摘要 发动机的最大缸盖跳跃量是影响气缸盖垫片密封性能的关键参数。为此,提出一种在全负荷耐久、冷起动和热冲击工况下最大缸盖跳跃量的实测方法,用于分析气缸盖垫片密封系统的密封性能,以检验气缸盖垫片设计的合理性,为气缸盖垫片的设计提供更加准确可靠的依据。
关键词:气缸盖垫片 缸盖跳跃量 密封性
0 引言
为了满足日趋严格的汽车燃油耗及排放法规要求,小排量涡轮增压发动机逐渐成为各大主机厂的重点开发机型。与此同时,双喷射、缸体分离式冷却、低摩擦等新技术的应用使发动机的升功率得以大幅度的提升,随之而来的是更大的爆发压力和更高的温度,这无疑给气缸盖垫片的密封能力提出了更高的要求。
发动机的气缸盖垫片位于缸体和缸盖之间,与缸体、缸盖、缸盖螺栓等零件共同构成了发动机的气缸盖垫片密封系统[1]。其功能是保证缸体与缸盖结合面的良好密封,对其中的燃烧室、油道和冷却水道均起着密封作用;同时防止缸体外的异物进入缸体。气缸盖垫片的工作环境十分严苛,需要承受极高的、交变的机械负荷和热负荷。若气缸盖垫片密封失效,会造成燃气泄漏、油水混合等严重问题,甚至导致整机失效。因此,气缸盖垫片的有效设计对于发动机的产品开发尤为重要。
气缸盖垫片的有效设计是指在开发阶段所有的试验验证都能满足泄漏等级标准,量产后不引起客户抱怨。全负荷耐久试验,冷起动试验和热冲击试验是考核气缸盖垫片密封系统的3个主要验证项目[2]。全负荷耐久试验是在稳态的温度场下考核气缸盖垫片燃烧室密封筋的密封能力,防止燃烧室气体泄漏;冷起动试验是在低温场下考核发动机的起动能力和气缸盖垫片的密封性能;热冲击试验是在瞬态温度场下考核气缸盖垫片机油和冷却液密封筋的密封能力,以及其他与气缸盖垫片配合的零件(如缸体、缸盖、缸盖螺栓等)设计对气缸盖垫片密封性能的影响。根据热胀冷缩原理,在交变温度场下发动机缸体、缸盖及其他相关零件的形变量是不同的,而气缸盖垫片需要在各接口零件发生形变的情况下均起到密封作用。相较于全负荷耐久试验,冷起动试验和热冲击试验对气缸盖垫片密封系统的设计提出了更高的要求。
发动机缸盖的跳跃量和气缸盖垫片密封筋的密封力是影响气缸盖垫片密封能力的关键因素,也是气缸盖垫片密封系统设计的关键[3]。目前行业内对两者的研究大多使用有限元建模模拟分析,通过调整缸体法兰结构、气缸盖垫片支撑结构高度、缸盖螺栓数量和分布等相关设计参数得到最优气缸盖垫片设计[4-5]。本文提出一种实测上述3种试验工况下缸盖跳跃量的方法,为气缸盖垫片的设计提供更加准确可靠的依据。
1 气缸盖垫片密封原理和密封结构设计
1.1 密封原理
工作过程中,发动机温度会发生变化,根据物质热胀冷缩的原理,缸体和缸盖均会产生形变。同时,发动机点火时,燃烧室内的爆发压力会不断作用于缸盖上,使缸盖向上移动。因爆发压力产生的移动量和因热胀冷缩产生的形变量使缸体与缸盖之间产生一个离合间隙,这个离合间隙称为缸盖跳跃量。气缸盖垫片的设计过程中,线密封力的大小和密封筋压缩后的回弹区间都需要根据缸盖跳跃量来决定。
当缸盖螺栓拧紧后,螺栓轴向力使缸体和缸盖法兰压缩气缸盖垫片密封筋而产生回弹力,回弹力的反作用力作用于缸体和缸盖法兰上,且在发动机工作过程中始终大于被密封的介质压力,从而达到密封的效果。
气缸盖垫片密封筋的失效模式主要为开裂泄漏和间隙泄漏2种,如图1所示。前者是密封筋发生过大的压缩,回弹时产生的疲劳开裂,线密封力随之下降从而发生泄漏;后者是密封筋发生过大的塑性形变,密封筋回弹后的高度小于缸盖跳跃量或回弹后的线密封力小于介质压力,从而导致泄漏。
1.2 密封结构设计
采用1台3缸小排量涡轮增压汽油机作为研究对象,其气缸盖垫片主要结构设计如下:1)功能层,是垫片实现密封功能的主要结构,由3层厚度均为0.2 mm的不锈钢钢板组成,上面分布着全波纹和半波纹的密封筋;2)停止片,缸口区域激光焊接高度为0.15 mm的停止片,用于调整垫片的面压分布;3)支撑结构,带有一定高度的、基本不可压缩的硬筋,用于调整密封筋的压缩回弹量,提高密封筋的抗疲劳能力;4)全筋和半筋,全筋为密封缸内高温高压燃气的主要结构,半筋为密封机油和冷却液的主要结构;5)氟橡胶 (FPM),涂敷于与缸体、缸盖接触的功能层上下盖板,厚度为0.2 mm,用于弥补缸体、缸盖表面的粗糙度,起到微密封的作用;6)丁睛橡胶 (NBR),涂敷于垫片层间,防止层间磨损,同时有一定的微密封能力。
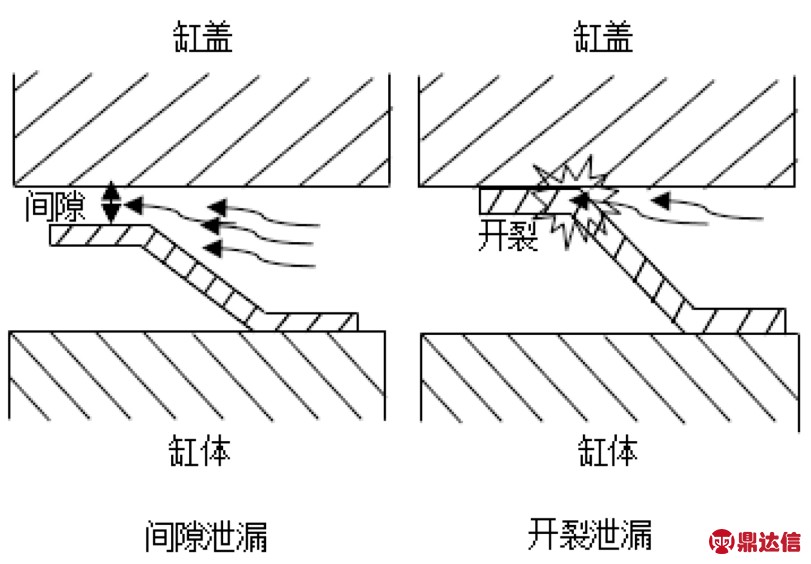
图1 气缸盖垫片密封筋失效模式
2 缸盖跳跃量试验分析
2.1 测量点选取
在专用台架设备上进行缸盖跳跃量试验,采用传感器来测量缸盖的跳跃量。
首先选取测量点,在测量点处打孔安装位置传感器。之后按照整机装配规范手工装配发动机,保证与当前生产的发动机一致性。测量点的选取应尽可能地反映气缸盖垫片密封筋附近的缸盖跳跃量。具体原则如下:1)根据气缸盖垫片计算机辅助工程 (computer aided engineering,CAE) 有限元分析结果,选取缸盖跳跃量较大的位置;2)根据前期工厂和售后表现,选取易出现密封问题的位置;3)保证发动机功能的完整性是试验的前提条件,所以测量点的位置不能离密封筋太近,避免打孔时造成密封筋贯穿,影响密封性能。结合以上3点,选取了8个点作为此次缸盖跳跃量的测量位置,如图2所示。以进气侧定位销孔为坐标原点,8个测量点的具体坐标如表1所示。其中5号测量点的传感器测量缸盖水平位移,其它7个测量点的传感器均测量缸盖垂直位移。设置1个水平位移测量点的原因是在爆发压力作用下,缸盖除了垂直方向跳动外亦在水平方向发生位移,使缸盖螺栓承受一定的剪切力;所以水平位移的监测对气缸盖垫片密封系统的设计也是具有一定意义的。
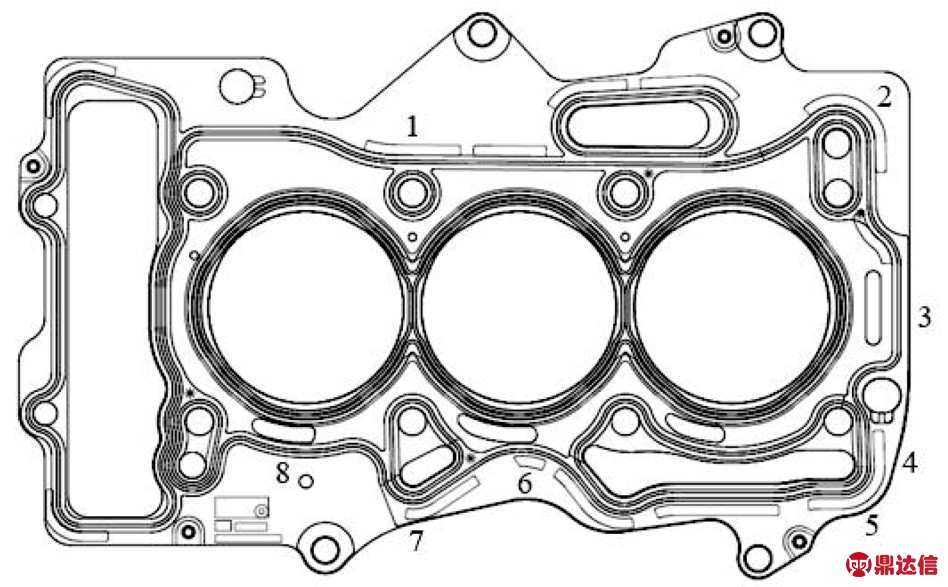
图2 缸盖跳跃量测量点位置
表1 缸盖跳跃量测量点坐标
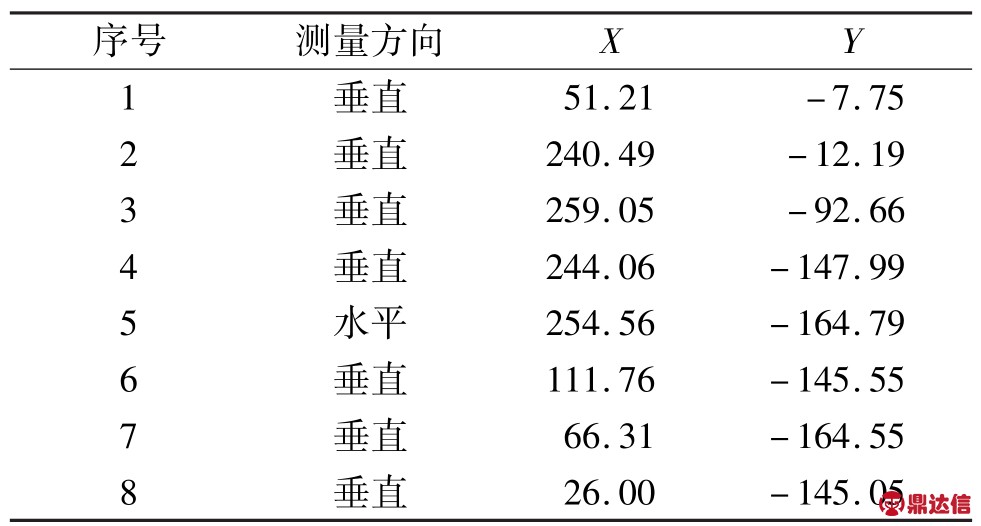
2.2 试验过程与结果分析
2.2.1 全速全负荷耐久试验
发动机全负荷,转速从1 200 r/min逐渐提高至5 500 r/min,转速增加速度为每90 s提高400 r/min。在转速为3 200 r/min,4 400 r/min和5 200 r/min时分别测量8个测量点的缸盖跳跃量,如图3所示。
观察数据可发现,各点的缸盖跳跃量均随着转速的增加而逐渐增大。同时,进气侧的缸盖跳跃量整体大于排气侧。由于排气侧温度较高,导致缸体和缸盖的变形量较大,缸盖跳跃量理应大于进气侧;但出现上述现象的原因是得益于支撑结构的设计。由于支撑结构是带有一定高度的、几乎不可压缩的硬筋,其支撑作用,导致密封筋的压缩量变小,回弹量随之变小,使得密封筋具有更加优良的抗疲劳能力。在气缸盖垫片的设计初期,就根据经验和CAE分析结果在不同的密封筋处设计了不同高度的支撑结构,排气侧高于进气侧,这使得密封系统的平衡被打破,排气侧拥有了更大的线密封力和更小的缸盖跳跃量。缸盖跳跃量的最大值出现在5 200 r/min时的2号测量点处,最大跳跃量仅为7.7 μm。因此,可以认为在全速全负荷工况下气缸盖垫片的缸盖跳跃量较低,安全符合设计要求。
2.2.2 冷起动试验
发动机在-40℃环境冷起动,全负荷工况运行,转速从1 200 r/min逐渐提高至5 500 r/min,转速提高速度分为慢速和快速2种,慢速为每90 s提高400 r/min,快速为每1 s提高616 r/min。分别测量8个测量点在这2种转速提高速率工况下的缸盖跳跃量,每种工况各测2组,得到如图4所示结果。
转速提高快慢与缸盖跳跃量的大小无直接关联,这是由于发动机始终处于全负荷状态,节气门全开,燃烧室爆发压力基本一致。缸盖跳跃量的最大值依然出现在2号测量点,最大值为21.6 μm。此外,转速提高速率对进气侧缸盖跳跃量的影响明显大于排气侧,这仍然得益于支撑结构的作用。对比冷起动试验数据和全速全负荷耐久试验数据,可以发现,相同的转速提高速率,冷起动的缸盖跳跃量明显大于常温起动,温度变化对缸盖跳跃量有较大影响。

图3 全速全负荷耐久试验缸盖最大跳跃量
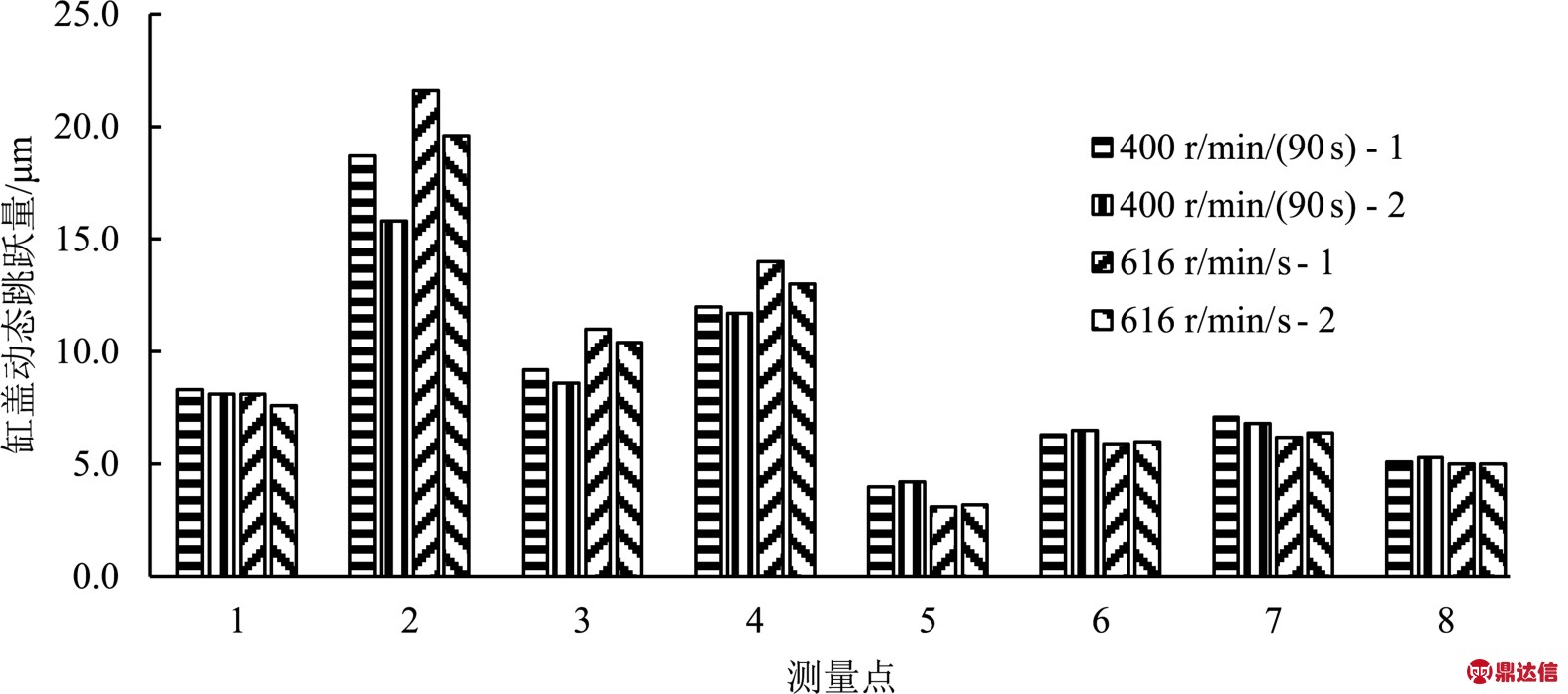
图4 冷起动试验缸盖最大跳跃量
2.2.3 热冲击试验
热冲击试验采用较复杂的循环工况,具体如下:1)发动机冷起动且达到全负荷后运行90 s,期间转速从1 200 r/min逐渐提高至5 500 r/min,然后进入升温过程,8 min后冷却液降温至初始温度,停机;2)发动机冷起动且达到全负荷后运行300 s,期间转速从1 200 r/min逐渐提高至5 500 r/min,然后进入升温过程,8 min后冷却液降温至初始温度,停机;3)发动机冷起动且达到全负荷后,转速以616(r/min)/s的速度从1 200 r/min逐渐提升至5 500 r/min,然后让冷却液逐渐升温至90℃,在此温度下继续运行8 min,随后冷却液降至室温,停机;4)发动机常温起动且达到全负荷后,转速以616(r/min)/s的速度从1 200 r/min逐渐提升至5 500 r/min,然后在90℃冷却液环境中运行8 min,随后转速逐渐降低至1 200 r/min;5)发动机在当前的运行状态下,运行90 s,期间转速从1 200 r/min逐渐提高至5 500 r/min,随后冷却液降温至冷起动状态,停机。
测量3组热冲击工况的缸盖跳跃量数据,如图5所示。
在热冲击工况下,3组缸盖跳跃量的测量值基本一致,最大的缸盖跳跃量为2号测量点的20.7 μm。进气侧的平均缸盖跳跃量仍然大于排气侧,与前文2个试验结果保持一致。
综合上述3个试验结果,发动机的最大缸盖跳跃量为2号测量点的21.6 μm,其它区域的缸盖跳跃量均不超过15 μm,符合气缸盖垫片的设计要求。
3 结论
(1)基于气缸盖垫片密封系统的设计理念,采用缸盖跳跃量作为评价指标可有效评定气缸盖垫片的密封性能,为降低气缸盖垫片泄漏提供了理论指导。
(2)缸盖跳跃量试验可用于实测不同工况下的缸盖最大跳跃量,可反映气缸盖垫片密封系统的设计是否合理,对气缸盖垫片密封系统的设计优化具有指导意义。

图5 热冲击试验缸盖最大跳跃量