[摘 要]液压挖掘机动臂液压缸回缩时,重力势能转化成压力能,若该压力能得不到回收利用,则只能通过阀口节流等方式消耗掉,导致系统能量利用低且发热严重等问题。提出采用液压蓄能器对动臂势能进行回收,并设计了相应回收方案。在一定程度上增大蓄能器体积和初始压力将有助于改善动臂的速度控制特性和提高能量回收效率。
[关键词]液压挖掘机;蓄能器;能量回收;节能
液压挖掘机的节能降耗是近年来行业的关注热点。液压挖掘机动臂属于大惯量往复升降系统,当动臂下落时,势能将被转换成压力能,具有较大的节能潜力[1]。据统计,在6t液压挖掘机典型工况中,动臂系统所消耗能量占整机总能量的20%[2]。因此,回收动臂下放过程中的势能对挖掘机的节能具有非常重要的意义。
目前,液压挖掘机动臂势能回收方案可分为电气式、液压式和混合式等。自20世纪70年代起,基于液压蓄能器能量回收的技术方案开始逐渐得到应用。蓄能器回收储能与电气式或混合式相比,具有技术成熟,功率密度大、成本低等优点。因此,近年来,相关的企业和科研机构先后提出了若干种基于蓄能器能量回收技术的挖掘机节能方案[3-7]。针对动臂势能回收技术,美国卡特彼勒公司提出了一种方案,该系统中包含高压回路和低压回路,当动臂下放时,高压油通过液压阀流入液压蓄能器中进行存储,被存储压力能可提供给其他执行机构使用[8]。2012年,三一重工申请了一种油缸能量回收的专利技术,当油缸收缩时,油缸中压力油驱动定量泵/马达,定量泵/马达又驱动变量泵/马达,向蓄能器供油储能[9]。文献[10]对一种挖掘机重力势能回收系统的控制性能和节能性能开展研究,该回收系统主要包括动臂调速阀,模式切换阀、模式切换先导阀、蓄能器和再利用切换阀等组成。
本文在对某6t液压挖掘机进行深入分析的基础上,提出了一种基于进出口独立控制的动臂势能蓄能器回收系统,在该系统中利用三个电液比例阀和液压蓄能器实现动臂势能的回收,由于采用了电液比例控制技术,该方案还有助于改善提高系统的控制特性。
1 系统结构和原理
基于蓄能器的动臂势能回收系统结构原理如图1所示,该系统包括三个电比例阀(阀A、阀B和阀C)、液压蓄能器、若干压力传感器、流量传感器、位移传感器和控制器。
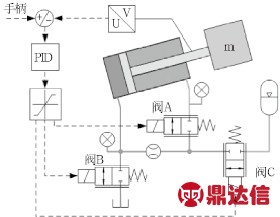
图1 动臂势能回收系统
该系统运行过程中采用流量再生和能量回收两种节能手段,在动臂下降时完全不用其他油源供油,因而不仅可对动臂下降势能进行回收,而且还可降低原动机的输出功率。
液压挖掘机采用速度控制方式,与操作者一起构成位置闭环,并且由于挖掘机工况复杂,要求速度控制器具有较好的响应特性,因此在该系统中,设计了速度闭环反馈控制器,通过PID控制完成三个比例阀的同步控制,以达到速度闭环控制和能量回收的目的。
当操作者希望动臂下落时(即油缸回缩),其通过操作手柄给出速度控制信号,给定信号与传感器反馈的油缸速度值进行比较,通过PID控制器计算出三个比例阀的开度,并将相应的控制信号施加阀A、阀B和阀C。在动臂下降过程中,油缸大腔中的油液一部分通过阀A进入小腔实现流量再生,一部分通过阀B流回油箱,另一部分通过阀C进入蓄能器。在控制器和系统参数的匹配过程中,原则上要求有更多的压力油进入蓄能器,即较少的油液流回油箱。
2 系统参数设计
挖掘机动臂液压缸:活塞直径为100mm,活塞杆直径为50mm。当动臂全行程下降时,大腔体积变化约为5L,小腔体积变化约为3.75L。在该系统中,由于大腔和小腔采用了差动连接,则其中的3.75L油液将被补充到小腔,实现流量再生。假设系统不存在泄漏且油液不流回油箱,则流向蓄能器的油液体积约为1.25L。因此,基于以上条件,可初步选定蓄能器的体积为2.5L、5L、7.5L和10L四个等级。
根据负载独立流量分配(LUDV)系统试验数据可知,动臂下降过程中,油缸大腔回油压力约为8~9MPa,为了获得更好的动臂势能回收效果,通常希望蓄能器压力尽可能与回油背压接近,减少阀上的压降损失。然而蓄能器压力是随充液体积增加而变大,所以需要合理设置蓄能器的初始压力以获得更好的回收效率。图2、图3分别为不同蓄能器参数条件下的能量回收效率,图4、图5为改变蓄能器参数时动臂液压缸的速度控制特性。由图2和图5可知,蓄能器体积和初始压力对势能回收效率和速度控制特性有着较大影响。从总体变化趋势而言,随着蓄能器体积增大,速度控制特性变好,能量回收效率增高,即有更多的能量被储存到蓄能器内;但当蓄能器体积大于5L以后,其体积变化对能量回收率和速度控制特性的影响将减弱,并不显著。随着蓄能器初始压力的升高,回收效率随之降低,但并不显著;综合考虑图3、图5中的数据,当初始压力为5MPa时,具有良好的综合性能。根据上述分析结果,可以确定该系统中蓄能器预充压力为5MPa,体积为5L。
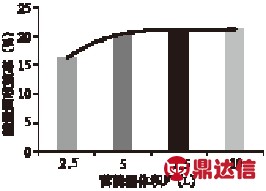
图2 蓄能器变体积能量回收效率
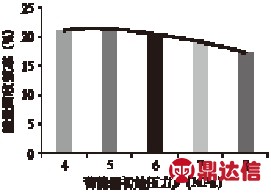
图3 蓄能器不同预充压力能量回收效率
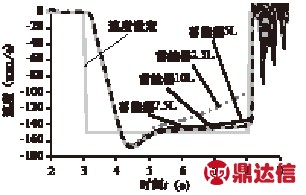
图4 蓄能器变体积速度控制特性
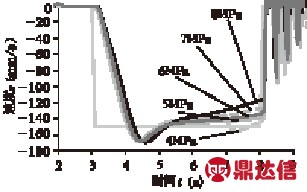
图5 蓄能器不同预充压力速度控制特性
3 节能性能对比分析
为了检验文中所提出新的挖掘机动臂势能蓄能器回收系统的综合性能特性,将该系统与传统的LUDV系统进行对比。
3.1 LUDV性能分析
图6、图7为传统的LUDV系统动臂下降工况下的速度控制特性和功率损失情况。由图6可知,在0~1.9s、5.9~7s时间间隔内,执行机构不动作;在1.9~5.9s时间间隔内,动臂以139.5mm/s的速度下降;下降过程中,在动臂重力作用下,大腔内油液压力约为6.5MPa,小腔压力则为0.8MPa,此时泵输出压力比执行机构大约高出约3.5MPa(这由LUDV系统特性决定的)。在LUDV系统中,动臂下降时的重力势能被转换为液压能,并损失在阀口节流上;由图7可知,在动臂下降过程中,小腔进油多路阀节流功率损失约为1.4kW,由于大腔回油节流损失严重,节流功率损失约为6.3kW,此时液压泵输出功率为3.5kW。
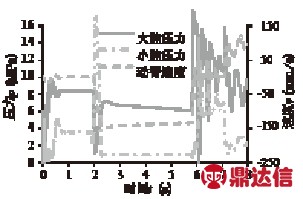
图6 LUDV动臂下降控制特性
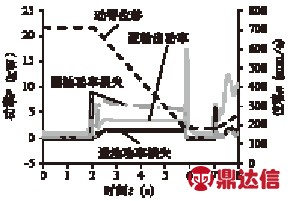
图7 LUDV动臂下降功率损失
3.2 新系统性能分析
图8、图9为新系统的蓄能器初始压力为5MPa时动臂速度特性和功率损失情况。由图8可知,在动臂下降过程中,在0~3s、8~12s时间间隔内,执行机构不动作;在3~8s时间间隔内,动臂以150mm/s的速度下降,速度相对较稳定。由图9可知,在6s时刻,动臂大腔流出功率约为8.5kW,再生功率为1.7kW,蓄能器回收功率约为1.9kW,阀A功率损失约为4.1kW,阀B功率损失约为0.48kW,阀C功率损失约为0.19kW。在工作全程内,动臂大腔流出能量约为38.7kJ,动臂小腔流入能量约为8.6kJ,蓄能器回收能量约为8.3kJ,能量回收效率约为21.4%。由于在此过程中,油缸的大腔和小腔之间采取了差动连接,从理论角度而言,液压泵不需要向油缸小腔供油。因此,与LUDV系统相比,新系统具有明显的节能优势。
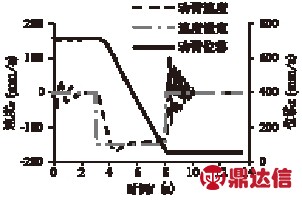
图8 新系统动臂下降控制特性
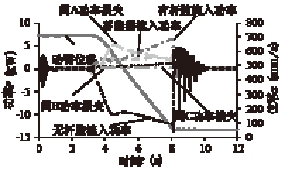
图9 新系统动臂下降功率特性
图10为新系统的蓄能器初始压力为5MPa时动臂各种下降速度下,蓄能器回收效率(计算按蓄能器能量变化/无杆腔输出能量)。由图10可知,新设计系统在各种运行速度下均能达到良好的回收特性,平均回收功率变化不大,并且不随系统设定速度变化而变化。主要原因是控制系统中动臂无杆腔压力大小与稳定运行速度不存在必然关系,即在各种速度情况下,无杆腔压力水平近似一致,并且蓄能器压力变化与流入蓄能器的油液体积成一定关系,各种速度情况下,当蓄能器预充压力保持一致时,最终回收油液体积基本一致,因此回收效率近似。
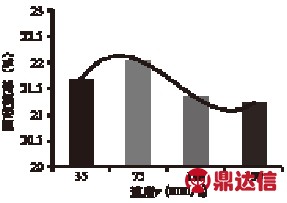
图10 新系统动臂下降几种速度回收效率
4 结 论
本文设计了一种基于液压蓄能器的挖掘机动臂势能回收再生系统,通过控制器控制再生、回收及回油三个两位两通比例阀的开度,实现对动臂下降速度的精确控制,同时也实现动臂势能回收,研究结果表明该系统的能量回收效率约为21.4%;蓄能器体积和初始压力对动臂下降速度特性和能量回收效率有着较大的影响,对于本文所研究的液压挖掘机而言,当蓄能器体积为5L、初始压力为5MPa时,可取得良好的综合性能,并且回收效率基本不受速度设定值的影响,具有良好的回收特性。