6000 r/min范围内差异较小,由此可知,在高转速时油压引起的密封变形对泄漏量的影响减小。在压力作用下,油液出现压差流动,横向流动增强,与此同时,在高转速下,由于离心作用增强,油液绕轴旋转效应明显,油液更加贴紧旋转壁面,横向流动减弱,因此在同样的压力条件下,随着转速的增大泄漏量会相应减小。由图10可知,在旋转轴转速相同时,压力对泄漏量的影响显著,而且油温越高,油液黏度越小,油液的流动性越好,容易引起泄漏。流固耦合计算获得的泄漏量始终大于单独流场计算的泄漏量,油压作用下密封环变形,改变了密封间隙流场的通流特性,所以通过流固耦合计算获得的密封泄漏量结果更加合理。对比发现,压力引起的泄漏量变化大于转速引起的泄漏量变化。
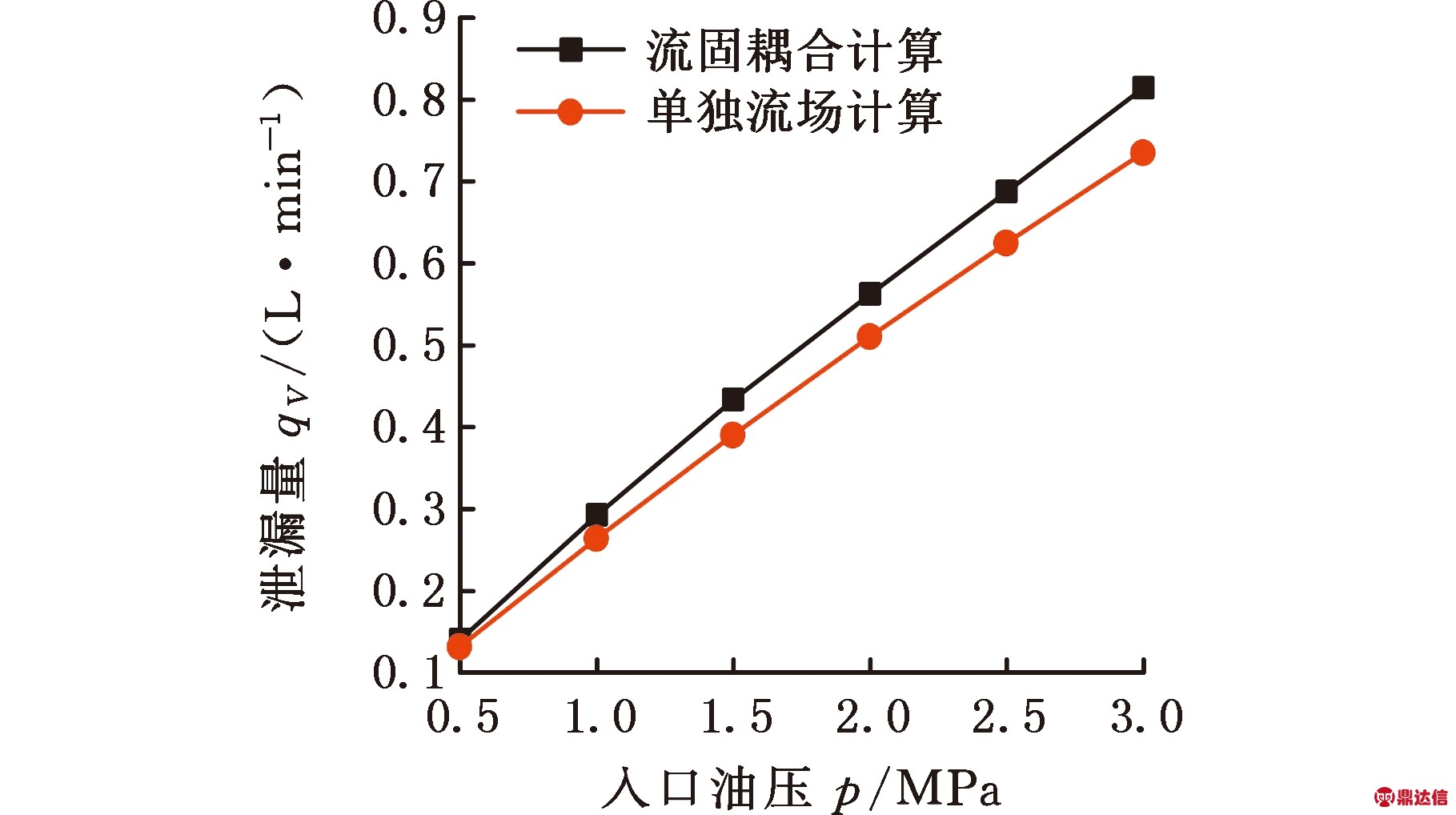
(a)40 ℃
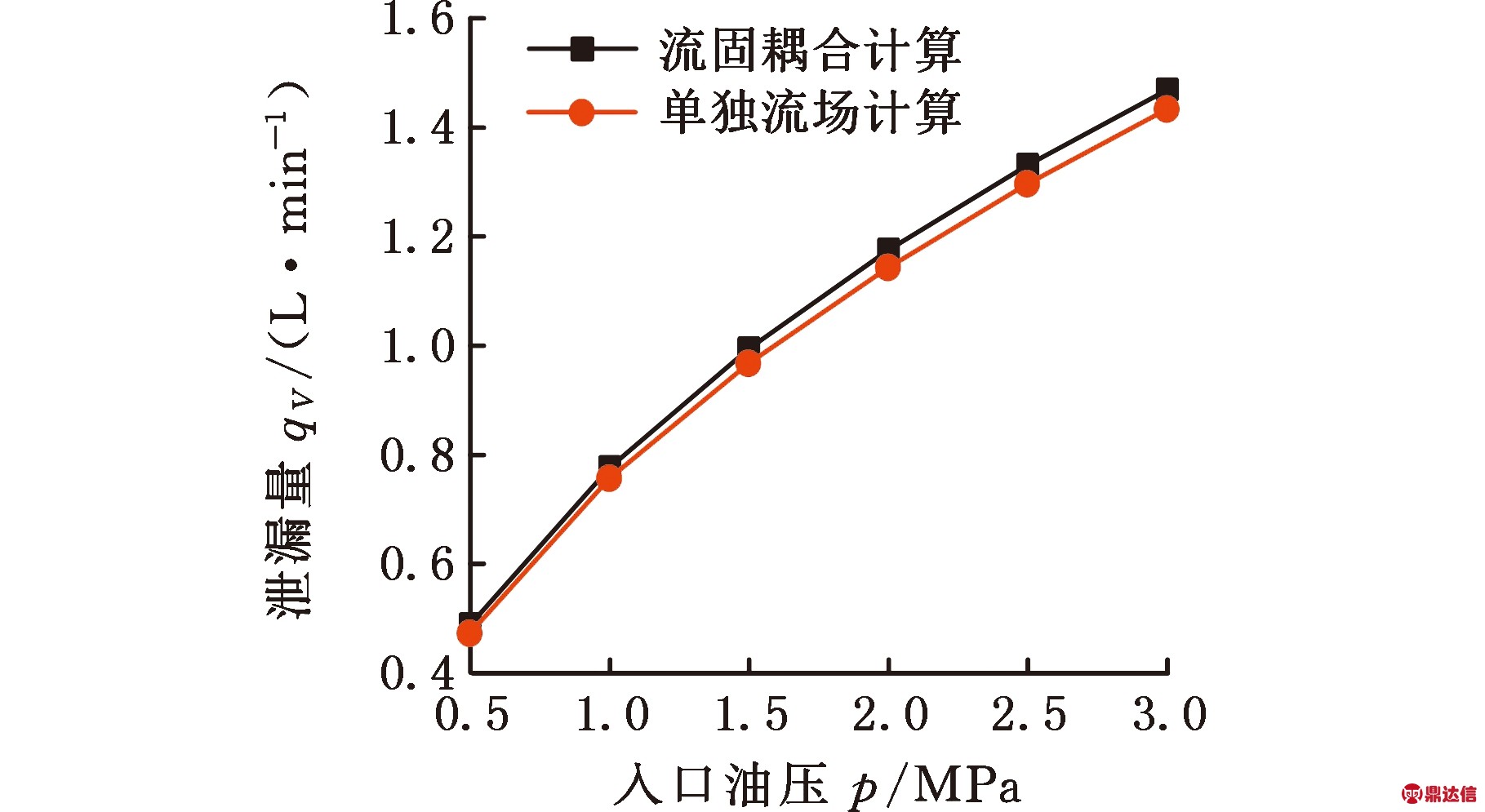
(b)100 ℃
图10 泄漏量随压力变化曲线图(n=3000 r/min)
Fig.10 Leakage curves with pressures(n=3000 r/min)
3 密封性能试验
利用自主研发的密封环性能试验台开展密封性能试验,对计算结果进行分析与验证。试验台主要由动力与机械系统、电气控制系统与数据采集系统、液压系统组成。图11a为试验台结构图,图11b为试验油腔结构图。密封环安装在旋转轴上。旋转轴贯穿于试验油腔,另一端与变频电动机相连。通过液压系统实现恒压供流。油腔加热带、油温传感器和温度控制器组成密封油腔的温度控制系统。通过上位机发送指令给温度控制器,配合油温传感信号,对油腔内油温进行调节,保证油温的控制误差在±5 ℃内。转矩转速传感器与旋转轴连为一体,发送脉冲信号给上位机,经过转换成为测量值。在试验前先测试空载转矩,进行密封转矩量值的标定。泄漏流量的测量采用高精度流量计。试验系统根据设定的温度进行油温加热,然后在给定的油压与转速下跑合。每个测试点保持稳定运行2 min后再测量。
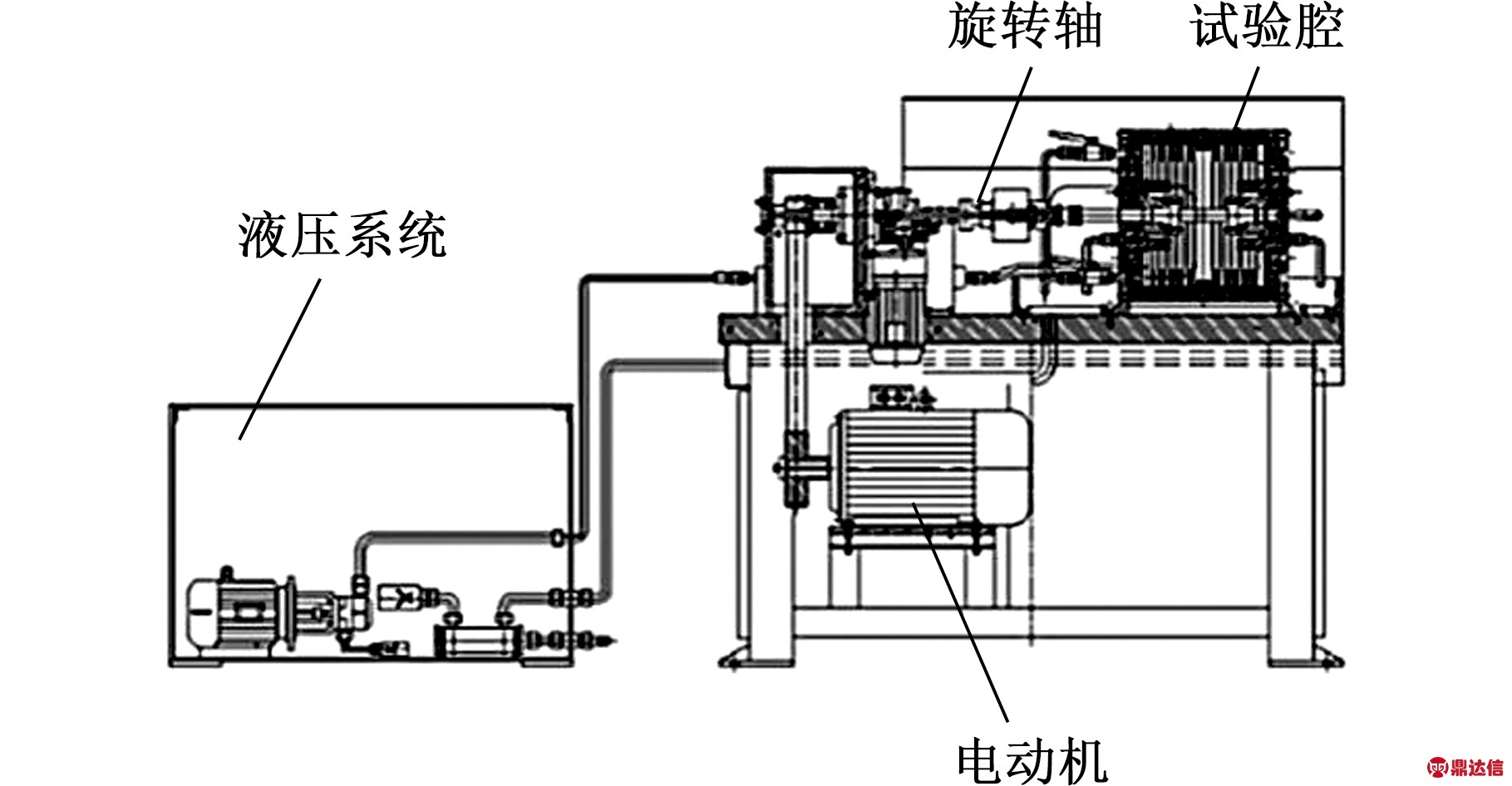
(a)试验台架
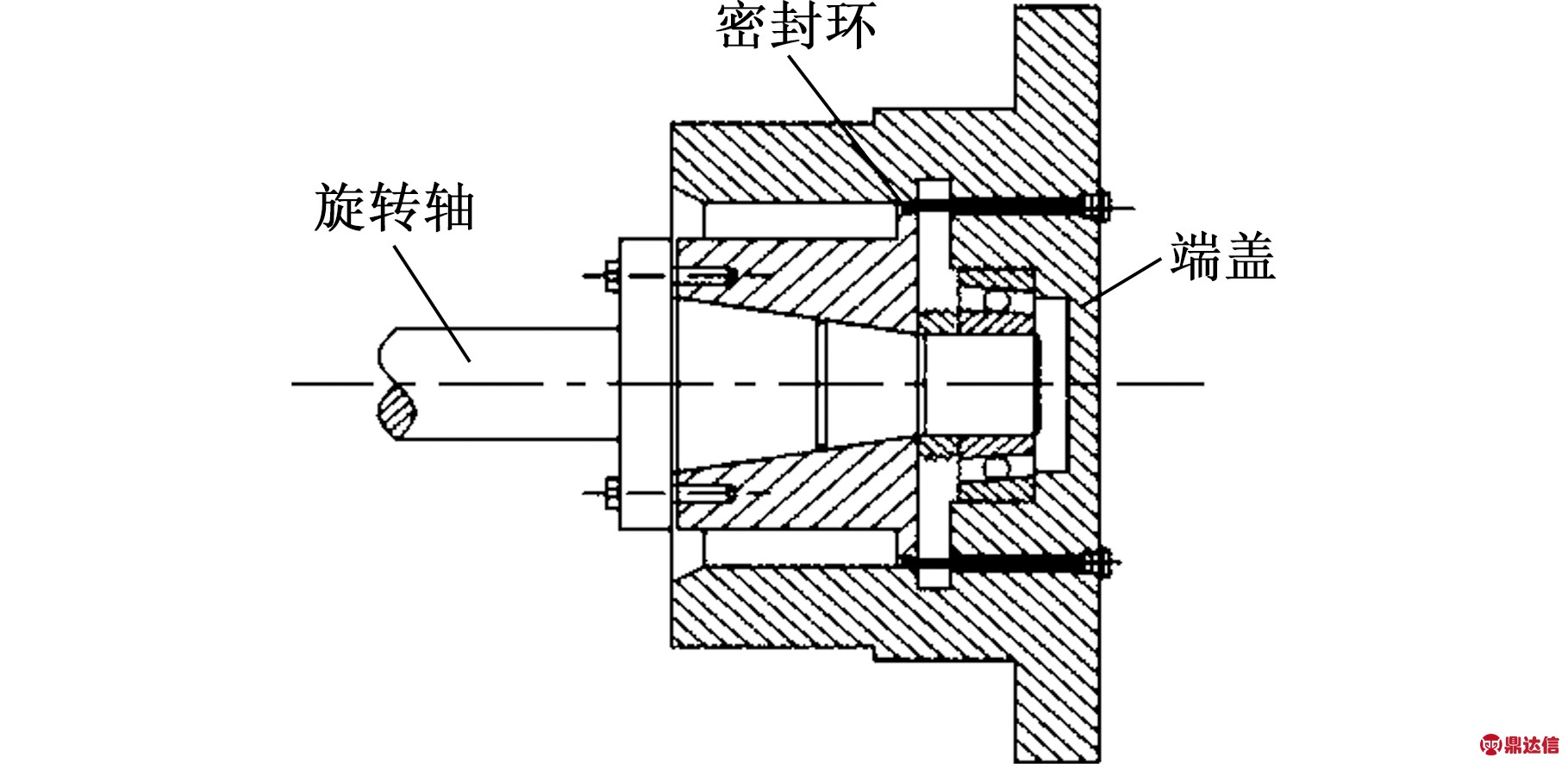
(b)密封环安装位置
图11 密封试验台结构图
Fig.11 Schematic of sealing test rig
在转速1000~6000 r/min、压力1~3 MPa下试验,设置油液试验温度为40 ℃和100 ℃,得到图12所示的泄漏量随旋转轴转速的变化曲线,试验中泄漏量共测量5次。由图可知,泄漏量随着入口压力的增大显著增加,随着旋转轴转速的增大而减小,但幅度不大。同时,随着油温的升高泄漏量明显增大。从试验数据和仿真结果对比来看,两者的变化规律趋于一致,但是试验值大于计算值,这是由于在计算时忽略了密封环的加工质量和装配精度,而实际使用的密封环密封面会存在一定的不平度误差,导致密封面处泄漏。
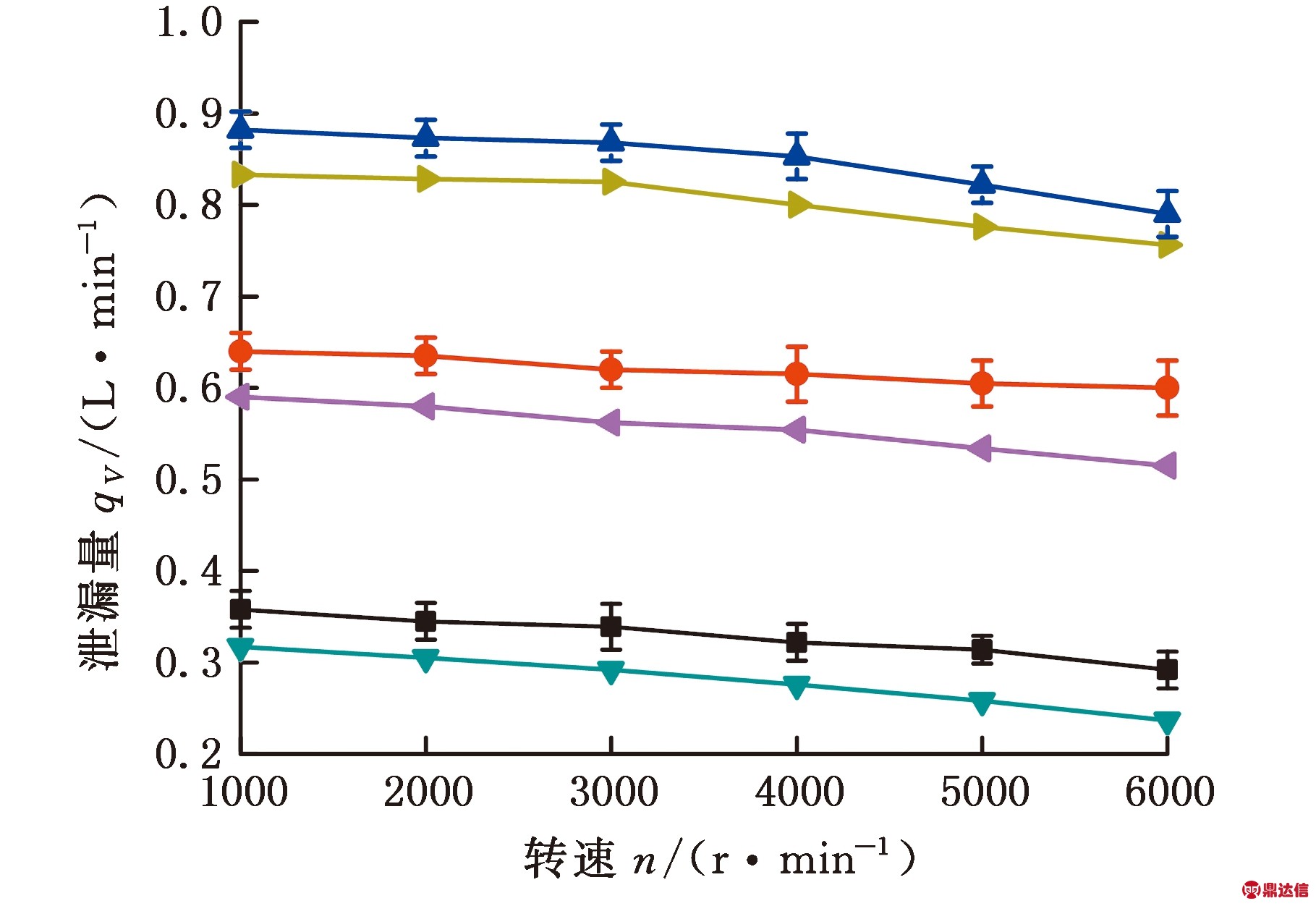
(a)40 ℃
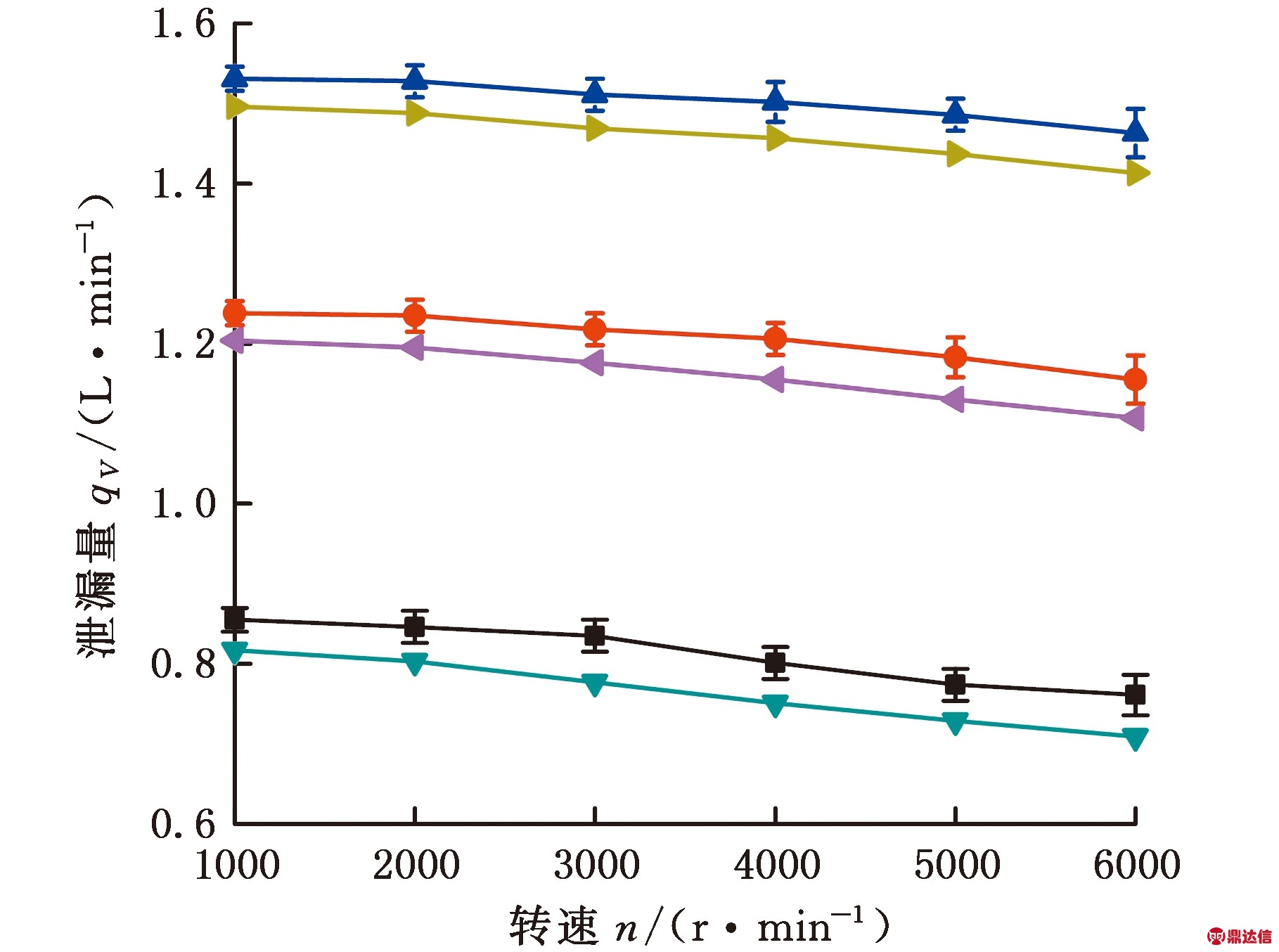
(b)100 ℃
图12 泄漏量试验与仿真曲线
Fig.12 Test and simulation curves of leakage
图13为油温在40 ℃和100 ℃,油压为1 MPa、2 MPa和3 MPa时,摩擦转矩随旋转轴转速的变化曲线。由图可知,摩擦转矩随入口压力和旋转轴转速的增大而增大。入口压力增大会引起主密封面所受接触力增大,使得密封副的摩擦转矩明显增大。转速提高导致密封流体的剪切力增大。油温升高时,油液黏度相应减小,其黏性剪切力减小,所以摩擦转矩变小。最终摩擦转矩随转速的增大而增大,试验值和计算值的趋势保持一致,两者的误差在12%以内。
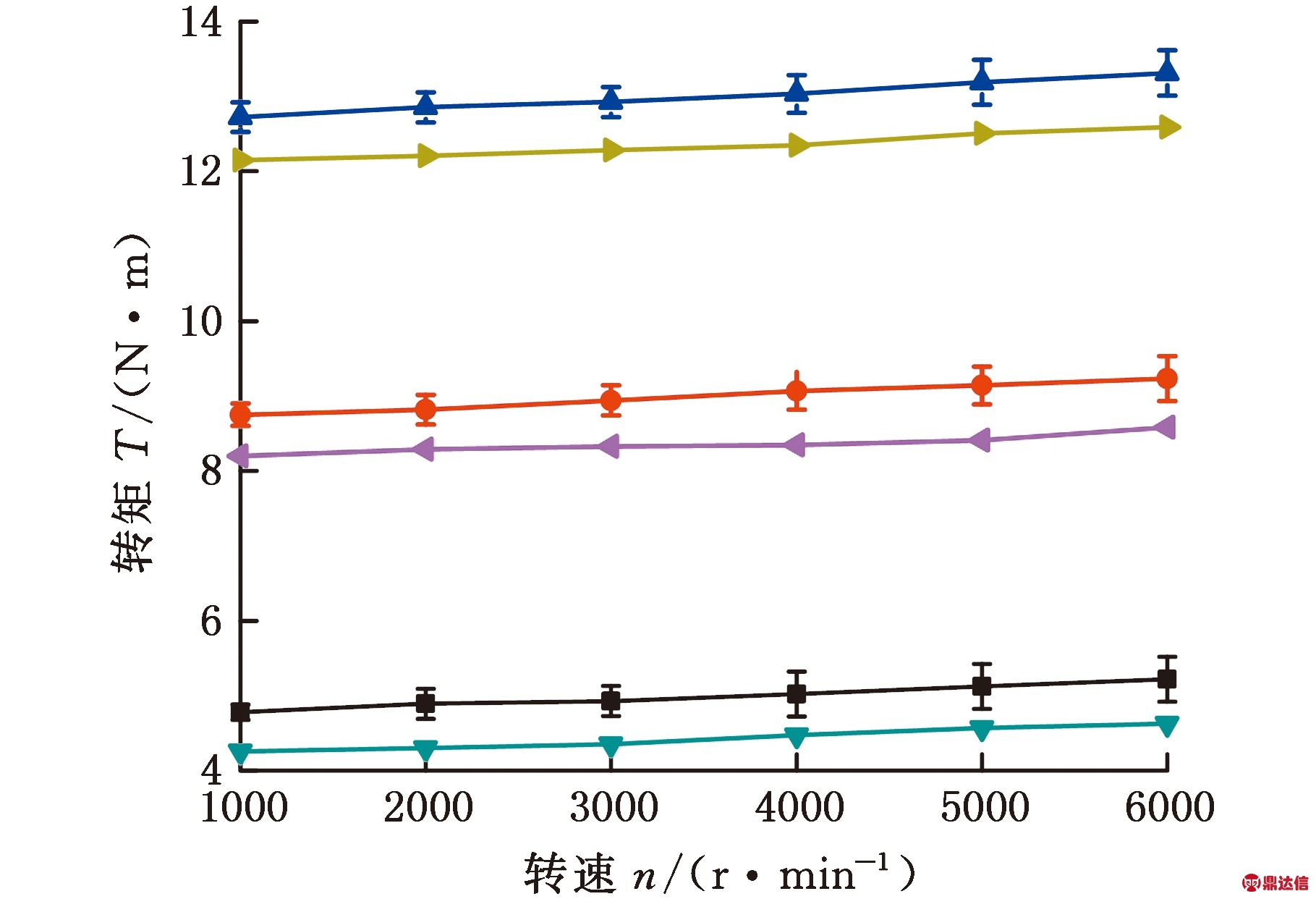
(a)40 ℃
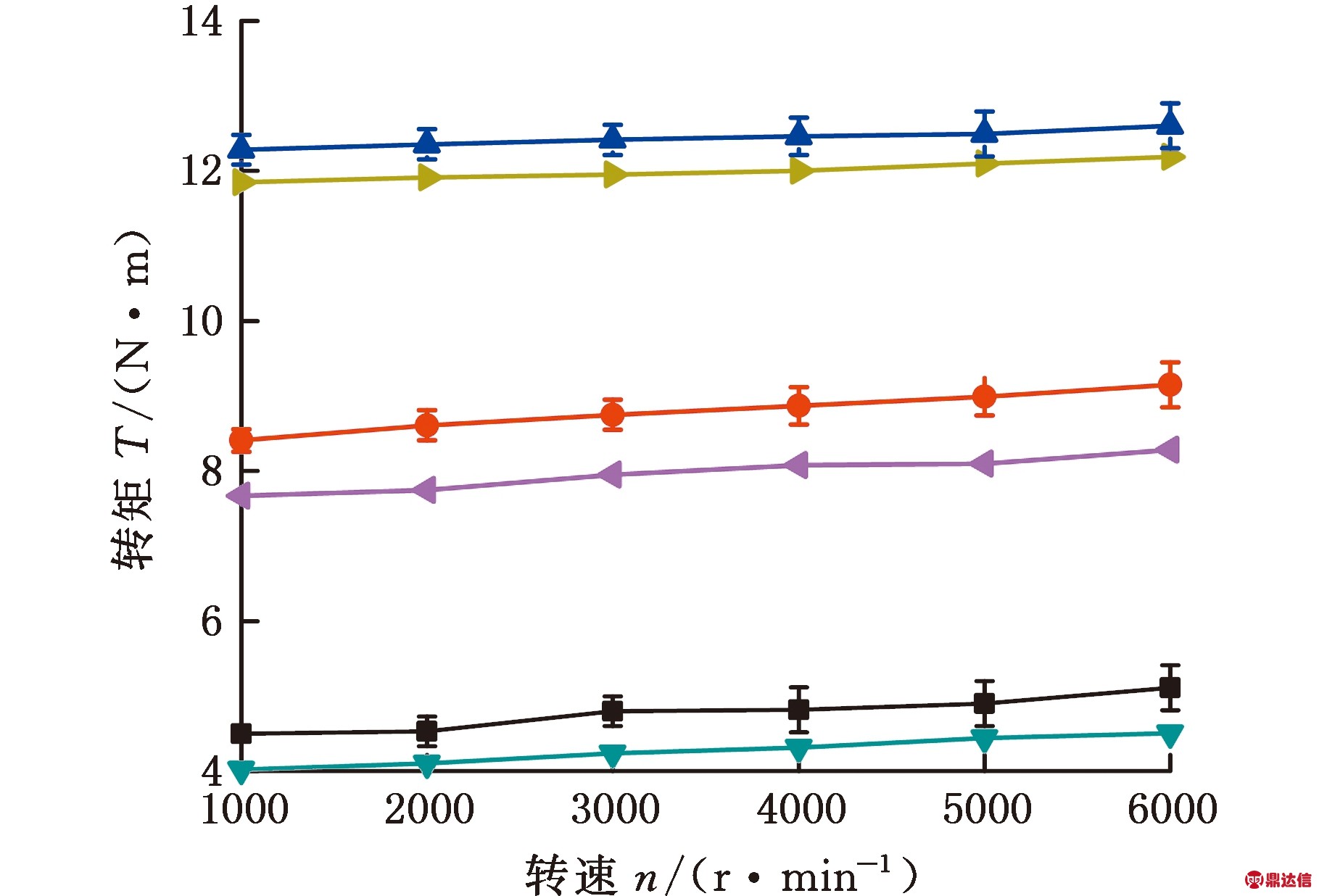
(b)100 ℃
图13 摩擦转矩试验与仿真曲线
Fig.13 Test and simulation curves of friction torque
4 结论
(1)根据车辆传动系统密封环的工作特点,采用FLUENT+Abaqus+MpCCI构建了密封间隙流场和结构场的求解模型,开展了密封系统双向流固耦合数值计算,形成了一种基于MpCCI的流固耦合作用下密封性能参数预测方法。
(2)考察了流固耦合作用下工况参数对密封性能的影响机制,得到了不同入口压力、不同转速和不同油温状态下密封泄漏量和摩擦转矩的变化关系。研究发现,旋转密封系统泄漏量随着转速的增大而减小,随着入口油压和油温的增大,泄漏量显著增大;密封摩擦转矩随着旋转轴转速增大略有增大,随着入口油压的增大而明显增大,油温升高使得摩擦转矩略有减小。
(3)通过密封环综合性能试验获得了复合材料密封环的密封性能参数的变化规律,与流固耦合计算的结果对比发现,计算值和试验值的变化规律具有一致性,表明基于MpCCI的密封流固耦合计算方法的有效性,并为相似摩擦元件的流固耦合计算提供了一种新思路。