摘要:由于大型锥形筒节存在锥度,考虑金属沿锥向的流动,首先采用微分分层计算法和切块法建立了大型锥形筒节轧制力力学模型;然后基于ABAQUS有限元软件,建立了大型锥形筒节轧制过程仿真模型。模型计算结果和有限元仿真结果表明:力学模型计算轧制力与有限元计算总轧制力的相对误差在20%以内。对比分析了力学模型和有限元模拟计算单位轧制力的分布。通过分析芯辊和外辊的转速比,得出了所建力学模型的稳定轧制的适用范围。
关键词:大型锥形筒节;轧制力;锥向金属流动;分层计算法;有限元模型
0 引言
大型锥形筒节主要应用在核电、石油、化工、航天等领域,是我国重点领域关键技术装备的关键零部件。目前大型锥形筒节的成形方法是自由锻,其缺点是能耗大、效率低,同时锻造筒节的尺寸精度差,表面上存在凹凸不平的锻痕,材料利用率低、成本高。轧制成形具有生产效率高、尺寸精度高、材料利用率高、综合成本低等优点[1-2]。目前大型直壁筒节已经实现轧制成形,如果大型锥形筒节能够实现轧制成形,则对创新设计大型锥形筒体轧制装备,完成大型筒体制造技术的升级,解决制约我国大型筒体批量化生产能力瓶颈,实现我国重点领域关键技术装备的自主化和产业化都具有十分重要的意义。目前关于大型锥形筒节的轧制,以及相关轧制设备和轧制工艺的研究只有少量报道,且实际中还无法进行试验验证。轧制力计算模型是锥形筒节轧制过程控制的关键模型,因此本文针对大型锥形筒节轧制过程的轧制力计算模型进行研究。
目前关于环形件轧制力计算模型的研究较多。华林等[3-5]利用小型环件轧机进行轧制实验时,根据实验数据对环件轧制中的轧制力性能参数及工艺参数进行了分析,并通过初等分析法建立了环件轧制的物理模型和力学模型。QIAN等[6]建立了环件沟槽截面的轧制咬入力学模型,并分析了咬入条件的影响因素。GUO等[7]建立了环件在径轴向的稳定轧制条件下的数学模型,并提出了一种合理的轧制工艺。PARVIZI等[8]基于上限法求解出了环件轧制力和力矩的解析解。蒋日东等[9-10]基于环件轧制过程与特征,建立了热轧的环件轧制模型,并提出了环件轧制过程的自适应与自学习控制结构。汤翼等[11]提出了在轧制过程中环件中心不在芯辊和驱动辊中心连线上的轧制几何模型,建立了环件的运动学参数与环件壁厚和轧制进给量之间的关系。罗晓东等[12]基于有限元仿真软件,研究了环件轧制过程中咬入和锻透情况、应力-应变分布、轧制力与轧制力矩等金属的变形规律。韩星会等[13]基于有限元对内台阶锥形环件的轧制过程进行了数值模拟,提出了轧制毛坯尺寸和轧制孔型的优化方案,并进行了实验验证。WANG等[14]研究了锥形环件虚拟轧制过程的关键技术。上述轧制力计算模型适用于小型环件,由于大型环件直径、高度和厚度大,金属变形规律复杂,上述模型并不适用于大型筒节轧制,但为大型筒节轧制提供了思路和基础。
关于大型筒节轧制力计算的研究,中国第一重型机械集团提出了一种大型筒节轧制设备及其轧制工艺[15]。程瑞敏[16]对大型环件成形过程的数值模拟进行了研究,极大改进了大型环件的工艺优化及尺寸精度。兰箭等[17]以缩比环件轧制实验和有限元数值模拟为基础,研究材料轴向转移模式及其变形机理,提出包含环件形状因素的成形性能评定方法。华林等[18]研究了大型环件的径轴向轧制工艺,揭示了大型环件径轴向轧制过程的变形规律和机理,分析了轧制过程中产生的问题和缺陷的实质,为实际的工业生产提供了依据。门正兴等[19]对大型筒体锻造成形中产生的缺陷进行分析,并提出了合理的预防措施及解决方法。孙建亮等[20]为了准确计算筒节轧制力,建立了一种基于切块法的考虑筒节不均匀应力分布的轧制力计算模型。张博[21]研究了2.25Cr1Mo0.25V 大型筒节高温轧制过程中微观组织演变规律。陈素文[22]基于条层法对大型筒节热轧三维变形进行模拟,研究了筒节宽展的分布规律。
上述主要是针对直壁筒节的研究,关于大型锥形筒节轧制成形的研究,施熔刚等[23]对三代核电蒸发器锥形筒体锻件各部位进行检验分析,为轧制大型锥形筒节的尺寸及性能要求提供了参考。王实[24]优化了大型锥形筒体轧机辊系布置和辊系参数,进行了锥形筒体轧制过程仿真。
由于大型锥形筒节存在锥度,必须考虑金属沿锥向的流动规律,因此本文提出一种考虑金属锥向流动的大型锥形筒节轧制力计算模型。
1 考虑锥向金属流动的轧制力计算数学模型
大型锥形筒节尺寸巨大、自重大,采用卧式轧制会产生巨大的轴向力,导致轧辊磨损严重和宽展不可控。本文采用大型锥形筒节立式轧制,轧制稳定性较好,其物理模型如图1所示。大型锥形筒节由若干支撑辊支撑,支撑辊为主动辊,转速与筒节转速相匹配,目的在于减小支承辊与筒节之间的摩擦力,进而防止筒节下端面的扭曲变形;轧制变形由主辊和芯辊完成,主辊和芯辊立式布置,均为主动辊,通过芯辊调节压下量和进给速度。为便于计算分析,作如下假设[22]:锥形筒节轧机轧辊为刚体;锥节为刚塑性体;忽略轧辊和筒节的弹性变形。
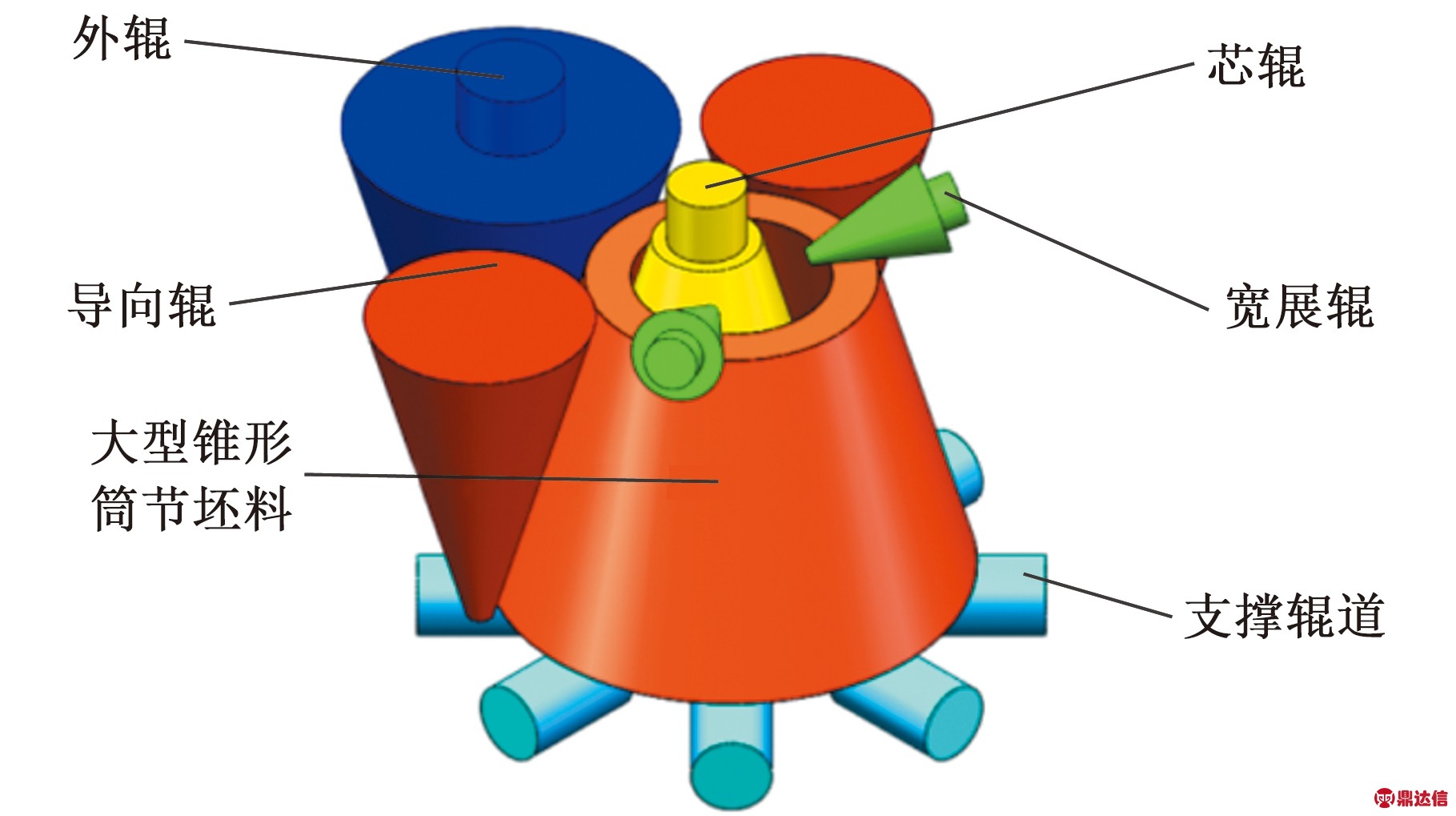
图1 大型锥形筒节轧制物理模型
Fig.1 Physical model of large conical cylinder
大型锥形筒节不同于直壁筒节,由于锥度的存在,锥形筒节轧制过程中变形区金属沿锥向流动,为了理论解析计算出大型锥形筒节轧制力分布规律,本文采用分层法来计算,即将锥形筒节沿轴向分层,建立以锥形筒体轧制方向为x轴、轧辊中心线为y轴、锥形筒体轴线为z轴的三维坐标系,坐标原点o位于筒体小端面轧制变形区,垂直截面受力如图2所示。
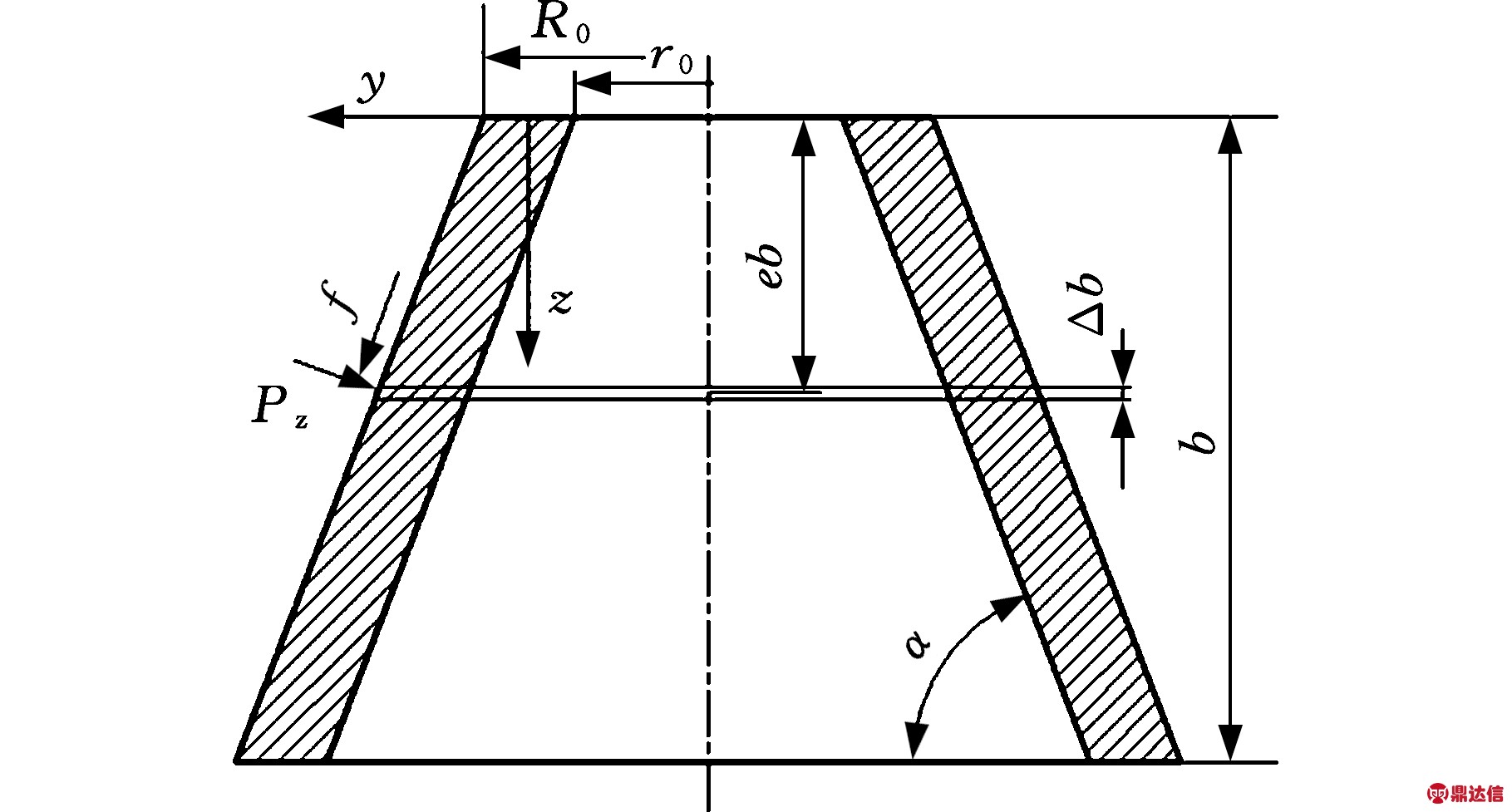
图2 大型锥形筒节垂直截面受力示意图
Fig.2 Stress diagram of vertical section of large
conical cylinder
取任意一微层(图2),根据几何关系,可得每一微层锥形筒体半径和轧辊半径:
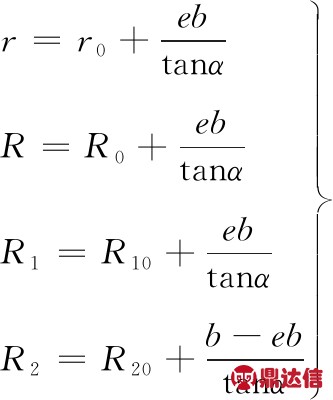
(1)
式中,r0为锥形筒体最小端内壁半径;R0为锥形筒体最小端外壁半径;r为锥形筒体某一层内壁半径;R为锥形筒体某一层外壁半径;R10为芯辊最小端半径;R20为外辊最小端半径;R1为芯辊某一层半径;R2为外辊某一层半径;b为锥形筒体宽度;e为锥形筒体宽度系数,0≤e≤1;eb为选取层与锥形筒节小端的距离;α为锥形筒体倾斜角度。
由图3并根据外辊半径、芯辊半径、锥形筒节内外壁半径的几何关系,可得变形区厚度:

(2)


式中,H为变形区厚度;h为出口厚度;H1为变形区上半部分厚度,H2为变形区下半部分厚度。
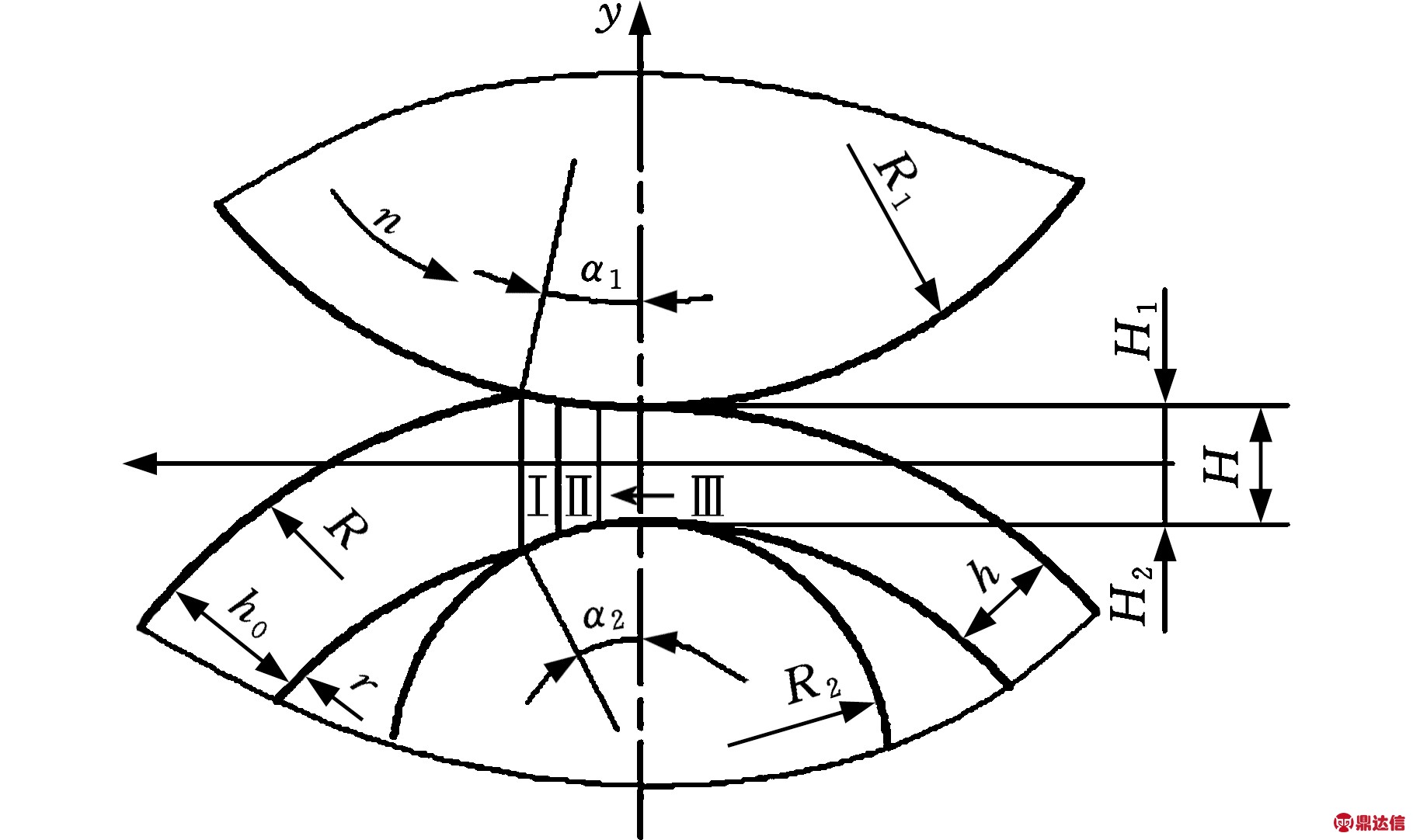
图3 大型锥形筒节轧制示意图
Fig.3 Schematic drawing of rolling large conical cylinder
根据建立的坐标系,由图3中各个圆弧的几何关系得出变形区的取值区间,在此区间轧辊与大型锥形筒节相接触。变形区的取值区间为
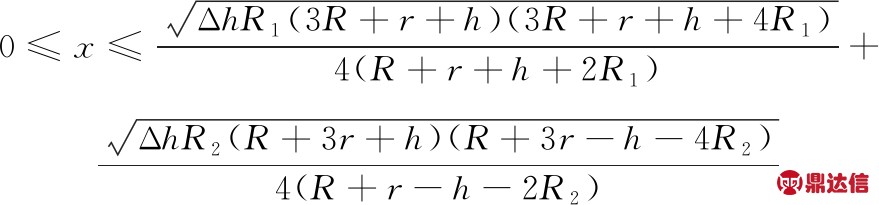
(3)
式中,Δh为每转压下量。
由于接触角足够小,故接触弧长[25]
L≈xmax
下面对锥形筒节受力进行分析。根据图2中大型锥形筒节的受力分析,列出平衡方程:
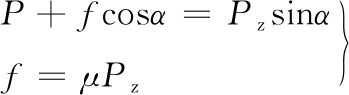
(4)
式中,P为锥形筒节受到的轧制力;Pz为轧辊施加的总轧制力;f为锥形表面受到的摩擦力;μ为摩擦因数。
则总的轧制力和锥形筒节变形产生的轧制力关系为
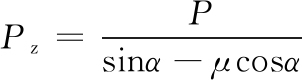
(5)
由于变形区上下轧辊直径和转速均不同,是典型的异步轧制,因此每一层的变形区可分为后滑区、搓轧区和前滑区,如图3所示的Ⅰ区、Ⅱ区和Ⅲ区,该层的前滑区(Ⅲ区)中,轧辊圆周速度的水平分量要大于金属流动速度,因此轧件上下接触面所受摩擦应力与轧制方向相同,轧件被拽入辊缝;在搓轧区(Ⅱ区),轧件速度在外辊和芯辊速度之间,因此轧件的接触摩擦应力在芯辊与外辊接触的地方是相反的,该区域受到有利于金属变形的剪切力;在后滑区(Ⅰ区),轧辊圆周速度的水平分量要小于金属流动速度,所以轧件上下接触面受到与轧制方向相反的摩擦应力,从而阻碍轧件运动。变形区中单元体受力见图4。
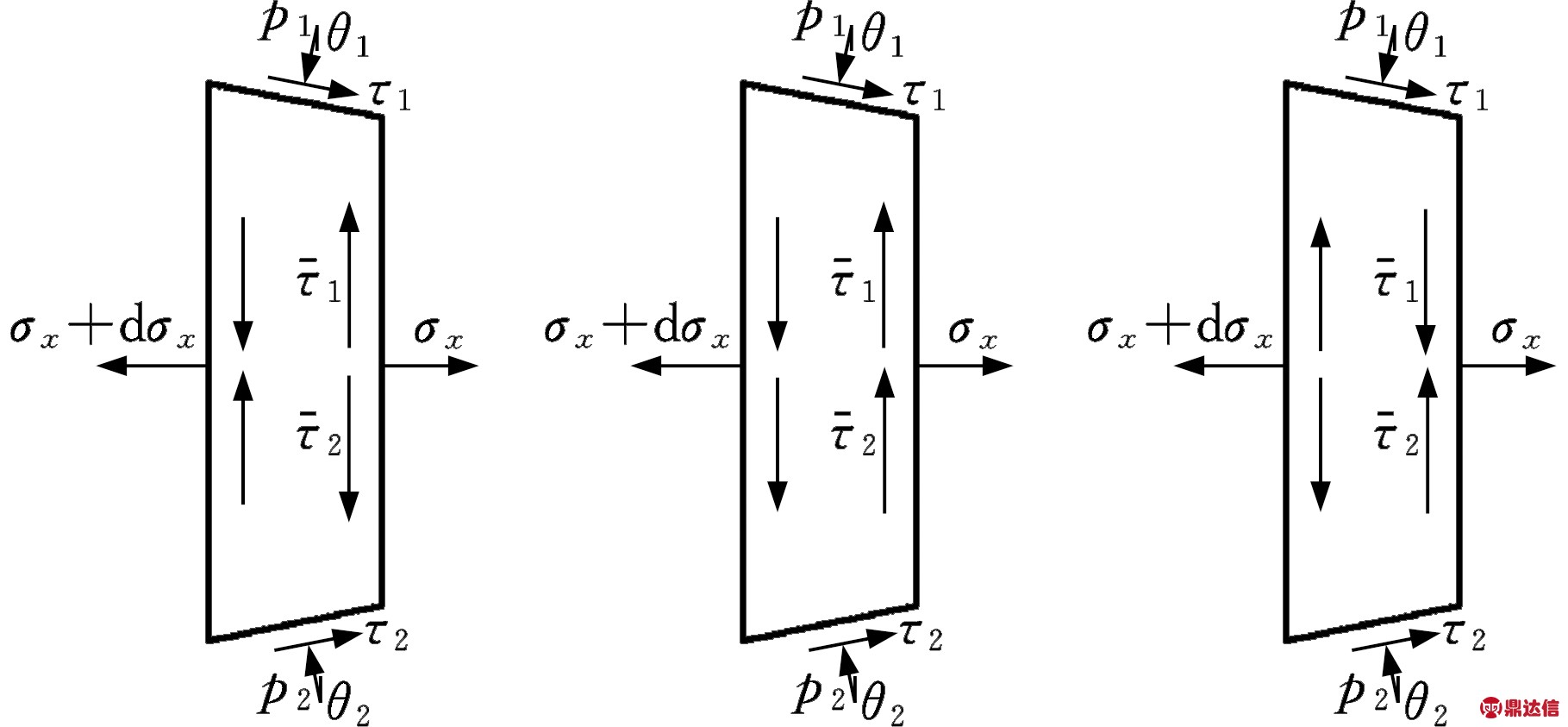
(a)Ⅰ区 (b)Ⅱ区 (c)Ⅲ区
图4 变形区中单元体受力图
Fig.4 The force diagram of the element in the
deformation zone
分析Ⅰ区的单元体受力情况(图4a),在水平方向上受力平衡,平衡方程为
+p1tanθ1+p2tanθ2-τ1-τ2=0
(6)
式中,q为水平方向应力;p1、p2分别为上下辊作用在变形区上的单位压力;θ1、θ2分别为p1、p2作用点与上下轧辊连心线夹角;τ1、τ2分别为上下轧辊与轧件接触面的摩擦应力。
计算单元体上半部分横截面上受到的平均剪应力
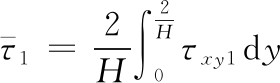
(7)
式中,τxy1为变形区上半部分剪应力。
在Ⅰ和Ⅲ区,τxy1=2mk1y/H,在Ⅱ区,τxy1=mk1(其中,m为剪切系数;k1为上表面剪切变形抗力)。下半部分剪应力与上半部分类似。
由于咬入角比较小,故断面上剪应力对垂直方向平衡方程的影响可以忽略不计,可得
p1+τ1tanθ1=p2+τ2tanθ2=p
(8)
式中,p为垂直方向单位压力。
金属变形区内任一点服从von Mises屈服准则,根据平面应变条件下接触面上剪应力分布规律(τyz=τzx=0),和金属流动准则代入von Mises屈服准则公式得

(9)
式中,σx、σy为x、y方向上的正应力; τxy、τyz、τxz为三向剪应力;σs为轧件材料的流变应力。
假设轧辊与轧件间摩擦为黏摩擦,在变形区上下接触面的剪切应力将达到最大值,即
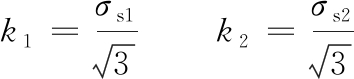
(10)
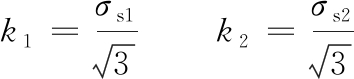
式中,k2为下表面剪切变形抗力。
因此,轧件上下两部分屈服条件为
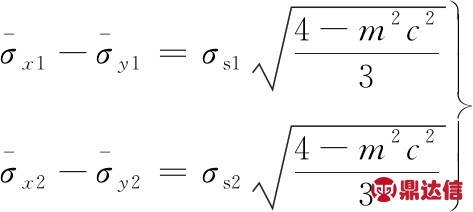
(11)
其中,在Ⅰ区和Ⅲ区,c=1,在Ⅱ区,c=2。
考虑到可得

(12)
将式(12)和式(8)代入式(6),可得
mk1+mk2=0
(13)
解上式微分方程,可得
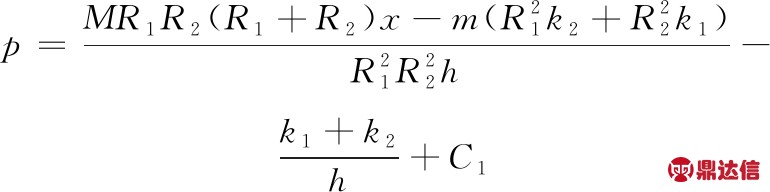
(14)
在入口处,x=L,q=0,代入式(12)可得
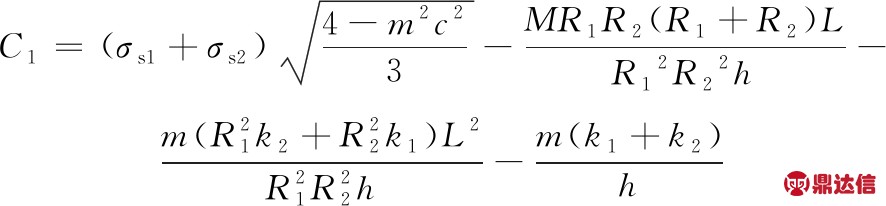
(15)
由此计算出C1的值:
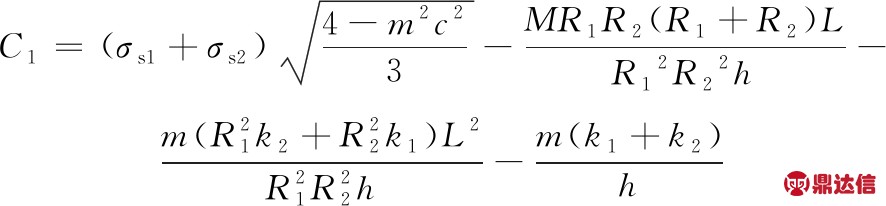
那么,在Ⅰ区受到的单位轧制力为式(15)解得的p。
在前滑Ⅲ区,单位体受力情况如图4c所示,由于咬入角比较小,故单元体在水平方向和垂直方向的受力平衡方程为
p1tanθ1+p2tanθ2+τ1+τ2=0
(16)
p1-τ1tanθ1=p2-τ2tanθ2=p
(17)
整理可得
mk1-mk2=0
解上式微分方程,可得
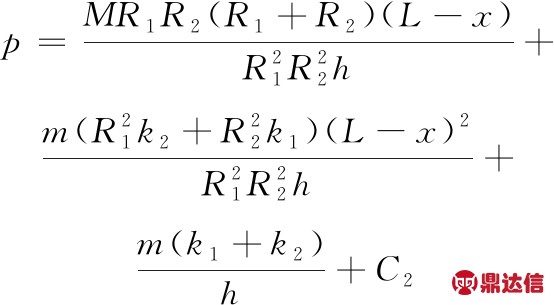
(18)
在变形区出口处,x=0,q=0,代入式(12)可得
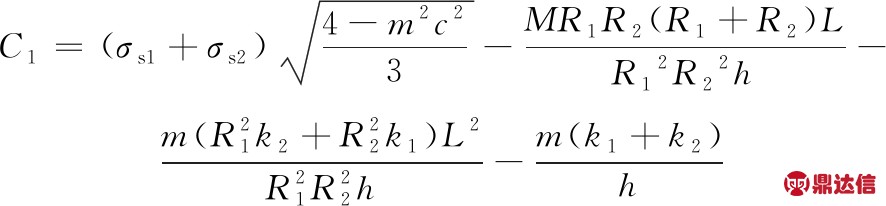
(19)
由此计算出C2的值为

那么,在Ⅱ区受到的单位轧制力为式(19)解得的p。
在搓轧区,单位体受力情况如图4b所示,由于咬入角比较小,故单元体在水平方向和垂直方向的受力平衡方程为
p1tanθ1+p2tanθ2+τ1-τ2=0
(20)
p1-τ1tanθ1=p2+τ2tanθ2=p
(21)
整理可得
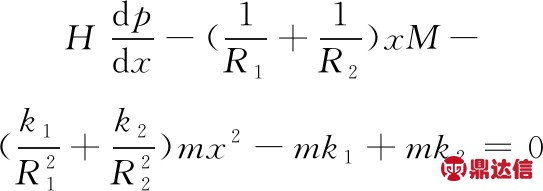
(22)
解上式微分方程,可得
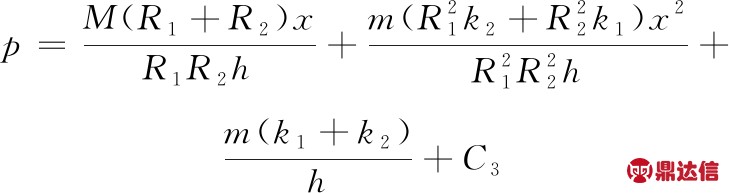
(23)
由于单位轧制力在上中性点xn1和下中性点xn2处是连续的,故有:
pⅠ(x=xn1)=pⅡ(x=xn1)
pⅡ(x=xn2)=pⅢ(x=xn2)
联立可求出C3。
那么,在Ⅲ区受到的单位轧制力为式(23)解得的p。
以上计算得到的为大型锥形筒节某一层的单位轧制力分布,单位轧制力随着大型锥形筒节的宽度系数e的变化而变化。
那么总轧制力为在接触弧长和宽度方向上的定积分:
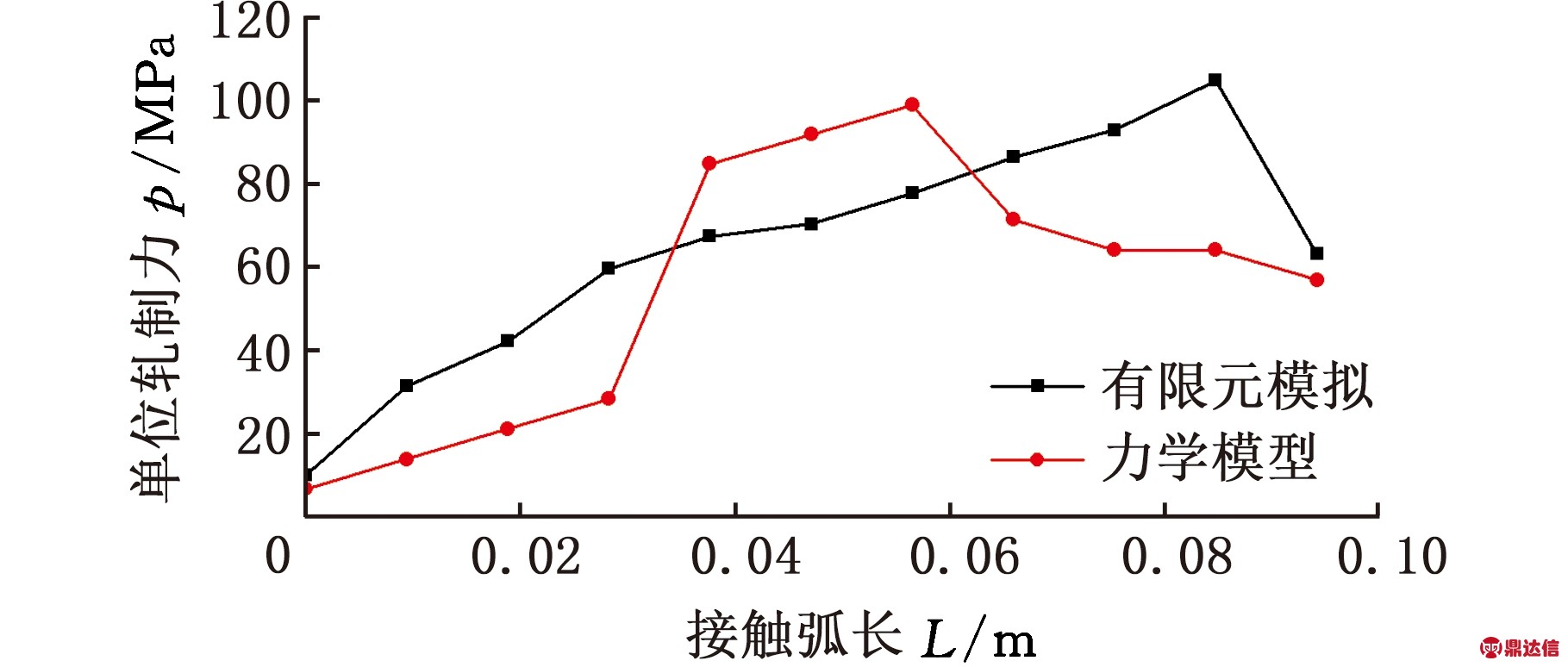
进而根据式(5)可求得轧辊施加到筒节的总轧制力。
2 锥形筒节轧制过程有限元计算模型
由于大型锥形筒节轧制初期理论研究还不成熟,故ABAQUS有限元模拟是一种较好的选择。ABAQUS有限元模拟具有较高的精度和可信度,在进行实际的实验生产之前进行有限元模拟,可以提前模拟实际轧制的情况,预知轧制可能出现的问题,大大节省时间和成本。本文以某接管段锥形筒节轧制成形为例,采用的材料是2.25Cr1Mo0.25V,其基本参数通过实验测定,如表1所示。
传统加工过程需要经过5个工序:下料、镦冲、芯棒拔长、马杠扩孔和最终成形。本文研究的轧制坯料来自扩孔后的锻件,且坯料锥度与目标尺寸相同。本文基于有限元软件,建立大型锥形筒节轧制过程有限元模型,如图5所示,轧辊简化为刚体,包括外辊、芯辊、宽展辊、支承辊。外辊和芯辊为锥形辊,锥度和筒节目标锥度一致,外辊和芯辊为主动辊,芯辊同时承担道次压下功能,芯辊和外辊的转速要与轧辊直径和轧件尺寸匹配,道次压下量根据产品而定,防止筒节受力不均,变形严重;宽展辊为从动辊,控制锥形筒节宽度,由于轧制过程中锥形筒节径向速度不同,所以宽展辊设计为锥形辊,与锥形筒节径向速度分布一致,可
表1 有限元模型材料参数
Tab.1 Material parameters of finite element model
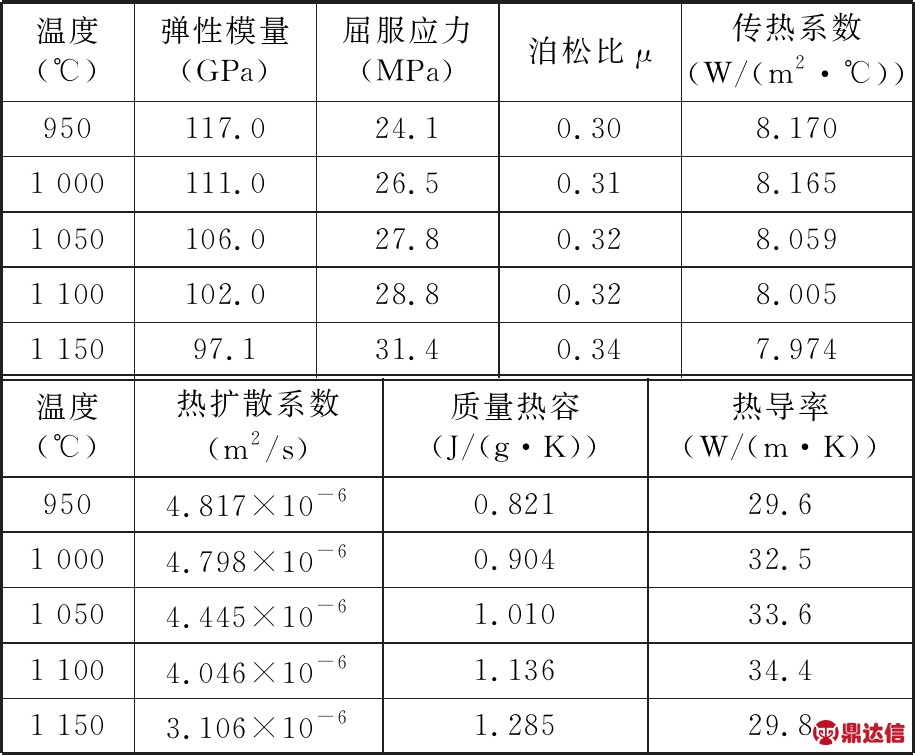
以减小宽展辊的磨损;支承辊承受锥形筒节自重及轴向力,因此设计多个支撑辊共同支撑。锥形筒节初始温度为1 100 ℃,轧制过程主要有辐射传热和接触换热。辐射传热主要是锥形筒节向周围环境进行热辐射,定义辐射换热系数;接触换热主要是在轧辊与锥形筒节之间的热传导,另外还存在摩擦热,定义摩擦因数以及法向硬接触[26]。由于锥形筒节尺寸巨大,既要保证计算精度,又要保证计算成本,所以本文采用质量缩放来加快计算速度[27]。建模参数如表2所示。
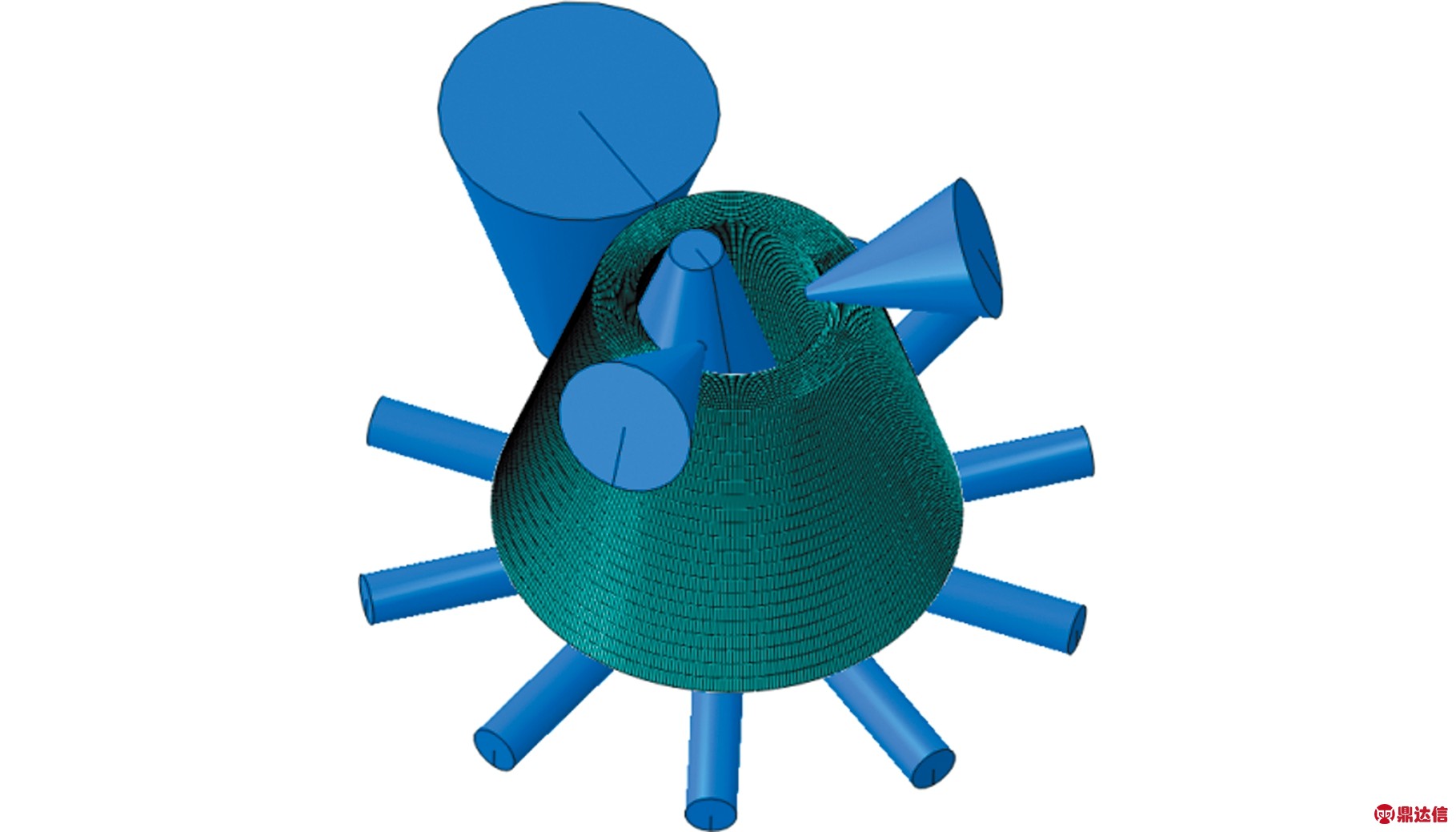
图5 有限元几何模型
Fig.5 Finite element geometric model
表2 大型锥形筒节轧制有限元模型参数
Tab.2 Finite element model parameters of large
conical cylinder
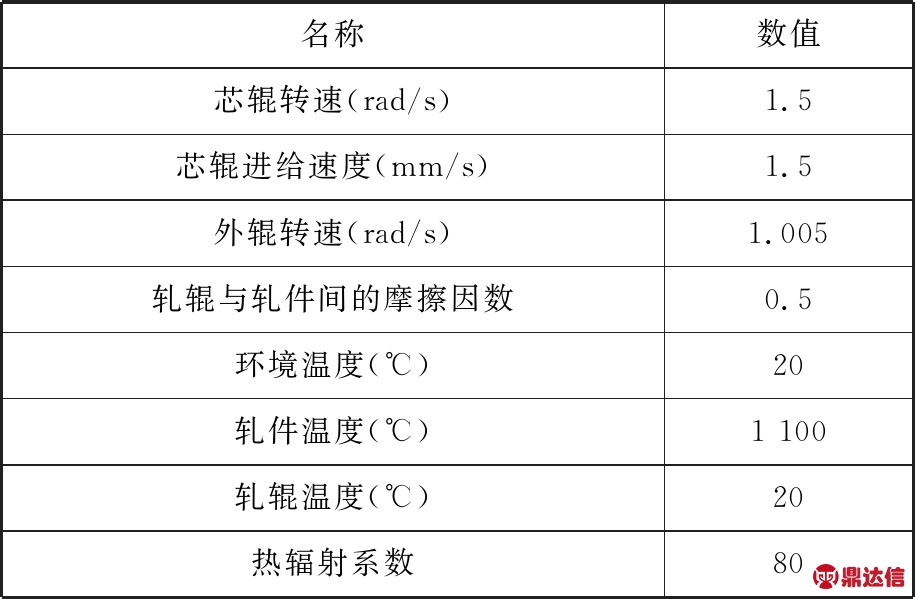
3 结果分析与讨论
以某锥形筒节为研究对象,选取不同规格大型锥形筒节在不同条件下的轧制作为计算算例,表3为大型锥形筒节轧制主要设备参数,表4给出不同轧制条件下力学模型计算和有限元模拟计算总轧制力结果对比,保持芯辊转速为1.5 rad/s,进给速度为1.5 mm/s,外辊转速与之匹配。由表4可知,力学模型计算结果和ABAQUS有限元模拟计算结果误差在20%以内,间接表明理论模型计算与有限元计算结果的准确性,能够满足工业应用要求。
表3 大型锥形筒节轧制主要设备参数
Tab.3 Main equipment parameters of large
conical cylinder
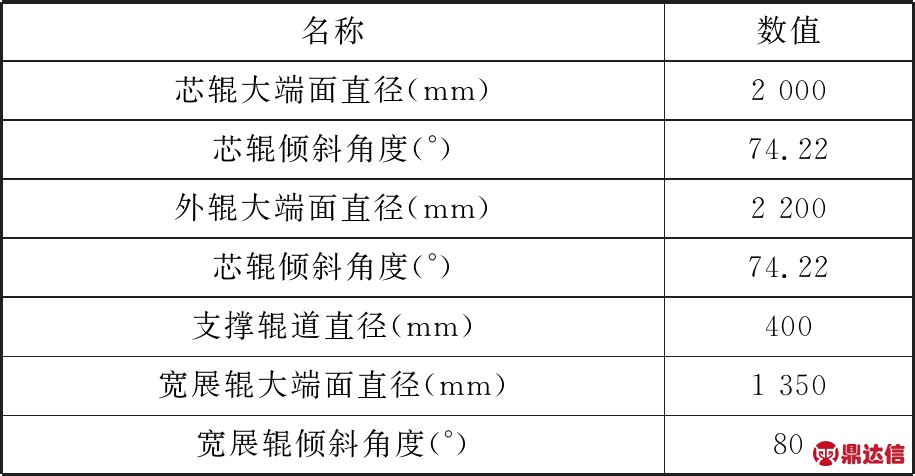
表4 力学模型计算和有限元模拟计算结果对比
Tab.4 Comparisons between mechanical model
calculation and finite element simulation calculation
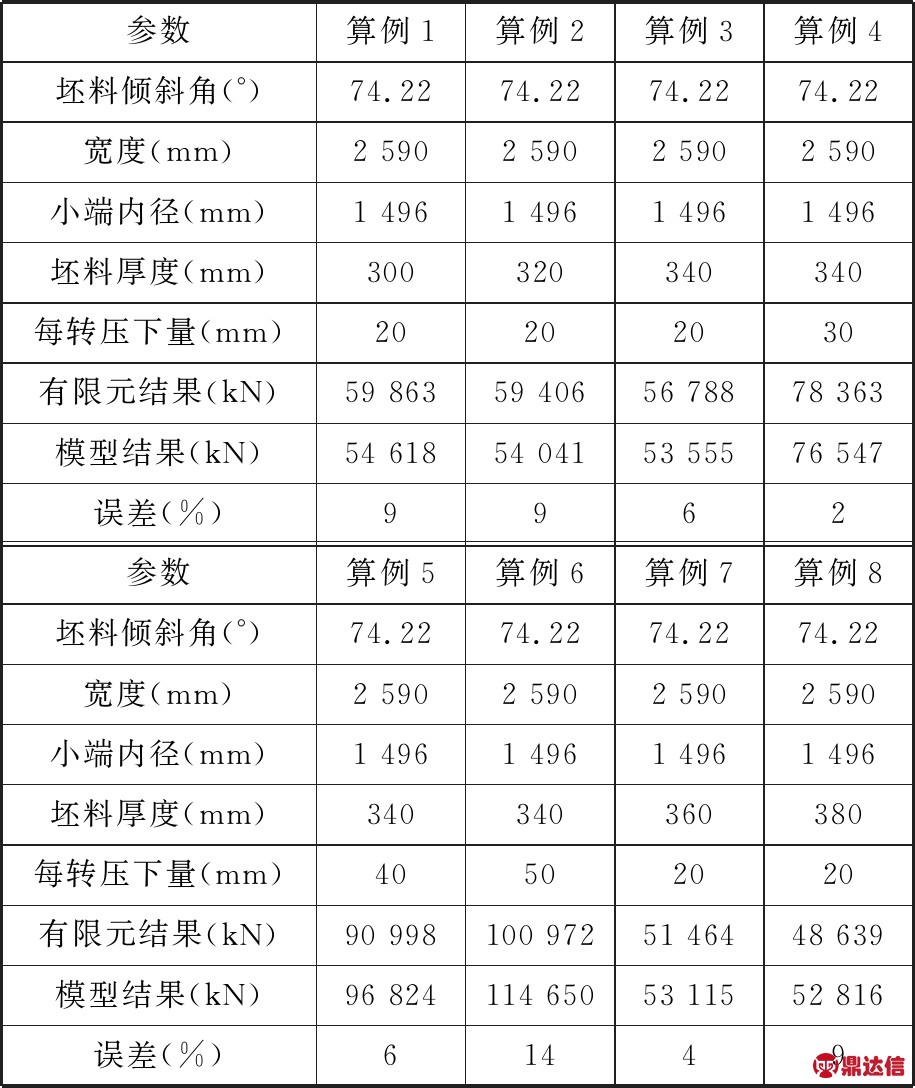
图6是不同压下量时力学模型计算总轧制力和有限元模拟计算的总轧制力的对比图。由图6可知,每转压下量由20 mm增加到60 mm时,总轧制力力学模型计算结果由53 555 kN增加到129 600 kN,ABAQUS有限元模拟计算结果由56 788 kN增大到108 390 kN,两者变化趋势相同,都呈现增大趋势。ABAQUS有限元模拟计算总轧制力变化存在波动,这与网格划分有一定的关系,并且误差在允许范围之内。力学模型和ABAQUS有限元模拟计算结果误差保持在20%以内,并且在实际轧制过程中轧制力是随着每转压下量增大而增大,从而可以相互印证本文所建立的轧制力力学模型与有限元轧制模型的正确性。
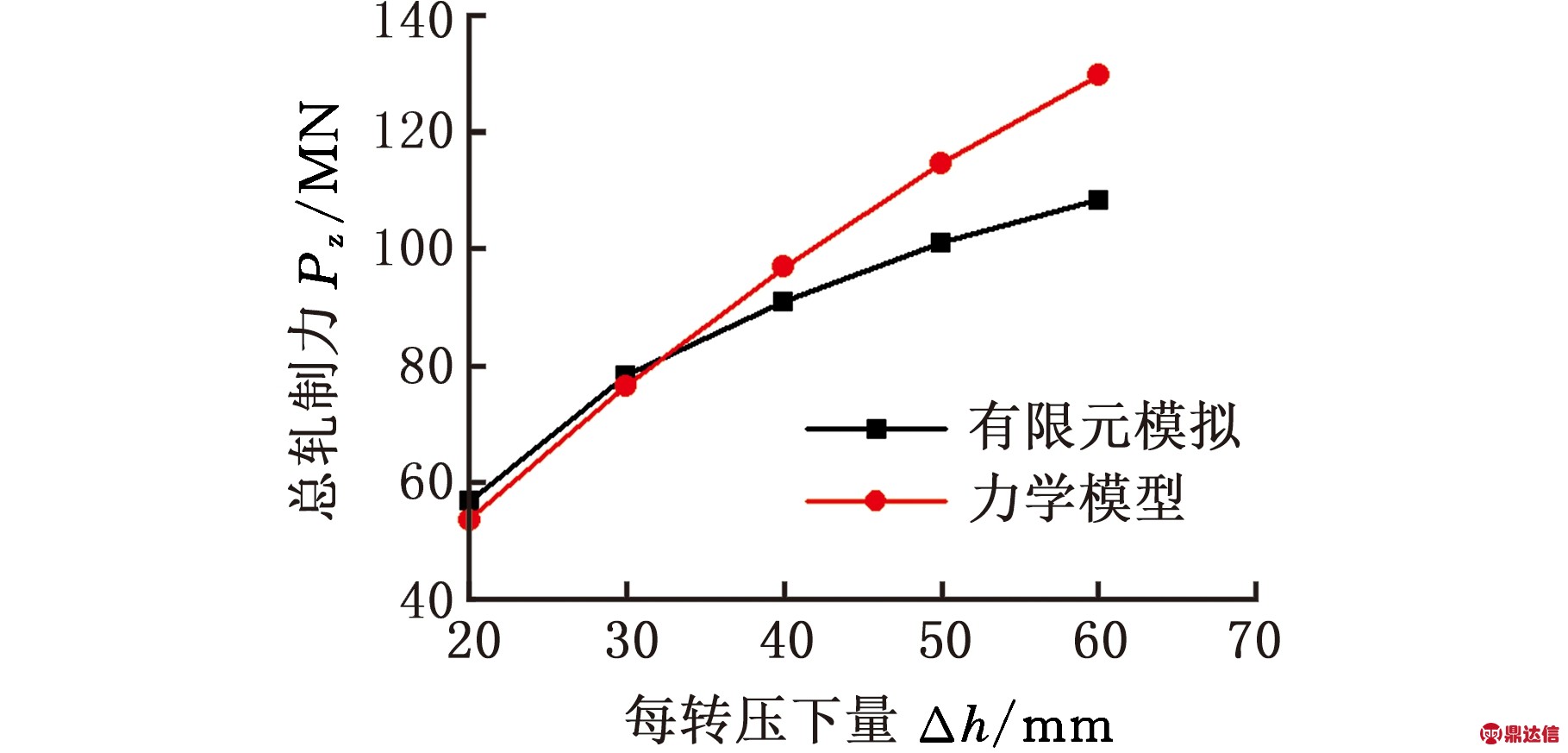
图6 总轧制力随每转压下量的变化
Fig.6 Change of total rolling force with reduction
per rotary pressure
图7是不同厚度、相同压下量情况下,力学模型和有限元模拟计算结果对比图。由图7可知,在轧制过程中,大型锥形坯料厚度由300 mm增大到380 mm时,总轧制力力学模型计算结果由54 618 kN减小到52 816 kN,ABAQUS有限元模拟计算结果由59 863 kN减小到48 639 kN,两者变化趋势相同,都呈现降低趋势,同样ABAQUS有限元模拟计算总轧制力变化存在波动,但误差在允许范围之内。力学模型和ABAQUS有限元模拟总轧制力计算结果误差保持在20%以内,并且在实际轧制过程中轧制力是随着坯料厚度增大而减小,从而可以相互印证本文所建立的轧制力力学模型与有限元轧制模型的正确性。
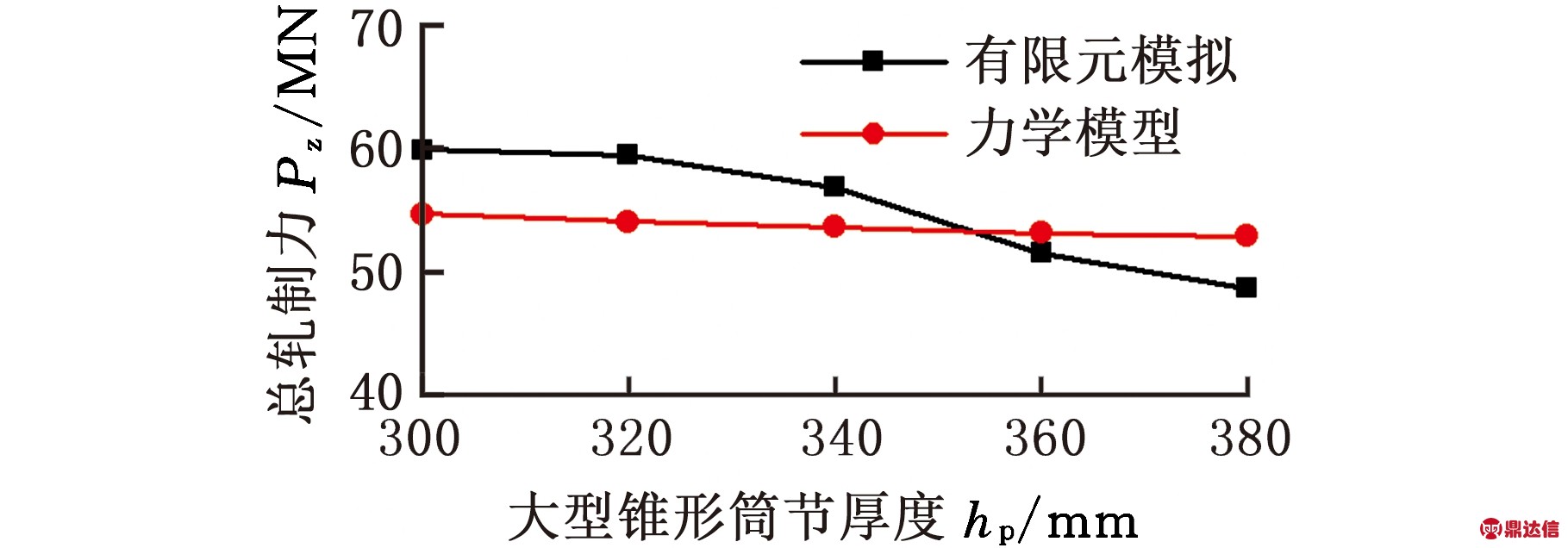
图7 总轧制力随筒节厚度的变化
Fig.7 The variation of total rolling force with the
thickness of barrel joint
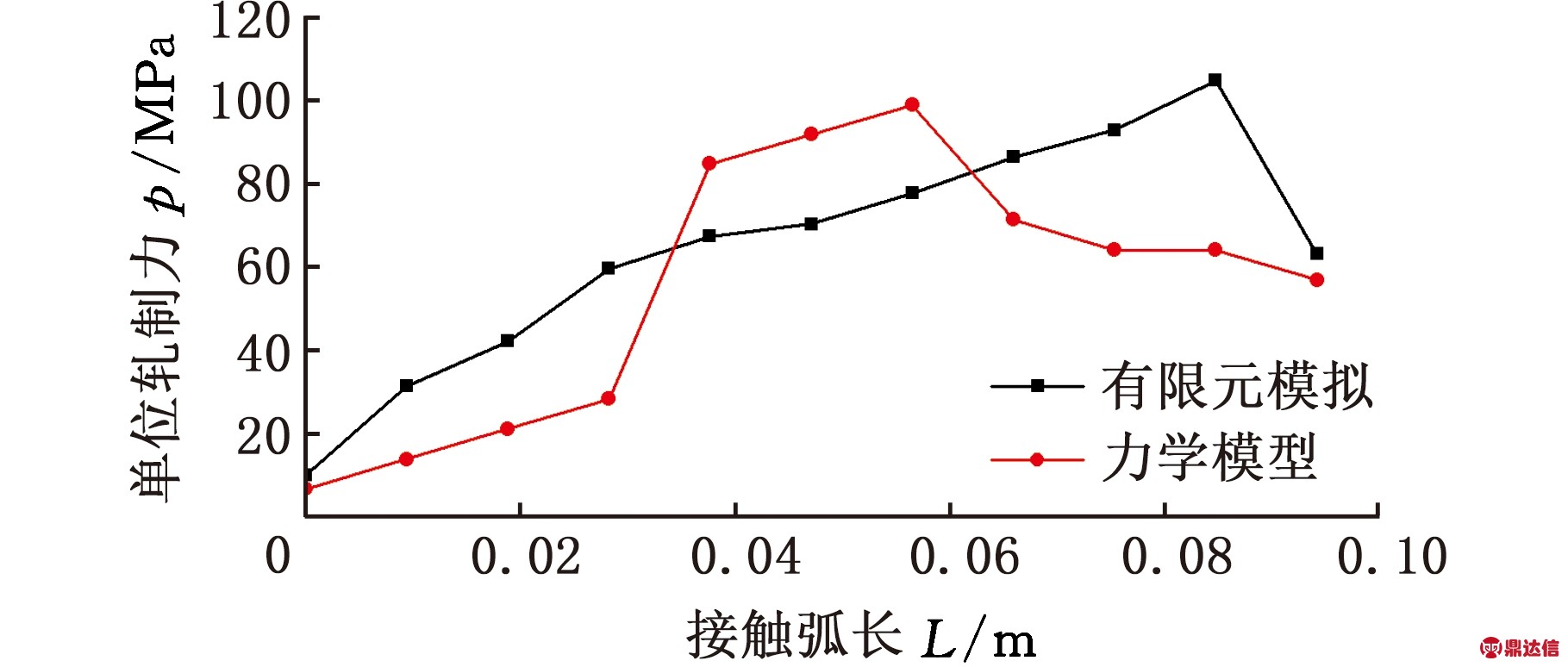
图8 力学模型单位轧制力分布
Fig.8 Mechanical model unit rolling force distribution
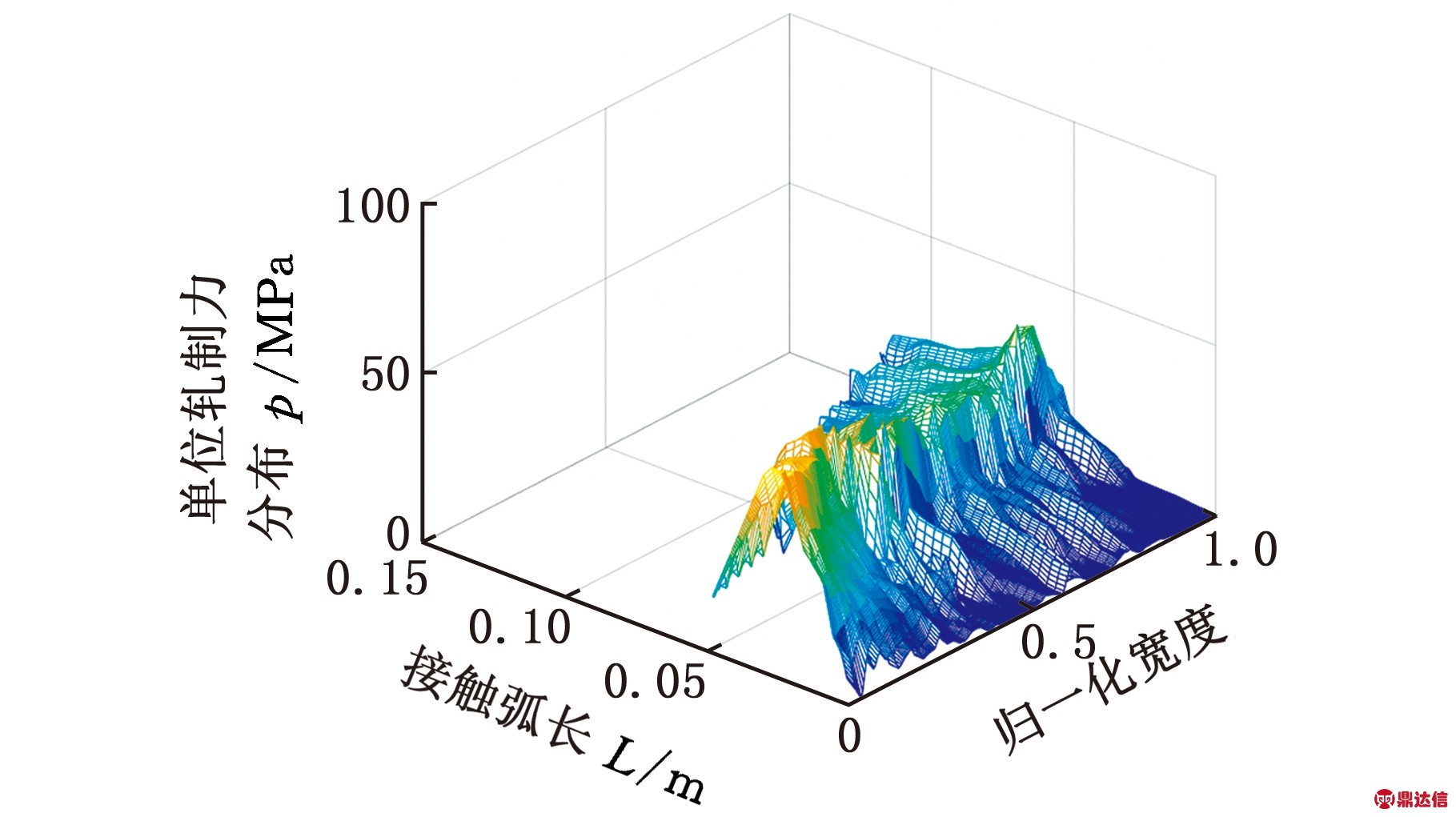
图9 有限元模拟单位轧制力分布
Fig.9 Finite element simulation of rolling force
distribution per unit
图8所示是采用轧制力力学模型计算的大型锥形筒节轧制变形区单位轧制力分布。图9所示是采用ABAQUS有限元模拟得到的轧制变形区单位轧制力分布。由图8和图9可知,模型计算结果和有限元计算结果总体变化趋势是一致的,单位轧制力在宽度方向上由锥形筒节小端到大端逐渐减小,小端面最大单位轧制力在98 MPa左右,大端面最大单位单位轧制力为62 MPa左右;接触弧长从小端到大端逐渐增大,最小端接触弧长在0.6 m左右,最大的接触弧长在0.11 m左右。在轧制变形区沿接触弧方向上单位轧制压力先增大后减小,在搓轧区轧制力变化平缓,最大单位轧制压力出现在靠近出口端的后滑区。
选取力学模型和有限元模型同一位置层,进行单位轧制力对比,如图10所示。两者单位轧制力分布趋势基本一致,最大单位轧制力均为靠近出口端的后滑区和搓轧区,单位轧制力力学模型为100 MPa,有限元模型为103 MPa,有较小的误差,说明所建立的力学模型与有限元计算模型有较高的精度。
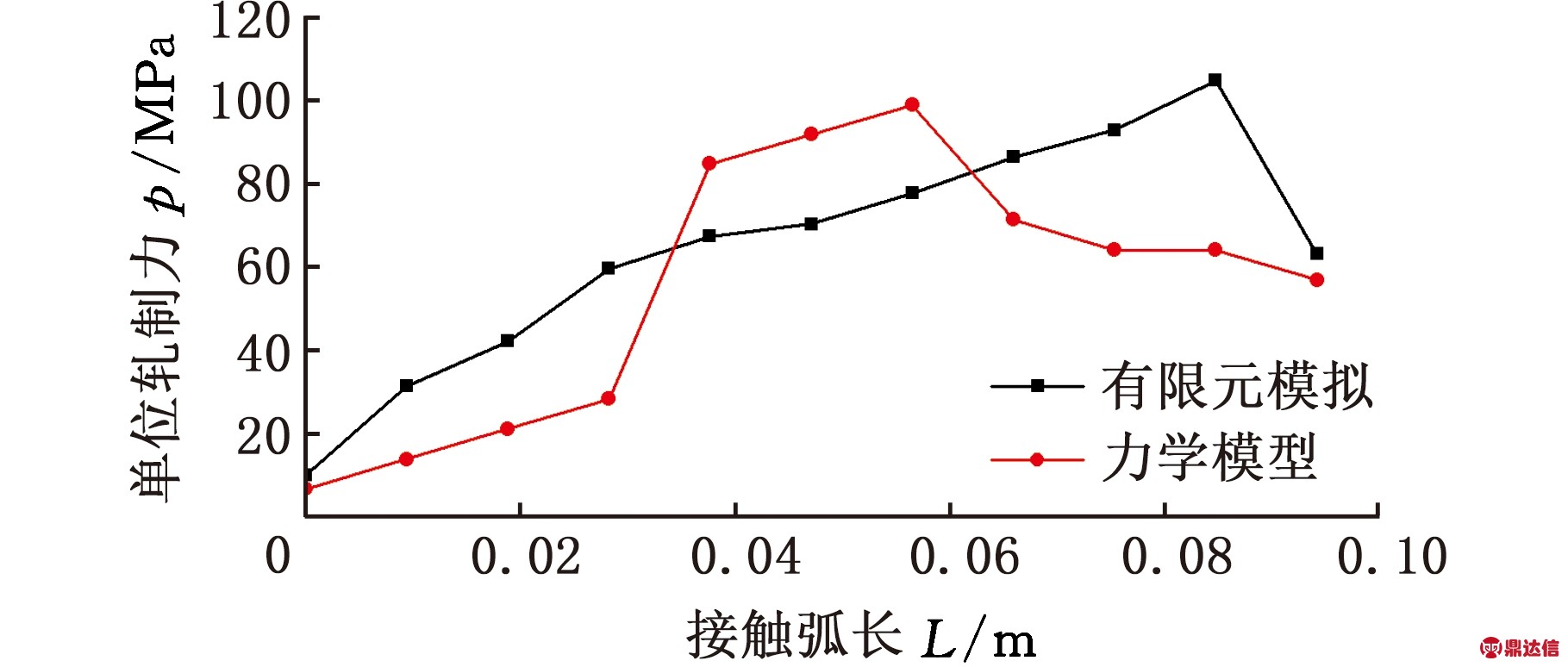
图10 接触弧长方向单位轧制力
Fig.10 Unit rolling force distribution in contact arc
length direction
图11所示是不同芯辊和外辊转速比下的总轧制力。由图11可知,当n2/n1<1.25和n2/n1>1.6时,力学模型与有限元模拟计算结果误差较大,有限元计算结果波动范围大,说明该范围内轧制过程稳定性差、轧制失稳;当1.25<n2/n1<1.6时,力学模型与有限元模拟计算结果趋势相同,误差较小,转速比对轧制稳定性影响较大,为了保证轧制稳定进行,转速比要在1.25~1.60范围内。
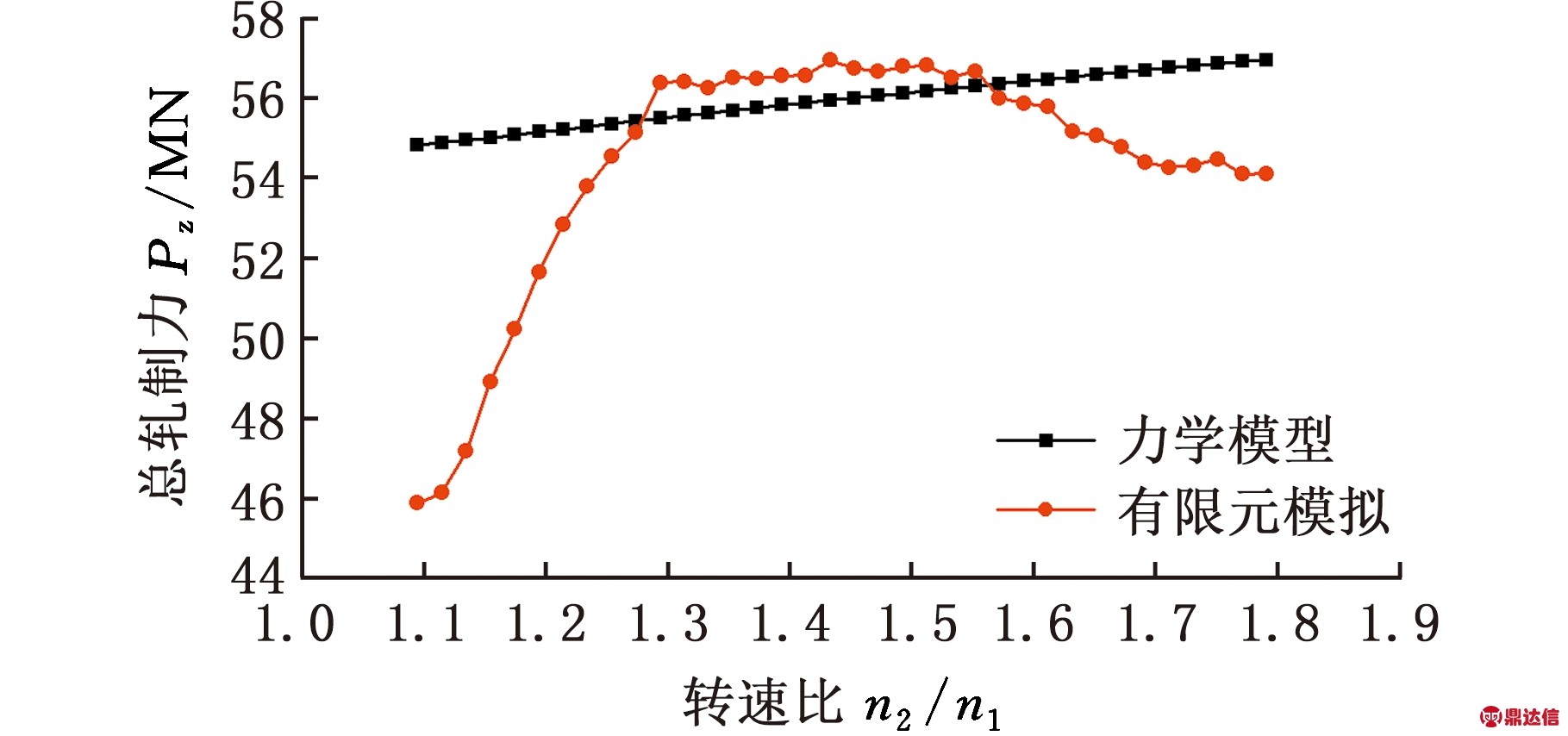
图11 不同芯辊和外辊转速比下的总轧制力对比
Fig.11 Comparison of total rolling force under
different rotational speed ratios of core roll to
outer roll
4 结论
本文针对大型锥形筒节轧制过程,提出一种微分分层方法,结合主应力法,建立了大型锥形筒节轧制过程轧制力力学模型,计算得到了大型锥形筒节总轧制力的计算公式以及变形区轧制力分布状态;同时在目前无法进行实验的条件下采用ABAQUS有限元模拟大型锥形筒节轧制过程,对比分析计算结果,力学模型计算结果与有限元仿真结果误差在20%以内,有较高的精度;根据力学模型和有限元计算结果分析了大型锥形筒节轧制变形区单位轧制力三维分布规律,单位轧制力在宽度方向上由锥形筒节小端到大端逐渐减小,接触弧长从小端到大端逐渐增大,在轧制变形区沿接触弧方向上单位轧制压力先增大后减小,在搓轧区轧制力变化平缓,最大单位轧制压力出现在靠近出口端的后滑区;在有限元模拟的基础上进行芯辊与外辊转速比对轧制力和轧制稳定性的影响研究,得出保证锥形筒节轧制稳定运行的转速比范围区间为1.25~1.60。