摘要:目的研究消除蓄能器外壳底部冷挤开裂的预成形设计方案。方法对原成形工艺过程进行数值模拟,发现冷挤凹六角星时裂纹发生位置的损伤值较大。为消除底部凹六角星开裂问题,提出在原工艺温反挤成形阶段进行筒底凹六角星处的凹圆台预成形,以降低后续冷挤凹六角星时该区域的流动变形程度。结果通过具有不同圆台高度和凸台锥角的预成形设计方案成形过程的对比分析,给出了合理的凹圆台预成形设计方案。采用改进方案进行冷挤凹六角星时,裂纹发生处的损伤值显著降低,且筒底六角星区域的损伤值分布更均匀。结论采用预成形挤压方案可有效消除蓄能器外壳底部开裂,产品成品率达到 100%,生产质量得到了保证。
关键词:挤压;蓄能器外壳;开裂;预成形;数值模拟;损伤值
精密锻造作为一种少无切削加工技术,被广泛应用于工程机械行业的零件加工制造中。随着零件结构的复杂化以及加工精度要求的提高,单一锻造技术已经不能满足加工需要。温、热锻与冷加工复合的精密成形技术得到了迅速发展,这种加工方法主要解决了温锻和热锻成形精度不高,大规格产品冷锻成形设备能力不够和变形量制约的问题,大大降低了成形压力,且加工出的零件具有较高的尺寸精度和表面粗糙度。温、热锻与冷锻复合成形工艺成为汽车零部件制造业的重要发展趋势[1—5]。
蓄能器是汽车液压动力系统中的重要辅件,是一种能把压力油储存起来,待需要时将其释放出来的能量储存装置,对保证液压系统正常运作、改善其动态品质、保持工作稳定性、延长使用寿命等起着重要的作用[6—7]。蓄能器外壳主要应用于汽车自动变速器上,产品底部凹六角星处与外部零件连接,承受较大载荷,产品形状见图1c。
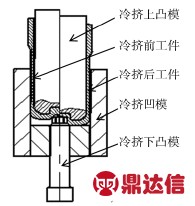
图1 蓄能器外壳温冷复合挤压工序
Fig.1 The diagram of warm and cold precision forging process of the accumulator shell
目前,蓄能器外壳一般采用较为先进的温冷复合成形工艺以取代传统的热锻及切削加工工艺进行生产。该产品的成形工艺流程如下:将圆棒料加热到850 ℃进行反挤产品内部型腔(见图1a);之后经退火和磷皂化处理,在常温下精整蓄能器外壳的外侧壁,见图1b;最后对产品进行底部凹六角星冷挤压成形,见图 1c。在底部凹六角星冷挤过程中,在凹六角星内切圆处顶角侧壁有时产生横向裂纹,导致废品率高达20%~30%,严重影响产品质量,蓄能器外壳底部凹六角星开裂见图2。
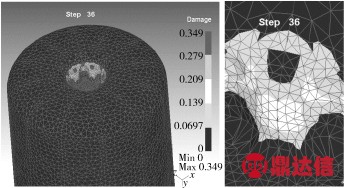
图2 蓄能器外壳底部凹六角星开裂
Fig.2 The crack of the accumulator shell's bottom concave hexagonal star
对蓄能器外壳产品的开裂问题进行研究,分析缺陷产生原因并通过工艺改进予以解决。目前数值模拟技术日渐成熟,通过有限元模拟软件对锻件加工工艺进行缺陷原因分析,进而优化改进零件的原有成形工艺,可有效解决锻件加工中的一系列成形问题[8]。对蓄能器外壳成形工艺进行有限元模拟,改善甚至消除底部凹六角星冷挤成形的开裂现象,可以提高蓄能器外壳产品温冷复合成形的质量和成品率,增加生产效益。
1 温冷挤成形过程模拟及开裂产生原因分析
为分析现有成形工艺产生开裂问题的原因,利用Deform-3D软件对冷精整工序和冷挤底部凹六角星工序进行有限元模拟分析,并以冷挤凹六角星后处理中的损伤系数作为损伤评判标准对成形工艺进行改进,以求消除底部凹六角冷挤成形时的开裂问题。
分别建立精整前工件、精整凸凹模和冷挤凸凹模型,并进行装配定位,导入到有限元软件Deform-3D中,冷精整工序的装配图见图 3,箭头所指方向为凸模运动方向。为了简化模拟计算过程,提高计算效率,同时考虑到底部凹六角的形状,选取模型的1/6进行模拟。坯料材质为Q345D,对坯料进行四面体网格划分,坯料和模具温度设置为常温20 ℃,选取剪切摩擦因数为0.12,凸模运行速度为60 mm/s,通过模拟发现,冷精整过程中不同成形阶段坯料的受力均匀,成形状况较好。
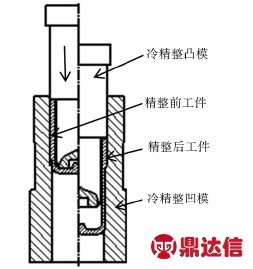
图3 冷精整装配
Fig.3 Cold sizing assembly diagram
继续进行冷挤凹六角星成形模拟,导入冷精整结束时的坯料和冷挤凸凹模,重新对坯料底部进行四面体网格细化分,冷挤凹六角星装配见图4。
在冷挤凹六角星过程中,不同成形阶段坯料的变形情况及成形结束时的损伤分布情况见图 5—6。由图6可看出,损伤最大值出现在内六角腔侧壁,与实际生产中侧壁出现的破裂位置相符合。因为冷挤凹六角星时局部变形量较大,同时,成形中材料变形抗力过大,导致此处材料流动损伤严重,实际生产中出现了拉裂。
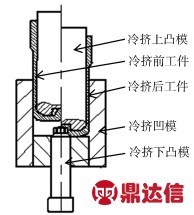
图4 冷挤压装配
Fig.4 Cold extrusion assembly diagram
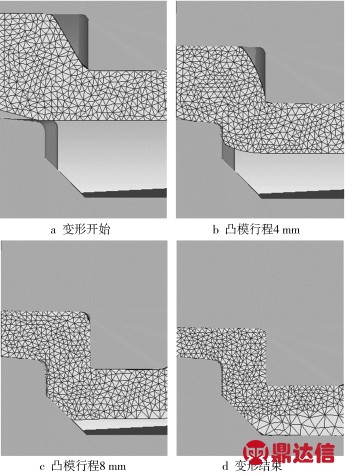
图5 底部凹六角冷挤变形过程
Fig.5 Cold extrusion deformation process of bottom concave hexagonal star
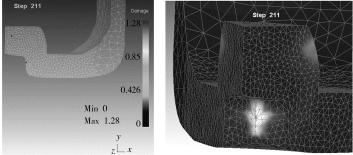
图6 冷挤过程结束时损伤分布及局部放大图
Fig.6 The diagram of damage distribution and partial enlargement at the end of cold extrusion process
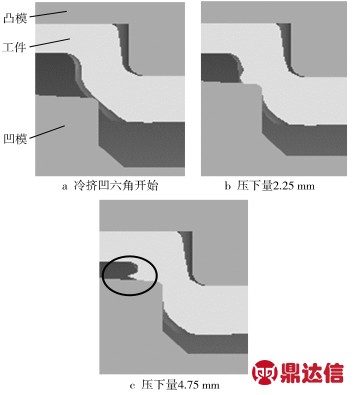
图7 冷挤凹六角过程
Fig.7 The schematic diagram of cold extrusion deformation process of concave hexagonal star
2 工艺改进方案
开裂是冷成形时常出现的缺陷之一。数值模拟获得的损伤值是反映锻件断裂倾向的重要物理量,损伤值越大,产生断裂的可能性就越大[9]。针对零件终锻成形力过大的问题,很多学者提出了先预锻后终锻的加工方法,合理分配材料的变形量来减小终锻的变形力,从而防止零件或模具结构的破裂,并通过不同预锻结构的有限元模拟结果对预锻毛坯进行了优化设计[10—12]。冀东生[13]在研究结合齿零件终锻齿形型腔底部拉应力过大的问题时,采用先预锻出空心孔状结构再进行终锻齿形的工艺方法,有效减少了终锻变形量及变形压力,以改善锻件成形均匀性为目标。邵勇等[14]提出了渐进结构优化的预成形设计方案。孟彬等[15]对汽车转向球铰壳体不同预成形件的形状进行了终成形模拟,得出了最优的预成形件形状。
为消除开裂,提出了底部凹六角的预成形改进方案,即将底部凹六角的成形分为2步,首先在坯料温反挤过程中预成形底部凹坑,然后在冷挤过程进行终成形。改进方案的目的是减小冷成形时底部材料一次成形的流动距离,减小冷变形程度及材料流动抗力,进而降低材料流动损伤,消除成形裂纹。
因预成形后坯料的形状将直接影响终成形件的成形质量,反挤过程中预成形底部凹坑形状设计不合理会导致冷挤压凹六角星时出现折叠和填充不足等缺陷。数值模拟发现,如果预成形的凹坑高度过大,在终成形凹六角时会发生折叠(见图7)。当凹圆台高度L2与终锻件凹六角对应区域的高度L1相等,即L2=L1时,不会出现折叠缺陷,故设计了不同锥角凸台和相同高度凹圆台的预成形形状。进行预成形设计时,应保证该区域材料在变形前后体积相等。
改进后的预成形凹六角的成形工序见图8。温反挤中,凹圆台高度L2与最终底部凹六角星入口斜边高度L1(图1c)保持一致,凹圆台的斜度β2与最终底部凹六角星入口斜度β1(图 1c)保持一致,同时为保证该区域材料在变形前后体积相等,在凸台高度不变的前提下,改变现有筒内底侧凸台斜角α1(图1a)为α2(图8a),改变凸台上表面直径d1(图1a)为d2(图8a)。
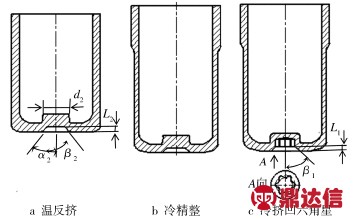
图8 改进的蓄能器外壳温冷复合挤压工序
Fig.8 The diagram of warm and cold precision forging process of the accumulator shell after improving
最终预成形反挤工序装配见图9,而终成形冷挤凹六角星的装配见图10。
模拟发现,在冷挤凹六角星时,不同筒内侧凸台锥角α2的预成形,会影响凹六角星的填充情况。α2在0°到20°之间取值,分别选取凸台锥角为19°,15°,10°,5°等 4种情况进行模拟,终成形结束后坯料的填充情况见图 11。随着凸台锥角的逐渐减小,凹六角星的填充越来越好,直至锥角为5°时,凹腔内实现完全充满,见图11d。不同凸台锥角预成形时冷挤凹六角星的损伤分布情况见图12。
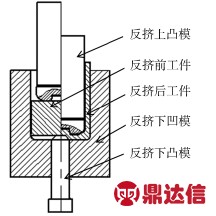
图9 改进方案的预成形反挤压装配图
Fig.9 Preform backward extrusion assembly diagram after improving
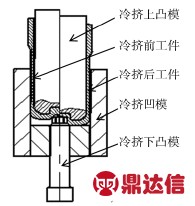
图10 改进方案冷挤压装配图
Fig.10 Cold extrusion assembly diagram after improving
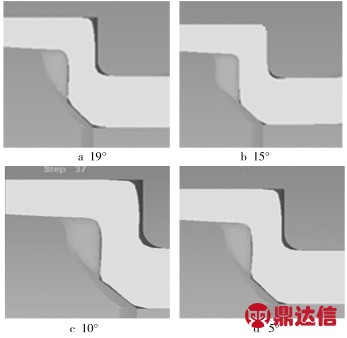
图11 不同凸台锥角预成形件在终成形结束时的填充情况
Fig.11 The filling situation of preform pieces of different convex cone angles at the end of the final forming
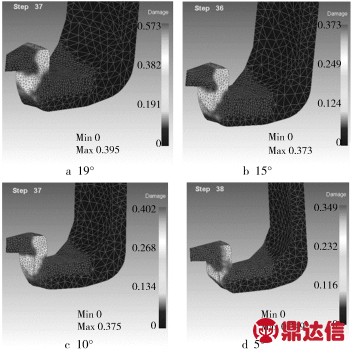
图12 不同夹角条件下终成形结束时损伤分布
Fig.12 The damage distribution under the conditions of different angles at the end of the final forming
由图 12可看出,4种情况的终成形过程中损伤系数均较小,但当夹角为5°时,成形过程的损伤系数最小为0.349,工艺改进后冷挤损伤分布见图13。
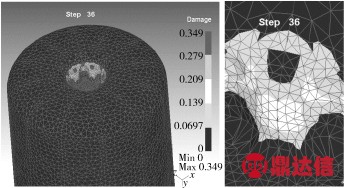
图13 工艺改进后冷挤损伤分布
Fig.13 The damage distribution diagram of cold extrusion after process improvement
由图6可以看出,原工艺方案中,材料损伤系数最大为1.28,位于内腔侧壁,且分布较为集中,最大点附近的损伤值急剧下降,变形不均匀,容易造成腔壁开裂。改进后的工艺方案损伤系数最大值为0.349,且分布较为均匀。可见改进后的工艺方案,冷挤凹六角星的成形情况会得到显著改善。
采用改进方案冷挤凹六角,蓄能器外壳的开裂问题得到消除,成品率可达 100%,冷挤后锻件成品见图14。
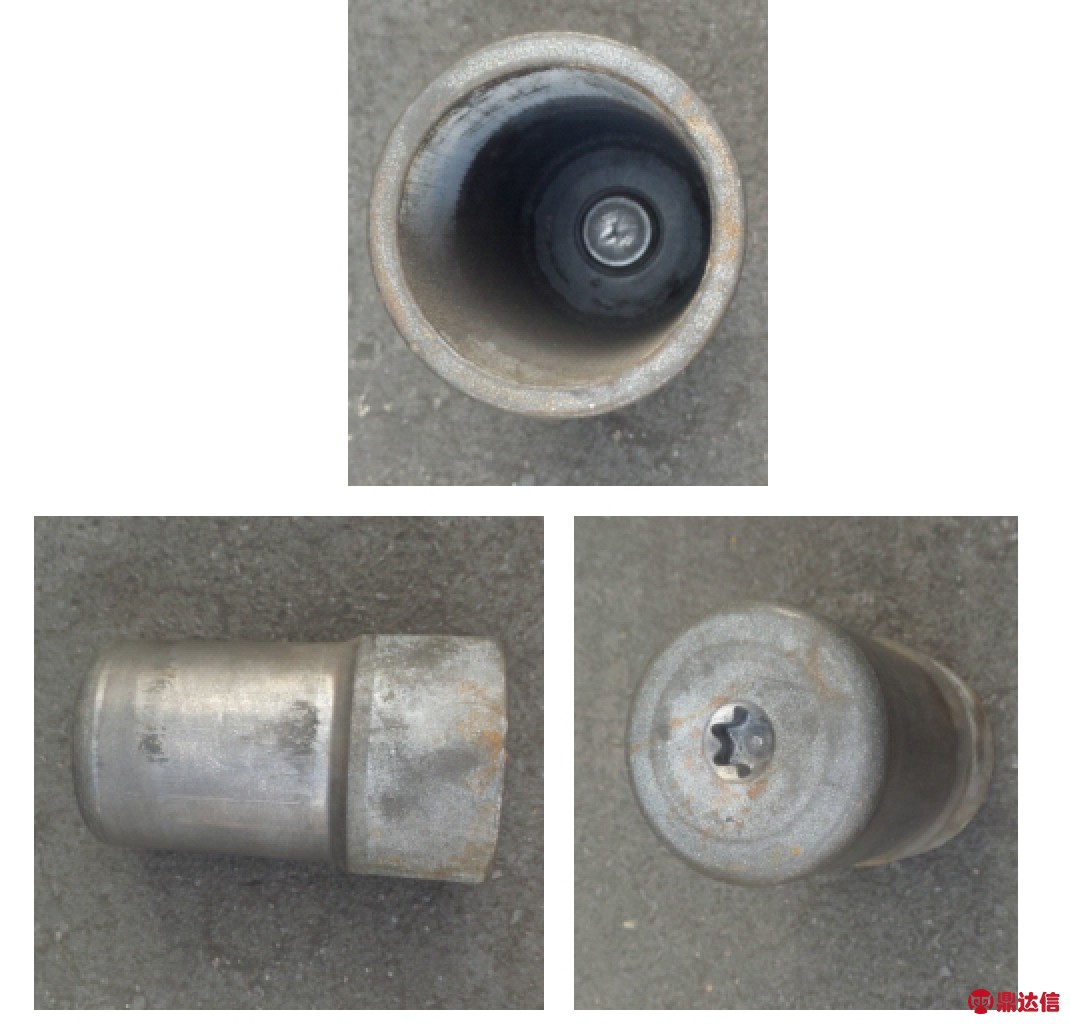
图14 蓄能器外壳锻件冷成形后的成品
Fig.14 The finished product of accumulator shell forgings after cold forming
3 结论
1)通过对蓄能器外壳温反挤与冷成形过程进行模拟发现,冷挤凹六角成形损伤值最大处与实际生产中的开裂位置相符,说明可以通过改进凹六角星区域的材料变形流动状态解决开裂问题,提出了温成形工序进行预成形底部凹坑的改进方案。
2)通过对具有不同圆台尺寸的预成形设计方案进行成形过程模拟分析,最后给出了合理的凹圆台预成形设计方案。采用改进方案进行冷挤凹六角星时,裂纹发生处的损伤值由原来的1.28降到0.349,且筒底六角星区域的损伤值分布更均匀。
3)将改进方案应用于实际生产,消除了原蓄能器外壳冷挤底部凹六角星开裂问题,成品率达100%。