摘要: 针对悬臂式多级离心泵易出现陀螺效应,造成转子失稳与泵机组振动等问题,根据理论公式计算所得的密封流体激励力、泵腔流体激振力和附加质量代入有限元模型进行仿真计算,得到悬臂式多级离心泵的轴心轨迹图,并分别与未加载3种激励力、只加载密封流体激励力与添加密封和泵腔流体激振力的计算结果进行对比分析,最后利用Bently 408型便携式数据采集系统对轴心轨迹进行试验,对仿真进行验证。研究结果表明:加载叶轮口环密封力能够提高转子系统的稳定性,并能有效降低径向位移幅值;泵腔中流体激振力增加了转子系统的交叉刚度,导致振幅增加;相比于密封流体激励力和泵腔流体作用力,流体附加质量对悬臂式转子系统的瞬态响应的影响更为显著。
关键词: 悬臂式多级离心泵; 转子; 轴心轨迹; 多重激励; 密封
引言
悬臂式多级离心泵具有效率高、结构紧凑、易安装、维护方便等优点,被广泛应用于国民经济各个领域。但是此类泵易出现由悬臂式结构与非线性激励所带来的陀螺效应,在产生碰摩、振动与噪声的同时,对转子及泵的安全稳定运转带来较大的影响[1-2]。作为反映旋转机械转子振动状态的重要特征信号,轴心轨迹能直观且有效表征转子的实际运转状况,并逐渐成为旋转机械稳定性、可靠性研究以及故障诊断的重要手段[3]。
国内外针对轴心轨迹的研究主要集中在汽轮机、压缩机以及风机等大型旋转机械[4]。在泵领域,BRYAN等[5]通过主轴加标准球来进行主轴回转误差测量;ERIC等[6]分别用多步法、反转法和多点法测试回转精度,并将误差缩小为纳米级;RUHL[7]通过建立转子-轴承系统的有限元模型并利用ANSYS 等软件进行有关临界转速、瞬态响应等动力学特性计算;蒋小平等[8]通过研究某高压多级离心泵的不平衡响应等,完成了水润滑轴承-转子耦合系统的稳定性分析及判定;黄志伟[9]用非线性转子动力学理论和方法建立了不同故障作用下的轴心轨迹图、时域波形图等,系统分析了机组轴系的动态响应等问题;李伟等[10]对轴流泵在0.8、1.0、1.2倍设计流量工况下的轴心轨迹进行了试验研究,分析了不同工况下混流泵转子的振动情况;胡敬宁等[11]通过数值求解得到了水润滑轴承-转子系统启动过渡阶段的轴心轨迹,并对启动瞬态的轴心轨迹进行了试验研究。以上研究主要针对过流部件位于双支撑内侧的离心泵。对于叶轮、导叶等被布置到双支撑外侧的悬臂式多级泵,尚未发现相关的文献报道。本文基于CFD数值计算,预测悬臂式多级离心泵转子系统不加载激励力、只加载密封流体激励力、加载密封与泵腔流体激振力、加载密封与泵腔流体激振力以及附加质量等4种情况下的轴心轨迹,并将预测数据与利用Bently 408型便携式数据采集系统测得的轴心轨迹试验值进行对比与分析,为研究和提高悬臂式多级离心泵的稳定性及可靠性提供参考依据。
1 激励源分析
本文研究的多级离心泵为卧式双支撑悬臂式结构。图1是简化后的轴承-转子示意图,转子总长347.5 mm,轴承跨距143 mm,转子系统包括泵轴、四级叶轮和叶轮螺母等。
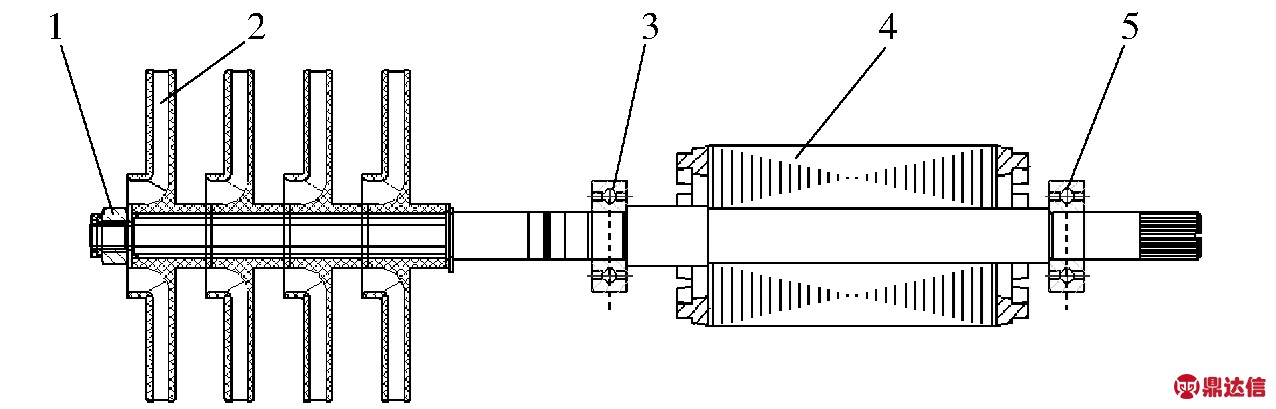
图1 悬臂式多级离心泵轴承-转子系统三维实体模型
Fig.1 3D cantilever type multistage centrifugal pump rotor bearing system model
1.叶轮螺母 2.叶轮 3.轴承B1 4.泵轴 5.轴承B2
由于不加载激励力的情况(即“干态”)的转子动力学特性分析不能反映泵实际运转特征,也不能为显存或潜存故障的诊断与分析提供准确可靠的原始数据,因此有必要进行最接近真实工况(即“湿态”)的转子动力学特性分析。获得悬臂式多级泵的“湿态”轴心轨迹,不仅要考虑零件不平衡质量对转子系统瞬态响应所产生的影响,还要同时考虑口环密封激励力、泵腔流体作用力以及流体附加质量等对转子系统的影响。
1.1 密封激励力
多级离心泵通常在每级叶轮前后都设有口环或级间密封,主要目的是防止高压侧流体向低压侧流动,减少内泄(即容积损失),从而提高整泵效率。如图2所示,悬臂式多级泵的密封结构是一种环形非接触式结构,密封环隙内介质的流动情况非常复杂,不仅有导致泄漏的轴向流动,还可能存在由入口预旋效应和转子表面摩擦导致的周向流动。在实际运转过程中,转子的不平衡质量也会导致转子产生涡动,使密封环隙内流体介质处于偏心状态,导致其压力分布出现不均匀性的同时,产生能够改变转子临界转速、动力学特性类似于滑动轴承的不可忽略的流体支反力。当环隙内压力变化的频率与转子模态频率接近时,还可能带来转子的自激振动,导致轴心轨迹产生剧烈波动。
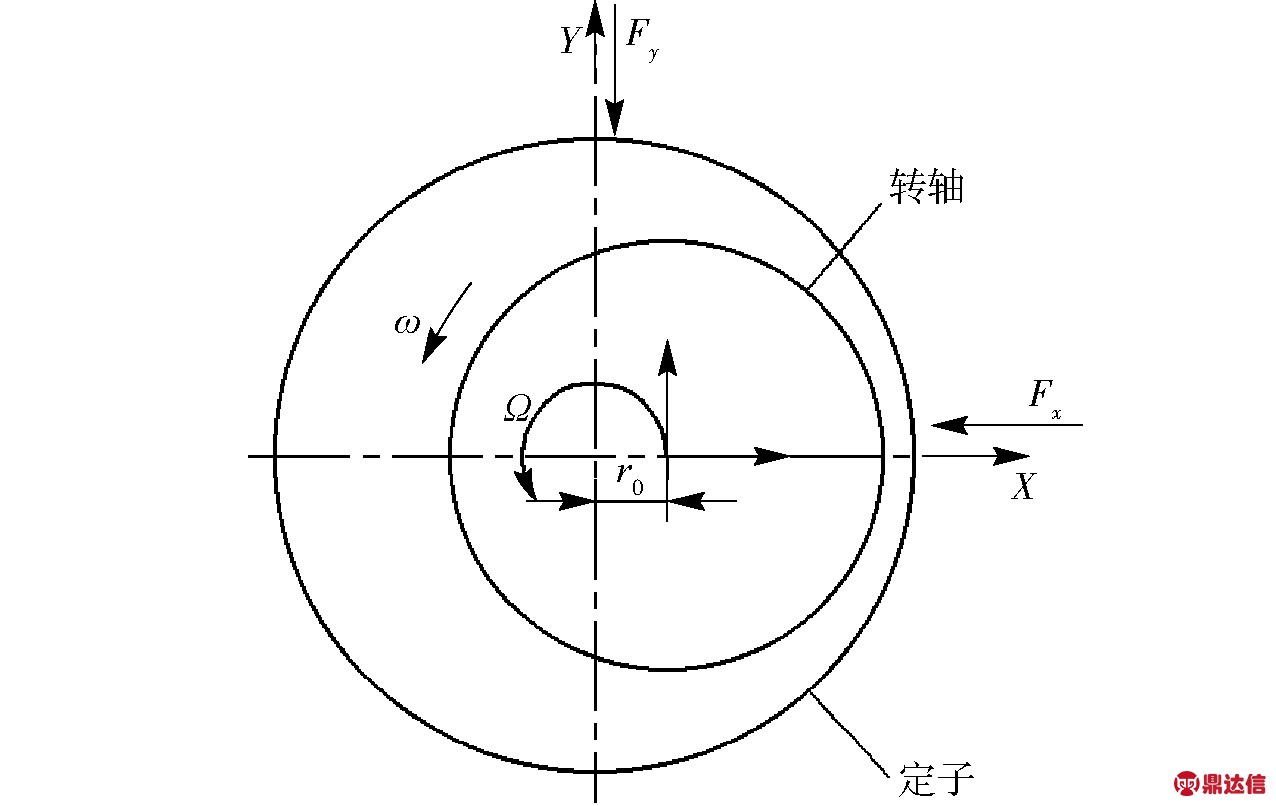
图2 环压密封模型
Fig.2 Model of ring pressure seal
研究表明:密封力与油膜力具有相似的动力学特征[12]。本文根据求解油膜力的Black模型,得到密封流体激励力的动力学方程为
(1)
其中

(2)

(3)
cxx=cyy=μ1μ3T
(4)
cxy=-cyx=μ2μ3ωT2
(5)
mxx=myy=μ2μ3T2
(6)
mxy=-myx=0
(7)

(8)
μ1=(1+ξ)2σ+(1+ξ)(2.33+2ξ)σ2+
(9)
μ2=0.33(1+ξ)2(2ξ-1)σ+(1+ξ)(1+2ξ)σ2+
(10)
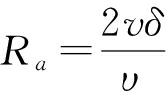
(11)
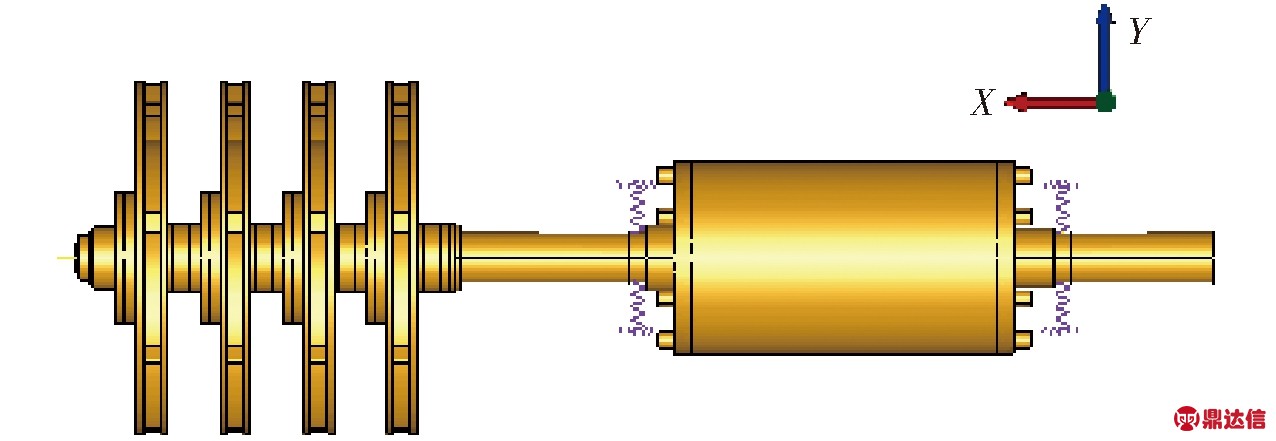
(12)
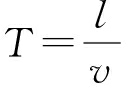
(13)
(14)
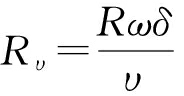
(15)
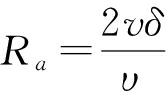
(16)
式中 kxx、kyy、kxy、kyx——刚度系数
cxx、cyy、cxy、cyx——阻尼系数
mxx、myy、mxy、myx——附加质量
Δp——密封轴向压降
ξ——密封流体周向进口损失系数
l——密封长度
δ——径向密封间隙
v——密封腔中流体轴向平均流速
R——密封半径
Ra——轴向流动雷诺数
Rυ——周向流动雷诺数
λ——摩擦因子
ω——转子自转角速度
σ——摩擦损失梯度系数
υ——流体粘度系数
其中交叉刚度系数kxy、kyx和主阻尼系数cxx、cyy是影响密封-转子耦合系统稳定性的主要因素,交叉刚度越大,耦合系统稳定性越差,主阻尼越大,耦合系统稳定性越好。
本文所研究悬臂式离心泵的口环密封内外径分别为39 mm和40 mm(即单边间隙0.5 mm),密封宽度2.5 mm;级间间隙的内外径分别为10 mm和10.5 mm(即单边间隙0.25 mm),密封宽度4.5 mm;额定转速2 800 r/min。按上述计算方法得到设定点工况口环间隙的刚度和阻尼系数矩阵如表1所示,级间密封的刚度和阻尼系数矩阵如表2所示。由于计算所得口环密封和级间密封mf值较小,故计算时该项可以忽略。
表1 口环密封的刚度系数矩阵和阻尼系数矩阵
Tab.1 Stiffness coefficient matrix and damping coefficient matrix of wear ring seal
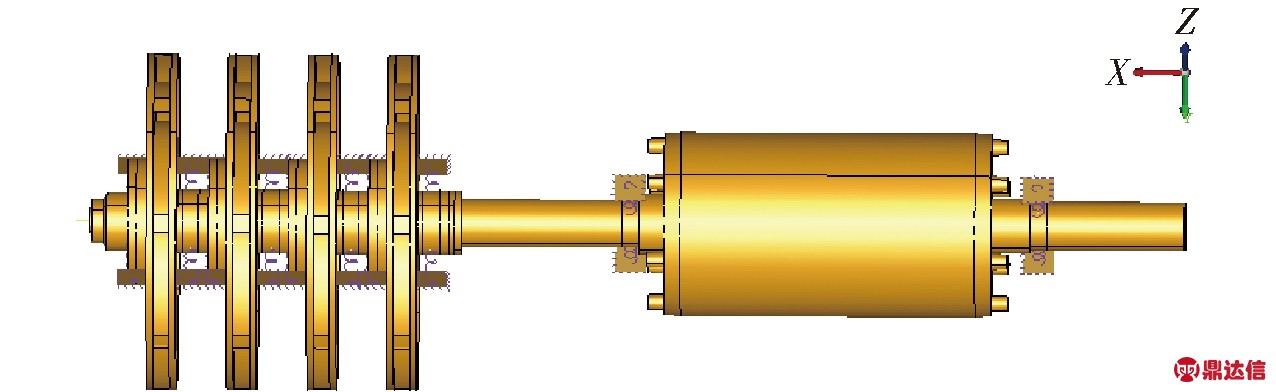
1.2 泵腔间隙流体作用力
泵腔中环绕在泵前后盖板上的流体对转子系统所受的涡动力有显著影响,研究表明,叶轮所受涡动力中70%的径向力和30%的切向力由泵腔中的间隙流诱导所产生[13]。悬臂式多级泵转子在高速运转时,转子系统所受的陀螺力容易造成叶轮在泵腔中出现静偏心和动偏心现象,泵腔中的流体对转子产生激励力。与之相对应,泵腔也会产生相应转速的涡动。间隙小的地方作用在叶轮上的切向力增大,间隙大的地方作用在叶轮上的切向力减小;在转子运转中最大切向力的相位滞后于间隙最小处。叶轮所受的切向力力矩促进转子发生正进动。泵腔流体作用在由叶轮等所组成的转子系统上的激励力计算公式为
表2 级间密封的刚度系数矩阵和阻尼系数矩阵
Tab.2 Stiffness coefficient matrix and damping coefficient matrix of seal between stages

Fn=∑pAn
(17)
Fτ=∑pAτ
(18)
式中 Fn——激励力在n方向上的分力
Fτ——激励力在τ方向上的分力
An——面积A在n方向上的投影
Aτ——面积A在τ方向上的投影
p——A所对应的压强
后处理叶轮表面压力统计积分可得到额定工况下的径向力,数值也可由后处理统计计算得到。
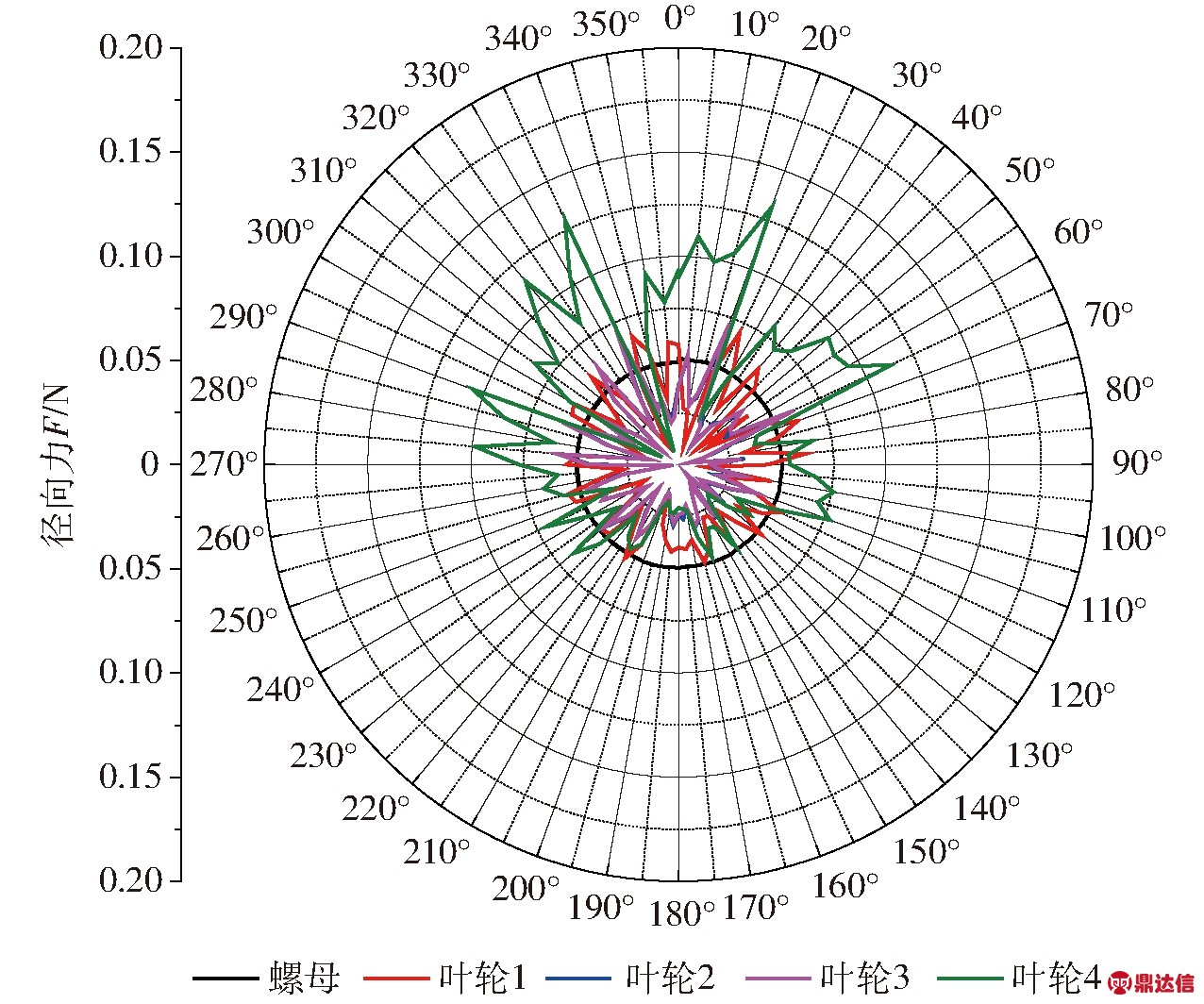
图3 一个周期内径向力变化趋势图
Fig.3 Trend diagram of radial force of a cycle
如图3所示,各叶轮径向力分布规律相似,其峰值皆沿周向均匀分布,峰值数等于叶片数。一个周期内螺母径向力变化很小,几乎可以忽略不计。模拟结果表明,径向力的波动呈现周期性变化,其周期与叶轮叶片数有关。多级离心泵各级叶轮的径向力变化规律基本相同。
1.3 流体附加质量
为了精确研究多级离心泵工作状态(即“湿态”)下的轴心轨迹,不仅要考虑零件不平衡质量、口环动力特性、流体激励力等对转子系统瞬态响应产生的影响,还要考虑流体附加质量对转子系统的影响。计算时参考有关经验,将叶轮内流体质量的10%~35%作为附加质量,并作为激励力加载到计算模型中。
2 “湿态”转子耦合计算前处理
图4为研究对象的三维结构图。实际的转子是一个质量连续分布的弹性系统,具有无穷多个自由度,在转子动力学的有限元分析中,需要把转子系统简化为具有若干个集中质量的多自由度系统。将图4所示的悬臂多级泵转子系统沿着轴线从左向右划分为由螺母、叶轮、轴段和滚动轴承等单元组成的离散模型,并将各单元用结点来替代,按从左向右的顺序进行编号,最终得到该系统的有限元简化模型,如图5所示。
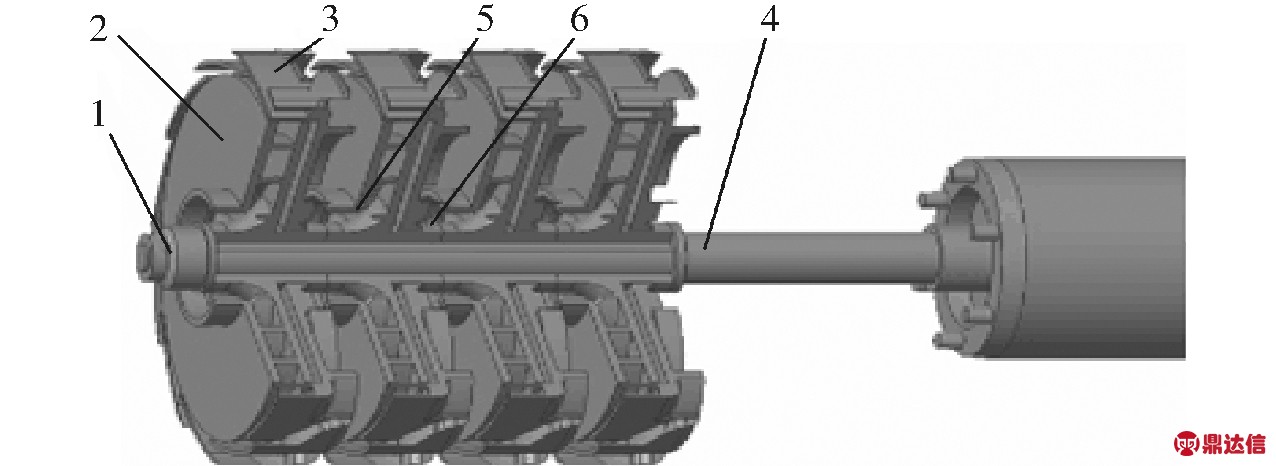
图4 悬臂式多级离心泵结构图
Fig.4 Diagram of cantilever type multistage centrifugal pump structure
1.叶轮螺母 2.叶轮 3.导叶 4.泵轴 5.口环 6.级间间隙

图5 一维梁-弹簧-集中质量模型
Fig.5 One dimensional beam-spring-lumped mass model
轴承B1、B2对应的节点号分别为11、16;叶轮螺母与四级叶轮对应的节点号分别为2、5、6、7、8。对于滚动轴承,由于液膜的阻尼小,远小于轴承刚度,故一般动力学分析中忽略不计。此外,在SAMCEF软件中计算得到的轴承刚度系数为124 880 N/mm。
传统的转子动力学分析往往采用传递矩阵法,由于该方法将大量结构信息简化为极简单的集中质量-梁单元模型,故不能保证模型的完整性和分析的准确度。有限元法分析转子动力学的思路是将一个典型的轴承-转子系统划分成有限个单元,并建立单元节点与节点位移之间的关系,综合各单元的运动方程,得到以节点位移为广义坐标的系统运动微分方程,将一个质量连续分布转子的振动问题转化为有限个自由度的振动问题。根据上述原理得到各单元分析的主要参数:质量矩阵、阻尼矩阵、刚度矩阵等。转子动力学有限元分析计算是基于整个转子的运动方程

(19)
式中 M——质量矩阵
C——外部阻尼矩阵
G——陀螺矩阵
K——刚度矩阵
F——外部激励力
Q——不平衡质量引起的质量力
q——广义位移
阻尼矩阵C依据Rayleigh 理论可表示为质量矩阵和刚度矩阵的线性组合
C=αM+βK
(20)
其中 α=2(ζiωj-ζjωi)/[(ωj+ωi)(ωj-ωi)]ωiωj
(21)
β=2(ζiωj-ζjωi)/[(ωj+ωi)(ωj-ωi)]
(22)
式中 ωi、ωj——第i、 j阶固有频率
ζi、ζj——第i、 j阶振型的阻尼比
在Pro/E中建模,将表3所示的材料属性添加到转子动力学分析软件SAMCEF中,添加表1、2所示的密封流体激励力、泵腔间隙激振力以及流体附加质量,划分六面体网格,得到4个模型,分别为:未加载密封流体激励力、泵腔间隙流体作用力和附加质量;仅加载密封流体激励力;同时加载密封流体激励力和泵腔间隙流体作用力;同时加载密封流体激励力、泵腔间隙流体作用力和附加质量。本文通过对4个模型的对比分析,得到3种激励力对悬臂式转子系统轴心轨迹的影响规律。
表3 转子各部件材料属性
Tab.3 Material properties of rotor
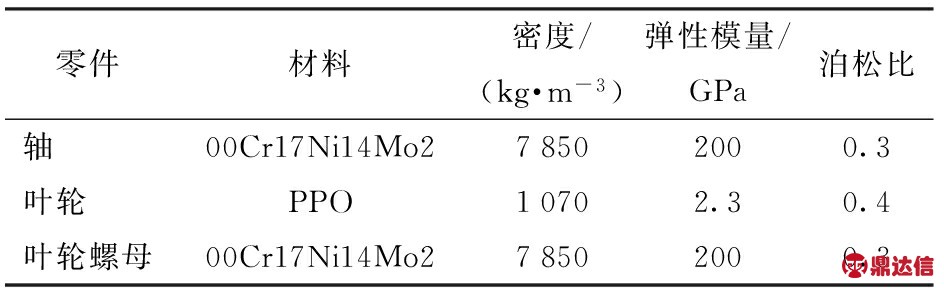
3 轴心轨迹的数值仿真与分析
3.1 未加载3种激励力的情况
首先对悬臂式多级泵转子系统在“干态”下的不平衡质量瞬态响应进行分析,即只考虑不平衡量对瞬态响应的影响。“干态”下转子在SAMCEF中的设置如图6所示。
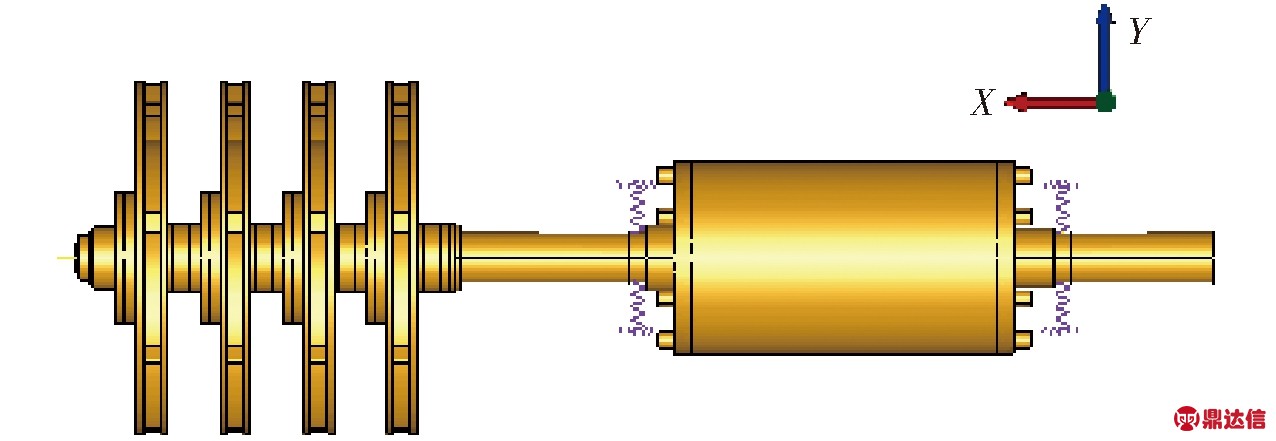
图6 未加载激励力时SAMCEF中悬臂式转子模型
Fig.6 Cantilever type multistage centrifugal pump model in SAMCEF
转子系统在“干态”下计算得到的轴心轨迹图如图7所示。其最大径向位移为2.16 μm,最小径向位移为1.16 μm,轴心轨迹曲线为同心圆环。
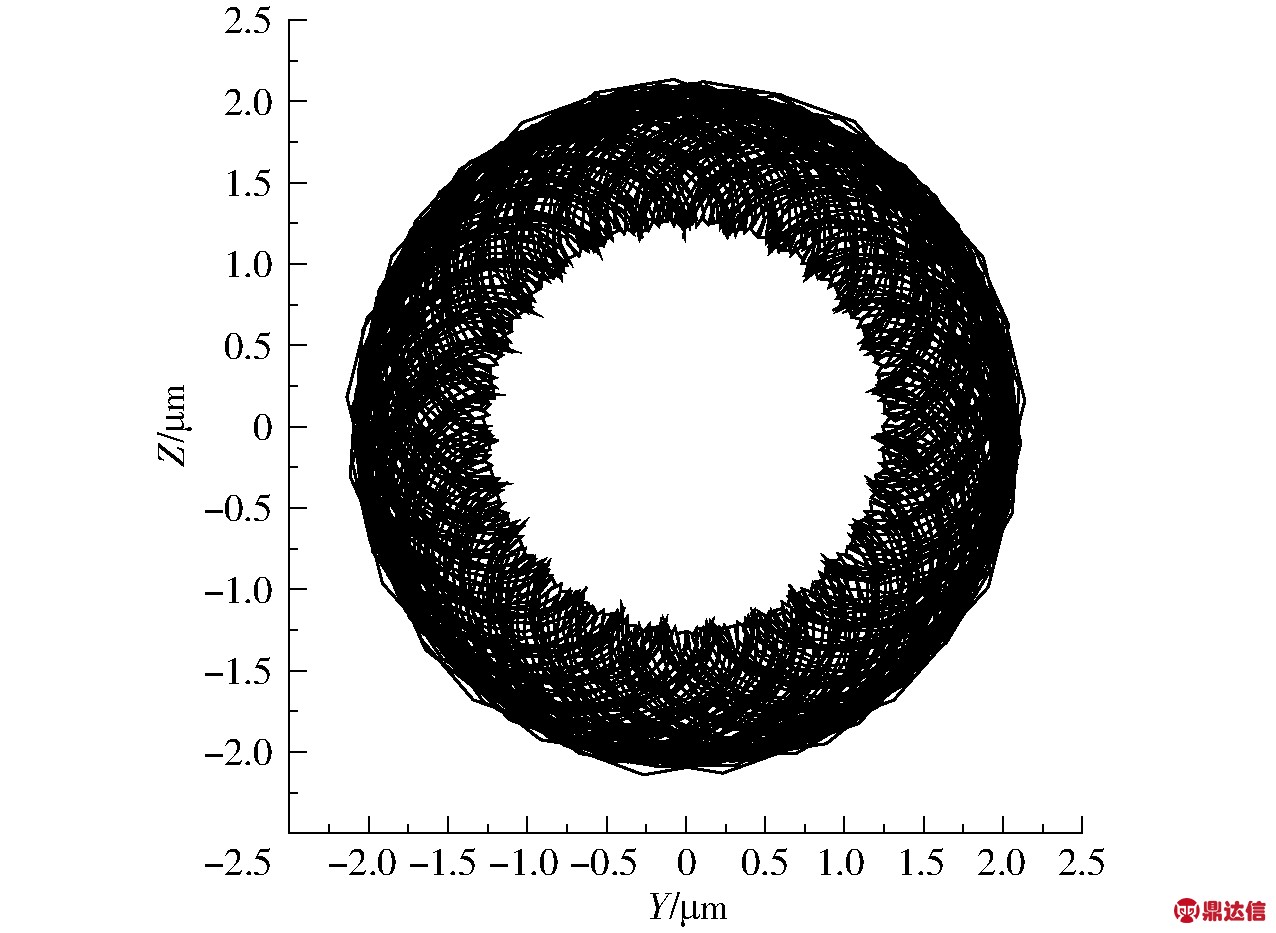
图7 干态下转子的轴心轨迹
Fig.7 Axis trajectory in dry state
3.2 仅加载密封流体激励力的情况
计算转子部件在仅添加密封流体激励力时,需要计入叶轮口环密封间隙动力特性系数,在叶轮口环位置处施加弹簧约束,建立了如图8所示的有限元计算模型。
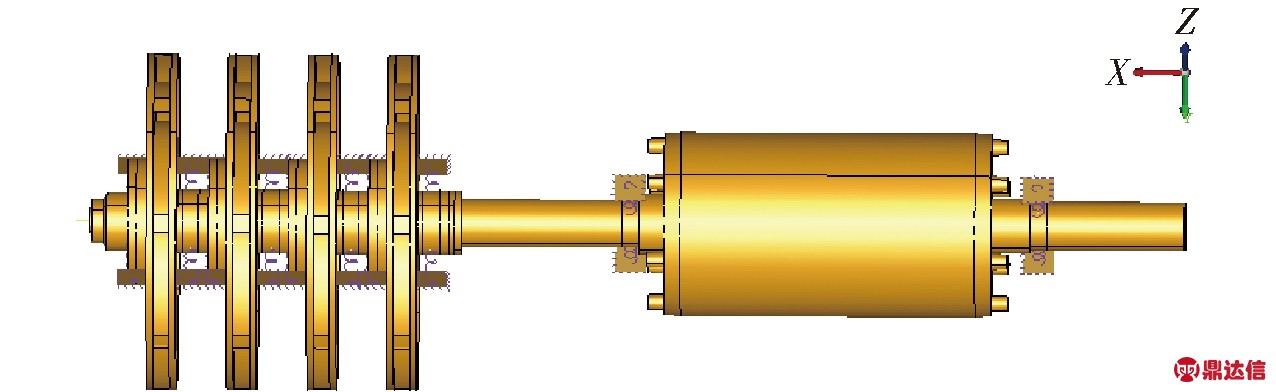
图8 仅加载密封流体激励力时SAMCEF中悬臂式转子
计算模型
Fig.8 Calculation model of cantilever rotor in SAMCEF
在实际运转过程中,口环间隙所产生的动力特性系数对提高转子系统的稳定性具有一定作用。因此,首先考虑设计点工况下口环动力特性对瞬态响应的影响,在叶轮口环位置与级间间隙位置处施加轴承约束。计算得到了额定转速下叶轮螺母位置处的轴心轨迹图,如图9所示。
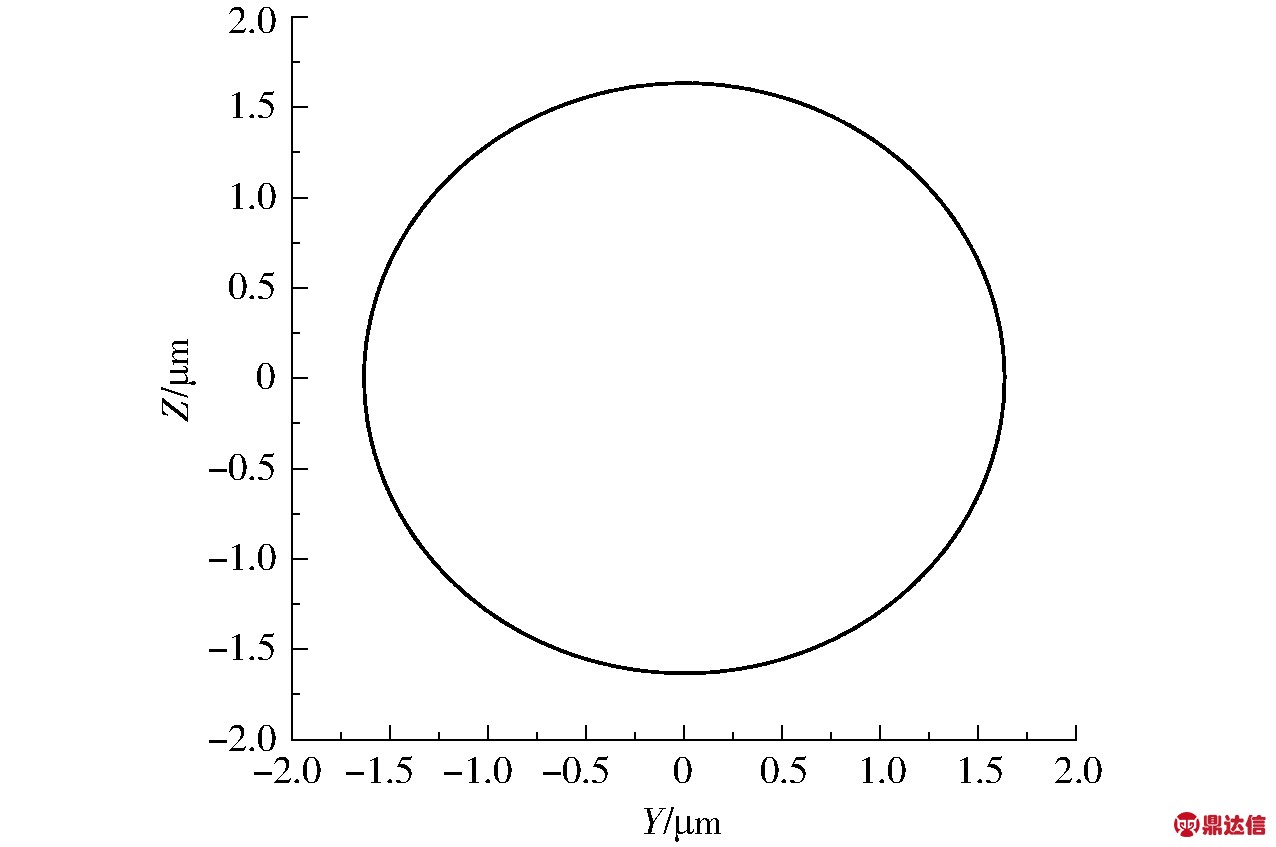
图9 考虑口环动力特性的轴心轨迹曲线
Fig.9 Axis trajectory considering dynamic characteristics of seal
可以看出,考虑口环动力特性后,叶轮螺母位置处的最大径向位移为1.64 μm,最小径向位移为1.63 μm,轴心轨迹曲线较为稳定。对比图7和图9,可以看出叶轮口环动密封力能够提高转子系统的稳定性,这是由于添加密封流体激励力增加了系统的对称刚度和阻尼系数,而阻尼系数是影响转子系统动力学稳定性的主要因素。
3.3 同时加载密封激励力和泵腔间隙作用力的情况
除了与传统双支撑结构不同外,各级泵体内部产生的流体作用力也是产生振动的重要原因。不仅要将CFX中计算得到的各级叶轮、螺母受到的切向力、法向力作为泵腔间隙流体激励力施加在对应的节点上,各级口环动力特性系数也是如此。不同运行工况条件下叶轮前后口环密封力不同,对转子的支撑作用也有所差异,这里只列出了处于最远端的叶轮螺母处的设计点工况轴心轨迹曲线(图10)。可以看出,轴心轨迹呈扇形,与该工况下各级叶轮所受径向力分布趋势相同,径向位移幅值最大达到了2 μm,分布不均匀;轴心轨迹曲线径向位移较大,有一定偏心,轨迹曲线复杂。
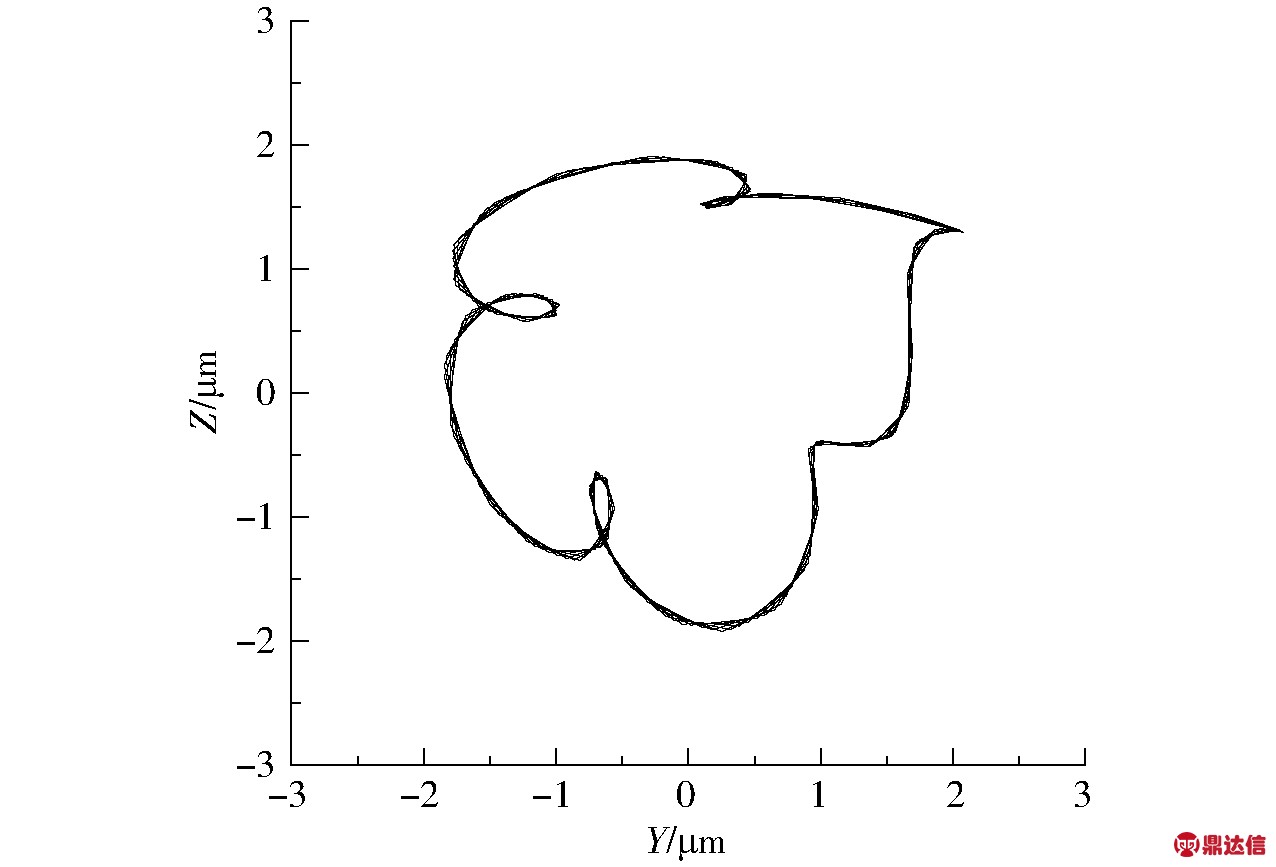
图10 考虑流体作用力的轴心轨迹曲线
Fig.10 Axis trajectory considering fluid force
3.4 同时加载所述3种激励力的情况
为了研究多级离心泵在工作状态下的轴心轨迹,即“湿态”下的轴心轨迹,不仅要考虑零件不平衡质量对转子系统瞬态响应产生的影响,还要考虑口环动力特性、泵腔间隙流体激励力以及流体附加质量等对转子系统的影响,叶轮内流体质量的10%~35%作为附加质量考虑[14]。通过Creo 3.0对各级叶轮水体进行称量,水体密度设为水的密度,得到每级叶轮内的流体质量为39.8 g。将叶轮内的流体质量简化为10%、15%、20%、25%、30%、35%的附加质量,与流体激振力一同施加到各级叶轮所对应的节点上,其余设置保持不变。计算得到如图11所示的不同流体附加质量下叶轮螺母位置处的最大径向位移及轴心轨迹图。
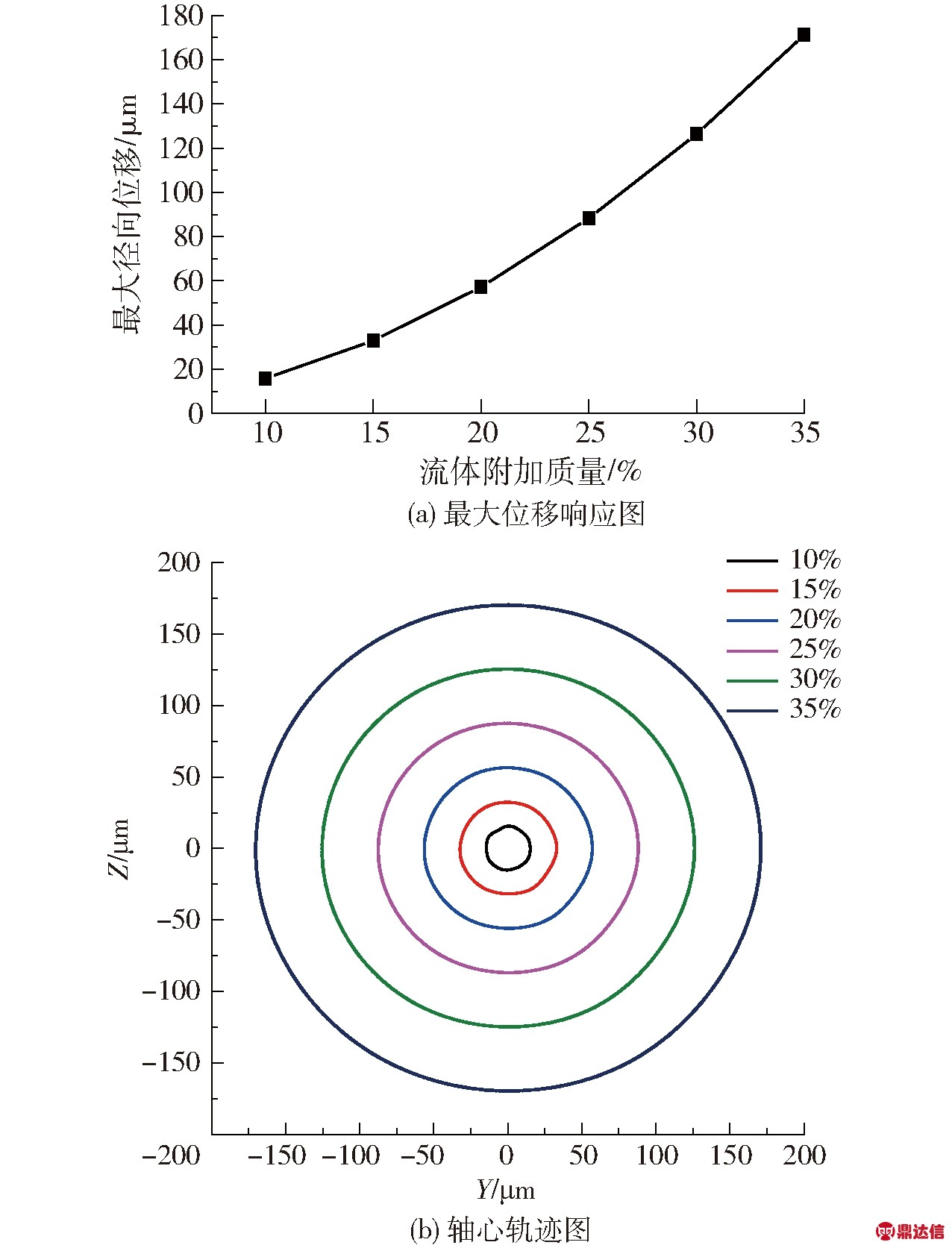
图11 考虑附加质量的瞬态响应图
Fig.11 Transient response diagram considering added mass
可以看出位移响应曲线随附加质量的增加呈指数增加,当流体附加质量简化为20%时,螺母位置处的最大径向位移达到了57 μm;当流体附加质量简化为25%时,螺母位置处的最大径向位移达到了88 μm;当流体附加质量简化为30%时,螺母位置处的最大径向位移达到了126 μm,其轴心轨迹曲线均为长短轴相差不大的椭圆。
3.5 数值仿真结果分析
数值模拟分析结果表明:叶轮口环密封力能够提高转子系统的稳定性,有效降低径向位移幅值,本文中幅值降低了31.7%。考虑叶轮在添加泵腔中流体激振力的情况下轴心轨迹曲线较为复杂,说明泵腔中流体激励力相对于密封结构对转子系统产生反进动,故降低了转子系统的稳定性,并导致振幅增加。而将叶轮内流体的质量简化为不同的附加质量后计算得到的最大径向位移随流体附加质量的增加而呈现出指数增长趋势,径向位移的幅值远大于添加密封流体激励力和泵腔间隙作用力的轴心振动幅值,且轴心轨迹曲线为长短轴相差不大的椭圆,说明流体附加质量相对于密封流体激励力和泵腔流体作用力对悬臂式转子系统的瞬态响应更为显著。因此,“湿态”下的轴心轨迹分析应同时考虑密封力、流体激励力以及流体附加质量等因素。
4 轴心轨迹的试验研究
4.1 试验台组成与传感器安装
如图12a所示,在江苏大学国家水泵及系统工程中心实验室搭建了以Bently ADRE 408型高速动态信号测试仪为核心的轴心轨迹测试系统。该系统主要包括408DSPI(Dynamic signal procession instrument)16通道数据采集处理仪以及ADRE Sxp软件等,使用光学键相传感器实现同步采样,位移传感器采用由探头、前置器和延长线等共同组成的Bently Nevada 3300XL 5/8 mm型电涡流式位移传感器,灵敏度系数为7.878 V/mm,量程为-10~10 V;同步采样率为128 Hz,数据采样方式为每次采样采集10个样本,每个样本间隔时间为100 ms(即1 s内采集10个样本)。
如图12b所示,2个位移传感器相互垂直地安装在同一个轴截面上,并保证两探头间夹角在90°±5°范围内;调整传感器与被测主轴之间的距离,使输出的电压控制在量程范围内,对采集得到的传感器数据进行相应处理即可得到转子在该轴截面位置的轴心运动轨迹。键相传感器则直接垂直安装在转子主轴上。
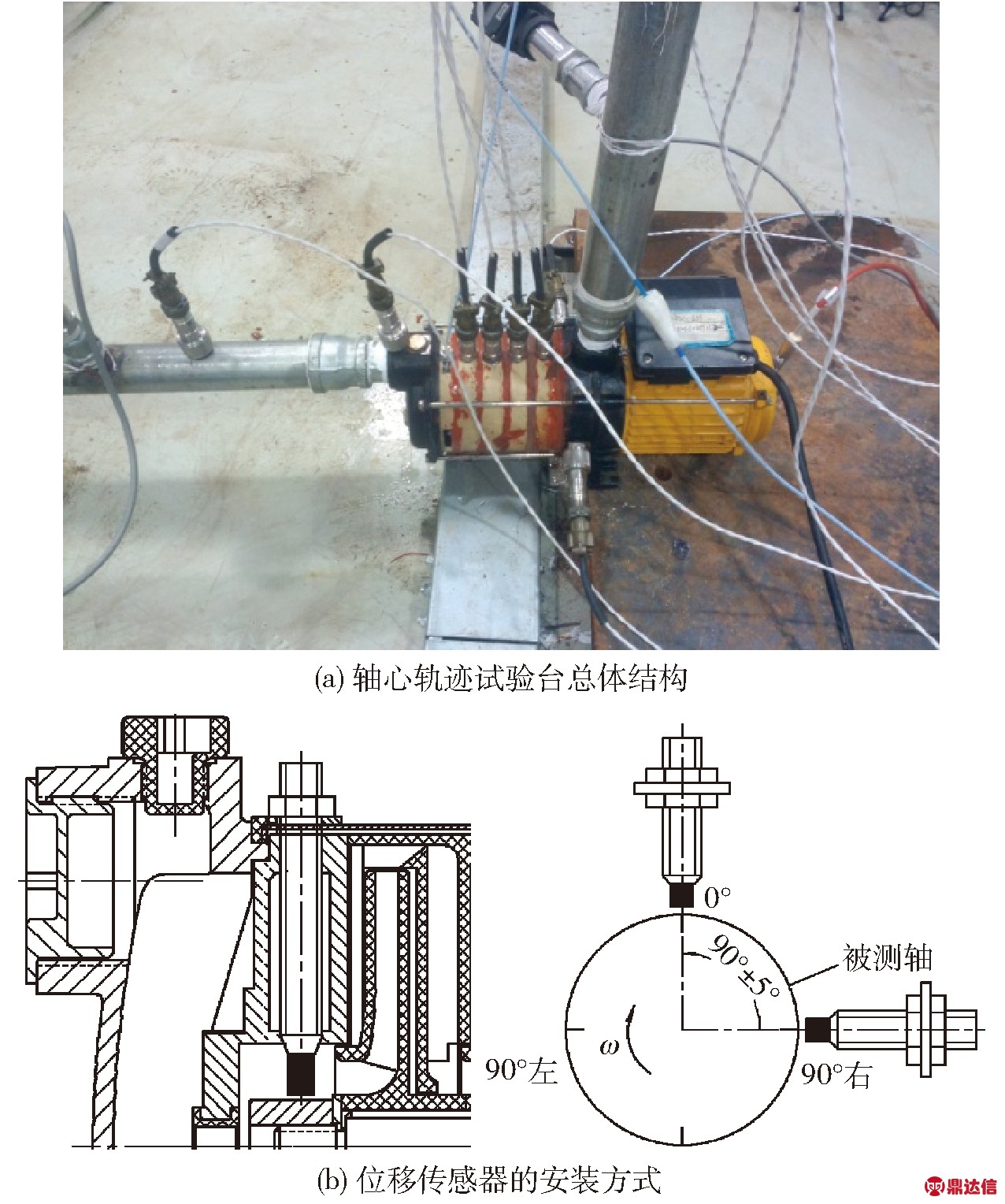
图12 轴心轨迹试验台结构以及传感器安装方式示意图
Fig.12 General structure diagrams of axis trajectory test rig and installation location of sensor

图13 轴心X、Y坐标随时间变化曲线
Fig.13 Changing curves of X and Y coordinates
4.2 试验结果分析
由于受到水力振动和白噪声等高频谐波分量的影响,测得的设计点工况下的轴心轨迹带有许多锯齿状尖角。为了得到清晰、真实的轴心轨迹并准确分析转子的实际涡动情况,将测得的离散位移数据导入Excel中,利用OriginPro的数据分析工具对原始轴心轨迹进行分解提纯及滤波,获得了如图13所示的排除高频谐波信号的轴心X、Y坐标随时间t变化的时域图。可以看出X、Y方向的时域图为周期性谐波,相位差为π/4,都围绕各自的均值做幅度相对较小的波动,相位特征表现较为稳定。频率以工频为主,在采集到的8周数据中,波形均存在削波现象。
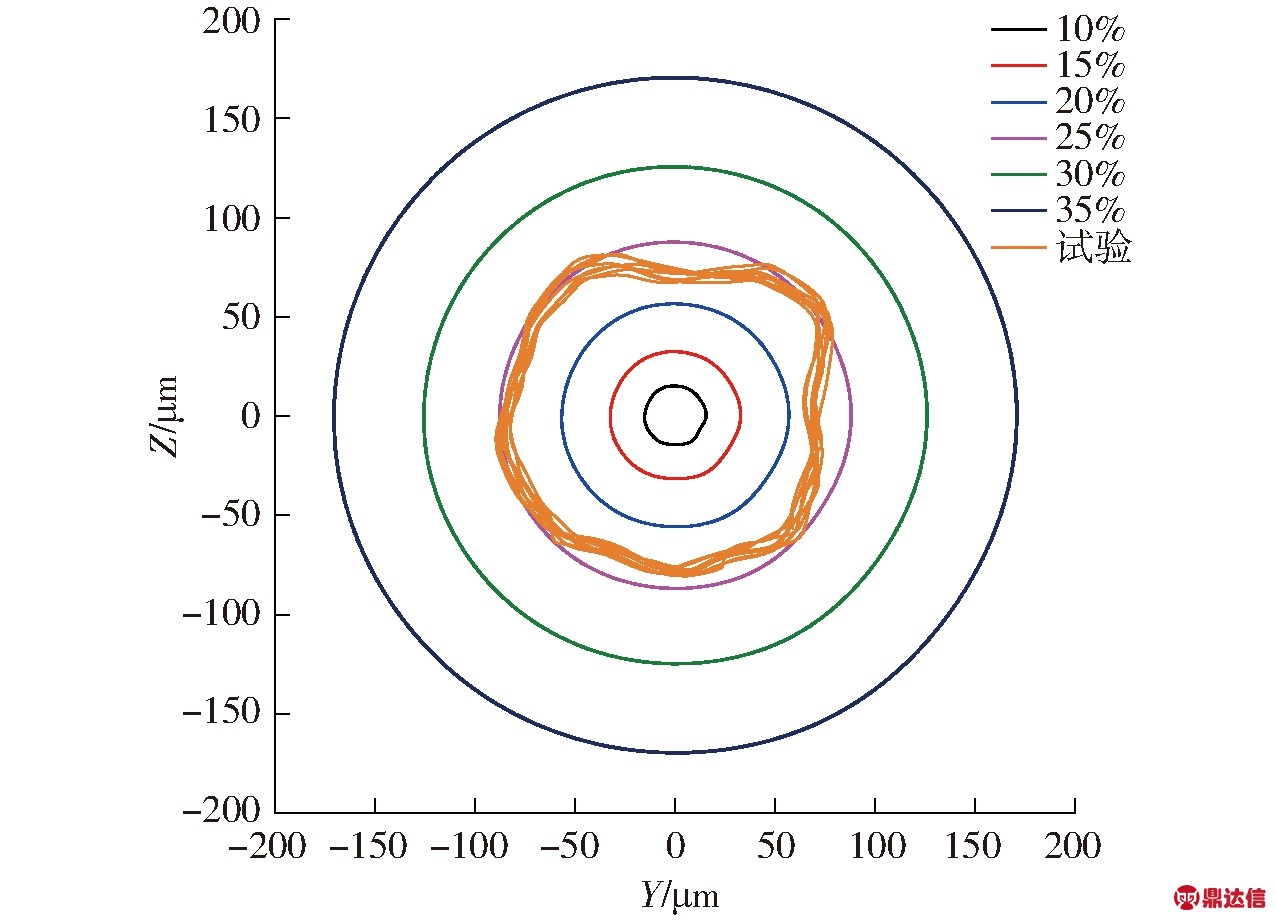
图14 轴心轨迹试验数据与模拟数据对比
Fig.14 Comparison of experimental and simulated data of axis trajectory
合并图13的X、Y时域图,得到了设计点工况的转子轴心轨迹图。将轴心轨迹试验值与理论计算数据对比(同时添加3种激励力)如图14所示,可以看出:实测轴心轨迹与理论计算一样,都近似为圆形或椭圆形,转子运动方向相同,都为正进动。实测轴心轨迹相对稳定,重复性较好,表明转子运行过程偏心不大。实测轴最大径向位移为93.8 μm,与流体附加质量量化为25%时的“湿态”轴心轨迹趋势较为接近。由于理论计算时假设叶轮的不平衡质量都相同,并且忽略了轴段的质量偏心、转子与导叶定子等的碰摩以及外界输入能量所引起的振动(如电动机本身运转时的振动和流体动静干涉等),故理论计算的“湿态”轴心轨迹往往呈现为长短轴相差不大的椭圆。而实测值由于以上因素的共同作用,加上传感器存在安装精度等问题,导致测得的轴心轨迹波动曲线不会显得光滑平整。
5 结论
(1)轴心轨迹的仿真结果表明:与未加载任何激励力相比,加载密封流体激励力可以提高转子系统的稳定性,并有效降低径向位移幅值;与只加载密封流体激励力相比,同时加载密封流体与泵腔流体激振力的轴心轨迹曲线更复杂,且径向位移幅值有所增大;与同时加载密封流体和泵腔流体激振力相比,添加叶轮内流体附加质量后的轴心轨迹呈现为长短轴相差不大的椭圆,且最大径向位移随附加质量的增加呈指数增长趋势。
(2)仿真计算与试验结果对比分析表明,试验测得的轴心轨迹变化趋势与添加3种激励力且附加质量为25%的计算结果基本一致。理论计算 “湿态”轴心轨迹为长短轴相差不大的椭圆,而实测的轴心轨迹波动曲线形状不光滑平整。