摘 要:本文针对板坯连铸机结晶器振动液压伺服系统跟随精度不高且回油管道存在振动的工况,通过对回油蓄能器参数进行分析,采用Matlab\<FounderNode name="KG" value="-0.1mm"/>Simulink仿真软件建立了该振动液压伺服系统的控制模型,并对该模型进行了仿真分析及现场试验,验证了回油蓄能器参数选取的正确性及控制模型参数设置的合理性。
关键词:连铸;结晶器液压振动;液压伺服控制;蓄能器
0 前言
现代连铸技术的快速发展,几乎所有的结晶器振动均采用液压振动方式。与传统的结晶器机械振动方式相比,液压振动具有结构简单、布置灵活、精度高、响应快、振动参数设定和调整方便等优点,并且无需对机械设备进行调整即可在线进行正弦和非正弦振动方式的实时切换,以及振幅、振频、非正弦参数的调整,完全满足连铸工艺的需要。
结晶器液压振动参数根据工艺的要求能在线调整,合理的振动参数能有效减少铸坯与结晶器的摩擦力,从而减少铸坯振痕、提高铸坯质量和金属收得率。振幅、频率作为结晶器液压振动的两项重要参数,通常用振动系统的跟随性能来表示该参数,用来表征结晶器振动液压伺服控制系统的振动性能等级。
本文将对结晶器振动液压伺服控制系统进行建模及仿真,并对该仿真结果进行现场实验,以期使振动性能达到最佳效果,通过实验,证明了该模型的正确性以及液压伺服系统蓄能器参数设置的合理性。
1 结晶器振动液压伺服模型的研究
结晶器振动液压伺服控制系统分为四部分,包括结晶器振动液压伺服机械结构、振动液压系统、连接管路、蓄能器。分别建立它们的模型,并通过流体连续性方程把它们联系起来,得到结晶器振动液压伺服控制系统的模型。
1.1 结晶器振动液压伺服机械结构
如图1所示,连续浇注用结晶器1安装并固定在两个振动单元体2上,该振动单元体2由振动液压缸装置3驱动,通过控制两台振动液压缸装置3的伺服振动曲线能实现结晶器1的正弦或者非正弦运动。
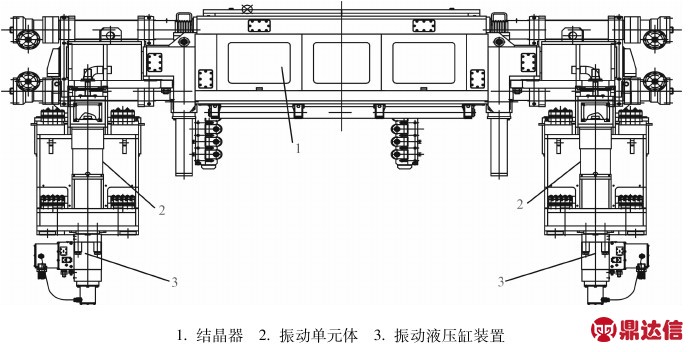
图1 结晶器液压振动伺服机构
Fig.1 Mechanical structure of mold servo oscillator
1.2 结晶器振动载荷分析
结晶器振动液压伺服液压缸所承受的载荷有:坯壳与铜板之间的摩擦力WK,振动体的惯性力PMA,振动体自重G,振动单元体板弹簧及缓冲弹簧的反力F,如果结晶器具备在线热调宽功能则还需要考虑结晶器调宽时在窄边铜板上产生的拉坯阻力FS。
(1) 坯壳与铜板之间的摩擦力WK。钢液静压力作用在结晶器宽边铜板和窄边铜板上的力为

式中,B为结晶器内钢水最高液面处的铸坯宽度,cm;D为结晶器内钢水最高液面处的铸坯厚度,cm;γ为钢液重度,取7 g/cm3;f为铜板和铸坯之间的摩擦系数,一般取0.5。
(2) 振动体的惯性力PMA。
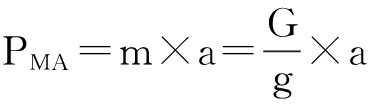
式中,G为振动体的重量(包括结晶器本体、冷却水、振动单元体振动部分的重量),kg。
(3) 振动体的自重G。
G=G1+G2+G3
式中,G1为结晶器本体重量,kg;G2为结晶器内冷却水的重量,kg;G3为振动单元体振动部分的重量,kg。
1.3 蓄能器模型
(1) 蓄能器的流量方程。设蓄能器的进油阀末端的流量为q,即油腔油液流量变化和蓄能器气腔体积变化有
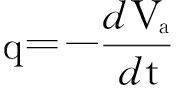
式中,Va为密封气体的某一时刻气体体积,m3;负号表示气腔体积变化和油液流量相反。
(2) 蓄能器的流量连续性方程。每增加单位压力,流体体积所产生的相对压缩量称为压缩系数,压缩系数表达式为
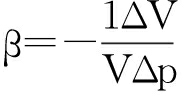
式中,β为油液压缩系数;V为流体原体积,m3;ΔV为体积减少量;Δp为压力增量,由于压力增加时油液体积减少,两者变化相反,所以前面加负号。
压缩系数的倒数称为体积弹性模量,体积弹性模量为
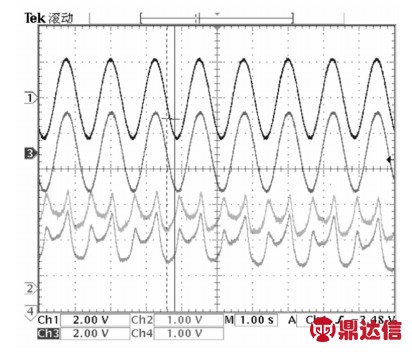
所以蓄能器内的流量连续性方程为
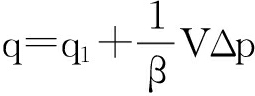
式中,q1为流进或排出蓄能器的流量。
(3) 蓄能器内油液的力平衡方程。

式中,Aa为油腔的截面积,m2;ma为油腔流体质量,ma=ρVb;Va为蓄能器内气腔气体体积,m3;Vb为蓄能器内油腔里油液体积,m3;qa为油腔油液流速;Ba为油腔中的阻尼系数,Ba=8πμ1lba;μ1为油液的动力粘度;Ka为气体的弹簧刚度;Ca为气体阻尼系数,,μ2为气体的粘度系数。
(4) 气体状态方程。气体的压力、体积和温度是理想气体的重要参数,这三个参数可以完整地描述气体的状态。
对一定质量的理想气体,其状态方程为
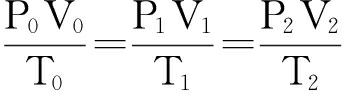
式中,P0、P1、P2分别为充气压力、最高工作压力、最低工作压力,Pa;V0、V1、V2分别为蓄能器气囊的总容积、最高工作压力时对应的气囊总容积、最低工作压力时对应的气囊总容积,m3;T1、T2、T3分别为充气时、最高工作压力时和最低工作压力时所对应的气体热力学温度。
2 仿真分析
2.1 结晶器振动液压伺服系统回油蓄能器控制模型
结晶器振动液压伺服系统回油蓄能器模型的仿真是利用Matlab\<FounderNode name="KG" value="-*8"/>Simulink仿真软件来实现的,Simulink仿真软件提供了各类可用于控制系统仿真的模块,支持各种机、电、液耦合控制系统的建模与仿真研究。
图2所示为根据上述推导并在MatlabSimulink软件下建立的结晶器振动液压伺服系统回油蓄能器模型。图3为伺服阀后部回油管路的仿真模型。
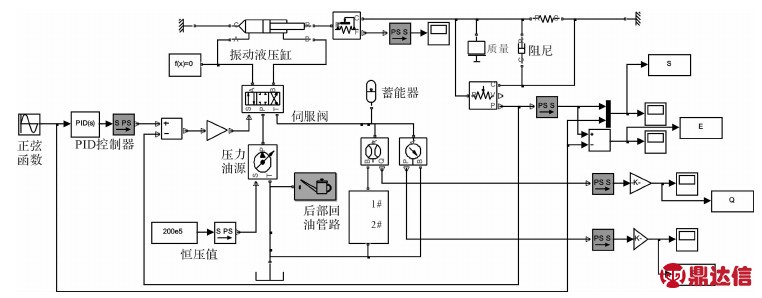
图2 结晶器振动液压伺服系统回油蓄能器模型
Fig.2 Oil return accumulator model of mold servo oscillation system
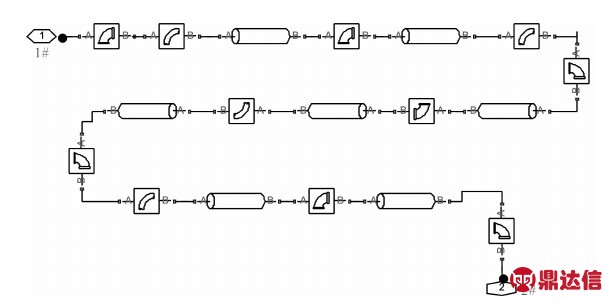
图3 伺服阀后部回油管路仿真模型
Fig.3 Return line model at end of servo valve
结合结晶器液压振动液压缸的载荷分析及计算公式,代入结晶器液压振动模型的相关参数,可以得出结晶器液压振动用回油蓄能器参数的结果,在Matlab\<FounderNode name="KG" value="-*8"/>Simulink软件环境下,对结晶器振动的载荷进行构建并赋值。该项目实际液压系统中,假设高压油源完全能满足系统使用要求,所以在模型中压力源选用恒压模块;伺服阀选用MOOG公司的某系列伺服阀产品。该系统在控制过程中属于线性定常系统,在控制模型中采用普通PID参数控制,在建立模型的基础上,对PID参数进行修正,观察系统的响应,使控制系统的动、静态特性满足设计要求。
2.2 仿真分析
结晶器液压振动作为连铸机最核心的设备,能大大提高板坯的表面质量,同时有利于铸坯的脱模,防止连铸机发生粘接的漏钢事故。结合结晶器振动液压伺服回油蓄能器的仿真模型,在Matlab\<FounderNode name="KG" value="-*8"/>Simulink软件下对液压伺服回油中无回油蓄能器,有回油蓄能器且考虑蓄能器的安装位置、蓄能器的工作参数等情况作仿真分析。
2.2.1 无回油蓄能器的仿真分析
图2所示的结晶器振动液压伺服系统回油蓄能器模型中,关闭回油蓄能器的相关参数,即结晶器振动液压伺服中无回油蓄能器,且分别输入振幅3 mm、频率3 Hz;振幅4 mm、频率6 Hz两组参数,整定P(比例)系数、I(积分)系数,系统的响应分别如图4、图5所示。该仿真结果表明:在伺服振动回油管路上没有安装蓄能器时,振动曲线不能很好地跟随输入值,而且振幅/频率越大,振动曲线越失真。
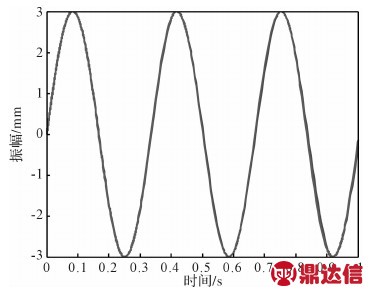
图4 振幅3 mm、频率3 Hz时系统响应特性
Fig.4 System response characteristics at 3mm amplitude, 3Hz frequency
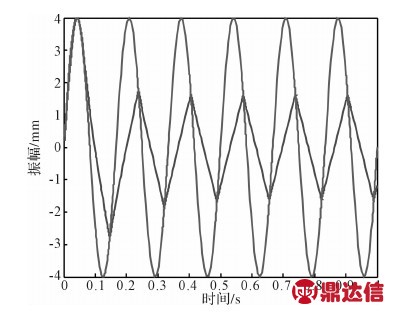
图5 振幅4 mm、频率6 Hz时系统响应特性
Fig.5 System response characteristics at 4mm amplitude, 6Hz frequency
2.2.2 有回油蓄能器的仿真分析
图2所示的结晶器振动液压伺服系统回油蓄能器模型中,设置回油蓄能器的相关参数,即结晶器振动液压伺服中设置有回油蓄能器,设定振幅4 mm、频率6 Hz,蓄能器容积为1 L,且分别输入回油蓄能器的充气压力为0.05 MPa、0.15 MPa、0.2 MPa、0.5 MPa、1.0 MPa,整定P(比例)系数、I(积分)系数,系统的响应如图6所示。该仿真结果表明:在伺服振动回油管路上设置有蓄能器时,选择合适的充气压力,振动曲线能较好地跟随输入值,随着充气压力的增大,振动曲线逐渐失真,在0.15~0.2 MPa之间能较好地满足要求。
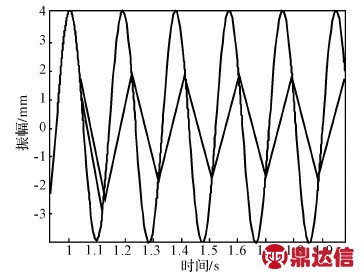
图6 不同充气压力时系统响应特性
Fig.6 System response characteristics at different air charging pressure
在图2所示的结晶器振动液压伺服系统回油蓄能器模型中,设定振幅4 mm、频率6 Hz,蓄能器充气压力为0.2 MPa,且分别输入回油蓄能器的容积为0.5 L、1 L、2.5 L、5 L、10 L,整定P(比例)系数、I(积分)系数,系统的响应如图7所示。该仿真结果表明:在伺服振动回油管路上设置有蓄能器时,选择合适的容积,振动曲线能较好地跟随输入值,随着容积的减小,振动曲线逐渐失真,考虑到经济性,选用2.5 L能较好地满足要求。
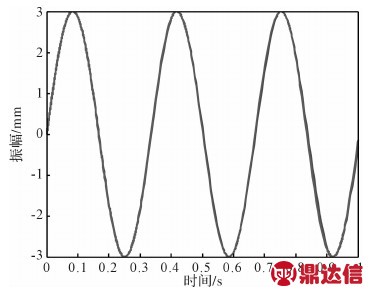
图7 不同容积时系统响应特性
Fig.7 System response characteristics with different volume
图2所示的结晶器振动液压伺服系统回油蓄能器模型中,设定振幅4 mm、频率6 Hz,蓄能器充气压力为2×105 Pa,容积为2.5 L,分别将回油蓄能器设置在图3的中部及后部位置(远离伺服阀),整定P(比例)系数、I(积分)系数,系统的响应如图8所示。该仿真结果表明:在伺服振动回油管路上设置有蓄能器时,回油蓄能器的位置影响着系统的响应特性,蓄能器远离伺服阀,则振动曲线逐渐失真。
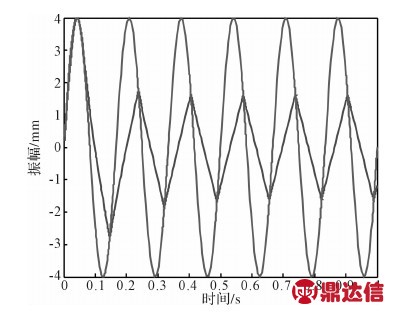
图8 蓄能器位置不同时系统响应特性
Fig.8 System response characteristics in accumulator different position
3 试验研究
在实验室对结晶器振动进行试验分析,组建的振动机械结构如图9所示。在实验过程中,结合对结晶器的载荷分析及借助上述的仿真结果对试验进行指导。
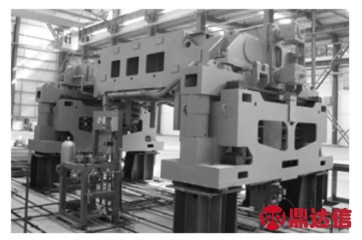
图9 结晶器振动试验装置
Fig.9 Testing device of mold servo oscillator
图10为对应的结晶器振动试验过程中,回油蓄能器容积为2.5 L、充气压力0.2 MPa、位置靠近伺服阀所采集的实际振动曲线,图中通道1为系统的输入值,通道3为实际振动曲线,从图中可以看出,该振动系统参数设置合理、振动曲线跟随性好,完全能满足控制要求。
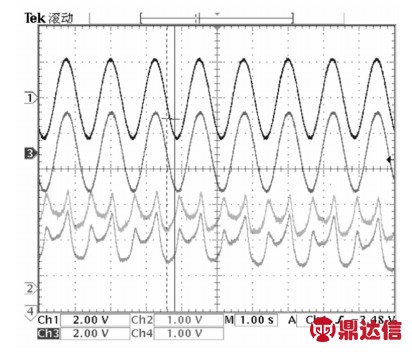
图10 结晶器振动实测响应曲线
Fig.10 Practical feature response of mold servo oscillator
4 结论
(1) 结晶器振动液压伺服阀产生的流量脉动经过管路的作用,形成压力脉动并由此诱发的管道振动和噪音会对管网产生严重的破坏,这是由于伺服阀开关回油管路时,阀后回油管道产生大幅值压力脉动,其压力变化率越大,则引起的振动和噪音越强烈。
(2) 在伺服阀回油管道中并联设置蓄能器能有效消除由压力脉动引起的振动、噪声以及振动波形失真,同时能大大提高系统的振动跟随性能,提升动态特性品质。
(3) 考虑到经济性,设置的蓄能器容量适中即可,但要求惯性小反应灵敏且固有频率在几十赫兹以内,用于吸收低频压力脉动比较有效。
(4) 合理的选用蓄能器的容积、充气压力以及考虑伺服阀后部回油管道的设计是减少和控制液压冲击的有效方法。通常采用尽可能短的回油管路、减少弯头及增大管路的弯曲半径、蓄能器尽可能靠近伺服阀。