0 前言
在轧机控制系统中,液压压下系统是控制较为复杂、干扰因素多、负载力较大、交联耦合比较严重、且控制精度和响应性要求颇高。因此,油源系统的稳定性必须得到保证。300 mm可逆冷轧机的油源[1]系统由恒压变量泵、泵口蓄能器、管道、阀前蓄能器等组成,其供油系统简图如图1所示,其功能是向轧机电液控制系统提供压力稳定、流量充裕、洁净的工作介质。由于柱塞泵本身存在高频脉动,恒压伺服结构存在变量时间常数,恒压油源出口容腔越大,时间常数就越大,相应响应速度变慢;且油源瞬时流量的波动导致瞬时压力变化,进而影响系统的控制精度[2,3];而电液伺服阀所控制的伺服液压缸存在负载冲击,这种冲击进而又影响油源压力的波动。要达到系统的控制精度。必须保证压力的稳定性。阀前蓄能器能够吸收波动,稳定压力,因此,阀前蓄能器的选取和充气压力值至关重要。
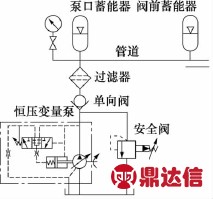
图1 供油系统原理图
1 300 mm可逆冷轧机压下系统的组成
300 mm可逆冷轧机液压压下系统是板带轧制厚度自动控制(AGC)系统的基本环,接受AGC系统的控制,进行压下缸的位置(或力)闭环控制,使压下缸实时准确的跟踪设定值。液压压下系统由控制器、电液伺服阀、液压缸、轧机负载、位置传感器、压力传感器等构成。测厚仪闭环作为AGC的监控外环,对板厚差作最后的修正[4]。其控制功能示意图[3]如图2所示。
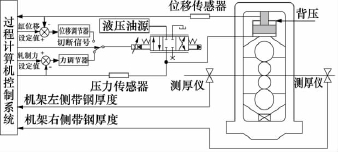
图2 冷带轧机板厚自动控制系统功能示意图
2 压下系统与阀前蓄能器
试验在本校的300 mm 4辊可逆冷轧机上进行,轧机系统主要试验参数如表1和参考文献[5,6],阀前蓄能器所采用的是浙江奉化生产的容积为0.63 L,1.0 L,1.6 L的NXQ系列囊式蓄能器,公称压力均为20 MPa。阀前压力传感器的量程为20 MPa的TKE1B02MV传感器,采集周期为0.005 s。
表1 轧机参数列表
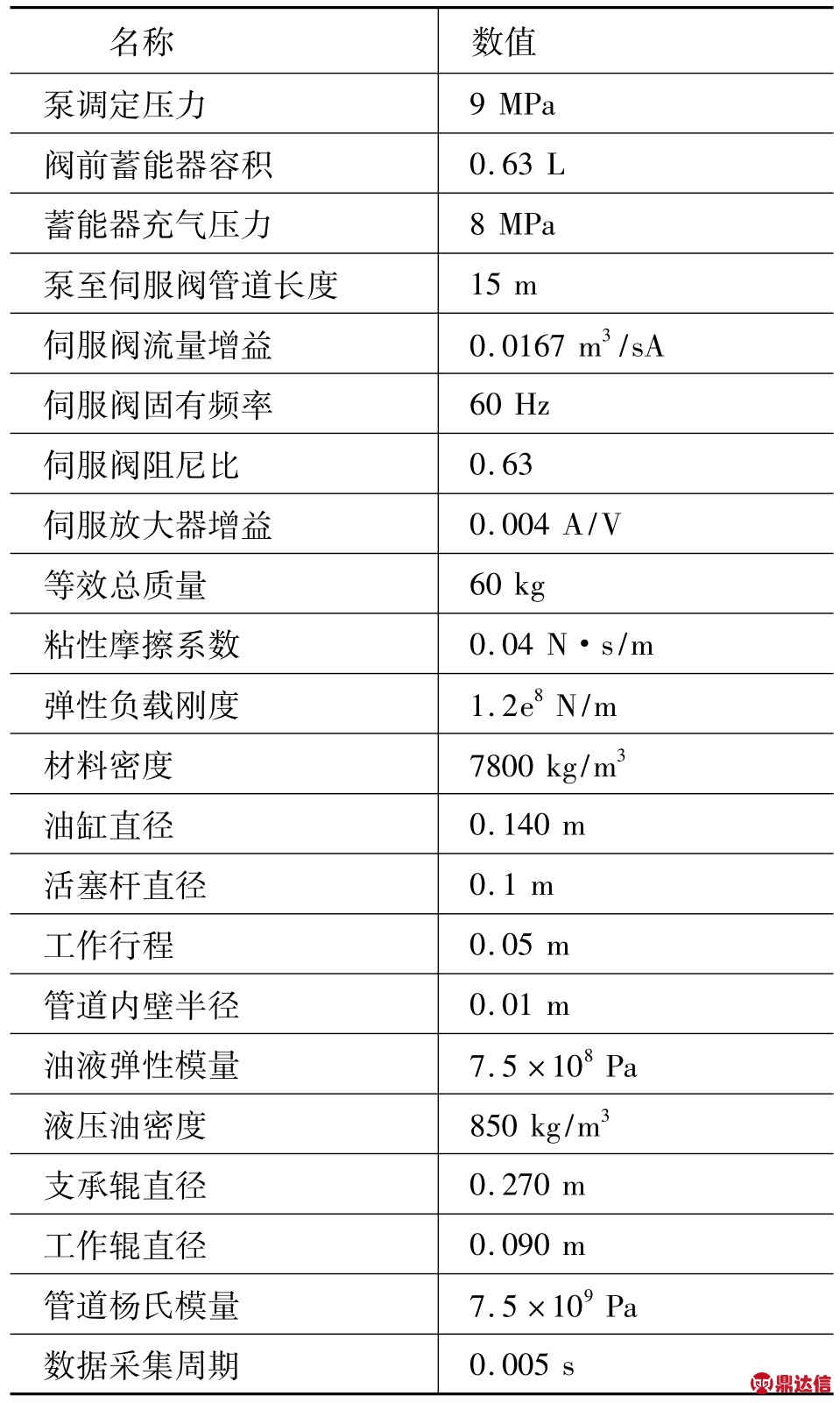
3 阀前蓄能器与油源压力波动的实验研究
因泵出口到阀前距离较大,对压下控制精度产生影响的是阀前压力波动,故需测量研究阀前油源压力波动的变化。当输入负载指令为4 Hz的正弦信号,阀前入口处蓄能器打开(VP)和关闭(NVP)两种情况下阀前油源压力变化如图3所示,从图中可看出轧机阀前蓄能器能够吸收抑制一定的压力波动[6]。
3.1 阀前蓄能器充气压力对油源波动的影响
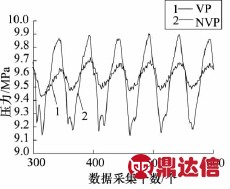
图3 蓄能器开关试验曲线
闭压力环,轧机压下控制系统输入周期2 s,幅值为5T±2T的方波指令信号,泵出口压力调为9 MPa。阀前蓄能器公称容积为0.63 L,充气压力为4 MPa,6 MPa,8 MPa时,阀前油源压力波动如图4a。
阀前蓄能器为0.63 L,在充气压力为4 MPa,5 MPa,6 MPa,7 MPa,8 MPa时,可得阀前油源压力波动幅度与充气压力之间的关系,如表2以及相应的拟合方程和曲线,如图4b。
表2
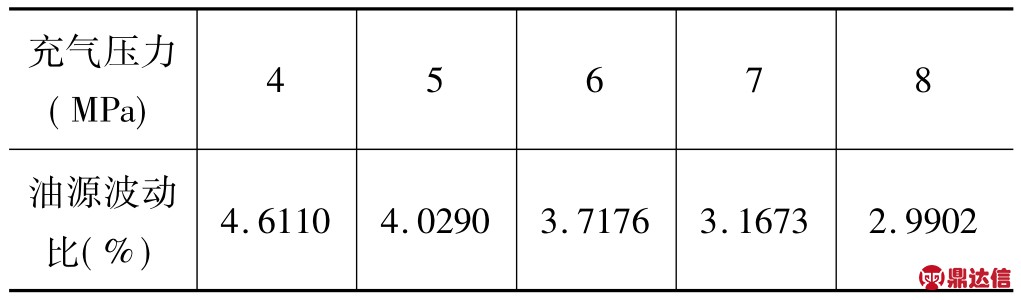
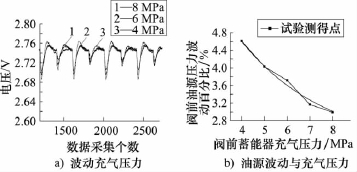
图4 0.63 L蓄能器
轧制力同上,阀前蓄能器为1.0 L,充气压力为4 MPa,6 MPa,8 MPa 时,阀前油源压力波动如图 5a。
1.0 L 蓄能器充气压力为 4 MPa,5 MPa,6 MPa,7 MPa,8 MPa时,阀前油源压力波动幅度与充气压力之间的关系如表3及相应的拟合方程和曲线图5b所示。
表3
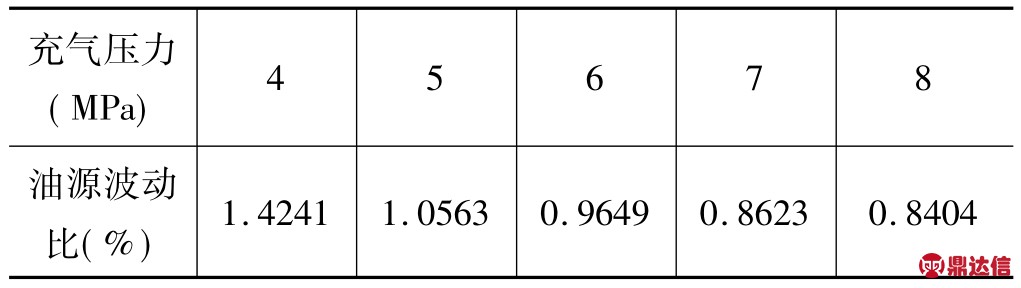
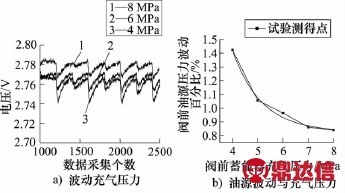
图5 1.0 L蓄能器
轧制力同上,阀前蓄能器为1.6 L,充气压力为4 MPa,6 MPa,8 MPa 时,阀前油源压力波动如图 6a。
阀前蓄能器为 1.6 L,在充气压力为 4 MPa,5 MPa,6 MPa,7 MPa,8 MPa 时,可得阀前油源压力波动幅度与阀前蓄能器充气压力之间的关系如表4以及相应的拟合方程和曲线(光滑曲线)如图6b。
表4
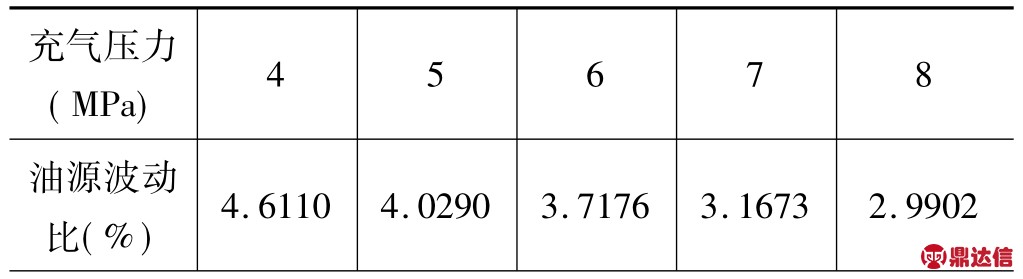
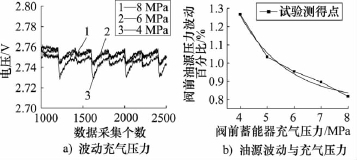
图6 1.6 L蓄能器
由图6可知在阀前蓄能器为1.6 L时,当充气压力达到一定值后,阀前油源压力的波动随着充气压力的增加变化不再明显。
在轧制力相同的条件下,以上3种不同容积蓄能器分别在充气压力为 4 MPa,5 MPa,6 MPa,7 MPa,8 MPa时的对比图如图7。
从阀前油源压力波动图和对比图知:与其他公称容积较大蓄能器相比,容积较小的阀前蓄能器对油源压力波动的抑制较弱,油源波动较大且有锋刺,易对系统造成冲击,降低系统寿命;蓄能器为0.63 L时,油源压力波动百分比随着蓄能器充气压力的增加而减小,但油源波动多在3%以上。保证轧机压下AGC系统的控制精度不受影响[7],油源压力的波动幅度应小于3%。
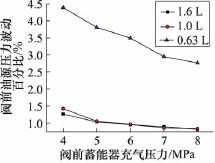
图7 蓄能器阀前波动对比图
4 结论
通过以上分析得出:(1)油源压力的波动幅度随着阀前蓄能器充气压力的增大而减小;随着蓄能器容积的增加,油源波动幅度的变化不再明显;(2)现今300 mm 4辊可逆冷轧机阀前蓄能器采用0.63 L不够合理,较难满足液压压下控制系统精度对油源压力波动幅度低于3%的要求;(3)阀前蓄能器为1 L时,能够满足液压压下系统精度对油源波动的要求,比其他两容积的蓄能器较为合理。本文结论为轧机油源结构的优化和进一步提高液压压下控制精度提供了参考。